
ОТД_Краткий курс лекций_2010
.pdfТаблица 6.1– Идентификация недопустимых дефектов корпусных деталей арматуры и узла затвора
Элементы арматуры |
Описание дефекта |
Недопустимые размеры дефекта |
Метод контроля для обнаружения |
|
|
|
|
дефекта |
|
Необработанные поверхно- |
Подповерхностные трещи- |
Не допускается |
Капиллярный, магнитопорошковый |
|
сти корпуса, крышки, пат- |
ны, свищи |
|
|
|
рубков |
|
|
|
|
Поверхностные трещины, |
Не допускается |
Визуально-измерительный, капиллярный, |
||
|
||||
|
наплавки вполненные в про- |
|
магнитопорошковый |
|
|
цессе эксплуатации |
|
|
|
|
|
|
|
|
|
Раковины |
Одиночные в плане более 5 мм и глубиной более 15 % тол- |
Визуально-измерительный, ультразвуковой, |
|
|
|
щины стенки |
капиллярный, магнитопорошковый |
|
|
|
|
|
|
|
|
Рассредоточенные в плане более 3 мм и глубиной более 15 % |
Визуально-из мерительный, ультразвуковой |
|
|
|
толщины стенки, в количестве более трех на площади разме- |
|
|
|
|
ром 100 на 100 мм при расстоянии между ними менее 15 мм. |
|
|
|
Риска (царапина, задир) |
Глубиной более 5% толщины стенки |
Визуально-измерительный |
|
|
внутренние несплошности |
площадью более 20 мм2 для толщин до 50 мм и более 30 мм2 |
Ультразвуковой |
|
|
|
для толщин от 50 до 100 -мм |
|
|
Обработанные поверхности |
|
|
|
|
корпуса, крышки, в том чис- |
|
|
|
|
ле: |
|
|
|
|
отверстия под запрессовку |
Трещины, наплавки, ракови- |
Не допускается |
Визуально-измерительный |
|
втулок или под сальниковую |
ны |
|
|
|
набивку |
|
|
|
|
|
|
|
|
|
сопрягаемые поверхностях |
Трещины, наплавки |
Не допускается |
Визуально-измерительный |
|
фланцевого соединения |
|
|
|
|
Раковины |
В плане более 1 мм и глубиной более 1 мм |
Визуально-измерительный |
||
«корпус-крышка» |
||||
|
|
|
||
|
|
|
|
|
Сварные швы корпусных |
Трещины, незаваренные кра- |
Не допускается |
Визуально-измерительный, ультразвуковой, |
|
деталей |
теры, прожоги, свищи |
|
радиографический |
|
|
|
|
|
|
|
непровары, несплавления |
глубиной от 1 мм и длиной от 30 мм. |
Ультразвуковой, радиографический |
|
|
подрезы |
глубиной от 0,5 мм и длиной от 150 мм. |
Визуально-измерительный |
|
|
|
|
|
|
|
норы |
более 5% толщины свариваемых деталей. |
Ультразвуковой, радиографический |
|
|
|
|
|
|
|
шлаковые включения |
глубиной от 10% толщины шва и длиной от 7 мм. |
Ультразвуковой, радиографический |
|
|
несоответствие размеров |
Несоответствие размеров, выходящее за пределы допуска на |
Визуально-измерительный |
|
|
|
размер. |
|
|
Узел затвора в целом |
негерметичиость |
величины протечек, превышающие величины, указанные в |
Испытания на герметичность затвора |
|
|
|
таблице 1 и 2 |
|
|
|
|
|
|
|
|
|
|
121 |
Узел затвора, в том числе |
поверхностные несплошно- |
не допускается |
Визуально-измерительный |
уплотнительные поверхно- |
сти, эрозионный износ |
|
|
сти узла затвора |
|
|
|
122

Таблица 6.2- Недопустимые дефекты выемных элементов арматуры
|
Элементы арматуры |
Недопустимые дефекты |
Метод контроля для |
|
|
|
|
обнаружения дефекта |
|
|
|
|
|
|
|
Шпиндель |
Поверхностные трещины, изогнутость, задиры, |
Визуально- |
|
|
|
несоответствие геометрических размеров резь- |
измерительный, ка- |
|
|
|
бовой части шпинделя паспортным данным |
пиллярный, магнито- |
|
|
|
|
порошковый |
|
|
|
Подповерхностные трещины и несплошности |
Ультразвуковой |
|
|
Втулки бугельного |
Трещины, смятие, сколы, срыв резьбы у резь- |
Визуально- |
|
|
узла |
бовой втулки |
измерительный |
|
клиновая |
|
|
|
|
Подшипник |
Трещины колец, выкрашивание металла на |
Визуально- |
||
|
||||
|
|
кольцах, телах качения, выбоины на беговых |
измерительный |
|
|
|
дорожках колец, забоины, вмятины, глубокие |
|
|
Задвижка |
|
риски на кольцах подшипников, цвета побежа- |
|
|
|
лости, трещины, забоины, вмятины на сепара- |
|
||
|
|
|
||
|
|
торе. |
|
|
|
Нажимное и опорное |
Износ, смятие, трещины, сколы |
Визуально- |
|
|
кольца сальникового |
|
измерительный |
|
|
узла (втулка) |
|
|
|
|
Направляющие клина |
Трещины, задиры, направляющие должны |
Визуально- |
|
|
|
быть приварены к корпусу по всей длине |
измерительный |
|
|
Шпильки |
Трещины, задиры, смятие и срез витков или |
Визуально- |
|
|
|
витка резьбы, остаточная деформация, приво- |
измерительный |
|
|
Гайки |
дящая к .изменению профиля резьбы, износ |
Визуально- |
|
|
|
боковых граней гаек. |
измерительный |
|
|
Шпиндель |
Поверхностные трещины, изогнутость, задиры, |
Визуально- |
|
|
|
несоответствие геометрических размеров резь- |
измерительный, ка- |
|
|
|
бовой части шпинделя паспортным данным |
пиллярный, магнито- |
|
|
|
|
порош-ковый |
|
|
|
Подповерхностные трещины и несплошности |
Ультразвуковой |
|
|
Втулки бугельного |
Трещины, смятие, сколы. |
Визуально- |
|
|
узла |
|
измерительный |
|
|
Подшипник |
Трещины колец, выкрашивание металла на |
Визуально- |
|
шиберная |
|
кольцах, телах качения, выбоины на беговых |
измерительный |
|
|
лости, трещины, забоины, вмятины на сепара- |
|
||
|
|
дорожках колец, забоины, вмятины, глубокие |
|
|
|
|
риски на кольцах подшипников, цвета побежа- |
|
|
Задвижка |
|
торе. |
|
|
Втулка сальникового |
Износ, смятие, трещины, срыв резьбы |
Визуально- |
||
|
||||
|
уплотнения |
|
измерительный |
|
|
Шпильки |
Трещины, задиры, смятие и срез витков или |
Визуально- |
|
|
|
витка резьбы, остаточная деформация, приво- |
измерительный |
|
|
Гайки |
дящая к изменению профиля резьбы, износ бо- |
Визуально- |
|
|
|
ковых граней гаек. |
измерительный |
|
|
Дренажный трубо- |
Отсутствие функционирования дренажного |
Визуально- |
|
|
провод |
трубопровода, отсутствие герметичности отно- |
измерительный |
|
|
|
сительно внешней среды по соединениям дре- |
|
|
|
|
нажного трубопровода, коррозионное утонение |
|
|
|
|
стенки более 20%. |
|
|
|
|
|
123 |
Продолжение таблицы 6.2
Элементы арматуры |
Недопустимые дефекты |
Метод контроля для обна- |
||
|
|
|
ружения дефекта |
|
|
|
|
|
|
|
Шток |
Поверхностные трещины, задиры, несоответ- |
Визуально-измерительный, |
|
|
|
ствие геометрических размеров штока пас- |
капиллярный, магнитопо- |
|
|
|
портным данным |
рошковый |
|
|
|
|
|
|
|
|
Подповерхностные трещины и несплошности |
Ультразвуковой |
|
|
Подшипник |
Трещины колец, выкрашивание металла на |
Визуально-измерительный |
|
шаровой |
|
кольцах, телах качения, выбоины-на беговых |
|
|
|
дорожках колец, забоины, вмятины, глубокие |
|
||
|
|
|
||
|
|
риски на кольцах подшипников, цвета побежа- |
|
|
|
|
лости, трещины, забоины, вмятины на сепара- |
|
|
Кран |
|
торе. |
|
|
Кольца уплотни- |
Трещины, разрывы |
Визуально-измерительный |
||
|
||||
|
тельные |
|
|
|
|
Шпильки |
Трещины, задиры, смятие и срез витков или |
Визуально-измерительный |
|
|
Гайки |
витка резьбы, остаточная деформация, приво- |
|
|
|
|
дящая к изменению профиля резьбы, износ бо- |
|
|
|
|
ковых граней гаек. |
|
|
|
Штифты |
Трещины, задиры, смятие. |
Визуально-измерительный |
|
|
|
|
|
|
|
Шток |
Поверхностные трещины, задиры, несоответ- |
Визуально-измерительный, |
|
|
|
ствие геометрических размеров штока пас- |
капиллярный, магнитопо- |
|
|
|
портным данным |
рошковый |
|
|
|
Подповерхностные трещины и несплошности |
Ультразвуковой |
|
|
Подшипник |
Трещины колец, выкрашивание металла на |
Визуально-измерительный |
|
трехходовый |
|
кольцах, телах качения, выбоины на беговых |
|
|
|
дорожках колец, забоины, вмятины, глубокие |
|
||
|
|
|
||
|
|
риски на кольцах подшипников, цвета побежа- |
|
|
|
|
лости, трещины, забоины, вмятины на сепара- |
|
|
|
|
торе. |
|
|
Кран |
Кольца уплотни- |
Трещины, разрывы |
Визуально-измерительный |
|
тельные |
|
|
||
|
|
|
||
|
Шпильки |
Трещины, задиры, смятие и срез витков или |
Визуально-измерительный |
|
|
|
витка резьбы, остаточная деформация, приво- |
|
|
|
Гайки |
|
||
|
дящая к изменению профиля резьбы, износ бо- |
|
||
|
|
|
||
|
|
ковых граней гаек. |
|
|
|
Штифты |
Трещины, задиры, смятие. |
Визуально-измерительный |
|
|
|
|
|
|
|
Ось |
Поверхностные трещины, задиры, несоответ- |
Визуально-измерительный, |
|
затвор |
|
ствие геометрических размеров оси паспорт- |
капиллярный, магнитопо- |
|
|
ным данным |
рошковый |
||
|
|
|
||
|
Подповерхностные трещины и несплошности |
Ультразвуковой |
||
Обратный |
|
|
|
|
Шпильки |
Трещины, задиры, смятие и срез витков или |
Визуально-измерительный |
||
|
||||
|
Гайки |
витка резьбы, остаточная деформация, приво- |
|
|
|
|
дящая к изменению профиля резьбы, износ бо- |
|
|
|
|
ковых граней гаек. |
|
|
|
Демпфер (проти- |
Следы протечки на гидравлическом устройстве |
Визуально-измерительный |
|
|
вовес) |
|
|
|
|
|
|
124 |
Арматура (кроме списанной по результатам диагностики) после выполнения работ по дефектоскопии или диагностированию проверяется на прочность по зо-
нам, имеющим наибольшие напряжения. При этом должны быть проведены:
расчет на прочность корпуса и крышки;
расчет минимально допустимой толщины корпуса и крышки;
Нормирование прочности узлов и деталей арматуры необходимо выполнять по следующим нормативным документам:
ГОСТ 14249-89 Сосуды и аппараты. Нормы и методы расчета на проч-
ность (с учетом поправок 1997 г.);
РТМ 26-01-92-76 Сосуды и аппараты. Нормы и методы расчета на проч-
ность с учетом малоцикловых нагрузок;
РД 26-15-88 Сосуды и аппараты. Нормы и методы расчета на прочность
игерметичность фланцевых соединений;
ГОСТ 25221 -82 Сосуды и аппараты стальные. Днища и крышки сфери-
ческие необработанные. Нормы и методы расчета на прочность;
Оценочные расчеты необходимо выполнять с использованием инженерных методов, содержащихся в нормативных документах, указанных в предыдущем пункте, либо в другой нормативной документации или в справочной литературе.
Более полные расчеты численными методами необходимо выполнять по аттесто-
ванным компьютерным программам.
Расчеты выполняются с учетом фактических значений параметров, полу-
ченных при дефектоскопии и диагностировании:
толщины стенок (минимальное значение) с учетом дефектов;
предела прочности, который пересчитывается по значениям твердости материала.
Техническое состояние арматуры определяется по совокупности результа-
тов:
анализа документации на арматуру;
125
диагностирования арматуры методами неразрушающего контроля и ана-
лиза параметров технического состояния, повреждений и дефектов;
гидравлические испытания (во время освидетельствования при капи-
тальном ремонте);
поверочных расчетов на прочность.
Арматура допускается к дальнейшей эксплуатации в установленном поряд-
ке, если в результате проведенного технического освидетельствования определе-
но, что:
при расчетных параметрах нагружения (давлении и температуре) она на-
ходится в работоспособном состоянии (в том числе, коррозионный и эрозионный износ металла не снижает несущую способность нагруженных элементов ниже расчетной);
материальное и конструктивное исполнение арматуры отвечает требова-
ниям нормативной документации;
состояние металла удовлетворяет требованиям нормативной документа-
ции;
прочность и плотность соединений и элементов арматуры не ниже пока-
зателей, регламентируемых технической документацией на арматуру;
отсутствуют недопустимые дефекты и иные отклонения от требований нормативной документации, которые могут повлиять на работоспособное состоя-
ние арматуры;
Для арматуры, допускаемой к дальнейшей эксплуатации, определяется ос-
таточный срок службы.
Для определения остаточного срока службы арматуры выполняется расчет минимально допустимой толщины стенки δmin по допускаемым напряжениям ζдоп
для корпусов цилиндрической формы:
min |
|
K1 K |
2 |
Pном |
Dвн |
(6.1) |
2 |
доп |
|
||||
|
|
|
|
для корпусов сферической формы:
126
min |
|
K1 K |
2 |
Pном |
Dвн |
(6.2) |
2 |
доп |
|
||||
|
|
|
|
где δmin – минимально допустимая толщина стенки, мм,
Рном – номинальное рабочее давление согласно паспортным данным,
K1 = 1,1 коэффициент, учитывающий воздействие внешних сил, создавае-
мых опорами, фундаментом, другим оборудованием,
К2 = 1,25 коэффициент, применяемый для арматуры, изготовленной мето-
дом литья. Значения σдоп берутся из таблицы 6.3.
При этом должно быть соблюдено условие
ф min |
(6.3) |
Если условие (6.3) не соблюдается, то арматура должна быть снята с экс- |
|
плуатации. |
|
Таблица 6.3 – Допускаемые напряжения для углеродистых и низколегиро- |
|
ванных сталей по ГОСТ 14249 |
|
Расчетная темпера- |
Допускаемое напряжение, МПа (кгс/см2) для сталей марок |
||||
тура стенки армату- |
|
|
|
|
|
ВСтЗ |
20и20к |
09Г2С, 16ГС, |
10Г2 |
||
ры, |
|||||
|
|
17ГС, 16Г1С, |
|
||
|
|
|
|
||
|
|
|
10Г2С1 |
|
|
20 |
140 (1400) |
147 (1470) |
183 (1830) |
180(1800) |
|
|
|
|
|
|
|
100 |
134(1340) |
142 (1420) |
160 (1600) |
160 (1600) |
|
|
|
|
|
|
Остаточный срок службы арматуры, эксплуатирующейся в условиях стати-
ческого нагружения, где, определяющим повреждением являются общая коррозия или эрозия, протекающие с постоянной скоростью, осуществляется по формуле:
Остаточный срок службы по коррозионному износу определяется как:
T |
|
ф |
min |
(6.4) |
|
|
v |
||
|
|
|
|
где Т - остаточный срок службы;
δф - фактическая толщина стенки корпуса арматуры на момент проведения освидетельствования;
127
δmin - минимально допустимая толщина стенки корпуса арматуры; v - скорость коррозии (эрозии).
Средняя скорость коррозии v для корпусов арматуры за весь период экс-
плуатации рассчитывается по формуле
v |
|
и |
ф |
(6.5) |
|
|
|
||
|
|
t |
||
|
|
|
|
где δи – исполнительная толщина стенки элемента;
δф – фактическая толщина стенки элемента;
t – время от начала эксплуатации до момента обследования.
Если неизвестна исполнительная толщина стенки элемента, то скорость коррозии v для корпусов арматуры рассчитывается по формуле
v |
|
ф1 |
ф |
(6.6) |
|
|
|
||
|
|
t |
||
|
|
|
|
где δф1 – фактическая толщина стенки элемента по результатам предыдуще-
го обследования;
δф – фактическая толщина стенки элемента на момент обследования; t - время между обследованиями.
Для расчета остаточного ресурса арматуры, подвергающейся воздействиям циклических нагрузок, берутся наиболее нагруженные элементы арматуры (кор-
пус) и определяются фактические напряжения ζф.
Для корпусов арматуры, имеющих цилиндрическую форму, фактическое напряжение определяется по формуле
ф |
|
K1 K |
2 |
Pраб |
Dвн |
(6.7) |
|
2 |
ф |
|
|||
|
|
|
|
|
Для корпусов сферической формы фактическое напряжение определяется по формуле
ф |
|
K1 K |
2 |
Pраб |
Rвн |
(6.8) |
|
2 |
ф |
|
|||
|
|
|
|
|
где K1 – коэффициент, учитывающий воздействие внешних сил, создавае-
мых опорами, фундаментом, другим оборудованием, K1 = 1,1;
128

К2 – коэффициент, применяемый для арматуры, изготовленной методом ли-
тья, К2 = 1,25;
Рраб – максимальное рабочее давление;
Dвн – внутренний диаметр;
δф – фактическая минимальная толщина стенки корпуса арматуры.
Остаточный ресурс рассчитывается, исходя из количества циклов нагруже-
ния N от 0 до Рраб, которое может выдержать арматура, и полученных фактиче-
ских свойств материала.
Предельное число циклических нагрузок согласно модели Коффина – Мэн-
сона определяется по формуле
|
|
|
|
|
|
|
|
|
|
|
|
1 |
|
|
|
|
|
|
|
|
|
|
|
|
|
|
|
|
|
|
|
|
|
|
|
1 |
|
|
m |
|
||||
|
|
|
|
l |
n |
|
|
|
|
|
|
|
|
|
|
|
|
|
|
|
|
|
|||||||
|
1 |
|
|
|
1 K |
|
|
|
|
|||||
N |
|
|
|
|
|
(6.9) |
||||||||
|
|
|
|
|
|
|
|
|
|
|
|
|||
K |
|
|
|
|
|
0,4 |
|
|
||||||
|
N |
|
|
|
в |
|
|
|||||||
|
|
4 |
|
|
|
|
|
|||||||
|
|
0 |
|
|
|
|
||||||||
|
|
|
|
|
|
|
|
E |
|
|
|
|
||
|
|
|
|
|
|
|
|
|
|
|||||
|
|
|
|
|
|
|
|
|
|
|
|
где N – число циклов до зарождения трещины;
KN – коэффициент надежности, KN = 10;
ε0 – амплитуда истинных деформаций;
Е – модуль упругости;
ψК – относительное сужение;
m — показатель жесткости циклического нагружения, для арматуры НПС и линейной части нефтепроводов m = 0,53.
Величину ε0 вычисляют по формуле
0 |
K p |
(6.10) |
где p ф – упругие номинальные деформации в стенке оборудования;
E
Кε – коэффициент концентрации деформации.
Рассчитанное по формуле (6.9) число циклов N до зарождения трещин оп-
ределяет остаточный ресурс арматуры в циклах нагружения. Остаточный срок службы в годах определяется делением N на число циклов нагружения, которому арматура подвергается в течение года.
129
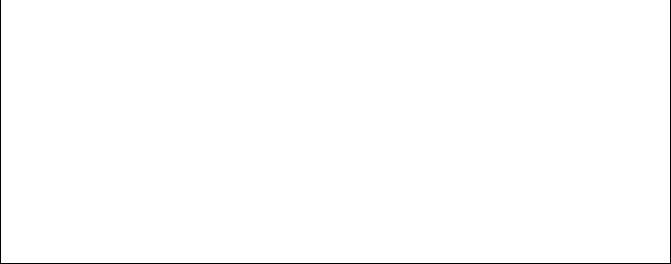
Остаточный срок службы
T |
N |
(6.11) |
|
i |
|||
|
|
где i – прогнозируемая годовая цикличность арматуры.
По результатам расчетов устанавливается срок следующего освидетельст-
вования, который должен выполняться до истечения ресурса оборудования, но который не может быть более 10 лет.
В таблице 6.4 приведены данные по определению остаточного ресурса ар-
матуры в зависимости от материала арматуры и толщины стенок.
Таблица 6.4 – Данные по определению остаточного ресурса арматуры в за-
висимости от коррозионно-эрозионного износа, материала арматуры и толщины стенок
Марка |
Скорость |
|
Остаточный ресурс при толщине стенок |
|
|||
стали ар- |
эрозии, |
Единица |
1,2…1,4∙δmin |
1,4…1,5∙δmin |
1,5…1,8∙δmin |
1,8…2,0∙δmin |
|
матуры |
коррозии, |
измерений |
|
|
|
|
|
|
мм/год |
|
|
|
|
|
|
ВСтЗ |
0,15 |
Цикл |
2200 |
5060 |
11930 |
|
22600 |
20 и 20к |
0,15 |
Цикл |
1142 |
2400 |
4990 |
|
8310 |
17ГС, |
0,15 |
Цикл |
2110 |
4920 |
12020 |
|
23750 |
16Г1С, |
|
|
|
|
|
|
|
10Г2С1 |
|
|
|
|
|
|
|
10Г2,09Г2 |
0,15 |
Цикл |
1210 |
2380 |
5380 |
|
9080 |
Примечание. δmin – минимально допустимая толщина стенки, определенная по формулам (6.1) и (6.2). Расчет выполнен при Kε = 3,0.
130