
2828.Экспертиза качества и разрушений
..pdfДля этого вида разрушения характерен межкристаллитный излом. Склонность к задержанному разрушению существенно зависит от склонности примесей к образованию сегрегаций на границах зерен аустенита перед закалкой. По сравнению с закалкой от 1000 °С, изотермическая выдержка при 860 °С перед закалкой увеличивает склонность стали к задержанному разрушению, уменьшая время до разрушения при одинаковом уровне напряжения, и уровень порогового напряжения, ни-
же которого разрушение не происходит.
Отпуск при 200 оС закаленной стали 20С2Г3Н2Х2Ф в присутствии водорода резко усиливает ее склонность к задержанному разрушению (см. рис. 4.56). Отдых и низкий отпуск увеличивает водородопроницаемость и эффективный коэффициент диффузии водорода в стали.
Наличие в структуре закаленного мартенсита областей объемного растяжения обусловливает ряд аномальных свойств закаленной стали: низкое сопротивление малым пластическим деформациям, низкий модуль упругости, высокий уровень внутреннего трения. Предполагается, что низкая водородопроницаемость свежезакаленного мартенсита обусловлена возникновением микродефектов типа микротрещин, в которых водород теряет свою подвижность, концентрируясь в областях объемного растяжения, способствуя образованию микротрещин.
Специфическим является более высокое сопротивление водородной хрупкости закаленного мартенсита по сравнению с отпущенным. Возможно, это связано с низкой подвижностью водорода в результате наличия ловушек, затрудняющих его перемещение в вершину трещины.
Низкий отпуск ослабляет сопротивление водородной хрупкости в результате повышения подвижности водорода в стали, что облегчает диффузионное перемещение водорода в вершину трещины и способствует ее распространению.
С понижением температуры, а также с уменьшением содержания кислорода и азота вероятность замедленного разрушения уменьшается.
Макроскопические изломы замедленного разрушения хрупкие. Зона замедленного разрушения в большинстве случаев блестящая, зернистого или кристаллического строения; зона долома имеет более волокнистое строение. В ряде случаев в зоне излома, соответствующей постепенному развитию трещины, наблюдаются следы фронта разрушения в виде тонких борозд или даже заметных на глаз кольцевых линий. В пределах кольцевых линий металл разрушается более пластично.
201
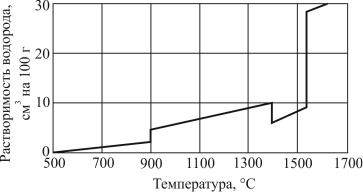
4.6.4. Влияние водорода на разрушение при статическом нагружении
Водород в сталь попадает в ходе различных процессов:
–литье, сварка (термическая диссоциация и ионизация воды);
–газовая цементация;
–термическая диссоциация газов;
–травление;
–коррозия;
–гальванические покрытия;
–ионная бомбардировка.
Концентрация растворенного водорода очень сильно зависит от температуры (рис. 4.57). На растворимость водорода в стали влияют элементы, входящие в состав стали. Это влияние характеризуется параметрами взаимодействия их с водородом.
Кислород, кремний и углерод понижают растворимость H2 в жидком железе, причем особенно сильно в этом направлении действует кислород. Титан, напротив, повышает растворимость водорода в стали. Влияние других элементов (Ni, Al, Cr и др.) незначительно.
Рис. 4.57. Растворимость водорода в стали при парциальном давлении 10,233 кН/м2 (760 мм рт.ст.)
Особое значение имеет резкое понижение растворимости H2 в стали при затвердевании и дальнейшем понижении температуры. Из рис. 4.57 видно, что при температуре 1600 °С и PН2 = 10,223 кН/м2 (760 мм рт.
ст.) растворимость водорода в жидком железе равна примерно 28 см3 на 100 г, а в твердом железе при комнатной температуре она равна практически нулю.
202
Вследствие этого во время кристаллизации H2 в значительной мере переходит в маточный раствор, что вызывает его сильную зональную ликвацию в слитке, а после затвердевания полностью выделяется из твердого раствора.
С водородом связаны следующие виды повреждений:
–водородное охрупчивание;
–задержанное разрушение;
–водородная коррозия.
Водородное охрупчивание встречается в двух видах. Первый тип, известный как внутреннее водородное охрупчивание, возникает, когда водород попадает в расплавленный металл, который становится пересыщенным по водороду сразу после затвердевания. Второй тип − внешнее водородное охрупчивание − возникает в результате абсорбции водорода твердым металлом.
Это может происходить во время тепловой обработки при высокой температуре и при эксплуатации, в процессе нанесения гальванического покрытия, при контакте с эксплуатационной химической средой, в результате коррозионных реакций, катодной защиты, при работе в водородной среде при повышенных давлениях.
Водородная хрупкость проявляется в виде понижения относительных сужения и удлинения, а иногда и ударной вязкости при содержании водорода более 2 см3 на 100 г и в тем большей степени, чем больше это содержание.
Ввиду узко локального характера высокое давление водорода в стали, даже если оно превышает предел прочности стали, само по себе не может вызвать разрушение металла, так как упруго передается на слои, следующие за микропустотой. Однако в случае приложения внешнего усилия возле микрообъемов с высоким давлением H2 возникает объемное напряженное состояние, вызывающее резкое понижение пластичности стали – водородную хрупкость.
Водород (его содержание в среднем 10–5 %) диффундирует в решетку металла в виде атома или протона. Он проникает в сталь при наличии в ней пор, скопления дислокаций и включений. В различного рода пустотах в структуре стали скапливается и молизуется, вследствие чего развиваются большие давления и создаются весьма высокие напряжения (рис. 4.58).
203
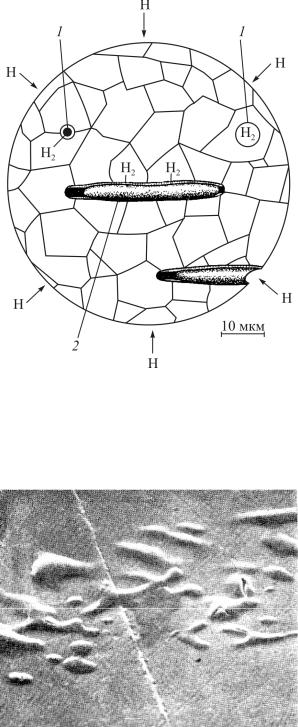
Рис. 4.58. Проникновение водорода в сталь при наличии пор и включений
Так, например, при бомбардировке поверхности аустенитной стали Х5CrNi18 ионами дейтерия под поверхностью образуются пузырьки и трещины (рис. 4.59).
Рис. 4.59. Образование пузырьков под поверхностью стали Х5CrNi18
204
Сероводород, сульфиды, мышьяк, селен, фосфор являются катализаторами процесса растворения водорода в металлах. Из-за присутствия водорода уменьшается подвижность дислокаций. Уже при 20 °С металлы могут настолько охрупчиваться, что уже при приложении малого растягивающего напряжения образуется трещина.
В сталях с ферритной структурой охрупчивание наблюдается только при относительно малой скорости деформации и только в области температур 70–140 °С. При содержании водорода более 10–3 и в отсутствии внешнего напряжения образуются локальные микротрещины, так как в результате моляризации водорода возникают высокие напряжения. При мягком напряженном состоянии водородное охрупчивание практически не наблюдается.
В отсутствие остаточных напряжений или внешней нагрузки внешнее водородное охрупчивание проявляется в различных формах: типа образования вздутий, внутреннего трещинообразования, формирования гидрида и снижения вязкости.
При растягивающих напряжениях или интенсивности напряжений, превышающих удельное пороговое значение, атомарный водород взаимодействует с металлом, что стимулирует рост докритической трещины вплоть до разрушения. В отсутствие коррозионной реакции (при катодной поляризации) обычно используется термин «водородное растрескивание» (НАС в английской транскрипции) или «водородное трещинообразование в напряженном состоянии» (HSC).
4.6.5. Влияние флокенов на разрушение при статическом нагружении
Разновидностью хрупкости, вызванной водородом, являются флокены – внутренние трещины (дефекты) в стальных поковках и прокатной продукции (иногда в слитках и отливках). На шлифовованных и протравленных темплетах флокены выявляются в виде тонких волосных трещин, а в изломе закаленных образцов представляют собой овальные кристаллические, серебристо-белые пятна, отличающиеся от основной поверхности излома.
Флокены обычно располагаются в средней части поковки в ликвационных участках, обогащенных С, Р, S, и не имеют определенной ориентировки. Флокены понижают пластичность и вязкость стали, сокращают срок службы изделий и приводят к неожиданным авариям. Наи-
205
большую флокеночувствительность имеют углеродистые и легированные стали мартенситного и перлитного классов. В сталях аустенитного и ледебуритного классов флокены практически не встречаются.
Основная причина образования флокенов – присутствие в стали повышенного количества Н2, наиболее вероятный механизм этого процесса – диффузия и адсорбция на поверхностях микронесплошностей кристаллической решетки. При этом происходит молизация Н2. Его давление в микронесплошностях вызывает микронапряжения, превышающие прочность металлической основы, что приводит к разрушению(разрыву).
Стимулирующую роль в образовании зон с повышенной адсорбцией Н2 играют внутренние растягивающие напряжения, возникающие в стали при структурных превращениях, пластической деформации и неравномерном охлаждения. Снижение сопротивления металла разрушению в местах концентрации напряжений, скоплений дефектов кристаллической решетки, неметаллических включений, ликвационных неоднородностей также способствует возникновению флокенов.
Способы борьбы с флокенами − вакуумирование жидкой стали, при котором содержание Н2 снижается до безопасного уровня, а также длительный изотермический отжиг заготовок или изделий при 650–750 °С. Продолжительность отжига зависит от их сечения.
Зоны металла с повышенным содержанием ликватов и легирующих элементов служат ловушками (накопителями) водорода. Повышенное содержание неметаллических включений, особенно продолговатых строчечных или пленочных оксисульфидов; границы раздела «металл– неметаллическое включение» являются своеобразными линзамибарьерами на пути диффузии атомарного водорода, концентраторами напряжений и накопителями молекулярного водорода, давление в которых достигает 200–400 МПа. В этих участках создаются условия для водородного охрупчивания металла, которое, при наличии внутренних напряжений, завершается образованием флокенов. Различные виды деформации, оказывающие влияние на ход диффузионных и окклюзионных процессов, увеличение внутренних напряжений повышают окклюзионную способность микрообъемов металла. Так, при напряжениях, равных 0,3–0,6σ0,2, резко сокращается время образования флокенов при насыщении металла водородом.
По отношению к бывшему аустенитному зерну вызванное водородом разрушение может быть как транскристаллитным, так и межкристаллитным (рис. 4.60). При разрушении, обусловленном действием во-
206
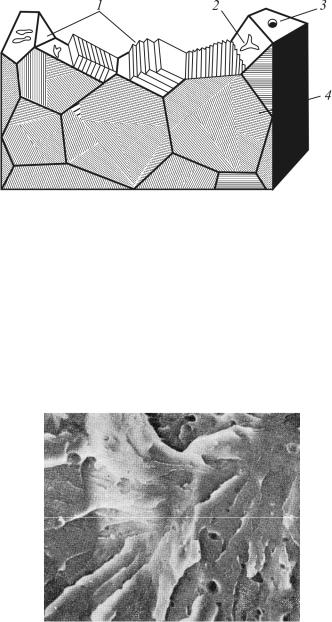
дорода, транскристаллитные и межкристаллитные участки излома встречаются совместно на общей поверхности разрушения.
Рис. 4.60. Схема образования излома, обусловленного водородным охрупчиванием: 1 − поверхность излома; 2 − пластически деформированные волосовины; 3 − микропоры; 4 − шлифованная поверхность; толстые линии − границы бывших зерен аустенита; тонкие линии − границы мартенситных пакетов
На рис. 4.61 представлен излом с флокенами. На фрактограмме видны микроквазисколы, поры и тонкие, пластически раскрытые волосовины. Поверхность разрушения состоит из крупных плоских фасеток скола, пересекаемых участками ямок. На фасетках скола наблюдаются гребни отрыва и ручьистые узоры.
Рис. 4.61. Транскристаллитное водородное охрупчивание стали. Видны микроквазискольные изломы, транскристаллитные вторичные трещины, микропоры и пластически раскрытые волосовины
207
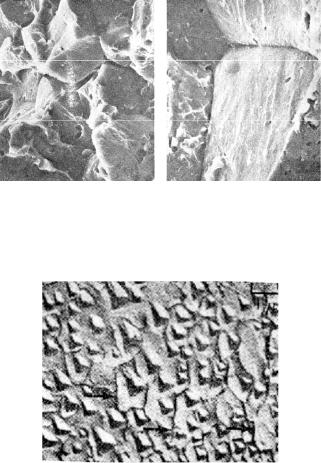
В закаленных и отпущенных высокопрочных сталях с пределом текучести от 1035 до 1725 МПа разрушение в результате водородного охрупчивания и коррозии под напряжением при низком уровне коэффициента интенсивности напряжения обычно носит межзеренный характер.
Пример строения излома, зародившегося вследствие диффузии водорода, например при нанесении электрогальванического покрытия, приведен на рис. 4.62.
Рис. 4.62. Гальванически оцинкованный болт из стали 37Сr4. Разрушение вызвано водородом. Характерны межкристаллитное разрушение, микропоры и частично раскрытые волосовины, расположенные внутри зерен и имеющие вид «вороньей ноги»
Рис. 4.63. Разрушение вокруг выделений на поверхности границ зерен мартенситностареющей стали. Следует отметить гребни отрыва.
Разрушение вызвано водородным охрупчиванием
На рис. 4.63 показан случай межзеренного разрушения высокопрочных сталей в результате охрупчивания под действием внешней среды в присутствии водорода. Мартенситностареющую сталь подвер-
208
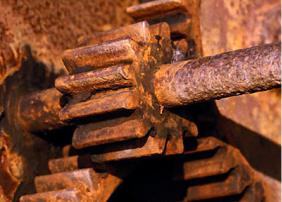
гали одновременному воздействию напряжению и электролитеческому насыщению водородом в растворе HCl. Показана одна зернограничная фасетка, покрытая большим количеством межзеренных выделений. На некоторых участках можно видеть гребни отрыва, связанные с разрушением вокруг границ выделений. Эти гребни отрыва образовались при общем объединении трещин, зародившихся в результате насыщения водородом.
4.7. Разрушение вследствие коррозии
4.7.1. Общие представления
Коррозия – это самопроизвольное разрушение металлов в результате химического или физико-химического взаимодействия с окружающей средой (рис. 4.64).
Рис. 4.64. Коррозия на поверхности ведущей шестерни
В общем случае это разрушение любого материала, будь то металл или керамика, дерево или полимер. Причиной коррозии служит термодинамическая неустойчивость материалов к воздействию веществ, находящихся в контактирующей с ними среде. Так, на поверхности железа под действием воды происходит кислородная коррозия в соответствии с реакцией 4Fe + 6Н2О + 3О2 = 4Fe(OH)3. Гидратированный оксид железа Fe(OН)3 и является тем, что называют ржавчиной.
Коррозионное разрушение многообразно по своим проявлениям. Оно может происходить за счет химических и электрохимических процессов и реакций. Коррозия часто не изменяет механические свойства материала, а приводит к постепенному равномерному уменьшению
209
размеров нагруженной детали, например вследствие постепенного растворения. В результате этого напряжения, действующие в опасном сечении, растут, и, когда они превысят допустимый уровень, произойдет разрушение.
Экономические потери от коррозии металлов огромны. В США, по последним данным, ущерб от коррозии и затраты на борьбу с ней составили 3,1 % от ВВП (276 млрд долл.). В Германии этот ущерб составил 2,8 % от ВВП. По оценкам специалистов различных стран, эти потери в промышленно развитых странах составляют от 2 до 4 % валового национального продукта. При этом потери металла, включающие массу вышедших из строя металлических конструкций, изделий, оборудования, составляют до 20 % годового производства стали.
Масштабы коррозии и убытки, причиняемые ею, станут очевидными, если учесть, что около 10 % всего производимого металла безвозвратно теряется вследствие разрушающего действия коррозии.
Экономические потери от коррозии можно разделить на прямые и косвенные.
Прямые потери включают стоимость заменяемых металлических конструкций и механизмов или их частей, стоимость коррозионностойких металлов и сплавов, применяемых вместо материалов, имеющих те же механические свойства, но нестойких к коррозии, стоимость различных видов защиты от коррозии и т.д.
К косвенным потерям относятся расходы, связанные с простоем оборудования во время замены части машины или аппарата, разрушаемых коррозией, с загрязнением выпускаемых изделий продуктами коррозии и др.
Повышение цен в России на энергоресурсы и металлы до мирового уровня привело к резкому сокращению и объемов, и областей применения нержавеющих сталей, титана. Одновременно повышается интерес к современным полимерным коррозионно-стойким материалам в области химического машиностроения. Химические, физические и биологические загрязнения природной среды приводят к заметной интенсификации коррозионных процессов.
Один из примеров таких разрушений – обрушение Серебряного моста (рис. 4.65). Оно произошло из-за ржавчины. 15 декабря 1967 г. Серебряный мост, соединяющий Поинт Плезант, штат Западная Виржиния, и Канауга, штат Огайо, неожиданно рухнул в р. Огайо. В момент
210