
2828.Экспертиза качества и разрушений
..pdf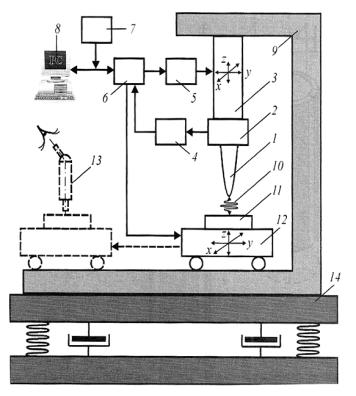
Рис. 3.46. Принципиальная схема сканирующего зондового микроскопа: 1 – зонд; 2 – датчик полезного сигнала; 3 – трехкоординатный пьезосканер; 4 – цепь обратной связи; 5 – высоковольтный усилитель; 6 – контроллер; 7 – программное обеспечение; 8 – компьютер; 9 – рама; 10 – взаимодействие вершины зонда с поверхностью образца; 11 – образец; 12 – координатный столик;
13 – оптический микроскоп; 14 – виброзащитный стол
В сравнении с растровым электронным микроскопом сканирующий зондовый микроскоп обладает рядом преимуществ. Так, в отличие от РЭМ, который дает псевдотрехмерное изображение поверхности образца, СЗМ позволяет получить истинно трехмерный рельеф поверхности. Кроме того, в общем случае сканирующий зондовый микроскоп позволяет получать изображение как проводящей, так и непроводящей поверхности, тогда как для изучения непроводящих объектов с помощью РЭМ необходимо металлизировать поверхность. Для работы с РЭМ необходим вакуум, в то время как большая часть режимов СЗМ предназначена для исследований на воздухе, вакууме и жидкости. В принципе, СЗМ способен дать более высокое разрешение, чем РЭМ. Так, было по-
111
казано, что СЗМ в состоянии обеспечить реальное атомное разрешение в условиях сверхвысокого вакуума при отсутствии вибраций. Сверхвысоковакуумный СЗМ по разрешению сравним с просвечивающим электронным микроскопом.
3.5.2.3. Дефектоскопия
Дефектоскопия – это контроль качества материалов, полуфабрикатов и готовой продукции без их разрушения различными физическими методами с помощью разнообразной приборной техники
В 1922 г. запатентован магнитный метод обнаружения дефектов артиллерийских стволов с помощью магнитного порошка, открытый Уильямом Э. Хоуком во время Первой мировой войны. Первые дефектоскопы, работающие на непрерывном звуке, создали в 1928 г. С.Я. Соколов и в 1931 г. Мюльхойзер. В 1937–1938 гг. появилась первая в мире установка, использующая переменный ток для контроля конструкций железной дороги и колесных пар (компания MAGNAFLUX, США). Эхо-импульсные дефектоскопы (принцип действия и прибор) создали впервые в 1939– 1942 гг. Файрстон в США, Спрулс в Великобритании и Крузе вГермании.
Физическая основа любого метода дефектоскопии связана с тем, что встречающиеся в исследуемом объекте нарушения его сплошности, химической и структурной неоднородности, изменение фазового и структурного состояния вызывают изменение тех ли иных физических величин. Наиболее широкое применение нашли методы визуальной, инфракрасной, ультразвуковой, магнитной, токовихревой, рентгеновской и γ-дефектоскопии.
Дефектоскоп – устройство для обнаружения дефектов в изделиях из различных металлических и неметаллических материалов методами неразрушающего контроля. К регистрируемым дефектам относятся нарушения сплошности или однородности структуры, зоны коррозионного поражения, отклонения химического состава и размеров и др. Область техники и технологии, занимающаяся разработкой и использованием дефектоскопов, называется дефектоскопия. С дефектоскопами функционально связаны и другие виды средств неразрушающего контроля: течеискатели, толщиномеры, твердомеры, структуроскопы, интроскопы и стилоскопы.
Типы дефектоскопов, основанные на различных физических принципах, разнообразны. В промышленности и для исследовательских целей используют:
112
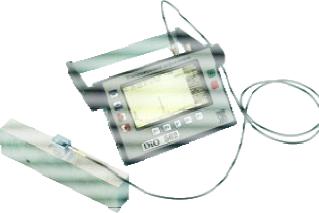
•акустические (ультразвуковые) дефектоскопы:
–импульсные ультразвуковые дефектоскопы;
–импедансные дефектоскопы;
–резонансные дефектоскопы и др.;
•магнитные методы:
–магнитно-порошковые дефектоскопы;
–вихретоковые дефектоскопы;
–феррозондовые дефектоскопы;
•электроискровые дефектоскопы;
•термоэлектрические дефектоскопы;
•радиационные дефектоскопы:
–облучение рентгеновскими лучами;
–облучение нейтронами;
–облучение γ-лучами и др.;
•инфракрасные дефектоскопы;
•радиоволновые дефектоскопы;
•электронно-оптические дефектоскопы;
•капиллярные дефектоскопы и др.
Виды акустических дефектоскопов. В импульсных дефектоскопах
(рис. 3.47) используются эхо-метод, теневой и зеркально-теневой методы контроля.
Рис. 3.47. Ультразвуковой импульсный дефектоскоп DIO-562
Эхо-метод основан на посылке в изделие коротких импульсов ультразвуковых колебаний и регистрации интенсивности и времени прихода эхосигналов, отраженных от дефектов. Для контроля изделия
113
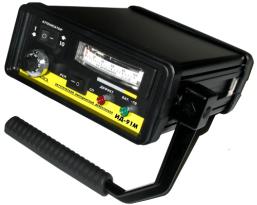
датчик эходефектоскопа сканирует его поверхность. Метод позволяет обнаруживать поверхностные и глубинные дефекты с различной ориентировкой.
При теневом методе ультразвуковые колебания, встретив на своем пути дефект, отражаются в обратном направлении. О наличии дефекта судят по уменьшению энергии ультразвуковых колебаний или по изменению фазы ультразвуковых колебаний, огибающих дефект. Метод широко применяют для контроля сварных швов, рельсов и др.
Импедансные дефектоскопы (рис. 3.48). Принцип работы основан на определении отличия полного механического сопротивления (импеданса) дефектного участка по сравнению с доброкачественным, для чего контролируемая поверхность сканируется с помощью двух пьезоэлементов, один из которых возбуждает колебания в материале, а другой воспринимает колебания.
Рис. 3.48. Акустический импедансный дефектоскоп ИД-91М
Импедансные дефектоскопы предназначены для обнаружения дефектов, расслоений, непроклеев, пористости и нарушения целостности композитных материалов и сотовых структур в авиастроении, космической, автомобильной и других отраслях промышленности.
Резонансный метод основан на определении собственных резонансных частот упругих колебаний (частотой 1–10 МГц) при возбуждении их в изделии. Этим методом измеряют толщину стенок металлических и некоторых неметаллических изделий. При возможности измерения с одной стороны погрешность измерения составляет около 1 %. Кроме того, при помощи резонансной дефектоскопии можно выявлять зоны коррозионного поражения. Вариантом резонансного метода является спектрально-акустическая дефектоскопия.
114
Реверберационный метод основан на анализе времени объемной реверберации – процесса постепенного затухания звука в некотором объеме контролируемого объекта.
Акустико-эмиссионный метод контроля основан на приеме и анализе волн акустической эмиссии, возникающих в изделии при развитии трещин в процессе его нагружения.
Велосиметрический метод эходефектоскопии основан на измерении изменения скорости распространения упругих волн в зоне расположения дефектов в многослойных конструкциях, используется для обнаружения зон нарушения сцепления между слоями металла.
Акустико-топографический метод основан на возбуждении в кон-
тролируемом изделии мощных изгибных колебаний заданной (в первом варианте метода) или непрерывно меняющейся (во втором варианте) частоты с одновременной визуализацией картины колебаний поверхности изделия, например, путем нанесения на эту поверхность тонкодисперсного порошка. При достаточно сильных колебаниях поверхности изделия с заданной частотой частицы порошка из мест, не принадлежащих узлам, постепенно смещаются к узлам колебаний, рисуя картину распределения узловых линий на поверхности – так называемые фигуры Хладни. Для бездефектного изотропного материала эта картина получается четкой и непрерывной. Если же в материале имеется дефект, то в зоне дефекта картина меняется: узловые линии искажаются в месте наличия включений, а также на участках, характеризующихся анизотропией механических свойств, или прерываются при наличии расслоения. Если используется второй вариант метода, то при наличии расслоения находящийся над ним участок верхнего слоя изделия рассматривается как колеблющаяся, закрепленная по краю диафрагма; в момент резонанса, т.е. совпадения частоты возбуждения с собственной частотой этой диафрагмы, амплитуда ее колебаний резко возрастает, и частицы порошка перемещаются к границам дефектной зоны, оконтуривая ее с большой точностью. Работа ведется на частотах 30–200 кГц. Чувствительность метода весьма высока: в многослойном изделии (например, биметаллических или триметаллических листах) с толщиной верхнего листа 0,25 мм обнаруживаются дефекты протяженностью 1–1,5 мм.
Магнитно-порошковые дефектоскопы позволяют контролировать различные по форме детали, сварные швы, внутренние поверхности отверстий путем намагничивания отдельных контролируемых участков или изделия в целом циркулярным или продольным полем, создаваемым
115
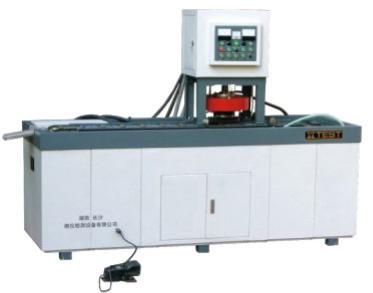
с помощью набора намагничивающих устройств, питаемых импульсным либо постоянным током, или с помощью постоянных магнитов (рис. 3.49). Принцип действия основан на создании поля рассеяния над дефектами контролируемой детали с последующим выявлением их магнитной суспензией. Наибольшая плотность магнитных силовых линий поля рассеяния наблюдается непосредственно над трещиной (или над другой несплошностью) и уменьшается с удалением от нее. Для обнаружения несплошности на поверхность детали наносят магнитный порошок, взвешенный в воздухе (сухим способом) или в жидкости (мокрым способом). На частицу в поле рассеяния будут действовать силы: сила магнитного поля, направленная в область наибольшей плотности магнитных силовых линий, т.е. к месту расположения трещины; тяжести; выталкивающего действия жидкости; трения; силы электростатического
имагнитного взаимодействия, возникающие между частицами.
Вмагнитном поле частицы намагничиваются и соединяются в цепочки. Под действием результирующей силы частицы притягиваются к трещине и накапливаются над ней, образуя скопление порошка. Ширина полоски (валика) из осевшего порошка значительно больше ширины раскрытия трещины. По этому осаждению – индикаторному рисунку – определяют наличие дефектов.
Рис. 3.49. Стационарный магнитный дефектоскоп CDG-2000QB
фирмы XYTEST
116
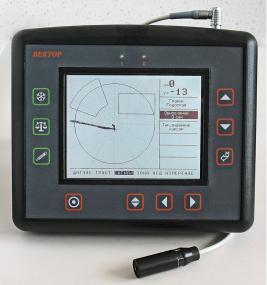
Вихретоковые дефектоскопы (рис. 3.50). Принцип действия осно-
ван на методе вихревых токов, заключающемся в возбуждении вихревых токов в локальной зоне контроля и регистрации изменений электромагнитного поля вихревых токов, обусловленных дефектом и электрофизическими свойствами объекта контроля.
Рис. 3.50. Вихретоковый дефектоскоп «Вектор»
Феррозондовые дефектоскопы используют метод магнитной дефектоскопии, основанный на том, что при движении феррозонда (чувствительного элемента, реагирующего на изменение магнитного поля) вдоль изделия вырабатываются импульсы тока, форма которых зависит от наличия дефектов в изделии. Высокая чувствительность дефектоско- пов-градиентометров позволяет выявлять дефекты с шириной раскрытия в несколько микрометров и глубиной от 0,1 мм. Возможно выявление дефектов под немагнитным покрытием толщиной до 6 мм. Шероховатость контролируемых поверхностей – до Rz = 320 мкм. Дефектоско- пы-градиентометры применяются для контроля литых деталей, проката, сварных соединений.
Принцип действия термоэлектрических дефектоскопов основан на измерении электродвижущей силы (термоЭДС), возникающей в замкнутой цепи при нагреве места контакта двух разнородных материалов. Если один из этих материалов принять за эталон, то при заданной раз-
117
ности температур горячего и холодного контактов величина и знак термоЭДС будут определяться химическим составом второго материала. Этот метод обычно применяют в тех случаях, когда требуется определить марку материала, из которого состоит полуфабрикат или элемент конструкции (в том числе в готовой конструкции).
В радиационных дефектоскопах осуществляется облучение объектов рентгеновскими, α-, β- и γ-лучами, а также нейтронами. Принцип действия основан на различной поглощающей способности. Источники излучений – рентгеновские аппараты, радиоактивные изотопы, линейные ускорители, бетатроны, микротроны. Радиационное изображение дефекта преобразуют в радиографический снимок (радиография), электрический сигнал (радиометрия) или световое изображение на выходном экране радиационно-оптического преобразователя или прибора (радиационная интроскопия, радиоскопия).
Радиационный контроль проводится в целях выявления в сварных соединениях трещин, непроваров, пор, шлаковых, вольфрамовых и окисных включений, прожогов, подрезов, выпуклостей и вогнутостей корня шва.
Инфракрасные дефектоскопы используют инфракрасные (тепловые) лучи для обнаружения непрозрачных для видимого света включений. Так называемое инфракрасное изображение дефекта получают в проходящем, отраженном или собственном излучении исследуемого изделия. Дефектные участки в изделии изменяют тепловой поток. Поток инфракрасного излучения пропускают через изделие и регистрируют его распределение теплочувствительным приемником.
Радиодефектоскопия основана на проникающих свойствах радиоволн сантиметрового и миллиметрового диапазонов (микрорадиоволн), позволяет обнаруживать дефекты главным образом на поверхности изделий обычно из неметаллических материалов. Радиодефектоскопия металлических изделий из-за малой проникающей способности микрорадиоволн ограничена. Этим методом определяют дефекты в стальных листах, прутках, проволоке в процессе их изготовления, а также измеряют их толщину или диаметр, толщину диэлектрических покрытий и т.д. От генератора, работающего в непрерывном или импульсном режиме, микрорадиоволны через рупорные антенны проникают в изделие и, пройдя усилитель принятых сигналов, регистрируются приемным устройством.
118
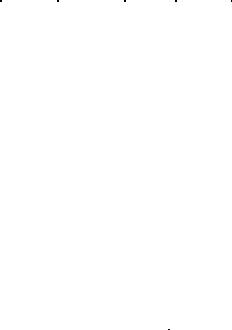
Капиллярный дефектоскоп представляет собой совокупность приборов капиллярного неразрушающего контроля. Капиллярный контроль основан на искусственном повышении свето- и цветоконтрастности дефектного участка относительно неповрежденного. Методы капиллярной дефектоскопии позволяют обнаруживать невооруженным глазом тонкие поверхностные трещины и другие несплошности материала, образующиеся при изготовлении и эксплуатации деталей машин. Полости поверхностных трещин заполняют специальными индикаторными веществами (пенетрантами), проникающими в них под действием сил капиллярности.
В целом методы дефектоскопии успешно используются для контроля макродефектов литейного и деформационного происхождения
(табл. 3.1).
Таблица 3 . 1 Применение методов неразрушающего контроля в промышленности
Виды дефектов |
|
|
Методы неразрушающего контроля |
|
|||||||||
|
|
магнит- |
вихре- |
ультра- |
капил- |
рентге- |
опти- |
||||||
|
|
ный |
токовый |
звуковой |
лярный |
новский |
ческий |
||||||
1 |
|
2 |
|
3 |
|
4 |
|
5 |
|
6 |
|
7 |
|
Внутренние расслоения |
– |
+– |
++ |
|
– |
++ |
|
– |
|||||
Линии текучести и |
+– |
– |
– |
– |
– |
++ |
|||||||
складки |
|||||||||||||
|
|
|
|
|
|
|
|
|
|
|
|||
Раковины, отслоения |
++ |
|
+– |
+– |
– |
– |
++ |
||||||
Скопление неметалли- |
– |
+– |
++ |
|
– |
– |
– |
||||||
ческих включений |
|
||||||||||||
|
|
|
|
|
|
|
|
|
|
|
|||
Отслоения и пузыри |
+– |
– |
– |
+– |
– |
++ |
|||||||
Трещины и разрывы на |
++ |
|
– |
+– |
– |
– |
++ |
||||||
поверхности |
|
||||||||||||
|
|
|
|
|
|
|
|
|
|
|
|||
Отпечатки валков, узоры |
|
|
|
|
|
|
|
|
|
|
|
||
механических повреж- |
– |
– |
– |
– |
– |
++ |
|||||||
дений |
|
|
|
|
|
|
|
|
|
|
|
||
Горячекатанные |
и холоднотянутые прутки и проволока |
|
|||||||||||
Поверхностныетрещины |
|
++ |
|
+– |
|
++ |
|
– |
|
– |
|
++ |
|
Закаты |
|
++ |
|
+– |
|
+– |
|
– |
|
– |
|
+– |
|
Волосовины |
|
++ |
|
+– |
|
+– |
|
+– |
|
– |
|
– |
|
Пережог |
|
– |
|
+– |
|
++ |
|
– |
|
– |
|
– |
|
Скопления неметалли- |
|
– |
|
+– |
|
++ |
|
– |
|
– |
|
– |
|
ческих включений |
|
|
|
|
|
|
|||||||
|
|
|
|
|
|
|
|
|
|
|
|
||
Грубая ликвация |
|
– |
|
++ |
|
++ |
|
– |
|
++ |
|
– |
|
Расслоения |
|
– |
|
+– |
|
++ |
|
+– |
|
++ |
|
+– |
|
Внутренние надрывы |
|
– |
|
+– |
|
++ |
|
– |
|
++ |
|
– |
119
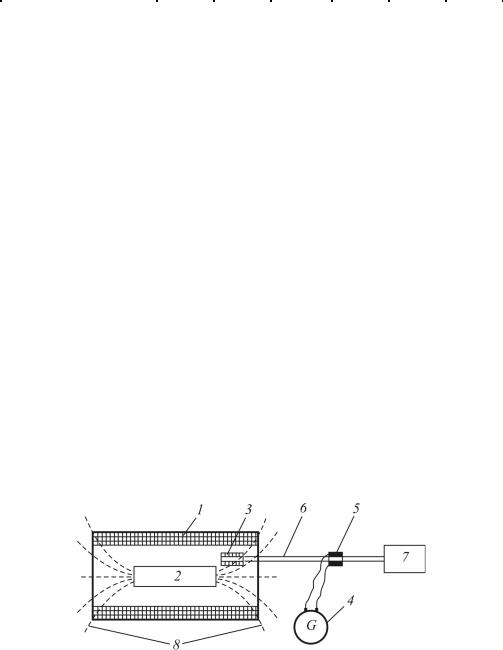
Окончание табл. 3 . 1
1 |
2 |
3 |
4 |
|
5 |
6 |
7 |
Внешние механические |
+– |
+– |
+– |
|
+– |
– |
++ |
повреждения |
|
|
|
|
|
|
|
|
Горячекатанные заготовки |
|
|
|
|||
Поверхностные трещи- |
++ |
+– |
++ |
|
– |
– |
++ |
ны продольные |
|
||||||
|
|
|
|
|
|
|
|
Поверхностные трещи- |
++ |
+– |
++ |
|
– |
– |
++ |
ны поперечные |
|
||||||
|
|
|
|
|
|
|
|
Шлифовочные трещины |
++ |
+– |
++ |
|
– |
– |
++ |
Пережог поверхности |
– |
++ |
++ |
|
– |
– |
– |
Закаты на поверхности |
++ |
++ |
++ |
|
+– |
– |
+– |
Включения, плены и ра- |
++ |
+– |
+– |
|
– |
– |
++ |
ковинынаповерхности |
|
||||||
|
|
|
|
|
|
|
|
Риски |
+– |
+– |
+– |
|
+– |
– |
++ |
Внутренняя рыхлота от |
– |
+– |
++ |
|
– |
++ |
– |
усадочной раковины |
|
||||||
|
|
|
|
|
|
|
|
Расслоения |
– |
++ |
++ |
|
– |
++ |
– |
Скопления неметалли- |
|
|
|
|
|
|
|
ческих включений в |
– |
+– |
++ |
|
– |
– |
– |
объеме |
|
|
|
|
|
|
|
Флокены |
– |
+– |
++ |
|
– |
– |
– |
Примечание. Знаки «+» и «–» обозначают эффективное, малоэффективное и нецелесообразное применение метода.
Также контроль структуры может быть проведен путем измерения тех или иных физических свойств. Особенно широко используется для этой цели измерение магнитных свойств, в частности коэрцитивная сила, намагниченность и магнитная проницаемость. Для измерения коэрцитивной силы используют приборы, называемыми коэрцитиметрами (рис. 3.51).
Рис. 3.51. Коэрцитиметр с измерительным генератором (блок-схема): 1 – намагничивающая катушка; 2 – образец; 3 – катушка измерительного генератора; 4 – магнитоэлектрический гальванометр, присоединенный к щеткам коллектора 5; 6 – вал электродвигателя 7; 8 – силовые линии магнитного поля образца
120