
Metodichka_po_stroymatu
.pdfМІНІСТЕРСТВО ОСВІТИ І НАУКИ УКРАЇНИ ДОНБАСЬКА ДЕРЖАВНА АКАДЕМІЯ БУДІВНИЦТВА І АРХІТЕКТУРИ
КАФЕДРА ТЕХНОЛОГІЙ БУДІВЕЛЬНИХ МАТЕРІАЛІВ, ВИРОБІВ ТА АВТОМОБІЛЬНИХ ДОРІГ
МЕТОДИЧНІ ВКАЗІВКИ
до лабораторних випробувань будівельних матеріалів
(для студентів всіх будівельних спеціальностей денної форми навчання)
ЗАТВЕРДЖЕНО на засіданні кафедри технологій будівельних
матеріалів, виробів та автомобільних доріг Протокол № 6 від 23 грудня 2003 р
.
.
Макіївка ДонДАБА – 2004 р.
УДК 691 (071)
Методичні вказівки до лабораторних випробувань будівельних матеріалів (для студентів всіх будівельних спеціальностей денної форми навчання)/ Укл. В.І. Братчун, О.М. Єфремов, В.Г. Вишневська, М.В. Деркач. – Макіївка: ДонДАБА, 2004. – 28 с.
Викладена методика визначення основних фізико-механічних властивостей будівельних матеріалів: цегли керамічної і керамічних плиток для підлог, скла і виробів зі скла, мінеральних гіпсових в’яжучих, повітряного будівельного вапна, портландцементу.
Укладачі: |
В.І. Братчун, д.т.н., професор |
|
О.М. Єфремов, к.т.н., доцент |
|
В.Г. Вешневська, к.т.н., доцент |
|
М.В. Деркач, к.т.н., доцент |
Рецензент |
Беспалов В.Л., к.т.н., доцент |
Відповідальний |
|
за випуск |
Базжин Л.І., ., к.т.н., доцент |
2

1. ФІЗИЧНІ ВЛАСТИВОСТІ БУДІВЕЛЬНИХ МАТЕРІАЛІВ
Властивості матеріалу - це показники, за допомогою яких можна оцінити взаємодію матеріалу з навколишнім середовищем. Властивості матеріалів поділяють на фізичні, механічні, хімічні, технологічні, експлуатаційні та спеціальні.
Фізичні властивості характеризують фізичний стан матеріалу (фазовий стан, густину, структуру), а також визначають його відношення до фізичних процесів навколишнього середовища. До таких властивостей відносять істину і середню густину, пористість, теплопровідність, теплоємність, звукопроникність, вологість, водопроникність, водопоглинання, усадку, вогнестійкість, світлостійкість та ін.
1.1. Істина густина
Це маса одиниці об'єму матеріалу в абсолютно щільному стані, тобто без пор і пустот. Обладнання і матеріали. Пікнометр або об’ємомір, терези технічні з гирками, сушильна шафа, ступка фарфорова або агатова з пестиком, сито з сіткою №0,125 і №0,063, чашка для зважування, ложка, вода дистильована або інша рідина, що інертна стосовно випро-
бовуваного матеріалу, фільтрувальний папір, випробуваний матеріал.
Випробування. Істину густину визначають за допомогою пікнометру Ле-Шательє (рис. 1.1). Наважку випробуваного матеріалу до 200 г подрібнюють до розміру часток близько 5 мм, потім подрібнюють у фарфоровій або агатовій ступці до повного проходження через сито №015. Підготовлений таким чином порошок висушують до сталої маси при 105-110°С і охолоджують до кімнатної температури в ексикаторі над концентрованою сірчаною кислотою або безводним хлористим кальцієм.
|
|
|
Пікнометр Ле-Шательє заповнюють рідиною до нижньої нульової |
|
|
|
|
відмітки. З висушеної проби матеріалу відбирають наважку 75 г з точні- |
|
|
|
|
стю до 0,1 г і засипають невеликими порціями до пікнометру Ле- |
|
|
|
|
Шательє, доки рівень рідини не досягне одного з поділів у межах верх- |
|
|
|
|
ньої градуйованої частини (наприклад 20 см3). Залишок порошку зважу- |
|
|
|
|
ють разом із чашкою. Щоб видалити пухирці повітря, яке потрапило в |
|
|
|
|
рідину разом із порошком, прилад повертають і тримають у похиленому |
|
|
|
|
положенні протягом 10 хвилин на гладкому гумовому килимі. Після цьо- |
|
|
|
|
го визначають рівень рідини у приладі. |
|
Рис. 1.1. Пікнометр |
Маса порошку, засипаного до приладу, визначається як різниця між |
|||
Ле-Шательє |
масою початкової проби і масою залишку. |
|||
|
|
|
Істину густину ρ, кг/м3 (г/см3), обчислюють за формулою (1.1.): |
|
|
|
|
ρ = m1 |
(1.1) |
|
|
|
Va |
, |
де m1 - маса порошку, засипаного до приладу, кг (г);
Vа – об’єм рідини, що витіснив засипаний порошок, м3 (см3). Результати випробування заносять до табл. 1.1.
Істину густину матеріалу обчислюють як середнє арифметичне трьох результатів випробування. Розбіжність у результатах не повинна перевищувати 20 кг/м3 (0,02 г/см3). При великих розбіжностях істину густину зразків визначають повторно.
Таблиця 1.1 Результати визначень дійсної густини матеріалу за допомогою пікнометру Ле-Шательє
№ |
Маса порош- |
Маса |
порошку в |
Маса |
засипано- |
Об’єм, зайнятий |
Дійсна густина, кг/м3 |
|||
чашці |
після заси- |
|
|
|
|
|||||
ку в чашці, |
го |
порошку, |
|
|
|
|
||||
п/п |
пання до пікномет- |
порошком, V1, см3 |
ρі |
|
|
|
||||
|
ρ |
|||||||||
|
m, г |
ру Ле-Шательє, m2, г |
m1=m-m2, г |
|
|
|
|
|
||
1 |
|
|
|
|
|
|
|
|
|
|
2 |
|
|
|
|
|
|
|
|
|
|
3 |
|
|
|
|
|
|
|
|
|
|
3
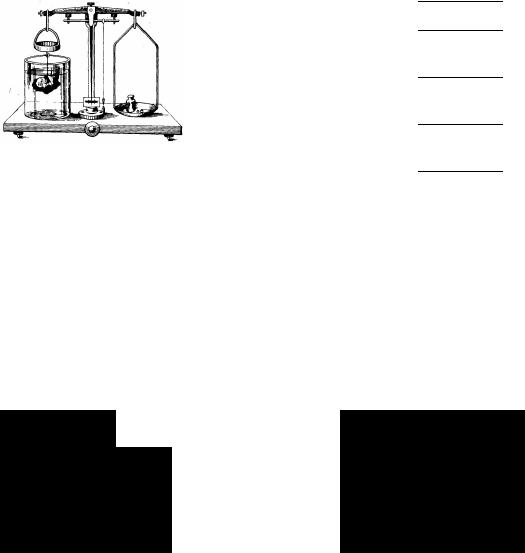
Висновок робиться на підставі порівняння отриманих результатів із табличними (або нормативними) даними для випробовуваного матеріалу.
1.2. Середня густина
Це маса одиниці об'єму матеріалу в природному стані, тобтоізпорамиіпустотами. Метод визначеннясередньоїгустинизалежитьвідформизразкаматеріалу.
1.2.1. Визначення середньої густини матеріалу на зразках правильної геометричної форми
Обладнання і матеріали. Штангенциркуль, терези технічні, шафа сушильна, зразки випробуваного матеріалу у вигляді куба, паралелепіпеда, циліндра.
Середню густину зразка правильної геометричної форми визначають із точністю до 10 кг/м3 за формулою (1.2.):
|
|
|
|
|
ρ0 = m , |
|
|
(1.2.) |
|
|
||
|
|
|
|
|
v |
|
|
|
|
|
|
|
де m - маса сухого зразка, г; v – об’єм зразка, см3. |
|
|
|
|
|
|
||||||
Результати випробувань заносять до табл. 1.2. |
|
|
|
Таблиця 1.2 |
||||||||
|
|
|
|
|
|
|
|
|
|
|||
Результати визначень середньої густини зразків правильної геометричної форми. |
||||||||||||
Форма |
№ |
Розміри, см |
Об’єм зразка, |
|
Маса зраз- |
Середня |
густина, кг/м3 |
|||||
зразка |
зразка |
а (r) |
b |
h |
V, см3 |
|
ка, m, г |
ρ0.i |
|
|
ρ |
0 |
Куб |
1 |
|
|
|
|
|
|
|
|
|
|
|
2 |
|
|
|
|
|
|
|
|
|
|
|
|
|
3 |
|
|
|
|
|
|
|
|
|
|
|
Паралеле- |
1 |
|
|
|
|
|
|
|
|
|
|
|
2 |
|
|
|
|
|
|
|
|
|
|
|
|
піпед |
|
|
|
|
|
|
|
|
|
|
|
|
3 |
|
|
|
|
|
|
|
|
|
|
|
|
|
|
|
|
|
|
|
|
|
|
|
|
|
Циліндр |
1 |
|
|
|
|
|
|
|
|
|
|
|
2 |
|
|
|
|
|
|
|
|
|
|
|
|
|
3 |
|
|
|
|
|
|
|
|
|
|
|
1.2.2. Визначення середньої густини зразків неправильної геометричної форми
Обладнання і матеріали. Терези технічні з гирками і пристроєм для гідростатичного зважування, шафа сушильна, склянка місткістю 1000 см3, ексикатор, баня парафінова, нитка шовкова, зразки випробуваного матеріалу.
Випробування. При відсутності зразків правильної форми відколюють шматок породи (матеріалу) масою 100-200 г, очищають його від пилу і висушують при 105-110°С у сушильній шафі.
Далі зразки охолоджують до кімнатної температури, зважують і кожний зразок опускають у розплавлений (t=80±5°C) парафін, а потім швидко виймають, видаляючи пузирчики повітря, що утворюються на парафіновій плівці, або тріщини гарячою голкою
Підв'язують кожний зразок тонкою ниткою і підвішують по черзі до гака гідростатичних терезів (рис. 1.3).
До насосу
Рис. 1.2. Видалення повітря вакуумуванням |
Рис. 1.3. Гідростатичні терези |
4

Зважують зразки на повітрі і у воді. Середню густину таких зразків обчислюють за формулою:
ρ0 |
= |
|
|
m |
, |
(1.3) |
|
m1 |
−m2 |
− m1 −m |
|||||
|
|
|
|
||||
|
|
|
ρ |
ρпар |
|
|
де m - маса сухого зразка, г; m1 - маса зразка, покритого парафіном, на повітрі, г; m2 - маса зразка, покритого парафіном, у воді, г; ρnap - густина парафіну, г/см3, ρв - густина води, г/см3.
Результати заносять до табл. 1.3.
|
|
|
|
|
|
|
Таблиця 1.3 |
||
|
Результати визначення середньої густини зразків неправильної геометричної форми |
||||||||
№ |
|
Маса су- |
Маса парафіно- |
Маса парафіно- |
Густина |
Середня густина, кг/м3 |
|||
|
|
||||||||
|
хого зраз- |
ваного зразка, |
ваного зразка, |
парафіну, |
|
|
|
|
|
ρ0і |
|
ρ0 |
|||||||
п.п. |
|
ка, m, г |
зваженого на по- |
зваженого у воді, |
3 |
|
|||
|
|
вітрі, m1, г |
m2, г |
ρn, г/см |
|
|
|
|
|
1 |
|
|
|
|
|
|
|
|
|
2 |
|
|
|
|
|
|
|
|
|
3 |
|
|
|
|
|
|
|
|
|
Для щільних і рівномірно тонкопористих порід орієнтовно визначають середню густину, попередньо насичуючи зразок водою (без парафінування). Водонасичений зразок опускають у мірний циліндр (500 см3) діаметром 7 см, попередньо заповнюючи водою на 1/3. Виміряний за поділками шкали новий об’єм води дорівнює об’єму зразка.
Для цього може бути використаний також об’ємомір (рис. 1.2).
1.3. Пористість матеріалу визначають на підставі встановлених значень дійсної і середньої густини.
Пористість (П) – доля об’єму пор і мікрощілин в матеріалі (%), яку обчислюють за формулою:
|
|
ρ |
0 |
|
|
%, |
(1.4) |
П = 1 |
− |
|
|
100 |
|||
ρ |
|
||||||
|
|
|
|
|
|
|
де ρ0- середня густина, г/см3; ρ- дійсна густина, г/см3.
1.4. Водопоглинання
Це здатність матеріалу поглинати воду при тривалому витримуванні у воді при нормальному атмосферному тиску і температурі 18-20°С.
Обладнання і матеріали. Шафа сушильна; терези технічні; посудина з водою, що обладнана решіткою для забезпечення вільної циркуляції води між зразками і її дном; нагрівальні прилади; зразки матеріалу; форми і розміри якого мають відповідати вимогам Держстандарту.
Випробування. Готують зразки матеріалу кубовидної форми з довжиною ребра близько 6 см (для гірських порід) або штучні вироби (цегла, плитки та ін.).
Підготовлені зразки висушують до постійної маси при 105-110°С, охолоджують до кімнатної температури, очищають поверхню від пилуватих часток і зважують.
Маркіровані зразки занурюють у посудину з водою кімнатної температури так, щоб рівень води в ній був вище верху зразків не менш як на 20 мм, і витримують у воді 48 годин.
По черзі виймають кожний зразок, витирають м'якою, вологою тканиною і зважують. При цьому маса води, що витікає з пор зразків, покладених на шальку терезів повинна включатися до маси зразків.
Водопоглинання в процентах (за масою або за об’ємом) обчислюють за формулами 1.6; 1.7 відповідно:
5
|
|
|
W = |
m1 −m |
100% або W = |
m1 −m |
|
100% , |
(1.5 ), (1.6) |
||||
|
|
|
|
|
|
||||||||
|
|
|
m |
m |
|
v |
V ρводи |
|
|
|
|
|
|
|
|
|
|
|
|
|
|
|
|
|
|
||
де m - маса сухого зразка, г; m1 |
- маса зразка, насиченого водою, г; V – об’єм зразка, см3, |
||||||||||||
ρводи – густина води, г/см3. |
|
|
|
|
|
|
|
|
|
||||
|
Результати випробування заносять до табл. 1.4. |
|
|
|
|
Таблиця 1.4 |
|||||||
|
|
|
Результати визначення водопоглинення |
|
|||||||||
|
|
|
|
|
|
||||||||
№ |
|
Маса сухого |
|
|
Маса водонасиченого |
|
|
Водопоглинання, % |
|||||
п.п. |
|
зразка, m, г |
|
|
|
зразка, m1, г |
|
Wmi |
|
|
m |
||
|
|
|
|
W |
|||||||||
1 |
|
|
|
|
|
|
|
|
|
|
|
|
|
2 |
|
|
|
|
|
|
|
|
|
|
|
|
|
3 |
|
|
|
|
|
|
|
|
|
|
|
|
|
Висновок дається на підставі порівняння отриманих результатів з вимогами стандартів для випробуваного матеріалу.
2. МЕХАНІЧНІ ВЛАСТИВОСТІ БУДІВЕЛЬНИХ МАТЕРІАЛІВ
Механічні властивості - здатність матеріалу опиратися деформуванню і руйнуванню під дією напружень, що виникають у результаті прикладання зовнішніх сил. До них відносяться: міцність (при стиску, при вигині, при розтягу, опір удару), пружність, в’язкість, пластичність, крихкість, стираність, релаксація, повзучість, твердість матеріалів тощо.
Механічні властивості визначають на зразках, кубовидної, циліндричної форми або іншої форми.
2.1. Міцність при стиску
Обладнання і матеріали. Прес з тарувальною таблицею до нього, лінійки масштабні, совок і щітка для видалення уламків зразка після випробування, ніж і штукатурна лопатка для вирівнювання гіпсового тіста, гіпсове в'яжуче, випробовувані зразки правильної геометричної форми (куб, циліндр, паралелепіпед).
Випробування. Підготовлені зразки в кількості 3-5 шт. маркірують, висушують і встановлюють по черзі на нижню плиту гідравлічного преса точно посередині плити, користуючись при цьому квадратними розмітками на поверхні плити. Плита повинна бути попередньо старанно очищена (рис. 2.1). Притискають зразок верхньою плитою. Установлюють вимірювач тиску на нульову позначку і вмикають електромотор насосу. Масло подають з таким розрахунком, щоб тиск підвищувався в межах 1,2-1,5 МПа за секунду. Записують показання манометра при появі першої тріщини, а потім зусилля, при якому зразок зруйнувався. Міцність при стиску визначають за формулою (2.1.):
|
|
|
|
R ст = |
F |
, |
|
|
|
|
(2.1.) |
||
|
|
|
|
S |
|
|
|
||||||
|
|
|
|
|
|
|
|
|
|
|
|
|
|
|
де - F - руйнівна сила, Н (кгс); S - площа зразка, м2 (см2). |
|
|
|
|
|
|||||||
|
Результати визначень записують до табл. 2.1. |
|
|
|
Таблиця 2.1 |
||||||||
|
|
|
|
Результати визначення міцності при стиску |
|
|
|||||||
|
|
|
|
|
|
|
|
||||||
№ |
Розміри зраз- |
Площа робочого |
|
Руйнівна сила, |
|
Міцність при стиску |
|||||||
п.п. |
|
ка, см |
перерізу, S, см2 |
|
F, кгс |
|
|
|
|
|
|
||
а |
|
b |
|
|
Rсті, кгс/см |
2 |
|
Rст , МПа |
|||||
|
|
|
|
|
|
|
|
|
|||||
1 |
|
|
|
|
|
|
|
|
|
|
|
|
|
2 |
|
|
|
|
|
|
|
|
|
|
|
|
|
3 |
|
|
|
|
|
|
|
|
|
|
|
|
|
6
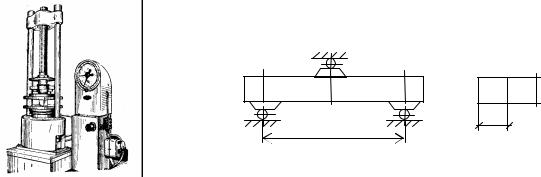
2.2. Міцність при вигині
Обладнання і матеріали. Те саме, що і в п. 2.1., окрім зразків у формі прямокутних призм-балочок, пластинок або смуг; пристосування (опори) для випробування на вигин.
Випробування. Виготовлені зразки оглядають, дефектні заміняють. При наявності допустимих тріщин зразки перед випробуванням орієнтують так, щоб тріщини розташовувалися в розтягнутій зоні (унизу). Верхня і нижня грані зразків повинні бути плоскими і паралельними, для чого їх відшліфовують, або на грані наносять смужки, як, наприклад, при випробуванні цегли.
Далі на зразках роблять розмітку в такій послідовності. На боковій поверхні зразка посередині довжини проводять вертикальну лінію, перпендикулярну довжині зразка. Ця лінія визначає положення робочого перетину. Від неї на відстані, рівній половині розрахункового прольоту, вліво і вправо проводять дві інші лінії, паралельні перший. Величина розрахункового прогону визначається стандартами на випробовуваний матеріал. Схема розмітки і випробування зразка на вигин наведена на рис.2.2.
F
h
b
L
Рис. 2.1. Гідравлічний прес |
Рис. 2.2. Схема випробування зразка на вигин |
На нижню плиту преса встановлюють і центрують пристрій для випробування на вигин, на його опори вкладають зразок, зверху - верхній “ніж”. Опускають верхню плиту преса таким чином, щоб між верхнім “ножем” і плитою був зазор. Далі ведуть випробування, як в п. 2.1.
Границю міцності при вигині для прямокутного зразка визначають за формулою (2.2.):
|
R |
в |
= 3FL , |
(2.2) |
|
|
2bh2 |
|
|
де |
F - руйнівна сила, Н (кгс); L - відстань між опорами, м (см); |
|
||
b - ширина перерізу, м (см); h - висота перерізу, м (см). |
|
Границю міцності при вигині серії зразків приймають як середнє арифметичне значення результатів усіх випробувань. Зразки-балочки розміром 4х4х16 см можна випробувати на машині МВВ-100.
Результати випробувань заносять до табл. 2.2.
|
|
|
|
Результати визначення границі міцності при вигині |
|
Таблиця 2.2 |
|||
|
|
|
|
|
|
||||
№ |
|
Розміри, см |
Руйнівна сила, |
Міцність при вигині |
|||||
п.п. |
b |
|
h |
L |
F, кгс |
Rві, кгс/см2 |
|
|
в, МПа |
R |
|||||||||
1 |
|
|
|
|
|
|
|
|
|
2 |
|
|
|
|
|
|
|
|
|
3 |
|
|
|
|
|
|
|
|
|
|
2.3. Міцність при розтягу |
|
|
|
|
Обладнання і матеріали. Розривна машина, масштабні лінійки, штангенциркуль, випробовувані зразки у формі смуг – “вісімок” або стержнів.
7
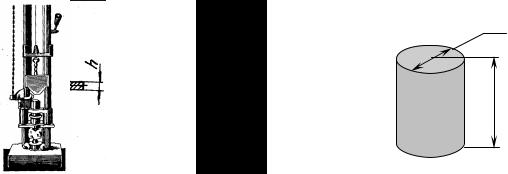
Випробування. Зразки для випробування оглядають, вибраковують дефектні, заміряють й обчислюють площу робочого перерізу. Кінці зразка закріплюють у затискачах розривної машини (рис. 2.3), вмикають двигун, надаючи потрібну за нормами швидкість розходження затискачів. Після руйнування зразка визначають за показниками силовимірника руйнівне (розривне) зусилля і обчислюють границю міцності при розтягу Rр із точністю до 0,1 МПа за формулою (2.3.):
|
|
|
R p = |
F |
, |
|
|
(2.3.) |
||
|
|
|
|
|
|
|||||
|
|
|
|
|
S |
|
|
|
|
|
|
де F - руйнівна сила, Н (кгс); S - площа робочого перерізу, м2(см2). |
|
|
|||||||
|
Границю міцності при розтягу партії зразків обчислюють як середнє арифметичне зна- |
|||||||||
чення результатів усіх випробувань. |
|
|
|
|
|
Таблиця 2.3. |
||||
|
|
|
Результати визначення границі міцності при розтягу |
|||||||
|
|
|
|
|
||||||
№ |
Розміри, см |
Площа робочого |
Розривна |
Міцності при розтягу |
||||||
п.п. |
h |
b |
перерізу, S, см2 |
сила, F, кгс |
Rрі, кгс/см2 |
|
|
р, МПа |
||
R |
||||||||||
1 |
|
|
|
|
|
|
|
|
|
|
2 |
|
|
|
|
|
|
|
|
|
|
3 |
|
|
|
|
|
|
|
|
|
|
2.4. Опір ударові - властивість матеріалу чинити опір динамічним (ударним) навантаженням без помітних пластичних деформацій; залежить від мінералогічного складу, структури, текстури і вологості.
За показником міцності при ударі матеріали поділяють на такі групи: дуже крихкі - 2; крихкі - 2-5; в’язкі - 5-10; дуже в’язкі - понад 10 ударів.
Обладнання і матеріали. Копер лабораторний для випробування циліндричних зразків, масштабні лінійки, штангенциркуль, випробовувані зразки у формі циліндра діаметром і висотою 25 мм у кількості не менш трьох.
F d
h
Рис. 2.3. Схема випробування |
Рис. 2.4. Копер |
Рис. 2.5. Схема випробування |
зразка на розтяг |
|
зразка на удар |
Випробування. Зразки нумерують і вимірюють, дані заносять до лабораторного журна-
лу.
Випробування на удар полягає в тому, що на встановлений зразок (циліндр, куб) наносять удари гирею заданої маси зі все зростаючої висоти (в см) або гирями різної маси до руйнування зразка.
Зразок випробують на копрі (рис. 2.4, 2.5.), який складається з металевої станини, що переходить донизу в сталеве ковадло. Зразок встановлюють на ковадло копра (рис. 2.4.) і наносять удар по зразку за допомогою баби (гирі), яку скидають з висоти 1 см. Для випробувань готують зразки діаметром 2 і висотою 2,5 см. Установлюють зразок на ковадло копра і притискують його підбабком точно по центру. Наносять удар гирею, що падає з висоти 1 см, потім - 2 см і так далі, збільшуючи висоту падіння гирі кожного разу на 1 см. Записують порядковий удар гирі, при якому зруйнувався зразок.
8
Показник опору ударові – є порядковий номер удару по зразку, який передує появі на ньому першої тріщини. Опір ударові необхідно визначити на трьох паралельних зразках (для одного матеріалу), а потім обчислюють середнє арифметичне значення, яке округлюють до цілого числа в менший бік.
2.5. Стираність. Стираність – це властивість матеріалу зменшувати масу і об’єм під дією стираючих зусиль, яка залежить від твердості і щільності матеріалу.
Обладнання і матеріали. Прилад ЛКС-3 (коло стирання), терези технічні, пісок кварцовий фракцій 0,50 - 0,25 мм (50%) і 0,25 - 0,16 мм (50%), зразки плиток розмірами 50х50 або
70х70 мм.
Випробування. Зразки плиток висушують і зважують з точністю до 0,1 г, вимірюють їх довжину і ширину з точністю до 0,1 мм. Зразки вкладають лицьовою поверхнею на диск і притискують вантажем із розрахунку 0,06 МПа (0,6 кгс/см2). На шліфувальну доріжку насипають рівномірно шар абразивного (кварцового піску) матеріалу в кількості 0,4 г на 1 см2 поверхні зразку і на 1 хвилину включають шліфувальний диск. Після 30 обертів машину відключають, зразок виймають, очищають від пилу і зважують із точністю до 0,1 г. Шліфувальний диск обчищають від спрацьованого матеріалу. Потім зразок повертають на 90° і знову шліфують з новою порцією абразивного матеріалу. Цей процес повторюють 4 рази, обертаючи зразок на 90°.
Якщо розбіжності між найменшою і найбільшою втратами маси після окремих циклів менше 3% загальної втрати маси після чотирьох циклів, то випробування вважається завершеним. Якщо ця розбіжність більше 3%, то випробування продовжують за тією ж методикою, проводячи 12 циклів шліфування.
Стираність (г/см2) обчислюють за формулою (2.4.):
Ст = |
m1 −m2 |
, |
(2.4.) |
|
S |
||||
|
|
|
де m1 - маса зразка до стирання, г; m2 - маса зразка після стирання, г; S - площа стирання, см2. Результати випробувань заносять до табл. 2.4.
|
|
|
Результати визначення стираності зразків |
|
Таблиця 2.4 |
|||||
|
|
|
|
|
|
|
||||
|
|
|
|
|
|
|
|
|
|
|
№ |
Маса |
зразка |
Маса зразка |
Розміри |
Площа грані |
Стираність |
||||
до |
випробу- |
після випро- |
зразка, см |
стирання, |
||||||
п.п. |
вання, m1, г |
бування, m1, г |
|
|
S=а·b,см2 |
|
|
|
|
|
а |
b |
Ст, г/см2 |
|
C |
т , кг/м2 |
|||||
1 |
|
|
|
|
|
|
|
|
|
|
2 |
|
|
|
|
|
|
|
|
|
|
3 |
|
|
|
|
|
|
|
|
|
|
За стираність приймається середнє арифметичне результатів випробування не менш трьох зразків. Висновок робиться на підставі порівняння отриманих результатів із вимогами стандарту. Значення стираності керамічних плиток для підлог не повинна перевищувати
0,18 г/см2 (1,8 кг/м2).
3. КЕРАМІЧНІ МАТЕРІАЛИ
Керамічними називають матеріали і вироби, що виготовляють з природних глин або їх сумішей з органічними і мінеральними добавками після формування і випалювання матеріалів, виробів.
3.1. Цегла керамічна.
При оцінці якості цегли керамічної визначають зовнішні ознаки, форму і розміри, водопоглинання, границі міцності при стиску і вигині, середню густину, морозостійкість.
9

Для контролю якості від кожної партії цегли відбирають вироби у кількості 0,5%, але не менш як 100 шт. Усі відібрані зразки піддають зовнішньому огляду і вимірюванню, потім кілька зразків виділяють для визначення границі міцності при стиску – 10 шт., границі міцності при вигині – 5 шт., середньої густини і водопоглинання – 3 шт., морозостійкості – 5 шт., наявності вапнякових включень.
3.1.1. Зовнішній вигляд, форми і розміри.
Обладнання і матеріали. Еталон нормально випаленої цегли, лінійка металева, кутник, молоток, зразки цегли.
Випробування. Зразки цегли ретельно оглядають, встановлюють при цьому ступінь випалювання, наявність або відсутність тріщин, відбитості кутів та інші дефекти. Потім перевіряють відхилення форми і розмірів цегли від допустимих стандартом.
Ступінь випалювання встановлюють, порівнюючи колір і водопоглинання відібраних зразків з еталоном нормально випаленої цегли. Недопал і перепал цегли є браком. Якщо відсутній еталон, ступінь випалювання можна визначити (умовно) за звуком при ударі молотком.
Викривлення граней і ребер визначають вимірюванням із точністю до 1 мм найбільшого зазору між гранню або ребром і прикладених до них металевою лінійки чи кутника.
Непрямолінійність ребер і граней цегли має бути не більше: на постелі 3 мм, на ложку
4 мм.
Цегла повинна мати форму прямокутного паралелепіпеда з рівними гранями на лицьових поверхнях. Допускається виготовлення цегли із заокругленими кутами з радіусом заокруглення до 15мм.
Відбитості або притупленості ребер і кутів цегли визначають вимірюванням найбільшої довжини їх по ребру з точністю до 1мм. Відбитостей кутів глибиною від 10 до 15мм має бути не більше 2, відбитостей і притупленостей ребер довжиною по ребру від 10 до 15мм також допускається не більше 2. Загальна кількість цегли з відбитостями, що перевищують норму, не повинна бути більше 5%. Допускаються тріщини протягом по постелі повнотілої цегли до 30 мм, пустотілих виробів не більше як до першого ряду пустот, на ложкових і тичкових гранях не більш як одна. При наявності тріщини більших розмірів, цеглу відносять до половняку, кількість якого не повинна бути більше як 5%.
Розміри цегли визначають із точністю до 1мм при вимірюванні в трьох місцях–по ребрах і посередині грані. За остаточний результат приймають середнє арифметичне трьох розмірів. Залежно від розмірів цеглу поділяють на три види: 250х120х65мм (цегла рядова), 250х120х88мм (потовщена) і 288х138х63мм (модульних розмірів). Відхилення від розмірів не повинні перевищувати: за довжиною ±5мм, за шириною ±4мм, за товщиною ±3мм.
Вапнякові включення (дутики), що визначаються при пропарюванні виробів і спричиняються після випробувань до руйнування виробів або відколів на їх поверхні найбільшим розміром від 5 до 10мм, кількістю більше трьох не допускаються.
Результати записують у табл. 3.1.
Таблиця 3.1
|
|
|
Зовнішній вигляд, форма і розміри цегли |
|||
|
|
|
|
Викрив- |
Відбитості |
Наявність |
|
Розміри |
Ступінь |
|
тріщин, їх |
||
Номер |
|
лення |
кутів і ребер, |
|||
зразка |
цегли, |
випалю- |
|
граней і |
кількість, |
кількість, |
|
мм |
вання |
|
ребер, мм |
розмір, мм |
протяж- |
|
|
|
|
ність, мм |
||
|
|
|
|
|
|
|
1 |
|
|
|
|
|
|
2 |
|
|
|
|
|
|
3 |
|
|
|
|
|
|
Наявність |
|
дутиків, |
Інші |
їх кіль- |
дефе- |
кість і |
кти |
розміри |
|
|
|
|
|
|
|
Якщо в результаті випробувань зразків буде встановлено невідповідність їх хоча б одному з показників, то за цим показником проводять повторне випробування подвійної кі-
10