
pract-2788
.pdfк) разрабатываем чертеж модели, который будет отличаться увеличением размеров по отношению к размерам отливки на величину усадки (для стали 2 %) (рис. 3.16);
л) разрабатываем чертеж модельной плиты. Размеры модельной плиты будут зависеть от: количества моделей на модельной плите; габаритных размеров модели и литниковой системы; расстояний от кромки модели до стенок опоки и между кромками моделей, которые выбираются от массы отливки (табл. 3.12, рис. 3.17);
м) разрабатываем чертеж стержневого ящика, размеры которого будут определяться количеством изготовляемых стержней, их размерами и конструктивными размерами и материалом стержневого ящи-
ка (рис. 3.18);
н) разрабатываем чертеж литейной формы (рис. 3.19). Размеры опоки в плане будут соответствовать размерам модельной плиты, а высота верхней и нижней опоки будут зависеть от высоты модели в форме и толщины формовочной смеси между верхней или нижней кромкой модели и верхом или низом опоки, соответственно. Эта толщина формовочной смеси зависит от массы отливки (табл. 3.11).
Таблица 3.11
Допустимые расстояния между моделями и элементами формы
Вес |
|
Допустимые расстояния, мм |
|
|||
отлив- |
От вер- |
От низа |
От мо- |
От |
Между |
От |
ки, кг |
ха мо- |
модели |
дели до |
кромки |
кром- |
кромки |
|
дели |
до низа |
стенок |
стояка |
ками |
шлако- |
|
до вер- |
опоки |
опоки |
до |
моде- |
ул. до |
|
ха опо- |
|
|
стенки |
лей |
кромки |
|
ки |
|
|
опоки |
|
модели |
До 5 |
40 |
40 |
30 |
30 |
30 |
30 |
5-10 |
50 |
50 |
40 |
40 |
40 |
30 |
10-25 |
60 |
60 |
40 |
50 |
50 |
30 |
25-50 |
70 |
70 |
50 |
50 |
60 |
40 |
50-100 |
90 |
90 |
50 |
60 |
70 |
50 |
100-250 |
100 |
100 |
60 |
70 |
100 |
60 |
250-500 |
120 |
120 |
70 |
80 |
- |
70 |
49
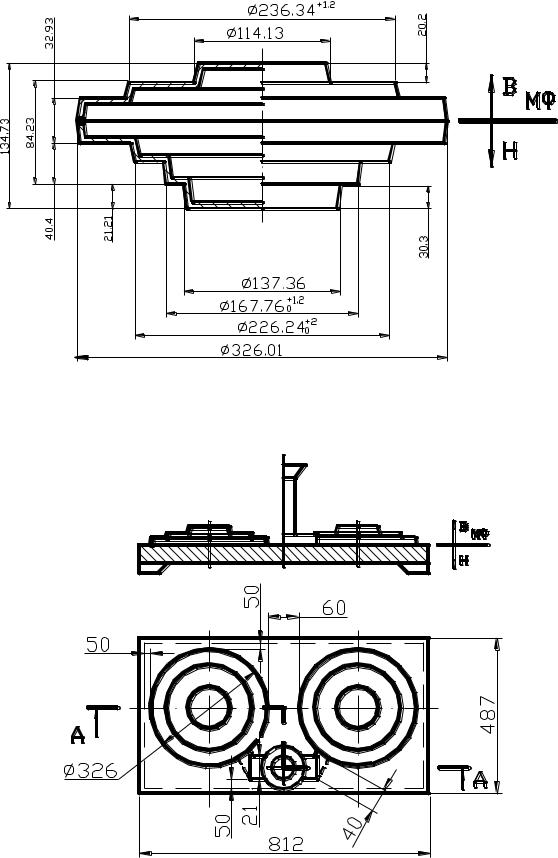
Не указанные литейные радиусы 3-5мм |
Рис. 3.16. Модель отливки крышки насоса |
Рис. 3.17. Модельная плита с моделями
50
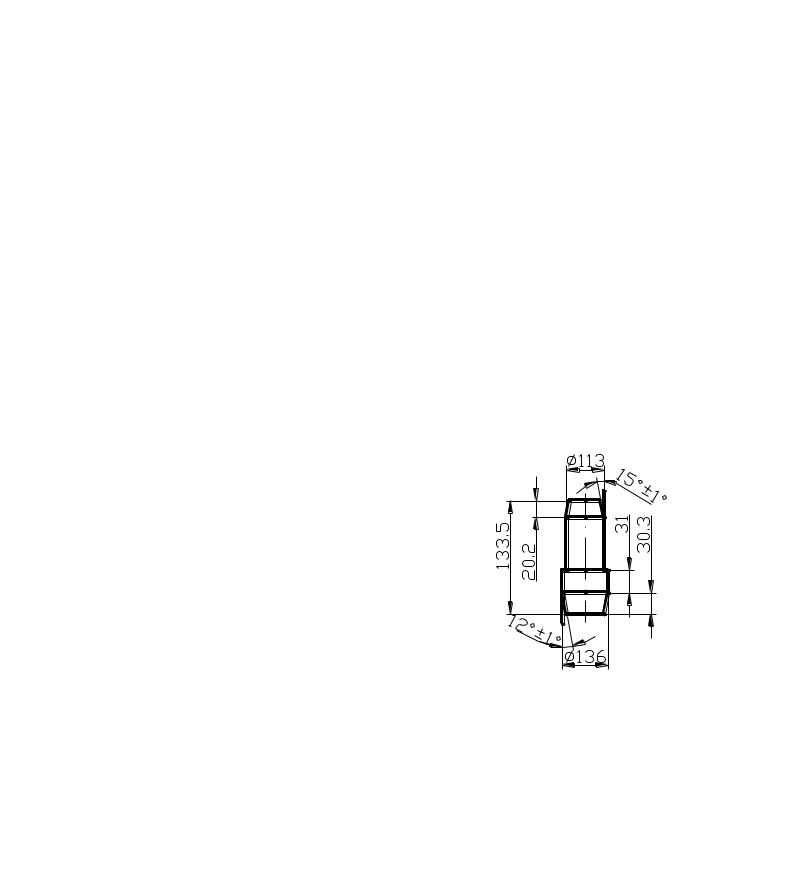
а |
б |
Рис. 3.18. Стержневой ящик (а) и стержень (б)
51
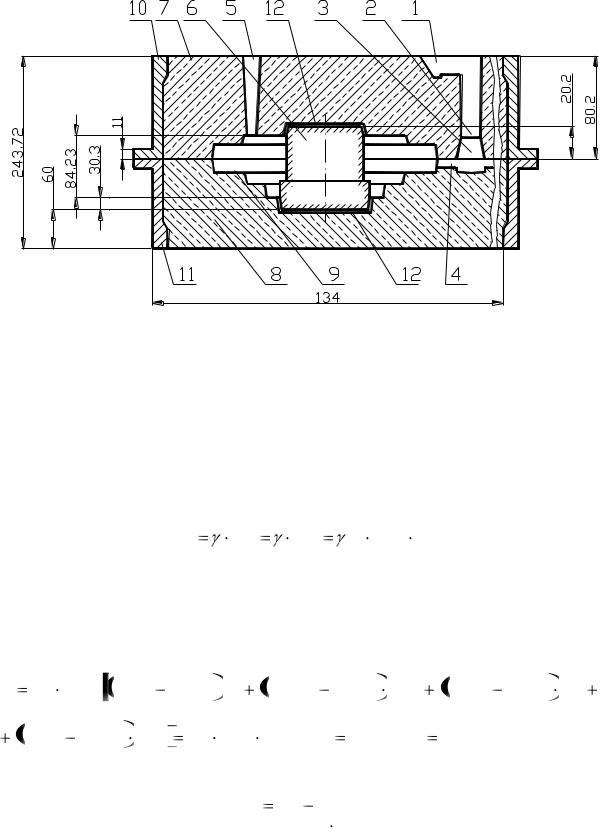
Рис. 3.19. Литейная форма в сборе
2.3. Расчет размеров литниковой системы
Для определения размеров литниковой системы при получении отливки крышки (рис. 3.17) необходимо рассчитать:
а) массу отливки:
Gот Vот УVi Уdi 2 hi ,
4
где Vот, Vi, di, hi – объем отливки, объемы частей отливки, диаметры и высоты частей отливки;
= 0,0078 кг/см3 – плотность стали в жидком состоянии;
G |
7,8 |
3,14 |
23,4 2 |
11,32 |
1,6 |
|
32,282 |
11,32 |
2,74 |
22,4 2 |
11,32 |
0,9 |
|||
4 |
|||||||||||||||
|
|
|
|
|
|
|
|
|
|
|
|
|
|
||
|
16,6 2 |
13,6 2 3,1 |
7,0 |
|
3,14 |
3794,312 2084975г |
20,85 кг; |
|
|||||||
|
4 |
|
|||||||||||||
|
|
|
|
|
|
|
|
|
|
|
|
|
|||
|
|
|
|
|
|
|
|
|
Р2 |
|
|
|
|
||
|
б) статический напор Н р |
Нс |
|
, |
|
|
|
|
|||||||
|
|
|
|
|
|
||||||||||
|
|
|
|
|
|
|
|
|
2 С |
|
|
|
|
52
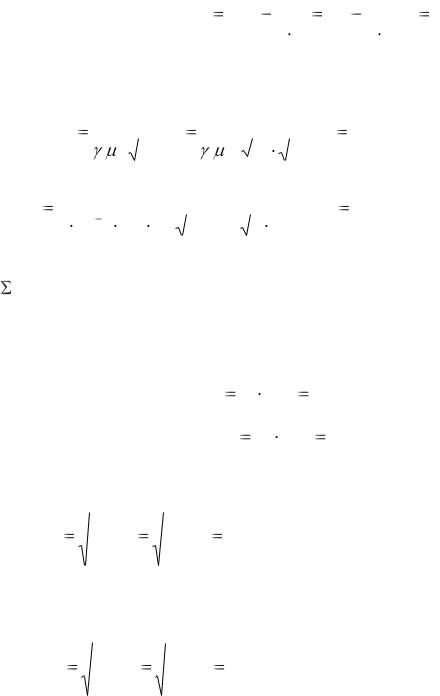
гдн Нст – высота от верхнего уровня металла в чаше стояка до верхнего уровня металла в питателе, в соответствии со схемой рис. 3.16. Нст
=7,6 см;
Р – высота отливки от места подвода металла в форму. Р = 1,6 см; С – высота отливки С = 8,34 см.
Следовательно, Н р Нст |
Р2 |
1,62 |
7,45 см. |
|
|
7,6 |
|
||
|
|
|||
|
2 С |
2 8,34 |
Сечение питателя определяем по формуле, приняв = 0,5; S =1,5
(табл. 12-18) [6].
УFn |
|
G |
|
|
|
|
|
G |
|||||||
|
|
|
|
|
|
|
|
|
|
|
|
|
|
||
|
|
|
|
|
|
|
|
|
|
|
|
|
|
||
t 2qHp |
|
|
|
S |
G |
|
2qHp |
||||||||
|
|
|
|
|
|
|
|||||||||
|
|
|
20,85 |
|
|
|
|
|
|
3,62 см. |
|||||
|
|
|
|
|
|
|
|
|
|
|
|
|
|
|
|
7 10 3 |
|
|
|
|
|
|
|
|
|
|
|
|
|||
0,5 1,5 |
20,85 |
2 |
4807,45 |
|
По рассчитанной суммарной площади сечения питателя ( Fn) определяем площадь сечения шлаковика (Fш) и стояка (Fст) из соотношения:
УFn : Fш : Fст = 1 : 1,1 : 1,2; |
откуда |
||
Fш = 1,1 УFn; |
Fш |
1,1 3,62 |
3,98 см. |
Fст = 1,2 УFn; |
Fст |
1,2 3,62 4,35 см. |
Размеры трапецеидального сечения питателя, шлаковика и стояка будут равны:
аn |
|
УFn |
|
3,62 |
|
3,389 |
см |
||
|
|
|
|
|
|
||||
|
|
|
|
|
|||||
0,315 |
0,315 |
|
|
вu = 1,1 х аn = 1,1 х 3,389 = 3,73 см hn = 0,3 х аn = 0,3 х 3,389 = 1,02 см
аш |
|
Fш |
|
3,98 |
|
2,1 |
см |
||
|
|
|
|
|
|
||||
0,935 |
0,935 |
|
|
вш= 0,7 аш= 0,7 х 2,1 = 1,44 см hш = 1,1 аш = 1,1 х 2,1 = 2,27 см
53
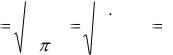
dст |
|
4Fст |
|
|
|
4 4,35 |
2,3 |
см |
|
|
|
3,14 |
|
||||||
|
|
|
|
|
|
Эскизы сечений элементов литниковой системы показываются на рис. 3.21.
2.3. Выбор формовочных, стержневых смесей, способа изготовления форм и стержней, сборка, заливка литейных форм, охлаждение, выбивка отливок форм, очистка, отделка и термическая их обработка
2.3.1. Выбор формовочных и стержневых смесей
Формовочные и стержневые смеси выбирают в зависимости от марки материала отливки, толщины стенок, способа формовки.
Литейные легированные стали имеют плохие литейные свойства: пониженную жидкотекучесть, значительную усадку (до 2,5 %), что приводит к образованию усадочных раковин, пористости и трещин. Для предупреждения трещин необходимо формы изготовлять из податливых формовочных и стержневых смесей. А высокая температура заливки (1550-1600 0С) требует применения формовочных и стержневых смесей с высокой огнеупорностью.
В качестве исходных материалов выбираем рекомендуемый типовой состав стержневой и формовочной смесей, применяемых при получении стальных отливок.
Состав стержневой смеси:
– оборотная смесь |
– 40 % |
– кварцевый песок |
– 45 % |
– огнеупорная глина |
– 8 % |
– связующее СП |
– 4-5 % |
– опилки древесины |
– 3 % |
Марка песка КО2А с содержанием глинистых до 12 %. Газопроницаемость смеси в сыром состоянии не менее 70 единиц.
Состав формовочной смеси:
– оборотная смесь |
– 97 % |
– кварцевый песок |
– 0,5-3 % |
– глина |
– 0,1-0,2 % |
– гранулированный уголь |
– 0,1 % |
54

– газопроницаемость не менее – 95 %
– влажность |
– 3 % |
– текучесть |
–70 % |
Для других марок и сплавов выбор формовочных и стержневых смесей осуществляем в соответствии [2, 3, 5, 7].
2.3.2. Выбор способа изготовления литейной формы и стержня
Применяют два способа изготовления форм и стержней: ручной и машинный. В данном случае имеем недостаточно большую серийность, но с учетом развития производства выбираем машинную формовку. Применение пескодувных машин позволяет совмещать две операции: наполнение и уплотнение. При изготовлении литейных форм и стержней на пескодувных машинах достигается большая скорость формообразования. Рациональным давлением надува при формообразовании является 4,5 6,5 Па. Время надува около 1 с. Этим параметром соответствуют пескодувный полуавтомат модели 912857. Цикловая производительность до 150 съемов в час.
Сборку литейных форм начинаем с установки нижней полуформы на заливочную площадку. Затем устанавливаем стержни в последовательности, указанной в технологической карте. После этого нижнюю полуформу накрывает верхней полуформой по направляющим штырям. Устойчивое положение стержней обеспечивается стержневыми знаками. Верхнюю полуформу с нижней скрепляем болтами, скобами или накладываем груз.
Заливку металла в полости литейной формы осуществляем из чайникового ковша, который от электродуговой плавильной печи с расплавленным металлом к месту заливки перевозят по монорельсовому пути. Температуру заливки металла назначаем на 100-150 0С выше температуры ликвидуса: при этой температуре обеспечивается оптимальное питание отливок и исключается сильное окисление, газонасыщение, и пригар на поверхности отливок, а так же исключается незаполнение полости формы металлом.
Охлаждение отливок в форме до выбивки осуществляем обдувом воздухом. После охлаждения отливок до температуры 450 0С [6] удаляем их из формы на вибрационных машинах (марки 0-15) [7] путем разрушения литейной формы. Пустые опоки отправляются на изготовление новых литейных форм, формовочная смесь – в смесеприготовительное отделение, а отливки – на отжиг, очистку. Одновременно удаляются и стержни. Очистку поверхности отливок от прига-
55
ра, формовочной и стержневой смеси осуществляем в дробеметных камерах. После очистки отливок газовой резкой удаляются литниковая система и прибыли, а затем их отправляют к обдирочным станкам, где зачищают остатки прибылей, литниковой системы, заливы.
Для снижения твердости поверхности отливки и снятия внутренних напряжений перед механической обработкой производится отжиг при 650-700 0С. После отжига отливки отправляются на механическую обработку.
Контрольные вопросы
1.Какие способы литья применяют для получения отливок?
2.В зависимости от каких факторов выбирают линию разъема?
3.Как выбирают линию разъема?
4.В зависимости от каких параметров выбирают уклоны?
5.Какие факторы влияют при назначении припусков на механическую обработку?
6.От каких показателей зависят размеры стержневых знаков?
7.Какие параметры оказывают влияние на размеры модельной плиты, стержневого ящика, литейной формы?
8.В зависимости от чего выбирают состав формовочных и стержневых смесей?
Литература
1.ГОСТ 3.1125-88 Единая система технологической документации. Правила графического выполнения элементов литейных форм и отливок.
2.ГОСТ 26645-85 Отливки из металлов и сплавов.
3.ГОСТ 3212-92 Комплекты модельные, стержневые знаки.
4.ГОСТ 2789-73. Шероховатость поверхности
5.Титов Н.Д. Технология литейного производства. – М.: Машино-
строение, 1974. – 471 с.
6.Емельянова Л.П. Технология литейной формы. – М.: Машино-
строение. 1979. – 240 с.
7.Справочник по чугунному литью /Под ред. Н.Г. Гиршовича. – М.: Машиностроение. 1978. – 758 с.
8.Матюхов В.Г. Техника безопасности в литейном производстве. – М.: Высшая школа, 1980. – 90 с.
56
9.Анисимов Н.Ф., Влачев В.Н. Проектирование литых деталей. – М.: Машиностроение, 1977. – 664 с.
57
Лабораторная работа № 4 ИЗУЧЕНИЕ ВЫРУБКИ ЛИСТОВОГО МАТЕРИАЛА
Цель работы: изучение технологического процесса вырубки, конструкции и работы вырубного штампа, принципа действия оборудования для листовой штамповки, освоение методики расчета усилия вырубки, экспериментальная проверка результатов расчета.
Содержание работы: изучение устройства и принципа действия оборудования и инструмента для разделительных операций холодной листовой штамповки; овладение навыками разработки технологического процесса вырубки; ознакомление с экспериментальными и теоретическими методами определения усилия вырубки.
Применяемое оборудование и материалы: лабораторный гид-
равлический пресс ПСУ-10, вырубной штамп, полоса из стали 10 КП толщиной 0,8-2 мм, машинное масло, штангенциркуль.
Порядок выполнения
1.Получить от учебного мастера полосовую заготовку, уточнить марку стали и ее механические свойства.
2.Расчетным путем определить усилие вырубки.
3.Ознакомиться с принципом действия вырубного штампа. Замерить диаметр пуансона, толщину заготовки.
4.Провести вырубку. Зафиксировать полученное усилие вырубки. Определить погрешность между экспериментальным и расчетным значением, усилия вырубки и сделать вывод по данной работе.
1. Общие сведения
Листовая штамповка – процесс обработки металлов давлением, при котором из листовой заготовки получается деталь плоской или пространственной формы. При этом толщина заготовки, как правило, не изменяется.
Все операции листовой штамповки делятся на разделительные и формоизменяющие. К разделительным относятся: отрубка, обрезка, вырубка, пробивка и др. Они обеспечивают отделение части заготовки.
Формообразующие операции изменяют форму заготовки без ее разделения. Это – вытяжка, гибка, обжим, отбортовка, скручивание, чеканка и др.
58