
Проектирование штампованных поковок
.pdfФ е д е р а л ь н о е а г е н т с т в о п о о б р а з о в а н и ю Г о с у д а р с т в е н н о е о б р а з о в а т е л ь н о е у ч р е ж д е н и е в ы с ш е г о
п р о ф е с с и о н а л ь н о г о о б р а з о в а н и я У ф и м с к и й г о с у д а р с т в е н н ы й а в и а ц и о н н ы й т е х н и ч е с к и й у н и в е р с и т е т
К а ф е д р а о б щ е й т е х н о л о г и и и м е т а л л о в е д е н и я
П Р О Е К Т И Р О В А Н И Е Ш Т А М П О В А Н Н Ы Х П О К О В О К , П О Л У Ч А Е М Ы Х Н А М О Л О Т А Х И К Г Ш П
П р а к т и к у м
п о д и с ц и п л и н е « Т е х н о л о г и я к о н с т р у к ц и о н н ы х м а т е р и а л о в »
Уфя 2006
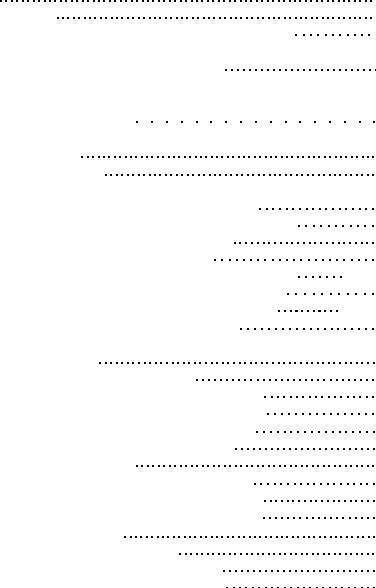
Составители: Ф.Ш. Шарифьянов, А.А. Маркелов
УДК 621.73(07) ЬВК 34.623(я7)
Проектирование штампованных „оковок, получаемых на молотах и К Г Ш П : Практикум по дисциплине «Технология конструкционных материалов» / У ф и м ^ о с . авиац. тех,',. у..-.-; С о е , Ф.Ш. Шарифьянов, А.А. Маркелов. - Уфа, 2006. - 56с.
Приведены основные характеристики различных марок ^сформируемых сталей для получения поковок, а также основные сведении об исходных заготовках, методике расчета их размеров. Главное внимание уделено основным этапам проектирования поковок, получаемых горячей объемной штамповкой вдоль оси заготовок на молотах и КГШП . Даны примеры расчета припусков и размеров поковки, а также оформления ее чертежа. В приложении представлены сравнительные характеристики различных способов горячей объемной штамповки, а также справочный материал, необходимый для проектирования поковок
Предназначен для студентов, обучающихся по направлениям подю/омки дипломированного специалиста 150201, 150202, 150204, 1М12()о, 150207, 150501, 151001, а также может быть использоилн п у д е н ш м и других специальностей.
Табл. 9. Ил. 10. Библиогр : 12 назв.
Рецензенты: Хайретдинов Э.Ф.,
Зарипова Р.Г.
СОДЕРЖАНИЕ |
|
Введение |
5 |
1. Цель работы |
7 |
2. Основные сведения о горячей объемной штамповке |
7 |
2.1. Материалы, применяемые при изготовлении поковок.... |
8 |
2.1.1. Категории прочности поковок |
9 |
2.1.2.Группы стальных поковок по видам испытаний ... 9
2.1.3.Обозначение на чертеже категории прочности и
|
ГТЗУППЫ поковок |
|
|
10 |
|
2.2. Исходные |
заготовки, |
обрабатываемые |
ковкой |
|
|
и штамповкой |
|
|
|
11 |
|
2.3. Тип производства |
|
|
13 |
||
3. Этапы проектирования штампованных поковок, получаемых |
|
||||
ГОШ вдоль оси заготовок на молотах и КГШП |
|
13 |
|||
3.1. Выбор поверхности (плоскости) разъёма штампа |
|
14 |
|||
3.2. Припуски на механическую обработку |
|
14 |
|||
3.2.1. |
Определение массы поковки |
|
15 |
||
3.2.2. |
Определение степени сложности поковки |
,. |
15 |
||
3.2.3. Определение группы стали для поковок |
— |
17 |
|||
3.2.4. |
Определение класса точности поковок |
18 |
|||
3.2.5. |
Определение исходного индекса |
|
19 |
||
3.2.6. Определение основных и дополнительных |
|
||||
|
припусков |
|
|
19 |
|
3.3. Назначение кузнечных напусков |
|
25 |
|||
3.3.1. |
Назначение штамповочных уклонов |
|
25 |
||
3.3.2. |
Установление радиусов закруглений |
|
26 |
||
3.4. Проектирование углублений и перемычек |
|
27 |
|||
3.4.1. |
Наметка с плоской перемычкой |
|
27 |
||
3.4.2. |
Глухая наметка |
|
|
28 |
|
3.4.3. |
Наметка с перемычкой с раскосом |
|
30 |
||
3.4.4. |
Наметка с перемычкой с карманом |
|
30 |
||
3.4.5. |
Наметка с перемычкой с магазином |
|
30 |
||
3.5. Назначение допусков |
|
|
31 |
||
3.6.Оформление чертежа поковки |
|
|
31 |
||
3.6.1. Правила выполнения чертежа |
|
31 |
|||
3.6.2 |
Базы механической обработки |
|
32 |
Уфимский государственный авиационныи технический университет, 2006
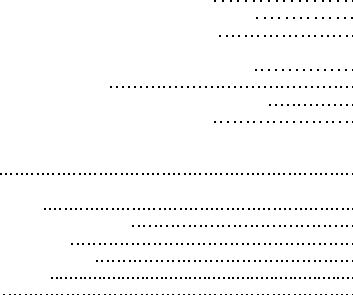
3.7. Составление технических требований |
|
|
34 |
|||
4. Пример проектирования штампованной п о к о в к и |
|
35 |
||||
4.1. |
Отработка втулки на технологичность |
|
|
35 |
||
4.2. |
Расчет |
(назначение) |
допусков |
и |
допускаемых |
|
|
отклонений и припусков на поковку втулки |
|
37 |
|||
|
4.2.1. Расчет покоики |
|
|
|
37 |
|
|
4.2.2. Кузнечные напуски на размеры |
втулки |
39 |
|||
4.3. |
Составление чертежа поковки втулки |
|
|
40 |
||
4.4. |
Содержание технических требований на поковку втулки |
40 |
5.Расчет размеров исходной заготовки для штампованной
|
поковки |
41 |
|
|
5.1. |
Пример расчета размеров |
заготовки под поковку |
|
|
для втулки |
44 |
6. |
Порядок выполнения работы |
46 |
|
7. |
Содержание отчета |
46 |
|
8. |
Контрольные вопросы. |
46 |
|
Список |
литературы |
47 |
|
Приложения |
49 |
ВВЕДЕНИЕ
Кузнечно-штамповочное производство предназначено для изготовления изделий, являющихся машиностроительными заготовками. Кузнечно-штамповочное производство уступает литейному производству в сложности конфигурации получаемых заготовок. Однако кованые и штампованные поковки отличаются высокими механическими свойствами, что обеспечивает надежность и долговечность изготавливаемых из них деталей. Поэтому наиболее ответственные, сильно нагруженные детали изготавливают из заготовок, полученных ковкой или штамповкой.
Среди множества способов получения заготовок обработкой давлением наибольшее распространение получили свободная ковка и горячая объёмная штамповка (ГОШ). Заготовки, полученные свободной ковкой, называют коваными поковками, а изготовленные объёмной штамповкой - штампованными поковками или штамповками. В дальнейшем изделия, полученные ГОШ, будем называть поковками (согласно ГОСТ 7505 - 89).
Ковку обычно применяют в единичном и мелкосерийном производствах. Объёмная штамповка наиболее эффективна при серийном и массовом производстве поковок массой от нескольких граммов до 3 тонн, но чаще оказывается целесообразным изготовление поковок и штамповок массой 50...200 кг [1, 2]. ГОШ обеспечивает высокую точность заготовок и малый отход металла при окончательной механической обработке.
В зависимости от используемого оборудования различают объёмную штамповку на штамповочных паровоздушных молотах (ПМ), кривошипных горячештамповочных прессах (КЗПШТ), горизонтально-ковочных машинах (ГКМ), гидравлических прессах (ГП) и т. д.
Выбор способа получения поковки зависит от пластичности материала и его сопротивления деформированию, конфигурации детали, степени ее сложности, массы, объема выпуска и условий работы детали. При низкой пластичности материала затруднительно получить качественную поковку, усложняется технологический процесс, повышается себестоимость детали. Способ штамповки ориентировочно можно выбрать по сравнительным характеристикам различных способов штамповки, приведенным в приложении 1.
5
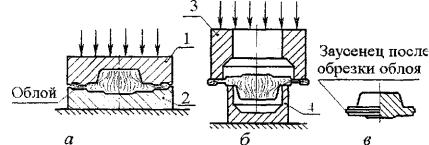
Окончательно |
способ изготовления заголовки мо*,1о , с т а к ^ ш , |
||
стшь проведя |
сравнительный |
анализ экономимся», о |
расчет |
нескольких вариантов получения поковок. |
О С Н О В Н ы е |
||
В работе рассмотрена |
последовательность и |
основные |
положения разработки чертежа штампованных поковок, получаемых
Г : " и КГ1ЛП штамповкой |
в торец |
( в д о л ь ^ и ) |
з а — |
Приведен также порядок расчета размеров |
ноковки и |
исходной |
|
заготовки. |
|
|
|
ft
ПРОЕКТИРОВАНИЕ ШТАМПОВАННЫХ ПОКОВОК, ПОЛУЧАЕМЫХ НА МОЛОТАХ И КГШП
1.Цель работы
1.1.Научиться проектировать штампованные поковки, получаемые на молотах и КГШП.
1.2.Усвоить методику расчета размеров поковки и исходной
заготовки.
1.3.Изучить ГОСТы, регламентирующие припуски, допуски, напуски при штамповке и устанавливающие правила выполнения чертежей поковок, содержание основных технических требований.
2.Основные сведения о горячей объемной штамповке
Для получения штампованных поковок широко используется открытая штамповка (рисЛ). Штамповка в открытых штампах характеризуется тем, что штамп по периметру чистового штамповочного ручья имеет облойную канавку.
Р и с . 1. С х е м а п о л у ч е н и я п о к о в к и : а - открытая штамповка; б - схема обрезки облоя; в - поковка; 1 - подвижная часть штампа; 2 - неподвижная часть штампа; 3 - верхний нож;
4 - нижний нож.
В процессе штамповки в облойную канавку выдавливаются излишки металла, образуя облой, который закрывает выход из полости штампа и способствует ее полному заполнению. Такая конструкция штампа позволяет не предъявлять особо высоких требований к точности исходных заготовок по массе.
При выборе открытой штамповки следует учесть, что наличие облоя увеличивает расход металла, кроме того, для его удаления требуется применение специальных обрезных прессов и штампов
(рис. 1, б). Этот вид штамповки можно применять для получения поковок любой конфигурации.
2.1. Материалы, применяемые при изготовлении поковок
Материал, из которого будет изготовлена деталь, устанавливается конструктором еще на стадии проектирования изделия или детали. При выборе материала конструктор учитывает возможный метод получения заготовки (штамповка или литье) под проектируемую деталь. Если предполагается изготовление заготовки обработкой давлением (ковкой, штамповкой, поперечно-клиновой прокаткой и т. д.), то выбирается деформируемый сплав, а если литая заготовка (отливка) - литейный сплав. Заготовки, получаемые порошковой металлургией, требуют исходных порошковых материалов. При выборе конкретного материала детали конструктор учитывает его технологические свойства, условия эксплуатации (среда агрессивная или нейтральная; нагрузки статические, динамические или циклические; деталь работает в условиях трения или покоя и т. д.), сложность конфигурации, габаритные размеры. Следует также учесть стоимость материала. Если выбрана сталь, то следует подобрать марку по возможности с меньшим содержанием углерода и легирутощих, элементов, которая окажется дешевле и с повышенной ковкостью.
В зависимости от назначения, ответственности, габаритных размеров и условий работы для поковок могут быть использованы:
—сталь углеродистая конструкционная обыкновенного качества (ГОСТ 380— 94);
—сталь углеродистая конструкционная качественная (ГОСТ 1050—88);
—сталь легированная конструкционная (ГОСТ 4543—71);
—высоколегированные, коррозионно-стойкие, жаростойкие и (ГОСТ 5632-72)
—цветные деформируемые сплавы (алюминиевые, магниевые, титановые, медные и др.).
В приложении 2 приведены наиболее распространенные марки сталей для изготовления поковок, область их применения и условия деформирования.
При выборе марки стали для деталей, подвергаемых упрочняющей термической обработке, кроме общепринятых
критериев и регламентируемых стандартами механических свойств сталей, следует учитывать и размеры их сечения. При этом решающее влияние на свойства может оказать прокаливаемость стали. Так, чем больше диаметр или толщина детали, тем больше сталь должна иметь легирующих элементов, увеличивающих глубину закаленного слоя (прокаливаемости) детали и повышающих механические свойства.
2.1.1. Категории прочности поковок. По механическим свойствам поковки, поставляемые после окончательной термической обработки, разделяются на категории прочности. Категории прочности и соответствующие им нормы механических свойств, определяемые при испытании на продольных образцах, а также нормы твердости приведены в приложении 3.
В соответствии с ГОСТ 8479—70 поковка может быть изготовлена одной из шестнадцати категорий прочности. Каждой категории прочности соответствуют минимальные нормы механических свойств, и в зависимости от размера поперечного сечения необходимо выбрать ту или иную марку стали.
2.1.2. Группы стальных поковок по видам испытаний.
Согласно ГОСТ 8479—70, по видам испытаний, установленных
потребителем, а также |
в зависимости от назначения деталей, для |
|
которых используются |
поковки, их подразделяют на пять групп: |
|
I — поковки, |
не подвергаемые |
испытаниям с целью |
определения механических свойств;
II— поковки с обязательным определением твердости для партии поковок, прошедших совместную термическую обработку;
III— поковки с определением твёрдости каждой поковки;
IV — поковки, для которых требуется проведение испытаний на растяжение, определение ударной вязкости и твердости для партии поковок, прошедших совместную термическую обработку. Основанием для сдачи поковки являются соответствия свойств ав , °"о,2; S, ц), KCU, НВ заданным в технических требованиях чертежа величинам;
V— поковки, для каждой из которых определяют комплекс механических свойств: ств, а0 ,2 , 5, у, KCU, НВ.
Для испытания поковки комплектуются предприятиемизготовителем в партии. В партию входят поковки, изготовленные по одному чертежу. В отдельных случаях, допускается объединять в
8
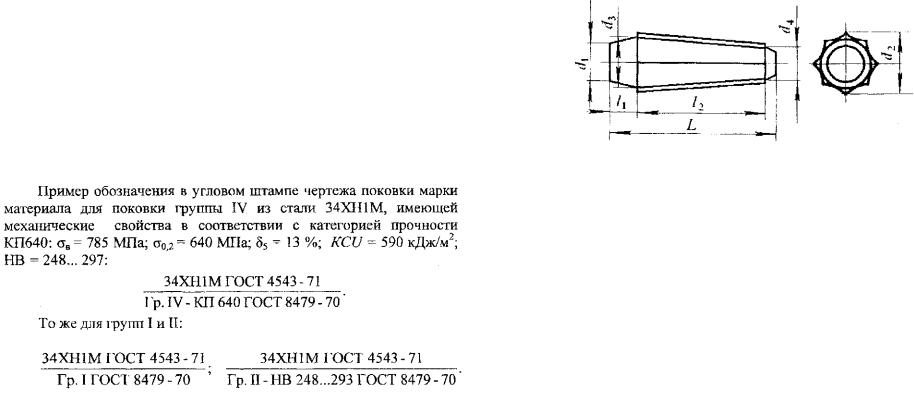
партию поковки, изготовленные из одной марки стали, по разным чертежам, по близкие по конфигурации. Для каждой группы (за исключением группы I) устанавливается определенный объем обязательных испытаний (приложение 4).
При разработке технологического процесса необходимо на чертеже поковок IV и V трупп предусмотреть дополнительные объемы металла пробы для механических испытаний.
2.1.3. Обозначение на чертеже категории прочности и группы поковок. Нормы твердости для поковок II и Ш групп и категории прочности для поковок IV и V групп устанавливаются по соглашению изготовителя с потребителем.
Конструктор на чертеже поковки указывает не только марку стали, но и категорию прочности сплава, и группу поковок по видам испытаний.
Согласно ГОСТ 8479-70 группа, к которой относится поковка,
обозначается в технических требованиях следующим образом: |
|
|
- |
поковка группы I - Гр. I ГОСТ 8479-70. Эта группа поковок |
|
поставляется потребителю без механических испытаний; |
|
|
- |
поковки группы II и Ш с твердостью НВ 143..Л79 - |
Гр. II |
(III) НВ 143... 179ГОСТ8479-70; |
|
|
- |
поковки группы IV (V) с категорией прочности КП490 |
- Гр. |
IV (V) |
КП490 ГОСТ8479-70. |
|
Материал поковки, а также ее группа также может указываться в угловом штампе.
2.2. Исходные заготовки, обрабатываемые ковкой и штамповкой
Исходными стальными заготовками для ковки и объёмной штамповки могут быть слитки (рис. 2) и сортовой прокат.
С л и т о к является заготовкой для крупных поковок, может использоваться для одной или нескольких поковок. Слитки получают разливкой стали в изложницы из конверторов или мартеновских и электрических печей. Форма слитков может быть различной и зависит от металлургического предприятия, выпускающего слитки. Чаще встречается форма слитка в виде многогранной усеченной пирамиды. Поперечное сечение средней части слитков может быть 4-, 6-, 8- и 12-угольным. Основные размеры и масса стальных слитков приведены в приложении 5, а также в [3, с. 65...72; 4, с. 57...60].
Рис. 2. Стальной слиток Новокрамоторского металлургического завода
Верхняя (прибыльная) часть слитка (/,) содержит усадочную раковину и не может быть использована в поковке. Нижняя (донная) часть [L ~ ( /, + /2)] также является отходом слитка. Отход слитка составляет по прибыльной части 18... 30 %, а по донной - 3...8 % от общей массы слитка. Меньшие значения
отхода |
соответствуют слиткам |
из углеродистой |
стали, |
а большие — |
из |
||
легированной. Донная и прибыльная части отделяются |
от слитка |
кузнечной |
|||||
рубкой |
в начале ковки (после |
биллетировки) |
или |
от |
концов |
поковки |
на |
заключительной стадии и отправляются на переплав. |
|
|
|
|
Сортовой прокат используют для большинства штампованных и мелких кованых поковок. Длина прутков составляет 2...6 м. Поперечное сечение горячекатаного проката может быть квадратное (ГОСТ 2591—88) или круглое (ГОСТ 2590—88). Размеры поперечного сечения (диаметр, сторона квадрата) устанавливаются этими стандартами и по сортаменту составляют: 5; 6; 8; 10; 12; 15; 18; 20; 22; 24; 25; 26; 28; 30; 32; 34; 36; 38; 40; 42; 45; 48; 50;
10 |
II |
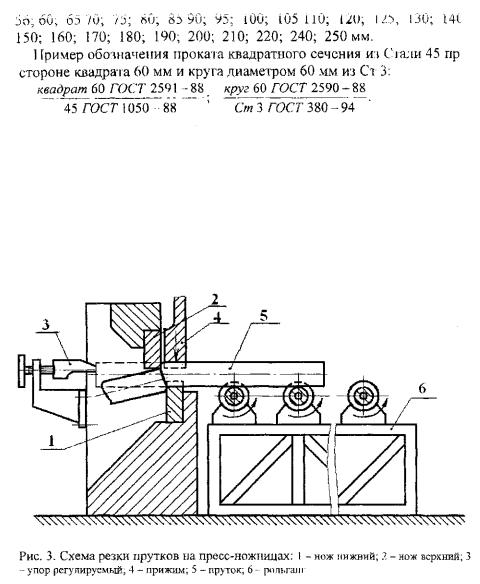
Исходные материалы подлежат разделке на штучные заготовки. Слитки разделывают непосредственно в процессе ковки, а сортовой прокат - на заготовительных участках. Разрезку проката производят пилами, газовой резкой, но чаще всего на кривошипных прессножницах и хладноломах. Рабочим инструментом ножниц (рис. 3) являются нижний 1 и верхний 2 ножи. Рольганг 6 подает пруток 5 в окно между кромками ножей 1 и 2 до роулируемого упора 3. Прижим 4 предохраняет искривление прутка и улучшает качество среза. Отделение заготовки происходит при ходе верхнего подвижного ножа 2 вниз.
Точность резки на пресс-ножницах удовлетворяет основным видам штамповки и ковки. Существующие пресс-ножницы позволяют разделять прутки с поперечным размером до 250 мм. Причем прутки крупных сечений (более 80 мм), а также из хрупких и
легированных |
сталей разделяют после |
подогрева до |
температуры |
450 550 °С. |
|
|
|
2.3. Тип |
производства |
|
|
Тип производства задается в |
техническом |
задании на |
проектирование технологического процесса изготовления поковки. Ориентировочно тип производства в зависимости от объема годового выпуска поковок и от массы определяется по данным приложения. 6.
3. Этапы проектирования штампованных поковок, получаемых ГОШ вдоль оси заготовок на молотах и КГШП
Качество поковок, их стоимость, время изготовления, возможности механизации и автоматизации процессов и т. п. зависят не только от технологического процесса их изготовления, но и от того, как спроектирована конкретная деталь, каковы ее форма и размеры, а также - насколько учтены конструктором возможности технологии производства поковок.
Проектировать поковки необходимо по возможности наиболее приближенными к конфигурации окончательно-обработанной детали, что позволит сократить стоимость их изготовления за счет малых
припусков, |
повысить точность поковок по размерам и форме. |
Чертеж поковки разрабатывается на основе чертежа детали в |
|
следующей |
последовательности: |
-проводится анализ детали на технологичность (см. п. 4.1);
-устанавливается положение поверхности разъёма штампа;
-определяется ориентировочная (расчетная) масса поковки;
-назначаются по ГОСТ 7505-89 припуски на обрабатываемые резанием поверхности детали и допуски на размеры, относящиеся к этим поверхностям;
-назначаются напуски на отверстия и проточки;
-выбираются радиусы закругления; назначаются штамповочные уклоны;
-определяются форма и размеры наметок отверстий и перемычки под их прошивку;
- оформляется чертёж поковки в соответствии с ГОСТ 3.1126-88 с указанием технических требований на изготовление и приемку поковки по ГОСТ 8479-70.:
Рассмотрим основные этапы конструирования поковки.
12
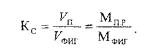
3.1. Выбор поверхности (плоскости) разъёма штампа
1 IoBcpxiiocTb разъема - это поверхность, по которой соприкасаются верхняя и нижняя части штампа. В открытом штампе ни мой поверхности располагают облойную канавку (см. рис.1).
При выборе плоскости разъёма штампа следует руководствоваться следующими основными правилами [5, с. 37...39; 6, с. 122; 7, с. |9|:
1) плоскость разъёма должна располагаться в плоскости наибольшего сечения (периметра), что позволяет свободно извлекать поковку из штампа. При этом, полости штампа будут иметь наименьшую возможную глубину и наибольшую ширину и длину, что обеспечивает повышенную стойкость штампа и легкость его изготовления;
2)плоскость разъёма должна учитывать возможность контроля сдвига между верхней и нижней половинами штампа, который устанавливается по внешнему виду поковки после обрезки облоя. Контроль смещения частей штампа упрощается, если поверхность разъёма пересекается вертикальными образующими поковки;
3)поверхность разъёма должна быть плоской во избежание сдвига штампа, а также коробления поковки при обрезке облоя;
4)плоскость разъёма не должна перерезать волокнистую структуру поковки, что приведет к снижению прочностных свойств детали;
5) при штамповке на молотах высокие и тонкие выступы располагают в верхней половине штампа. В этом случае они охлаждаются медленнее за счет меньшего времени контакта заготовки со штампом;
6) плоскость разъема должна ориентировать ручьи штампа таким образом, чтобы их заполнение осуществлялась по возможности за счет осадки, а не вылавливания.
3.2. Припуски на механическую обработку
Припуск - это поверхностный слой материала заготовки, подлежащий удалению при последующей механической обработке. Припуск на механическую обработку включает основной, а также дополнительный припуски, учитывающие отклонения формы и размеров поковки. Величина припусков назначается на одну сторону
номинального размера поковки. По ГОСТ 7505-89 припуски устанавливаются на стальные поковки массой до 250 кг и с линей ными размерами до 2500 мм, изготовляемые на различных видах кузнечно-прессового оборудования ГОШ. Припуски устанавливаются в зависимости от массы, степени сложности, группы стали, требуемой точности изготовления поковки, шероховатости поверхностей обработанной детали, номинальных размеров, а также - исходного индекса. Рассмотрим последовательность определения исходного индекса, т. е. строки табл. 3, по которой назначается основной припуск на размеры поковки.
3.2.1. Определение массы поковки. Точная масса поковок рассчитывается для последующего определения размеров исходной заготовки на основе разработанного чертежа поковки, исходя из ее размеров и объёма. Первоначально, при назначении припусков определяется расчетная (ориентировочная) величина массы поковки
(МПР) по формуле |
Мпр=Мд-КР , |
(1) |
где МП Р - расчетная |
масса поковки, кг; |
Мд - масса детали, кг; КР - |
расчетный коэффициент, устанавливаемый в зависимости от конфигурации поковки. Так, например, для поковок круглых в плане (шестерни, ступицы, фланцы) он составляет КР = 1,4... 1,8. Если масса детали не задана на чертеже, то ее вычисляют как произведение
объема на плотность (р = 7, 8 |
г/см3 или 7800 |
кг/м3). Объем |
определяется как сумма объемов |
элементарных |
геометрических |
фигур, образующих конфигурацию детали по размерам, указанным на ее чертеже. При этом для удобства расчетов, чтобы не оперировать при расчете объема большими числами, размеры детали рекомендуется брать в см или в м (при размерности плотности стали соответственно в г/см3 или кг/м3).
3.2.2. Определение степени сложности поковки. Степень сложности является одной из конструктивных характеристик формы поковок. По ГОСТ 7505-89 различают четыре степени сложности поковки (CI, С2, СЗ, С4) в зависимости от отношения объёма V„ или массы поковки МПР к объёму УФЖ или массе фигуры МФ И г в виде цилиндра или прямоугольного параллелепипеда, описанного вокруг поковки. Таким образом, коэффициент сложности Кс определяется по формуле:
14
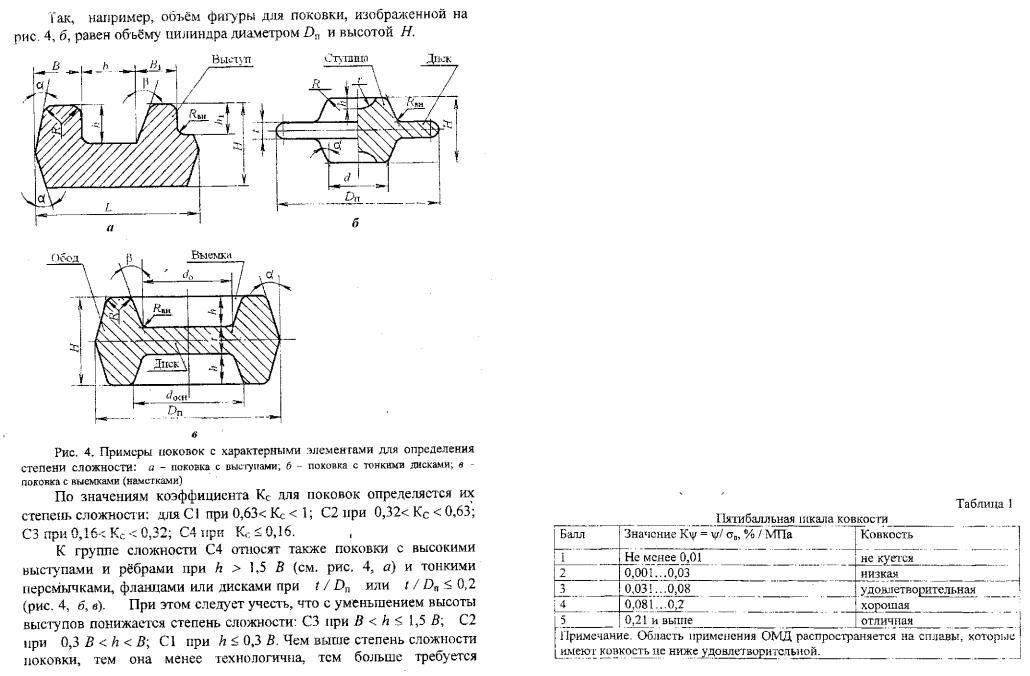
штамповочных переходов, сложнее получаются но конфигурации и в изготовлении ручьи штампа, их количество возрастает, понижается точность поковок, больше потери металла при механической обработке, выше требуемая мощность оборудования.
При проектировании поковок следует избегать высоких и тонких рёбер, бобышек, тонких перемычек и буртов, узких и глубоких полостей. При ГОШ наличие перечисленных элементов на поковке приводит к местному охлаждению металла, следовательно, снижению пластичности материала поковки, резкому повышению усилия штамповки и снижению стойкости штампа.
3.2.3. Определение группы стали для поковок. Все стали для получения поковок по ГОСТ 7505-89 разделены на три группы (Ml, М2 и МЗ). При определении группы стали исходят из среднего массового содержания углерода и легирующих элементов ( Si, Мп, Ni, Cr, Mo, W, В).
К первой группе Ml относятся углеродистые и легированные стали с содержанием углерода до 0,35 % или с суммарной долей легирующих элементов до 2,0 %.
Во вторую группу М2 - стали с содержанием углерода свыше 0,35 до 0,65 % или легирующих элементов свыше 2,0 до 5,0 % .
Третью группу МЗ составляют стали с содержанием углерода свыше 0,65 % или легирующих элементов свыше 5,0 %.
Цветные сплавы на такие группы не делятся, их способность к пластическому деформированию определяют по критерию ковкости и пятибалльной шкале.
Ковкость м а т е р и а л а . Способность металлов и сплавов к ковке и штамповке проверяют по численному значению критерия ковкости и
ттатибягпт^нг>й ттшягтр Лгя^тт 1 ^
16
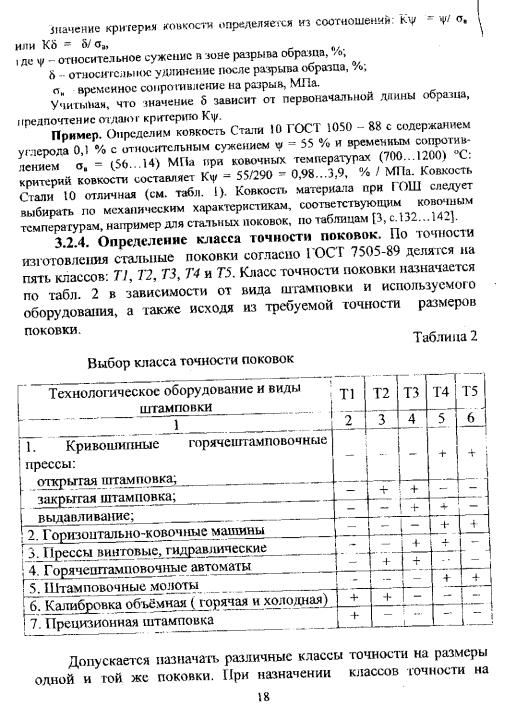
поковки следует учесть, что при пламенном нагреве заготовок допускается снижение точности для классов Т2...Т4 на один класс, а при холодной или плоскостной калибровке точность принимается на один класс выше.
Прецизионная штамповка является самой точной и обеспечивает устанавливаемую точность и шероховатость одной или нескольких функциональных поверхностей поковки, которые не подвергаются обработке резанием.
3.2.5. Определение исходного индекса. Исходный индекс определяется в зависимости от расчетной массы поковки Мп .р, степени сложности, марки стали и класса точности поковки по табл. 3 и используется для последующего назначения основных припусков, допусков и допускаемых отклонений. Исходный индекс показывает строку, но которой назначаются припуски (табл. 4) и допуски (табл. 5) на размеры поковки.
Для определения исходного индекса по табл. 3 в графе «Масса поковки» находят соответствующую данной массе строку и, смещаясь по горизонтали или по утолщенным наклонным линиям, устанавливают исходный индекс. Например, для поковки с массой 0,75 кг, группой стали M l , степенью сложности СЗ и классом точности Т2 исходный индекс соответствует 6. Класс точности, а также группа стали, степень сложности, исходный индекс должны указываться в технических требованиях чертежа поковки.
3.2.6. Определение основных и дополнительных припусков.
Основные припуски на механическую обработку поковок устанавливаются в зависимости от исходного индекса, линейных размеров и шероховатости поверхности детали по табл. 4. Значения дополнительных припусков определяются исходя из массы, класса точности и наибольших размеров поковки по табл. 4...6 ГОСТ 7505-
89.Дополнительные припуски назначаются в следующих случаях:
-на смещения по поверхности разъема штампов. Устанавливаются на размеры элементов поковки параллельных плоскостей разъема при штамповке в открытых штампах (табл. 4
ГОСТ 7505-89) в зависимости от массы и класса точности поковки Т; - на изогнутость и отклонения от плоскостности. Назначаются на размеры элементов, перпендикулярные плоскости разъема, если
размеры торцевой поверхности в 2 и более раза превышают высоту (D(B)/ Н> 2) по табл. 5 ГОСТ 7505-89;