
- •Рис. 9.2. К расчету теплообмена в реакторе вытеснения
- •Рис. 7.2. К примеру 10.1
- •Рис. 11.4. К примеру 11.1
- •Рис. 11.9. К расчету шпилек
- •Рис. 11.10. К примеру 11.3
- •Рис. 11.11. К примеру 11.5
- •Рис. 13.10. Рамные мешалки
- •Рис. 13.11. Якорные мешалки
- •Предисловие
- •Экологическое и технико-экономическое обоснование проектов химических производств.
- •Этапы проведения экологической экспертизы
- •Принципы экологической экспертизы
- •Рис. 1.1. Общая система организации проектирования
- •Рис. 1.2. Основные этапы и стадии разработки проектов для промышленного строительства
- •1.2. Задание на проектирование
- •Рис. 1.3. Пример построения розы повторяемости и силы ветров
- •Рис.1.4. Схема выпадения дымовых частиц при наличии зеленых защитных насаждений между застройкой и источником задымления и при отсутствии их:
- •Рис. 1.5. Совмещенная схема движения загрязненных нижнего и верхнего потоков
- •1.5. Разработка проектной документации по охране окружающей среды
- •1.5.2. Разработка прогноза загрязнения воздуха
- •1.5.4. Прогноз воздействия объекта при возможных авариях
- •1.6. Технологический процесс как основа промышленного проектирования
- •Рис. 1.6. Схема производства серной кислоты контактным способом:
- •Рис. 1.8. Процессы и аппараты химической технологии
- •Рис. 1.9. Виды оборудования химической технологии
- •Рис. 1.11. Уровни организации химического предприятия
- •1.7. Генеральный план химических предприятий
- •Рис. 1.12. Генеральный план предприятий химической промышленности
- •1.8. Типы промышленных зданий
- •1.8.1. Одноэтажные промышленные здания
- •Рис. 1.13. Одноэтажное здание павильонного типа:
- •Рис. 1.14. Многоэтажное производственное здание:
- •1.8.2. Многоэтажные здания
- •Рис. 1.15. Многоэтажное производственное здание:
- •Рис. 1.16. Поперечные разрезы зданий I и II очередей сернокислотного производства:
- •1.8.3. Вспомогательные здания и помещения химических предприятий
- •1.8.4. Склады промышленных предприятий
- •1.9. Инженерные сооружения
- •инженерных сооружений
- •1.10. Специальные вопросы проектирования химических предприятий
- •2.1. Основные стадии проектирования химических производств и оборудования
- •Рис. 2.1. Основные стадии проектирования
- •2.2. Виды конструкторских документов
- •2.4.1. Курсовое проектирование
- •2.4.2. Дипломное проектирование
- •2.4.3. Пример использования АвтоЛиспа
- •Рис. 2.2. Схема установки для ректификации трехкомпонентной смеси:
- •СИСТЕМЫ АВТОМАТИЗИРОВАННОГО ПРОЕКТИРОВАНИЯ
- •3.1. История развития САПР
- •3.2. Основные принципы создания САПР
- •Рис. 3.1. Модульная структура программного обеспечения
- •Рис. 3.2. Области использования ЭВМ в процессе проектирования
- •3.4. Автоматическое изготовление чертежей
- •3.5. Основные преимущества автоматизации проектирования
- •3.6. Основные требования к САПР
- •Рис. 3.3. Схема взаимодействия пользователя со средствами САПР:
- •3.7. Связь САПР с производством, расширение области применения
- •3.8. Система автоматизированного проектирования цементных заводов
- •3.8.1. Функционирование САПР
- •ВВЕДЕНИЕ В ПРОЕКТИРОВАНИЕ
- •4.1. Проектно-сметная документация
- •4.2.1. Исходные положения
- •4.2.2. Обоснование способа производства химической продукции
- •ВЫБОР И РАЗРАБОТКА ТЕХНОЛОГИЧЕСКОЙ СХЕМЫ ПРОИЗВОДСТВА
- •5.1. Общие положения
- •5.2. Последовательность разработки технологической схемы
- •Рис. 5.1. Примерная схема стадий технологического процесса:
- •Рис. 5.2. Блок-схема физико-химических процессов, протекающих в гетерофазном реакторе с мешалкой
- •5.3. Принципиальная технологическая схема
- •5.4. Размещение технологического оборудования
- •Выбор технологического оборудования химических производств
- •6.1. Основные типы химических реакторов
- •Рис. 6.1. Установка для непрерывного процесса:
- •Рис. 6.5. Изменение концентрации веществ в реакторах:
- •Рис. 6.6. Реакторы смешения:
- •6.2. Химические факторы, влияющие на выбор реактора
- •6.2.1. Реакции расщепления
- •Рис. 6.7. Относительный выход реакции расщепления:
- •Реактор
- •6.2.2. Реакции полимеризации
- •6.2.3. Параллельные реакции
- •Объем реактора
- •РВНД
- •6.3. Эскизная конструктивная разработка основной химической аппаратуры
- •6.3.1. Общие положения
- •6.3.2. Реакторы
- •6.4. Оптимизация процессов химической технологии
- •УРАВНЕНИЯ МАТЕРИАЛЬНОГО БАЛАНСА ТЕХНОЛОГИЧЕСКОГО ПРОЦЕССА
- •7.1. Стехиометрические расчеты
- •7.2. Термодинамический анализ процессов
- •7.2.1. Равновесие химической реакции
- •Рис. 1.1. Зависимость коэффициента активности газв от приведенных давления и температуры
- •7.2.2. Расчет состава равновесной смеси
- •7.3. Общее уравнение баланса массы
- •7.4. Практический материальный баланс
- •7.5. Физико-химические основы технологического процесса
- •8.1. Общие положения
- •8.2. Расчет объемов реакторов
- •8.2.1. Основные положения химической кинетики
- •8.2.2. Расчет идеальных реакторов
- •8.3. Определение объемов аппарата
- •Тепловой расчет основного оборудования
- •9.1. Общее уравнение баланса энергии
- •Рис. 9.1. К примеру 9.1
- •9.2. Практический тепловой баланс
- •9.3. Теплообмен в реакторах
- •9.4. Расчет энтальпий и теплоемкостей
- •9.6. Расчет реактора периодического действия
- •Рис. 9.3. К тепловому расчету реактора периодического действия
- •9.7. Степень термодинамического совершенства технологических процессов
- •Рис. 9.6. Технологическая схема 1:
- •Рис. 9.7. Технологическая схема 2
- •Рис. 9.8. Схемы использования тепла реакций:
- •Гидравлические расчеты
- •10.1. Расчет диаметра трубопровода
- •Пары, насыщенные при абсолютном давлении (МПа)
- •Рис. 10.1. Зависимость коэффициента трения от критерия Рейнольдса и степени шероховатости трубы
- •10.3. Гидравлическое сопротивление кожухотрубчатых теплообменников
- •10.4. Подбор насосов
- •МЕХАНИЧЕСКИЙ РАСЧЕТ
- •11.1. Расчет сварных химических аппаратов
- •11.1.1. Основные расчетные параметры
- •11.1.2. Расчет на механическую прочность
- •11.1.3. Требования к конструированию
- •11.1.4. Расчет цилиндрических обечаек
- •Рис. 11.1. Номограмма для определения толщины цилиндрических обечаек, работающих под наружным давлением
- •Рис.11.2. Схема пользования номограммой на рис. 11.1:
- •11.1.5. Расчет крышек и днищ
- •Рис. 11.3. Основные конструкции днищ сварных аппаратов:
- •11.1.6. Подбор стандартных элементов
- •11.2. Расчет толстостенных аппаратов
- •Рис. 11.7. Основные конструкции уплотнений затворов высокого давления:
- •Рис. 11.8. К расчету усилий, действующих на затворы высокого давления
- •КОНСТРУКционНЫЕ МАТЕРИАЛЫ В ХИМИЧЕСКОМ МАШИНОСТРОЕНИИ
- •12.1. Виды конструкционных материалов
- •12.2. Коррозия металлов и сплавов
- •12.2.1. Виды коррозии
- •12.2.2. Виды коррозионных разрушений
- •12.2.3. Способы борьбы с коррозией
- •12.3. Влияние материала на конструкцию аппарата и способ его изготовления
- •12.3.1. Конструкционные особенности аппаратов из высоколегированных сталей
- •Рис. 12.1. Сварка встык:
- •Рис. 12.2. Способы подготовки кромок под сварку
- •Рис. 12.4. Способы сварки легированной и углеродистой стали
- •12.3.2. Конструктивные особенности эмалированных аппаратов
- •Рис. 12.5. Элементы конструкции эмалированных аппаратов
- •Рис 12.6. Пайка элементов медных аппаратов
- •12.3.3. Конструктивные особенности аппаратов из цветных металлов
- •Рис. 12.7. Основные типы паяных соединений
- •12.3.4. Конструктивные особенности аппаратов из пластмасс
- •ОФОРМЛЕНИЕ ОТДЕЛЬНЫХ ЭЛЕМЕНТОВ ХИМИЧЕСКОЙ АППАРАТУРЫ
- •13.1. Оформление поверхности теплообмена
- •Рис. 13.5. Реактор со змеевиковой рубашкой
- •Рис. 13.6. Рубашка с вмятинами
- •Рис. 13.8. Вывод змеевика через крышку аппарата:
- •13.2. Перемешивающие устройства
- •Рис. 13.12. Листовая мешалка
- •Рис. 13.13. Пропеллерные мешалки
- •Рис. 13.14. Турбинные мешалки открытого (а) и (б) закрытого типа
- •Рис. 13.15. Крепление мешалок к ступице:
- •13.3. Уплотнения вращающихся деталей
- •Рис. 13.18. Одинарное торцовое уплотнение:
- •ТРУБОПРОВОДЫ И ТРУБОПРОВОДНАЯ АРМАТУРА
- •Рис 14.5. Фасонные части трубопроводов
- •Рис. 14.7. Крепление горизонтальных и вертикальных трубопроводов на подвесках
- •Рис. 14.8. Компенсаторы:
- •ВСПОМОГАТЕЛЬНОЕ ОБОРУДОВАНИЕ ХИМИЧЕСКИХ ЗАВОДОВ
- •15.1. Виды вспомогательного оборудования
- •Рис. 15.1. Схема многостадийного диспергирования твердой фазы с контрольной классификацией продукта
- •15.2. Транспортные средства
- •15.2.1. Классификация транспортных средств для твердых материалов
- •15.2.2. Машины для транспортировки жидкостей и газов
- •ТЕХНОЛОГИЧЕСКИЕ СХЕМЫ И ОБОРУДОВАНИЕ ДЛЯ ГРАНУЛИРОВАНИЯ ДИСПЕРСНЫХ МАТЕРИАЛОВ
- •16.1. Классификация методов гранулирования и особенности уплотнения гранул
- •Рис. 16.1. Тарельчатый гранулятор:
- •Рис. 16.2. Гранулятор барабанного типа конструкции НИИХиммаша
- •16.3. Основные закономерности и аппаратурное оформление метода экструзии
- •16.5. Гранулирование в псевдоожиженном слое
- •16.6. Технологические схемы процессов гранулирования дисперсных материалов
- •Рис. 16.11. Технологическая схема гранулирования шихты методом окатывания
- •Рис. 16.13. Схема уплотнения шихты в роторном грануляторе
- •Рис. 16.14. Схема гранулирования шихты методом экструзии
- •Рис. 16.15. Схема установки для компактирования шихты
- •ЛИТЕРАТУРА
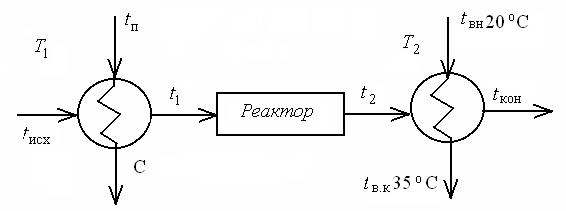
T = tèñõ + t1 |
+ 273 = |
30 + 195 + 273 = 386 К. |
|
c |
2 |
|
2 |
|
|
Рис. 9.6. Технологическая схема 1: T1 и Т2 – теплообменники
Температура греющего пара не меняется, так как идет процесс конденсации пара
Тп=tп+273=200+273=473K;
DT1T = 298Ч1Ч473 −Ч 386 = − 0,142 МДж. 473 386
В теплообменнике Т2
|
|
|
|
|
|
TT2 |
− TT2 |
||||
|
DT2T = T0 |
ЧQT2 Ч |
ï ð |
|
â |
, |
|||||
|
T |
|
T |
||||||||
|
|
|
|
|
|
Tï ð2 |
|
ЧTâ |
2 |
|
|
где |
QT2 = Q |
|
= |
0,939 МДж. |
|
|
|||||
|
î õë |
|
|
|
|
|
|
|
|||
Средняя температура продуктов реакции равна |
|
|
|||||||||
ΤñðΤ2 = |
t2 + têî í |
|
+ 273 = 185 + 30 + |
273 = 380К, |
|||||||
2 |
|||||||||||
|
|
|
|
2 |
|
|
|
|
|||
а средняя температура воды |
20 + |
35 + 273 = 300 К; |
|||||||||
|
ΤâΤ2 = |
||||||||||
|
|
|
|
2 |
380 − 300 |
|
|
|
|||
|
|
|
|
|
|
|
|
||||
DT2T = 298Ч0,939 Ч 380 Ч300 |
|
= 0,196 МДж. |
|||||||||
Общие потери эксергии по первой схеме равняются: |
|||||||||||
е D1T = |
DT1T + DT2T = |
0,142 + 0,196 = 0,338 МДж. |
Потери эксергии, отнесенные к сумме теплот на нагревание и охлаждение продуктов реакции (Dе) сырья, равны
De = |
е |
D1T |
Ч100% = |
0,338 |
Ч100 = 17,4% . |
е |
|
1,939 |
|||
|
Q |
|
227
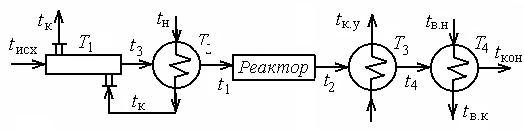
Второй вариант технологической схемы включает котел-утилизатор и возможность использования теплоты конденсата водяного пара для подогрева исходного сырья (рис. 9.7).
Для расчета потерь эксергии необходимо определить количество передаваемой в каждом теплообменнике теплоты и температуры t3 и t4.
Рис. 9.7. Технологическая схема 2
Как следует из условий, общее количество теплоты, передаваемой в теплообменниках Т1 и Т2, равно 1 МДж. Принимаем, что распределение теплоты по этим теплообменникам прямо пропорционально количеству теплоты, отдаваемой килограммом конденсирующегося пара при его охлаждении от (tn) до температуры конденсата на выходе из теплообменника
Т1−(tк), т. е. |
Q2 |
= |
3 |
|
1 . |
||
Q |
Считая, что теплоносители в теплообменнике Т1 движутся противотоком, примем tк на десять градусов выше, чем температура другого теплоносителя на входе (tисх).
Tк=tисх+10=30+10=40 °С.
Для 1 кг пара теплота конденсации, по справочным данным, составляет при 200 °С − 1938 кДж/кг; теплота охлаждения конденсата
Qê = 1ЧCH2O ( tí − tê ) = 4,19 Ч( 200 − 40) = 670 кДж/кг.
Отсюда, количество теплоты, передаваемое в каждом теплообменнике, составит:
втеплообменнике Т1 − QT1 = 670 кДж/кг;
втеплообменнике T2 − QT2 = 1938 кДж/кг. Определяем температуру t3 из уравнения:
|
QT1 |
|
|
°С. |
|
t3 = tèñõ + |
m Чc = 30 + 0,25Ч(185 − 30) = |
71 |
|||
|
Потери эксергии в теплообменнике Т1 определяем из уравнения:
DT1T = T0 ЧQT1 ЧTêT1 − TñT1 , TêT1 ЧTñT1
228
где |
TT1 |
= tí |
+ |
tê + 273 = 200 + |
40 + 273 = 393 К − |
усредненная температура |
|||||||||||
|
ê |
|
|
2 |
|
2 |
|
|
|
|
|
|
|
|
|
||
конденсата; |
|
|
|
|
|
|
|
|
|
|
|||||||
|
|
|
|
|
|
|
|
|
|
|
|
|
|||||
TT2 |
= |
tèñõ + t3 |
+ 273 = 30 + 71 + 273 = 323 К − усредненная температура сырья. |
||||||||||||||
|
|||||||||||||||||
ñ |
|
|
2 |
|
|
|
|
2 |
|
|
|
|
|
|
|
|
|
Отсюда следует, что |
|
|
393 − |
323 |
|
|
|
||||||||||
|
|
|
|
|
|
|
DT1T = 298Ч0,25Ч |
= 0,041 |
МДж. |
||||||||
|
|
|
|
|
|
|
393Ч323 |
||||||||||
|
|
Потери эксергии в теплообменнике Т2 |
|
|
|
||||||||||||
|
|
|
|
|
|
|
|
TΤ |
|
2 |
|
|
TΤ2 |
− TΤ2 |
|
|
|
|
|
|
|
|
|
|
|
|
2 |
|
|
ï |
c |
|
|
||
|
TT2 |
|
|
|
|
|
D |
T = T0 |
ЧQ |
|
Ч |
TïΤ2 ЧTcΤ2 |
, |
|
|||
где |
= t |
ï |
+ 273 = 200 + 273 = 473К; |
|
|
|
|
|
|
|
|||||||
|
ï |
|
|
|
|
= t3 + t1 |
+ 273 = 71+ 195 + 273 = 406 К. |
||||||||||
|
|
|
|
|
|
|
TΤ2 |
||||||||||
|
|
|
|
|
|
|
c |
2 |
|
|
|
|
2 |
|
|
|
|
Отсюда следует, что |
|
|
|
|
|
|
|
||||||||||
|
|
473 − |
406 |
|
|
|
|||||||||||
|
|
|
|
|
|
|
DT2T = 298Ч0,75Ч |
= 0,078 |
МДж. |
||||||||
|
|
|
|
|
|
|
473Ч406 |
Примем температуру t4 на 20 оС выше, чем температура воды в котле-у- тилизаторе, т. е. t4=tку+20=170 °С. Тогда количество теплоты, передаваемое в каждом теплообменнике Т3 и Т4, будет равно соответственно
QT3 |
= m Чc Ч( t2 − t4 ) |
= |
1 |
Ч(185 |
− 170) = 0,091МДж; |
||||||
|
195 − 30 |
||||||||||
QT4 |
= m Чc Ч( t4 − têî í |
) |
1 |
|
|
Ч(170 − 30) = 0,848 МДж. |
|||||
= |
|
|
|||||||||
195 − 30 |
|||||||||||
Проверяем общую сумму теплот: |
|
|
|||||||||
е Q = QT1 |
+ QT2 + QT3 + QT4 |
= 0,25 + 0,75 + 0,091+ 0,848 = 1,939 МДж. |
|||||||||
Потери эксергии в теплообменнике Т3 |
|
|
|||||||||
|
|
TΤ |
|
|
|
|
|
TΤ3 − TΤ3 |
|||
|
|
|
ï ð |
êó |
|
||||||
|
|
D 3T |
= T0 ЧQ 3 Ч |
|
, |
||||||
|
|
TïΤð3 ЧTêóΤ3 |
|||||||||
где |
|
t2 + t4 |
+ 273 = 185 + 170 = 450 К; |
||||||||
|
TT3 = |
||||||||||
|
|
||||||||||
|
ï ð |
2 |
|
2 |
|
|
|||||
|
TêóT3 |
|
|
|
|||||||
|
= têó + 273 = 150 + 273 = 423К; |
||||||||||
|
|
|
|
|
|
450 − 423 |
|
|
|||
|
DT3T = 298Ч0,091Ч 450 Ч423 |
= 0,004 МДж |
Потери эксергии в теплообменнике Т4:
229
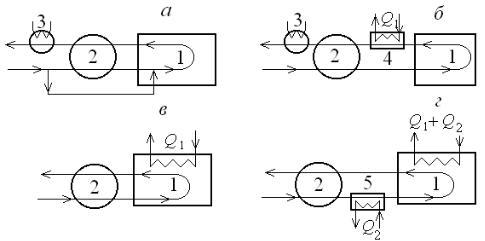
|
|
|
|
|
|
TΤ |
|
|
=Q 0 Ч |
4 Ч |
ΤïΤð4 − ΤâΤ4 |
|
|||||
|
|
|
|
|
|
DΤ4T |
|
|
|
, |
|
||||||
|
|
|
|
|
|
ΤïΤð4 ЧTâΤ4 |
|
||||||||||
где |
|
|
t4 + |
têî í |
|
|
|
273 = 170 + |
30 + 273 = |
|
|||||||
|
TΤ4 |
= |
+ |
373К; |
|||||||||||||
|
|
|
|
|
|||||||||||||
|
ï ð |
|
2 |
|
|
|
|
|
2 |
|
|
|
|
|
|||
|
TΤ4 |
= |
|
tâí |
+ tâê |
|
+ |
273 = |
20 + |
35 + |
273 = |
300 К; |
|||||
|
|
|
|
|
|
|
|
||||||||||
|
â |
|
|
|
|
2 |
|
|
|
|
|
2 |
|
|
|
|
|
|
|
|
|
|
|
|
|
|
|
373 − |
300 |
|
|
|
|
||
|
DT4T = 298Ч0,848Ч 373Ч300 |
= |
0,165МДж. |
||||||||||||||
Общая сумма потерь эксергии во второй сумме равна |
|
||||||||||||||||
е |
D2T = DT1T + DT2T + DT3T + |
DT4T = |
0,041+ 0,078 + |
||||||||||||||
|
|
+ 0,004 + 0,165 = |
0,288 Ì Äæ. |
||||||||||||||
Отношение потерь эксергии во второй схеме |
|
||||||||||||||||
|
|
|
|
|
е |
D2T |
= |
0,288 |
Ч100% |
= |
14,8% |
|
|||||
|
|
|
|
|
е |
Q |
|
|
|
1,939 |
|
|
Рис. 9.8. Схемы использования тепла реакций:
а– с холодным байпасом; б – с отводом тепла реакции в выносном аппарате;
в– с отводом тепла непосредственно из реактора; г – с предварительным подогревом реактивов; 1 – реактор; 2 – теплообменник; 3 – холодильник; 4 – аппарат для использования тепла реакции; 5 – подогреватель реагентов
Как показали расчеты, более совершенной с точки зрения использования энергии является второй вариант технологической схемы.
Необходимо отметить, что реальные схемы утилизации тепла сложнее и могут быть многоступенчатыми.
Существует три группы методов экономии энергетических ресурсов:
230
1.Методы, связанные с увеличением поверхностей аппарата, времени протекания реакции, использованием более активных катализаторов, что позволяет приблизиться к равновесному состоянию на выходе из аппарата.
2.Методы, основанные на изменении технологического режима и не связанные с изменением технологической схемы, что может привести к увеличению габаритов аппарата.
3.Методы, требующие наряду с приемами, изложенными выше, изменение технологической схемы.
При разработке технологической схемы необходимо производить совместный анализ энергетического и эксергетического балансов с целью установления уровня возврата и возможности использования электрической, тепловой и механической энергии с существенным сокращением потребляемой извне энергии. Кроме того, при выборе относительного варианта технологической схемы должны быть учтены технико-экономические показатели.
231