
ОХТ в вопросах и ответах Ч2
.pdfВопрос. Какие существуют решения по усовершенствованию производ-
ства серной кислоты?
Ответ. Одним из наиболее эффективных решений по значительному улучшению технико-экономических показателей производства серной кислоты является повышение единичной мощности системы. Как известно,
повышение единичной мощности системы в 2-3 раза позволит снизить удельные капитальные затраты на 15-20%, при этом производительность труда возрастёт примерно в 2 раза. В настоящее время типовой является система производительностью 1000 т/сутки серной кислоты. В ближайшие годы можно ожидать ввода в действие систем мощностью 2000 и даже
3000 т/сутки.
Другим важным мероприятием может стать увеличение давления процесса. Реакция окисления диоксида серы сопровождается уменьшением объёма и согласно принципу Ле-Шателье увеличение давления благопри-
ятствует смещению равновесия в правую сторону и позволяет достигать более высоких значений степени переработки сырья. Дополнительным ар-
гументом в пользу применения повышенного давления является возмож-
ность перестройки традиционной ресурсо-энергосберегающей системы в систему энерго-технологическую. Такая система полностью снабжает себя энергией и дополнительно выдает на сторону энергетический пар. Приме-
ры эффективной работы сернокислотных систем имеются в зарубежной практике.
Следующее важной направление в усовершенствовании производ-
ства серной кислоты состоит в замене воздуха, используемого на стадиях сжигания серосодержащего сырья и окисления диоксида серы, кислородом или воздухом, обогащенным кислородом. Расчёты показывают, что приме-
нение технического кислорода или воздуха, обогащенного кислородом,
позволит примерно в 4-5 раз увеличить интенсивность этих стадий.
21
3. ХТС производства аммиака
Вопрос. Какие реакции образуют химическую схему ХТС производства аммиака?
Ответ. Химическая схема представляет собой последовательность основ-
ных химических реакций, осуществляемых для переработки азотоводород-
ной смеси в аммиак:
паровая конверсия метана |
CH4 + H2O CO + 3H2 Qp1; |
(1) |
воздушная конверсия метана |
CH4 + 1/2 O2 CO + 2H2 + Qp2; (2) |
|
конверсия оксида углерода |
СО + H2O CO2 + H2 + Qp3; |
(3) |
синтез аммиака |
N2 + 3H2 2NH3 + Qp4. |
(4) |
Все реакции каталитические, из них (1), (3) и (4) – обратимые, реак-
ция (1) – эндотермическая, остальные реакции – экзотермические.
Вопрос. Что представляет собой операционная модель ХТС производства аммиака?
Ответ. Операционная модель ХТС производства аммиака представляет собой последовательность технологических операций переработки азото-
водородной смеси в аммиак.
Производство аммиака описывается следующей операционной схе-
мой:
1) перевод всех серосодержащих соединений, отравляющих катали-
заторы, в сероводород путём их каталитического гидрирования;
2)очистка природного газа от сероводорода;
3)паровая конверсия метана;
4)воздушная конверсия метана (служит для окончательного превра-
щения метана в Н2). Одновременно в производство вовлекается азот, вхо-
дящий как основной компонент в состав воздуха и необходимый для син-
теза аммиака;
22

5)конверсия оксида углерода СО с водяным паром;
6)вывод СО2 как побочного продукта из реакционной смеси;
7)очистка газа от оксидов углерода. После стадий 5 и 6 остаётся не-
большое количество СО и СО2, которые мешают дальнейшим превраще-
ниям азотоводородной смеси в аммиак. Удаляют оксиды углерода путём их каталитического гидрирования;
8)синтез аммиака из практически чистой азото-водородной смеси;
9)утилизация отдувочных газов из отделения синтеза аммиака.
Вопрос. Что представляет собой функциональная схема ХТС производства аммиака?
Ответ. Функциональная схема ХТС производства аммиака представляет собой последовательность основных отделений (подсистем) производства аммиака и соответствует приведённым выше химической и операционной схемам (рис. 3.1). Цифрами на схеме обозначены подсистемы ХТС.
|
|
Н2О |
Воздух (N2+O2) |
|
|
|||||||
СН4 |
|
|
|
|
|
|
|
|
|
|
|
NH3 |
1 |
|
|
2 |
|
|
3 |
|
4 |
|
5 |
||
|
|
|
|
|
|
|
|
|||||
|
|
|
|
|
|
|
|
|
|
|
|
|
Рис. 3.1. Функциональная схема ХТС производства аммиака:
1 – подсистема очистки природного газа от серосодержащих соединений; 2 – подсистема паровоздушной конверсии метана; 3 – подсистема конверсии оксида углерода водяным паром; 4 – подсистема очистки азотоводородной смеси от оксидов углерода;
5 – подсистема синтеза аммиака
Вопрос. Почему необходима очистка природного газа от серосодержащих соединений?
Ответ. Природный газ изначально содержит примеси серосодержащих со-
единений: меркаптаны (RSH), тиофен (гетероциклическое соединение
C4H4S), сероуглерод (CS2), сульфиды (R2S), сероводород (H2S) и др. Кроме того, перед транспортировкой по трубопроводам природный газ дополни-
тельно одорируют, добавляя этилмеркаптан, обладающий сильным запа-
23
хом. Одорирование придаёт специфический запах природному газу, что необходимо в целях безопасности.
Для очистки от серосодержащих соединений можно использовать сорбционные методы, но различные компоненты удаляются разными спе-
цифичными сорбентами. Чтобы избежать многоступенчатой сорбционной сероочистки (минимизировать затраты), все серосодержащие соединения природного газа переводят в одну форму – их гидрируют до сероводорода:
RSH + H2 = H2S + RH;
C4H4S + 4H2 = H2S + C4H10;
CS2 + 4H2 = 2H2S + CH4 и т.д.
Водород для гидрирования используется из азотоводородной смеси.
После операции гидрирования природный газ, содержащий серу в виде
H2S, направляется на стадию собственно сероочистки.
Вопрос. Как осуществляется очистка природного газа от сероводорода?
Ответ. Очистка природного газа от сероводорода проводится путём хими-
ческой адсорбции на оксиде цинка ZnO:
ZnO + H2S = ZnS + H2O.
Это гетерогенный процесс, протекающий в системе «газ–твёрдое», с
образованием твёрдого продукта реакции и описываемый моделью «сжи-
мающееся ядро». Процесс проводится при 520 690 К и лимитируется внутренней диффузией.
Вопрос. В чём заключаются термодинамические закономерности процесса паровой конверсии метана?
Ответ. Реакция конверсии метана с водяным паром является обратимой и эндотермической:
CH4 + H2O CO + 3H2 Qp
24
Согласно принципу Ле Шателье увеличение температуры благоприят-
но влияет на равновесие и приводит к увеличению равновесной степени превращения хр. Температура, необходимая для полного превращения ме-
тана составляет 1300 К. Реакция конверсии метана сопровождается по-
вышением объёма реакционной смеси, поэтому с ростом давления равно-
весие сдвигается в сторону исходных веществ. Сдвиг равновесия в сторону продукта можно осуществить путём использования избытка второго реа-
гента λ (в данном случае водяного пара по отношению к CH4). Практически полное превращение метана xр = 99 % может быть достигнуто при дву-
кратном избытке водяного пара. Характерные зависимости хр(Т), хр(Р),
хр( ) приведены в [3, рис. 2, c. 18].
Вопрос. В чём заключаются кинетические закономерности процесса паро-
вой конверсии метана?
Ответ. Основным понятием кинетики является скорость реакции. Чтобы обосновано судить о том, как и какие параметры влияют на скорость реак-
ции, необходимо иметь её кинетическую модель. Скорость реакции про-
порциональна концентрации метана и описывается кинетическим уравне-
нием 1-го порядка. Тогда для анализа влияния параметров на скорость ре-
акции удобно воспользоваться уравнением (37) или (38) [3, c. 27].
Температура влияет на константы скоростей прямой и обратной ре-
акции, константу равновесия и равновесную степень превращения. С уве-
личением температуры они растут, соответственно возрастает и скорость реакции. Однако из-за ограничений по температуре (материал реактора допускает нагрев не выше 1180 –1200 К степень превращения метана не превышает 75 %.
С увеличением давления скорость реакции сначала растёт в связи с повышением концентрации или парциального давления метана, а затем начинает снижаться из-за значительного уменьшения равновесной степени
25
превращения и движущей силы обратимой реакции, равной (хр – х). Зави-
симость скорости реакции от давления проходит через максимум. Таким образом, необходимо некоторое избыточное давление для достижения максимальной скорости паровой конверсии метана.
С увеличением избытка водяного пара равновесие реакции сдвигает-
ся вправо, возрастает xр и движущая сила в кинетическом уравнении ско-
рости реакции. Однако создание избытка водяного пара больше двукрат-
ного нецелесообразно, так как при этом снижается концентрация метана и скорость его превращения.
Вопрос. Какая форма зерна катализатора в условиях паровой конверсии метана обеспечит высокую эффективность его использования при относи-
тельно небольшом гидравлическом сопротивлении слоя?
Ответ. При температуре процесса 1070 1200 К значения константы скоро-
сти и скорости реакции значительные, так что химическая реакция не мо-
жет быть лимитирующей стадией процесса. Если скорость реакция боль-
шая, при контакте реагентов с зерном катализатора они мгновенно реаги-
руют на его внешней поверхности.
Процесс паровой конверсии метана протекает во внешнедиффузион-
ной области, и согласно закону Фика интенсивность массопереноса про-
порциональна внешней поверхности зерна. Развитие у зерна катализатора внутренней поверхности и пористости становится бесполезным (даже вредным), так как это приводит к снижению его механической прочности.
Поэтому с точки зрения эффективности процесса конверсии метана, ми-
нимизации загрузки и затрат на катализатор в реакторе целесообразно ис-
пользовать катализатор с высокой внешней поверхностью (например, фи-
гурные зёрна в форме звездочек или колец). Одновременно при этом обес-
печивается значительная доля свободного объёма в слое катализатора, что будет способствовать снижению гидравлического сопротивления и соот-
26
ветственно уменьшению энергозатрат на транспортировку реакционной смеси через реактор.
Вопрос. Как выбирается оптимальное давление процесса паровой конвер-
сии метана?
Ответ. Оптимальное давление процесса паровой конверсии метана при размещении реактора в технологической схеме рассчитывается с учётом минимизации затрат на компримирование азотоводородной смеси. На ста-
дии синтеза аммиака оптимальное давление составляет 30 МПа. После па-
ровой конверсии метана в соответствии со стехиометрией реакции значи-
тельно увеличивается объём реакционной смеси.
Техноэкономические расчёты показали, чтобы избежать чрезмерных затрат на сжатие после реакции и минимизировать таким образом затраты на компримирование газа в производстве аммиака, давление на стадии конверсии метана должно составлять около 4 МПа. Такое давление не яв-
ляется оптимальным для процесса паровой конверсии метана, но оказыва-
ется выгодным для производства в целом. Здесь проявляется одно из свойств ХТС: оптимальные условия одиночного реактора отличаются от оптимальных условий реактора, включённого в технологическую схему.
Вопрос. Чем обоснована двухстадийная схема конверсии (превращения)
метана в трубчатой печи и в шахтном реакторе?
Ответ. Для более полного превращения метана по реакции:
CH4 + H2O CO + 3H2 (1)
следует увеличить температуру процесса. На 1-й ступени это сделать за-
труднительно из-за ограничений по температуре (материал реактора до-
пускает нагрев не выше 1070 1200 К). Поэтому необходима 2-я ступень конверсии. Она представлена адиабатическим реактором, или, как его называют, шахтным конвертором. Стенки его внутри футерованы огне-
упором. Необходимую температуру создают тем, что в реактор подают
27
воздух. Часть метана сгорает, и температура повышается до 1230 1280 К.
Высокая температура и разбавление реакционной смеси инертным газом
(азотом) способствуют сдвигу равновесия реакции (1) вправо.
С воздухом вводится и азот, необходимый для синтеза аммиака, так что 2-я ступень конверсии ещё выполняет функцию поставщика азота в производство аммиака. Количество подаваемого воздуха должно быть та-
ким, чтобы соотношение водород : азот соответствовало стехиометриче-
скому для синтеза аммиака, равным 3:1.
Вопрос. В чём заключаются физико-химические закономерности процесса конверсии оксида углерода?
Ответ. Конверсия СО каталитический процесс с обратимой экзотерми-
ческой реакцией:
СО + H2O CO2 + H2 + Qp
Смещению равновесия в правую сторону благоприятствуют умень-
шение температуры и использование избытка пара по отношению к СО.
Скорость конверсии СО как обратимой реакции, можно представить в виде выражения (37) или (38) в [3, с. 27], в соответствии с которым на неё влия-
ет концентрация и температура. Использование избытка пара по отноше-
нию к СО не только сдвигает равновесие реакции вправо, но также увели-
чивает движущую силу этой обратимой реакции (хр – х) и соответственно её скорость. Однако при чрезмерном избытке пара снижается концентра-
ция полезного реагента СО и скорость реакции падает. Оптимальное со-
отношение Н2О : СО 2. Давление не влияет на равновесие, но приводит к росту концентрации реагентов и скорости реакции. Процесс проводят под повышенным давлением, близким к давлению на стадии конверсии метана.
Чтобы достигнуть наибольшей степени превращения СО при мини-
мальном времени пребывания смеси в реакторе, процесс следует вести при
28
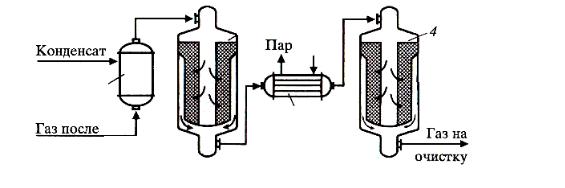
максимально возможной скорости. Максимально возможная скорость обеспечивается, если процесс осуществляется в режиме, близком к линии оптимальных температур (ЛОТ). Для конверсии СО не существует одного типа катализатора, одинаково активного при низких и высоких температу-
рах. Используют два типа катализаторов: один активен в области высоких температур 870–970 К и неактивен при низких температурах, другой – проявляет высокую активность уже при 750–800 К.
Вопрос. Как эффективно провести процесс конверсии СО в адиабатиче-
ских условиях?
Ответ. Если реакцию конверсии СО проводят в адиабатических условиях,
необходимо секционировать реакционную зону, т.е. расположить катали-
затор по слоям, и процесс проводить с промежуточным охлаждением ре-
акционной смеси между слоями. Технологическая схема конверсии СО приведена на рис. 3.2.
2
1
3
конверсии сн4
Рис. 3.2. Технологическая схема процесса конверсии СО:
1 – увлажнитель; 2 – реактор с высокотемпературным катализатором; 3 – котелутилизатор; 4 – реактор с низкотемпературным катализатором
Диаграмма «Т–x» конверсии СО представлена на рис. 3.3. В первом слое реактора загружен высокотемпературный катализатор, а во втором низкотемпературный. Остаточное содержание СО не превышает 0,3–0,5 %.
29
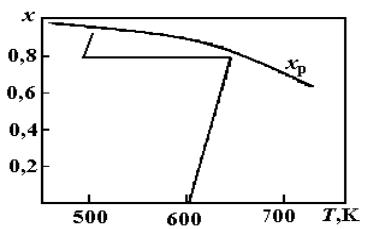
Рис. 3.3. Диаграмма «Т–х» конверсии СО:
х р – равновесные степени превращения СО; ломаная линия – режим конверсии
Вопрос. Зачем нужно чистить конвертированный газ от диоксида уг-
лерода?
Ответ. Конвертированный газ содержит до 20 об. % СО2. Необходимость очистки обусловлена следующими причинами:
-присутствие диоксида углерода в азотоводородной смеси снижает концентрации полезных компонентов, ухудшает работу стадии синтеза аммиака;
-диоксид углерод является побочным продуктом, имеет коммерче-
ское значение.
Диоксид углерода выделяют путём селективной абсорбции раство-
ром моноэтаноламина (МЭА) NH2CH2CH2OH.
Вопрос. В чём заключаются физико-химические основы процесса очистки конвертированного газа от диоксида углерода?
Ответ. Диоксид углерода абсорбируют 19 21 %-м водным раствором мо-
ноэтаноламина (МЭА-очистка):
2RNH2 + H2O + CO2 (RNH3)2CO3.
Это гетерогенный процесс с обратимой реакцией. МЭА как вещество
30