
КЛ01Введение рус
..pdfЛекция 2. Доставка разгрузка, хранение сырьевых материалов.
Приготовление бетонной смеси. Бетоносмесительные цехи.
Основная задача БСЦ – производство различных бетонных смесей с неизмен-
ными качественными показателями, как по составу, так и по марке бетона.
БСЦ может входить в структуру предприятия в сочетании с формовочным цехом,
арматурным цехом, а так же может работать автономно, т.е. выдавать только бетон-
ную смесь.
Для обеспечения работы БСЦ существуют следующие технологические процес-
сы:
-прием сырья (доставка, разгрузка), хранение, транспортирование, включая подогрев, рыхление заполнителей, имеющих определенную влажность (обыч-
но это операция требуется в зимний период времени т.к. влажный заполни-
тель при отрицательных температурах смерзается, что вызывает трудности при загрузке);
-прием вяжущих веществ (разгрузка, хранение и транспортирование);
-прием добавок (подготовка к рабочей консистенции);
-хранение исходных материалов в промежуточных (расходных) бункерах;
-дозирование, смешивание компонентов, вігрузка и дальнейшее транспортиро-
вание бетонной смеси.
Средства по доставке щебня, песка, цемента классифицируют по следующим критериям: назначению, виду транспорта, способу загрузки, конструктивному при-
знаку, виду транспортируемых грузов и др.
По назначению транспортные средства могут быть: общего назначения (крытые и открытые вагоны и полувагоны, автомобили, речные баржи и др.). Специализиро-
ванные (вагоны-цементовозы с аэрационно-пневматической разгрузкой, автоцементо-
возы, контейнеровозы и др.).
По виду транспорта: железнодорожные, автомобильные, водные средства и др.
По способу загрузки и выгрузки: гравитационно-пневматическая, самозагрузка,
саморазгрузка (за счет гравитации).
По конструктивным признакам предлагается следующее деление: самоходные
прицепные, специальные (например, контейнеры).
Вид материала определяет выбор транспортного средства.
К машинам с механическим перемещением (транспортированием) относятся:
конвейеры (ленточные, ковшовые – элеваторы, винтовые – шнековые, роторные и др.).
Порошкообразные предпочтительно перемещать пневмотранспортом по трубо-
проводам, с помощью аэрожелобов и др. в дальнейшем необходимо предусмотреть систему воздухоочистки (осаждение – циклон, очистка – рукавный фильтр, электро-
фильтр).
Хранение сырьевых материалов осуществляется в специальных складах: склады инертных заполнителей (щебень, гравий, песок), склады цемента и минеральных тон-
кодисперсных порошков, склады добавок.
Склады для хранения заполнителей классифицируют:
-по способам хранения – открытые, закрытые и полузакрытые;
-по типу емкостей – штабельные, бункерные, силосные, полубункерные, шта-
бельно-полубункерные и др.
Заполнители перевозимые при отрицательных температурах, смерзаются, что значительно затрудняет их выгрузку. Сыпучесть заполнителей восстанавливается различными бурорыхлительными и вибрационными машинами.
Особенности проектирования складов заполнителей исходят из норм технологи-
ческого проектирования (ОНТП 07-85).
Запас заполнителей (расчетные рабочие сутки):
железнодорожным транспортом ……………………………………………. 7-10
автомобильным транспортом ……………………………………………….. 5-7
Максимальная высота штабелей при свободном падении, м:
для щебня …………………………………………………………………….. 12
для песка ……………………………………………………………………… 15
Максимальный угол наклона ленточных конвейеров, град, ……………… 18
Число отсеков:
для песка ………………………………………………………………………. 2
для щебня ……………………………………………………………………... 4
Угол естественного откоса при отсыпке в штабель, град, ………………… 40
Максимальная температура нагрева заполнителей в зимнее время, С ….. 70
Склады для хранения цемента классифицируют:
по типам силосов – металлические, железобетонные;
по способу управления – механизированные и автоматизированные;
по способу подачи цемента в расходные бункера – с пневматической и механиче-
ской подачей;
по вместимости – на склады 240, 360, 480, 720 до 4000 т.
Особенности проектирования складов цемента следующие (из норм технологи-
ческого проектирования):
Запас цемента, расчетные сутки:
железнодорожный транспорт ……………………………………………… 7-10
автомобильный транспорт …………………………………………………. 5-7 Число емкостей (силосов) ………………………………………………….. 4-6
Углы наклона, град:
течки днищ силосов …………………………………………………… не менее 60 аэрационных желобов …………………………………………………. не менее 15
Следует учитывать специфические особенности порошкообразных материалов:
влажность, слеживаемость, абразивность.
Влажность для большинства порошкообразных материалов (в т.ч. гипсов, цемен-
тов) не должна превышать 1% по массе, кроме того, влажные вяжущие вещества преждевременно теряют химическую активность, т.е. гидратируют.
При влажности более 4% (для щебня и песка) зернистые материалы подвержены смерзанию в зимний период при отрицательных температурах.
Слеживаемость – свойство порошкообразных материалов при длительном хранении или при воздействии вибрации терять подвижность частиц. За исключением золы ТЭС,
все порошкообразные материалы слеживаются. Чтобы предотвратить слеживаемость не-
обходимо периодически осуществлять механическое или аэрационное рыхление. Напри-
мер, цемент необходимо перекачивать не реже одного раза в 15 дней.
Абразивность – свойство сыпучих материалов истирать соприкасающиеся с ними поверхности (транспортеры, питатели, шнеки, трубопроводы, и др.). Значительной ис-
тирающей способностью обладают – цемент, минеральный порошок, зола песок.
Одним из прогрессивных методов борьбы с абразивным износом является по-
крытие поверхности полимерными материалами, которые обладают малым коэф-
фициентом трения, демпфирующей способностью и высокой износостойкостью.
Приготовление бетонной смеси
В состав БСЦ (БСУ) входит следующее оборудование: смесители, дозаторы,
расходные бункера, транспортирующие устройства и системы управления.
По методам приготовления смесители классифицируют на циклические и не-
прерывного действия. В свою очередь циклические смесители подразделяют на ба-
рабанные (гравитационные), тарельчатые (принудительные с вертикальным ва-
лом), лотковые (с горизонтальным валом).
Процесс приготовления бетонной смеси следующий. Вначале дозируют щебень
и песок, затем цемент и смесь в сухом виде перемешивают еще в течение 2-3-х ми-
нут.
Готовая бетонная смесь выгружается на транспортное средство (конвейер, те-
лежка и др.) и цикл повторяется.
Особенности проектирования бетоносмесительных цехов следующие (из норм
технологического проектирования ОНТП 07-85):
Расчетное число замесов в 1 час (в зависимости от подвижности и типа смесителей) ………………………………………………………… 25 – 30
Коэффициент выхода бетонных смесей:
тяжелый бетон ……………………………………………………… 0,67 легкий бетон ………………………………………………………… 0,75
запас материалов в расходных бункерах, ч:
заполнителей (песок, щебень) ……………………………………… 1-2
цемент ………………………………………………………………… 2-3
рабочего раствора добавок ………………………………………….. 3-4 Максимально допустимая высота свободного падения бетонной смеси, м …………………………………………………… 2
Наибольше допустимая температура бетонной смеси, С ..………. 35
По принципу действия бетоносмесительные цехи разделяют на предприятия цикли-
ческого и непрерывного действия, по компоновке оборудования – на партерные – двух-
ступенчатые и высотные. По схеме расположения смесительных машин в плане – на ли-
нейные (однорядные и двухрядные) и гнездовые. По способу управления производствен-
ными процессами – на механизированные, автоматизированные и заводы-автоматы.
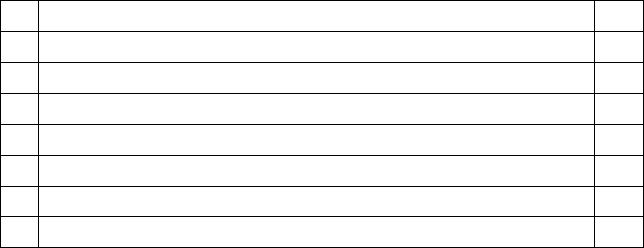
План лекции
Содержание раздела
ОБЩИЕ ПОНЯТИЯ
КЛАССИФИКАЦИЯ
ОБЩИЕ ТРЕБОВАНИЯ К ФОРМАМ
ТЕХНОЛОГИЯ ИЗГОТОВЛЕНИЯ ФОРМ
ПРИНЦИПЫРАСЧЕТА
ПРИМЕНЯЕМОЕ ОБОРУДОВАНИЕ, БОРТОСТНАСТКА
ЛИТЕРАТУРА
ОБЩИЕ ПОНЯТИЯ
Форма – многозначительное понятие, означающее в данном случае конструк-
цию, с помощью которой можно придать определенные размеры, углы между плоско-
стями и кривизну поверхности железобетонным и бетонным изделиям.
Формоостнастка – конструктивные элементы, крепящиеся на формах для полу-
чения определенного эффекта. Например, упоры для напрягаемой арматуры, ограни-
чители угла поворота бортов, фиксаторы положения несущей арматуры или заклад-
ных деталей.
Опалубка – конструкция, с помощью которой придают определенные размеры,
углы между плоскостями и кривизну поверхности железобетонным и бетонным кон-
струкциям, изготавливаемыми монолитным способом различают разборно-
переставную, скользящую, подъемно-переставную, несъемную и др.
Процесс формования – технологический передел, важнейшая и неотъемлемая стадия процесса изготовления железобетонных и бетонных изделий, получения изде-
лия, укладкой и уплотнением бетонной смеси в форме и отделкой лицевой поверхно-
сти.
КЛАССИФИКАЦИЯ ФОРМ
Формы классифицируют по различным признакам.
В зависимости от условий работы формы подразделяют на передвижные и не-
подвижные. Передвижные используют при агрегатно-поточном и конвейерном спосо-
бе производства. Основной принцип этих способов производства изделия передвига-
ются, а оборудование и оснастка остаются на месте (посту). Неподвижные использу-
ются при стендовом и кассетном способах производства. Принцип – изделия непод-
вижны, а оборудование и оснастка и обслуживающий персонал перемещаются от формы к форме (кассете).
По числу изделий, одновременно изготавливаемых в формах, различают оди-
ночные и групповые формы (кассеты).
По положению изделий при формовании различают формы горизонтальные и вертикальные. Изделия могут формовать «лицом вниз» и «лицом вверх».
По нагрузке на форму, различают силовые и несиловые формы. Силовые вос-
принимают нагрузку от натяжения арматуры.
По виду определенных поверхностей, формы называют с плоским или про-
фильным (криволинейным) днищем, с проемами или пустотами.
По виду материала различают формы металлические, деревянные, пластмас-
совые, железобетонные и комбинированные.
По конструктивным особенностям формы бывают разъемные, неразъемные.
С открывающимися бортами или стенками. Имеющими только, бортовую оснастку и использующие плоское днище камеры твердения или пол цеха.
Формы, в зависимости от отношения расстояния между опорами к ширине,
бывают узкие (а/b >2) и широкие (а/b <2)
ОБЩИЕ ТРЕБОВАНИЯ К ФОРМАМ
Деревянные формы могут выдержать не более 20-30 формовок. Качество по-
верхности бетона низкое, требуется покрывать поверхность олифой или лаком. Наи-
больший эффект деревянные формы приносят при изготовлении железобетонных изделий очень сложной конфигурации, малых партий до 10 шт и в регионах богатых лесом.
Железобетонные формы практически не транспортабельны, наибольший эф-
фект приносят при стендовом производстве при ограниченном выпуске железобетон-
ных изделий.
Наибольшее распространение получили металлические формы, т.к. они гораздо долговечнее. Оборот форм достигает 1000 оборотов.
Для обеспечения проектного срока службы форм необходим своевременный уход и тщательная чистка и смазка формы, а также легкая расформовка изделий.
Формы требуется изготавливать с точностью на 1-2 порядка выше, чем железобе-
тонные изделия. Допуски на изготовление формы в целом и составных деталей назна-
чаются с минусовыми значениями, так как в процессе эксплуатации крепления форм слабеют и размеры увеличиваются.
Устанавливают допуски на криволинейность и чистоту поверхностей соприка-
сающихся с поверхностью железобетонных изделий.
Следует избегать острых углов и сопряжений. Днище форм должно иметь пло-
скую поверхность для придания устойчивости.
Металлоемкость форм составляет на заводах ЖБИ до 50% общей металлоемко-
сти всего технологического оборудования. Расход металла на 1 м3 бетона доходит до 4
тонн в силовых формах. Наиболее перспективны следующие направления экономии металла при создании форм.
С немедленной распалубкой.
Многоместные формы.
Без днища.
ТЕХНОЛОГИЯ ИЗГОТОВЛЕНИЯ ФОРМ
Под изготовлением металлических форм для формования железобетонных изделий подразумевают: правку стали; разметку металла; гибку профилей, фрезерование, свар-
ку и зачистку поверхностей.
Сборку отдельных узлов, элементов и форм в целом производят на выверенных стендах с использованием кондукторов и приспособлений, обеспечивающих жест-
кость и точность соединений.
Зачистка после сборки и сварки является наиболее трудоемкой и ответственной операцией. Зачистку швов производят шлифовальными кругами с помощью перенос-
ных пневмомашинок.
Правку по необходимости выполняют с помощью винтовых и гидравлических дом-
кратов. Контроль качества изготовления полуфабрикатов и деталей осуществляется поопе-
рационноспомощьюшаблоновищупов.
Готовыеформыпринимают ОТКпоштучно.Приэтомпроверяют:
-габаритныеразмеры;
-диагоналивсехпрямоугольников;
-плоскостностьподдонов;
-перпендикулярностьбортоввовсехнаправлениях;
-криволинейностьповерхностейприихналичии.
Наформувыдаетсяпаспорт,вкоторомуказываются:
-номери датасоставленияпаспорта;
-наименованиеиадресзаводаизготовителя;
-наименованиеимаркаизделия,длякоторогопредназначенаформа;
-маркаформы;
-номерТУилиДСТУнаизготовлениеформ.
ПРИНЦИПЫРАСЧЕТА
Форму рассчитывают как стальную конструкцию, с учетом особенностей нагрузок, их динамики, условий формования, твердения, транспортирования и т.д. По рабочим постам она переносится краном или конвейером. Она многократно загружается полной расчетной нагрузкой и подвергается динамическому воздействию при виброуплотнении. Форма многократно прогревается в среде насыщенного пара при условии отсутствия защиты от коррозии, что вызывает температурные деформации.
Расчет формы ведется по допустимым деформациям (второе предельное состояние) с проверкой принятой конструкции на устойчивость (первое предельное состояние). Проверка на прочность металлических форм проводится только при эксцентриситете m1>20.
Сечение формы подбирают по допускаемому прогибу и потерям напряжения в арматуре изделия, возникающих при деформациях формы при передаче на ее упоры усилия натяжения арматуры. Потери напряжения в арматуре изделия не должны превышать 50,0 МПа.
Борта формы рассчитывают на горизонтальное давление, которое создается свежеуложенной смесью и нагрузкой от пригрузочного щита, штампа или другого формующего оборудования.
Расчет наружной обшивки борта, образующей паровую полость, ведется на избыточное давление.
Узкие формы рассчитываются как балки. Поддон в широкой форме рассчитывается по приведенным моментам инерции сечений, перпендикулярных и параллельных продольной оси.
ПРИМЕНЯЕМОЕ ОБОРУДОВАНИЕ, БОРТОСТНАСТКА
Бортовые элементы откидных бортов крепятся шарнирами или замками. Шар-
ниры бывают трубчатые или пластинчатые. Замки бывают натяжного, клинового или
накидного типа. Трубчатые легче забиваются цементным молоком, но они крепче.
пластинчатые проще в изготовлении, но они легко изгибаются и ломаются. Замки на-
тяжного типа обеспечивают наиболее плотное соединение бортов, они не раскрыва-
ются и не ослабляют соединение под воздействием вибрации.