
- •Термическая обработка углеродистой стали
- •Критические точки диаграммы железо-углерод при нагреве и охлаждении
- •Диаграмма распада аустенита
- •Распад аустенита в перлитной области
- •Структура перлита, сорбита и троостита
- •Мартенситное превращение
- •Бейнитное (промежуточное) превращение
- •Виды термической обработки
- •Виды отжига
- •Рекристаллизационный отжиг – это нагрев стали до 680-700 0С (легированных прутков – до
- •Отжиг для снятия напряжений проводят для деталей из углеродистой стали с выдержкой 2,5
- •Изотермический отжиг – это нагрев высоколегированной стали выше Ас3 и быстром охлаждении до
- •Нормализация – это нагрев стали на 50-600С выше Ас3 и охлаждение на спокойном
- •Закалка
- •Мн – температура начала мартенситного превращения.
- ••Закаливаемость – способность стали принимать закалку, т.е. приобретать высокую твердость при закалке.
- •Прокаливаемость различных марок стали
- •Закалку в одном охладителе применяют для деталей простой формы. Нагретую до температуры закалки
- •Закалка с самоотпуском. Охлаждение проводят в одном охладителе и прерывают, когда сердцевина изделия
- ••Поверхностная закалка. Она является одним из способов увеличения твердости поверхностных слоев изделия. Одновременно
- ••При низком отпуске деталь нагревают до ≈150-200 0С, выдерживают в течение 1-3 часов
- •Отжиг – охлаждение в печи. Структура – перлит.
Отжиг для снятия напряжений проводят для деталей из углеродистой стали с выдержкой 2,5 мин на 1 мм сечения. Основное его назначение – возможно более полное изменение фазового состава.
•Полный отжиг – это нагрев доэвтектоидной стали до температур выше Ас3 на 30-500С, выдержка и охлаждение в печи, что обеспечивает полную перекристаллизацию.
•Неполный отжиг – это нагрев заэвтектоидной стали до температур выше Ас1 на 30-500С, выдержка и охлаждение в печи В структуре сохраняется вторичный цементит, который в результате отжига получается в виде зерен (глобулей). Получению зернистого цементита способствует предшествующая отжигу горячая пластическая деформация, при которой цементитная сетка дробится. Зернистый цементит улучшает обработку резанием.
Изотермический отжиг – это нагрев высоколегированной стали выше Ас3 и быстром охлаждении до температур на 1000С ниже Ас1 и выдержке в печи при этой температуре до полного превращения аустенита в перлит. Этот отжиг приводит к экономии времени отжига, но лишь для деталей с небольшим сечением из легированных сталей с целью получения более однородной структуры.
Нормализация – это нагрев стали на 50-600С выше Ас3 и охлаждение на спокойном
воздухе, в кипящей воде и т.п.
Получаемая структура – сорбит или троостит (в зависимости от скорости охлаждения).
Применяется для измельчения зерна.
Ее применяют как промежуточную операцию и как окончательную, например, при изготовлении сортового проката (рельсы, швеллеры и т.д.).
Нормализацию с последующим высоким отпуском часто применяют для исправления структуры легированных сталей вместо отжига.
Закалка
Цель закалки – получить максимальную твердость за счет достижения максимально неравновесного состояния с высокими внутренними напряжениями.
Пересыщение приводит к искажению кристаллической решетки и большим внутренним напряжениям.
Большая скорость охлаждения приводит к образованию мартенсита бездиффузицонным способом.
-Вода при температуре, 180С - мартенсит+остаточный аустенит. Скорость охлаждения 600 0С/мин.
-10%-ный раствор NaOH в воде 180С - мартенсит. Скорость охлаждения 1200 0С/мин.
-10%-ный раствор NaCl в воде 180С – мартенсит. Скорость охлаждения 1100 0С/мин.
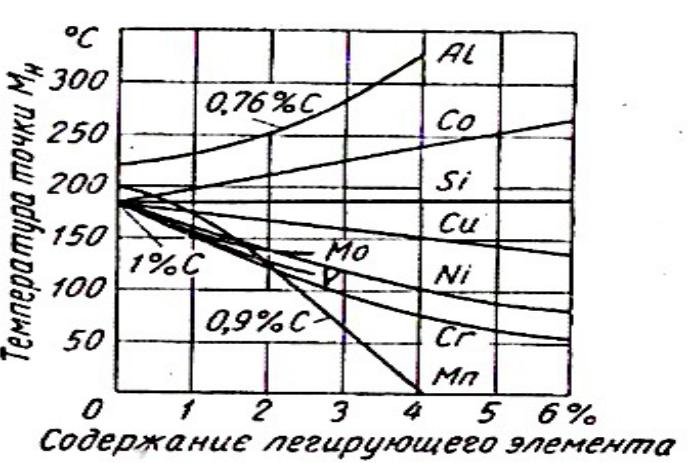
Мн – температура начала мартенситного превращения.
•Закаливаемость – способность стали принимать закалку, т.е. приобретать высокую твердость при закалке.
•Прокаливаемость – глубина проникновения закаленной зоны. Это расстояние от поверхности до слоя, где в структуре будут примерно одинаковые объемы мартенсита и троостита. Величиной, по которой
оценивается прокаливаемость, называется критическим диаметром Dкр. Критический диаметр – это диаметр цилиндра из данной стали, который в данном охладителе прокаливается насквозь.
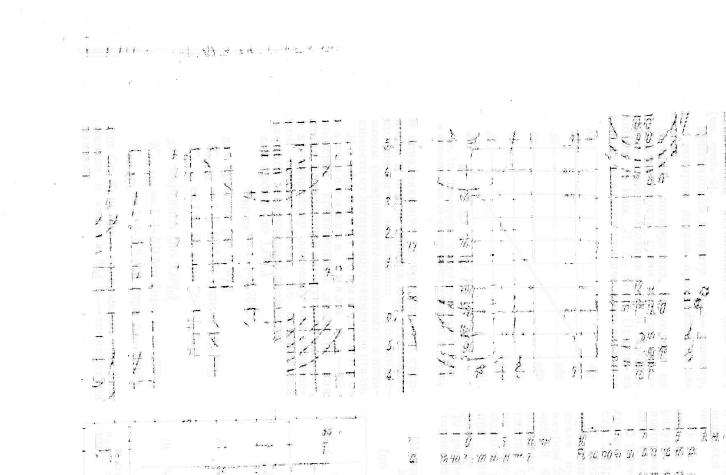
Прокаливаемость различных марок стали
Закалку в одном охладителе применяют для деталей простой формы. Нагретую до температуры закалки деталь быстро переносят в охладитель (вода, масло и т.д.). Для углеродистых сталей диаметром менее 10 мм закалочной средой служит вода, а для больших размеров – масло. Недостаток – вследствие неравномерного охлаждения возникают большие термические напряжения.
Прерывистую закалку или закалку в двух средах
используют для деталей более сложной формы и инструментов из высокоуглеродистой стали. Сначала деталь охлаждают в воде до 300 0С, затем переносят в масло. Уменьшение скорости охлаждения в области мартенситного превращения уменьшает структурные напряжения.
Закалка с самоотпуском. Охлаждение проводят в одном охладителе и прерывают, когда сердцевина изделия имеет еще значительное количество тепла (не совсем охладилась). За счет этого тепла поверхностные слои изделия вновь нагреваются и таким образом происходит отпуск. Применяется в мелкосерийном производстве для изготовления ударных инструментов (кернов, зубил и т.д.).
•Обработка холодом. Метод обработки стали, имеющей в своей структуре остаточный аустенит. Для того, чтобы избавиться от остаточного аустенита, нужно охладить деталь до нижней мартенситной точки, т.е. ниже 0 0С. Остаточный аустенит вреден тем, что со временем он может распасться на феррито-цементитную смесь, что нежелательно для калиброванных деталей. Применяется этот метод также для повышения износостойкости, твердости, стабилизации размеров (инструменты, шарикоподшипники и т.д., а также для сталей с аустенитной структурой Р18, 12Х2Н4А, ХГ, 18ХНВА и т.д.).
•Поверхностная закалка. Она является одним из способов увеличения твердости поверхностных слоев изделия. Одновременно повышаются сопротивление истиранию, предел выносливости и т.д. Общим для всех способов поверхностной закалки является нагрев поверхностного слоя детали до температуры закалки с последующим быстрым охлаждением. Быстрым нагревом поверхности создается резкий градиент температур и повышенная скорость охлаждения. Различие в методе нагрева изделий. Толщина закаленного слоя определяется глубиной нагрева. 1 способ – закалка с нагревом токами высокой частоты (ТВЧ).
2 способ – закалка с нагревом пламенем газовой горелки. Применяется главным образом для закалки изделий с большой поверхностью, при индивидуальном производстве и ремонте, иногда для закалки чугунных и стальных валков.
Струйчатая закалка заключается в обрызгивании детали интенсивной струей воды. Применяется тогда, когда нужно закалить часть детали после индукционного нагрева. Например, коренные и шатунные шейки коленвала. Закаленный слой получается до 4 мм.