
№11033 методичка
.pdf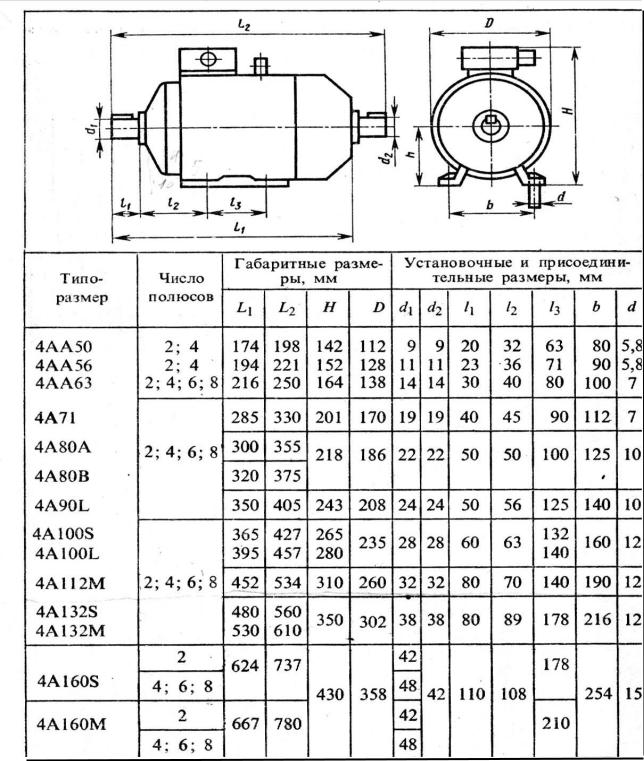
Таблица 5
Основные размеры электродвигателей
Данный раздел расчётов необходимо завершить указанием выбранного электродвигателя. Например: «Выбран электродвигатель 4А 112М4 УЗ ГОСТ
19523-81 с мощностью Рдв = 5,5 кВт с синхронной частотой вращения вала электродвигателя nдв = 1500 об/мин.
11

2.2. Определение передаточного числа редуктора
После выбора электродвигателя определяют передаточное число редуктора
|
|
|
|
|
|
|
|
u |
ред |
|
|
|
nдв |
n1 |
(2.6) |
|
|
|||||||
|
|
|
|
|
|
|
|
|
|
uо.п. nв ых |
|
n2 |
|
|
|
|||||||||
|
|
|
|
|
|
|
|
|
|
|
|
|
|
|
|
|||||||||
где |
nдв |
- частота вращения вала двигателя под нагрузкой (асинхронная); |
||||||||||||||||||||||
n1 |
= nдв / uо.п. – частота вращения входного (быстроходного)вала редуктора; |
|||||||||||||||||||||||
n2 |
= nвых – частота вращения выходного (тихоходного) вала редуктора. |
|||||||||||||||||||||||
|
|
Передаточное число редуктора необходимо согласовать со стандартным |
||||||||||||||||||||||
значением, приведенным в табл.6; при этом отклонение |
u не |
должно |
||||||||||||||||||||||
превышать 4% для цилиндрических передач и 2,5% для конических [4, 5, 6]. |
||||||||||||||||||||||||
|
|
|
|
|
|
|
|
|
|
|
|
|
|
|
|
|
||||||||
|
|
|
|
u |
|
|
uст u ред |
|
100% [ u] . |
(2.7) |
|
|||||||||||||
|
|
|
|
|
|
|||||||||||||||||||
|
|
|
|
|
|
ucт |
|
|
||||||||||||||||
|
|
|
|
|
|
|
|
|
|
|
|
|
|
|
|
|
|
|
|
|
|
|
||
|
|
|
|
|
|
|
|
|
|
|
|
|
|
|
|
|
|
|
|
|
Таблица 6 |
|||
|
|
|
Стандартные передаточные числа u по ГОСТ 2185-66 |
|
|
|||||||||||||||||||
|
1 ряд |
1,0 |
1,25 |
|
1,6 |
2,0 |
|
|
2,5 |
|
3,15 |
4,0 |
5,0 |
6,3 |
8,0 |
|
10,0 |
|
||||||
|
2 ряд |
1,12 |
1,4 |
|
1,8 |
2,24 |
|
2,8 |
3,55 |
4,5 |
5,6 |
7,1 |
9,0 |
|
11,2 |
|
||||||||
Примечание. 1-ый ряд предпочтителен 2-ому. |
|
|
|
|
Если погрешность превышает стандартное значение, то следует принять двигатель той же мощности, но с другой частотой вращения, либо изменить передаточное число открытой передачи (в допустимых пределах) и повторить расчеты.
2.3. Определение мощности и вращающих моментов на валах
Частота вращения входного вала редуктора n1 = nдв / uо.п .
Частота вращения выходного вала редуктора определяется с учетом
принятого стандартного передаточного числа uст
n2 n1
uст
Мощности (кВт), передаваемые валами, определяются с учетом КПД составляющих звеньев кинематической цепи (см. рис.4):
12
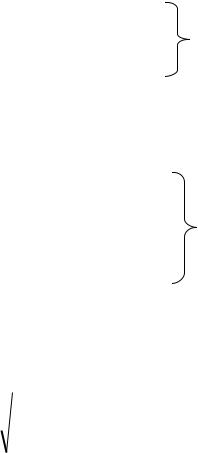
Р1 = Рдв ∙ ηоп ∙ ηп
Р2 = Р1∙ ηзп∙ ηп ∙ηм |
(2.8) |
Вращающие моменты ( Н∙м) на валах редуктора могут быть определены по следующим зависимостям:
|
|
P |
|
|
для входного вала - |
T1 9550 |
.1 |
, |
(2.9) |
|
||||
|
|
n1 |
|
для выходного вала - |
T 9550 |
P2 |
|
|
|||
2 |
n2 |
||
|
|
||
Далее производится |
предварительный расчет диаметров валов по |
заниженным допускаемым напряжениям, т.е. считая, что вал работает только на кручение, без учета изгиба:
|
|
|
16 Т |
103 |
|
|
|
|
3 |
|
i |
|
|
|
|
di |
|
|
кр |
(2.10) |
|||
|
|
||||||
|
|
|
|
|
|
где Тi – крутящий момент, передаваемый валом, Н. м;
[τкр]– допускаемые напряжения на кручение; [τкр]=15…20 МПа [3, c.161].
Полученные значения диаметров валов редуктора следует округлить до ближайшего большего значения из ряда нормальных линейных размеров по ГОСТ 6636-69 [1, с. 481]. Для удобства дальнейших расчётов найденные параметры редуктора сводятся в таблицу:
№ вала |
u ред |
ni , об/мин |
Рi , кВт |
Т, Н∙м |
d i , мм |
1 |
|
|
|
|
|
2 |
|
|
|
|
|
3. ВЫБОР МУФТ
Основными параметрами для выбора муфт служат диаметры выходных концов соединяемых валов и вращающие моменты.
Затем, для обеспечения соединения вала электродвигателя с быстроходным валом редуктора стандартной муфтой, необходимо выполнить
13

следующее условие – разница диаметров соединяемых валов должна отличаться не более чем на 20%.
Исходя из этого условия и ориентировочно найденного диаметра под
муфту по (2.10), принимают окончательное значение диаметра вала равным
ближайшему значению отверстия стандартной муфты. Кроме этого необходимо
проверить следующее: допускаемый крутящий момент выбранной муфты
должен быть больше или равен крутящему моменту вала.
Для соединения вала электродвигателя с быстроходным валом редуктора
может быть рекомендована муфта упругая втулочно-пальцевая МУВП ГОСТ
21424-93 (см. ниже). Эта муфта, за счёт резиновых гофрированных втулок насаженных на пальцы, соединяющие полумуфты, обладает упругими свойствами, необходимыми для предотвращения поломки деталей, которые могут возникнуть, например, при включении машины, т.к. пусковой момент электродвигателя превышает номинальный.
.
Рис.5. Муфта упругая втулочно-пальцевая
Для соединения тихоходного вала редуктора с валом исполнительного механизма машины могут быть рекомендованы компенсирующие муфты – цепные ГОСТ 20742-81 или зубчатые ГОСТ 5006-94.
Эти муфты позволяют компенсировать радиальные и угловые смещения валов, а зубчатые – также и осевые (венец зубчатой обоймы шире венца полумуфты), которые могут возникнуть из-за тепловых или силовых деформаций, или из-за неточности сборки, или из-за деформируемого основания, на котором находятся узлы машины, например на раме автомобиля и т.д. (Здесь выполнения условия – «разница диаметров соединяемых валов
должна отличаться не более чем на 20%» - не требуется).
14
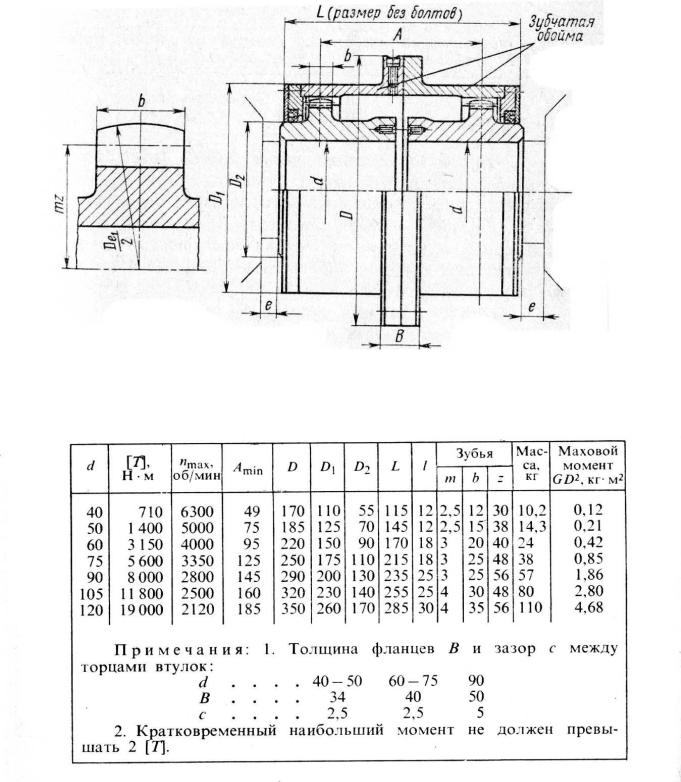
Зубчатые муфты ГОСТ 5006-94
15
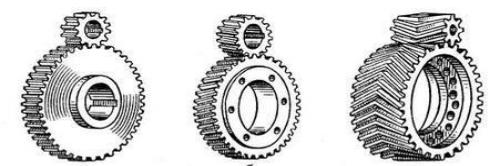
4.РАСЧЕТ ПЕРЕДАЧИ РЕДУКТОРА
4.1.Расчет цилиндрической зубчатой передачи
|
|
в |
|
с |
а |
|
|
||
|
|
|
|
|
|
|
|
|
|
Рис.6. Цилиндрическая передача а) – прямозубая, в) - косозубая, с) - шевронная
4.1.1. Выбор материалов, термообработки и допускаемых
напряжений
При выборе материалов зубчатых колес следует учитывать назначение передачи, условия эксплуатации и требования к габаритным размерам,
возможную технологию изготовления колес. Зубчатые колеса редукторов в большинстве случаев изготавливаются из сталей, подвергнутых термическому упрочнению. В зависимости от твердости материала стальные зубчатые колеса разделяются на две группы: с твердостью НВ ≤ 350 (ТО: нормализация или улучшение) и с твердостью НВ > 350 (ТО: закалка ТВЧ, цементация,
азотирование и др.). Для редукторов, к размерам которых не предъявляют особых требований, редукторов индивидуального и мелкосерийного производства, назначают стали первой группы. Для лучшей приработки рекомендуется назначать материал шестерни и колеса с соотношением твердости: (Шестерней условно называют колесо меньших размеров,
участвующее в зацеплении).
НВ1 = НВ2 + (20…70) – при твердости зубьев НВ ≤ 350 и
НВ1 = НВ2 + (25…30) – при твердости зубьев НВ > 350,
где НВ1 – твердость шестерни;
НВ2 – твердость колеса.
16
Необходимую разность в твердости материалов колес можно получить,
применяя как различные, так и одинаковые марки стали для шестерни и колеса,
но с различной термообработкой.
|
|
|
|
Таблица 7 |
||
Рекомендуемые сочетания материалов зубчатых колес [ 1, с.16] |
|
|||||
Шестерня |
|
Колесо |
|
Область |
|
|
Марка стали |
термообработка |
Марка стали |
термообработка |
применения |
||
40 |
|
35 |
|
Основное |
|
|
45 |
|
35Л |
|
|
||
|
Нормализация, |
применение |
для |
|||
50 |
|
35 |
||||
Нормализация, |
улучшение, |
большинства |
||||
45Л |
||||||
|
улучшение, |
закалка, закалка |
металлургических, |
|||
35Х |
|
|||||
закалка, |
50 |
ТВЧ, для |
подъемно- |
|
||
40Х |
|
|||||
закалка ТВЧ, |
40ГЛ |
стального литья |
транспортных |
|||
45Х |
||||||
НВ ≤ 350 |
|
и нормализации |
машин и |
машин |
||
|
35Х |
|||||
40ХН |
|
НВ ≤ 350 |
непрерывного |
|||
|
40Х |
|||||
30ХГС |
|
|
транспорта |
|
||
|
40ГЛ |
|
|
|||
|
|
|
|
|
||
20Х |
|
|
|
Особо |
|
|
Цементация и |
|
Цементация и |
ответственные |
|||
12ХН3А |
20Х |
|||||
закалка |
закалка |
быстроходные |
||||
20ХН2М |
12ХН3А |
|||||
НВ > 350 |
НВ > 350 |
передачи станков |
||||
40ХН2МА |
18ХГТ |
|||||
40…63 НRС |
40…63 НRС |
и транспортных |
||||
16ХГТ |
|
|||||
|
|
|
машин |
|
||
|
|
|
|
|
|
|
|
|
|
Таблица 8 |
|
|
|
Механические свойства сталей [1, с.17] |
|
|
||
|
|
Твердость по HRC |
Предел |
Предел |
Термическая |
|
|
Марка |
прочности |
текучести σТ, |
|||
|
или по НВ |
обработка |
||||
|
|
σВ, МПа |
МПа |
|||
|
|
|
|
|
||
|
35 |
140 … 187 |
470 |
235 |
Н |
|
|
|
195 … 212 |
685 |
345 |
У |
|
|
40 |
152 … 207 |
490 |
245 |
Н |
|
|
|
187 … 217 |
580 |
340 |
У |
|
|
45 |
167 … 217 |
570 |
285 |
Н |
|
|
|
180 … 236 |
735 |
390 |
У |
|
|
50 |
180 … 229 |
590 |
300 |
Н |
|
|
|
228 … 255 |
735 |
520 |
У |
|
|
|
40 … 66HRC |
|
|
ТВЧ |
|
|
35Х |
190 … 220 |
685 |
440 |
Н |
|
|
|
220 … 200 |
735 |
490 |
У |
|
|
40Х |
200 … 230 |
685 |
440 |
Н |
|
|
|
215 … 285 |
795 |
490 |
У |
|
|
|
45 … 50 HRC |
980 |
785 |
З |
|
|
|
40 … 56 HRC |
|
|
ТВЧ |
|
|
|
|
|
|
|
|
|
|
|
17 |
|
|
|

окончание таблицы 8
45Х |
230 … 280 |
835 |
640 |
У |
35ХМ |
241 … 269 |
880 |
785 |
У |
|
38 … 55 HRC |
|
|
ТВЧ |
40Х |
220 … 250 |
735 |
550 |
Н |
|
241 … 295 |
785 |
570 |
У |
|
48 … 54 HRC |
980 |
785 |
З |
ЗОХГС |
215 … 250 |
785 |
635 |
Н |
|
235 … 280 |
880 |
610 |
У |
20Х |
52 … 62 HRC |
640 |
390 |
Ц |
12ХНЗА |
56 … 63 HRC |
920 |
700 |
Ц |
Примечание: Н – нормализация, У – улучшение, З – закалка, Ц – цементация, ТВЧ – закалка токами высокой частоты.
Допускаемые контактные напряжения для стальных зубчатых колес
σ |
|
|
σH lim b |
K |
|
Z |
|
Z |
|
H i |
|
HL |
R |
(4.1) |
|||||
|
|
[ sH ] |
|
V |
|||||
|
|
|
|
|
|
|
|
||
Допускаемые напряжения изгиба |
|
|
|
|
|
|
σ |
|
|
σF lim b |
|
K |
|
K |
|
|
|
|
|
|
|
|
F i |
[ sF ] |
|
FL |
Fс |
|
(4.2) |
|
|
||||||
|
|
|
|
|
|
|
|
|
|
||||||
|
|
|
|
|
|
|
|
|
|
|
|
|
|
|
|
где H limb , F limb – базовые пределы контактной и изгибной выносливости |
|||||||||||||||
поверхности зубьев; SH , SF – коэффициенты безопасности. |
|
|
|
||||||||||||
|
|
|
|
|
|
|
|
|
|
|
|
|
Таблица 9 |
||
Пределы базовой выносливости и коэффициенты безопасности [3, с. 34] |
|||||||||||||||
|
|
|
|
|
|
|
|
|
|
|
|
|
|
|
|
Термическая |
Твердость |
|
Стали |
|
|
|
σH lim b |
|
[SH] |
σF lim b |
|
[SF] |
|
||
обработка |
зубьев |
|
|
|
|
|
|
|
|
||||||
|
|
|
|
|
|
|
|
|
|
|
|
|
|
||
|
|
|
35,40,45, |
|
|
|
|
|
|
|
|
|
|
|
|
Нормализация, |
< 350 НВ |
50,40Х, |
|
|
2НВ+70 |
|
1,8 НВ |
|
|
|
|||||
улучшение |
|
|
40ХН, |
|
|
1,1 |
|
|
|
|
|||||
|
|
|
|
|
|
|
|
|
|
|
|
||||
|
|
|
35ХМ |
|
|
|
|
|
|
|
|
|
1,75 |
|
|
Объемная |
40…56 HRC |
40Х,40ХН |
|
|
18 HRC+150 |
|
500…600 |
|
|
|
|||||
закалка |
35ХМ |
|
|
|
|
|
|
|
|||||||
|
|
|
|
|
|
|
|
|
|
|
|
|
|||
|
|
|
|
|
|
|
|
|
|
|
|
|
|
|
|
Закалка ТВЧ |
|
|
12ХНЗА, |
|
|
17HRC+200 |
|
500 |
|
|
|
||||
Цементация и |
|
|
20ХН2М, |
|
|
|
|
|
|
1,2 |
|
|
|
|
|
> 56 HRC |
40ХН2МА, |
|
|
|
23HRC |
|
|
710…750 |
|
1,55 |
|
||||
закалка |
|
18ХГТ |
|
|
|
|
|
|
|
||||||
|
|
|
|
|
|
|
|
|
|
|
|
|
|
||
|
|
|
|
|
|
|
|
|
|||||||
Примечание: Для |
проката SF |
1,9...2,0 , для |
литья SF 2,1...2,2 . |
|
|
|
|
||||||||
|
|
|
|
|
18 |
|
|
|
|
|
|
|
|
При постоянном режиме работы передачи: KH L = KF L = ZR = Z V = 1,0;
KFc – коэффициент, учитывающий реверсивность работы передачи и твердость поверхностей зубьев; при отсутствии реверса KFc = 1,0; при реверсивной нагрузке KFc = 0,7…0,8 [7, с. 17-18].
Поскольку долговечность зубчатой передачи определяется контактной прочностью зубьев, а прочность зубьев колеса ниже прочности зубьев шестерни, то проектный расчет выполняют по σН2. Проверочные расчеты изгибной прочности зубьев шестерни и колеса выполняют по σF1, σF2.
По формулам (4.1) и (4.2) необходимо определить допускаемые напряжения для шестерни и для колеса - H1 , H 2 , F1 , F 2 .
4.1.2. Определение расчетного крутящего момента
Проектный расчет зубчатой передачи можно выполнять как по крутящему моменту на входном, так и на выходном валу. Расчётные крутящие моменты на выходном (тихоходном) валу, Н∙м:
T2H T2 KH |
|
KH |
; |
T2F T2 KF |
KF , |
(4.3) |
|
|
v |
|
v |
|
|
где Т2 - номинальный крутящий момент на тихоходном валу (см. раздел 2). |
||||||
KH , KF коэффициент неравномерности распределения нагрузки по |
длине контактных линий. Если колёса полностью прирабатываются (НВ ≤ 350),
то можно принять |
KH , KF 1. |
K H V , K F V |
коэффициенты динамичности, зависящие от окружной |
скорости в зацеплении и от степени точности изготовления. Значения приведены в табл.10.
Для редукторов общего назначения можно предварительно принять 8-ю
степень точности, как более экономичную; окончательное решение принимается после расчета геометрических параметров и фактической окружной скорости в зацеплении.
19

|
|
|
|
|
|
Таблица 10 |
|
Значение коэффициентов динамичности КНV [4, с.19] |
|
||||
|
|
Окружная скорость, м/с |
|
|
KHV , KFV |
|
Степень |
|
Цилиндрическая |
Коническая |
|
||
точности |
|
|
|
|||
|
|
|
|
|
|
|
|
|
прямозубая |
косозубая |
прямозубая |
|
|
7 |
|
до 10 |
до 15 |
до 5 |
|
1,2 |
|
до 6 |
до 10 |
до 2 |
|
1,4 |
|
8 |
|
|
||||
|
|
|
|
|
|
4.1.3. Расчет основных геометрических параметров цилиндрической зубчатой передачи
1). Ориентировочное значение межосевого расстояния аw определяют из условия контактной выносливости.
Межосевое расстояние, мм [1, с.21 ]
|
|
|
|
|
|
T2H |
|
|
|
|
|
|
|
|
|
|
|
|
|
|
|
|
|||
aw K1 u ред |
1 |
3 |
|
|
u |
2 |
|
2 , |
(4.4.) |
|||
|
|
|
|
|||||||||
|
|
|
|
|
ba |
|
ред |
H 2 |
|
где К 1 = 495 - для передач с прямыми зубьями;
К 1 = 430 - для передач с косыми и шевронными зубьями.
Коэффициент ширины зубчатого венца по межосевому расстоянию Ψba
Таблица 11 Значение коэффициента ширины зубчатого венца колеса [1, с.20]
|
|
|
Вид передачи |
|
Коэффициент |
|
Прямозубая или |
|
|
Шевронная |
|
|
|||||||||||||
|
|
|
|
ширины |
|
|
|
|
косозубая |
|
|
|
|
|
|
||||||||||
|
|
|
|
|
|
|
|
|
|
|
|
|
|
|
|
|
|
|
|
||||||
|
|
|
Цилиндрическая |
b a |
|
bw |
|
|
0,2; 0,25; 0,315; |
|
|
0,4; |
0,5; |
|
|
||||||||||
|
|
|
aw |
|
0,4 |
|
|
|
|
|
|
|
|||||||||||||
|
|
|
|
|
|
|
|
|
|
|
|
|
|
|
|
|
|
|
|
|
|||||
|
|
|
|
|
|
|
|
|
|
|
|
|
|
|
|
|
|
||||||||
|
|
Вычисленное значение межосевого расстояния aw необходимо сравнить |
|||||||||||||||||||||||
со стандартным рядом и принять ближайшее стандартное (табл. 12). |
|
|
|
|
|||||||||||||||||||||
|
|
|
|
|
|
|
|
|
|
|
|
|
|
|
|
|
|
|
|
|
Таблица 12 |
||||
|
|
|
Межосевое расстояние зубчатых передач по ГОСТ 2185-66 |
|
|
|
|
||||||||||||||||||
|
aw |
|
I ряд |
80 |
100 |
|
125 |
|
|
160 |
|
200 |
|
250 |
|
315 |
|
400 |
|
500 |
|
|
|||
|
|
II ряд |
90 |
112 |
|
140 |
|
|
180 |
|
225 |
|
280 |
|
355 |
|
450 |
|
660 |
|
|
||||
|
|
|
|
|
|
|
|
|
|
|
|
|
|||||||||||||
П р и м е ч а н и е . Первый ряд следует предпочитать второму. |
|
|
|
|
|
|
|
|
|||||||||||||||||
|
|
2). Значения модуля зубчатых колес вычисляют по соотношению |
|||||||||||||||||||||||
|
|
|
|
|
|
m = (0,01 …0,02)·aw , |
|
|
|
|
|
|
(4.5) |
|
|
||||||||||
|
|
после чего принимают стандартное значение по ГОСТ 9563-80. |
|
|
|
|
|||||||||||||||||||
|
|
|
|
|
|
|
|
|
|
|
|
20 |
|
|
|
|
|
|
|
|
|
|
|
|
|