
ИХТ / ХТОСА / Технология энергоемких материалов(Юдин) / Еще некоторые материалы / УВ из нефти и кокса
.pdfЭтот коксохимический метод был первым промышленным методом получения фенола, крезолов и ксиленолов.
Следующим этапом является очистка фракций от олефинов. Так как в коксохимических продуктах содержание олефинов невелико, применяется сернокислотный способ, состоящий в обработке фракций 9093 %-й H2SO4. При этом часть олефинов дает кислые алкилсульфаты и переходит в неорганический слой, а остальные полимеризуются. Заключительной стадией процесса очистки является ректификация, целью которой является получение товарных продуктов.
Для выделения ароматических углеводородов с конденсированными циклами (нафталин, антрацен, фенантрен) используется метод кристаллизации. Из антраценовых фракций каменноугольной смолы (270330 оС) сплавлением с КОН и последующим гидролизом выделяют ценное для органического синтеза вещество – карбазол.
Нафталин до сих пор получают из нафталиновой фракции каменноугольной смолы (210-230 оС). Ее кристаллизуют в охлаждаемых водой барабанных кристаллизаторах. Сырой продукт отжимают от масел при нагревании на гидравлических прессах, получая так называемый прессованный нафталин (температура кристаллизации не менее 78 оС, содержание нафталина 96-98 %). После обработки H2SO4 и перегонки получают чистый кристаллический нафталин.
Путем переработки из каменного угля в общей сложности можно получить более 400 различных продуктов, стоимость которых, по сравнению, со стоимостью самого угля, возрастает в 20-25 раз, а побочные продукты, получаемые на коксохимических заводах, превосходят стоимость самого кокса.
Выход химических продуктов коксования зависит как от состава исходной шихты, так и от условий ее коксования. Так, газовые угли дают больший выход смолы и бензола по сравнению с углями коксовыми или отощенными.
На состав химических продуктов значительное влияние оказывают температура коксования и время пребывания парогазовой смеси в камере печей.
43
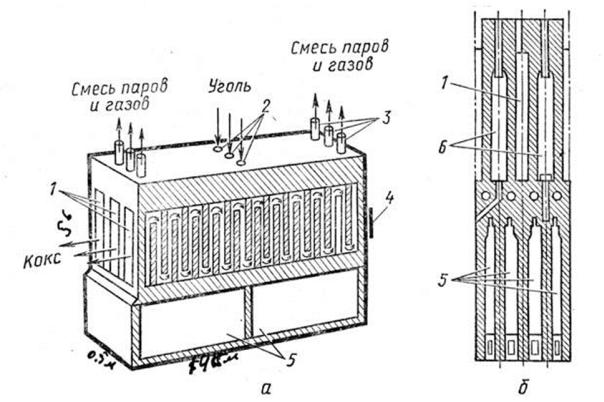
2.2.1. Технология коксования и выделение продуктов коксования.
Коксуют уголь в аппаратах периодического действия – коксовых печах.
Рис. 7. Коксовая печь (коксовая батарея). а – разрез по обогревательному простенку; б – поперечный разрез камеры: 1 - камеры; 2 - загрузочные люки; 3 - стояки для отвода газа; 4 – коксовыталкиватель; 5 - регенераторы; 6 - обогревательный простенок.
Коксовая печь — реактор периодического действия, поэтому температура угольной шихты в ней изменяется во времени. Непосредственно после загрузки шихты в холодную шихту поступает в единицу времени большее количество теплоты и уголь у стенок камеры начинает коксоваться, в то время как вследствие низкой теплопроводности шихты средние слои остаются холодными. По мере прогрева шихты ее температура возрастает при одновременном повышении температуры по сечению камеры.
Коксовая печь состоит из: - камеры коксования;
44
-обогревательных простенков для сжигания и циркуляции отопительного газа;
-регенераторов для утилизации теплоты отходящих дымовых газов. Камера коксовой печи является реактором косвенного нагрева, где
теплота передаётся к коксуемому углю от теплоносителя (горючего газа) через стенку. Камера имеет прямоугольное сечение и образована двумя обогревательными простенками, подом и сводом, облицованным динасовыми огнеупорами.
С торцов камера закрывается дверями, которые снимаются по окончании коксования для выдачи готового кокса из камеры с помощью коксовыталкивателя.
В своде камеры находятся: три отверстия для загрузки угля, закрываемые крышками; два отверстия для отвода летучих продуктов коксования – прямого коксового газа, который через газоотвод поступают в газосборник, откуда направляются в цех улавливания. В кирпичных простенках между соседними камерами устроены вертикальные отопительные каналы или вертикалы (обычно по 27 штук в каждом простенке) в которых сжигается газообразное топливо. После обогрева камер горячие газы удаляются из печи через регенераторы – камеры, заполненные кирпичной насадкой, и нагревают их. Аккумулированная в нагревателях теплота используется для предварительного подогрева воздуха и отопительного газа с целью достижения необходимой температуры ~ 1400-1500 ºС в вертикалах и уменьшения расхода топлива. Регенераторы работают попарно по принципу противотока. Через один пропускают нагреваемый воздух, а через другой в противоположном направлении - отходящие топочные газы. Газообразным топливом для обогрева коксовых печей служит обратный коксовый газ, доменный газ, или их смесь. Коксовые печи компонуют в батареи, а батареи - в блоки. Одна коксовая батарея включает 61-79 параллельно работающих камер.
Батарея обслуживается комплектом механизмов: вагоном для загрузки угля; коксовыталкивателем; машиной для съемки дверей коксовых камер; коксотушительным вагоном с электровозом.
После выгрузки предыдущей партии кокса в сильно нагретую камеру загружают угольную шихту из специального загрузочного вагона,
45
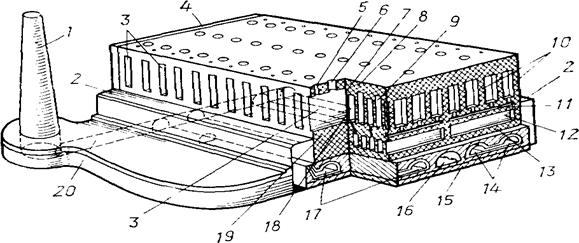
передвигающегося по рельсовому пути, проложенному по верху батареи. Продолжительность коксования составляет 12-14 часов.
После окончания коксования специальными механизмами: снимают переднюю и заднюю дверцы камеры и с помощью коксовыталкивателя готовый кокс («коксовый пирог») выгружают в вагон. Вагон отвозит кокс под тушильную башню, где он орошается водой, охлаждается и растрескивается на мелкие кусочки. При мокром тушении кокса безвозвратно теряется около 50%тепловой энергии, затраченной на коксование. В настоящее время всё более широко используется метод сухого тушения кокса с помощью циркулирующего инертного газа азота.
Высокотемпературное коксование углей является наиболее распространенным в настоящее время процессом термической переработки угля. Суммарная производительность коксохимических заводов мира превышает 350 млн. т кокса в год, а перерабатывается ежегодно около 500 млн. т обогащенных коксующихся углей.
Схема коксохимического производства в достаточной мере унифицирована во всем мире. Как правило, коксование угля осуществляют в горизонтальных коксовых камерах периодического действия с внешним обогревом, с улавливанием химических продуктов. Группы коксовых печей объединяют в коксовые батареи, работающие в едином технологическом режиме. Батареи имеют общий фундамент — устройства для подвода отопительных газов и воздуха, отвода продуктов горения и коксования (рис. 8).
Рис. 8 . Коксовая батарея. 1—дымовая труба; 2—рабочая площадка; 3—камеры коксования; 4—контрфорс; 5— люк для отвода газа: 6—загрузочный люк; 7 — свод камеры; 8
—перекрытие печей; 9— уровень обогрева; 10—вертикалы; 11—газоподводящий канал
46
(корнюр); 12—регенератор; 13—подовый канал; 14, 16 — борова: 15—плита: 17— соединительный канал (косой ход); 18—отопительный простенок: 19—под камеры; 20—общий боров
Уголь загружается, как правило, через люки на верху печи, а кокс выдается специальными механизмами в горизонтальном направлении. Отдельная коксовая печь является устройством периодического действия (продолжительность коксования изменяется в различных конструкциях от 12 до 24 ч). Однако коксовая батарея, объединяющая большое число коксовых печей, представляет собой устройство, обеспечивающее непрерывное получение кокса и химических продуктов.
Каждая камера коксовой батареи работает периодически, но вся батарея – в целом – непрерывно: одни камеры загружаются, другие – находятся в рабочем режиме, третьи выдают кокс.
Система обогрева коксовых печей позволяет осуществлять равномерный прогрев кокса по высоте и длине камеры, а система теплообмена и переключения потоков газов в системе обогрева — достаточно экономное расходование тепла.
Полезный объем камер несколько меньше полного объема. так как угольная шихта загружается в коксовую печь не на всю высоту, а остается свободный проход для парогазовых продуктов коксования. Камеры коксования современных коксовых печей имеют следующие размеры: ширина 350—560 мм, полная длина 11000—17000 мм, высота 3000—7500 мм при полезном объеме 14—52 м3. Средний срок службы коксовых батарей 20—25 лет при максимуме более 40 лет. Производительность коксовой батареи от 200 до 1200 тыс. т кокса в год.
Химические реакции, идущие при коксовании, эндотермичны, поэтому требуют непрерывного подвода теплоты и высокой температуры теплоносителя.
Процесс коксования начинается в слоях шихты, соприкасающихся с нагретыми до высокой температуры простенками и подом. Затем он медленно распространяется в направлении к середине толщи шихты, причём возникающий в результате выделения смолы при ~ 350ºС вязкий пластический слой перемещается в том же направлении. Соответственно этому и состав слоев (начиная от стенок) меняется в последовательности:
47
кокс — полукокс — уголь в пластическом состоянии — сухой уголь — сырой уголь.
При нагревании угля до 200 °С вначале происходит испарение влаги и удаление растворенных в угле газов, состоящих в основном из метана и азота. За счет отщепления гидроксильных и карбоксильных групп в газовой фазе появляется некоторое количество оксида и диоксида углерода, а также пары пирогенной воды. При последующем нагревании до 300 °С разложение угольного вещества несколько интенсифицируется (о чем свидетельствует образование небольших количеств водорода и метана), однако существенной потери массы еще не наблюдается.
Температурный диапазон 350—450 °С характеризуется изменением агрегатного состояния угля: из сыпучего он переходит в пластическое (тестоподобное) за счет того, что начинается выделение смолы. В результате термической деструкции органической массы спекающихся углей вначале образуется жидкая пленка на поверхности угольных частичек, которые как бы оплавляются. Затем происходит размягчение зерен, появляется пластический слой, толщина которого определяется свойствами угля и равна 15—30 мм. Пластическая масса представляет собой сложную гетерогенную систему, состоящую из газообразной, жидкой и твердой фаз. Вначале она имеет высокую вязкость и достаточно хорошую газопроницаемость. По мере повышения температуры возрастает количество жидкой фазы, уменьшается вязкость пластической массы, а свободные промежутки между твердыми частицами сокращаются, в результате чего увеличивается сопротивление эвакуации газообразных продуктов. Вследствие этого возникает внутреннее давление, приводящее к вспучиванию среды. При дальнейшем повышении температуры до 500— 550 °С происходит резкое уменьшение массы угля и бурное выделение газа и смолы. При этом одновременно протекают вторичные реакции термического разложения компонентов смолы, за счет которых конечные продукты обогащаются наиболее термически стабильными соединениями (водородом, метаном, ароматическими углеводородами). В результате реакций полимеризации и поликонденсации продуктов разложения происходит накопление твердой фазы в пластической массе, вновь возрастают ее вязкость и газопроницаемость, и начинает формироваться жесткая структура полукокса. Постепенно жидкая фаза исчезает, а твердый
48
остаток представляет собой полукокс. При последующем увеличении температуры до 900—1000°С протекают термохимические превращения в твердой фазе, соответствующие переходу полукоксовой структуры в коксовую. Твердый остаток уплотняется, увеличивается его прочность и уменьшается объем — происходит усадка. Благодаря этому «коксовый пирог» отделяется от стенок камеры, что облегчает его выгрузку. Вследствие небольшой теплопроводности угольной шихты [от 0,75 до 0,8 Дж/(м·ч·К) или ~2·l0-4 Вт/(м·К)] температура в центре камеры заметно ниже, чем у стенок. Она выравнивается лишь через 13—14 ч. В соответствии с динамикой прогрева шихты в ней протекают описанные выше процессы. К концу коксования оба пластических слоя, перемещающиеся от стенок, соединяются в центре камеры, образуя шов, по которому «коксовый пирог» при выгрузке из печи распадается на две примерно равные части. Большинство реакций вторичного превращения паров смолы происходит в подсводовом пространстве, над поверхностью раскаленного кокса. Оптимальные условия образования ценных побочных продуктов, получаемых при коксовании: температура 700—720°С, время пребывания паров смолы в подсводовом пространстве ~40 с.
2.2.2. Состав и переработка коксового газа.
Прямой коксовый газ, отсасываемый газодувками из камер коксования содержит в г/м3 (при 0ºС и 0,1 МПа):
-пары каменноугольной смолы (КУС) – 110-130;
-пары бензольных углеводородов 35-42;
-нафталин и гомологи – 10;
-аммиак 8-14;
-сероводород и другие сернистые соединения – 6-25;
-пары воды – 250-450.
Кроме того, в газе содержится: водород, метан, углеводороды этиленового ряда, оксиды углерода, азот.
Выход прямого коксового газа составляет 340-350 м3/т сухой шихты. Основные компоненты из прямого коксового газа извлекают в виде
сырого бензола и каменноугольной смолы. Химические продукты коксования выделяются постадийно по мере охлаждения газа.
49
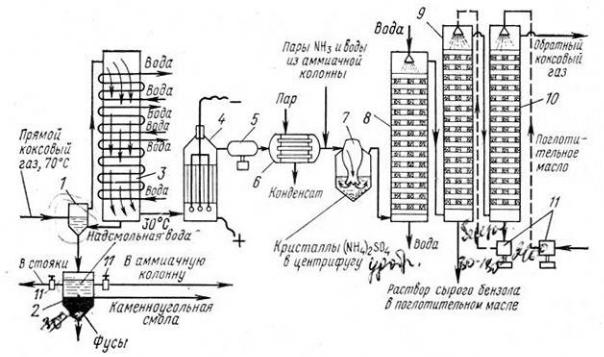
Улавливание химических продуктов коксования основано на гетерогенных процессах конденсации, хемосорбции и физической абсорбции.
Схема переработки прямого коксового газа представлена на рисунке 9.
Рис. 9. Схема улавливания летучих продуктов коксования. 1 – сепаратор; 2 -
отстойник; 3 - водяной холодильник; 4 – мокрый электрофильтр; 5 – газовый насос; 6 – паровой подогреватель; 7 – сатуратор; 8 – холодильник непосредственного действия; 9,10 – поглотительные башни; 11 - насосы.
Охлаждение газа до 70-80 ºС начинается в газосборнике, общем для всех камер коксовой батареи. Газосборник орошается надсмольной водой, циркулирующей в системе. При этом происходит интенсивная конденсация паров смолы и воды. Одновременно от газа отделяются и удаляются твердые частицы – фусы. В результате охлаждения образуется конденсат, содержащий смолу и воду, с частично растворёнными в ней аммиаком и фенолами.
Конденсат отделятся от газа в сепараторах.
Из сепараторов конденсат подают в отстойники-осветлители, где он разделяется на:
-каменноугольную смолу;
-надсмольную (аммиачную) воду;
50
- твёрдый остаток.
На выходе их холодильников газ несёт тонкодисперсные частицы не сконденсировавшейся смолы – смоляной туман, который выделяют из газа с помощью электрофильтров. Аммиак, оставшийся в газе после конденсации паров воды, улавливают, используя хемосорбционный процесс - взаимодействие с серной кислотой. Для этого газ подогревают в теплообменнике и подают в реакторы-сатураторы. В реакторах газ барботирует через 75%-ный раствор серной кислоты с образованием сульфата аммония - азотного удобрения. На эту же стадию подают аммиак, отгоняемый из воды, образующейся при первичном охлаждении коксового газа. Серная кислота одновременно связывает содержащиеся в газе пиридиновые основания в сульфаты, из которых затем в отдельной установке выделяют свободные основания.
Далее газ предварительно охлаждают в полочном холодильнике прямого смешения (холодильник-промыватель) для повышения степени улавливания бензольных углеводородов. При охлаждении от газа отделяется твёрдый нафталин, который уносится с потоком отработанной воды. Сюда же подают смолу, отделяемую на стадии первичного охлаждения газа; смола растворяет нафталин. После отстаивания смолу направляют на переработку, а газ — на извлечение бензольных углеводородов.
Для извлечения сырого бензола охлаждённый газ подаётся в башни с насадкой. Этот процесс осуществляют абсорбционно-десорбционным методом; в качестве поглотителя используют каменноугольное или соляровое масло. Башни орошаются холодным маслом, которое движется противотоком газу, поэтому пары сырого бензола извлекаются из газа практически полностью.
Для отделения сырого бензола его отгоняют в ректификационной колонне.
Далее газ очищают от цианида водорода, обрабатывая его раствором полисульфида натрия (или аммония), в результате образуются соответствующие тиоцианиды. Последним этапом является извлечение сернистых соединений, которые либо разделяются, либо идут на получение свободной серы или серной кислоты.
51
Очищенный коксовый газ, далее используется как топливо, а также в качестве сырья для синтеза аммиака.
Прямой коксовый газ после улавливания из него всех продуктов называют обратным коксовым газом, потому что раньше он полностью возвращался обратно для сжигания в коксовых печах.
2.3. Гидрирование твердого топлива
Гидрированием (гидрогенизацией) твердого топлива называется процесс превращения органической части топлива в жидкие продукты, обогащенные водородом и используемые как жидкое топливо. Проблема гидрирования твердого топлива возникла в связи с возросшим потреблением нефти и необходимостью эффективно использовать низкокалорийные и высокозольные ископаемые угли, представляющие сложности при их сжигании. В промышленном масштабе гидрирование твердого топлива впервые было организовано в 30-х годах XX века в Германии и получило развитие в связи с необходимостью использовать для производства моторных топлив тяжелых смолистых нефтей с высоким содержанием серы. В настоящее время в различных странах работают установки деструктивной гидрогенизации топлив производительностью от
200 до 1600 т/сутки.
Гидрирование твердого топлива представляет собой каталитический процесс, протекающий при температуре 400-600 °С под давлением водорода 10-80 МПа. В этих условиях происходит разрыв ковалентных связей в органической массе топлива и протекают реакции деструкции и деполимеризации высокомолекулярных структур угля:
Cn + nH2 CnH2n
гидрирования образовавшихся алкенов; деструкции высших алканов до алкенов и алканов меньшей
молекулярной массы:
CpH2p+2 CnH2n + CmH2m+2
гидрирования конденсированных ароматических систем с последующим разрывом цикла и деалкилированием:
52