
ИХТ / ХТОСА / Технология энергоемких материалов(Юдин) / Еще некоторые материалы / УВ из нефти и кокса
.pdf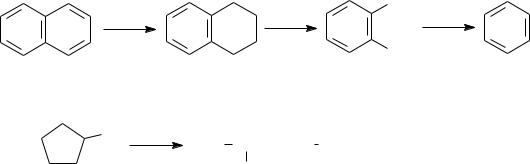
H |
H |
|
C2H5 |
H2 |
|
2 |
|
|
|||
2 |
|
|
|
+ 2C2H6 |
|
|
|
|
|
|
|
|
|
|
C2H5 |
|
|
раскрытия пятичленных циклов с образованием изоалканов:
R
CH3 CHCH2CH2 CH3 R
и другие процессы.
Так как процесс гидрогенизации протекает в избытке водорода, то реакции полимеризации и поликонденсации первичных продуктов деструкции подавляются и при достаточно высоком отношении водород/углерод продукты уплотнения почти не образуются.
Одновременно с гидрированием углеродных соединений протекают реакции гидрирования соединений, содержащих серу, кислород и азот по реакциям, аналогичным реакциям гидроочистки нефтепродуктов.
Процесс гидрогенизации является каталитическим. В качестве катализаторов используют контактные массы на основе соединений молибдена, кобальта, никеля или железа с различными активаторами, например:
Мо2О3 + NiS + СаО + ВаО + А12О3. катализатор активатор носитель
Изменением параметров процесса (температура, давление, время контакта) и состава катализатора процесс гидрогенизации может быть направлен в сторону получения продуктов заданного состава. Выход жидких и газообразных продуктов гидрирования твердого топлива существенно зависит от содержания в нем летучих веществ, то есть от степени его углефикации. Угли с высокой степенью углефикации (антрацит, тощие угли) не могут быть использованы в качестве сырья для гидрогенизации. Из топлив для этой цели пригодны бурые угли или каменные угли с отношением водород/углерод не ниже 0,06 и содержанием золы не более 0,13 массовых долей.
Процесс гидрогенизации твердых топлив может проводиться в жидкой или паровой фазе. Из многочисленных технологических схем жидкофазной гидрогенизации наиболее экономичной является циклическая схема. Она отличается от других меньшим расходом
53
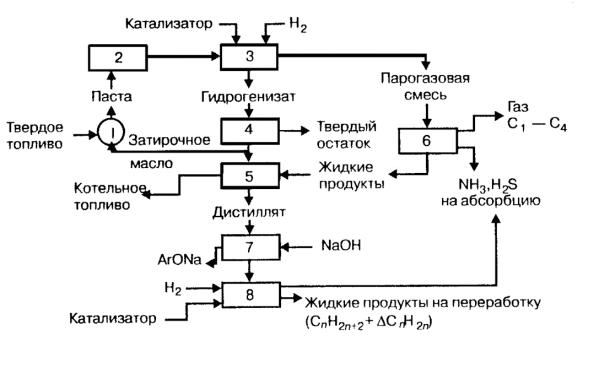
водорода, более низкими температурой и давлением процесса и позволяет полностью использовать все компоненты перерабатываемого сырья.
Принципиальная схема подобной установки гидрогенизации приведена на рисунке 10.
Рис. 10 : Схема гидрогенизации угля. 1 – смеситель; 2 – гомогенизатор; 3 – реактор; 4 – сепаратор; 5 -- колонна дистилляции; 6 – холодильник-сепаратор; 7 – промывная колонна;8
–реактор второй стадии.
Врезультате гидрогенизации всех видов твердого топлива образуются жидкий продукт, содержащий изоалканы и нафтены, используемый в качестве сырья для каталитического риформинга и гидрокрекинга, а также котельное топливо и бытовой газ.
С момента возникновения направление получения так называемой "угольной нефти" из низкокалорийного природного твердого топлива - бурого угля, торфа и сланца остаётся достаточно перспективным, и хотя запасы любого природного топлива исчерпаемы, однако на ближайшие 300-400 лет их хватит.
Большая часть современных технологий ограничивает содержание золы в углях, которое не должно превышать 10% (т.е. необходимо предварительное обогащение); нормируется и сера - не более 1,0%. В
54
результате возможно получение бензина, дизтоплива, топочного мазута, а также ценных смол для органического синтеза. В ЮАР фирма "Sasol" уже перерабатывает около 50 млн тонн угля (по схеме "Фишера-Тропша"), производя 7-8 млн тонн жидкого топлива. Китай планирует производить из угля не менее одного миллиона баррелей дизтоплива в день.
Наиболее перспективный путь - пиролитическое или гидрогенизационное (т.е. с участием "внешнего" водорода) «ожижение» таких углей. Поскольку соотношение водород-углерод (Н/С) в нефти равно 1,2, а в угле - лишь 0,7, гидрогенизация позволяет значительно увеличить выход углеводородных фракций.
Как уже упоминалось, технология получения «угольной нефти» методом гидрогенизации требует жёстких условий. Этот процесс протекает при высоких температурах ( до 600 ºС) и при высоких (50-80 МПа) давлениях, в токе водорода (от трёх процентов Н2 от массы угля, и, значит, для этих целей можно использовать коксовый газ) и в присутствие катализатора (система Al2O3-Мо3+, Co2+ или Fe3+, например, в составе пирита). Но важно подчеркнуть, что в «угольной нефти», полученной по такой технологии, содержится до 50% фракций моторных топлив (до 15%- бензиновые и до 35% - дизельные); остальные фракции - котельное топливо (мазут) и ценные соединения для органического синтеза - фенольные, пиридиновые, инден-кумароновые).
Выход «угольной нефти» из 1 т углей – примерно 500 кг; оставшиеся 500 кг представляют собой нечто вроде мелкодисперсного «полукокса», значительно более калорийного, чем исходные уголь; кроме того, образуется около 300 м3 синтез-газа (смесь СО+Н2 в соотношении 1:2) с теплотой сгорания 14-16 МДж/м3.
Однако уже появились технологии ожижения, в которых взрывоопасный водород заменён на менее опасную смесь СО+Н2О (при высокой температуре идёт конверсия угарного газа: СО+Н2О = CО2+ Н2), а давление в реакторе удалось снизить до 10 МПа.
55
2.4. Газификация угля.
Все разновидности процесса газификации угля включают в себя его реакцию с водяным паром, в результате которой образуются окись углерода и водород:
С+ Н2О → СО + Н2.
Всвязи с тем, что данная реакция высоко эндотермична и для ее
проведения требуется специальный источник энергии, параллельно (одновременно) идет реакция части угля с кислородом (т. е. его сгорание), в результате которой выделяется требуемое количество тепла. Продуктом второй реакции является двуокись углерода, но при соответствующем контроле за количеством кислорода, вступающего в реакцию, больше образуется окиси углерода:
nС + mО2 → pCO + kСО2.
Таким образом, основной топливный газ, полученный из угля, состоит главным образом из окиси углерода и водорода, количество которых варьируется в зависимости от условий прохождения процесса.
Известно несколько технологий газификации угля с получением высококалорийного горючего газа, богатого водородом. Наиболее распространенными являются технологии Лурги (стационарный слой кускового угля), Винклера (кипящий слой мелких угольных частиц), Тексако (водноугольная суспензия), газогенератор Копперса-Тотцека с аэрозольным потоком топлива.
Одна тонна угля может дать в среднем около 2000 м3 горючей газовой смеси.
Существуют технологии газификации с использованием предварительно нагретых промежуточных теплоносителей. Например, технология Kellog предусматривает использование расплава карбоната натрия: в слой расплава, вводят угольную пыль и водяной пар, при этом протекают реакции газификации с образованием СО, Н2 и СН4.
На рисунке 11 приведена схема, используемая в технологии Винклера.
56
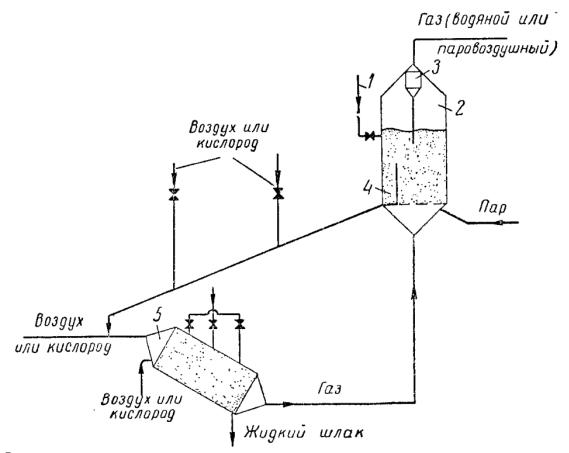
Рис. 11. Принципиальная схема газификации мелкозернистых твёрдых топлив в псевдоожиженом слое с газообразным носителем. 1 – загрузка топлива; 2 – газогенератор;
3 – пылеотделитель; 4 – переточный карман; 5 – циклонная топка.
Заманчивые перспективы газификации с применением газообразного теплоносителя открывает способ, основанный на использовании тепла ядерного реактора. Такой вариант позволяет полностью превратить органическую массу угля в газообразные продукты.
Еще одна технология - газификация топливной пыли с использованием низкотемпературной плазмы (3000-3500 оC). В этом случае получается горючий газ с высоким содержанием СО и Н2 и малым содержанием диоксида углерода, метана и азота (водяной пар в этом процессе используется в качестве плазмообразующего газа.
57

Таблица 1.
Средний состав горючего газа (об. %) при газификации угля.
Газ |
|
|
Технология газификации |
|
|
|
|
|
|
|
|
|
Винклера |
Копперса |
Лурги |
Низкотемпературная |
На базе |
|
|
-Тотцека |
|
плазма водяного пара |
тепла АЭС |
|
|
|
|
|
|
СО2 |
19 |
12 |
27 |
2 |
1 |
СО |
38 |
56 |
22 |
42 |
4 |
|
|
|
|
|
|
Н2 |
40 |
29 |
40 |
55 |
63 |
|
|
|
|
|
|
СН4 |
2 |
1 |
10 |
- |
32 |
N2 |
1 |
2 |
1 |
1 |
- |
Благодаря развитию технологий газификации углей угольные теплоэлектростанции (ТЭС) переживают нынче "второе рождение". Так, немецкие фирмы "E.On" и "RWE", а также шведская "Vattenfall" реализовали в Германии и Англии грандиозные проекты по строительству сети мощных суперсовременных, экологически чистых ТЭС.
Сейчас в мире популярны две новые технологии, улучшающие сжигание угля (особенно бурого) в котлах ТЭС и уменьшающих выброс СО2. Это технологии "Oxefuel" и "Precombusion". В обоих технологиях уголь предварительно измельчают, а затем сушат и "газифицируют", т.е. обе технологии сводятся к превращению угля (до подачи в топку) в горючую газовую (или пылегазовую) смесь.
58
3. СИНТЕЗ ГАЗ: СОСТАВ, СПОСОБЫ ПОЛУЧЕНИЯ, ПРИМЕНЕНИЕ
В 1926 году Ф. Фишер и Г. Тропш опубликовали работу "О прямом синтезе нефтяных углеводородов при нормальном давлении", где сообщалось, что при восстановлении монооксида углерода водородом при атмосферном давлении в присутствии катализаторов при температуре в 270 градусов Цельсия можно получить жидкие и твердые гомологи метана.
Так на свет появился знаменитый способ синтеза углеводородов из монооксида углерода, называемый с тех пор методом Фишера-Тропша. В дальнейшем усилия учёных и технологов всех ведущих стран были обращены на получение смесь водорода и угарного газа, которая, как показали исследования, может быть получена как из каменного угля, так и из любого другого сырья, содержащего углерод. Полученную в результате таких процессов смесь газов начали называть синтез-газом.
3.1.Состав синтез-газа
Как мы уже упомянули выше, в состав синтез-газа входят такие вещества как CO и H2. В зависимости от метода получения синтез-газа соотношение CO : Н2 в нем варьируется от 1:1 до 1:3. В прямой зависимости от применяемого сырья и метода его получения, соотношение компонентов в синтез-газе изменяется в широких пределах. Как правило, процентное содержание веществ в сыром неочищенном синтез-газе следующее:
CO - 15-18 %
H2 - 38-40 %
CH4 - 9-11 %
CO2 - 30-32 %
Стоит заметить, что данное соотношение является весьма
приблизительным, поскольку повышением температуры в процессе синтеза можно увеличить количество СО, а увеличив давление можно повысить содержание Н2 и СН4.
Также, помимо данных веществ синтез-газ может содержать и другие вещества – инертные газы (N2) и серосодержащие соединения
59

(H2S), если исходное сырье содержало серу. Синтез-газ очищают от Н2S и СО2 селективными растворителями (например, этаноламинами); соотношение между СО и Н2 регулируют, если необходимо, конверсией оксида углерода водяным паром.
3.2. Оксид углерода.
Монооксид углерода представляет собой бесцветный газ без вкуса и запаха. Так называемый «запах угарного газа» на самом деле представляет собой запах органических примесей.
Его температура плавления ̶ 205оС, кипения ̶ 191,5оС, критическая температура −140,23 °C, Критическое давление 3,499 МПа.
Растворимость в воде 0.0026 г/100 мл Основными типами химических реакций, в которых участвует
монооксид углерода, являются реакции присоединения и окислительновосстановительные реакции, в которых он проявляет восстановительные свойства.
При комнатных температурах CO малоактивен, его химическая активность значительно повышается при нагревании и в растворах (так, в растворах он восстанавливает соли Au, Pt, Pd и других до металлов уже при комнатной температуре. При нагревании восстанавливает и другие металлы, на пример CO + CuO → Cu +CO2↑. Это широко используется в пирометаллургии. На реакции CO в растворе с хлоридом палладия основан способ качественного обнаружения CO.
Предельно допустимая концентрация монооксида углерода в воздухе промышленных предприятий составляет 0,02 мг/л. Концентрация более 0,1
%— смертельна. В выхлопе бензинового двигателя допускается до 1,5-3%.
Влаборатории угарный газ получают разложением муравьиной кислоты под действием горячей концентрированной серной кислоты.
Оксид углерода (СО) образуется при горении угля или углеводородов в условиях недостатка кислорода. Промышленными способами получения СО является восстановление СО2 углём при 1000 оС и разделение синтез-газа методом низкотемпературной конденсации и абсорбции СО медноаммиачными комплексами под давлением:
Cu+(NH3)4 + CO |
Cu+(NH3)3CO + NH3 |
|
60 |

3.3. Способы получения синтез-газа.
Первым известным человечеству способом получения синтез-газа была газификация каменного угля. Данный способ был осуществлен в Англии еще в 30-е годы XIX века, и во многих странах мира до 50-х годов XX века. Впоследствии данная методика была вытеснена методами, основанными на использовании нефти и природного газа. Однако в связи с существенным сокращением мировых нефтяных ресурсов, значение процесса газификации каменного угля снова стало возрастать. К тому же, благодаря такому необходимому процессу как переработка ТБО, ученые научились добывать синтез-газ из новых, нетрадиционных источников.
Сегодня существуют три основных метода получения синтез-газа. 1. Газификация угля. Данный процесс основан на взаимодействии
каменного угля с водяным паром и происходит по формуле:
C + H2O → H2 + CO.
Данная реакция является эндотермической, и только при температуре 900-1000 оС равновесие сдвигается вправо.
Разработаны различные технологические процессы, использующие парокислородное дутье, благодаря которому наряду с упомянутой реакцией параллельно протекает экзотермическая реакция частичного сгорания угля, которая обеспечивает необходимый тепловой баланс:
C + 1/2O2 → CO
Процесс газификации угля в настоящее время используется ограниченно. Для повышения производительности аппаратуры и её габаритов газификацию ведут под давлением до 25 МПа.
2. Конверсия метана и других парафинов. Данная реакция взаимодействия водяного пара и углеводородов проводится при повышенной температуре (800-900 оС) и давлении в присутствии никелевых катализаторов (Ni-Al2O3). В настоящее время это основной промышленный способ получения синтез-газа:
CH4 + H2O |
CO + 3H2 |
Реакция сильно эндотермична (ΔНо293 = 206 кДж/моль). При использовании метана, как следует из уравнения, водород получается с большим избытком (3:1), что, как правило, не подходит для большинства
61

реакций на базе синтез-газа. Для снижения доли водорода в газовую смесь, идущую на конверсию, добавляют СО2, который тоже реагирует с метаном:
CH + CO2 |
2CO + 2H O |
4 |
2 |
В настоящее время вместо метана используют жидкие углеводороды (в том числе и непредельные), что более удобно технологически, выгодно экономически и, что главное, позволяет получить синтез-газ с требуемым соотношением водорода и угарного газа. Эти процессы ведут под давлением порядка 2-3 МПа.
3. Парциальное окисление углеводородов. Данный процесс, происходит при температуре 1300 оС и более. Суть его в неполном окислении углеводородов в присутствии небольшого количества водяного пара:
CnH2n+2 + Н2О + 1/2nO2 → nCO + (n + 1)H2
При такой организации процесса его удаётся вести автотермически (за счёт реакции окисления сырья), при этом, образующийся побочно СО2 срабатывается в реакции с исходным углеводородом.
Данный способ применим к любому сырью, содержащему углеводороды, но наиболее часто используется высококипящая фракция нефти - мазут.
3.4. Производство синтез-газа
Сегодня производство синтез-газа постоянно совершенствуется, поскольку востребованность данного сырья неизменно растет с каждым годом. В настоящее время учеными разработаны проекты подземной газификации угля, то есть планируется, что получение синтез-газа будет происходить непосредственно в пласте угля глубоко под землей. Интересен тот факт, что подобную идею уже высказывал известнейший русский ученый Д.И. Менделеев, причем более 100 лет назад.
Также, благодаря современным разработкам, сегодня синтез-газ стало возможным получать газификацией не только угля и нефти, но и нетрадиционных источников углерода, вплоть до бытовых и сельскохозяйственных отходов. Таким образом, сегодня и
62