
pract-2788
.pdfЛабораторная работа № 7
РАЗРАБОТКА ТЕХНОЛОГИИ ПОЛУЧЕНИЯ ПОКОВОК ГОРЯЧЕЙ ОБЪЕМНОЙ ШТАМПОВКОЙ
Цель работы: ознакомление с разработкой технологического процесса получения поковок горячей объемной штамповкой.
Содержание работы: в соответствии с вариантом студент разрабатывает этапы технологического процесса получения поковки горячей объемной штамповкой.
Порядок выполнения работы: в представленном отчете вы-
полненной лабораторной работы должно быть приведено:
1.Эскиз заданной детали: расчет объема детали (Vд) и массы детали
(Gд).
2.Обоснование и выбор оборудования.
3.Эскиз поковки, нанесенной на эскиз детали:
–выбор плоскости разъема;
–определение припусков, напусков штамповочных уклонов и радиусов закруглений;
–расчет заусенечной канавки;
–конструирование наметки под прошивку;
–расчет объема (Vn) и массы поковки (Gn).
4.Определение размеров заготовки: объема заготовки (Vзаг), ее диаметра (dзаг), длины (Lзаг).
5.Определение количества переходов.
6.Определение температурного интервала нагрева заготовок под обработку давлением.
7.Схема объемной штамповки на выбранном оборудовании (рис.
7.6).
Схема прошивки перемычки и обрезки заусенца (рис. 7.6).
При выполнении и оформлении лабораторной работы чертеж детали и другие схемы выполняются чертежами.
1. Получение поковки горячей объемной штамповкой
Горячей объемной штамповкой называют процесс обработки металлов давлением нагретой заготовки с помощью специального инструмента – штампа. В результате приложенного усилия к частям штампа деформируемый металл заполняет полости штампа (ручьи) по конфигурации, соответствующей форме будущей поковки. В зависи-
80
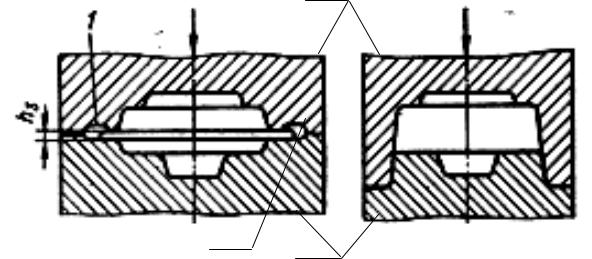
мости от вида штампа выделяют штамповку в открытых и закрытых штампах (риc. 7.1 а, б).
Штамповка в открытых штампах (рис. 7.1 а) характеризуется переменным зазором между подвижной (1) и неподвижной (2) частями штампа. В этот зазор выдавливается облой и закрывает выход из полости штампа, что заставляет металл полностью заполнить всю полость. В заключительной стадии формирования поковки в заусенец выжимаются излишки металла, находящиеся в полости. Этим способом получают поковки всех типов (круглые и квадратные в плане, фланцы, крестовины, стержень с фланцем, удлиненные в плане, поковки с изогнутой осью и др.). Штамповка в закрытых штампах (рис.7.1 б) характеризуется тем, что полость штампа в процессе штамповки закрыта, а зазор между частями штампа постоянный и образование заусенца в нем не предусматривается. Существенное преимущество штамповки в закрытых штампах: уменьшение расхода металла, поскольку нет отхода в заусенец, более благоприятная микроструктура, т. к. волокна обтекают контур поковки, а не пересекаются в месте выхода металла в заусенец.
1
3
2
а |
б |
Рис. 7.1. Схема штамповки в а) открытых и б) закрытых штампах 1) верхняя половина штампа; 2) нижняя половина штампа; 3) заусенечные канавки
81
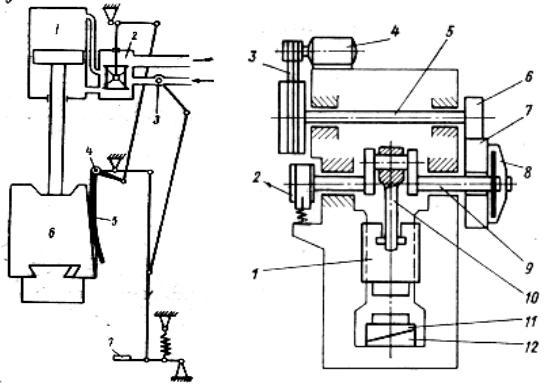
2. Обоснование и выбор штампового оборудования
Оборудование выбирают исходя из назначения детали, технологических возможностей изготовления поковки, экономической целесообразности применения выбранного метода получения поковок.
Для горячей объемной штамповки применяют молоты (рис. 7.2), кривошипные горячештамповочные прессы (рис. 7.3), гидравлические прессы, горизонтально-ковочные машины и др.
В зависимости от массы поковки и с учетом ее сложности формы по таблицам справочников [3, 4] или методическим указаниям (табл. 7.1) устанавливается усилие пресса или молота.
Рис. 7.2. Кинематическая схема |
Рис. 7.3. Кинематическая схемакри- |
паровоздушного молота двойного |
вошипного пресса: 1 – ползун; 2 – тор- |
действия: 1 – рабочий цилиндр; моз; 3 – клиноременная передача, элек- 2 – золотник; 3 – дроссель; 4 – тродвигатель; 5 – промежуточный вал; 6 – опора саблеобразного рычага; 5 шестерня;7 – зубчатое колесо; 8 – дис-
– саблеобразный рычаг; 6 – баковая муфта; 9 – кривошипный вал; 10 ба; 7 – педаль – шатун; 11 – стол пресса; 12 – клин
82

Таблица 7.1
Ориентировочные данные для выбора усилия в зависимости
от массы поковки
Вид оборудо- |
Масса |
Масса падаю- |
Производитель- |
|
вания |
поковок, кг |
щих частей |
ность, кг/ч |
|
|
|
молота или |
|
|
|
|
усилие пресса, |
|
|
|
|
т |
|
|
|
1 |
0,63 |
200 |
|
|
|
|
|
|
Штамповочные |
1-2,5 |
1,00 |
300 |
|
|
|
|
||
2,5-7 |
2,00 |
600 |
||
паровоздушные |
||||
|
|
|
||
7-17 |
3,15 |
1000 |
||
молоты двойно- |
||||
|
|
|
||
20-40 |
5,00 |
1750 |
||
го действия |
||||
|
|
|
||
70-100 |
10,00 |
3000 |
||
|
||||
|
|
|
|
|
|
180-360 |
16 |
5000 |
|
|
|
|
|
|
|
1 |
0,630 |
300-400 |
|
|
|
|
|
|
|
1-2,5 |
1,0 |
400-600 |
|
|
|
|
|
|
|
2,5-4 |
1,6 |
600-800 |
|
|
|
|
|
|
Горячештампо- |
4-7 |
2,0 |
800-900 |
|
|
|
|
||
7-12 |
2,5 |
900-1100 |
||
вочные криво- |
||||
|
|
|
||
12-18 |
3,1 |
1100-1500 |
||
шипные прессы |
||||
|
|
|
||
18-22 |
4,0 |
1500-1800 |
||
|
||||
|
|
|
|
|
|
22-30 |
5,0 |
1890-2200 |
|
|
|
|
|
|
|
30-50 |
6,3 |
2200-2800 |
|
|
50-80 |
8,0 |
2800-3500 |
|
|
|
|
|
4. Разработка чертежа поковки
Чертеж детали является основным документом для разработки чертежа поковки. По чертежу поковки определяют количество ручьев в штампе и их конфигурацию, количество переходов.
Разработка чертежа поковки выполняется в следующей последовательности:
1. Выбор плоскости разъема (рис. 7.4 б), т. е. поверхности, по которой соприкасаются между собой верхняя и нижняя половины
83
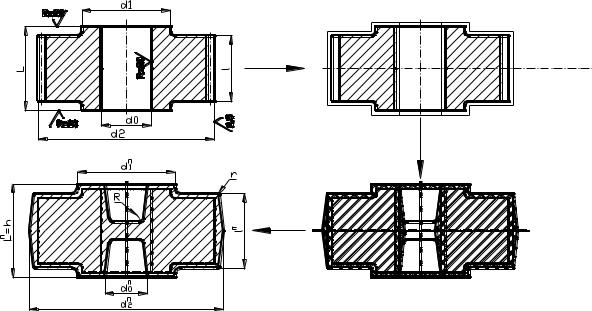
штампа. Плоскость разъема делит поковку на две части. Положение плоскости разъема должно обеспечивать:
а) свободное удаление поковки из штампа; б) минимальную глубину полости штампа; в) минимальные штамповочные уклоны.
Плоскость разъема должна пересекать вертикальную поверхность поковки для контроля сдвига одной половины штампа относительно другой (рис. 7.4 б) при штамповке в открытых штампах.
а |
б |
|
плоскость |
|
разъема |
г |
в |
|
Рис. 7.4. Последовательность разработки чертежа поковки
Линию разъема указать на чертеже поковки.
1. Определить припуски на механическую обработку (рис. 7.4 б). Припуски на механическую обработку назначают главным образом на сопрягаемые поверхности. Величина припуска зависит от массы и габаритных размеров поковки, от вида оборудования, шероховатости обрабатываемой поверхности. Припуски выбирают по ГОСТу 7505-74 (табл. 7.2) с учетом группы точности поковок.
Группы точности поковок
1 – поковки большой точности массового производства, обрабатываемые резанием на специальном оборудовании и в специальных приспособлениях;
84
2 – поковки средней точности крупносерийного производства, обрабатываемые резанием на универсальных станках в специальных приспособлениях;
3 – поковки малой точности мелкосерийного производства, обрабатываемые на универсальных станках;
4 – поковки, подвергаемые плоскостной холодной калибровке на отдельных участках.
Таблица 7.2
Припуски на обработку на сторону в мм для чистоты обрабатываемых поверхностей до Rz 80
Масса |
|
|
|
Линейные размеры, мм |
|
|
|||
поков- |
До 50 |
|
50- |
120-180 |
180- |
260- |
360- |
500- |
630- |
ки, кг |
|
|
120 |
|
260 |
360 |
500 |
630 |
800 |
|
|
Поковки 1-й группы на прессах |
|
|
|||||
До 0,25 |
0,6 |
|
0,6 |
0,7 |
0,8 |
0,7 |
1 |
1,1 |
1,3 |
0,25-0,63 |
0, |
|
0,8 |
0,9 |
1,0 |
1,1 |
1,2 |
1,3 |
1,5 |
0,63-1,6 |
0,9 |
|
1,0 |
1,1 |
1,2 |
1,3 |
1,5 |
1,6 |
1,7 |
1,6-2,5 |
1,0 |
|
1,2 |
1,3 |
1,4 |
1,5 |
1,7 |
1,8 |
1,7 |
2,5-4 |
1,2 |
|
1,3 |
1,4 |
1,5 |
1,7 |
1,9 |
2,0 |
2,1 |
4-6,3 |
1,5 |
|
1,6 |
1,7 |
1,8 |
1,9 |
2,1 |
2,2 |
2,3 |
6,3-10 |
1,6 |
|
1,7 |
1,8 |
1,9 |
2,1 |
2,3 |
2,4 |
2,5 |
10-16 |
1,8 |
|
1,9 |
2 |
2,1 |
2,2 |
2,4 |
2,6 |
2,7 |
16-25 |
2,0 |
|
2,1 |
2,2 |
2,3 |
2,4 |
2,6 |
2,8 |
2,9 |
25-40 |
2,1 |
|
2,2 |
2,3 |
2,4 |
2,6 |
2,8 |
3,0 |
3,1 |
40-63 |
- |
|
- |
- |
- |
- |
- |
- |
- |
|
|
Поковки 1-й группы на молотах |
|
|
|||||
До 0,25 |
0,6 |
|
0,7 |
0,7 |
0,8 |
0,9 |
1,1 |
1,2 |
1,4 |
0,25-0,63 |
0,8 |
|
0,9 |
1,0 |
1,1 |
1,2 |
1,3 |
1,4 |
1,5 |
0,63-1,6 |
0,9 |
|
1,1 |
1,2 |
1,3 |
1,5 |
1,6 |
1,7 |
1,8 |
1,6-2,5 |
1,1 |
|
1,3 |
1,4 |
1,5 |
1,7 |
1,8 |
1,9 |
2,1 |
2,5-4 |
1,2 |
|
1,5 |
1,6 |
1,7 |
1,9 |
2,0 |
2,1 |
2,3 |
4-6,3 |
2,5 |
|
1,7 |
1,8 |
1,9 |
2,1 |
2,2 |
2,3 |
2,5 |
6,3-10 |
1,7 |
|
1,9 |
2,0 |
2,1 |
2,3 |
2,4 |
2,5 |
2,7 |
10-16 |
1,2 |
|
2,1 |
2,2 |
2,3 |
2,5 |
2,6 |
2,7 |
2,9 |
16-25 |
2,1 |
|
2,3 |
2,4 |
2,5 |
2,7 |
2,8 |
2,9 |
3,1 |
25-40 |
2,3 |
|
2,5 |
2,6 |
2,7 |
2,9 |
3,0 |
3,1 |
3,3 |
40-63 |
2,6 |
|
2,7 |
2,8 |
2,9 |
3,1 |
3,2 |
3,3 |
3,5 |
85
63-100 |
2,9 |
|
3,0 |
3,2 |
3,5 |
3,5 |
3,6 |
3,7 |
4,0 |
|
|
Поковки 2-й группы на прессах |
|
|
|||||
|
|
|
|
|
|
|
|
|
|
До 0,25 |
0,9 |
|
1,0 |
1,2 |
1,3 |
1,5 |
- |
- |
- |
0,25-0,63 |
1,1 |
|
1,2 |
1,4 |
1,5 |
1,7 |
2,0 |
- |
- |
0,63-1,6 |
1,3 |
|
1,4 |
1,6 |
1,7 |
1,9 |
2,2 |
2,5 |
- |
1,6-2,5 |
1,5 |
|
1,6 |
1,8 |
1,9 |
2,1 |
2,4 |
2,7 |
3,0 |
2,5-4 |
1,7 |
|
1,8 |
2,0 |
2,1 |
2,3 |
2,6 |
2,9 |
3,2 |
4-6,3 |
1,9 |
|
2,0 |
2,2 |
2,3 |
2,5 |
2,8 |
3,1 |
3,4 |
6,3-10 |
2,1 |
|
2,2 |
2,4 |
2,5 |
2,7 |
3,0 |
3,3 |
3,6 |
10-16 |
2,3 |
|
2,4 |
2,6 |
2,7 |
2,9 |
3,2 |
3,5 |
3,8 |
16-25 |
2,5 |
|
2,6 |
2,8 |
2,9 |
3,1 |
3,4 |
3,7 |
4 |
25-40 |
2,7 |
|
2,8 |
3,0 |
3,1 |
3,1 |
3,6 |
3,9 |
4,2 |
|
|
Поковки 2-й группы на молотах |
|
|
|||||
До 0,25 |
1,0 |
|
1,1 |
1,2 |
1,4 |
1,6 |
- |
- |
- |
0,25-0,63 |
1,2 |
|
1,3 |
1,4 |
1,6 |
1,8 |
2,1 |
- |
- |
0,63-1,6 |
1,4 |
|
1,5 |
1,6 |
1,8 |
2,0 |
2,3 |
2,5 |
- |
1,6-2,5 |
1,6 |
|
1,7 |
1,8 |
2,0 |
2,2 |
2,5 |
2,7 |
3,1 |
2,5-4 |
1,9 |
|
2,0 |
2,1 |
2,3 |
2,5 |
2,8 |
3,0 |
3,4 |
4-6,3 |
2,1 |
|
2,2 |
2,3 |
2,5 |
2,7 |
3,0 |
3,2 |
3,6 |
6,3-10 |
2,3 |
|
2,4 |
2,5 |
2,7 |
2,9 |
3,2 |
3,4 |
3,8 |
10-16 |
2,5 |
|
2,6 |
2,7 |
2,9 |
3,1 |
3,4 |
3,6 |
4,0 |
16-25 |
2,7 |
|
2,8 |
2,9 |
3,1 |
3,3 |
3,6 |
3,8 |
4,2 |
25-40 |
2,9 |
|
3,0 |
3,1 |
3,3 |
3,5 |
3,8 |
4,0 |
4,4 |
40-63 |
3,2 |
|
3,3 |
3,4 |
3,6 |
3,8 |
4,1 |
4,3 |
4,7 |
63-100 |
3,7 |
|
3,8 |
3,9 |
4,1 |
4,3 |
4,6 |
4,8 |
5,2 |
100-125 |
4,0 |
|
4,1 |
4,2 |
4,4 |
4,6 |
4,9 |
5,1 |
5,5 |
|
|
Поковки 3-й группы на прессах |
|
|
|||||
До 0,25 |
1,2 |
|
1,4 |
1,6 |
1,8 |
2,1 |
- |
- |
- |
0,25-0,63 |
1,4 |
|
1,6 |
1,8 |
2,0 |
2,3 |
2,7 |
- |
- |
0,63-1,6 |
1,7 |
|
1,9 |
2,1 |
2,3 |
2,6 |
3,0 |
3,4 |
- |
1,6-2,5 |
2,0 |
|
2,2 |
2,4 |
2,6 |
2,9 |
3,3 |
3,7 |
4,2 |
2,5-4 |
2,2 |
|
2,4 |
2,6 |
2,8 |
3,1 |
3,5 |
3,9 |
4,4 |
4-6,3 |
2,5 |
|
2,7 |
2,9 |
3,1 |
3,4 |
3,8 |
4,2 |
4,7 |
6,3-10 |
2,8 |
|
3,3 |
3,2 |
3,4 |
3,7 |
4,1 |
4,5 |
5,0 |
10-16 |
3,0 |
|
3,2 |
3,4 |
3,6 |
3,9 |
4,3 |
4,7 |
5,2 |
16-25 |
3,3 |
|
3,5 |
3,7 |
3,9 |
4,2 |
4,6 |
5,0 |
5,5 |
25-40 |
3,6 |
|
3,8 |
4,0 |
4,2 |
4,5 |
4,9 |
5,3 |
5,8 |
|
|
|
|
|
|
|
|
|
|
86
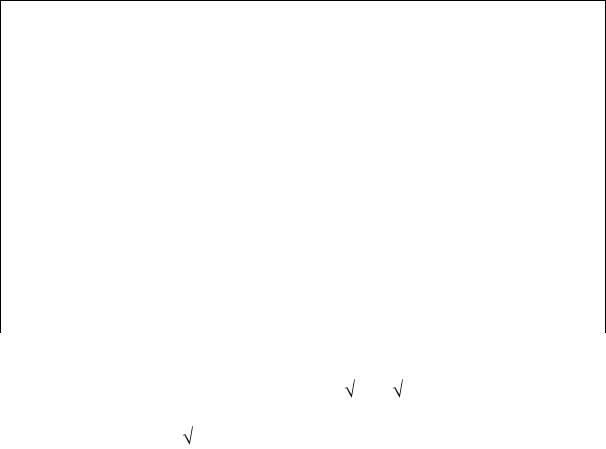
Поковки 3-й группы на молотах
До 0,25 |
1,2 |
1,4 |
1,6 |
1,8 |
2,1 |
- |
- |
- |
0,25-0,63 |
1,5 |
1,7 |
1,9 |
2,1 |
2,4 |
2,9 |
- |
- |
0,63-1,6 |
2,0 |
2,2 |
2,4 |
2,6 |
2,9 |
3,4 |
3,7 |
- |
1,6-2,5 |
2,3 |
2,5 |
2,7 |
2,9 |
3,2 |
3,7 |
4,0 |
4,6 |
2,5-4 |
2,5 |
2,7 |
2,9 |
3,1 |
3,4 |
3,9 |
4,2 |
4,8 |
4-6,3 |
2,8 |
3,0 |
3,2 |
3,4 |
3,7 |
4,2 |
4,5 |
5,1 |
6,3-10 |
3,2 |
3,4 |
3,6 |
3,8 |
4,1 |
4,6 |
4,9 |
5,5 |
10-16 |
3,4 |
3,6 |
3,8 |
4,0 |
4,3 |
4,8 |
5,1 |
5,7 |
16-25 |
3,7 |
3,9 |
4,1 |
4,3 |
4,6 |
5,1 |
5,4 |
6,0 |
25-40 |
4,1 |
4,3 |
4,5 |
4,7 |
5,0 |
5,5 |
5,8 |
6,4 |
40-63 |
4,5 |
4,7 |
4,9 |
5,1 |
5,4 |
5,9 |
6,2 |
6,8 |
63-100 |
5,4 |
5,6 |
5,8 |
6,0 |
6,3 |
6,8 |
7,1 |
7,7 |
100-125 |
5,8 |
6,0 |
6,2 |
6,4 |
6,7 |
7,2 |
7,5 |
8,1 |
Примечание. При более чистых поверхностях обработки при-
бавляют к припускам: |
40 |
2,5 |
|
|
|
||
а) при чистоте поверхности от Rz |
до прибавляют 0,3-0,5 мм |
||
на сторону; |
1,25 |
|
|
|
|
|
|
б) при частоте |
и выше – 0,5-0,8 мм. |
Полученные размеры округляют в сторону увеличения припусков с точностью до 0,1 мм для поковок 1-й группы; до 0,5 мм для поковок 2-й группы; для поковок 3-й группы – до 1мм.
Порядок назначения припусков на поковку
Во всех приведенных вариантах вычислить объем и массу поковки и назначить припуски в зависимости от массы и габаритных размеров.
Пример назначения припусков на поковку (рис. 7.4): d1 = 4,8 см; d2 = 8,8 см; d0 = 3,5 см; l1 = 4,5 см; L = 1,5 см. Объем и масса поковки:
Vn = 247,34 см3; mn = 1,929 кг.
Для поковки массой 1,929 кг второй группы точности, изготовляемой на КГШП: d2 = 88 мм припуск составляет 1,6 мм на сторону, с учетом шероховатости добавляем 0,5 мм. Получим d2n = 88+2 (1,6 + 0,5) = 92,2 мм. Округляем с точностью до 0,5, получим размер поковки равный 92,5 мм.
Для d1 = 48 мм припуск составит 1,5 мм на сторону, с учетом шероховатости добавляем 0,3 мм, т. е. d1n = 48 + 2 (1,5 + 0,3) = 51 мм, округляя с точностью до 0,5, получим размер равный 51,5 мм.
87

Для диаметра d0 = 35 мм припуск составит 1,5 мм на сторону, т.
е.
d0 = 35 – 2(1,5 + 0,3) = 31,4 мм, округляя с точностью до 0,5, получим размер, равный 31,5 мм.
Величину припусков и размеров поковок занести в таблицу 7.3 и указать на чертеже детали.
|
|
|
|
Таблица 7.3 |
|
|
|
|
|
Размер де- |
Чистота |
Величина |
Припуск с |
Размер по- |
тали, мм |
обработки |
припуска |
учетом ше- |
ковки, мм |
|
поверхно- |
(по таблице |
роховато- |
|
|
сти Rа, Rz |
3), мм |
сти, мм |
|
d2 = 88 |
2,5 |
1,6 |
0,5 |
d2n = 92,5 |
d1 = 48 |
80 |
1,5 |
0,3 |
d1n = 51,5 |
d0 = 35 |
20 |
1,5 |
0,3 |
d0n = 31,5 |
Определение штамповочных уклонов
Штамповочные уклоны назначают для облегчения удаления поковки из ручья штампа. Они устанавливаются на всех поверхностях поковки, параллельных направлению движения ползуна пресса (рис. 7.4 в).
Штамповочные уклоны наружных поверхностей ( ) определяются по ГОСТ 7505-74 в зависимости от высоты поковки. Рекомендуется применять следующий ряд штамповочных уклонов: 3, 5, 7 и 100. До 70 – для штамповочных наружных уклонов и 100 – для внутренних уклонов. При штамповке на молотах уклоны: внешних поверхностей 5-70 и внутренних 7-100. При штамповке на прессах с выталкивателя-
ми в ползуне и столе уклоны внешних поверхностей составляют 30 и внутренних 5-70.
Размеры горизонтальных отрезков, образуемых этими уклонами, даны в таблице 7.4.
88

Таблица 7.4
Размеры горизонтальных отрезков, образуемых нормальными штамповочными уклонами (мм)
Высота по- |
Размеры горизонтальных отрезков мм при штам- |
|||
ковки, мм |
|
повочных |
|
|
|
|
уклонах в градусах |
|
|
|
3 |
5 |
7 |
10 |
1 |
0,05 |
0,09 |
0,12 |
0,18 |
2 |
0,1 |
1,17 |
0,25 |
0,35 |
3 |
0,16 |
0,26 |
0,37 |
0,53 |
4 |
0,21 |
0,35 |
0,49 |
0,71 |
5 |
0,20 |
0,44 |
0,61 |
0,88 |
6 |
0,31 |
0,52 |
0,74 |
1,06 |
7 |
0,37 |
0,61 |
0,86 |
1,23 |
8 |
0,42 |
0,7 |
0,98 |
1,41 |
9 |
0,47 |
0,79 |
1,11 |
1,59 |
10 |
0,52 |
0,87 |
1,23 |
1,76 |
20 |
1,05 |
1,75 |
2,46 |
3,53 |
30 |
1,57 |
2,62 |
3,68 |
5,29 |
40 |
2,1 |
3,5 |
4,91 |
7,05 |
50 |
2,02 |
4,37 |
6,14 |
8,82 |
60 |
3,14 |
5,25 |
7,37 |
10,58 |
70 |
3,67 |
6,12 |
8,6 |
12,34 |
80 |
4,19 |
7,00 |
9,82 |
14,11 |
90 |
4,72 |
7,87 |
11,05 |
15,87 |
100 |
5,24 |
8,75 |
12,28 |
17,66 |
Определение наметки под прошивку
При штамповке с одной плоскостью разъема нельзя получить сквозное отверстие в поковке, поэтому делают только наметку отверстия с перемычкой (рис. 7.4 г). Толщина перемычки определяется по формуле:
|
|
|
|
Ln |
|
|
|
|
t 0,45 d |
|
0,25 |
5 0,6 |
L |
, мм. |
|||
о n |
|
|
||||||
|
|
2 |
|
|
2 |
|
||
|
|
|
|
|
|
89