
Лекция 5. Гибка листового проката
.pdfЛекция 5 ГИБКА ЛИСТОВОГО ПРОКАТА
5.1 Общие сведения
Основным методом изготовления деталей в химическом аппаратостроении является гибка листового проката, выполняемая большей частью на валковых листогибочных машинах. От правильности выбора технологии гибки листового проката во многом зависят трудоемкость изготовления аппарата и его эксплуатационные характеристики.
Изготовление листовых деталей путем изгиба между валками имеет значительные преимущества перед выполнением подоб-ных операций на прессах и в штампах. В первом случае практически отпадает надобность в изготовлении оснастки, либо требуется оснастка очень простого исполнения. Так, например, технологический анализ двух методов изготовления толстостенных обечаек штамповкой на прессах и гибкой листа на валковой листогибочной машине показывает значительные преимущества последнего (табл. 5.1).
Таблица 5.1 – Сравнительная трудоемкость изготовления обечаек
Метод |
Норма времени (час) на изготовление одной |
||||
изготовления |
|
обечайки диаметром, мм |
|
||
|
|
|
|
|
|
|
1000 |
|
1500 |
|
2000 |
|
|
|
|
|
|
гибка |
9,6 |
|
11,4 |
|
12,0 |
|
|
|
|
|
|
штамповка |
79,4 |
|
104,4 |
|
108,5 |
Возможность изгиба на валковой листогибочной машине не только листового проката, но и различных видов профильного проката делает этот вид оборудования универсальным и практически незаменимым в условиях аппаратостроения.
Гибка осуществляется посредством пластического изгиба при перемещении заготовки между вращающимися валками. Зона
39

деформаций в данный момент времени охватывает небольшой участок заготовки и в процессе деформирования непрерывно перемещается по ее длине. Подача заготовки происходит за счет сил трения, возникающих между нею и валками. Технологические процессы гибки между валками можно разделить на три вида:
-выполняемые цилиндрическими валками,
-профилированными валками; и
-с применением специальных приспособлений - колец, надеваемых на гладкие валки.
В процессе гибки изменяются механические свойства ма- те-риала, повышаются прочностные характеристики материала, а показатели пластических свойств падают. В этом случае действи-
тельная зависимость между напряжениями и деформациями наиболее близко аппроксимируется степенной функцией вида
где
риала.
A m A и
, |
(5.1) |
m - постоянные коэффициенты для данного мате-
Определение коэффициентов производится по следующим формулам:
|
lg |
|
|
в |
|
|
||
|
|
|
|
|
|
|||
|
|
|
|
|
|
|||
m |
|
|
|
т |
; |
|
||
|
|
|
|
|
||||
|
|
|
|
|
|
|||
|
lg |
в |
|
|
||||
|
|
|
|
|
||||
|
|
|
|
|
||||
|
|
|
|
т |
|
|
||
|
|
|
|
|
|
|
|
|
A |
|
в |
|
, |
|
|
||
|
|
|
|
|
||||
|
|
m |
|
|
|
|||
|
в |
|
|
|
|
|
|
|
|
|
|
|
|
|
|
|
|
где |
T |
|
|
и |
в |
- деформации, соответствующие |
текучести и В - пределу прочности.
|
Т |
|
(5.2)
(5.3)
- пределу
Значения напряжений и деформаций в формуле (5.3) определяются путем обычных механических испытаний образцов на растяжение или по справочным данным.
40
В таблицах 5.2 и 5.3 приведены значения |
A |
и |
m |
для |
наиболее распространенных в аппаратостроении марок сталей в холодном и нагретом состояниях. Материал одной марки, но разных поставок может иметь колебания механических свойств в пределах, установленных стандартами. Поэтому коэффициенты
A |
и |
m |
определяются не по предельным, а по средним значениям |
механических свойств. В этом случае колебания механических свойств материала в меньшей степени отразятся на точности технологических расчетов.
Таблица 5.2 – Механические свойства наиболее употребительных марок сталей в холодном состоянии
Марка стали |
στ, |
σ в , |
А, |
m |
n |
|
кгс/мм2 |
кгс/мм2 |
кгс/мм2 |
|
|
|
|
|
|
|
|
Ст.3 |
23 |
43 |
47,7 |
0,141 |
0,0057 |
|
|
|
|
|
|
12Х18Н10Т |
20 |
55 |
67,0 |
0,2 |
0,0071 |
ЭИ 943 |
27 |
55 |
67,7 |
0,162 |
0,0081 |
Таблица 5.3 – Механические свойства наиболее употребительных марок сталей в нагретом состоянии
Марка стали |
t, |
στ, |
σ в , |
А, |
m |
n |
|
0 С |
кгс/мм2 |
кгс/мм2 |
кгс/мм2 |
|
|
Ст.3 |
400 |
18,7 |
21,3 |
22,3 |
0,03 |
0,0037 |
|
600 |
13 |
15,8 |
16,4 |
0,039 |
0,0035 |
|
800 |
5,2 |
6,4 |
6,5 |
0,037 |
0,0017 |
12Х18Н10Т |
400 |
18,5 |
46 |
56,7 |
0,194 |
0,0065 |
|
600 |
16,5 |
38,5 |
46,6 |
0,179 |
0,0055 |
|
700 |
15 |
32 |
39,3 |
0,165 |
0,0046 |
ЭИ 943 |
600 |
20 |
45 |
52,9 |
0,168 |
0,0063 |
Величина изгибающего момента определяется из уравнения равновесия между внешними и внутренними силами и равна
41
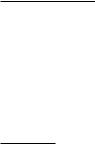
bhm 2 A
М2m 1 Rm (m 2)
где |
R |
- радиус изгиба; |
b |
- ширина листа; |
h |
- толщина листа. |
Величина остаточного радиуса определяется по формуле:
R0
(5.4)
(после пружинения)
R |
|
R |
, |
(5.5) |
|
1 m |
|||
0 |
1 |
|
|
|
|
nr |
|
|
|
где r – радиус валка листогибочной машины. |
|
Одной из основных характеристик пружинения заготовки являются ее физико-механические свойства, зависящие от температурного состояния материала. Формулы (5.4) и (5.5) сохраняются и для случая деформирования металлов в нагретом состоя-
нии. В этом случае значения |
A , |
m |
и |
n |
должны подставляться |
для соответствующих значений температур. Влияние каждого из указанных параметров на величину пружинения различно. Если модуль упругости Е с повышением температуры изменяется незначительно (табл. 5.4), то значения A и m , зависящие от предела текучести и предела прочности, при соответствующих значениях температур будут иметь значительные изменения.
Таблица 5.4 – Величина модуля упругости при повышенных температурах
(Е-10 -4 кгс/мм2)
Марка стали |
|
|
Температура, °С |
|
|
||
|
|
|
|
|
|
|
|
|
20 |
100 |
200 |
300 |
400 |
500 |
600 |
|
|
|
|
|
|
|
|
Ст.3 |
2,1 |
2,05 |
1,96 |
1,85 |
1,73 |
1,55 |
1,35 |
12Х18Н10Т |
2,02 |
1,98 |
1,93 |
1,85 |
1,77 |
1,69 |
1,6 |
ЭИ - 943 |
- |
- |
- |
- |
- |
- |
- |
|
|
|
42 |
|
|
|
|
В интервале температур 400-800°С величины радиусов изгиба для различных марок сталей отличаются между собой не более чем на 2%, поэтому величину радиуса изгиба с достаточной для практики точности можно определять по формуле (5.5), используя известные величины коэффициентов A , m и n для стали, например 12Х18Н10Т.
5.2 Выбор типа валковой листогибочной машины
Для выбора типа машины рассмотрим предъявляемые к ней технологические требования. На валковой листогибочной машине выполняются в основном три операции: подгибка кромок листа, круговая гибка, правка обечайки. При этом должны быть обеспечены:
А - минимальная ширина прямых участков после подгибки концов;
Б - минимальное количество проходов при круговой гибке; В - минимальный прогиб верхнего вала в целях получения
правильной геометрической формы обечайки по длине; Г - необходимая точность при правке.
Следует учитывать также не менее важный фактор - серийность производства. Большинство видов производств аппаратуры носят индивидуальный или мелкосерийный характер. Отсюда возникает потребность в универсальном характере листогибочной машины.
Известные типы машин делятся на три группы: двух, трех- и четырехвалковые (рис. 5.1).
Многообразие их конструктивного исполнения создает в практике значительные трудности при выборе оптимального типа машины. В связи с этим выбор типа машины должен базироваться на детальном технико-экономическом анализе условий производства с учетом всех операций, выполняемых на машине.
43
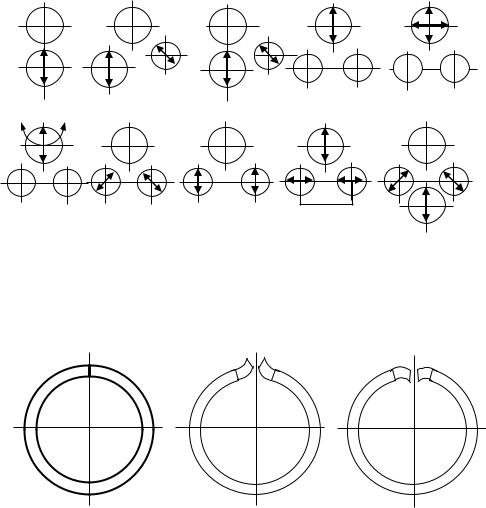
а) |
б) |
в) |
г) |
д) |
е) ж) з) и) к) Рисунок 5.1 – Типовые схемы расположения и перемещения валков в листогибочных машинах
В результате выполнения операции подгибки кромок форма их в околошовной зоне может быть различной (рис. 5.2).
а) |
б) |
в) |
Рисунок 5.2 – Форма кромок после операции подгибки:
а – нормальная; б – выпуклость; в – вогнутость
44
В связи с трудностью исправления при правке выпуклость прямых участков является совершенно нежелательной. Вогнутость и прямые участки исправляются при правке сравнительно легко. Однако и их размеры должны быть ограничены. Во всех случаях, чем меньше величина прямых участков, тем качественнее правка. В связи с широким развитием электрошлаковой сварки толстостенной аппаратуры прямые участки необходимы для движения ползуна, обеспечивающего формирование сварного шва. В связи с этим качество подгибки кромок или величина прямых участков должны быть согласованы с общей технологией изготовления обечаек.
Длина плоских участков, остающихся на кромках листов, зависит от межцентрового расстояния между боковыми валками. В связи с этим можно сделать вывод, что наибольшая длина прямых участков получается в машинах, у которых расстояние между боковыми валками не регулируется.
Поэтому наихудшим вариантом исполнения машины является вариант по рис. 5.1 г. Ниже приведены величины остаточных плоских участков на листах при гибке на машинах подобного типа.
Толщина листа, мм |
6 |
16 |
25 |
32 |
38 |
Длина прямых участков, мм |
76 |
100 |
141 |
178 |
217 |
Для уменьшения величины плоских участков обрабатываемых листов используют машины, у которых можно изменять расстояние между боковыми валками (рис. 5.1 ж) или верхними и нижними боковыми валками (рис. 5.1 д, е, з, и, к). На таких машинах при гибке толстых и тонких листов расстояние между центрами валков различно (при гибке тонких листов оно меньше, при гибке толстых - больше).
Технологические требования к универсальности машины находятся в противоречии с конструктивным ее исполнением. Для выполнения операции подгибки кромок требуется наименьшее расстояние между боковыми валками, но с уменьшением этого расстояния увеличивается усилие, т. е. сужается диапазон изгибаемых листов по толщине. Отсюда следует, что расстояние
45
между боковыми валками должно быть регулируемым. В этом случае при выполнении операции подгибки кромок расстояние между боковыми валками уменьшается. При круговом изгибе листа это расстояние устанавливается в соответствии с толщиной листа. С другой стороны, часто оказывается, что диаметр верхнего валка больше, чем диаметр обечайки. В этом случае целесообразно снабжать машины запасными верхними валками меньшего диаметра. В общем случае минимальный диаметр обечайки, который можно получить без предварительной подгибки кромок равен 1,3 диаметра верхнего валка.
В целях расширения производственных возможностей машин при их заказе необходимо оговаривать поставку сменных взаимозаменяемых верхних валков меньшего диаметра. Это позволит на одной машине изготовлять широкий диапазон обечаек.
С целью повышения качества изделий и стабильности их размеров целесообразно оснащать машину измерительными устройствами, контролирующими размеры обечайки в процессе гибки. Машины для изготовления обечаек больших диаметров из листов малой толщины должны быть оснащены поддерживающими устройствами, чтобы избежать потери устойчивости заготовки при гибке.
5.3 Подгибка кромок
Сущность подгибки кромок заключается в том, что перед изгибанием листа в цилиндр кромки листа, образующие продольный стык, подгибаются на заданный радиус кривизны. Необходимость и качество подгибки кромок зависят от типа валковой листогибочной машины и требований сварочной технологии.
Эту операцию выполняют в том случае, когда процесс гибки обечаек не обеспечивает заданный профиль по всей длине окружности и обечайка имеет прямые кромки в месте их стыковки, т. е. угловатость (рис.5.3.).
46
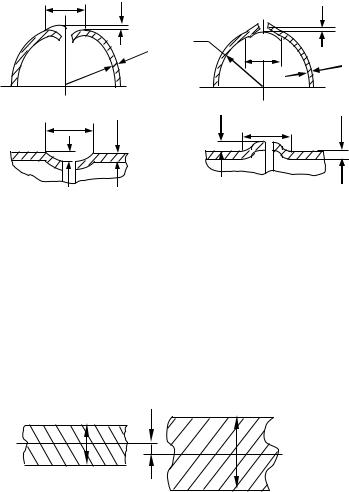
l
f
R
S
R
а)
l
S |
f |
f
|
f |
l |
S |
|
б)
l
S
в) |
г) |
Рисунок 5.3. – Угловатость в месте стыка кромок обечаек:
а, б – продольные; в, г – кольцевые стыки
Увод (угловатость) кромок в сварных швах не должен превышать f= 0,1S + 3 мм.
Смещение кромок b листов (рис. 5.4), измеряемое по срединной поверхности, в стыковых соединениях, определяющих прочность сосуда, не должно превышать b = 0,1S, но не более 3 мм.
b
S1
S
Рисунок 5.4 – Смещение кромок листов
Смещение кромок в кольцевых швах, за исключением швов, выполняемых электрошлаковой сваркой, не должно превышать величин, приведенных в табл. 5.5. Смещение кромок в кольцевых швах, выполняемых электрошлаковой сваркой, не должно превышать 5 мм.
47
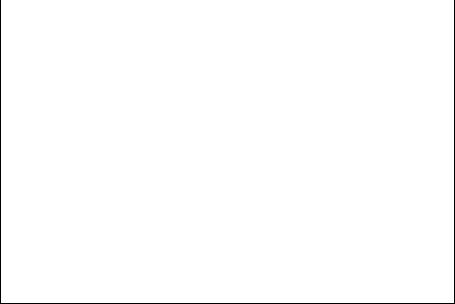
Таблица 5.5 – Максимально допустимые смещения стыкуемых кромок в кольцевых швах
|
Максимально допустимые смещения |
|
Толщина |
стыкуемых кромок в кольцевых швах, мм |
|
свариваемых |
|
|
на монометалличе- |
на биметаллических |
|
листов s, мм |
ских сосудах |
сосудах со стороны |
|
|
коррозионного слоя |
до 20 |
0,1S+1 |
50 % толщины плакиру- |
свыше 20 до 50 |
0,15S, |
ющего слоя |
|
но не более 5 |
|
свыше 50 до |
|
0,04S + 3, но не более |
100 |
0,04S + 3,5* |
толщины плакирующего |
|
|
слоя |
свыше 100 |
0,025S + 5*, |
0,025S + 5, но не более 8 и |
|
но не более 10 |
не более толщины |
|
|
плакирующего слоя |
* При условии наплавки на стыкуемые поверхности с уклоном 1:3 для сварных соединений, имеющих смещение кромок более 5 мм
Смещение кромок в стыковых сварных соединениях труб не должно превышать величин, приведенных в табл. 5.6.
Таблица 5.6 – Смещение кромок в стыковых сварных соединениях труб
Толщина стенки трубы S, мм |
Максимально допустимые |
|
|
|
смещения кромок, мм |
|
|
|
до 3 |
|
0,2S |
свыше 3 |
до 6 |
0,1S + 0,3 |
|
|
|
свыше 6 до 10 |
0,15S |
|
|
|
|
свыше 10 |
до 20 |
0,05S + 1 |
|
|
|
свыше |
20 |
0,1S, но не более 3 |
|
|
|
Чтобы исключить угловатость, кромки листа подгибают на заданный радиус кривизны. Необходимость подгибки зависит от
48