
2828.Экспертиза качества и разрушений
..pdfС понижением температуры все происходит наоборот. Повышается относительная влажность среды, что способствует конденсации влаги. Скорость атмосферной коррозии увеличивается.
Жидкостная коррозия – весьма распространенный вид коррозии. В зависимости от того, в какой жидкой среде происходит коррозия, различают кислотную, щелочную, солевую, морскую и речную коррозии.
По условиям воздействия жидкости на поверхность металла эти виды коррозии получают добавочные характеристики: с полным погружением, с неполным погружением, с переменным погружением, капельная, струевая. Коррозионный процесс в жидких средах для большинства металлов протекает с участием кислорода. Особенное усиление коррозии наблюдается вблизи ватерлинии. Это объясняется легким доступом кислорода. Исключительно энергичное коррозионное воздействие оказывают, например, брызги морской воды. На скорость коррозии в жидкости сильно влияет наличие окалины. Так, в морской воде окалина может в 30–40 раз увеличить скорость коррозии.
4.7.5.Газовая коррозия в технологических средах
Вметаллургии, химической промышленности множество процессов или их определенных стадий протекает в условиях повышенных температур и давлений. При низких температурах (100–200 °С) большинство газов и их смесей не представляет опасности. При повышенных температурах (выше 200–300 °С) и давлениях химическая активность газов сильно возрастает, и они начинают оказывать вредное влияние на металлы и сплавы.
При температуре выше 200 °С вредное воздействие оказывает хлор,
авыше 300 °С – хлористый водород (HCl). С повышением температуры до 500 °С пары серы, диоксид серы (оксид серы (IV), сернистый ангидрид, сернистый газ, SO2) и диоксид азота (оксид азота (IV), бурый газ, NO2) также становятся химически активными.
Втехнологических средах часто встречаются следующие случаи газовой коррозии:
– водородная коррозия;
– обезуглероживание стали;
– сернистая коррозия;
– карбонильная коррозия;
– разрушение в среде хлора и хлористого водорода.
221
Водородная коррозия – вид коррозионного разрушения, который наблюдается в основном в технологических средах, содержащих водород, при воздействии повышенных температур и давлений. Очень часто водородная коррозия наблюдается при гидрировании нефти и угля, синтезе метанола и аммиака и т.п.
При воздействии водорода металл может подвергаться двум видам разрушения: водородная коррозия и водородная хрупкость (о водородной хрупкости см. подразд. 4.6.4). Зачастую эти два вида разрушения протекают одновременно.
Водородная коррозия происходит вследствие химического взаимодействия водорода среды и карбидной составляющей стали. При повышенных температурах и давлениях водород, попадая на поверхность стального изделия, диссоциирует. Образовавшиеся атомы H2 очень подвижны, их диаметр составляет 0,1 нм. Атомы водорода диффундируют в глубь металла, растворяясь в нем. Некоторая часть вступает в реакцию с углеродом: C + 4H = CH4.
Обычно водородная коррозия появляется из-за нескольких причин:
–повышение внутреннего давления при образовании в порах CH4
ив результате растрескивание по границам зерен;
–обезуглероживание стали, которое происходит из-за восстановления водородом цементита (Fe3C входит в состав сталей): Fe3C + 2H2 =
=3Fe + CH4;
–водород проникает в глубь стали, образуя хрупкий твердый рас-
твор водорода в железе.
У водородной коррозии есть так называемый инкубационный период, при котором какие-либо внешние признаки разрушения отсутствуют. В среднем этот период может составлять около 1000 ч (зависит от условий).
Расчеты по термодинамике показывают, что при повышенном давлении и температуре около 350–600 °С цементит почти полностью разрушается.
Реакция, при которой образуется СН4 (метан), может протекать в сторону уменьшения объема, т.е. она обратимая. При повышении температуры равновесие реакции сдвигается вправо. Поэтому на нефтехимических производствах температуру поддерживают до 200 °С, при давлении около 50 МПа.
Скорость протекания водородной коррозии зависит не только от рабочих давлений итемператур, но и от глубины обезуглероживания стали.
222
Обезуглероживание стали (декарбюризация) – процесс обеднения поверхностного слоя металла углеродом. Наблюдается при температурах свыше 650 °С. Чаще всего процесс обезуглероживания стали протекает в окислительных атмосферах (O2, H2O, CO), но может происходить и в атмосфере водорода. Кислород окисляет сначала углерод, а потом только железо. Обезуглероживание стали проходит интенсивнее с увеличением в газовой среде количества углекислого газа, влаги и кислорода. Если газовая среда содержит больше угарного газа и метана, скорость декарбюризации уменьшается.
Процесс восстановления цементита Fe3C является основой процесса обезуглероживания стали.
При температуре выше 650 °С атомы углерода более подвижны, чем атомы основного металла (железа), коэффициент диффузии атомов углерода также превышает коэффициент диффузии атомов Fe. Обезуглероживание стали протекает тогда, когда углерод диффундирует быстрее, чем окисляется железо.
Обезуглероживание сопутствует очень многим технологическим процессам, таким как разнообразные реакции горения, окислительного крекинга и др. Сталь, подвергшаяся декарбюризации, теряет свою прочность и твердость, тем самым ухудшается ее качество, сокращается срок службы готовых изделий.
Декарбюризация (обезуглероживание стали) наблюдается после образования пленки оксидов на поверхности металла. С утолщением пленки окалина образуется медленнее, при этом обезуглероженный слой утолщается (может уходить на несколько миллиметров в глубь основного металла).
Для уменьшения степени обезуглероживания в сталь вводятся добавки вольфрама и алюминия. Незначительное влияние оказывают хром, марганец и кобальт.
Сернистая коррозия (коррозия в среде серы). Различные соединения серы оказывают большое влияние на высокотемпературную газовою коррозию. Самым вредным и опасным среди таких соединений является сероводород (даже более, чем сернистый ангидрид). Он увеличивает скорость коррозии в десятки раз по сравнению со средами, не содержащими его соединений.
Склонность к сульфидному растрескиванию возрастает с уровнем предела текучести стали, растягивающих напряжений и содержанием в воде сульфидов.
223
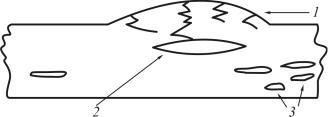
Усилению влияния сероводорода на металл способствует увеличение его содержания в ряде месторождений нефти и газе. Так, в нефтяном газе содержание Н2S с 1975 г. по 1984 г. увеличилось в 1000 раз.
Сульфидное растрескивание диагностируется по появлению сетки мелких микротрещин и пузырчатости на поверхности стенок силового элемента. Наиболее удивительное явление − образование пузырьков (отдулин) на поверхности стенок сосудов давления (рис. 4.68).
Рис. 4.68. Схема образования отдулин (1) и последующего трещинообразования (2 – полость, 3 – слоистые трещины)
Сернистый ангидрид (SO2) выделяется в результате многих технологических процессов. Под воздействием этого соединения при температуре свыше 300 °С образуется на поверхности черных металлов слоистая окалина, которая состоит из FeS, FeO и Fe3O4.
Детали из чугуна окисляются изнутри, идет увеличение объема до 10 %. Сильно уменьшается прочность чугунных изделий, наблюдается коробление, появляются поверхностные трещины и деталь разрушается. Это явление получило название «рост чугуна». Максимальное повреждение наблюдается при температуре около 700 °С.
Щелочное растрескивание. Щелочное, или каустическое, растрескивание − разновидность коррозионного растрескивания под напряжением в концентрированых растворах щелочей при повышенных температурах (45–150 °С). Растрескиванию в щелочных растворах подвержены углеродистые, низколегированные, высоколегированные хромистые и хромоникелевые нержавеющие стали. Склонность к щелочному растрескиванию существенным образом зависит от химического состава, структуры уровня прочности стали, уровня приложенных напряжений, концентрации щелочи и температуры эксплуатации.
Металлографический анализ структуры в зоне трещинообразования показывает, что трещины, как правило, имеют межзеренный характер (рис. 4.69), ветвятся и зарождение их связано с порами и другими де-
224
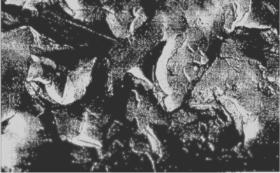
фектами. Вершины трещин тонкие, почти не имеющие раскрытия. Наличие лидирующих микротрещин у вершины макротрещины предполагает, что растрескивание осуществляется зарождением лидирующих микротрещин в зоне концентрации напряжений перед фронтом магистральной трещины и последующим слиянием с ней.
Рис. 4.69. Излом стали Ст.3сп (разрушение вызвано щелочным растрескиванием)
Полагают, что проявление щелочного растрескивания связано с образованием ионов HFeO2–. Для щелочного растрескивания свойственны склонность к ветвлению трещин, межкристаллитный характер распространения трещины и отсутствие следов пластической деформации вдоль траектории трещины. Строение излома подтверждает предпочтительно межзеренный характер разрушения.
4.8. Особенности проявления коррозионного разрушения
Коррозионное разрушение по характеру своего развития проявляется как общее или сплошное, местное или локальное (рис. 4.70).
Общая, или сплошная, коррозия охватывает всю поверхность металла, находящуюся под воздействием агрессивной среды, и может быть:
–равномерной, например коррозия углеродистой стали в растворах серной кислоты;
–неравномерной, например коррозия этой же стали в присутствии хлорионов.
Местная коррозия охватывает отдельные участки поверхности металла. Она подразделяется:
–на коррозию пятнами, которая занимает относительно большие участки поверхности и распространяется неглубоко;
225
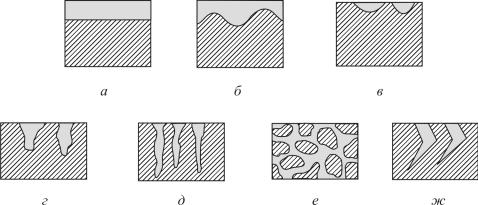
–коррозию язвами, которая поражает металл на большую глубину
ина ограниченной площади;
–точечную, или питтинговую, которая поражает металл в отдельных точках на большую глубину, в некоторых случаях насквозь;
–межкристаллитную коррозию;
–коррозию по границам кристаллитов металла (распространяется на обширной поверхности металла и набольшую глубину. Этот вид коррозии опасен тем, что внешний вид металлического изделия не изменяется, но при этом металл теряет прочность и пластичность, например коррозия стали Х18Н10 после ее нагрева до 600 °С);
–растрескивающую коррозию (вид коррозии при одновременном воздействии на металл коррозионной среды и механических напряжений. При этом скорость коррозии металла резко возрастает, например сезонное растрескивание холодно деформированных α- и β-латуней, содержащих более 10 % цинка).
Рис. 4.70. Виды коррозии: а – равномерная; б – неравномерная;
в– коррозия пятнами; г – коррозия язвами; д – точечная;
е– межкристаллитная; ж – растрескивающая
Из перечисленных видов локальной коррозии часто встречаются питтинговая, щелевая, ножевая, межкристаллитная виды коррозий, усталостное растрескивание
Питтинговая (точечная) коррозия – вид коррозионного разрушения, которому подвергаются исключительно пассивные металлы и сплавы. Питтинговая коррозия наблюдается у никелевых, циркониевых, хромоникелевых, хромистых, алюминиевых сплавах и др.
226
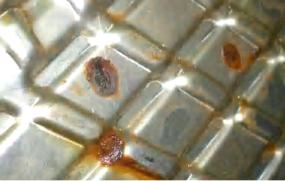
При питтинговой (точечной) коррозии разрушению подвергаются только отдельные участки поверхности (рис. 4.71), на которых образуются глубокие поражения – питтинги (точечные язвы). Наблюдается питтинговая коррозия при воздействии на металл или сплав не только пассиваторов (приводят поверхность в пассивное состояние, например, окислитель), но и ионов-активаторов (Cl, Br–, J–). Активно протекает питтинговая (точечная) коррозия в морской воде, смеси азотной и соляной кислот, растворах хлорного железа, других агрессивных средах.
Рис. 4.71. Питтинг-коррозия на поверхности низкоуглеродистой стали
По размерам различают:
–микропиттинги (до 0,1 мм);
–питтинги (0,1–1 мм);
–пятно, язва (более 1 мм).
Рост питтинга происходит по электрохимическому механизму, вследствие интенсивного растворения пассивной оксидной пленки. Изза активного растворения пленки происходит усиление анодного процесса в самом питтинге (активационный рост питтинга). Со временем, когда питтинг будет достаточно расширен, активационный рост замедляется, начинается диффузионный режим роста питтинга.
Щелевая коррозия – один из видов местной электрохимической коррозии металла. Щелевая коррозия подразумевает усиленное коррозионное разрушение в щелях, трещинах, зазорах (фланцевые, резьбовые соединения, места неплотного соединения металла с резиновыми или другими прокладочными материалами и т.д.). Щелевая коррозия может протекать как в атмосфере воздуха или газовой смеси, так и в условиях смачивания электролитом (морская вода). В морской атмосфере наблю-
227
дается в щелях и зазорах между металлом (трубопровода, днища корабля или любой другой конструкции, омываемой водой) и обрастающими организмами (водоросли, полипы, различные микроорганизмы). При атмосферной щелевой коррозии в щелях, зазорах постоянно скапливается и задерживается влага, что обусловливает ее протекание.
Этот вид коррозионного разрушения может наблюдаться в растворах, не содержащих окислитель (кислород), в электролитах с повышенной кислотностью.
Щелевая коррозия протекает в условиях малого количества окислителя, так как его подход к стенкам узкой щели затруднен. Самыми чувствительными к щелевой коррозии считаются пассивирующиеся металлы, сплавы. Это связано с их возможной активацией в зазоре. К таким относится алюминий, его сплавы, хромистые, хромоникелевые сплавы.
Интересным фактом является то, что в одной щели может возникнуть макроэлемент. В ее вершине и середине скапливается большое количество продуктов коррозии – они будут являться анодом, а края (места с более свободным подводом окислителя к поверхности) будут играть роль катода.
Межкристаллитная коррозия (МКК) – один из видов местной коррозии металла, который приводит к избирательному разрушению границ зерна. Межкристаллитная коррозия – очень опасный вид разрушения, так как визуально ее не всегда можно определить. Металл теряет свою пластичность и прочность.
Межкристаллитной коррозии чаще всего подвергаются металлы и сплавы, которые легко становятся пассивными. К ним относятся хромоникелевые и хромистые сплавы (нержавеющие стали), сплавы алюминия, никеля, некоторые другие (рис. 4.72).
Причина возникновения межкристаллитной коррозии – структурные превращения на границах зерен металла. Зона структурных превращений становится анодом, который усиленно растворяется. Связь между зернами металла нарушается, и происходит их выкрашивание. Вследствие этих процессов металлические конструкции при эксплуатации теряют свои свойства и быстро приходят в негодность.
Межкристаллитная коррозия нержавеющих сталей связана с обеднением границ зерен хромом или образованием примесей (карбидов хрома). Наиболее часто встречается карбид Cr23C6, который сильно снижает пластичность и ударную вязкость металла.
228
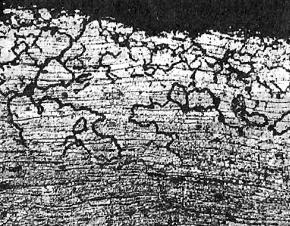
Рис. 4.72. Межкристаллитная коррозия стали 12Х18Н10Т со стороны внутренней поверхности бесшовной трубы вблизи зоны разрыва трубопровода гидрогенизатора. ×200
Карбиды выступают в роли анода, из-за чего происходит резкое увеличение скорости межкристаллитной коррозии.
При повышенной температуре атомы углерода, которые намного меньше атомов хрома и обладают большей подвижностью, диффундируют к границам зерен не только с приграничных зон, но и с объема. При этом в карбидообразовании участвуют почти весь углерод зерна и только те атомы хрома, которые расположены почти у самых его границ. Карбиды концентрируются возле границ зерен, образуя сплошную цепочку. Так границы зерен оказываются обедненными хромом.
При воздействии агрессивной среды карбиды хрома растворяются. О скорости межкристаллитной коррозии нержавеющих сплавов можно судить по концентрации в зерне атомов хрома. Чем больше разность концентраций хрома на границах зерна и в объеме, тем быстрее протекает межкристаллитная коррозия.
На склонность к карбидообразованию очень сильно влияет легирование нержавеющих сталей. V, W, Mo, Mn, Nb снижают активность углерода, предотвращая возможность возникновения межкристаллитной коррозии. Si, Co, Ni – напротив, увеличивают активность атомов углерода, усиливая МКК.
На протекание межкристаллитной коррозии при воздействии сильных окислителей большое влияние оказывает не один, а несколько факторов одновременно (интенсивное растворение избыточных фаз, неус-
229
тойчивых в данной среде; избирательное растворение границ зерна, обедненных хромом; избирательное растворение мест концентрации примесей и т.д.).
«Ножевая» коррозия – разновидность межкристаллитной коррозии. Ножевая коррозия – местное разрушение, которое наблюдается на сварных швах. Протекает в узкой зоне, на границе «основной металл – сварной шов». Ножевой коррозии подвержены многослойные сварные швы высокоуглеродистых хромоникелевых сталей, стабилизированные титаном стали, которые эксплуатируются в азотной кислоте.
При сварке почти расплавленный металл (с температурой около 1300 °С) контактирует с холодным. В расплавленном металле растворяются карбиды хрома или титана, а при его охлаждении не успевают выделиться новые карбиды. При этом углерод остается в твердом растворе. Из-за достаточно медленного охлаждения выпадает большое количество карбидов Cr. В агрессивных средах происходит постепенное растворение (на межкристаллитном уровне) узкой зоны возле сварного шва.
Почвенной коррозии подвержены различные металлические трубопроводы, опоры, сваи, днища резервуаров, кабельные сети и другие конструкции, находящиеся полностью или частично в почве. Почвенная коррозия часто связана с блуждающими токами. Источниками блуждающих токов являются электротранспорт (трамваи, метро, электропоезда), различные электроустановки, питающиеся постоянным током. Величина блуждающего тока может быть весьма значительной. Радиус действия иногда достигает нескольких десятков километров. Коррозия металлов в почве имеет ряд специфических особенностей, например возможность образования коррозионных элементов протяженностью в десятки и сотни метров (коррозия трубопроводов). Во влажных, кислых и щелочных почвах коррозия может быть значительной.
Коррозионное растрескивание возникает в металлах и сплавах только в том случае, когда одновременно действуют три фактора: напряжение, неблагоприятное определенное структурное состояние материала; особая коррозионная среда; различные случаи сочетания этих факторов. При коррозионном растрескивании возможно появление транскристаллитного и межкристаллитного разрушения. Возникшие вследствие деформации дефекты кристаллического строения группируются на поверхности металла и являются местами коррозионного растрескивания (рис. 4.73).
230