
ОХТ в вопросах и ответах Ч2
.pdf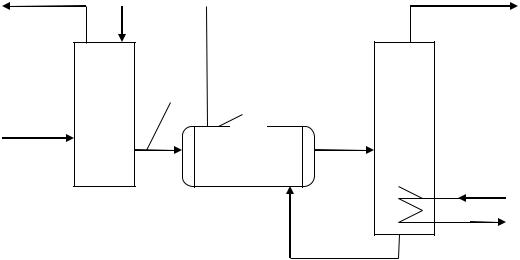
обладает основными свойствами, CO2 имеет кислые свойства, а сама реак-
ция является реакцией нейтрализации. Учитывая природу веществ, можно с большой вероятностью предположить, что процесс не будет лимитиро-
ваться химической реакцией. Тогда скорость процесса определяется по уравнению диффузионной кинетики [3, с. 88], согласно которому для ин-
тенсификации процесса хемосорбции целесообразно увеличить поверх-
ность контакта фаз, давление, степень турбулентности контактирующих потоков и снизить температуру.
Вопрос. Какой будет технологическая схема МЭА-очистки?
Ответ. Очистка конвертированного газа от диоксида углерода осуществ-
ляется в соответствии со схемой, содержащей два основных аппарата аб-
сорбер и десорбер (рис. 3.4).
H2 , N2 |
МЭА |
CO2 |
МЭАотр |
3 |
1 |
2 |
|
H2 , N2
CO2
4 Пар
МЭА
Рис. 3.4. Технологическая схема МЭА-очистки:
1 – абсорбер; 2 – теплообменник; 3 – десорбер, 4 – подогреватель
В схеме МЭА-очистки используется известный приём регенерация с рециклом, который позволяет наиболее эффективно использовать обору-
дование и сырьевые ресурсы. После поглощения СО2 отработанный рас-
31

твор моноэтаноламина (МЭАотр) подогревают в теплообменнике 2 и
направляют в десорбер 3, обогреваемый паром. При нагревании выделяет-
ся СО2 как побочный продукт, а раствор МЭА возвращают в абсорбер 1.
Схема работает с минимальными потерями сорбента раствора МЭА и получением дополнительного продукта CO2, который используют в дру-
гих производствах (для получения карбамида, «сухого» льда и т.д.).
Вопрос. В чём заключаются физико-химические основы синтеза аммиака?
Ответ. Синтез аммиака представляет собой каталитический процесс с об-
ратимой экзотермической реакцией, протекающей с уменьшением объёма:
N2 + 3H2 2NH3 + 103,6 кДж
Под физико-химическими основами процесса синтеза аммиака по-
нимают влияние параметров (температуры, давления) на равновесие, ско-
рость реакции и степень использования внутренней поверхности катализа-
тора. Эти знания позволяют предложить оптимальный режим синтеза ам-
миака и в последующем выбрать реактор, в котором обеспечивается мак-
симальная скорость реакции и достигается наибольшая степень превраще-
ния азотоводородной смеси.
Вопрос. Как выразить константу равновесия, если исходная азотоводород-
ная смесь имеет стехиометрический состав?
Ответ. Для стехиометрической смеси двух реагентов степени превращения каждого из них одинаковые. Если исходная стехиометрическая смесь со-
держала 1 моль N2 и 3 моля Н2, то при равновесной степени превращения xр останется молей N2 (1 xр) и Н2 3(1 xр), образуется 2xр молей NH3, а
общий объём уменьшится и станет равным (4 2xр) молей. Объёмные кон-
центрации для Н2, N2 и NH3 станут равными, соответственно,
1 xр |
, |
3(1 xр ) |
и |
2xр |
. |
4 2x |
|
4 2x |
|
4 2x |
|
р |
|
р |
|
р |
32

Равновесие реакции синтеза аммиака опишем уравнением:
|
|
|
P |
2 |
|
|
|
|
4 |
2 |
2 x |
|
x |
2 |
|
|||
K |
|
|
|
NH |
3 |
|
|
|
|
|
p |
|
p |
|
||||
|
|
|
|
|
|
|
|
|
|
|
||||||||
|
p |
|
P |
|
|
P |
|
|
|
3 |
P |
|
|
|
|
4 |
||
|
|
|
N |
2 |
H |
2 |
равн |
|
|
|
|
|
1 |
x |
|
|||
|
|
|
|
|
|
|
|
|
|
|
|
p |
|
.
Вопрос. Как влияет температура и давление на равновесие реакции синте-
за аммиака?
Ответ. Согласно принципу Ле-Шателье понижение температуры и повы-
шение давления сдвигает равновесие реакции в сторону увеличения со-
держания аммиака. Зависимости хр(Т), хр(Р) приведены в [3, рис. 2, c. 18].
Вопрос. Как влияют температура и давление на скорость реакции синтеза аммиака?
Ответ. Для оценки влияния параметров на скорость обратимой реакции удобно воспользоваться уравнением (37) или (38) в [3, c. 27] в соответ-
ствии с которым, на неё влияют концентрация (давление) и температура.
Скорость реакции с увеличением температуры проходит через максимум,
как и для всех других обратимых экзотермических реакций (в [3, рис. 5, c.
28]). Чтобы достигнуть наибольшей степени превращения азотоводород-
ной смеси или максимального содержания аммиака в реакционной смеси при минимальном времени пребывания, процесс следует вести при макси-
мально возможной скорости. Катализатор синтеза аммиака активен при температурах 920–1100 К. Максимальная скорость реакции обеспечивает-
ся, если она осуществляется в режиме, близком к линии оптимальных тем-
ператур (ЛОТ).
С ростом давления возрастает равновесное содержание аммиака в реакционной смеси, что приводит к увеличению движущей силы обрати-
мой реакции, растёт также концентрация компонентов азотоводородной смеси. Поэтому давление влияет положительно на скорость синтеза амми-
ака.
Вопрос. Как выбирают оптимальное давление синтеза аммиака?
33
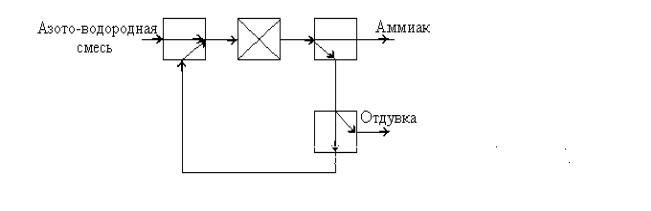
Ответ. При атмосферном давлении (0,1 МПа) превращение компонентов азотоводородной смеси очень мало. Промышленно важная область давле-
ний синтеза аммиака, при которых степень превращения будет более 20 %,
составляет выше 20 МПа. Техноэкономическое обоснование процесса по-
казало, что оптимальным будет осуществление процесса при давлении около 30 МПа. Более высокое давление резко увеличивает затраты на обо-
рудование и компрессию, а снижение давления увеличивает затраты на выделение аммиака.
Вопрос. Какой является структурная схема процесса синтеза аммиака?
Ответ. Выходящий газ из промышленного реактора содержит 16 об.%
аммиака. Для полноты использования азотоводородной смеси применяют фракционный рецикл (см. рис. 1.2, схема 7 на с.8).
Рис 3.5. Подсистема синтеза аммиака
Для этого после реактора из реакционной смеси выделяют аммиак путём его конденсации, а не прореагировавшие H2 и N2 возвращают в реак-
тор. В поступающей смеси содержится до 1,2 % инертных веществ (СH4 и
Ar, вносимый с воздухом). При увеличении содержания инертных газов в цикле синтеза аммиака снижается концентрация водорода и азота, что приводит к уменьшению интенсивности процесса синтеза аммиака. С це-
лью недопущения накопления инертов в цикле синтеза аммиака содержа-
ние их в циркулирующем газе поддерживают на определённом уровне
34
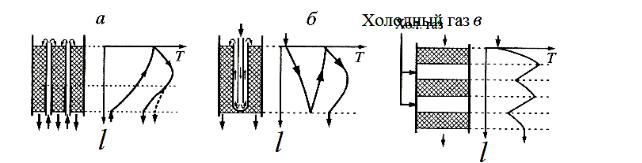
(10 15 об. %) путём вывода (отдувки) части рециркулирующего газа (рис. 3.5). Отдувка составляет около 8 об.% от потока свежей азото-водородной смеси.
Вопрос. Какие реакторы можно предложить для эффективного проведения синтеза аммиака?
Ответ. Реакция синтеза аммиака – обратимая и экзотермическая. Макси-
мальная скорость реакции и высокая степень превращения обеспечивают-
ся, если процесс вести в режиме, близком к ЛОТ. Режим процесса, близкий к оптимальному, можно организовать в трубчатом реакторе с охлаждением или в многослойном реакторе с промежуточным теплообменом. Схемы ре-
акторов показаны на рис. 3.6.
Холодный газ |
в |
l |
l |
l |
|
Рис. 3.6. Схемы реакторов синтеза аммиака и профили температур по высоте l:
а – с простыми противоточными трубками;б – с двойными трубками (трубками Фильда); в – многослойный реактор
Вопрос. Как осуществить синтез аммиака в трубчатом реакторе?
Ответ. В трубчатом реакторе тепло из реакционной зоны отводится к све-
жей реакционной смеси (рис. 3.6а). Реактор, в котором теплоотвод от ре-
акционной зоны осуществляется не посторонним носителем, а самой реак-
ционной смесью, носит название автотермического реактора. Катализатор располагают в межтрубном пространстве. Газ поступает в трубки, нагрева-
ется и затем входит противотоком в слой катализатора. По мере продвиже-
ния газа возрастает содержание аммиака z и одновременно происходит
35
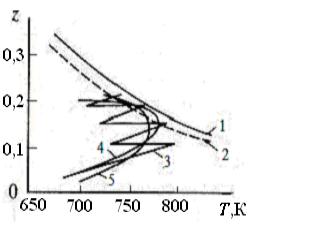
снижение температуры. На рис. 3.6а приведён профиль температуры в ре-
акторе.
Аналогичный эффект достигается при использовании двойных тру-
бок (трубок Фильда) – рис. 3.6б. Газ поступает во внутренние трубки, за-
тем входит в кольцевое пространство между внутренними и наружными трубками. Проходя это пространство, газ нагревается от слоя катализатора и одновременно отдаёт часть тепла газу, циркулирующему во внутренних трубках. Режим процесса в слое в координатах «Т z» показан на рис. 3.7.
Содержание аммиака, об. доли
Рис. 3.7. Диаграмма «Т–z» режима процесса в реакторе синтеза аммиака:
1 – равновесные концентрации; 2 – оптимальные температуры; 3 – процесс в многослойном реакторе; 4, 5 – процесс в трубчатом реакторе (одинарные и двойные трубки соответственно)
а рис. 3.7 в координатах "Т–z" иллюстрирует режим процесса в слое ката-
лизатора.
Вопрос. Как осуществить синтез аммиака в многослойном реакторе?
Ответ. В многослойном реакторе (рис. 3.6в) процесс проводят в адиабати-
ческом режиме в нескольких слоях катализатора с промежуточным охла-
ждением. Компактность конструкции реактора достигается, если темпера-
туру между слоями снижать вводом холодного газа. Режим процесса в слое катализатора в координатах "Т–z" показан на рис. 3.7 (кривая 3). Во всех типах реакторов предварительный нагрев газа в теплообменнике потоком,
36
выходящим из слоя катализатора. Все элементы реактора – слои катализа-
тора, теплообменники, смесители – располагаются в одном корпусе высо-
кого давления. Поступающий холодный газ проходит в узком кольцевом пространстве вдоль стенок, предохраняя их от нагрева (рис. 3.6в). Это важно для сохранения прочности корпуса, находящегося под высоким дав-
лением.
Вопрос. Является ли ХТС производства аммиака энерготехнологической системой?
Ответ. В производстве аммиака используется энергоёмкое оборудование,
мощные турбокомпрессоры. Обеспечить необходимую мощность возмож-
но путём подвода энергии со стороны, либо за счёт использования соб-
ственных энергоносителей, в частности, энергетического водяного пара.
Суммарная энергия образующихся высокопотенциальных технологиче-
ских потоков (конвертированный и дымовые газы после конверсии метана,
синтез-газ после метанирования, газ после конверсии метана) не покрывает общих затрат производства на сжатие природного газа и воздуха, азотово-
дородной смеси, циркуляцию в подсистеме синтеза. Необходим дополни-
тельный высокотемпературный источник энергии. Им является энергети-
ческий узел (рис. 3.8), представляющий собой дополнительный котёл 6 с
огневым обогревом 3, установленный в газоходе 1 после трубчатой печи.
Пар, получаемый в котлах-утилизаторах в линиях технологических потоков (4 и 5) и в дополнительном котле, собирается в паросборнике 2 и
оттуда распределяется на паровые турбины – приводы компрессоров. Та-
ким образом, производство аммиака становится автономным по энергии,
но для выработки необходимого энергетического пара, помимо использо-
вания собственных вторичных энергетических ресурсов, необходимо определенное количество топлива – природного газа. Такая схема обеспе-
чения производства энергией и есть энерготехнологическая система.
37
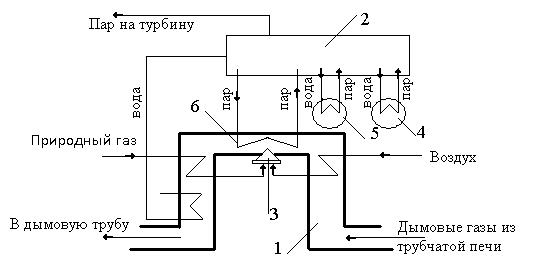
Рис. 3.8. Энерготехнологическая схема агрегата синтеза аммиака:
1 – газоход после трубчатой печи; 2 – паросборник; 3 – огневой обогрев; 4, 5 – котлы-утилизаторы (после шахтного конвертора метана и после конвертора
оксида углерода соответственно); 6 – вспомогательный котёл
Вопрос. Какие технические и технологические приёмы реализованы или могут быть предложены в производстве аммиака для решения концеп-
ции наиболее полного использования сырьевых ресурсов?
Ответ. Концепция наиболее полного использования сырьевых ресурсов
(сырья и вспомогательных материалов) в производстве аммиака может быть реализована благодаря применению следующих приёмов:
- избыток одного из компонентов водяного пара в процессах кон-
версии природного газа и оксида углерода;
- регенерация с рециклом при выделении побочного продукта ди-
оксида углерода из азотоводородной смеси;
-фракционный рецикл в синтезе аммиака;
-переработка и использование продувочных газов цикла синтеза ам-
миака;
- противоток при абсорбции СО2 раствором МЭА.
38
Вопрос. Какие технические и технологические приёмы реализованы или могут быть предложены в производстве аммиака для решения концепции наиболее полного использования топливно-энергетических ресурсов
(ТЭР)?
Ответ. Концепция наиболее полного использования ТЭР в производстве аммиака реализуется благодаря утилизации и регенерации тепла в отделе-
ниях конверсии метана, оксида углерода, метанирования, синтеза аммиака.
Вопрос. Какие технические и технологические приёмы реализованы или могут быть предложены в производстве аммиака для решения концепции эффективного использования оборудования?
Ответ. Концепция эффективного использования оборудования в производ-
стве аммиака может быть реализована следующими приёмами:
-оптимизацией стадий конверсии CO и синтеза аммиака;
-использованием реакторов с радиальным ходом газа через слои ка-
тализатора в конверсии оксида углерода и синтезе аммиака;
-совмещением процессов, например, в реакторе конверсии метана,
синтеза аммиака (реакционная зона в виде слоёв катализатора, теплооб-
менники, смесители расположены в одном корпусе).
Вопрос. Какие технические и технологические приёмы реализованы или могут быть предложены в производстве аммиака для решения концепции минимизации отходов:
Ответ. Концепция минимизации отходов в производстве аммиака может быть реализована следующими приёмами:
-регенерацией отработанного поглотителя сернистых соединений на основе сульфида цинка;
-переработкой и использованием отдувочных газов синтеза аммиака с получением продуктов, имеющих коммерческое значение (Аr, He…);
-использованием замкнутого водооборота.
39
Вопрос. Какие существуют решения по усовершенствованию производ-
ства аммиака?
Ответ. Наиболее важными направлениями в развитии производства амми-
ака являются увеличение единичной мощности, создание энерго-
технологической системы и снижение давления. В настоящее время произ-
водительность по аммиаку уже достигла 1500 т/сутки и более. В производ-
стве аммиака применена энерго-технологическая схема с паровым циклом,
позволяющая осуществить энергетическую автономию агрегата синтеза.
Высокопотенциальное тепло дымовых газов используется для проведения эндотермическогопроцесса конверсии метана в трубчатых печах. Это теп-
ло, наряду с теплом газа после конверсии оксида углерода используют также для получения пара высокого давления, применяемого в турбинах,
установленных на одном валу с насосами и компрессорами.
С понижением давления в синтезе аммиака уменьшаются энергети-
ческие затраты, но при этом возникает потребность в разработке низко-
температурных катализаторов, способных проявлять свою активность при температурах около 570 К и позволяющих вести процесс при давлении около 0,1 МПа без снижения выхода аммиака.
4. ХТС производства азотной кислоты
Вопрос. Какие реакции образуют химическую модель ХТС производства азотной кислоты?
Ответ. Химическая модель производства азотной кислоты может быть представлена следующими основными уравнениями реакций:
4NH3 + 5O2 = 4NO + 6H2O + Q1 |
(1) |
2NO + O2 = 2NO2 + Q2 |
(2) |
3NO2 + H2O = 2HNO3 + NO + Q3 |
(3) |
Вопрос. Что такое операционная модель производства азотной кислоты?
40