
ИХТ / ХТОСА / Технология энергоемких материалов(Юдин) / Еще некоторые материалы / УВ из нефти и кокса
.pdf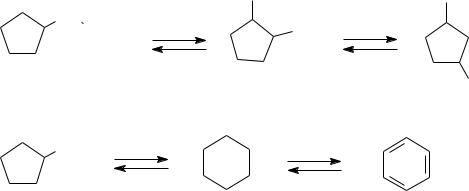
Бициклические шестичленные циклоалканы дегидрируются так же легко, как моноциклические, образуя производные нафталина.
Гидрокрекинг шестичленных циклоалканов в незначительной степени происходит по схеме, описанной для алканов. В условиях риформинга скорость дегидрирования шестичленных циклоалканов в арены значительно выше скорости других реакций (изомеризации в пятичленные и гидрокрекинга). Поэтому селективность превращения циклоалканов в арены составляет практически 100 %.
Пятичленные замещенные циклоалканы в условиях риформинга вступают в следующие реакции:
1)Изомеризация по положению заместителей (через промежуточные карбкатионы):
|
|
CH3 |
|
CH3 |
CH2 |
CH3 |
K |
CH3 |
K |
|
||||
|
|
|
CH3
2) Дегидроизомеризация:
CH3 |
K |
Pt |
+ 3H2
Первая реакция протекает на кислотных центрах катализатора, вторая — на металлических. Выход бензола возрастает с повышением температуры и снижением давления. При температуре 500 °С снижение давления с 3,6 до 1,5 МПа приводит к увеличению выхода бензола с 45 до 90 % (масс.). Дегидрирование циклопентана в циклопентен и циклопентадиен практически не идет, так как скорость этой реакции значительно ниже скорости дегидроизомеризации. Циклопентадиен прочно адсорбируется на металле и отравляет катализатор.
3) Раскрытие кольца (гидрокрекинг):
33
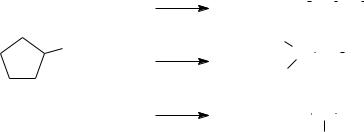
|
|
CH3 |
|
|
|
CH2CH2CH2CH2 |
|
CH3 |
(1) |
|||||
|
|
|
|
|
||||||||||
|
|
|||||||||||||
CH3 |
H2 |
CH3 CHCH2CH2 |
|
|
CH3 |
(2) |
||||||||
|
|
|||||||||||||
|
|
CH3 |
|
|||||||||||
|
|
CH3 |
|
CH2 |
CHCH2 |
|
CH3 |
(3) |
||||||
|
|
|
|
|
|
|||||||||
|
|
|
|
|
|
CH3 |
|
Относительная скорость гидрогенолиза различных С—С-связей зависит от строения исходного углеводорода, свойств катализатора и условий реакции. На свежем алюмоплатиновом катализаторе гидрогенолиз идет на платине, и соотношение продуктов по реакциям (1), (2) и (3) равно 2,4:2,1:1. В условиях процесса происходит частичная дезактивация платины, и гидрогенолиз далее протекает на кислотных центрах по карбкатионному механизму. Главным продуктом реакции становится н- гексан.
Скорость реакции дегидроизомеризации метилциклопентанов выше, чем изомеризации и гидрокрекинга, поэтому выход бензола при риформинге метилциклопентана достигает 60—70%.
Превращения аренов.
Незамещенные соединения в условиях процесса риформинга устойчивы. Метилзамещенные арены (толуол, ксилолы) подвергаются изомеризации по положению заместителей, а также, частично и деалкилированию. По современным представлениям, изомеризация ксилолов протекает через образование карбокатионов, обусловленное деформацией р-электронного облака:
34
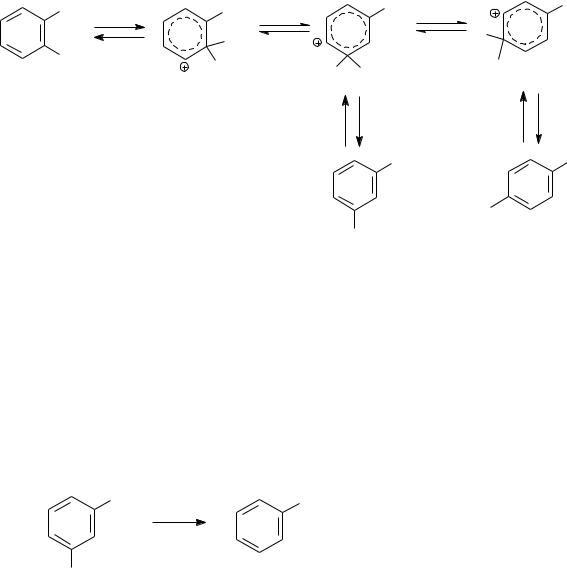
CH |
+ |
CH |
|
CH3 |
CH3 |
3 |
H |
3 |
|
|
|
|
|
CH3 |
|
|
H |
|
|
|
|
|
|
CH3 |
|
H |
H |
CH3 |
CH3 |
|
|
||||
|
|
|
|
||
|
|
|
|
+ |
-H+ |
|
|
|
|
-H |
|
|
|
|
|
CH3 |
CH3 |
|
|
|
|
|
CH3 |
|
|
|
|
CH3 |
|
р-Электроны оказывают стабилизирующее действие, и перегруппировки алкилароматических карбокатионов происходят с меньшей скоростью, чем алифатических. Алкиларены, содержащие в боковой цепи 3 и более атомов углерода, деалкилируются на кислотных центрах по схеме, аналогичной каталитическому крекингу, с последующим гидрированием выделяющегося алкена на металле. В отличие от каталитического крекинга, в условиях риформинга на металлическом катализаторе происходит также деалкилирование метилзамещенных аренов. В результате образуются сначала толуол, а затем бензол и метан:
CH3 |
H2 |
CH |
3 |
+ CH4
CH3
Наряду с деалкилированием протекают и реакции уплотнения, продуктами которых являются конденсированные ароматические углеводороды (алкилнафталины, алкилинданы и др.) в количестве 0,5-0,7% на исходное сырье риформинга.
Мощность современных установок риформинга в среднем — от 1,5 до 2,5 млн тонн, однако на заводах ведущих мировых компаний существуют установки мощностью и 4,0 млн. тонн в год.
1.3.5.2. Катализаторы процесса риформинга
Наиболее широкое распространение получили бифункциональные алюмоплатиновые катализаторы в которых платина в тонкодисперсном
35
состоянии нанесена на оксид алюминия. Платина активна в реакциях гидрирования и дегидрирования. Она способствует образованию аренов и гидрированию промежуточных алкенов. Содержание платины в катализаторе составляет обычно 0,3-0,65 %. Увеличение концентрации платины повышает активность катализатора и октановое число бензина. Однако чрезмерно высокое содержание платины нежелательно, так как при этом усиливается роль реакций деметилирования аренов и расщепления циклоалканов, уменьшающих выход бензина. Основной причиной деактивации катализатора является его закоксовывание, поэтому повышение стабильности достигается в основном введением модифицирующих добавок, влияющих на коксообразование.
Прогресс каталитического риформинга в последние годы был связан с разработкой и применением сначала биметаллических и затем полиметаллических катализаторов, обладающих повышенной активностью, селективностью и стабильностью.
Используемые для промотирования металлы можно разделить на две группы. К первой из них принадлежат металлы VIII ряда: рений и иридий, известные как катализаторы гидро-дегидрогенизации и гидрогенолиза. К другой группе модификаторов относятся металлы, практически неактивные в реакциях риформинга, такие, как германий, олово и свинец (IV группа), галлий, индий и редкоземельные элементы (III группа) и кадмий (из II группы). К биметаллическим катализаторам относятся платино-рениевые и платиноиридиевые, содержащие 0,3 – 0,4 % масс., платины и примерно столько же Rе и Ir. Рений или иридий образуют с платиной биметаллический сплав, точнее кластер, типа Pt-Re-Re-Pt-, который препятствует рекристаллизации – укрупнению кристаллов платины при длительной эксплуатации процесса. Биметаллические кластерные кристаллизаторы (получаемые обычно нанесением металлов, обладающих каталитической активностью, особенно благородных, на носитель с высокоразвитой поверхностью) характеризуются, кроме высокой термостойкости, еще одним важным достоинством – повышенной активностью по отношению к диссоциации молекулярного водорода и миграции атомарного водорода. В результате отложение кокса происходит на более удаленных от биметаллических центров катализатора, что способствует сохранению активности при высокой его закоксованности (до 20 % массовых кокса на катализаторе). Из биметаллических катализаторов платино-иридиевый превосходит по стабильности и активности в реакциях дегидроциклизации парафинов не только монометаллический, но и платино-рениевый катализатор. Применение биметаллических катализаторов позволило снизить давление
36
риформинга (от 3,5 до 2-1,5 МПа) и увеличить выход бензина с октановым числом по исследовательскому методу до 95 пунктов примерно на 6 %.
Полиметаллические кластерные катализаторы обладают стабильностью биметаллических, но характеризуются повышенной активностью, лучшей селективностью и обеспечивают более высокий выход риформата. Срок их службы составляет 6-7 лет. Эти достоинства их обусловливаются, по-видимому, тем, что модификаторы образуют с платиной (и промоторами) поверхностные тонко диспергированные кластеры с кристаллическими структурами, геометрически более соответствующими и энергетически более выгодными для протекания реакций ароматизации через мультиплетную хемосорбцию. Среди других преимуществ полиметаллических катализаторов следует отметить возможность работы при пониженном содержании платины и хорошую регенерируемость.
Успешная эксплуатация полиметаллических катализаторов возможна лишь при выполнении определенных условий:
1)содержание серы в сырье риформинга не должно превышать 0,1-0,4 % масс., что требует глубокого гидрооблагораживания сырья в блоке предварительной гидроочистки;
2)содержание влаги в циркулирующем газе не должно превышать 2*10-3- 3*10-3 % мольных;
3)пуск установки на свежем и регенерированном катализаторе требует использования в качестве инертного газа - чистого азота;
4)для восстановления катализатора предпочтительно использование электролитического водорода.
1.3.5.3. Технологическое оформление риформинга (платформинга).
Технологическая схема установки каталитического риформинга с блоком предварительной гидроочистки сырья (прямогонной бензиновой фракции) приведена на рисунке 6.
37
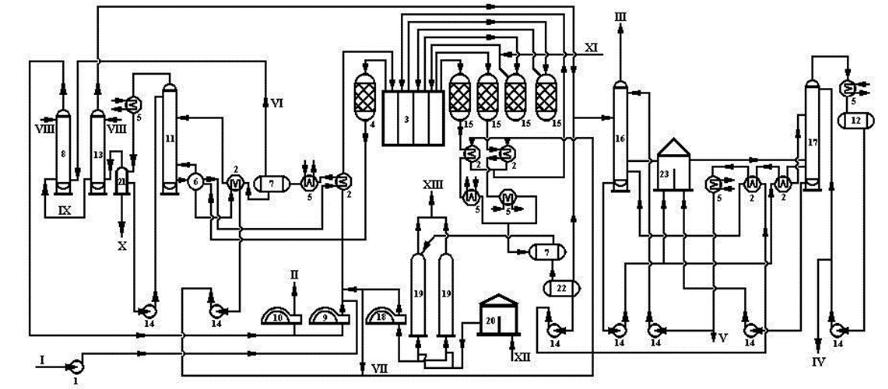
Рис. 6. Технологическая схема установки каталитического риформинга. I - сырье (прямогонная бензиновая фракция); II -
водородсодержащий газ; III - сухой газ; IV - сжиженный газ; V - стабильный высокооктановый бензин; VI - циркулирующий газ блока гидроочистки; VII - циркулирующий газ блока риформинга; VIII - водный раствор моноэтаноламина; IX - раствор моноэтаноламина, насыщенный сероводородом; X - вода; XI - дихлорэтан; XII - инертный газ; XIII - продукты десорбции (влага, инертный газ).
1, 14 – насосы; 2 – теплообменники; 3 – многосекционная трубчатая печь; 4 – реактор гидроочистки; 5 – холодильники; 6– ребойлеры; 7
– газосепараторы; 8, 13 – колонны очистки газа от H2S; 9, 10, 18 – компрессоры;11, 17 – стабилизационные колонны; 12 – емкость отгона стабилизации; 15 – реакторы риформинга; 16 – фракционирующий абсорбер; 19 – адсорберы-осушители циркуляционного газа; 20 – печь для нагревания инертного газа; 21 – сборник-водоотделитель; 22 – сепаратор низкого давления; 23 – трубчатая печь.
38
2. КАМЕННЫЙ УГОЛЬ
Химический состав ископаемого угля зависит от его возраста. Самый молодой вид – бурый уголь. Он залегает на глубине порядка 1
км. Воды в нем еще много – около 43%. Содержит большое количество летучих веществ. Хорошо воспламеняется и горит, но тепла дает мало.
Каменный уголь занимает в этой классификации промежуточное положение. Залегает он на глубинах до 3 км. Так как давление верхних пластов больше, то и содержание воды в каменном угле меньше – около 12%, летучих веществ – до 32%, зато углерода содержится до 97 %. Он также легко воспламеняется, но горит лучше. А за счет малого количества влаги дает больше тепла.
Антрацит – более древняя порода. Залегает на глубинах порядка 5 км. В нем больше углерода и практически нет влаги. Антрацит – твердое топливо, плохо воспламеняется, зато удельная теплота сгорания самая высокая – до 7400 ккал/кг.
Таким образом, каменный уголь — это осадочная порода, представляющая собой продукт глубокого разложения остатков растений (древовидных папоротников, хвощей и плаунов, а также первых голосеменных растений).
2.1. Химические свойства каменного угля
Каменный уголь, твёрдое горючее полезное ископаемое растительного происхождения; разновидность углей ископаемых с более высоким содержанием углерода и большей плотностью, чем у бурого угля. Представляет собой плотную породу чёрного, иногда серо-чёрного цвета с блестящей, полуматовой или матовой поверхностью. Удельный вес каменного угля 1,28-1,53 г/см3. механическая прочность – 40-300 кг/см2; содержит 75—97% углерода; 1,5—5,7% водорода; 1,5—15% кислорода; 0,5—4% серы; до 1,5% азота; 45—2% летучих веществ; количество влаги колеблется от 4 до 14%; золы —обычно от 2-4% до 45%. Высшая теплота сгорания, рассчитанная на влажную беззольную массу каменный уголь, не менее 23,8 Мдж/кг (5700 ккал/кг).
39
Большинство залежей каменного угля было образовано в палеозое, преимущественно в каменноугольном периоде, примерно 300-350 миллионов лет тому назад.
Уголь – это остатки растений, погибших многие миллионы лет назад, гниение которых было прервано в результате прекращения доступа воздуха. Поэтому они не смогли отдать в атмосферу отобранный у нее углерод. Доступ воздуха прекращался особенно резко там, где болота и заболоченные леса опускались в результате тектонических подвижек и изменения климатических условий и покрывались сверху другими веществами. При этом растительные останки превращались под воздействием бактерий и грибов (углефицировались) в торф и дальше в бурый уголь, каменный уголь, антрацит и графит.
По составу основного компонента – органического вещества угли подразделяются на три генетические группы: гумолиты, сапропелиты, сапрогумолиты. Преобладают гумолиты, исходным материалом которых явились остатки высших наземных растений. Отложение их произошло преимущественно в болотах, занимавших низменное побережье морей, заливов, лагун, пресноводных бассейнов. Накапливающийся растительный материал в результате биохимического разложения перерабатывался в торф, при этом значительное влияние оказывали обводнённость и химический состав водной среды. Содержание углерода в каменном угле колеблется от 75 до 90 %. Точный состав обуславливается месторасположением и условиями преобразования угля. Минеральные примеси находятся либо в тонкодисперсном состоянии в органической массе, либо в виде тончайших прослоек и линз, а также кристаллов и конкреций. Источником минеральных примесей в ископаемых углях могут быть неорганические части растений – углеобразователей, минеральные новообразования, выпадающие из растворов вод, циркулирующих в торфяниках и т.д.
В результате длительного воздействия повышенных температур и давления бурые угли преобразуются в каменные угли, а последние – в антрациты. Необратимый процесс постепенного изменения химического состава, физических и технологических свойств органического вещества на стадии превращения от бурых углей до антрацитов носит название метаморфизма углей.
40
Наиболее крупные по объему добычи месторождения каменного угля в мире это Тунгусский, Кузнецкий, Печорский бассейны – в Российской Федерации; Карагандинский – в Казахстане; Аппалачский и Пенсильванский бассейны – в США; Рурский – в Германии; Большой Хуанхэ – в Китае; Южно-Уельский – в Англии; Валансьен – во Франции и др.
Каменный уголь считается пригодным для технологического использования если после сгорания зола составляет 30% или менее.
Основные направления промышленного использования угля: получение металлургического кокса, сжигание в энергетических целях, получение синтетического, жидкого и газообразного высококалорийного топлива, ароматических продуктов путём гидрогенизации. Значительно потребление углей для получения высокоуглеродистых углеграфитовых конструкционных материалов, горного воска, пластических масс.
2.2. Коксование каменных углей.
Коксование — промышленный метод переработки угля путем нагревания до 950-1050 0С без доступа воздуха. Основными коксохимическими продуктами являются: кокс, коксовый газ, продукты переработки сырого бензола, каменноугольной смолы, аммиачная вода, содержащая аммиак и азотистые основания.
Получение кокса осуществляется на коксохимических заводах. Каменный уголь подвергается сухой перегонке (коксованию) путём нагревания в специальных коксовых печах. При этом получается кокс – твердое пористое вещество. Кроме кокса при сухой перегонке каменного угля образуются также летучие продукты, при охлаждении которых до 2575 0С образуется каменноугольная смола, аммиачная вода и газообразные продукты. Каменноугольная смола подвергается фракционной перегонке, в результате чего получают несколько фракций:
легкое масло (температура кипения до 170 оС) в нем содержится ароматические углеводороды (бензол, толуол, кислоты и др. вещества;
среднее масло (температура кипения 170-230 оС). Это фенолы, нафталин;
41
тяжелое масло (температура кипения 230-270 оС). Это нафталин и его гомологи
антраценовое масло – антрацен, фенатрен и др.
В состав газообразных продуктов (коксового газа) входят бензол, толуол, ксилолы, фенол, аммиак и другие вещества. Из коксового газа после очистки от аммиака, сероводорода и цианистых соединений извлекают сырой бензол, из которого выделяют отдельные углеводороды и ряд других ценных веществ.
Из коксового газа углеводороды извлекают промывкой в скрубберах жидкими поглотительными маслами. После отгонки от масла, разгонки из фракции, очистки и повторной ректификации получают чистые товарные продукты, как-то: бензол, толуол, ксилолы и др. Из непредельных соединений, содержащихся в сыром бензоле, получают кумароновые смолы, использующиеся для производства лаков, красок, линолеума и в резиновой промышленности. Перспективным сырьем является также циклопентадиен, который также получают из каменного угля.
Каменный уголь – сырье для получения нафталина и других индивидуальных ароматических углеводородов. Важнейшими продуктами переработки являются пиридиновые основания и фенолы.
Коксовый газ, выходящий из печи, содержит пары летучих органических соединений, воды, аммиака. Дальнейшая переработка газа состоит в конденсации мало летучих веществ и улавливании NH3, пиридиновых оснований и не сконденсировавшихся соединений.
Ароматические соединения, образовавшиеся при коксовании, находятся в каменноугольной смоле и в сыром бензоле. Выход каменноугольной смолы составляет 32-34 кг, а сырого бензола – 10-11 кг на 1 т сухого угля. Выделение и очистка ароматических соединений проводятся на широких или более узких фракциях, полученных при ректификации продуктов. В случае сырого бензола и смолы коксования одной из стадий является выделение фенолов путем обработки фракций водным раствором щелочи, а из щелочного раствора фенолы регенерируют при помощи диоксида углерода:
ArOH + NaOH → ArONa + H2O;
2ArONa + H2O + CO2 → 2ArOH + Na2CO3.
42