
ОХТ в вопросах и ответах Ч2
.pdf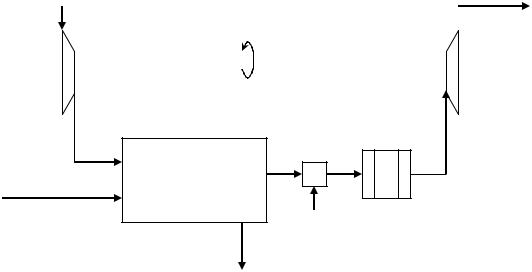
Вопрос. Какие технические и технологические приёмы реализованы или могут быть предложены в производстве азотной кислоты для решения концепции эффективного использования оборудования?
Ответ. Эффективное использование оборудования в производстве HNO3
может быть реализовано путём совмещения процессов.
Вопрос. Какие технические и технологические приемы реализованы при создании энерготехнологической системы в производстве азотной кисло-
ты?
Ответ. Энергетический потенциал отходящих газов из абсорбера недоста-
точен для того, чтобы компенсировать затраты энергии на сжатие воздуха,
поступающего на окисление аммиака, так как часть энергии сжатого воз-
духа была затрачена на получение азотной кислоты.
Воздух |
|
|
Отходящие |
||||
|
|
|
|
|
|
газы |
|
|
|
|
К |
ГТ |
|
|
|
|
|
|
|
||||
|
|
|
|
|
|
|
|
Р
Г
ХТП
Аммиак
СН4
Азотная кислота
Рис. 4.6. Энерготехнологическая схема производства азотной кислоты:
К – компрессор, Г – газовая горелка (энергетический узел), Р – реактор каталитической очистки, ГТ – газовая турбина
Этот недостаток энергии компенсируют увеличением температуры отходящих газов путём сжигания природного газа. Энергия сжатого газа увеличивается за счёт увеличения его температуры. Высокая температура
51
отходящих газов используется для каталитической очистки от оксидов азота путём их восстановления с помощью небольшого избытка метана в реакторе очистки. Сжатый газ с повышенной энергией подаётся в газовую турбину, которая находится на одном валу с компрессором для сжатия воздуха перед его смешением с аммиаком (рис. 4.6).
Вопрос. В чём заключается очистка отходящих газов в производстве азотной кислоты?
Ответ. Отходящие газы производства азотной кислоты содержат после абсорбционных колонн от 0,05 до 0,2 об. % оксидов азота, которые по са-
нитарным требованиям без дополнительной очистки запрещено выбрасы-
вать в атмосферу.
Очистка отходящих газов производится каталитическим восстанов-
лением оксидов азота природным газом или аммиаком.
Реактор каталитической очистки при использовании природного га-
за в качестве восстановителя устанавливают в системе после энергетиче-
ского узла (рис. 4.6), так как высокая температура (973–1023 К) позволяет провести процесс восстановления оксидов азота на палладиевом катализа-
торе:
CH4 + 2NO2 = N2 + 2H2O + CO2
CH4 + 4NO = 2N2 + 2H2O + CO2
Вопрос. Какие существуют решения по усовершенствованию производ-
ства азотной кислоты?
Ответ. На экономические показатели большое влияние оказывает давле-
ние, так как при увеличении давления уменьшается объём оборудования
(особенно отделения абсорбции диоксида азота), снижаются капитальные затраты, возрастает интенсивность процесса. Кроме того, в системах,
функционирующих под давлением, увеличивается выход пара (как вто-
52

ричного энергетического ресурса), что существенно отражается на расход-
ном коэффициенте по энергии и себестоимости азотной кислоты.
Однако при использовании повышенного давления снижается сте-
пень окисления аммиака, и возрастают потери платиноидного катализато-
ра. В целом, для систем под давлением по отношению к системам, работа-
ющим при атмосферном давлении себестоимость азотной кислоты на 20%
выше.
Технология производства азотной кислоты с применением высоко-
температурных газовых турбин и природного газа уже становится не акту-
альной как вследствие роста стоимости природного газа, так и преждевре-
менного износа газотурбинных агрегатов и снижения их надёжности.
Усовершенствование показателей производства азотной кислоты и решение экологических проблем, связанных с выбросами оксидов азота,
возможно путём замены высокотемпературной очистки с использованием природного газа на низкотемпературную селективную очистку аммиаком.
Поскольку при этом отпадает потребность в природном газе, весь сжатый увеличение диаметра как контактного аппарата для окисления ам-
миака, так и абсорбционной колонны.
Для существенного снижения потерь драгметаллов, уносимых нит-
розными газами из контактного аппарата, слой платиноидного катализато-
ра содержит сетки из палладиевого сплава, который является эффектив-
ным сорбентом для платины.
5. ХТС производства стирола
Вопрос. Какова химическая модель ХТС производства стирола?
Ответ. Химическая модель ХТС производства стирола может быть пред-
ставлена уравнением:
С6Н5-С2Н5 С6Н5-С2Н3 + Н2 – Q |
(1) |
53
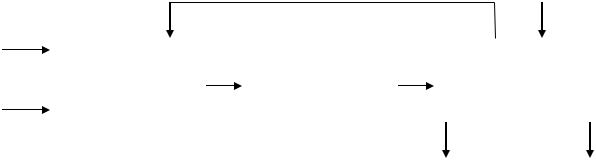
Вопрос. Какова операционная модель производства стирола?
Ответ. Производство стирола включает следующие основные стадии пе-
реработки этилбензола:
- подготовка смеси этилбензола с водяным паром. Исходный этилбен-
зол смешивается с водяным паром и этилбензолом, выделенным после ректификации продукционной реакционной смеси, и испаряется в тепло-
обменнике. Смесь, состоящая из газообразного этилбензола и водяного пара, нагревается до 873–913 К и поступает в реактор.
-дегидрирование этилбензола по реакции (1);
-охлаждение и конденсация реакционной смеси. После охлаждения
иконденсации воды и углеводородов из контактного газа в воздушном холодильнике смесь поступает в сепаратор, где отделяются газообразные продукты реакции и углеводороды отделяются от воды;
-ректификация углеводородов с получением продукта – стирола.
Вопрос. Что представляет собой функциональная схема производства стирола?
Ответ. Функциональная схема производства стирола включает подсисте-
мы подготовки сырья, дегидрирования этилбензола, выделения продукта
(рис. 5.1).
|
|
|
Этилбензол, |
|
|
|
|
|
|
водяной пар |
|
|
Вода |
Этилбензол |
|
|
|
|
|
|
(ЭБ) |
|
|
|
|
|
|
Подготовка сырья |
|
Химическое пре- |
|
|
Выделение продукта |
|
|
|
|
|
|||
|
(смешение исх. ре- |
|
вращение (дегид- |
|
|
(охлаждение, разде- |
|
агентов, подогрев) |
|
рирование ЭБ) |
|
|
ление, ректифика- |
|
|
|
|
|
|
ция) |
|
|
|
|
|
|
|
Водяной |
|
|
Стирол |
Жидкие и га- |
||
пар |
|
|
|
|
|
зообразные |
|
|
|
|
|
|
продукты |
Рис. 5.1. Функциональная схема производства стирола
54
Вопрос. Каковы физико-химические основы процесса дегидрирования этилбензола?
Ответ. Реакция (1) – обратимая, эндотермическая. Согласно принципу Ле Шателье повышение температуры приводит к увеличению равновесной степени превращения этилбензола в стирол. Реакция протекает с увеличе-
нием объёма, поэтому для увеличения глубины превращения сырьё раз-
бавляют водяным паром, являющимся инертным для данной реакции, что эквивалентно снижению давления реагирующей смеси. В промышленно-
сти используют разбавление пар : газ = (15–20) и реакцию проводят при температуре 830–900 К.
Вопрос. Какие кинетические особенности имеет реакция дегидрирования этилбензола?
Ответ. Реакция дегидрирования этилбензола– сложная, каталитическая. В
ходе реакции протекают также побочные превращения этилбензола в бен-
зол, толуол, углерод:
С6Н5-С2Н5 |
= С6Н5-С2Н3 + Н2 |
(1) |
|
С6Н5-С2Н5 |
= С6Н6 + С2Н4 |
(2) |
|
С6Н5-С2Н5 |
+ Н2 |
= С6Н5-СН3 + СН4 |
(3) |
С6Н5-С2Н5 |
+ Н2 |
= С6Н6 + С2Н6 |
(4) |
С6Н5-С2Н5 |
= 7С + СН4 + 3Н2 |
(5) |
Вследствие протекания реакции (5) на поверхности катализатора происходит образование кокса, что приводит к потере активности катали-
затора. Водяной пар, подаваемый на разбавление, не только сдвигает рав-
новесие в сторону образования продукта, но и газифицирует углистые от-
ложения:
С + Н2О = СО + Н2,
что обеспечивает непрерывную регенерацию катализатора.
55
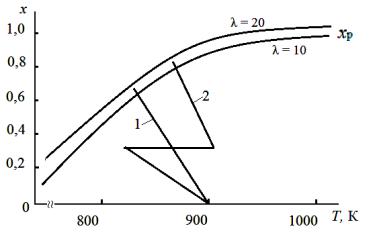
С повышением температуры скорость реакции (1) возрастает как за счёт увеличения константы скорости процесса, так и благодаря уве-
личению равновесной степени превращения этилбензола [3, с. 27]:
r = (k1 + k–1)c0(xp –x)
где k1 и k-1 – константы скорости прямой и обратной реакции соответ-
ственно, x – степень превращения, xр – равновесная степень превраще-
ния, c0 – начальная концентрация этилбензола
При температуре выше 900 К происходит разложение этилбензола и стирола с образованием бензола и толуола по реакции (2).
Вопрос. Как проводят реакцию дегидрирования этилбензола в промыш-
ленных условиях?
Ответ. Дегидрирование этилбензола проводят в адиабатическом режиме в неподвижном слое катализатора. Так как реакция эндотермическая, то для поддержания высокой скорости дегидрирования требуется осуществлять подогрев реакционной смеси в ходе процесса. Целесообразно секциониро-
вать реакционную зону на ряд слоёв катализатора, между которыми мож-
но установить теплообменные устройства.
Рис. 5.2. Диаграмма «Т – х» процесса дегидрирования этилбензола:
хр – равновесные степени превращения; λ – отношение пар : газ; 1 – режим процесса в однослойном реакторе; 2 – режим процесса в двухслойном реакторе
56
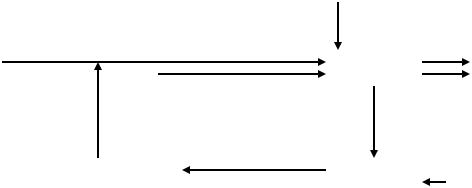
Обычно достаточно двух слоёв катализатора, между которыми по-
даётся водяной пар, обеспечивающий необходимый подогрев реакцион-
ной смеси и способствующий сдвигу равновесия реакции в правую сторо-
ну и удалению отложений кокса на катализаторе (рис. 5.2).
Вопрос. Какими способами (приёмами) выполняется концепция наибо-
лее полного использования сырьевых ресурсов при создании ХТС про-
изводства стирола?
Ответ. Фракционный рецикл. В результате неполного превращения этилбензола возможны его потери. Поэтому в системе ректификационного выделения и очистки стирола этилбензол отделяют от стирола и возвра-
щают на дегидрирование в потоке рецикла, смешивая его перед входом в реактор со свежим этилбензолом. Такая организация процесса позволяет при неполном превращении этилбензола в реакторе обеспечить общее полное превращение исходного реагента в системе.
Регенерация с рециклом. Стирол является мономером полистирола и чрезвычайно склонен к реакции полимеризации в условиях разделения продукционной смеси на стадии ректификации.
|
|
|
|
Продукты дегидри- |
|||
|
|
|
|
рования ЭБ |
|
|
|
Сера |
|
|
|
|
|
|
|
|
|
1 |
|
|
Стирол |
||
|
|
|
|
|
|
||
|
|
Стирол, ЭБ |
|
|
|
(продукт) |
|
|
|
|
|
||||
|
|
|
|
|
|
||
Сера |
|
|
ЭБ (возвратный) |
||||
|
|
|
|
||||
|
|
|
|
|
|
|
|
|
3 |
|
Стирол, угле- |
2 |
|
|
|
|
|
|
|
|
|
|
|
|
|
|
водороды |
|
|
|
|
Рис. 5.3. Схема производства стирола с регенерацией реагентов:
1 – ректификация; 2 – растворение кубовых остатков ректификации (КОРС) и кристаллизация серы; 3 – мономеризация КОРС
57
Для предотвращения полимеризации стирола в системе ректифика-
ции продуктов дегидрирования этилбензола в стирол в колонну отгонки продукта добавляют элементарную серу (рис. 5.3).
Однако полимеризация стирола всё же частично протекает. Её про-
дукты вместе с серой накапливаются в кубовых остатках ректификации
(КОРС). Серу регенерируют растворением в углеводородной среде с по-
следующей её кристаллизацией. Стирол регенерируют из полимерных продуктов при повышенных температурах. Регенерация серы и стирола в таком процессе достигает 90–95 %.
Вопрос. Как выполняется концепция минимизации отходов при создании ХТС производства стирола?
Ответ. Замкнутый водооборот. Вода в производстве стирола служит ис-
точником пара, для повышения эффективности процесса дегидрирования.
Организация замкнутого водооборота позволяет избежать образования одного из отходов – загрязнённой воды. Реакционная смесь после реакто-
ра дегидрирования содержит углеводороды и воду, разделение которых проходит в разделителе фаз. Водный слой после очистки подаётся на пи-
тание котла-утилизатора для выработки технологического пара и далее в рецикл. Избытки воды направляют на биологическую очистку.
Замена способа теплообмена. Замена водяного холодильника на воздушный при охлаждении и конденсации углеводородов из контактно-
го газа позволяет отказаться от дорогостоящей очистки оборотной воды.
Использование отходов производства. Бензол и толуол, являющиеся от-
ходами данного производства, являются полезными продуктами и после выделения могут быть использованы в других производствах. Водород,
выделяемый на стадии разделения продуктов, может использоваться в синтезе аммиака.
58
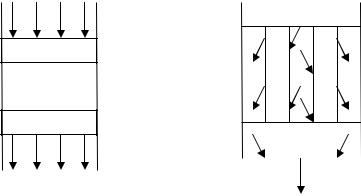
Вопрос. Как выполняется концепция эффективного использования обору-
дования при создании ХТС производства стирола?
Ответ. Если выполнить слой катализатора в виде цилиндра и направить по-
ток через него в радиальном направлении (рис. 5.4б), то это позволит со-
здать более компактную конструкцию, а также сделать слой катализатора с большим сечением и меньшей толщины для прохождения потока по срав-
нению с реактором с аксиальным слоем катализатора (рис. 5.4а). Это суще-
ственно уменьшает также гидравлическое сопротивление слоя, снижая тем самым энергетические расходы.
а |
б |
Рис. 5.4. Реакторы с аксиальными (а) и радиальными (б) слоями катализатора
Вопрос. Какими способами выполняется концепция полного использо-
вания энергетических ресурсов при создании ХТС производства стиро-
ла?
Ответ. Регенерация теплоты (рис. 5.5).
В ХТС производства стирола теплота контактного газа, выходящего из реактора дегидрирования 3 (рис. 5.5) при температуре 850–860 К, ис-
пользуется в теплообменнике-подогревателе этилбензола 4 перед реак-
тором и далее в котле-утилизаторе 5 перед пароперегревательной печью
1 для выработки технологического пара.
Регенерация энергии (рис.5.5). Контактный газ после реактора 3, пройдя стадию охлаждения 4,5 и очистки 6, а также конденсации воды и углево-
59
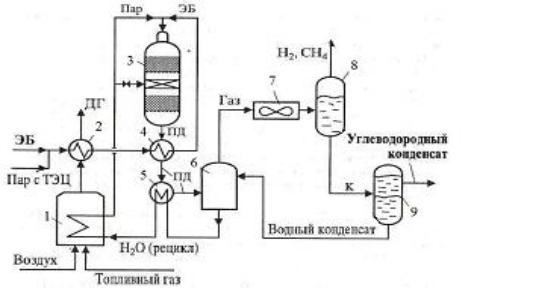
дородов 7, попадает в сепаратор 8, где газообразные продукты реакции от-
деляются как вторичные энергетические ресурсы (ВЭР). Далее они (топ-
ливный газ) сжигаются в пароперегревательной печи 1 вместе с топливом из заводской сети для получения перегретого водяного пара с температу-
рой 973–1003 К, идущим на смешение с парами этилбензола перед входом в реактор дегидрирования 3.
Рис. 5.5. Схема дегидрирования этилбензола в стирол:
1 – пароперегревательная печь; 2 – испаритель этилбензола; 3 – реактор дегидрирования; 4 – подогреватель этилбензола; 5 – котел-утилизатор (подогреватель воды); 6 – пенный аппарат; 7 – воздушный холодильник; 8 – сепаратор; 9 – разделитель фаз;
потоки: ЭБ – этилбензол (свежий и рецикл); Н2, СН4 – горючие газы в топливную сеть; ДГ – дымовые газы; К – конденсат; ПД – продукты дегидрирования
Энерготехнологическая система. В промышленных агрегатах дегидриро-
вания этилбензола тепловой КПД имеет низкое значение 28–33 %. Это свя-
зано с необратимыми энергетическими потерями, многократной конденса-
цией и испарением водяного пара, утилизацией теплоты во многих тепло-
обменниках и т.д. Значительно улучшить использование энергетического потенциала процесса можно в энерготехнологической системе, которая включает в себя энергетический узел, потребляющий топливо и вырабаты-
вающий энергию для компенсации необратимых потерь. Водяной пар, яв-
60