
Лекция 2. Материалы, применяемые для изготовления аппаратуры
.pdfЛекция 2 МАТЕРИАЛЫ
2.1 Материалы, применяемые для изготовления аппаратуры
Общие требования к материалам.
Требования к основным материалам, их пределы применения, назначение, условия применения, виды испытаний должны удовлетворять эксплутационным требованиям.
Качество и характеристики материалов должны подтверждаться соответствующими сертификатами.
При выборе материалов для изготовления сосудов (сборочных единиц, деталей) следует учитывать: расчетное давление, температуру стенки (минимальную и максимальную), химический состав и характер среды, технологические свойства и коррозионную стойкость материалов.
Для сосудов, устанавливаемых на открытой площадке или в неотапливаемом помещении, при выборе материалов также следует учитывать:
-абсолютную минимальную температуру наружного воздуха данного района, если температура стенки сосуда, находящегося под давлением, может стать отрицательной от воздействия окружающего воздуха;
-среднюю температуру воздуха наиболее холодной пятидневки данного района, если температура стенки сосуда, находящегося под давлением, положительная.
Элементы, привариваемые непосредственно к корпусу сосуда изнутри или снаружи (лапы, цилиндрические опоры, подкладки под фирменные таблички, опорные кольца под тарелки и др.), следует изготавливать из материалов того же класса, что и корпус.
Неметаллические материалы, применяемые для изготовления сосудов, должны быть совместимы с рабочей средой в части коррозионной стойкости и нерастворимости (изменении свойств)
14
в рабочем диапазоне температур. Среда, для которой предназначен сосуд, должна быть указана в паспорте на сосуд. Прибавка к расчетной толщине для компенсации коррозии (эрозии) назначается; с учетом условий эксплуатации, расчетного срока службы, скорости коррозии (эрозии).
Прибавку С для компенсации коррозии к толщине внутренних элементов следует принимать:
-2С - для несъемных нагруженных элементов, а также для внутренних крышек и трубных решеток теплообменников;
-0,5С, но не менее 2 мм - для съемных нагруженных эле-
ментов;
-С - для несъемных ненагруженных элементов.
Для внутренних съемных ненагруженных элементов прибавка для компенсации коррозии может не учитываться.
Если невозможно или нецелесообразно увеличивать толщину стенки за счет прибавки для компенсации коррозии, выполняется коррозионная защита: плакирование, футеровка или наплавка.
Основные характеристики материалов.
Коррозионная стойкость: В зависимости от скорости коррозии различные стали и сплавы по отношению к определенной среде классифицируются согласно (ГОСТ 13819-68) как:
-совершенно стойкие;
-весьма стойкие;
-стойкие;
-пониженно-стойкие;
-малостойкие;
-нестойкие.
Детали аппаратов должны обладать необходимой стойкостью против коррозии, обеспечивающей срок их службы не менее чем в течение 5-8 лет.
Прочность. Стали и другие металлы и сплавы для аппаратуры должны иметь предел прочности и предел текучести, обеспечивающие надежную работу аппаратов под внутренним
15
давлением, ветровой и другими нагрузками, когда явление ползучести практически можно не принимать во внимание.
Ударная вязкость. Значения ударной вязкости характеризуют вязкостные свойства металла и особенно важны для оценки возможности хрупкого разрушения элементов оборудования при низких температурах и ударных нагрузках. Наряду с этим показатели ударной вязкости позволяют косвенно судить и о качестве металла, степени его загрязненности неметаллическими включениями, сплошности, соблюдении режима термической обработки.
Пример: ферросилид
Теплоустойчивость (длительная прочность, ползучесть). Потеря работоспособности и даже разрушение оборудования, эксплуатируемого под внутренним давлением при высоких температурах, возможны в результате постепенного, более или менее равномерного по длине аппарата увеличения диаметра с одновременным уменьшением толщины стенки. Причиной этого является свойство металлов медленно и непрерывно пластически деформироваться при высоких температурах под воздействием постоянной нагрузки (ползучесть). Способность металла противостоять развитию ползучести, называемая теплоустойчивостью, оценивается по результатам длительных испытаний.
Тепловая хрупкость и разупрочнение. В результате дли-
тельного пребывания при повышенных температурах некоторые стали теряют свои исходные значения вязкости, пластичности и прочности, что связано, прежде всего, с изменениями кристаллической решетки и микроструктуры стали. Указанное явление потери вязкости и пластичности получило название «тепловой хрупкости». Подобные изменения свойств сталей крайне нежелательны и опасны, так как могут, привести к разрушению оборудования во время эксплуатации и при ремонтах. Поэтому к материалам обязательно, предъявляется требование достаточной стабильности механических свойств и структуры в процессе длительного воздействия рабочих температур.
16
Пластичность. Кроме прочности, металл должен обладать достаточно высокой пластичностью, оцениваемой показателями относительного удлинения и поперечного сужения. Это требование обусловливается тем, что стальной прокат при изготовлении из него сборочных элементов и деталей аппаратуры, а также при сборке и монтаже аппаратуры и трубопроводов подвергается пластической деформации (штамповка днищ, гибка листа, развальцовка труб и т.д.), выдержать которую без разрушения хрупкий металл не способен.
Свариваемость. Подавляющее большинство аппаратов изготовляют и монтируют с помощью сварки, поэтому металл должен обеспечивать возможность создания надежных сварных соединений, у которых механические и физико-химические свойства одинаковы со свойствами основного металла или весьма близки к ним.
Взависимости от материала детали работают при температурах от - 253 до +700 °С.
Вкачестве заготовок используются листовой и сортовой прокат, трубы, поковки, штамповки и отливки.
2.2 Технологическая характеристика производства
Заводы химического аппаратостроения отличаются инди- ви-дуальным и мелкосерийным характером производства. Серийность некоторых видов аппаратов (кроме теплообменных) составляет 7-10 шт. в год. Только около 50% наименований изделий являются повторяющимися, т.е. изготовляются в течение двух или более лет по одним и тем же чертежам, остальные 50% заказываются каждый раз по совершенно новым моделям и техническим условиям. Это определяет использование преимущественно универсального металлорежущего и кузнечно-прессового оборудования, невысокую технологическую оснащенность специальным оборудованием и приспособлениями, отсутствие операционных расчетно-режимных карт, затрудняет создание временных специализированных производств.
17
С точки зрения технологической структуры производства в зависимости от его характера и состава трудоемкость работ по изготовлению химаппаратуры составляет, примерно (%):
- механическая обработка |
28-56; |
- кузнечно-прессовые работы |
1-5; |
- литейные |
0-8; |
- сборочно-сварочные |
13-44; |
- слесарно-сборочные |
14-55. |
Анализ дает следующее примерное распределение загото- |
|
вок по способам их получения (%): |
|
- литые детали |
4; |
- кованые |
2; |
- холодноштампованные |
3; |
- из проката и труб |
85; |
- из пластмасс |
1,0; |
- после механической обработки |
5. |
Нормализованные детали составляют 30% общего количества наименований обрабатываемых деталей.
2.3 Предпосылки организации поточного производства
Несмотря на индивидуальный и мелкосерийный характер производства аппаратов, анализ их конструкций показывает, что они в основном состоят из однотипных деталей и сборочных единиц: обечаек, днищ, люков, штуцеров, опор и т.д., а это создает возможности для организации изготовления деталей и сборочных единиц и в отдельных случаях аппаратов в целом по принципу поточного производства.
Пример: чертеж теплообменника
Технологический процесс, изготовления деталей и сборки сборочных единиц и изделий характеризуется различными видами обработки: сваркой, механической обработкой, слесарными работами, термической обработкой и т.д.
Основной вид соединения деталей в аппаратостроении -
18
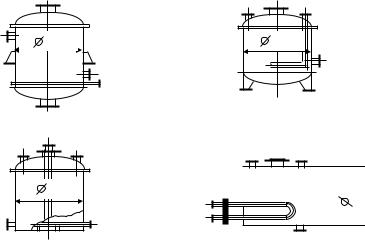
сварка. Однако в результате сварочных операций возникают различного рода деформации, не позволяющие вести сборку аппаратов по принципу взаимозаменяемости. Это увеличивает трудоемкость сборочных операций и нарушает ритм работы линии. Поэтому, при разработке технологического процесса необходимо заранее учитывать расчетным или статическим методом сварочные деформации.
Одним из основных условий организации поточных линий производства аппаратуры являются типизация технологических процессов, технологической оснастки и создание нестандарт-ного оборудования на основе конструктивной преемственности, возможной лишь при высоком уровне состояния унификации конструкций химической аппаратуры (рис. 2.1).
1200 |
а)
1200 |
в)
1200 |
б)
1200
г)
Рисунок 2.1 – Унифицированные конструкции химической аппаратуры:
а – сборник; б – автоклав; в – мерник; г – цистерна
Важным этапом типизаций технологических процессов должна явиться их классификация, основанная на признаках кон-
19
структивно-технологической общности и учитывающая конфигурацию деталей, габаритные размеры, материалы, степень сложности и класс точности обработки, объем производственного задания.
При внедрении поточных методов в индивидуальное и мелкосерийное производство необходимо руководствоваться следующими основными требованиями:
1.Максимально применять в конструкции аппаратов и машин нормализованные и унифицированные детали и сборочные единицы.
2.Расчленять аппарат на ряд законченных независимых сборочных единиц.
3.Обеспечить взаимозаменяемость сборочных единиц и деталей, изготовляемых поточным методом.
4.При проектировании ненормализованных сборочных единиц максимально использовать нормализованные детали и сборочные единицы, применяя при этом различные виды соединений, в том числе и неразъемные.
5.Уделять особое внимание технологичности конструкции. Удовлетворительной можно считать только такую конструкцию, которая, будучи эффективной и надежной в эксплуатации, является наименее металлоемкой и трудоемкой в изготовлении.
20