
- •Рис. 9.2. К расчету теплообмена в реакторе вытеснения
- •Рис. 7.2. К примеру 10.1
- •Рис. 11.4. К примеру 11.1
- •Рис. 11.9. К расчету шпилек
- •Рис. 11.10. К примеру 11.3
- •Рис. 11.11. К примеру 11.5
- •Рис. 13.10. Рамные мешалки
- •Рис. 13.11. Якорные мешалки
- •Предисловие
- •Экологическое и технико-экономическое обоснование проектов химических производств.
- •Этапы проведения экологической экспертизы
- •Принципы экологической экспертизы
- •Рис. 1.1. Общая система организации проектирования
- •Рис. 1.2. Основные этапы и стадии разработки проектов для промышленного строительства
- •1.2. Задание на проектирование
- •Рис. 1.3. Пример построения розы повторяемости и силы ветров
- •Рис.1.4. Схема выпадения дымовых частиц при наличии зеленых защитных насаждений между застройкой и источником задымления и при отсутствии их:
- •Рис. 1.5. Совмещенная схема движения загрязненных нижнего и верхнего потоков
- •1.5. Разработка проектной документации по охране окружающей среды
- •1.5.2. Разработка прогноза загрязнения воздуха
- •1.5.4. Прогноз воздействия объекта при возможных авариях
- •1.6. Технологический процесс как основа промышленного проектирования
- •Рис. 1.6. Схема производства серной кислоты контактным способом:
- •Рис. 1.8. Процессы и аппараты химической технологии
- •Рис. 1.9. Виды оборудования химической технологии
- •Рис. 1.11. Уровни организации химического предприятия
- •1.7. Генеральный план химических предприятий
- •Рис. 1.12. Генеральный план предприятий химической промышленности
- •1.8. Типы промышленных зданий
- •1.8.1. Одноэтажные промышленные здания
- •Рис. 1.13. Одноэтажное здание павильонного типа:
- •Рис. 1.14. Многоэтажное производственное здание:
- •1.8.2. Многоэтажные здания
- •Рис. 1.15. Многоэтажное производственное здание:
- •Рис. 1.16. Поперечные разрезы зданий I и II очередей сернокислотного производства:
- •1.8.3. Вспомогательные здания и помещения химических предприятий
- •1.8.4. Склады промышленных предприятий
- •1.9. Инженерные сооружения
- •инженерных сооружений
- •1.10. Специальные вопросы проектирования химических предприятий
- •2.1. Основные стадии проектирования химических производств и оборудования
- •Рис. 2.1. Основные стадии проектирования
- •2.2. Виды конструкторских документов
- •2.4.1. Курсовое проектирование
- •2.4.2. Дипломное проектирование
- •2.4.3. Пример использования АвтоЛиспа
- •Рис. 2.2. Схема установки для ректификации трехкомпонентной смеси:
- •СИСТЕМЫ АВТОМАТИЗИРОВАННОГО ПРОЕКТИРОВАНИЯ
- •3.1. История развития САПР
- •3.2. Основные принципы создания САПР
- •Рис. 3.1. Модульная структура программного обеспечения
- •Рис. 3.2. Области использования ЭВМ в процессе проектирования
- •3.4. Автоматическое изготовление чертежей
- •3.5. Основные преимущества автоматизации проектирования
- •3.6. Основные требования к САПР
- •Рис. 3.3. Схема взаимодействия пользователя со средствами САПР:
- •3.7. Связь САПР с производством, расширение области применения
- •3.8. Система автоматизированного проектирования цементных заводов
- •3.8.1. Функционирование САПР
- •ВВЕДЕНИЕ В ПРОЕКТИРОВАНИЕ
- •4.1. Проектно-сметная документация
- •4.2.1. Исходные положения
- •4.2.2. Обоснование способа производства химической продукции
- •ВЫБОР И РАЗРАБОТКА ТЕХНОЛОГИЧЕСКОЙ СХЕМЫ ПРОИЗВОДСТВА
- •5.1. Общие положения
- •5.2. Последовательность разработки технологической схемы
- •Рис. 5.1. Примерная схема стадий технологического процесса:
- •Рис. 5.2. Блок-схема физико-химических процессов, протекающих в гетерофазном реакторе с мешалкой
- •5.3. Принципиальная технологическая схема
- •5.4. Размещение технологического оборудования
- •Выбор технологического оборудования химических производств
- •6.1. Основные типы химических реакторов
- •Рис. 6.1. Установка для непрерывного процесса:
- •Рис. 6.5. Изменение концентрации веществ в реакторах:
- •Рис. 6.6. Реакторы смешения:
- •6.2. Химические факторы, влияющие на выбор реактора
- •6.2.1. Реакции расщепления
- •Рис. 6.7. Относительный выход реакции расщепления:
- •Реактор
- •6.2.2. Реакции полимеризации
- •6.2.3. Параллельные реакции
- •Объем реактора
- •РВНД
- •6.3. Эскизная конструктивная разработка основной химической аппаратуры
- •6.3.1. Общие положения
- •6.3.2. Реакторы
- •6.4. Оптимизация процессов химической технологии
- •УРАВНЕНИЯ МАТЕРИАЛЬНОГО БАЛАНСА ТЕХНОЛОГИЧЕСКОГО ПРОЦЕССА
- •7.1. Стехиометрические расчеты
- •7.2. Термодинамический анализ процессов
- •7.2.1. Равновесие химической реакции
- •Рис. 1.1. Зависимость коэффициента активности газв от приведенных давления и температуры
- •7.2.2. Расчет состава равновесной смеси
- •7.3. Общее уравнение баланса массы
- •7.4. Практический материальный баланс
- •7.5. Физико-химические основы технологического процесса
- •8.1. Общие положения
- •8.2. Расчет объемов реакторов
- •8.2.1. Основные положения химической кинетики
- •8.2.2. Расчет идеальных реакторов
- •8.3. Определение объемов аппарата
- •Тепловой расчет основного оборудования
- •9.1. Общее уравнение баланса энергии
- •Рис. 9.1. К примеру 9.1
- •9.2. Практический тепловой баланс
- •9.3. Теплообмен в реакторах
- •9.4. Расчет энтальпий и теплоемкостей
- •9.6. Расчет реактора периодического действия
- •Рис. 9.3. К тепловому расчету реактора периодического действия
- •9.7. Степень термодинамического совершенства технологических процессов
- •Рис. 9.6. Технологическая схема 1:
- •Рис. 9.7. Технологическая схема 2
- •Рис. 9.8. Схемы использования тепла реакций:
- •Гидравлические расчеты
- •10.1. Расчет диаметра трубопровода
- •Пары, насыщенные при абсолютном давлении (МПа)
- •Рис. 10.1. Зависимость коэффициента трения от критерия Рейнольдса и степени шероховатости трубы
- •10.3. Гидравлическое сопротивление кожухотрубчатых теплообменников
- •10.4. Подбор насосов
- •МЕХАНИЧЕСКИЙ РАСЧЕТ
- •11.1. Расчет сварных химических аппаратов
- •11.1.1. Основные расчетные параметры
- •11.1.2. Расчет на механическую прочность
- •11.1.3. Требования к конструированию
- •11.1.4. Расчет цилиндрических обечаек
- •Рис. 11.1. Номограмма для определения толщины цилиндрических обечаек, работающих под наружным давлением
- •Рис.11.2. Схема пользования номограммой на рис. 11.1:
- •11.1.5. Расчет крышек и днищ
- •Рис. 11.3. Основные конструкции днищ сварных аппаратов:
- •11.1.6. Подбор стандартных элементов
- •11.2. Расчет толстостенных аппаратов
- •Рис. 11.7. Основные конструкции уплотнений затворов высокого давления:
- •Рис. 11.8. К расчету усилий, действующих на затворы высокого давления
- •КОНСТРУКционНЫЕ МАТЕРИАЛЫ В ХИМИЧЕСКОМ МАШИНОСТРОЕНИИ
- •12.1. Виды конструкционных материалов
- •12.2. Коррозия металлов и сплавов
- •12.2.1. Виды коррозии
- •12.2.2. Виды коррозионных разрушений
- •12.2.3. Способы борьбы с коррозией
- •12.3. Влияние материала на конструкцию аппарата и способ его изготовления
- •12.3.1. Конструкционные особенности аппаратов из высоколегированных сталей
- •Рис. 12.1. Сварка встык:
- •Рис. 12.2. Способы подготовки кромок под сварку
- •Рис. 12.4. Способы сварки легированной и углеродистой стали
- •12.3.2. Конструктивные особенности эмалированных аппаратов
- •Рис. 12.5. Элементы конструкции эмалированных аппаратов
- •Рис 12.6. Пайка элементов медных аппаратов
- •12.3.3. Конструктивные особенности аппаратов из цветных металлов
- •Рис. 12.7. Основные типы паяных соединений
- •12.3.4. Конструктивные особенности аппаратов из пластмасс
- •ОФОРМЛЕНИЕ ОТДЕЛЬНЫХ ЭЛЕМЕНТОВ ХИМИЧЕСКОЙ АППАРАТУРЫ
- •13.1. Оформление поверхности теплообмена
- •Рис. 13.5. Реактор со змеевиковой рубашкой
- •Рис. 13.6. Рубашка с вмятинами
- •Рис. 13.8. Вывод змеевика через крышку аппарата:
- •13.2. Перемешивающие устройства
- •Рис. 13.12. Листовая мешалка
- •Рис. 13.13. Пропеллерные мешалки
- •Рис. 13.14. Турбинные мешалки открытого (а) и (б) закрытого типа
- •Рис. 13.15. Крепление мешалок к ступице:
- •13.3. Уплотнения вращающихся деталей
- •Рис. 13.18. Одинарное торцовое уплотнение:
- •ТРУБОПРОВОДЫ И ТРУБОПРОВОДНАЯ АРМАТУРА
- •Рис 14.5. Фасонные части трубопроводов
- •Рис. 14.7. Крепление горизонтальных и вертикальных трубопроводов на подвесках
- •Рис. 14.8. Компенсаторы:
- •ВСПОМОГАТЕЛЬНОЕ ОБОРУДОВАНИЕ ХИМИЧЕСКИХ ЗАВОДОВ
- •15.1. Виды вспомогательного оборудования
- •Рис. 15.1. Схема многостадийного диспергирования твердой фазы с контрольной классификацией продукта
- •15.2. Транспортные средства
- •15.2.1. Классификация транспортных средств для твердых материалов
- •15.2.2. Машины для транспортировки жидкостей и газов
- •ТЕХНОЛОГИЧЕСКИЕ СХЕМЫ И ОБОРУДОВАНИЕ ДЛЯ ГРАНУЛИРОВАНИЯ ДИСПЕРСНЫХ МАТЕРИАЛОВ
- •16.1. Классификация методов гранулирования и особенности уплотнения гранул
- •Рис. 16.1. Тарельчатый гранулятор:
- •Рис. 16.2. Гранулятор барабанного типа конструкции НИИХиммаша
- •16.3. Основные закономерности и аппаратурное оформление метода экструзии
- •16.5. Гранулирование в псевдоожиженном слое
- •16.6. Технологические схемы процессов гранулирования дисперсных материалов
- •Рис. 16.11. Технологическая схема гранулирования шихты методом окатывания
- •Рис. 16.13. Схема уплотнения шихты в роторном грануляторе
- •Рис. 16.14. Схема гранулирования шихты методом экструзии
- •Рис. 16.15. Схема установки для компактирования шихты
- •ЛИТЕРАТУРА

b |
b - |
a é |
|
n− 1 |
n− 2 |
ù |
|
I = ò y(x)dx » |
|
y(xn ) + 4å |
y(xi ) + 2å |
||||
|
|
ê |
y(x0 ) + |
y(xi )ú . |
|||
3n |
|
||||||
a |
ë |
|
i= 1 |
i= 2 |
û |
Здесь a и b –пределы интегрирования;
n – четное число интервалов разбиения отрезка интегрирования. Расчет проводится в следующей последовательности: задаться точно-
стью вычисления интеграла e и вычислить интеграл при n=4. Затем n все вре-
мя удваивается, пока не выполнится условие ½I(n)−I(2n)½< e . Формула Симпсона легко программируется.
Достаточно точными являются две следующие простые формулы:
пятиточечная |
|
b − a |
|
|
|
|
|
|
|
|
|
|
|
|
|
|
|
|
|
|
|
|||
I(4) » |
|
[7y(x |
0 |
) + 32y(x ) + 12y(x |
2 |
) + |
32y(x ) + |
7y(x |
4 |
)]; |
|
|
||||||||||||
|
|
|
|
|
||||||||||||||||||||
|
|
90 |
|
|
|
|
1 |
|
|
|
|
|
3 |
|
|
|
|
|||||||
|
|
|
|
|
|
|
|
|
|
|
|
|
|
|
|
|
|
|
|
|
|
|||
и семиточечная формула Уэддля |
|
|
|
|
|
|
|
|
|
|
|
|
|
|
|
|||||||||
I (6) » |
b − |
a |
[ y(x |
0 |
) + 5y(x ) + |
y(x |
2 |
) + 6y(x |
3 |
) + |
y(x |
4 |
) + 5y(x ) + |
y(x |
6 |
)]. |
||||||||
|
|
|||||||||||||||||||||||
20 |
|
|
|
|
1 |
|
|
|
|
|
|
5 |
|
|
|
|||||||||
|
|
|
|
|
|
|
|
|
|
|
|
|
|
|
|
|
|
|
|
|
|
Задача расчета реальных реакторов в подавляющем большинстве случаев является весьма сложной, так как при этом требуется постановка специальных исследований по оценке эффективной диффузии компонентов реакции в конкретных технологических условиях. При наличии таких коэффициентов расчет можно провести по методикам, описанным в соответствии со списком литературы.
8.3. ОПРЕДЕЛЕНИЕ ОБЪЕМОВ АППАРАТА
Определение количества операций, совершаемых одним реактором в
сутки
n = τt , где n – количество операций в сутки;
t - время работы реактора в сутки, час;
t – длительность стадии технологического процесса, час. Значение «n» может быть найдено и другим путем:
n = Vc , Vp
где Vс – суточный объем перерабатываемых материалов, м3;
Vр – рабочая емкость всех аппаратов данной технологической стадии. Определение рабочей емкости всех аппаратов данной стадии
Vp = Vnc . Расчет общего объема всех аппаратов
194
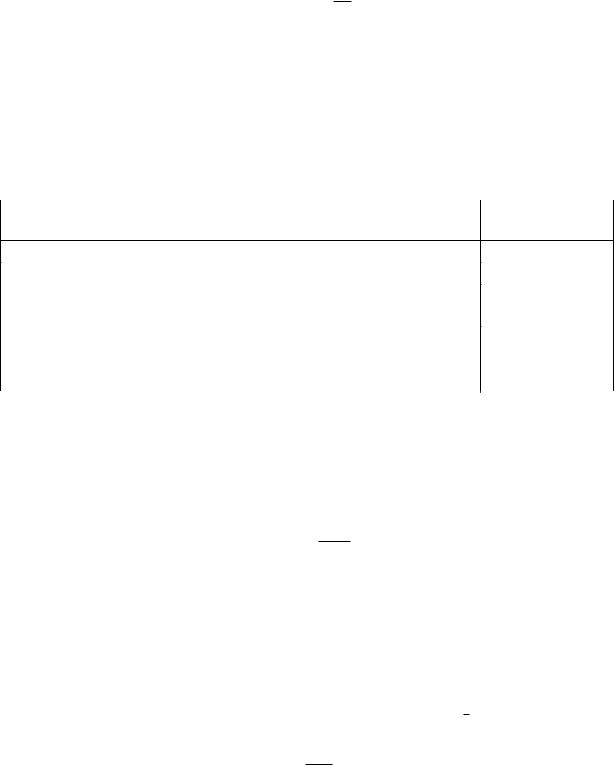
Vî áù = Vjp ,
где Vобщ – общий объем всех аппаратов данной технологической стадии; j - коэффициент заполнения аппарата.
Коэффициент заполнения j имеет различные значения в зависимости от характера процесса, осуществляемого в данном аппарате.
При выборе коэффициента заполнения можно руководствоваться следующими данными, представленными в табл. 8.1.
Таблица 8.1. Значения коэффициентов заполнения
Характер процесса, протекающий в реакторе |
Степень |
|
заполнения |
||
|
||
Хранение жидкости (хранилище) |
0,8÷0,90 |
|
Отмеривание жидкостей (мерники) |
0,8÷0,85 |
|
Физические или химические процессы без пенообразующих |
|
|
эффектов |
0,75÷0,80 |
|
Процессы, сопровождающиеся пенообразованием |
0,4÷0,6 |
|
(экзотермические реакции, кипячение и пр.) |
||
Суспензионная и водоэмульсионная полимеризация |
0,65÷0,75 |
|
|
|
Оптимальная емкость реактора выбирается в зависимости от конкретных условий проведения данного процесса. Необходимо использовать практические данные по объему аппарата существующего производства.
Расчет количества аппаратов данной стадии определяется выражением
K = VVî áù ,
где К - оличество аппаратов;
V – общий объем одного аппарата (по каталогу), м3.
Если проектируемый аппарат не предусмотрен каталогом, то объем аппарата выбирается по практическим соображениям. В любом случае после выбора аппарата дается краткое описание его конструктивных особенностей с указанием марки материала.
Расчет объемов аппаратов непрерывного действия заключается в определении объема перерабатываемых материалов, в час (или в секунду)
V÷àñ = V24ñóò , м3/ч.
Расчет рабочей емкости всех аппаратов
Vр=Vчас×t,
где Vр – рабочая емкость всех аппаратов, м3;
t - время пребывания реакционной массы в аппарате, часы. Расчет общей емкости всех аппаратов:
195

Vî áù = Vjp .
Выбор стандартного аппарата или конструирование нового заключается в следующем. Для аппаратов непрерывного действия – аппаратов «идеального» вытеснения – необходимо, прежде всего, определить соотношение между высотой (или длиной) аппарата и его поперечным сечением.
При заданной скорости протекания реакционной массы можно рассчитать высоту (длину) аппарата идеального вытеснения по формуле
Н=W×t, где Н – высота (длина) аппарата, м;
t - время пребывания реакционной массы, с.
Площадь поперечного сечения аппарата идеального вытеснения определяется следующим образом:
F = WV .
Количество аппаратов непрерывного действия определяется, как для периодических процессов:
K = VVî áù ,
где V – объем одного реактора, м3.
Вконце расчета следует привести подробное описание конструктивных особенностей и материала выбранного аппарата, а также описание пускового периода реактора до ввода его в непрерывный процесс.
Для комбинированных аппаратов смешения каскадного и секционного типов основным вопросом технологического расчета является определение оптимального количества последовательно включенных аппаратов или секций, а также их рабочего объема.
Втех случаях, когда имеется уравнение кинетики процесса и известны значения констант скорости реакций, используется аналитический метод расчета многосекционного реактора или каскада аппаратов.
Ниже приводятся некоторые типовые примеры, иллюстрирующие методы определения объемов реакторов, которые характеризуют производство
сзаложенными в них различными химическими реакциями как с известными кинетическими уравнениями, так и без них.
Пример 8.1. Рассчитать поликонденсатор дигликольтерефталата производительностью W=3 т/сут. Процесс периодический. Данные о работе аппарата при загрузке 1 т дигликольтерефталата приведены в табл. 8.2.
Решение:
Vðï ä |
G Чτ |
= |
3510 Ч6 |
= 2,11ì 3 . |
|
24 Чr Чj |
24 Ч1040 Ч0,4 |
||||
|
|
|
По ГОСТ 9931-61 объем РПД принимают равным 2,5 м3.
196
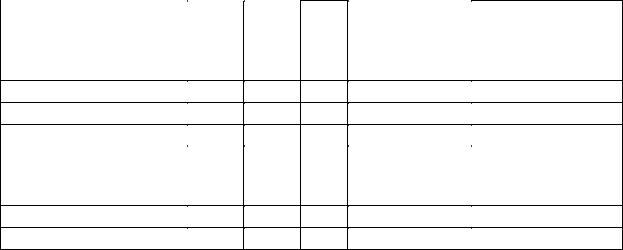
Таблица 8.2. Режим работы реактора периодичесого действия (РПД)
|
Время, |
tнач, |
tкон, |
Количество |
Количество |
Технологическая |
массы |
отгоняемого |
|||
стадия |
τ, ч |
°С |
°С |
в аппарате, |
этиленгликоля, |
|
|
|
|
G, кг |
кг |
Загрузка |
0,3 |
513 |
513 |
1170 |
− |
Подогрев РПД |
1,0 |
513 |
533 |
1170 |
− |
Отгон этиленгликоля |
1,0 |
533 |
533 |
1005 |
165 |
Снижение давления |
|
|
|
|
|
до 0,1 мм.рт.ст. и |
2,0 |
533 |
548 |
1000 |
5 |
поликонденсация |
|
|
|
|
|
Выгрузка |
0,7 |
548 |
548 |
1000 |
− |
Охлаждение аппарата |
1,0 |
548 |
513 |
1000 |
− |
Пример 8.2. Расчет продолжительности реакции с использованием кинетики реакции. В реакторе периодического действия протекает химический процесс, скорость которого определяется уравнением вида
RA = KCAn при n=1 и К=0,000895 с−1.
Начальная концентрация исходного продукта А равна СА0=1 моль/л. Конечная степень превращения хА=0,96.
Требуется определить продолжительность реакции t3.
Решение:
|
XadX A |
|
XadX A |
Xa |
|
dX A |
|
|
|
CA0 |
Xa dX A |
|
|
|||||||
t 3 = CA0 ò |
r |
= CA0 ò kC |
|
|
= CA0 ò |
|
|
|
|
|
= |
|
|
ò |
|
|
= |
|||
A |
kC |
A0 |
(1- X |
A |
) |
kC |
A0 |
1 - X |
|
|||||||||||
|
0 |
A |
0 |
|
0 |
|
|
|
|
|
0 |
|
A |
|||||||
|
1 ln(1 - |
|
|
|
|
1 |
|
|
|
|
|
|||||||||
= |
X A ) |
0X A = |
- |
|
|
ln(1 - |
0,96) = |
3600 c = 1 ч. |
|
|
||||||||||
0,000895 |
|
|
||||||||||||||||||
|
k |
|
|
|
|
|
|
|
|
|
|
|
|
|
|
|
|
Далее подставляем t3 в величину tn и заканчиваем расчет так же, как указано в примере 8.1.
Пример 8.3. В реакторе вытеснения протекает реакция в газовой фазе по уравнению 4А®В+6С при 648,89 К, скорость которой описывается выражением RA=2,78×10−3×CA. Степень превращения хА=0,80. Давление в системе –
4,6 атм. Скорость подачи реагента А равна GА=5,03×10−4 кмоль/с. Рассчитать объем РВНД.
Решение: Объем РВНД находим по формуле
|
|
|
x |
dxA |
V |
= G |
|
Ч тA |
|
|
|
|||
ðâí ä |
|
A |
0 K ЧCA |
При постоянном давлении
197

CA = CA0 11+− ex×Ax , где С0 – начальная концентрация реагента,
e – коэффициент, учитывающий изменение объема системы
ε = |
7 − 4 |
= 0,75. |
|
4 |
|
Подставляем соответствующие величины в первоначальную формулу
V |
= |
GA |
x |
1+ e ЧxA |
dx |
A . |
|
|
|||||
ðâí ä |
|
K ЧCA0 |
т0 1- xA |
|||
|
|
|
После интегрирования получаем следующее выражение:
|
|
|
|
|
|
|
G |
A |
|
|
й |
|
|
|
|
|
|
1 |
|
|
щ |
|
|
|
|||
|
Vðâí ä = |
|
|
|
|
|
|
к |
(1+ |
e )ln |
|
|
|
|
|
- e ЧxA ъ |
; |
|
|
||||||||
|
|
|
|
|
|
|
|
|
1 |
- xA |
|
|
|||||||||||||||
|
|
|
PA0 |
|
K ЧCA0 л |
|
|
|
|
ы |
|
|
|
||||||||||||||
|
CA0 = |
|
|
= |
|
|
|
|
|
4,6 |
|
|
= |
0,293 кмоль/м3. |
|
||||||||||||
|
|
RT |
|
0,024 |
|
× |
648,89 |
|
|
||||||||||||||||||
|
|
|
|
|
|
|
|
|
|
|
|
|
|
|
|
||||||||||||
|
5,03Ч10− 4 |
|
|
|
|
й |
(1 |
|
|
0,75) ln |
1 |
|
|
|
щ |
|
3 |
||||||||||
Vðâí ä = |
|
|
|
|
|
|
|
|
|
к |
+ |
|
- |
0,75Ч0,8ъ |
= 1,46 |
м . |
|||||||||||
2,72 Ч10 |
− 1 |
Ч0,293 |
0,2 |
||||||||||||||||||||||||
|
|
|
л |
|
|
|
|
|
|
|
|
|
|
|
|
ы |
|
|
По ГОСТ 13372-87 принимаем ближайший объем трубчатого реактора равным 1,6 м3.
В том случае, когда неизвестны кинетические константы скорости реакции, время пребывания принимают по практическим данным (из регламента цеха).
Ниже приводится пример расчета объема РВНД по принятому значению времени пребывания t.
Пример 8.4. Рассчитать объем РВНД для ежедневного производства 50 т этилацетата из уксусной кислоты. Исходные данные: время t=7270 с,
плотность реагирующей смеси постоянна r=120,56 кг/м3.
Решение: Определяем объемную скорость реагирующей смеси для производства 50 т вещества.
Vc = |
GA |
50000 |
= 4,8Ч10 |
− 3 |
|
|
|
= |
|
|
м3/с. |
||
24 Чr Ч3600 |
24 Ч120,56 Ч3600 |
|
||||
Определяем объем РВНД по уравнению |
|
|
||||
|
VРВНД=VС×t=4,8×10−3×7270=34,8 м3. |
|
|
|||
По ГОСТ 13372-67 принимаем ближайший объем |
аппарата, равным |
|||||
40 м3. |
|
|
|
|
|
|
Пример 8.5. В РСНД проводится реакция типа А®В, которая характе-
198

ризуется кинетическим уравнением RА=5,55×10−5×СА, с−1. Необходимо полу-
чить 2,77×10−5 кмоль/с вещества В из исходной смеси, содержащей вещество А в количестве 0,1 кмоль/м3. Степень превращения хА=0,5. Требуется определить объем реактора смешения.
Решение: Объем РСНД определяем по уравнению
Vðñí ä = GA Ч xA .
RA
Выражаем СА=СА0×(1-хА). Определяем скорость подачи исходной смеси
GA = |
2,77 × 10− 5 |
= |
2,77 × 10 |
− 5 |
− 5 кмоль/с. |
xA |
0,5 |
= 5,54 × 10 |
|||
|
|
|
|
Подставляем указанные значения в первое уравнение и получаем искомое значение объема
V |
= |
5,54 Ч10− 5 Ч0,5 |
= 10 ì 3 . |
|
|||
ðñí ä |
|
5,54 Ч10− 5 Ч0,1Ч0,5 |
|
|
|
По ГОСТ 13372-67 принимаем объем РСНД равным 10 м3.
При выполнении проекта инженер-проектировщик обязан произвести технологические расчеты вспомогательной аппаратуры, всех транспортных устройств (ленточные и шнековые транспортеры, пневмотранспорт и др.), а также рассчитать необходимую производительность и выбрать соответствующие типы питателей, дозаторов, мерников, циклонов и т. д.
Расчет соответствующего оборудования здесь не рассматривается, его можно найти в литературе по процессам и аппаратам химической технологии.
199