
1168
.pdf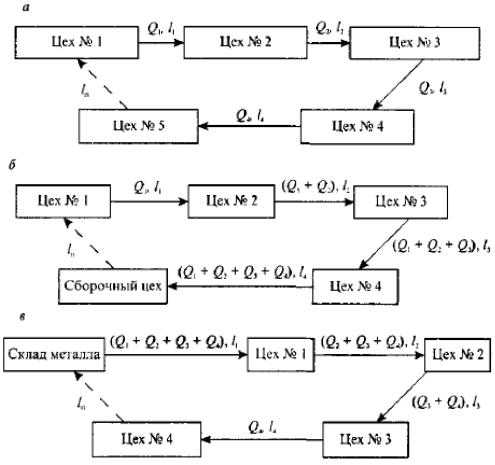
подготовительная работа. Из всего многообразия перевозок в цехах особое внимание уделяется межоперационному перемещению объектов производства, которое должно осуществляться в точном соответствии с последовательностью протекания и ритмом производственного процесса.
Рис. 2.6 – Схемы кольцевых маршрутов [4]:
а– с равномерным грузопотоком, б – с нарастающим грузопотоком,
в– с уменьшающимся грузопотоком.
Для изображения транспортно-технологических процессов составляются транспортно-технологические системы (ТТС), которые показывают последовательность и способы выполнения всех погрузочно-разгрузочных и транспортных операций, места и методы укладки и разборки грузов. По ТТС можно определить число операций перемещения во всем транспортном процессе с выделением погрузочно-разгрузочных и транспортных операций, выполняемых вручную и механизированным способом. Все операции перемещения ТТС должны быть нормированы по затратам труда рабочих и времени работы различных подъемно-транспортных машин.
53
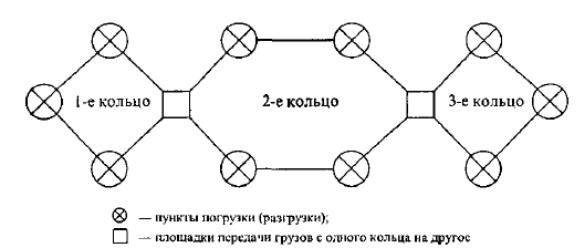
Рис. 2.7 – Схема циклового маршрута [4]
Необходимо учитывать, что границы системы, в которых производят перевозки, выходят за пределы предприятий и включают поставщиков (сырья, тары), потребителей готовой продукции предприятия, а также транспортные организации.
Эти вопросы необходимо решать совместно уже в рамках логистической системы.
Формы организации внутризаводского транспорта зависят от мощности грузопотоков и объема грузооборота.
Грузопоток – показатель, характеризующий объем перевозок грузов, перемещаемых в единицу времени между двумя пунктами – погрузки и выгрузки. Различают грузопотоки внешние и внутренние.
Внешние грузопотоки, характеризующие объем прибывающих на предприятие грузов, называются грузопотоками прибытия, а объем отправляемых с предприятия грузов – грузопотоками отправления. Эти грузопотоки измеряются в тоннах или тонно-километрах. Мощность грузопотоков на внутризаводском транспорте в зависимости от специфики производства может измеряться в тоннах, в условных тоннах, в таропотоках и в тарооперациях.
Сумма отдельных грузопотоков на предприятии представляет собой грузооборот – основной показатель, характеризующий объем транспортной работы на предприятии.
Грузооборот – это общее количество грузов, перемещаемых на территории предприятия (цеха) за расчетный период (год, месяц). Расчет грузооборота предприятия производится на основе грузооборотов цехов и общезаводских складов.
54
На основе схемы грузопотоков, объема перевозок по каждой группе грузов производят выбор транспортных средств и расчет потребности в них.
При выборе транспортных средств необходимо учитывать следующие условия:
1)транспортные средства должны удовлетворять всей совокупности показателей данного грузопотока, т.е. мощности грузопотока, расстоянию и трассе грузоперемещения, габаритным размерам и физико-техническим свойствам груза. Грузы в зависимости от их характеристики, способов погрузки и перемещения делятся на следующие группы:
сыпучие (наволочные, формованные материалы, уголь и т.д.);
наливные грузы (нефтепродукты, химические, жидкие и др.);
штучные грузы:
длинномерные (длиной более 3 м) – сортовой и профильный прокат,
трубы, крупный лес и др.;
короткомерные (длиной до 3 м) – заготовки, детали и др.;
штучные массовые (массой до 50 кг) – болванки, заготовки, детали и др.;
тарно-упаковочные – контейнеры, ящики, бочки, рулоны и др.;
тяжеловесные – оборудование, поковки, слитки и др.;
2)транспортные средства должны соответствовать техническим и организационным особенностям обслуживаемого ими производственного процесса;
3)транспортные средства должны обеспечивать максимальную производительность труда и наиболее благоприятные условия труда на обслуживаемом участке;
4)технические характеристики транспортных средств, работающих на смежных участках, должны быть согласованы для дальнейшего повышения уровня механизации транспортных и разгрузочнопогрузочных работ;
5)избранные транспортные средства по экономическим показателям должны быть наиболее эффективными среди имеющихся вариантов
[4].
Вданном разделе приведены расчеты необходимого количества транспортных средств, используемых внутри и между цехами предприятия, а также их технико-экономических показателей [3].
55
Схема маршрутов межцеховых перевозок устанавливается на основе шахматной ведомости, которая дает наглядную картину грузооборота и служит основой для расчета количества транспортных средств.
Как известно, на предприятиях используют различные схемы маршрутов: маятниковые односторонние, двусторонние, смешанные, маятниковые центробежные и центростремительные кольцевые. В зависимости от выбранной схемы маршрута определяют количество транспортных средств.
Число транспортных средств прерывного действия (автомобилей, авто- и электрокаров, робоэлектрокаров и т.д.), необходимых для межцеховых перевозок, может быть определено по одной из следующих формул.
Для маятниковых перевозок:
при одностороннем маршруте движения
|
|
|
H |
|
|
|
|
|
|
|
|
|
|
|
|
|
N j |
QШТ j |
|
|
2 L |
|
|
|
|
|
|||
|
|
|
j 1 |
|
|
|
|
|
|
|
(2.54) |
|||
KТ.С |
|
|
|
|
|
|
|
|
tЗ |
|
; |
|||
q K |
|
F K |
|
60 |
|
|||||||||
|
ИС |
CM |
|
|
|
|
tР |
|
||||||
|
|
|
|
Э |
|
VСР |
|
|
|
|
|
при двустороннем маршруте движения
|
|
H |
|
|
|
|
|
|
|
|
|
|
|
N j QШТ j |
|
|
|
2 L |
|
|
|
|
|
|
|
j 1 |
|
|
|
|
|
|
|||
KТ.С |
|
|
|
|
|
|
|
2 |
|
, |
(2.55) |
|
|
|
|
||||||||
|
q KИС |
FЭ KCM |
60 |
|
|
tЗ |
|
tР |
|
||
|
|
|
VСР |
|
|
|
|
где Nj – количество изделий j -го типоразмера (наименования), перевозимых в течение расчетного периода, шт.; QШТ j – масса единицы изделия j -го типоразмера, кг; q – грузоподъемность единицы транспортных средств, кг; KИС – коэффициент использования грузоподъемности транспортного средства; FЭ – эффективный фонд времени работы единицы транспортного средства для односменного режима, ч; KCM – число рабочих смен в сутки; L – расстояние между двумя пунктами маршрута, м; VCP – средняя скорость движения транспортного средства, м/мин; tЗ и tР – соответственно время на одну погрузочную и разгрузочную операции за каждый рейс, мин; Н – номенклатура транспортируемых изделий.
Для кольцевых перевозок:
с нарастающим грузопотоком
56

|
|
H |
|
|
|
|
|
|
|
|
|
|
|
|
N j QШТ j |
|
|
|
' |
|
|
|
|
||||
|
|
j 1 |
|
|
|
|
|
|
|
|
|||
KТ.С |
|
|
|
|
|
|
|
L |
k |
ПР t |
|
(2.56) |
|
q K |
ИС |
F |
K |
CM |
60 |
|
|
З tP ; |
|||||
|
|
Э |
|
|
|
VСР |
|
|
|
|
с затухающим грузопотоком
|
|
H |
|
|
|
|
|
|
|
|
|
|
N j QШТ j |
|
|
|
' |
|
|
||||
|
|
j 1 |
|
|
|
|
|
|
|||
KТ.С |
|
|
|
|
|
|
|
L |
|
(2.57) |
|
q K |
|
F |
K |
|
60 |
|
|||||
ИС |
CM |
|
|
tЭ kПР tР ; |
|||||||
|
|
Э |
|
|
|
VСР |
|
|
с равномерным грузопотоком
|
|
H |
|
|
|
|
|
|
|
|
|
|
|
|
|
|
N j QШТ j |
|
|
|
' |
|
|
|
|
|
|
|
|
|
|
j 1 |
|
|
|
|
|
|
|
|
|
|||
KТ.С |
|
|
|
|
L |
k |
ПР |
t |
З |
t |
P |
, |
(2.58) |
|
|
|
|
||||||||||||
|
q KИС FЭ KCM |
60 |
|
|
|
|
|
|
||||||
|
|
VСР |
|
|
|
|
|
|
|
|
где L' – длина всего кольцевого маршрута, м; kПР – число погрузочноразгрузочных пунктов.
Масса груза QCM (кг,т), перевозимого за смену, определяют по формуле
QСМ |
QГ |
, |
(2.59) |
ДР КСМ kН |
где QГ – годовой грузооборот на данном маршруте, кг (т); ДР – число рабочих дней в году; kH – коэффициент неравномерности перевозок (принимается kH = 0,85).
Время пробега транспортного средства по заданному маршруту определяют по формуле
ТПРОБ |
L |
. |
(2.60) |
|
|||
VСР |
|
Время, затрачиваемое транспортным средством на один рейс, рассчитывают по формуле
TP 2 TПРОБ tЗ tP. |
(2.61) |
Число рейсов, совершаемых единицей транспортного средства за сутки, определяют по формуле
P |
tСМ КСМ kВ |
, |
(2.62) |
|
ТР
где kB – коэффициент использования фонда времени работы транспортного средства.
Массу груза, перевозимого за один рейс, определяют по формуле
57
|
|
П |
QCМ |
. |
|
|
|
(2.63) |
|
|
|
|
|||||
|
|
|
P |
|
|
|
|
|
Число конвейеров определяют по формулам: |
|
|||||||
для штучных грузов (изделий, деталей и т.д.) |
|
|||||||
КС |
|
QС lO |
|
|
, |
(2.64) |
||
|
|
|
|
|||||
|
3,6 QШТ V tCM KCM kB |
|
||||||
для сыпучих грузов |
|
|
|
|
||||
КС |
|
QС |
|
, |
(2.65) |
|||
3,6 qП V tCM KCM |
|
|||||||
|
|
kB |
|
где QC – суммарный транспортируемый груз в течение суток, кг; lO – шаг конвейера (расстояние между двумя изделиями), м; 3,6 – постоянный коэффициент; QШТ – масса (вес) одного транспортируемого изделия, кг; V – скорость движения конвейера, м/с; qП – нагрузка (масса груза) на 1 м² конвейера, кг.
Число грузовых крюков на подвесном конвейере рассчитывают по формуле
АК |
NC |
LP |
, |
(2.66) |
|
nИ V tCM KCM kB |
|||||
|
|
|
где NC – количество транспортируемых изделий в течение суток, шт.; LP – длина рабочей части конвейера, м; nИ – количество изделий, навешиваемых на один крюк, шт.
Число электрокаров определяют по формуле
KЭК |
TP NC |
|
. |
(2.67) |
tCM KCM |
|
|||
|
kB |
|
Потребное число электро- и автокаров для внутрицеховых перевозок определяют укрупненно по формуле
|
Q k |
n |
1 |
|
|
|
2 L |
|
|
||||
|
CM |
|
|
|
|
|
|
|
|
|
(2.68) |
||
KТ.С |
|
|
|
|
|
|
|
|
|
|
|
tЗ tР , |
|
q K |
ИС |
t |
CM |
k |
|
V |
|||||||
|
|
|
|
B |
|
CP |
|
|
где (kB + 1) – среднее число передач партии деталей между операциями на склад и со склада за смену.
Часовую пропускную способность конвейера рассчитывают по формулам
qЧ 3,6 qM V; |
(2.69) |
58
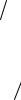
при перемещении штучных грузов на подвесном круговом конвейере
qЧ 3,6 QШТ V l0 ; |
(2.70) |
при перемещении штучных грузов в специальной таре по р штук на поточной линии цеха
qЧ 3,6 QШТ р V l0 , |
(2.71) |
где qM – масса груза, приходящаяся на 1 м длины конвейера, кг/м; p – величина транспортной партии, шт.
Примеры типовых задач с пошаговым решение по разделу «Организация транспортного хозяйства», приведены в приложении
12.
2.5.5.Организация складского хозяйства
Впроцессе движения материальных ценностей между службой материально-технического обеспечения и производственными подразделениями, между цехами предприятия, а также между выпускающими цехами и службой сбыта возникает необходимость в организации складских помещений, образующих складское хозяйство предприятия. Основными задачами складского хозяйства являются: 1) бесперебойное обеспечение производства соответствующими материальными ресурсами; 2) обеспечение сохранности материальных ресурсов;
3) максимальное сокращение затрат, связанных с осуществлением складских операций.
Складское хозяйство предприятия выполняет следующие функции:
приемка и хранение материальных ценностей;
подготовка их к выдаче в производство (расфасовка, комплектование, перетаривание и т.п.);
выдача материальных ценностей в производство в установленном порядке;
подготовка готовой продукции к отправке потребителю (комплектование, этикетирование, упаковка и т.п.);
отпуск готовой продукции потребителю с оформлением необходимой документации;
организация учета движения запасов и их регулирование;
59
разработка и внедрение мероприятий по совершенствованию складского хозяйства.
Организация складского хозяйства оказывает прямое влияние на результаты производственно-хозяйственной деятельности предприятия, так как обеспечивает бесперебойность работы основного производства очередь эффективность складского хозяйства зависит прежде всего от складских помещений. Применение универсальных складов с низким уровнем механизации увеличивает стоимость складских операций и может привести к сбою в их работе.
Вто же время высокомеханизированные и специализированные внутризаводские склады позволяют добиваться высокой организации их работы.
Классификация складских помещений осуществляется по ряду признаков.
1. В зависимости от рода хранимых ценностей различают следующие внутризаводские склады: материальные, полуфабрикатов и заготовок, инструментов, оборудования и запасных частей, готовой продукции, хозяйственные, отходов и утиля.
Всвою очередь материальные склады подразделяются на склады металлов, топлива, химикатов и т.д. в зависимости от номенклатуры и объема потребляемых материалов.
2. В зависимости от характера и номенклатуры хранимых ценностей
различают: универсальные и специализированные склады. На универсальных складах хранятся разнообразные по характеру материальные ценности с широкой номенклатурой (центральный материальный склад). Специализированные склады используются для хранения однородной продукции (склады лесоматериалов, чугуна и т.п.).
3. По масштабу работы склады делятся на общезаводские, обслуживающие несколько цехов, и цеховые, обслуживающие подразделения одного цеха.
4. По роли в процессе производства и подчиненности общезаводские склады подразделяются на:
снабженческие – подчиненные отделу материальнотехнического обеспечения (склады сырья, топлива, покупных полуфабрикатов);
производственные – подчинены производственному отделу предприятия и предназначены для хранения полуфабрикатов
60
собственного производства (склады заготовок и полуфабрикатов собственного производства);
сбытовые – подчиненные отделу сбыта, хранящие готовую продукцию, подлежащую отправке потребителю (склады готовой продукции и отходов);
инструментальные – подчинены инструментальному отделу
(ЦИС);
оборудования и запчастей, подчинены отделу главного механика;
6)хозяйственные, предназначены для хранения хозяйственных товаров, спецодежды.
5. Цеховые склады подразделяются на склады материалов и заготовок, инструмента (ИРК) и промежуточные – для хранения межоперационных заделов.
6. По конструктивным особенностям склады классифицируются на:
закрытые, представляют собой одноили многоэтажные здания, отапливаемые или неотапливаемые и т.д.;
полузакрытые склады, представляют собой навесы одно- и двухскатные, с подсыпкой и без подсыпки и т.д.;
открытые – это площадки или платформы, оборудованные или необорудованные;
специальные – это резервуары, элеваторы, бункеры, цистерны и т.п.
Количество и тип складских помещений зависят от производственной структуры предприятия, масштабов и типа производства, характера связей по кооперации с другими предприятиями. Размещение складских помещений решается с учетом требований, предъявляемых к генеральному плану предприятия, и наиболее рациональной транспортно-технической схемы. Склады необходимо оборудовать подъездными путями, погрузочно-разгрузочными и транспортными средствами, различного рода стеллажами. Они должны быть оснащены измерительным оборудованием: весами, бензо- и нефтесчетчиками, линейными мерами и т.п. Техническое оснащение складов зависит от рода, формы и количества хранимых материалов, характера, типа и расположения складских помещений и существующей системы транспортировки материалов [4].
В данном разделе приведены расчеты площадей складских помещений и других технико-экономических показателей [3].
61
Общую площадь склада S (м²) определяют по формуле |
|
||
S |
SИСП |
, |
(2.72) |
|
|||
|
KИСП |
|
где SИСП – полезная площадь склада, непосредственно занятая хранимыми материалами, м²; КИСП – коэффициент использования площади склада, учитывающий вспомогательную площадь для проездов, проходов, приема и выдачи материалов, весов, шкафов, стола кладовщика и т.д.
Полезную площадь рассчитывают в зависимости от способа хранения материалов по следующим формулам:
при напольном хранении в штабелях
SПОЛ |
Zmax |
, |
(2.73) |
|
|||
|
qg |
|
|
при хранении в стеллажах |
|
||
SПОЛ SСТ nСТ , |
(2.74) |
где Zmax – величина максимального складского запаса материалов, определяемого по формуле; qg – допустимая масса груза на 1 м² площади пола (согласно справочным данным), т (кг); SCT – площадь, занимаемая одним стеллажом, м; nCT – расчетное количество стеллажей.
n |
|
|
Zmax |
|
, |
(2.75) |
||
|
|
|
||||||
CT |
V |
k |
ЗП |
q |
|
|||
|
|
o |
|
|
У |
|
где Vo – объем стеллажа, м³ (см³); kЗП – коэффициент заполнения объема стеллажа; qУ – плотность хранимого материала, т/м³ (г/см³).
Vo a b h, |
(2.76) |
где a, b и h – соответственно длина, ширина и высота стеллажа, м.
Принятое количество стеллажей устанавливается после проверки соответствия их числа допустимой нагрузке по формуле
nCT.ПP |
|
Zmax |
. |
(2.77) |
|
||||
|
|
SCT qg |
|
62