
ответы ДМ
.pdf
1. Классификация деталей машин. Основные требования, предъявляемые к машинам и их деталям.
Деталь – изделие, выполненное из однородного материала, выполненное без сборки.
Выделяют детали, которые применяются в широком круге различных машин – это болты, муфты, валы, механические передачи, подшипники – они называются деталями общего назначения. Все другие детали – поршни, лопатки турбин, гребневые винты – относятся к деталям специального назначения.
Требования к деталям:
1)Надёжность и выс. производительность;
2)Экономичность изготовления и эксплуатации;
3)Габариты и низкая металлоёмкость;
4)Взаимозаменяемость.
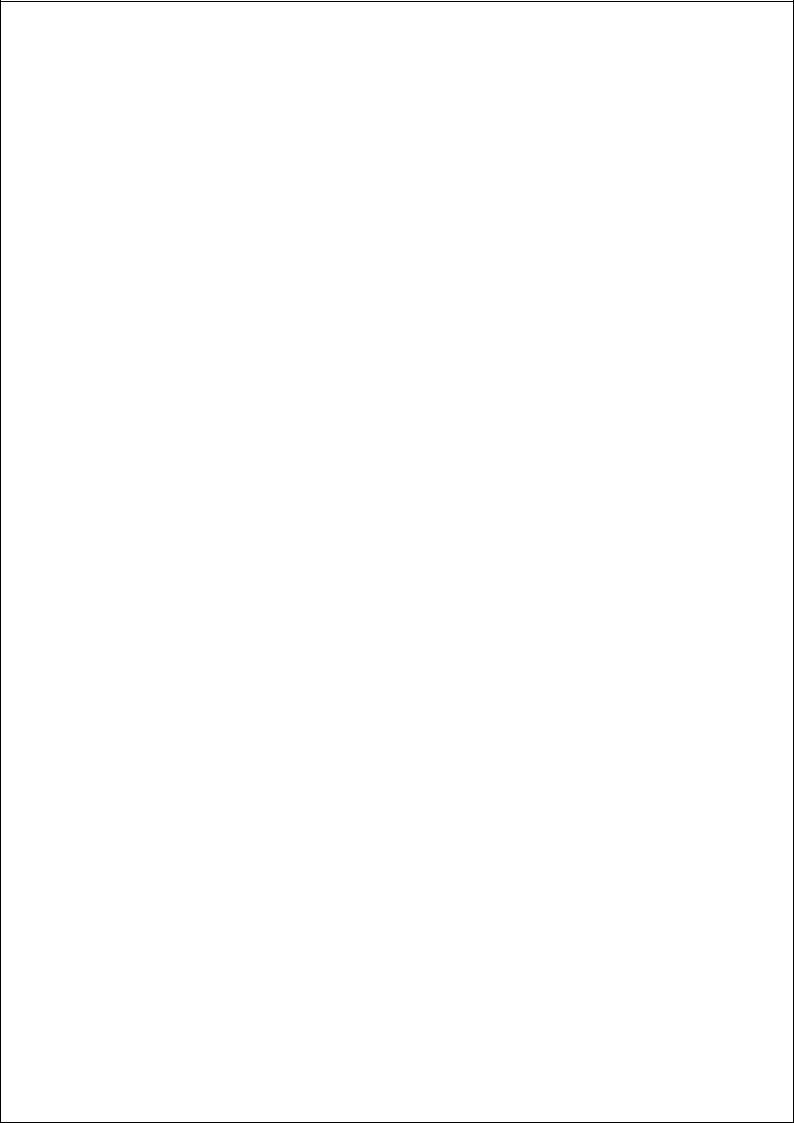
2. Основные критерии работоспособности и расчёта деталей машин. Классификация нагрузок, действующих на детали машин.
Критерии работоспособности:
1)Прочность (статическая прочность и сопротивление усталости)
2)Жёсткость
3)Износостойкость (абразивное изнашивание, коррозийно-механическое, заедание).
4)Теплостойкость
5)Виброустойчивость.
Все расчёты приближённые. Большое значение имеет выбор правильной расчётной модели, оценка факторов.
Неточности компенсируют за счёт запаса прочности. Сначала делают проектный расчёт, потом - проверочный.
Различают расчётную и номинальную нагрузку.
Расчётную нагрузку определяют как произведение наминальной на динамический коэффициент режима нагрузки (например для вращающего момента: Т=КТн). Номинальный момент соответствует паспортной мощности машины.

4. Предел выносливости. Факторы, влияющие на предел выносливости.
Предел выносливости – основная характеристика сопротивления усталости.
Усталость – процесс постепенного накопления повреждений под действием переменных напряжений, приводящий к появлению, развитию и разрушению трещин.
Сопротивление усталости – свойство сопротивляться разрушению под действием нагрузок.
Nо – база напряжений (N – количество циклов) σ-1 – предел выносливости
Факторы влияющие на предел выносливости:
1)концентрация напряжений Kσ= σ-1 /σ-1Д (стандартный образец и образец с концентратором)
2)абсолютные размеры детали Кd= σ-1d /σ-1
3)качество обработки поверхности КF= σ-1F /σ-1
4)упрочнение поверхности КV= σ-1V /σ-1
( K |
) D |
( |
K |
|
1 |
1) |
1 |
|||
K d |
K F |
K V |
||||||||
|
|
|
|
|
|
|
||||
K 1D |
|
|
1 |
|
|
|
|
|
||
|
( K ) D |
|
|
|
|
|
||||
|
|
|
|
|
|
|
|
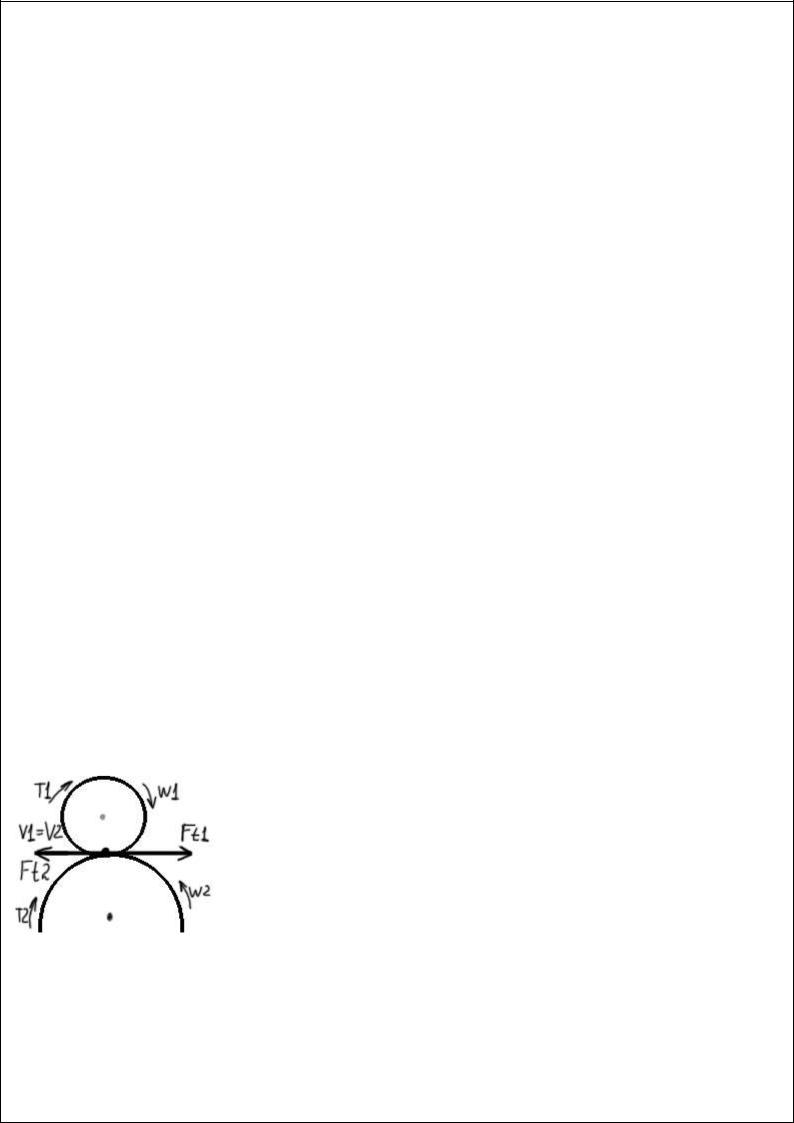
5. Механические передачи: их назначение и классификация. Основные кинематические и силовые соотношения в передачах.
Передачи служат для передачи механической энергии на расстояние. Бывают: передачи трения (ремённые, фрикционные) и передачи зацепления.
Основные характеристики:
1) Р1, Р2 – мощности входа и выхода [кВт]
2) w1, w2 – угловая скорость [рад/с] или [с-1] w=2πn/60=πn/30
3)V1, V2 – окружная скорость [м/с]
4)Ft1, Ft2 – окружная сила, действующая на ведущее звено, всегда противоположна направлению вращения, на ведомое – совпадает. Ft=P/V
5)η - КПД передачи η=Р2/Р1
6)Т – вращающий момент на ведущем звене всегда совпадает с направлением вращения, на ведомом – противоположен. [H*mm] T=P/w=Ft*r
7)u – передаточное отношение u=w1/w2=d2/d1=z2/z1 (u>1 – редуктор, u<1 - мультипликатор)
Если передача состоит из ведущего и ведомого валов, то она – одноступенчатая.
Механизм с переменным передаточным отношением называется вариатор.

6. Зубчатые передачи. Классификация зубчатых передач. Основные геометрические параметры цилиндрической прямозубой передачи.
Принцип действия основан на зацеплении пары зубчатых колёс.
Классификация по расположению осей валов:
1) параллельны (цилиндрическая)
2) пересекаются (коническая)
3) скрещиваются (червячная)
Классификация по расположению зубьев:
1) прямозубые
2) косозубые
Классификация по профилю зубьев:
1) эвольвентные
2) круглые.
Окружности, касающиеся в полюсе зацепления P называются начальными. Линия зацепления N-N – нормаль к профилю зубьев.
Угол м/у линией зацепления и общей касательной T-T 200 – угол зацепления αW
Основная окружность rb; Окружность вершин ra; Окружность впадин rf
p – делительный окружной шаг зубьев (шаг исходной зубчатой рейки) pb=p*cosα – основной окружной шаг зубьев
α – угол профиля делительный (угол профиля исходного контура) m=p/π – окружной модуль зубьев
d=pz/π=mz – делительный диаметр db=d*cosα – основной диаметр
dW – начальный диаметр dW1=2*aW/(z2/z1+1) dW2=2*aW - dW1
У передач без смещения начальные и делительные окружности совпадают: dW1=d1=mz1 dW2= d2=mz2
aW=0.5(dW1- dW2) – межосевое расстояние

7. Основная теорема зацепления. Эвольвентный профиль зуба.
Эвольвента и её свойства - кривая, которую описывает каждая точка прямой, катящейся по окружности (основной) без скольжения.
1)Любые качательные проведённые к основной окружности являются нормалями к эвольвенте
2)Основная окружность является эволютой, т. е. геометрическим местом центра кривизны эвольвенты.
3)Разность длин касательных, проведённых к основной окружности, равна длине дуги, заключённой м/у точками касания.
Скорость точки касания М зуба С: V1=w1*O1M, а скорость точки касания М зуба D: V2= w2*O2M.
N-N – общая нормаль к касающимся профилям зубьев, Т-Т – общая касательная ТТ┴NN в точке М.
Разложим скорости по направлению нормали и касательной.
Из подобия треугольников O1AM и Mae : Vn1=V1*O1A/ O1М=w1*ρ1 Из подобия треугольников O2BM и Mbf : Vn1=V2*O2B/ O2М=w2*ρ2 Где ρ1 и ρ2 – длины перпендикуляров O1A и O2B на общую нормаль
Vn1 = Vn2 или |
w1*ρ1 = w2*ρ2 откуда |
w1/w2 = ρ1/ ρ2 |
|
при условии постоянства передаточного отношения |
u = w1/w2 = ρ2/ ρ1 |
||
Из подобия треугольников О1АР и О2ВР : |
ρ2/ ρ1= О2Р/ О1Р |
u= w1/w2 = ρ2/ ρ1= О2Р/ О1Р=const
т.е. точка Р пересечения нормали с линией центров, называемая полюсом зацепления, должна занимать постоянное положение на линии центров.
Общая нормаль в любой точке касания должна проходить через полюс зацепления, который делит линию центров колёс на отрезки, обратно пропорциональные угловым скоростям.
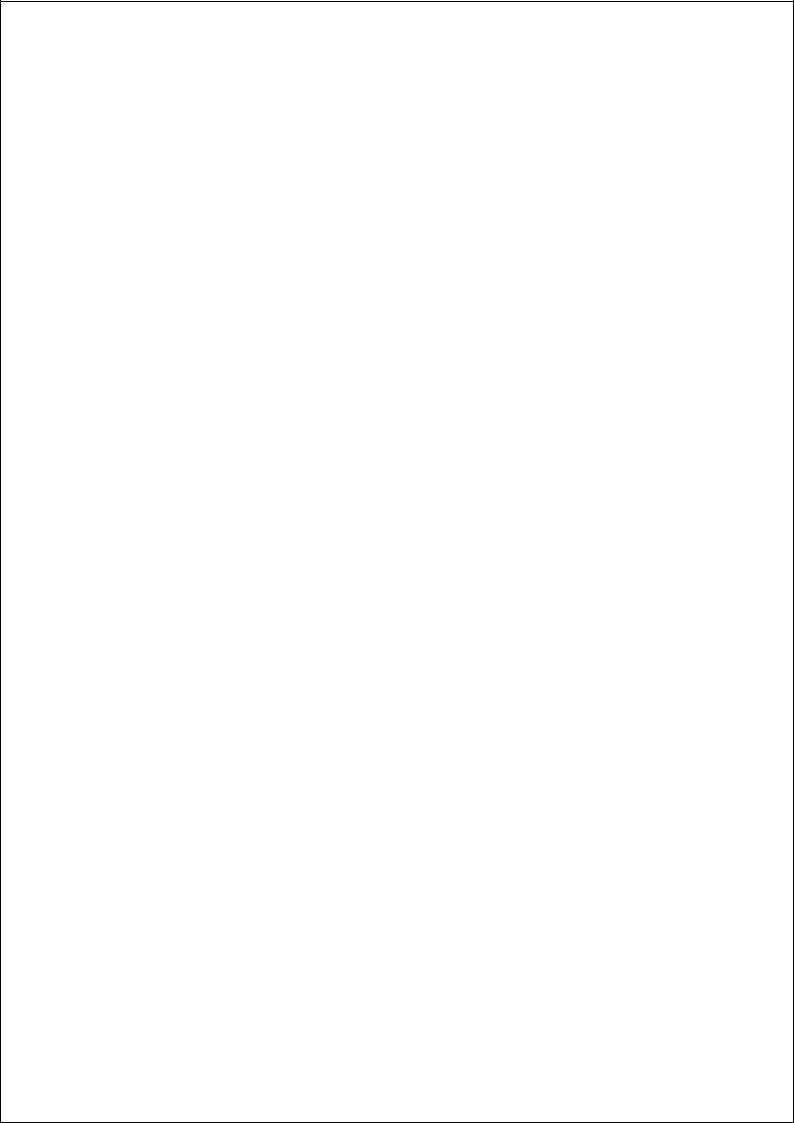
8. Понятие о расчетной нагрузке в зубчатых передачах. Коэффициент неравномерности распределения нагрузки. Коэффициент динамической нагрузки.
За расчётную нагрузку принимают максимальное значение удельной нагрузки, распределённой по линии контакта зубьев: q=FnK/lΣ
Fn – нормальная сила в зацеплении зубьев К=КβКV – коэффициент расчётной нагрузки Кβ – коэффициент концентрации нагрузки КV – коэффициент динамической нагрузки lΣ – суммарная длина линии контакта зубьев
Коэффициент концентрации нагрузки Кβ.
При симметричном расположении опор прогиб валов не вызывает перекоса зубчатых колёс и, следовательно, почти не нарушает распределения нагрузки по длине зуба. Это самый благоприятный случай. При несимметричном и консольном расположении опор колеса перекрещиваются на угол γ, что приводит к нарушению правильного касания зубьев.
Деформация зубьев уменьшает влияние перекосов и сохраняет их соприкасание по всей длине, но при этом нагрузка перераспределяется в соответствии с деформацией отдельных участков зубьев : qmax/qср= Кβ,
где qср – средняя интенсивность нагрузки.
При конструировании передачи необходимо учитывать все факторы, влияющие на концентрацию нагрузки, и в первую очередь не применять нежёстких валов, опор и корпусов.
При постоянной нагрузке, при НВ<350 и V<15м/с Кβ =1.
Коэффициент динамической нагрузки КV.
Значение дополнительных динамических нагрузок зависит от значения ошибки шагаЮ окружной скорости, присоединённых масс, упругости системы и пр. КV
=1 + qV / q,
где qV - удельная динамическая нагрузка; q – удельная расчётная рабочая нагрузка в зоне её наибольшей концентрации.

9. Виды разрушений зубьев зубчатых колёс. Критерии работоспособности и расчёта зубчатых передач.
Решающее влияние на работоспособность оказывают два основных напряжения: контактны напряжения σН и напряжения изгиба σF.
Поломка зубьев связана с напряжениями изгиба. На практике чаще наблюдается выламывание углов зубьев.
1)Поломка от больших перегрузок ударного или статического действия
2)Усталостная поломка от действия переменных напряжений в течение длительного времени.
Общие меры предупреждения : увеличение модуля, термообработка, наклёп, уменьшение концентраторов.
Повреждение поверхности зубьев связано с контактными напряжениями и трением.
1)Усталостное выкрашивание – масло запрессовывается в трещины и способствует вырыванию частиц металла. При выкрашивании нарушаются условия образования сплошной масляной плёнки, появляется металлический конакт с последующим задиром поверхности.
Начальное выкрашивание не всегда плохо, оно может быть из-за приработки зубьев.
2)Абразивный износ. Главная причина – плохая смазка.
3)Заедание наблюдается в высоконагруженных и высокоскоростных передачах. Повышается температура, разрывается масляная плёнка, образуется металлический контакт, происходит свариванеи частиц металл с последующим их отрывом, образуются наросты.
4)Пластические сдвиги наблюдаются у тяжелонакруженных тихоходных колёс из мягкой стали. У ведомого колеса образуется хребет, а у ведущего – канавка.
5)Отслаивание твёрдого поверхностного слоя зубьев, подвергнутых упрочнению наблюдается при недостаточном качестве термической обработки.

10. Расчёт цилиндрических колёс на прочность по контактным напряжениям.
Проектный расчёт на контактную прочность (пример из семестровки)
a |
|
K |
|
(u 1) 3 |
T K |
H |
43 * 4.9 3 |
523891 |
116 м м. 125 м м |
|
|
|
|
|
|
||||||
W |
a |
|
]2 u 2 ba |
6432 * 3.9 2 * 0.5 |
||||||
|
|
[ H |
|
|
||||||
|
|
|
|
|
|
b2 b a aW 0 .5 * 1 2 5 6 3 м м b1 1 .1 2b2 1 .1 2 * 6 3 7 1 м м
m=(0.01...0.02)aW=0.01*125...0.02*125=1.25...2.5 m=2.5
β=100 cosβ=0.98
ZC=2 aW cosβ /m=2*125*0,98/2.5=98
Z1= ZC(u+1)=98*4.9=20 > 17 cos3β Z2= ZC-Z1=98-20=78
u= Z2/Z1=78/20=3,9 (уточнение передаточного числа) aW=0.5(Z2+Z1)m/cosβ=0.5(78+20)2.5/0.98=125 мм
(проверяем межосевое расстояние) d1=Z1m/ cosβ=20*2.5/0.98=52 мм d2=Z2m/ cosβ=78*2.5/0.98=199 мм da1=d1+2m=52+2*2.5=52+5=57 мм da2=d2+2m=199+2*2.5=199+5=204 мм df1=d1-2m=52-2.5*2.5=52-6.25=46 мм df2=d2-2m=199-2.5*2.5=199-6.25=193 мм
Проверочный расчёт на контактную прочность
H |
|
f |
z |
TK |
H |
(u 1)3 |
|
270 |
|
523891*1.15 *1.1* (3.9 1)3 |
616.139, М П а [ H ] 643, М П а |
|
|
|
|
|
|
|
|
||||||
aW |
|
|
b2 u 2 |
125 |
63 * 3.9 2 |
|||||||
|
|
|
|
|
|
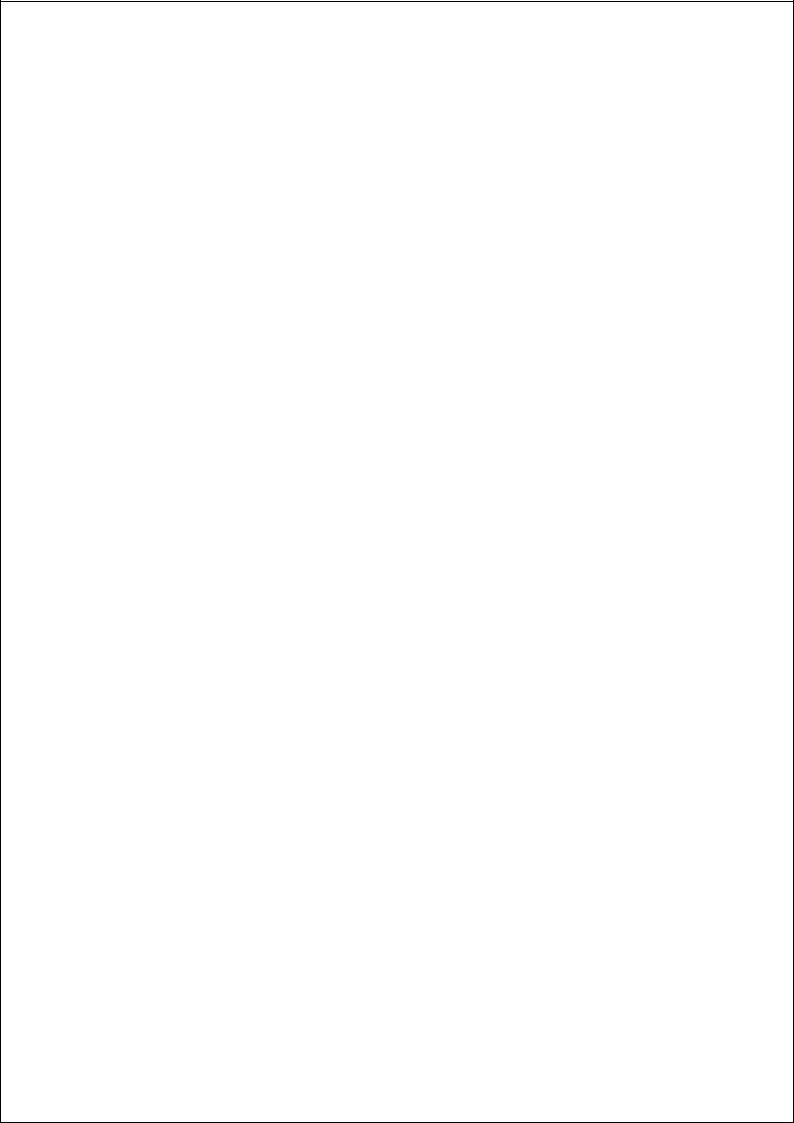
11. Расчёт цилиндрических колёс на прочность по напряжениям изгиба.
Проверочный расчёт по напряжениям изгиба (пример из семестровки)
F |
|
|
2T2 |
|
2 * 5 2 3 8 9 1 |
5 2 6 5 H |
t |
|
|
||||
|
|
d 2 |
1 9 9 |
|
||
|
|
|
|
|||
K F |
1 |
|
|
|
Y |
1 ( / 1 4 0 ) 1 1 0 / 1 4 0 0 .9 |
|||||||||||
|
|
|
|
|
|
|
|
1 |
|
1 |
|
|
|
[1 .8 8 3 .2 |
|
|
|
] / co s [1 .8 8 |
|||||||
z1 |
z 2 |
|||||||||||
|
|
|
|
|
|
|
|
|
|
|||
Z F |
K F Y / |
0 .9 / 1 .7 1 0 .5 3 |
||||||||||
Z |
v1 |
|
z |
1 |
/ co s 3 |
2 0 / 0 .9 4 2 1, 2 7 |
||||||
|
|
|
|
|
|
|
|
|
||||
Z |
v 2 |
|
z |
2 |
/ co s 3 |
7 8 / 0 .9 4 8 2, 9 8 |
||||||
|
|
|
|
|
|
|
|
|
|
|||
YF 1 |
|
4 .0 7 |
|
|
|
|
|
|||||
YF 2 |
|
3 .6 |
|
|
|
|
|
[ F ] / YF 1 3 1 5 / 4 .0 7 7 7 .4 [ F ] / YF 2 2 7 8 / 3 .6 7 7 .2
K F K F K F V 1 .5 * 1 .3 1 1 .9 7 |
|
||||||||||
|
|
F |
K |
F |
Y |
F |
Z |
F |
|
5 2 6 5 * 1 .9 7 * 3 .6 0 .5 3 |
|
F |
|
t |
|
|
|
|
|
|
|||
|
|
b m |
|
|
6 3 * 2 |
.5 |
|||||
|
|
|
|
|
|
|
3 .2 (1 / 2 0 1 / 7 8)] / 0 .9 8 1 .7 1
1 2 5 М П а [ F ] 2 7 8 М П а