
- •Рис. 9.2. К расчету теплообмена в реакторе вытеснения
- •Рис. 7.2. К примеру 10.1
- •Рис. 11.4. К примеру 11.1
- •Рис. 11.9. К расчету шпилек
- •Рис. 11.10. К примеру 11.3
- •Рис. 11.11. К примеру 11.5
- •Рис. 13.10. Рамные мешалки
- •Рис. 13.11. Якорные мешалки
- •Предисловие
- •Экологическое и технико-экономическое обоснование проектов химических производств.
- •Этапы проведения экологической экспертизы
- •Принципы экологической экспертизы
- •Рис. 1.1. Общая система организации проектирования
- •Рис. 1.2. Основные этапы и стадии разработки проектов для промышленного строительства
- •1.2. Задание на проектирование
- •Рис. 1.3. Пример построения розы повторяемости и силы ветров
- •Рис.1.4. Схема выпадения дымовых частиц при наличии зеленых защитных насаждений между застройкой и источником задымления и при отсутствии их:
- •Рис. 1.5. Совмещенная схема движения загрязненных нижнего и верхнего потоков
- •1.5. Разработка проектной документации по охране окружающей среды
- •1.5.2. Разработка прогноза загрязнения воздуха
- •1.5.4. Прогноз воздействия объекта при возможных авариях
- •1.6. Технологический процесс как основа промышленного проектирования
- •Рис. 1.6. Схема производства серной кислоты контактным способом:
- •Рис. 1.8. Процессы и аппараты химической технологии
- •Рис. 1.9. Виды оборудования химической технологии
- •Рис. 1.11. Уровни организации химического предприятия
- •1.7. Генеральный план химических предприятий
- •Рис. 1.12. Генеральный план предприятий химической промышленности
- •1.8. Типы промышленных зданий
- •1.8.1. Одноэтажные промышленные здания
- •Рис. 1.13. Одноэтажное здание павильонного типа:
- •Рис. 1.14. Многоэтажное производственное здание:
- •1.8.2. Многоэтажные здания
- •Рис. 1.15. Многоэтажное производственное здание:
- •Рис. 1.16. Поперечные разрезы зданий I и II очередей сернокислотного производства:
- •1.8.3. Вспомогательные здания и помещения химических предприятий
- •1.8.4. Склады промышленных предприятий
- •1.9. Инженерные сооружения
- •инженерных сооружений
- •1.10. Специальные вопросы проектирования химических предприятий
- •2.1. Основные стадии проектирования химических производств и оборудования
- •Рис. 2.1. Основные стадии проектирования
- •2.2. Виды конструкторских документов
- •2.4.1. Курсовое проектирование
- •2.4.2. Дипломное проектирование
- •2.4.3. Пример использования АвтоЛиспа
- •Рис. 2.2. Схема установки для ректификации трехкомпонентной смеси:
- •СИСТЕМЫ АВТОМАТИЗИРОВАННОГО ПРОЕКТИРОВАНИЯ
- •3.1. История развития САПР
- •3.2. Основные принципы создания САПР
- •Рис. 3.1. Модульная структура программного обеспечения
- •Рис. 3.2. Области использования ЭВМ в процессе проектирования
- •3.4. Автоматическое изготовление чертежей
- •3.5. Основные преимущества автоматизации проектирования
- •3.6. Основные требования к САПР
- •Рис. 3.3. Схема взаимодействия пользователя со средствами САПР:
- •3.7. Связь САПР с производством, расширение области применения
- •3.8. Система автоматизированного проектирования цементных заводов
- •3.8.1. Функционирование САПР
- •ВВЕДЕНИЕ В ПРОЕКТИРОВАНИЕ
- •4.1. Проектно-сметная документация
- •4.2.1. Исходные положения
- •4.2.2. Обоснование способа производства химической продукции
- •ВЫБОР И РАЗРАБОТКА ТЕХНОЛОГИЧЕСКОЙ СХЕМЫ ПРОИЗВОДСТВА
- •5.1. Общие положения
- •5.2. Последовательность разработки технологической схемы
- •Рис. 5.1. Примерная схема стадий технологического процесса:
- •Рис. 5.2. Блок-схема физико-химических процессов, протекающих в гетерофазном реакторе с мешалкой
- •5.3. Принципиальная технологическая схема
- •5.4. Размещение технологического оборудования
- •Выбор технологического оборудования химических производств
- •6.1. Основные типы химических реакторов
- •Рис. 6.1. Установка для непрерывного процесса:
- •Рис. 6.5. Изменение концентрации веществ в реакторах:
- •Рис. 6.6. Реакторы смешения:
- •6.2. Химические факторы, влияющие на выбор реактора
- •6.2.1. Реакции расщепления
- •Рис. 6.7. Относительный выход реакции расщепления:
- •Реактор
- •6.2.2. Реакции полимеризации
- •6.2.3. Параллельные реакции
- •Объем реактора
- •РВНД
- •6.3. Эскизная конструктивная разработка основной химической аппаратуры
- •6.3.1. Общие положения
- •6.3.2. Реакторы
- •6.4. Оптимизация процессов химической технологии
- •УРАВНЕНИЯ МАТЕРИАЛЬНОГО БАЛАНСА ТЕХНОЛОГИЧЕСКОГО ПРОЦЕССА
- •7.1. Стехиометрические расчеты
- •7.2. Термодинамический анализ процессов
- •7.2.1. Равновесие химической реакции
- •Рис. 1.1. Зависимость коэффициента активности газв от приведенных давления и температуры
- •7.2.2. Расчет состава равновесной смеси
- •7.3. Общее уравнение баланса массы
- •7.4. Практический материальный баланс
- •7.5. Физико-химические основы технологического процесса
- •8.1. Общие положения
- •8.2. Расчет объемов реакторов
- •8.2.1. Основные положения химической кинетики
- •8.2.2. Расчет идеальных реакторов
- •8.3. Определение объемов аппарата
- •Тепловой расчет основного оборудования
- •9.1. Общее уравнение баланса энергии
- •Рис. 9.1. К примеру 9.1
- •9.2. Практический тепловой баланс
- •9.3. Теплообмен в реакторах
- •9.4. Расчет энтальпий и теплоемкостей
- •9.6. Расчет реактора периодического действия
- •Рис. 9.3. К тепловому расчету реактора периодического действия
- •9.7. Степень термодинамического совершенства технологических процессов
- •Рис. 9.6. Технологическая схема 1:
- •Рис. 9.7. Технологическая схема 2
- •Рис. 9.8. Схемы использования тепла реакций:
- •Гидравлические расчеты
- •10.1. Расчет диаметра трубопровода
- •Пары, насыщенные при абсолютном давлении (МПа)
- •Рис. 10.1. Зависимость коэффициента трения от критерия Рейнольдса и степени шероховатости трубы
- •10.3. Гидравлическое сопротивление кожухотрубчатых теплообменников
- •10.4. Подбор насосов
- •МЕХАНИЧЕСКИЙ РАСЧЕТ
- •11.1. Расчет сварных химических аппаратов
- •11.1.1. Основные расчетные параметры
- •11.1.2. Расчет на механическую прочность
- •11.1.3. Требования к конструированию
- •11.1.4. Расчет цилиндрических обечаек
- •Рис. 11.1. Номограмма для определения толщины цилиндрических обечаек, работающих под наружным давлением
- •Рис.11.2. Схема пользования номограммой на рис. 11.1:
- •11.1.5. Расчет крышек и днищ
- •Рис. 11.3. Основные конструкции днищ сварных аппаратов:
- •11.1.6. Подбор стандартных элементов
- •11.2. Расчет толстостенных аппаратов
- •Рис. 11.7. Основные конструкции уплотнений затворов высокого давления:
- •Рис. 11.8. К расчету усилий, действующих на затворы высокого давления
- •КОНСТРУКционНЫЕ МАТЕРИАЛЫ В ХИМИЧЕСКОМ МАШИНОСТРОЕНИИ
- •12.1. Виды конструкционных материалов
- •12.2. Коррозия металлов и сплавов
- •12.2.1. Виды коррозии
- •12.2.2. Виды коррозионных разрушений
- •12.2.3. Способы борьбы с коррозией
- •12.3. Влияние материала на конструкцию аппарата и способ его изготовления
- •12.3.1. Конструкционные особенности аппаратов из высоколегированных сталей
- •Рис. 12.1. Сварка встык:
- •Рис. 12.2. Способы подготовки кромок под сварку
- •Рис. 12.4. Способы сварки легированной и углеродистой стали
- •12.3.2. Конструктивные особенности эмалированных аппаратов
- •Рис. 12.5. Элементы конструкции эмалированных аппаратов
- •Рис 12.6. Пайка элементов медных аппаратов
- •12.3.3. Конструктивные особенности аппаратов из цветных металлов
- •Рис. 12.7. Основные типы паяных соединений
- •12.3.4. Конструктивные особенности аппаратов из пластмасс
- •ОФОРМЛЕНИЕ ОТДЕЛЬНЫХ ЭЛЕМЕНТОВ ХИМИЧЕСКОЙ АППАРАТУРЫ
- •13.1. Оформление поверхности теплообмена
- •Рис. 13.5. Реактор со змеевиковой рубашкой
- •Рис. 13.6. Рубашка с вмятинами
- •Рис. 13.8. Вывод змеевика через крышку аппарата:
- •13.2. Перемешивающие устройства
- •Рис. 13.12. Листовая мешалка
- •Рис. 13.13. Пропеллерные мешалки
- •Рис. 13.14. Турбинные мешалки открытого (а) и (б) закрытого типа
- •Рис. 13.15. Крепление мешалок к ступице:
- •13.3. Уплотнения вращающихся деталей
- •Рис. 13.18. Одинарное торцовое уплотнение:
- •ТРУБОПРОВОДЫ И ТРУБОПРОВОДНАЯ АРМАТУРА
- •Рис 14.5. Фасонные части трубопроводов
- •Рис. 14.7. Крепление горизонтальных и вертикальных трубопроводов на подвесках
- •Рис. 14.8. Компенсаторы:
- •ВСПОМОГАТЕЛЬНОЕ ОБОРУДОВАНИЕ ХИМИЧЕСКИХ ЗАВОДОВ
- •15.1. Виды вспомогательного оборудования
- •Рис. 15.1. Схема многостадийного диспергирования твердой фазы с контрольной классификацией продукта
- •15.2. Транспортные средства
- •15.2.1. Классификация транспортных средств для твердых материалов
- •15.2.2. Машины для транспортировки жидкостей и газов
- •ТЕХНОЛОГИЧЕСКИЕ СХЕМЫ И ОБОРУДОВАНИЕ ДЛЯ ГРАНУЛИРОВАНИЯ ДИСПЕРСНЫХ МАТЕРИАЛОВ
- •16.1. Классификация методов гранулирования и особенности уплотнения гранул
- •Рис. 16.1. Тарельчатый гранулятор:
- •Рис. 16.2. Гранулятор барабанного типа конструкции НИИХиммаша
- •16.3. Основные закономерности и аппаратурное оформление метода экструзии
- •16.5. Гранулирование в псевдоожиженном слое
- •16.6. Технологические схемы процессов гранулирования дисперсных материалов
- •Рис. 16.11. Технологическая схема гранулирования шихты методом окатывания
- •Рис. 16.13. Схема уплотнения шихты в роторном грануляторе
- •Рис. 16.14. Схема гранулирования шихты методом экструзии
- •Рис. 16.15. Схема установки для компактирования шихты
- •ЛИТЕРАТУРА
6. Футерование химического оборудования термопластами. Защитное действие полимерных покрытий и футеровок в общем случае определяется их химической стойкостью в конкретной агрессивной среде, степенью непроницаемости (барьерная защита), адгезионной прочностью соединения с подложкой, стойкостью к растрескиванию и отслоению, зависящей от внутренних механических свойств полимера и подложки, неравновесностью процессов формирования защитных слоев и соединений.
Наибольшее распространение при футеровании химического оборудования получили листы и пленки из полиэтилена (ПЭ), полипропилена (ПП), политетрафторэтилена (ПТФЭ), поливинилхлорида (ПВХ), пентапласта (ПТ) и других композиционных материалов. Для повышения физико-механических и защитных свойств, износостойкости листовые футеровочные материалы наполняют минеральными наполнителями (сажа, графит, сернокислотная обработка, ионная бомбардировка и др.). Для повышения адгезионной активности по отношению к клеям листовые материалы дублируют различными тканями.
Правильно выбранный способ антикоррозионной защиты позволит обеспечить максимальную долговечность защиты химического оборудования в конкретных условиях его эксплуатации.
12.3. ВЛИЯНИЕ МАТЕРИАЛА НА КОНСТРУКЦИЮ АППАРАТА И СПОСОБ ЕГО ИЗГОТОВЛЕНИЯ
Правильный выбор конструкционного материала оказывает непосредственное влияние на технологичность отдельных деталей и узлов, сварных, паяных и клеевых соединений, а также на конструкцию проектируемого аппарата или машины.
Технологические свойства конструкционных материалов в значительной степени определяют выбор способа изготовления из него отдельных деталей и узлов.
Например, большинство чугунных деталей получают методом литья. Изделия из стали, наряду с литьем, могут быть получены резанием, ковкой, штамповкой, гибкой из стального проката. Способы соединения отдельных деталей также зависят от вида конструкционного материала: для стали
– сварка, для цветных металлов − пайка, для пластмасс – клейка.
12.3.1. Конструкционные особенности аппаратов из высоколегированных сталей
Основным способом соединения отдельных элементов стальных аппаратов является сварка.
Высокое качество сварных соединений обеспечивается совокупностью конструктивных и технологических решений, принимаемых на этапах выбора материалов конструкции, размеров и формы деталей, рациональных способов изготовления, сборки и сварки.
284
Существуют различные способы сварки:
−термическая – дуговая, электронно-лучевая, плазменная, лазерная, газовая, электрошлаковая, термитная, многодуговая;
−термомеханическая– контактная, прессовая, кузнечная, диффузионная, высокочастотная, печная и др.;
−механическая – холодная, сварка взрывом, ультразвуковая, сварка трением, магнитно-импульсная.
Кроме того, сварка может быть автоматической, полуавтоматической и ручной.
Выбор способа сварки во многом определяется отношением металла к термомеханическому циклу сварки, так как при перегреве сталей происходит выгорание легирующих элементов, приводящее к потере их химической стойкости и механической прочности.
Поэтому при конструировании сварных аппаратов проектировщик должен выполнить следующее:
−выбрать способ сварки;
−выбрать тип сварного шва;
−выбрать схему подготовки кромок с учетом способа сварки;
−разработать конструкцию сварного шва.
1.Способ сварки. Способ сварки выбирается в зависимости от вида конструкционного материала свариваемых частей, их геометрических размеров и формы. Наиболее распространенным видом сварки является электродуговая автоматическая сварка под флюсом, а также полуавтоматическая и ручная дуговая сварка.
2.Тип сварного шва. Тип сварного шва зависит от расположения свариваемых поверхностей, доступности места сварки с учетом выбранного метода сварки. Как видно из рис. 12.1, свариваемые детали соединены встык и в местах сварки имеют одинаковую толщину. Практика эксплуатации сварных аппаратов показала, что сварка встык является наиболее надежным типом сварного шва.
285
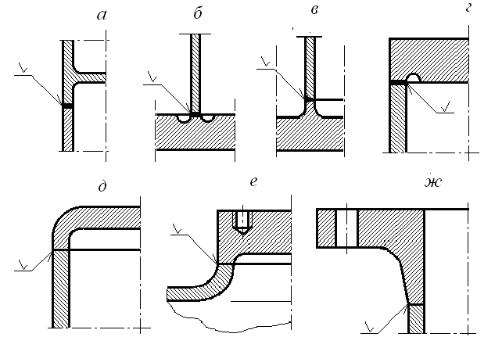
Рис. 12.1. Сварка встык:
а– полый вал; б − д – соединение обечайки с трубной решеткой;
е– соединение бобышки с обечайкой; ж – соединение фланца с обе-
чайкой
3.Подготовка кромок (рис. 12.2). Обработка кромок зависит от толщины свариваемых листов и метода сварки. Разделка кромок под углом необходима в тех случаях, когда требуется увеличить степень участия металла электрода в формировании структуры сварного шва. Например, при сварке нержавеющей стали с углеродистой разделка кромок обязательна для того, чтобы избежать растрескивания шва. Двухсторонняя разделка кромок служит для того, чтобы в сварном шве доминировал материал электрода, а также при сварке листов толщиной более 50мм.
4.Конструкция сварного шва. Конструкция сварного шва должна обеспечить хорошее качество сварки и сохранение прочностных и коррозионных свойств металла конструкции.
Кроме соединения встык, используют соединения втавр и внахлест (рис. 12.3).
Как уже отмечалось, длительный перегрев легированных сталей, даже содержащих титан или ниобий, приводит к выгоранию легирующих добавок
ипотере сталью коррозионной стойкости. Поэтому для сохранения состава и структуры сварного шва необходимо соблюдать следующие условия:
286
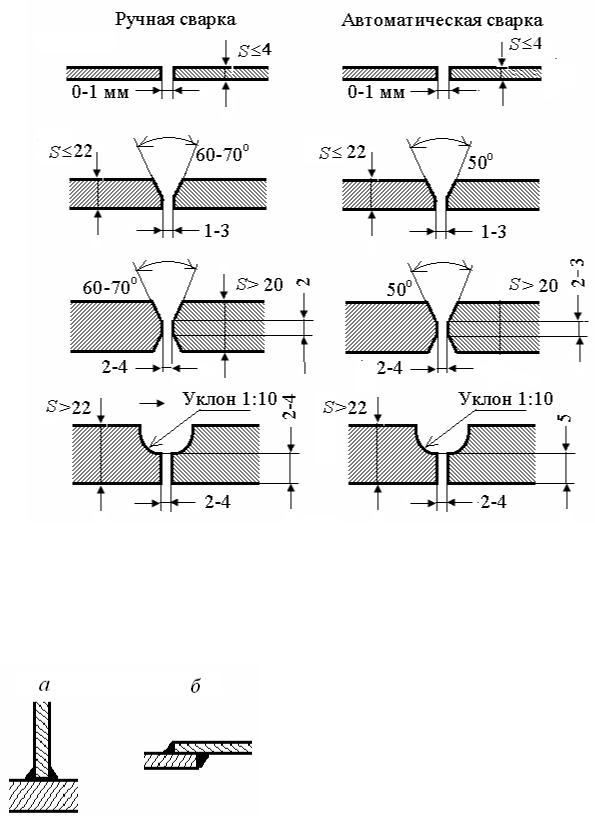
Рис. 12.2. Способы подготовки кромок под сварку
− свариваемые детали в местах сварки должны иметь одинаковую толщину; − свариваемые детали должны быть выполнены из материалов, имеющих
одинаковую или близкую по значению температуру плавления;
|
− правильно выбирать материал элек- |
|
трода или состав флюса, для восполнения |
|
возможных потерь легирующих элементов |
|
в процессе сварки; |
|
− не подвергать многократному пере- |
|
греванию места сварки с целью сохране- |
|
ния состава стали в шве; |
Рис. 12.2. Сварка втавр (а) и |
− сварные швы следует располагать в |
внахлест (б) |
местах с минимальным значением напря- |
жения и остаточных деформаций в материале;
−минимальный диаметр обечаек для сварки внутренних швов – 600 мм,
анаружных – 100 мм;
287