
ИХТ / ХТОСА / Технология энергоемких материалов(Юдин) / Еще некоторые материалы / УВ из нефти и кокса
.pdf
циклов работы и регенерации получили название цикличных. Регенерация заключается в выжигании кокса и смолистых отложений с поверхности катализатора воздухом при 540 - 680 °С. Для предохранения катализатора от местных перегревов воздух разбавляют инертными газами. Однако число циклов регенерации не беспредельно.
Свойство катализатора сохранять активность во время эксплуатации называется стабильностью активности. С течением времени вследствие постепенного уменьшения удельной активной поверхности катализатора и изменения его пористой структуры индекс активности катализатора падает. Это происходит в результате механического истирания частиц катализатора, спекания его и постепенного отравления активных центров металлами, содержащимися в сырье в виде сложных металлорганических соединений, а также продуктов коррозии. Частичная замена катализатора проводится периодически или непрерывно.
Изучение строения и свойств алюмосиликатного катализатора показало, что он обладает явно выраженной кислотностью. В наибольшей степени это относится к цеолитсодержащим катализаторам. Смеси безводных оксидов кремния и алюминия мало активны. Следовательно, катализаторами следует считать только гидратированные алюмосиликаты. Отметим, что вода удерживается в катализаторе даже при нагревании его до 700 °С. Носителем активности поверхностного слоя катализатора считается соединение (HAlSiО4)x, которое может диссоциировать:
(HAlO4)x (AlO4)x- + H+
Таким образом, катализатор способен к водородному обмену, в этом и состоит его активность.
Карбокатионы образуются при взаимодействии протона
катализатора с олефинами: |
|
|
|
|
|
|
||||||||||||
R-СН=СН2 + Н+ |
→ R-СН+-СН3 |
|
|
|
|
|
|
|||||||||||
Далее карбокатионы претерпевают следующие превращения: |
||||||||||||||||||
1. Перегруппировка атомов в молекуле с перемещением водорода |
||||||||||||||||||
или метильных групп, т. е., скелетная изомеризация: |
|
|
|
|
|
|||||||||||||
+ |
|
|
|
|
+ |
|
+ |
|
|
|||||||||
R |
|
CH |
|
CH2 |
|
CH3 |
R |
|
|
CH |
|
CH2 |
R |
|
C |
|
CH3 |
|
|
|
|
|
|
|
|
||||||||||||
|
|
|
|
|
|
|
|
|
||||||||||
|
|
|
|
|
|
|
|
|
CH3 |
|
|
CH3 |
23

2. Взаимодействие с нейтральными молекулами с образованием новых ионов карбония и новых молекул как предельных, так и непредельных:
+ |
|
|
|
|
|
|
+ |
|
|
|
|
|
|
|
|
|
|
||||
|
|
|
|
|
C4H10 |
C4H9 |
|
R |
|
|
CH2 |
|
CH3 |
||||||||
R |
|
|
CH |
|
|
CH3 |
+ |
+ |
|
|
|
||||||||||
|
|
|
|
|
|
|
|||||||||||||||
+ |
|
|
|
|
|
|
+ |
|
|
|
|
|
|
|
|
|
|
||||
R |
|
CH |
|
CH3 |
+ |
C4H8 |
C H |
9 |
+ |
R |
|
CH |
|
CH |
3 |
||||||
|
|
|
|
|
|||||||||||||||||
|
|
|
|
|
|
|
|
|
|
|
4 |
|
|
|
|
|
|
|
|
||
3. Распад карбокатиона по β-связи, считая от заряженного атома |
|||||||||||||||||||||
углерода: |
|
|
|
|
|
|
|
|
|
|
|
|
|
||||||||
СН3-СН+-СН2-R → CН3СН→СН2 |
+ R+ |
|
|
|
|
|
|
|
|
||||||||||||
Ионно-каталитический механизм приводит к сравнительно малой |
|||||||||||||||||||||
доле углеводородов С1 и С2 |
в продуктах каталитического крекинга, так как |
соотвествующие карбокатионы малоустойчивы и рекомбинируют. Рекомбинация карбокатионов может происходить также и с участием
аниона катализатора – алюмосиликата:
R-CH+-СН3 + А- → R-CH=CH2 + НА
Катализатор в итоге регенерируется, и процесс может начинаться снова, если поверхность катализатора еще сохраняет активность.
По убыванию реакционной способности в процессе каталитического крекинга углеводороды различных классов можно расположить с следующем порядке:
Олефины > ароматические углеводороды с большим количеством боковых цепей > нафтены > парафины > незамещённые арены.
Характерная черта каталитического крекинга - развитие процессов перераспределения водорода. В общем виде этот процесс заключается в том, что молекулы, адсорбированные на катализаторе, склонны терять водород, т. е. дегидрироваться. Это приводит к увеличению ненасыщенности и, как следствие, к более прочной адсорбции на катализаторе. В итоге вновь образовавшиеся непредельные углеводороды начинают полимеризоваться и превращаться в конечный продукт процесса - кокс, который необратимо откладывается на катализаторе. Постепенно все активные центры закрываются коксом, и катализатор необходимо регенерировать.
Остановимся кратко на поведении при каталитическом крекинге углеводородов различных гомологических рядов.
24
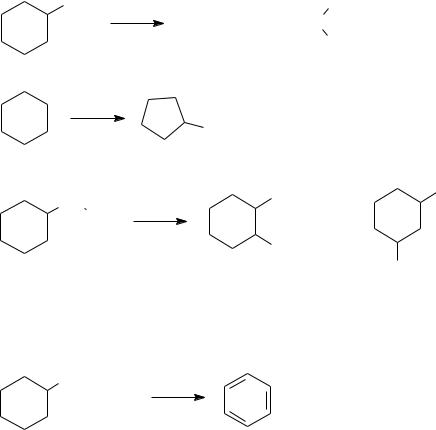
Алканы. Так же как и при термическом крекинге, алканы распадаются на алкен и алкан меньшей молекулярной массы. Распад происходит в нескольких местах углеродной цепи, но не на самом её конце. Выходы метана, этана и этилена незначительны. В газе скапливаются углеводороды С3—С4. Скорость распада в десятки раз больше, чем при термическом крекинге.
Алкены. Скорость распада алкенов при каталитическом крекинге в тысячи раз больше, чем при термическом крекинге. Помимо распада алкены вступают в реакции полимеризации - деполимеризации, перераспределения водорода, изомеризации, циклизации.
Особенно разнообразны реакции изомеризации. Здесь имеют место структурная перегруппировка, перемещение двойной связи вдоль цепи, возможна и цис-, транс-изомерия.
Нафтены. Реакции, характерные для крекинга циклоалканов - деалкилирование, дегидрирование, распад кольца, - ускоряются в присутствии катализатора в 500 - 4000 раз. В отличие от термического крекинга, кроме того, заметно развиты перечисленные ниже реакции:
распад кольца с образованием изоалкенов
CH3 |
|
|
CH3 |
|||
CH3 |
|
CH2 |
|
|
|
CH |
|
|
|
||||
|
|
|
||||
|
|
|
||||
|
|
|
|
|
|
CH3 |
изомеризация циклов
|
|
CH3 |
|
перераспределение боковых цепей |
|
||
CH2 |
|
CH3 |
CH3 |
CH3 |
|
||
|
|
+ |
|
|
|
CH3 |
|
|
|
|
CH3 |
Дегидрирование и деалкилирование циклоалканов протекает с перераспределением водорода. В результате в продуктах крекинга накапливаются арены и алканы. Например:
CH2CH2CH3
+ C3H8 + 2H2
25
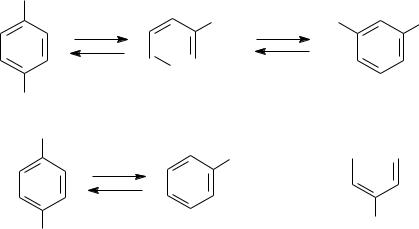
Бициклические циклоалканы в результате дециклизации, дегидрирования, деалкилирования и изомеризации дают начало моноциклическим аренам, циклогексанам, циклопентанам и алканам.
Для всех реакций распада циклоалканов, так же как и для углеводородов с открытой цепью, характерно образование осколков не ниже С3.
Арены. Скорость и направление превращений аренов при каталитическом крекинге в большой мере зависит от строения и молекулярной массы крекируемого углеводорода.
Гомологи бензола преимущественно полностью теряют боковые цепи, что приводит к накоплению бензола. Труднее всего крекируется толуол. По мере увеличения длины боковой цепи и ее разветвления глубина деалкилирования резко возрастает.
Полиметилированные гомологи бензола легко изомеризуются с перераспределением метильных групп. Так, при крекинге п-ксилола в, продуктах реакции обнаружены толуол, триметилбензол, м- и о-ксилолы:
CH3
CH3 |
CH3 |
CH3 |
CH3
CH3
CH3
CH3 CH3 CH3
2 |
+ |
CH3
CH3
В данном случае под каталитическим воздействием алюмосиликата происходят как миграция метильных групп по бензольному кольцу, так и их диспропорционирование. Все эти реакции обратимы.
Конденсированные полициклические углеводороды очень легко адсорбируются на катализаторе и крекируются на нем до кокса. Бензол практически в реакции не вступает и поэтому накапливайся в крекингбензине.
Особенности механизма каталитического крекинга в сравнении с термическим крекингом резко сказываются на составе и свойствах газа и
26
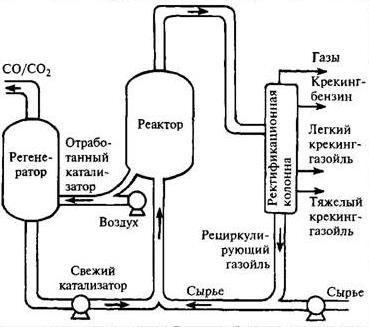
бензина. В газе меньше низкомолекулярных соединений, но гораздо больше изобутана. Бензины обогащаются изоалканами и аренами.
Углеводородные газы каталитического крекинга содержат не менее 75 - 80 % смеси пропан-пропиленов, бутан-бутиленов и пентан-амиленов. Содержание изомерных соединений достигает 25 - 40 %, Это делает газы каталитического крекинга ценным сырьем для нефтехимических процессов.
1.3.4.2. Технологическое оформление каталитического крекинга
Ключевым участком установки является реакторно-регенераторный блок. В состав блока входит печь нагрева сырья, реактор, в котором непосредственно происходят реакции крекинга, и регенератор катализатора. Назначение регенератора - выжиг кокса, образующегося в ходе крекинга и осаждающегося на поверхности катализатора. Реактор, регенератор и узел ввода сырья связаны трубопроводами (линиями пневмотранспорта), по которым циркулирует катализатор.
Наиболее удачная, хотя и не новая, отечественная технология используется на установках мощностью 2 млн. тонн в Уфе, Омске, Москве. Схема реакторно-регенераторного блока представлена на рисунке 5.
Рис.5. Схема реакторно-регенераторного блока установки каталитического крекинга
27
Сырьё с температурой 500-520 °С в смеси с пылевидным катализатором движется по лифт-реактору вверх в течение 2-4 секунд и подвергается крекингу. Продукты крекинга поступают в сепаратор, расположенный сверху лифт-реактора, где завершаются химические реакции и происходит отделение катализатора, который отводится из нижней части сепаратора и самотёком поступает в регенератор, в котором при температуре 700 °С осуществляется выжиг кокса. После этого восстановленный катализатор возвращается на узел ввода сырья. Давление в реакторно-регенераторном блоке близко к атмосферному. Общая высота реакторно-регенераторного блока составляет от 30 до 55 м, диаметры сепаратора и регенератора - 8 и 11 м соответственно для установки мощностью 2,0 млн тонн. Продукты крекинга уходят с верха сепаратора, охлаждаются и поступают на ректификацию.Каталитический крекинг может входить в состав комбинированных установок, включающих предварительную гидроочистку или легкий гидрокрекинг сырья, очистку и фракционирование газов.
1.3.5. Каталитический риформинг
Каталитический риформинг предназначен для повышения октанового числа прямогонных бензиновых фракций путём химического превращения углеводородов, входящих в их состав, до 92-100 пунктов. Процесс ведётся в присутствии алюмо-платино-рениевого катализатора. Повышение октанового числа происходит за счёт увеличения доли ароматических углеводородов. Научные основы процесса разработаны нашим соотечественником - выдающимся русским химиком Н. Д. Зелинским в начале ХХ века. Выход высокооктанового компонента составляет 85-90% на исходное сырьё. В качестве побочного продукта образуется водород, который используется на других установках НПЗ. Мощность установок риформинга составляет от 300 до 1000 тыс. тонн и более в год по сырью.
Оптимальным сырьём является тяжёлая бензиновая фракция с интервалами кипения 85-180 °С. Сырьё подвергается предварительной
28
гидроочистке - удалению сернистых и азотистых соединений, даже в незначительных количествах необратимо отравляющих катализатор риформинга.
Установки риформинга существуют 2-х основных типов - с периодической и непрерывной регенерацией катализатора - восстановлением его первоначальной активности, которая снижается в процессе эксплуатации. В России для повышения октанового числа в основном применяются установки с периодической регенерацией, но в 2000-х гг. в Кстово и Ярославле введены установки и с непрерывной регенерацией, которые эффективнее технологически (возможно получения компонента с октановым числом 98-100), однако, стоимость их строительства выше.
Процесс осуществляется при температуре 500-530 °С и давлении 1,8- 3,5 МПа (0,2-0,3 МПа на установках с непрерывной регенерацией). Основные реакции риформинга поглощают существенные количества тепла, поэтому процесс ведется последовательно в 3-4 отдельных реакторах, объёмом от 40 до 140 м3, перед каждым из которых продукты подвергаются нагреву в трубчатых печах. Выходящая из последнего реактора смесь отделяется от водорода, углеводородных газов и стабилизируется. Полученный продукт - стабильный риформат охлаждается и выводится с установки. При регенерации осуществляется выжиг образующегося в ходе эксплуатации катализатора кокса с поверхности катализатора с последующим восстановлением водородом и ряд других технологических операций. На установках с непрерывной регенерацией катализатор движется по реакторам, расположенным друг над другом, затем подаётся на блок регенерации, после чего возвращается в процесс.
Каталитический риформинг на некоторых НПЗ используется также в целях производства ароматических углеводородов - сырья для нефтехимической промышленности и органического синтеза. Продукты, полученные в результате риформинга узких бензиновых фракций, подвергаются разгонке с получением бензола, толуола и смеси ксилолов (сольвента).
29
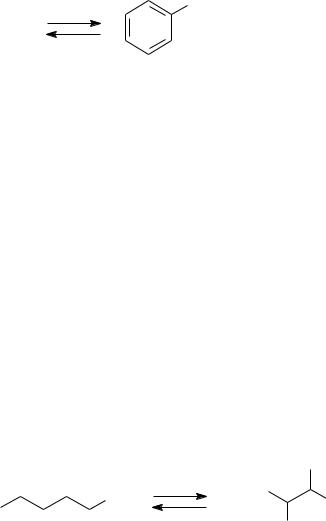
1.3.5.1. Основные процессы, протекающие при риформинге.
При риформинге алканы подвергаются изомеризации, дегидроциклизации и гидрокрекингу.
Изомеризация алканов протекает по карбкатионному механизму с образованием малоразветвленных изомеров, наиболее термодинамически стабильных в условиях риформинга. Скорость изомеризации возрастает с увеличением молекулярной массы алкана.
Дегидроциклизация — одна из важнейших реакций риформинга, заключающаяся в превращении алканов в арены:
R
CnH n |
+2 |
+ |
4H2 |
2 |
|
|
Дегидроциклизация протекает с поглощением теплоты (около 250 кДж/моль), поэтому константа равновесия реакции возрастает с повышением температуры. Давление сдвигает равновесие реакции влево, т. е. в сторону гидрирования аренов. Однако на практике для уменьшения отложений кокса на катализаторе процесс проводят под повышенным давлением водорода. При температуре 500 °С под давлением водорода 1,5— 1,7 МПа равновесная степень конверсии н-гептана в толуол составляет 95 %. Дегидроциклизация парафинов является практически необратимой, но протекает медленнее и менее глубоко и селективно, чем дегидрогенизация нафтенов. Кроме того, она сопровождается гидрокрекингом (температура промышленного риформинга >500 °С) парафинов. При этом имеет место изомеризация парафиновых углеводородов С4-С8 с образованием высокооктановых изомеров. Например, нормальный гексан (Октановое Число 25) изомеризуется в 2,3- диметилбутан (ОЧ 95):
|
|
CH3 |
CH3 |
CH3 |
CH3 |
CH3 |
|
|
|
|
|
|
|
CH3 |
Однако ее значение в процессе риформинга невелико, так как для этой реакции благоприятны более низкие (350-380°С) температуры.
30
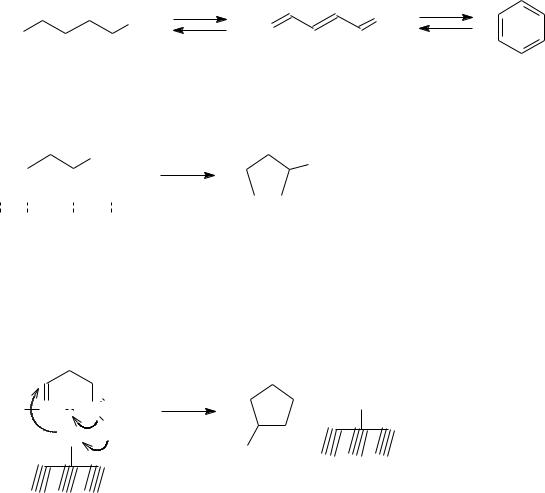
Механизм ароматизации алканов окончательно не ясен. Возможны следующие пути:
1) Дегидрирование алканов на платине до триена с последующей циклизацией на платине или оксиде алюминия:
CH3 |
CH3 |
|
CH2 |
|
|
CH2 |
|
|
-3H |
2 |
-H2 |
|
|
|
2) С5-циклизация на платине через циклический переходный комплекс:
|
|
|
|
|
CH3 |
|
CH3 |
|
||
|
|
|
|
|
|
|
|
+ |
H2 |
|
H |
|
CH2 |
CH2 |
|
H |
|||||
|
|
|
|
|
||||||
Pt |
Pt |
Pt |
Pt |
|
|
|
3) Дегидрирование алканов в алкены на платине и циклизация алкенов на оксиде алюминия также с образованием пятичленного цикла. Реакция протекает по согласованному механизму, включающему протонирование двойной связи кислотным центром и одновременный отрыв протона от атома углерода в цепи:
|
H |
|
H+ |
CH3 CH CH |
|
+ |
|
|
|
||
|
|
|
|
H+ |
H |
|
|
CH3 |
|
A- |
|
|
|
||
A- |
|
|
|
Образовавшиеся пятичленные циклы изомеризуются на кислотных центрах в шестичленные и далее дегидрируются на металле в арены.
Экспериментальные данные свидетельствуют, что ароматизация идет по всем рассмотренным направлениям.
Если исходный алкан содержит менее шести атомов углерода в основной цепи, то ароматизации предшествует изомеризация алкана с удлинением основной цепи. Скорость ароматизации возрастает с увеличением длины цепи алкана. Алканы, содержащие десять и более атомов углерода, образуют арены с конденсированными кольцами. Арены с достаточно длинными боковыми цепями могут замыкать дополнительные циклы.
31
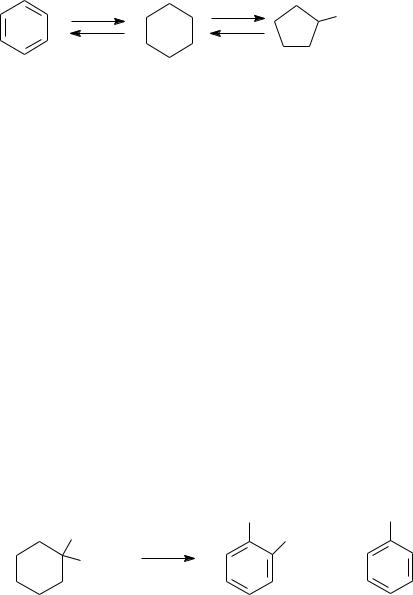
В результате дегидроциклизации алканов образуются гомологи бензола и нафталина с максимальным содержанием метильных заместителей в ядре, которое допускается строением исходного алкана.
Превращения циклоалканов.
В условиях риформинга циклоалканы также подвергаются изомеризации, дегидрированию до аренов и гидрокрекингу.
Шестичленные циклоалканы изомеризуются в пятичленные по карбкатионному механизму:
Pt |
K |
CH3 |
|
|
Хотя равновесие изомеризации, как и.при каталитическом крекинге, почти нацело смещено вправо, реакция обратима, так как шестичленные циклоалканы в условиях риформинга дегидрируются в арены, причем равновесие сильно сдвинуто в сторону аренов.
Избирательность превращения циклогексана в метилциклопентан и бензол в конечном счете определяется соотношением скоростей реакций и зависит от активности компонентов катализатора. Изомеризация протекает на кислотных центрах по карбкатионному механизму, поэтому при высокой кислотности катализатора будет увеличиваться выход метилциклопентана. Дегидрирование происходит на металлическом компоненте катализатора, и с увеличением активности металла будет возрастать скорость образования бензола.
Реакция эндотермична, поэтому с повышением температуры равновесный выход аренов увеличивается. Скорость дегидрирования гомологов циклогексана выше, чем циклогексана. Гем-замещенные циклогексаны ароматизируются с отщеплением метильной группы или с ее миграцией:
|
|
CH3 |
|
CH3 |
|
CH3 |
|
CH3 |
|
2 |
CH |
3 |
+ |
+ CH4 |
|
|
|
32