
Конспект лекций УЛП
.pdf-цей підхід здебільшого покладається на прогнози, через що можуть виникати похибки.
Найбільш росповсюджений спосіб позбавитися цих ускладнень – зіставити пропозицію логістичних послуг з фактичним попитом на них. Тобто необхідний спосіб для визначення реального попиту замість використання ненадійних прогнозів. Цим займається така діяльність як планування потреби у матеріалах (ППМ).
Основний підхід к плануванню виходить з припущення, що загальний попит на продукцію складається з окремих складових попиту великої кількості споживачів. Ці попити незалежні один від одного, тому попит одного споживача не пов’язаний з попитом іншого. Такий варіант дає незалежний попит, при якому планування відбувається на базі стандартних методів.
Однак, оскільки в реальному житті виробники використовують ряд компонентів для виробництва кінцевого продукту, то попит на кожний з таких компонентів буде залежати від попиту на суміжні. В цьому випадку ми одержуємо залежний попит. Типовий підхід на базі ППМ полягає в тому, що основний графік попиту поділяється на складові, та на базі цього планується постачання всіх необхідних матеріалів.
Основна різниця між традиційним плануванням ресурсів (маркетинг, метод регресивного аналізу і т.і.) та плануванням на базі ППМ пов’язана з характером запасів матеріалів. При незалежному попиті запаси не пов’язуються з виробничими планами,
тому вони повинні бути достатньо високими, що дозволяти задовольнити будь-який можливий попит. Ці запаси зменшуються під час виконання операцій, але швидко поповнюються. При використанні ППМ запаси зазвичай низькі, але підвищуються, коли замовлення доставляються безпосередньо перед початком виконання операцій. Після цього запас під час виробництва використовується та знов знижується до загального рівня.
При ППМ використовується великий обсяг інформації про продукти та матеріали. Ця інформація надходить з наступних витоків:
-основного графіку, де наводиться об’єм кожного продукту, який виготовляється в кожний період часу;
-відомості специфікації матеріалів, де перелічуються матеріали, необхідні для виробництва кожного продукту;
-облікової документації по запасах, де наведено наявність матеріалів.
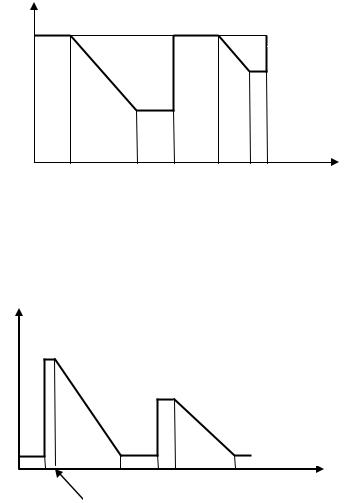
Обсяг запасу
Звичайний обсяг запасу
Початок |
Постачання |
Час |
|
виробництва |
замовлення |
||
|
Кінець
виробництва
Рисунок 13.1 Обсяг запасу при незалежному попиті
Обсяг запасу
|
|
Звичайний |
|
|
обсяг запасу |
Постачання |
Кінець |
Час |
замовлення |
виробництва |
|
Початок
виробництва
Рисунок 13.2 Обсяг запасу при залежному попиті.
Усі деталі в ланцюгу мають рівень деталізації, який показує, коли вони включаються в процес. Готова продукція має рівень 0; рівень 1 – це складові з яких безпосередньо можна виробити одиницю рівня 0; складові рівня 2 використовуються для виробництва складових рівня 1 і т.д.
Узагальнити досить багатоелементну процедуру ППМ можна представивши її у вигляді наступних кроків:
1.Використати основний графік для визначення валової потреби в одиницях рівня 0.
2.Відняти будь-який запас що вже мається та об’єм замовлень які повинні надійнти,
та визначити чисту потребу в одиницях рівня 0. Після цього скласти виробничий графік, вказавши час початку робіт, визначених чистою потребою.
3.Перейти на наступний рівень. Використати специфікацію на матеріали, щоб перетворити чисту потребу попереднього рівня та визначити валову потребу послідуючого рівня.
4.По черзі проаналізувати кожен матеріал та:
-відняти запас, що мається у наявності, та заплановані постачання, щоб визначити необхідний обсяг матеріалів;
-використати час виконання замовлення та будь-яку іншу вагому інформацію, щоб визначити об’єм замовлень та час їх розміщення;
-якщо в результаті отримані великі рівня матеріалів, повернутися до етапу 3.
5.Скласти фінальний росклад, додавши до нього будь-які необхідні вимоги.
Як вже зазначалося, традиційна система з незалежними замовленнями прогнозує імовірний попит на матеріали, після чого зберігає достатньо високий запас для задоволення цієї потреби. Використання ППМ дозволяє уникнути витрат на ці запаси,
безпосередньо пов’язуючи матеріали з попитом на них. Це дає наступні переваги:
-зменшення обсягу запасів, що дозволяє досягти економії на капіталі, площах що використовується, складських процесах і т.і.;
-підвищення швидкості оберту запасів;
-підвищення якості обслуговування споживачів, оскільки немає затримок, які викликаються нестачею матеріалів;
-підвищення стабільності часу та швидкості постачання замовлень;
-зменшення часу на експедування та на виконання термінових замовлень;
-можливість використання графіків ППМ для планування інших логістичних видів діяльності.
Планування потреби у матеріалах може заздалегіть попередити про можливі проблеми або наближення дефіциту. Якщо графіки ППМ показують, що окремі матеріали надходять дуже пізно, організація може спробувати прискорити їх постачання,
або змінити свої виробничі плани. Таким чином при цьому покращуються загальні показники діяльності організації: коефіціент використання обладнання, продуктивність,
якість обслуговування споживачів, швидкість реагування на умови що змінюються і т.і.
Однак використання ППМ пов’язано з рядом проблем, основна з яких – великий обсяг інформації та необхідних розрахунків. Основна інформація надходить з детального основного графіку який розробляється заздалегідь, тому за його відсутності ППМ
використати неможна. До інших необхідних витоків інформації належать специфікації на матеріали, дані про наявні запаси, дані про розміщені але не виконані замовлення, час виконання замовлень та інші дані про постачальників. При цьому дуже важлива точність,
оскільки навить невелика кількість неточних заказів на запаси може привести до істотних втрат. На початку похибки можуть бути невеликі та не звертати на себе уваги,
оскільки наявний запас дозволяє їх корегувати до того як вони проявляться. Однак ППМ не передбачає наявності страхових запасів, тому резерву для покриття помилок не існує.
Звідси випливає ще одна проблема ППМ – негнучкість. В нявності є лише ті матеріали,
які необхідні для виконання конкретного основного графіку, тому імовірність корегування дуже невелика. Найбільш загальними недоліками ППМ вважаються наступні:
-низька гнучкість не дозволяє оперативно реагувати на зовнішні зміни;
-потрібен великий обсяг детальної та точної інформації;
-наявність дуже складних систем;
-розмір замовлень, що передбачає ППМ, може бути неефективним;
-ППМ може не враховувати обмежень по потужності та по деяким іншим параметрам;
-цей варіант може бути дорогим та вимагати багато часу для реалізації.
Лекція 14. Принципи роботи «точно в строк».
Робота «точно в строк» передбачає принципово новий спосіб планування. Всі види діяльності організуються таким чином, щоб вони виконувалися точно в той час, коли необхідно. Іншими словами, вони не виконуються зарано (через що матеріали повинні чекати, коли вони фактично потрібні) та вони не виконуються запізно (через що зменшується якість обслуговування замовників або споживачів).
Така робота є очевидною ідеєю, але вона може досить суттєво вплинути на спосіб організації всіх матеріалів. Це можна побачити на прикладі закупівлі сировини. При традиційному підході закупівлі сировини здійснюються на ранніх етапах, заздалегідь,
після чого вона зберігається в запасах до того моменту, коли буде потрібно. Вже розглянута методика ППМ зменшує розмір запасів, координуючі прибуття матеріалів з запитом на них. Мета «точно в строк» - забезпечення постачання матеріалів
безпосередньо до часу виконання конкретних операцій, завдяки чому запас фактично ліквідується.
Описання роботи «точно в строк» необхідно почати з аналізу його впливу на запаси.
Основна мета накопичення запасів – мати резервний їх обсяг між операціями. Запаси накопичуються в період коли все йде за планом компанії, для використання їх коли виникають проблеми. Тому, якщо якесь обладнання ломається, або затримується постачання чи раптово виникає попит, все далі працює нормально на наявних запасах.
При традиційному погляді вважається що запаси – це важливий елемент всієї системи,
оскільки вони гарантують відсутність порушень при виконанні операцій.
Існуючі системи контроля запасів встаовлюють достатньо високі їх рівні, щоб завжди можна було подолати потенційні проблеми. Нажаль через широке коливання попиту обсяг цих запасів можу бути дуже високим, тому надто дорогим для компанії. На практиці визначення обсягу замовлення на базі встановлених правил фактично дозволяє мати деякий запас, який зберігається на випадок виникнення невизначеностей або проблем. Однак зрозуміло, що чім вище буде забезпечено ступінь відповідності між постачанням матеріалів та попитом на них, тим менший запас нам потрібен. Ідеальний випадок – повна відсутність неспівпадіння між постачанням та попитом, тобто запаси взагалі відсутні.
Можна сформувати наступні точки зору системи «точно в строк» на запаси:
-запаси створюються для корегування короткострокових невідповідностей між постачанням та попитом;
-ці запаси не несуть корисного навантаження, вони існують тільки через погану координацію, що не дозволяє мати точну відповідність між постачанням матеріалів та попитом на них;
-поки запаси зберігаються, ніяких очевидних проблем не виникає, тому менеджери не мають стимулів вдосконалювати матеріальний потік, результатом чого стає те,
що операції погано управляються, а всі проблеми ховаються в запаси;
-реальне рішення – покращення операцій що виконуються, пошук причин різниці між попитом та пропозицією, після чого вживання заходів щодо усунення цих невідповідностей.
Отже, загальна база системи «точно в строк» - замість зберігання запасів та примирення з наявністю вузьких місць необхідно виявити проблемні ділянки та усунути їх.
З цього видно, що така система використовується не лише у відношенні запасів, а й призводить до загального перегляду операцій компанії. Крім вже розглянутих запасів до них відносяться:
1.Постачальники. При роботі «точно в строк» необхідно в повній мірі покладатися на постчальників, які повинні працювати на базі довгострокових партнерських відносин, переслідуючі загальні цілі.
2.Обсяг партій. В ході операцій часто випускаються великі партії продукції,
оскільки це дозволяє знизити витрати на переналадку обладнання та перерви у виробництві. Однак при низькому попиті, то продукція виготовлена великими партіями довго зберігається в запасах. Частина системи «точно в строк» спрямована на пошук способів зменшити об’єми партії при незмінних витратах,
для кращої відповідності попиту.
3.Час на виконання замовлень. Тривалий час на виконання замовлень сприяє накопиченню великих запасів, оскільки дозволяє уникнути будь-яких невизначеностей, які можуть виникнути до наступної поставки. При роботі «точно в строк» постачання зазвичай здійснюються частіше та меншими партіями, при цьому час на виконання таких замовлень зменшується.
4.Надійність. В основ «точно в строк» лежить безперервне постійне виробництво,
тому всі операції повинні виконуватися надійно. Якщо обладнання ломається,
менеджери повинні відшукати причини поломок та впевнитися, що такого більше не буде.
5.Робітники. В деяких організаціях спостерігаються конфлікти між «менеджерами» та «робітниками». При роботі «точно в строк» необхідно розуміти, що така різниця не має смислу, бо благополуччя всіх працюючих залежить від кінцевого
результату діяльності організації, тому відношення до всіх робітників повинно бути однаковим та справедливим.
Основною глобальною проблемою системи «точно в строк» є те, що вона працює тільки у деяких типах організацій. Найбільш вигідна вона для збиральних заводів великої
потужності, які в ході постійного процесу випускають практично одну й ту саму
продукцію. Це викликано наступними аргументами:
1.Кожен раз, коли в процес необхідно внести зміни, або необхідно перейти від випуску одного виду продукції до іншого, виникають затримки та збої в роботі, в
результаті чого зростають витрати. Тобто найкращий варіант – стабільне середовище, коли в ході одного процесу виготовляється більше стандартного продукту.
2.Таке стабільне середовище може скоротити витрати, використовуючі спеціалізоване автоматизоване обладнання. Через це «точно в строк» краще працює при великих обсягах виробництва, тобто при випуску масової продукції.
3.Рівень виробництва повинен забезпечувати постійний безперебійний потік продуктів через усі процеси. Кожен з цих процесів повинен використовуватися в повній мірі, і лише в цьому випадку збіркова лінія буде добре збалансована.
Оскільки матеріали доставляються саме коли потрібні та саме у потрібній кількості, постачальникам доведеться адаптуватися до таких операцій. Саме практичне рішення при цьому – постачання невиликими партіями.
4.Оскільки використовується постачання невеликими партіями, необхідно максимально скоротити витрати на повторні замовлення, оскільки в іншому разі часті постачання будуть дуже дорогі.
5.Необхідно скоротити час на виконання замовлень, оскільки затримки після одержання замовлення на матеріали можуть стати дуже великими. Для цього необхідна тісна взаємодія з постачальниками та їх стимулювання створювати свої підприємства навколо структур замовника.
6.Оскільки відсутні страхові запаси, будь-яка нестача матеріалів призводить до порушення процеса виробництва. Тому постачальники повинні надійно постачати безбракові матеріали.
7.Якщо має місце збій, працівники, що зайняті в цьому процесі повинні оперативно відшукати його причину та вжити заходів для усунення помилок. Це потребує заохочення професійно підготовлених та гнучко діючих працівників, які
заінтерисовані в успіхах організації.
В загальному вигляді світове використання системи «точно в строк» дозволило в середньому на 65% скоротити запаси, на 40% зменшити площі на яких виконуються
роботи, на 15% знизити обсяги інвестицій в запаси. В цілому використовуючі цю систему можна одержати наступні вигоди:
-знизити запаси сировини та незакінченого виробництва;
-скоротити час виконання замовлень;
-скоротити час виробництва продукції;
-збільшити продуктивність;
-підвищити ступінь використання обладнання;
-спростити планування та диспетчеризацію;
-зменшити обсяги паперової роботи;
-підвищити якість матеріалів та продуктів;
-зменшити обсяг відходів;
-збільшити стувінь відповідальності робітників;
-покращити відносини з постачальниками;
-з’являється спрямуваня на самостійне вирішення проблем в роботі.
Нажаль деяких переваг з перелічених можна досягти лише заплативши за них досить високу ціну. В самих положеннях цієї системи є протиріччя, через які досягнення економії на одному, тягне за собою подорожчання виробництва на іншому етапі.
У компаній, що працюють по такій схемі виникіють специфічні проблеми, основні з яких наступні:
-більш високий ризик від повного впровадження нових систем та операцій;
-великі першопочаткові інвестиції та витрати на реалізацію;
-великий проміжок часу до початку істотного покращення роботи;
-залежність від високої якості матеріалів, що поставляють постачальники;
-неспроможність окремих постачальників пристосуватися до роботи на умовах
«точно в строк»;
-необхідність у стабільному виробництві, при умові коливання попиту чи його сезонних відхилень;
-зниження гнучкості, що ускладнює задоволення особливих чи змінних потреб споживачів;
-складність скорочення часу на переналадку обладнання та пов’язаних з цим витрат;
-відсутність ентузіазма до цього методу в організації;
-відсутніст духу співробітництва та довіри між робітниками;
-проблеми прив’язки цієї системи до інших інформаційних систем;
-необхідність зміни зовнішнього планування споруд;
-робота співробітників в умовах підвищеного стресу;
-нездатність окремих співробітників взяти на себе велику відповідальність.
БІБЛІОГРАФІЧНИЙ СПИСОК
1.А.Кофман, Р.Фор. Займемся исследованием операций. М.:Мир 1961 г.
2.А.Гаджинский. Практикум по логистике. М.: Инфра, 2007 г.
3.В.Аникин. Практикум по логистике. С-П.: 2001 г.
4.Д.Уотерс. Логистика: управление цепями поставок. М.: Инфра, 2003 г.
5.В.Марченко. Задачі з логістики. Київ: МАУП, 2006 р.
6.М.Оклендер. Логистика.Учебник. М.:ЦУЛ, 2008 г.
7.А.Смирнов. Транспортная логистика. М.:ЦУЛ, 2008 г.
8.С.Гамильтон. Управление цепочками поставок. М.: Альпина бизнес букс, 2005 г.
9.Управление цепями поставок. Под ред. Д.Гатторны. М.: Инфра-М, 2007 г.
10.М.Линдерс, Ф.Джонсон. Управление закупками и поставками. М.: Юнити, 2007 г.
11.А.Харрисон, Р.В.Хоук. Управление логистикой. М.:Баланс бизнес букс, 2006 г.
12.С.В.Саркисов. Управление логистическими цепями поставок. М.: Дело, 2006 г.
13.Д.Шехтер, Г.Сандер. Логистика. Искусство управления цепочками поставок.
М.:Перетекст, 2008 г.
14. А.М.Сумец. Логистика. Теории, ситуации, практические задания. М.: Хай-тек
пресс, 2007 г.