
- •Рис. 9.2. К расчету теплообмена в реакторе вытеснения
- •Рис. 7.2. К примеру 10.1
- •Рис. 11.4. К примеру 11.1
- •Рис. 11.9. К расчету шпилек
- •Рис. 11.10. К примеру 11.3
- •Рис. 11.11. К примеру 11.5
- •Рис. 13.10. Рамные мешалки
- •Рис. 13.11. Якорные мешалки
- •Предисловие
- •Экологическое и технико-экономическое обоснование проектов химических производств.
- •Этапы проведения экологической экспертизы
- •Принципы экологической экспертизы
- •Рис. 1.1. Общая система организации проектирования
- •Рис. 1.2. Основные этапы и стадии разработки проектов для промышленного строительства
- •1.2. Задание на проектирование
- •Рис. 1.3. Пример построения розы повторяемости и силы ветров
- •Рис.1.4. Схема выпадения дымовых частиц при наличии зеленых защитных насаждений между застройкой и источником задымления и при отсутствии их:
- •Рис. 1.5. Совмещенная схема движения загрязненных нижнего и верхнего потоков
- •1.5. Разработка проектной документации по охране окружающей среды
- •1.5.2. Разработка прогноза загрязнения воздуха
- •1.5.4. Прогноз воздействия объекта при возможных авариях
- •1.6. Технологический процесс как основа промышленного проектирования
- •Рис. 1.6. Схема производства серной кислоты контактным способом:
- •Рис. 1.8. Процессы и аппараты химической технологии
- •Рис. 1.9. Виды оборудования химической технологии
- •Рис. 1.11. Уровни организации химического предприятия
- •1.7. Генеральный план химических предприятий
- •Рис. 1.12. Генеральный план предприятий химической промышленности
- •1.8. Типы промышленных зданий
- •1.8.1. Одноэтажные промышленные здания
- •Рис. 1.13. Одноэтажное здание павильонного типа:
- •Рис. 1.14. Многоэтажное производственное здание:
- •1.8.2. Многоэтажные здания
- •Рис. 1.15. Многоэтажное производственное здание:
- •Рис. 1.16. Поперечные разрезы зданий I и II очередей сернокислотного производства:
- •1.8.3. Вспомогательные здания и помещения химических предприятий
- •1.8.4. Склады промышленных предприятий
- •1.9. Инженерные сооружения
- •инженерных сооружений
- •1.10. Специальные вопросы проектирования химических предприятий
- •2.1. Основные стадии проектирования химических производств и оборудования
- •Рис. 2.1. Основные стадии проектирования
- •2.2. Виды конструкторских документов
- •2.4.1. Курсовое проектирование
- •2.4.2. Дипломное проектирование
- •2.4.3. Пример использования АвтоЛиспа
- •Рис. 2.2. Схема установки для ректификации трехкомпонентной смеси:
- •СИСТЕМЫ АВТОМАТИЗИРОВАННОГО ПРОЕКТИРОВАНИЯ
- •3.1. История развития САПР
- •3.2. Основные принципы создания САПР
- •Рис. 3.1. Модульная структура программного обеспечения
- •Рис. 3.2. Области использования ЭВМ в процессе проектирования
- •3.4. Автоматическое изготовление чертежей
- •3.5. Основные преимущества автоматизации проектирования
- •3.6. Основные требования к САПР
- •Рис. 3.3. Схема взаимодействия пользователя со средствами САПР:
- •3.7. Связь САПР с производством, расширение области применения
- •3.8. Система автоматизированного проектирования цементных заводов
- •3.8.1. Функционирование САПР
- •ВВЕДЕНИЕ В ПРОЕКТИРОВАНИЕ
- •4.1. Проектно-сметная документация
- •4.2.1. Исходные положения
- •4.2.2. Обоснование способа производства химической продукции
- •ВЫБОР И РАЗРАБОТКА ТЕХНОЛОГИЧЕСКОЙ СХЕМЫ ПРОИЗВОДСТВА
- •5.1. Общие положения
- •5.2. Последовательность разработки технологической схемы
- •Рис. 5.1. Примерная схема стадий технологического процесса:
- •Рис. 5.2. Блок-схема физико-химических процессов, протекающих в гетерофазном реакторе с мешалкой
- •5.3. Принципиальная технологическая схема
- •5.4. Размещение технологического оборудования
- •Выбор технологического оборудования химических производств
- •6.1. Основные типы химических реакторов
- •Рис. 6.1. Установка для непрерывного процесса:
- •Рис. 6.5. Изменение концентрации веществ в реакторах:
- •Рис. 6.6. Реакторы смешения:
- •6.2. Химические факторы, влияющие на выбор реактора
- •6.2.1. Реакции расщепления
- •Рис. 6.7. Относительный выход реакции расщепления:
- •Реактор
- •6.2.2. Реакции полимеризации
- •6.2.3. Параллельные реакции
- •Объем реактора
- •РВНД
- •6.3. Эскизная конструктивная разработка основной химической аппаратуры
- •6.3.1. Общие положения
- •6.3.2. Реакторы
- •6.4. Оптимизация процессов химической технологии
- •УРАВНЕНИЯ МАТЕРИАЛЬНОГО БАЛАНСА ТЕХНОЛОГИЧЕСКОГО ПРОЦЕССА
- •7.1. Стехиометрические расчеты
- •7.2. Термодинамический анализ процессов
- •7.2.1. Равновесие химической реакции
- •Рис. 1.1. Зависимость коэффициента активности газв от приведенных давления и температуры
- •7.2.2. Расчет состава равновесной смеси
- •7.3. Общее уравнение баланса массы
- •7.4. Практический материальный баланс
- •7.5. Физико-химические основы технологического процесса
- •8.1. Общие положения
- •8.2. Расчет объемов реакторов
- •8.2.1. Основные положения химической кинетики
- •8.2.2. Расчет идеальных реакторов
- •8.3. Определение объемов аппарата
- •Тепловой расчет основного оборудования
- •9.1. Общее уравнение баланса энергии
- •Рис. 9.1. К примеру 9.1
- •9.2. Практический тепловой баланс
- •9.3. Теплообмен в реакторах
- •9.4. Расчет энтальпий и теплоемкостей
- •9.6. Расчет реактора периодического действия
- •Рис. 9.3. К тепловому расчету реактора периодического действия
- •9.7. Степень термодинамического совершенства технологических процессов
- •Рис. 9.6. Технологическая схема 1:
- •Рис. 9.7. Технологическая схема 2
- •Рис. 9.8. Схемы использования тепла реакций:
- •Гидравлические расчеты
- •10.1. Расчет диаметра трубопровода
- •Пары, насыщенные при абсолютном давлении (МПа)
- •Рис. 10.1. Зависимость коэффициента трения от критерия Рейнольдса и степени шероховатости трубы
- •10.3. Гидравлическое сопротивление кожухотрубчатых теплообменников
- •10.4. Подбор насосов
- •МЕХАНИЧЕСКИЙ РАСЧЕТ
- •11.1. Расчет сварных химических аппаратов
- •11.1.1. Основные расчетные параметры
- •11.1.2. Расчет на механическую прочность
- •11.1.3. Требования к конструированию
- •11.1.4. Расчет цилиндрических обечаек
- •Рис. 11.1. Номограмма для определения толщины цилиндрических обечаек, работающих под наружным давлением
- •Рис.11.2. Схема пользования номограммой на рис. 11.1:
- •11.1.5. Расчет крышек и днищ
- •Рис. 11.3. Основные конструкции днищ сварных аппаратов:
- •11.1.6. Подбор стандартных элементов
- •11.2. Расчет толстостенных аппаратов
- •Рис. 11.7. Основные конструкции уплотнений затворов высокого давления:
- •Рис. 11.8. К расчету усилий, действующих на затворы высокого давления
- •КОНСТРУКционНЫЕ МАТЕРИАЛЫ В ХИМИЧЕСКОМ МАШИНОСТРОЕНИИ
- •12.1. Виды конструкционных материалов
- •12.2. Коррозия металлов и сплавов
- •12.2.1. Виды коррозии
- •12.2.2. Виды коррозионных разрушений
- •12.2.3. Способы борьбы с коррозией
- •12.3. Влияние материала на конструкцию аппарата и способ его изготовления
- •12.3.1. Конструкционные особенности аппаратов из высоколегированных сталей
- •Рис. 12.1. Сварка встык:
- •Рис. 12.2. Способы подготовки кромок под сварку
- •Рис. 12.4. Способы сварки легированной и углеродистой стали
- •12.3.2. Конструктивные особенности эмалированных аппаратов
- •Рис. 12.5. Элементы конструкции эмалированных аппаратов
- •Рис 12.6. Пайка элементов медных аппаратов
- •12.3.3. Конструктивные особенности аппаратов из цветных металлов
- •Рис. 12.7. Основные типы паяных соединений
- •12.3.4. Конструктивные особенности аппаратов из пластмасс
- •ОФОРМЛЕНИЕ ОТДЕЛЬНЫХ ЭЛЕМЕНТОВ ХИМИЧЕСКОЙ АППАРАТУРЫ
- •13.1. Оформление поверхности теплообмена
- •Рис. 13.5. Реактор со змеевиковой рубашкой
- •Рис. 13.6. Рубашка с вмятинами
- •Рис. 13.8. Вывод змеевика через крышку аппарата:
- •13.2. Перемешивающие устройства
- •Рис. 13.12. Листовая мешалка
- •Рис. 13.13. Пропеллерные мешалки
- •Рис. 13.14. Турбинные мешалки открытого (а) и (б) закрытого типа
- •Рис. 13.15. Крепление мешалок к ступице:
- •13.3. Уплотнения вращающихся деталей
- •Рис. 13.18. Одинарное торцовое уплотнение:
- •ТРУБОПРОВОДЫ И ТРУБОПРОВОДНАЯ АРМАТУРА
- •Рис 14.5. Фасонные части трубопроводов
- •Рис. 14.7. Крепление горизонтальных и вертикальных трубопроводов на подвесках
- •Рис. 14.8. Компенсаторы:
- •ВСПОМОГАТЕЛЬНОЕ ОБОРУДОВАНИЕ ХИМИЧЕСКИХ ЗАВОДОВ
- •15.1. Виды вспомогательного оборудования
- •Рис. 15.1. Схема многостадийного диспергирования твердой фазы с контрольной классификацией продукта
- •15.2. Транспортные средства
- •15.2.1. Классификация транспортных средств для твердых материалов
- •15.2.2. Машины для транспортировки жидкостей и газов
- •ТЕХНОЛОГИЧЕСКИЕ СХЕМЫ И ОБОРУДОВАНИЕ ДЛЯ ГРАНУЛИРОВАНИЯ ДИСПЕРСНЫХ МАТЕРИАЛОВ
- •16.1. Классификация методов гранулирования и особенности уплотнения гранул
- •Рис. 16.1. Тарельчатый гранулятор:
- •Рис. 16.2. Гранулятор барабанного типа конструкции НИИХиммаша
- •16.3. Основные закономерности и аппаратурное оформление метода экструзии
- •16.5. Гранулирование в псевдоожиженном слое
- •16.6. Технологические схемы процессов гранулирования дисперсных материалов
- •Рис. 16.11. Технологическая схема гранулирования шихты методом окатывания
- •Рис. 16.13. Схема уплотнения шихты в роторном грануляторе
- •Рис. 16.14. Схема гранулирования шихты методом экструзии
- •Рис. 16.15. Схема установки для компактирования шихты
- •ЛИТЕРАТУРА
Г л а в а 11
__________________________________________________________________
МЕХАНИЧЕСКИЙ РАСЧЕТ
__________________________________________________________________
Целью механического расчета химического и нефтехимического оборудования является определение размеров отдельных элементов, обеспечивающих безопасную эксплуатацию машин и аппаратов за счет достаточной механической прочности, плотности разъемных соединений, устойчивости к сохранению формы и необходимой долговечности.
При выполнении дипломного проекта механический расчет производится только для основного оборудования проектируемого цеха или участка. При этом следует с максимальной возможностью использовать стандартизованные или нормализованные размеры отдельных элементов оборудования.
Все сосуды и аппараты, работающие под давлением, должны проектироваться, изготовляться и эксплуатироваться в соответствии с правилами устройства и безопасной эксплуатации сосудов, работающих под давлением Госгортехнадзора. Эти правила распространяются на:
а) сосуды, работающие под давлением свыше 0,07 МПа (без учета гидростатического давления);
б) цистерны и бочки для перевозки сжиженных газов, давление паров которых при температуре до 50 °С превышает 0,07 МПа;
в) сосуды, цистерны для хранения, перевозки сжиженных газов, жидкостей и сыпучих тел без давления, но опорожняемые под давлением газа свыше 0,07 МПа;
г) баллоны, предназначенные для перевозки и хранения сжатых, сжиженных и растворенных газов под давлением свыше 0,07 МПа.
Эти правила не распространяются на:
а) приборы парового и водяного отопления; б) сосуды и баллоны емкостью не свыше 25 л, у которых произведение
емкости в литрах на рабочее давление в мегапаскалях составляет не более 20; в) сосуды из неметаллических материалов; г) трубчатые печи независимо от диаметра труб и т. д.
11.1. РАСЧЕТ СВАРНЫХ ХИМИЧЕСКИХ АППАРАТОВ
Специфические условия работы химического оборудования, характеризуемые широким диапазоном давлений (от вакуума до давлений 250 МПа и
244
выше), большим интервалом температур (от –250 до +1000°С и выше) при агрессивном воздействии среды, предъявляют высокие требования к выбору конструкционных материалов. Так, наряду с требованиями высокой коррозионной стойкости в заданных агрессивных средах, к конструкционным материалам одновременно предъявляют требования высокой механической прочности, жаростойкости и жаропрочности, сохранения пластических свойств при высоких и низких температурах, циклической прочности, малой склонности к старению и др.
11.1.1. Основные расчетные параметры
Основными расчетными параметрами для выбора конструкционного материала и расчета элементов аппарата на прочность являются температура и давление рабочего процесса.
Температура. Различают рабочую и расчетную температуру.
Рабочая температура t – это температура содержащейся или перерабатываемой среды в аппарате при нормальном протекании в нем технологического процесса.
Расчетная температура tR – это температура для определения физикомеханических характеристик конструкционного материала и допускаемых напряжений. Расчетная температура определяется на основании тепловых расчетов или результатов испытаний. При положительных температурах за расчетную температуру стенки аппарата принимают наибольшее значение температуры стенки. При отрицательной температуре стенки элемента сосуда или аппарата за расчетную температуру при определении допускаемых напряжений следует принимать температуру 20 °С.
При невозможности произвести тепловые расчеты или измерения и в тех случаях, когда во время эксплуатации температура стенки повышается до температуры среды, соприкасающейся со стенкой, за расчетную температуру следует принимать наибольшую температуру среды, но не ниже 20 °С.
Давление. Различают рабочее, расчетное, условное (номинальное) и пробное давления.
Рабочее давление p – максимальное внутреннее избыточное или наружное давление среды в аппарате при нормальном протекании технологического процесса без учета гидростатического давления среды и без учета допустимого кратковременного повышения давления во время действия предохранительного устройства (клапана и др.).
Расчетное давление pR – максимальное допускаемое рабочее давление, на которое производится расчет на прочность и устойчивость элементов аппарата при максимальной их температуре. Расчетное давление принимают, как правило, равным рабочему давлению или выше.
Расчетное давление может быть выше рабочего в следующих случаях:
245
−если во время действия предохранительных устройств давление в аппарате может повыситься более чем на 10 % от рабочего, то расчетное давление должно быть равно 90 % от давления в аппарате при полном открытии предохранительного устройства;
−если на элемент действует гидростатическое давление от столба жидкости в аппарате, значение которого свыше 5 % от расчетного, то расчетное давление этого элемента соответственно повышается на значение гидростатического давления.
Для элементов аппарата с раздельными пространствами, имеющими разные давления, за расчетное давление принимается каждое из них (без учета других). Допускается производить расчет на разность давлений, если при эксплуатации в любом случае надежно обеспечивается наличие давлений во всех пространствах.
Пробное давление – избыточное давление, на которое аппарат испыты-
вается на прочность и плотность после его изготовления и периодически при эксплуатации.
Гидравлическое испытание сосудов, за исключением литых, должно проводиться пробным давлением, определяемым по формуле
p |
= 1,25p |
[σ ]20 |
, |
|
|||
ï ð |
|
[σ ]t |
|
|
|
где p − расчетное давление сосуда, МПа;
[σ]20, [σ]t − допускаемые напряжения для материала сосуда или его элементов соответственно при 20 °С и расчетной температуре.
Отношение [σ]20/[σ]t принимается по тому из использованных материалов элементов (обечаек, днищ, фланцев, крепежа, патрубков и др.) сосуда, для которого оно является наименьшим.
Гидравлическое испытание деталей, изготовленных из литья, должно проводиться пробным давлением, определяемым по формуле
p |
= 1,5 p |
[σ ]20 |
. |
|
|||
ï ð |
|
[σ ]t |
|
|
|
Испытание отливок разрешается проводить после сборки и сварки в собранном узле или готовом сосуде пробным давлением, принятым для сосудов, при условии 100 % контроля отливок неразрушающими методами.
Гидравлическое испытание сосудов и деталей, изготовленных из неметаллических материалов с ударной вязкостью более 20 Дж/см2 (2 кгс × м/см), должно проводиться пробным давлением, определяемым по формуле
p |
= 1,3p |
[σ ]20 |
. |
|
|||
ï ð |
|
[σ ]t |
|
|
|
Гидравлическое испытание сосудов и деталей, изготовленных из неметаллических материалов с ударной вязкостью 20 и менее Дж/см2, должно проводиться пробным давлением, определяемым по формуле
246
p |
= 1,6 p |
[σ ]20 |
. |
|
|||
ï ð |
|
[σ ]t |
|
|
|
Гидравлическое испытание криогенных сосудов при наличии вакуума в изоляционном пространстве должно проводиться пробным давлением, определяемым по формуле
pпр=1,25p−0,1.
Расчетным давлением при гидравлическом или пневматическом испытании аппарата является пробное давление.
Условное (номинальное) давление pу – избыточное рабочее давление при температуре элемента 20 °С (без учета гидростатического давления). Для более высоких температур элементов аппарата условное давление снижается соответственно уменьшению прочности конструкционного материала.
Условные давления применяются при стандартизации аппаратов и их отдельных элементов. Согласно ГОСТ 356−68 применительно к рассматриваемым аппаратам рекомендуется следующий ряд условных давлений, МПа:
0,1; 0,25; 0,4; 0,6; 1,0; 1,6; 2,5; 4,0; 6,4; 10; 16; 20.
11.1.2. Расчет на механическую прочность
Расчет на механическую прочность от внутреннего избыточного или наружного давления и внешних нагрузок (силы тяжести, ветровых, сейсмических и др.) производится для всех основных элементов аппарата (обечаек, крышек, днищ, трубных решеток теплообменников, тарелок колонн, фланцевых соединений и их крепежных деталей, перемешивающих устройств, опор и т. д.). Стандартные элементы при применении их в конструируемом аппарате выбираются на ближайшее большее условное давление для рабочей температуры и на прочность, как правило, не рассчитываются.
Допускаемые напряжения для конструкционных материалов из сталей для рабочих условий принимаются:
− для углеродистых сталей при расчетной температуре ≤380 °С и низколегированных сталей при расчетной температуре ≤420 °С равны меньшему из значений:
[σ ] = |
η σ Â ; [σ ] = |
η σ Ò ; |
|
n |
n |
|
 |
T |
− для высоколегированной (аустенитной) стали при расчетной температуре ≤525 °С – меньшему из равенств:
[σ ] = |
η σ T ; [σ ] = |
η σ B |
|
n |
n |
|
T |
B |
или
247
[σ ] = |
η σ B ; |
[σ ] = |
η σ 0,2 |
. |
|
||||
|
nB |
|
nT |
При больших значениях расчетных температур допускаемые напряжения для любой стали принимаются равными наименьшему значению из равенств:
[σ ] = |
η σ B ; [σ ] = |
η σ T ; [σ ] = |
η σ D |
; |
[σ ] = |
η σ 1% . |
|
n |
n |
n |
|
|
n |
|
B |
T |
D |
|
|
ï |
В этих выражениях:
[σ] – допускаемое напряжение; σТ – предел текучести;
σB – предел прочности (временный предел прочности); σ0,2 – условный предел текучести;
σD – предел длительной прочности;
σ1% - предел ползучести;
nT, nB, nD, nп– соответствующие коэффициенты запаса прочности;
η- поправочный множитель.
Кдопускаемым напряжениям для деталей вводится поправочный мно-
житель η:
−для деталей из стальных отливок при индивидуальном контроле неразрушающими методами, равный 0,8;
−для остальных стальных отливок– 0,7;
−для прочих деталей, как правило, 1.
Коэффициенты запаса прочности принимаются по табл. 11.1. Коэффициент запаса устойчивости при расчете элементов аппарата на
устойчивость по нижним критическим напряжениям принимается: для рабочих условий – nу = 2,4; для условий испытания и монтажа – nу = 1,8.
Таблица 11.1. Коэффициенты запаса прочности |
|
|
|||
Условия нагружения |
|
Коэффициенты запаса прочности |
|
||
nТ |
nB* |
nD |
nп |
||
|
|||||
Рабочие условия |
1,5 |
2,4 |
1,5 |
1,0 |
|
Условия испытания |
|
|
|
|
|
гидравлические |
1,1 |
− |
− |
− |
|
пневматические |
1,2 |
− |
− |
− |
|
Усовия монтажа |
1,1 |
− |
− |
− |
При расчете на прочность и устойчивость сварных элементов аппаратов в расчетные формулы вводятся коэффициенты прочности сварных швов, значения которых в зависимости от конструкции шва и условий сварки принимаются по табл. 11.2.
248
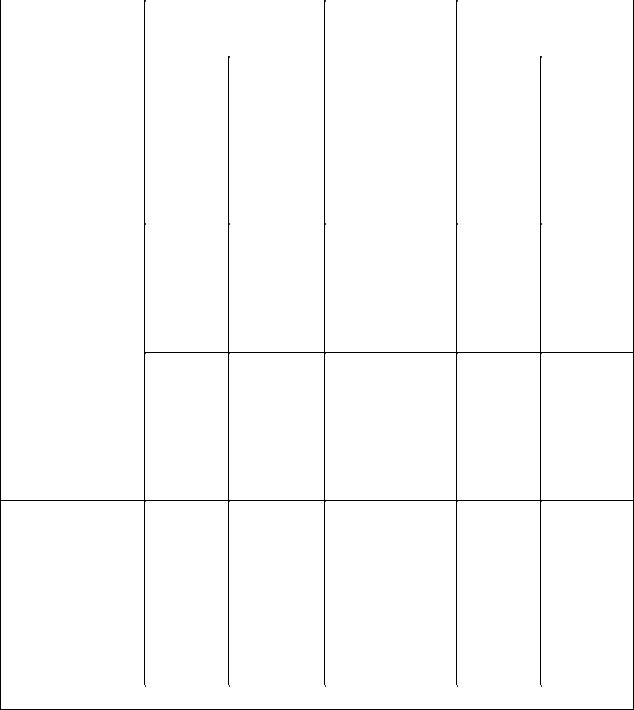
Таблица 11.2. Коэффициенты прочности сварных швов для стальных сосудов и аппаратов по ГОСТ Р 52857.1−2007
|
Коэффициент прочности |
|
Коэффициент прочности |
|
|||
|
сварных швов для сталь- |
|
сварных швов для сталь- |
|
|||
|
ных сосудов и аппаратов |
|
ных сосудов и аппаратов |
|
|||
Вид сварного шва и |
Длина |
Длина контро- |
Вид сварного шва и |
Длина |
Длина контро- |
||
способ сварки |
лируемых |
способ сварки |
контроли- |
||||
контролиру- |
швов состав- |
руемых |
лируемых |
||||
|
|
||||||
|
емых швов |
ляет от 10 до |
|
швов со- |
швов 10 до |
||
|
100 %* |
|
|
ставляет |
50 %* |
|
|
|
|
50 %* |
|
100 %* |
|
|
|
|
|
|
|
|
|
|
|
Стыковой или тавро- |
|
|
|
|
|
|
|
вый с двусто- |
|
|
В тавр, с конструк- |
|
|
|
|
ронним сплошным |
|
|
|
|
|
||
|
|
тивным зазором |
|
|
|
||
проваром, выпол- |
1,0 |
0,9 |
0,8 |
0,65 |
|
||
свариваемых дета- |
|
||||||
няемый автомати- |
|
|
|
|
|
||
|
|
лей |
|
|
|
||
ческой и полуавто- |
|
|
|
|
|
||
|
|
|
|
|
|
||
матической сваркой |
|
|
|
|
|
|
|
|
|
|
Стыковой, выпол- |
|
|
|
|
Стыковой с подвар- |
|
|
няемый автомати- |
|
|
|
|
кой корня шва или |
|
|
ческой и полуав- |
|
|
|
|
тавровый с двусто- |
1,0 |
0,9 |
томатической |
0,9 |
0,8 |
|
|
ронним сплошным |
сваркой с одной |
|
|||||
|
|
|
|
|
|||
проваром, выпол- |
|
|
стороны с флюсо- |
|
|
|
|
няемый вручную |
|
|
вой или керамиче- |
|
|
|
|
|
|
|
ской подкладкой |
|
|
|
|
Стыковой, доступ- |
|
|
|
|
|
|
|
ный сварке только с |
|
|
|
|
|
|
|
одной стороны и |
|
|
|
|
|
|
|
имеющий в процес- |
|
|
Стыковой, выпол- |
|
|
|
|
се сварки металли- |
|
|
|
|
|
||
0,9 |
0,8 |
няемый вручную |
0,9 |
0,65 |
|
||
ческую подкладку |
|
||||||
|
|
с одной стороны |
|
|
|
||
со стороны корня |
|
|
|
|
|
||
|
|
|
|
|
|
||
шва, прилегающую |
|
|
|
|
|
|
|
по всей длине шва к |
|
|
|
|
|
|
|
основному металлу |
|
|
|
|
|
|
|
* Объем контроля |
определяется техническими |
требованиями на |
изготовление. |
|
|||
|
|
|
|
|
|
|
Исполнительные или принимаемые при конструировании размеры рассчитываемых элементов, как правило, должны быть больше расчетных на значение конструктивной прибавки, т. е.
s³sR + c. Общее значение конструктивной прибавки
c = c1 + c2 + c3,
249