
капланова
.pdf21
Контрольные вопросы:
Определение понятия схватывания металлов.
Основные гипотезы схватывания металлов и их сущность.
Основные факторы, влияющие на процесс схватывания металлов, и их краткий анализ.
Неравномерность деформации слоев биметаллической заготовки и краткий анализ основных влияющих на нее факторов.
Методы расчета сопротивления деформации при прокатке биметаллических заготовок.
22
4.МЕТОДЫ ПОЛУЧЕНИЯ БИМЕТАЛЛОВ
Из-за большого разнообразия биметаллов существует большое количество методов их получения, и на выбор метода производства биметаллов, безусловно, накладывает отпечаток состав оборудования завода, на котором предполагается их производство.
Можно выделить следующие основные способы (методы) получения биметаллов (как заготовок: слитков, слябов и др., так и готовых изделий):
1)получение заливкой (метод заливки или литейный метод);
2)получение совместной пластической деформацией (как холодной, так и горячей);
3)так называемые специальные методы (например, получение
взрывом, электродуговой наплавкой или другим методом, не требующим обязательной пластической деформации для получения прочного соединения).
Рассмотрим кратко 1-ый и 3-ий методы, названные выше (2-ой метод выделен в отдельных лекциях настоящего курса для более детального его изучения и анализа).
4.1 Метод заливки
Этот метод применяется для получения практически всех известных в настоящее время групп биметаллов (коррозионностойких, износостойких, инструментальных и др.). В основе литейного метода лежит получение двухили многослойного слитка различной массы (от нескольких килограммов до 7-13 т) заливкой одного или более слоев на твердый слой другого состава и последующая его горячая прокатка с интенсивными частными обжатиями и большим суммарным обжатием (для получения более прочного соединения). При этом соединение слоев биметалла может происходить как в процессе заливки и кристаллизации, так и в процессе дальнейшей пластической деформации.
Следует также отметить, что литейный метод получения биметаллической заготовки не требует каких-либо капитальных затрат, специального оборудования и т.д. Тем не менее, данный метод
23
характеризуется увеличением расходного коэффициента металла и низким качеством готовой продукции.
Литейный метод имеет следующие основные разновидности: 1)заливка жидким металлом пластины или стержня другого состава,
вертикально расположенных в изложнице; 2)заливка жидкого металла на твердую составляющую (например,
пластину с предварительно приваренными к ней торцевыми и боковыми планками);
3)последовательная заливка двух различных металлов или сплавов в одну и ту же разъемную изложницу;
4)непрерывная разливка биметаллических заготовок (является наиболее перспективной разновидностью).
Рассмотрим кратко сущность каждой из указанных выше разновидностей.
1)Заливка жидким металлом пластины или стержня другого состава, вертикально расположенных в изложнице, может применяться, например, при производстве толстолистового коррозионностойкого биметаллического проката или сталемедной проволоки, которая используется для электротехнических целей.
Основные технологические операции при изготовлении методом заливки коррозионно-стойких толстых биметаллических листов следующие:
в изложницу для отливки слитков массой помещается специально подготовленный сляб из коррозионно-стойкой стали (подготовка сляба заключается в его стружке с четырех сторон для удаления
окалины и поверхностных дефектов, в обезжиривании, приварке ушек и штырей для монтажа сляба в изложнице и в обмазке сляба с двух сторон: с внешней магнезитовым порошком для предотвращения сварки с металлом изложницы, а с внутренней нашатырем для улучшения условий получения прочного соединения).
Схемы изложниц и размещения в них слябов плакирующего слоя представлены на рисунке 4.1. При этом следует заметить, что схемы 4.1,а и 4.1,б используются соответственно для получения одного двухслойного или двух двухслойных слитков, а схемы 4.1,в и 4.1, г – для

24
получения трехслойных слитков с расположением основного слоя внутри (рис. 4.1,в) или снаружи (рис. 4.1,г).
Рисунок 4.1 – Схемы изложниц и размещения в них слябов плакирующего слоя:
1 – изложница; 2 – сляб плакирующего слоя; 3 – разделительный слой; 4 – распорки; 5 – угольники
Необходимо также сказать, что ширина сляба плакирующего слоя, устанавливаемого в изложницу, должна быть на 20-30 мм, а длина примерно на 100 мм меньше соответствующих внутренних размеров изложницы. При этом толщину указанного сляба рекомендуется определять по следующему соотношению:
Нпл k |
а b c |
, |
(4.1) |
|
100 |
||||
|
|
|
где а– заданная толщина плакирующего слоя в готовом листе, в % от общей толщины листа;
b– средняя толщина двухслойного слитка (в направлении, перпендикулярном к широкой его грани), мм;
c– толщина так называемой «подливки» (т.е. зазора между слябом плакирующего слоя и стенкой изложницы), мм;
k– опытный коэффициент, учитывающий неравномерность деформации слоев при прокатке (для случая прокатки двухслойной стали с одинаковыми прочностными характеристиками основного и плакирующего слоев k=1,0).
Значения коэффициента k, которые могут быть использованы при разработке технологического процесса производства коррозионностойких биметаллических толстых листов, приведены в таблице 4.1.
25
Таблица 4.1 – Значения коэффициента неравномерности при прокатке некоторых марок нержавеющих сталей в сочетании со сталями Ст3сп, 15К, 20К
Марка стали |
Толщина двухслойного |
k |
плакирующего слоя |
листа, мм |
|
|
|
|
12Х18Н9Т |
5-6 |
0,57 |
|
|
|
12Х18Н9Т |
8 |
0,65 |
|
|
|
12Х18Н9Т |
12-25 |
0,70 |
|
|
|
12Х18Н9Т |
35-40 |
0,75 |
|
|
|
08Х17Н13М2Т |
30-40 |
0,55 |
|
|
|
08Х13 |
8-40 |
1,3 |
|
|
|
в изложницу со слябом плакирующего слоя заливают углеродистую сталь; при этом заливаемая сталь сначала образует защитный слой – так называемую «подливку», который необходим для защиты поверхности сляба от окисления (толщина указанного слоя составляет примерно 50-60 мм).
после заливки слитки охлаждают, извлекают из изложницы и передают на нагревательные колодцы, где их нагревают до температуры прокатки, определяемой составом основного и плакирующего слоя. Затем нагретые слитки прокатывается на обжимном стане – слябинге или блюминге до заданных размеров сляба с максимально возможными частными обжатиями (для повышения прочности сцепления слоев).
слябы охлаждают, после чего со слябов удаляется подливка; затем слябы зачищаются и нагреваются в методических печах; после нагрева слябы прокатываются на толстолистовом стане до требуемой толщины.
Полученные описанным способом листы после правки и обрезки
подвергаются термообработке, повторной правке, травлению и окончательной отделке.
Аналогично получают биметаллическую сталемедную проволоку. Разница заключается в том, что сердечник в слитке имеет круглую или квадратную форму. Прокатка слитков ведется на блюминге, а затем на сортовом стане до заданных размеров горячекатаного подката, который затем подвергают травлению и последующему волочению до конечных размеров.

26
2)Заливка жидкого металла на твердую составляющую применяется для получения биметаллов в виде стальных лент с плакирующим слоем из цветных металлов и сплавов, а именно меди, латуни или бронзы. Этот метод применяется не очень широко, т.к. требуется подогрев до высоких температур стального основания и последующая механическая обработка литой поверхности. При больших размерах листов требуются специальные нагревательные печи и дополнительный парк режущих и обрабатывающих станков.
Последовательность технологических операций для получения биметалла в сочетании сталь + цветной металл следующая:
сначала подготавливается стальная основа (т.е. стальная пластина): плоскость разъема строгают, обезжиривают и наносят на нее слой флюса, который способствует лучшей приварке слоев биметалла; к пластине по периметру привариваются бортики, и таким образом получается своеобразный «противень» (смотрите рисунок 4.2).
Рисунок 4.2 – К пояснению метода заливки жидкого металла на твердую составляющую
полученный «противень» помещается в подогревательную печь и нагревается до температуры от 800 до 950 0С, чтобы уменьшить охлаждение заливаемого расплава и растворить оксиды на границе раздела двух слоев.
затем на «противень» заливается металл или сплав плакирующего слоя.
после остывания строжкой или фрезерованием с поверхности плакирующего слоя удаляют литейные дефекты.
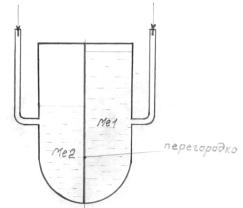
27
полученную описанным способом двухслойную заготовку нагревают и прокатывают в горячем состоянии до заданной
толщины (возможная также холодная прокатка). 3)Последовательная заливка двух различных металлов или сплавов в одну разъемную изложницу используется, например, для получения термобиметаллов и заключается в следующем: в разъемную изложницу, имеющую два сифонных канала помещают чугунный вкладыш (или перегородку); затем по первому каналу (смотрите рисунок 4.3) заливается более тугоплавкая составляющая биметалла; после некоторой выдержки (примерно до 1 мин) чугунный вкладыш вынимается, и по второму каналу заливается металл с более низкой температурой плавления. Причем следует сказать, что в процессе заливки подплавляется плоскость соединения с уже залитой составляющей и при этом обеспечивается более прочное соединение слоев.
Рисунок 4.3 – Схема заливки последовательной заливки двух металлов в одну изложницу
После затвердевания изложницу разбирают, а полученный слиток передают в прокатный цех и прокатывают.
Рассмотренный способ получения биметаллических заготовок имеет следующие основные преимущества:
позволяет соединять сплавы с резко отличающимися температурами плавления;
обеспечивается достаточно плотное соединение слоев.
3)Биметаллические заготовки также могут быть получены методами непрерывной разливки. Суть одного из указанных методов (смотрите рисунок 4.4) заключается в том, что сначала производится заливка

28
металла основного слоя в один кристаллизатор, а затем после образования толстой корочки у полученной непрерывно-литой заготовки последняя поступает во второй кристаллизатор, в который производиться заливка второго более легкоплавкого металла (т.е. металла плакирующего слоя). После затвердевания непрерывно-литые биметаллические заготовки разрезаются и передаются в прокатный цех для получения профиля требуемой конфигурации поперечного сечения и размеров.
Рисунок 4.4 – Схема отливки двухслойного (а) и трехслойного (б) биметаллических слябов:
1,2 – кристаллизаторы; 3,4 – соответственно основной и плакирующий слои сляба; 5 – тянущие ролики
Для получения трехслойных биметаллических заготовок также применяется способ заливки жидкого металла между двумя движущимися нагретыми лентами (смотрите рисунок 4.5). Сущность указанного способа заключается в следующем: жидкий металл из ковша 1 заливается между двумя движущимися навстречу друг другу предварительно нагретыми в печах 2 лентами; пройдя через кристаллизатор 3, систему роликов 4, заготовка затвердевает, вытягивается роликами 5 и сматывается в рулон моталкой 6. Для разматывания исходных полос служат разматыватели 7. Направляющие ролики 8 обеспечивают изгиб полосы в необходимом направлении.
Методы получения биметаллических заготовок, основанные на непрерывной разливке, являются в настоящее время более предпочтительными, чем рассмотренные ранее.

29
Рисунок 4.5 – Схема заливки жидкого металла между двумя лентами
4.2 Специальные методы получения биметаллов В последнее время получили распространение следующие
специальные способы получения биметаллов:
способ электродуговой наплавки плакирующего слоя из, например, меди, медных сплавов или высоколегированных сталей на плиту (сляб) из стали основного слоя с последующей горячей прокаткой; применяется данный способ как для производства листового, так и для производства сортового биметаллического проката, в частности, угловых и полособульбовых профилей; основным преимуществом способа является гарантированное получение прочного соединения вне зависимости от суммарной деформации при прокатке, а недостатком – необходимость дополнительной механической обработки поверхности плакирующего слоя.
способ получения биметаллов взрывом.
Сущность получения биметаллов взрывом заключается в следующем (смотрите рисунок 4.6). Нижняя неподвижная заготовка устанавливается на основании, в качестве которого используется песок, металлические плиты, древесно-стружечные плиты. Над этой неподвижной заготовкой с определенным для каждого сочетания металлов зазором устанавливается пластина другого металла, на

30
которую помещается заряд взрываемого вещества. При этом возможны две схемы расположения соединяемых поверхностей:
с исходным параллельным положением соединяемых поверхностей;
когда соединяемые поверхности расположены под некоторым углом друг к другу.
Рисунок 4.6 – Схема получения биметаллов взрывом
Практика показывает, что наиболее прочное соединение слоев происходит в том случае, когда соединяемые поверхности расположены друг по отношению к другу под некоторым углом. Расположение пластины под углом приводит к тому, что при взрыве пластина приобретает скорость порядка 2000 м/с, которая может быть разложена на касательную и нормальную составляющие по отношению к поверхности нижней пластины. Действие нормальной составляющей скорости приводит к возникновению больших давлений в местах соударения пластин, что сближает их до расстояний, достаточных для возникновения металлических связей, а также увеличивает истинную площадь контакта. Действие касательной составляющей вызывает тангенциальное перемещение метаемой пластины по неподвижной, что вызывает прочную сварку слоев.
Описанным способом соединяют пары металлов, которые затруднительно соединяются другими методами (например,