
- •С одержание
- •Введение
- •Сущность основных способов сварки плавлением и область их рационального применения.
- •3. Сущность основных способов сварки давлением.
- •Источники питания для сварки.
- •Влияние сварочных процессов на свариваемый металл.
- •1. Сварочные материалы
- •2. Тепловое воздействие сварочного источника на свариваемый металл.
- •3. Деформация и напряжения, возникающие при сварке, и способы борьбы с ними
Сущность основных способов сварки плавлением и область их рационального применения.
1. Электрическая дуговая сварка наиболее широко используется при изготовлении всевозможных сварных конструкций. В зависимости от материала сварной конструкции, ее габаритов, толщины свариваемого металла и других особенностей свариваемого изделия предпочтительное применение находят определенные разновидности электрической дуговой сварки.
Так, при изготовлении конструкций из углеродистых и низколегированных конструкционных сталей наибольшее применение находят как ручная дуговая сварка качественными электродами с толстым покрытием, так и автоматическая и полуавтоматическая сварка под флюсом, а также сварка в углекислом газе; при сварке конструкции из высоколегированных сталей, цветных металлов и сплавов на их основе предпочтительное использование находит аргоно-дуговая сварка, хотя при определенных условиях применяются и некоторые другие разновидности электрической дуговой сварки.
Ручная дуговая сварка плавящимися толстопокрытыми электродами имеет наибольший объем применения из всех дуговых способов сварки. Схема процесса сварки приведена на рис. 2.1, а. Питание дуги осуществляется от сварочного генератора или выпрямителя постоянным током или от сварочного трансформатора - переменным током. Наиболее широкое применение находит постоянный ток. В настоящее время применяются только толстопокрытые электроды, т. е. такие, у которых на металлический пруток определенных размеров («стержень») наносится обмазка (электродное покрытие).
У
Состав
покрытия при расплавлении вместе со
стержнем обеспечивает защиту от окисления
и азотирования металла шва и определенное
легирование направленного металла для
придания ему необходимых механических
свойств, а также придает устойчивость
горению дуги.
Рис. 2.1. Схема процессов при использовании различных разновидностей электрической дуговой сварки:
а-в–ручная дуговая сварка; а–толстопокрытыми плавящимися электродами; б–угольным электродом дугой прямого действия; в–угольными электродами дугой косвенного действия; г–автоматическая и полуавтоматическая сварка под флюсом; д–аргоно-дуговая сварка вольфрамовым электродом; е–плазменная сварка; ж–сварка в углекислом газе; з–атомноводородная сварка; 1–электрод с покрытием, 2–сварочный генератор, 3–свариваемые детали, 4–электрическая дуга, 5–присадочный пруток, 6–угольный электрод, 7–сварочный трансформатор, 8–вольфрамовый электрод, 9–электродная проволока, 10–электрическая дуга.
При питании дуги постоянным током в зависимости от марки электрода (в соответствии с рекомендациями паспорта электродов) может применяться прямая или обратная полярность подключения.
Прямой
полярностью называют такую, когда
отрицательный полюс источника питания
подключают к
электроду,
положительный - к изделию. Обратная
полярность - плюс на электрод, минус на
изделие. Для
большинства
марок качественных электродов
рекомендуется обратная полярность.
Ручная дуговая сварка угольным электродом дугой прямого действия используется при сварке тонколистовой углеродистой конструкционной стали, а также при сварке некоторых цветных металлов и сплавов на их основе. Схема процесса сварки приведена на рис, 2.1, б. Сварка производится при питании дуги постоянным током прямой полярности, что обеспечивает наилучшую стабильность процесса. В настоящее время объем применения этого способа невелик.
Ручная дуговая сварка угольными электродами дугой косвенного действия применяется только при сварке тонкого металла (стали, некоторых цветных металлов и сплавов на их основе). Схема процесса сварки приведена на рис. 2.1, в. Сварной шов в этом случае, как правило, образуется за счет расплавления отбортованных кромок без участия присадочного (добавочного) металла. Так как расход электродов при питании дуги постоянным током оказывается неодинаковым (электрод, являющийся анодом, вследствие большого тепловыделения на нем, расходуется значительно быстрее), то питание дуги в этом случае осуществляется переменным током, что позволяет обеспечить равномерный расход электродов.
Автоматическая и полуавтоматическая сварка под флюсом (рис. 2.1, г). Областью рационального применения этого способа сварки является сварка углеродистых низколегированных и некоторых марок высоколегированных сталей. В небольшом объеме этот способ используется при сварке некоторых цветных металлов и сплавов на их основе.
При сварке дуга горит в пузыре из расплавленного флюса, который толстым слоем (40 - 60 мм) насыпается на стык свариваемых металлов.
Так
как при сварке дуга закрыта расплавленным
и нерасплавленным порошкообразным
флюсом, то плотность тока по сравнению
со сваркой открытой дугой без опасения
разбрызгивания металла может быть
увеличена
в
несколько раз, что пред- определяет
существенное (в несколько раз) увеличение
производительности процесса.
По сравнению с ручной дуговой сваркой существенно расширяется диапазон толщин, свариваемых встык без скоса кромок, что сокращает время на подготовку деталей к сварке.
Питание дуги может осуществляться как переменным, т и постоянным током.
Так как объем сварочной ванны (расплавленного метал а и флюса) достаточно велик, то во избежание стекания их сварка этим способом осуществляется только в нижнем положении, т.е. когда шов располагается в горизонтальной плоскости или при очень небольших наклонах свариваемых листов, как правило, не более 7˚ к горизонту. Это несколько ограничивает объем применения данного способа.
Аргоно-дуговая сварка вольфрамовым электродом (рис. 2.1, д). Вольфрамовый электрод закрепляется в токоподводящем устройстве специальной горелки, к которой по шлангам подводится токоведущий провод и инертный газ аргон. Истекающая из сопла горелки струя аргона оттесняет воздух и надежно защищает электрод, дугу и сварочную ванну от окисления и азотирования. Таким образом, процесс осуществляется при струйной защите зоны сварки от контакта с воздухом. Если возникает необходимость в добавочном (присадочном) металле для усиления шва (валика), то в дугу подается присадочная проволока, как правило, того же или близкого состава, что и свариваемый металл.
Так
как при такой схеме процесса имеет место
весьма надежная изоляция сварочной
ванны (а если надо, то и остывающего шва)
от кислорода и азота воздуха, то этот
способ применяют главным образом при
сварке изделий из металлов и сплавов,
обладающих большим сродством к газам
воздуха (например, из титана, циркония,
алюминия, магния и других химически
активных металлов), либо при изготовлении
конструкций
ответственного
назначения из коррозионностойкой стали
и некоторых других материалов.
В особых случаях, когда при сложной конфигурации изделий струйная защита не может обеспечить надежной изоляции зоны шва и прилегающих участков от контакта с воздухом, применяют аргоно-дуговую сварку в камерах с контролируемой атмосферой (как правило, аргоном).
Такие камеры могут быть необитаемыми, в которых располагается автомат с дистанционным управлением, либо при небольших габаритах изделия сварщик держит электрододержатель и манипулирует дугой руками, вводя их в камеру через специальные герметические «рукава», заканчивающиеся перчатками; при этом наблюдение за процессом осуществляется через смотровое стекло.
Если свариваемое изделие имеет большие размеры, то сварка может осуществляться в так называемых обитаемых камерах, заполненных аргоном. Детали, подлежащие сварке, подаются в камеру через грузовой люк, имеющий специальный шлюз, исключающий попадание наружного воздуха внутрь камеры. Через эти же люки сваренные изделия выгружаются.
Сварщики в специальных скафандрах входят в камеры через пассажирские шлюзы и промежуточные камеры небольшого размера, в которых производится «промывка» аргоном наружной поверхности костюма от адсорбированного воздуха. Свежий воздух для дыхания сварщика и выдыхаемый воздух подводится и отводится по специальным шлангам, сообщающимся с внешней атмосферой.
Плазменная сварка (рис. 2.1, е) является разновидностью аргоно-дуговой сварки. В отличие от аргоно-дуговой, где дуга между электродом и изделием горит в свободно истекающем из сопла горелки потока аргона (рис. 2.1, д), при плазменной сварке дуга обжимается потоком газа, проходящим через узкое отверстие в горелке, называемой плазматроном.
Обжатие
дуги приводит к повышению температуры
ее столба: при свободно горящей дуге
эта температура составляет величину
около 5730˚С,
при
горении сжатой дуги температура
повышается до 14 730 - 24 730˚ С. Вследствие
этого возрастает и степень ионизации
газа, что в свою очередь создает более
высокую эффективность локального
нагрева свариваемого металла.
Кроме плазмообразующего через горелку подается также защитный газ, обеспечивающий надежную изоляцию зоны сварки от контакта с воздухом. Плазменная сварка применяется для соединения тех же материалов, что и аргоно-дуговая.
Сварка в углекислом газе (рис. 2.1, ж) применяется преимущественно при изготовлении конструкций из углеродистых и низколегированных конструкционных сталей, как общего назначения, так и машиностроительных. Как правило, сварка производится электродной проволокой, в составе которой имеется достаточное количество раскислителей - кремния и марганца.
Это необходимо в связи с тем, что углекислый газ при высоких температурах диссоциирует на оксид углерода и кислород, причем содержание последнего в зоне сварки может достигать 20 % и более. Таким образом, углекислый газ в зоне сварки представляет собой сильный окислитель и фактически защищает сварочную ванну только от азотирования.
При наличии в сварочной ванне достаточного количества кремния и марганца эти элементы выступают как раскислители и тем самым позволяют получить наплавленный металл требуемого состава, а надежная защита потоком газа от контакта сварочной ванны с воздухом исключает возможность образования нитридов.
Поэтому
для сварки в углекислом газе необходимо
использовать только кремнемарганцевую
проволоку, обычно марки Св-08Г2С, содержащую
до 2 % марганца (обычно 1,8 - 2,1 %) и около 1
% кремния (0,70 - 0,95 %). Значительная часть
кремния и марганца в процессе сварки
окисляется и переходит в шлак, покрывающий
шов тонким слоем, легко
удаляемый
стальной щеткой, а оставшееся неокисленным
количество этих элементов обеспечивает
оптимальные механические свойства шва.
В настоящее время этот способ получил широкое распространение при изготовлении сварных конструкций как общего назначения, так и специальных.
Атомно-водородная сварка (рис. 2.1, з). При этом способе сварки дуга горит между двумя вольфрамовыми электродами в потоке водорода, подаваемого через горелку от баллона. Проходя через дугу, водород нагревается до высоких температур (более 5730˚ С) и диссоциирует на атомы, поглощая большое количество тепловой энергии.
Поток диссоциированного водорода, попадая на свариваемые детали, охлаждается (до температуры плавления металла) и вновь образует молекулы, выделяя то количество тепловой энергии, которое было затрачено на диссоциацию (около 540 кДж/моль).
Этой тепловой энергии оказывается достаточно для локального расплавления кромок свариваемого металла и образования сварочной ванны. Примерно около 15 % тепловой энергии от общего тепловыделения образуется за счет горения водорода, окружающего дугу.
Одновременно с энергетическим воздействием водород, поступающий в зону сварки, изолирует сварочную ванну от контакта с воздухом, т. е. исключает возможность окисления и азотирования металла шва. Однако в настоящее время этот способ сварки используется крайне редко из-за ряда недостатков, присущих ему. Основным недостатком этого способа является то обстоятельство, что дуга в водороде горит при высоком напряжении (до 150 - 200 В), что требует использования источника питания (трансформатора) с напряжением холостого хода на вторичной обмотке 250 - 260 В.
В этом случае сварщик должен работать в специальных резиновых перчатках и специальной обуви, что создает определенные неудобства и не гарантирует полной безопасности.
2.
Электрошлаковая сварка (рис. 2.2) имеет
три основных разновидности: сварка
проволочными электродами (рис. 2.2, а),
пластинчатыми электродами (рис. 2.2, б) и
плавящимся мундштуком (пластино-проволочными
электродами, рис. 2.2, в. Как следует из
рис. 2.2, электрошлаковая сварка во всех
случаях выполняется при вертикальном
расположении шва.
Рис. 2.2. Схема процесса электрошлаковой сварки:
а–проволочными электродами;б–пластичными электродами;в–плавящимся мундштуком; 1–пластины,2–стальные трубки,3–электродные проволоки,4–шлаковая ванна,5–медные водоохлаждаемые пластины,6–свариваемые детали,7–металлическая ванна;∆–зазор между пластинами;В и δ–ширина и толщина пластинчатого электрода;S–толщина свариваемых деталей(Smax–максимальная;Smin–минимальная);υэл–скорость подачи электродов в шлаковую ванну; υсв–скорость сварки(скорость подъема металлической ванны);hш–глубина шлаковой ванны
Электрошлаковая
сварка проволочными электродами
применяется для соединений встык
толстого металла (толщиной около 40 мм
и более) при
относительно
большой протяженности швов, например
при сварке продольных швов барабанов
котлов высокого давления и других
изделий.
Сварка пластинчатыми электродами используется для соединения массивных деталей, имеющих прямоугольное сечение, если длина шва и толщина металла не намного отличаются друг от друга.
Сварка плавящимся мундштуком применяется для соединения массивных деталей, если сечение их отличается от прямоугольного, например имеет трапецеидальную форму или другую.
Сущность способа электрошлаковой сварки состоит в том, что расплавленный флюс образует так называемую шлаковую ванну, которая является проводником электрического тока. При прохождении тока через расплавленный флюс - шлак выделяется тепловая энергия, которая поддерживает температуру шлака около 1730˚С, т. е. выше температуры плавления основного (свариваемого) и электродного металла. В результате электродная проволока, подаваемая с определенной скоростью в зону сварки, и кромки основного (свариваемого) металла расплавляются, вследствие чего создается металлическая ванна, после затвердевания которой образуется шов.
Расплавленный основной металл, шлаковая и металлическая ванна удерживаются от вытекания специальными формирующими устройствами - подвижными (медными водоохлаждаемыми ползунами) или неподвижными (медными водоохлаждаемыми шинами).
Как видно из схемы рис. 2.2, при любой толщине металла сварка выполняется за один проход, что при изготовлении конструкций из толстого металла во много раз повышает производительность по сравнению с любым другим способом сварки.
Поэтому областью рационального применения является получение сварных соединений на металле большой толщины.
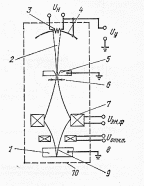
Электроннолучевая сварка. С
хема процесса электроннолучевой сварки показана на рис. 2.3.
Рис. 2.3. Схема процесса электроннолучевой сварки:
1–изделие, 2–электронный луч, 3–катод, 4–прикатодный управляющий электрод, 5–анод, 6–кроссовер, 7–магнитная линза, 8–система отключения луча, 9–сварочная ванна, 10–вакуумная камера; Uн–напряжения накала катода; Uу–ускоряющее напряжение; Uэм.ф–напряжение электромагнитной фокусировки; Uоткл–напряжение отклоняющей системы.
Катод 3 электронной пушки, нагретый проходящим током или электронной бомбардировкой до высокой температуры (вольфрамовый катод до 2130 - 2430˚С, эмитирует электроны, которые, попадая в электрическое поле, создаваемое прикатодным электродом электростатической фокусировки 4, направляются в виде пучка к аноду 5. Электрическое поле высокой напряженности разгоняет электроны до больших скоростей. Пройдя через центральное отверстие в аноде, пучок имеет наименьшее сечение (кроссовер 6), но начинает расходиться и для его фокусировки на изделии 1 используют электромагнитные линзы 7, представляющие собой плоские катушки, создающие магнитное поле высокой напряженности. В результате взаимодействия электронов с магнитным полем осуществляется электромагнитная фокусировка пучка электронов, причем фокусное расстояние рассчитывается так, чтобы сфокусировать пучок на поверхности изделия, либо на некотором заглублении.
Корректировка положения луча относительно кромок свариваемого металла выполняется с помощью магнитной отклоняющей системы 8.
При
электроннолучевой сварке используют
электронные пучки мощностью от 2 кВт
(например, A852.18) до 60 кВт (ПЛ-105, ЭЛА-60/60),
позволяющие
выполнять сварку различных металлов и
сплавов толщиной до 80 - 100 мм и более.
Для достижения и поддержания необходимого рабочего вакуума в камерах используют соответствующие откачные (вакуумные) системы. Эти системы комплектуются механическими насосами, создающими предварительное разрежение 1,33-1,33∙10-1 и высоковакуумными пароструйными насосами, обеспечивающими разрежение в камерах в пределах 1,33∙10-1-1,33∙10-4 Па.
4. Лазерная сварка. При лазерной сварке в основном применяют газовые СО2 - лазеры непрерывного действия, в которых рабочим телом служат смеси газов в соотношении 1 СО2; 20 N2; 20 Не.
На рис. 2.4 приведена принципиальная схема технологического СО2 - лазера с замкнутым циклом, в котором векторы скорости потока прокачиваемого газа, электрического поля и на- правления лазерного луча взаимно перпендикулярны. Такие лазеры возбуждаются электрическим разрядом.
Типичной конструкцией лазера, представленного на рис. 2.4, является камера, ограниченная с двух сторон строго параллельными зеркалами 6 - непрозрачным (слева) и полупрозрачным (справа), формирующими лазерный луч 7.
Поперек разряда с помощью компрессора или вентилятора 2 прокачивается и охлаждается в холодильнике 8 газовая смесь; газовый тракт условно изображен стрелками 1.
Рис.
2.4. Принципиальная схема технологического
CO2-лазер
с поперечной прокачкой газовой смеси:
1–газовый тракт, 2–вентилятор, 3–холодильник, 4,5–электроды, 6–непрозрачное и полупрозрачное зеркала, 7–лазерный луч, 8,9–линзы оптической системы, 10–свариваемое изделие, 11–пульт управления, 12,13–измерители мощности
В
результате электрического разряда
между электродами 4 и 5, расположенными
в камере, возникают быстрые электроны,
переводящие газовые молекулы в
возбужденное состояние. Возвращаясь в
исходное состояние, эти молекулы образуют
кванты света, который, проходя через
оптическую систему 6, 8 и 9, фокусируется
на свариваемом изделии 10, расположенном
на сварочном манипуляторе с пультом
управления 11 и при высокой концентрации
энергии осуществляется локальное
расплавление кромок свариваемого
изделия. Измеритель мощности проходного
12 и калориметрического типа 18 позволяет
контролировать параметры процесса.
Большим достоинством способа лазерной сварки является возможность ведения процесса как в вакууме, так и в защитных тазах, что позволяет получить высококачественные сварные соединения не только на обычных углеродистых и низколегированных сталях, но и на легированных сталях, а также цветных металлах и специальных сплавах.
5. Газовая (газокислородная) сварка. При газовой сварке кромки металла, подлежащие сварке, нагреваются до расплавления теплом экзотермической реакции, протекающей в пламени газовой горелки между горючим газом (как правило, ацетиленом) и кислородом (рис. 2.5).
Рис
2.5. Газовая сварка:
а–схема процесса, б–распределение температуры в пламени; 1–баллон с кислородом, 2–баллон с ацетиленом, 3–сварочная горелка, 4–присадочная проволока, 5–свариваемое изделие, 6–шланги для подвода газов к горелки
Ацетилен (С2Н2) получают из карбида кальция при взаимодействии его с водой:
СаС2 + 2Н2О = С2Н2 + Са(ОН)2.
Ацетилен сжигается в смеси с кислородом посредством специальной горелки.
Процесс подготовки ацетилено-кислородной смеси к горению и самого горения можно разделить на три стадии:
1-ая стадия: подготовка горючего к сгоранию (распад углеводорода)
С2Н2 → 2С + Н2 + 226 000 кДж/моль.
2-ая стадия: образование СО и Н2 (окисление углерода)
С2Н2 + О2 → 2С + Н2 + О2 = 2СО + Н2 + 2 472 200 кДж/моль.
3-ая стадия: окончательное окисление оксида углерода и водорода:
2СО + О2 → СО2 + 571 000 кДж/моль;
Н2 + 0,5О2 → Н2О + 242 000 кДж/моль.
Строение пламени при горении ацетилена в смеси с кислородом характеризуется наличием трех зон: ядра (I), средней зоны (II) и факела (III) (рис. 2.5, б). Наивысшая температура (2730 - 3230˚С) имеет место в районе II зоны. Поэтому при сварке горелку располагают так, чтобы ядро пламени касалось поверхности: сварочной ванны.
Газовая сварка применяется как при изготовлении изделий из тонколистовой стали, так и при сварке чугуна (при ремонтных работах) и некоторых цветных металлов и сплавов на их основе.
6.
Т
ермитная
сварка осуществляется за счет тепловой
энергии, выделяемой при обменной реакции
компонентов термита - смеси оксидов
железа ( 80 %) и измельченного алюминия
( 20): 3Fe3О4 + 8А1 = 4А12О3 + 9Fe + Q1
Fe2O3 + 2А1 = А12О3 + 2Fe + Q2
где Q1 ≈ 3344 кДж/кг; Q2 ≈ 3553 кДж/кг.
Термит
загружается в специальный тигель (рис.
2.6), сообщающийся с формой, облегающей
свариваемый стык (рельсов, стальных
приводов, гребных валов судов и других
изделий), и поджигается за счет магниевого
или электрического запала.
Рис. 2.6. Схема процесса термитной сварки
В результате горения перегретый металл затекает в стык (рис. 2.6, а и б), а образовавшийся шлак выпускают в специальный сосуд - приставку (рис. 2.6, в).
К
роме
варианта термитной сварки плавлением,
в некоторых случаях используют вариант
сварки давлением, отличающийся тем, что
разогретые и оплавленные шлаком кромки
соединяемых деталей сдавливают
специальным приспособлением.