
КЛ01Введение рус
..pdf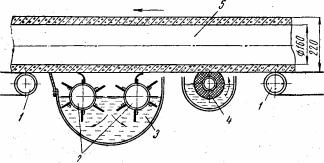
бочий.
Хорошее качество лицевой поверхности настилов может быть получено методом водной пластификации. Сущность метода состоит в том, что по поверхности смазан-
ного поддона равномерно распыляют воду, которая во время вибрирования формы проникает в бетонную смесь на 3—8 мм, придавая ей пластичность и тем самым, спо-
собствуя получению гладкой поверхности изделия.
Воду подают распылителем в количестве 0,5—0,7 л на 1 м2 поверхности поддона.
Несущая способность настилов при этом не снижается, и коррозии арматуры не про-
исходит.
Рис. 4. Конвейер для отделки поверхностей панелей:
/ — барабаны ленточных конвейеров, перемещающих настил, 2 — турбинки для нанесения и втирания шпаклевки в поры настила, 3 — ванна со шпаклевкой, 4 — ва-
лик с губкой, 6— обрабатываемая плита настила
4.4. Изготовление наружных стеновых панелей.
Наружные стеновые однослойные панели из керамзитобетона — одни из самых распространенных элементов стеновых ограждений, выпускаемых предприятиями промышленности сборного железобетона. Наряду со стендовым изготовлением, эти изделия выпускают на предприятиях с поточно-агрегатной и конвейерной технологи-
ей (рис. 5).
Процесс изготовления панелей начинается на посту 3 конвейера (первые два по-
ста предназначены для распалубки), где внутреннюю поверхность формы очищают от остатков бетона и смазывают с помощью пистолета-распылителя. В форму укладыва-
ют дверную или оконную коробку, что позволяет не устраивать опалубку проема и не заделывать в последующем щель между панелью и коробкой. При пропаривании па-
нелей оконные и дверные коробки не деформируются, происходит лишь, незначи-
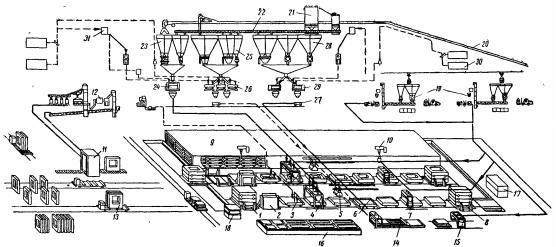
тельное (на 2—3%) повышение влажности древесины.
Одновременно с коробкой в форму устанавливают закладные части. Затем для укладки слоя фактурного бетона форму подают толкателем на следующий пост.
Слой фактурного бетона укладывают с помощью фактуроукладчика 4 с тремя ленточными питателями. Для части панелей на этом же посту в форму до укладки раствора укладывают коврики из облицовочной керамической плитки, прикрепленной клеем к бумажной основе. Когда фактуроукладчик проходит над оконной коробкой,
средний питатель автоматически выключается. Следующий пост, на который посту-
пает форма-вагонетка, предназначен для укладки арматуры.
Далее вагонетку передают на пост заполнения формы легкой бетонной смесью.
Рельсы, на которых стоит вагонетка, опускают, и электромагнит притягивает форму к виброплощадке. Подвесной бетоноукладчик 5 заполняет форму бетонной смесью, ко-
торая дозируется по весу, что позволяет более экономно расходовать материалы и вы-
держивать заданную среднюю плотность бетона панелей.
Одновременно с заполнением формы бетонную смесь вибрируют, после чего рельсы поднимают, устанавливают на них вагонетку и перемещают на следующий пост для укладки верхнего растворного (штукатурного) слоя. Раствороукладчик 7
имеет такую же конструкцию, как и фактуроукладчик; он снабжен валиком для уп-
лотнения и заглаживания поверхности штукатурного слоя. После формования форму-
вагонетку закатывают в тоннельную пропарочную камеру 9 непрерывного действия.
Рис. 5. Схема технологического процесса конвейерного производства керамзитобетонных панелей:
/—распакетировщик; 2 — кантователь; 3 — механизм закрывания бортов и
смазки форм; 4 — фактуроукладчик; 5 — бетоноукладчик; 6 — виброплощадка; 7 —
раствороукладчик; 8 — пакетировщик; 9 — тоннельная камера твердения, 10 — кран-
балка; 11 — камера обработки фактурного слоя готовых панелей; 12 — отделение под-
готовки песка; 13 — вывозная тележка; 14 — агрегатно-поточная установка для изго-
товления вентиляционных панелей; 15 — агрегатно-поточная установка для изготов-
ления карнизных блоков; 16 — ямные камеры твердения; 17 — центральный пульт управления; 18 — вспомогательный пульт управления; 19 — отделение подготовки фактуры; 20 — ленточный транспортер заполнителей, 21 — пневноосадительная уста-
новка для цемента; 22 — винтовой конвейер для цемента; 23 — бункера для компо-
нентов раствора, 24 — растворосмесители; 25 — бункера для компонентов легкого бе-
тона; 26 — смесительные роторные бегуны; 27 — самоходная раздаточная вагонетка,
28 — бункера для компонентов тяжелого бетона; 29 — бетоносмесители принуди-
тельного действия; 30 — приготовление добавок к бетону, 31 — баки для воды Чтобы рациональнее использовать камеры и упростить их конструкцию, на неко-
торых заводах рельсы прокладывают только по низу камер, а формы-вагонетки перед подачей в камеру устанавливают по высоте в виде пакета из трех или из четырех форм-вагонеток. Пакетировщик 8, оборудованный гидравлическими домкратами, ус-
танавливают на последнем посту конвейера, и он собирает формы в пакет. Пакетное расположение форм позволяет обойтись без подъемников-снижателей у торцов камер и почти вдвое уменьшить высоту камер.
Прошедшие камеру пакеты форм-вагонеток в обратной последовательности раз-
бираются аналогичным механизмом на первом посту конвейера.
На втором посту расположен кантователь 2, устанавливающий форму-вагонетку в вертикальное положение. Специальные механизмы открывают борта формы, после чего краном извлекают из формы в вертикальном положении готовую панель.
Вертикальное расположение панели при распалубке позволяет избежать напря-
жений, которые могут возникнуть при кантовании панели, что позволяет уменьшить количество арматуры в панели.
Освобожденная форма-вагонетка поступает на следующий (третий) пост, и опе-
рации повторяются, а панель передают в отделение доводки.
В закрытой камере 11, оборудованной пневмоотсосом, лицевую поверхность па-
нели обрабатывают пескоструйным: аппаратом, вскрывая фактуру декоративного бе-
тона, или смывают водой бумагу с облицованных плиткой панелей.
Далее панель транспортируют в отделение цеха, где выполняют заключительные операции: навешивают оконные переплеты и балконные двери, остекляют их, а также монтируют отопительные приборы.
После тщательного осмотра и контроля панель маркируют и вывозят на склад го-
товой продукции. На складе завода панели располагают в вертикальном положении в кассетах.
Поверхности панелей наружных стен часто отделывают, как уже упоминалось выше, керамической плиткой — крупной или мелкой, укладываемой на поддон фор-
мы. Мелкая керамическая плитка наклеена на листы бумаги, которую смывают при окончательной обработке панели.
Для отделки изделий используют также декоративный бетон или раствор, слой которого укладывают на поддон формы, либо на поверхность панели в зависимости от принятого способа формования. После отвердения бетона лицевую поверхность обра-
батывают пескоструйными аппаратами или механическими бучардами, при этом уда-
ляется цементная пленка и обнажается поверхность зерен декоративного заполнителя.
При использовании для отделки поверхности панелей цветного щебня или гравия его вдавливают в верхний слой свежеотформованной панели валками, установленны-
ми на бетоноукладчике.
Изготовление многослойных стеновых панелей со слоем утеплителя из шлакобе-
тонных плит или из ячеистого бетона, или из пенополистирола несколько сложнее. В
качестве примера рассмотрим изготовление наружной стеновой панели жилого дома с окном, состоящей из железобетонной скорлупы и слоя утеплителя — пенобетона.
На поддон очищенной и смазанной формы укладывают арматурную сетку и кар-
касы ребер и закрепляют в проектном положении закладные элементы и монтажные петли. Подготовленную форму устанавливают и закрепляют на виброплощадке. Под арматурную сетку укладывают подкладки для создания защитного слоя бетона, после чего форму заполняют бетонной смесью в количестве, необходимом для образования наружного слоя панели.
Затем в форму устанавливают вкладыш, образующий опалубку ребер панели,
включают виброплощадку и бетонную смесь уплотняют. Бетоноукладчик заполняет смесью ребра панели и вновь производится ее вибрирование. Поверхность ребер за-
глаживается.
Форму снимают краном с виброплощадки и устанавливают на пол цеха. Вкла-
дыш отрывают от бетона ручными домкратами, установленными на углах формы, по-
сле чего осторожно извлекают его из формы с помощью мостового крана и траверсы.
В отформованную железобетонную скорлупу панели устанавливают оконную коробку и нишеобразователи для создания под окном ниши батареи центрального отопления. Затем выливают в форму до верха бортов жидкую пенобетонную массу и после достаточного (примерно 4 ч) выдерживания пенобетона на его поверхность на-
носят слой штукатурки и затирают ее.
Форму с панелью переносят краном в ямную пропарочную камеру и пропарива-
ют до получения бетоном необходимой прочности.
Готовая панель поступает на пост отделки, где навешивают остекленные окон-
ные переплеты, устанавливают подоконную доску, внутренние наличники, скобяные изделия, наружный металлический слив и окрашивают наружную поверхность пане-
ли.
4.5. Изготовление ребристых и кессонных панелей и плит.
Для изготовления ребристых и кессонных плит и панелей применяют сложные металлические формы либо железобетонные матрицы. Такие изделия нередко изго-
товляют также и на виброплощадках поточно-агрегатных линий.
В этом случае панель или плиту изготовляют в форме ребрами вверх, накладывая сверху виброштамп. Кессоны и ребра панели формуют из жесткой бетонной смеси,
уплотняемой одновременно виброплощадкой снизу и штампом сверху. По окончании формования штамп осторожно поднимают, а форму с отштампованной плитой на-
правляют после некоторой выдержки в пропарочную камеру.
Для сокращения количества форм и повышения их оборачиваемости может быть применено формование таких изделий ребрами вниз. В этом случае изготовленные из жестких бетонных смесей плиты и панели немедленно распалубливают, переворачи-
вая свежеотформованные изделия на дополнительный щит-поддон в положение реб-
рами вверх.
Плиту изготовляют в открытой сверху форме, установленной на виброплощадке.
В форму укладывают арматурный каркас и загружают в процессе вибрирования бе-
тонную смесь. Поверхность изделия разравнивают и на нее укладывают щит из 50-
миллиметровых досок, прочно скрепляемых с формой хомутами.
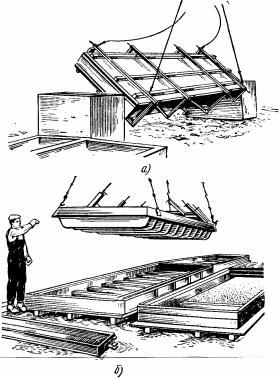
Затем краном снимают форму с виброплощадки, переворачивают ее на 180° (рис. 6, а) и опускают на пол. Сняв крепления, соединяющие щит-поддон с формой, убира-
ют форму с изделия, которое остается на поддоне вместе с бортовой оснасткой (рис. 6,
б). Бортовую оснастку снимают через 2—3 ч, а затем в комплекте с формой-матрицей используют вновь.
4.6. Изготовление изделий на стендах в неподвижных формах и мат-
рицах
Изготовление элементов сводов. В матрицах на стендах целесообразно изготов-
лять элементы сложной конфигурации, формы для которых были бы слишком тяже-
лыми и громоздкими. Этим способом изготовляют панели двоякой кривизны, предна-
значенные для сводов пролетом 18 м. Толщина панели 30— 40 мм, толщина продоль-
ных ребер 45 мм.
Панели армируют каркасом, заранее заготовленным на кондукторе. К арматуре продольных ребер приварены трубки длиной 25 мм с внутренней резьбой. Трубки предназначены для завинчивания винтов с проушинами, заменяющими монтажные петли.
Рис. 6. Изготовление реб-
ристых плит в поворотных формах:
а — поворачивание
Панели формуют в железобетонных матрицах сборно-монолитной конструкции
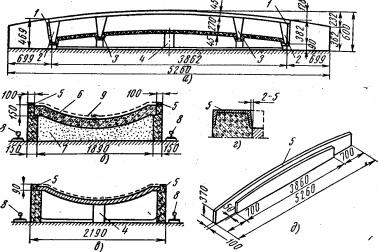
(рис. 7), состоящих из двух плоских железобетонных продольных стенок, железобе-
тонной оболочки двоякой кривизны и торцовых плоских стальных щитов. В оболочке забетонированы паровые регистры, состоящие из ряда труб диаметром 22 мм, объеди-
ненных в торцах оболочки коллекторами диаметром 54 мм.
Панели изготовляют из жесткой бетонной смеси с помощью формовочной ма-
шины (рис. 8), передвигающейся по рельсовому пути над шестью установленными в один ряд матрицами.
Машина своим ходом перемещается по рельсовому пути. В процессе движения машины над матрицами бетонная смесь из бункера-питателя / поступает на поверх-
ность матрицы 5 по всей ее ширине. Заслонка задней стенки бункера срезает излишки бетонной смеси, а расположенный за бункером виброшаблон 3 уплотняет бетонную смесь.
Рис. 7. Сборно-монолитная железобетонная матрица для сводов двоякой кри-
визны:
а — продольный разрез, б — поперечный разрез матрицы с паровыми регистра-
ми, в — поперечный разрез матрицы с внутренней полостью, г — деталь устройства скоса для облегчения съема панелей, д — железобетонные продольные стенки матри-
цы;
/ — стальные торцовые щиты, 2 — углубления для торцовых ребер основных па-
нелей, 3 — углубления для торцовых ребер доборных панелей, 4 — бетонные столби-
ки для поддержания оболочки матрицы. 5 — швеллеры, изогнутые по профилю • про-
дольных ребер панели, 6 — формуемая панель, 7 — песок, 8 — рельсовый путь для передвижения формующей машины, 9 — формуемая панель до усадки

Бункер-питатель и виброшаблон снабжены колесами, которыми они при движе-
нии машины опираются на направляющие швеллеры, матрицы 5, благодаря чему обеспечиваются заданный продольный и поперечный профиль формуемой панели и необходимая толщина ее оболочки.
Рис. 8. Формовочная машина:
а – общий вид, б — схема работы машины; / — бункер-питатель 2 — уплотнен-
ный бетон, 3 - виброшаблон, 4 - бетонная смесь, 5 – матрица. 6 — рама машины, 7 —
бетонная смесь в бункере Отформованные изделия накрывают паронепроницаемой пленкой и в регистры
пускают пар. После приобретения бетоном необходимой прочности панели снимают краном с матриц. За сутки с матрицы можно снимать две панели.
4.7. Изготовление изделий в кассетах
Кассетный способ изготовления изделий, является одним из видов механизиро-
ванного стендового производства изделий. Изделия изготовляют в кассетных формах или установках. В них детали формуются и проходят тепловую обработку на одном рабочем посту.
На кассетных установках можно изготовлять стеновые панели, панели перекры-
тий, лестничные площадки, марши и другие изделия.
Принципиальная схема кассетной установки и технологии кассетного производ-
ства плоских панелей показана на рис. 9.

Установка состоит из ряда металлических пустотных вертикальных щитов или сплошных листов — разделительных стенок кассеты, гладкие поверхности которых служат опалубкой для железобетонных панелей. В пустотелые щиты («паровые отсе-
ки» кассеты) подается пар для контактного обогрева отформованных панелей. Для распределения пара по отсекам кассеты применен коллектор с гибкими шлангами.
Одна крайняя стенка кассеты неподвижно закреплена в станине, все остальные могут перемещаться.
Работа установки происходит в такой последовательности. Очистив поверхности разделительных элементов кассеты от остатков схватившегося бетона и смазав их, ус-
танавливают арматурные каркасы и закладные детали в отсеки кассеты (поз. /—// на рис. 9). После того как все каркасы будут установлены, стенки кассеты сдвигают в проектное положение; при этом величина зазоров между ними соответствует толщине формуемых панелей. Далее заполняют кассету бетонной смесью (поз. ///) и уплотняют ее вибрацией. Затем в паровые отсеки кассеты пускают пар, при этом тепло передает-
ся через стальные стенки изготовляемым панелям.
После того как бетон отвердеет, крайняя (на рисунке правая) стенка отводится в сторону; при этом освобождается одна сторона панели (поз. IV). Затем панель подни-
мают краном (поз. V) и устанавливают в вертикальный стеллаж. Таким же путем сни-
мают и остальные панели. На поз. VI показана, последняя панель и сдвинутые в одну сторону стенки, а на поз. VII—та же панель, поднимаемая краном.
Рис. 9. Схема работы кассетной установки / и II — установка арматуры, /// — за-
полнение формы бетоном, IV—VII — отвод стенок кассет и снятие готовых изделий
Изготовление тонкостенных панелей в кассетах в вертикальном положении име-
ет ряд преимуществ по сравнению с обычным изготовлением в горизонтальных оди-
ночных формах: резко сокращается потребность в заводских площадях, получаются изделия с гладкой поверхностью, уменьшается продолжительность производственно-
го цикла, приходящаяся на одно изделие, и полностью механизируются рабочие про-
цессы.
Существует ряд конструкций кассетных установок, различающихся между собой по способу сборки кассет (вручную, с механическим и с гидравлическим приводом),
по способу уплотнения бетонной смеси (вибрирование через арматуру изделия, виб-
раторами, установленными на торцах разделительных стенок кассет), по конструкции и материалу разделительных стенок (стальные, железобетонные). В некоторых кас-
сетных установках паровые отсеки располагаются через два—четыре рабочих отсека.
Рабочие отсеки разделяются стенками из стального листа. Однако общий принцип конструкции установки во всех случаях не изменяется.
Широко распространена кассетная установка конструкции Гипростройиндуст-
рии (рис. 10). Ее основные узлы:
станина 10, разделительные стенки 6, паровые рубашки, механизмы перемеще-
ния и механизмы сжима.
Станина выполняется из двутавровых балок и несет на себе все прочие узлы ус-
тановки.
Разделительные стенки изготовляются из стального листа толщиной 24 мм и снабжаются снизу и сбоку бортами из уголков, полки которых образуют торцовые стенки формовочного отсека, и его днище.
Разделительные стенки снабжены консолями с роликами 8, на которых они пе-
ремещаются по балкам рамы. К этим же консолям прикреплены пальцы для зацепле-
ния цепи механизма перемещения стенок. Разделительные стенки перемещаются с помощью цепей, расположенных с двух сторон машины.
Паровые рубашки в виде плоских коробов из 24-миллиметрового стального лис-
та устанавливают по краям пакета и внутри панели.
В задней части установки находятся шесть винтов для окончательного сжатия кассеты и ликвидации зазоров между боковыми уголками и стальными листами раз-
делительных стенок. Винты приводятся в действие электродвигателем с редуктором.
На торцах разделительных стенок кассеты укреплены вибраторы ИВ-2 (С-414)
мощностью 0,8 кВт, частотой колебаний 2800 оборотов в минуту, а на торцах паро-
вых рубашек—вибраторы мощностью 0,4 кВт, частота колебаний 2800 об/минуту.