
Лекция 9. Сварка корпусов
.pdfЛекция 9 СВАРКА КОРПУСОВ
9.1 Сборка под сварку
Подготовка кромок
Способы подготовки кромок свариваемых деталей должны обеспечивать отсутствие на кромках механических повреждений и зон термического влияния, снижающих регламентированные свойства сварных соединений. Форма подготовки кромок должна соответствовать стандартам и требованиям чертежа.
Кромки подготовленных под сварку элементов аппаратов зачищаются до металлического блеска на ширину не менее 20 мм, а для электрошлаковой сварки - не менее 50 мм без следов ржавчины, масла и прочих загрязнений. Кромки листов из углеродистой стали очищают химическим способом. Непосредственно перед сваркой ржавые кромки смазывают 15%-ным водным раствором соляной кислоты. Раствор практически безопасен для работающих (при попадании на руки не вызывает ожогов). Если толщина слоя ржавчины не более 1 мм, раствор наносят один раз, если больше - 2-3 раза. Для интенсификации процесса перед повторным нанесением раствора желательно смоченную кромку протереть жесткой волосяной щеткой. Изделие с очищенными кромками сушат на воздухе, не промывая водой. Положительные стороны этого метода: раствор реагирует только с ржавчиной и окалиной; не выделяются вредные вещества, что позволяет очищать кромки непосредственно на рабочем месте; конечный продукт реакции (хлорное железо) не влияет на качество сварного соединения.
Для удаления с поверхности черных металлов окалины и ржавчины толщиной до 3 мм используется паста «Целлочель». В состав пасты входят: соляная кислота, уротропин, жидкое стекло, бумажная масса или мелкие древесные опилки и вода. Соляная кислота, легко растворяя ржавчину, не действует на основной металл благодаря присутствию ингибитора – уротропина. Жидкое
72
стекло и наполнитель служат сгустителями пасты и улучшают ее технологические свойства. Пасту приготовляют, смешивая компоненты в кислостойкой посуде при комнатной температуре. Паста годна к использованию через сутки после приготовления.
На очищаемые поверхности деталей пасту наносят кистью или шпателем, а при больших размерах поверхностей - растворонасосом. Толщина слоя пасты 2-5 мм, время выдержки пасты на детали 15-60 мин. В этом случае гарантируется снятие слоя ржавчины, толщиной до 1 мм. Если слой ржавчины большей толщины, увеличивают время выдержки пасты на детали или наносят пасту повторно. После удаления пасты поверхность обильно промывают водой или насухо протирают ветошью, а затем 10%-ным раствором соли или 10%-ным раствором ортофосфорной кислоты. На очищенной поверхности металла образуется пленка, защищающая металл от окисления на 1-2 суток. Кроме того, пленка улучшает адгезию лакокрасочных покрытий с поверхностью и удлиняет срок их службы.
Для защиты поверхности изделий от брызг металла используют жидкий концентрат сульфитно-спиртовой барды (КБЖ ГОСТ 8518 - 57). Концентрат разбавляют в горячей воде (60 - 900 С; отношение 1 : 4 по массе или 1 : 5 по объему) до однородного раствора и наносят на изделие (кистью, пульверизатором или окунанием) за 1 ч до сварки. Защитные свойства раствора не исчезают со временем, его можно наносить за 20 дней до сварки. При использовании раствора КБЖ брызги не прилипают к металлу и легко удаляются щеткой.
Сборка
Методы сборки элементов под сварку должны обеспечивать правильное взаимное расположение сопрягаемых элементов и свободный доступ к выполнению сварочных работ в последовательности, предусмотренной технологическим процессом. При сборке допускается применение методов подгонки, которые должны исключать появление дополнительных напряжений в металле или повреждений поверхности металла.
73
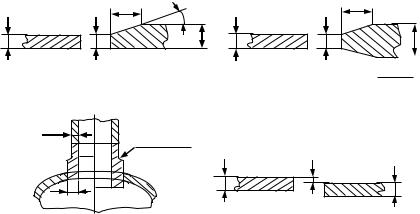
Подготовленные к сборке под сварку кромки элементов аппаратов и прилегающие к ним поверхности основного металла, а также величина зазора между кромками должны быть в соответствии с требованиями чертежей и действующих стандартов на сварку. Сварщик приступает к сварке только после установления контролером ОТК правильности сборки и тщательности зачистки всех поверхностей металла, подлежащих сварке.
При приварке к корпусу или днищу аппарата опор и внут- рен-них устройств расстояние между краем шва приварки детали и краем ближайшего шва должно быть не менее толщины стенки корпуса или днища, но не менее 20 мм. Продольные швы смещенных обечаек и днищ должны быть смещены один относительно другого на величину трехкратной толщины наиболее толстого элемента, но не менее, чем на 100 мм между осями швов.
В сварных стыках элементов разной толщины предусматривается плавный переход от одного элемента к другому путем постепенного утонения более толстого элемента в соответствии, а в случаях, не предусмотренных стандартами, угол скоса разностенных элементов должен быть не более 15° (уклон 1 : 4) (рисунок 9.1 а, б). Сварка патрубков разной толщины может выполняться как показано на рисунке 9.1 в,г.
h
|
l |
h1 |
150 |
|
|
|
l |
|
|
|
|
|
|
|
|
|
|
|
h |
|
1 |
|
|
|
|
1 |
|
|
h |
h |
h |
|
|
h |
|
|
|
|
|
|
|
|
4 |
h h |
|
l 4( h1 |
h ) |
|
|
l |
1 |
||
|
|
|
|
|||||
|
|
|
|
2 |
||||
|
|
|
|
|
|
|
|
|
|
|
а) |
|
|
|
|
б) |
|
h1 |
|
r = h2 - h1 |
|
|
|
|
|
|
|
|
|
|
|
|
|
h |
b |
h |
h21 |
|
|
в) г) Рисунок 9.1 – Допустимое смещение кромок
74
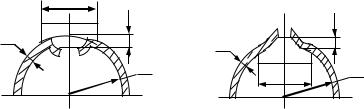
Допускается применение стыковых швов без предварительного утонения более толстой стенки, если разность в толщинах соединяемых элементов не превышает 30% толщины более тонкого элемента.
Совместный увод f кромок (рис. 9.2) в продольных и кольцевых швах (угловатость) не должен превышать 10% толщины h листа плюс 3 мм и не должен быть более 5 мм. Угловатость продольных швов определяется по шаблону, длина которого по хорде равна 1/3 радиуса обечайки.
L=1/3R |
|
f |
f |
h |
h |
|
R |
L=1/3R |
R |
|
||
|
|
Рисунок 9.2 – Допустимая угловатость кромок
При сборке под электрошлаковую сварку продольных стыков (обечаек, трубных решеток, плоских заготовок днищ и т.д.) кромки продольных стыков обечаек диаметром менее 2000 мм должны иметь, после круговой гибки, прямые участки шириной не менее 200 мм. Совместный увод кромок не должен превышать 1,5мм на длине 400 мм. Отклонения от перпендикулярности реза кромок свариваемого стыка не должны превышать по углу 6-8°, а по линейной величине 4 мм.
Вверхней части продольного стыка при длине его более 2
мзазор увеличивается на 2-3 мм от первоначального на каждый метр длины стыка.
При сборке днища и корпуса под электрошлаковую сварку, если толщина стенки днища превышает толщину корпуса, кромка днища утоняется механическим способом до величины, равной толщине стенки корпуса на ширине 70-80 мм.
75
Требования к сварке
При изготовлении, монтаже, ремонте сосудов должна применяться технология сварки, аттестованная в соответствии с требованиями Правил (ПБ 03-576-03).
Для выполнения сварки должны применяться исправные установки, аппаратура и приспособления, обеспечивающие соблюдение требований НД.
К производству сварочных работ допускаются сварщики, аттестованные в соответствии с Правилами аттестации сварщиков и специалистов сварочного производства (ПБ 03-273-99), утвержденными постановлением Госгортехнадзора России.
Сварные соединения элементов, работающих под давлением, с толщиной стенки более 6 мм подлежат маркировке (клеймению), позволяющей установить фамилию сварщика, выполнившего сварку.
Сварочные материалы, применяемые для сварки сосудов, должны соответствовать требованиям стандартов и технических условий, что должно подтверждаться документом организацииизготовителя.
Подготовка кромок и поверхностей под сварку должна выполняться механической обработкой либо путем термической резки или строжки (кислородной, воздушно-дуговой, плазменнодуговой) с последующей механической обработкой.
Кромки деталей, подлежащих сварке, и прилегающие к ним участки должны быть очищены от окалины, краски, масла и других загрязнений.
Требования к контролю сварных соединений
Организация-изготовитель, монтажная или ремонтная организация обязаны применять такие виды и объемы контроля своей продукции, которые гарантировали бы выявление недопустимых дефектов, ее высокое качество и надежность в эксплуатации.
Контроль качества сварки и сварных соединений включает: - проверку аттестации персонала;
76
-проверку сборочно-сварочного, термического и контрольного оборудования, аппаратуры, приборов и инструментов;
-контроль качества основных материалов;
-контроль качества сварочных материалов и материалов для дефектоскопии;
-операционный контроль технологии сварки;
-неразрушающий контроль качества сварных соединений;
-разрушающий контроль качества сварных соединений;
-контроль исправления дефектов.
Виды контроля определяются конструкторской организацией и указываются в конструкторской документации сосудов.
Перед визуальным осмотром поверхность сварного шва и прилегающие к нему участки основного металла шириной не менее 20 мм в обе стороны от шва должны быть зачищены от шлака и других загрязнений, при электрошлаковой сварке это расстояние должно быть не менее 100 мм.
Осмотр и измерение сварных соединений должны производиться с наружной и внутренней сторон по всей протяженности швов. В случае невозможности осмотра и измерения сварного соединения с двух сторон его контроль должен производиться в порядке, предусмотренном автором проекта.
Объем контроля ультразвуковой дефектоскопией или радиографическим методом стыковых, угловых, тавровых и других сварных соединений сосудов и их элементов (днищ, обечаек, штуцеров, люков, фланцев и др.), включая соединения люков и штуцеров с корпусом сосуда, должен соответствовать указанному в таблице 9.1.
Механическим испытаниям должны подвергаться контрольные стыковые сварные соединения в целях проверки соответствия их механических свойств требованиям Правил и технических условий на изготовление сосуда.
Обязательные виды механических испытаний:
- на статическое растяжение - для сосудов всех групп;
77
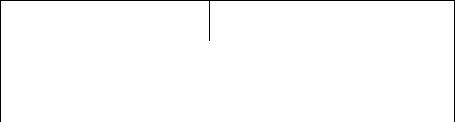
Таблица 9.1 – Объем контроля сварных соединений сосудов и их элементов
Группа сосудов (см.табл. 1.1.) Длина контролируемого участка швов от длины каждого шва, %
1 |
100 |
|
|
2 |
100 |
|
|
3 |
не менее 50 |
4 |
не менее 25 |
|
|
-на статический изгиб или сплющивание - для сосудов всех групп;
-на ударный изгиб - для сосудов, предназначенных для работы при давлении - более 5 МПа (50 кгс/см2) или температуре выше 450°С, и сосудов, изготовленных из сталей, склонных к подкалке при сварке;
-на ударный изгиб - для сосудов 1, 2, 3-й групп, предназначенных для работы при температуре ниже - 20°С.
Испытания на ударный изгиб сварных соединений производятся для сосудов и их элементов с толщиной стенки 12 мм и более при температуре 20°С.
Из каждого контрольного стыкового сварного соединения должны быть вырезаны два образца для испытания.
В сварных соединениях сосудов и их элементов не допускаются следующие дефекты:
-трещины всех видов и направлений, расположенные в металле по линии сплавления и в околошовной зоне основного металла;
-непровары (несплавления) в сварных швах, расположенные в корне шва, или по сечению сварного соединения (между основным металлом и металлом шва);
-поры, шлаковые и другие включения;
-наплывы (натеки);
-незаваренные кратеры и прожоги;
-свищи;
78
- смешение кромок свыше норм.
Качество сварных соединений считается неудовлетворительным, если в них при любом виде контроля будут обнаружены внутренние или наружные дефекты, выходящие за пределы норм.
Дефекты, обнаруженные в процессе изготовления, должны быть устранены с последующим контролем исправленных участков. Методы и качество исправления дефектов должны обеспечивать необходимую надежность и безопасность работы сосуда.
Применение нахлесточных сварных швов допускается для приварки к корпусу укрепляющих колец, опорных элементов, подкладных листов, пластин под площадки, лестницы, кронштейны и т.п.
Сварные швы должны быть доступны для контроля при изготовлении, монтаже и эксплуатации сосудов.
В горизонтальных сосудах допускается местное перекрытие седловыми опорами кольцевых (поперечных) сварных швов на общей длине не более 0,35 D , а при наличии подкладного листа - не более 0,5 D где D - наружный диаметр сосуда. При этом перекрываемые участки сварных швов по всей длине должны быть проверены методом радиографии или ультразвуковой дефектоскопии. Перекрытие мест пересечения швов не допускается.
Требования к контролю сварных соединений
Контроль качества сварных соединений следует проводить следующими методами:
а) визуальным осмотром и измерением; б) механическими испытаниями;
в) испытанием на стойкость против межкристаллитной коррозии;
г) металлографическими исследованиями; д) ультразвуковой дефектоскопией; е) радиографией;
ж) цветной или магнитопорошковой дефектоскопией; з) другими методами по требованию проекта.
79

Окончательный контроль качества сварных соединений сосудов, подвергающихся термической обработке, проводится после термической обработки.
9.2 Гидравлическое (пневматическое) испытание
Гидравлическому испытанию подлежат все сосуды после изготовления. Сосуды, изготовление которых заканчивается на месте установки, транспортируемые на место монтажа частями, подвергаются гидравлическому испытанию на месте монтажа.
Сосуды, имеющие защитное покрытие или изоляцию, подвергаются гидравлическому испытанию до наложения покрытия или изоляции.
Сосуды, имеющие наружный кожух, подвергаются гидравлическому испытанию до установки кожуха.
Допускается эмалированные сосуды подвергать гидравлическому испытанию рабочим давлением после эмалирования.
Гидравлическое испытание сосудов, за исключением литых, должно проводиться пробным давлением, определяемым по
формуле: |
|
|
|
|
|
|
1,25Р |
|
|||
Рпр |
20 |
(9.1) |
|||
|
|||||
|
|
|
|
||
|
|
|
р |
|
|
где Р – расчетное давление сосуда, МПа (кгс/см2); |
|||||
|
20 , |
р |
– допускаемые напряжения для материала |
сосуда или его элементов соответственно при 20°С и расчетной температуре, МПа (кгс/см2).
Отношение 20 / р принимается по тому из исполь-
зованных материалов элементов (обечаек, днищ, фланцев, крепежа, патрубков и др.) сосуда, для которого оно является наименьшим.
Гидравлическое испытание вертикально устанавливаемых сосудов допускается проводить в горизонтальном положении при
80
условии обеспечения прочности корпуса сосуда, для чего расчет на прочность должен быть выполнен разработчиком проекта сосуда с учетом принятого способа опирания в процессе гидравлического испытания.
При этом пробное давление следует принимать с учетом гидростатического давления, действующего на сосуд в процессе его эксплуатации.
В комбинированных сосудах с двумя и более рабочими полостями, рассчитанными на разные давления, гидравлическому испытанию должна подвергаться каждая полость пробным давлением, определяемым в зависимости от расчетного давления полости.
При заполнении сосуда водой воздух должен быть удален полностью. Для гидравлического испытания сосудов должна применяться вода температурой не ниже 5°С и не выше 40°С, если в технических условиях не указано конкретное значение температуры, допускаемой по условию предотвращения хрупко-го разрушения.
Разность температур стенки сосуда и окружающего воздуха, во время испытаний не должна вызывать конденсации влаги на поверхности стенок сосуда.
По согласованию с разработчиком проекта сосуда вместо воды может быть использована другая жидкость.
Давление в испытываемом сосуде следует повышать плавно. Скорость подъема давления должна быть указана в технической документации. Использование сжатого воздуха или другого газа для подъема давления не допускается. Давление при испытании должно контролироваться двумя манометрами. Оба манометра выбираются одного типа, предела измерения, одинаковых клас-сов точности, цены деления.
Время выдержки сосуда под пробным давлением устанавливается разработчиком проекта. При отсутствии указаний в проекте время выдержки должно быть не менее значений, указанных в табл. 9.2.
81