
- •Рис. 9.2. К расчету теплообмена в реакторе вытеснения
- •Рис. 7.2. К примеру 10.1
- •Рис. 11.4. К примеру 11.1
- •Рис. 11.9. К расчету шпилек
- •Рис. 11.10. К примеру 11.3
- •Рис. 11.11. К примеру 11.5
- •Рис. 13.10. Рамные мешалки
- •Рис. 13.11. Якорные мешалки
- •Предисловие
- •Экологическое и технико-экономическое обоснование проектов химических производств.
- •Этапы проведения экологической экспертизы
- •Принципы экологической экспертизы
- •Рис. 1.1. Общая система организации проектирования
- •Рис. 1.2. Основные этапы и стадии разработки проектов для промышленного строительства
- •1.2. Задание на проектирование
- •Рис. 1.3. Пример построения розы повторяемости и силы ветров
- •Рис.1.4. Схема выпадения дымовых частиц при наличии зеленых защитных насаждений между застройкой и источником задымления и при отсутствии их:
- •Рис. 1.5. Совмещенная схема движения загрязненных нижнего и верхнего потоков
- •1.5. Разработка проектной документации по охране окружающей среды
- •1.5.2. Разработка прогноза загрязнения воздуха
- •1.5.4. Прогноз воздействия объекта при возможных авариях
- •1.6. Технологический процесс как основа промышленного проектирования
- •Рис. 1.6. Схема производства серной кислоты контактным способом:
- •Рис. 1.8. Процессы и аппараты химической технологии
- •Рис. 1.9. Виды оборудования химической технологии
- •Рис. 1.11. Уровни организации химического предприятия
- •1.7. Генеральный план химических предприятий
- •Рис. 1.12. Генеральный план предприятий химической промышленности
- •1.8. Типы промышленных зданий
- •1.8.1. Одноэтажные промышленные здания
- •Рис. 1.13. Одноэтажное здание павильонного типа:
- •Рис. 1.14. Многоэтажное производственное здание:
- •1.8.2. Многоэтажные здания
- •Рис. 1.15. Многоэтажное производственное здание:
- •Рис. 1.16. Поперечные разрезы зданий I и II очередей сернокислотного производства:
- •1.8.3. Вспомогательные здания и помещения химических предприятий
- •1.8.4. Склады промышленных предприятий
- •1.9. Инженерные сооружения
- •инженерных сооружений
- •1.10. Специальные вопросы проектирования химических предприятий
- •2.1. Основные стадии проектирования химических производств и оборудования
- •Рис. 2.1. Основные стадии проектирования
- •2.2. Виды конструкторских документов
- •2.4.1. Курсовое проектирование
- •2.4.2. Дипломное проектирование
- •2.4.3. Пример использования АвтоЛиспа
- •Рис. 2.2. Схема установки для ректификации трехкомпонентной смеси:
- •СИСТЕМЫ АВТОМАТИЗИРОВАННОГО ПРОЕКТИРОВАНИЯ
- •3.1. История развития САПР
- •3.2. Основные принципы создания САПР
- •Рис. 3.1. Модульная структура программного обеспечения
- •Рис. 3.2. Области использования ЭВМ в процессе проектирования
- •3.4. Автоматическое изготовление чертежей
- •3.5. Основные преимущества автоматизации проектирования
- •3.6. Основные требования к САПР
- •Рис. 3.3. Схема взаимодействия пользователя со средствами САПР:
- •3.7. Связь САПР с производством, расширение области применения
- •3.8. Система автоматизированного проектирования цементных заводов
- •3.8.1. Функционирование САПР
- •ВВЕДЕНИЕ В ПРОЕКТИРОВАНИЕ
- •4.1. Проектно-сметная документация
- •4.2.1. Исходные положения
- •4.2.2. Обоснование способа производства химической продукции
- •ВЫБОР И РАЗРАБОТКА ТЕХНОЛОГИЧЕСКОЙ СХЕМЫ ПРОИЗВОДСТВА
- •5.1. Общие положения
- •5.2. Последовательность разработки технологической схемы
- •Рис. 5.1. Примерная схема стадий технологического процесса:
- •Рис. 5.2. Блок-схема физико-химических процессов, протекающих в гетерофазном реакторе с мешалкой
- •5.3. Принципиальная технологическая схема
- •5.4. Размещение технологического оборудования
- •Выбор технологического оборудования химических производств
- •6.1. Основные типы химических реакторов
- •Рис. 6.1. Установка для непрерывного процесса:
- •Рис. 6.5. Изменение концентрации веществ в реакторах:
- •Рис. 6.6. Реакторы смешения:
- •6.2. Химические факторы, влияющие на выбор реактора
- •6.2.1. Реакции расщепления
- •Рис. 6.7. Относительный выход реакции расщепления:
- •Реактор
- •6.2.2. Реакции полимеризации
- •6.2.3. Параллельные реакции
- •Объем реактора
- •РВНД
- •6.3. Эскизная конструктивная разработка основной химической аппаратуры
- •6.3.1. Общие положения
- •6.3.2. Реакторы
- •6.4. Оптимизация процессов химической технологии
- •УРАВНЕНИЯ МАТЕРИАЛЬНОГО БАЛАНСА ТЕХНОЛОГИЧЕСКОГО ПРОЦЕССА
- •7.1. Стехиометрические расчеты
- •7.2. Термодинамический анализ процессов
- •7.2.1. Равновесие химической реакции
- •Рис. 1.1. Зависимость коэффициента активности газв от приведенных давления и температуры
- •7.2.2. Расчет состава равновесной смеси
- •7.3. Общее уравнение баланса массы
- •7.4. Практический материальный баланс
- •7.5. Физико-химические основы технологического процесса
- •8.1. Общие положения
- •8.2. Расчет объемов реакторов
- •8.2.1. Основные положения химической кинетики
- •8.2.2. Расчет идеальных реакторов
- •8.3. Определение объемов аппарата
- •Тепловой расчет основного оборудования
- •9.1. Общее уравнение баланса энергии
- •Рис. 9.1. К примеру 9.1
- •9.2. Практический тепловой баланс
- •9.3. Теплообмен в реакторах
- •9.4. Расчет энтальпий и теплоемкостей
- •9.6. Расчет реактора периодического действия
- •Рис. 9.3. К тепловому расчету реактора периодического действия
- •9.7. Степень термодинамического совершенства технологических процессов
- •Рис. 9.6. Технологическая схема 1:
- •Рис. 9.7. Технологическая схема 2
- •Рис. 9.8. Схемы использования тепла реакций:
- •Гидравлические расчеты
- •10.1. Расчет диаметра трубопровода
- •Пары, насыщенные при абсолютном давлении (МПа)
- •Рис. 10.1. Зависимость коэффициента трения от критерия Рейнольдса и степени шероховатости трубы
- •10.3. Гидравлическое сопротивление кожухотрубчатых теплообменников
- •10.4. Подбор насосов
- •МЕХАНИЧЕСКИЙ РАСЧЕТ
- •11.1. Расчет сварных химических аппаратов
- •11.1.1. Основные расчетные параметры
- •11.1.2. Расчет на механическую прочность
- •11.1.3. Требования к конструированию
- •11.1.4. Расчет цилиндрических обечаек
- •Рис. 11.1. Номограмма для определения толщины цилиндрических обечаек, работающих под наружным давлением
- •Рис.11.2. Схема пользования номограммой на рис. 11.1:
- •11.1.5. Расчет крышек и днищ
- •Рис. 11.3. Основные конструкции днищ сварных аппаратов:
- •11.1.6. Подбор стандартных элементов
- •11.2. Расчет толстостенных аппаратов
- •Рис. 11.7. Основные конструкции уплотнений затворов высокого давления:
- •Рис. 11.8. К расчету усилий, действующих на затворы высокого давления
- •КОНСТРУКционНЫЕ МАТЕРИАЛЫ В ХИМИЧЕСКОМ МАШИНОСТРОЕНИИ
- •12.1. Виды конструкционных материалов
- •12.2. Коррозия металлов и сплавов
- •12.2.1. Виды коррозии
- •12.2.2. Виды коррозионных разрушений
- •12.2.3. Способы борьбы с коррозией
- •12.3. Влияние материала на конструкцию аппарата и способ его изготовления
- •12.3.1. Конструкционные особенности аппаратов из высоколегированных сталей
- •Рис. 12.1. Сварка встык:
- •Рис. 12.2. Способы подготовки кромок под сварку
- •Рис. 12.4. Способы сварки легированной и углеродистой стали
- •12.3.2. Конструктивные особенности эмалированных аппаратов
- •Рис. 12.5. Элементы конструкции эмалированных аппаратов
- •Рис 12.6. Пайка элементов медных аппаратов
- •12.3.3. Конструктивные особенности аппаратов из цветных металлов
- •Рис. 12.7. Основные типы паяных соединений
- •12.3.4. Конструктивные особенности аппаратов из пластмасс
- •ОФОРМЛЕНИЕ ОТДЕЛЬНЫХ ЭЛЕМЕНТОВ ХИМИЧЕСКОЙ АППАРАТУРЫ
- •13.1. Оформление поверхности теплообмена
- •Рис. 13.5. Реактор со змеевиковой рубашкой
- •Рис. 13.6. Рубашка с вмятинами
- •Рис. 13.8. Вывод змеевика через крышку аппарата:
- •13.2. Перемешивающие устройства
- •Рис. 13.12. Листовая мешалка
- •Рис. 13.13. Пропеллерные мешалки
- •Рис. 13.14. Турбинные мешалки открытого (а) и (б) закрытого типа
- •Рис. 13.15. Крепление мешалок к ступице:
- •13.3. Уплотнения вращающихся деталей
- •Рис. 13.18. Одинарное торцовое уплотнение:
- •ТРУБОПРОВОДЫ И ТРУБОПРОВОДНАЯ АРМАТУРА
- •Рис 14.5. Фасонные части трубопроводов
- •Рис. 14.7. Крепление горизонтальных и вертикальных трубопроводов на подвесках
- •Рис. 14.8. Компенсаторы:
- •ВСПОМОГАТЕЛЬНОЕ ОБОРУДОВАНИЕ ХИМИЧЕСКИХ ЗАВОДОВ
- •15.1. Виды вспомогательного оборудования
- •Рис. 15.1. Схема многостадийного диспергирования твердой фазы с контрольной классификацией продукта
- •15.2. Транспортные средства
- •15.2.1. Классификация транспортных средств для твердых материалов
- •15.2.2. Машины для транспортировки жидкостей и газов
- •ТЕХНОЛОГИЧЕСКИЕ СХЕМЫ И ОБОРУДОВАНИЕ ДЛЯ ГРАНУЛИРОВАНИЯ ДИСПЕРСНЫХ МАТЕРИАЛОВ
- •16.1. Классификация методов гранулирования и особенности уплотнения гранул
- •Рис. 16.1. Тарельчатый гранулятор:
- •Рис. 16.2. Гранулятор барабанного типа конструкции НИИХиммаша
- •16.3. Основные закономерности и аппаратурное оформление метода экструзии
- •16.5. Гранулирование в псевдоожиженном слое
- •16.6. Технологические схемы процессов гранулирования дисперсных материалов
- •Рис. 16.11. Технологическая схема гранулирования шихты методом окатывания
- •Рис. 16.13. Схема уплотнения шихты в роторном грануляторе
- •Рис. 16.14. Схема гранулирования шихты методом экструзии
- •Рис. 16.15. Схема установки для компактирования шихты
- •ЛИТЕРАТУРА
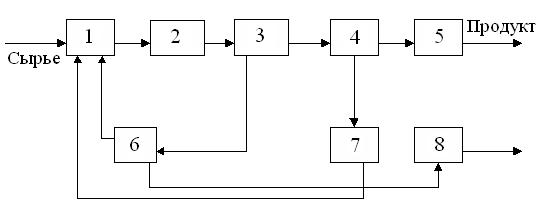
5.2. ПОСЛЕДОВАТЕЛЬНОСТЬ РАЗРАБОТКИ ТЕХНОЛОГИЧЕСКОЙ СХЕМЫ
После сбора и обработки данных на разработку технологической схемы приступают к составлению операционной технологической схемы. Результаты изображают графически: отдельные процессы обозначают прямоугольником или кружками, пути перемещения материалов – сплошными линиями различной толщины. Каждому процессу и технологической линии присваивается номер; весь чертеж называется схемой материальных и технологических потоков производства.
Такая схема дает только общее представление о характере проектируемого производства, поэтому следующим этапом является составление операционных блок-схем отдельных стадий производства. Блок-схема обычно включает следующие стадии:
−подготовка сырья;
−проведение химического превращения;
−выделение и очистка целевого продукта;
−создание товарной формы целевого продукта. Пример блок-схемы представлен на рис. 5.1.
Рис. 5.1. Примерная схема стадий технологического процесса:
1 – подготовка сырья; 2 – химическое превращение; 3 – выделение не превращенного сырья; 4 – выделение и очистка целевого продукта; 5 – придание товарной формы целевому продукту; 6 – регенерация и очистка непревращенного сырья; 7 – регенерация и очистка вспомогательных веществ; 8 – обезвреживание отходов
Следующим этапом детализации блок-схемы является разбивка каждой стадии процесса на отдельные физико-химические и химические операции. Это один из важнейших моментов проектирования, определяющий технический уровень и качество всего проекта. Анализ большого числа технологических схем показал, что чаще всего встречается ограниченное число операций.
Кним можно отнести:
−подачу и выдачу газообразных, жидких и твердых веществ с их дозировкой, разбавлением или концентрированием;
129
−массообменные процессы – растворение, кристаллизация, простая перегонка и ректификация, экстракция, абсорбция, адсорбция, десорбция;
−гидромеханические процессы – осаждение, фильтрование, центрифугирование;
−теплообменные процессы – нагревание, охлаждение, испарение, конденсация, выпаривание, сушка;
−механические процессы – дробление, измельчение, классификация и дозирование твердых веществ; транспортирование и перемешивание жидкостей;
−химические процессы – хлорирование, нитрование, окисление, восстановление, гидрирование, пиролиз и т. д.
На этом этапе решаются вопросы о непрерывном, периодическом или полупериодическом режиме проведения отдельных операций с учетом экономической эффективности их работы. Прежде чем приступить к определению состава операций стадии подготовки сырья необходимо уточнить, какие
формы состояния сырья наиболее рациональны для проведения в дальнейшем химических превращений в оптимальных условиях. Следует стремиться к созданию однофазной системы в аппаратах, где происходит химическое превращение, так как однофазные системы позволяют упростить технологическое и конструктивное оформление химического процесса и легче поддаются комплексной автоматизации. Наиболее предпочтительна работа с жидкостями, так как в этом случае можно обрабатывать в единице объема реактора большую массу реагентов в единицу времени по сравнению с газовыми системами. Но газовые (паровые) системы имеют ряд достоинств, например возможность смешивать любые вещества в любом соотношении. Наименее предпочтительно использование трех и более фаз в одном аппарате.
Изучив стандарты и технические условия (ТУ) на сырьевые продукты, выбирают процессы и операции перевода их в рациональную форму. Чаще всего встречаются операции приема жидких, твердых и газообразных продуктов, операции отмеривания, взвешивания, растворения, перемешивания, измельчения и пр.
При приеме продуктов в условиях Сибири иногда приходится предусматривать их предварительный подогрев для уменьшения вязкости или плавления в железнодорожной цистерне перед перекачкой. В случае создания склада на открытой площадке предусматривается постоянный подогрев емкостей.
При приеме газообразных продуктов уделяется внимание удалению конденсированных фаз, например фильтрованием, осушкой, сорбцией и т. д. Иногда приходится прибегать к увлажнению газов, например для безопасной работы с ацетиленом в него добавляется «транспортный» водяной пар.
При приеме и удалении из цеха твердых продуктов уделяется внимание механизации следующих основных операций:
− доставка материалов в цех, разгрузка и размещение их в цехе;
130
−вскрытие тары и ее обработка;
−подготовка материалов к использованию;
−доставка материалов к технологическим аппаратам и их дозировка;
−обработка и удаление твердых и сыпучих отходов производства;
−переработка твердых целевых продуктов.
В некоторых случаях на стадии подготовки сырья приходится осуществлять процессы и операции по повышению качества сырья в связи с тем, что требования технологического процесса превышают показатели стандартов или ТУ. Обычно применяются процессы перегонки, сорбции, сушки, фильтрования и т. п. Иногда приходится использовать и химические процессы, например гидрирование для удаления следов ацетилена, разложение перекисей, которые могут образоваться во время хранения ряда продуктов, и т. д.
Особого внимания требует составление схемы стадий химического превращения, так как проведение технологического процесса при этом предопределяет во многом экономическую эффективность всего производства в целом.
Исходными данными для составления операционной схемы в этом случае являются данные по термодинамике, кинетике, механизму химической реакции, данные о фазовом состоянии реагентов. На основании этих данных необходимо задаться определенным типом аппарата. При проведении стадии химического превращения приходится иметь дело с явлениями различной физико-химической природы: химическими, тепловыми, диффузионными и гидромеханическими. Они, как правило, совмещены в объеме аппарата и характеризуются большим числом элементов и связей, иерархий уровней элементарных физико-химических эффектов, связанных цепью причинно-след- ственных отношений. Поэтому необходимо стремиться, прежде всего, провести качественный анализ физико-химической системы и процессов, протекающих в ней. Следует заметить, что глубина детализации зависит от степени изученности рассматриваемой системы и явлений, связанных с проектируемым процессом.
На основе проведенного анализа можно составить набор операций, обеспечивающих стадию химического превращения, и определить их локализацию. Результаты анализа можно представить в текстовом виде или дополнить текст графической иллюстрацией (см. пример на рис. 5.2).
Выбирая определенную операцию или их набор, надо точно уяснить достигаемую цель. Необходимо иметь представление, как осуществляется та или иная операция. Например, целью перемешивания может являться:
−ускорение течения химической реакции;
−равномерное распределение твердых частиц в объеме жидкости;
−интенсификация теплообмена.
131
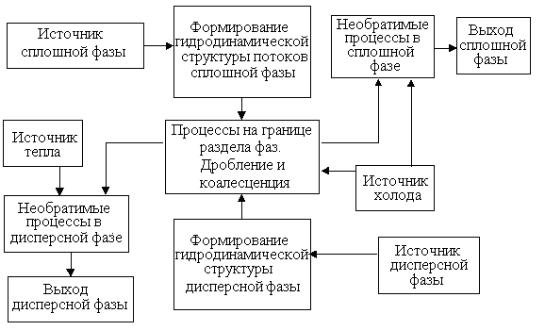
Рис. 5.2. Блок-схема физико-химических процессов, протекающих в гетерофазном реакторе с мешалкой
Перемешивание может происходить как в реакционных аппаратах, так и в специальных аппаратах-смесителях или в трубопроводах. Перемешивание может осуществляться механическими мешалками, газом или паром, циркуляцией с помощью насосов, вибраторами или пульсаторами.
При составлении операционной схемы стадии выделения целевого продукта решаются задачи:
−выпуск готовой продукции в соответствие с требованием стандартов и технических условий;
−максимально возможная утилизация побочных продуктов;
−выделение и регенерация не прореагировавшего сырья и вспомогательных продуктов.
Обычно эти задачи решаются за счет использования процессов дистилляции и ректификации, кристаллизации, переосаждения, сорбционных процессов и т. д. Критерием выбора процесса или комбинации процессов является удовлетворение требований стандартов и экономическая эффективность. Набор операций зависит от принятия решения по выбору вывода из цеха готовой продукции (по трубопроводам, в цистернах, бочках, контейнерах, мешках и т. п.).
Операционная схема должна решать и вопросы удаления отходов произ-
водства. Под отходами производства понимают удаляющиеся в технологическом процессе продукты, которые не могут быть использованы ни на данном, ни на другом предприятии, и поэтому подлежат уничтожению или обезвреживанию.
Отходами могут быть отработанная охлаждающая вода, отходящие газы, жидкие органические соединения, химически загрязненные водные стоки,
132