
- •Раздел 1. Механика, машиностроение, металлургия
- •Раздел 2. Мехатроника, робототехника и автоматизация
- •Раздел 4. Программная инженерия
- •Раздел 5. Менеджмент и экономика
- •Раздел 6. Профессиональное обучение
- •Раздел 8. Системный анализ и управление
- •Раздел 9. Дизайн и реклама
- •Раздел 10. Строительство и строительные материалы
- •Раздел 11. Транспортные системы
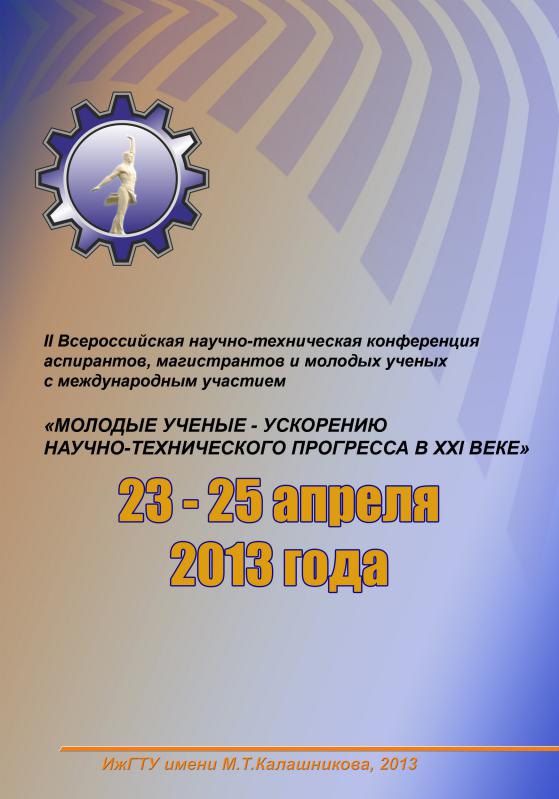
МИНИСТЕРСТВО ОБРАЗОВАНИЯ И НАУКИ УДМУРТСКОЙ РЕСПУБЛИКИ
ФГБОУ ВПО «ИЖГТУ ИМЕНИ М. Т. КАЛАШНИКОВА»
IIВсероссийская научно-техническая конференция аспирантов, магистрантов и молодых ученых
смеждународным участием
Молодые ученые – ускорению научно-технического прогресса в XXI веке
Ижевск
(23 – 25 апреля 2013 г.)
Сборник научных трудов
Ижевск, 2013
УДК 62(06)
ББК 30у
М75
Редакционная коллегия
В.В. Хворенков, доктор технических наук, профессор; Ю.В. Турыгин, доктор технических наук, профессор; А.М. Липанов, академик, директор института механики УрО РАН; Ю.А. Шихов, доктор педагогических наук, профессор; А.В. Щенятский, доктор технических наук, профессор; Р.А. Галиахметов, доктор экономических наук, профессор; М.М. Горохов, доктор физико-математических наук, профессор; Г.Е. Калинкина, доктор экономических наук, профессор; В.Н. Диденко, доктор технических наук, профессор; А.В. Алиев, доктор физикоматематических наук, профессор; Ю.О. Михайлов, доктор технических наук, профессор; В.И. Гольдфарб, доктор технических наук, профессор; В.А. Умняшкин, доктор технических наук, профессор; Н.М. Филькин, доктор технических наук, профессор; В.В. Муравьев, доктор технических наук, профессор; В.А. Алексеев, доктор технических наук, профессор; И.З. Климов, доктор технических наук, профессор; П.А. Ушаков, доктор технических наук, профессор; В.С. Клековкин, доктор технических наук, профессор; В.А. Куликов, доктор технических наук, профессор; Лялин В.Е. – доктор технических наук, доктор экономических наук, доктор геолого-минералогических наук, профессор; Г.Н. Первушин, доктор технических наук, профессор; Б.В. Севастьянов, доктор технических наук, профессор; М.М. Черных, доктор технических наук, профессор; Ревенко Н.Ф. – доктор экономических наук, профессор
Ответственные за выпуск
Ю.В. Турыгин, доктор технических наук, профессор; А.П. Тюрин, доктор технических наук, профессор.
Молодые ученые – ускорению научно-технического прогресса в XXI веке [Электронный ресурс] : электронное научное издание : сборник трудов II Всероссийской научно-технической конференции аспирантов, магистрантов и молодых ученых с международным участием, Ижевск, 23-25 апреля 2013 года / Министерство образования и науки Удмуртской Республики, Федеральное гос. бюджетное образовательное учреждение высш. проф. образования «Ижевский государственный технический университет имени М.Т. Калашникова». – Электрон. дан. (1 файл : 39,3 Мб.). – Ижевск, 2013. – 1415 c. – 1 электрон. опт.
диск (CD-ROM). – Систем. требования: Acrobat reader 6.0 и выше – ISBN 978-5- 7526-0603-8.
Сборник составлен из работ аспирантов, магистрантов, молодых ученых и студентов ИжГТУ и вузов-партнеров, отражающих результаты исследования в области приоритетных направлений развития науки и техники. Работы молодых ученых представлены в 12-ти тематических разделах.
|
|
УДК 62(06) |
|
ISBN 978-5-7526-0603-8 © ФГБОУ ВПО |
«Ижевский |
государственный |
|
технический |
университет |
имени |
М.Т. |
Калашникова», 2013 |
|
|
УДК 621(045)
Раздел 1. МЕХАНИКА, МАШИНОСТРОЕНИЕ, МЕТАЛЛУРГИЯ
|
|
Содержание |
|
|
Абашева А. В., Бесогонов В. В. Исследование топологии поверхности |
||||
керамики методом атомно-силовой полуконтактной микроскопии |
......................... |
7 |
||
Аникеев А. Н., Чуманов И. В. Влияние концентрации дисперсных частиц |
||||
WC на предел прочности центробежно-литых заготовок ....................................... |
|
11 |
||
Байков В. В., Матвеев А. В., Даненко В. Ф. Устройство для механического |
||||
удаления окалины с поверхности катаной стальной заготовки .............................. |
|
13 |
||
Башкиров И. А., Терентьев А. Н. Исследование характеристик |
||||
газораспределительного механизма ДВС ............................................................... |
|
16 |
||
Белинин Д. С., Щицын Ю. Д., Кучев П. С., Неулыбин С. Д. Упрочнение |
||||
рабочих поверхностей изделий методом плазменной поверхностной закалки |
||||
на токе обратной полярности |
.................................................................................. |
|
20 |
|
Бербек А. М., Малинин В. И., Бульбович Р. В. Расчет процессов в камере |
||||
сгорания ракетного двигателя на порошкообразном алюминии и воде ................. |
25 |
|||
Бербек А. М., Обросов А. А., Шатров А. В. Истечение порошка алюминия |
||||
из струйной форсунки установки синтеза нанопорошка оксида алюминия ........... |
30 |
|||
Болонкин В. А., Уразбахтин Ф. А. Исследование процесса |
||||
функционирования управляющих твердотопливных ракетных двигателей........... |
35 |
|||
Болховских Д. А., Малинин В. И., Бульбович Р. В. Расчет процессов в |
||||
форкамере установки синтеза нанооксида алюминия............................................. |
|
37 |
||
Бондарева О. С., Мельников А. А. Исследование формирования |
||||
модифицированных цинковых покрытий на изделиях из кремнийсодержащих |
||||
сталей ...................................................................................................................... |
|
|
|
41 |
Брызгалов К. А., Королева М. Р. Численное моделирование стационарного |
||||
турбулентного течения газа во впускном канале двигателя внутреннего |
||||
сгорания................................................................................................................... |
|
|
|
47 |
Волкова Л. В., Чувашов И. А., Байкалова Т. Н., Муравьев В. В. Расчетно- |
||||
экспериментальные исследования напряженно-деформированного состояния |
||||
бандажей локомотивных колес ..............................после термической обработки |
|
51 |
||
Волкова О. И., Лукин В. А., Ризванов Р. Г. Моделирование напряженно- |
||||
деформированного состояния сосуда давления с локальным утонением стенки |
||||
и накладным элементом .......................................................................................... |
|
|
56 |
|
Вылегжанин Д. Г., Кугультинов С. Д. Воздушное охлаждение при |
||||
обработке резанием ................................................................................................. |
|
|
|
61 |
Гончаров А. А., Жуков Б. А. Оценка влияния прижимного устройства на |
||||
самоторможение клиновых механизмов ....................................свободного хода |
|
65 |
||
Горбунов А. С., Каримов Р. Д., Гусаков Д. В., Рогинская Л. Э. |
||||
Параметрический |
синтез |
индукторно - конденсаторного |
модуля |
в |
полупроводниковом преобразователе .................частоты для электротехнологий |
70 |
|||
Горзолия А. Р., Губерт А. В. Проектирование лабораторного |
||||
пульсирующего воздушно-реактивного .................................................двигателя |
|
75 |
||
Деев А. О., Победин А. В. Метод оценки и снижения внутреннего шума |
||||
легковых автомобилей ............................................................................................ |
|
|
77 |
3
Дмитриев И. А., Русяк И. Г. Математическое моделирование истечения |
|
газа из цилиндрического канала.............................................................................. |
80 |
Докукин М. Ю., Пушкарев А. Э. Синтез структурных схем механизмов с |
|
пироприводом ......................................................................................................... |
83 |
Домнин А. К., Шаврин О. И. Повышение эффективности дробеструйной |
|
обработки винтовых пружин сжатия ...................................................................... |
86 |
Земерев Е. С., Малинин В. И., Шатров А. В. Экспериментальная установка |
|
получения дисперсных нанооксидов методом сжигания порошка алюминия ....... |
90 |
Зинатуллина А. М., Вахрушев А. В. Анализ методов управления |
|
наночастицами ........................................................................................................ |
95 |
Караваева А. С., Морозов С. А. Совершенствование технологии |
|
штамповки детали «лапа» ....................................................................................... |
98 |
Каримов Р. Д., Вавилов В. Е., Горбунов А. С., Гусаков Д. В., Хайруллин И. |
|
Х. Намагничивающая установка............................................................................ |
102 |
Коновалов С. С., Фирсенко В. В., Шулешко Д. Г., Руцкий Д. В., Зюбан Н. А. |
|
Влияние технологии вакуумной отливки на развитие и особенности |
|
формирования внеосевой ликвационной неоднородности крупных слитков ....... |
105 |
Копылов К. А. О выявлении низкоскоростных зон процесса |
|
взаимодействия теплоносителя с пружиной в спрейере ....................................... |
109 |
Кострюков Е. Е. Методы динамической калибровки датчиков |
|
импульсного давления........................................................................................... |
113 |
Козырева Е. Н., Алиев А. В. Методы контроля утечек в магистральных |
|
нефте- и газопроводах ........................................................................................... |
115 |
Кривда А. А., Уразбахтин Ф. А. Аэродинамический нагрев головных |
|
частей ракеты ........................................................................................................ |
118 |
Кривенцева Е. Ю., Кучеров В. Г., Карлов В. И. Пути стабилизации длины |
|
отката артиллерийских орудий ............................................................................. |
119 |
Кучев П. С., Белинин Д. С., Шилов А. Ю., Щицын Ю. Д. Исследование |
|
различных схем подключения двухкамерного плазмотрона ................................ |
124 |
Манукян Д. С., Матлин М. М. Неразрушающая методика контроля предела |
|
прочности деталей болтовых соединений............................................................. |
128 |
Матвеева М. А., Чуманов И. В. Получение металлической композиции |
|
методом электрошлакового переплава.................................................................. |
131 |
Мельников А. С., Каракулов М. Н. Исследование многопарного контакта |
|
плунжерной передачи............................................................................................ |
132 |
Миронов А. Н., Алиев А. В. Метод оценки влияния возможных перекосов в |
|
телескопических соплах РДТТ на силу тяги ......................................................... |
137 |
Мышкин А. В., Муравьев О. В. Влияние конструктивных особенностей |
|
электромагнитно-акустических преобразователей на формирование диаграмм |
|
направленности ..................................................................................................... |
141 |
Назаров Н. А., Галаган Л. А. Дополнение оснастки к газобаллонному |
|
оружию для стрельбы при отрицательной температуре окружающей среды....... |
145 |
Неулыбин С. Д., Белинин Д. С., Кучев П. С., Щицын Ю. Д. Закалка |
|
тяжелонагруженных изделий на токе прямой полярности ................................... |
147 |
Нурисламова Г. М., Коленченко А. Б., Коленченко О. В. Расчет и |
|
обеспечение технологических условий обработки сложнопрофильных деталей |
|
uазотурбинного двигателя..................................................................................... |
152 |
Осокин В. М., Сальников А. Ф., Петрова Е. Н. Исследование параметров |
|
воздушного потока в сопле при взаимодействии с выдвигающимся цилиндром. 156 |
4
Петров Р. А., Бендерский Б. Я. Моделирование пространственных |
|
процессов вентиляции салона автобуса ................................................................ |
160 |
Подшивалин К. П., Тескер Е. И. Способ лазерно-плазменного нанесения |
|
покрытий на детали............................................................................................... |
164 |
Покрас И. Б., Чикуров Г. А. Устройство для экспериментального |
|
определения реологических характеристик неньютоновских жидкостей при |
|
переменных давлениях и температурах ................................................................ |
167 |
Полянских И. Н., Кугультинов С. Д. Изучение проблем технологической |
|
операции развертывания канала ствола гладкоствольного оружия ...................... |
171 |
Полтанов А. Г., Королева М. Р. Исследование газодинамических |
|
параметров в соплах с переменным критическим сечением................................. |
175 |
Пушина Е. С., Вахрушев А. В. Анализ методов и процессов перемешивания |
|
наночастиц и микрочастиц.................................................................................... |
178 |
Пушкарев М. А., Трифонов О. А. Точность токарно-винторнезных станков.. |
181 |
Русинов Г. В., Земерев Е. С., Малинин В. И., Шатров А. В. Устройство |
|
форкамеры установки синтеза нанооксида алюминия.......................................... |
184 |
Рыбин А. Н., Уразбахтин Ф. А. Особенности конструктивно- |
|
компоновочных схем головных частей ракет и ракет-носителей ......................... |
188 |
Савин С. С., Шляпугин А. Г. Особенности моделирования процесса |
|
обжима-раздачи в программе DEFORM-2D.......................................................... |
189 |
Савин Д. В., Михеев В. А. Моделирование процесса формообразования |
|
обтяжкой крупногабаритных листовых деталей обшивок сложных |
|
геометрических форм с учетом реологического состояния алюминиевого |
|
сплава .................................................................................................................... |
194 |
Сагитов Э. Г., Макушин А. А. Изменение технического состояния головки |
|
блока цилиндров дизельного двигателя и износ его деталей в процессе |
|
эксплуатации ......................................................................................................... |
201 |
Синицын А. Н., Синицына В. В., Абрамов И. В. Анализ воздействий, |
|
возникающих при различных методах сборки ...................................................... |
204 |
Слащев Е. С., Осетров В. Г. Компенсаторы непрерывного действия............. |
207 |
Слободской С. В., Михрютин В. В. Автоматизация построения модели |
|
геометрического образа режущего инструмента оснащенного СМП................... |
210 |
Слободской С. В., Михрютин В. В. Анализ направлений |
|
совершенствования режущего инструмента оснащенного СМП.......................... |
215 |
Сокотов В. А., Исаков С. Н. Колебания вертикальных роторов сортировок |
|
бумажной массы .................................................................................................... |
220 |
Сулейманова И. Р., Попов И. П. Совершенствование процессов формовки |
|
и отбортовки за один переход в конической матрице с использованием |
|
программного продукта PAM-STAMP.................................................................. |
224 |
Трефилова Т. В. Методика экспериментальных исследований кинетики |
|
коррозии материалов и сплавов в различных агрессивных средах....................... |
228 |
Трунов М. Д., Карлов В. И. Кинематическое исследование плоских |
|
механизмов второго класса средствами AUTOCAD ............................................. |
232 |
Трунов М. Д., Проничев Д. В. Моделирование термических напряжений в |
|
медно-алюминиевых слоистых композитах под действием электрического |
|
тока ........................................................................................................................ |
235 |
Уразбахтин В. Ф., Уразбахтин Ф. А. Аварии и критические ситуации при |
|
эксплуатации жидкостных ракетных двигателей.................................................. |
239 |
5
Федоровцев П. И., Земерев Е. С., Малинин В. И., Шатров А. В. Устройство |
|
||
отбора конденсированной фазы установки синтеза нанооксида алюминия ......... |
242 |
||
Фокеева Е. Н., Зорин В. А., Муравьева О. В. Контроль пруткового проката |
|
||
электромагнито-акустическим методом с использованием рэлеевских волн....... |
246 |
||
Фролова А. И., Матлин |
М. М. |
Универсальный способ оценки |
|
эффективности обработки пластическим деформированием ............................... |
250 |
||
Харинова Ю. Ю., Уразбахтин |
Ф. А. Принципы построения |
|
|
математической модели нанесения теплозащитных покрытий на поверхности |
|
||
ракет методом напыления ..................................................................................... |
|
|
254 |
Худякова М. А., Безгласный С. П. Стабилизация программных движений |
|
||
гиростата переменной структуры.......................................................................... |
|
|
256 |
Чевелева А. О., Болотов М. А., Проничев Н. Д., Болотов М. А. Разработка |
|
||
информационной модели при исследовании погрешностей координатных |
|
||
измерений геометрических параметров деталей газотурбинного двигателя........ |
260 |
||
Черемных С. Е., Гарифуллин А. Н., Тананин А. И. Влияние режима резания |
|
||
на силы резания и оптимизация процесса точения углеродистых сталей ............ |
266 |
||
Чирков Д. В., Галаган Л. А. Способы повышения устойчивости оружия со |
|
||
сбалансированной автоматикой ............................................................................ |
|
|
269 |
Шаклеин А. А., Тюрин А. П. Моделирование звукопоглощения в |
|
||
акустическом интерферометре.............................................................................. |
|
|
273 |
Шамурадов Ф. А. Исследование устройства автоматического розжига |
|
||
котельной установки с низкотемпературным кипящим слоем ............................. |
276 |
||
Шевцова О. А., Зюбан Н. А. Роль окисленности металла в формировании |
|
||
оксидных, сульфидных и оксисульфидных включений и свойств готовых |
|
||
изделий .................................................................................................................. |
|
|
279 |
Шерстобитов М. А., Михрютин В. В. Анализ формообразующих систем |
|
||
станков для обработки тонкостенных листовых заготовок сложной формы........ |
281 |
||
Широбоков В. Н., Шаврин О. И. Перспективы повышения хладостойкости |
|
||
упругих элементов деталей машин ....................................................................... |
|
|
285 |
Шулятьев М. И., Постнов А. С., Тепин Н. В., Шеногин В. П. Оценка |
|
||
упрочнения заготовки в местах изгиба при профилировании .............................. |
290 |
6
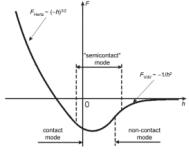
А. В. Абашева, магистрант В. В. Бесогонов, кандидат технических наук, доцент
Ижевский государственный технический университет имени М. Т. Калашникова
Исследование топологии поверхности керамики методом атомно-силовой полуконтактной микроскопии
Сканирующая зондовая микроскопия (СЗМ) ‒ один из мощных современных методов исследования морфологии и локальных свойств поверхности твердого тела с высоким пространственным разрешением. За последние годы метод превратился из экзотического, доступного лишь ограниченному числу исследовательских групп, в широко распространенный и успешно применяемый инструмент для исследования свойств поверхности. В настоящее время практически ни одно исследование в области физики поверхности и тонкопленочных технологий не обходится без применения методов зондовой микроскопии.
Пространственное разрешение атомно-силового микроскопа зависит от размера кантилевера и кривизны его острия. Разрешение достигает атомарного уровня по горизонтали и существенно превышает его по вертикали. Когда игла находится на достаточно большом расстоянии от образца, зонд слабо притягивается к образцу. С уменьшением расстояния это притяжение усиливается до тех пор, пока электронные облака иглы и атомов поверхности не начнут испытывать электростатическое отталкивание. Сила притяжения и отталкивания уравновешиваются на расстоянии порядка длины химической связи (несколько десятых нм), при меньших расстояниях доминирует отталкивание [2].
«Склеивая» потенциалы сил, действующих на различных расстояниях между образцом и кантилевером, можно получить кривую вида рис. 1, позволяющую классифицировать режимы работы атомно-силового микроскопа [2].
Рис.1. Потенциал взаимодействия зонда с образцом [2].
7
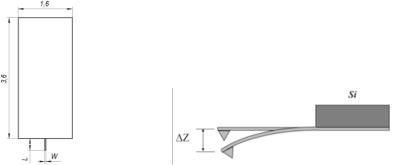
Зондирование поверхности в атомно-силовом микроскопе производилось с помощью специальных зондовых датчиков «Golden»Silicon cantilevers NSG 10, представляющих собой упругую консоль (L = 100мкм, W = 35 мкм, рис. 2) – кантилевер (cantilever) с острым зондом на конце (рис. 3). Датчик изготавлен методом фотолитографии и травления из кремниевых пластин фирмой NT-MDT (город Зеленоград, Россия).
Рис.2. Размеры кантилевера |
Рис. 3. Схематичное изображение |
|
зондового датчика АСМ [1]. |
Расчетную модель кантилевера можно представить следующим образом. Один конец консольной балки жестко закреплен на кремниевом основании ‒ держателе. На другом конце консоли располагается зонд в виде острой иглы с радиусом закругления ~50 нм в зависимости от типа зондов и технологии их изготовления. Угол при вершине зонда ‒ 22º, толщина консоли 1 мкм. Силу взаимодействия зонда с поверхностью F можно оценить из соотношения:
F = k∙ΔZ,
где k – жесткость кантилевера; ∆Z – величина, характеризующая его изгиб. Коэффициент жесткости кантилевера k в диапазоне 5,5‒22,5 Н/м в закупленной партии.
В данной работе были исследованы образцы ситалла СТ-50-1. Важнейшим параметром стеклокерамики, определяющим качество изделий, является состояние поверхности. Улучшение характеристик поверхности керамических оснований необходимо для общего повышения качества конечных изделий и перехода к фотолитографическим процессам с меньшими топологическими размерами.
При исследовании топологии поверхности были использованы два режима работы АСМ: контактный (contact mode) и полуконтактный режим
(tapping mode).
При контактном режиме расстояние от иглы до образца составляет порядка нескольких десятых нанометра. Таким образом, игла АСМ находит-
8
ся в мягком физическом контакте с образцом и подвержена действию сил отталкивания. В этом случае взаимодействие между иглой и образцом заставляет кантилевер изгибаться вверх (ΔZ откладывается от положения равновесия балки вверх, в отличие от случая, показанного на рис.3), повторяя топографию поверхности.
При полуконтактном режиме игла кантилевера в нижней точке каждого колебания, то есть колеблющееся острие слегка «стучит» по поверхности образца.
Сравнение результатов сканирования поверхности ситалла в вышеуказанных режимах АСМ показали, что полуконтактый режим дает более четкую картину топологии поверхности ситалла СТ-50-1, чем контактный. Поэтому все нижеприведенные данные относятся к режиму полуконтактной АСМ.
Процесс перемещения зонда над поверхностью в сканирующем зондовом микроскопе имеет сходство с движением электронного луча по экрану в электроннолучевой трубке телевизора. Зонд движется вдоль линии (строки) сначала в прямом, а потом в обратном направлении (строчная развертка), затем переходит на следующую строку (кадровая развертка). Движение зонда осуществляется с помощью сканера небольшими шагами под действием пилообразных напряжений, формируемых цифроаналоговыми преобразователями. Регистрация информации о рельефе поверхности производится на прямом проходе.
Информация, полученная с помощью сканирующего зондового микроскопа, хранится в виде СЗМ кадра ‒ двумерного массива целых чисел аij
(матрицы). Физический смысл данных чисел определяется той величиной, которая оцифровывалась в процессе сканирования. Каждому значению пары индексов ij соответствует определенная точка поверхности в пределах поля сканирования. Координаты точек поверхности вычисляются с помощью простого умножения соответствующего индекса на величину расстояния между точками, в которых производилась запись информации:
хi х0 i . у j у0 j
Здесь х0 и у0 – расстояния между соседними точками вдоль оси X и Y,
в которых производилась запись информации. Визуализация СЗМ кадров производится средствами компьютерной графики, в основном, в виде трехмерных (3D) и двумерных яркостных(2D) изображений с помощью программы Nova 1.0.26.1474.
В режиме полуконтактной АСМ микроскопии на атомно-силовом микроскопе SOLVER P47-PRO были исследованы ситалловые подложки СТ-50-1, обработанные лазерным излучением. Аморфизация поверхности ситалла осуществлялась на лазере Trotec Speedy 100.
Ниже представлены сканы подложки, обработанной на СО2 ‒ лазерной установке Speedy 100 при уголе падения луча на поверхность 25°.
9
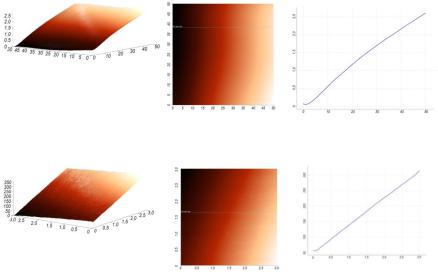
а) |
б) |
в) |
Рис. 4. Скан поверхности ситалловой подложки СТ-50-1 размером 50×50 мкм: а) ‒ 3D формат; б) ‒ 2D формат; в) – профилограмма
а) |
б) |
в) |
Рис. 5. Скан поверхности ситалловой подложки СТ-50-1 |
размером 3×3 мкм: а) |
|
|
‒ 3D формат; б) ‒ 2D формат; в) ‒ профилограмма |
Места на поверхности, в которых приведены профилограммы 4-в и 5-в указаны на рис. 4-б и 5-б горизонтальными светлыми линиями. Сравнение профилограмм показывает, что перепад высот рельефа поверхности на образце размером 50×50 мкм не заметен. При рассмотрении образца с большим разрешением (размер рассматриваемой области 3×3 мкм) видны перепады порядка 5 нм, что, в свою очередь, не несет в себе какой-либо практической значимости.
Сканирующий зондовый микроскоп позволяет выполнять работы, требующие определения характеристик материалов на атомно-молекулярном уровне и проводить их анализ.
Список литературы
1.Миронов, В.Л. Основы сканирующей зондовой микроскопии / В.Л. Миронов . - Нижний Новгород : Техносфера, 2004. – 110 с.
2.Основы СЗМ: // НТ-МДТ. [Зеленоград, 2012]. URL: http://www.ntmdt.ru/spm-basics/view/probe-sample-interaction-potential (дата обра-
щения 07.02.2013).
10
А. Н. Аникеев, аспирант
И. В. Чуманов, доктор технических наук, профессор Южно-Уральский государственный университет, г. Челябинск
Влияние концентрации дисперсных частиц WC на предел прочности центробежно-литых заготовок
Исследование влияния дисперсных частиц тугоплавких карбидов на механические свойства металлов является актуальным в области металлургии и машиностроения. Известно, что такие частицы, введенные в
металл, существенно повышают его физико-механические свойства [1]. Как правило, введение частиц в жидкий металл связано с трудностью их распределения по объему получаемого материала (вследствие разности плотностей), что приводит к непрогнозируемому изменению концентрации в различных объемах получаемого металла. Произвольное распределение частиц приводит к непрогнозируемому изменению свойств металла в различных объемах.
Для обеспечения возможности управлять распределением частиц был разработан способ введения частиц при разливке на машине центробежного литья [2] и проведена серия экспериментов по получению упрочненных заготовок [3, 4].
В результате проведения серии экспериментов были получены 8 цен- тробежно-литых заготовок с различным содержанием карбидов вольфрама (табл. 1).
Таблица 1. Количество упрочняющей частицы введенной в формируемые
заготовки
№ плавки |
1 |
2 |
3 |
4 |
5 |
6 |
7 |
8 |
|
Количество карбидов |
0 |
40 |
80 |
120 |
0 |
120 |
240 |
360 |
|
вольфрама, г. |
|||||||||
|
|
|
|
|
|
|
|
||
Общее кол-во карби- |
|
|
|
|
|
|
|
|
|
дов по отношению к |
0 |
0,4 |
0,8 |
1,2 |
0 |
1,2 |
2,4 |
3,6 |
|
массе слитка, % |
|
|
|
|
|
|
|
|
Из полученного материала были вырезаны образцы для исследования концентрации частиц в различных сечениях полученных заготовок, а также
Физико-механических свойств, в частности, предела прочности. Образцы вырезались с внешней и внутренней поверхности заготовки, а также из центра. Исследование распределения проводила на электронном микроскопе «JEOL» JSM –6460 LV.
Исследование показало, что распределение по сечению полученных заготовок не равномерно: повышенное содержание введенных частиц наблюдается на внешней поверхности полученных заготовок, которое уменьшается в направлении от внешней поверхности к внутренней. Результаты исследования распределения карбидов вольфрама по сечениям
11
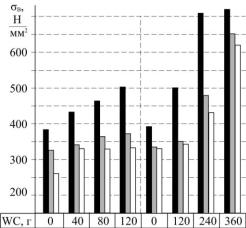
полученных заготовок представлены в табл. 2.
Таблица 2. Плотность распределения частиц карбида вольфрама по сечению
полученных заготовок
№ заготовки |
1 |
2 |
3 |
4 |
5 |
6 |
7 |
8 |
Внешняя поверхность |
0 |
0,4 |
0,6 |
2,5 |
0 |
2,8 |
5,1 |
5,1 |
заготовки, шт./мкм2 |
||||||||
Середина заготовки, |
0 |
0 |
0 |
0 |
0 |
0 |
2,6 |
3,5 |
шт./мкм2 |
||||||||
Внутренняя поверх- |
|
|
|
|
|
|
|
|
ность заготовки, |
0 |
0 |
0 |
0 |
0 |
0 |
0,5 |
3,4 |
шт./мкм2 |
|
|
|
|
|
|
|
|
Для исследования предела прочности использовалась разрывная машина типа УТС 110М–5. На основании полученных данных была построена диаграмма, отражающая предел прочности полученных заготовок в различных сечениях (рис. 1).
Исследование показало, что введение дисперсных частиц карбидов существенно повлияло на предел прочности полученного металла: в различных сечениях полученных заготовок предел прочности различен. В результате анализа полученных данных, выявлено, что даже в заготовках, не имеющих в своем составе дисперсных частиц карбидов, предел прочности по сечению различен. Так, для образцов с внешних поверхностей заготовок 1 и 5 характерно увеличение исследуемого параметра по сравнению с образцами вырезанных из середины и внутренней поверхности тех же заготовок. Это объясняется более мелкой кристаллической структурой, полученной вследствие быстрой кристаллизации в начальные моменты разливки.
Рис. 1. Диаграмма предела прочности полученного материала: темный – внешняя сторона; серый – середина;
белый – внутренняя сторона заготовок.
12
Таким образом, экспериментально доказано, что дисперсные частицы карбидов вольфрама, введенные в кристаллизующийся расплав при разливке на машине центробежного литья, существенно повышают предел прочности получаемого металла.
Работа выполнена в рамках государственного задания Министерства образования, шифр 7.2938.2011, а также поддержана РФФИ, проект №
12-08-00896.
Список литературы
1.Гольдшмидт, Х.Д. Сплавы внедрения / Х.Д. Гольдшмидт. – М.: Мир, 1971. –
464 с.
2.Патент РФ 2381087 МПК В 22 D 13/02 Способ формирования трубной заготовки / В.И. Чуманов, И.В. Чуманов, Д.А. Пятыгин, Р.Р. Гарифулин, О.Ю. Вершинина, А.Н. Аникеев. – №2008128677/02; заявл. 14.07.2008.; опубл. 10.02.2010.– 5 с.
3.Чуманов, И.В. Упрочнение металлических материалов дисперсными тугоплавкими частицами / И.В. Чуманов, В.И. Чуманов, А.Н. Аникеев // Проблемы черной металлургии и материаловедения. - 2010. - №1. – С. 24-28.
4.Чуманов, И.В. Получение дисперсно–упрочненных полых заготовок для роторных диспергаторов / И.В. Чуманов, В.И. Чуманов, А.Н. Аникеев // Металлург. - 2011. - №6. – С.69–72.
В. В. Байков, магистрант; А. В. Матвеев, магистрант В. Ф. Даненко, кандидат технических наук, доцент
Волгоградский государственный технический университет
Устройство для механического удаления окалины с поверхности катаной стальной заготовки
Удаление окалины с поверхности заготовки является актуальным в области обработки металлов давлением, в частности перед волочением. Изза дороговизны и вредности химического метода наиболее перспективным считается механическое удаление окалины. Применение механического удаления окалины позволяет получить большую экономию в результате сокращения расхода дорогостоящих кислот и металла, снижения эксплуатационных расходов и высвобождения рабочей силы. Кроме того, оно позволяет оздоровить водный и воздушный бассейны и уменьшить производственную площадь для оборудования.
Известна схема приспособления для механического удаления окалины, состоящая из калибрующей волоки, вращающегося патрона с резцами для нанесения на поверхность заготовки спиральной нарезки и волоки для строжки (скальпирования) заготовки [1]. Реализация этой схемы возможна с помощью устройства для зачистки поверхности длинномерных изделий [2].
13
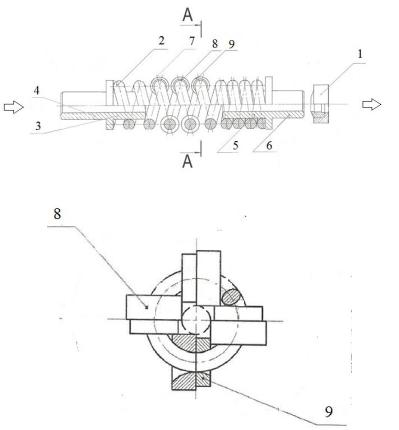
Конструкция устройства обеспечивает зачистку поверхности режущими дисками, установленными на витках пружины, при их вращении вокруг заготовки (рис. 1). Стрелкой показано направление движения стальной заготовки. Устройство для зачистки поверхности содержит рабочий стол, на котором установлена волока для скальпирования 1 и пружина сжатия 2, в полости которой со стороны переднего конца с натягом установлена входная направляющая втулка 3 с передним хвостовиком 4, а со стороны заднего конца - выходная направляющая втулка 5 с задним хвостовиком 6. На передних рабочих витках пружины 2 со стороны входной втулки 3 направляющие ролики 7 и далее зачистные элементы в виде режущих твердосплавных дисков 8, установленных с возможностью вращения вокруг своей оси, между которыми располагаются разделительные элементы в виде стружколомающих шайб 9 (рис. 2).
Рис. 1. Устройство для зачистки поверхности длинномерных изделий
Рис 2. Разрез А-А
14
На конце переднего хвостовика 4 установлен ременной шкив, получающий вращение от двигателя (не показаны). Направляющие втулки 3 и 5 и волока для скальпирования 1 установлены соосно. Посадочные отверстия режущих дисков 8 выполнены воронкообразными с наименьшим диаметром, равным диаметру витка пружины 2, при этом образующая стенки воронки выполнена выпуклой по дуге с радиусом, равным внутреннему радиусу витка пружины (рис. 2).
Конструкция устройства обеспечивает разделение процесса зачистки поверхности на два этапа: а) грубая зачистка поверхности режущими дисками, установленными на витках пружины, при их вращении вокруг заготовки; б) тонкая зачистка поверхности, при протягивании заготовки через волоку для скальпирования. Это позволяет уменьшить глубину резания режущими дисками, что снижает силы резания и повышает долговечность режущего инструмента, и повысить качество обрабатываемой поверхности. Волоки для скальпирования могут изготавливаться из изношенных твердосплавных волок. Для этого стачивают выходную зону волоки до создания режущей кромки, а затем шлифуют калибрующую зону на заданный размер.
Устройство было опробовано при удалении окалины и обезуглероженного слоя с бунтовой катанки диаметром 6,5 мм из углеродистой стали 35. На витки входной части пружины устанавливались направляющие ролики с образованием внутренней полости диаметром D=6,5 мм, затем режущие диски с образованием внутренней полости диаметром d=6,2 мм. Диаметр волоки для скальпирования составлял 6,0 мм. После сборки ротора, закрепления пружины на направляющие втулки и проталкивания подготовленного конца заготовки через отверстия этих втулок и волоки для скальпирования осуществлялось включение привода вращения ротора с частотой до 3000 об/мин и протягивание проволоки через устройство со скоростью 40 м/мин. В процессе эксплуатации рабочая часть пружины и волока для скальпирования обильно поливались СОЖ.
На этапе грубой зачистки происходило уменьшение сечения с 6,5 до 6,2 мм. При этом осуществлялось удаление основного дефектного слоя и образование спиральной канавки. На этапе тонкой зачистки происходило уменьшение сечения с 6,2 до 6,0 мм. При этом осуществлялась калибрование профиля с целью придания точных размеров. Спиральная канавка на поверхности заготовки способствовала образованию сыпучей стружки, а также облегчала условия работы волоки для скальпирования.
Целью дальнейших исследований является обеспечение возможности радиальной настройки режущих дисков по мере их износа в процессе эксплуатации.
15
Список литературы
1.Хаяк, Г.С. Инструмент для волочения проволоки / Г.С. Хаяк. – М.: Металлургия, 1974. – 128 с.
2.Патент на полезную модель № 123693, Российская Федерация, МПК В08В 1/00. Устройство для зачистки поверхности длинномерных изделий / В. Ф. Даненко, А. В. Скрипников, В. А. Павлов, Н. В. Бурыкина, С. В. Чечин, В. В. Байков ; заявитель и патентообладатель ФГБОУ ВПО «Волгоградский государственный технический университет». - №2012120942/05; заяв. 22.05.12; опубл. 10.01.13, Бюл. № 1.
И. А. Башкиров, магистрант
А. Н. Терентьев, кандидат технических наук, доцент Ижевский государственный технический университет
имени М. Т. Калашникова
Исследование характеристик газораспределительного механизма ДВС
Исследование характеристик газораспределительного механизма актуально в области автомобилестроения. Исследование основывается на поиске оптимального альтернативного механизма газораспределения, который улучшит показатели двигателя. Существует методика для расчета рабочего процесса двигателя внутреннего сгорания, которая учитывает особенности механизма газораспределения, а именно это высота подъема клапана и фазы открытия и закрытия клапанов механизма.
В поршневом двигателе внутреннего сгорания (ДВС) все рабочие процессы превращения химической энергии сжигаемого топлива в механическую работу коленчатого вала происходят внутри двигателя за счет воз- вратно-поступательного движения поршней в цилиндрах [1].
Газораспределительный механизм (ГРМ) является основным устройством, обеспечивающим работу поршневого ДВС.
Не секрет, что для оптимальной работы двигателя нужно управлять фазами газораспределения в зависимости от частоты вращения, положения и нагрузки коленчатого вала. Традиционный кулачковый распределительный вал не позволяет решить эту задачу.
Незначительные изменения соотношения фаз газораспределения можно создавать с помощью механических, электромеханических, гидравлических, пневматических приводов клапанов. Но наиболее перспективным считается электромагнитный привод, управляемый электроникой. С его помощью можно добиться оптимизации работы двигателя и расширить его функциональные возможности. Например, изменяя порядок работы клапанов можно добиться равномерной работы при переменных нагрузках, сокращения расхода топлива на максимальных оборотах при задан-
16
ной мощности.
Электромагнитный привод клапанов представляет собой подпружиненный клапан, помещенный между двумя электромагнитами, которые удерживают его в крайних положениях: закрытом или полностью открытом. Специальный датчик выдает блоку управления информацию о текущем положении клапана. Это необходимо для того, чтобы снизить до минимальной его скорость в момент посадки в седло.
Якорь электромагнита состоит из двух пружин для открытия и закрытия клапана. Когда электрический ток еще не подведен к электромагнитам, клапан находится в среднем положении, при этом он полуоткрыт, что позволяет легко раскручивать коленчатый вал во время пуска двигателя. При достижении необходимой частоты вращения блок управления подает сигнал и в верхний электромагнит открытия подается электрический ток, клапан закрывается. Одновременно осуществляется впрыск топлива.
При открывании клапана прерывается подача напряжения в верхний электромагнит. Энергия, накопленная в верхней пружине, движет клапан вниз до тех пор, пока накопленная энергия полностью не израсходуется. Для дальнейшего перемещения клапана вниз напряжение подается в нижний электромагнит и якорь, втягиваясь под действием магнитного поля, открывает клапан. При этом, учитывая потери энергии пружины в конце ее движения, в нижний электромагнит кратковременно подается ток повышенной силы, до тех пор, пока клапан полностью не откроется.
Информация для блока управления поступает от датчика оборотов коленчатого вала. Для каждого клапана компьютер определяет начало его открытия и закрытия, а значит и ход, в зависимости от положения коленчатого вала.
Расчеты работы ДВС с электромагнитным приводом клапанов проводятся по методике теплового расчета на основе безразмерных дифференциальных уравнений [2]. Подобная система пригодна одновременно для расчета и анализа рабочих процессов в ДВС, так как уравнения включают взаимозаменяемые слагаемые, что позволяет получить соотношение, связывающее непосредственно давление и объем, то есть описывающие индикаторную диаграмму.
Так же говоря о фазах газораспределения имеют ввиду и ход клапана, для оптимальной работы двигателя необходимо мгновенное открытие и такое же мгновенное закрытие клапанов в нужный момент. Отобразим такой ход клапана на рис. 1а.
Но в силу того что мгновенное срабатывание невозможно, в особенности с механическим приводом клапанов от распределительного вала, который перемещает клапан как показано на рис. 1б, близким к быстрому срабатыванию является электромагнитный привод клапанов (рис. 1в).
17
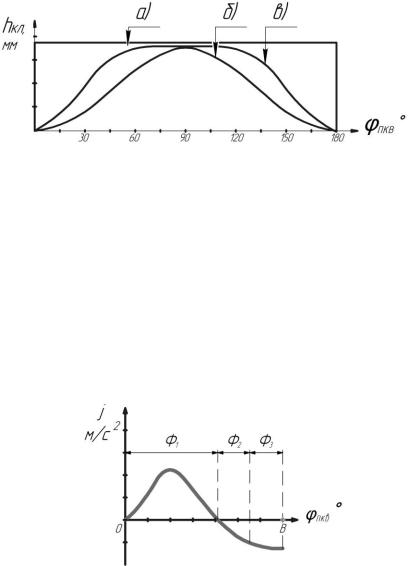
Рис.1. Графики перемещения клапана
Расчет толкателя начинают с построения диаграммы ускорений клапана. По выбранному закону изменения ускорений определяют законы изменения скорости перемещения клапана. Для получения этих законов используют графоаналитические методы, методы графического интегрирования и дифференцирования.
Для проектирования «виртуального» безударного кулачка изначально задаем фазы газораспределения пр , зп , p0 , максимальную высоту
подъема клапана hкл max и толкателя hт max . Определяем закон изменения
ускорения толкателя, при котором положительные ускорения не превышают 1500-3500 м/с2, а отрицательные не превышают 500‒1500 м/с2 [3].
Графики ускорения «виртуального» безударного кулачка клапана должны, по возможности, иметь плавно изменяющийся профиль, как на рис. 2.
Рис. 2. График ускорения клапана
График ускорения «виртуального» безударного кулачка состоит из трех участков: 1) положительных ускорений Ф1, 2) первого участка отрицательных ускорений Ф2, 3) второго участка отрицательных ускорений Ф3.
В первом приближении угловая протяженность Ф1, Ф2, Ф3 различных участков ускорения толкателя, в случае с электромагнитным приводом
18
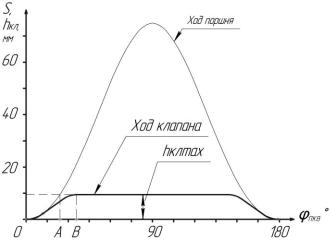
клапанов, будет определяться графическим методом, путем наложения графика перемещения поршня и графика перемещения клапана.
Рис. 3. Графическое построение графика перемещения клапана
Максимальная высота подъема клапана определяется конструктивными размерами электромагнита и механических элементов ГРМ в составе конкретного ДВС.
Длительность B находим путем проведения касательной линии к графику перемещения поршня на середине участка OA, где точка A определяется точкой пересечения хода клапана с ходом поршня, тогда:
В Ф1 Ф2 Ф3
И согласно [3]:
Ф2 ( 0,10 0,25 ) Ф3 |
(3) |
Ф2 Ф3 (1,5 3,0 ) Ф1 |
(4) |
После выбора угловой протяженности расчеты кинематики толкателя проводятся по методике, описанной в литературе [3].
В результате проведенных расчетов получены следующие характеристики двигателя с механическим и электромагнитным приводом клапанов.
Таблица. Сравнение полученных выходных характеристик
|
Механический |
Электромагнитный при- |
|
|
привод клапанов |
вод клапанов |
|
Эффективная мощность |
116 кВт |
121 кВт |
|
Эффективный удельный |
213, 4 г/кВт·ч |
189,5 г/кВт·ч |
|
расход топлива |
|||
|
|
19
Рассмотренную методику предлагается применять для расчетов ДВС с электромагнитным приводом клапанов. Исходя из расчетных данных электромагнитный привод клапанов позволяет повысить мощность двигателя до5% и снизить удельный расход топлива до 10 %.
Список литературы
1.Соснин, Д.А. Новейшие автомобильные электронные системы / Д.А. Соснин, В.Ф. Яковлев . - М : СОЛОН-Пресс, 2005. – 240 с.
2.Тойменцев, А.С. Исследование изменения фаз газораспределения и высоты подъема клапана: дис. маг. техники и технологии.: защищена 23.06.09. Ижевск:
ИжГТУ, 2009.
3.Колчин, А.И. Расчет автомобильных и тракторных двигателей / А.И. Колчин, В.П. Демидов. - М : Высшая школа, 2002. – 495 с.
Д. С. Белинин, аспирант; Ю. Д. Щицын, доктор технических наук, профессор П. С. Кучев, аспирант; С. Д. Неулыбин, магистрант
Пермский национальный исследовательский политехнический университет
Упрочнение рабочих поверхностей изделий методом плазменной поверхностной закалки на токе обратной полярности
Низкотемпературная плазма относится к концентрированным источникам энергии и находит все большее применение для поверхностного упрочнения деталей машин и инструмента из различных сплавов. При закалке концентрированными источниками энергии в силу высоких скоростей нагрева и охлаждения удается получить такую структуру и свойства поверхностного слоя, которые недостижимы при традиционных способах термической обработки.
Сущность плазменной закалки заключается в высокоскоростном локальном нагреве участка поверхности до высоких температур и последующим охлаждением со сверхкритической скоростью за счет теплоотвода во внутренние слои материала изделия. При этом формируется структура с высокими эксплуатационными характеристиками.
Основные преимущества плазменной закалки:
‒локальность нагрева, упрочняется только поверхностный слой, а сердцевина остается вязкой, что обусловливает повышенное сопротивление износу и усталости;
‒высокая твердость и износостойкость упрочняемой поверхности;
‒отсутствие или минимальные деформации упрочняемых деталей, что позволяет снизить трудоемкость механической обработки и затраты на изготовление деталей;
20
‒при закалке без оплавления поверхности не требуется последующая механическая обработка (шлифовка), т.е. плазменную закалку можно использовать как финишную операцию;
‒отсутствие необходимости применения охлаждающих среды и приспособления.
‒возможность замены дефицитных высоколегированных сталей на низколегированные, упрочненные плазменной закалкой;
‒возможность замены износостойких сталей на низкоуглеродистые с наплавленным рабочим слоем, упрочненным плазменной закалкой;
‒возможность закалки локальных участков поверхности (кромки дисковых ножей, вырубных и гибочных штампов, зубьев пил, шин электро- и бензопил, места под манжеты, подшипники, прокатные валки и т.д.);
‒возможность автоматизации процесса и включение закалочных установок в состав гибких производственных систем, автоматических линий.
По сравнению с лазерной закалкой плазменная имеет следующие преимущества:
‒стоимость оборудования такой же мощности на порядок ниже;
‒простота работы на установке и ее обслуживания;
‒мобильность установки, возможность перемещения оборудования и быстрого монтажа на любом станке, обеспечивающем нужную скорость вращения детали или перемещения плазмотрона;
‒не требуется наносить на поверхность специальные покрытия для увеличения поглощательной спсобности;
‒высокий КПД, достигающий 85 %;
‒возможность плавного регулирования в процессе закалки параметров режимов в широких пределах, т.е. изменения глубины, ширины, структуры и свойств закаленной зоны.
К недостаткам плазменной закалки относятся:
‒частичный отпуск в местах наложения закаленных полос;
‒необходимость зачистки поверхности закаливаемых изделий от различных загрязнений;
‒необходимость принудительного охлаждения изделий малого диаметра и малой толщины для получения высокой твердости поверхности.
Одним из путей устранения недостатков плазменной поверхностной закалки видится применение плазменной дуги прямого действия обратной полярности (рис. 1).
21
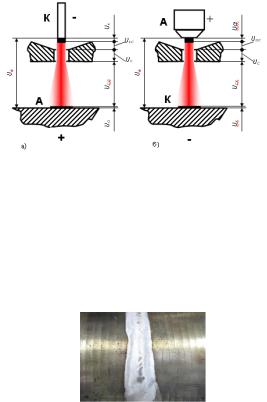
Рис. 1. Структурная модель плазменной дуги прямого действия ( а – прямая полярность; б – обратная полярность)
Использование обратной полярности позволяет, за счет эффекта катодной очистки, проводить активацию поверхности. Также эффект катодной очистки позволяет значительно снизить требования к чистоте обрабатываемой поверхности (рис. 2). Широкие возможности регулирования мощности сжатой дуги и тепловложения в обрабатываемое изделие позволяют избежать необходимости принудительного охлаждения малогабаритных деталей и тонкостенных изделий.
Рис. 2. Внешний вид поверхности подвергнутой плазменной закалке на токе обратной полярности
Накопленный опыт по практическому применению плазменного поверхностного упрочнения позволяет выделить следующие варианты:
‒упрочнение без оплавления и с оплавлением поверхности детали;
‒упрочнение с зазором между упрочненными зонами (ЗТВ), без перекрытия ЗТВ и с перекрытием ЗТВ;
‒химико-термическая плазменная обработка;
‒упрочнение в сочетании с другими способами объемной или поверхностной термической обработки.
Технологические параметры процесса плазменной поверхностной закалки включают в себя величину и полярность тока дуги, скорость вращения изделия(скорость перемещения плазмотрона), расход плазмообразующего и защитного газа.
Обработка без оплавления как правило не меняет параметров шероховатости обрабатываемой поверхности и является финишной. Вариант же с оплавлением поверхности применяется в случае необходимости получе-
22
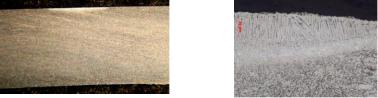
ния более глубоких, нежели без оплавления, упрочненных слоев.
В данной работе исследовали особенности плазменной поверхностной закалки на токе обратной полярности изделия из стали мартенситного класса 15Х5М с толщиной стенки 5 мм.
Плазменная закалка осуществляется путем сканирования сжатой дуги или плазменной струи по поверхности изделия (рис. 2.)
Исследования проводились в двух вариантах:
1.Плазменная поверхностная закалка на токе обратной полярности без оплавления поверхности (рис. 3).
2.Плазменная поверхностная закалка на токе обратной полярности с оплавлением поверхности (рис. 4).
При внешнем осмотре образцов установлено:
‒ ширина упрочненной зоны образца обработанного по варианту № 1 порядка 15–20 мм; изменение рельефа поверхности не происходит, поверхность разных оттенков светло-серого цвета, изменение цвета наблюдается в виде неравномерной пятнистости
‒ ширина упрочненной зоны образца обработанного по варианту № 2 порядка 20 - 22 мм.; рельеф поверхности изменен до небольшой шероховатости, по центру дорожки проходит полоса шириной примерно 5 мм со следами направленной кристаллизации и наличием небольшого усиления
врайоне начала шва. Поверхность дорожки серого цвета.
Вид макрошлифов исследуемых образцов представлен на рис. 3 и 4.
Рис. 3. Вид макро- и микроструктуры образца № 1
При просмотре макрошлифов под микроскопом было установлено, что на всех исследованных образцах имеются следы поверхностного нагрева, зоны нагрева различны по степени изменения структуры, ширине и глубине. Пор, раковин и плен на макрошлифах не обнаружено.
Результаты замера геометрических параметров зон приведены в табл. 1.
Таблица 1. Геометрические характеристики упрочненной зоны
№ образца |
Глубина, мм |
Ширина обработанной зоны, мм |
|
|
|
1 |
0,5 |
15–20 |
|
|
|
2 |
3,5 |
20‒22 |
|
|
|
При анализе микроструктуры выявлено, что микроструктура упроч-
23
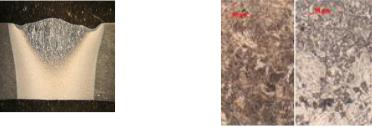
ненного слоя образца № 1 является структурой пластинчатого типа с равномерно распределенными отдельными зернами белой травимости (предположительно, феррита) (рис. 3). Остальная часть обработанной зоны представляет собой дисперсную феррито-карбидную смесь (предположительно, сорбит). Глубина обработанной зоны составляет 0,5 мм.
Рис. 4. Вид макро- и микроструктуры образца № 2
Для образца № 2: дорожка выполнена с расплавлением. В зоне расплавления структура мартенситного типа с пластинчатыми выделениями фазы белой травимости (феррита). В зоне термовлияния – ферритокарбидная смесь сорбитного типа. Результаты замеров микротвердости закаленного слоя представлены в табл. 2.
Таблица 2. Микротвердость упрочненного слоя
|
Микротвердость по зонам, Нμ50, кгс/мм2 |
|
|||
№ |
зона обработки/зона |
ЗТВ вблизи гра- |
|
основной |
|
образца |
кристаллизации рас- |
ЗТВ |
|||
ницы сплавления |
материал |
||||
|
плавленной ванны |
|
|||
|
|
|
|
||
|
|
|
|
|
|
1 |
256…412 |
‒ |
‒ |
159…198 |
|
2 |
395…410 |
405…411 |
270…399 |
||
|
|||||
|
|
|
|
|
Из анализа микротвердости закаленных слоев можно сделать вывод, что на всех образцах в зоне обработки значения твердости выше значений твердости основного материала. В случае с оплавлением поверхности в зоне кристаллизации расплавленной ванны значения твердости выше, чем в ЗТВ. В зоне термовлияния (структура на всех образцах представляет собой феррито-карбидную смесь сорбитного типа) по мере удаления от границы сплавления твердость плавно снижается.
Заключение:
Плазменная поверхностная закалка на токе обратной полярности может проводиться как в варианте с оплавлением, так и без оплавления поверхности и позволяет упрочнять как малогабаритные и тонкостенные изделия так и крупногабаритные конструкции в зависимости от требований к прочностным и геометрическим характеристикам упрочненного
24
слоя.
Применение обратной полярности позволяет, при обработке без оплавления поверхности, достичь резкого изменения структуры приповерхностного слоя и получать тонкие упрочненные слои глубиной до 0,5 мм. Обработка с оплавлением поверхности позволяет достичь глубины упрочненного слоя более 3 мм.
В зависимости от варианта обработки значения твердости упрочненной зоны возрастают примерно в 1,5–2,5 раза по сравнению с основным материалом.
Список литературы
1.Лещинский, Л.К. Плазменное поверхностное упрочнение / Л.К. Лещинский, С.С. Самотугин, И.И. Пирч. - Киев : Тэхника, 1990. – 109 с.
2.Дресвин, С.В. Физика и механика низкотемпературной плазмы / С.В. Дресвин, А.В. Донской, В.М. Гольдфраб, В.С. Клубникин. - М : Атомиздат, 1972. – 352 с.
3.Быховский, Д.Г. Энергетические характеристики плазменной дуги при сварке на обратной полярно-сти / Д.Г. Быховский, В.М. Беляев // Автоматическая сварка. - 1971. - №5. – С. 27-30.
А. М. Бербек, кандидат технических наук В. И. Малинин, доктор технических наук, профессор
Р. В. Бульбович, доктор технических наук, профессор Пермский национальный исследовательский политехнический университет, Пермь
Расчет процессов в камере сгорания ракетного двигателя на порошкообразном алюминии и воде
При проектировании многозонной камеры сгорания (КС) ракетного двигателя на порошкообразном алюминии и воде, добываемой на космическом объекте [1], требуется расчетная методика, позволяющая оценить массогабаритные характеристики камеры. Ниже приведена методика оценочного расчета процессов в КС, состоящей из форкамеры (ФК) и основной камеры.
Рассматривается течение реагирующей смеси капель воды и газа, содержащего продукты первичного сгорания алюминия в форкамере, пары испарившейся воды и продукты сгорания в основной зоне. Скорость процессов считается минимальной, чтобы рассмотреть наихудший по габаритам (длине) вариант КС.
Принимаются два упрощающих предположения:
1. Лимитирующим процессом в основной зоне КС является испарение
25

капель воды.
2. Расход испарившейся (и вступившей в химическую реакцию) воды вдоль камеры сгорания увеличивается линейно.
Расход поданной через форсунки и испарившейся воды вдоль камеры сгорания определяется выражением:
где
ную
|
|
|
|
GH O x GH O |
x / lc GH |
O |
, |
(1) |
|||
|
|
|
|
|
|
c |
|
fc |
|
|
|
|
|
|
|
2 |
|
2 |
2 |
|
|
|
|
c |
O и |
fc |
|
– общий расход воды, поданный соответственно в основ- |
|||||||
GH |
GH |
O |
|||||||||
2 |
|
2 |
|
|
|
|
|
|
|
|
|
зону КС и форкамеру, lc |
– длина основной зоны КС. |
|
|||||||||
Скорость потока определяется по формуле: |
|
|
|
||||||||
|
|
|
|
|
f |
Gec GH2O x |
|
|
|
||
|
|
|
|
|
|
|
, |
|
|
(2) |
|
|
|
|
|
|
f |
|
|
|
|||
|
|
|
|
|
|
* Fк |
|
|
|
где Gec – расход земных компонентов топлива, Fк – площадь проходного сечения основной зоны камеры сгорания; f * f (1 Z f ) – плотность
потока с учетом доли к-фазы Z; f pк / Rf Tf – плотность газового
потока (Rf , Tf – газовая постоянная и температура потока соответственно). Значения Z, Rf и Tf от L (отношения расходов внеземных компонентов топлива GH2O x к земным Gec в основной зоне) получены в результате
выполнения расчетов в программе «АСТРА.4» [2].
Максимальный диаметр капель D0 max , образующихся при подаче из форсунок воды в поток газа, с учетом того, что число Вебера не превышает свое максимальное критическое значение ( Weкрmax =14), равен:
D0 max Weкрmax u0 2 f *
где ‒ коэффициент поверхностного натяжения воды; u – скорость обду-
ва капли (определяется векторным вычитанием скоростей капли vк и по-
|
|
|
|
|
|
|
тока v f ). В начальный момент времени скорость капли равна скорости |
||||||
|
|
|
|
|
|
|
истечения струи из форсунки |
vф , соответственно, начальная скорость об- |
|||||
|
|
|
|
|
|
|
дува капли u0 : |
u0 |
vф |
v f 0 . |
|
|
|
Результаты оценки максимальных |
Dmax и |
Dm медианных диаметров |
||||
|
|
|
|
|
0 |
0 |
образующихся капель воды для разных мест установки (расстояние форсунок от начала основной зоны lф) и углов распыливания форсунок приведены в табл. 1.
Для оценок были назначены значения: расходонапряженности Gуд0 (суммарный расход компонентов через единицу площади поперечного сечения цилиндрической части форкамеры) – 350 кг/м2, давление в форкамере p0 – 0,25 МПа. Отношение расходов окислителя к горючему для камеры сгорания в целом равно 3.
26
Принятое значение расходонапряженности получается при назначении начальной скорости смеси алюминия и компонентов, в которых происходит его воспламенение, в начальном сечении ФК, равной 10 м/с, что обеспечит стабилизацию пламени в соответствии с данными [1].
Таблица 1. Максимальный и медианный диаметры образующихся капель воды в зависимости от скорости обдува при р0 = 0,25 МПа, ф = 45 м/с, Weкрmax = 14
|
lф, м |
|
0,1 |
0,35 |
0,6 |
Угол распыливания форсунки |
150 |
120 |
90 |
||
Скорость потока f |
50 |
80 |
90 |
||
|
u, м/с |
|
92 |
106 |
100 |
Dmax / Dm |
, мкм |
320/160 |
240/120 |
270/135 |
|
0 |
0 |
|
|
|
|
Задача испарения капель воды решается при допущениях, принятых выше, и дополнительных: движение капель происходит в плоскости, проходящей через форсунку и продольную ось камеры сгорания; движение потока продуктов горения и испарения капель происходит вдоль оси камеры со скоростью vf; потери тепла в стенку, как путем конвективного теплообмена, так и радиационным путем, не учитываются; капли друг с другом не взаимодействуют; частицы Al2O3, образующиеся в газовом потоке в результате реакций, малы, находятся в тепловом и скоростном равновесии с газовым потоком и не взаимодействуют с каплями воды.
За основу описания испарения капель воды принята методика, приведенная в [3]. В соответствии с принятым подходом и допущениями, записана система дифференциальных уравнений и начальных условий, описывающая движение и испарение капель в основной зоне горения.
Уравнение испарения капли:
( D / D0 ) |
d( D / D0 ) |
Kv |
Nu |
|
|
|
|
. |
(3) |
||
d |
D 2 |
||||
|
|
|
0 |
|
|
Уравнение движения капли вдоль оси x (продольной оси КС):
dvкx |
B v |
|
v |
|
2 D |
/ D . |
(4) |
d |
|
|
|||||
|
f |
|
кx |
0 |
|
|
|
|
|
|
|
|
Уравнение движения капли вдоль оси y (перпендикулярно оси КС):
|
|
dvкy |
B v 2 |
D / D . |
|
(5) |
|
|
|
|
|
||||
|
|
d |
кy |
0 |
|
|
|
|
|
|
|
|
|
||
Начальные условия: |
|
|
|
|
|
|
|
при 0 vкx vфx , vкy vфy |
, D D0 , |
x x0 |
, y 0 . |
|
(6) |
||
Здесь – время; vкx ,vкy |
– компоненты скорости капли вдоль осей x и y |
||||||
соответственно; В – параметр; Nu – критерий Нуссельта; K |
v |
– константа |
|||||
|
|
|
|
|
|
|
испарения; vf, D, u описаны ранее; индекс 0 относится к начальному значению, ф – к форсунке, к – к капле, f – к потоку.
27

Параметр В в уравнениях (4), (5) рассчитывается по формуле:
|
3 |
|
|
|
|
|
|
|
B |
|
C |
|
|
* |
|
|
|
|
|
|
f |
|
ж |
|||
|
4 |
|
f |
|
|
D |
|
|
|
|
|
|
|
|
|||
|
|
|
|
|
|
|
0 |
|
,
где Cf – коэффициент сопротивления движению капли (определяется по стандартной методике). За величину коэффициента принимается его среднее значение во время испарения капли, равное примерно 0,7. Учитывается влияние на коэффициент процессов испарения капли и ее деформации.
Зависимость коэффициентов вязкости и теплопроводности f от L получена в результате выполнения термодинамических расчетов в программе «АСТРА.4» [2]. Расход рассчитывается по формуле (1). В
результате преобразований уравнение испарения капли (3) примет следующий вид:
( D / D )0 ,5 |
|
d( D / D ) |
|
С u 0 ,5 |
|
||
0 |
|
|
. |
(7) |
|||
d |
D 1,5 |
|
|||||
0 |
|
|
a( L ) |
|
|||
|
|
|
|
0 |
|
|
|
В уравнении (7) константа С определяется через параметры в начальном сечении основной зоны горения, значения которых получены расчетным путем в программе «АСТРА.4» [2]. Значения плотности ж , теплоты
испарения Qисп воды и функции Ф взяты из [3]: |
|
|
|
|
|
|
|
|
|
|
||||||||||||||||
|
|
|
|
|
|
|
|
|
|
|
|
|
T ) Ф /( |
|
)0 ,5 |
|
|
|
|
|||||||
|
|
|
|
1,1 |
f |
( T |
f |
|
|
|
|
|
||||||||||||||
|
|
С |
|
|
|
|
|
|
|
|
к |
|
|
|
|
|
с 0 |
. |
|
|||||||
|
|
|
|
|
|
|
|
|
ж |
Qисп |
|
|
|
|
|
|
|
|||||||||
|
|
|
|
|
|
|
|
|
|
|
|
|
|
|
|
|
|
|
|
|
||||||
Численное значение константы С равняется: |
|
|
|
|
|
|
|
|
|
|||||||||||||||||
С |
1,1 0,245 (2360 400) 0,56 |
|
|
1,17 10 |
5 |
[м/(с0,5)]. |
|
|||||||||||||||||||
|
(1,25 10 4 )0,5 |
1 103 2,26 106 |
|
|
|
|
||||||||||||||||||||
Функцию а(L) определим следующим образом: |
|
|
|
|
|
|||||||||||||||||||||
|
|
|
|
|
|
|
|
|
|
|
|
|
|
0,5 |
|
|
|
|
f |
(Tf |
Tk ) Ф |
|
||||
|
|
|
|
|
|
|
|
|
|
|
|
|
|
|
|
|||||||||||
a(L) |
|
1 |
, где |
a1 |
|
|
c0 |
|
|
; a2 |
|
|
|
|
|
|
|
|
|
. |
||||||
|
|
|
|
f |
(Tf |
Tk ) Ф c 0 |
||||||||||||||||||||
|
|
|
|
|
|
|
|
|||||||||||||||||||
|
a1 a2 |
|
|
|
|
|
|
|
||||||||||||||||||
|
|
|
|
|
|
|
|
|
|
|
|
|
|
|
||||||||||||
|
|
|
|
|
|
|
|
|
|
|
|
|
|
|
|
|
|
|
|
|
|
|
|
Здесь все переменные величины в квадратных скобках берутся в начальном сечении основной зоны горения, чему соответствует индекс с0.
Значение функции a( L ) представлено на рис. 1.
28
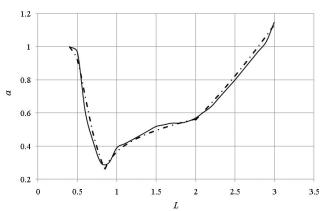
Рис. 1. Значение функции a (сплошная линия) и ее аппроксимация (штрихпунктирная линия) в основной зоне КС в зависимости от L
График функции a( L ) имеет три характерных участка, которые можно аппроксимировать с достаточной степенью точности:
|
|
1 |
|
|
, |
|
|
|
1 3,5(L 0,4) 2,3 |
0,4 L 0,85; |
|||
|
|
|
|
|
|
|
a(L) |
0,54(L 0,8)0,24 |
, |
|
0,85 L 2; |
||
|
|
|
|
|
|
2 L 3. |
|
0,166 L1,75 |
, |
|
|
||
|
|
|
|
|
|
|
Таким образом, в системе дифференциальных уравнений (3) – (5) описаны все переменные величины, параметры и начальные условия. Интегрирование уравнений (3) (в виде (7)), (4) и (5) позволяет определить размер капель и их координаты в основной зоне горения в любой момент времени для любого места расположения форсунок.
Система дифференциальных уравнений первого порядка (4)–(7) интегрируется методом Рунге-Кутта 4-го порядка точности по времени . Интегрирование выполняется от начального момента времени = 0 до момента времени, когда отношение D/D0 станет менее 0,2 или координата x превысит заданную длину основной зоны камеры сгорания lc. За время пребывания принимается время испарения капли или время, за которое неиспарившаяся капля достигает конца зоны основного горения.
Длина основной зоны камеры сгорания определяется методом последовательных приближений, за начальное значение берется расстояние, на котором от начала основной зоны расположен последний ряд форсунок (0,6 м). Критерием достаточности длины является доля неиспарившихся капель менее 1 %:
29

G |
|
|
G |
|
|
|
|
|
исп |
|
|
|
Н |
O |
Н |
O |
|
|
2 |
|
2 |
|
|
|
|
G |
Н O |
|
|
|
|
|
2 |
|
|
0,01
.
(8)
Оценочные расчеты показали, что длиной, обеспечивающей выполнение условия (8), является lc 1,2 м. Расчет проводился для капель максимальных и медианных размеров, полученных при распыливании тремя рядами форсунок в основной зоне камеры сгорания.
Список литературы
1.Бербек, А.М. Организация рабочего процесса в камере сгорания ракетного двигателя на порошкообразном алюминии и воде / А.М. Бербек, В.И. Малинин // Вестник КГТУ им. А.Н. Туполева. - 2010. - №3. – С. 22 – 27.
2.Трусов, Б.Г. Моделирование химических и фазовых равновесий при высоких температурах / Б.Г. Трусов. – М.: МГТУ им. Н.Э. Баумана, 1991. – 40 с.
3.Луканин, В.Н. Теплотехника / В.Н. Луканин, М.Г. Шатров, Г.М. Камфер. – М.: Высш. шк., 2003. – 671 с.
А. М. Бербек, кандидат технических наук А. А. Обросов, заместитель директора по испытаниям
ООО «Лаборатория Эффективных Материалов» А. В. Шатров, главный инженер
ООО «Лаборатория Эффективных Материалов» Пермский национальный исследовательский
политехнический университет
Истечение порошка алюминия из струйной форсунки установки синтеза нанопорошка оксида алюминия
Для получения нанопорошка Al2O3 методом испарения частиц алюминия с последующей конденсацией оксида с размером частиц от десятков до сотен нанометров требуется устойчивая подача порошка алюминия с необходимым расходом в форкамеру установки [1]. Кроме того требуется погасить скорость частиц алюминия после их вылета из форсунки и равномерно распределить их по сечению форкамеры.
Классическим способом подачи алюминия считается вытеснение поршнем предварительно псевдоожиженного порошкового элемента ПЭ. Однако трудность в реализации этого способа в том, что ПЭ в баке системы подачи находится в состоянии максимальной плотности и перевести его в псевдоожиженное состояние невозможно, т. к. для этого требуется свободный объем в баке и определенная ориентация его в пространстве. Можно создать псевдоожиженное состояние ПЭ в конусе перед форсункой (запорно-регулирующим клапаном КЗР), подавая газ на псевдоожи-
30
жение в сечение основания конуса. Однако, как показали экспериментальные исследования в этом случае порошок из конуса перемещается через форсунку в форкамеру, а новые порции порошка в конус либо не подаются, либо подаются крайне не стабильно, что приводит к образованию газового канала и прекращению подачи порошка. Это происходит вследствие возникновения распорных усилий ПЭ на стенки бака при давлении на него поршня со стороны заднего торца. Для того, чтобы снять распорные усилия необходимо как показали экспериментальные исследования, насытить ПЭ газом во всем его объеме через задний торец ПЭ. Таким образом, задача пневмотранспорта ПЭ к выпускному отверстию решается путем газонасыщения всего объема ПЭ и создания давления поршня на задний торец ПЭ. При открывании выпускного отверстия КЗР происходит истечение порошка за счет фильтрации газа через ПЭ и создания псевдоожиженного слоя порошка только в выпускном отверстии системы подачи.
Скорость истечения частиц порошка из выпускного отверстия может превышать 50 м/с. Такие скорости частиц на входе в форкамеру установки намного превышают требуемые для надежного воспламенения всех частиц [2]. Поэтому с целью увеличения эффективности процесса воспламенения и испарения необходимо увеличить время пребывания частиц в форкамере за счет торможения потока на входе в форкамеру установки. При экспериментальном исследовании было выяснено, что поток частиц, истекающих из выпускного отверстия, имеет форму узкой и плотной струи с малым углом раскрытия (6…8°). Поэтому процесс смешения частиц алюминия с потоком кислорода в форкамере происходит не эффективно. Образуется большая неравномерность коэффициента избытка окислителя, что так же является одной из причин низкой эффективности рабочего процесса воспламенения частиц алюминия.
С целью повышения эффективности этого процесса необходимо не только затормозить поток частиц, но и равномерно распределить его по сечению форкамеры.
Как показали эксперименты, эффективным способом торможения потока частиц, с одновременным распылом их по сечению форкамеры, оказался способ, включающий сталкивание четырех симметричных потоков частиц в точке, лежащей на оси форкамеры под углом к ней 300. Этот способ был реализован в конструкции КЗР и камеры изменения направления потоков частиц алюминия.
Конструкция системы подачи на которой проводились экспериментальные исследования рабочего процесса перемещения ПЭ из бака в форкамеру установки приведена на рис. 1. Она состоит из корпуса бака 4, переднего конуса 7 с отверстием истечения, КЗР 8, задней крышки 1 с штуцером для подвода газа. Внутри бака находится ПЭ 5 с максимальной плотностью, поршень 2 с пружинным перепадным клапаном 3. Запорнорегулирующий клапан управляется приводом 6 и имеет четыре продоль-
31
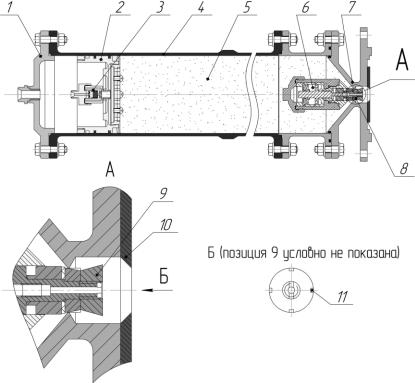
ных паза 11 переменного сечения по длине. Через эти пазы при открытии клапана истекает порошок. Конусная гайка 9 направляет потоки в камеру, где потоки, проходя конус 10, снова меняют направление и сталкиваются на оси форкамеры под углом 30°, тормозятся и распыливаются по ее сечению до смешения с кислородом.
Предварительно, до открытия КЗР 8, через штуцер в крышке 1 подается газ под давлением. Давлением газа поршень прижимается к ПЭ через перепадный клапан 3 и газораспределительную решетку с сеткой производится газонасыщение ПЭ. Время полного газонасыщения ПЭ зависит от его длины. При длине L = 830 мм это время составляет 35…40 с. Перепадный клапан в поршне настроен на перепад давления 0,25…0,3 МПа.
Рис. 1. Система подачи установки синтеза нанопорошка оксида алюминия.
1 – задняя крышка, 2 – поршень, 3 – перепадный клапан, 4 – бак, 5 – ПЭ, 6 – привод КЗР, 7 – конус с выходным отверстием, 8 – КЗР, 9 – конусная гайка, 10 – конус для изменения направления потоков, 11 – пазы КЗР
В процессе подачи ПЭ происходит фильтрационное истечение газа и его давление начинает уменьшаться. Возникает градиент давления по длине заряда dP/dx, который доходит до заднего торца ПЭ. Перепад дав-
32
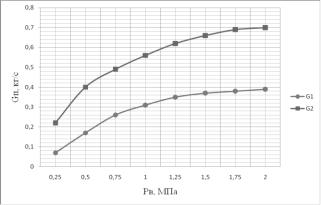
ления на поршне становится больше настроечного на перепадном клапане. Он открывается и пропускает через себя газ с тем большим расходом, чем больше фильтрационный расход газа через ПЭ. Поэтому давление газонасыщения в ПЭ поддерживается постоянным, что повышает стабильность расхода порошка алюминия. Перепад давления на поршне необходим для создания усилия на торце ПЭ, что предотвращает образование газовых каналов в ПЭ, которые нарушают стабильность подачи порошка.
Для выбора режимных параметров системы подачи порошка необходимо знать расходонапорные характеристики, т.е. зависимости расхода порошка от давления газа перед выпускным отверстием системы подачи (Gп = f(Pв)). Эти характеристики были определены и представлены на рисунке 2. Истечение осуществлялось в среду с атмосферным давлением. В качестве ПЭ использовался АСД-1ПСК с порозностью ε =0,34. Суммарная площадь сечения пазов КЗР была фиксированная и составляла 8 и 16 мм2.
Для обеспечения нужного расхода порошка алюминия необходимо также знать регулировочную характеристику системы подачи. Это зависимость расхода порошка от суммарной площади сечения пазов запорнорегулирующего клапана Gп = f(Fкзр)). При постоянном давлении перед ним.
Рис. 2. Зависимость расхода порошка АСД-1ПСК от давления газа перед выпускным отверстием:
G1 – значения расхода порошка, когда сечение пазов КЗР 8 мм2, G2 – значения расхода порошка, когда сечение пазов КЗР 16 мм2.
На рис. 3 приведены результаты испытаний системы подачи с порошком АСД-1ПСК при давлениях перед КЗР Рв=1,0 МПа и Рв = 2,0 МПа.
33
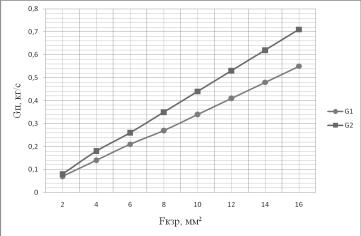
Рис. 3. Зависимость расхода порошка АСД-1ПСК от площади сечения пазов. G1 – значения расхода порошка, когда давление перед КЗР 1,0 МПа,
G2 – значения расхода порошка, когда давление перед КЗР 2,0 МПа.
Заключение:
Расходонапорные характеристики системы подачи Gп = f(Pв) имеют корневую зависимость, как и при испытании жидкостей.
Регулировочная характеристика имеет линейную зависимость Gп = f(Fкзр). Предлагаемый способ и конструкция системы подачи порошка алю-
миния в форкамеру установки синтеза позволяют получить стабильный расход порошка в широком диапазоне от 0,06 до 0,7 кг/с.
Список литературы
1.Малинин, В.И. Внутрикамерные процессы в установках на порошкообразных металлических горю-чих / В.И. Малинин. - Екатеринбург - Пермь: УрО РАН,
2006. – 262 с.
2.Крюков, А.Ю. Адаптация внутрикамерных процессов и элементов конструкции энергоустановок на порошковом горючем к технологиям получения ультра- и нанодисперсных материалов: монография / А.Ю. Крюков. - Пермь: Перм. нац. исслед. политехн. ун-т., 2011. – 236 с.
34
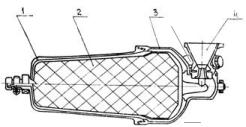
В. А. Болонкин, студент
Ф. А. Уразбахтин, доктор технических наук, профессор Ижевский государственный технический университет имени М.Т. Калашникова, Воткинский филиал
Исследование процесса функционирования управляющих твердотопливных ракетных двигателей
Исследование процесса функционирования управляющих твердотопливных ракетных двигателей является актуальным в области ракетостроения. Повышение требования к точности параметров движения космических летательных аппаратов (КЛА) приходят к созданию специальных устройств, среди которых: корректирующие и тормозные двигатели, двигатели системы ориентации и стабилизации, двигатели закрутки, увода, отстрела.
5
Рисунок. Конструкция РДТТ управления по каналу крена: 1 - корпус; 2 – заряд ТТ; 3 – заднее днище; 4 – сопло;
5 – воспламенительное устройство
Одним из таких устройств является малогабаритный двигатель вспомогательного назначения (рисунок). Он используется для управления по каналу вращения (крена) верхней ступени баллистической ракеты. Воспламенительным устройством данного типа ракет являются два пиропатрона предохранительного типа находящиеся на заднем днище. Процесс воспламенения заряда РДТТ состоит из нескольких последовательных стадий.
На предварительной первой стадии происходит замыкание контактов линии накаливания, разогрев мостика накаливания, нагрев инициирующей смеси, ее сгорание, нагрев легковоспламеняющегося пороха (передаточного заряда), которое приводит к возгоранию основного воспламенительного заряда и поступлению продуктов сгорания в основную камеру.
Вторая стадия процесса воспламенения состоит из двух этапов. На первом этапе продукты сгорания, поступающие из ВУ, заполняют свободный объем заднего днища, вытесняя оттуда воздух. Происходит частичное перемешивание продуктов сгорания с воздухом. Продукты сгора-
35
ния ВУ двигаются к соплу. Создав волну давления, происходит повышение давления до тех пор, пока не разрушатся заглушки в сопловом блоке РДТТ. С этого момента начинается второй этап стадии, при котором из камеры истекают воздух и продукты сгорания. На этой стадии происходит частичный нагрев поверхности основного заряда [1].
На третьей стадии происходит горение воспламенителя и нагрев поверхности твердотопливного заряда. Стадия заканчивается моментом загорания твердотопливного заряда РДТТ. Выделяемое при этом тепло у поверхности заряда в результате термического разложения конденсированной фазы и реакций в газовой фазе не успевает отводиться от зоны реакции, из-за чего реакция разложения топливного заряда протекает устойчиво, что приводит к увеличению температуры поверхности заряда. Увеличение температуры происходит до критического предела, при котором воспламеняется основной заряд РДТТ.
На четвертой стадии пламя распространяется по поверхности основного заряда РДТТ. Происходит теплообмен между газовым потоком и продуктами сгорания заряда ВУ и основного топлива РДТТ. После смешивания газовых потоков увеличивается зона распространения фронта пламени по поверхности заряда. Интенсивное нарастание давления в камере сгорания на этой стадии происходит за счет включения в процесс горения все новых участков поверхности заряда и прихода в объем камеры РДТТ продуктов сгорания ВУ [2].
На последней, пятой стадии происходит совместное горение основного заряда и остатков заряда ВУ. Приход продуктов сгорания в объем камеры становится больше расхода через сопло, что приводит к увеличению давления в камере. В момент, когда ВУ полностью сгорает, РДТТ выходит на установившийся режим работы, при котором происходит торцевое горение.
ВУ управляющих РДТТ накопила множество различных вариантов исполнения. Однако ВУ находятся на стадии разработки и совершенствования. Следующим этапом исследования процесса функционирования ВУ является составление математической модели.
Список литературы
1.Тишунин, И.В. Вспомогательные системы ракетно-космической техники / И.В. Тишунин. – М.: Мир, 1970. – 129 с.
2.Присняков, В.Ф. Динамика ракетных двигателей твердого топлива / В.Ф. Присняков . – М.: Машиностроение, 1984. – 248 с.
36
Д. А. Болховских, аспирант
В. И. Малинин, доктор технических наук, профессор Р. В. Бульбович, доктор технических наук, профессор Пермский национальный исследовательский политехнический университет
Расчет процессов в форкамере установки синтеза нанооксида алюминия
Нанооксиды металлов находит свое применение в различных отраслях промышленности. Поэтому исследование возможности получения нанодисперсных оксидов методом сжигания газовзвесей порошков металлов представляет практический и теоретический интерес. Экспериментальная установка синтеза нанооксида алюминия, созданная в ОКБ «Темп» при ПНИПУ [1] состоит из системы подачи, форкамеры (ФК), камеры сгорания, устройства отбора дисперсных продуктов. Форкамера предназначена для смешения порошка с первичным воздухом, воспламенения и первичного горения. Наиболее значимыми факторами, влияющими на получение нанооксида алюминия в установке, являются температура продуктов первичного горения, доля конденсированной и газообразной фазы алюминия, образованные в ФК. Учитывая влияние этих факторов, подобраны компоненты, способствующие улучшению процесса синтеза и качества нанооксида алюминия.
В монографии [1] представлены исследования по получению оксида алюминия в экспериментальной установке синтеза, с применением в ФК смеси Al+воздух. Авторами проведен анализ эффективности использования данной смеси. Выявлены следующие недостатки:
−высокая температура продуктов первичного горения (> 2500 К);
−образование большой доли конденсированной фазы (> 15 %);
−недостаточное количество газообразной фазы алюминия попадает в
камеру сгорания (qvap < 80 %).
Следствием перечисленных недостатков является то, что большой
тепловой поток попадает на стенки, и возникают трудности с их охлаждением. Также происходит налипание на стенки большого количества конденсированной фазы, из-за этого усложняется процесс их охлаждения и уменьшается проходное сечение ФК. Увеличивается количество алюминия, не преобразованного в газообразную фазу, то есть доля Al, находя-
щегося в К-фазе в форкамере КAlRf (KAlRf = 1 ‒ qvap).
В [1, 2] предлагалось непрерывное функционирование ФК обеспечивать за счет процесса транспирационного охлаждения пористой оболочки камеры такими охладителями, как вода, воздух. В данной работе в качестве охладителя при транспирационном охлаждении стенок предлагается использовать аргон.
На основании вышеописанного, задачи настоящего исследования:
37
−снижение температуры протекания реакции;
−уменьшение доли конденсированной фазы (К-фаза);
−уменьшение доли алюминия преобразованного в оксид алюминия. Для решения поставленных задач рассматриваются следующие метал-
логазовые смеси: Al+O2+H2О; Al+O2+Ar; Al+H2O+воздух. Термодинамический расчет проводится с помощью программного
комплекса АСТРА.4 [3], определяются характеристики равновесия, исследуемых металлогазовых смесей, и содержание компонентов смеси.
С помощью математических формул определяются: − коэффициент избытка окислителя
|
Gox |
, |
|
G |
L |
||
|
Al |
0 |
|
где Gox – расход окислителя, GAl – расход алюминия, L0 – стехиометрический коэффициент окислителя; − доля алюминия в К-фазе в форкамере
|
2M |
Al |
|
|
|
M |
Al |
|
|
G |
|||
KAlRf |
|
|
ZAl O |
|
ZAl ZAlN |
|
|
|
|
|
. |
||
M |
|
|
|
M |
|
|
|
||||||
|
|
|
2 |
3 |
|
|
|
|
|
G |
|||
|
|
Al2O3 |
|
|
|
|
AlN |
|
Al |
Здесь MAl, MAlN, MAl2O3 – молекулярная масса соответственно алюминия, нитрида алюминия, Al2O3; ZAl2O3, ZAl, ZAlN– массовая доля конденсированной фазы соответственно Al2O3, алюминия, AlN (при расчете сме-
сей, не содержащих воздух ZAlN = 0), G – суммарный расход компонен-
тов, GAl – расход алюминия.
В расчетах изменяется отношение расхода окислителя и охлаждающих компонентов к алюминию (Gок/GAl, Gохл/GAl). На основе термодинамических расчетов построены графики зависимостей суммарной массовой доли конденсированной фазы (ZΣ) и доли алюминия в К-фазе в ФК (КAlRf) от коэффициента избытка окислителя α, представленные на рис. 1, 2 и 3. Из
анализа зависимостей ZΣ и КAlRf от α (рис. 1, 2 и 3) следует, что у каждой из кривых существует минимум. Точки, в которых ZΣ минимальное, име-
ют соотношение расхода компонентов смеси, при котором меньше веществ налипает на стенки и они лучше охлаждаются. Точки, в которых значение КAlRf – минимальное, имеют соотношение расхода компонентов смеси, при котором максимальное количество газообразного Аl поступит в камеру сгорания для дальнейшего синтеза.
38
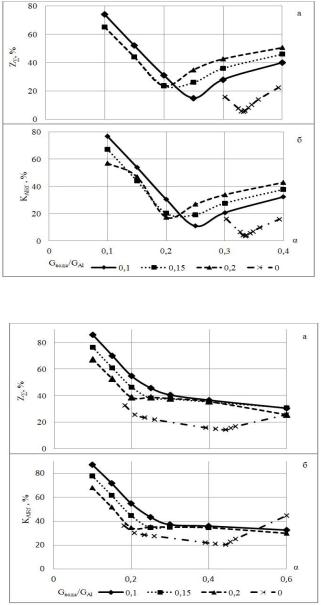
Рис. 1. Зависимости суммарной доли конденсированной фазы (а) и доли алюминия в К-фазе (б) от коэффициента избытка окислителя: смесь Al+H2O+O2
Рис. 2. Зависимости суммарной доли конденсированной фазы (а) и доли алюминия в К-фазе (б) от коэффициента избытка окислителя: смесь Al+H2O+воздух
39
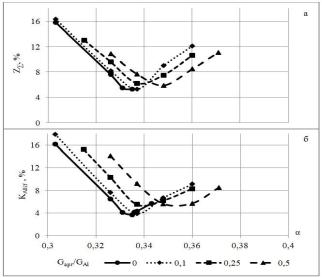
Рис. 3. Зависимости суммарной доли конденсированной фазы (а) и доли алюминия в К-фазе (б) от коэффициента избытка окислителя: смесь Al+Ar+O2
Анализ полученных данных Т показывает, что в большинстве случаев точки, обладающие приемлемой температурой для форкамеры совпадают с точками, в которых ZΣ ‒ min и КAlRf ‒ min. Отсюда следует вывод о том, что точки, в которых ZΣ, Т и КAlRf ‒ min, обладают оптимальным соотношением расхода компонентов металлогазовой смеси.
Результаты исследования приведены в таблице, которая отображает основные характеристики металлогазовых смесей.
Таблица. Параметры металлогазовых смесей
Компонент |
αопт |
Gохл/GАl |
ZΣ, % |
T, K |
KAlRf, % |
|
|
|
|
|
|
Вода+О2 |
0,20...0,40 |
0,10…0,15 |
15…40 |
2600…2900 |
11…30 |
Аргон |
0,34…0,35 |
0,25...0,5 |
6…7 |
2450…2500 |
5…5,5 |
Воздух |
0,40…0,50 |
1,5…1,9 |
14…20 |
2650…2900 |
20…30 |
Вода+возд. |
0,3…0,6 |
0,15…0,2 |
25…30 |
2600…2650 |
28…33 |
Сравнивая результаты, отображенные в таблице стоит отметить, что при использовании металлогазовой смеси Al+O2+Ar суммарная массовая доля конденсированной фазы ниже в 2‒7 раз, доля алюминия в конденсированной фазе в 3‒6 раз и температура продуктов сгорания меньше на 200
... 400 К, чем у двух других смесей.
40
В литературе [4] для охлаждения стенок камеры сгорания рекомендовано применять окислитель, если коэффициент избытка окислителя α>1, и горючее, если α<1. В форкамере установки синтеза дисперсных оксидов α всегда меньше и даже много меньше единицы [1], поэтому для охлаждения необходимо использовать горючие или химически нейтральные, по отношению к Al, компоненты. Стоит отметить, что вода и воздух для алюминия являются окислителями. Поэтому H2O и воздух вместо того чтобы охлаждать стенки форкамеры будут их нагревать, так как эти компоненты вступят в экзотермическую реакцию с алюминием и продуктами его первичного горения (газообразный алюминий и субоксиды алюминия
AlO, Al2O).
Использование данной смеси Al+O2+Ar позволяет решить поставленные в работе задачи, а также обеспечить непрерывное функционирование ФК установки за счет решения проблемы охлаждения стенок форкамеры.
Дополнительно подчеркнем экономическую эффективность применения данной смеси, экологическую и взрывопожарную безопасность. Также выделим то, что использование смеси Al+O2+Ar способствует повышению чистоты конечного продукта.
Список литературы
1.Малинин, В.И. Внутрикамерные процессы в установках на порошкообразных металлических горючих / В.И. Малинин. - Екатеринбург - Пермь: УрО РАН,
2006. – 262 с.
2.Крюков, А.Ю. Адаптация внутрикамерных процессов и элементов конструкции энергоустановок на порошковом горючем к технологиям получения ультра- и нанодисперсных материалов: монография / А.Ю. Крюков. - Пермь : Перм. нац. исслед. политехн. ун-т., 2011. – 236 с.
3.Трусов, Б.Г. Моделирование химических и фазовых равновесий при высоких температурах / Б.Г. Трусов. – М.: МГТУ им. Н.Э. Баумана, 1991. – 40 с.
4.Алемасов, В.Е. Теория ракетных двигателей: Учебник для студентов высших технических учебных заведений / В.Е. Алемасов, А.Ф. Дрегалин, А.П. Тишин. – М.: Машиностроение, 1989. – 268 с.
О. С. Бондарева, магистрант
А. А. Мельников, кандидат технических наук, доцент Самарский государственный аэрокосмический университет имени С. П. Королева
Исследование формирования модифицированных цинковых покрытий на изделиях из кремнийсодержащих сталей
Исследование формирования цинковых покрытий является актуальным в сфере коррозионной защиты металлов. Горячее оцинкование ме-
41
таллоконструкций из сталей с содержанием кремния до 0,8‒1 %, ведет к ухудшению качества покрытия, связанного с нарушением его сплошности, повышенной толщиной и плохой адгезией к основному металлу. Устранение этих недостатков требует доработки технологии горячего оцинкования. Основная задача сводилась к поиску новых решений в области горячего оцинкования, которые направлены на получение заданных механических, технологических и функциональных свойств защитного покрытия, регулирующих материальные и производственные затраты.
При нанесении цинковых покрытий методом погружения в расплав процесс смачивания и растекания цинка сопровождается ростом интерметаллических слоев. На свойства защитного слоя (коррозионную стойкость, пластичность, прочность покрытия и его сцепление с основой) существенное влияние оказывает толщина, природа, строение и взаимное расположение фаз в диффузионном переходном слое. Образование интерметаллического слоя происходит за счет взаимной диффузии железа и цинка с преобладанием диффузии одного из компонентов. Даже небольшое изменение в составе стали, в частности в содержании кремния, или в температуре и составе расплава, может в значительной степени повлиять на соотношение скоростей диффузии железа и цинка [1]. Влияние содержания кремния в стали на толщину и структуру покрытий объясняется тем, что кремний обладает низкой растворимостью в столбчатой фазе. Он выделяется из нее и накапливается в межфазных областях, вступая в реакцию с железом фазы δ [2]. Увеличение содержания кремния до 0,8‒1 %, ведет к ухудшению качества покрытия, связанного с нарушением его сплошности, повышенной толщиной и плохой адгезией к основному металлу [3]. Устранение этих недостатков требует изменения технологии горячего цинкования. Таким образом, цель работы заключалась в исследовании влияния температурного режима на качество и свойства цинкового покрытия сталях с различным содержанием кремния.
Для исследования были использовали образцы 4 партий размером 150×150×3 мм из стали Ст3 и 09Г2С, химический состав которых приведен в табл. 1.
Таблица 1. Химический состав исследуемых сталей
№ пар- |
|
C |
Si |
Mn |
P |
S |
Cr |
Ni |
тии |
|
|
|
|
|
|
|
|
№1 |
09Г2С |
До |
0,61 |
1,3- |
До |
До |
До |
До 0,3 |
|
|
0,12 |
|
1,7 |
0,035 |
0,04 |
0,3 |
|
№2 |
Ст3сп |
|
0,2 |
|
|
|
|
|
№3 |
Ст3сп |
0,14 |
0,23 |
0,47 |
0,019 |
0,019 |
0,03 |
0,04 |
№4 |
Ст3сп |
|
0,31 |
|
|
|
|
|
Процесс жидкофазного цинкования образцов проводили по схеме: обезжиривание, промывка, травление, промывка, флюсование, сушка, цинкование. Подготовка образцов к цинкованию проводилась по обычной
42
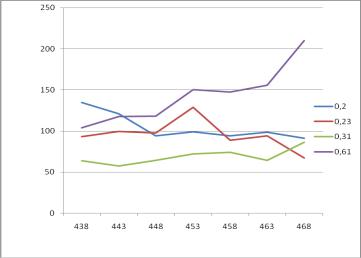
технологии принятой на ОАО «Продмаш». Цинкование образцов проводили на лабораторной установке в диапазоне температур от 438°С до 468 °С с шагом в 5 °С. Время выдержки в расплаве цинка– 4 мин. Скорость опускания и подъема образцов из ванны для всех партий была одинаковая. Расплав цинка был легирован алюминием (0,005%) и никелем (0,03-0,035 %). Структуру и толщину покрытий определяли с помощью электронного микроскопа на шлифах, которые травили в 2%-ном растворе азотной кислоты в этиловом спирте. Результаты исследований представлены в табл. 2.
Таблица 2. Зависимость средней толщины покрытия (мкм) от температуры
(°С) и содержания Si в стали (%)
T |
|
Si |
0,2 |
0,23 |
0,31 |
0,61 |
|
438 |
134,489 |
93,289 |
63,575 |
103,663 |
|
|
443 |
120,818 |
99,543 |
57,266 |
117,407 |
|
|
448 |
93,921 |
97,619 |
64,000 |
117,781 |
|
|
453 |
99,008 |
128,627 |
71,758 |
150,026 |
|
|
458 |
94,054 |
88,656 |
73,745 |
147,208 |
|
|
463 |
98,55 |
93,912 |
64,072 |
155,723 |
|
|
468 |
91,02 |
67,23 |
86,042 |
209,814 |
Наглядно эти зависимости продемонстрированы на рис. 1 и 2.
Рис. 1. Зависимость толщины цинкового покрытия (мкм) от температуры (°С).
43
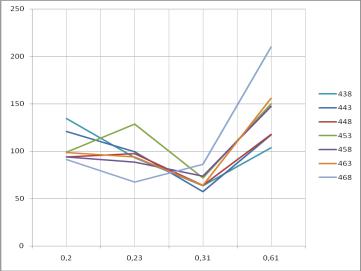
Рис. 2. Зависимость толщины цинкового покрытия (мкм) от содержания Si (%)
Анализируя полученные данные, можно сделать вывод, что на сталях с содержанием Si = 0,31 % толщина цинкового покрытия наименьшая во всем диапазоне температур и не превышает 90 мкм. При содержании кремния 0,2 и 0,23 толщина покрытия выше, но в целом постоянна, отклонения от среднего значения 100 мкм не значительны. Для стали с содержанием кремния 0,61% картина принципиально иная. Наблюдается прямая зависимость толщины покрытия от температуры, при 468°С толщина цинкового слоя в два раза больше, чем при 438 °С. Исходя из полученных зависимостей, можно выбрать оптимальную температуру цинкования для сталей с разным содержанием кремния.
Проведенные исследования фазового состава показали, что в слое цинкового покрытия в соответствии с диаграммой железо-цинк имеются все структурные составляющие: а‒, Γ‒, δ1‒, δ‒, ε‒фазы. Структура покрытия для всех образцов с повышенным содержанием кремния (09Г2С) отличается преобладающим развитием δ‒фазы (рис. 3).
44
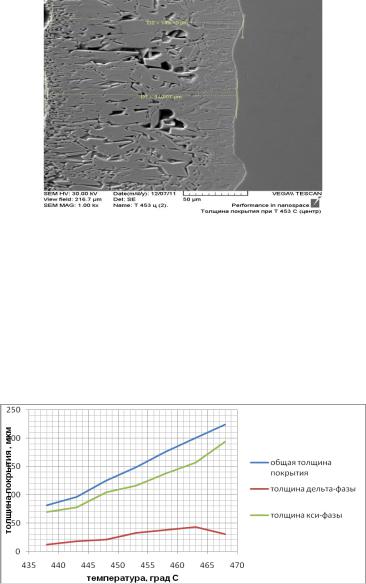
Рис. 3. Строение цинкового покрытия на стали с Si ‒ 0,61%, Т = 453 °С
При этом столбчатые кристаллы фазы δ могут выходить на поверхность покрытия и придавать ему серый цвет. Однако, при этом, как известно, коррозионная стойкость и пластичность таких покрытий снижается. Анализ толщины отдельных фаз в структуре цинкового покрытия показывает, что до 80‒86 % толщины покрытия приходится на δ‒фазу, которая образуется первой и в последующем подавляет рост Г‒фазы и δ‒фазы. δ‒фаза имеет выраженную столбчатую и пористую структуру и характеризуется хрупкостью и плохой адгезией к основе.
Зависимость толщины покрытия и отдельных фаз от температуры представлена на рис. 4.
Рис. 4. Зависимость толщины цинкового покрытия (мкм) на стали 09Г2С от температуры (°С).
Цинковое покрытие на стали Ст3сп (Si ‒ 0,23 %) имеет другую структуру (рис. 5 а, б, в).
45
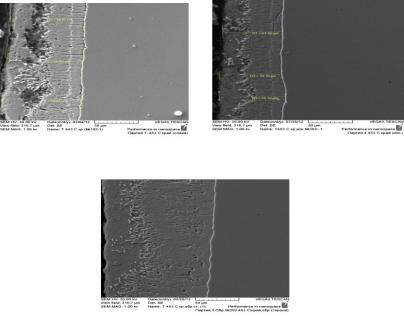
(а) |
(б) |
(в)
Рис. 5. Строение цинкового покрытия на стали с Si ‒ 0,31 % (а), Si ‒ 0,23 % (б),
Si ‒ 0,2 %, (в) Т = 453 °С
При одинаковой температуре (453°С) общая толщина покрытия на стали Ст3сп гораздо меньше, чем на стали 09Г2С, порядка 100 мкм. Это существенно экономит расход цинка. Принципиально другое строение имеет δ‒фаза, кристаллы ее мельче и выходят на поверхность не везде, а только местами. Доля δ‒фазы в общей толщине покрытия около 50 %, появляется ярко выраженная фаза чистого цинка на поверхности, который дает красивый блеск покрытию и повышает коррозионную стойкость. Повышение температуры процесса не ведет к резкому увеличению толщины покрытия. Можно сделать вывод, что для сталей с содержанием кремния 0,2‒0,3 % при легировании расплава алюминием 0,005 % и никелем 0,03‒0,035 % создаются условия для хорошей адгезии цинка к железу. На стали с содержанием кремния 0,61 % идеальной поверхности для смачивания не создается. Для подавления неблагоприятного влияния кремния на толщину и качество цинкового покрытия необходимо подобрать другие соотношения добавок алюминия и никеля в расплав цинка. Процесс влияния алюминия и никеля на смачивание железа цинком недостаточно изучен. Считается, что в момент погружения стального компонента в расплав цинка, легированного алюминием, на поверхности их взаимодействия образуется тонкая пленка в виде соединений Fe2Al5 и FeAl3, затрудняющая диффузию железа в цинк. Это приводит к уменьшению толщины железоцинкового слоя и преобладанию в покрытии пластичной ε-
46
фазы (поверхностный цинк), при этом повышается пластичность и адгезия покрытия. Есть также мнение, что никель, находясь в расплаве, концентрируясь в δ‒фазе, вызывает уплотнение δ и δ‒фазы, что существенно препятствует диффузии железа в цинк.
Таким образом, в результате исследований выявлены зависимости толщины цинкового покрытия от температуры процесса и от содержания кремния в стали. С помощью электронного микроскопа изучен фазовый состав цинковых покрытий. Обнаружено, что на сталях с повышенным содержанием кремния (09Г2С) до 80‒86% толщины покрытия приходится на δ‒фазу, которая образуется первой и в последующем подавляет рост Г‒фазы и δ‒фазы. Из этого следует, что для стали 09Г2С необходимо подобрать другое соотношение добавок алюминия и никеля. Результаты исследований позволили определить оптимальный температурный режим цинкования для используемого состава цинкового расплава и обеспечить получение качественных цинковых покрытий на кремнийсодержащих сталях.
Список литературы
1.Тарасова, А.А. Особенности цинкования кремнийсодержащих сталей / А.А. Тарасова. – М.: Металлургия, 1984. – 72 с.
2.Бочаров, А.Я. Особенности формирования модифицированных цинковых покрытий на изделиях из кремнийсодержащих сталей / А.Я. Бочаров, Е.В. Проскурин, И.Е. Митников // Сталь. - 1989. - №7. - С.72-74.
3.Парамонов, А.В. Проблемы производства горячеоцинкованных металлоконструкций / А.В. Парамонов, А.С. Адамов, В.Ю. Чернецов // Металлург. - 2010.
-№11. - С. 82-84.
К. А. Брызгалов, магистрант
М. Р. Королева, кандидат физико-математических наук, доцент Ижевский государственный технический университет
имени М. Т. Калашникова
Численное моделирование стационарного турбулентного течения газа во впускном канале двигателя внутреннего сгорания
Газодинамические процессы в проточных частях двигателей внутреннего сгорания характеризуются сложным пространственным, нестационарным течением газа, связанным с геометрией проточной части.
Проектирование впускных каналов ДВС связано, прежде всего, со значительными затратами на проведение экспериментальных исследований и испытаний, на устранение выявленных недостатков и дефектов. В связи с этим, задача автоматизации процесса проектирования, предполагает проведение как теоретических, так и экспериментальных исследований слож-
47

ных физических явлений, происходящих во впускном канале двигателя, и является актуальной [1].
Использование численных методов расчета течений газа в проточных частях ДВС позволяет проводить детальное исследование характеристик течения в любой точке потока [1, 2]. В данной работе проводится моделирование стационарного течения вязкого сжимаемого газа во впускном канале ДВС на основе осредненных по Рейнольдсу уравнений Навье – Стокса [2].
Осредненные уравнения Навье – Стокса предполагают использование замыкающей модели турбулентности, связывающей тензор турбулентных напряжений с параметрами осредненного течения.
В работе использовалась двухпараметрическая модель турбулентности k , хорошо зарекомендовавшая себя при моделировании течений в проточных частях ДВС [3].
В декартовой системе координат уравнения имеют следующий вид:
−уравнение неразрывности:
vi 0 ,xi
−уравнения движения:
|
vivj |
|
|
|
2 |
|
|
ij |
|
|
|
p |
|
k |
|
|
, |
||
xj |
|
|
xj |
||||||
|
|
xi |
3 |
|
|
|
|
|
|
|
vi |
|
vj |
|
|
||
где |
|
|
|
|
|
|
|
|
, |
|
|
|
x |
|
x |
|
|
||||
|
ij |
|
T |
|
|
|
|
|||
|
|
|
|
|
j |
|
|
i |
|
|
‒уравнение для кинетической энергии:
|
|
|
|
|
|
|
k |
|
|
2k |
|
|
|
kv |
|
|
|
G |
, |
||||||
x |
|
|
|
|
y2 |
|||||||
|
|
j |
|
T |
|
x |
|
|
|
|
||
|
j |
|
|
|
|
|
j |
|
|
|
где vi , p , k , – осредненные компоненты вектора скорости, давление,
кинетическая энергия турбулентности, скорость диссипации турбулентной энергии.
Численный эксперимент проводился с использованием программного комплекса ANSYS CFX для расчета газодинамических процессов.
Геометрическая модель объекта исследования представлена на рис. 1.
48
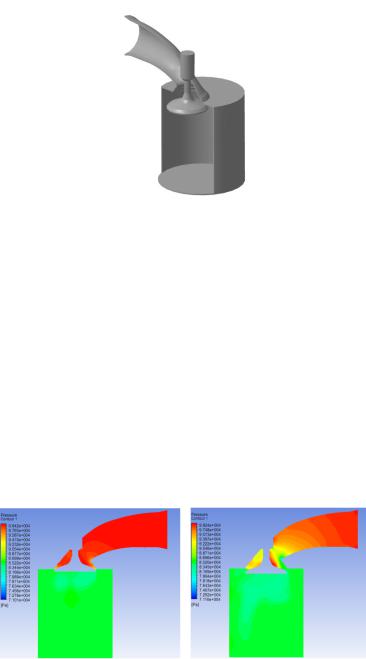
Рис. 1. Геометрическая модель объекта исследования.
Расчетная область включает в себя впускной канал, впускной клапан и цилиндр. Используемые граничные условия на твердых стенках учитывали шероховатость поверхности впускного канала с величиной эквивалентной шероховатости 0,5 мм. На оставшихся твердых поверхностях использовалось граничное условие прилипания. На входе во впускной канал задавалась величина полного давления. На выходе использовалось граничное условие свободного выхода (нижняя плоскость цилиндра).
Расчеты проводились при высотах поднятия клапана 2, 4, 6 и 8 мм до установления.
Высота поднятия клапана влияет на распределение давления в области, а также на картину течения в канале. На рис. 2 показано распределение давления в расчетной области в сечении по оси клапана.
При малой высоте подъема клапана область высокого давления сосредоточена во впускном кале ДВС – рис. 2а. При открытии клапана более 2 мм наблюдается локальное падение давления в области обтекания втулки клапана, и чем больше высота поднятия клапана, тем большие размеры имеет зона пониженного давления – рис. 2б-г.
а |
б |
49
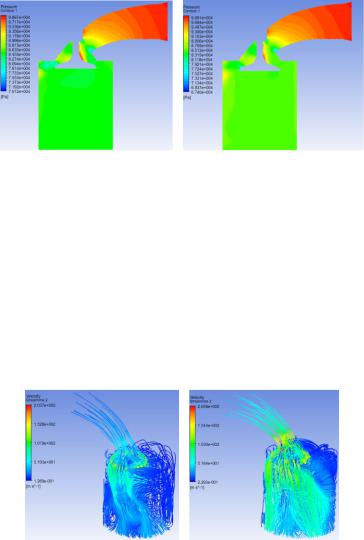
в г
Рис. 2. Распределение давления в сечении по оси клапана при высоте поднятия клапана: а – 2 мм, б – 4 мм, в – 6 мм, г – 7 мм
На рис. 3 приведены линии тока пространственного течения.
Течение во всех случаях является отрывным, сопровождается повышением скорости при прохождении потока через клапан. Чем меньше величина клапанной щели, тем более резко возрастает скорость течения. В случае открытия клапана на высоту 2мм течение имеет плавный характер. В области под клапаном образуются обширные зоны возвратного течения с низкой скоростью движения. С увеличением высоты подъема клапана размер таких зон уменьшается, а скорость потока в них возрастает. Во всех рассмотренных случаях течение в канале имеет ярко выраженный пространственный характер.
а) |
б) |
50
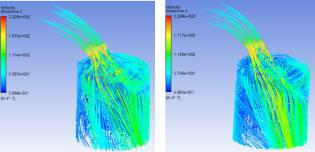
в) |
г) |
Рис. 3. Линии тока пространственного течения при высоте поднятия клапана: а) 2 мм, б) 4 мм, в) 6 мм, г) 7 мм
Численное моделирование течения сжимаемого газа во впускном канале ДВС позволяет получить распределение всех характеристик потока в любой точке канала, что в свою очередь даст возможность рассчитать необходимые локальные и интегральные характеристики потока и могут быть использованы для оптимизации геометрии впускных каналов ДВС.
Список литературы
1. Тюнин, А.В. Математическое моделирование потоков во впускном трубопроводе ДВС / А.В. Тюнин // Научные разработки автотранспортного факультета Алтайскому краю. - Барнаул, 2007. - С. 53-57.
2.Хандримайлов, А.А. Численная модель сжимаемого вязкого турбулентного течения во впускных кана-лах и цилиндрах поршневых двигателей. Часть II. Верификация / А.А. Хандримайлов, В.Г. Солодов // Двигатели внутреннего сгорания.
-2009. - №2. - С. 16 – 20.
3.Андерсон, Д. Вычислительная гидромеханика и теплообмен / Д. Андерсон, Дж. Таннехилл, Р. Плетчер. – М.: Мир, 1990. – 728 с.
Л. В. Волкова, ведущий специалист
И. А. Чувашов, магистрант; Т. Н. Байкалова, студентка
В. В. Муравьев, доктор технических наук, профессор Ижевский государственный технический университет
имени М. Т. Калашникова
Расчетно-экспериментальные исследования напряженнодеформированного состояния бандажей локомотивных колес после термической обработки
Бандаж локомотивного колеса представляет собой наружное съемное стальное кольцо специального профиля, надеваемое на обод колесного
51
центра. Бандаж изготовляется цельным, без шва, из высококачественной углеродистой мартеновской стали. В процессе изготовления, подвергается механической и термической обработке для придания определенной формы и механических свойств.
Термическая обработка – процесс тепловой обработки изделий из металлов и сплавов с целью изменения их структуры и свойств, заключающийся в нагреве до определенной температуры, выдержке и последующем охлаждении с заданной скоростью. Локомотивный бандаж, подвергается операции термической обработки – закалке с последующим отпуском, в результате закалки образуются внутренние напряжения.
При закалке возникают внутренние напряжения, которые по величине могут быть настолько большими, что это приводит к трещинам и разрушению стали без всякого дополнительного воздействия. Причиной возникновения термических напряжений является неравномерность охлаждения деталей при закалке. Наружные поверхности бандажа охлаждаются быстрее, и уменьшается в объеме. Внутренняя же зона охлаждается замедленно и потому препятствует сжатию наружного слоя. В результате внутренняя зона металла окажется сжатой, а наружная – растянутой. В последующий период внутренняя зона, охлаждаясь, уменьшится в объеме и потянет к центру наружный кольцевой слой, стремясь уменьшить его диаметр. Но металл снаружи уже остыл и потому утратил пластичность. Теперь наружная зона играет роль жесткого каркаса, которая уже не может уменьшиться по диаметру. Поэтому в заключительный период охлаждения в наружных слоях металла возникнут сжимающие напряжения. Внутренняя же зона металла, будучи связана с наружными слоями, не сможет уменьшиться в объеме, хотя и будет стремиться к этому. В результате в ней возникнут растягивающие внутренние напряжения. Растягивающие напряжения являются более опасными, чем сжимающие. При закалке массивных деталей, когда различие в температуре внутренних и наружных слоев достигает значительной величины, такие напряжения могут вызвать трещины или даже привести к полному разрушению металла.
В результате закалки изменяется и структура металла по объему, в результате чего также появляются напряжения. Различные структуры стали имеют различный удельный объем: мартенсит – максимальный, аустенит
– минимальный, перлит – средний между ними.
Обод железнодорожного колеса имеет большие габариты, поэтому не может прокаливаться полностью при внешнем охлаждении. После закалки около поверхности будет мартенситная структура, а в центральной части – перлитная. При образовании мартенсита объем стали возрастает, и поэтому наружное мартенситное кольцо будет стремиться увеличиться в диаметре. Но этому препятствует центральная зона, стремясь стянуть кольцо к центру. В результате в наружном мартенситном слое металла возникнут сжимающие напряжения σс, а в центральной зоне, наоборот, –
52
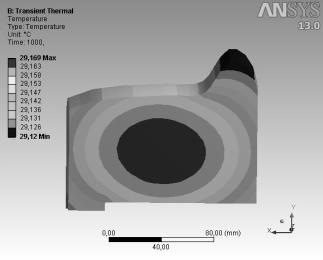
растягивающие σр.
Эти напряжения также связаны с изменениями объема металла, но такие изменения в данном случае вызваны структурными превращениями. Поэтому и напряжения называются структурными.
Результатом моделирования процесса охлаждения в программной среде ANSYS является распределение температуры стали обода во времени. Распределение температуры в бандаже локомотивного колеса через 10 секунд после начала охлаждения представлено на рис 1.
Рис. 1. Распределение температуры в ободе железнодорожного колеса через 10 секунд после начала охлаждения
На рис. 1 видно распространение теплового фронта с поверхности бандажа к центральной части бандажа. При этом температура внутренней части колес охлаждается значительно медленнее. Даже после окончания охлаждения внутренняя часть бандажа будет оставаться сильно раскаленной. Раскаленная внутренняя часть бандажа будет нагревать внешнюю часть, что в результате приведет к самоотпуску обода колеса и образованию структур троостита вблизи поверхности катания и места посадки.
Для моделирования напряжений в бандаже в процессе охлаждения рассмотрим данные рис. 1. На поверхности обода происходит полное превращение аустенита в мартенсит, а в центральной части охлажденная сталь имеет структуру перлита. Разобьем модель ANSYS на несколько частей, для каждой части определим среднюю структуру
На рис. 2 изображен график относительного изменения удельного объема при фазовых превращениях в углеродистой стали в зависимости от содержания углерода [16].
53
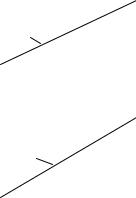
Изменение удельного, % объема
3 |
|
|
|
|
|
|
|
|
|
|
|
|
|
|
|
2 |
|
|
|
|
|
|
|
|
2 |
|
|
|
|
|
|
|
|
|
|
|
|
|
|
1 |
|
|
|
|
|
|
|
|
|
|
|
|
|
|
|
0 |
|
|
|
|
|
|
|
|
|
|
|
|
|
|
|
-1 |
|
|
|
|
|
|
|
|
|
|
|
|
|
|
|
-2 |
|
|
|
|
|
|
|
|
1 |
|
|
|
|
|
|
|
|
|
|
|
|
|
|
-3 |
|
|
|
|
|
|
|
|
|
|
|
|
|
|
|
-4 |
|
|
|
|
|
|
|
0,4 |
0,8 |
1,2 |
1,6 |
||||
|
|
Содержание углерода, % |
|
|
Рис. 2. Относительное изменение удельного объема при фазовых превращениях относительно перлитной структуры
1 – 100% аустенита; 2 – 100% мартенсита
Для стали, содержащей 0,6% углерода, изменение удельного объема относительно перлитной структуры составляет для аустенита -3,3%, для мартенсита 0,9%.
Определим влияние теплового расширения на изменение объема в процессе охлаждения табл. 1 [2].
Таблица 1. Физические свойства стали 60
Температура, °С |
20 |
100 |
200 |
300 |
400 |
500 |
600 |
|
Коэффициент теплопро- |
– |
67 |
53 |
– |
36 |
– |
– |
|
водности, Вт/(м·°С) |
||||||||
|
|
|
|
|
|
|
||
Удельная теплоемкость, |
– |
481 |
486 |
– |
528 |
– |
565 |
|
Дж/(кг·°С) |
||||||||
|
|
|
|
|
|
|
||
Коэффициент линейного |
11,0 |
11,9 |
– |
13,5 |
14,6 |
– |
– |
|
расширения α, 10-6/°С |
||||||||
Модуль нормальной упру- |
204 |
– |
208 |
189 |
175 |
– |
– |
|
гости E, ГПа |
||||||||
|
|
|
|
|
|
|
||
Коэффициент Пуассона ν |
0,28 |
– |
– |
– |
– |
0,33 |
– |
|
Плотность, кг/м3 |
780 |
– |
– |
– |
– |
– |
– |
|
|
0 |
|
|
|
|
|
|
С учетом влияния на изменение объема теплового расширения и структурных превращений изменение удельного объема для первой части модели составляет 2,710 % объема, для второй части 2,485 % объема, для третьей части модели 2,260 % объема.
Зададим изменение объема в модели ANSYS. Результатом моделирования является распределение напряжений в бандаже (рис. 3).
54
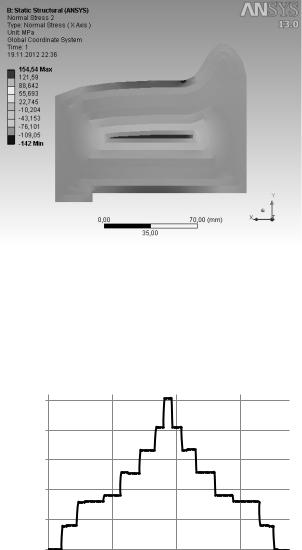
Рис. 3. Распределение напряжений в ободе после охлаждения
График напряжения модели на различном расстоянии от поверхности представлен на рис. 4.
Из результатов моделирования видны сильные сжимающие напряжения на поверхности обода колеса, достигающие 100 МПа. Растягивающие напряжения внутри обода имеют меньшую интенсивность напряжений – 160 МПа. Граница перехода напряжений со сжимающих на растягивающие проходит примерно на 21 мм от поверхности катания обода.
Напряжения σ,МПа
Рис. 4.
150
100
50
0
0 |
20 |
40 |
60 |
-50
-100
Расстояние от поврехности катания, мм
Расстояние от поверхности катания, мм
Напряжения в бандаже на расстоянии от поверхности катания
Данная модель не показывает точное распределение напряжений после закалки, поскольку при задании модели использовалось грубое разбиение на крупные части. Для идеальной модели расстояние между частями разбиения должно стремиться к нулю.
55
Предел текучести закаленной стали 60 равняется 580 МПа, предел прочности при разрыве 900 МПа. Таким образом, для данной модели напряжения при закалке достигают таких величин, при которых на поверхности обода не образуются закалочные дефекты (трещины).
Работа выполнена при частичной поддержке:
‒ Программы стратегического развития Ижевского государственного технического университета им. М. Т. Калашникова на 2012‒2016 годы
(ПСР/М2/Н2.5/МВВ);
- Программы инициативных проектов фундаментальных исследований, выполняемых в Учреждении УрО РАН в 2012-2014 гг. (регистрационный номер: 12-
У-2-1013).
Список литературы
1.Лахтин, Ю.М. Термическая обработка в машиностроении. Справочник / Ю.М. Лахтин, А.Г. Рахштадт. – М.: Машиностроение, 1980. – 783 с.
2.Зубченко, А.С. Марочник сталей и сплавов / А.С. Зубченко, М.М. Колосков, Ю.В. Каширский. – М.: Машиностроение, 2003. – 784 с.
О. И. Волкова, магистрант; В. А. Лукин, аспирант Р. Г. Ризванов, доктор технических наук, профессор
Уфимский государственный нефтяной технический университет
Моделирование напряженно-деформированного состояния сосуда давления с локальным утонением стенки и накладным элементом
В процессе эксплуатации сосудов давления, применяемых в нефтегазовой, нефтеперерабатывающей и нефтехимической отраслях промышленности, в их корпусах возможно возникновение локального утонения стенки из-за коррозионно-эрозионного воздействия рабочей среды, что приводит к местному возрастанию механических напряжений в металле. Дальнейшая эксплуатация сосуда давления, имеющего локальное утонение стенки с остаточной толщиной, меньшей допускаемой величины, возможна после выполнения наплавки металла в зоне утонения, замены дефектного участка установкой ремонтной латки. Но данные способы ремонта имеют следующие недостатки: необходимость вывода из эксплуатации сосуда давления, опорожнения его от продукта, промывки, пропаривания и очистки внутренней поверхности. Все это связано с продолжительным периодом ремонта и значительными экономическими потерями от простоя оборудования. Другим альтернативным способом ремонта является приварка накладки снаружи к корпусу в месте уменьшения толщины стенки. Данный вид ремонта не имеет вышеуказанных недостатков, но не допускается по существующей нормативно-технической документации. Для обоснования возможности применения данного способа ремонта
56
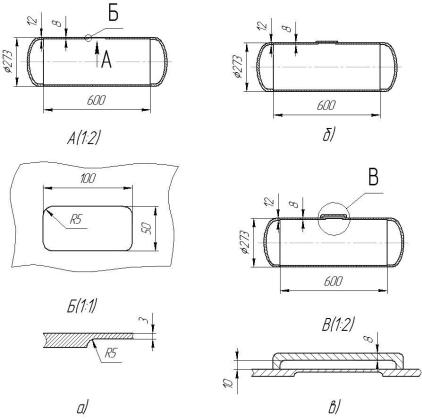
в настоящей работе выполнено численное моделирование напряженнодеформированного состояния сосудов давления без накладного элемента и при его наличии.
Для оценки влияния накладного элемента на несущую способность сосуда давления было выполнено с применением конечно-элементного программного комплекса ANSYS исследование напряженнодеформированного состояния трех одинаковых сосудов, имеющих утонение стенки в виде прямоугольной выборки на внутренней поверхности цилиндрического корпуса (рис. 1). Первый сосуд не имел укрепляющего элемента в зоне утонения (сосуд № 1 – рис. 1, а), два других сосуда были усилены снаружи накладными элементами: сосуд № 2 – плоским приварным накладным элементом (рис. 1, б); сосуд № 3 – колпачковым приварным накладным элементом (рис. 1, в).
Рис. 1. Схемы исследуемых сосудов:
а – сосуд № 1 без укрепления в зоне утонения, б – сосуд № 2 с плоским накладным элементом, в – сосуд № 3 с колпачковым накладным элементом
57
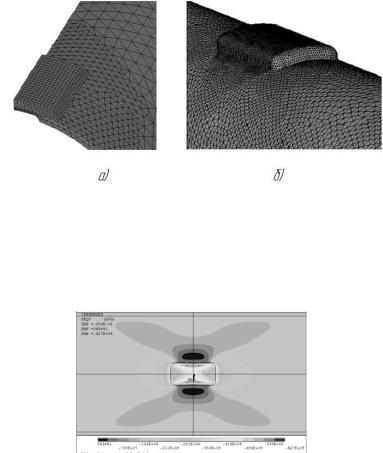
Исследуемые сосуды имели следующие параметры: наружный диаметр корпуса D = 273 мм, толщина стенки корпуса 8 мм, толщина эллиптических днищ 12 мм, длина цилиндрического корпуса 600 мм. В средней части корпуса каждого сосуда имелось утонение с остаточной толщиной 3 мм, размерами 100×50 мм. Физико-механические свойства для материала корпуса и накладного элемента приняты такие же, как для стали 09Г2С.
Первоначально в препроцессоре программы ANSYS были получены конечно-элементные модели исследуемых сосудов (на рисунке 2 показаны фрагменты моделей сосудов с накладными элементами). Далее данные модели нагружались пошагово внутренним давлением от 0 до 16 МПа. При этом учитывалось упруго-пластическое поведение материала сосудов.
Рис. 2. Фрагменты конечно-элементных моделей сосудов: а – сосуд № 2, б – сосуд № 3
На рис. 3, 4 и 5 представлено распределение возникающих под действием внутреннего давления величиной 1 МПа эквивалентных напряжений (по теории прочности Мизеса [1]) на внутренней поверхности цилиндрического корпуса сосудов № 1, № 2 и № 3 соответственно. Максимальные эквивалентные напряжения в сосуде №1 достигают величины 62,7 МПа в зоне утонения, в сосуде № 2 – 54,7 МПа, в сосуде № 3 – 54,6 МПа.
Рис. 3. Распределение эквивалентных напряжений на внутренней поверхности цилиндрического корпуса сосуда № 1 под действием внутреннего давления 1 МПа
58
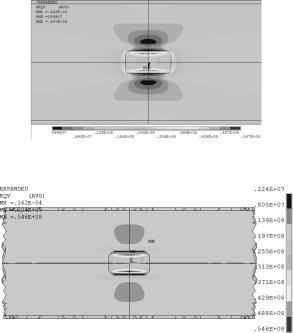
Рис. 4. Распределение эквивалентных напряжений на внутренней поверхности цилиндрического корпуса сосуда № 2 под действием внутреннего давления 1 МПа
Рис. 5. Распределение эквивалентных напряжений на внутренней поверхности цилиндрического корпуса сосуда № 3 под действием внутреннего давления 1 МПа
Из сравнения рис. 3, 4 и 5 видно, что усиление зоны утонения плоским и колпачковым накладными элементами позволяет снизить максимальные эквивалентные напряжения в упругой области деформирования в 1,15 раза.
На рис. 6 показано изменение максимальных эквивалентных напряжений в трех исследуемых сосудах при увеличении внутреннего давления от 1 до 16 МПа. В диапазоне от 1 до 6 МПа максимальные напряжения в сосуде № 1 незначительно превышают напряжения в сосудах № 2 и № 3. При внутреннем давлении в диапазоне от 6 до 10 МПа максимальные напряжения практически одинаковы в трех сосудах и приблизительно равны 240 МПа. При дальнейшем увеличении давления максимальные эквивалентные напряжения в зоне утонения сосуда № 1 начинают резко возрастать, ввиду появления в металле значительных пластических деформаций, и достигают величины 440 МПа при давлении 14 МПа, в то время как в сосудах с накладными элементами указанные напряжения увеличиваются незначительно, и при давлении 14 МПа они не превышают 270 МПа.
59
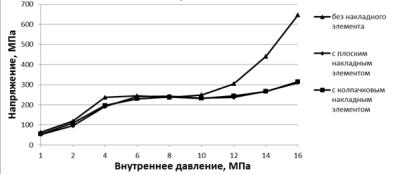
Рис. 6. Зависимость максимальных эквивалентных напряжений от величины внутреннего давления для трех сосудов
Результаты численного моделирования показали, что установка приварного накладного элемента в зоне локального утонения стенки позволяет значительно повысить прочность сосуда давления, особенно в области действия значительного внутреннего давления. Но колпачковые накладные элементы более предпочтительны по сравнению с плоскими накладками. Это связано с тем, что если произойдет сквозное разрушение металла в зоне утонения и рабочая среда попадет в пространство между накладным элементом и корпусом сосуда, то колпачковый элемент способен выдержать большее внутреннее давление, чем плоский элемент.
Таким образом, можно рекомендовать применение наружных колпачковых накладных элементов для ремонта корпусов сосудов давления, а также технологических трубопроводов, имеющих локальное утонение стенки. Это позволит выполнять ремонтные операции без вывода оборудования из эксплуатации, без его опорожнения от продукта, промывки и пропарки. При дальнейшей остановке всей технологической установки на капитальный ремонт можно будет выполнить ремонт сосудов давления и трубопроводов с применением традиционных способов – наплавки или замены дефектного участка.
Список литературы
1. Гольденблат, И.И. Критерии прочности и пластичности конструкционных материалов / И.И. Гольденблат, В.А. Копнов. – М.: Машиностроение, 1968. – 191с.
60
Д. Г. Вылегжанин, аспирант
С. Д. Кугультинов, доктор технических наук, профессор Ижевский государственный технический университет
имени М. Т. Калашникова
Воздушное охлаждение при обработке резанием
Значительное количество деталей машин в современной промышленности получается обработкой резанием. Применительно к охлаждению материалов при резании – можно выделить следующие проблемы: процесс резания сопровождается значительным повышением температуры, вследствие чего возникает значительная тепловая напряженность элементов зоны резания; из-за высокой температуры снижается прочность режущего инструмента, что приводит к снижению его стойкости, преждевременному износу и поломке; повышенная температура приводит к структурным изменениям поверхности обрабатываемого материала, к плавлению его поверхности, короблению, возникновению прижогов, трещин, что, в конечном счете, может привести к браку изделия.
Таким образом, решение вышеописанных проблем – а именно охлаждение зоны резания – позволит: проанализировать и систематизировать существующие методы охлаждения; предложить новые решения по охлаждению; повысить стойкость режущего инструмента; уменьшить негативные тепловые воздействия на обрабатываемый материал, тем самым увеличив его качество; все это, в конечном счете, приведет к повышению качества обработки материалов резанием.
Наиболее распространенный способ охлаждения при резании – полив СОЖ. Применительно к предмету моего исследования охлаждающей средой является воздух. У воздуха, как охладителя мы можем добиться значительного снижения его собственной температуры и значительного расхода, что позволяет эффективно отводить тепло. Кроме того, воздух не имеет стоимости, что позволяет снизить затраты на охлаждение. Достоинство СОЖ по сравнению с воздухом – высокий коэффициент теплопроводности; недостатки – ограниченные возможности по расходу, невозможность охлаждения ниже 0 °С (т.к. по достижении данной температуры вода переходит в твердое состояние), сложность в организации гидросети (по сравнению с пневмосетью), денежные затраты на покупку СОЖ.
Учитывая параметры охладителя (воздуха) выделены следующие задачи работы: анализ и выбор системы подачи потока сжатого воздуха; выбор способа охлаждения воздушного потока; создание конструкции шлифовального круга с предложенной системой охлаждения.
Выбор способа подачи сжатого воздуха
Подача воздуха осевым вентилятором: Основные размеры вентилятора:
‒ внешний диаметр колеса D = 300мм; внутренний диаметр колеса
61
d=150мм; размер колеса в осевом направлении l = 22,5мм; угол наклона лопастей θк = 25°; количество лопастей равно 6; угол между соседними лопастями равен 60°.
Начальные данные:
‒частота вращения вала n = 8000 об/мин; мощность на валу N = 10 кВт; плотность газа ρ = 1,2 кг/м3; давление газа на входе Р = 100000 Па; температура газа Т = 293 К.
Расчетные параметры вентилятора:
‒средняя скорость потока на выходе из вентилятора Uи=36,1 м/с; дав-
ление потока на выходе из вентилятора Рвых=102600 Па; массовый расход воздуха g = 2,2 кг/с; температура газа на выходе Т = 293 К.
Положительными сторонами данного варианта подачи сжатого воздуха являются: высокий массовый (объемный) расход, отсутствие отдельных требований к применяемому оборудованию. Среди отрицательных сторон следует отметить: низкая величина давления подаваемой воздушной струи, большие габариты, большая масса, сложность конструкции, сложность формообразования отдельных частей конструкции, таких как наклонные лопасти, невозможность использования предлагаемого способа охлаждения потока в связи с недостаточным давлением. Исходя из вышесказанного, данный вариант из дальнейшего рассмотрения исключается.
Подача воздуха из заводской пневмосети.
Самым распространенным источником подачи сжатого воздуха является воздушный компрессор. На каждом современном машиностроительном предприятии присутствует система подачи сжатого воздуха с использованием компрессоров. При этом в цехах присутствует пневмосеть со стандартным давлением в ней 4–6 атмосфер и выше.
Параметры сети:
‒давление в сети Р = 4‒5 атм.; температура газа Т = 293 К; диаметр отверстия трубы d= 20 мм.
В качестве системы подачи воздуха решено использовать пневмосеть.
Выбор системы охлаждения потока.
Вданной работе рассмотрены следующие варианты охлаждения:
1)использование сопла Лаваля;
2)использование суживающегося сопла;
1)Сопло Лаваля ‒ техническое приспособление, которое служит для ускорения проходящего по нему газового потока до скоростей, превышающих скорость звука (рис.1).
62
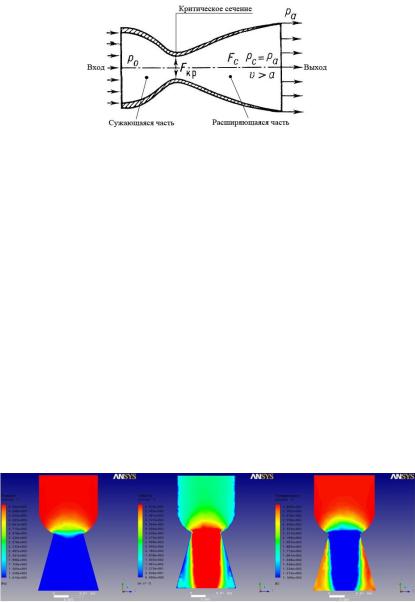
Рис. 1. Схематичное изображение сопла Лаваля
Сопло представляет собой канал, суженный в середине. В простейшем случае такое сопло может состоять из пары усеченных конусов, сопряженных узкими концами.
На сужающемся, докритическом участке сопла движение газа происходит с дозвуковыми скоростями. В самом узком, критическом сечении сопла локальная скорость газа достигает звуковой. На расширяющемся, закритическом участке, газовый поток движется со сверхзвуковыми скоростями. Перемещаясь по соплу, газ расширяется, его температура и давление падают, а скорость возрастает. Внутренняя энергия газа преобразу-
ется в кинетическую энергию его направленного движения. КПД этого преобразования в некоторых случаях (например, в соплах современных ракетных двигателей) может превышать 70 %, что значительно превосходит КПД реальных тепловых двигателей всех других типов. Поскольку притока энергии извне нет, то скачек кинетической энергии сопровождается снижением температуры потока.
Параметры воздуха на входе в сопло: давление Р0 = 500000 Па; температура Т0 = 293 К; рабочее тело – атмосферный воздух.
Результаты расчета параметров потока на срезе сопла в первом приближении: давление P = 150 000 Па; температура Т = 107,3 К; скорость v = 610 м/с; массовый расход газа g = 0,2 кг/с (рис. 2).
Рис. 2. Результаты расчета течения газа в сопле:
распределение давлений (слева), распределение скоростей (по центру), распределение температур(справа)
Параметры рабочего тела (воздуха) на срезе сопла: температура Т ≈ 190 К;
63
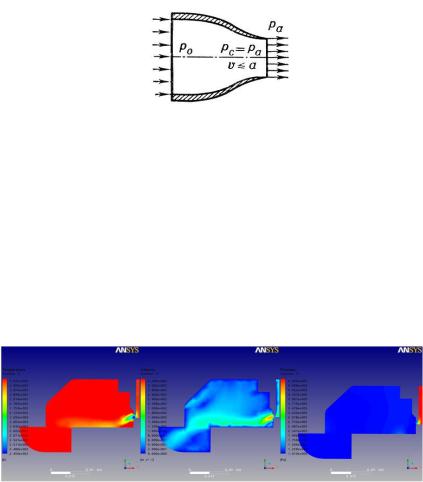
скорость (ядро потока) v ≈ 580 м/с; массовый расход g = 0,2 кг/с.
Параметры рабочего тела (воздуха) в охлаждаемой области детали: температура Т = 230…240 К; скорость v = 180…230 м/с; массовый расход
g= 0,2 кг/с.
2)Суживающееся сопло ‒ это сопло, в котором скорость газового потока способна достичь критического значения (под критической скоростью понимают скорость потока, равную скорости звука), но не способна перейти звуковой барьер (рис. 3).
Рис. 3. Схематичное изображение суживающегося сопла
Фактически суживающееся сопло представляет собой то ‒ же сопло Лаваля, но без расширяющейся обечайки. При достаточном перепаде давлений выходное сечение сопла становится критическим и скорость потока в нем может достичь скорости звука. Соответственно, при таком изменении скорости потока можно добиться значительного снижения температуры потока в критическом сечении и после него.
Параметры на входе: давление Р0 = 500000 Па; температура Т0=293 К; рабочее тело – атмосферный воздух.
Результаты расчета параметров потока на срезе сопла в первом приближении: давление P = 260 000 Па; температура Т = 244 К; скорость v = 313,219 м/с; массовый расход газа g = 0,2 кг/с.
Результаты расчета течения газа при вытекании в условную полость представлены на рис. 4:
Рис. 4. Результаты расчета течения газа в сопле:
распределение температур (слева), распределение скоростей (по центру), распределение давлений (справа)
Параметры рабочего тела на срезе сопла: температура Т ≈ 250 К; ско-
64
рость (ядро потока) v ≈ 320 м/с; массовый расход g = 0,2 кг/с.
Параметры рабочего тела в охлаждаемой области детали: температура
Т= 280…285 К; скорость v = 100‒130 м/с; массовый расход g = 0,2 кг/с.
Вданной статье проиллюстрирована возможность охлаждения воздуха без использования внешних источников энергии, за счет геометрического воздействия на поток. В качестве способов данного геометрического воздействия рассмотрено использование сопла Лаваля и суживающегося сопла. Согласно представленным расчетам, оба варианта позволяют достичь значительного снижения температуры потока воздуха. Полученный таким образом охлажденный воздушный поток можно в дальнейшем использовать для охлаждения зоны резания при механической обработке
Список литературы
1.Кугультинов, С.Д. Технология обработки конструкционных материалов / С.Д. Кугультинов, А.К. Ковальчук, И.И. Портнов. – М.: МГТУ им. Н.Э. Баумана,
2006. – 680 с.
2.Резников, А.Н. Теплофизика процессов механической обработки материалов / А.Н. Резников. – М.: Машиностроение, 1981. – 279 с.
3.Нащокин, В.В. Техническая термодинамика и теплопередача / В.В. Нащокин. – М.: Высшая школа, 1980. – 560 с.
4.Гримитлин, А.Н. Насосы, вентиляторы, компрессоры в инженерном оборудовании зданий / А.Н. Гримитлин, О.П. Иванов, В.А. Пухкал. - Санкт-Петербург: АВОК Северо-Запад, 2006. – 202 с.
5.Поляков, В.В. Насосы и вентиляторы / В.В. Поляков, Л.С. Скворцов. – М.: Стройиздат, 1990. – 336 с.
6.Богословский, В.Н. Отопление и вентиляция / В.Н. Богословский, В.П. Щеглов, Н.Н. Разумов. – М.: Стройиздат, 1980. – 295 с.
7.Иров, Ю.Д. Газодинамические функции / Ю.Д. Иров, Э.В. Кейль, Б.Н. Маслов. - М : Машиностроение, 1965. – 399 с.
8.Ковальногов, Н.Н. Расчет течения и сопротивления трения потока в соплах Лаваля / Н.Н. Ковальногов, А.С. Ртищева. - Ульяновск : УлГТУ, 2007. – 32 с.
А. А. Гончаров, аспирант
Б. А. Жуков, доктор технических наук, профессор Волгоградский государственный технический университет
Оценка влияния прижимного устройства на самоторможение клиновых механизмов свободного хода
Высокие эксплуатационные характеристики (нагрузочная способность угловая жесткость и быстродействие) выдвигают клиновые механизмы свободного хода (МСХ) с кинематической связью [1] в разряд наиболее перспективных для использования в качестве выпрямителей механиче-
65
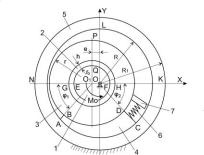
ских колебаний. Указанные МСХ представляют собой сложную триботехническую систему, структура и поведение которой зависит от геометрии элементов, коэффициентов трения, реализуемых на их контактных поверхностях, и условий нагружения. Исследования [2] позволили определить закономерности распределения наиболее важных контактных характеристик и получить теоретические оценки работоспособности указанных механизмов. В публикуемой работе приводятся результаты моделирования поведения МСХ в стоповом режиме при наличии прижимного устройства. Приведем краткую формулировку контактной задачи.
Рассмотрим процесс заклинивания МСХ в условиях квазистатического нагружения. Расчетная схема триботехнической системы МСХ представлена на рис. 1. Упругие свойства элементов задают значения материальных констант ‒ модуля Юнга (Е) и коэффициента Пуассона ( ), конфигурацию звеньев фрикционной модели механизма ‒ геометрические параметры: эксцентриситет e, радиусы вала, подшипника и обойм (клина) соответственно ro, r, R, R1, толщина подшипника h и углы радиальных срезов клина θ1, θ2.
Граничноэлементная модель построена на следующих упрощающих допущениях. Считалось, что нагрузка ширине тел распределена равномерно; элементы МСХ находятся в условиях плоского напряженного состояния, и имеют идеально сопрягаемые контактные поверхности; валэксцентрик является абсолютно жестким телом, подшипник, обоймы и клин – идеально упругими; в области контакта вала-эксцентрика с жестко закрепленным в ведущей обойме радиальным подшипником отсутствует трение; в областях контакта клина с обоймами силы трения подчиняются закону Амонтона. В стоповом режиме ведомая обойма 5 жестко закреплена, и остановка ведущего звена 1 механизма, нагруженного внешним моментом Mo, должна осуществляться за счет внутренних сил ‒ сил трения, возникающих на контактных поверхностях клина BD и AC, и действующего на клин 4 усилия пружины 6.
Рис. 1. Триботехническая система клинового МСХ:
1 – вал-эксцентрик, 2 ‒ подшипник, 3 – ведущая обойма, 4 – клин, 5 – ведомая обойма, 6 – пружина, 7 – упор
66
При граничноэлементной аппроксимации [3] напряженнодеформированное состояние (НДС) элементов триботехнической системы описывает формируемая для узловых значений нормальных и касательных перемещений, (un, uη)и напряжений (ζ, η) система алгебраических уравнений следующего вида:
[C] {X} = {Y}, |
(1) |
где [C] – матрица коэффициентов влияния, {X} – вектор неизвестных граничных параметров, {Y} ‒ вектор линейных комбинаций известных параметров, задаваемых как граничные условия на контурах элементов.
Уравнения статического равновесия (1) дополняют граничные усло-
вия, имитирующие действие механической нагрузки, внешние и внутренние связи системы: un = un*, η = 0, (x, y) EF, η = ζ = 0, (x,y) EQF. ζ = ζ*, η = 0 (x, y) CD, un = uη = 0 (x, y) KNLK. un2 = -un3, uη2 = -uη3, ζ2 =
ζ3, η2 = η3, (x,y) GPH; un4 = -un5, ζ4 = ζ5, | η4| ≤ fAC| ζ4|, | η5| ≤ fAC| ζ5|, (x,y)AC, где un*= f (ε, θ) – нормальные перемещения точек поверхности
подшипника, ε – угол поворота эксцентрика 1, θ – угол, задающий положение исследуемой точки в области контакта EF ; ζ* – нормальные напряжения, соответствующие усилию пружины; fBD, fAC – реализуемые на границах клина коэффициенты трения. Буквенные и цифровые обозначения соответствуют обозначениям и позициям элементов на рис.1.
В качестве критериев кинематического состояния системы использовались соотношения между нормальными и касательными усилиями в областях BD и AC контакта клина с обоймами, определяющими в рамках закона Амонтона два состояния фрикционного взаимодействия – жесткого сцепления и относительного проскальзывания элементов соответственно:
| η| ≤ fBD| ζ|, | η| ≤ fAC| ζ|, (2) |
| η| ≥ fBD| ζ|, | η| ≥ fAC| ζ| |
(3). |
Нелинейный анализ выполнялся в процессе поэтапного нагружения при помощи двух основных итерационных процедур, одна из которых связана с моделированием процесса нагружения механизма, вторая – с определением его кинематического состояния. В качестве параметра, управляющего процессом деформирования, использовался пропорциональный величине момента M0 угол поворота эксцентрика . Распределения нормальных давлений в сформированной области контакта EF связаны со значением момента внешней нагрузки интегральным соотношением:
M0 = r0 e ∫EF ζ sinθ dθ |
(4) |
Алгоритм процедуры определения кинематического состояния МСХ базировался на анализе распределений нормальных давлений и сил трения на границах клина с обоймами с учетом условий (2) и (3).
Ниже представлены результаты исследования влияния усилия пружины на условия фрикционного сцепления элементов МСХ. Моделиро-
67
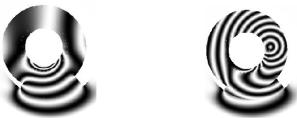
вание, выполненное на сетке из 720 граничных элементов, показало, что при значениях fAC = fBD = 0,118 МСХ с геометрическими параметрами: e =
5 мм; ro =13 мм; h = 3 мм; r = 29 мм; R = 35 мм; R1 = 50 мм; 1 = 60 ; 2
=60 и соответствующими их нумерации на рис.1 упругими характери-
стиками: Е2 =1,05105 МПа, Е3 = Е4 = Е5= 2,1
105 МПа, 2 = 0,3, 3 = 4 = 5
= 0,29 является самотормозящимся в отсутствие поджимающего устройства. С уменьшением коэффициентов МСХ в идентичных условиях нагружения утрачивает эту способность. Изменение кинематического состояния механизма при уменьшении коэффициента трения показывают
на рис. 2 картины деформированного состояния модели МСХ [4]. Изолинии суммарных перемещений usum = (ux2+uy2)1/2, где ux, uy ‒ компоненты
вектора, соответствуют цене полосы 0,015 мм. Очевидно, что в самотормозящемся механизме они имеют деформационный характер (рис. 2а), в несамотормозящемся механизме – кинематический (рис. 2б).
На рис. 3 показаны результаты моделирования поведения несамотормозящегося МСХ (f = fAC = fBD = 0,1) при совместном действии момента M0 и постоянного усилия пружины F = 30 Н.
а) f =0,118 |
б) f = 0,1 |
Рис. 2. Трансформирование кинематического состояния МСХ при уменьшении коэффициента трения
Решение задачи осуществлялось в процессе поэтапного нагружения: M0 = 0,..., M0max , где M0max – величина момента, вызывающая проскаль-
зывание МСХ. На рис. 3 даны распределения поверхностных усилий в неблагоприятной для сцепления области контакта клина с ведомой обоймой. Семейства кривых построены при определяемых равенством (4) значениях удельного момента M0: 4,4, 6,6, 8,0 и 8,8 Нм. Анализ зависимостей показал, что усилие пружины оказывает влияние на механизм контактного взаимодействия элементов. При неизменном характере нормальных давлений (рис. 3а) от усилия пружины существенно зависит формирование системы сил трения, создающей сопротивление относительному скольжению элементов (рис. 3б). Более детально состояние фрикционного контакта клина с обоймами описывают построенные на его границах графические зависимости модуля отношения указанных сил | η/ζ|. Данное отношение определяет локализацию и протяженность зон с различными условиями (2) и (3) фрикционного контакта тел – жесткого сцепления Lst
68
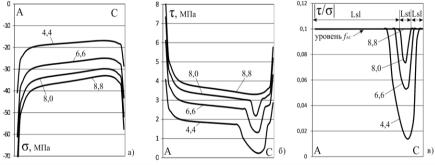
и относительного проскальзывания Lsl. Распределения | η/ζ| на рис. 3в иллюстрируют процесс эволюционного вырождения зон жесткого сцепления в области контакта AC при увеличении M0 до значения 8,8 Нм. Определяя момент усилия пружины относительно центра механизма Mпр = 0,96 Нм, получим силовое условие самоторможения исследуемого механизма в виде: 0 < M0 < 9 Mпр. Отметим, что данное соотношение между параметрами нагружения имеет частный характер, оно определяет кинематическое состояние только исследованной триботехнической системы.
Результаты моделирования показывают, что в условиях нестабильности коэффициента трения запас по сцеплению элементов МСХ может создаваться усилием поджимающего клин устройства. При этом следует иметь в виду, что изменение геометрических параметров элементов МСХ оказывает существенное влияние на величину минимального усилия пружины.
Рис. 3. Распределение нормальных давлений (а), сил трения (б)
и модуля отношения | η/ζ| в зоне контакта клина с ведомой обоймой
Выполненный анализ позволяет сделать следующие выводы:
1.Разработанная статическая гранично-элементная модель и контактный алгоритм позволяют исследовать поведение клиновых МСХ как неконсервативных механических систем переменной структуры в фазе активного нагружения при условиях сухого и граничного трения и определять наиболее важные триботехнические характеристики с учетом явлений макро- и микроскольжения тел.
2.Поджимающее устройство создает положительный эффект, заключающийся в улучшении фрикционного сцепления обойм с клином. Использование данного эффекта позволяет осуществлять проектирование клиновых МСХ при нестабильных значениях коэффициентов трения. Выбор оптимального усилия пружины должен осуществляться с учетом типа проектируемого механизма, конструктивных и динамических особенностей привода.
69
Список литературы
1.Благонравов, А.А. Механические бесступенчатые передачи нефрикционного типа / А.А. Благонравов. – М.: Машиностроение, 1977. – 145 с.
2.Гончаров, А.А. Неконсервативная гранично-элементная модель клиновых механизмов свободного хода / А.А. Гончаров // Проблемы машиностроения и надежности машин. - 2008. - №2. - С. 28-36.
3.Крауч, С. Методы граничных элементов в механике твердого тела / С. Крауч, А. Старфилд. – М.: Мир, 1987. – 328 с.
4.Гончаров, А.А. Определение триботехнических характеристик клинового
механизма свободного хода / А.А. Гончаров // Трение и смазка в машинах и механизмах. - 2011. - №11. - С. 3-11.
А. С. Горбунов, аспирант; Р. Д. Каримов, аспирант Д. В. Гусаков, аспирант
Л. Э. Рогинская, доктор технических наук, профессор Уфимский государственный авиационный технический университет
Параметрический синтез индукторно-конденсаторного модуля в полупроводниковом преобразователе частоты для электротехнологий
Электротехнологией следует считать область промышленной технологии, в которой электрические и магнитные явления используются для непосредственного воздействия на обрабатываемый объект. При этом индукционным нагревом называют электротехнологические процессы передачи энергии обрабатываемому объекту за счет явления электромагнитной индукции [1].
Индукционный нагрев металлов, применяемый в промышленных установках с конца XIX в., в настоящее время получил широкое распространение во многих областях промышленности. Причиной такого успеха индукционного нагрева являются достоинства, присущие этому виду нагрева, которые в основном определяются тем, что при индукционном нагреве теплота выделяется непосредственно в нагреваемом теле, благодаря чему, во-первых, использование тепла оказывается более совершенным (т.е. при более высоком тепловом КПД) и, во-вторых, обеспечивается значительно большая скорость нагрева [2].
Моделирование полупроводникового преобразователя частоты
В настоящее время в связи с расширяющимся применением индукционного нагрева в промышленности возникает необходимость улучшения технико-экономических показателей применяемых установок для индукционного нагрева, а также определения и учета параметров применяемых в них взаимоиндуктивных модулей.
На сегодняшний день основными элементами индукционных установок являются: высокочастотный источник питания и нагрузочный колеба-
70
тельный контур, состоящий из индуктора и компенсирующей батареи конденсаторов [1]. Компенсирующая батарея конденсаторов необходима для повышения коэффициента мощности нагрузочного контура до единицы, так как коэффициент мощности индукторов очень низок, и составляет значения около 0,1 для средних частот и подключение такой индуктивной нагрузки непосредственно к источнику питания вызовет потребление значительной реактивной мощности из сети, бесполезно загружая провода, а также значительно увеличивая установленную мощность элементов индукционных установок [3].
В качестве высокочастотного источника питания могут выступать тиристорные и транзисторные (полупроводниковые), а также ламповые преобразователи частоты.
Кроме того, следует отметить, что у применяемых высокочастотных источников питания для индукционных установок выходное напряжение нестандартно, и может составлять, например, 250…400 В для источника питания на базе несимметричного одноячейкового инвертора. Для согласования такого нестандартного выходного напряжения с номинальным напряжением индукторов в источниках питания для индукционных установок часто применяют согласующие высокочастотные трансформаторы [3].
Кроме согласующего высокочастотного трансформатора в индукционных установках применяются такие взаимоиндуктивные модули, как дроссели переменного тока, сглаживающие дроссели и дроссели насыщения.
Для исследования электромагнитных процессов в индукционных установках рационально применение моделирования в пакете Matlab, что позволяет на этапе расчетов и проектирования без проведения дорогостоящих экспериментов и с приемлемой точностью определить параметры элементов индукционных установок, оценить работоспособность проектируемых индукционных установок, а также осуществлять оптимизацию параметров элементов индукционных установок.
На рис. 1 показана имитационная модель индукционной установки, созданная в пакете Matlab. Ее особенностью является то, что в данной установке осуществлена параллельная компенсация реактивной мощности индуктора. Как видно из рис. 1, в данной установке имеется три резонансных контура: фильтровый (представленный сопротивлением Rd, индуктивностью Ld), коммутирующий (представленный индуктивностью Lk, емкостью Ck) и нагрузочный (представленный сопротивлением Rn, индуктивностью Ln и емкостью Cn), что значительно усложняет данную установку.
71
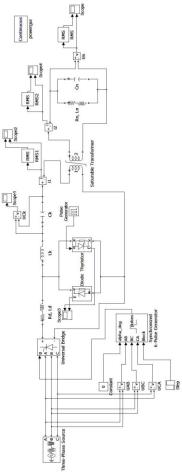
Рис. 1. Имитационная модель индукционной установки с параллельной компенсацией
Для решения задачи повышения технико-экономических показателей индукционных установок путем упрощения конструкции индукционной установки и, соответственно, повышения надежности данной установки, предлагается схема, имитационная модель которой представлена на рис. 2. Особенностью данной схемы является то, что в ней осуществлена последовательная компенсация реактивной мощности индуктора, с одновременным упрощением схемы индукционной установки путем объединения коммутирующего и нагрузочного контуров с соответствующим уменьшением числа элементов индукционной установки.
72
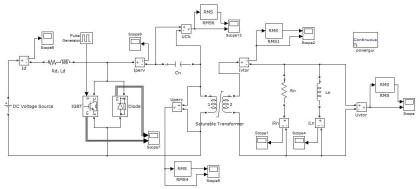
Стоит также отметить, что в схеме на рис. 2, по сравнению со схемой на рис. 1, в качестве управляемого полупроводникового прибора использован транзистор (IGBT или MOSFET), что позволяет значительно расширить частотный диапазон применения данных индукционных установок, так как данные транзисторы могут работать при значительно большей частоте переключения, нежели тиристоры вследствие того, что транзисторам не требуется время для восстановления управляющих свойств.
Рис. 2. Имитационная модель индукционной установки с последовательной компенсацией
Результатами моделирования являются графики мгновенных значений напряжений на первичной uперв и вторичной uвтор обмотках согласующего высокочастотного трансформатора, а также действующие значения токов в активном iRn и индуктивном iLn сопротивлении индуктора (рис. 3).
По результатам моделирования можно отметить, что применение согласующих высокочастотных трансформаторов позволяет согласовать выходное напряжение источника питания с номинальным напряжением индуктора. Данный трансформатор моделировался с магнитопроводом из аморфных или нанокристаллических сплавов, при этом, как показали расчеты, данный трансформатор имеет малые габариты и значительно более высокие технико-экономические показатели, нежели обычно применяемые согласующие высокочастотные трансформаторы с магнитопроводами, выполненными из электротехнической стали, ферритов, магнитодиэлектриков. Во время работы данной установки наблюдаются два режима:
1.Ток проводят транзистор, а затем диод. При этом происходит колебательный перезаряд компенсирующего конденсатора и в нагрузке протекает синусоидальная волна тока, с периодом, зависящим от соотношения индуктивности Ln и емкости Cn.
2.Режим паузы в работе транзисторно-диодной пары, когда в нагрузке протекает ток, сглаженный фильтровым дросселем, и происходит заряд компенсирующего конденсатора.
73
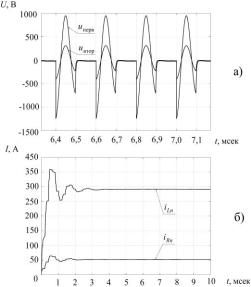
Рис. 3. Результаты моделирования:
а) Кривые мгновенных значений напряжений на первичной uперв и вторичной uвтор обмотках согласующего трансформатора;
б) Кривые действующих значений токов в активном iRn и индуктивном iLn сопротивлении индуктора
Применение имитационного моделирования в пакете Matlab позволяет исследовать электромагнитные процессы в индукционных установках с учетом применяемых модулей. Применение магнитопроводов из аморфных или нанокристаллических сплавов позволяет повысить энергетические и массогабаритные показатели всех взаимоиндуктивных модулей.
Список литературы
1.Белкин, А.К. Элементы индукционных установок / А.К. Белкин, Л.И. Гутин, И.Н. Таназлы. – М.: Энергоатомиздат, 2007. – 140 с.
2.Вайнберг, А.М. Индукционные плавильные печи / А.М. Вайнберг. – Л.: Госэнергоиздат, 1960. – 456 с.
3.Белкин, А.К. Тиристорные преобразователи частоты / А.К. Белкин, Т.П. Костюкова, Л.Э.Рогинская. - М : Энергоатомиздат, 2000. – 263 с.
74

А. Р. Горзолия, магистрант
А. В. Губерт, кандидат технических наук, доцент Ижевский государственный технический университет имени М. Т. Калашникова
Проектирование лабораторного пульсирующего воздушно-реактивного двигателя
Лабораторный пульсирующий воздушно-реактивный двигатель (ПуВРД) проектируется в учебных целях, для наглядной демонстрации работы двигателя и рабочих процессов.
Среди всех реактивных двигателей, менее изученными до сих пор остаются пульсирующие воздушно-реактивные двигатели. Интерес к созданию пульсирующего воздушно-реактивного двигателя вызывает простота конструкции и дешевизна.
Для расчета термодинамических параметров рабочего процесса ПуВРД ввели допущение о изохорности процесса и применили термодинамический цикл Ленуара.
Рис. 1. Термодинамический цикл Ленуара в pv-координатах
Данная модель является наиболее простой, и позволяет провести грубую оценку термодинамических параметров рабочего цикла ПуВРД, необходимых на первом этапе изучения.
В начальный момент труба на заданную длину заполнена сжатым горячим газом с заданными параметрами. Работа расширения рабочего тела считается равной кинетической энергии газа на срезе трубы [3].
75
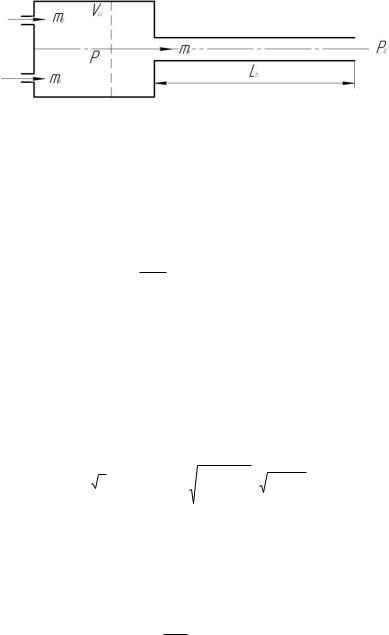
Рис. 2. Расчетная схема аппарата пульсирующего горения:
mg – расход топлива, ma – расход воздуха, me – расход продуктов сгорания через резонансную трубу, Vcc – объем камеры сгорания, Ltp – длина резонансной
трубы, P – давление в камере сгорания, P0 – атмосферное давление
При составлении модели рассматривался закон сохранения энергии применительно ко всей системе, а также уравнение баланса расхода для камеры сгорания и уравнение сохранения импульса для потока в резонансной трубе [1].
Уравнение энергии формулируется в следующем виде[2]:
dEcc Q hr mr he me , dt
где Ecc – энергия в камере сгорания, t – время, Q – количество подведенного тепла, hr и he – удельная энтальпия смеси и продуктов сгорания соответственно, mr – расход смеси в камеру сгорания, me – расход продуктов сгорания из камеры в резонансную трубу.
Расход газообразного топлива и воздуха моделируется уравнением расхода через отверстие для квазистационарного потока, исходя из допущения, что механические клапаны имеют два положения ‒ полностью открыты или полностью закрыты. Давление на входе в топливный клапан считается равным давлению на входе в воздушный клапан и равно атмосферному P0.
Уравнение переменного расхода заряда имеет вид:
|
|
|
|
|
|
|
|
|
|
|
|
|
|
|
|
m t |
2 |
|
C A |
1 |
|
a |
|
Ca Aa |
|
|
P P |
|
f |
P P , |
|
|
|
|
|
||||||||||||
|
|
|
|
C A |
|||||||||||
r |
|
g |
g g |
|
|
|
|
|
|
0 |
|
1 |
0 |
||
|
|
|
|
|
|
|
g |
|
g g |
|
|
|
|
|
где ρa и ρg – плотность воздуха и топлива соответственно, Сa и Сg – коэффициенты расхода для воздушного топливного клапанов соответственно, Aa и Ag – проходные площади для воздушного и топливного клапанов, P – давление в камере сгорания, f1(P-P0) – индикаторная функция, зависящая от значения избыточного давления в камере сгорания.
Изменение импульса в резонансной трубе описывается уравнением:
Lтр dme Aтр P P0 , dt
76
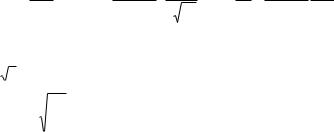
где Lтр – длина резонансной трубы, Aтр – площадь поперечного сечения резонансной трубы.
На основе уравнений выведено нелинейное дифференциальное уравнение второго порядка для изменения давления в камере сгорания:
|
d 2 p |
|
|
|
|
|
1 h |
|
|
1 |
|
|
dp |
|
1 h |
A |
|
|||
|
|
|
|
kg 1 r |
e |
|
|
|
|
f1 p |
|
|
e |
тр |
0 , |
|||||
|
dt |
2 |
|
V |
|
|
|
|
|
|
V |
L |
||||||||
|
|
|
|
|
|
|
|
|
2 |
|
|
p |
|
dt |
|
|
||||
|
|
|
|
|
|
|
|
|
cc |
|
|
|
|
|
|
cc |
тр |
|
||
|
p P P0 |
|
|
|
|
|
|
|
|
|
|
|
|
|
||||||
где |
|
– |
избыточное |
|
|
давление в камере сгорания, |
||||||||||||||
kg |
2g Cg Ag – |
параметр характеризующий расход через топливный |
||||||||||||||||||
клапан, r |
|
a |
|
Ca Aa |
– соотношение расхода воздуха и топлива, γ – со- |
|||||||||||||||
|
|
g |
C |
A |
||||||||||||||||
|
|
|
|
|
|
|
|
|
|
|
|
|
|
|
|
|||||
|
|
|
|
|
g g |
|
|
|
|
|
|
|
|
|
|
|
|
|
отношение удельных теплоемкостей.
Данная модель позволяет оценить параметры ПуВРД необходимые для проектирования лабораторного двигателя и исследовать его характеристики при различных начальных условиях.
Список литературы
1.Акимов, В.М. Теория и расчет воздушно-реактивных двигателей / В.М. Акимов, В.И. Бакулев, Р.И. Курзинер. – М.: Машиностроение, 1987. – 568 с.
2.Бородин, В.А. Авиамодельный пульсирующий воздушно-реактивный двигатель / В.А. Бородин . – М.: Всесоюзное добровольное общество содействия авиации, 1951. – 96 с.
3.Сейфетдинов, Р. Рабочий процесс воздушных-турбореактивных двигате-
лей. LAP LAMBERT Academic Publishing GmbH & Co. KG, 2011. – 127 с.
А. О. Деев, магистрант А. В. Победин, кандидат технических наук, профессор
Волгоградский государственный технический университет, Волгоград
Метод оценки и снижения внутреннего шума легковых автомобилей
Исследование шума является актуальным в области машиностроения. Находясь за рулем автомобиля, водитель постоянно испытывает на себе звуковое давление, чрезмерный уровень которого способен негативно повлиять на его состояние. Необходимо проводить исследования и выявлять методы по снижению шума.
Проведение эксперимента по измерению и снижению уровня шума, в общем случае, можно разделить на два этапа:
‒ Проведение замеров уровня шума в автомобиле с заводскими эле-
77
ментами вибро- и шумоизоляции.
‒ Проведение замеров уровня шума в этом же автомобиле, но уже после виброшумоизоляционной подготовки пола, дверей, потолка, а также колесных арок.
Измерения проводились при разгоне автомобиля на каждой передаче в режиме 2000 об/мин, 3000 об/мин, 4000 об/мин.
При замерах не допускалось движение автомобиля накатом.
На каждой передаче, при каждом режиме, проводилось не менее трех измерений. За результат измерения принималось среднее арифметическое трех полученных значений[2].
На начальном этапе эксперимента производятся замеры уровня шума в салоне автомобиля в заводском исполнении, после чего, полученные результаты сводятся в таблицу. Результаты, полученные при измерении уровня шума в салоне автомобиля ВАЗ 2170, представлены в табл. 1.
Для измерения уровня шума использовался измерительный прибор – шумомер SL-401. Измерения проводились по шкале А, при этом диапазон измеряемых уровней шумности лежит в пределах от 30 до 90 дБ при частотных границах от 20 до 20 кГц [1].
Таблица 1. Результаты, полученные после первого этапа эксперимента
Частота, Гц |
|
I передача |
|
II передача |
III передача |
IV передача |
|||||||
2000 |
|
3000 |
|
4000 |
2000 |
3000 |
4000 |
2000 |
3000 |
4000 |
2000 |
3000 |
|
|
|
|
|||||||||||
All |
64,1 |
|
69,8 |
|
71,5 |
70,3 |
72,6 |
74,9 |
71,8 |
74,2 |
77 |
74,9 |
79,8 |
20 Hz |
41,7 |
|
35,5 |
|
39 |
40,8 |
52,4 |
39 |
40,1 |
51,9 |
42,2 |
45,6 |
41,8 |
40 Hz |
53,6 |
|
5,9 |
|
53,7 |
53,4 |
60,5 |
52,8 |
60,3 |
55,6 |
60,2 |
51,9 |
55,2 |
80 Hz |
45,7 |
|
50,5 |
|
50,7 |
54,4 |
49,9 |
51,6 |
49,3 |
48,3 |
52,7 |
48,3 |
50,9 |
160 Hz |
50,8 |
|
64,6 |
|
57,9 |
62,9 |
61,4 |
62,3 |
63,9 |
61,8 |
62,6 |
61,4 |
65,5 |
200 Hz |
50,3 |
|
57,2 |
|
61,4 |
58 |
61 |
66,5 |
60,8 |
63,4 |
68,9 |
65,9 |
69,6 |
400 Hz |
46,2 |
|
53,6 |
|
56,3 |
51,7 |
56,4 |
58,5 |
52,9 |
58,5 |
61,2 |
57,8 |
65,5 |
500 Hz |
45,5 |
|
50,2 |
|
58,3 |
52,4 |
56,3 |
59,4 |
54,6 |
57,5 |
66 |
57,2 |
66,7 |
800 Hz |
45,4 |
|
49,5 |
|
56 |
52,5 |
54,9 |
60,2 |
54,1 |
59,4 |
63,7 |
59,8 |
62,9 |
1k Hz |
44,1 |
|
51,2 |
|
55,3 |
50,2 |
54,5 |
58,8 |
55,1 |
60,7 |
65,3 |
57,8 |
63,5 |
1k25 Hz |
40,2 |
|
45,9 |
|
51,2 |
50,5 |
51,3 |
54,9 |
50 |
56,1 |
59,1 |
55,6 |
58,7 |
1k6 Hz |
37,6 |
|
43,5 |
|
49,3 |
46,4 |
50,4 |
50,6 |
47,3 |
53,9 |
56,7 |
52,9 |
57,2 |
2k Hz |
33,8 |
|
40,3 |
|
50,1 |
42,8 |
47,7 |
47,8 |
42,9 |
47,2 |
51,3 |
46,1 |
51,1 |
2k5 Hz |
33 |
|
40,7 |
|
50,7 |
43,2 |
48 |
49,4 |
41,1 |
46 |
52,9 |
40,4 |
49,9 |
3k15 Hz |
31,2 |
|
38,3 |
|
48,2 |
38,4 |
44,6 |
47,8 |
38,8 |
42 |
48,8 |
38,2 |
45,7 |
4k Hz |
30,1 |
|
35,2 |
|
40,1 |
32,6 |
38,1 |
40,7 |
32,5 |
38,7 |
41,7 |
33,1 |
39,6 |
После проведения первого этапа эксперимента, обработки полученных данных, была произведена разборка салона автомобиля с целью нанесения на внутренние поверхности виброшумопоглощающего материала. Оклейка внутренних полостей автомобиля производилась по следующему принципу.
78
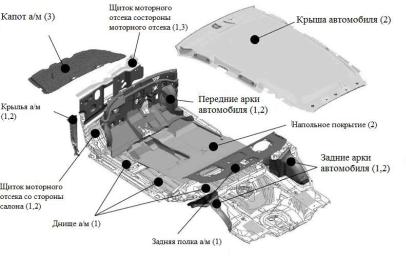
Рис. 1. Схема оклейки автомобиля шумо-виброизоляционными материалами: 1 – вибропоглощающий материал (Бипласт, Бимаст, Визомат);
2 –звукопоглощающий материал (Акцент, Бипласт); 3 – тепло-звукоизоляционный материал (Шумофф П)
После завершения нанесения шумоизоляционных материалов были произведены повторные замеры уровня шума в салоне автомобиля, при этом место время и погодные условия вторых замеров максимально приближены к условиям, имевшим место быть в первой части эксперимента. Результаты, полученные во второй части эксперимента представлены в табл. 2.
Таблица 2. Результаты, полученные после второго этапа эксперимента
Частоты, Гц |
|
I передача |
|
II передача |
III передача |
IV передача |
|||||||
2000 |
|
3000 |
|
4000 |
2000 |
3000 |
4000 |
2000 |
3000 |
4000 |
2000 |
3000 |
|
|
|
|
|||||||||||
All |
61,8 |
|
67,6 |
|
69,8 |
66,3 |
69,3 |
72,3 |
68,9 |
71,5 |
73,5 |
70,5 |
74,3 |
20 Hz |
40,5 |
|
33,9 |
|
37,4 |
38,3 |
50,7 |
37,5 |
38,4 |
50,2 |
40,6 |
43,7 |
39,8 |
40 Hz |
52,9 |
|
5,2 |
|
52,9 |
51,7 |
59,4 |
52,1 |
59,5 |
54,9 |
59,5 |
51 |
53,6 |
80 Hz |
44,6 |
|
49,4 |
|
49,6 |
48,2 |
48,6 |
50,8 |
48 |
47,1 |
51,3 |
46,9 |
48,6 |
160 Hz |
49,8 |
|
63,6 |
|
56,9 |
59,5 |
60,4 |
61,1 |
62,1 |
60,8 |
61,8 |
59,9 |
63,6 |
200 Hz |
48,7 |
|
55,6 |
|
59,8 |
54,4 |
59,4 |
64,7 |
59,1 |
61,8 |
66,9 |
63,7 |
68,1 |
400 Hz |
44,9 |
|
52,3 |
|
55 |
49,9 |
55 |
57,2 |
51,6 |
57,6 |
59,9 |
56 |
63,4 |
500 Hz |
44,6 |
|
49,3 |
|
57,4 |
49,8 |
55,2 |
58,5 |
53,5 |
56,1 |
65,1 |
54,5 |
64,7 |
800 Hz |
43,1 |
|
47,2 |
|
53,7 |
47,1 |
52,4 |
57,9 |
52,3 |
57,1 |
61,4 |
55,6 |
59,7 |
1k Hz |
41,4 |
|
48 |
|
52,6 |
46,4 |
51,6 |
56,1 |
52,8 |
58,2 |
62,6 |
54,7 |
59,9 |
1k25 Hz |
38,3 |
|
44 |
|
49,3 |
45,5 |
49,4 |
53 |
48,1 |
54,2 |
57,2 |
52,8 |
56 |
1k6 Hz |
35,1 |
|
41 |
|
46,8 |
43,2 |
47,9 |
48,1 |
44,8 |
51,4 |
54,2 |
50,1 |
53,8 |
2k Hz |
32,2 |
|
38,8 |
|
49 |
39,3 |
46 |
46,2 |
40,7 |
46,1 |
49,9 |
43,7 |
48,9 |
2k5 Hz |
31,4 |
|
39,2 |
|
49 |
38,5 |
46,4 |
47,5 |
40 |
44,4 |
51,3 |
39,8 |
47,6 |
3k15 Hz |
31 |
|
36,3 |
|
47 |
34,2 |
42,4 |
45,6 |
36,6 |
39,8 |
46,6 |
35,1 |
42,7 |
4k Hz |
30,1 |
|
31,2 |
|
38,9 |
32,1 |
36,7 |
38,6 |
30,4 |
36,6 |
39,6 |
30,2 |
36,8 |
79
В результате эксперимента было установлено, что благодаря нанесению виброшумоизоляционных материалов, общий уровень шума в салоне автомобиля снизился в среднем на 3,2 дБ, что соответствует изменению интенсивности звука в 2 раза. В дальнейшем предполагается использование новых материалов, а также методов их нанесении позволяющих добиться более лучших результатов.
Список литературы
1.ГОСТ 31327-2006. Метод сравнения данных по шуму машин и оборудования. – М.: Изд-во стандартов, 2007. – 8 с.
2.ГОСТ 31333-2006. Измерение шума легковых пассажирских автомобилей в условиях, соответствующих городскому движению. – М.: Изд-во стандартов, 2007.
–5 с.
3.Победин, А.В. Статистическая оценка шумности автомобиля ГАЗ-3110 / А.В. Победин, Ф. С. Домолазов, А. А. Долотов // Известия ВолгГТУ. - 2007. - №8.
- С. 115-116.
И. А. Дмитриев, магистрант
И. Г. Русяк, доктор технических наук, профессор Ижевский государственный технический университет имени М. Т. Калашникова
Математическое моделирование истечения газа из цилиндрического канала
Исследование математического моделирования течения газа внутри полых тел и на выходе из них является актуальным в области проектирования стрелкового и артиллерийского оружия, систем вентиляции, машиностроения. Как правило, такие исследования выполняются в различных программных средах, позволяющих моделировать потоки, либо создавать модели. К таким средствам можно отнести любые среды программирова-
ния, такие как Visual Studio, Borland Delphi, Borland C++ Builder (как ста-
рых, так и самых новых их версий), которые позволяют самостоятельно запрограммировать математику процесса и произвести численные эксперименты. Стоит отметить, что существуют программные продукты, которые позволяют работать уже с готовыми математическими структурами, например ANSYS.
Cистема трехмерных уравнений гидромеханики вместе с уравнениями неразрывности и энергии записывается в следующей форме [1]:
|
|
U |
|
V |
|
W |
0 |
(1) |
t |
|
x |
|
y |
|
z |
|
|
80
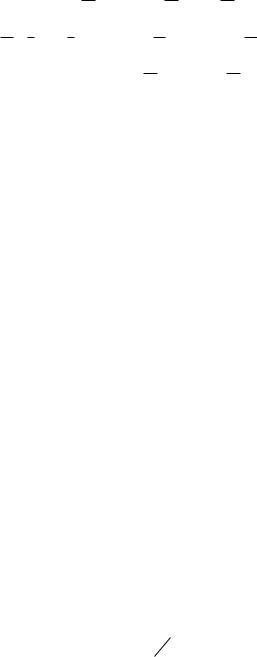
|
|
|
|
|
U |
|
|
P U |
2 |
|
|
UV |
|
|
|
UW |
|
|
||||||||
|
|
|
|
|
t |
x |
|
y |
z |
|
|
|||||||||||||||
|
|
|
|
|
|
|
|
|
|
|
|
|
|
|
|
|
|
|
|
|
||||||
|
|
|
|
4 U |
|
2 |
|
V |
|
W |
|
|
|
U |
|
V |
|
|
U |
|
W |
|||||
|
|
|
|
|
|
|
|
|
|
|
|
|
|
|
|
|
|
|||||||||
|
x |
|
3 |
x |
|
3 |
|
y |
|
z |
|
|
|
y |
|
y |
|
x |
|
|
z |
|
|
|||
|
|
|
|
|
|
|
|
|
|
|
|
|
z |
|
x |
|||||||||||
|
|
|
|
|
|
|
|
|
|
|
|
|
|
|
|
|
|
|
|
|
|
|
|
|||
|
|
|
|
|
V |
|
V U |
|
|
|
P V |
2 |
|
|
V W |
|
|
|||||||||
|
|
|
|
|
|
t |
|
|
x |
|
|
|
z |
|
|
|||||||||||
|
|
|
|
|
|
|
|
|
|
y |
|
|
|
|
|
|
|
|
|
|
|
|
U |
|
|
|
|
|
|
||
|
x |
|
y |
|
|
|
|
|
W |
||
|
|
|
t |
||
|
|
|
U |
|
|
|
|
|
|
|
|
x |
z |
||||
|
|
|
|
V |
|
|
|
|
|
|
4 V |
|
2 U |
|
W |
|
|
|
|
|
|
V |
||||||||||||
|
|
|
|
|
|
|
|
|
|
|
|
|
|
|
|
|
|
|
|
|
|
|
|
|
|
|
|
|
|||
|
|
|
|
|
|
|
|
|
|
|
|
|
|
|
|
||||||||||||||||
|
x |
|
|
|
y |
|
|
y |
|
3 x |
|
|
|
|
|
|
z |
|
z |
||||||||||||
|
|
|
|
|
|
3 |
|
|
|
z |
|
|
|
||||||||||||||||||
W U |
|
|
W V |
|
|
P W 2 |
|
||||||||||||||||||||||||
|
|
|
|
||||||||||||||||||||||||||||
|
|
|
x |
|
|
|
|
|
|
|
y |
|
|
|
|
z |
|
|
|
|
|
|
|
|
|
|
|||||
W |
|
|
|
|
|
|
V |
|
W |
|
|
|
|
4 W |
|
|
2 |
|
|
U |
|
||||||||||
|
|
|
|
|
|
|
|
|
|
|
|
|
|
|
|
|
|
|
|
|
|
|
|
|
|
|
|
|
|
||
|
|
y |
|
z |
y |
z |
3 z |
|
|
|
|
x |
|||||||||||||||||||
x |
|
|
|
|
|
|
|
|
|
|
|
|
3 |
|
|
|
|||||||||||||||
|
|
|
|
|
|
|
|
|
|
|
|
|
|
|
|
|
|
|
|
|
|
|
|
|
|
|
|
|
|
|
Wy
Vy
E |
|
|
P E U |
|
P E V |
|
P E W |
|
t |
x |
y |
z |
|||||
|
|
|
|
(2)
(3)
(4)
|
|
2 |
|
U |
|
|
V |
|
|
W |
|
|
|
|
|
U |
|
|||||||
|
|
|
|
|
|
U |
|
|
|
|
|
|
|
|
2 |
|
U |
|
|
|||||
|
|
|
|
|
|
|
|
|
|
|
||||||||||||||
|
|
3 x |
|
x |
|
|
y |
|
|
|
|
|
|
x |
|
|
|
x |
|
|||||
|
|
|
|
|
|
|
z |
|
|
|
|
|
||||||||||||
|
|
|
|
U |
|
V |
|
|
|
|
U |
|
W |
|
||||||||||
|
|
|
|
|
|
V |
|
|
|
|
|
|
|
|
W |
|
|
|
|
|
|
|||
|
|
|
|
|
|
|
|
|
|
|
|
|||||||||||||
|
|
x |
|
|
y |
|
|
|
|
x |
|
|
z |
|
|
x |
|
|||||||
|
|
|
|
|
|
x |
|
|
|
|
|
|
||||||||||||
|
|
|
|
|
U |
|
V |
|
|
|
|
|
|
U |
|
W |
|
|||||||
|
|
|
|
|
U |
|
|
|
|
|
|
|
|
|
W |
|
|
|
|
|
|
|||
|
|
|
|
|
|
|
|
|
|
|
|
|
||||||||||||
|
|
y |
|
|
|
y |
|
|
x |
|
|
y |
|
|
|
z |
|
|
|
|
||||
|
|
|
|
|
|
|
|
|
|
|
|
|
y |
|
|
|
2 |
|
|
|
U |
|
|
V |
|
|
|
W |
|
|
|
|
|
|
|
|
|
|
|
V |
|
|||||||||||||||
|
|
|
|
|
|
|
|
|
|
|
V |
|
|
|
|
|
|
|
|
|
|
|
|
2 |
|
|
|
|
V |
|
|
||||||||||
|
|
|
|
|
|
|
|
|
|
|
|
|
|
|
|
|
|
|
|
|
|
|
|
||||||||||||||||||
|
|
3 y |
|
|
x |
|
|
y |
|
|
|
|
z |
|
|
|
|
|
|
|
y |
|
|
y |
|
||||||||||||||||
|
|
|
|
|
|
|
|
|
|
|
|
|
|
|
|
|
|
|
|
||||||||||||||||||||||
|
|
|
|
|
|
|
|
U |
|
|
W |
|
|
|
|
|
|
|
|
|
V |
|
W |
|
|||||||||||||||||
|
|
|
|
|
|
|
|
U |
|
|
|
|
|
|
|
|
|
|
V |
|
|
|
|
|
|
|
|
|
|||||||||||||
|
|
|
|
|
|
|
|
|
|
|
|
|
|
|
|
|
|
|
|||||||||||||||||||||||
|
|
|
z |
|
|
|
z |
|
|
x |
|
|
|
z |
|
|
|
|
|
z |
|
|
|
|
|||||||||||||||||
|
|
|
|
|
|
|
|
|
|
|
|
|
|
|
|
|
y |
|
|||||||||||||||||||||||
|
2 |
|
|
|
|
|
U |
|
|
V |
|
|
|
W |
|
|
|
|
|
|
|
|
|
|
|
|
W |
|
|||||||||||||
|
|
|
|
|
|
|
|
|
|
|
W |
|
|
|
|
|
|
|
|
|
|
|
2 |
|
|
|
|
|
W |
|
|
||||||||||
|
|
|
|
|
|
|
|
|
|
|
|
|
|
|
|
|
|
|
|
|
|
|
|
||||||||||||||||||
|
3 z |
|
|
|
x |
|
|
y |
|
|
|
|
z |
|
|
|
|
|
|
|
z |
|
|
z |
|
||||||||||||||||
|
|
|
|
|
|
|
|
|
|
|
|
|
|
|
|
|
|
|
|
||||||||||||||||||||||
|
|
|
|
|
|
|
|
|
|
|
|
|
|
|
T |
|
|
|
|
|
|
T |
|
|
|
|
T |
|
|
|
|||||||||||
|
|
|
|
|
|
|
|
|
|
|
|
x |
x |
|
y |
y |
z |
z |
|
|
|
||||||||||||||||||||
|
|
|
|
|
|
|
|
|
|
|
|
|
|
|
|
|
|
|
|
|
|
|
|
|
|
||||||||||||||||
|
|
|
|
|
|
|
|
|
|
|
|
|
|
U 2 V 2 W 2 |
|
|
1 |
|
|
|
|
P |
, |
|
|
|
|||||||||||||||
|
|
|
|
|
|
|
|
|
|
|
|
E |
|
|
|
|
|
|
|
|
|
|
|
|
|
|
|
|
|
|
|
||||||||||
|
|
|
|
|
|
|
|
|
|
|
|
|
|
|
|
2 |
|
|
|
|
|
|
|
k 1 |
|
|
|
|
(5)
(6)
здесь x, y, z, t – декартовы координаты и время. Коэффициенты молекулярной вязкости – µ и λ – теплопроводности. k – отношение изобарной и изохорной теплоемкостей газа.
В уравнении (5) температура исключается с помощью уравнения Клайперона-Менделеева:
P R T .
81
В результате под знаками частных производных по времени оказываются: ρ – плотность газа; ρU, ρV, ρW – компоненты вектора плотности потока; E – полная удельная энергия газа.
Именно переменные ρ, ρU, ρV, ρW, ρE и являются неизвестными, определяемыми в результате решения уравнений.
Однако стоит отметить, что данная система уравнений применима к системам с ортогональной сеткой, характерной для анализа поведения потока в прямом канале прямоугольного сечения, для которого заранее определены параметры ширины, длины и глубины канала. В этом случае мы разделяем канал по каждому из направлений на отрезки длиной l, получая для расчета сетку. Заменяя последовательно уравнения системы их разностными аналогами, мы получим систему уравнений, позволяющей обсчитывать состояния потока в каждый конкретный момент времени в каждой точке сетки.
В общем случае моделирование истечения из какого-либо канала используемыми методами (прямое численное моделирование, метод конечных элементов) подразумевает использование при моделировании конечных областей. Вне зависимости от сечения и формы канала на выходе из него внешнюю среду будем задавать как область по линейным размерам много большую, чем сечение канала. Поскольку в общей постановке задачи об условиях симметрии нам ничего неизвестно, то к границам области внешней среды не применяется никаких условий. Они выбираются исходя из соображения о том, что движение потока у границ области пренебрежимо мало.
Постановка задачи требует от нас реализации метода для конкретного случая, а именно для прямого цилиндрического канала. Следовательно, нам необходимо преобразовать исходную систему уравнений (1-6) в цилиндрические координаты. Дальнейший ход решения задачи не будет отличаться от решения на ортогональной сетке.
Решение трехмерной модели для прямого цилиндрического канала является продолжением решения двумерной задачи для прямоугольного канала. Точное преобразование системы уравнений и результаты трехмерного моделирования являются целью дальнейших исследований.
|
Список литературы |
1. Липанов, |
А.М. Численный эксперимент в классической гидромехани- |
ке турбулентных |
потоков / А.М. Липанов, Ю.Ф. Кисаров, И.Г. Ключников. – |
Екатеринбург: УрО РАН, 2001. – 9 с.
82
М. Ю. Докукин, аспирант
А. Э. Пушкарев, доктор технических наук, профессор Ижевский государственный технический университет имени М. Т. Калашникова
Синтез структурных схем механизмов с пироприводом
Сегодня самым ценным ресурсом является время. В зависимости от складывающейся ситуации оно может быть бесценно, например, для спасения человеческой жизни, в аварийной ситуации, для ликвидации последствий чрезвычайной ситуации и т. д.
Специалисты МЧС для ликвидации аварий, чрезвычайных ситуаций и последствий стихийных бедствий используют специальное оборудование. К ним относятся: гидравлические ножницы, гидравлические раздвижники, специальные домкраты, развивающие усилие в несколько десятков килоньютон. Гидравлический инструмент требует специального ухода, дополнительного оборудования, насосных станций высокого давления, гидролиний и т. д. Для работы гидравлического инструмента требуется время для достижения необходимого давления, что осуществляется в несколько десятков циклов, и отдельный источник энергии (электрогенератор для работы насосных станций).
Возможной альтернативой гидравлическому инструменту являются устройства с использованием энергии пороховых газов – механизмы с пироприводом: пирорезаки для резки металлических прутьев, пирораздвижники для раздвигания прутьев решетки или вскрытия заклинивших дверей и др.
Данные механизмы уже используются в различных отраслях: пироболты для разделения ступеней в ракетной технике, механизмы катапультирования в авиации и т.д. [1].
К механизмам с использованием пиропатронов в первую очередь относятся системы катапультирования (катапультируемое сидение, спасательная капсула) в авиации.
Пироустройство натяжения ремня в автомобиле помогает решить проблему плотного прилегания ремня безопасности в аварии и свободного, комфортного натяжения ремня в обычных условиях. В большинстве случаев механизм прячется в стойке автомобиля и является частью механизма наматывания ремня. Существуют также варианты размещения натяжителя в механизме замка ремня безопасности.
Устройство одноразового действия, применяемое как активная охрана автомобиля, кроме шумового эффекта может обеспечить задымление салона автомобиля слезоточивым газом. При срабатывании пиропатрона в кабине никому не удастся воспользоваться автомобилем в течение
10...15 мин.
Пироустройства применяются в составе автоматической установки га-
83
зового пожаротушения для открытия устройства и подачи жидкости, содержащейся в баллоне, через трубопровод и насадки в защищаемое помещение.
Наконец, начали появляться конструкции пирорезаков для разрезания металлических прутьев [2].
Между тем, достаточно надежные и компактные устройства для использования в чрезвычайных ситуациях находятся еще в стадии разработки, что подчеркивает актуальность исследования.
Проектирование пиромеханизмов связано, в первую очередь, с задачами внутренней баллистики порохового заряда [3]. В баллистическом проектировании решается основная задача: определить конструктивные данные канала пирорезака и условия, при которых толкатель определенного диаметра и веса приобретает заранее заданную начальную скорость. При этом наибольшее давление газов, развивающихся при горении пороха, не должно превышать определенной величины.
К конструктивным данным канала относятся: объем каморы W0 , поперечное сечение канала S , длина пути толкателя по каналу lд , длина каморы lкм с учетом ее уширения χ по сравнению с сечением канала, относительный путь толкателя по каналу ΛД = lд / l0 = W0 / Wд , длина канала
Lкн и объем канала Wкн =W0 + Slд = S( l0 +lд ) .
Каждое пироустройство характеризуется определенной системой баллистических характеристик, которые можно разделить на три группы:
а) конструктивные характеристики канала устройства; б) характеристики условий заряжания; в) энергетические характеристики.
Особенности внутренней баллистики у пирорезаков в отличие от стрелкового оружия заключаются в следующем. Процесс срабатывания пирорезака во многом отличается от процесса выстрела, толкатель не покидает пределов корпуса, а пороховые газы стравливаются в крайнем переднем положении толкателя.
Рациональная методика баллистического проектирования должна давать кратчайший путь к нахождению решения, удовлетворяющего всем поставленным требованиям.
После расчета баллистических параметров и получения усилия на толкателе производится расчет системы рычагов режущих кромок пирорезака и расчет буфера отдачи из эргономических условий, откуда определяется максимальный диаметр разрезаемого прутка. После этого решается обратная задача: исходя из заданного диаметра прутка и механических свойств материала, из которых он изготовлен, рассчитывается усилие на режущих кромках пирорезака и на толкателе. Зная усилие на толкателе, можно определить требуемые условия заряжания. С другой стороны, имеется ограничение по максимальной величине виброудара при срабатыва-
84
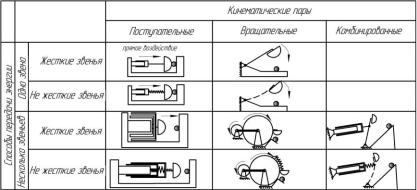
нии устройства, исходя из условий эксплуатации его человеком.
Для проектирования пирорезака требуется проработать все возможные варианты работы пироустройства. Для этого требуется составить морфологическую матрицу данного устройства со всеми возможными вариантами компоновки, составить его подробную структурную модель с учетом всех уровней. Также требуется составить его функциональную модель с выявлением главных, основных, простых и вспомогательных функций.
После составления морфологической матрицы, и составления структурной и функциональной моделей, требуется совместить их и составить функционально-структурную модель. Для дальнейшей работы требуется синтезировать схемы пироустройств на основе функциональноструктурной модели. Синтезированные схемы представлены в таблице
Таблица Синтезированные схемы на основе монтажного патрона
Таким образом, для дальнейшего проектирования требуется выбрать наилучшую схему работы пироустройства, а проектирование механизмов с пироприводом является сложной проблемой, связанной с решением задач внутренней баллистики. Необходимо произвести расчет стенок газовой камеры, силовой расчет системы рычагов и расчет на прочность конструкции в целом. В связи с неопределенно большим числом возможных решений задачи при баллистическом проектировании возникает вопрос о выборе критериев для оценки получаемых расчетом вариантов проекта.
Создание и совершенствование механизмов с пироприводом, предназначенных для работы в чрезвычайных ситуациях, обладающих повышенным быстродействием и сниженной ударовиброотдачей, возможно путем разработки методов их структурного и параметрического синтеза.
Окончательное решение о выборе той или иной структурной схемы возможно только после проведения подробного параметрического анализа и синтеза.
85
Список литературы
1.Пат. 2084710 РФ, МПК F15B15/19, F15B15/22. Пиропривод. Щеглов В. А.
–№ 5024256/06; заявлено 29.01.1992. – Опубл. 20.07.1997. – Бюл. № 3.
2.Пат. 2024368 РФ, МПК B23K7/00. Ручной пиротехнический резак. Симонов В. В.; Симонова Е. М. – № 5063929/08; заявлено 05.10.1992. – Опубл.
15.12.1994. – Бюл. № 2.
3.Вентцель, Д.А. Внутренняя баллистика / Д.А. Вентцель. – М.: Внутренняя баллистика, 1948. – 416 с.
А. К. Домнин, ст. преподаватель О. И. Шаврин, доктор технических наук, профессор
Ижевский государственный технический университет имени М. Т. Калашникова
Повышение эффективности дробеструйной обработки винтовых пружин сжатия
Проблема эффективности обработки дробью крупногабаритных винтовых пружин становится актуальной в связи с развитием производства высокопрочных пружин для подвижного состава железных дорог [5].
Согласно нормативным документам, регламентирующим выпуск вагонных пружин [1, 4], термически обработанные пружины должны быть упрочнены наклепом дробью.
Для наклепа дробью вагонных пружин применяют, как правило, механические дробеметы [2, 3].
Контроль качества и эффективности дробенаклепа проводят по замерам прогибов контрольных пластин, закрепляемых в специальных держателях и подвергаемых наклепу дробью [4]. Такой вид контроля проводят как для листовых рессор, так и для пружин. Не трудно заметить, что контрольная пластина конструктивно подобна листовой рессоре, поэтому в данном случае не возникает особых сомнений в адекватности полученных результатов контроля, чего нельзя сказать при оценке качества и эффективности наклепа дробью винтовых пружин указанным методом.
В общем случае при обработке пружин в дробемете механического действия требуется равномерная обработка витка как по его длине, так и по окружности поперечного сечения. Первое обеспечивается вращением пружины, а равномерность обработки поперечного сечения зависит от геометрических параметров пружины – диаметра пружины и межвиткового зазора. Максимальный эффект упрочнения наружной поверхности витка достигается при угле встречи потока дроби и поверхности пружины 90°±15° [3]. Обработке внутренней поверхности витка препятствует рикошетирование дроби от боковых поверхностей витка, влияющее на энергию той части потока дроби («энергоэффективной»), которая проходит по
86
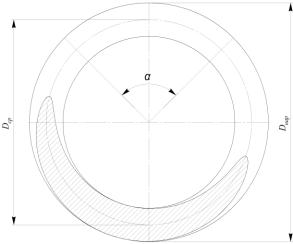
межвитковому зазору к внутренней поверхности витка. Чем меньше величина межвиткового зазора и больше диаметр пружины, тем меньше эффективность обработки внутренней поверхности витка.
Это уменьшает общую эффективность дробеструйной обработки, т.к. наиболее напряженный в эксплуатации участок поверхности витка пружины оказывается наименее упрочненным.
Для оценки эффективности обработки дробью пружин необходимо установить, какое количество дроби отражается от наружной поверхности витка и взаимодействует с дробью направленной в межвитковый зазор, какое количество «энергоэффективной» дроби, направленной в межвитковый зазор, остается после этого взаимодействия.
Для ответа на эти вопросы рассмотрим некоторый сектор α в поперечном сечении пружины. Данный сектор ограничивает элемент витка винтовой пружины, который находится в зоне действия потока дроби с углом встречи с обрабатываемой поверхностью равным 90º (рис. 1), кроме этого примем допущение о том, что в пределах этого сектора условия обработки пружины одинаковые.
Рис. 1. Поперечное сечение пружины
Площадь межвиткового зазора в пределах сектора α (площадь элемента боковой поверхности цилиндра в пределах сектора):
S |
|
|
|
H d D , |
(1) |
М |
|
||||
|
|
180 |
ср |
|
|
|
|
|
|
|
где H – шаг пружины; d – диаметр прутка; Dср – средний диаметр пружины.
Далее все выкладки будем производить в пределах сектора α. Для определения площади рикошетирования и эффективной площади наклепа рассмотрим продольное сечение витка пружины в пределах сектора α.
87

В общем случае дробь рикошетирует в нескольких направлениях, но нас будет интересовать та дробь, которая отражается в зону межвиткового пространства.
Рикошетирование будем учитывать от наружной поверхности витков (рис. 2), ограниченной зоной в 60° (зона между углами в 15° и 75°). Дробь, приходящаяся на поверхность витка в зоне от 0° до 15°, взаимодействует с поверхностью витка по траектории близкой к касательной, поэтому меняет траекторию своего движения не значительно и движется совместно с центральным потоком. Дробь, взаимодействующая с поверхностью витка
взоне от 75° до 90°, обеспечивает эффективное упрочнение наружной поверхности витка, поэтому после отражения имеет минимальную энергию и не оказывает активного воздействия на поток дроби, направленный
вмежвитковый зазор.
Площадь наружной поверхности двух соседних витков, при отражении от которой происходит взаимодействие отраженной дроби с потоком дроби в межвитковом зазоре:
S |
|
|
1 |
|
2 d |
D |
dsin . |
(2) |
Р |
|
|
||||||
|
6 |
|
180 |
ср |
|
|
||
|
|
|
|
|
|
Рис. 2. К определению площади рикошетирования
Рис. 3. К определению эффективной площади наклепа
88

Площадь наружной поверхности витка, подвергающейся эффективному наклепу дробью, т.е. при углах встречи потока дроби и обрабатываемой поверхности 90°±15° (зона в 30° на рис. 3):
S нар |
1 |
|
2 d D |
d . |
(3) |
|
|
||||||
эф |
24 |
|
180 |
ср |
|
|
|
|
|
|
|
Запишем выражения для определения количества дроби, приходящегося на каждый участок площади:
M M Q SM ,
M P Q SP ,
M нар Q S нар , |
(4) |
|
эф |
эф |
|
M эфвнут Q Sэфвнут ,
где Q – плотность потока дроби; ММ – количество дроби, приходящееся на межвитковый зазор; МР – количество дроби, отраженное от боковой по-
верхности витков; М эфнар – количество дроби, приходящееся на площадь эффективного упрочнения наружной поверхности витка; М эфвнут – количе-
ство дроби, приходящееся на площадь эффективного упрочнения внутренней поверхности витка.
Сформулируем условие эффективной обработки внутренней поверхности витка следующим образом: обработка внутренней поверхности витков пружины дробью будет эффективной в том случае, когда к этой поверхности будет доставлено столько же «энергоэффективной» дроби, сколько необходимо для эффективной обработки наружной поверхности.
Запишем условие эффективной обработки внутренней поверхности витка в виде равенства:
М эфнар М эфвнут
В свою очередь можно записать:
М внут М |
|
М |
|
или |
М эфвнут |
1. |
М |
Р |
|
||||
эф |
|
|
М М М Р |
|
||
|
|
|
|
|
|
Тогда запишем условие (6) с учетом выражений (4), (1), (2) и (3):
|
|
|
Q 1 |
|
|
2 d |
D d |
|
|
|
|||||
|
|
|
|
|
|
|
|||||||||
|
|
|
|
24 |
|
180 |
|
|
|
ср |
|
|
|
|
|
|
|
|
|
|
|
|
|
|
|
|
|
1. |
|||
|
|
|
|
|
|
|
|
|
|
|
|
|
|
||
Q |
|
H d D |
|
Q 1 |
|
2 d |
D |
d sin |
|||||||
|
|
|
|||||||||||||
|
180 |
|
ср |
|
6 |
|
|
180 |
|
ср |
|
|
|||
|
|
|
|
|
|
|
|
|
|||||||
|
|
|
|
|
|
|
|
|
|
|
|
|
|
После преобразований получим:
(5)
(6)
(7)
89
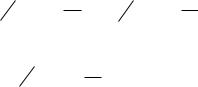
H |
d |
1,65 |
|
|
где с – индекс пружины. Также данное выражение
0,5 |
или |
H |
|
1,65 |
|
0,5 |
|
|
d |
|
|
||||
с |
|
с |
, |
||||
|
|
|
|
||||
|
|
|
|
|
|||
|
|
|
|
|
|
|
можно записать в следующем виде:
(8)
h d
0,65 |
0,5 |
|
с |
||
|
,
(9)
где h – межвитковый зазор.
Из анализа чертежей различных вагонных пружин видно, что у большинства пружин отношение шага рабочих витков к диаметру прутка меньше вычисленного по (8) либо незначительно превышает значение отношения, вычисленного по (8) для конкретной пружины.
Таким образом, при обработке вагонных пружин на дробеметных установках не обеспечивается эффективное упрочнение внутренней поверхности витка. Процесс упрочнения дробью реализуется более полно для наружной поверхности витков, а внутренняя поверхность остается минимально обработанной.
Список литературы
1.ГОСТ 1452-2011 Пружины цилиндрические винтовые тележек и ударнотяговых приборов подвижного состава железных дорог. Технические условия. – Взамен ГОСТ 1452-2003; введ. 01.01.2012 М.: Стандартинформ, 2012. - 19 с.
2.Лузгин, Н.П. Изготовление пружин: Учебник для подготовки рабочих на производстве / Н.П. Лузгин. - М.: Высшая школа, 1980. – 144 с.
3.Остроумов, В.П. Производство винтовых цилиндрических пружин / В.П. Остроумов. – М.: Машиностроение, 1970. – 136 с.
4.РД 32.52-95 Инструкция по дробенаклепу пружин и листовых рессор при изготовлении и ремонте рессорного подвешивания подвижного состава
5.Шаврин, О.И. Высокопрочные пружины для подвижного состава железных дорог / О.И. Шаврин // Техника железных дорог. - 2012. - №3. - С. 71-80.
Е. С. Земерев, аспирант
В. И. Малинин, доктор технических наук, профессор А. В. Шатров, главный инженер
ООО «Лаборатория Эффективных Материалов» Пермский национальный исследовательский политехнический университет
Экспериментальная установка получения дисперсных нанооксидов методом сжигания порошка алюминия
Для исследования процесса сжигания аэровзвесей металлических порошков и синтеза дисперсных оксидов в научно-исследовательских работах в ОКБ «Темп» при ПГТУ была разработана и испытана эксперимен-
90
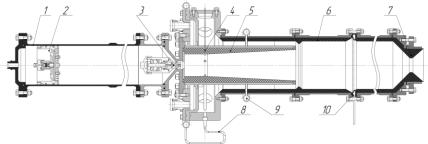
тальная установка. На данной установке проводились исследования процесса воспламенения и горения аэровзвеси порошков алюминия, синтез оксида алюминия, с улавливанием конденсированной фазы из потока продуктов сгорания [1]. Установка состоит из системы подачи, форкамеры (ФК), камеры сгорания (КС), устройства отбора дисперсных продуктов. Несовершенством конструкции экспериментальной установки являлось малое время работы и большой процент содержания примесей в целевом продукте, что является основным недостатком промышленного получения порошка нанооксида алюминия.
Данная работа посвящена описанию конструктивных решений принятых для увеличения продолжительности работы установки, повышению чистоты целевого продукта и улучшению технологического процесса получения нанооксида алюминия.
Рис.1. Экспериментальная установка синтеза нанооксида алюминия.
1 – бак для исходного порошка алюминия, 2 – газопроницаемый поршень, 3 – устройство подачи порошка, 4 – воспламенитель, 5 – форкамера, 6 – КС, 7 – сопло, 8 – подвод кислорода, 9 – подвод аргона в ФК, 10 – узел подвода воды в КС.
На рис. 1 представлена схема модернизированной авторами экспериментальной установки получения дисперсных нанооксидов. Установка включает в себя несколько ключевых узлов и элементов: устройство подачи порошка 3, форкамеру (ФК) 5, воспламенитель 4, камеру сгорания (КС) 6, узел подвода воды в КС 10.
Системы подачи данной установки не отличается от описанной в [1]. Только в отличие от [1], где в качестве транспортирующего порошок газа применяется воздух или азот, вытесняющим газом является аргон. Очевидно, что инертный газ не будет взаимодействовать в форкамере установки с алюминием и загрязнять конечный продукт.
В [2] представлены исследования по получению оксида алюминия в экспериментальной установке, с применением в ФК смеси Al+воздух. В
[3]выявлены следующие недостатки данной смеси:
−высокая температура продуктов первичного горения (> 2500 К);
−образование большой доли конденсированной фазы (> 15 %);
−недостаточное количество газообразной фазы алюминия попадает в КС (qvap < 80 %).
91
Было предложено заменить смесь Al+воздух другими компонентами – Al+O2+Ar [3]. Данная замена позволяет решить ряд проблем:
−снижение температуры продуктов первичного горения;
−уменьшение доли конденсированной фазы;
−увеличение количества газообразного алюминия поступающего в КС для дальнейшего синтеза;
−осуществление возможности транспирационного охлаждения пористой оболочки с помощью аргона, с целью замены абляционного материала (полиметилакрилата) и повышения чистоты конечного продукта.
Пористая оболочка форкамеры позволит проникновение инертного газа через собственное тело. Струи аргона снизят температуру оболочки и удалят конденсированную фазу от ее внутренней поверхности, что обеспечит продолжительную и стабильную работу установки.
Использование в качестве окислителя кислорода вместо первичного воздуха позволит уменьшить содержание посторонних примесей в целевом продукте и понизить конечное содержание конденсированной фазы в форкамере до значений 6…7% [3]. Данный тип окислителя также уменьшит осаждение конденсированного оксида алюминия на внутреннюю стенку оболочки.
В форкамере предложен способ зажигания металловоздушной смеси с помощью электрической дуги [4], как наиболее просто реализуемый. Применение способа зажигания описанного в [1] не оправдано ввиду загрязнения конечного порошка нанооксида алюминия продуктами сгорания воспламенителя, представляющего из себя заряд металлизированного смесевого топлива.
Конструкция камеры сгорания установки синтеза представляет собой корпус из набранных секций и сопла и предназначена для сжигания вторичной смеси и образования нанооксида с заданными свойствами.
С целью увеличения чистоты конечного продукта, уменьшения температуры внутри камеры сгорания и уменьшения вредных выбросов NOx предложено применять в камере сгорания в качестве окислителя воду. Для решения данной задачи спроектирован узел подачи воды, который позволяет избавиться от подвода вторичного воздуха и обеспечивает диспергирование дистиллированной воды навстречу высокотемпературному металлогазовому потоку. Ранее подобная схема организации горения предлагалась в [5].
92
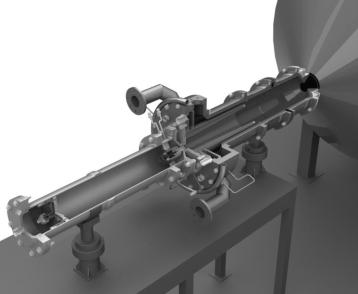
Рис. 2. Внешний вид модернизированной установки получения дисперсных нанооксидов
Одним из лимитирующих факторов работы установки является температуростойкость облицовочного материала камеры сгорания. В перспективах стоит цель избавления от теплозащитного покрытия и увеличения общего времени работы установки.
Модернизация установки была проведена с целью отработки решений принятых для увеличения продолжительности и качества технологического процесса получения дисперсных нанооксидов методом сжигания и является первым этапом к разработке опытно-промышленной установки синтеза. Применяя все вышеописанные изменения, можно будет осуществлять синтез нанооксида алюминия в промышленных масштабах. Внешний вид модернизированной установки синтеза представлен на рис. 2.
В перспективе остается проектирование и сборка комплекса оборудования, системы управления и измерения установки синтеза и отбора дисперсных нанооксидов представленных на рис. 3.
93
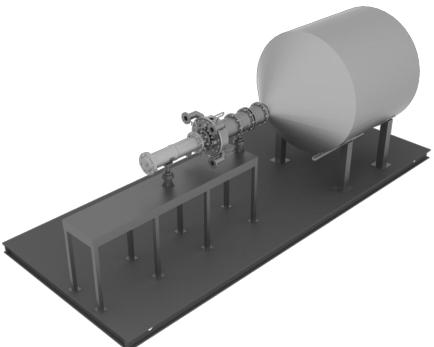
Рис. 3. Комплекс оборудования синтеза и отбора дисперсных нанооксидов
Список литературы
1.Малинин, В.И. Внутрикамерные процессы в установках на порошкообразных металлических горючих / В.И. Малинин. - Екатеринбург - Пермь : УрО РАН, 2006. – 262 с.
2.Малинин, В.И. Воспламенение и горение аэровзвеси алюминия в реакторе высокотемпературного синтеза порошкообразного оксида алюминия / В.И. Малинин, Е.И. Коломин, И.С. Антипин // Физика горения и взрыва. - 2002. - Т.38, №5. - С. 41-51.
3.Болховских, Д.А. Исследование составов металлогазовых смесей для получения нанодисперсного оксида алюминия / Д.А. Болховских, В.И. Малинин, Р.В.
Бульбович // Вестник ПНИПУ. Аэрокосмическая техника. - 2012. - №33. - с. 109-
123с.
4.Бобров, А.Н. Воспламенение и горение двухкомпонентной газовзвеси порошкообразного горючего и окислителя / А.Н. Бобров, Д.А. Ягодников, И.В. Попов // Физика горения и взрыва. - 1992. - Т.28, №5. - С. 3-5.
5.Бербек А.М. Теоретическое обоснование создания ракетного двигателя на порошкообразном металлическом горючем и воде в качестве окислителя: автореф. дис. канд. техн. наук: 05.07.05 / А.М. Бербек. - Пермь, 2012. – 20 с.
94
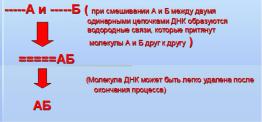
А. М. Зинатуллина, магистрант
А. В. Вахрушев, доктор физико-математических наук, профессор Ижевский государственный технический университет
имени М. Т Калашникова
Анализ методов управления наночастицами
Исследование методов управления наночастицами является актуальным в области наномеханики. Как правило, такие исследования выполняются в экспериментальных условиях, с целью получения новых материалов и устройств. Обзорными будут являться теоретические и экспериментальные основы для обоснования методов управления наночастиц в области наномеханики.
Метод самоорганизации наночаночастиц. Данным методом занимает-
ся супрамолекулярная химия. В наше время разработан метод синтеза, использующий специфические свойства молекулы ДНК. Берется комплементарная ДНК, к одному из концов подсоединяется молекула А или Б. Имеем 2 вещества: -----А и -----Б, где ---- - условное изображение одинарной молекулы ДНК.
Рис. 1. Схема самоорганизации наночастиц
Существует опасность, что наночастицы будут образоваться в агломераты, то есть слипаться друг с другом. Одно из возможных решений проблемы агломерации ‒ введение веществ ‒ диспергентов, их можно добавлять в среду, содержащую наночастицы [3].
Метод дистанционно управляемых наночастиц. Сильвейн Мартель исследователь политехнической школы в Монреале определяет дистанционно управляемые наночастицы как носители из биоразлагаемого полимера диаметром 50 микрометров, наполненные химиопрепаратом (в данном случае доксорубицином) и мельчайшими магнитными наночастицами. Таким образом, были доставлены нагруженные противоопухолевым препаратом наночастицы по печеночной артерии кролика в пораженный опухолью участок его печени (рис. 1). Данный метод позволит повысить эффективность лечения злокачественных опухолей, а также снизить в тяжесть побочных эффектов [4].
95
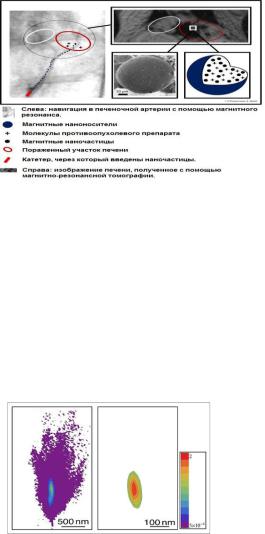
Рис. 2. Схема дистанционного управления наночастиц
Метод управления чувствительными наночастицами лазером. Лазер-
ный луч, контролирующий ведение наночастиц является системой обратной связи, для контроля направления наночастиц. А именно для задания и выравнивания курса и придания ускорения. Благодаря этому уменьшится средняя интенсивность лазерного луча и одновременно увеличится время жизни наночастиц. Используя новый метод управления наночастицами, удалось удерживать 100-нанометровые золотые частицы в 26 раз дольше, чем в предыдущих экспериментах с использованием пассивной лазерной ловушки (рис. 3)
Авторы разработки надеются, что теперь смогут построить сложные наноразмерные устройства, чтобы тестировать поведение наночастиц внутри живых клеток [5].
Рис. 3. «Золотые наночастицы (слева) быстро покидают пассивную статическую ловушку, в то время как в новой ловушке (справа) частицы остаются предельно сконцентрированными (Иллюстрация NIST)»
Метод контроля над наночастицами с помощью лиганда. Группа ученых из государственного университета Северной Каролины обнаружили, что большое количество лигандов, являющиеся органическими молекулами, используется в синтезе наночастиц золота и определяют размер этих наночастиц ‒ что означает, что чем больше лигандов, тем меньше
96
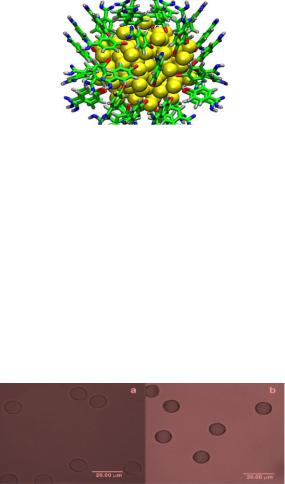
наночастиц(рис. 4). Данное исследование помогает понять формирование наночастиц и предоставляет новый инструмент для управления размерами и свойствами наночастиц золота.
Рис. 4. Схема синтеза наночастиц
В процессе синтеза наночастиц атомы золота располагаются возле лигандов, что позволяет им сформировать наночастицы. Во время этого процесса лиганды собираются воедино, тем самым, окружая наночастицы со всех сторон.
Метод управления наночастицами с помощью микрокапсул. Получен-
ные нанокомпозитные микрокапсулы были охарактеризованы методами просвечивающей электронной, атомно-силовой и конфокальной микроскопии. Из анализа фотографий конфокальной микроскопии (рис. 5 a, б) следует, что полученные нанокомпозитные микрокапсулы, содержащие наночастицы коллоидного золота и магнетита, имеют сферическую форму, низкую степень агрегации, монодисперсны. Введение наночастиц в оболочку микрокапсул увеличивает контрастность их изображения (рис. 5 б) по сравнению с полиэлектролитными микрокапсулами (рис. 5 a), что согласуется с результатами работы.
Рис. 5. Изображения полиэлектролитных микрокапсул состава (PAH/PSS) 8 (a) и нанокомпозитных микрокапсул, содержащих наночастицы золота и магнетита (б), полученные методом конфокальной сканирующей микроскопии
Исследование оболочек полученных нанокомпозитных микрокапсул методом атомно-силовой микроскопии показало (рис. 6), что внедрение в оболочку наночастиц магнетита повышает степень ее неоднородности по сравнению с оболочками, содержащими только золотые наночастицы
(рис. 6 б, в) [2].
97
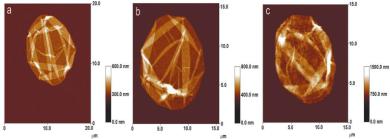
Рис. 6. Атомно-силовые изображения нанокомпозитных микрокапсул: a - магнетит; б, в – золото.
Предполагается, что все методы управления наночастиц будут проработаны и будут служить во благо человечества. Целью дальнейших исследований является разработка программы и математической модели движения наночастиц, учитывая методы управления ими. В планах исследователей очень много задач, которые нужно изучать для развития науки и жизни человека.
Список литературы
1.Омельченко, А.И. Биофункциональные наночастицы в лазерной медицине / А.И. Омельченко // Вестник Югорского Государственного Университета. - 2011. - №2. - С.40-50.
2.Ященок, А.М. Нанокомпозитные микрокапсулы, содержащие наночастицы
коллоидного золота и магнетита: формирование и характеризация / А.М. Ященок
//Коллоидный журнал. - 2009. - №3. - С. 40-50.
3.Shanefield, D. J. Organic Additives and Ceramic Processing, 2nd edition, Kluwer Academic Publishers, Boston, MA, 2000.
4.Интернет-ресурс:
http://rnd.cnews.ru/natur_science/news/line/index_science.shtml.2011/03/17/432429 5. Chemical Communications., 2007, 4602-4604. DOI: 10.1039/B713528
А. С. Караваева, магистрант
С. А. Морозов, кандидат технических наук, доцент Ижевский государственный технический университет имени. М. Т. Калашникова
Совершенствование технологии штамповки детали «лапа»
В настоящее время идет бурное развитие горной, нефтяной и газовой промышленности. В буровых установках используется деталь «Лапа» (рис. 1), материал – легированная сталь марок 14ХН3МА-В, 20ХН3А, 14ХН3МА-Ш, условия эксплуатации от -70 °С до +450 °С. Годовая программа выпуска в 2012 году составила 19 тыс. штук.
98
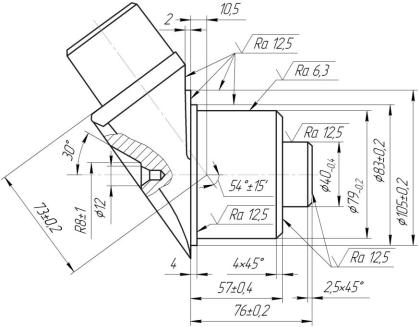
Рис. 1. Эскиз детали «Лапа»
Проведем анализ базовой технологии изготовления детали «Лапа»:
1.Нагрев проката перед разделением на заготовки до 800°С.
2.Отрезка заготовок с базировкой по упору на пресс-ножницах усилием 1000тс марки Эрфурт.
3.Нагрев заготовки в полуметодической пламенной печи до температуры 1200 °С не более 5 часов. При пламенном нагреве образуется окалина. Процент брака по данному дефекту составляет 0,34 % от годовой программы штамповки поковок.
4.Подкатка в подкатном ручье за 3‒5 ударов.
5.Штамповка на 2-тонном штамповочном молоте в окончательном ручье за 6‒9 ударов. При недостаточном распределении металла в подкатном ручье на поковках образуется дефект незаполнения, который составляет 0,01 % от годовой программы штамповки поковок.
6. Обрезка облоя и правка поковки на кривошипном прессе усилием 250 тс марки К‒9534. После обрезки облоя поковка перемещается по транспортеру в мульду, при этом происходит соударение горячих поковок друг о друга, образуются такие дефекты, как забоины и вмятины. Брак по этим дефектам составляет 0,045 % и 0,04 % от годовой программы штамповки поковок соответственно.
7. Охлаждение поковки на воздухе в открытых мульдах.
99
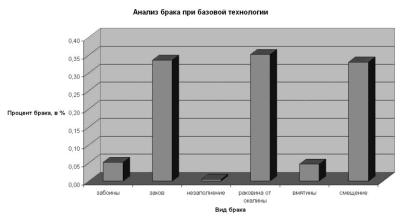
Поковка имеет изогнутую линию разъема штампов. Масса поковки равна 8,7 кг, масса заготовки 10,0 кг, угар при нагреве заготовки 0,2 кг, вес облоя 1,1 кг. Так, как линия разъема изогнутая, имеется значительный брак по смещению вдоль осей штампов, который составляет 0,32% от годовой программы штамповки поковок, и брак по заковам, составляющий 0,33% от годовой программы штамповки поковок.
Стоимость штампов составляет 237 759 рублей. Стойкость инструмента – 1200 поковок. Поковка штампуется на 2-х тонном штамповочном молоте марки ИРИ бригадой в составе 5 человек. Норма выработки составляет 585 штук в смену.
Основными недостатками базовой технологии являются высокая себестоимость изготовления детали «Лапа», высокий процент брака (заковы, раковины от окалины, смещение – рис. 2).
Для устранения этих недостатков была разработана новая технология объемной штамповки детали «Лапа».
Был разработан новый чертеж поковки. Меняем изогнутую линию разъема на прямую линию разъема штампов по центру симметрии поковки. Это позволяет снизить брак по смещению и позволяет легче доставать поковку с облоем из ручья штампа.
Рис. 2. Анализ брака по базовой технологии
Масса поковки уменьшилась до 7,8 кг, масса заготовки до 8,95 кг, угар при нагреве заготовки до 0,15 кг, вес облоя до 1,0 кг. Для получения более точных данных по весу поковки при внедрении новой технологии было проведено 3D-моделирования в программе КОМПАС-3D (рис. 3).
100
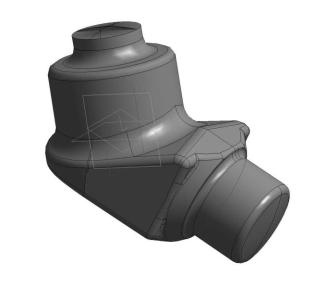
Рис. 3. 3D модель поковки детали «Лапа»
Изменились следующие этапы технологического процесса:
3.Нагрев заготовки в индукционном нагревателе марки КИМ-750 до температуры 1240 °С. При замене пламенного нагрева индукционным, образование окалины значительно снизилось, так как нагрев заготовки осуществляется за 10‒15 секунд. Брак по данному дефекту стал составлять 0,095 % от годовой программы штамповки поковок.
4.Гибка в гибочном ручье за 1 ход пресса усилием 4000 тс.
5.Штамповка в окончательном ручье за 1 ход пресса усилием 4000 тс. Благодаря правильному распределению металла в гибочном ручье дефект незаполнения был исключен.
6.Обрезка облоя и правка поковки осуществляется на кривошипном прессе усилием 400тс марки К-9536. Из-за снижения высоты транспортера, по которому поковка перемещается в мульду, дефект забоины был исключен, а дефект вмятины снизился до 0,095 % от годовой программы штамповки поковок.
Стоимость инструмента составила 80 767 рублей. Стойкость штампов возросла до 1 800 поковок.
Штамповка поковки производится бригадой в составе 3-х человек на кривошипно-горячештамповочный пресс усилием 4 000 тс марки КА8546. Норма выработки увеличивается до 615 штук в смену.
Таким образом, внедрение новой технологии объемной штамповки детали «Лапа» позволило:
1.Снизить себестоимость одного изделия на 200 рублей.
101
2.Уменьшить брак в 2,5 раза.
3.Снизить цену одного комплекта штамповой оснастки на 156992
рубля.
4.Повысить коэффициент использования материала с 73,7% до 83,3%.
5.Получить экономическую эффективность от внедрения новой технологии в 2012 году 3,71 млн. рублей.
6.Ожидаемая экономическая эффективность на программу 2013 года составит 6,4 млн. рублей.
Р. Д. Каримов, аспирант; В. Е. Вавилов, аспирант А. С. Горбунов, аспирант; Д. В. Гусаков, аспирант
И. Х. Хайруллин, доктор технических наук, профессор Уфимский государственный авиационный технический университет
Намагничивающая установка
Одной из основных задач современного энергомашиностроения является снижение коэффициента удельной мощности электромеханических преобразователей энергии (ЭМПЭ). Минимальным коэффициентом удельной мощности без учета систем стабилизации и управления обладают высокоскоростные бесконтактные магнитоэлектрические машины (БММ) [1, 2, 3]. Возможными методами снижения массогабаритных показателей БММ являются либо повышение энергетического произведения (BH) применяемых постоянных магнитов, что ограничивается экономически (чем выше энергетическое произведение магнита, тем выше его цена) и физически (повышение характеристик магнитов приводит к насыщению стали магнитопровода статора), либо оптимизацией магнитной системы ротора.
Распределение магнитной индукции в намагничивающих установках Одной из перспективных магнитных систем ротора БММ является
магнитная система Halbach [4], рис. 1. Внедрение на практике системы Halbach сопряженно с рядом технологических трудностей: сложность сборки, бандажирования, а также сложность намагничивания постоянных магнитов криволинейной формы. Современные намагничивающие установки (НУ), не позволяют осуществлять полное и однородное промагничивание, что снижает характеристики получаемых на них постоянных магнитов.
102
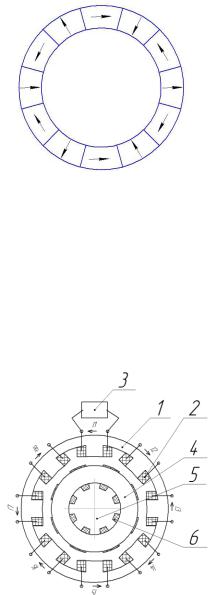
Рис. 1. Магнитная система Halbach
В связи с этим, целью данной работы является разработка устройства позволяющего решить указанные выше проблемы намагничивания постоянных магнитов.
Оригинальное техническое решение, предложенное авторами, рис. 2, содержит электромагнит, выполненный в виде n–полюсного сердечника 1 с катушками 2, соединенными электрически с источником импульсного тока 3, намагничиваемый элемент 4, установленный на сердечнике 5, на котором намотаны дополнительные катушки 6, соединенные электрически с источником импульсного тока 3, и отличается от известных [5–7] введением дополнительных обмоток, задачей которых является усиление магнитного потока электромагнита.
Рис. 2. Предлагаемое техническое решение намагничивающей установки
С целью подтверждения перспективности предлагаемой конструкции авторами было произведено компьютерное моделирование двух НУ: с дополнительными обмотками и традиционного исполнения.
103
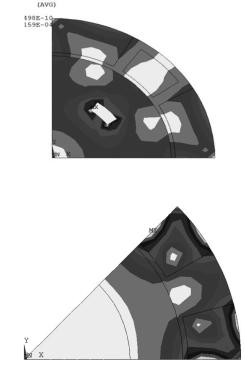
Компьютерное моделирование производилось в программном комплексе ANSYS при этом решалась задача двухмерного анализа электромагнитного поля системы. При компьютерном моделировании применя-
лись граничные условия Дирихле:
|
M |
|
|
|
f |
( |
1 |
|
x, y,z
)
. В результате компью-
терного моделирования были получены спектры распределения магнитной индукции в НУ с дополнительными обмотками и без них. Спектры распределения магнитной индукции представлены на рис. 3, 4.
Рис. 3. Спектр распределения магнитной индукции постоянного магнита в намагничивающей установке с дополнительными обмотками (на рис. 3, более темный цвет соответствует максимуму магнитной индукции)
Рис. 4. Спектр распределения магнитной индукции постоянного магнита в традиционной намагничивающей установке (на рис. 4, более темный цвет соответствует максимуму магнитной индукции)
Анализ данных моделирования показал, что при применении дополнительных полюсов намагничиваемый элемент промагничивается полностью, в отличии от традиционных установок [5-7].
Применение предлагаемого технического решения позволяет повысить энергетические характеристики постоянных магнитов.
Полученный результат подтверждает перспективность внедрения на практике предлагаемого технического решения.
104
Список литературы
1. Кузьмичев Р. В. Генератор в системе электроснабжения самолета с повышенным уровнем электрификации // [Электронный ресурс]
URL:http://www.uacrussia.ru/ru/common/img/news/con/Kuzmichev.pdf (дата обращения 21.07.2012).
2.Moore, M.J. Micro-turbine generators – Professional Engineering. Printed in the USA. 2002. – 113 с.
3.Балагуров, В.А. Электрические генераторы с постоянными магнитами / В.А. Балагуров. - М : Энергоатомиздат, 1988. – 279 с.
4.Permanent magnet based sources of magnetic field // [Электронный ресурс]
URL: http://www.magnetocaloric.com/Code/pub01.htm (дата обращения 01.2013)
5.Патент РФ №2328788С1, H01F13/00, 10.07.2008
6.Преображенский, А.А. Магнитные материалы и элементы / А.А. Преображенский, Е.Г. Биширд. - М : Высшая школа, 1986. – 352 с.
7.Патент РФ № 2222843 С2, H01F13/00, 20.07.2003.
С. С. Коновалов, аспирант; В. В. Фирсенко, студент Д. Г. Шулешко, студент
Д. В. Руцкий, кандидат технических наук, доцент Н. А. Зюбан, доктор технических наук, профессор
Волгоградский государственный технический университет
Влияние технологии вакуумной отливки на развитие и особенности формирования внеосевой ликвационной неоднородности крупных слитков
Интенсивное развитие энергетической, атомной, химической и металлургической отраслей обусловливает необходимость повышения качества изделий из крупных кованых заготовок, полученных из слитков большой массы, с гарантированным сроком службы не менее 60 лет. Это невозможно без детального исследования закономерностей образования дефектов кристаллической структуры, большинство которых образуется в процессе кристаллизации жидкой стали.
Одним из мало устранимых дефектов является внеосевая ликвационная неоднородность в крупных кузнечных слитках конструкционной стали, которая проявляется в виде так называемых «шнуров» (рис. 1). В зоне шнура наблюдается значительное падение характеристик пластичности стали, большое количество неметаллических включений, а иногда и пористость. В настоящее время нет общепринятой точки зрения на механизм образования внеосевой ликвационной неоднородности в крупных стальных слитках. Выдвинуто более десятка гипотез, но ни одна из них не может в полной мере объяснить реальную картину формирования шнуров ликвационной неоднородности. Это, в свою очередь, сильно затрудняет разработку эффективных технологических мероприятий по борьбе с этим дефектом [1].
105
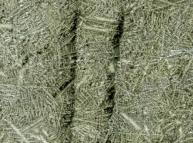
Рис. 1. Вид шнуров внеосевой ликвации в крупных стальных слитках
Оказывать влияние на формирование внеосевой неоднородности можно, управляя процессом вакуумной отливки крупного слитка с применением инокулирования струи с целью изменения теплофизических условий его затвердевания [2].
Объектами исследования являлись два вакуумных слитка стали 38ХН3МФА массой 24,2 т, один из которых отливался по штатной технологии (сравнительный слиток), второй – с применением инокулирования струи. Геометрические параметры слитков одинаковы. Из продольных осевых плит слитков были изготовлены темплеты, с которых по методу Баумана снимались серные отпечатки. Исследование серных отпечатков проводилось по их оцифрованным копиям.
Результаты исследования показали, что в опытном слитке шнуров больше в 2,5 раза, чем в слитке обычной геометрии. Максимальный диаметр шнура уменьшился с 14 мм в слитке обычной геометрии до 7 мм в инокулированном (в 2 раза). Доля области внеосевой ликвации от площади осевого темплета в слитке с изменѐнной технологией отливки в 2 раза больше в сравнении с обычным слитком и составляет 40,3 %.
На основе проведѐнных исследований удалось построить кривые распредления шнуров внеосевой ликвации по высоте и сечению обычного и опытного слитков.
По кривой распределения шнуров по высоте слитка обычной геометрии (рис. 2) видно, что большинство шнуров в нѐм располагается в верхней трети (на уровне от 60 до 100 % высоты слитка находится 56 % шнуров), область внеосевой ликвации распространена на 70 % высоты слитка. Абсолютно другая картина распределения наблюдается в инокулированном слитке, где шнуры распределены более равномерно, чем в обычном, не имеется ярко выраженных пиков и впадин, большинство (50 %) шнуров располагается в средней части (на уровне 40–80 % высоты слитка).
106
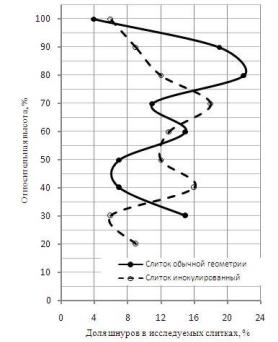
Рис. 2. Распределение шнуров внеосевой ликвации по высоте исследуемых слитков
Анализируя кривые распределения шнуров по сечению исследуемых слитков (рис. 3), можно сказать, что в опытном слитке шнуры располагаются значительно равномернее по сечению, чем в слитке обычной геометрии, в котором 85% шнуров находится на расстоянии от 1/3 до 2/3 радиуса слитка от поверхности. В опытном слитке большинство шнуров залегает ближе к поверхности, половина шнуров находится на расстоянии до 1/3 радиуса от поверхности слитка (в слитке обычной геометрии в этой зоне шнуров нет). Подобные результаты свидетельствуют о более раннем формировании шнуров внеосевой ликвации в инокулированном слитке в результате увеличения скорости кристаллизации.
107

Рис. 3. Распределение шнуров внеосевой ликвации по сечению исследуемых слитков
Результаты исследования свидетельствуют о том, что в опытном слитке в результате изменения технологии удалось увеличить скорость кристаллизационных процессов, что привело к более скорому созданию благоприятных для образования шнуров условий. Количество шнуров в нѐм значительно больше, но при этом средний диаметр меньше, а значит распределение ликвирующих примесей в слитке, отлитом по изменѐнной технологии, более равномерное, что в конечном итоге приводит к более равномерному распределению механических свойств по длине и сечению поковок и будущих изделий. Применение указанной технологии позволяет повысить качество металла в целом, так как указанный слиток имеет более благоприятную макроструктуру, меньшие размеры зоны осевой пористости и трещин, меньшую протяжѐнность зоны дугообразных трещин.
Работа выполнена в рамках гранта РФФИ (соглашение № 12-08-31328/12).
Список литературы
1.Жульев, С.И. Производство и проблемы качества кузнечного слитка / С.И. Жульев, Н.А. Зюбан. - Волгоград : РПК «Политехник», 2003. – 168 с.
2.Жульев, С.И. Влияние инокуляторов на качество металла слитков и изделий / С.И. Жульев, Н.А. Зюбан // Сталь. - 2001. - №6. - С. 57-60.
108
К. А. Копылов, аспирант Ижевский государственный технический университет
имени М. Т. Калашникова
О выявлении низкоскоростных зон процесса взаимодействия теплоносителя с пружиной в спрейере
Внастоящее время курс развития машиностроения в России взят на разработку и использование материалов, повышающих надежность и срок службы изделий, для чего была создана Государственная комплексная программа развития машиностроительного комплекса [1]. Ряд мер, которые выделяет Правительство, должен привести к развитию взаимодействия современных технологий и исследований с производством, улучшению ситуации, связанной с критическим моральным и физическим износом оборудования, низким уровнем развития технологий, а также методов их исследования. Поскольку термическая обработка сталей является неотъемлемой частью подавляющего большинства технологий изготовления изделий машиностроения, поэтому одной из важнейших задач становится оптимизация режимов термической обработки. При этом, высокотемпературная механическая обработка (ВТМО) пружин является одной из задач, которой данная программа не затронула.
Особенность ВТМО состоит в том, что после горячей деформации происходит закалка пружины, которая позволяет получить в материале пересыщенный твердый раствор с нерекристаллизованной структурой [3,4]. При этом отмечается, что классические технологии термической обработки, включающие закалку с последующим отпуском, уже практически исчерпали свой потенциальный оптимизационный запас и нуждаются в качественной модификации с целью повышения вязкостнопластических свойств при сохранении прочностных характеристик.
Впроцессе закалки в основном используют газожидкостные смеси, которые представляют собой дисперсные системы. Главной особенностью таких систем является наличие изменяющейся в пространстве и во времени поверхности раздела фаз. Эти изменения влекут за собой силовые и тепловые взаимодействия на границе раздела, которые, в свою очередь, могут являться причиной появления градиентов скорости течения обеих фаз, давления, температуры и концентраций компонентов. Все эти эффекты воздействуют на процессы тепло- и массопереноса и могут, как интенсифицировать, так и тормозить тепломассообмен. С другой стороны, указанные явления сами воздействуют на поверхность раздела фаз, изменяя
еераспределение в пространстве [6].
Технологический процесс изготовления пружин методом ВТМО характеризуется последовательностью операций нагрева, горячей деформации (навивки на оправку) и закалки [7]. В [2] представлены результаты оценки тепловых потерь процесса изготовления пружин методом ВТМО,
109
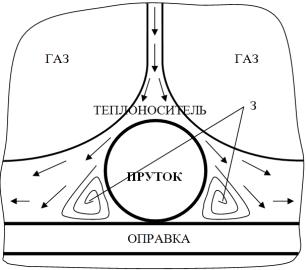
в рамках решения нестационарных двухмерных задач теплопроводности, с учетом принятого допущения о равномерном отводе тепла от поверхности охлаждаемого прутка. На практике охлаждение тел при помощи теплоносителя нарушает принятое допущение, поэтому исследовано расположение низкоскоростных зон (областей) при взаимодействии теплоносителя с прутком.
На рис. 1 представлена схема взаимодействия теплоносителя с прутком и оправкой в спрейерной камере.
Рис. 1. Схема движения теплоносителя в спрейерной камере. «З» ‒ области низкоскоростного движения теплоносителя (интервал скорости в области
vОБТ≤0,001 м/с)
Теплоноситель поступает в пространство спрейерной камеры, которое в первоначальный момент времени заполнено газом (воздух). При взаимодействии теплоносителя с поверхностью прутка и оправки возможно образование застойных зон (циркуляционного течения), где отсутствуют передняя и задняя критические точки, а линии тока представляют собой замкнутые кривые, огибающие профиль. Такое течение независимо от величины циркуляции будет требовать наличия бесконечной скорости в точке, лежащей на задней кромке профиля и так же как бесциркуляционное течение, не может быть реализовано без отрыва потока [5].
В расчетах низкоскоростной принята область со скоростями обтека-
ния vОБТ≤0,001 м/с. В [2] отмечено что, чем меньше скорость vОБТ, тем ниже местный коэффициент теплоотдачи α. Таким образом, следствием об-
разования низкоскоростных зон, будет являться снижение местного α. Задачей исследования является определение условий (скорость впрыс-
ка, расположение и число форсунок, геометрия спрейерной камеры),
110
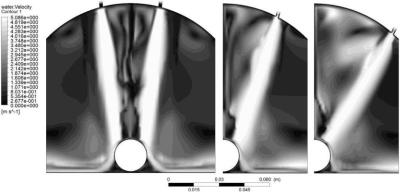
обеспечивающих равномерный подвод теплоносителя к охлаждаемой поверхности.
Ввиду нестационарности и пространственности процесса в постановке задач используется ряд допущений:
Пространство спрейерной камеры рассматривает, как двухфазная двухкомпонентная изотермическая среда (вода – вязкая несжимаемая жидкость, воздух ‒ газ);
Каждая из сред принята неразрывной; Изменение потока жидкости происходит за счет тензора поверхност-
ных сил со стороны газа, сопротивление воздуха не учитывается. Обсуждение результатов. Выделенная область спрейерной камеры с
циркуляционным движением теплоносителя со скоростью движения vОБТ≤0,001 м/с будем считать застойной зоной. Для количественной оценки и характеристики данной области вводится коэффициент KЗ, представляющий отношение суммы длин дуг области застойных зон к длине окружности поперечного сечения прутка.
На рис. 2 представлено распределение скорости движения теплоносителя в расчетной области при подаче с постоянной скоростью vA=5 м/с через две форсунки, расположенные под углом ψ=20°(а), 40°(б), 60°(в). Можно видеть, что при увеличении угла между осями форсунок доля застойных зон в расчетной области снижается.
(а) (б) (в)
Рис. 2. Распределение скорости движения теплоносителя в расчетной области при подаче через две форсунки, расположенные под углом ψ=20°(а), 40°(б), 60°(в)
при R = 55 мм, vA=5 м/с.
Результаты исследования распределения скорости движения теплоносителя в расчетной области при впрыске СОЖ через две форсунки позволяют сделать вывод о том, что режим, обеспечивающий минимальный KЗ=0,407 реализуется при ψ=60°, R=100 мм. Поскольку для данного случая KЗ≠0, сделано предположение о необходимости увеличения количе-
111

ства форсунок для подачи теплоносителя до трех, что приводит к результатам, представленным на рис. 3.
(а) (б) (в)
Рис. 3. Распределение скорости движения в расчетной области при подаче теплоносителя через три форсунки, расположенные под углом ψ=20°(а), 40°(б), 60°(в)
при R=55 мм, vA=5 м/с.
Из рис. 3 видно, что минимальное значение KЗ=0,375 получено при режиме (ψ=60°, R=100 мм). Отметим, что подвод теплоносителя через две и три форсунки при R=55 мм, позволяет получить KЗ=0,764 (впрыск через 2 форсунки), KЗ=0,919 (впрыск через 3 форсунки).
Оценка полученных результатов показала, что режим впрыска теплоносителя через одну форсунку не обеспечит требуемого охлаждения прутка при условиях минимального появления застойных зон. В общем случае, для выполнения всех условий, в том числе теплоотвода, необходимо использовать режим подачи СОЖ через три форсунки со скоростью vA≥7 м/с (KЗ=0,346).
Список литературы
1.Ахметов, Ю.М. Исследование гидродинамических и термодинамических процессов высоконапорно-го многофазного вихревого течения жидкости / Ю.М. Ахметов // Вестник УГАТУ. - Уфа : УГАТУ, 2012. - №2. - С.163-168.
2.Бендерский, Б.Я. Моделирование процессов теплообмена при изготовлении пружин методом высоко-температурной термомеханической обработки (ВТМО) / Б.Я. Бендерский, К.А. Копылов // Химическая физика и мезоскопия. - Ижевск : ИПМ УрО РАН, 2011. - №1. - С. 28-36.
3.Давлетшин, И.А. Отрыв пульсирующего потока / И.А. Давлетшин, Н.И. Михеев, В.М. Молочников // Доклады Академии наук. - М : Академиздатцентр,
2007. - №6. - С. 760-763.
4.Новиков, И.И. Теория термической обработки металлов / И.И. Новиков. -
М: Металлургия, 1986. – 480 с.
5.Перепелица, Б.В. Пространственная структура потока при истечении круглой струи в узкий канал / Б.В. Перепелица, М.В. Шестаков // Теплофизика и аэро-
112
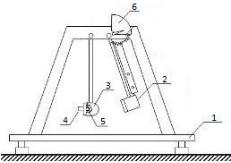
механика. - Новосибирск : ИТ СО РАН, 2009. - №1. - С. 57-60.
6.Протодьяконов, И.О. Гидродинамика и массообмен в системах газжидкость / И.О. Протодьяконов, И.Е. Люблинская. - Л : Наука Ленингр. отд-ние, 1990. – 349 с.
7.Редькин, Л.М. Повышение долговечности жестких пружин высокотемпературной термомеханической обработкой / Л.М. Редькин, О.И. Шаврин, A.C. Потапов // Конструирование и технология изготовления пружин. - 1986. - С.83-91.
Е. Е. Кострюков, старший лаборант научно-исследовательской лаборатории «Прогрессивные технологические процессы пластического деформирования», НИЛ-41
Самарский государственный аэрокосмический университет имени академика С. П. Королева
Методы динамической калибровки датчиков импульсного давления
Датчики импульсного давления применяются для регистрации быстропротекающих импульсных процессов, например, в гидравлических и пневматических системах, в системах диагностики двигателей внутреннего сгорания, испытаниях взрыва и ударной волны.
Для получения достоверного значения давления необходимо откалибровать датчик. Наиболее простым методом является метод калибровки на стенде с падающим грузом [1]. Импульс давления формируется при падении груза с заданной высоты на неуплотненный поршень, опирающийся на жидкость, заключенную в камеру. В камере расположены поверяемый
иобразцовый датчики давления. Недостатками такого метода являются:
‒плохая повторяемость;
‒ограниченный диапазон изменения длительности формируемых им-
пульсов давления.
Большую точность позволяет получить калибровка датчика на баллистической установке (например, установки AP8001, AP8002 фирмы «ГлобалТест») [2]. Принцип действия основан на методе баллистического маятника.
Рис. 1. Баллистическая установка AP8001, AP8002: 1 – станина установки; 2 – молот; 3 – наковальня; 4 – поверяемый датчик; 5 – образцовый датчик; 6 – стре-
лочный указатель угла наклона молота
113
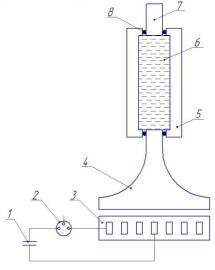
Амплитуда ударного ускорения зависит от высоты подъема молота, нестабильность амплитуды ударного ускорения составляет 10%, погрешность воспроизведения амплитуды ударного ускорения составляет 6%. Длительность удара можно изменять, устанавливая прокладки из разных материалов на молоте.
Известен метод калибровки с помощью импульсного магнитного поля [3].
Рис. 2. Устройство для динамической калибровки датчиков импульсного давления
При разряде емкостного накопителя энергии 1 через разрядник 2 на индуктор 3, в основании волновода 4, выполненного из электропроводного материала, наводятся вихревые токи. В результате электродинамического взаимодействия магнитного поля индуктора и вихревых токов формируется импульс давления в волноводе. Распространяясь по волноводу, он поступает в камеру 5 и через несжимаемую диэлектрическую жидкость 6 воздействует на калибруемый датчик 7. Уплотняющие резиновые кольца 8 препятствуют вытеканию жидкости.
Преимуществами такого метода являются:
‒высокая стабильность формирования импульсов давления;
‒длительность и амплитуда формируемых импульсов может выбираться в широких пределах изменением параметров разряда накопителя энергии и индуктора.
Была проведена калибровка датчика с помощью импульсного магнитного поля. Емкость накопителя энергии изменялась в диапазоне 30…400 мкФ, напряжение заряда изменялось от 1до 5 кВ. Энергия разряда составляла 0,015…5 кДж. В результате длительность импульса давления составила 30…500 мкс с высокой повторяемостью.
114
Список литературы
1.Ястребцов, О.В. Упрощенная методика расчета параметров импульсов давления для установок с падающим грузом / О.В. Ястребцов // Измерительная техника. - 1976. - №7. - С. 37-38.
2.http://www.globaltest.ru (Дата обращения: 05.02.2013 г.)
3.Пат. 2461806 Российская Федерация, МПК G01L 27/00. Устройство для динамической тарировки датчиков импульсного давления [Текст] / Попов А.П., Юсупов Р.Ю.; заявитель и патентообладатель Самарский государственный аэрокосмический университет имени акад. С.П.Королева (национальный исследователь-
ский университет) (СГАУ). - №2011116713/28 ; заявл. 27.04.2011 ; опубл. 20.09.2012, Бюл. №26. – 5 с.
Е. Н. Козырева, магистрант
А. В. Алиев, доктор физико-математических наук, профессор Ижевский государственный технический университет имени М. Т. Калашникова
Методы контроля утечек в магистральных нефте- и газопроводах
Всвязи с увеличением добычи нефти и газа интенсивно развивается и трубопроводный транспорт этих продуктов, причем развивается как сеть трубопроводов для перекачки продукции скважин, так и сеть магистральных трубопроводов, перекачивающих товарную нефть и нефтепродукты, а также природный газ. Трубопроводный транспорт является самым экономически целесообразным транспортом жидких и газообразных продуктов. Однако трубопроводный транспорт всегда сопровождается потерями продукта. Есть неизбежные потери, величина которых учитывается при ведении технологического процесса. Но также существуют потери перекачиваемого продукта, которые невозможно предвидеть. Это потери, возникающие при аварийных ситуациях с выходом продукта в окружающую среду и при несанкционированных врезках для хищения перекачиваемых продуктов. Все это приносит огромные убытки эксплуатирующим трубопроводным организациям связанные как с потерей продукта, так и с экологическими последствиями при некачественном их обустройстве.
Внастоящее время существует много способов и устройств, позволяющих обнаружить утечки из трубопроводов (СОУ), работа которых основана на различных физических принципах [1-6]. Наиболее известные существующие методы обнаружения утечек приведены в таблице.
Восновном, в настоящее время в системах обнаружения утечек используются следующие методы:
− по профилю давления;
−объемно-балансовый;
−метод акустической эмиссии.
115
Таблица Методы обнаружения утечек из трубопроводов
Критерии обнаружения |
Методы постоянного |
Методы периодического |
утечки |
контроля |
контроля |
Обнаружение утечки по |
─ Метод гидравличе- |
─ Метод гидравличе- |
технологическим пара- |
ской локации утечки; |
ских испытаний |
метрам перекачки (с |
─ Метод сравнения рас- |
(опрессовка); |
использованием средств |
ходов; |
─ Метод дифференци- |
АСУ ТП и КИП) |
─ Метод сравнения скоро- |
альных давлений |
|
сти изменения расходов; |
|
Обнаружение утечки по |
─ Метод материального |
|
технологическим пара- |
баланса; |
|
метрам перекачки (с |
─ Метод отрицательных |
|
использованием средств |
ударных волн |
|
АСУ ТП и КИП) |
|
|
Обнаружение утечки на |
─ Волоконно-оптический |
─ Методы визуального |
основе других физиче- |
метод (на основе решеток |
контроля; |
ских параметров (с ис- |
Брэгга); |
─ Акустический метод; |
пользованием дополни- |
─ Волоконно-оптический |
─ Радиоактивный |
тельных аппаратных |
метода (на основе ре- |
метод; |
средств) |
флектометрического |
─ Лазерный газоанали- |
|
принципа); |
тический метод; |
|
─ Метод акустической |
─ Ультразвуковой |
|
эмиссии |
(зондовый) метод; |
|
|
─ Методы внутритруб- |
|
|
ной инспекции; |
|
|
─ Аэрокосмический |
|
|
мониторинг |
Рассмотрим эти методы подробнее 1. Метод выявления утечек по анализу профиля давления основывает-
ся на моделировании распределения давления вдоль трубопровода и статистическом анализе. При возникновении утечки расход на участке до места утечки возрастает по сравнению с первоначальным, а расход на участке после места утечки снижается. В связи с этим, перепад давления на участке до места утечки увеличивается, а после утечки уменьшается, что приводит к появлению излома в приведенном профиле давления.
Недостатки метода: Данный метод работает только в стационарном режиме и обладает низкой точностью и наличием ложных срабатываний, так как многие факторы вызывают похожие изменения.
Для предотвращения ложных срабатываний отклонения фиксируются, как минимум, в двух соседних точках. Также используется «усредненный» профиль распределения давления, являющийся квазистационарным профилем. Такой профиль получается в результате специальной фильтрации давления в точках трубопровода. «Усредненный» профиль давления изменяется, но медленнее, чем реальное давление, что приводит к увеличению времени обнаружения утечек.
В настоящее время данный метод из-за неспособности обнаружения
116
небольших утечек и большой погрешности при определении координаты места утечки, в основном, используется только совместно с другими методами.
2. Объемно-балансовый метод контроля основывается на том, что при образовании утечки расход на входе становится больше расхода на выходе. Помимо этого, в методе учитывается количество газа в самой трубе, которое при образовании утечки уменьшается.
Параметром контроля газопровода здесь является нормализованный расход газа через сечение трубы, то есть, по сути, сохранение количества перекачиваемого газа. Контроль участка газопровода осуществляется путем вычислений разности нормализованных объемов газа, входящих и выходящих из участка газопровода между двумя локальными расходомерами. Расход объемного баланса по участкам позволяет определять возможное место утечки в газопроводе только с точностью до участка.
Достоинства метода: Данный метод позволяет диагностировать и быстро развивающиеся разрывы в трубе, и медленно развивающиеся утечки. Также, метод позволяет определять утечки на больших участках трубопровода между расходомерами. Минимальная величина диагностируемой утечки, в настоящее время, находится на уровне 0,5-1%.
Недостатки метода: Этот метод не позволяет определять координату утечки. Его точность зависит от точности расходомеров. Обнаружение утечки, которая меньше, чем погрешность измерения расхода - невозможно. В данном случае абсолютно не имеет значения абсолютная величина погрешности измерения, а только относительная погрешность одного прибора относительно другого.
3. Метод акустической эмиссии основывается на регистрации и анализе акустических волн, возникающих в процессе пластической деформации и разрушения (роста трещин) трубопровода, а также при истечении рабочего тела (жидкости или газа) через сквозные отверстия в контролируемом объекте.
Для приема сигналов акустической эмиссии используются пьезоэлектрические преобразователи и быстродействующие измерители давления.
Достоинства метода: Данный метод обладает высокой чувствительностью к растущим дефектам и высокой точностью определения координат места утечки. Также методу необходимо довольно малое время для обнаружения дефектов.
Недостатки метода: На фоне шумов и помех появляется трудность выделения сигнала акустической эмиссии. Для снижения количества ложных срабатываний, а также для повышения помехоустойчивости применяются специальные алгоритмы обработки принимаемых сигналов.
Данный метод анализа акустической эмиссии является лидирующим среди методов автоматического обнаружения утечек трубопроводов.
В заключение следует отметить следующее. Анализ литературы показывает, что многие вопросы, связанные с повышением точности при обнаружении утечек (по точности локализации места утечек, по количеству
117
ложных срабатываний и пр.), могут быть решены при улучшении алгоритмов обработки результатов, получаемых с размещенных вдоль по трубопроводу датчиков.
Список литературы
1.РД-13.320.00-КТН-223-09. Системы обнаружения утечек комбинированного типа на магистральных нефтепроводах. ОАО «АК «Транснефть», 2009.
2.Глушков, Э.И. Системы обнаружения утечек нефти в трубопроводах – но-
вая продукция ОАО «Нефтеавтоматика» / Э.И. Глушков, Р.В. Аскаров // Автоматизация, телемеханизация и связь в нефтяной промышленности. - М : ВНИИОЭНГ, 2009. - №4. - С.19-20.
3.Коршак, А.А. Диагностика объектов нефтеперекачивающих станций / А.А. Коршак, Л.Р. Байкова. - Уфа : ДизайнПолиграфСервис, 2008. – 176 с.
4.Кузнецов, Н.С. Теория и практика неразрушающего контроля изделий с помощью акустической эмиссии / Н.С. Кузнецов. - М : Машиностроение, 1998. - 197.
5.Клюев, В.В. Неразрушающий контроль и диагностика / В.В. Клюев. - М : Машиностроение, 2003. – 636 с.
5.Анализ методов обнаружения утечек, применяемых в параметрических СОУ
–2012 [Электронный ресурс]. URL: http://conf.sfu-kras.ru/ sites/mn2012/thesis/s026/ s026-058.pdf (дата обращения: 15.12.2012).
6.Безопасность трубопроводного транспорта углеводородов – 2007 [Электронный ресурс]. URL: http://www.vipstd.ru/gim/content/view/535/206/ (дата обращения: 11.03.2012).
А. А. Кривда, студент
Ф. А. Уразбахтин, доктор физико-математических наук, профессор Ижевский государственный технический университет
имени М. Т. Калашникова, Воткинский филиал
Аэродинамический нагрев головных частей ракеты
Аэродинамический нагрев (АН) является одной из наиболее важных проблем в области ракетостроения. Он происходит при входе ракет в слои атмосферы и оказывает сильное влияние на обтекаемость ракеты.
При входе в слои атмосферы происходит торможение потока носовой частью ракеты, что вызывает сжатие и нагревание воздуха перед ней. Вся кинетическая энергия переходит в потенциальную. Температура, которую при этом имеет воздух является температура торможения (ТТ). При высоких скоростях сжатие и температура воздуха возрастает. При этом часть тепла отводится в окружающее пространство, а остальная ― воспринимается носовой частью поверхности ракеты. Другой причиной, вызывающей торможение потока, являются вязкие свойства воздуха. У поверхности обтекаемой ракеты образуется тонкий пограничный слой заторможенного воздуха, скорость в котором, изменяется от нуля, на поверхности ракеты,
118
до скорости потока на внешней границе пограничного слоя. Из-за разности скоростей в соприкасающихся слоях воздуха у поверхности ракеты возникает внутренний напор, который вызывает в тонком пограничном слое нагрев. И в этом случае часть тепла уходит в окружающую среду, а часть остается в пограничном слое.
Увеличение скорости полета ракеты очень сильно повышает ТТ. Температура поверхности ракеты несколько ниже ТТ вследствие теплового излучения в окружающее пространство и отвода части тепла внутрь ракеты. Чтобы избежать нагрева используются различные методы теплозащиты:
1)Создание тупого угла головной части (ГЧ) ракеты. При полете в атмосфере такой ракеты впереди нее образуется очень мощная ударная волна, которая тормозит и отражает в атмосферу приблизительно 90% тепловой энергии. При такой форме ГЧ только одна десятая тепла идет на нагрев корпуса ракеты.
2)Покрытие ГЧ ракеты такими веществами, которые для плавления и испарения требуют очень большого количества тепловой энергии и имеют, меньшую скорость передачи тепла. Этот слой при полете обгорает, но ракета остается невредимой. Для покрытия ГЧ можно использовать, например, углерод, окись магния и другие вещества.
3)Применение термостойких покрытий и искусственного охлаждения.
4)Создание обшивки с циркулирующей по ее внутренней поверхности жидкостью (тепловая подушка).
5)Обработка наружных поверхностей до зеркальной чистоты для отражения солнечных лучей.
Предполагается, что при помощи подбора материала и модернизации известных средств теплозащиты современными методами обработки материала, используемых для ГЧ, можно эффективно бороться с АН.
Список литературы
1. Киселев, С.П. Физические основы аэродинамики ракет / С.П. Киселев. –
М.: Воениздат, 1976. – 111 с.
Е. Ю. Кривенцева, магистрант
В. Г. Кучеров, кандидат технических наук, профессор В. И. Карлов, кандидат технических наук, доцент Волгоградский государственный технический университет
Пути стабилизации длины отката артиллерийских орудий
Современные танковые и самоходные орудия располагаются в стесненных по габаритам боевых отделениях, что требует уменьшения объемов, занимаемых ограждениями откатных частей. Для рационального выполнения указанных требований на одно из первых мест выходит необхо-
119
димость стабилизации длины отката.
Решение задачи стабилизации длины отката зависит от конкретного типа тормоза отката, от устройства его основных элементов. Так, например, в тормозах отката с клапаном внутри поршня нестабильность длины отката объясняется большим допуском на усилие пружины клапана [1, с.230]. Более стабильной длина отката будет при введении в клапанное устройство не менее одного дополнительного клапана, расположенного последовательно с основным, что и обосновывается в патенте [2].
Интересным решением проблемы стабилизации длины отката и наката является предложение снабжения тормоза отката веретенного типа двумя дополнительными дросселями [3]. Авторы патента предложили устанавливать дополнительные дроссельные каналы для тормозов отката веретенного и канавочного типов, срабатывающих как при откате, так и при накате, что обеспечивает плавность торможения в крайних положениях откатных частей.
Однако эти предложения не учитывают изменения температуры жидкости в тормозе отката, что особенно необходимо при интенсивной стрельбе из танковых и самоходных орудий. Возможным вариантом решения данной задачи может быть перемешивание жидкости в тормозе отката с жидкостью в дополнительном резервуаре (рис. 1), при этом резервуар может быть как расположенным отдельно от тормоза отката в наиболее целесообразном месте, так и охватывающим рабочий цилиндр тормоза.
В патентах [4] и [5] описаны различные варианты, обеспечивающие указанный подход к конструированию таких теплообменников. Практически подобные решения только увеличивают объем жидкости в тормозе отката, замедляя процесс еѐ нагревания.
При интенсивной стрельбе нагрев жидкости в тормозе отката может сказываться двояко: увеличение объема жидкости, приводящее к необходимости введения в конструкцию тормоза отката компенсатора; изменение свойств жидкости, при нагревании она становится более текучей и оказывает меньшее сопротивление, следовательно, увеличивает длину отката. Для стабилизации длины отката целесообразно автоматизировать процесс таким образом, чтобы, например, уменьшать площадь отверстия истечения жидкости в тормозе отката. При этом возможно такое изменение площади отверстия истечения, которое обеспечит силу сопротивления по длине отката за счет изменения коэффициента силы сопротивления вследствие нагрева жидкости. Следует отметить, что конструктивное обеспечение решения такой задачи будет зависеть от типа тормоза отката, от его конструктивных особенностей.
Использование дополнительного объема жидкости при ее нагревании во время интенсивной стрельбы приведено в патенте на полезную модель [6].
120
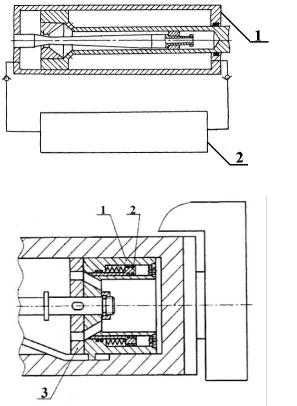
Рис. 1. Схема тормоза отката с теплообменником: 1 – тормоз отката; 2 ‒ теплообменник
Рис. 2. Гидравлический тормоз отката золотникового типа: 1 – полый поршень; 2 – плавающий поршень; 3 – золотник
В тормозе отката золотникового типа (рис. 2) поршень закреплен на штоке и может вращаться только относительно штока за счет вхождения зубьев поршня в винтовые пазы цилиндра тормоза отката. Золотник, размещенный на штоке, может перемещаться лишь вдоль штока. При откате давлением жидкости золотник поджимается к поворачивающемуся поршню, они взаимно разворачиваются, перекрывая соответствующие рабочие отверстия в золотнике и поршне, регулируя площадь дроссельного канала для обеспечения заданной силы сопротивления тормоза отката. Отличительной особенностью полезной модели является изготовление поршня полым и размещение в нем компенсатора жидкости со ступенчатым плавающим поршнем и пружиной, расположенных в стенке поршня тормоза отката.
При разогреве жидкости в случае интенсивной стрельбы ее «излишний» объем поступает в компенсатор, сжимает пружину и сдвигает ступенчатый плавающий поршень, выступы которого входят в рабочие отверстия поршня тормоза отката, что ведет к изменению площади дрос-
121
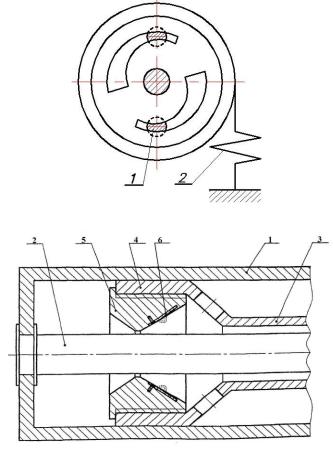
сельного канала, но, учитывая одновременное изменение свойств жидкости, сохраняется расчетная сила сопротивления тормоза отката.
Тем самым установка теплового компенсатора в тормоз отката золотникового типа обеспечивает постоянство длины отката при изменяющейся температуре жидкости.
Для перекрытия отверстия истечения жидкости при ее нагреве можно также использовать изменение формы термобиметаллических пластин или пружин. Например, в патенте на полезную модель [7] изменение формы спиральной пружины используется для вращения золотника в тормозе отката золотникового типа, что изменяет площадь канала истечения жидкости в зависимости от ее температуры, тем самым стабилизируется длина отката (рис. 3).
Рис. 3. Вариант вращения золотника: 1 – изменяющаяся площадь; 2 – пружина
Рис. 4. Гидравлический тормоз отката веретенного типа:
1 – цилиндр; 2 – веретено; 3 – шток; 4 – поршень; 5 – регулирующее кольцо; 6 – термобиметаллическая пластина
122
Возможно регулирование силы сопротивления в тормозе отката и не за счет изменения площади отверстия истечения, а за счет создания вихревых сопротивлений в потоке жидкости [8].
Были проведены эксперименты по изменению вихревых потоков жидкости на модели тормоза отката веретенного типа (рис. 4). При нагревании жидкости расположенная в канале истечения термобиметаллическая пластина деформировалась на величину, превосходящую толщину пограничного слоя жидкости, создавая дополнительные вихревые сопротивления, что приводило к стабилизации силы сопротивления тормоза отката. Подобное решение задачи стабилизации длины отката можно осуществить в тормозе отката практически любого типа.
Таким образом, задача стабилизации длины отката является актуальной, что показывают рассмотренные нами конструктивные решения, опубликованные в патентной литературе.
Список литературы
1.Артиллерийское вооружение. Основы устройства и конструирование: учеб. для вузов / И.И. Жуков [и др.]. – М.: Машиностроение, 1975. – 420 с.
2.Гидравлический тормоз отката артиллерийского орудия: пат. 2163995 Рос.
Федерация: МПК F 41 A 25/00/ Вахрушев Ю.В.; заявитель и патентообладатель ОАО «Мотовилихинские заводы». ‒ № 99126138/02; заявл. 14.12.1999; опубл.
10.03.2001.
3.Тормоз отката и наката артиллерийского орудия: пат. 2309359 Рос. Федерация: МПК F 41 A 25/00/ Набоков Ф.В., Суханов М.Б.; заявитель и патентообладатель ОАО «Мотовилихинские заводы». ‒ № 2006101365/02; заявл. 17.01.2006; опубл. 17.01.2006.
4.Гидравлический тормоз отката артиллерийского орудия: пат. 2146035 Рос. Федерация: МПК F 41 A 25/00/ Шварев Р.Я.; заявитель и патентообладатель ОАО «Мотовилихинские заводы». - № 4518255/02; заявл. 17.07.1989; опубл. 27.02.2000.
5.Гидравлический тормоз отката и наката артиллерийского орудия: пат. 2165576 Рос. Федерация: МПК F 41 A 25/00/ Набоков Ф.В., Шварев Р.Я.; заявитель и патентообладатель ОАО «Мотовилихинские заводы». ‒ № 99118147/02; заявл. 18.08.1999; опубл. 20.04.2001.
6.Гидравлический тормоз отката золотникового типа: пат. 109841 Рос. Федерация: МПК F 41 A 25/00/ Кучеров В.Г., Арсентьева О.Ю.; заявитель и патентообладатель ГОУ ВПО ВолгГТУ. – опубл. 2010.
7.Тормоз отката золотникового типа: пат. 2276487 Рос. Федерация: Кучеров В.Г., Шалыгина Е.В.; заявитель и патентообладатель ГОУ ВПО ВолгГТУ. – опубл.
2004.
8.Гидравлический тормоз отката веретенного типа: пат. 61403 Рос. Федерация: МПК F 41 A 25/00/ Кучеров В.Г., Шалыгина Е.В.; заявитель и патентообладатель ГОУ ВПО ВолгГТУ. ‒ № 2006135248/22; заявл. 05.10.2006; опубл. 27.02.2007, Бюл. № 6.
123
П. С. Кучев, аспирант; Д. С. Белинин, аспирант; А. Ю. Шилов, студент
Ю. Д. Щицын, доктор технических наук, профессор Пермский национальный исследовательский политехнический университет
Исследование различных схем подключения двухкамерного плазмотрона
Каждый из способов сварки имеет определенные как преимущества, так и недостатки. Создание комбинированных и гибридных технологий сопровождается совмещением технологических и других преимуществ отдельных способов сварки и сведением к минимуму недостатков. Основными задачами, стоящими перед сварочным производством, являются: повышение скорости сварки, снижение энерго- и материалоемкости, управление формой шва и повышение качества соединения. При сварке плавлением на протяжении многих лет успешно решается задача расширения диапазона толщин соединяемых деталей, а при наплавке – задача минимального проплавления, уменьшения зоны сплавления между деталью и наплавляемым слоем (валиком). Эффективно эти задачи могут решаться путем разделения тепловложения, нагрева и расплавления между двумя (и более) источниками энергии, одновременно «действующими» в общей зоне сварки/наплавки. При этом каждый из источников выполняет незначительно или принципиально различающиеся функции. Следует отметить, что в публикациях иногда такие способы называют «комбинированными» или «гибридными», полагая, что для этих названий обобщающим признаком является новый технологический эффект.
Среди принципиально новых технологий, основанных на использовании концентрированных потоков энергии, плазменные процессы занимают ведущее место. Перспектива их широкого применения, кроме высокой концентрации энергии, обусловлена возможностью совмещения в едином технологическом цикле различных видов обработки, локальностью и прецизионностью нагрева, мобильностью и технологической гибкостью.
В настоящей работе предлагается рассмотреть способы плазменной сварки:
−однодуговой (плазменная струя);
−однодуговой с использованием различной конфигурации стабилизирующего сопла;
−комбинированный с использованием двух источников питания, плюсовые клеммы которых подключены к стабилизирующему соплу;
−комбинированный с использованием двух источников питания, плюсовые клеммы которых подключены к плазмообразующему соплу;
−комбинированный, при котором один источник питания подключен
кэлектроду и плазмообразующему соплю, второй – к стабилизирующему соплу и изделию;
124
−комбинированный, при котором один источник питания подключен
кэлектроду и стабилизирующему соплу, второй – к плазмообразующему соплу и изделию.
Целью работы является установление принципиальной возможности использования комбинированного процесса плазменной сварки в сравнении с однодуговым процессом плазменной сварки, оценка тепловых нагрузок и их распределения между элементами плазматрона и изделием, а также оценка влияния параметров процесса на это распределение. Также целью работы является установление ресурса работы плазмотрона и его элементов, выявление особенностей формирования комбинированной дуги.
Оценка влияния параметров на тепловые нагрузки плазмотрона и теплоотдачу в изделие проводились методом калориметрирования тепловложения в электродный узел, плазмообразующее сопло и изделие. Охлаждая имитатор изделия водой, можно количественно оценить энергию, вложенную в изделие и переданную воде, измеряя ее начальную и конечную температуры:
Ри = С ∙ m ∙ ∆t,
где С – удельная теплоемкость воды, 4190 Дж/кг∙град; m – расход воды, кг/с (л/с); ∆t – разность температур на входе и выходе магистрали.
Вкачестве основных факторов были выбраны технологические пара-
метры: I1 ‒ сила тока плазменной струи, I2 – сила тока плазменной дуги, Qпл ‒ расход плазмообразующего газа, Qст – расход стабилизирующего газа и геометрические параметры: dпс – диаметр плазмообразующего сопла, hэс ‒ расстояние от электрода до среза плазмообразующего сопла, hси – расстояние от среза сопла до изделия.
Первую серию экспериментов проводили по схеме подключения однодугового плазмотрона, приведенной на рис. 2. Диаметр электрода 2 мм, диаметр плазмообразующего сопла изменяли в пределах 3‒4 мм, ток
плазменной дуги I1 изменяли в пределах от 40 до 200 А.
Далее проводили серию экспериментов с использованием двух источников питания (комбинированная схема). Плазменная струя имела прямую полярность, сжатая дуга – обратную.
Вкомбинированной схеме подключения плазмотрона № 1 (рис. 2) стабилизирующее сопло является кольцевым анодом. Диаметр плазмообразующего сопла изменяли в пределах 3,5–4мм, стабилизирующего: 4‒5мм, ток плазменной струи изменяли в пределах 80–120 А, сжатой дуги фиксировали в пределах 60–80 А.
125
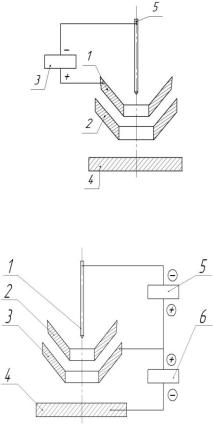
Рис. 1. Схема подключения однодугового плазмотрона: 1 – плазмообразующее сопло; 2 – стабилизирующее сопло; 3 – источник питания;
4 – имитатор изделия; 5 ‒ электрод
Рис. 2. Комбинированная схема подключения плазмотрона № 1: 1 – электрод; 2 – плазмообразующее сопло; 3 – стабилизирующее сопло; 4 – имитатор изделия;
5,6 – источники питания
В комбинированной схеме подключения плазмотрона № 2 (рис. 3) плазмообразующее сопло является кольцевым анодом. Диаметр плазмообразующего сопла изменяли в пределах 4‒5мм, стабилизирующего: 5‒7мм, ток плазменной струи изменяли в пределах 10–120 А, сжатой дуги: 60–160 А.
С повышением силы тока плазменной струи увеличивается стабильность процесса. При силе тока плазменной струи I1 = 10 А и увеличении силы тока сжатой дуги I2 от 40 до 180 А, произошло оплавление плазмообразующего сопла. Тепловложение в изделие на 25 % выше, чем при схеме подключения однодугового плазмотрона № 1.
126
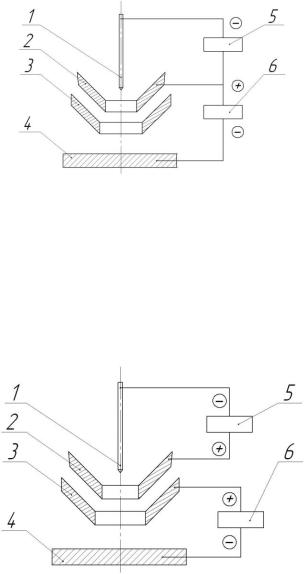
Рис. 3. Комбинированная схема подключения плазматрона № 2: 1 – электрод; 2 – плазмообразующее сопло; 3 – стабилизирующее сопло; 4 – имитатор изделия; 5,6 – источники питания.
В комбинированной схеме подключения плазмотрона № 3 (рис. 4) один источник питания подключен на электрод – плазмообразующие сопло, второй – стабилизирующее сопло – изделие.
Данная схема подключения отличается нестабильностью процесса. Дуга зажигалась и гасла, периодически с небольшими интервалами. При увеличении расходов плазмообразующего и защитного газов, а также при повышении силы тока сжатой дуги, стабильность процесса не возросла. Поэтому данная схема не рассматривалась в дальнейшем.
Рис. 4. Комбинированная схема подключения плазмотрона № 3: 1 – электрод; 2 – плазмообразующее сопло; 3 – стабилизирующее сопло; 4 – имитатор изделия; 5,6 – источники питания.
Проведенные исследования различных схем двухдугового плазмотро-
127
на показали, что использование комбинированного подключения плазмотрона с использованием двух источников питания, плюсовые клеммы которых подключены к стабилизирующему соплу обеспечивают наибольшую эффективность при работе на обратной полярности.
Установлено, что процесс обладает высокой стабильностью в широком диапазоне изменения параметров. На устойчивость горения влияют соотношения токов плазменной струи и сжатой дуги, расхода газа и диаметра канала сопла. Увеличение расхода плазмообразующего газа и уменьшение длины участка сопло-изделие приводит к увеличению напряжения сжатой дуги.
Д. С. Манукян, аспирант
М. М. Матлин, доктор технических наук, профессор Волгоградский государственный технический университет
Неразрушающая методика контроля предела прочности деталей болтовых соединений
Разработка неразрушающих методик контроля прочности деталей резьбовых соединений актуальна в областях машиностроения, судостроения и авиастроения. В современных автомобилях и тракторах количество болтовых соединений достигает нескольких десятков тысяч, а в планерах пассажирских лайнеров и нескольких сотен тысяч и в связи с этим становится актуальной проблема экспресс-контроля их прочности.
В качестве объекта исследования были взяты болты, наиболее часто применяемые в автомобилестроении и авиастроении: болты с диаметром 8, 10, 12 и 14 мм со стандартной метрической резьбой классов прочности
5.8и 8.8 [1].
Для указанных выше болтов была определена пластическая твердость
НД [2, 3] и определен, согласно методике приведенной в работе [4], предел прочности. Результаты представлены в табл. 1.
Метод реализуют следующим образом. Сферический индентор (шарик с диаметром D) внедряют нагрузкой F в испытуемую поверхность детали. Измеряют после разгрузки диаметр d0 остаточного отпечатка и вычисляют ζв, используя формулу (1).
В |
|
|
|
|
0,955(1 2 2 )F |
|
|
|
, |
(1) |
||||||
|
|
|
d0 |
|
|
|
F |
|
|
|
|
245/ НД |
||||
|
|
|
|
|
|
|
|
|
|
|||||||
|
d 2 |
0,0017 |
9,43К |
|
|
1 |
2 |
|
НД |
|
|
|||||
|
1 d 2 |
|
|
|
||||||||||||
0 |
|
|
D |
|
|
|
|
2 |
|
|
|
|||||
|
|
|
|
|
|
|
|
0 |
|
|
|
|
|
|
|
|
где дополнительно |
К 1 2 / Е |
; |
1 |
и |
Е |
– соответственно коэффи- |
||||||||||
|
|
|
1 |
|
1 |
1 |
|
|
|
1 |
|
|
|
|
циент Пуассона и модуль нормальной упругости материала сферического индентора; НД – контактный модуль упрочнения (пластическая твердость,
128
определяемая по ГОСТ 18835-73 [2]) материала поверхности испытуемой детали; 2 – коэффициент Пуассона материала испытуемой детали.
В качестве примера приведен расчет для болта М10×90 класса прочно-
сти 5.8: |
|
К 1 2 / Е 1 0,292 / 2,1 105 1,388 10 6 |
||||||||||
|
|
|
||||||||||
|
|
|
1 |
|
1 |
1 |
|
|
|
|
(2) |
|
В |
|
|
|
|
0,955(1 2 2 |
)F |
|
|
|
|||
|
|
|
d0 |
|
|
F |
|
|
|
245/ НД |
||
|
|
|
|
|
|
|
||||||
|
d 2 |
0,0017 |
9,43К |
|
1 |
2 |
|
HД |
|
|||
|
|
|
|
|||||||||
0 |
|
|
D |
|
1 d02 |
|
2 |
|
|
|||
|
|
|
|
|
|
|
|
|
|
|
|
|
|
|
|
|
|
0,955(1 2 0,3 ) 29400 |
|
|
|||
|
|
|
4,15 |
|
29400 |
|
|
245/ 2533,6 |
||
4,152 |
0,0017 |
|
9,43 1,388 10 6 |
|
1 |
2 |
0,3 2533,6 |
|
||
|
4,152 |
|
||||||||
|
|
|
|
10 |
|
|
|
|
|
|
|
|
|
|
|
|
|
|
|
|
|
662,8 МПа
(3)
С целью сравнения результатов, полученных неразрушающим методом, были проведены испытания на растяжение (статическую прочность) [5] с использованием программно-технического комплекса для испытания материалов ИР-5143-200, которые представлены в табл. 1. С помощью комплекса ИР-5143-200 получены диаграммы растяжения, представленные на рис. 1.
Результаты выполненного экспресс контроля временного сопротивления (предел прочности) для каждого болта были сопоставлены с результатами испытаний болтов на растяжение и представлены также в табл. 1.
По классу прочности болтов, использованных в испытаниях, можно отметить, что минимальное значение предела прочности для класса прочности 5.8 составляет 500 МПа, а для класса 8.8 ‒ 800 МПа. Из опытов видно, что реальный предел прочности выше регламентируемого. Это связано с тем, что заявленные величины являются минимальными и реальные значения предела прочности могут быть и больше.
129

Рис. 1. Диаграммы растяжения болтов М10×70 класса прочности 8.8.
Таблица 1. Погрешности измерения предела прочности и условного предела
текучести двумя способами
|
Из опыта |
Из опыта на твердость |
Погрешность |
|
на растяжение |
||
|
|
|
|
Маркировка болта |
ζв, |
ζв , |
δζв , |
|
|||
|
МПа |
МПа |
% |
|
|
|
|
М8×50 (5.8) |
656,41 |
662,89 |
0,98 |
М10×70 (8.8) |
938,35 |
912,21 |
2,87 |
М10×90 (5.8) |
652,08 |
662,89 |
1,63 |
М12×80 (8.8) |
894,84 |
873,82 |
2,41 |
М12×90 (5.8) |
555,32 |
624,80 |
7,12 |
М14×120 (5.8) |
582,46 |
527,12 |
6,50 |
М8×50 (5.8) |
830,03 |
869,18 |
4,50 |
|
|
|
|
М10×70 (8.8) |
830,00 |
869,77 |
4,57 |
Как видно, подавляющее большинство результатов по определению предела прочности неразрушающим методом расходятся менее, чем на 5%, что вполне удовлетворительно для инженерных расчетов.[6].
Таким образом, данный метод можно рекомендовать для практического использования.
Список литературы
1.ГОСТ 1759.0-87. Болты, винты, шпильки и гайки. Технические условия. - М. : Стандартинформ, 2006. - 15 с.
2.ГОСТ 18835-73. Металлы. Метод измерения пластической твердости. – М.: Издательство стандартов,1974. - 10 с.
130
3.Дрозд, М. С. Инженерные расчеты упругопластической контактной деформации / М. С. Дрозд, М. М. Матлин, Ю. И. Сидякин. - М. : Машиностроение, 1986.
-224 c.
4.Пат. 2011182 РФ, МПК G01N 3/40. Способ определения предела прочности материалов / Ю.И. Славский, М.М. Матлин; ВолгГТУ. - 1997.
5.ГОСТ 1759.4-87 (ИСО 898/1-78). Болты, винты и шпильки. Механические свойства и методы испытаний.- М. : Стандартинформ, 2006. - 17 с.
6.Манукян, Д. С. Экспресс-контроль прочности резьбовых соединений / Д. С. Манукян // Международная молодежная научная конференция «XIX Туполевские чтения» материалы конференции. - Т. 1 - Казань : Изд-во Казан. гос. техн. ун-та. -
2011. - С. 183-184.
М. А. Матвеева, аспирант
И. В. Чуманов, доктор технических наук, профессор Южно-уральский государственный университет, Златоуст, Россия
Получение металлической композиции методом электрошлакового переплава
Развитие техники вызывает необходимость создания материалов, обладающих уникальным комплексом свойств, таких как высокая прочность, коррозионная стойкость, электро- и теплопроводность, жаропрочность, износостойкости др. Монометаллы и сплавы часто не могут обеспечить требуемую гамму свойств. Поэтому важная роль в создании новых материалов со специальными свойствами принадлежит многослойным металлическим композициям. Такие материалы могут быть изготовлены с помощью соединения разнородных материалов в композицию, сохраняющую надежную связь составляющих ее компонентах при дальнейшей технологической обработке и в условиях эксплуатации.
Применение слоистых металлических композиций позволит не только повысить надежность и долговечность деталей и оборудования, но и значительно сократит расходы на их изготовление в результате экономии легирующих металлов. Кроме того, использование слоистых композиций с новым комплексом свойств, способствует разработке более совершенных конструктивных решений при создании машин, приборов, аппаратов.
Однако, не смотря на большое количество работ, посвященным вопросам создания слоистых композиционных материалов, остается важная проблема – проблема обеспечения надежного соединения слоев в композиции.
Возможно получение композиционного материала с помощью электрошлакового переплава. Электрошлаковая технология позволяет получить материал высокого качества с прочным соединением слоев. К тому же электрошлаковый переплав обладает рядом преимуществ, которые позволяют получить металл высокого качества: плотная структура слитка,
131
отсутствие усадочной раковины и пористости; высокое качество поверхности; возможность управления направлением и скорость кристаллизации; возможность введения добавок по ходу процесса с высокой степенью их усвоения. Один из методов получения металлического композиционного материала методом ЭШП был разработан в филиале ЮУрГУ (НИУ) в г. Златоусте. Суть способа – получение композиционного материала с многослойной структурой посредством электрошлакового переплава, заключающегося в присадке, в процессе переплава, одинаковых порций добавок через равные промежутки времени [1]. Согласно разработанному способу, проведен переплав электрода стали марки 30Х13 с присадкой науглероживателя [2]. В результате переплава получен слиток с ярко выраженной слоистой структурой. В процессе изучения материала [3], нами были сделаны следующие выводы:
1.Исследования микроструктурные показали, что полученный материал обладает плотной структурой с надежным сплавлением слоев. Отмечается так же и высокая чистота материала по наличию неметаллическим включениям.
2.Наличие слоев с высоким (в сравнении с исходным материалом) содержанием углерода – позволяет утверждать об упрочнении материала, за счет армирования его высокоуглеродистым слоем.
Список литературы
1.Пат. №2163269 Российская Федерации, «Способ получения многослойного слитка электрошлаковым способом» /В.И.Чуманов, В.Е. Рощин, И.В.Чуманов, Ю.Г.Кадочников.– 2001. Бюл.5.
2.Чуманов, И. В. Особенности жидкофазного получения слоистого материала / И.В. Чуманов, В.И.Чуманов, М.А. Матвеева // Металлургия машиностроения. – 2012. – №2. – С.11–14.
3.Чуманов, И.В. Исследование композиционного материала с многослойной
структурой полученного методом электрошлакового переплава / И.В. Чуманов, В.И.Чуманов, М.А. Матвеева //Электрометаллургия. 2011. №9. С.35–38.
А. С. Мельников, аспирант
М. Н. Каракулов, доктор технических наук, профессор Воткинский филиал Ижевского государственного технического университета
имени М. Т. Калашникова
Исследование многопарного контакта плунжерной передачи
Как показывают результаты теоретических и экспериментальных исследований [1‒3], в плунжерной передаче возможно получение многопарного контакта, что заставляет искать пути решения задачи распределения
132
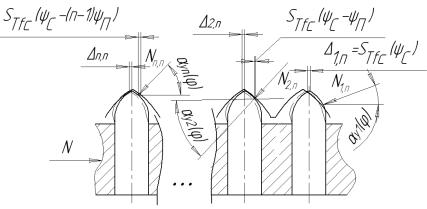
сил в n-парном зацеплении.
Изначально количество плунжеров, участвующих в контакте, неизвестно, так как оно зависит как от геометрии зацепления, так и от величины деформаций, определяемой уровнем нагружения передачи. Очевидно, что в передаче с одной и той же геометрией зацепляющихся поверхностей возможно получение разной парности контакта в зависимости от величины крутящего момента на выходном валу.
В качестве примера на рис. 1 показана схема n-парного контакта в плунжерной передаче. В дальнейших рассуждениях примем следующие обозначения: N , ‒ нормальная сила в ‒ парном зацеплении, прило-
женная к -ому плунжеру, , ‒ деформация отдельного плунжера под действием силы N , .
Рис. 1. К определению распределения сил в n-парном плунжерном зацеплении
Контакт рассматриваемого плунжера с зубом колеса происходит в точке, расположение которой определяется углом C C ( C ) . При
этом, если пренебречь (в целях упрощения) деформациями зубьев колеса, точка контакта смеситься в окружном направлении на расстояние STfc ( C ) , равное деформации плунжера 1,n под действием силы N1,n . В
этом случае зазор между следующим плунжером и зубом колеса будет равен Tfc2,n S 2,n C П , где S ‒ зазор без учета деформаций элементов зацепления. Если Tfc2,n 0 , то зацепление перейдет в фазу двух-
парного контакта, что вызовет появление силы N2,n и деформации следующего плунжера на величину 2,n STfc C П и т. д. до получения n ‒ парного контакта.
На рис. 2 и 3 схематично показан плунжер, находящийся под действием сил, приложенных к нему со стороны однопарного и двухпарного зацепления.
133
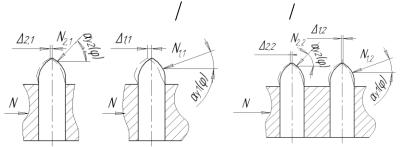
Приложение к ведомому валу передачи постоянного по величине крутящего момента Tкр2 вызывает возникновение окружной силы N, которая его уравновешивает. В зависимости от рассматриваемого положения плунжера к нему со стороны зуба колеса будет приложена нормальная
сила |
N , , уравновешивающая силу N. Для упрощения расчетов силу N, |
уравновешивающую номинальный крутящий момент, приложенный к выходному валу, можно принять постоянной и определить из выражения: N 2Tкр2 / mZ K k2 . Сила, приложенная к плунжеру, в зависимости от его
положения, вызывает его деформацию , STfc , .
Если рассматривать пару плунжеров, угловой шаг между которыми определяется углом П П , то можно выделить два их состояния. Пер-
вое состояние (рис. 2) – контакт зуба колеса и плунжера в условиях однопарного зацепления, второе (рис. 3) – контакт в условиях двухпарного зацепления. Исходя из теоремы о взаимности работ (теорема Бетти) [4],
можно записать, что |
|
|
|
|
|
|
|
N |
cos |
|
N |
cos |
; |
|
|
|
1,1 |
|
y1 1,2 |
1,2 |
|
y1 1,1 |
(1) |
|
|
|
|
|
|
|
N2,1 cos y 2 2,2 N2,2 cos y 2 2,1.
Наибольшее влияние на положение точки контакта зуба колеса и плунжера оказывают деформации плунжера, т. к. они складываются из множества составляющих: деформации плунжера под действием изгиба, контактные деформации в зацеплении, контактные деформации в паре плунжер-сепаратор и т.д. Поэтому, если пренебречь (в целях упрощения) деформациями зубьев колеса, можно считать, что в двухпарном зацепле-
нии 1,2 2,2 . С |
другой |
стороны, в однопарном |
зацеплении |
N1,1cos y1 N2,1cos y2 |
N . Учитывая вышесказанное, выражение (1) |
||
можно переписать в виде: |
N2,2 cos y 2 2,1 1,1 . |
|
|
N1,2 cos y1 |
(2) |
Рис. 2. К определению распределения |
Рис. 3. Двухпарный контакт в плун- |
сил в зацеплении плунжерной передачи |
жерном зацеплении |
134
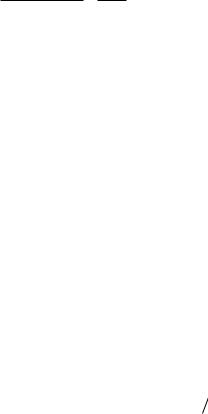
Проведя аналогичные рассуждения для n - парного контакта можно получить связь между деформациями плунжеров, участвующих в зацеплении, которая определяется выражением:
N |
,n |
cos |
|
|
|
|
|
N |
1,n |
cos |
|
|
|
y, |
|
|
1,1 |
, |
|
|
|||||
|
|
|
|||
y, 1 |
|
,1 |
|
||
|
|
|
|
при
=1..
(n
1)
.
(3)
Учитывая, что нормальные силы в зацеплении уравновешиваются крутящим моментом, приложенным к выходному валу, уравнения, позволяющие определить распределение сил в зацеплении, можно представить в виде системы, состоящей из n уравнений, т.е.
|
n |
|
|
|
|
|
|
|
|
|
|
|
|
|
|
|
|
|
|
N ,n ( ) cos y, ( 1 П ) N , |
|
|
|
|
|
|
|
(4) |
|||||||||||
|
1 |
|
|
|
|
|
|
|
|
|
|
|
|
|
|
|
|
||
|
N |
,n |
cos |
y, |
|
|
1,1 |
|
S ( ( ) 1 |
П |
( |
П |
)) |
|
|||||
|
|
|
|
|
|
|
Tfc |
|
|
|
|
|
, |
||||||
N |
1,n |
cos |
y, 1 |
|
,1 |
S ( ( ) |
П |
( |
П |
)) |
|
||||||||
|
|
|
|
||||||||||||||||
|
|
|
|
|
|
|
Tfc |
|
|
|
|
|
|
где первое уравнение связывает нормальные силы в зацеплении с крутящим моментом на выходном валу, а остальные (n-1) уравнений связывают деформации плунжеров.
Учитывая, что распределение сил в зацеплении во многом определяется распределением зазоров в ненагруженной передаче, в общем случае определение парности контакта и распределения сил в плунжерном зацеплении рекомендуется проводить в следующей последовательности:
1)вычисление деформации плунжера в условиях однопарного контакта:
1 1,1 STfc ( C ) ;
2)вычисление зазора между зубом колеса и следующим плунжером с учетом деформаций в зацеплении можно произвести с помощью выражения:
Tfc2,1 S 2,1( C П ) 1 ;
3) если |
0 , то принимается парность контакта n=1 и распределение |
||||||||||||||||
Tfc2,1 |
|
|
|
|
|
|
|
|
|
|
|
|
|
|
|
|
|
сил в зацеплении определяется зависимостью |
N ( ) N cos |
y1 |
( ) ; |
||||||||||||||
|
|
|
|
|
|
|
|
|
|
|
1,1 |
|
|
|
|
|
|
4) если |
0, то принимается n = 2 и распределение сил в зацеплении |
||||||||||||||||
Tfc2,1 |
|
|
|
|
|
|
|
|
|
|
|
|
|
|
|
|
|
определяется системой уравнений (4), т. е. |
|
|
|
|
|
|
|
||||||||||
|
N1,2 ( ) cos y1( ) N2,2 |
( ) cos y 2 ( П ) N, |
|
|
|||||||||||||
|
|
STfc ( ( )) |
|
|
|
|
N2,2 ( ) cos y 2 ( |
|
|
|
(5) |
||||||
|
|
|
|
|
|
П ) |
; |
|
|
||||||||
|
|
|
|
|
|
|
|
|
|
|
|
|
|
|
|||
|
S |
( ( ) |
П |
( |
П |
)) |
|
N ( )cos |
y1 |
( ) |
|
|
|
||||
|
Tfc |
|
|
|
|
|
1,2 |
|
|
|
|
|
|
5)определение деформаций плунжеров при n = 2 можно произвести с помощью выражения: 2 2,2 1,1(N1,2 ( C )) ;
6)вычисление зазора между зубом колеса и следующим плунжером:
Tfc3,1 S 3,1( C 2 П ) 2 ;
135
7) если |
0 |
, то парность контакта n=2 и распределение сил в зацеп- |
||||||||||||||||||||
|
|
|
Tfc3,1 |
|
|
|
|
|
|
|
|
|
|
|
|
|
|
|
|
|
|
|
лении определяется зависимостями |
N |
( ) |
и |
N |
2,2 |
( ) |
; |
|||||||||||||||
|
1,2 |
|
|
|
|
|
||||||||||||||||
|
|
|
|
|
|
|
|
|
|
|
|
|
|
|
|
|
|
|
|
|
||
8) если |
0 |
, то принимается n = 3 и распределение сил в зацеплении |
||||||||||||||||||||
|
|
|
Tfc3,1 |
|
|
|
|
|
|
|
|
|
|
|
|
|
|
|
|
|
|
|
определяется системой уравнений: |
|
|
|
|
|
|
|
|
|
|
||||||||||||
|
|
|
|
|
|
|
|
|
|
|
|
|
|
|
|
|
|
|
|
|
|
|
|
|
( ) cos y1 ( ) |
N2,3 ( ) cos y 2 ( П ) N3,3 ( ) cos y 2 ( 2 П ) N, (6) |
|||||||||||||||||||
N1,3 |
||||||||||||||||||||||
|
|
|
STfc ( ( )) |
|
|
|
|
N2,3 ( ) cos y 2 cos y 2 ( П ) |
|
|
||||||||||||
|
|
|
|
|
|
, |
|
|||||||||||||||
|
|
|
|
|
|
|
|
|
|
|
|
|
|
|
|
|
|
|
|
|||
|
( ( ) П ( |
|
|
|
N1,3 ( ) cos y1( ) |
|
|
|
|
|||||||||||||
STfc |
П )) |
|
|
|
|
|
|
|
|
|||||||||||||
|
S |
|
( ( ) |
|
( )) |
|
N ( ) cos |
|
cos |
|
( 2 ) |
|
||||||||||
|
Tfc |
|
|
П |
|
П |
|
3,3 |
|
y3 |
|
|
y 2 |
|
|
|
|
П |
|
|||
|
|
|
|
|
|
|
|
|
|
|
|
|
|
|
||||||||
STfc ( ( ) 2 П ( П )) |
|
|
N2,3 ( ) cos y 2 cos y 2 ( П ) |
|
||||||||||||||||||
|
|
|
|
|
|
|
|
|
|
|
|
|
|
|
|
|
|
|
|
|
|
|
и т. д.
Стоит отметить, что при проведении прочностных расчетов элементов плунжерного зацепления, наиболее нагруженным будет контакт в момент пересопряжения, соответствующий (n‒1) ‒ парному зацеплению.
Предлагаемый алгоритм применялся для определения распределения сил в двухпарном зацеплении изделия ПВР-2.
Величина сил N1,2 и N2,2 на протяжении всего двухпарного зацепления, в зависимости от угла поворота волнообразователя , определяется вы-
ражением (5). Тогда величина силы, действующей на рассматриваемый плунжер, определяется выражением:
N1,2 ( ) |
|
|
|
2Tкр 2 |
|
|
|
|
|
|
|
|
|
|
|
(7) |
|
|
|
|
|
|
|
|
|
|
|
|
|
|
, |
|
|||
|
|
|
|
|
STfc ( ( )) |
|
|
|
|
|
|||||||
|
|
|
|
|
|
|
|
|
|
||||||||
|
mZK k2 cos y1( ) 1 |
|
|
|
|
|
|
|
|
|
|
|
|
|
|||
S ( ( ) |
|
( |
|
|
|
|
|
||||||||||
|
|
|
|
|
П |
П |
)) |
|
|
||||||||
|
|
|
|
|
Tfc |
|
|
|
|
|
|
|
|
|
|||
а на плунжер, следующий за ним |
|
|
|
|
|
|
|
|
|
|
|
|
|
|
|||
N2,2 ( ) N1,2 ( ) |
|
STfc ( ( )) |
|
|
cos y1( ) |
|
|
|
. |
(8) |
|||||||
STfc |
( ( ) П |
( П )) cos y 2 ( |
П ) |
|
|||||||||||||
|
|
|
|
Список литературы
1.Калабин, С.Ф. Коэффициент перекрытия плунжерной передачи / С.Ф. Калабин // Механические передачи. - Ижевск : ИМИ, 1977. - С 16-19.
2.Каракулов, М.Н. Исследование зацепления плунжерной передачи / М.Н. Каракулов // Вестник машиностроения. - 2008. - №11. - С.12-14.
3.Каракулов, М.Н. Геометро-кинематическое исследование плунжерной передачи с круговым профилем плунжера / М.Н. Каракулов // Вестник ИжГТУ. - 2009. - №1. - С.15-17.
4.Писаренко, Г.С. Справочник по сопротивлению материалов / Г.С. Писаренко. - Киев : Научная мысль, 1988. – 327 с.
136
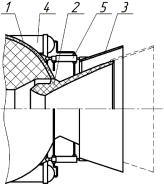
А. Н. Миронов, аспирант
А. В. Алиев, доктор физико-математических наук, профессор Ижевский государственный технический университет
имени М. Т. Калашникова
Метод оценки влияния возможных перекосов в телескопических соплах РДТТ на силу тяги
Исследование является актуальным при проектировании сверхзвуковых раздвижных сопловых блоков ракетных двигателей. Так же представляет интерес изменение структуры потока при изменении геометрии сопла.
Применение телескопических сопловых блоков обусловлено различными конструкционными и эксплуатационными требованиями к конструкции РДТТ. В частности в работе [1] указан ряд предпосылок создания телескопических сопловых блоков. Исключить влияние отрицательных факторов можно, применив телескопический сопловой блок, в соответствии со схемой на рис. 1.
Рис. 1. Вариант конструктивно-компоновочной схемы РДТТ высотной ступени с телескопическим раздвижным соплом: 1 – корпус РДТТ, 2 – неподвижная часть сопла, 3 – выдвижной насадок, 4 – газогенератор, 5 – силовой привод
Тем не менее, показанная схема имеет ряд недостатков и мест, нуждающихся в дополнительном исследовании. Например, в месте стыка неподвижной части сопла 2, жестко скрепленной с корпусом 1 и выдвижного насадка 3 необходимо обеспечить плотное прилегание частей сопла, для минимизации возможных перекосов и утечек газа через стык. Кроме того, в конструкцию двигателя необходимо ввести дополнительные элементы 4 и 5, обеспечивающие выдвижение подвижной части сопла. Возможные перекосы, в соплах с выдвижными насадками исследовались ранее экспе-
137
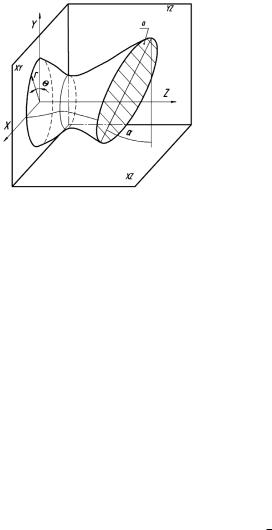
риментально и расчетами по линейной теории и численно в одномерной постановке, например в [2].
Для определения сил и моментов, возникающих при несимметричном течении газа из реактивных сопловых блоков, необходимо решить систему газодинамических уравнений в трехмерной постановке [4].
На рис. 2 представлена расчетная схема для определения действующих сил с обозначениями координатных направлений, углов, плоскостей. Схема приведена с учетом того, что сопло может быть кососрезанным.
Рис. 2. Расчетная схема для определения боковой силы
Уравнения для определения действующих сил, запишутся следующим
образом: |
|
|
Rx v2 |
pн sin dа, |
Ry v2 pн cos dа, |
а |
|
а |
|
Rz u 2 p pн dа. |
а
Особенности задачи о течении продуктов сгорания в телескопическом сопловом блоке с перекосом оси в сверхзвуковой части выражаются в задании граничных условий.
Для выполнения расчета разработано программное обеспечение основанное на решении газодинамических уравнений нестационарным методом крупных частиц [3] с модификациями и дополнениями, предложенными в [4], которые позволяют вести счет с числами Куранта близкими к единице (Ku = 0,8 ‒ 0,9).
После определения параметров газа в сопловом блоке выполняется интегрирование давления по внутренней поверхности соплового блока, что позволяет определить величину управляющей силы.
Рассчитаны боковые силы, создаваемые сопловым блоком с перекосом оси раздвижного насадка относительно оси сопла. Данные, полученные при перекосе сопла, равном шесть градусов в сечении с радиусом r 1,11 ,
138
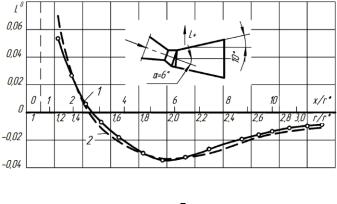
всоответствии с рис. 3, сравнивались с данными полученными в работе [2].
Втабл. 1 приведен профиль рассматриваемого соплового блока, направления обозначены в соответствии с рис. 2.
Таблица 1. Профиль телескопического соплового блока
Номер точки |
1 |
2 |
3 |
4 |
5 |
6 |
7 |
|
Расстояние в |
0 |
30 |
70 |
123 |
155 |
200 |
2211 |
|
направлении z, мм |
||||||||
|
|
|
|
|
|
|
||
Расстояние в |
225 |
200 |
182 |
174 |
177 |
185 |
552 |
|
направлении r, мм |
||||||||
|
|
|
|
|
|
|
Заданный сопловой блок при параметрах газа в камере сгорания, приведенных в табл. 2, без перекоса и смещения в месте стыка подвижных частей, развивает тягу двести сорок килоньютон.
Таблица 2. Параметры газа в камере сгорания
Наименование |
Обозначение |
Размерность |
Значение |
|
параметра |
параметра |
|||
|
|
|||
Температура в камере |
Tк |
К |
3400 |
|
сгорания |
||||
|
|
|
||
Давление в камере |
pк |
Мпа |
2,5 |
|
Показатель адиабаты |
k |
– |
1,25 |
|
Газовая постоянная |
R |
Дж/кг·К |
302 |
Ниже приведены результаты расчетов заданного соплового блока.
Рис. 3. Изменение боковой силы по длине конического сопла (ϴк=10°), при перекосе его оси в сечении r 1,11 на угол 6 . Сравнение с результатами работы [2]: 1 – эксперимент, 2 – расчет по разработанной методике
на расчетной сетке 50 2012
Из рис. 3 видно, что разработанная методика даже на грубой расчетной сетке дает удовлетворительные результаты, совпадающие с результатами
139
эксперимента в пределах нескольких процентов.
В табл. 3 представлены результаты расчета относительной боковой силы по длине соплового блока. Потери осевой составляющей силы тяги составили двадцать два процента.
Таблица 3. Результаты определения управляющих сил
Относительная длина соплового блока x/r* |
Относительная боковая сила L0 |
1,5 |
0,055 |
2,3 |
0,082 |
3,1 |
‒ 0,011 |
3,9 |
‒ 0,023 |
4,7 |
‒ 0,029 |
5,5 |
‒ 0,033 |
6,3 |
‒ 0,033 |
7,1 |
‒ 0,020 |
7,9 |
‒ 0,031 |
8,7 |
‒ 0,022 |
9,5 |
‒ 0,017 |
10,3 |
‒ 0,015 |
11,1 |
‒ 0,012 |
11,9 |
‒ 0,011 |
12,7 |
‒ 0,010 |
Предложенная методика может быть полезна при проектировании и отработке телескопических сопловых блоков ракетных двигателей. Кроме определения управляющих сил, разработанная методика позволяет оценить структуру течения, сделать выводы о режиме работы соплового блока, целесообразности конструктивных изменений, влиянии перекосов и «ступенек» в месте стыка телескопического насадка и неподвижной части сопла.
Список литературы
1.Гапаненко, В.И. Некоторые тенденции развития конструктивнокомпоновочных схем РДТТ / В.И. Гапаненко, О.С. Думин, Л.Н. Лавров, М.И. Соколовский. - Баллистические ракеты подводных лодок России: Избранные статьи :
Миасс, 1994. – 279 с.
2.Никулин, Г. З. Пространственные течения газа в соплах: Сб. Вычислительные методы и программирование (численные методы в механике сплошных сред) / Г. З. Никулин, У. Г. Пирумов, Л. В. Пчелкина, Г. С. Росляков. - М : Изд-во Моск.
ун-та, 1979.
3.Белоцерковский, О.М. Метод крупных частиц в газовой динамике. Вычислительный эксперимент. / О.М. Белоцерковский, Ю.М. Давыдов. - М. : Наука,
1982. – 392 с.
4.Липанов, А.М. Численный эксперимент в теории РДТТ / А.М. Липанов, В.П. Бобрышев, А.В. Алиев. - Екатеринбург : УИФ «Наука», 1994. – 300 с.
140
А. В. Мышкин, аспирант
О. В. Муравьев, доктор технических наук, профессор Ижевский государственный технический университет имени М. Т. Калашникова
Влияние конструктивных особенностей электромагнитноакустических преобразователей на формирование диаграмм направленности
В настоящее время ультразвуковой (УЗ) контроль в качестве методики дефектоскопии занимает одно из лидирующих положений среди прочих видов неразрушающего контроля. Основным узлом любого УЗ дефектоскопа является УЗ преобразователь, от которого в существенной мере зависит качество получаемого изображения. К одним из основных характеристик качества изображения относятся фронтальная (поперечная) разрешающая способность, а также наличие геометрических искажений, обусловленных наличием аппаратурных артефактов. Указанные характеристики определяются в основном диаграммой ДН используемого преобразователя, в частности ее шириной, наличием боковых и дополнительных лепестков. Алгоритм получения дефектограммы предполагает отсутствие эхо-сигналов в любых других направлениях, кроме направления основного лепестка диаграммы направленности (ДН). При наличии боковых лепестков значительной амплитуды, либо наличии хорошо отражающей поверхности в направлении бокового лепестка, эхо-сигналы могут восприниматься как полезные, а следовательно искажать изображение.
ЭМАП рассчитывают, как правило, в виде сплошной ленты с током, либо как цельную катушку, имеющую определенное количество витков. Такой подход не учитывает особенностей магнитного поля вблизи преобразователя, а, значит, не учитывает особенности магнитострикционных эффектов в приповерхностном слое объекта контроля от которого зависит распределение акустического поля в объеме объекта контроля.
Для учета этих эффектов на кафедре ПМКК ИжГТУ разработана модель, описывающая ЭМАП как набор отдельных проводников, имеющих свои линейные размеры и учитывающая зазор между ними.
Конструктивно рассчитываемый преобразователь представляет собой печатную плату с вытравленными дорожками–индукторами.
Данный преобразователь имеет следующие параметры: число дорожек
– 6, размер активной апертуры – 13×15 мм.
Такой преобразователь прост в изготовлении и расчетах, что позволит легко рассмотреть математическую модель на его примере.
Из [1] следует, что поле такой решетки можно найти из выражения:
141
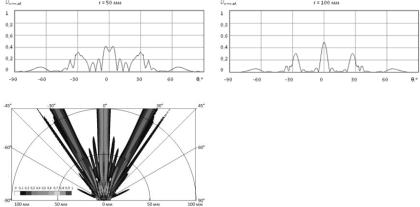
|
N |
1 |
n |
|
E |
|
|||
|
Af |
( , )cos t kr |
||
|
n 1 |
|
|
|
где A – постоянный (амплитудный) множитель, не зависящий от углов Θ, θ; f1(ϴ, θ) – диаграмма направленности эквивалентного излучателя в решетке, которая одинакова для всех излучателей [3]; k – волновое число; rn – расстояние от n–го излучателя до точки наблюдения.
В связи с тем, что диапазон рабочих расстояний промышленных сканеров может лежать либо в ближней зоне, либо близко к ее границе, применена формула прямого сложения колебаний единичных излучателей. Кроме того, сделан шаг для учета небольших расстояний прозвучивания – введен угол направления излучения единичного элемента в рассчитываемую точку пространства с целью учесть его ДН при сложении на малых расстояниях:
|
N 1 |
|
|
||
|
sin |
|
|
n |
p |
|
|
||||
arctan |
2 |
|
|
||
cos |
|
|
|||
|
|
|
где N – общее число единичных элементов решетки; n – условный номер единичного элемента; p – расстояние между соседними элементами – параметр решетки.
Результаты исследований
Расчет поля преобразователя был выполнен в программной среде MathCAD (рис. 1). Параметры при которых рассчитывался данный преобразователь: частота f = 2,8 МГц, высота индуктора над поверхностью ОК (толщина протектора) h = 0,2 мм, ширина единичного элемента a = 0,25 мм, зазор между элементами d = 2,3 мм.
а |
б |
Рис. 1. Поле преобразователя:
а – ДН на расстоянии 50 мм от центра излучателя;
б – ДН на расстоянии 100 мм от центра излучателя;
в – распределение поля в пространстве перед излучателем.
в
ЭМА преобразователь вплотную приложенный к объекту контроля об-
142
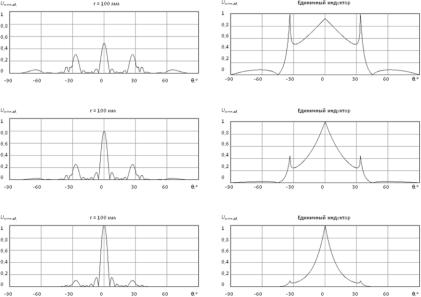
ладает наибольшей эффективностью преобразования магнитного поля в ультразвуковое. Однако близкое расположение имеет свои минусы – диаграмма направленности становится очень широкой и обладает большим количеством боковых и дополнительных лепестков.
Интересна также зависимость поля преобразователя и единичного элемента от толщины протектора (рис. 2).
а |
б |
в |
г |
д |
е |
Рис. 2. ДН преобразователя и единичных индукторов в зависимости от толщины протектора: а, б – толщина протектора 0,2 мм; в, г – толщина протектора 0,5 мм; д, е – толщина протектора 1 мм (масштаб Uотн.ед. для графиков не совпадает)
Анализ расчетов показывает, что отдаление индуктора от поверхности объекта контроля ведет к сильному снижению амплитуды дополнительных лепестков относительно основного лепестка. Этот эффект справедлив и для единичных индукторов и для преобразователя в целом. Однако при отдалении индуктора от поверхности ОК снижается энергия магнитного поля, что ведет в конечном итоге к уменьшению амплитуды ультразвуковой волны.
Для проверки результатов расчетов на кафедре ПМКК был поставлен опыт с расчетным преобразователем. По результатам опыта модель подтвердилась удовлетворительно – влияние дополнительных лепестков было обнаружено. Однако для более точных количественных оценок амплитуды этих лепестков и диаграммы направленности в целом планируется серия опытов с большим количеством преобразователей.
143
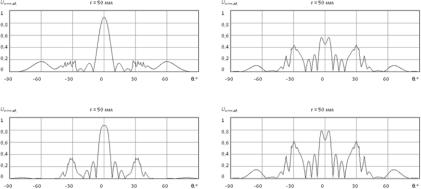
Влияние величины зазора между элементами, рабочей частоты преобразователя и ширины единичного элемента также было исследовано математически. По результатам этих исследований можно сделать следующие выводы (рис. 3):
–увеличение рабочей частоты ведет к сужению ДН в целом и к сближению дополнительных лепестков с основным;
–увеличение зазора и уменьшение ширины единичного элемента при неизменной апертуре увеличивает амплитуду дополнительных лепестков.
а |
б |
в |
г |
Рис. 3. Зависимость ДН от рабочей частоты (а, б) и зазора (в, г). Расчетный датчик (графики в одном масштабе): а – с рабочей частотой 1,5 МГц;
б – с рабочей частотой 2,8 МГц; Расчетный датчик на частоте 2,8 МГц (графики в одном масштабе): в – с зазором
0,8 мм и шириной элемента 1,5 мм; г – с зазором 2,3 мм и шириной элемента 0,25 мм.
Работа выполнена в соответствии с разделом 2 мероприятий Программы стратегического развития ФГБОУ ВПО «ИжГТУ имени М.Т. Калашникова» на 2012-2016 гг. (проект ПСР/М2/Н2.5/МВВ).
Список литературы
1.Воскресенский, Д.И. Антенны и устройства СВЧ. Проектирование фазированных антенных решеток. / Д.И. Воскресенский. - М. : Радио и связь, 1994. – 592 с.
2.Бобров, С.В. Диаграммы направленности прямых ЭМАП для возбуждения сдвиговых волн с горизонтальной поляризацией / С.В. Бобров // Контроль. Диагностика. - 2012. - №8. - С. 21-26.
3.Буденков, Г.А. Динамические задачи теории упругости. В приложении к проблемам акустического контроля и диагностики / Г.А. Буденков, О.В. Недзвецкая. - М. : Физматлит, 2004. – 135 с.
144
Н. А. Назаров, студент
Л. А. Галаган, доктор технических наук, профессор Ижевский государственный технический университет имени М. Т. Калашникова
Дополнение оснастки к газобаллонному оружию для стрельбы при отрицательной температуре окружающей среды
Разработка затрагивает проблему с эксплуатацией пневматического газобаллонного оружия при отрицательной температуре окружающей среды и содержит предложение по решению данной проблемы.
Газобаллонное оружие – это вид пневматического оружия, в котором в качестве источника энергии используются сменные баллончики со сжиженным газом. Наибольшее распространение получили 12-граммовые баллончики с углекислым газом СО2.
Основное преимущество газобаллонного оружия перед другими видами пневматического оружия состоит в том, что при эксплуатации не требуется приложения мускульной силы для перезаряжания.
Однако использование в качестве источника энергии баллончиков со сжиженным газом обусловливает существенное ограничение на температуру окружающей среды, при которой возможна эффективная эксплуатация данного вида пневматического оружия. Как правило, диапазон температур эксплуатации представляет собой интервал (+10…+30) °С (например, [1]). При более низких значениях температуры окружающей среды наблюдается понижение давления газа в баллончике, что приводит к снижению дульной скорости метаемого элемента (пули) и ухудшению эффективности стрельбы.
Один из возможных путей расширения диапазона температур (в сторону отрицательных значений), при которых возможна эффективная эксплуатация газобаллонного оружия, – это принудительное поддержание определенного значения температуры газа, лежащего в диапазоне допустимых температур.
Поддержание определенного значения температуры газа возможно, например, за счет применения нагревательного элемента, присоединяемого к баллончику с газом.
Рассмотрим возможность создания одноразового нагревательного элемента с химическим принципом действия.
Количество теплоты Qн , которое необходимо сообщить баллончику с
газом для изменения температуры на t градусов, равно |
|
Qн сб mб cг mг t , |
(1) |
где cб , cг – удельные массовые теплоемкости, mб , mг |
– массы материала |
баллончика и находящегося в нем газа соответственно. |
|
145 |
|

Для стального баллончика, содержащего 12 г углекислого газа, используя данные из [2], получим Qн 1,05 кДж для нагревания от температуры 20C до температуры 20 C ( t 40 C ).
Запишем уравнение химической реакции, которая может быть применена в нагревательном элементе:
3CuCl2 2 Al 2 AlCl3 3Cu 789,6 кДж .
Исходя из молярной пропорции реагирующих веществ и данных, приведенных в [3], определяется тепловой выход реакции в пересчете на 1 г основного реагента. Для записанной реакции этот показатель составляет 1,96 кДж на 1 г хлорной меди CuCl2 .
Таким образом, для однократного нагревания 12-граммового баллончика с углекислым газом и поддержания температуры на протяжении 2030 минут должно быть достаточно нескольких граммов хлорной меди (необходим запас на рассеивание теплоты в окружающую среду и нагревание частей самого нагревательного элемента). Конкретные значения масс реагентов подлежат уточнению.
Рис. 1. Конструкция одноразового химического нагревательного элемента
Предлагаемая конструкция одноразового химического нагревательного элемента показана на рис. 1. Нагревательный элемент представляет собой полый цилиндрический трубчатый корпус 1, изготовленный из полимерного материала (например, полиэтилентерефталата, ПЭТФ), разделенный разрушаемой перегородкой 3 на две замкнутые полости. В верхнюю полость залит растворитель 2 на водной основе, имеющий температуру замерзания ниже 30C . На дно нижней полости помещено разомкнутое спиральное кольцо 5 из алюминиевой проволоки, а свободное пространство заполнено смесью 4 хлорной меди и деревянных опилок,
146
накапливающих теплоту и замедляющих протекание реакции.
Для приведения в действие нагревательного элемента достаточно нанести энергичный удар по верхней части корпуса с целью разрушения перегородки. Химическая реакция будет протекать необратимо до исчерпания одного из реагентов.
Подбор величины теплового выхода при конструировании нагревательного элемента с данной конструкцией осуществляется назначением масс реагирующих веществ. Регулирование тепловой мощности нагревания по времени может быть обеспечено варьированием диаметра алюминиевой проволоки, а также покрытием части наружной поверхности проволоки составом (например, слоем краски), стойким к протекающей реакции. В процессе протекания реакции площадь поверхности соприкосновения веществ будет изменяться (в основном, уменьшаться), что приведет к изменению скорости протекания реакции и интенсивности выделения теплоты в единицу времени.
Предлагаемый нагревательный элемент позволит расширить диапазон температур эффективной эксплуатации газобаллонного оружия, что должно способствовать повышению интереса к данному виду пневматического оружия.
Список литературы
1.Пистолет пневматический газобаллонный спортивный МР-661К «Дрозд».
Паспорт МР-661К.776325.012 ПС.
2.Субботина, Е.П. Сборник физических констант и параметров: справ. для студ. хим. и др. естеств. фак. ун-тов / Е.П. Субботина. - Л. : Изд-во ЛГУ, 1967. – 148 с.
3.Кибенко, В.Д. Справочные таблицы по курсу химии / В.Д. Кибенко. - Ижевск : ИжГТУ, 2004. – 36 с.
С. Д. Неулыбин, студент; Д. С. Белинин, аспирант;
П. С. Кучев, аспирант Ю. Д. Щицын, доктор технических наук, профессор
Пермский национальный исследовательский политехнический университет
Закалка тяжелонагруженных изделий на токе прямой полярности
Для повышения работоспособности деталей и изделий в настоящее время основным способом упрочнения является объемная термическая обработка. При назначении оптимальных режимов закалки и отпуска достигаются стандартные значения эксплуатационных свойств изделий из инструментальных сталей и сплавов. Однако практически всегда термообработка на максимальную твердость и износостойкость приводит к рез-
147
кому снижению вязкости и, в связи с этим, к преждевременному выходу узла из строя по причине хрупких разрушений.
Повышение эксплуатационных свойств инструментальных материалов возможно также при использовании способов поверхностного упрочненияиндукционной закалки, химико-термической обработки, нанесения покрытий.
Качественно новый уровень эксплуатационных свойств инструментальных материалов достигается при обработке высококонцентрированным источником энергии – плазменной дугой прямого действия.
Технологический процесс плазменного поверхностного упрочнения изделий в общем случае включает следующие операции:
1) подготовка изделия к упрочнению; 2) плазменное упрочнение; 3) контроль качества упрочнения (замеры твердости, механические испытания, металлографические исследования образцов – свидетелей); 4) окончательная термическая или механическая обработка.
Накопленный опыт по практическому применению плазменного поверхностного упрочнения позволяет выделить следующие традиционные варианты: упрочнение без оплавления и с оплавлением поверхности детали, упрочнение с зазором между упрочненными зонами (ЗТВ), без перекрытия ЗТВ и с перекрытием ЗТВ; химико-термическая плазменная обработка, упрочнение в сочетании с другими способами объемной или поверхностной термической обработки.
Вданной работе исследовали некоторые нетрадиционные (комбинированные) варианты плазменного поверхностного упрочнения применительно к сталям мартенситного класса типа 40Х13, с целью получения слоев с уникальными характеристиками. Были выбраны следующие варианты: 1) закалка с оплавлением поверхности без зазора и перекрытия ЗТВ
споследующим переплавом обработанной поверхности на более жестком режиме; 2) закалка с оплавленим поверхности и с зазором между ЗТВ с последующим повторным проходом без плавления в зазоре между ЗТВ; 3) закалка с оплавлением поверхности без перекрытия и без зазора ЗТВ и последующим повторным проходом без плавления по обработанной поверхности.
Врезультате проведенной работы были опробованы все три предложенных варианта.
Проведя металлографическое исследование и замеры микротвердости полученных образцов установили следующее:
Для образца полученного по 1 варианту (рис. 1): Глубина упрочненного слоя составляет 6,0мм, ширина прохода 12‒14мм, усиление около 1,0мм., в центральной части закаленных полос у поверхности наблюдается наличие мелких усадочных рыхлот (рис. 1). Растрескиваний, несплавлений, пор в обработанной зоне нет. Структура основного материала образца представляет собой феррито-карбидную смесь (рис. 1). Структура характерна для данного материала в состоянии после отжига либо высо-
148
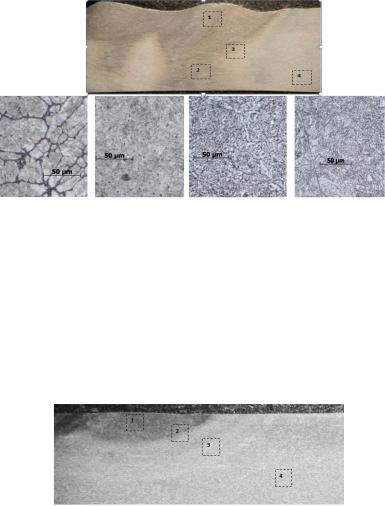
кого отпуска. Структура закристаллизовавшейся сварочной ванны представляет собой структуру мартенситного типа с выделениями карбидной сетки в осях дендритов (рис. 1). В ЗТВ структура от мартенсита (у границы сплавления и в зоне высокотемпературного нагрева под сварочной ванной) с переходом к структуре мартенситного типа с выделениями карбидов и феррито-карбидной смеси в зоне перехода к основному материалу.
Рис. 1. Вид макро и микроструктуры образца № 1
Для образца, полученного по 2-му варианту (рис. 2): усиления нет, ширина прохода 5–7 мм, глубина проплавления 1,4–2 мм.
Структура основного материала аналогична образцу № 1. Структура закристаллизовавшейся зоны представляет собой структуру бейнитного типа с включениями свободного феррита и выделениями карбидной фазы по границам кристаллитов. На границе сплавления структура бейнитного типа с мелкими включениями свободного феррита. В зоне повторного прохода – структуры мартенсита отпуска с плавным переходом к структуре основы.
Вид макрошлифа приведен на рис. 2.
а)
149

б)
Рис. 2. Вид макро- (а) и микроструктуры (б) образца № 2.
Для образца, полученного по 3 варианту (рис. 3): усиление составляет менее 0,1 мм, ширина прохода 7,5…9 мм, глубина проплавления 2,1…3,3мм.
Структура основного материала аналогична образцам №№ 1, 2. Структуры бейнитного типа наблюдаются в приповерхностной зоне закаленной дорожки (очевидно, в дорожке повторного прохода) и в шве первого прохода (рис.3). Структура остальной части закаленной дорожки второго прохода мартенситного типа с выделениями карбидов по границам первичного зерна и участками выделений феррита. В зоне переходной зоне – структура мартенсита отпуска с плавным переходом к структуре основы.
а)
б)
Рис. 3. Вид макро- (а) и микроструктуры (б) образца № 3.
Значения микротвердости основных зон упрочненных слоев представ-
150
лены в табл. 1.
Таблица 1. Значения микротвердости основных зон упрочненных слоев
№ образца |
Микротвердость по зонам, Нμ50, кгс/мм2 |
|
|||
|
Зона оплав- |
Зона закалки |
Переходная |
|
Основной |
|
ления |
из твердой |
зона |
|
материал |
|
|
фазы |
|
|
|
1 |
Центральная |
488 |
426…486 |
|
201…207 |
|
зона шва |
|
|
|
|
|
310…506, |
|
|
|
|
|
остальная |
|
|
|
|
|
часть |
|
|
|
|
|
535…715 |
|
|
|
|
2 |
413…489 |
358…484 |
206…415 |
|
209…225 |
3 |
432…507 |
411…468 |
187…468 |
|
187…193 |
Исходя из анализа микротвердости можно сделать вывод о том, что твердость в обработанной зоне гораздо выше твердости основного материала. Однако в случаях повторного прохода (повторного нагрева) происходит незначительное разупрочнение центральной приповерхностной области обработанной зоны. В остальном же распределение значений микротвердости равномерное с плавным переходом к значениям твердости основного металла.
1.Применение комбинированных способов плазменной поверхностной закалки на токе прямой полярности позволяет получать упрочненные слои глубиной около 8 мм. с равномерно распределенными по сечению прочностными свойствами.
2.Значения твердости упрочненных зон возрастают в 2-3 и более раза в зависимости от способа обработки.
3.Наличие бейнитной структуры в результате некоторых вариантов обработки сдерживает применения такой технологии к деталям работающим в условиях динамического и циклического нагружения из-за высокой хрупкости бейнитной структуры.
Список литературы
1. Щицын, Ю.Д. Плазменные технологии в сварочном производстве: Учеб. пособие для магистров. Ч.1. / Ю.Д. Щицын. - Пермь : Перм. гос. техн. ун-т., 2004.
– 73 с.
151
Г. М. Нурисламова, А. Б. Коленченко,
О. В. Коленченко, старший преподаватель Уфимский государственный авиационный технический университет
Расчет и обеспечение технологических условий обработки сложнопрофильных деталей газотурбинного двигателя
Проблемы повышения эффективности производства сложнопрофильных деталей газотурбинного двигателя (валов, дисков, лопаток и др.) неразрывно связны с рациональным использованием автоматизированного оборудования с ЧПУ с повышенными технологическими возможностями.
Эффективная эксплуатация такого оборудования возможна на базе широкого внедрения научно обоснованных моделей процессов механической обработки. Применение ранее разработанных нормативов по выбору технологических условий выполнения, как отдельных операций, так и всего технологического процесса механической обработки не позволяет обеспечить эффективное применение такого оборудования и стабилизировать погрешность обработки, глубину и степень наклепа, шероховатость при изготовлении сложнофасонных деталей.
Особенности мелкосерийного производства, необходимость сокращения времени подготовки его с одной стороны, и ужесточение требований к качеству и надежности изготавливаемых деталей, с другой, предопределяют более эффективное использование достижений теоретических наук, экспериментальных исследований, возможностей современного математического аппарата и средств вычислительной техники.
Теоретические и экспериментальные исследования, а также производственный опыт показывают, что у технологов на этапе технологической подготовки производства имеется большой арсенал средств и методов оптимального управления механической обработкой [1], в том числе определения режимов резания, обеспечивающих на основе теоретических зависимостей точность, характеристики качества, производительность и себестоимость обработки, а также возможность управления процессом резания.
Процесс лезвийной обработки сопровождается достаточно сложными по своей природе физическими явлениями, математическое описание которых представляет собой довольно трудную задачу [1].
Однако, назначение технологических условий выполнения операций механической обработки лезвийном инструментом, обеспечивающих необходимое качество обработанной поверхности и эффективность выполнения операции, возможно лишь на основе либо теоретических, либо тео- ретико-экспериментальных зависимостях между основными технологическими параметрами, характеризующими процесс резания (режимы обработки, геометрия инструмента, свойства материала и т. п.) и параметрами качества поверхностного слоя, точности, себестоимости и производитель-
152
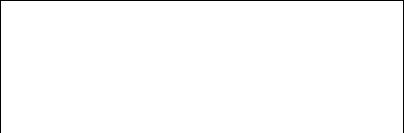
ности обработки, т. е. на основе комплексных математических моделей [2]. В общем случае структура модели должна включать в себя уравнения и неравенства, определяющие область допустимых значений независимых переменных и требования на верхние и нижние границы изменения характеристик функциональной системы – технологические ограничения.
На основе этого алгоритма при заданных технологических условиях обработки (V, S, t, δ и т. д.) может быть определен и с помощью автоматизированной системы управления обеспечен любой из требуемых показателей, характеризующих условия выполнения технологической операции, т. е.
T f V ,S ,t,δ,rв ; Ra f V ,S ,t,δ,rв ;
N% f V ,S ,t,δ,rв ; hc f V ,S ,t,δ,rв ;f V ,S ,t,δ,rв ; СТ f V ,S ,t,δ,rв ; ПТ f V ,S ,t,δ,rв .
Подставив конкретное значение требуемого параметра в целевую функцию, можно получить аналитическую зависимость целевой функции от входных переменных или определить характер их изменения с целью обеспечения заданного уровня выходных параметров. Расчет режимов механической обработки и управление процессом является весьма актуальным и эффективным при изготовлении сложнопрофильных ответственных деталей газотурбинного двигателя. В работе показана целесообразность применения комплексной математической модели для выбора режимов резания при чистовой обработке вала среднего из титанового сплава ВТ9 резцом фирмы SANDVIK ТК20 геометрии SNMP.
На основании анализа литературных данных и производственных условий чистовой обработки титановых сплавов твердосплавным инструментом был выбран диапазон изменения независимых переменных (V, S, t, δ) для разработки комплексной математической модели. Скорость резания изменялась от 100 до 130 м/мин, подача – от 0,05 до 0,25 мм/об, глубина – от 0,3 до 1 мм и угол резания – от 86 до 91 град. Общий вид математических зависимостей, входящих в модель чистового точения титанового сплава ВТ9 резцом ТК20, и коэффициент регрессии представлены в таблице.
Таблица. Модель обрабатываемости
lnY C0 C1 lnV C2 lnS C3 lnt C4 lnδ
Выходные параметры |
С0 |
С1 |
С2 |
С3 |
С4 |
Т, мин |
6,42 |
‒ 3,87 |
‒ 2,01 |
‒ 0,99 |
2,14 |
СТ, руб. |
3,16 |
0,73 |
0,07 |
0,31 |
‒ 0,39 |
ПТ, мин-1 |
‒ 2,37 |
0,22 |
0,23 |
0,001 |
0,004 |
Ra,мкм |
2,30 |
‒ 0,21 |
0,78 |
0,15 |
0,31 |
и, мкм |
1,6 |
0,25 |
‒ 0,031 |
0,036 |
0,12 |
N, % |
4,84 |
‒ 0,136 |
0,61 |
0,48 |
‒ 0,022 |
hc, мкм |
18,84 |
‒ 2,23 |
0,68 |
0,75 |
‒ 0,91 |
153
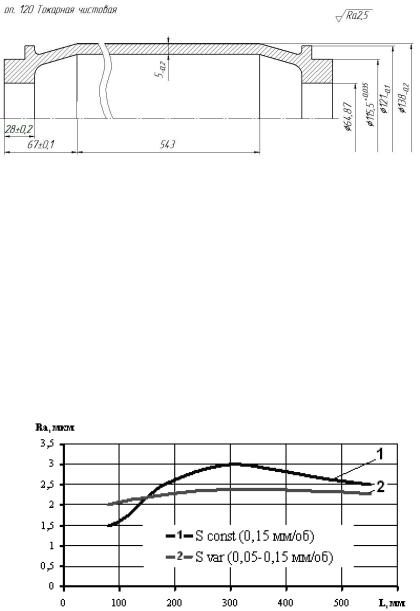
Общий вид обрабатываемой детали представлен на рис. 1.
Рис. 1. Вал средний
Расчет режимов резания выполнялся для обработки цилиндрической поверхности протяженностью 543 мм и диаметром 138 мм. Конструкция детали предполагает малую и переменную жесткость системы СПИЗ при выполнении этой операции, поэтому при приложении постоянной силы резания в различных поперечных сечениях обрабатываемой заготовки неизбежно будут возникать различные деформации, приводящие к формированию переменных характеристик качества обработанной поверхности (рис. 2 и рис. 3, зависимости 1).
Разработанная система расчета режимов резания и управления процессом механической обработки на основе комплексной математической модели позволяет обеспечить и стабилизировать требуемые показатели качества поверхностного слоя детали.
Стабилизация температурно-силовых условий формирования поверхностного слоя в данном случае проводилась за счет изменения величины подачи при постоянстве значений остальных параметров, характеризующих технологические условия выполнения операции. Полученные результаты показывают (рис. 2 и рис. 3):
Рис. 2. Шероховатость обработанной поверхности по длине детали
V = 120 м/мин; t = 0,5 мм; δ = 90°
154

‒при обработке на постоянной подаче S = 0,15мм/об шероховатость изменяется по длине вала от Ra = 1,5 мкм до Ra = 3,1 мкм (на 50 %), степень упрочнения от 16 % до 25 % (36 %);
‒обработка на переменной подаче S = 0,05‒ 0,15мм/об позволяет повысить эффективность процесса за счет обеспечения более стабильной шероховатости (Ra изменяется от 2,0 до 2,4 мкм (16 %)), и степени упрочнения материала поверхностного слоя (от 18 до 20 % (10 %)).
Рис. 3. Степень наклепа по длине обработанной поверхности V = 120 м/мин; t = 0,5 мм; δ = 90°
Таким образом, расчет режимов механической обработки, выполненный на основе комплексной математической модели, и применение системы управления процессом резания позволяет обеспечить достаточно стабильные показатели качества поверхности при изготовлении сложнопрофильных деталей современных машин.
Список литературы
1.Безъязычный, В.Ф. Метод подобия в технологии машиностроения / В.Ф. Безъязычный. - М.: Машиностроение, 2012. – 320 с.
2.Коленченко, О.В. Исследование влияния условий фрезерования на величину деформаций и характеристики качества обработанной поверхности (на примере лопаток компрессора ГТД) / О.В. Коленченко // СТИН. - 2010. - №5. - С. 32-36.
155
В. М. Осокин, аспирант
А. Ф. Сальников, доктор технических наук, профессор Е. Н. Петрова, кандидат технических наук, доцент Пермский национальный исследовательский политехнический университет
Исследование параметров воздушного потока в сопле при взаимодействии с выдвигающимся цилиндром
При воздействии двухфазных продуктов сгорания ракетного двигателя на выдвигающийся цилиндр, являющийся элементом конструкции сопла изменяемой геометрии, возникает газодинамическая сила, состоящая из двух составляющих: силы газодинамического трения и силы за счет передачи части импульса конденсированных частиц при их взаимодействии со стенкой цилиндра.
Расчет обеих этих составляющих представляет значительные трудности. В особенности это касается силы от конденсированных частиц. В связи с этим актуальной задачей является проведение расчетноэкспериментальных исследований газодинамической силы возникающаяся на выдвижном цилиндре (ВЦ).
Математическая постановка
Опираясь на метод крупных частиц [2] при решении газодинамических задач по формированию газового потока, разработан алгоритм, базирующийся на двухмерной модели течения многофазной газовой смеси [3, 4] в сверхзвуковом диффузоре и в следе свободной струи сопла. Данный алгоритм универсален и позволяет включать различные модификации с учетом реальных физических процессов (коагуляция, дробление, прилипание к стенке сопла), которые существенно усложняют физическую картину течения, приближая его к условиям физического моделирования.
Математическая модель базируется на основе уравнений НавьеСтокса, ранее описанных в статье [1] и дополняется:
‒ уравнением состояния; ‒ уравнением межфазового взаимодействия;
‒ газодинамической силой, возникающая на ВЦ.
Газодинамическая сила Fгд состоит из двух составляющих: силы газодинамического трения Fтр и силы за счет передачи части импульса конденсированных частиц при их взаимодействии со стенкой цилиндра Fконд.
Fтр lц c f i 1 i u1 i 2 h ,
i 0
где 1 – плотность газа; u1 – скорость газа; h – длина ВЦ; c f ‒ коэффици-
ент трения является функцией двух величин: числа Рейнольдса и относительной шероховатости и может определяться по формуле:
156
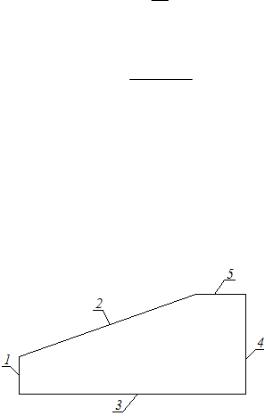
|
|
|
|
68 |
0,25 |
c f |
|
|
|||
0,11 |
|
. |
|||
|
d |
|
Re |
|
|
Для конденсированных частиц импульс pi mi |
за время |
количеством столкновений частиц с ВЦ. |
||||||
|
lц |
m |
u |
2 |
|
|
|
|
Fконд k2 |
2 |
i |
|
i |
ni , |
|
|
|
|
|
|
|
||
|
i 0 |
|
i |
|
|
|
|
|
|
|
|
|
|
ui
, передаваемый ВЦ
где kт – коэффициент трения конденсированной частицы о ВЦ; mm – масса конденсированной частицы; um– скорость конденсированной фазы; n – количество столкновений частиц с ВЦ.
lц |
|
lц |
m2 i u2 i |
|
|
Fгд c f i |
1 i u1 i |
2 h k2 |
ni Fтр Fконд . |
||
|
|||||
i 0 |
|
i 0 |
i |
Движение фаз рассматривается как движение взаимопроникающих и взаимодействующих сред, которое осуществляется в осесимметричном диффузоре сопла [5]. При этом считается, что течение двумерное, все параметры зависят от координат z, r и времени t [6].
Решаемая задача состоит из расчетной области сопла:
1 – критическое сечение сопла, 2 – стенка сопла, 3 – ось симметрии, 4 – срез сопла, 5 – стенка ВЦ
Также при постановке начальных и граничных условий были приняты следующие допущения:
–все расчетные модели – осесимметричны;
–не учитывается условия коагуляции, дробления и прилипания к стенке;
–k-фаза рассматривается как твердая частица;
–при формировании фракций к-фазы на входе в критическое сечение сопла принимается нормальный закон распределения.
Граничные условия задаются в зависимости от вида границы, ранее указанных в статье [1].
Практическая реализация математической модели Опираясь на принятую математическую модель, был доработан алго-
ритм для расчета параметров газового потока, ранее описанный в статье
[1].Расчет проводится с применением метода крупных частиц и состоит
157
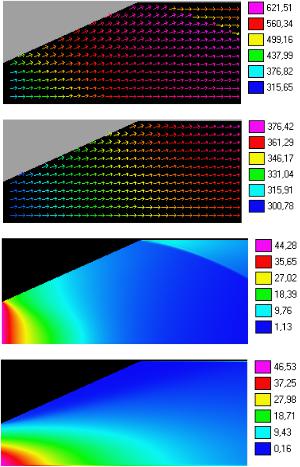
из основных трех этапов: эйлеров, лагранжев и заключительный.
На основе параметров (таблица) проведен расчет параметров газового потоки и газодинамической силы, возникающей на выдвижном целиндре раструба сопла с выдвижением 46 мм.
Таблица. Расчетные параметры
Параметры |
Значение |
Коэффициент адиабаты |
1,4 |
Газовая постоянная, Дж/(кгК) |
283 |
Коэффициент динамической вязкости, кг/(мс) |
1,79∙10-5 |
Давление в камере, МПа |
6,1 |
Температура в камере, К |
263 |
Количество ячеек вдоль оси |
300 |
Рис. 1. Расчетные значения скорости газа в раструбе сопла
Рис. 2. Расчетные значения скорости k-фазы в раструбе сопла
Рис. 3. Расчетные значения плотности газа в раструбе сопла
Рис. 4. Расчетные значения плотности k-фазы в раструбе сопла
158
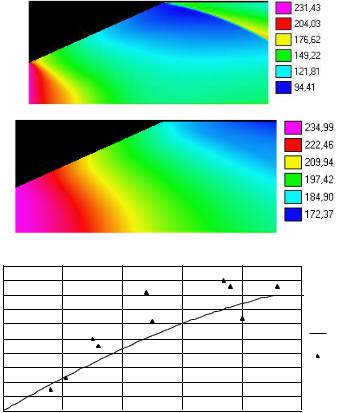
Рис. 5. Расчетные значения температуры газа в раструбе сопла
|
Рис. 6. Расчетные значения температуры k-фазы в раструбе сопла |
|||||
F, Н |
|
|
|
|
|
|
10 |
|
|
|
|
|
|
9 |
|
|
|
|
|
|
8 |
|
|
|
|
|
|
7 |
|
|
|
|
|
|
6 |
|
|
|
|
|
|
5 |
|
|
|
|
|
Расчет |
|
|
|
|
|
|
|
4 |
|
|
|
|
|
Эксперимент |
|
|
|
|
|
|
|
3 |
|
|
|
|
|
|
2 |
|
|
|
|
|
|
1 |
|
|
|
|
|
|
0 |
|
|
|
|
|
|
0 |
0,01 |
0,02 |
0,03 |
0,04 |
0,05 |
х, м |
|
Рис. 7. Расчетные значения газодинамической силы на ВЦ |
Полученные значения газодинамической силы, возникающей на ВЦ в зависимости от степени его выдвижения в поток, были верифецированны с результатами натурных лабораторных исследований проводимые на воздухе. Проведенный сравнительный анализ показал удовлетворительно согласующиеся результаты расчетных значений с результатами экспериментальных исследований.
Список литературы
1.Осокин, В.М. Моделирование распределения к-фазы в сверхзвуковой части сопла ракетного двигателя / В.М. Осокин, Е.Н. Петрова, А.Ф. Сальников . - М : Машиностроение, 2011.
2.Белоцерковский, М.Ю. Метод крупных частиц в газовой динамике / М.Ю. Белоцерковский, Ю.М. Давыдов . - М : Наука, 1980. - 488.
3.Стернин, Л.Е. Многофазные течения газа с частицами / Л.Е. Стернин, А.А. Шрайбер . - М : Машиностроение, 1994. - 320.
159
4.Стернин, Л.Е. Двухфазные моно- и полидисперсные течения газа с частицами / Л.Е. Стернин. - М : Машиностроение, 1980.
5.Пирумов, У.Г. Течения газа в соплах / У.Г. Пирумов, Г.С. Росляков. - М : Изд-во Моск.ун-та, 1978. - 288.
6.Сальников, А.Ф. Анализ численного моделирования течения в осесимметричном канале со вдувом с боковой поверхности. / А.Ф. Сальников // Метод крупных частиц: теория и приложение. - M : ВИМИ, 1987. - Т. 2. - 114-120.
Р. А. Петров, аспирант
Б. Я. Бендерский, доктор технических наук, профессор Ижевский государственный технический университет имени М. Т. Калашникова
Моделирование пространственных процессов вентиляции салона автобуса
Исследования вентиляции салонов автотранспорта в настоящее время, в основном, базируются на экспериментах и дорожных испытаниях, а имеющиеся интегральные методы расчета позволяют определять лишь осредненные параметры воздушного потока, но не дают полного представления о его структуре [3], [4].
Втаких условиях численное моделирование пространственных процессов вентиляции салонов транспортных средств с использованием систем инженерного анализа является актуальным методом исследования.
Вкачестве объекта исследования выбран салон автобуса модели ПАЗ3205. На основе имеющегося двумерного чертежа, создана твердотельная модель автобуса. В силу сложности создания точной геометрической модели, при ее построении приняты следующие упрощения:
‒ отсутствуют пассажиры; ‒ сиденья выполнены схематично; ‒ отсутствуют поручни;
‒ в геометрии деталей отсутствует большинство скруглений.
При решении задачи о вентиляции необходимо рассматривать совместно задачи внешней и внутренней аэродинамика автобуса. В силу значительной сложности и ресурсоемкости такой постановки задачи, было принято решение от нее отказаться.
На основании предварительного анализа выполнена упрощенная модель, в которой реализуется неполное обтекание автобуса. Расчетная область представлена на рис. 1.
Воздух, обтекая корпус автобуса, попадает в салон через люки, окна, и дефлекторы на приборной панели. Рассматривается эксплуатация автобуса в теплое время. Температура окружающего воздуха 20 °С. В рассматриваемой модели автобуса двигатель расположен внутри салона, и тепло-
160
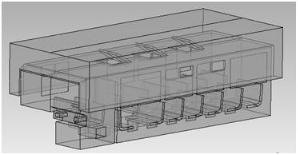
та, выделяющаяся при его работе, поступает в пассажирский салон. Также следует учесть тепловыделение пассажиров. Исходя из этого, в салоне задана температура 27 °С.
При решении задачи приняты следующие допущения:
‒скоростной режим внутри расчетной области не зависит от времени;
‒течение является однофазным;
‒внешние границы расчетной области непроницаемы, кроме входных
ивыходных сечений;
‒теплообмен стенок с внешней средой отсутствует;
‒движение воздуха рассматривается, как турбулентное движение несжимаемой среды
Рис. 1. Расчетная область
Для расчета турбулентных пространственных потоков использованы уравнения Навье-Стокса осредненные по Рейнольдсу. Для замыкания системы уравнений используется модель турбулентности SST [5].
Проведено параметрическое исследование влияния скорости движения автобуса и количества открытых вентиляционных проемов на гидродинамические параметры в салоне. Расчеты проведены при трех различных скоростях движения (20 км/ч, 40 км/ч, 60 км/ч) и для трех конфигураций вентиляционных проемов (окна закрыты, открыто 2 окна, открыты все 5 окон). Люки на крыше автобуса во всех случаях оставлены открытыми.
Общая структура потока в салоне при различных скоростях движения автобуса приблизительно идентична. Поэтому рассмотрим поведение потока в салоне только при одной скорости движения автобуса 40 км/ч.
Воздух проникает в салон через люки, движется вдоль крыши до заднего стекла, постепенно замедляясь, и растекается. Скорость воздуха перед натеканием на стекло, в зависимости от начальной скорости движения воздушного потока, уменьшается в 3,5‒4 раза.
Поток частично покидает салон через вентиляционное отверстие на задней стенке, движется вдоль пола со скоростью 3‒5 м/с, поднимается и выходит через окна. Окна работают как вытяжные отверстия, что показано на рис. 2. Это обусловлено возникающим перепадом давления в салоне
161
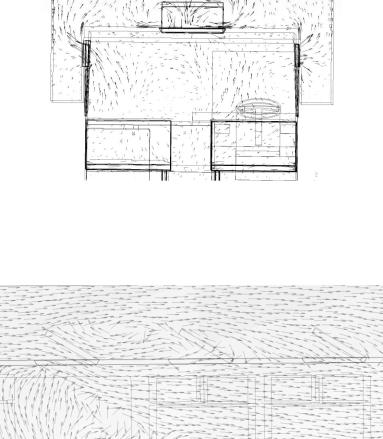
и снаружи.
Рис. 2. Структура потока в области окон
Основная часть воздуха поступает в салон через передний люк. Это вызвано структурой течения в области люков, представленной на рис.3. При обтекании крышки первого люка образуется циркуляционная зона, препятствующая поступлению воздуха в средний и задний люк.
Рис. 3. Структура потока в области люков
При движении с закрытыми окнами воздух проникает в салон через передний люк. Часть воздуха сразу же вытекает через средний и задний люки. Поток движется вдоль крыши до задней стенки. Далее поток разделяется на две части: одна покидает салон через вентиляционное отверстие, вторая – растекается вдоль пола со скоростью 2‒4 м/с, поднимается и выходит через люки.
При двух открытых окнах поведение потока подобно случаю с пятью окнами. Воздушный поток покидает салон через два открытых окна и вентиляционное отверстие на задней стенке. Вытекания воздуха через люки не наблюдается.
Скоростные и температурные показатели, полученные в результате расчетов, на рис. 4 и 5 представлены в графическом виде. Рядом с каждым
162
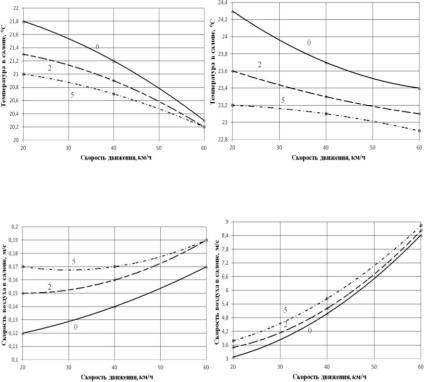
графиком указано соответствующее количество открытых окон. Особое внимание уделено гидродинамическим показателям на высоте соответствующей уровню головы сидящих пассажиров, поскольку эта область наиболее чувствительна к охлаждению.
а) б)
Рис. 4. Графики минимальной (а) и максимальной (б) температур в салоне автобуса на уровне головы пассажиров
а) б)
Рис. 5. Графики минимальной (а) и максимальной (б) скоростей в салоне автобуса на уровне головы пассажиров
На основании полученных результатов, проведена оценка микроклиматических условий в салоне автобуса на соответствие требованиям нормативных документов (ГОСТ). Показатели микроклимата в салонах транспортных средств регламентируются ГОСТ Р 50993-96 и ГОСТ 12.1.005-88 [1],[2]. Сравнение полученных результатов с требованиями нормативных документов приведено в таблице.
По результатам пространственного моделирования процесса вентиляции автобуса определена структура воздушного потока и значения гидродинамических параметров в салоне автобуса при различных скоростях движения и конфигурациях вентиляционной системы.
163
Таблица. Сравнение результатов расчетов с требованиями ГОСТ
Регламентируемый параметр |
ГОСТ |
Расчеты |
Подвижность воздуха в зоне головы и пояса, м/с |
0,5‒1,5 |
0,114‒ 9,17 |
Перепад между температурами в салоне и снаружи, °С |
до 5 |
до 4,3 |
Допустимая температура в салоне в теплое время года, °С |
18‒25 |
20,2–24,3 |
Целью дальнейших исследований является разработка более детальной геометрической модели и исследование процесса вентиляции в условиях полного обтекания автобуса воздушным потоком.
Список литературы
1.ГОСТ 12.1.005–88. Система стандартов безопасности труда. Общие сани- тарно-гигиенические требования к воздуху рабочей зоны. - Введ. 1989–01–01. - М: Изд-во стандартов, 1988. - 48.
2.ГОСТ Р 50993-96. Автотранспортные средства. Системы отопления, вентиляции и кондиционирования. Требования к эффективности и безопасности. - Введ. 1996–09–12. - М : Изд-во стандартов, 1997. - 11.
3.Евграфов, А.Н. Аэродинамика автомобиля: учебное пособие / А.Н. Евграфов. - М : МГИУ, 2010. - 356.
4.Михайловский, Е.В. Аэродинамика автомобиля / Е.В. Михайловский. - М : Машиностроение, 1973. - 224.
5.Юн, А.А. Теория и практика моделирования турбулентных течений: Монография / А.А. Юн. - М : Либроком, 2009. - 272.
К. П. Подшивалин, магистрант
Е. И. Тескер, доктор технических наук, профессор Волгоградский государственный технический университет
Способ лазерно-плазменного нанесения покрытий на детали
Исследование лазерного нанесения покрытий является актуальным в области машиностроения. Как правило, такие исследования имеют большое значение для надежности, стойкости коррозии и высоким температурам деталей, применяемых в авиа- и кораблестроении. Существует несколько способов нанесения специальных покрытий на деталь, наиболее лучшим из них является способ лазерно-плазменного напыления.
Со времен бронзового века металлы и изготовленные из них изделия играли в жизни человечества очень важную роль. Несмотря на то, что металлы обладают отличными физическими и химическими свойствами и износостойкостью, с ними все еще связано много проблем. Часть из этих проблем удалось решить улучшением физических и химических свойств
164
металлических изделий путем изменения структуры металлического материала (применением сплавов и композитов). В то же время попытки решить проблемы, ассоциируемые с поверхностными свойствами, оказались не столь успешными.
Проблемы в отношении поверхностных свойств металлических изделий связаны, в основном, со стойкостью к коррозии и износу, с трибологическими свойствами, термостойкостью с использованием металлических изделий в строительстве, а также для других внутренних и наружных применений.
Поскольку представляется затруднительным нанести покрытия на химические реакторы и трубы, а также на любые металлические изделия, контактирующие с реагентами, вызывающими коррозию, химические реакторы и трубы, а также любые металлические изделия, вступающие в контакт с вызывающими коррозию реагентами или находящиеся в иных опасных или способствующих износу средах, необходимо, как правило, изготавливать из специальных дорогостоящих металлов, таких как титан или различные титановые сплавы [1]. Чтобы избежать этого применяют способ лазерно-плазменного нанесения покрытий.
Согласно способу плазмотроном создают плазменный поток, направленный на напыляемую поверхность, подают в него частицы напыляемого порошка, а на выход из сопла плазмотрона перпендикулярно плазменному потоку подают модулированное лазерное излучение и фокусируют его на противоположной от источника лазерного излучения стороне пламенного потока. При этом лазерное излучение подают перед подачей частиц напыляемого порошка и с интенсивностью, не менее пороговой, при которой происходит оптический пробой. Технический результат - повышение прочности сцепления покрытия с подложкой.
Данный способ превосходит обычное плазменное напыление два раза, так как на поверхность попадают неоднородно нагретые частицы напыляемого порошка, который приводит к попаданию на поверхность обрабатываемой детали частиц, не достигших температуры плавления, и получение покрытия с низкими эксплуатационными характеристиками из-за низкой прочности вследствие отслаивания и высокой пористости. На рис. 1 представлена принципиальная схема реализации способа.
Схема включает внешний блок управления установки плазменного напыления 1, блок электропитания установки плазменного напыления 2, плазмотрон 3, источник модулированного лазерного излучения 4, поворотное устройство комбинированного узла для лазерно-плазменного напыления 5, кронштейн 6, связанный с системой фокусировки лазерного излучения 7, переходник 8, предметный стол 9, систему датчиков 10 и компьютер 11.
Способ лазерно-плазменного нанесения покрытий реализуется следующим образом: создается плазменный поток, направленный на напыляемую поверхность, в который после выхода из сопла плазмотрона перпен-
165
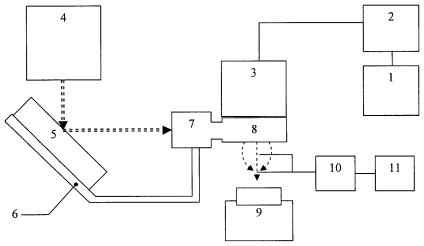
дикулярно подается модулированное лазерное излучение с интенсивностью, не менее пороговой.
Рис. 1. Схема реализации способа лазерно-плазменного напыления покрытий
Лазерное излучение фокусируется системой фокусировки 1 на противоположной от источника лазерного излучения стороне плазменного потока. Температура плазменного потока повышается, что фиксируется с помощью датчиков 2, и после этого в разогретый плазменный поток подаются частицы напыляемого материала. Достаточность нагрева частиц напыляемого порошка в плазменном потоке оценивается с помощью программного обеспечения, установленного на компьютере 3 [2].
Дальнейшей задачей является использование подобного способа и средств, для решения более сложных проблем надежности, износостойкости, стойкости коррозии и температуре, а также для нанесения покрытий на поверхности изделий, уже имеющих покрытия.
Список литературы
1. Пат. 2467092 Российская Федерация, МПК7 C23C14/28, B23K26/06. Способ нанесения покрытия на металлическое изделие снабженное покрытием [Текст] / РУУТТУ Яри; заявитель и патентообладатель ПИКОДЕОН ЛТД ОЙ. - №2008137492/02. заявл. 23.02.07, опубл. 20.11.12. – 19 с.: 35 ил.
2. Пат. 2449048 Российская Федерация, МПК7 C23C4/12. Способ лазерноплазменного напыления покрытий [Текст] / Чащин Е.А., заявитель и патентообладатель ГОУ ВПО «Ковровская государственная технологическая академия имени В.А. Дегтярева». - №2010120868/02. заявл. 24.05.10, опубл. 27.04.12. – 2 с.: 1 ил.
166
И. Б. Покрас, доктор технических наук, профессор Г. А. Чикуров, кандидат технических наук, доцент, докторант
Ижевский государственный технический университет имени М. Т. Калашникова
Устройство для экспериментального определения реологических характеристик неньютоновских жидкостей при переменных давлениях и температурах
Устройства для исследования вязкого течения жидкостей называют вискозиметрами. Существует множество различных конструкций вискозиметров для измерения вязкости жидкостей при нормальном атмосферном давлении. Однако, вязкость жидкости существенно зависит от ее температуры и воздействующего на нее давления, а число вискозиметров для определения вязкости при переменных температурах и давлениях невелико и их конструкции довольно сложны.
Вискозиметры основанные на определении скорости свободно падающего шарика при высоких давлениях использовать неудобно, поскольку вязкость жидкости значительно увеличивается, и поэтому шарик падает очень медленно [1]. Ротационные вискозиметры позволяющие измерять вязкость при высоких давлениях жидкости имеют сложную конструкцию и очень трудоемки при изготовлении [2]. Вискозиметры с капиллярной трубкой предпочтительнее, если данные используются в задачах течения жидкости по трубам. Большим преимуществом капиллярных вискозиметров является относительная простота их конструкции, простота вспомогательного оборудования для контроля и измерения разности давлений и скорости течения в капиллярной трубке.
Предлагаемая конструкция капиллярного вискозиметра, общий вид которой представлен на рис. 1, позволяет определять реологические характеристики жидкостей с неньютоновским поведением при высоких давлениях и различных температурах.
Для привода вискозиметра в действие может быть использована любая машина для испытаний на сжатие, которая позволяет изменять скорость движения подвижной траверсы, и рабочее пространство которой позволяет разместить и закрепить вискозиметр.
Особенностью разработанного капиллярного вискозиметра является то, что капилляр выполнен в виде кольцевого зазора между цилиндрическим отверстием в корпусе 1 вискозиметра и расположенным внутри этого отверстия стержнем 2. Схема течения жидкости по такому капилляру наилучшим образом соответствует схеме течения смазки при гидродинамическом волочении и гидропрессовании.
Корпус 1 вискозиметра выполнен в виде толстостенного цилиндра с внутренним отверстием переменного диаметра из стали 45ХНМФА и закален до твердости HRC 42.
167
Давление и течение жидкости в вискозиметре обеспечивается плунжером 3, который прикреплен к машине для испытаний на сжатие, обеспечивающей его перемещение вниз. Плунжер 3 выполнен из стали 45ХНМФА и закален до твердости HRC 54.
Устройство снабжено узлом контроля и поддержания заданной температуры, состоящим из датчика температуры 4 – датчик температуры, нагревательного элемента – спирали 5, навитой на корпус 1, теплоизоляционного кожуха 6. Спираль подключается к сети переменного тока.
Вискозиметр имеет систему циркуляции жидкости, состоящую из обратного клапана 7, уплотненного в корпусе 1, сливной 8 и подающей 9 трубок, концы которых опущены в бак с исследуемой жидкостью. Бак с исследуемой жидкостью подогревается до температуры вискозиметра – температуры при которой определяются реологические характеристики исследуемой жидкости. Циркуляционная система позволяет использовать одну и ту же жидкость для всей серии экспериментов при различных температурах и давлениях.
Выходное отверстие В капилляра снабжено дросселем 10, позволяющим регулировать объемный расход и давление исследуемой жидкости.
Электронные датчики давления 11, 12 и 13 позволяют измерять давление жидкости в процессе ее истечения и отображают информацию о давлении в реальном времени. Датчик 11 измеряет давление в начале капилляра, датчик 12 показывает давление жидкости в средней части капилляра, датчик 13 фиксирует давление жидкости в конце капилляра.
Капиллярный вискозиметр работает следующим образом. Предварительно в вискозиметр сверху через отверстие для плунжера заливают исследуемую жидкость. Концы сливной 8 и подающей 9 трубок опускают в бак с исследуемой жидкостью. Включают нагревательный элемент 5, доводят температуру вискозиметра и бака с исследуемой жидкостью до температуры, при которой необходимо измерить вязкость жидкости. Температуру контролируют датчиком температуры 4. Объемный расход смазки и давление, при котором определяются характеристики исследуемой жидкости, регулируются с помощью дросселя 10. На плунжер 3 сверху действуют с некоторым усилием, при этом плунжер начинает двигаться вниз, сжимая исследуемую жидкость и создавая в ней давление. Жидкость из верхней полости А через кольцевой капиллярный зазор между цилиндрическим корпусом 1 и расположенным внутри него стержнем 2 попадает в нижнюю полость Б откуда сливается через дроссель 10 по сливной трубке 8 в бак с исследуемой жидкостью. С помощью электронных датчиков давления 11, 12 и 13 определяются величины давления жидкости в разных частях капилляра. При движении плунжера 3 вверх, обратный клапан 7 открывается, и исследуемая жидкость заполняет верхнюю полость А. Вискозиметр готов к следующему опыту.
168
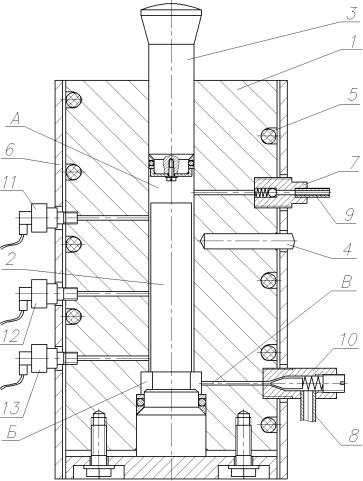
Рис. 1. Общий вид вискозиметра
При проведении эксперимента фиксируются: p1 ‒ давление в начале капилляра по показанию датчика 11; p2 ‒ давление в средней части капилляра по показанию датчика 12; p3 ‒ давление в конце капилляра по показанию датчика 13; H величина хода плунжера вискозиметра; T ‒ время в течении которого осуществлялся ход плунжера величиной H.
По полученным в ходе эксперимента значениям p1, p2, p3, H, T можно определить:
‒объемный расход смазки Q;
‒перепад давления p на длине L ‒ расстояние между датчиками
давления.
Объемный расход смазки Q определяется следующим выражением:
169

|
|
|
|
Q V S |
H |
S |
|
|
|
|
(1) |
|||||||
|
|
|
|
T |
|
|
|
|
||||||||||
|
|
|
|
|
|
|
|
|
|
|
|
|
|
|
|
|
|
|
где V – скорость движения плунжера; S – площадь поперечного сечения |
||||||||||||||||||
отверстия под плунжер. |
|
|
|
|
|
|
|
|
|
|
|
|
|
|
|
|
|
|
Перепад давления p |
на длине L |
: |
|
|
|
|
|
|
|
|||||||||
|
|
|
|
|
p p3 |
p1. |
|
|
|
|
(2) |
|||||||
По полученным значениям объемного расхода смазки |
Q |
и перепада |
||||||||||||||||
давления p можно определить скорость сдвига |
|
|
|
|||||||||||||||
и напряжение сдвига |
||||||||||||||||||
исследуемой жидкости по формулам [3]: |
|
|
|
|
|
|
|
|||||||||||
|
|
|
|
|
|
|
|
|
|
|
Q |
|
|
|
|
|
||
|
|
Q |
|
|
|
h P |
|
d |
|
Rh |
2 |
|
|
|
||||
|
|
|
|
|
|
|
|
|
|
|
; |
|
(3) |
|||||
|
|
2 |
|
|
2L |
|
|
h P |
|
|
|
|||||||
|
Rh |
|
|
|
|
|
|
d |
|
2L |
|
|
||||||
|
|
|
|
|
|
|
|
|
|
|
||||||||
|
|
|
|
h P |
|
, |
|
|
|
|
|
|
|
(4) |
||||
|
|
|
2L |
|
|
|
|
|
|
|
|
|||||||
|
|
|
|
|
|
|
|
|
|
|
|
|
|
|
|
|
где h ‒ величина зазора между корпусом 1 вискозиметра и стержнем 2. Проведя серию экспериментов с исследуемой жидкостью при опреде-
ленной температуре и давлении при различных степенях открытия дросселя 10 вискозиметра и, определив значения скоростей и напряжений сдвига в этих экспериментах по формулам (3) и (4), можно построить кри-
вую течения исследуемой неньютоновской жидкости в координатах .
На рис. 2 приведены кривые течения для различных типов неньютоновских жидкостей. По виду кривой можно определить тип исследуемой жидкости.
Рис. 2. Кривые течения различных типов неньютоновских жидкостей:
1 – псевдопластичная жидкость с пределом текучести (пластичная жидкость); 2 – псевдопластичная; 3 – дилатантная
Аппроксимируя таблицу значений и , полученных в серии экспе-
170
риментов при одной и той же температуре и давлении, можно найти ана-
литическую зависимость
|
|
|
f ( ) |
для исследуемой жидкости при задан-
ной температуре и давлении. Полученную аналитическую зависимость можно использовать для расчетов технологических процессов, в которых применяется исследуемая жидкость, например, при расчетах процессов обработки металлов давлением в режиме жидкостного трения, где необходимо знать свойства смазки при высоком давлении и температуре.
Список литературы
1.Золотых, Е.В. Исследование зависимости вязкости жидкости от давления / Е.В. Золотых // Измерительная техника. - 1955. - №3. - 32-37.
2.Глухов, В.П. Исследование процесса обратного выдавливания с жидкостным трением / В.П. Глухов // Дисс. на соиск. уч. степени канд.техн.наук. - Ижевск,
1973. - №3. - 161.
3.Покрас, И.Б. Определение реологических характеристик неньютоновских жидкостей / И.Б. Покрас, Г.А. Чикуров // Научно-практический журнал «Интеллектуальные системы в производстве». - Ижевск : Изд-во ИжГТУ, 2009. - №2(14).
-42-46.
И. Н. Полянских, аспирант
С. Д. Кугультинов, доктор технических наук, профессор Ижевский государственный технический университет имени М. Т. Калашникова
Изучение проблем технологической операции развертывания канала ствола гладкоствольного оружия
Воружейном производстве детали типа «ствол» очень актуальна проблема промежуточной обработки внутренних поверхностей канала ствола. Существует множество видов обработки отверстий. Одним из инструментов обработки отверстий является развертка. В настоящее время эта операция не эффективна, а применение устаревшего оборудования и имеющегося на производстве инструмента приводит к получению не качественного товара. Исследование этого вопроса актуально на ОАО «ИМЗ».
Внастоящее время все каналы стволов гладкоствольных охотничьих ружей на ИМЗ обрабатываются по типовой схеме: прошивка – горячее радиальное обжатие – термообработка – развертывание – свинцевание. В такой последовательности обработки сделан акцент на достижение наибольшей производительности при наименьших затратах.
Наиболее проблемным звеном этой цепочки является развертывание. Существуют два способа, развертывания каналов стволов стрелкового
оружия:
171

1) на сжатие канала ствола (рис. 1);
Рис. 1. Способ протягивания развертки
2) на растяжение канала ствола (рис. 2).
Рис. 2. Способ проталкивания развертки
На данный момент в производстве развертывание из-за дульного сужения ведется способом на растяжение, но затем необходимо извлечь инструмент, что может привести к задирам. Весь процесс развертывания канала ствола на ИМЗ состоит из четырех этапов. Первые два этапа – это операции чернового развертывания направленные на устранение оставшегося после горячего радиального обжатия конуса, снимая припуск величиной по 0,15мм на сторону, на каждую операцию Далее два ствола спаиваются, в результате чего на внутренней поверхности канала ствола образуются дефекты в виде вздутия металла. Этот дефект вместе со следующим припуском снимает получистовая развертка. И конечным этапом механической обработки ствола является чистовое развертывание.
В используемой на производстве ИМЗ схеме развертывания замечен ряд недостатков, одним из которых является плохие условия отвода стружки вследствие ограниченного объема канала ствола, что приводит к попаданию стружки под заднюю поверхность режущей кромки, ее заматыванию и возникновению порезок. В процессе развертывания используется самоустанавливающийся инструмент, что неизбежно влечет за собой равномерность срезаемого слоя по диаметру и невозможность исправления несоосности наружной и внутренней поверхностей ствола. Также исправление непрямолинейности канала ствола происходит на ограниченном участке поверхности, определяемом длиной развертки. Недостатком инструмента является сложность создания механизма его регулирования по диаметру для компенсации износа из-за сложности компановки конструкции развертки при маленьком диаметре канала ствола, что в свою очередь ограничивает стойкость разверток. Аналогом процесса является растачивание, которое обычно применяется для отверстий диаметром 30
172
мм и более.
Развертывание глубоких отверстий представляет сложную технологическую проблему, это обусловлено изнашиванием развертки, что влечет за собой изменения диаметра и шероховатости поверхности вдоль оси обработанного отверстия. Кроме этого, глубокие отверстия при отношении длины ствола к его диаметру, как L/d ≥ 20, чаще всего обрабатываются с горизонтальной осью развертки на токарно-револьверных и других станках. Проблемным при этом является обеспечение достаточной жесткости развертки и звеньев станка, исключающей прогиб инструмента изза несовпадения осей металлорежущего инструмента и обрабатываемого отверстия, что является источником возникновения возмущающей силы, вызывающей колебания системы. Это является существенной причиной снижения стойкости развертки, ухудшения шероховатости обработанной поверхности и снижения точности и особенно проявляется при выводе инструмента из глубокого отверстия (задиры, царапины) из-за усадки отверстия (диаметр отверстия меньше диаметра развертки), так как при этом происходит резание (соскабливание) калибрующими зубьями со стороны шейки [1].
Для достижения возможно большей производительности и получения качественного канала особое внимание обращают на отвод стружки и на строгое совпадение осей развертки и изделия. Нестабильный отвод стружки неизбежно приводит к ухудшению качества поверхности, к уменьшению стойкости инструмента и понижению производительности [2].
Чтобы обеспечить нормальный отвод стружки из глубокого отверстия при непрерывном процессе развертывания, необходимо снабжать станки добавочными агрегатами и приспособлениями для подвода смазывающеохлаждающей жидкости под определенным давлением, а с другой стороны, применять режущий инструмент в таком конструктивном оформлении, при котором выталкивание стружки жидкостью из канала становится наиболее благоприятным.
Строго установившихся типов конструкций оружейных разверток, как например ружейное сверло, нет. В практике ружейные развертки различают по числу зубьев, конструкции и геометрии режущей части, по конструкции державки и способу соединения ее с разверткой.
Наиболее широкое применение получили оружейные развертки трех- и пятизубые.
Державки разверток бывают двух видов: с внутренним каналом и без него.
Внутренний канал в державке служит для подвода смазывающеохлаждающей жидкости к режущей части развертки. Для выхода жидкости в месте соединения державки с рабочей частью развертки делают боковое окно.
При использовании разверток без внутреннего канала жидкость поступает в зазор между державкой и поверхностью развертываемого отвер-
173
стия.
В первом случае жидкость подводят в месте крепления развертки, а вовтором ‒ в месте захода развертки в канал ствола. Развертки с внутренним каналом в державке обеспечивают более рациональный расход жидкости, неизменное давление и лучший доступ ее к режущим лезвиям. Изготовление державок с внутренним каналом сложнее [3].
Принимая во внимание вышеизложенные проблемы процесса развертывания, стоит отметить ряд требований которому должны удовлетворять развертки:
1.Обеспечивать получение поверхности канала требуемой чистоты и точности при максимальной производительности и достаточной стойкости.
2.Давать возможность подводить смазывающе-охлаждающую жидкость к месту резания.
3.Обеспечивать возможность «помещения» стружки между зубьями развертки и хорошее вымывание стружки смазывающе-охлаждающей жидкостью.
4.Четко базироваться во время развертывания.
5.Не допускать конусности отверстия.
6.Обладать высокой износостойкостью и твердостью
7.Быть регулируемой
8.Быть простыми в изготовлении и эксплуатации.
Предполагается, что развертка, спроектированная таким образом, чтобы удовлетворять всем указанным требованиям позволит решить остро стоящие вопросы на производстве в области качества канала ствола. При этом сократится количество переходов при развертывании, а значит сократится время и трудоемкость обработки. Проработка конструкции такой развертки является целью дальнейших исследований.
Список литературы
1.Проектирование металлорежущих инструментов / Под ред. И.И. Семенченко. - М : Машгиз, 1963. - 952.
2.Уткин, Н.Ф. Обработка глубоких отверстий / Н.Ф. Уткин, Ю.И. Кижняев, С.К. Плужников. - Л : Машиностроение, 1988. - 269.
3.Развертки, методическое руководство по курсу «Проектирование металлорежущего инструмента». – Фрунзе, 1985.
174
А. Г. Полтанов, магистрант
М. Р. Королева, кандидат физико-математических наук, доцент Ижевский государственный технический университет
имени М. Т. Калашникова
Исследование газодинамических параметров в соплах с переменным критическим сечением
Важность и актуальность настоящей задачи определяется рядом причин. Повышение энергетических характеристик двигателей и других их параметров привело к увеличению геометрических степеней расширения сопел и размеров двигателей. Использование сопел с переменным критическим сечением позволит сохранить достаточно высокие тяговые характеристики [1]. Именно исследованию такого типа двигательных установок с центральным телом, имеющих несколько меньший коэффициент тяги, чем идеальное сопло Лаваля, но значительно меньшую длину, посвящена настоящая работа.
Численные исследования выполнялись в коммерческом пакете ANSYS
CFX 14 (Academic research CFD Pad App лицензия инв. №М000014044 от 2007г.). Данный пакет входит в состав комплекса конечно-элементного анализа и вычислительной гидродинамики ANSYS Workbench.
Задача о течении газа в осесимметричном сопле с коротким центральным телом решалась в цилиндрической системе координат на основе осредненных по Рейнольдсу уравнений Навье-Стокса [2]. В декартовой системе координат данные уравнения запишутся следующим образом
|
|
|
|
|
|
|
|
|
|
|
|
|
|
|
|
|
|
v |
x |
|
|
vy |
|
v |
z |
0 |
|
|
|
|
|
|
|
|
|
|
|
|
|
|
|
|
||||||||||||||||||||||||||
|
|
|
|
|
|
|
|
|
|
|
|
|
|
|
|
|
|
|
|
|
|
|
|
|
|
|
|
|
|
|
|
|
|
|
|
|
|
|
|
|
|
|
|
|
|
|
|
|
|
|
|
|
||||||||||||||||
|
|
|
|
|
|
|
|
|
|
|
|
|
|
|
t |
|
x |
|
|
|
|
y |
|
|
|
|
|
|
|
z |
|
|
|
|
|
|
|
|
|
|
|
|
|
|
|
|
|
|
|
|||||||||||||||||||
|
|
|
|
|
|
|
|
|
|
|
|
|
|
|
|
|
|
|
|
|
|
|
|
|
|
|
|
|
|
|
|
|
|
|
|
|
|
|
|
|
|
|
|
|
|
|
|
|
|
|
|
|
|
|
|
|
||||||||||||
v |
x |
|
|
v |
2 |
|
|
|
vx vy |
|
|
v |
v |
z |
|
|
|
p |
|
|
xx |
|
xy |
|
|
|
xz |
|
||||||||||||||||||||||||||||||||||||||||
|
|
|
|
|
|
x |
|
|
|
|
|
|
|
|
|
|
|
|
|
|
x |
|
|
|
|
|
|
|
|
|
|
|
|
|
|
|
|
|
|
|
|
|
|
|||||||||||||||||||||||||
|
|
t |
|
|
x |
|
|
|
|
y |
|
|
|
|
|
z |
|
x |
|
x |
|
|
y |
|
z |
|
||||||||||||||||||||||||||||||||||||||||||
|
|
|
|
|
|
|
|
|
|
|
|
|
|
|
|
|
|
|
|
|
|
|
|
|
|
|
|
|
|
|
|
|
|
|
|
|
|
|
|
|
||||||||||||||||||||||||||||
vy |
|
|
vxvy |
|
|
|
vy2 |
|
|
vyvz |
|
|
|
|
p |
|
|
xy |
|
yy |
|
|
yz |
|
||||||||||||||||||||||||||||||||||||||||||||
|
|
t |
|
|
x |
|
|
|
|
|
|
|
y |
|
|
|
|
z |
|
|
|
|
|
y |
|
x |
|
|
y |
|
|
z |
|
|||||||||||||||||||||||||||||||||||
|
|
|
|
|
|
|
|
|
|
|
|
|
|
|
|
|
|
|
|
|
|
|
|
|
|
|
|
|
|
|
|
|
|
|
|
|
|
|
|
|
||||||||||||||||||||||||||||
|
v |
z |
|
|
v |
x |
v |
z |
|
|
|
vyvz |
|
|
v2 |
|
|
|
|
p |
|
|
xz |
|
yz |
|
|
zz |
|
|||||||||||||||||||||||||||||||||||||||
|
|
|
|
|
|
|
|
|
|
|
|
|
|
|
|
|
|
|
|
|
|
z |
|
|
|
|
|
|
|
|
|
|
|
|
|
|
|
|
|
|
|
|
|
|||||||||||||||||||||||||
|
|
t |
|
|
x |
|
|
|
|
|
|
|
|
|
y |
|
|
|
|
|
|
z |
|
|
z |
|
x |
|
y |
|
|
|
z |
|
||||||||||||||||||||||||||||||||||
|
|
|
|
|
|
|
|
|
|
|
|
|
|
|
|
|
|
|
|
|
|
|
|
|
|
|
|
|
|
|
|
|
|
|
|
|
|
|
|
|
|
|
|
|
||||||||||||||||||||||||
|
|
E |
|
|
vx E |
|
vy E |
|
vz E |
|
|
|
|
pvx |
|
|
pvy |
|
|
pvz |
|
|
||||||||||||||||||||||||||||||||||||||||||||||
|
|
t |
|
x |
|
|
|
|
|
|
|
y |
|
|
|
|
|
z |
|
|
|
|
|
|
x |
|
|
y |
|
|
|
|
z |
|
|
|||||||||||||||||||||||||||||||||
|
|
|
|
|
|
|
|
|
|
|
|
|
|
|
|
|
|
|
|
|
|
|
|
|
|
|
|
|
|
|
|
|
|
|
|
|
|
|
|
|
|
|
|
|
|
|
||||||||||||||||||||||
|
|
|
|
( v v v ) |
|
|
|
( v v v ) |
|
|
|
|
||||||||||||||||||||||||||||||||||||||||||||||||||||||||
|
x |
|
y |
|
|
|
|
|
|
|||||||||||||||||||||||||||||||||||||||||||||||||||||||||||
|
|
|
|
|
x x x |
|
|
|
|
|
|
x y y |
|
|
x z z |
|
|
|
|
|
|
|
|
x y x |
|
|
|
|
yy y |
|
|
yz z |
|
|
|
|
|
|
|
|
||||||||||||||||||||||||||||
|
|
|
|
|
|
|
|
|
|
|
|
|
|
|
|
|
|
|
|
|
|
|
|
|
|
|
|
|
|
|
|
|
|
|
|
|
|
|
|
|||||||||||||||||||||||||||||
|
|
|
|
( v v v ) |
|
|
|
|
T |
|
|
|
|
|
|
T |
|
|
|
|
|
|
T |
|
|
|||||||||||||||||||||||||||||||||||||||||||
|
z |
|
x |
|
|
x |
|
|
|
|
|
|
y |
|
z |
|
|
z |
|
|||||||||||||||||||||||||||||||||||||||||||||||||
|
|
|
|
|
x z x |
|
|
|
|
|
yz y |
|
|
|
z z |
|
|
z |
|
|
|
|
|
|
|
|
|
|
|
|
|
|
y |
|
|
|
|
|
|
|
|
|||||||||||||||||||||||||||
|
|
|
|
|
|
|
|
|
|
|
|
|
|
|
|
|
|
|
|
|
|
|
|
|
|
|
|
|
|
|
|
|
|
|
|
|
|
|
|
|
|
|
|
|
|
|
|
|
|
|
|
|
|
|
|
|
|
|
|
175
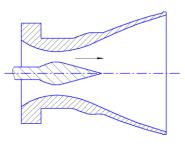
Для замыкания уравнений Рейнольдса использовалась |
k |
модель |
турбулентности [3], использующая для описания турбулентных величин систему двух нелинейных уравнений ‒ для кинетической энергии турбулентности k и скорости диссипации турбулентной энергии .
Геометрия расчетной области представлена на рис. 1.
Рис. 1. Схема соплового блока с ЦТ
На левой входной границе расчетной области, задавались значения давления и температуры, полученные при теоретическом расчете сопла Р = 97,466 атм, Т = 3 245 К. На выходной границе задавалось сверхзвуковое истечение газа, поэтому определение каких-либо параметров течения не требовалось. На твердых стенках сопла и поверхности центрального тела ставились условия прилипания. Расчет течения продолжался до установления.
Для исследования сходимости были проведены расчеты на шести сетках, содержащих разное количество ячеек от 310 000 до 187 000. Исследование сходимости проводилось по коэффициенту расхода – отношению фактического расхода газа на выходе из сопла к теоретическому. Результаты представлены на рис. 2. Видно, что процесс сходится, и дальнейшее увеличение мощности сетки не приведет к существенному изменению результатов расчета.
Результаты расчетов приведены на рис. 3 и рис. 4. На рисунках показано стационарное поле скорости течения и распределение числа Маха в случае минимального размера критического сечения сопла (в дальнейшем будут рассматриваться и другие случаи). На выходе имеем сверхзвуковой поток со скоростью истечения wa 2501 м/с и числом Маха порядка
M 3,125 . Тяга рассматриваемого двигателя определяется по следующей формуле:
|
Р mwa Fa ( pa ph ), |
где |
m ‒ расход, полученный в пакете ANSYS, Fa ‒ площадь среза, pa и |
ph |
‒ давление на срезе и давление окружающей среды. |
|
Получаем тягу двигателя P 9846 Н. |
|
176 |
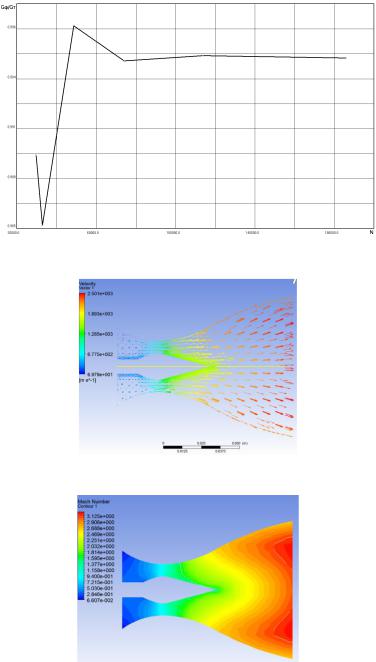
Рис. 2. Изменение коэффициент расхода в зависимости от количества ячеек разбиения
Рис. 3. Распределение скорости течения в сопле
Рис. 4. Распределение числа маха в сопле
177
Предполагается, что дальнейшее исследование регулирования критического сечения с помощью центрального тела в двигательной установке будет способствовать получению максимальных тяговых и массовых характеристик двигателя, что является целью дальнейших исследований.
Список литературы
1.Пирумов, У.Г. Течение газа в соплах / У.Г. Пирумов, Г.С. Росляков. - М :
МГУ, 1978. - 351.
2.Лойцянский, Л.Г. Механика жидкости и газа / Л.Г. Лойцянский. - М :
Наука, 1970. - 904.
3.Menter, F.R. Two-equation eddy-viscosity turbulence models for engineering applications / F.R. Menter // AIAA J. - 1994. - v. 32. - 1598-1605.
Е. С. Пушина, магистрант А. В. Вахрушев, доктор физико-математических наук, профессор
Ижевский государственный технический университет имени М. Т. Калашникова
Анализ методов и процессов перемешивания наночастиц и микрочастиц
В настоящее время наиболее интересным и в то же время малоизученным в сфере нанотехнологий является процесс перемешивания наночастиц и микрочастиц. Поэтому даже незначительная неравномерность распределения компонентов нанокомпозитов недопустима, а задача исследования формирования однородных нанодисперсных смесей и оперативного контроля параметров однородности их перемешивания является весьма актуальной [4].
Рассмотрим основные методы перемешивания наночастиц:
1. Метод перемешивания частиц с использованием технологии Мас-
сарта. Рене Массарт рассматривал технологию получения магнетита путем перемешивания: смесь полиакриловой кислоты, соли железа (III) (обычно хлорид) и диэтиленгликоля нагревают при перемешивании до 220 °С в атмосфере азота; после образования прозрачного раствора, к этой смеси быстро добавляется раствор гидроксида натрия в диэтиленгликоле, оставляют реакцию при перемешивании на 10 минут и центрифугированием выделяют наночастицы магнетита. Высокая растворимость наночастиц в воде обеспечивается за счет гидрофильности карбоксильных групп полиакриловой кислоты, которые в то же время взаимодействуют с поверхностью наночастиц, предохраняя их от агломерации представленной на рис. 1 [1].
178
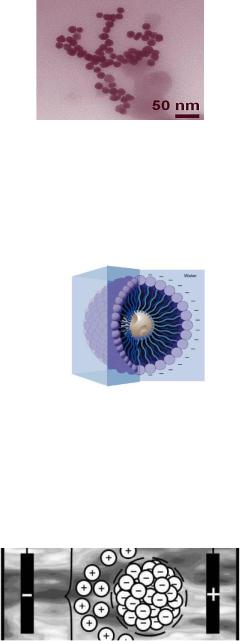
Рис. 1. Агломерации наночастиц
2. Перемешивание наночастиц для создания мицелл.
Мицеллы возникают в результате самоорганизации бифункциональных молекул, классических ПАВ, содержащих в своем составе ионогенную гидрофильную и гидрофобную группы. При интенсивном перемешивании с небольшим количеством воды и избытком неполярного растворителя происходит самоорганизация молекул ПАВ в сферические образования, полярными хвостами внутрь, вокруг микро или нанокапелек воды, на рис. 2 [2].
Рис. 2. Мицелла в водной среде (частица, состоящая из нерастворимого ядра покрытого стабилизирующей оболочкой)
3. Способ перемешивания наночастиц посредством электрических взаимодействий. Способ перемешивания наночастиц осуществляется посредством электрических взаимодействий. За основу принципа действия устройства использовано притяжение электрических зарядов противоположной полярности: наночастицы одного материала наделяются положительными зарядами, другого материала – отрицательным, процесс перемешивание посредством электрических взаимодействий представлен на рис. 3 [3].
Рис. 3. Перемешивание + частиц композита А с частицами композита Б, помещенных в электрическое поле катода (‒) и анода (+)
179
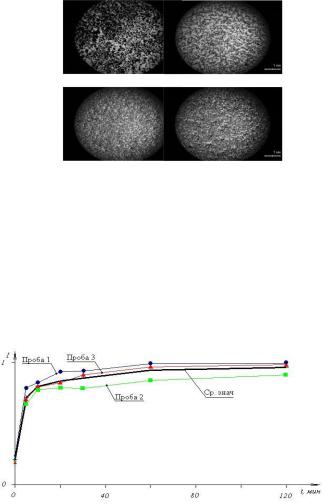
4. Перемешивание наночастиц с микрочастицами.
Перемешивание осуществлялось в ультразвуковой ванне, затем с помощью пипетки бралась проба, и производился цифровой снимок с оптического микроскопа, представленный на рис. 4.
а) без перемешивания |
б) время перемешивания 10 минут |
в) время перемешивания 20 минут г) время перемешивания 30 минут
Рис. 4. Фотографии образцов смеси, сделанные при десятикратном увеличении
Видно, что все фотографии кроме первой практически не отличаются друг от друга, и визуально определить равномерность перемешивания невозможно. Однако степень перемешивания исследуемой смеси изменяется от снимка к снимку, на что указывает представленная на рис. 5 зависимость степени перемешивания смеси от времени воздействия ультразвука. Видно, что усредненное значение степени перемешивания смеси имеет вид плавной, постоянно возрастающей кривой (линия без маркеров на рис. 5).
Рис. 5. Зависимость степени перемешивания от времени
Как следует из графика, наиболее интенсивно перемешивание происходит в первые пятнадцать-двадцать минут процесса, затем степень перемешивания стабилизируется, и график приближается к горизонтальной асимптоте близкой к единице. Дальнейшее увеличение степени переме-
180
шивания за счет увеличения времени процесса перемешивания весьма неэффективно.
Спомощью методов перемешивания возможно создание новых частиц
иматериалов. Благодаря этим методам наметился значительный прогресс
идальнейшие перспективы развития нанонауки.
Проведенный анализ опубликованных за последние годы работ по вопросу перемешивания наночастиц с микрочастицами показывает актуальность и огромную практическую значимость этих уникальных объектов [5].
Список литературы
1.Ge, J. One-Step Synthesis of Highly Water-Soluble Magnetite Colloidal Nanocrystals / J. Ge, Y. Hu, M. Biasini // Chem. Eur. J. - 2007. - 13. - 7153-7161.
2.Pileni, M.P. The Role of soft colloidal templates in controlling the size and shape of inorganic nanocrystals / M.P. Pileni // Nature Materials. - 2003. - 2. - 145-150.
3.Патент Российской Федерации №2465008 МПК A61K47/04. Способ получения железоуглеродистых наночастиц / Митькина В.А., Галанов А.И., Сапрыкин Ф.Е.
4.Пат. 2301771 Российская Федерация, МПК B82B 3/00. Способ и устройство перемешивания наночастиц / Вахрушев А.В., Федотов А.Ю., Вахрушев А.А., Суетин М.В.
5.Вахрушев, А.В. Программно – аппаратный комплекс для анализа равномерности переме-шивания микро- и наноэлементов / А.В. Вахрушев, А.В. Земсков, А.Ю. Федотов. - Ижевск : Институт прикладной механики УрО РАН.
М. А. Пушкарев, магистрант О. А. Трифонов, кандидат технических наук, доцент
Ижевский государственный технический университет имени М. Т. Калашникова
Точность токарно-винторнезных станков
Исследование и прогнозирование точности токарно-винторезных станков является актуальным в области металлообработки [1]. Точность деталей, получаемых при обработке на токарно-винторезных станках, зависит от погрешности обработки (под погрешностью обработки понимают отклонение полученного при обработке значения геометрического или другого параметра от заданного [3]) и допуска (допуск – разность между наибольшим и наименьшим предельными размерами или абсолютная величина алгебраической разности между верхним и нижним отклонениями [3]). Погрешность обработки является следствием геометрических и кинематических неточностей станка, недостаточной жесткости, неточности и износа режущего инструмента, а так же температурной деформации системы и т. п. [2].
181

Причины возникновения погрешностей обработки:
‒ в процессе резания на режущий инструмент действуют силы Рx, Рy, Рz, что в сумме вызывает динамическую ошибку. Эта ошибка присутствует всегда;
‒ в процессе изготовления станины токарно-винторезных станков возникают внутренние напряжения. В случаях, когда напряжения по станине распределены не равномерно, происходит деформация;
‒ в сочетание погрешностей деталей станка.
Суммарная погрешность механической обработки [2]:
= у + т.р + о.д + о.и + ст + поз + и + x t ,
где у – погрешности обработки, возникающей в результате упругих де-
формаций технологической системы станок – приспособление – заготовка
– инструмент (СПИД), под влиянием сил резания; т.р и о.д – погрешно-
сти обработки в результате температурных деформаций резца и детали;о.и – погрешности обработки в результате размерного износа режущего
инструмента; ст – погрешности, обусловленные геометрическими неточностями станка; поз – погрешности отработки команд управления
станком или точности позиционирования; и – погрешности, |
появляю- |
щиеся в результате замены затупившегося инструмента; x t – |
система- |
тические погрешности. |
|
Погрешности, возникающие в результате температурных деформаций резца (мкм), т.р
т.р cт.р LSр va1 sbt c ,
где Lp – вылет резца, мм; S – сечение державки резца, мм2; cт.р – коэффи-
циент, зависящий от материала резца и условий работы; v – скорость резания, м/мин; s – подача, мм/мин; t – глубина резания, мм; a1 ,b,c – показатели степени.
Погрешность от температурных деформаций детали (мкм), о.д , т.д ‒ при растачивании
о.д cт.д |
|
t Dl |
; |
|||||
|
|
|
|
|
|
|||
|
sb m |
|||||||
|
|
|
|
|||||
‒ при обтачивании |
|
|
|
|
|
|
|
|
т.д |
1,5 103 t 0,56 |
|
||||||
|
|
, |
|
|||||
v0,34s |
|
|
||||||
|
0,54D |
|
||||||
|
182 |
|
|
|
|
|

где D, l – соответственно диаметр и длина растачивания, мм; m – масса детали, кг.
Погрешность износа резца (мкм)
и.о
и.о
|
|
L |
k |
|
|
2И |
|
рез |
|
||
0 |
1000 |
н |
|||
|
|
||||
|
|
|
|
1
,
где |
Lрез |
‒ путь резания, м; |
kн |
‒ коэффициент начального износа; |
И0 |
– |
относительный износ, мкм/км;
И0 cи vm snt p k a k y k z
Погрешность от упругих деформаций системы (мкм) у
|
|
2Р |
|
( j |
|
М j |
|
N |
1000 |
|
Dl |
k |
) , |
у |
у |
пб |
зб |
|
|
||||||||
|
|
|
|
|
3EJ |
|
G |
1 |
|
||||
|
|
|
|
|
|
|
|
|
|
|
|
||
где Py – радиальная составляющая силы резания, дН; |
jпб , jзб – податли- |
вость упругой системы, мкм/дН; cu, cт.д – коэффициенты, зависящие от материала заготовки и резца; M, N ‒ коэффициенты, учитывающие деформацию деталей и их соединений в устройстве закрепления режущего инструмента.
Систематические погрешности являются разностью математических ожиданий выходных и входных переменных систем. При некорригированных входных воздействиях данное определение распространяется и на многомерные системы
mxн
Для линейной системы
x t |
n |
|
|
|
|
t , |
|
c |
rx |
m |
xн |
||
|
r |
0 |
|
|
||
|
|
|
|
|
где xt ‒ значение систематической ошибки по координате х; mхн ‒ про-
изводная степени r от математического ожидания входной переменной mхн , сrx ‒ коэффициент ошибки по координате х;
Итак, погрешность обработки на токарно-винторезных станках, есть суммарная векторная величина ошибки, определяемая многими физическими процессами, возникающими в процессе снятия стружки, в длительном процессе релаксации напряжений в несущих конструкциях под действием тепловых процессов.
Список литературы
1.Пуш, В.Э. Металлорежущие станки / В.Э. Пуш. - М : Машиностроение,
1985. - 256.
2.Монахов, Г.А. Станки с программным управлением /справочник / Г.А. Монахов, А.А. Оганян, Ю.И. Кузнецов. - М : Машиностроение, 1975. - 288.
183
3. Косилова, А.Г. Справочник технолога –машиностроителя / А.Г. Косилова, Р.К. Мещеряков. - М : Машиностроение, 1986. - 496.
Г. В. Русинов, аспирант; Е. С. Земерев, аспирант
В. И. Малинин, доктор технических наук, профессор А. В. Шатров, главный инженер
ООО «Лаборатория Эффективных Материалов» Пермский национальный исследовательский политехнический университет
Устройство форкамеры установки синтеза нанооксида алюминия
Получение дисперсных нанооксидов методом сжигания порошка алюминия, исследовалось на экспериментальной установке [1], созданной в ОКБ «Темп» при ПГТУ. Основными узлами установки является система подачи, форкамера (ФК), камера сгорания (КС) и устройство отбора дисперсных продуктов. В форкамере происходит смешение порошка истекающего из выпускного отверстия системы подачи с окислителем, воспламенение и первичное горение смеси.
Ранее [1] в качестве теплозащиты стенок ФК применялся абляционный материал (полиметилакрилат), который при воздействии высоких температур газифицировался и происходило разложение покрытия в процессе работы с уносом продуктов разложения потоком смеси воздуха и порошка алюминия.
Применение теплозащиты данного типа было оправдано только для экспериментальной установки. Однако для опытно-промышленной установки она неприемлема, так как имеет ряд недостатков:
−неспособность осуществления непрерывной работы, так как теплозащитное покрытие полностью выгорает в течение короткого промежутка времени;
−невозможность получения высокочистого целевого продукта, поскольку сгорание теплозащитного покрытия приводит к его загрязнению.
В качестве решения данной проблемы, в работе [2] было принято использование транспирационной системы охлаждения. Данный тип охлаждения является наиболее эффективным, поскольку подача охладителя осуществляется непосредственно сквозь стенку самой ФК, тем самым не только охлаждая внутреннюю поверхность, но и препятствует налипанию на нее конденсированной фазы. Однако высокопористые материалы (пористость 80…90%), предлагаемые в работе [2] обладают следующими недостатками: излишней проницаемостью, обусловленной высокой пористостью материала, которая приводит к неоднородности подачи охладителя; сложностью механической обработки материалов. Кроме того в [2] предлагаются материалы на основе веществ (графит, углерод-углерод)
184
которые в процессе горения приводят к загрязнению целевого продукта. В качестве пористого материала для транспирационного охлаждения
ФК в данной работе принято использование микрофильтрационной пористой керамики на основе электрокорунда (α-оксида алюминия). Керамический фильтр обладает пористостью на уровне 30-38% с размером пор от 25 до 44мкм., данные параметры обеспечивают достаточную проницаемость, чтобы обеспечить равномерность подачи газа по всей длине ФК, не создавая излишнего сопротивления. Помимо этого керамика обладает повышенной стойкостью к высоким температурам, что особенно важно для обеспечения длительной работы форкамеры.
По результатам исследовательской работы [3] выявлено, что применение в качестве охладителя инертного газа аргона, наиболее эффективно и приемлемо для чистоты целевого продукта. В этом случае применение смеси Al+O2+Ar позволило добиться следующих результатов:
‒снижение температуры продуктов первичного горения;
‒уменьшение доли конденсированной фазы;
‒увеличение количества газообразного алюминия поступающего в КС для дальнейшего синтеза;
‒повышение чистоты конечного продукта.
Применение метода воспламенения описанного в [1] не оправдано ввиду загрязнения конечного порошка нанооксида алюминия продуктами сгорания металлизированного смесевого топлива. Поэтому в качестве воспламенителя для металловоздушной смеси в форкамере принято использование электрической дуги [4], как наиболее просто реализуемого способа. Предлагаемый в модернизированной установке воспламенитель представляет собой два неплавящихся электрода рисунок 1, вид А-А, способных выдержать температуру электрической дуги. Во время запуска установки подается напряжение на электроды воспламенителя и возникает дуговой разряд, который в свою очередь воспламенит металлогазовую смесь порошка алюминия. Основной недостаток данного метода – налипание конденсированной фазы на поверхность электродов.
На рис. 1 представлена схема предлагаемой конструкции форкамеры с транспирационной системой охлаждения. Данная схема работает следующим образом: через отверстия 6 подается аргон, газ постепенно заполняет свободное пространство 3 и за счет создаваемого сопротивления пористой структурой ФК 2, аргон равномерно заполняет среднюю ее часть. Затем через отверстия 5 осуществляется подача кислорода, после чего на электроды воспламенителя 2 подается напряжение, возникает дуговой разряд, который в свою очередь воспламеняет металлогазовую смесь порошка алюминия, подаваемую через узел подачи 4. Созданный поток воспламененной смеси заполнит все внутреннее пространство ФК 2, а аргон, подаваемый сквозь пористую стенку форкамеры, снизит температуру стенки и удалит конденсированную фазу от ее внутренней поверхности, что обеспечит продолжительную и стабильную работу установки.
185
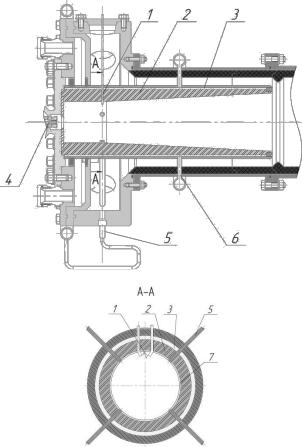
Рис. 1. Схема форкамеры с транспирационной системой охлаждения.
1 – воспламенитель, 2 – форкамера из пористой керамики, 3 – полость между ФК и корпусом, 4 – узел подачи порошка алюминия, 5 – узел подачи кислорода, 6 – узел подачи аргона, 7 – поверхностный слой аргона.
Конструкция ФК такова рис. 1, что аргон подается по всей длине пористой стенки, в том числе через «холодный» участок, находящийся на входе в устройство. Общий расход аргона состоит из расхода через «холодный» и «горячий» (охлаждаемый) участки пористой стенки. Расход через «холодный» участок физически не ограничен, а расход через «горячий» участок не может иметь значение ниже предельного. Это значение определяется расчетом. Однако результаты расчета зависят от термодинамического состояния (замороженное или равновесное) продуктов сго-
186
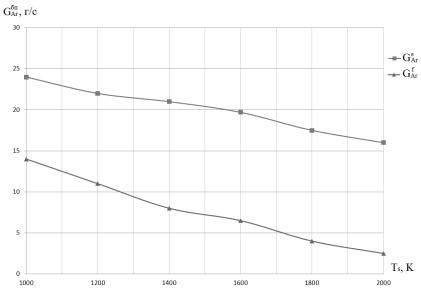
рания у внутренней поверхности «горячей» стенки ФК. Расход охладителя при замороженном состоянии внутренней поверхности стенки GfAr, а равновесном состоянии – GeAr. Реальный расход охладителя сквозь «горячую» стенку ФК будет иметь промежуточное значение между GfAr и GeAr. Результаты расчетов GfAr (замороженное состояние) и GeAr (равновесное состояние) приведены на рис. 2.
Рис. 2. Зависимость расхода Ar через «горячую» стенку ФК от ее температуры для предельных состояний (замороженного и равновесного) при параметрах общего расхода 50 г/с.
Расход аргона через горячую стенку принимается максимальным из приведенных расчетов, что соответствует равновесному состоянию продуктов сгорания на внутренней поверхности стенки ФК. Общий расход аргона G∑Ar (через «холодный» и «горячий» участок) в расчетах был принят постоянным, равным 50 г/с.
В результате проектных работ была модернизирована форкамера установки синтеза нанооксида алюминия со следующими изменениями:
−в качестве материала форкамеры для транспирационного охлаждения применена микрофильтрационная керамика;
−конструкция форкамеры была адаптирована для применения металлогазовой смеси подобранной в работе [3];
−проведены оценочные расчеты количества подаваемого аргона, требуемого для эффективного охлаждения стенок форкамеры.
187
Список литературы
1. Малинин, В.И. Внутрикамерные процессы в установках на порошкообразных металлических горючих / В.И. Малинин. - Екатеринбург - Пермь: УрО РАН,
2006.
2.Крюков, А.Ю. Адаптация внутрикамерных процессов и элементов конструкции энергоустановок на порошковом горючем к технологиям получения ультра– и нанодисперсных материалов / А.Ю. Крюков. - Пермь : ПНИПУ, 2011. –
236 c.
3.Болховских, Д.А. Адаптация внутрикамерных процессов и элементов конструкции энергоустановок на порошковом горючем к технологиям получения ультра– и нанодисперсных материалов / Д.А. Болховских, В.И. Малинин, Р.В. Бульбович // Вестник ПНИПУ. Аэрокосмическая техника. - 2012. - 33. - 109-123.
4.Бобров, А.Н. Воспламенение и горение двухкомпонентной газовзвеси порошкообразного горючего и окислителя / А.Н. Бобров, Д.А. Ягодников, И.В. Попов // Физика горения и взрыва. - 1992. - Т. 28, №5. - 3-5.
А. Н. Рыбин, студент
Ф. А. Уразбахтин, доктор технических наук, профессор Ижевский государственный технический университет имени М. Т. Калашникова, Воткинский филиал
Особенности конструктивно-компоновочных схем головных частей ракет и ракет-носителей
Головная часть (ГЧ) ракеты необходима для защиты полезной нагрузки (ПН) от внешних воздействий при хранении, транспортировке и эксплуатации. В ходе развития ракетной техники накоплено большое количество конструктивно-компоновочных схем (ККС) ГЧ в зависимости от назначения. Исследование является чрезвычайно важной задачей в ракет- но-космической отрасли, начало которой производится с ранжирования ККС ГЧ и определения особенностей и недостатков каждой схемы.
ККС ГЧ классифицируют по следующим признакам (таблица):
1)отделяемость от корпуса (отделяемая/неотделяемая);
2)вариант исполнения (моноблочная/разделяющаяся);
3)расположение отсеков (последовательное/параллельнопоследовательное/комбинированное);
4)управляемость (управляемые/неуправляемые) и др.
Основными недостатками неотделяемых ГЧ является подверженность сносу на атмосферном участке траектории, бóльшая степень обнаружения для радиолокационных систем (РЛС). Однако такие конструкции имеют высокую степень надежности в силу простоты исполнения. В наибольшей степени проявляют свойства, отделяемые в конце активного участка ГЧ.
188
Таблица. Морфологическая таблица классификационных признаков
Тип головной |
Управляе- |
Назначение |
Форма головного |
Схема |
|
части |
мость |
обтекателя |
ДУ ГЧ |
||
|
|||||
|
|
научно- |
|
|
|
Неотделяе- |
управляемые |
исследовательское; |
одноконусная |
‒ |
|
мая ГЧ |
хобби (спорт); |
||||
|
|
|
|||
|
|
сигнальные ракеты |
|
|
|
Отделяемая |
|
|
одноконусная; |
|
|
|
военное; |
двухконусная; |
|
||
моноблочная |
управляе- |
тяну- |
|||
транспортное (кос- |
цилиндрокониче- |
||||
ГЧ |
мые; |
щая; |
|||
монавтика); |
ская |
||||
|
неуправляе- |
толка- |
|||
Отделяемая |
научно- |
|
|||
мые |
одноконусная; |
ющая |
|||
разделяюща- |
исследовательское |
||||
|
двухконусная |
|
|||
яся ГЧ |
|
|
|
||
|
|
|
|
Для ГЧ данного типа подверженность сносу минимальна, значительная скрытность от РЛС, высокая точность, управляемость на конечном участке траектории. Разделяющиеся ГЧ (РГЧ) имеют (по сравнению с моноблочной ГЧ) меньший коэффициент заполнения, в силу дифференциации полезного объема. В зависимости от типа применяемой двигательной установки (ДУ) на РГЧ взаимное расположение отсеков ГЧ делится на три класса: А) с последовательным расположением (П); Б) с последовательнопараллельным расположением (ПП); В) с комбинированным (К).
Для обеспечения выбора рационального конечного варианта исполнения ГЧ из нескольких альтернативных вариантов необходимо рассматривать различные ККС ГЧ и ракеты в целом, количество элементов оснащения ГЧ, типа носителя и ряда других факторов. Качественный анализ ККС ГЧ позволяет выявить характерные каждому классу достоинства и недостатки, сформулировать оценку применимости ГЧ того или иного класса на носителях различного типа (ЖРД/РДТТ).
С. С. Савин, инженер научно-исследовательской лаборатории «Прогрессивные технологические процессы пластического деформирования» НИЛ-41
А. Г. Шляпугин, кандидат технических наук, доцент Самарский государственный аэрокосмический университет имени академика С. П. Королева, Самара
Особенности моделирования процесса обжима-раздачи в программе DEFORM-2D
При разработке современных технологических процессов получения деталей различного назначения, все чаще и чаще применяют компьютерное моделирование.
В настоящее время существует большой ассортимент программных продуктов для решения различных задач моделирования, которые дают
189
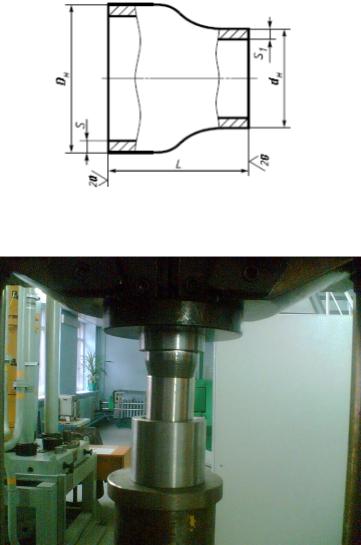
достаточно хорошие результаты в разработке технологии, в частности программа DEFORM-2D.
Данная работа направлена на оценку влияния различных параметров описания задачи в программе DEFORM-2D.
Рассматривался технологический процесс обжима-раздачи трубной заготовки для получения детали типа – переход концентрический. Типовая конструкция этой детали представлена на рис. 1.
Рис. 1. Переход концентрический
Для оценки результатов моделирования их сравнения был проведен эксперимент рис. 2. Заготовкой для получения перехода являлась труба из стали 12Х18Н10Т диаметром 50 мм, толщиной стенки 1,5 мм.
Рис. 2. Процесс обжима-раздачи трубной заготовки.
190
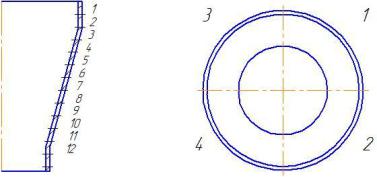
Для измерения изменения толщины на заготовку предварительно была нанесена координатная сетка состоящая из четырех продольных прямых и двенадцати поперечных линий с шагом 5 мм (рис. 3).
Рис. 3. Координатная сетка на заготовке.
При измерении разнотолщинность усреднялась по продольным сечениям заготовки.
При моделировании влияние скорости деформации на процесс деформирования не рассматривалось. Поскольку рассматривался процесс холодной штамповки, изменение свойств материала в зависимости от температуры тела не учитывалось. Свойства материала задавались для температуры тела 20 °С. В исследовании не принималась во внимание деформация инструмента, считалось, что инструмент ведет себя как абсолютно твердое тело. В то время как заготовка деформируется только пластически.
В данной работе исследовалось влияние количества конечных элементов (КЭ) на точность расчета, так же исследовалось влияние размера шага расчета относительно величины ребра конечного элемента и влияние коэффициента трения.
Достоверность результатов в моделировании подтверждалась оценкой напряженного состояния и изменения объема заготовки. Изменение объема детали в вычислительном эксперименте не должно превышать значе-
ния 10‒15 %.
191
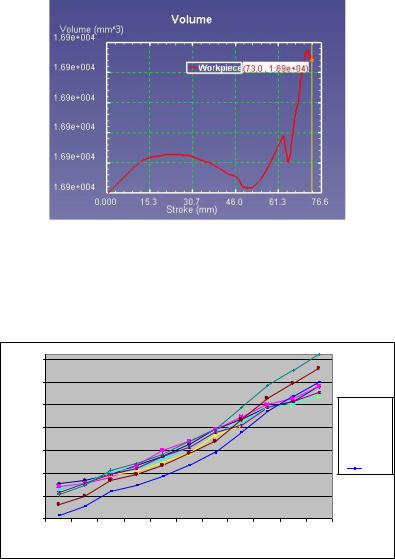
Рис. 4. График изменения объема заготовки.
Из графика на рис. 4 видно, что изменение объема заготовки происходит в пределах третьего знака, из этого следует, что допустимое значение изменения объема не превышено.
Для определения оптимальных параметров последующих расчетов были рассчитаны задачи с разным числом конечных элементов по толщине стенки, от 3 до 15 (рис. 5).
Sдеф/ So
1,22 |
|
|
|
|
|
|
|
|
|
|
1,17 |
|
|
|
|
|
|
|
|
|
|
1,12 |
|
|
|
|
|
|
|
|
|
|
1,07 |
|
|
|
|
|
|
|
|
|
|
1,02 |
|
|
|
|
|
|
|
|
|
|
0,97 |
|
|
|
|
|
|
|
|
|
|
0,92 |
|
|
|
|
|
|
|
|
|
|
0,87 |
|
|
|
|
|
|
|
|
|
|
1 |
2 |
3 |
4 |
5 |
6 |
7 |
8 |
9 |
10 |
11 |
|
|
|
|
|
№ сечения |
|
|
|
|
|
3КЭ
5КЭ
7КЭ
10КЭ
15КЭ
Эксп.
2,50% -2,50%
Рис. 5. График зависимости разнотолщинности от количества КЭ по толщине стенки детали
Из графика рис. 5 можно сделать вывод, что существенных отличий от экспериментальных данных нет, в основном все кривые равноудалены от экспериментальной, следовательно отпадает нужда в задании большого количества КЭ по толщине, что существенно сокращает машинное время расчета.
192
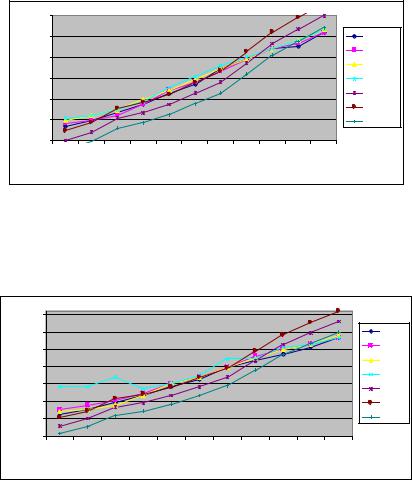
Так же были рассчитаны задачи с различными величинами шага расче- |
|||||||||||
та относительно длинны ребра минимального конечного элемента (рис. 6). |
|||||||||||
|
1,2 |
|
|
|
|
|
|
|
|
|
|
|
1,15 |
|
|
|
|
|
|
|
|
|
1/5 ребра |
|
1,1 |
|
|
|
|
|
|
|
|
|
1/3 ребра |
|
|
|
|
|
|
|
|
|
|
1/2 ребра |
|
Si/So |
|
|
|
|
|
|
|
|
|
|
|
1,05 |
|
|
|
|
|
|
|
|
|
ребро |
|
|
|
|
|
|
|
|
|
|
|
Эксп. |
|
|
1 |
|
|
|
|
|
|
|
|
|
|
|
|
|
|
|
|
|
|
|
|
2,50% |
|
|
|
|
|
|
|
|
|
|
|
|
|
|
0,95 |
|
|
|
|
|
|
|
|
|
-2,50% |
|
0,9 |
|
|
|
|
|
|
|
|
|
|
|
1 |
2 |
3 |
4 |
5 |
6 |
7 |
8 |
9 |
10 |
11 |
|
|
|
|
|
|
№ сечения |
|
|
|
|
|
Рис. 6. График зависимости разнотолщинности от величины шага расчета. |
Здесь результаты совпадают с рекомендациями разработчиков, наиболее близкое описание дает кривая, полученная при шаге 1/3 от ребра КЭ, однако и остальные кривые, не показывают особо грубых отклонений, зависимость линейна и с увеличением размера шага падает точность.
Влияние коэффициента трения на процесс представлено на рис. 7.
|
1,22 |
|
|
|
|
|
|
|
|
|
|
|
1,17 |
|
|
|
|
|
|
|
|
|
0,05 |
|
1,12 |
|
|
|
|
|
|
|
|
|
0,1 |
|
|
|
|
|
|
|
|
|
|
|
|
Si/So |
1,07 |
|
|
|
|
|
|
|
|
|
0,15 |
|
|
|
|
|
|
|
|
|
0,3 |
||
|
|
|
|
|
|
|
|
|
|
||
1,02 |
|
|
|
|
|
|
|
|
|
|
|
|
|
|
|
|
|
|
|
|
|
эксп. |
|
|
|
|
|
|
|
|
|
|
|
|
|
|
0,97 |
|
|
|
|
|
|
|
|
|
2,50% |
|
0,92 |
|
|
|
|
|
|
|
|
|
-2,50% |
|
0,87 |
|
|
|
|
|
|
|
|
|
|
|
1 |
2 |
3 |
4 |
5 |
6 |
7 |
8 |
9 |
10 |
11 |
|
|
|
|
|
|
№сечения |
|
|
|
|
|
|
Рис. 7. График зависимости разнотолщинности от коэффициента трения. |
Как видно из графика, наиболее сильная погрешность наблюдается у кривой с коэффициентом трения 0,3. Она достаточно далеко выходит за границы доверительного интервала. При других величинах коэффициента трения погрешность присутствует уже неявно. Наиболее точный результат показывает кривая, полученная при коэффициенте трения равном 0,15.
В данной работе были проанализированы следующие параметры, влияющие на точность моделирования процесса обжима-раздачи: количество
193
КЭ по толщине заготовки, коэффициент трения, шаг расчета. Результаты позвонили определить оптимальные значения параметров, при которых теоретический расчет совпадал с практикой. В дальнейшем эти результаты будут полезны при разработке технологий для всех типоразмеров концентрических переходов.
Список литературы
1.Гречников Ф.В. Использование программы DEFORM-2D для описания процессов листовой штамповки / Ф.В. Гречников, А.Г. Шляпугин, К.А. Николенко; Самар. гос. аэрокос. универ-т. – Самара, 2006. – Деп. в ВИНИТИ «Депонированные научные работы» 15.06.2006, №804-В2006.
2.Шляпугин А.Г. Моделирование процесса обжима в программе DEFORM2D / А.Г.Шляпугин; Самар. гос. аэрокос. универ-т. – Самара, 2012. – Деп. в ВИНИТИ «Депонированные научные работы» 17.01.2012, №8-В2012.
Д. В. Савин, магистрант В. А. Михеев, доктор технических наук, профессор
Самарский государственный аэрокосмический университет имени академика С. П. Королева, Самара
Моделирование процесса формообразования обтяжкой крупногабаритных листовых деталей обшивок сложных геометрических форм с учетом реологического состояния алюминиевого сплава
Освоение новых процессов формообразования обтяжкой в определенной степени сдерживается слабой изученностью реологии поведения алюминиевого сплава в отожженном, особенно в свежезакаленном состоянии. Кроме того, отсутствуют сведения о влиянии того или иного реологического состояния на напряженно-деформированное состояние очага деформации в этих процессах, определяющее характер поведения деформируемой листовой заготовки и формирование качества готового изделия.
Любой деформируемый металл может быть представлен в виде набора элементарных моделей: упругости, вязкости и пластичности [1]. На наш взгляд, наиболее точно поведение деформируемого тела во всем его многообразии отражает среда, где «пружина», описывающая деформационное упрочнение включена последовательно с вязким элементом, моделирующим диффузионно релаксационные процессы. Если деформация листовой заготовки при формообразовании протекает при таких условиях, когда диффузионно релаксационные процессы заторможены, то работой вязкого элемента можно пренебречь и рассматривать модель упругопластического тела с деформационным упрочнением.
194
Для сравнения различных реологий поведения алюминиевого листового материала используем результаты моделирования в программном комплексе ANSYS/LS-DYNA процесса формообразования обтяжкой анизотропной листовой заготовки, прежде всего, в состоянии упругопластического тела при деформационном упрочнении. В качестве реологической модели материала для заготовки была использована трехпараметрическая ЕPD-модель Барлата (3-Parameter Barlat Model) - модель, применяющаяся для моделирования алюминиевого листового материала в условиях плоского напряженного состояния. Для этой реологии материала необходимо было предварительно создать локальную систему координат с учетом направления прокатки листовой заготовки. Свойства материала заготовки по модели ЕPD-Барлата сведем в табл. 1.
Таблица 1. Свойства материала заготовки по трехпараметрической модели Барлата
Параметр |
Обозначение |
Размерность |
Значение |
|
параметра |
||||
|
|
|
||
Плотность |
DENS |
кг/м3 |
2700 |
|
Модуль упругости |
ЕХ |
Па |
7,2E+010 |
|
Коэффициент Пуассона |
NUXY |
– |
0,35 |
|
Тип критерия упрочнения |
HardeningRule |
– |
1 |
|
Тангенциальный модуль |
Tang Mod |
Па |
7E+008 |
|
Предел текучести |
Yld Strs |
Па |
1,12E+008 |
|
Значение экспоненты Барлата |
Barlat Expon |
– |
6 |
|
(R00) |
Width ratio-orig |
– |
0,613 |
|
(R45) |
Width ratio-45 deg |
– |
0,818 |
|
(R90) |
Width ratio-90 deg |
– |
0,639 |
|
Номер локальной системы |
CSID |
– |
2 |
|
координат материала |
||||
|
|
|
Вмоделировании, результаты которого приведены в работах [2, 3], было уделено, прежде всего, внимание симметричной обтяжки за счет внешней симметрии формообразующего пуансона относительно главных плоскостей и направлений в «полюсе» оболочки двойной кривизны. Они также совпадают с направлениями анизотропии листовой заготовки:
вдоль RD (rolling direction) и поперек TD (transverse direction) направления прокатки листа.
Врезультате была исследована кинематическая схема последовательной обтяжки в условиях симметричной обтяжки, совмещающая процессы обтяжки: предварительная обтяжка плоской заготовки на полный угол охвата формообразующего контура пуансона и последующая обтяжка заготовки изометрической формы, полученной после свободного разгиба предварительно отформованной оболочки до определенного угла по формообразующему контуру пуансона. Это же кинематическая схема в условиях симметричной обтяжки была исследована и по другой реологической модели в состоянии упруго-вязкопластического тела.
195
В качестве следующей реологической модели материала для заготов-
ки используется EVP-модель (Elastic Viscoplastic Thermal Model), позво-
ляющая учитывать внутреннее трение с необратимым переходом упругой энергии в тепло. Это сложная реологическая модель упруговязкопластической среды. Малые напряжения при обработке давлением, высокая пластичность и формуемость легко объясняет способность сплава при рассматриваемом реологическом состоянии к вязкому течению. Модель EVP среды может описывать реологию листового материала при формообразовании в широком диапазоне скоростей деформации.
Принимаемая модель может описывать реологию упруговязкопластического поведения материала, проявляющую эффекты квазипластического деформирования. Они могут быть связаны с активацией диффузии по границам или вблизи границ зерен. С реологической точки зрения упруго-вязкопластическое течение материала может быть приписано квазижидкой фазе деформируемого материала. Свойства материала упруго-вязкопластического поведения сведем в табл. 2, 3, и 4.
Таблица 2. Свойства материала заготовки по ЕVP-модели упруго-
вязкопластического поведения материала заготовки
Параметр |
Обозначение |
Размерность |
Значение пара- |
|
метра |
||||
|
|
|
||
Плотность |
DENS |
кг/м3 |
2 700 |
|
Коэффициент теплового |
ALPX |
м/м-C |
2,1E-005 |
|
расширения |
||||
|
|
|
||
Модуль упругости |
ЕХ |
Па |
7,2E+010 |
|
Начальное напряжение |
In Yld Strs |
Па |
1,12E+008 |
|
|
LCID1 |
– |
1 |
|
Номер кривой нагружения |
LCID2 |
– |
2 |
|
LCID3 |
– |
3 |
||
|
||||
|
LCID7 |
– |
7 |
Кривая нагружения представляет собой функциональную зависимость параметров и задается соотношением таблиц с данными о значениях этих параметров. Для данного материала задаются четыре кривые нагружения:
−LCID1 – функция зависимости эффективного напряжения (Effective stress) от эффективной пластической деформации (Effective plastic strain).
−LCID2 – функция зависимости модуля упругости (Elastic modulus)
от температуры (Temperature).
−LCID3 – функция зависимости коэффициента Пуассона (Poisson's ratio) от температуры.
−LCID7 – функция зависимости коэффициента теплового расшире-
ния (Coefficient of thermal expansion) от температуры.
196
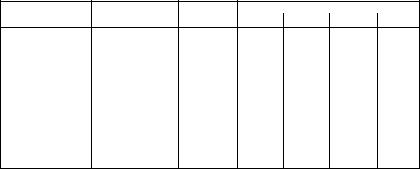
Таблица 3. Значения параметров кривой нагружения 1 (LCID1)
Параметр |
Обозначение |
Размерность |
|
|
Номер значения |
|
|||
1 |
2 |
|
3 |
4 |
5 |
6 |
|||
|
|
|
|
||||||
Эффективное |
STRESS |
МПа |
0 |
340 |
|
375 |
405 |
423 |
438 |
напряжение |
|
||||||||
|
|
|
|
|
|
|
|
|
|
Эффективная |
|
|
|
|
|
|
|
|
|
пластическая |
STRAIN |
– |
0 |
0,05 |
|
0,1 |
0,15 |
0,2 |
0,3 |
деформация |
|
|
|
|
|
|
|
|
|
Таблица 4. Значения параметров кривых нагружения 2, 3 и 7 (LCID2, 3 и 7)
Параметр |
Обозначение |
Размер- |
|
Номер значения |
|
||
ность |
1 |
2 |
3 |
4 |
|||
|
|
Модуль упруго- |
EX |
МПа |
67 000 |
66 000 |
65 000 |
52 500 |
|
сти |
|||||||
|
|
|
|
|
|
||
Температура |
TEMP_EX |
°C |
100 |
125 |
150 |
175 |
|
Коэффициент |
NUXY |
– |
0,3137 |
0,3195 |
0,3252 |
0,3478 |
|
Пуассона |
|||||||
|
|
|
|
|
|
||
Температура |
TEMP_NUXY |
°C |
100 |
170 |
240 |
310 |
|
Коэффициент |
|
|
|
2,94E- |
4,85E- |
11,7E- |
|
теплового рас- |
ALPHA |
м/м-C |
2,1E-005 |
||||
005 |
005 |
005 |
|||||
ширения |
|
|
|
||||
|
|
|
|
|
|
||
Температура |
TEMP_ALPHA |
°C |
100 |
200 |
300 |
390 |
Результаты моделирования одной и той же кинематической схемы в условиях симметричной обтяжки, но при различных реологических моделях материала приведены на рис. 1 и 3: ЕPD-модель Барлата упругопластического поведения при деформационном упрочнении (слева на рис. 1)
иЕVPмодель упруго-вязкопластического поведения (справа на рис. 1). Для контроля и сопоставления значений деформации по времени про-
цесса формообразования, обеспечивающего совмещение предварительной и последующей обтяжки, были выбраны характерные точки на поверхности оболочки: A, B, C (9751, 9551, 5051) – на контуре центрального поперечного сечения, начиная с краю, в середине и в «полюсе» оболочки и D, E, F (5072, 5082, 5090) ‒ на формообразующем продольном контуре вниз в сторону зажимов пресса, начиная с точки перехода криволинейной части контура на прямолинейную часть, в середине и в районе схода контура с пуансон (рис. 1).
Для просмотра результатов расчета использовался постпроцессор LS- PrePost-3.2. При сравнении результатов моделирования по «цветной палитре» распределения деформации по поверхности формуемой оболочки на отдельных этапах процесса обтяжки (рис. 1) видно, что при осуществлении той же кинематической схемы «картины» отличаются, прежде всего, нарушением их симметрии. Симметрия есть качественная характеристика любого тела, в частности листовой заготовки, и является отражением той или иной инвариантности или детерминированности принимаемой реологической модели материала заготовки.
197
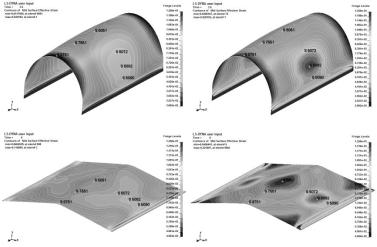
Реальная осуществимость обтяжки без локализации растяжения, в свою очередь, обусловлена свойствами симметрии листового материала вообще и оболочки в частности. В общем случае для анизотропного листа существуют три основных направления показателей анизотропии, одно из которых совпадают с направлением прокатки, а два других ортогональны к нему: по ширине и толщине листовой заготовки. Поэтому такое совпадение направления обеспечило кинематическую управляемость процессом формообразования оболочки. Это подтверждают графики деформации (рис. 2а) в характерных точках поверхности оболочки. Если обратить внимание на их правый край, где графики точек B, C, D, E и F сходятся к значению к значению деформации, равной, примерно, 0,13, что хорошо укладывается в допуск, определяемый требованиями к качеству деталей обшивок.
Вреальных условиях процесс пластического деформирования рассматривается как конкуренция двух противоположных, взаимосвязанных
иодновременно протекающих в деформируемых объемах факторов, одинаково необходимых для материала заготовки и обеспечивающих ее стационарное устойчивое реологическое состояние. При этом первый фактор связан с деформационным упрочнением материала, а второй – с релаксационными эффектами, сопровождающимися необратимым переходом упругой энергии в тепло.
Вэтом и проявляется степень неопределенности в поведении деформируемого материала, что подчеркивает асимметричный характер результатов моделирования вязкопластического течения материала при распределении значений деформации по поверхности формуемой оболочки на отдельных этапах последовательной обтяжки (рис. 1).
а) |
г) |
б) |
д) |
198
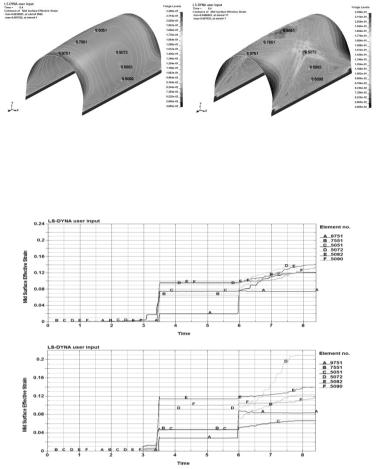
в) е)
Рис. 1. Сравнение данных по деформации на следующих этапах: после первой обтяжки на угол 90° (а, г), после разгиба детали на угол 12° и ее растяжения (б, д),
в конце операции формовки (в, е).
а, б, в ‒ распределение деформации для 1 модели материала; г, д, е ‒ распределение деформации для второй модели материала.
а)
б)
Рис. 2. Графики изменения деформации для первой (а) и второй (б) модели материала в ее характерных точках
При анализе результатов моделирования проявились соответствия со случаями, наблюдаемыми на практике разрывы листовой заготовки в процессе ее формообразования (рис. 3). Однако этот разрыв не является характерным для данного материала. Списывали его на случайность, хотя внешняя симметрия формообразующего пуансона относительно главных плоскостей и направлений в «полюсе» оболочки двойной кривизны была полностью под контролем системы управления обтяжного пресса.
Случайность или неопределенность можно отнести к поведению деформируемого материала. На практике известно, что механические характеристики материала усредняют в пределах поступившей партии, состоящей из определенного количества листов, реологическое состояние кото-
199
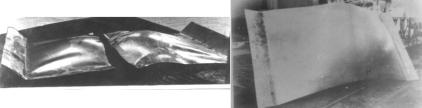
рых отожженное по факту поставки. Контроль механических характеристик каждого листа на практике не проводится. При этом, отсутствует информация о том, что данный лист в той или иной степени имеет способность поглощать механическую энергию (работу) при деформировании. Эта способность называется вязкостью и является функцией прочности и пластичности материала. Данная характеристика имеет вероятностную природу и определяет, в принципе, долю «квазижидкой» фазы в структуре рассматриваемого материала.
а) б)
Рис. 3. Деталь оболочки двойной кривизны с возможным разрывом, полученным в процессе формообразования (а) и успешно изготовленная деталь обо-
лочки двойной кривизны (б)
Месторасположение разрыва, приведенное на рис. 3а, в той или иной степени имеет совпадение с поперечной линией, проходящей через точку D, указывающей на локализацию деформации в результатах моделирования упруго-вязкопластического поведения материала заготовки (рис. 1 и 2). Кроме того, если рассматривать распространение внешнего силового поля от зажимов пресса, то оно локализуется в средней части поверхности оболочки и район ее «полюса» (точка С) блокируется и не деформируется. Оценку вероятности данного разрыва можно выполнить по разрабатываемой нами методике, используя результаты моделирования по обеим реологическим моделям. Внедрение такой методики минимизирует вероятность разрыва листовой заготовки и обеспечит устойчивость процессов формообразования обтяжкой и качество получаемых деталей оболочек двойной кривизны рис. 3б.
Список литературы
1.Колбасников, Н.Г. Структура. Энтропия. Фазовые превращения и свойства металлов [Текст] : научное издание / Н. Г. Колбасников, С. Ю. Кондратьев. – СПб.: Наука, 2006. – 363.
2.Михеев, В.А. Выбор кинематической схемы формообразования обтяжкой обводообразующих оболочек сложной пространственной формы [Текст] / В. А. Михеев, Ю. С. Клочков, А. А. Кузина, А. Ф. Гречникова, Д. В. Савин // Вестник Самар. гос. аэрокосм. ун-т им. С. П. Королева (нац. исслед. ун-т). 2012. № 6-1. - 253160.
200
3. Михеев, В.А. Моделирование последовательной схемы формообразования обтяжкой обводообразующих оболочек двойной кривизны минимальной разнотолщинности [Текст] / В. А. Михеев, Ю. С. Клочков, А. А. Кузина, А. Ф. Гречникова, Д. В. Савин // Вестник Самар. гос. аэрокосм. ун-т им. С. П. Королева (нац. исслед. ун-т). 2012. № 6-1. - 260-266.
Э. Г. Сагитов, студент
А. А. Макушин, кандидат технических наук, доцент Филиал Казанского (Приволжского) Федерального Университета
в г. Набережные Челны
Изменение технического состояния головки блока цилиндров дизельного двигателя и износ его деталей в процессе эксплуатации
Исследование изменения технического состояния деталей и узлов автомобилей является актуальным направлением исследовательской деятельности в области технической эксплуатации автомобильной техники. А изучение изменения технического состояния головки блока цилиндров двигателя, как одной из важнейших составных частей механизма газораспределения двигателя, является одним из важных направлений в технической эксплуатации. Оно приобретает актуальность в современных условиях, когда увеличивается количество автомобильной техники и грузовых автомобилей с дизельными двигателями.
Головка блока цилиндров. Головка блока цилиндров является одной из составных частей механизма газораспределения. Она, как и механизм газораспределения в целом, предназначена для впуска в цилиндр свежего заряда и выпуска отработавших газов в строгом соответствии с тактами работы двигателя и положением поршня во время рабочего процесса.
Износ головки блока цилиндров. В процессе эксплуатации головка блока цилиндров подвергается различным негативным воздействиям. Она подвергается воздействию различных сил сопротивления, моментов и нагрузок. Кроме того, она подвержена воздействию агрессивной среды, создаваемой различными агрессивными химическими эксплуатационными жидкостями. Также головка в процессе эксплуатации подвергается воздействию высоких температур.
Все эти факторы воздействия на головку блока вызывают ее износ. Износ деталей головки блока вызывает потерю работоспособного состояния и снижение ресурса агрегата.
Воздействие агрессивных жидкостей. При работе двигатель нагрева-
ется. Для его охлаждения применяют охлаждающие жидкости. В головке блока имеются отверстия для циркуляции охлаждающей жидкости. При наличии дефектов корпуса, неточной сборке, неплотном прилегании деталей друг к другу, либо впоследствии длительной эксплуатации каналы для
201
циркуляции охлаждающей жидкости могут быть негерметичными. Данные дефекты могут вызывать попадание жидкости в образовавшиеся полости и в процессе длительной эксплуатации в данных местах образуются промоины, неровности поверхности.
Воздействие высоких температур. Во время работы двигателя его температура меняется в очень широких пределах. Причем изменение температуры может происходить в короткий промежуток времени. Такие значительные перепады температуры негативно влияют на состояние и работоспособность двигателя. На корпусе появляются трещины, детали ломаются, гнутся.
Образование нагара. В процессе работы двигателя, при сгорании топлива внутри него появляется нагар. Он оседает на детали двигателя, в частности на детали головки блока и оказывает негативное влияние на процесс работы двигателя. Продукты сгорания оседают на клапаны, кольца, седла клапанов и впускной и выпускной каналы головки. Осевший нагар вызывает сбои в работе двигателя и газораспределительного механизма, ухудшает процесс и условия работы, снижает его эффективность и мощность.
Для снижения и предотвращения воздействия данных негативных факторов, а также продления ресурса двигателя и механизма газораспределения проводят ремонт головки блока цилиндров.
Ремонт головки блока цилиндров двигателя производится с целью восстановления работоспособного состояния, продления ресурса агрегата, и обеспечения стабильности характеристик детали на протяжении всего срока ее эксплуатации. В процессе ремонта головки блока проводится ее дефектация с целью выявления всех дефектов. Затем проводят все необходимые ремонтные работы: восстанавливают повреждения корпуса и составных частей головки блока, заменяют вышедшие из строя детали новыми. После ремонта проводят испытание и контроль по проверке качества ремонта. После проведенного ремонта техническое состояние изделия соответствует требованиям нормативов, и оно готово к дальнейшей эксплуатации.
Возникающие при эксплуатации дефекты головки блока могут иметь различный характер и виды. Рассмотрим их на наглядных фотографиях
(рис. 1–6).
При ремонте головки блока могут быть использованы различные технологии ремонта. От расточки и фрезеровки, до наплавки металла в местах дефектов.
Одним из способов ремонта головки блока является наплавка металла в места дефектов корпуса (рис. 7). Наплавка металла производится на места промоин и вырывов металла. После наплавки деталь обрабатывается на станке до ремонтных размеров.
202
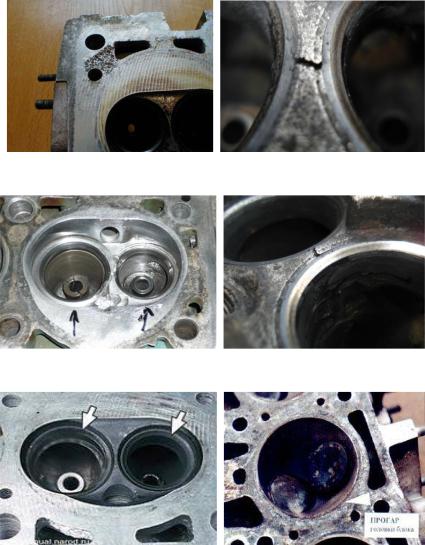
Рис. 1. Промоина головки блока |
Рис. 2. Трещина корпуса между |
|
клапанами |
Рис. 3. Дефекты головки и трещины |
Рис. 4. Трещина корпуса головки |
|
направляющих втулок |
Рис. 5. Дефекты седел клапанов |
Рис. 6. Прогар головки блока |
203
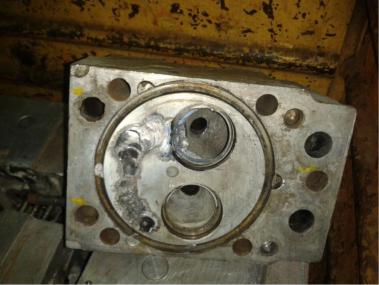
Рис. 7. Головка блока после наплавки металла в места дефектов
Таким образом, в процессе эксплуатации происходит изменение технического состояния, влекущее за собой ухудшение работоспособности и сокращение ресурса деталей и агрегатов. Проведение своевременного качественного технического обслуживания и квалифицированного ремонта с соблюдением всех требований, позволит замедлить процесс изменения технического состояния детали и продлит ее ресурс и срок безотказной эксплуатации. Дальнейшие исследования в этой области позволят повысить качество и продолжительность процесса эксплуатации автомобильной техники, снизить расходы на обслуживание и ремонт.
А. Н. Синицын, старший преподаватель В. В. Синицына, старший преподаватель
И. В. Абрамов, доктор технических наук, профессор Ижевский государственный технический университет имени М. Т. Калашникова
Анализ воздействий, возникающих при различных методах сборки
В настоящее время в расчетных схемах соединений с натягом (рис. 1) не учитываются дополнительные нагрузки, возникающие в зоне контакта в процессе сборки соединений и не связанные с натягом. Модели остаточного напряженно-деформированного состояния деталей при различных методах сборки не описаны.
204
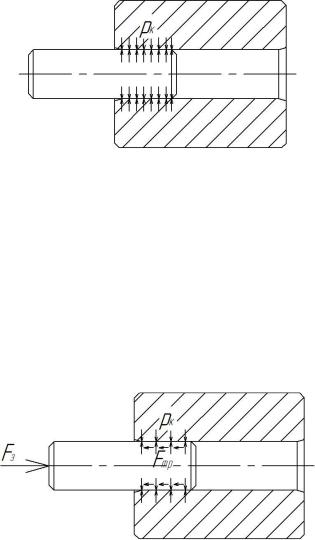
Рис. 1. Расчетная схема соединения с натягом
Для установления закономерностей влияния различных методов сборки соединений с натягом на напряженно-деформированное состояние (НДС) его деталей, в том числе и на остаточное, необходимо провести анализ методов сборки с точки зрения возникающих воздействий на детали. В данной статье рассматриваются воздействия, возникающие при трех наиболее распространенных методах сборки соединений с натягом: механическом, тепловом и гидропрессовом.
При механическом методе сборки (рис. 2) в результате воздействия продольной силы запрессовки возникают дополнительные деформации в контактном слое. Перемещение деталей при сборке сопровождается возникновением сил трения Fтр и касательных напряжений, обусловленных внешним силовым воздействием, а также спецификой взаимодействия деталей соединения под нагрузкой [2].
Рис. 2. Схема механической сборки соединений с натягом
В результате интенсивного многократного контактного взаимодействия микронеровностей рельефа сопрягаемых поверхностей деталей происходит изменение напряженного состояния поверхностных слоев, что выражается наклепом и возникновением остаточных напряжений. Наличие в зазоре срезанных частиц металла способствует локальной концентрации напряжений [2].
205
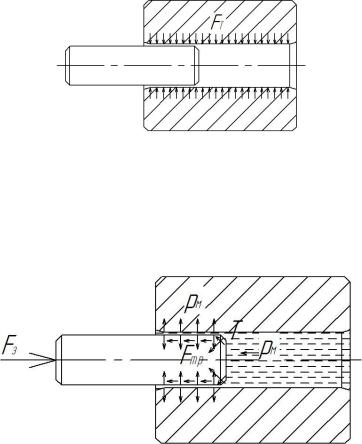
При тепловой сборке охватывающая деталь испытывает значительные температурные деформации и при остывании возникают дополнительные остаточные напряжения. Для рассматриваемого соединения, у которого длина втулки превышает длину посадки (рис. 3), вероятна концентрация напряжений в зоне внутреннего торца вала, обусловленная различными деформациями, возникающими в результате действия сжимающей нагрузки FT при охлаждении охватывающей детали. При сборке с нагревом охватывающей детали имеет значение частичное или полное снятие наклепа и остаточных напряжений в поверхностном слое нагреваемой детали [2].
Рис. 3. Схема тепловой сборки соединений с натягом
При гидропрессовой сборке соединений с натягом детали испытывают давление масла pм, превосходящее контактное давление pk. В результате перемещения деталей относительно общей оси при гидропрессовой сборке также возникают сборочные касательные напряжения. Помимо силы трения Fтр по цилиндрической поверхности в соединении возникают дополнительные силы трения T на заходных кромках и осевая сила Fз на кольцевых площадках вследствие разности в размерах отверстия ступицы и вала (рис. 4) [1, 3].
Рис. 4. Схема гидропрессовой сборки соединений с натягом
Таким образом, различные методы сборки соединений с натягом могут обусловливать различное остаточное НДС деталей, учет которого при проектировании позволит увеличить надежность соединений.
206
Список литературы
1.Абрамов, И.В. и др. Высоконапряженные соединения с гарантированным натягом. – Ижевск: Изд-во ИжГТУ, 2002. – 300 с.: ил.
2.Курносов, Н.Е. Обеспечение качества неподвижных соединений: Монография. – Пенза: Изд-во Пенз. гос. ун-та, 2001. – 220с.
3.Щенятский, А.В. Теория и технология гидропрессовых соединений: монография. – Ижевск: Изд-во ИжГТУ, 2012. – 496с. ISBN 978-5-7526-0541-3.
Е. С. Слащев, аспирант
В. Г. Осетров, доктор технических наук, профессор Ижевский государственный технический университет
имени М. Т. Калашникова
Компенсаторы непрерывного действия
Современное машиностроение требует постоянной оптимизации изделий, снижения себестоимости, увеличения работоспособности машин. Для этого важно на стадии проектирования технологического процесса сборки прогнозировать самые неблагоприятные варианты работы машины.
Для управления точностью и технологической наследственностью методы с компенсирующими взаимодействиями получили широкое распространение при сборке машин с многозвенными размерными цепями.
Под компенсирующими взаимодействиями понимается достижение точности замыкающего звена пригонкой, регулированием и с помощью групповой взаимозаменяемости (сортировки деталей). В данной статье рассмотрим метод регулирования и пригонки с использованием компенсаторов непрерывного действия [1, 2, 3]. Введение в изделие таких компенсаторов позволит сократить количество доработок в процессе сборки, продлить срок службы узлов машины на значительный период.
Компенсаторы непрерывного действия, с помощью которых получают требуемую точность замыкающего звена, классифицируют по следующим признакам[1, 2]: назначению, непрерывности регулирования, степени свободы и автоматизации. По назначению данный тип компенсаторов является комбинированным. Компенсаторы непрерывного действия объединяют между собой технологические свойства, устраняющие погрешности деталей, появившиеся при механической обработке и сборке машины, и эксплуатационные, устраняющие износ и температурные расширения.
С помощью непрерывности регулирования оценивают дискретность перемещения компенсатора. Дискретные компенсаторы применяют в основном для изменения угловых положений деталей, а непрерывные – для линейных смещений.
Компенсаторы с одной или двумя степенями свободы поглощают ли-
207
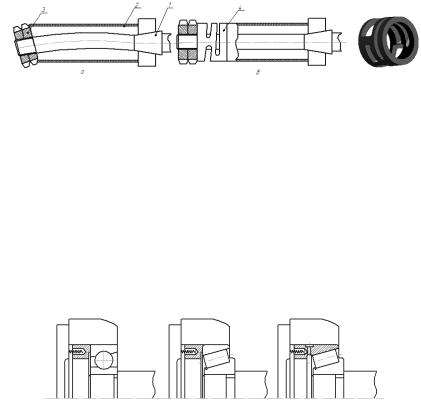
нейные погрешности, а с тремя степенями – погрешности относительных поворотов поверхности.
Важной характеристикой компенсаторов непрерывного действия является автоматическая компенсация погрешностей.
Рассмотрим принцип действия разработанных конструкций компенсаторов на конкретных примерах.
Цилиндрический компенсатор с двумя симметричными вырезами в одной плоскости, устраняющий осевые смещения и вырез, компенсирующий нежелательный поворот деталей вокруг оси (рис. 1). На рисунке показано положение шпинделя без компенсатора и с компенсатором, устраняющим изгиб шпинделя, возникающий от торцового биения втулки, при затяжке болтов.
Рис. 1. Схема шпиндельного узла без компенсатора (а) с компенсатором (б) компенсатор непрерывного действия (в) 1 ‒ шпиндель;2 ‒ втулка;3 ‒ гайка;
4 ‒ компенсатор.
При изменении режима работы в редукторах меняется температура, а вследствие этого зазор в подшипниках и их жесткость. Кроме того, с течением времени выполнения при сборке регулировка подшипников постепенно нарушается вследствие изнашивания и смятия микронеровностей. По этой причине требуются периодические повторные регулировки подшипников. Для устранения повторных регулировок и обеспечения постоянной жесткости опор применяют упругие элементы в виде пружин, рис. 2. Пружины располагают по окружности и устанавливают в кольца. Сила давления пружин должна превышать в радиально-упорных подшипниках сумму осевой составляющей от радиальной нагрузки и внешней осевой силы.
Рис. 2. Схемы узлов подшипников с упругими элементами.
Аналогичный цилиндрическому компенсатору, компенсатор s-типа, рис. 3. Компенсатор устраняет осевые перемещения, которые контролируются при помощи пружинных вставок.
208
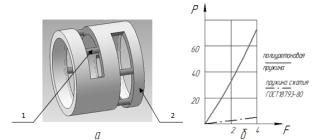
Рис. 3. а ‒ компенсатор s – типа: 1 ‒ полиуретановая пружина, 2 ‒ корпус; б ‒ график зависимости усилий (Р, Н) от деформации нагружения (F, мм).
Вместо пружин предлагается применять упругие полиуретановые элементы. Опыты показывают, что полиуретан широко используется при листовой штамповке и выдерживает нагрузки до 20 кН. Полиуретан в редукторах работает при циклической нагрузке до 5 кН и при температуре 50…60 °С его долговечность составляет 5∙102 циклов. На рис. 2б, представлен график зависимости усилий (Р, Н) от деформации нагружения (F,мм), при твердости полиуретана 82 по Шору тип А.
Нередко в условиях единичного и мелкосерийного производства изготовления изделий для обеспечения требуемой точности геометрической формы поверхности (плоскостности, цилиндричности) и шероховатости приходится прибегать к пригоночным работам. Часто объем таких работ доходит до 25‒30 % от общей трудоемкости сборки узлов и машин [4]. Поэтому в ряде случаев предлагается проводить пригоночные работы не в местах сопряжения деталей. В качестве примера рассмотрим рис. 4. В корпус замка поз. 1, со сложной геометрией внутреннего профиля, устанавливается личинка поз. 2 и фиксирующая часть замка поз. 3 для обеспечения хода личинки в корпусе замка вырезаны пазы глубиной превышающей радиус корпуса. Корпус работает как компенсатор непрерывного действия, при этом не требуется точность обработки пазов, а также удается избежать пригоночных работ внутри корпуса. При необходимости герметичность корпуса обеспечивается полиуретановыми вставками или самотвердеющими материалами.
209
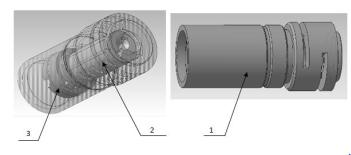
Рис. 4. Замок с пригоночными работами по корпусу: 1‒ корпус, 2 ‒ личинка замка, 3 ‒ фиксирующая часть
Проведенные исследования позволяют говорить, что введение в конструкцию изделия компенсаторов непрерывного действия, позволит снизить нагрузку на ответственные соединения, повысить работоспособность и снизить затраты на ремонт и обслуживание.
Список литературы
1.Балакшин, Б.С. Теория и технология машиностроения [Текст] / Б.С. Балакшин; В 2кн. - М.: Машиностроение, 1982.
2.Осеторов, В.Г. Технологические и организационные основы сборки машин/ В.Г. Осетров, Ф.И. Плеханов; Под общ.ред. В.Г. Осетрова.- Глазов, 2010.- 264.
3.Осетров, В.Г. Основы технологии механосборочного производства. Технологические наладки. Учебное пособие / В.Г. Осетров, Ю.Т. Схиртладзе, Ю.В. Пузанов, Г.Н. Гловетский. Под общ. ред. Пузанова Ю.В. – Ижевск: Изд-во ИжГТУ,
2007. – 205.
4.Новиков, М.П. Основы технологии сборки машин и механизмов / М.П. Новиков. – М.: Машиностроение, 1980. – 592.
С. В. Слободской, аспирант
В. В. Михрютин, кандидат технических наук, доцент Рыбинский государственный авиационный технический университет
имени П. А. Соловьева
Автоматизация построения модели геометрического образа режущего инструмента оснащенного СМП
Моделирование процесса обработки в процессе технологической подготовки производства позволяет определить наиболее подходящий инструмент и режимы обработки. Модель инструмента является необходимой составляющей общей модели процесса резания. Для создания модели инструмента большое значение имеет разработка трехмерной модели его
210
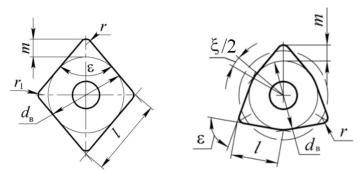
геометрического образа [1].
В настоящее время широкое распространение получил сборный режущий инструмент, оснащенный СМП. Для автоматизированного построения трехмерной модели геометрического образа целесообразно описывать его геометрию набором параметров, характеризующих его режущую часть [2, 3], но для реализации такого подхода требуется разработка алгоритма построения моделей геометрического образа СМП различной формы. Для прорисовки контура пластины целесообразно пользоваться рациональной кривой Безье или NURBS, позволяющими воспроизводить отрезки прямых, конические сечения, дуги окружностей. Контур режущих кромок пластины строится из отдельных сегментов кривых, которые могут иметь различный порядок. Сшивки сегментов между собой не предусматривается ввиду необходимости описания вершин острой формы.
Геометрические параметры равносторонних неравноугольных пластин, к которым относятся пластины ромбической и шестигранной формы (рис. 1) определяются по следующим зависимостям. Параметр определяется уравнением
m |
dв 2r |
r |
dв |
, |
|
||
|
|
(1) |
|||||
|
2sin |
|
2 |
|
|||
|
2 |
|
|
|
|
|
где n – порядок оси симметрии пластины; r – радиус при вершине пластины; – угол при вершине пластины; dв – диаметр вписанной окружности многоугольника.
Для пластин ромбической формы порядок оси симметрии имеет значение n = 2, для шестигранной n = 3.
Угловая величина дуги окружности при вершине с большим значением угла
|
2 |
|
(2) |
|
n |
||||
|
|
|
а) |
б) |
Рис. 1. Конструкция и размеры равносторонних и неравноугольных СМП а) – ромбической, б) – шестигранной формы
211
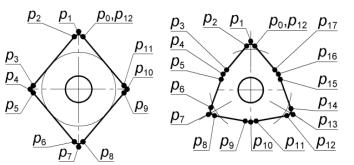
Ввиду центральной симметрии пластины для координат части узловых точек контура необходимо составить уравнения, часть других может быть получена путем преобразования поворота вокруг центра симметрии пластины координат точек, рассчитанных ранее. На рис. 1 показаны контрольные точки кривых, составляющих профиль режущих кромок ромбической и шестисторонней пластин.
а) |
б) |
Рис. 2. Узловые точки профиля равносторонних и равноугольных пластин а) – ромбической, б) – шестигранной формы
Для ромбической и шестигранной пластин потребуется рассчитать координаты шести точек с p0 по p5.
Координаты узловых точек контура режущих кромок определяются по следующим зависимостям.
|
|
|
|
|
|
|
|
|
|
|
dв |
|
|
|
|
|
|
|
|
T |
|
|||||||
|
|
|
|
|
|
|
|
|
r |
|
|
|
|
|
|
|
|
|
||||||||||
|
|
|
|
|
2 |
|
|
|
|
|
|
|
||||||||||||||||
|
p0 |
r sin |
|
|
|
|
|
|
|
|
|
|
|
|
|
r cos |
|
|
|
0 |
1 |
, |
|
|||||
|
|
2 |
|
|
|
|
|
|
|
|
2 |
|
|
|||||||||||||||
|
|
|
|
|
|
|
|
|
|
|
|
|
|
|
|
|
|
|
|
|
|
|||||||
|
|
|
|
|
|
|
|
|
|
|
|
|
|
|
|
|
|
|
|
|
|
|
||||||
|
|
|
|
|
|
|
|
|
|
|
|
sin 2 |
|
|
|
|
|
|
|
|
|
|
|
|||||
|
|
|
|
|
|
|
|
|
|
|
|
|
|
|
|
|
|
|
|
T |
|
|
|
|
|
|||
|
|
|
|
|
p1 |
|
|
|
dв |
|
|
|
|
|
|
|
|
|
|
(3) |
||||||||
|
|
|
|
|
0 |
|
|
|
|
0 |
|
1 |
|
, |
|
|
|
|||||||||||
|
|
|
|
|
|
|
|
|
|
|
|
|
|
|
|
|
|
|||||||||||
|
|
|
|
|
|
|
|
|
|
|
|
|
|
|
|
|
|
|
|
|
|
|
|
|
|
|||
|
|
|
|
|
|
|
|
|
|
|
|
|
|
|
|
|
|
|
|
|
|
|
|
|
||||
|
|
|
|
|
|
|
|
|
|
|
2sin |
2 |
|
|
|
|
|
|
|
|
|
|
||||||
|
|
|
|
|
|
|
|
|
|
|
|
|
|
dв |
|
|
|
|
|
T |
||||||||
p2 |
rsin |
|
|
|
|
|
|
m r |
|
|
rcos |
|
|
|
0 |
1 |
, |
|||||||||||
|
|
|
2 |
|
2 |
|
|
2 |
||||||||||||||||||||
|
|
|
|
|
|
|
|
|
|
|
|
|
|
|
|
|
|
|
|
|
|
|
|
|||||
|
|
|
dв |
|
|
|
d |
в |
|
|
|
|
|
T |
|
|
||||||||||||
|
v3 |
|
|
|
|
|
sin |
|
|
|
|
|
|
|
|
|
|
cos |
|
|
|
|
0 |
1 |
, |
|
||
|
2 |
|
2 |
2 |
|
2 |
|
|
|
|||||||||||||||||||
|
|
|
|
|
|
|
|
|
|
|
|
|
|
|
212

|
|
|
|
|
|
|
|
|
|
|
|
|
|
|
|
|
|
|
|
|
|
T |
|
|
|
|
|
|
|
|
|
|
|
|
|
|
|
|
|
|
|
|
|
|
|
||
|
|
p |
|
|
|
|
|
d |
в |
|
sin |
|
|
d |
в |
|
cos |
|
0 |
|
, |
|
|
|
|
4 |
|
|
|
|
|
|
|
|
|
|
1 |
|
|||||||||
|
|
|
|
|
|
|
|
|
|
n |
|
|
|
|
|
|
n |
|
|
|
|
||
|
|
|
|
|
|
|
2cos |
|
2cos |
|
|
|
|
|
|||||||||
|
|
|
|
|
|
|
|
|
|
|
|
|
|
|
|||||||||
|
|
|
|
|
|
|
|
|
|
2 |
|
|
|
|
|
|
2 |
|
|
|
|
|
|
|
|
|
|
|
|
|
|
|
|
|
|
|
|
|
|
|
|
|
|
|
|
||
|
|
|
|
|
|
|
|
|
|
|
|
d |
|
|
|
|
|
|
|
T |
|||
p |
|
|
rsin |
m r |
в |
rcos |
0 |
, |
|||||||||||||||
|
|
|
|
|
|
|
|
1 |
|||||||||||||||
|
2 |
|
|
|
|
|
|
2 |
|
|
|
|
2 |
|
|
|
|
2 |
|
|
|
||
|
|
|
|
|
|
|
|
|
|
|
|
|
|
|
|
|
|
|
|
|
dв |
|
v3 |
|
|
|
2 |
|||
|
|
|
|
|
|
dв |
|
|
|
|
|
|
|||||||
sin |
|
|
|
|
|
|
|
cos |
|
|
|
||||||
|
|
|
|
|
|
|
|
||||||||||
n |
|
|
2 |
|
2 |
|
|
n |
|
2 |
|||||||
t |
|
|
|
|
|
r |
|
|
|
|
|
, |
|
|
|||
|
|
|
|
|
|
|
|
|
|
|
|
|
|
|
|||
|
tg |
|
|
|
|
|
|
|
|
|
|
||||||
|
|
|
|
|
|
|
|
|
|
|
|
||||||
|
|
|
|
v |
3 |
p |
|
4 |
|
|
|
||||||
|
|
|
|
|
|
||||||||||||
|
|
|
|
|
|
2 |
|
|
|
|
|
|
|
|
|
|
|
|
p3 p4 v3 p4 t, |
|
|
|
|||||||||||||
|
p5 p4 v5 p4 t. |
|
|
T 0 1 ,
Матрица координат узловых точек профиля режущих кромок пластины:
p0 , p1 , p2 , p4 , p5 , |
|
|
|
|
|
|
|
|
|
|
|
|
|
|
|
|
|
|
(4) |
||||||
p R |
|
|
p |
|
|
p , R |
|
p |
|
|
p |
|
|
p |
|
|
|
p |
|
|
|
||||
|
, R |
, R |
, R |
, R |
,,...,p |
|
|
||||||||||||||||||
z |
|
i |
0 |
z |
i |
1 z |
i |
2 |
z |
i |
3 |
z |
|
i |
|
4 |
|
z |
i |
5 |
|
0 |
, |
|
|
где Rz(i) – матрица поворота вокруг оси z; |
|
|
2 |
|
– центральный угол |
||||||||||||||||||||
|
|
n |
|||||||||||||||||||||||
|
|
|
|
|
|
|
|
|
|
|
|
|
|
|
|
|
|
|
|
|
|
|
|
между вершинами многоугольника; i – номер вершины многоугольника i=0,…, n.
Вектор весов вершин рациональных кривых составляющих сегментов будет иметь блочную форму
|
м |
|
|
|
|
|
w 1,sin |
|
,1,sin |
|
,1 |
,1 |
(5) |
|
|
|||||
|
2 |
|
2 |
1,n 1 |
|
|
|
|
|
|
|
|
|
Вектор порядка рациональных кривых составляющих сегментов также
будет иметь блочную форму: |
|
|
d 2,1, 2,1 1,n |
. |
(6) |
|
|
Для пластин, в основе геометрической формы которых лежит правильный многоугольник, используются уравнения, приведенные в [2]. Аналогичным образом получаются уравнения для описания геометрии режущих кромок других форм пластин.
Исходными данными для построения контура режущих кромок является цифровой или буквенно-цифровой код в соответствии с ГОСТ 1904280. Анализ данного кода производит компьютерная программа, которая производит построение и визуализацию модели геометрического образа пластины в соответствии с предложенным алгоритмом. Изменяя код обо-
213
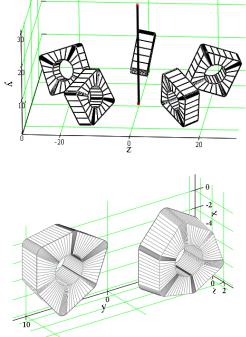
значения пластины, становится возможным эффективно изменять геометрию исследуемого инструмента, создавая новые варианты его конструкции.
С использованием результатов работы [3] становится возможным быстро изменять углы и число режущих зубьев сборного инструмента. Приведенный алгоритм построения геометрического образа режущих пластин для проверки его работоспособности реализован в виде рабочего документа учебной версии Mathcad 15. Результаты моделирования геометрического образа режущих пластин, установленных в требуемое положение в сборный режущий инструмент, показаны на рис. 3.
а)
б)
Рис. 3. Модели СМП сборного инструмента а) с черырехгранными равноугольными СМП б) шестигранными неравноугольными СМП
Предложенный в работе алгоритм позволяет повысить эффективность проведения модели геометрического образа режущего инструмента на этапе технологической подготовки производства и конструирования сборного инструмента, оснащенного СМП.
214
Целесообразна реализация алгоритма на языке высокого уровня с использованием одного из известных графических ядер, что позволит подготавливать графические данные модели сборного инструмента для экспорта во внешнюю систему трехмерного моделирования для последующей доработки модели и построения необходимых чертежей.
Список литературы
1.Михрютин, В.В. Методология построения комплексной системноаналитической модели процессов резания// Вестник РГАТА имени П.А. Соловьева, – Рыбинск: РГАТА, 2009.- 39 – 46.
2.Михрютин, В. В. Построение математических моделей рабочих кромок лезвий режущих инструментов// Вестник Рыбинской государственной авиационной технологической академии имени П. А. Соловьева. № 3(18) 2010. - . 158 – 166.
3.Михрютин, В. В. Математическое описание сборного режущего инструмента для моделирования процессов механической обработки// Сборка в машиностроении, приборостроении. № 6, 2011. -. 22 – 30.
С. В. Слободской, аспирант
В. В. Михрютин, кандидат технических наук, доцент Рыбинский государственный авиационный технический университет
имени П. А. Соловьева
Анализ направлений совершенствования режущего инструмента оснащенного СМП
Постоянное совершенствование конструкции твердосплавного режущего инструмента оказывает огромное влияние на прогресс всего механообрабатывающего производства. В настоящее время все большее распространение получает режущий инструмент сборной конструкции, в котором используются сменные многогранные режущие пластины.
Совершенствование конструкций режущих инструментов в основном направлено на повышение точности обработки, достижение требуемого качества обработанной поверхности, увеличение производительности и снижение себестоимости обработки, уменьшение себестоимости режущего инструмента.
Совершенствование конструкций сборного режущего инструмента, оснащенного СМП, происходит в следующих основных направлениях. Одно связано с совершенствованием инструментальных материалов, износостойких покрытий и форм режущих пластин. Другое – с совершенствованием конструкций корпуса режущих инструментов и поиском оптимального взаимного расположения режущих кромок, позволяющего повысить показатели производительности либо качества обработки.
Развитие конструкций СМП производится в направлениях [1]:
215
‒совершенствование инструментальных материалов, применяемых при изготовлении СМП;
‒совершенствование износостойких покрытий, наносимых на рабочие поверхности СМП;
‒совершенствование конструкций СМП, в том числе разработка форм СМП с криволинейными режущим кромками.
В настоящее время разработан ряд новых инструментальных материалов. Перспективным является применение минералокерамики и СТМ.
Разработаны многослойные покрытия, обеспечивающие высокую стойкость к срыву и отслаиванию, снижение сил трения и создающие эффект «залечивания» микродефектов инструментальной поверхности.
Для процессов токарной обработки существует проблема, связанная с возможностью образования сливной стружки, которая в процессе обработки может наматываться на инструмент, заготовки и технологическую оснастку. Для дробления сливной стружки на передней поверхности пластин выполняют специальные элементы, позволяющие завивать и ломать стружку. Использование данных элементов сравнительно простой формы не всегда обеспечивает дробление стружки для всех режимов резания и различных видов обрабатываемых материалов.
Известен целый ряд работ в данной области. Для увеличения степени пластических деформаций стружки при резании создаются условия для завивания стружки в вертикальной и в горизонтальной плоскости. Для управления деформацией при стружкообразовании на передней поверхности СМП предусматривают выступы и углубления, что позволяет изменять направление схода стружки [2], уменьшает площадь контакта стружки и облегчает доступ СОЖ, что приводит к уменьшению силы трения и количества тепла, передаваемого в инструмент [3].
В развитии конструкций корпуса сборных режущих инструментов режущих инструментов перспективными являются следующие направления.
Во время обработки необходимо обеспечить однозначное базирование и надежное закрепление режущих пластин. Отклонения формы базовых поверхностей пластин, а также гнезд корпусов сборных инструментов приводит к возникновению повышенных напряжений при закреплении. Возникновение дополнительных напряжений от действия силы резания и больших градиентов температур могут вызвать деформацию стенок гнезда, и привести к поломке режущей пластины. Для снижений таких деформаций на нижней и боковых стенках гнезда в [3] предложено выполнять контактные участки в виде кольцевых выступов, полученных при внедрении в нижнюю
ибоковые стенки гнезда вращающегося инденторов в виде конуса, пирамиды или сферы (рис.1).
216
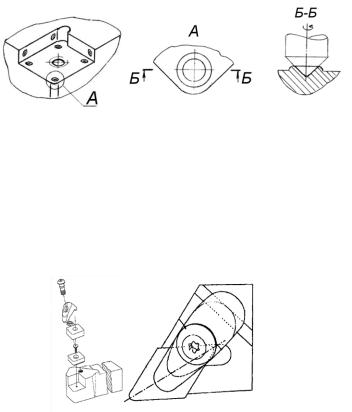
Рис. 1. Гнездо сборного режущего инструмента [3]
На надежность закрепления пластины в корпусе инструмента большое влияние оказывает конструкция зажимных элементов корпуса. Примером такой конструкций устройств является [4].
В [4] предложено прихват выполнять с обеспечением возможности его контактирования с задней поверхностью установочного отверстия режущей пластины только выступа его носовой части, а с верхней поверхностью режущей пластины ‒ только передней нижней стороны его носовой части (рис. 2).
Рис. 2. Устройство крепления режущей пластины [4]
При обработке деталей инструментом, имеющим режущие пластины с круглыми режущими кромками, может произойти непроизвольных поворот пластины вокруг своей оси. Также радиальные и осевые силы резания, воздействующие на режущую пластину, которая закреплена только крепежным винтом ограничивают применение подобного инструмента.
Поэтому разрабатываются корпуса инструментов со специальными устройствами для однозначного закрепления пластин, например, [5]. Конструкция данного инструмента предусматривает технологическое занижение гнезда для более плотного прилегания пластины и шарикфиксатор, ограничивающий вращение пластины вокруг своей оси.При размещении режущей пластины крепежный винт проходит через сквозное отверстие и взаимодействует с резьбовым отверстием, подпружиненный шарик фиксатор входит в выборку, выполненной на режущей пластине. В этом положении нижняя поверхность гнезда всегда остается удаленной от пластины из-за наличия занижения (рис. 3.).
217
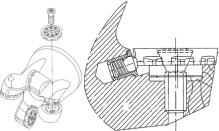
Рис.3. Устройство для закрепления режущей пластины [6]
Немаловажную роль в поиске оптимального расположения режущих кромок играет развитие методов расчета и автоматизированного проектирования инструмента. Известные работы в данной области в основном направлены на развитие расчетных методов и автоматизацию проектирования инструментов конкретных видов. В качестве методической основы данных работ используются [6, 7].
Вработе [6] расположение пластины в инструменте задается путем последовательности геометрических преобразований поворота и плоскопараллельного переноса для получения требуемой геометрии режущего клина, образованного телом СМП. Недостатком данного подхода является сложность определения последовательности необходимых геометрических преобразований.
Сборные инструменты централизовано выпускаются рядом производителей, при этом рекомендации по их выбору и использованию носят достаточно нечеткий характер. Поэтому актуальной являются работы, позволяющие подобрать существующий или спроектировать сборный инструмент для конкретных условий обработки. В области проектирования сборного инструмента выделены следующие работы.
Вработе [7] положение пластины рассчитывается на основе первоначального задания положения вершины инструмента и поиска расположения СМП с учетом требуемых значений углов режущего инструмента.
Расчет требуемого геометрического преобразования для позиционирования пластины в режущем инструменте может быть выполнено по методике работы [8]. Согласно данному подходу любая пластина СМП описывается контуром режущих кромок, заданных в системе координат (СК) пластины, связанной с режущей кромкой. В зависимости от направления работы инструмента задается СК, связанная с вершиной инструмента, и рассчитываются параметры необходимого геометрического преобразования.
Основным документом, нормирующим форму и размеры СМП, является ГОСТ 19042-80 «Пластины сменные многогранные. Классификация. Система обозначения. Формы». Ряд исследователей считает положения данного стандарта устаревшими [1] и даже предлагают свои классификации [8]. Однако, данный нормативный документ построен на основе меж-
218
дународного стандарта и предусматривает однозначную классификацию пластин по форме контура режущих кромок. При этом производителю пластин предоставлена свобода в отношении размеров и формы стружколомающих элементов. Данное обстоятельство позволяет выбрать данный стандарт в качестве методической основы для разработки основы алгоритма автоматизированной генерации модели геометрического образа СМП для разработки компьютерной системы моделирования сборного инструмента. При этом вопрос построения моделей пластин нестандартной формы должен быть рассмотрен отдельно.
Анализ существующей технической литературы в области совершенствования конструкций сборного режущего инструмента, оснащенного СМП показал, что в настоящее время значительное число исследований направлено на совершенствование инструментальных материалов, применяемых при изготовлении СМП, износостойких покрытий и конструкций СМП. Интенсивно ведутся работы в направлениях совершенствования конструкций корпусных деталей сборного инструмента, крепежных элементов, позволяющих повысить надежность закрепления и обеспечивающих снижения градиентов напряжений в СМП.
В то же время актуальной представляется разработка система компьютерного моделирования, позволяющая рассчитывать параметры установки режущей пластины в корпусе и оценивать выходные характеристики процесса обработки.
Список литературы
1.Михайлов, С.В. «Тенденция развития твердосплавного инструмента»// журнал «Ритм», №8, 2010.
2.Режущая пластина с выступами, образованными в ее угловой области: пат 2417864, KR, заявл. 26.06.2007, опубл. 10.05.2011.
3.Режущая многогранная сменная пластина: пат 2377099, RU, заявл. 31.10.2008, опубл. 27.12.2009.
4.Сборный режущий инструмент: пат 2438831, RU,заявл. 01.10.2010, опубл.
10.01.2012.
5.Инструмент для съемного закрепления режущей пластины и способы закрепления режущей пластины в инструменте: пат 2456127, US, заявл. 05.06.2008, опубл. 27.08.2011.
6.Режущий инструмент и режущая пластина для него: пат 2304489, IL,заявл. 10.06.2005, опубл. 20.07.2007.
7.Лукина, С.В. Особенности высокоскоростной обработки сиспользованием сборных торцовых фрез //Инженерный журнал: Справочник, 2005, № 8; - 27 – 31.
8.Петрушин, С.И. Математическое обеспечение геометрического анализа конструкций сборных режущих инструментов со сменными многогранными пла-
стинами//Вестник компьютерных и информационных технологий № 1, 2009. - 2635.
9. Михрютин, В.В. Математическое описание сборного режущего инструмента для моделирования процессов механической обработки// Сборка в машиностроении, приборостроении. № 6, 2011. - 22 -30.
219
В. А. Сокотов, аспирант
С. Н. Исаков, кандидат технических наук, доцент Уральский государственный лесотехнический университет, г. Екатеринбург
Колебания вертикальных роторов сортировок бумажной массы
Сортирование является последним этапом подготовки бумажной массы перед ее отливом на бумагоделательную машину. Основной целью процесса сортирования является удаление загрязнений, оставшихся после предыдущих стадий подготовки массы: мелких щепок, коры, непровара, пучков волокон, узелков, а также защита напорного ящика и сеточной части от повреждения посторонними включениями и дефлокуляция бумажной массы.
В настоящее время существует большое разнообразие машин для сортирования. Классификация на типы происходит по различным конструкциям роторов и сит сортировок, расположению оси ротора (вертикальный, горизонтальный), принципу работы, направлению потока в сите (внутрь, наружу), степени заполнения (полное, неполное), направлению движения сортируемой массы и др.
Напорные сортировки с цилиндрическим ротором - наиболее универсальный тип сортирующего оборудования. Они могут применяться на различных участках технологического потока для грубого и тонкого сортирования целлюлозы, древесной и макулатурной массы. К недостаткам этих сортировок следует отнести неодинаковость условий сортирования по высоте сита. Указанный недостаток является общим для рассмотренных выше сортировок закрытого тина. В результате процесса сортирования одновременно происходит увеличение концентрации сортируемой массы и снижение пропускной способности сита. Общий вид сортировки представлен на рис. 1.
К показателям качества бумаги и к равномерности их распределения предъявляются жесткие требования. Одна из причин колебания этих показателей непостоянство технологических режимов. В частности колебания давления бумажной массы вызывают неравномерность отлива бумаги и как следствие колебания массы квадратного метра бумаги и ее плотности. Одним из основных источников пульсаций давления является сортировка бумажной массы. Это связано с принципом работы, который основан на создании переменного давления на сито, а так же с дефектами и неисправностями сортировки. Неодинаковые зазоры между ситом и лопастями ротора вызовут повышенную пульсацию.
220

Рис. 1. Сортировка типа центрискрин: 1 – патрубок для подачи несортированной массы; 2 – наружное сито; 3 – внутреннее сито; 4 – патрубок для отвода
сортированной массы; 5 – гидродинамическая лопасть
На величину зазора влияют некачественная сборка, колебания ротора, нецилиндричность и несоосность сита и ротора и т. д. Основная причина колебаний роторов ‒ это остаточная неуравновешенность. Траектории (формы) колебаний, вызванные дисбалансом, зависят от положения ротора в пространстве.
В машиностроении наибольшее распространение получили горизонтальные валы. Центробежная сила, развиваемая остаточной неуравновешенностью горизонтального вала всегда меньше силы тяжести вращающихся элементов. Поэтому шейка вала совершает маятниковое колебание с некоторым угловым перемещением [1]. Для вертикального ротора картина иная.
При работе вертикального ротора сила тяжести не влияет на положение вала в подшипнике. Остаточная неуравновешенность вызывает контакт шейки вала с внутренней поверхностью подшипника в направлении центробежной силы. Таким образом, вал движется, повторяя форму подшипника. В результате на вал действует кинематическое возбуждение.
Вектор центробежной силы инерции вращается вместе с ротором с частотой, равной частоте вращения вала.
Колебания вертикального вала сортировки имеют различную природу возбуждения:
‒силовое воздействие (силы инерции от неуравновешенности ротора);
‒кинематическое воздействие (нецилиндричность посадочных мест вала и подшипника);
‒параметрическое воздействие (непостоянство жесткости при перекатывании по четному и нечетному числу тел качения).
Сила инерции от неуравновешенности определяется [2]:
FU mB e 2 cost ,
221
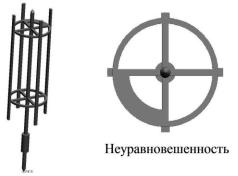
где mB − масса ротора, кг; e − удельный дисбаланс ротора, м; ω − угловая скорость вращения ротора, рад/с.
На неуравновешенную массу при ее смещении из положения равновесия на величину Z действуют силы:
‒ mZ
− сила инерции;
‒bZ − сила неупругого сопротивления;
‒cZ − сила упругого сопротивления.
Из равновесия с учетом принципа Даламбера получим дифференциальное уравнение описывающее колебание:
mZ bZ cZ mВe 2cos t .
Отклонение посадочных поверхностей вала и подшипника приводит к кинематическому возбуждению вибрации в виде перемещения S0 основания жесткостью C0:
k
S0 raicos i t i .
i 1
где i – номер гармоники отклонений радиуса вала от номинального значения, i=1, 2, 3, …, k; ∆rai – амплитуда отклонений радиуса вала от номинального значения i-й гармоники; βi – угол сдвига фаз i-й гармоники отклонений радиуса вала.
При i = 1 наблюдается биение вала, при i = 2 – овальность, i = 3 – огранка с тремя вершинами.
Моделирование вертикального ротора сортировки
Твердотельное моделирование производилось в программе Pro Engineer. Смоделированный ротор с лопастями представлен на рис. 2, а для наглядности его колебаний создана неуравновешенность.
Рис. 2. Модель ротора сортировки, созданная для расчета
Ротор закрепляется вертикально в двух опорах, причем нижняя опора представлена шарниром, а верхняя ‒ упруго закреплена с демпферами. Динамическая и компьютерная модели представлены на рис. 3.
222
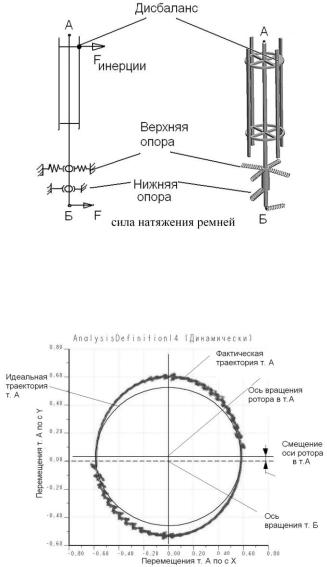
Рис. 3. Динамическая и твердотельная модели ротора
Ротору задается вращение, вследствие которого возникает сила инерции от неуравновешенности. Дополнительно на ротор действует сила натяжения ременной передачи.
Результаты расчета представлены в виде траектории движения точки А на рис. 4.
Рис. 4. Траектория движения точки А
Анализ результатов показал:
‒ ротор смещается от вертикальной оси под действием силы натяжения ремней, что приведет к несоосности ротора и сита, т.е. равномерности зазоров. В результате появляется результирующая сила, которая стремиться сместить ротор в вертикальное положение, но после прохождения точки максимального приближения результирующая сила уменьшается, и
223
ротор снова отклоняется от вертикальной оси. Этот эффект вызывает поворотным колебаниям ротора;
‒круговые колебания ротора из-за силы инерции от неуравновешенности вызывают повышенную пульсацию давления на оборотной частоте ротора, что будет «дополнять» пульсацию на лопастной частоте ротора;
‒результирующее воздействие вышеперечисленных факторов будет выражаться в эллипсовидной траектории вращения, причем эллипс не
симметричный. Смещение идет в обратную сторону от действия силы натяжения ремней.
Для уменьшения воздействия выше перечисленных факторов необходима разработка технических решений.
Список литературы
1.Квартин, Л.М. Динамика текстильных машин. М.: МГТУ им. А.Н. Косыги-
на. 2001. - 247.
2.Куцубина, Н.В. Виброзащита технологических машин и оборудования лесного комплекса: монография / Н. В. Куцубина, А. А. Санников ; Федер. агентство по образованию, Урал. гос. лесотехн. ун-т. - Екатеринбург: УГЛТУ, 2008. – 212.
И. Р. Сулейманова, аспирант
И. П. Попов, доктор технических наук, профессор Самарский государственный аэрокосмический университет имени академика С. П. Королева
Совершенствование процессов формовки и отбортовки за один переход в конической матрице с использованием программного продукта PAM-STAMP
Исследование совмещенных процессов формовки и отбортовки является актуальным в области изготовления авиационных двигателей, форсунок, камер сгораний. Полученные детали ограничены технологической возможностью известными способами листовой штамповки. Кольцевые тонкостенные заготовки имеют широкое распространение в изделиях аэрокосмической техники и отличаются разнообразием форм и размеров. Большое количество существующих в настоящее время способов формообразования тонкостенных заготовок характеризуют как наиболее сложный и трудоемкий процесс в изготовлении. Такие детали работают в условиях агрессивной среды, высоких температур и давлений. Подобные детали ввиду высокой степени возможного их гофрообразовния необходимо получать процессами со схемой напряженного состояния – плоского растяжения. К таким процессам относятся формовка и отбортовка [1].
224
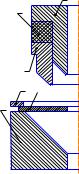
|
1 |
3 |
|
|
2 |
5 |
4 |
6
Рис. 1. Схема процесса формовки и отбортовки в матрицу:
1 – внутренний пуансон, 2 – наружный пуансон, 3 ‒ эластичный буфер, 4 – заготовка, 5 ‒ прижим, 6 – матрица
PAM-STAMP предназначен для моделирования оси симметричных процессов. Данное допущение упрощает постановку исходных данных для расчета и существенно сокращает время расчетов за счет уменьшения числа конечных элементов. Для решения поставленной задачи достаточно построить контур сечения детали и оснастки плоскостью проходящей через ось симметрии тела. Влияние скорости деформации на процесс деформирования рассматривать не будем. Причем в нашем случае достаточно использовать инструменты плоского построения. Таким образом, геометрической моделью в PAM-STAMP является одна часть сечения образованная при пересечении объекта с плоскостью, проходящей через оси симметрии инструментов, показанной на рис. 1.
После создания геометрии в Компасе 3D производится ее экспорт в распространенный формат обмена данными между CAD/CAE приложениями – IGES. Импортированная в программу PAM-STAMP геометрия показана на рис. 2.
В процессе формовки и отбортовки в коническую матрицу, участвует 5 объектов (пуансон внутренний и наружный, матрица, заготовка и прижим).
Так, в отличие от некоторых других систем, в программе PAM-STAMP используются оболочечные элементы, а не твердые объемные тела. Это позволяет избавиться от необходимости построения объемной расчетной сетки. Поверхностная же расчетная сетка строится средствами самого
PAM-STAMP.
225
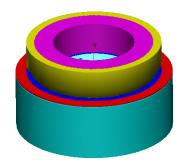
Рис. 2. Импортирование объектов в PAM-STAMP
Заготовка жестко зажимается по кромке. Усилие действует на наружный пуансон, эластичный буфер сжимается и передает действие на внутренний пуансон. В результате происходит формовка для периферийной части кольцевой заготовки, а для внутренних элементов кольцевой заготовки отбортовка.
Чтобы не было гофрообразований, используется прижим, так как заготовка тонкостенная. На начальном этапе происходит формовка для периферийной части заготовки за счет того, что диаметр наружного пуансона намного больше диаметра внутреннего пуансона, поэтому отбортовка не происходит, так как напряжений недостаточно для протекания этого процесса. При формовке из-за растягивающих напряжений происходит утонение кромки, радиусное отверстие же остается постоянным. Для случая, когда диаметры примерно одинаковы, под действием усилия начинает сжиматься эластичный буфер, пуансон движется вниз и происходит отбортовка. При отбортовке пластическую деформацию получает часть заготовки, расположенная над отверстием матрицы. В процессе деформирования по мере опускания пуансона, деформируемые элементы заготовки изгибаются на кромках пуансона и матрицы, диаметр отверстия увеличивается, а элементы заготовки перемещаются относительно пуансона в меридиональном направлении, постепенно приближаясь к стенке отверстия матрицы [2].
Полученные результаты моделирования представлены на рис. 3 и 4 после проведения процесса формовки и отбортовки соответственно.
226
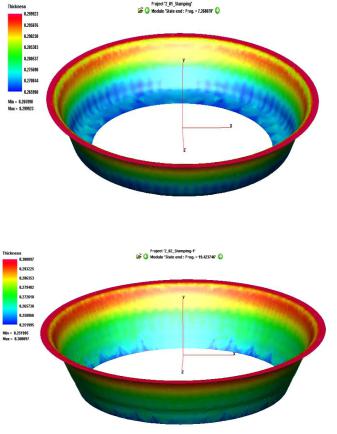
Рис. 3. Распределение толщин при протекании процесса формовка
Рис. 4. Распределение толщин при протекании процесса отбортовка
Предполагается, что в процессе формовки, а затем отбортовки неравномерность толщин по длине образующей будет минимальная. Это повысит качество деталей, а также срок их эксплуатации.
Список литературы
1.Сторожев, М.В. Теория обработки металлов давлением [Текст]: учебник для вузов / М.В. Сторожев, Е.А. Попов. – М.: Машиностроение, 1977. – 423.
2.Пат. 115256 Российская Федерация, МПК В21D 22/30. Устройство для формообразования кольцевой тонкостенной заготовки [Текст]/ Попов И.П., Демьяненко Е.Г., Сулейманова И.Р.; заявитель и патентообладатель Самар. госуд. аэрокос. ун-т. - № 2011144942/02; заявл. 07.11.11; опубл. 27.04.12, Бюл. № 12. – 3.
227
Т. В. Трефилова, старший преподаватель Удмуртский государственный университет Институт нефти и газа имени М. С. Гуцериева
Методика экспериментальных исследований кинетики коррозии материалов и сплавов в различных агрессивных средах
На характер и скорость коррозии подземного и наземного нефтепромыслового оборудования оказывают влияние факторы, связанные как с природой добываемой продукции, так и с условиями эксплуатации месторождений. К наиболее важным факторам следует отнести:
‒состав и свойства нефти и извлекаемой вместе с ней пластовой водой
ссодержанием сероводорода, кислорода, водорода и диоксида углерода;
‒состав и свойства нефтяного газа и содержание в нем воды и корро- зионно-активных примесей (сероводорода, диоксида углерода и др.);
‒соотношение фаз нефти и воды и характер распределения фаз между собой;
‒состав и физико-химические свойства защитных пленок органического и неорганического происхождения на поверхности металла (смолы, парафины, сульфиды железа, карбонаты кальция, магния, железа);
‒наличие и природа абразивных частиц.
Для исследования коррозионной стойкости материалов нефтепромыслового оборудования используется три метода:
1)гравиметрический;
2)метод поляризационного сопротивления;
3)метод потенциодинамических кривых.
При оценке коррозионной устойчивости металла наиболее распространен гравиметрический метод. Он применяется в двух вариантах: определение увеличения массы образца вследствие образования продуктов коррозии на его поверхности и определение потерь массы после удаления продуктов коррозии. Второй вариант является универсальным и поэтому получил более широкое распространение. Скорость коррозии
вычисляется по формуле [1]: |
|
n m1 |
m0 |
|
|
|
V |
|
, г/м2 ч , |
(1) |
|||
|
|
|||||
кор |
|
S |
t |
|
||
|
|
|
где m1- масса образца вместе с продуктами коррозии, г; m0- масса исходного образца, г, S ‒ площадь образца, м2, t – время испытания, ч, n – коэффициент, зависящий от состава продуктов коррозии. Эта формула применима только в тех случаях, когда известен химический состав продуктов коррозии, определенный с помощью химического или рентгенографического анализа. Последнее обстоятельство является существенным недостатком первого варианта гравиметрического метода, он применим в основном для исследования газовой коррозии, при которой на поверхности
228
металла образуется лишь негидратированная окись, так как при высокой температуре не может образоваться слой влаги.
Преимущество первого варианта состоит в том, что в случае его применения можно проследить за кинетикой процесса на одних и тех же образцах, поскольку ведется наблюдение за увеличением их массы.
При использовании второго варианта гравиметрического метода продукты коррозии удаляются различными составами, взаимодействующими не с основным металлом, а лишь с продуктами коррозии. Наряду с этим ставят и так называемую «слепую» пробу, т.е. обрабатывают неэкспонированные образцы, чтобы получить данные о растворении основного металла.
Скорость коррозии по второму варианту гравиметрического метода
вычисляют по формуле: |
|
m0 m2 |
|
|
|
V ' |
|
,г/м2 ч , |
(2) |
||
|
|||||
кор |
|
S t |
|
||
|
|
|
где m0 ‒ масса исходного образца, г; m2 ‒ масса образца после удаления продуктов коррозии, г. В этом случае химический состав продуктов коррозии не имеет значения для результатов расчета.
Метод определения плотности по потерям массы имеет ряд недостатков: трудно полностью удалить все продукты коррозии, не затрагивая основной металл, невозможно оценивать неравномерную коррозию и межкристаллитное коррозионное разрушение. Образцы, предназначенные для гравиметрических измерений, могут иметь разнообразную форму, но для получения точных результатов необходимо, чтобы они обладали максимальной площадью для испытаний при минимальной массе, что связано с разрешающей способностью аналитических весов. Поверхность образцов должна иметь высокий и одинаковый класс шероховатости, так как у образцов с неровной поверхностью реальная площадь может намного превышать геометрическую, что приводит к погрешностям в расчетах.
Метод поляризационного сопротивления, основанный на принципе Штерна-Гири: плотность тока коррозии обратно пропорциональна поляризационному сопротивлению поверхности электрода, измеренному вблизи стационарного потенциала коррозии.
Iкор |
|
ba bк |
|
|
dI |
|
B / Rp , |
(3) |
|||||||
2,303( ba bk |
|
|
|
|
|||||||||||
|
|
|
) dE |
|
|
|
|
|
|||||||
|
|
|
b b |
|
|
1 |
|
1 |
1 |
|
|
||||
|
|
|
|
|
|
|
|
|
|
|
|
|
|
|
|
B = |
|
2,303( b |
b |
|
|
|
b, |
, |
(4) |
||||||
|
) b, |
|
|||||||||||||
|
|
|
a |
k |
|
|
|
|
|
|
|
|
|
|
|
|
|
|
a |
k |
|
|
a |
|
|
k |
|
|
|||
где Rp =dE/dI ‒ поляризационное сопротивление, |
Iкор ‒ ток коррозии, ba = |
ba' ln10 и bk = bk' ln10 соответственно анодная и катодная постоянные Тафеля.
229
Метод поляризационного сопротивления исключает большинство проблем, связанных с интенсивной поляризацией электрода. В практических измерениях величина поляризации электрода редко превышает ±20 мВ и чаше всего ограничивается значением ±10 мВ. Метод предусматривает использование коррозиметров, основанных на измерении поляризационного сопротивления.
Одним из недостатков метода являются заложенные в нем предположением о линейности основного кинетического уравнения систематические ошибки. Эти ошибки тем больше, чем больше величина поляризации, и могут достигать нескольких десятков процентов. Другой недостаток метода связан с неопределенностью константы В, величина которой не может быть получена непосредственно при измерении Rp и задается теоретически, либо определяется в отдельном эксперименте. Использование того или иного ее количественного значения должно быть аргументировано в каждом конкретном случае. Теоретически величина В может изменяться от 6,5 до 51,11 [2]. Дополнительные затруднения в интерпретации полученных результатов имеют место в низкоэлектропроводных средах, а так же при отложении продуктов коррозии на корродирующей поверхности, как это имеет место и в случае сероводородной коррозии.
Применение коррозиметров, основанных на измерении поляризационного сопротивления может быть рекомендовано при необходимости получения большого числа измерений за короткий промежуток времени, например, при выборе ингибитора из большой серии проб, для получения зависимости изменения скорости коррозии во времени, для контроля за эффективностью ингибирования при неизменном характере коррозионного процесса и т. п.
Известен также и метод потенциодинамических кривых [1]. Метод заключается в изучении зависимости скорости электрохимической реакции (ионизации металла или восстановления водорода или кислорода) от потенциала электрода.
Экспериментальная установка для изучения анодного растворения и пассивации металлов (рис. 1) состоит из следующих основных частей:
1)малогабаритный цифровой потенциостат ‒ гальваностат IPC-Pro, контролирующий напряжение на ячейке и измеряющий ток, протекающий
вячейке;
2)персональный компьютер, использующийся для управления потенциостатом и регистрации результатов измерения;
230

3) трехэлектродная электрохимическая ячейка.
Рис. 1. Схема автоматизированной экспериментальной установки для проведения электрохимических измерений: 1 ‒ персональный компьютер,
2 ‒ цифровой малогабаритный потенциостат-гальваностат IPC-Pro,
3 ‒ экранированные кабели для подключения электрохимической ячейки (клемма W (Working) ‒ рабочий электрод, R (Reference) ‒ электрод сравнения, C (Counter) ‒ вспомогательный электрод), ЭЯ ‒ электрохимическая ячейка (Э.С. ‒ электрод сравнения; Р.Э. ‒ рабочий электрод; В.Э. ‒ вспомогательный электрод)
Для исследования коррозионной стойкости металла наиболее широко используется гравиметрический метод и метод потенциодинамических кривых в различных агрессивных средах, т. к. эти методы позволяют наблюдать и охарактеризовать кинетику процесса и характер коррозионного разрушения.
Метод поляризационного сопротивления может быть рекомендован при необходимости получения большого числа измерений за короткий промежуток времени, например, при выборе ингибитора из большой серии проб, для получения зависимости изменения скорости коррозии во времени, для контроля за эффективностью ингибирования при неизменном характере коррозионного процесса.
Таким образом, для исследования коррозионных свойств материалов и сплавов используются все три метода с учетом имеющихся преимуществ и недостатков, которые нашли широкое применение в изучении влияния агрессивных сред на коррозию нефтепромыслового оборудования.
Список литературы
1.Дамаскин, Б.Б. Электрохимия, М.: Химия, Колос, 2006. – 667.
2.Кеше, Г. Коррозия металлов. Физико-химические принципы и актуальные проблемы. М.: Металлургия. 1984. - 400.
231
М. Д. Трунов, аспирант
В. И. Карлов, кандидат технических наук, доцент Волгоградский государственный технический университет
Кинематическое исследование плоских механизмов второго класса средствами AUTOCAD
Вработе [1] возможные методы кинематического исследования механизмов разделены на графический и аналитический. При этом отмечено, что, несмотря на наглядность и универсальность графических методов, они не всегда обладают необходимой точностью. Однако при реализации графического метода на ЭВМ, можно добиться любой необходимой точности. В данной работе описан разработанный автором способ кинематического исследования плоских механизмов второго класса с одной степенью свободы, основанный на графическом методе, с использованием программ на языке Autolisp [2] системы AutoCAD.
Вработе [3] данным способом был исследован механизм поперечнострогального станка. В данной работе будет описан общий подход к реализации исследования из [3]. Рассмотрим задачу построения плана положений, скоростей и ускорений заданного механизма при определенном положении входного звена. При программировании удобно разделить задачу на следующие блоки:
1. Ввод исходных данных (истинные длины звеньев, длина какоголибо звена на чертеже, длины векторов линейных скоростей и ускорений входного звена, угол поворота входного звена и его угловая скорость, точки вставки планов механизма, скоростей и ускорений)
2. Расчет дополнительных параметров (масштабные коэффициенты, линейные скорости и ускорения точек входного звена)
3. Расчет точек плана механизма и его построение 4. Расчет точек плана скоростей и его построение, нахождение вели-
чин нормальных, кориолисовых ускорений 5. Расчет точек плана ускорений и его построение
Операции, проводимые в первых двух блоках весьма тривиальны, и не требуют особых пояснений. Вся их суть сводиться к последовательным операциям ввода данных и арифметическим расчетам.
Операции третьего блока поясним на примерах механизма шарнирного четырехзвенника (МШЧ), кривошипно-ползунного (КПМ) и кулисного механизмов (КМ) (рис. 1 а, б, в). Предположим положение точки O задано для всех трех типов механизмов. Положение точек A и C (предполагается, что C лежит на одной горизонтальной прямой с A) найти достаточно просто.
232
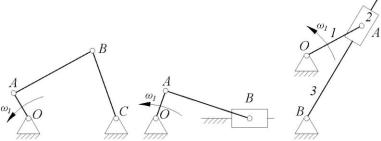
а |
б |
в |
|
Рис. 1. Схемы исследуемых механизмов |
|
Для нахождения положения точки B в механизме МШЧ нужно найти точки пересечения окружностей с центрами в A и C и радиусами AB и BC соответственно, затем выбрать точку с большей ординатой. Код, реализующий данную задачу на Autolisp, выглядит следующим образом:
(setq o (getpoint "\Точка O плана механизма: ") a (polar o fi oa)
c (polar a 0. ac) b (car (vl-sort
(2d_inters_circle a ab c bc)
(function (lambda (e1 e2) (> (cadr e1) (cadr e2))))
)
)
)
В данном фрагменте функция setq последовательно присваивает переменным o, a, c, b координаты соответствующих точек механизма. Функция polar вычисляет декартовы координаты по точке, представляющей начало полярной системы координат, а также полярному углу и радиусу в данной системе. Предполагается, что всем переменным, представляющим размеры (oa, ab, ac, bc) и угол поворота входного звена fi, предварительно присвоены необходимые значения. Функция 2d_inters_circle предложена в [4], возвращает список с точками пересечения двух окружностей, а функция vl-sort сортирует список согласно правилу в (function (lambda (e1 e2) (> (cadr e1) (cadr e2)))), т.е. сначала ставит точку с большей ординатой, которую и извлекает функция car, как первую в списке.
Для нахождения координаты точки B КПМ, необходимо найти точки пересечения окружности с центром в A, радиусом AB с прямой, по которой движется ползун, далее отсортировать полученные значения точек согласно необходимому условию (в случае КПМ рис. 1 б по убыванию абсциссы). Код для расчета положений точек КПМ аналогичен коду для МШЧ, функцию пересечения окружностей нужно поменять на функцию пересечения прямой и окружности, где прямая должна быть задана двумя точками. Пример такой функции приведен в [5]. При сортировке для схе-
233
мы б рис. 1 необходимо функцию cadr в примере кода выше поменять на car. Для КМ вычисление координат всех точек можно составить, используя
только функцию polar.
Построить положения механизмов по полученным координатам можно используя, например, функцию command, предварительно выключив при-
вязку: (command “._line” o a b c “”).
Для нахождения точек плана скоростей МШЧ можно использовать следующий код:
(setq pol (getpoint "\nУкажите полюс плана скоростей") av (polar pol (+ (angle o a) (/ pi 2)) pa)
bv (inters
av (polar av (+ (angle a b) (* 0.5 pi)) 10.) pol (polar pol (+ (angle c b) (* 0.5 pi)) 10.) nil
)
)
Здесь av, bv и pol – точки a и b плана скоростей и его полюс. Точка av имеет полярный угол (+ (angle o a) (/ pi 2)) – угол представляющий сумму между π/2 и углом поворота входного звена и полярный радиус pa – заданная длина вектора линейной скорости точки A на плане, находится в полярной системе координат с началом в полюсе. Координаты bv находятся как пересечение (функция inters) двух прямых, заданных точками av
и(polar av (+ (angle a b) (* 0.5 pi)) 10.) – линия действия вектора относи-
тельной скорости υBA и линии действия вектора υB, заданной точками pol
и(polar pol (+ (angle c b) (* 0.5 pi)) 10.).
Используя описанные приемы, можно реализовать алгоритм нахождения точек плана скоростей для КПМ и КМ. По полученным данным можно рассчитать нормальные составляющие ускорений точки B для МШЧ и КПМ, и кориолисово ускорение точки B для КМ.
Построить полученные планы по рассчитанным точкам можно функ-
цией command.
Расчет координат точек на плане ускорений можно вести аналогично способу, представленному для плана скоростей. Наибольшую сложность может представить вычисление направления кориолисового ускорения для КМ. Для установки направления (рис. 1 в) необходимо проанализировать направление угловой скорости звена 3 и скорости υA3A2.
Это возможно реализовать следующим образом:
(if (clockwise-p b a (polar a (angle pol a3v) 10.)) (+ (angle a2v a3v) (* 0.5 pi)) (- (angle a2v a3v) (* 0.5 pi))
)
Функция clockwise-p возвращает значение t (правда), если вектор с началом в a и концом в (polar a (angle pol a3v) 10.) создает момент относительно точки b в направлении против часовой стрелки и значение nil
234
(ложь) в противном случае. Таким образом, можно сделать вывод о направлении угловой скорости и либо прибавить, либо отнять π/2 от угла между вектором относительной скорости и положительным направлением оси абсцисс (последующие строчки). Синтаксис clockwise-p:
(defun clockwise-p (polus p1 p2)
(> (sin (- (angle polus p2) (angle polus p1))) -1e-14)
)
Описанный в работе метод кинематического анализа можно применить к механизмам любой сложности. Полученные данные можно использовать для дальнейшего силового анализа, синтеза махового колеса [6].
Список литературы
1.Артоболевский, И.И. Теория механизмов и машин : учебник / И. И. Артоболевский. – М.: Наука, 1988. – 640.
2.Полещук, Н.Н. AutoLISP и Visual LISP в среде AutoCAD / Н. Н. Полещук, П.
В. Лоскутов. – СПБ. : БХВ-Петербург, 2006. – 960.
3.Кислов, С.Ю. Применение ПЭВМ для графоаналитического метода кинематического исследования механизма / С. Ю. Кислов, М.Д. Трунов, В.И. Карлов // Инновационные технологии в обучении и производстве : матер. VII всерос. науч.- практ. конф. (г. Камышин, 22-23 дек. 2010 г.). В 5 т. Т. 4 / ВолгГТУ, КТИ (филиал) ВолгГТУ. - Волгоград, 2011. - 22-24.
4.Черевков, Г. Функция пересечения окружностей Autolisp [Электронный ре-
сурс] // Портал dwg.ru. URL: http://forum.dwg.ru/showthread.php?t=12167 (дата обращения: 05.02.2013).
5.Функция пересечения прямой и окружности Autolisp [Электронный ресурс]
//Портал dwg.ru. URL: http://forum.dwg.ru/showthread.php?t=15703 (дата обращения: 05.02.2013).
6.Трунов, М.Д. Применение ПЭВМ для кинематического и динамического исследования механизмов / М.Д. Трунов, С.Ю. Кислов, В.И. Карлов // Тезисы докладов смотра-конкурса научных, конструкторских и технологических работ студентов ВолгГТУ, Волгоград, 10-13 мая 2011 г. / ВолгГТУ, Совет СНТО. – Волгоград,
2011. - 133.
М. Д. Трунов, аспирант
Д. В. Проничев, кандидат технических наук, доцент Волгоградский государственный технический университет,
Моделирование термических напряжений в медно-алюминиевых слоистых композитах под действием электрического тока
Медно-алюминиевые слоистые композиты используются в электрических узлах в качестве токопереходников, плотность тока в которых может достигать 100 А/см2 [1]. Джоулево тепло, выделяемое электрическим сопротивлением переходника и узлов, которые он соединяет, а также усло-
235
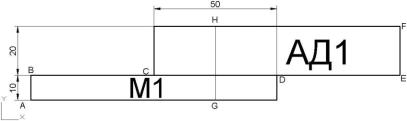
вия эксплуатации ведут к нагреву данных узлов до температур выше 200 °C [2]. Различные коэффициенты термического расширения меди и алюминия приводят к появлению термических напряжений в данных переходниках. Целью данной работы стала оценка уровня термических напряжений, возникающих при эксплуатации Cu-Al переходников, полученных сваркой взрывом (СВ), вследствие их нагрева джоулевым теплом, выделяемом в зоне контакта переходника.
Для осуществления моделирования прохождения тока была рассмотрена схема, представленная на рис. 1, которая является фрагментом клеммы, предложенной в [3].
Рис. 1. Схема для моделирования термических напряжений
Для осуществления моделирования необходимо решить уравнения для описания протекания тока, теплопроводности, а также необходимые уравнения теории упругости в соответствующих формах. Кроме того, для упомянутых уравнений необходимо задать граничные условия. Пусть на границе EF алюминия плотность тока, нормальная к EF, составляет J=100 А/см2, на границе AB меди электрический потенциал равен 0. После СВ между медным и алюминиевым слоями находится переходный слой. Точные данные по электропроводности этого слоя не известны, однако в работах [4, 5] авторы предлагают для описания электрического сопротивления данного перехода использовать, полученное экспериментально, произведение удельного сопротивления перехода ρ на его толщину Lпер. Авторы аргументируют такой подход непостоянством величины Lпер по толщине сварного соединения, а также трудностью ее измерения. Согласно данным [5] величина ρLпер, при отсутствии оплавов в сварном шве, составляет 30‒35 мкОм·мм2. Примем среднюю толщину Lпер равной 0,1 мм, тогда электропроводность слоя составит 2,86‒3,33 МСм/м, примем значение 3 МСм/м для расчетов. В качестве тепловых граничных условий примем на всех внешних границах тепловой поток равным:
q h Text |
T , |
(1) |
где h = 10 Вт/(м2·K) – соответствует спокойному воздуху, Text = 20 °С, T – температура соответствующей грани. Теплопроводностью переходной
зоны пренебрежем. В качестве условий закрепления примем, что точка A шарнирно оперта, точка B находится на подвижной опоре, ограничиваю-
236

щей ее движение в направлении X (рис. 1). Термическое расширение осуществляется под действием нагрева переходника на температуру:
T T T |
, |
ref |
|
(2)
где Tref = 20 °C.
Силами тяжести пренебрегаем. В качестве 2D аппроксимации примем плоское деформированное состояние, при котором компоненты тензора деформации εi3=0, i=1,2,3, компоненты тензора напряжений, не лежащие в плоскости модели, являются результатом расчета соответствующих уравнений. Материал представляется изотропным и упругим.
Необходимые для расчетов физические и механические свойства материалов считаются зависимыми от температуры.
Совместное решение уравнений, упомянутых выше, аналитически является, скорее всего, невыполнимой задачей, поэтому для решения воспользуемся численным методом конечных элементов, реализованном в
CAE-системе COMSOL Multiphysics.
Далее будут приведены графики распределения различных величин вдоль прямой GH (рис. 1), причем по горизонтальной оси будет отложена приводимая величина, а вдоль вертикальной – ось Y модели образца.
Распределение температуры в переходнике вдоль линии GH представлено на рис. 2. Хотя сопротивление перехода имеет весьма большое значение, оно локализовано на очень тонком участке в переходнике, поэтом у выделяющееся на нем тепло незначительно влияет на температурное поле.
Рис. 2. Температура в переходнике вдоль линии GH
237
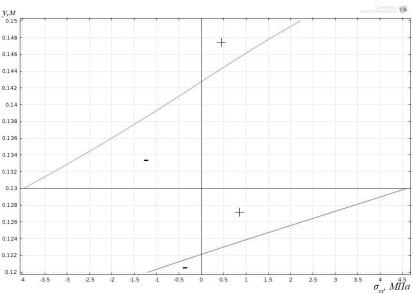
Рис. 3. Эпюра напряжения ζxx в переходнике вдоль линии GH
Распределение ζxx представлено на рис. 3. Как видно из рис. 3, нагрев переходника до 30 °C не вызывает больших напряжений.
Таким образом, сопротивление перехода в медно-алюминиевых композитах не оказывает большого влияния на его температуру, и, как следствие, на уровень термических напряжений.
Полученные данные свидетельствуют о том, что высокая температура, возникающая при эксплуатации переходника, измеренная в [2], возникает скорее от джоулева тепла выделяемого на стальном электроде, а также энергии разного рода процессов, происходящих при электролизе алюминия.
Список литературы
7.Verkamp, W.E. Copper-to-aluminum transition in high direct-current bus systems, IEEE Trans. paper No. PCIC-95-20 (1995). - 187–194.
8.Новые конструкции токоподводящего узла катодной секции электролизера алюминия / А. П. Пеев, Ю. Г. Долгий, С. В. Кузьмин и др. // Цветные металлы. –
2002. – № 8. – 51–54.
9.Пат. 2165483 РФ, МПК 7 С 25С3/16. Контактное соединение узла токоподвода к катодной секции электролизера / А.П. Пеев, В.И. Лысак, Ю.Г. Долгий, С.В. Кузьмин, Е.А. Чугунов, И.А. Соломатин, В.А. Чувичилов, А.В. Воронков, М.П. Кононов; ВолгГТУ, ОАО "Волгоградский алюминий". – 2001.
10.Исследование свариваемости взрывом, структуры и свойств медноалюминиевого биметалла / С.В. Кузьмин, В.И. Лысак, А.П. Пеев // Известия Волгоградского Государственного Технического Университета. – 2006. – №9. – 37-45.
238
11. Закономерности изменения структуры и свойств медно-алюминиевых композиционных материалов после сварки взрывом и последующей термической обработки / А.П. Пеев, С.В. Кузьмин, В.И. Лысак, А. А. Эрентраут // Вопросы материаловедения. – 2009. – №2(58). – 52-58.
В. Ф. Уразбахтин, студент
Ф. А. Уразбахтин, доктор технических наук, профессор Пермский национальный исследовательский
политехнический институт
Аварии и критические ситуации при эксплуатации жидкостных ракетных двигателей
Работа жидкостного ракетного двигателя (ЖРД) и всех его частей состоит в сопротивлении нагрузкам (внешним воздействиям). Все части двигателя работают синхронно, как система. Этим достигается работа ЖРД в расчетном режиме. В случае, когда хотя бы один элемент системы работает в нерасчетном режиме, возникает критическая ситуация. Такой режим работы распространяется последовательно на другие элементы системы. Этот процесс сопровождается перераспределением возможностей системы и увеличением количества критических ситуаций. Если какой-либо элемент не выдержит приложенной к нему нагрузки, т.е. возможностей, которые у него имеются, не хватит для сопротивления внешнему воздействию, то происходит его разрушение и создание аварийной ситуации в работе ЖРД.
Наиболее частыми причинами возникновения критических ситуаций являются:
1)резонанс, возникающий в отдельных частях ЖРД;
2)нерасчетное трение между подвижными частями ЖРД (например, в турбонасосном агрегате);
3)химические превращения: горение, окисление, испарение, изменение химического состава, увеличение вязкости компонентов топлива;
4)нагревание или чрезмерное охлаждение рабочего тела и топлива;
5)недопустимый перепад давления в магистралях топливного трубопровода;
6)несинхронность скоростей движения горючего и окислителя поступающего в камеру сгорания;
7)механические повреждения из-за коррозии на поверхностях деталей, нерасчетного распределения массы, а также потери устойчивости и появления нерасчетных деформаций.
Примеры возникновения критических ситуаций в отдельных частях, которые имеют место при эксплуатации ЖРД (рис.1).
Баки окислителя и горючего.
а) Компоненты жидкого топлива перемещаются “плескаются” во внут-
239
ренней полости баков. В результате может произойти внештатный расход одного из компонентов топлива. Это перемещение приводит к их неполной подаче в камеру сгорания, неравномерной скорости горения, и, в конце концов, к созданию прерывистой тяги ЖРД.
б) Разброс гидравлических сопротивлений трактов горючего и окислителя может привести к появлению нерасчетного соотношения расходов компонентов, что влечет за собой снижение тяги и удельного импульса. Обычно эта критическая ситуация приводит к нерациональному расходу одного из компонентов топлива в ЖРД, при этом, не достигнув расчетного изменения тяги.
в) Химическая агрессивность. Этим качеством обладают все окислители. Поэтому наличие в баках, предназначенных для окислителя, даже незначительных количеств органических веществ (например, жировых пятен, оставленных человеческими пальцами) может вызвать возгорание, последующее горение материала самого бака (известно, алюминий, магний, титан и железо очень энергично горят в среде ракетного окислителя).
г) Наличие даже незначительного количества воды или водяного пара в емкостях со сжиженными газами приводит к образованию очень твердых кристаллов льда, которые при попадании в топливную систему ЖРД, воздействуя на ее части как абразивный материал, царапают поверхность трубопроводов и могут стать причиной аварии.
Магистрали окислителя и горючего:
а) В результате трения при движении компонента топлива о поверхность может произойти его локальное накопление, которое заблокирует магистраль в процессе увеличения вязкости.
б) При возникновении повреждения в магистрали, известным процессом, например коррозией, может произойти утечка компонента топлива.
240
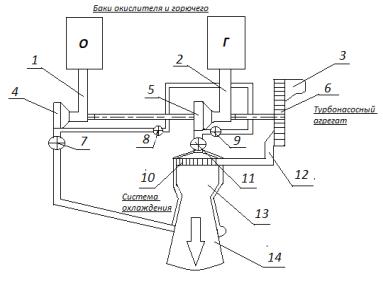
Рис. 1. Схема двухкомпонентного ЖРД: 1,2 – магистрали окислителя и горючего; 3 – газогенератор; 4,5 – насосы окислителя и горючего; 6 – турбина; 7,11 – главные клапаны окислителя и горючего; 8,9 – клапаны газогенератора окислителя и горючего; 12 – выхлоп турбины; 13 – камера сгорания; 14 – сопло
Турбонасосный агрегат.
а) Попадание на поверхность вращающегося вала инородных веществ, способствует снижению его скорости и даже остановке. Процесс подачи компонентов топлива при этом уменьшается, или происходит неравномерно, или вовсе прекращается;
б) Падение давления на выходе турбины. Если давление ниже, чем в камере сгорания ЖРД, процесс подачи компонентов не происходит.
Вытеснительная система
а) Давление в топливных баках в случае вытеснительной системы компонентов подачи падает. Если давление окислителя ниже, чем в камере сгорания, то процесс подачи компонентов в камеру сгорания не происходит.
б) Нерасчетный расход рабочего тела в виде газа в шаре - баллоне приводит к нерасчетному прекращению процесса вытеснения, т.е. возникновению критической ситуации.
Система охлаждения
а) Наличие технологических отклонений по толщине зазора приводит к возникновению неравномерности течения жидкости в рубашке охлаждения. Это может создать локальные зоны перегрева внутренней оболочки, прогоранию в этих зонах, и прекращению собственно процесса охлаждения.
241
б) Продавливание рубашки охлаждения приводит к уменьшению интенсивности охлаждения и появлению риска перегрева.
Камера сгорания и сопло
а) При несинхронной подаче в камеру сгорания компонентов топлива происходит их неполное сгорание и потеря части удельного импульса.
б) При технической недоработке пристеночного термального слоя может возникнуть прогар в камере сгорания и потери удельного импульса.
в) При закупоривании форсунок происходит уменьшение процесса разбрызгивания и потери удельного импульса.
Выявление критических ситуаций можно продолжать и дальше. Наличие вероятности их возникновения при работе ЖРД делает необходимым проводить их учет и выработку мероприятий по своевременному их предотвращению.
Список литературы
1.Железняков, А. «Тайны ракетных катастроф (Плата за прорыв в космос)»,
М.: Эксмо, 1962.
2.Уразбахтин, Ф. «Критические ситуации при производстве и технической эксплуатации транспортно-пусковых контейнеров ракет», М.: НИЦ «Регулярная и хаотическая динамика», Ижевск, 2009.
П. И. Федоровцев, аспирант; Е. С. Земерев, аспирант
В. И. Малинин, доктор технических наук, профессор А. В. Шатров, гл. инженер
ООО «Лаборатория Эффективных Материалов» Пермский национальный исследовательский политехнический университет
Устройство отбора конденсированной фазы установки синтеза нанооксида алюминия
В ходе научно-исследовательских работ в ОКБ «Темп» при ПГТУ по созданию принципиально новых энергетических установок на порошкообразном металлическом горючем был разработан новый простой и эффективный метод синтеза высокодисперсных оксидов металлов.
Для исследования процесса сжигания аэровзвесей металлических порошков и синтеза дисперсных нанооксидов была разработана экспериментальная установка [1]. Данная установка состоит из системы подачи, форкамеры (ФК), камеры сгорания (КС), устройства отбора дисперсных продуктов.
Одним из ключевых узлов установки синтеза является устройство отбора дисперсных продуктов, которое предназначено для выделения конденсированных продуктов сгорания из высокотемпературного потока, истекающего из сопла.
Из недостатков применяемого устройства, описанного в [1] можно вы-
242
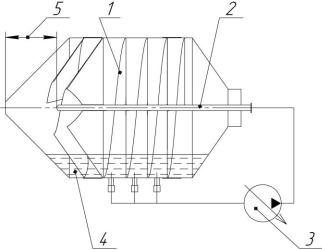
делить следующие:
−устройство не обеспечивает продолжительного цикла работы;
−испытания показали, что коэффициент улавливания (т. е. отношение массы синтезированного продукта к конечному) данного устройства составляет 45 %, большое количество наночастиц выносится вместе с паром в атмосферу;
−низкий уровень экологической безопасности.
Часть этих недостатков призвано устранить существенно переработанное устройство отбора конденсированной фазы, описанное в данной работе. На рисунке 1 представлена схема устройства, включающего в себя несколько основных узлов: винтовой шнек 1, узел диспергирования воды 2, циркуляционный насос 3.
Основным отличием представленного устройства от описанного в монографии [1] является наличие винтового шнека внутри и поддерживаемого уровня воды.
Рис. 1. Устройство отбора конденсированной фазы.
1 – винтовой шнек, 2 – узел диспергирования воды, 3 – циркуляционный насос,
4– поддерживаемый уровень воды, 5 – варьируемое расстояние.
Впередней зоне устройства улавливания преобладают процессы испарения подаваемой воды за счет тепла, поступающего с продуктами сгора-
ния. По мере движения потока продуктов сгорания внутри устройства и смешивания его с испаряющейся водой температура смеси падает до температуры конденсации воды. Конденсация воды начинается прежде всего на частицах к-фазы, даже очень малого размера, на чем и основан механизм улавливания. При достаточной концентрации водяного пара в газовой среде и существенном времени пребывания частиц в устройстве капли вырастают до большого размера, при этом действующие на них со стороны газового потока аэродинамические силы становятся меньше сил
243
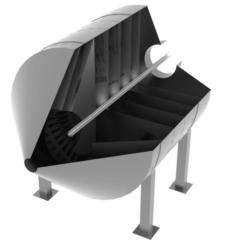
инерции. Поскольку траектория движения потока в устройстве винтовая, капли неминуемо отбрасываются на внешнюю стенку улавливателя и под действием силы тяжести стекают в его нижнюю часть. Из заднего конуса устройства улавливания истекает охлажденный, очищенный от конденсированной фазы газ.
Для эффективной работы устройства улавливания требуется, таким образом, увеличение времени пребывания в нем продуктов сгорания, истекающих из установки для сжигания металлических порошков, что реализовано за счет:
‒первичного торможения потока за счет передней расширяющейся части устройства улавливания;
‒аэродинамического торможения потока газа на большом количестве водяных капель, поступающих в устройство улавливания через форсунки узла диспергирования воды 2;
‒торможения потока за счет резкого снижения его температуры при охлаждении испаряющихся водяных капель;
‒движения потока по винтовой траектории за счет введения в конструкцию винтового шнека 1.
Внешний вид устройства отбора конденсированной фазы представлен
на рис. 2.
Рис. 2. Внешний вид устройства отбора конденсированной фазы
Поток, проходя сквозь распыленную воду (вода подается и распыляется через узел диспергирования 2) тормозится, охлаждается за счет испарения воды и очищается от конденсированной фазы. Проходя через винтовой шнек 1 внутри устройства поток двухфазной смеси несколько раз проходит через воду 4 и, таким образом, происходит процесс интенсивного барботирования [2, 3, 4], т.е. перемешивания двухфазного потока и воды. Частицы конденсированной фазы в результате смешивания с водой образуют суспензию.
244
Диспергирующий узел 2 отличается от описанного в [5] тем, что конструкция является цельной и представляет из себя трубу с отверстиями и струйную форсунку. Диаметры отверстий составляют порядка 1,5…2 мм, что создает необходимое распыливание капель воды. Узел диспергирования допускает варьирование размера 5.
В процессе проектирования были проведены оценочные расчеты количества воды, необходимого для эффективной работы устройства. Оценочное количество подаваемой воды должно составлять 13…16 кг/с, что обеспечивает необходимое снижение температуры продуктов сгорания. Большое количество подаваемой воды обусловлено необходимостью поглотить большой тепловой поток продуктов сгорания установки синтеза и обеспечить минимально необходимое для конденсации количество пара, чтобы часть целевого продукта не уносилась с водяным паром из устройства.
Обеспечение замкнутого цикла работы осуществляется за счет циркуляционного насоса 3. Жидкость из устройства отбора попадает в насос, где нагнетается и снова попадает через узел диспергирования в устройство. Таким образом осуществляется процесс рециркуляции жидкости, что позволяет экономить дистиллированную воду, продлит время работы устройства. Кроме того данный замкнутый контур позволяет обеспечивать необходимую концентрацию целевого продукта в суспензии. Циркуляционный насос допускает регулирование расхода воды, что позволяет определить наиболее оптимальный перепад давления и расход дистиллированной воды.
Таким образом, переработка устройства отбора конденсированной фазы позволит добиться увеличения коэффициента улавливания устройства за счет введения в конструкцию винтового шнека и избыточного расхода подаваемой воды. Предложенная схема работы устройства отбора обеспечит 100…200 секунд стабильной работы за счет замкнутого контура воды. Данное время лимитируется перегревом циркулирующей суспензии и концентрацией конденсированной фазы в воде, которая не должна превышать 10%. Превышение концентрации ведет за собой повышенный износ движущихся частей циркуляционного насоса и его поломку. В перспективе проектирования устройства отбора конденсированной фазы остается увеличение продолжительности цикла работы. Этого можно добиться с помощью введения на напорную линию насоса охладителя и устройств слива и подпитки циркулирующей суспензии чистой дистиллированной водой.
Список литературы
1.Малинин, В.И. Внутрикамерные процессы в установках на порошкообразных металлических горючих. Екатеринбург - Пермь: УрО РАН, 2006. - 262.
2.Балтренас, П.Б. Обеспыливание воздуха на предприятиях стройматериалов. М.: Стройиздат, 1990. - 181.
3.Пирумов, А.И. Обеспыливание воздуха. М.: Стройиздат, 1981. - 296.
245
4.Скрябин, Г.М. Пылеулавливание в химической промышленности. Л.: Хи-
мия, 1976. - 64.
5.Бербек, А.М. Устройство выделения конденсированной фазы из потока продуктов сгорания двигательных и технологических установок на металлическом горючем // Аэрокосмическая техника и высокие технологии - 2005. Материалы VIII Всероссийской научно-технической конференции / Под ред. А.Н. Аношкина, М.А. Нихамкина и К.В. Недопекиной – Пермь: ПГТУ, 2005.- 26.
Е. Н. Фокеева, аспирант; В. А. Зорин, студент
О. В. Муравьева, доктор технических наук, профессор Ижевский государственный технический университет
имени М. Т. Калашникова
Контроль пруткового проката электромагнито-акустическим методом с использованием рэлеевских волн
На промышленных предприятиях для контроля качества пруткового проката традиционно применяют акустический вид неразрушающего контроля. Большинство методик ультразвукового контроля требуют дополнительной подготовки образцов с помощью дорогостоящего оборудования и реализуют сложную методику обнаружения дефектов. Использование электромагнито-акустического метода позволяет устранить данные недостатки.
Вработе исследовано влияние различных видов дефектов (как искусственных, так и возникших в результате изготовления и обработки) пруткового проката на скорость и ослабление релеевских волн. Для проведения исследований разработаны и изготовлены образцы с искусственными дефектами, имитирующие производственные дефекты пруткового проката. Образцы изготовлены из пруткового проката круглого сечения со специальной отделкой поверхности в соответствии с ГОСТ 14955-77, стали 60С2А, диаметром 24 мм, длиной 200 мм. Образец № 3 и 4 с дефектом в виде частичной и полной засверловки, имитирующий дефекты в виде трещин, раковин и волосовин. Образцы № 7, 8, 9, изготовленные с пропилами различных размеров и направлений, имитируют риски и царапины, возникающие при не соблюдении технологического процесса обработки пруткового проката. Также для исследований отобраны прутки с производственными дефектами в виде трещин и закатов, недопустимые в соответствии с ГОСТ 14955-77.
На рис.1,а приведена блок-схема установки для измерений. Использование в экспериментах специализированного бесконтактного электромаг- нитно-акустического преобразователя рэлеевских волн обеспечивает возбуждение и прием волн в прямом и обратном направлениях по периметру прутка (рис.1,б) [2].
В[2] подробно изложена методика определения скорости рэлеевской
246
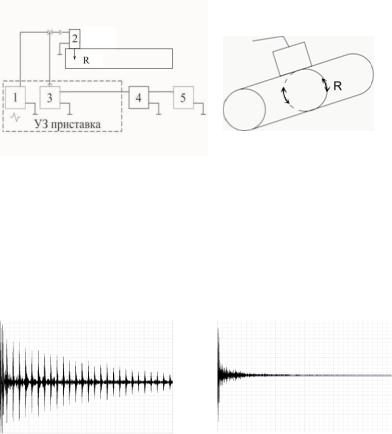
волны для оценки структуры поверхностного слоя пруткового проката.
а |
б |
|
Рис.1. Блок схема экспериментальной установки (а): 1 – генератор зондирующих импульсов; 2 – ЭМА преобразователь с системой подмагничивания; 3 – усилитель; 4 – аналого-цифровой преобразователь; 5 – персональный компьютер; путь релеевской волны по периметру прутка (б)
Проведенные расчеты показали, что наличие дефектов на образце не оказывает влияния на величину скорости распространения рэлеевской волны. Расчеты доказали, что размер и форма дефектов существенно влияет на ослабление амплитуды рэлеевской волны (рис. 2)
а б Рис. 2. Осциллограмма сквозных импульсов релеевской волны на бездефектном
прутке (а), дефектном прутке (б)
Следующим этапом исследований стало получение закономерностей чувствительности рэлеевской волны к различным типам дефектов.
Для реализации данного этапа составлена таблица.
247
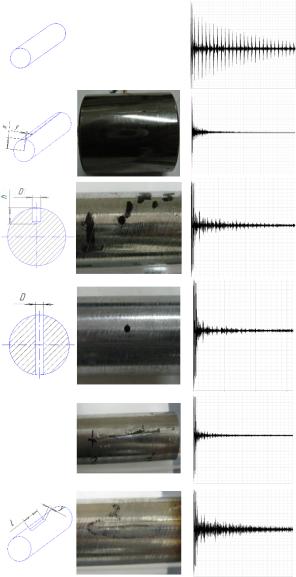
Таблица. Виды дефектов и их эхограммы
№ |
Вид и размеры |
Эскиз дефекта |
Фото |
Эхограмма |
|
п/п |
дефекта |
||||
|
|
|
|||
1. |
Бездефектный |
|
|
|
|
|
образец |
|
|
|
|
|
|
|
|
|
|
2. |
Трещина |
|
|
|
|
|
x = |
|
|
|
|
|
y = |
|
|
|
|
|
|
|
|
|
|
3. |
Засверловка |
|
|
|
|
|
D = 2 мм |
|
|
|
|
|
h = 7,5 мм |
|
|
|
|
|
|
|
|
|
|
4. |
Сквозная |
|
|
|
|
|
засверловка |
|
|
|
|
|
D = 2 мм |
|
|
|
|
|
|
|
|
|
|
5. |
Закат |
|
|
|
|
|
L = 41,2мм |
|
|
|
|
|
|
|
|
|
|
6. |
Продольный |
|
|
|
|
|
пропил |
|
|
|
|
|
L = 20,4мм; |
|
|
|
|
|
y = 1,7мм |
|
|
|
|
|
|
|
|
|
248
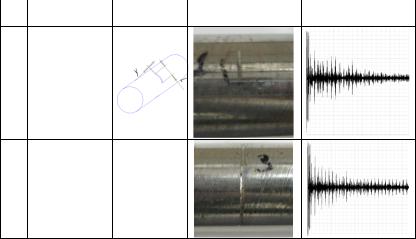
|
|
|
|
Окончание таблицы |
|
№ |
Вид и размеры |
Эскиз дефекта |
Фото |
Эхограмма |
|
п/п |
дефекта |
||||
|
|
|
7.Поперечный
пропил
L = 15,5 мм y = 1,7 мм
8.Пропил по окружности
Наибольшее ослабление рэлеевских волн происходит на образцах 2 и 5 с дефектами в виде трещины и заката, это обусловлено закономерностями распространения поверхностных волн. При резком изменении профиля поверхности рэлеевская волна частично отражается, частично проходит через препятствие, а частично трансформируется в объемные волны [1]. Также получены результаты высокой эффективности применения в качестве критерия браковки ‒ ослабления рэлеевской волны, для образцов № 3, 4 и 7 с искусственными дефектами в виде продольных пропилов. Наиболее сложным для выявления является пропил по окружности, замкнутый характер дефекта мешает дифракции поверхностной волны.
Представленные результаты показывают возможность эффективного использования рэлеевских волн для дефектоскопии поверхности пруткового проката ЭМА методом.
Коллективом кафедры «Приборы и методы контроля качества» ФГБОУ ВПО «ИжГТУ имени М. Т. Калашникова» параллельно ведется разработка технологии контроля пруткового проката ЭМА методом с использованием объемных волн, что в комплексе с контролем поверхностными волнами позволит существенно повысить эффективность выявления как поверхностных, так и внутренних дефектов.
Работа выполнена в соответствии с разделом 2 мероприятий Программы стратегического развития ФГБОУ ВПО «ИжГТУ имени М.Т. Калашникова» на 2012-2016 гг. (проект ПСР/М2/Н2.5/МВВ).
Список литературы
1. Клюев, В.В. Неразрушающий контроль: Справочник: В 7 т. ‒ Т. 3. ‒ Ультразвуковой контроль / И.Н. Ермолов, Ю.В. Ланге. ‒ Под общ. ред. В.В. Клюева. ‒ М.: Машиностроение, 2004. ‒ 864.
249
2. Кокорина, Е.Н. Влияние термообработки прутков из стали 60С2A на скорости рэлеевских волн: Сборник трудов II Всероссийской научно-технической конференции студентов, аспирантов и молодых ученых «Измерения, контроль и диагностика – 2012», 2012 г. – 25-33.
А. И. Фролова, аспирант
М. М. Матлин, доктор технических наук, профессор Волгоградский государственный технический университет
Универсальный способ оценки эффективности обработки пластическим деформированием
В промышленности широко используются упрочняющие технологии. Применение методов поверхностного пластического деформирования (ППД), изменяющего в широких пределах свойства поверхностного слоя, занимает важное место среди технологических способов, повышающих надежность деталей. В результате упрочнения ППД удается повысить запасы прочности деталей, работающих при переменных нагрузках в 1,5 … 3,0 раза, а срок службы повысить в десятки раз.
Такие методы нуждаются в контроле результатов упрочнения и оценке степени упрочнения поверхностного слоя, так как недостаточно упрочненная поверхность не будет обладать необходимой прочностью и износостойкостью, а перенаклеп грозит образованием трещин с последующим разрушением детали. Однако существующие методы контроля не всегда обладают достаточной точностью и не подходят для универсального применения для различных методов пластического деформирования.
Основной задачей данного исследования, являлось создание нового способа определения степени деформирования образца, который был бы справедлив для любых способов упрочнения пластическим деформированием (как поверхностных, так и объемных), позволял бы определять действительную степень относительной упругопластической деформации материала образца (в том числе и на готовых образцах), а также учитывал бы прочностные свойства материала образца до и после упрочняющей обработки и упругие свойства материала образца.
Как известно состояние поверхностного слоя детали во многом определяет ее нагрузочную способность, особенно в условиях воздействия переменных во времени нагрузок. При этом стоит отметить, что по показаниям рентгеноструктурных исследований [1] даже при растяжении стальных образцов пластическая деформация впервые возникает на поверхности, а сердцевина образца при этом еще находится в упругом состоянии. В связи с этим наиболее информативными являются не усредненные по объему физико-механические свойства материала детали, которые дают традиционные методы испытаний, а указанные свойства ее
250
поверхностного слоя.
Метод оценки степени упрочнения поверхностного слоя материала базируется на положении, согласно которому главная часть деформационного упрочнения исчерпывается на стадии равномерной деформации, когда деформация образца не превышает предельную равномерную деформацию εр, а наиболее интенсивный рост микродефектов (микротрещин) в металле еще не получает большого развития. Из условия существования обобщенной диаграммы деформирования, следует, что величина εр имеет физический смысл критической интенсивности деформации не только при одноосном растяжении, но и в условиях контактной упругопластической деформации, которая реализуется при поверхностном пластическом деформировании.
При достижении в процессе пластического деформирования деформации равной предельной, то есть равной р, истинные напряжения S обобщенной диаграммы деформирования станут равными истинному временному сопротивлению Sв (то есть S = Sв), а интенсивность напряжений i,0 в центре контакта согласно формуле примет вид
ζi,0 = |
Sв |
. |
(1) |
||
e |
εp |
||||
|
|
|
Как известно, временное сопротивление в связано истинным временным сопротивлением соотношением
ζв = |
Sв |
|
(2) |
|
eεp |
||||
|
|
|||
то есть |
|
|
|
|
ζi,0 = ζв . |
(3) |
По мере увеличения деформации материала возрастает (следуя диаграмме деформирования) и его предел текучести 0,2 при достижении оптимальной интенсивности деформации = р интенсивность напряжений i,0 в центре площадки контакта станет равной в (3) и одновременно будет соответствовать пределу текучести 0,2 упрочненного материала. Из этого следует вывод о том, что достижение отношением 0,2 / в значения равного единице соответствует максимально эффективному режиму ППД по критерию деформации в центре контакта детали и упрочняющего инструмента.
Следовательно, по уровню повышения предела текучести можно судить о степени упрочнения. При этом необходимо иметь возможность определения предела текучести непосредственно на упроченной в результате ППД поверхности детали.
251

Повышенный предел текучести
ζупр
0,2
можно вычислить по формуле [2]:
ζ |
у пр |
= |
|
|
0,955 1 2μ |
2 |
P |
|||||
|
|
|
|
|
|
|
|
|
||||
0 ,2 |
|
|
|
|
|
|
|
|
|
|
||
|
|
|
|
d |
|
|
|
|
|
|||
|
|
d 2 |
|
78 |
0 у пр 1 |
2μ |
|
|||||
|
|
|
|
2 |
|
|||||||
|
|
0 у пр |
|
|
|
D |
|
|
|
|
||
|
|
|
|
|
|
|
|
|
|
|
|
2 4 5/ НДисх
.
(4)
где P – нагрузка на шарик при его внедрении в поверхность образца до его упрочнения, НДисз – пластическая твердость материала, d0упр – диаметр отпечатка шарика на поверхности образца после упрочнения, D – диаметр шарика, которым наносят отпечатки на не упрочненную поверхность образца, 2 – коэффициент Пуассона материала образца.
Предел прочности в материала можно определить зависимостью [3]:
ζв |
|
|
|
0,955 1 2μ 2 P |
|
, |
(5) |
||||
|
|
|
d |
|
|
|
2 4 5/ НД |
||||
|
|
|
|
0 |
|
|
|
|
|||
|
|
d02 |
1,73 |
10 3 |
|
1 2μ 2 |
НД |
|
|
|
|
|
D |
|
|
|
|||||||
|
|
|
|
|
|
|
|
|
|
Соотношение 0,2 / в можно привести к обобщенному виду, используя выражения (4) и (5) [4]:
Uотн |
|
о ,у 0,0017( |
1 22 ) 1 |
/ 0 ,004Н |
(6) |
|||
|
|
о |
|
78у (1 |
2 |
2 |
у |
|
где о и о,у – соответственно интенсивность напряжений в центре отпечатка шарика на поверхности образца до и после его упрочнения
|
o |
0,955(1 2 |
2 |
)P / d 2 , |
(7) |
|||
|
o ,у |
0,955(1 2 |
2 |
)P |
/ d 2 |
(8) |
||
|
|
|
у |
у |
|
d и dу – соответственно диаметр отпечатка шарика на поверхности образца до и после упрочнения; P и Pу – соответственно нагрузка на шарик при его внедрении в поверхность образца до и после его упрочнения; d / D
и у d у / Dу – соответственно степень пластической деформации в отпе-
чатке при внедрении шарика в поверхность образца до и после его упрочнения; D и Dу – соответственно диаметр шарика, которым наносят отпечатки на не упрочненную и упрочненную поверхность образца; 2 – ко-
эффициент Пуассона материала образца; Н и Ну – соответственно контактный модуль упрочнения образца до и после его упрочнения, равные H P / Dh, H у Pу / Dу hу ; h и hу – соответственно глубина остаточно-
го отпечатка на не упрочненной и упрочненной поверхности образца. Испытания данной методики выполнялись для двух различных видов
упрочнения образца пластическим деформированием:
‒ упрочнение растяжением (объемное пластическое деформирование);
252

‒ упрочнение дробеобработкой (поверхностное пластическое деформирование).
В табл. 1 и 2 приведены результаты определения предлагаемым способом степени упругопластической деформации материала образца при соответственно упрочнении растяжением и дробеобработкой.
Таблица 1. Экспериментальное исследование степени упрочнения путем рас-
тяжения материала, на примере плоских образцов из стали 40ХН
№ |
|
Исходное состояние |
|
|
После упрочнения |
|
||||
НД |
ζ0,2 |
ζв |
|
|
НДупр |
упр |
|
|
упр |
|
обра |
|
|
|
|
||||||
εр |
ζ0,2/ζ |
0,2 |
εi,0 |
|
ζ0,2 ζв |
|||||
зца |
|
|
|
|
|
|||||
|
МПа |
|
|
в |
МПа |
|
|
|
||
|
|
|
|
|
|
|
|
|||
1 |
1400 |
280 |
490 |
0,175 |
0,57 |
2380 |
452 |
0,230 |
|
0,92 |
2 |
1460 |
288 |
510 |
0,168 |
0,56 |
2399 |
456 |
0,347 |
|
0,89 |
3 |
2100 |
445 |
630 |
0,117 |
0,71 |
2987 |
597 |
0,119 |
|
0,95 |
4 |
4000 |
770 |
890 |
0,061 |
0,87 |
4564 |
886 |
0,062 |
|
1,00 |
5 |
4020 |
800 |
930 |
0,061 |
0,86 |
4925 |
925 |
0,060 |
|
0,99 |
6 |
2080 |
430 |
630 |
0,118 |
0,68 |
2643 |
531 |
0,129 |
|
0,84 |
|
|
|
|
|
|
|
|
|
|
|
Таблица 2. Экспериментальное исследование степени упрочнения дробеобра-
боткой, на примере плоских образцов из стали 20ХГСА
|
|
Исходное состояние |
|
|
После упрочнения |
|
|
|||
№ |
|
|
|
|
|
|
|
|
|
|
НД |
ζ0,2 |
ζв |
|
|
НДупр |
упр |
|
|
|
|
|
|
|
|
|
|
|||||
обра |
|
|
0,2 |
|
упр |
|
||||
|
|
|
|
|
|
|
|
|||
зца |
|
|
|
εр |
ζ0,2/ζв |
|
|
εi,0 |
ζ0,2 |
ζв |
|
МПа |
|
МПа |
|||||||
|
|
|
|
|
|
|
|
|||
|
|
|
|
|
|
|
|
|
|
|
1 |
3983 |
876 |
1157 |
0,062 |
0,76 |
4681 |
1030 |
0,069 |
0,89 |
|
2 |
5534 |
1217 |
1391 |
0,044 |
0,88 |
6327 |
1392 |
0,063 |
1,00 |
|
3 |
5677 |
1249 |
1411 |
0,043 |
0,89 |
6822 |
1361 |
0,062 |
0,96 |
|
4 |
5821 |
1281 |
1431 |
0,042 |
0,90 |
7278 |
1401 |
0,062 |
0,98 |
В данном методе погрешность составляет не более 5 … 8%, что позволяет его использовать при выборе режимов упрочняющей обработки.
Таким образом, описанный метод пригоден для определения относительной степени упругопластической деформации материала образца при любом способе его упрочнения пластическим деформированием (объемным или поверхностным), поэтому он является универсальным. Кроме того, может использоваться в промышленности для определения эффективности и выбора технологических режимов упрочнения деталей пластическим деформированием (которое применяют для повышения усталостной прочности и долговечности металлоизделий).
253
Список литературы
1. Radhakrishnan, V. M. Relaxation of residual stress with fatigue loading // Eng. Fract. Mech. – 1976. – 8, № 4. – 593 – 597.
2.Патент 2086947 Российская Федерация, МКИ6 G01N 3/00. Способ определения предела текучести материалов / Ю.И. Славский, М.М. Матлин – Опубл. 10.08.1997. Бюл. № 22.
3.Патент 2011182 Российская Федерация, МКИ5 G01 N3/40 Способ определения предела прочности материала / Ю.И. Славский, М.М. Матлин – Опубл. 10.08.1994. Бюл. № 7.
4.Патент 2386116 Российская Федерация, МПК G01 N 3/28 Способ определения относительной степени упругопластической деформации материала / М. М. Матлин, С.Л. Лебский ; заявитель и патентообладатель ГОУ ВПО «Волгоградский государственный технический университет». – № 2009108630/02 ; заявл. 10.03.09 ; Опубл. 10.04.10, Бюл. № 10.
Ю. Ю. Харинова, аспирант
Ф. А. Уразбахтин, доктор технических наук, профессор Ижевский государственный технический университет
имени М. Т. Калашникова
Принципы построения математической модели нанесения теплозащитных покрытий на поверхности ракет методом напыления
Развитие энергетики неизменно связано с повышением интенсивности теплоэнергетических процессов, что в свою очередь, требует применение конструкционных материалов, обладающих необходимыми теплозащитными свойствами. Например, при производстве баллистических ракет и ракетнокосмических комплексов проблема теплозащиты решается путем нанесения специальных покрытий.
Существует несколько способов формирования покрытий и метод напыления как наиболее перспективный и часто применяемый в общем случае состоит из следующих этапов: подготовка материалов, инструментов и поверхности детали; напыление жидким составом на поверхности детали; сушка покрытия, механическая обработка; контроль основных параметров. Рассматривая этот процесс с точки зрения технической системы, можно выделить шесть основных элементов, каждый из которых выполняет определенные функции и характеризуется набором свойств: оборудование, инструмент, ТЗП, деталь, процесс нанесения и процесс отверждения. Эти элементы соединены между собой функциональными связями [1,2].
В ходе напыления теплозащитных покрытий (ТЗП) возникают критические ситуации (КС), развитие которых часто не позволяет изделию выполнить свое назначение. Между тем, математического аппарата, позволяющего оценить качество процесса нанесения ТЗП, выявить и управлять
254
КС, не существует.
Предлагается, на основе зависимостей, полученных теоретическим и опытным путем построение математической модели процесса напыления ТЗП на поверхности деталей и узлов баллистических ракет на основе системного подхода [3].
Математическая модель (ММ) процесса напыление ТЗП представляется в виде совокупности групп показателей, характеризующих определенный процесс, Каждая из этих групп является конечным множеством показателей. Например, одна из групп описывает свойства подсистемы «обо- рудование-инструмент». Замечено, что чем больше показателей будет входить в систему, тем полнее будет описание рассматриваемого объекта.
В модели, с одной стороны, учитываются изменения свойств инструмента (износ, загрязнение) и поверхности (материал, шероховатость, качество обработки), а так же самого ТЗП, с другой стороны – оценивается работа механизма процесса нанесения и отверждения ТЗП, его эффективность (производительность, затраты времени) и экономичность.
Крайние значения параметров, характеризующих эти процессы, будут характеризовать критические ситуации.
Входными параметрами ММ являются: характеристики ТЗП, давление, подводимое к пульверизатору, диаметр сопла пульверизатора, площадь поверхности, качество подготовки поверхности, количество слоев ТЗП, параметры режимов отверждения и т. д.
К выходным параметрам этой модели относятся: толщина ТЗП, степень отверждения, наличие поверхностных и внутренних дефектов, оценка формируемой шероховатости поверхности, температура, которую способно выдержать покрытие и его стойкость.
Создание такой модели процесса нанесения ТЗП позволяет значительно сократить время на принятие решения о допуске изделия в работу, избежать возможные ошибки проектирования, а так же спрогнозировать КС и управлять ими путем создания рекомендаций и значений конкретных параметров и показателей ТЗП.
Список литературы
1.Горлов, Ю.П. Технология теплоизоляционных и акустических материалов
иизделий. - М.: Высшая школа, 1989. - 384.
2.Полежаев, Ю.В. Тепловая защита. - М.: Энергия, 1976. - 392.
3.Нагибин, Г.В. Технология теплоизоляционных и гипсовых материалов. - М.: Высшая школа, 1966. - 424.
255
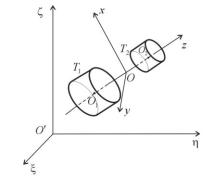
М. А. Худякова, аспирант
С. П. Безгласный, кандидат физико-математических наук, доцент Самарский государственный аэрокосмический университет
имени академика С. П. Королева
Стабилизация программных движений гиростата переменной структуры
Задача по реализации управляемых пространственных движений твердых тел и системы твердых тел имеют важное прикладное значение и широко рассматриваются авторами во многих работах, например [1]-[4]. В данной работе ставится и решается задача об определении управлений, реализующих и стабилизирующих произвольные заданные программные движения системы двух соосных тел с переменными моментами инерции относительно их общего центра масс. Решение проводится построением активного управления, приложенного к системе тел и представляющего собой совокупность программного управления и стабилизирующего управления по принципу обратной связи. Исследование программного движения сводится к анализу нулевого решения неавтономной системы и проводится на основе прямого метода Ляпунова [5]. Метод предельных систем [6] и его модификация [7] позволяют при использовании функций Ляпунова со знакопостоянными производными строить искомое управление в замкнутой аналитической форме в классе непрерывных функций.
Постановка задачи.
Рассмотрим пространственное движение системы гиростата – двух связанных соосных тел: носитель T1 массой m1 и тело T2 с массой m2. Точки O1, O2 – есть центры масс тел T1 и T2, точка O – общий для тел T1 и T2 центр масс; l1 = O1O, l2 = O2O ‒ расстояния между центрами масс тел и их общим центром масс, где l1m1 = l2m2. Примем ζ – угол закрутки второго тела относительно первого. Пусть O' – неподвижная система коорди-
нат; O – подвижная система координат, оси которой во все время движения остаются параллельными осям системы O' ; Oxyz – неинерциальная система координат, неизменно связанная с первым телом (рис. 1).
Рис. 1. Система двух соосных тел
256
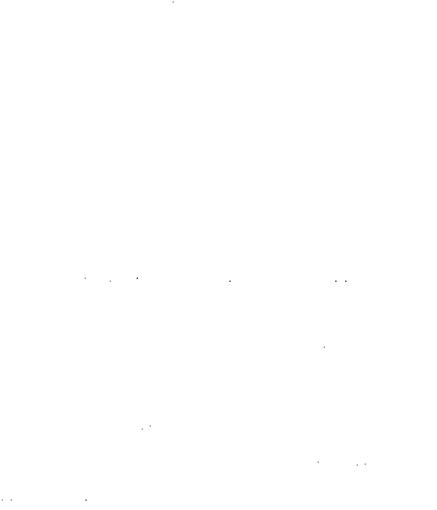
Поставим задачу о реализации управляющими силами, прикладываемыми к системе, произвольно заданных (программных) движений гиростата и стабилизации этих движений.
Вывод уравнений движения.
Уравнения движения исследуемой системы составим в форме уравнений Лагранжа второго рода
|
d T |
T |
|
(1) |
||
|
|
|
|
q |
Q. |
|
|
|
|
||||
|
dt |
q |
|
|
||
Положение гиростата относительно O будем характеризовать уг- |
||||||
лами Эйлера , , . Компоненты |
абсолютной угловой скорости |
1T p, q, r носителя в системе Oxyz имеют вид:
p cos sin sin ,q sin cos sin ,r cos
Абсолютная угловая скорость второго тела в системе координат Oxyz дается равенством 2 1 , а в системе координат, жестко связанной со вторым телом, равенством 2 Г 1 , где
cos |
sin |
0 |
||
|
sin |
cos |
0 |
|
Г |
|
|||
|
0 |
0 |
1 |
|
|
|
есть матрица перехода от Oxyz к жестко связанной со вторым телом системе координат. Тогда кинетическая энергия гиростата
|
|
T |
1 |
(m |
m )( 2 2 |
|
|
2 ) |
1 |
(I |
I |
|
|
) 2 (I |
|
I |
|
) cos |
||||||||||||||||||||||||||||
|
|
|
|
|
|
2 z |
1z |
2 z |
||||||||||||||||||||||||||||||||||||||
|
|
|
|
|
|
2 |
|
|
|
1 |
|
|
|
|
2 |
|
|
|
|
|
|
|
|
|
2 |
|
|
1z |
|
|
|
|
|
|
|
|
|
|
|
|||||||
|
|
|
|
|
|
|
|
|
|
|
|
|
|
|
|
|
|
|
|
|
|
|
|
|
|
|
|
|
|
|
|
|
|
|
|
|
|
|
|
|
|
|
||||
|
|
|
|
1 |
[(I |
|
|
I |
|
|
cos2 I |
|
|
sin2 ) sin2 sin (I |
I |
|
) cos2 |
|
|
|||||||||||||||||||||||||||
|
|
|
|
1x |
2 x |
2 y |
2 z |
|
|
|||||||||||||||||||||||||||||||||||||
|
|
|
|
2 |
|
|
|
|
|
|
|
|
|
|
|
|
|
|
|
|
|
|
|
|
|
|
|
|
|
|
|
|
1z |
|
|
|
|
|
|
|||||||
|
|
|
|
|
|
|
|
|
|
|
|
|
|
|
|
|
|
|
|
|
|
|
|
|
|
|
|
|
|
|
|
|
|
|
|
|
|
|
|
|
|
|
|
|
|
|
|
|
|
(I |
2 x |
I |
2 y |
sin 2 I |
I |
2 x |
sin2 I |
2 y |
cos2 ) cos2 sin2 ] 2 |
|
|||||||||||||||||||||||||||||||||
|
|
|
|
|
|
|
|
|
|
|
|
|
|
1y |
|
|
|
|
|
|
|
|
|
|
|
|
|
|
|
|
|
|
|
|
|
|
|
|
||||||||
|
1 |
[(I |
|
|
I |
|
) sin 2 sin (I |
|
I |
|
|
) cos 2 sin 2 sin |
|
|
|
|
||||||||||||||||||||||||||||||
|
|
|
|
2 x |
2 y |
|
|
|
|
|||||||||||||||||||||||||||||||||||||
2 |
|
1x |
|
|
|
|
1y |
|
|
|
|
|
|
|
|
|
|
|
|
|
|
|
|
|
|
|
|
|
|
|
|
|
|
|
|
|
|
|
|
|||||||
|
|
|
|
|
|
|
|
|
|
|
|
|
|
|
|
|
|
|
|
|
|
|
|
|
|
|
|
|
|
|
|
|
|
|
|
|
|
|
|
|
|
|
|
|||
(I |
|
cos 2 I |
|
) sin 2 sin ] |
|
1 |
[(I |
|
I |
|
|
cos2 I |
|
sin2 ) cos2 |
|
|||||||||||||||||||||||||||||||
2 x |
2 y |
|
|
|
2 x |
2 y |
||||||||||||||||||||||||||||||||||||||||
|
|
|
|
|
|
|
|
|
|
|
|
|
|
|
|
|
|
|
|
|
|
|
|
|
2 |
|
|
1x |
|
|
|
|
|
|
|
|
|
|
|
|||||||
|
|
|
|
|
|
|
|
|
|
|
|
|
|
|
|
|
|
|
|
|
|
|
|
|
|
|
|
|
|
|
|
|
|
|
|
|
|
|
|
|
|
|
|
|
||
(I |
|
I |
|
|
|
sin2 I |
|
cos2 |
) sin2 |
1 |
(I |
|
I |
|
) sin 2 sin 2] 2 I |
|
|
|||||||||||||||||||||||||||||
1y |
2 x |
2 y |
|
2 y |
2 x |
2 z |
||||||||||||||||||||||||||||||||||||||||
|
|
|
|
|
|
|
|
|
|
|
|
|
|
|
|
|
|
|
|
|
|
|
|
2 |
|
|
|
|
|
|
|
|
|
|
|
|
|
|||||||||
|
|
|
|
|
|
|
|
|
|
|
|
|
|
|
|
|
|
|
|
|
|
|
|
|
|
|
|
|
|
|
|
|
|
|
|
|
|
|
|
|
|
|
|
|
||
I |
|
cos |
|
|
1 |
I |
|
2 |
|
|
|
|
|
|
|
|
|
|
|
|
|
|
|
|
|
|
|
|
|
|
|
|
|
|
|
|||||||||||
|
|
|
|
|
|
|
|
|
|
|
|
|
|
|
|
|
|
|
|
|
|
|
|
|
|
|
|
|
|
|
||||||||||||||||
|
|
2 z |
|
|
|
|
|
|
|
|
|
|
|
2 |
|
2 z |
|
|
|
|
|
|
|
|
|
|
|
|
|
|
|
|
|
|
|
|
|
|
|
|
|
|
|
|
|
|
где |
Iix |
Iix (t), Iiy |
Iiy (t), Iiz |
Iiz (t), (i 1, 2) |
|
– главные моменты инерции |
тел Ti, вычисляемые относительно общего центра масс O согласно теоре-
257
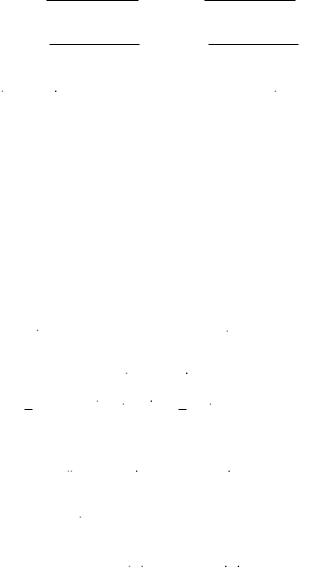
ме Гюйгенса-Штейнера через центральные главные моменты инерции тел
ˆ |
ˆ |
|
|
ˆ |
|
, (i 1, 2) |
согласно равенствам: |
|
|
|
|
|
|
|
|
|
|
|
|
|
|
|
|
|
|
|
|||||||||||||||||||||||||||||||||
I |
ix |
, I |
iy |
, I |
iz |
|
|
|
|
|
|
|
|
|
|
|
|
|
|
|
|
|
|
|
|||||||||||||||||||||||||||||||||||
|
|
|
|
|
|
|
|
|
|
|
|
|
|
|
|
|
|
|
|
|
|
|
|
|
|
|
|
|
|
|
|
|
|
|
|
|
|
|
|
|
|
|
|
|
|
|
|
|
|
|
|
|
|
|
|||||
|
|
|
|
|
|
|
|
|
|
|
|
|
|
|
|
m (m l |
|
m l ) |
2 |
|
|
|
|
|
|
|
|
|
|
m (m l m l ) |
2 |
|
|
|
|
|
|||||||||||||||||||||||
|
|
|
|
I |
|
|
|
|
I |
|
|
|
|
|
|
|
, I |
|
|
I |
|
|
|
, I |
|
|
I |
|
, |
||||||||||||||||||||||||||||||
|
|
|
|
|
|
|
|
|
|
|
|
1 |
|
|
2 1 |
|
|
2 |
2 |
|
|
|
|
|
|
|
|
|
1 |
|
|
2 1 |
2 |
2 |
|
|
|
|
|
||||||||||||||||||||
|
|
|
|
|
|
|
|
|
|
|
|
ˆ |
|
|
|
|
|
|
|
|
|
|
|
|
|
|
|
|
|
|
|
ˆ |
|
|
|
|
|
|
|
|
|
|
|
ˆ |
|
|
|||||||||||||
|
|
|
|
|
|
1x |
|
|
|
1x |
|
|
|
|
|
(m m ) |
2 |
|
|
|
|
|
|
1y |
|
1y |
|
|
|
|
(m m ) |
2 |
|
|
1z |
1z |
|
||||||||||||||||||||||
|
|
|
|
|
|
|
|
|
|
|
|
|
|
|
|
|
|
|
|
|
|
|
|
|
|
|
|
|
|
|
|
|
|
|
|
|
|
|
|
|
|
|
|
|
|
|
|||||||||||||
|
|
|
|
|
|
|
|
|
|
|
|
|
|
|
|
|
|
|
|
|
1 |
|
|
2 |
|
|
|
|
|
|
|
|
|
|
|
|
|
|
|
|
|
|
|
|
|
1 |
2 |
|
|
|
|
|
|
|
|
|
|
|
|
|
|
|
|
|
|
|
|
|
|
|
|
|
|
|
|
|
m (m l |
|
m l ) |
2 |
|
|
|
|
|
|
|
|
|
|
m |
|
(m l |
m l ) |
2 |
|
|
|
|
|
|||||||||||||||||||
|
|
|
|
I |
|
|
|
|
|
I |
|
|
|
|
|
|
|
, I |
|
|
|
I |
|
|
|
|
, I |
|
I . |
||||||||||||||||||||||||||||||
|
|
|
|
|
|
|
|
|
|
|
|
|
2 |
|
1 1 |
|
1 2 |
|
|
|
|
|
|
|
|
|
|
2 |
|
1 1 |
|
|
1 2 |
|
|
||||||||||||||||||||||||
|
|
|
|
|
|
|
|
|
|
|
|
ˆ |
|
|
|
|
|
|
|
|
|
|
|
|
|
|
|
|
ˆ |
|
|
|
|
|
|
|
|
|
|
ˆ |
|
||||||||||||||||||
|
|
|
|
|
|
2 x |
|
|
|
2 x |
|
|
|
|
(m m ) |
2 |
|
|
|
|
|
|
|
2 y |
|
|
2 y |
|
|
|
|
(m m ) |
2 |
|
|
|
|
2 z |
|
2 z |
|||||||||||||||||||
|
|
|
|
|
|
|
|
|
|
|
|
|
|
|
|
|
|
|
|
|
|
|
|
|
|
|
|
|
|
|
|
|
|
|
|
|
|
|
|
|
|
|
|
|
|
||||||||||||||
|
|
|
|
|
|
|
|
|
|
|
|
|
|
|
|
|
|
|
|
|
1 |
|
|
2 |
|
|
|
|
|
|
|
|
|
|
|
|
|
|
|
|
|
|
|
|
|
1 |
2 |
|
|
|
|
|
|
|
|
|
|
|
|
|
|
Величина T представлена в виде |
|
суммы: T = |
T2 |
|
+ T1 |
+ T0, где |
|||||||||||||||||||||||||||||||||||||||||||||||||||
T |
|
1 |
qT A(t, q )q |
|
‒ квадратичная форма скоростей |
q , |
задаваемая сим- |
||||||||||||||||||||||||||||||||||||||||||||||||||||
|
2 |
|
2 |
|
|
|
|
|
|
|
|
|
|
|
|
|
|
|
|
|
|
|
|
|
|
|
|
|
|
|
|
|
|
|
|
|
|
|
|
|
|
|
|
|
|
|
|
|
|
|
|
|
|
|
|
|
|||
|
|
|
|
|
|
|
|
|
|
|
|
|
|
|
|
|
|
|
|
|
|
|
|
|
|
|
|
|
|
|
|
|
|
|
|
|
|
|
|
|
|
|
|
|
|
|
|
|
|
|
|
|
|
|
|
||||
метричной матрицей A(t, q) {aij } с элементами |
|
|
|
|
|
|
|
|
|
|
|
|
|||||||||||||||||||||||||||||||||||||||||||||||
|
|
|
|
a11 I1z I2 z , a12 |
a21 2(I1z |
I2 z ) cos , a13 a31 0, |
|
|
|
|
|
||||||||||||||||||||||||||||||||||||||||||||||||
|
|
|
|
a |
|
|
|
(I |
1x |
I |
2 x |
cos2 I |
2 y |
sin |
2 ) sin2 sin2 (I |
|
|
I |
2 z |
) cos2 |
|||||||||||||||||||||||||||||||||||||||
|
|
|
|
|
|
22 |
|
|
|
|
|
|
|
|
|
|
|
|
|
|
|
|
|
|
|
|
|
|
|
|
|
|
|
|
|
|
|
|
|
1z |
|
|
|
|
|
||||||||||||||
|
|
|
|
(((I |
2 x |
I |
2 y |
) sin 2 I |
|
|
|
|
I |
2 x |
sin2 I |
2 y |
cos2 ) sin2 cos2 , |
||||||||||||||||||||||||||||||||||||||||||
|
|
|
|
|
|
|
|
|
|
|
|
|
|
|
|
|
|
|
|
|
|
|
|
1y |
|
|
|
|
|
|
|
|
|
|
|
|
|
|
|
|
|
|
|
|
|
|
|
|
|||||||||||
|
|
|
a23 a32 (I1x |
|
I1y ) sin sin 2 (I2 x I2 y ) sin cos 2 sin 2 |
||||||||||||||||||||||||||||||||||||||||||||||||||||||
|
|
|
(I2 x cos 2 I2 y ) sin sin 2 , |
|
|
|
|
|
|
|
|
|
|
|
|
|
|
|
|
|
|
|
|
|
|
||||||||||||||||||||||||||||||||||
|
|
|
a |
|
|
|
|
(I |
|
I |
2 x |
cos2 I |
2 y |
|
sin2 |
) cos2 (I |
I |
2 x |
sin2 |
|
|
||||||||||||||||||||||||||||||||||||||
|
|
|
|
|
33 |
|
|
|
|
1x |
|
|
|
|
|
|
|
|
|
|
|
|
|
|
|
|
|
|
|
|
|
|
|
|
|
|
1y |
|
|
|
|
|
|
|
|
|
|||||||||||||
|
|
|
I |
|
|
|
cos2 ) sin2 |
|
1 |
(I |
|
|
|
|
|
I |
|
|
) sin2 sin2 . |
|
|
|
|
|
|
|
|
|
|
|
|
||||||||||||||||||||||||||||
|
|
|
2 y |
2 |
2 y |
|
2 x |
|
|
|
|
|
|
|
|
|
|
|
|
||||||||||||||||||||||||||||||||||||||||
|
|
|
|
|
|
|
|
|
|
|
|
|
|
|
|
|
|
|
|
|
|
|
|
|
|
|
|
|
|
|
|
|
|
|
|
|
|
|
|
|
|
|
|
|
|
|
|
|
|||||||||||
|
|
|
|
|
|
|
|
|
|
|
|
|
|
|
|
|
|
|
|
|
|
|
|
|
|
|
|
|
|
|
|
|
|
|
|
|
|
|
|
|
|
|
|
|
|
|
|
|
|
|
|
|
|
|
|
|
|
||
T BT (t, q)q ‒ |
линейная форма скоростей |
|
q , определяемая вектором- |
||||||||||||||||||||||||||||||||||||||||||||||||||||||||
|
1 |
|
|
|
|
|
|
|
|
|
|
|
|
|
|
|
|
|
|
|
|
|
|
|
|
|
|
|
|
|
|
|
|
|
|
|
|
|
|
|
|
|
|
|
|
|
|
|
|
|
|
|
|
|
|
|
|
|
|
столбцом B(t, q) |
|
с компонентами: |
|
|
|
|
|
|
|
|
|
|
|
|
|
|
|
|
|
|
|
|
|
|
|
B1 I2z , B2 I2 z cos , B3 0.
T0 12 (m1 m2 )( 2 2 2 ) 12 I2 z 2 – скалярная функция.
С учетом структуры кинетической энергии уравнения (1) запишутся в следующем виде:
Aq M |
A |
B |
|
BT |
)q |
B |
|
T |
Q, |
|
t q ( |
qT |
q |
t |
q |
(2) |
|||||
|
|
|
|
|
|
|
|
0 |
|
|
где через M M (q, q) обозначен вектор-столбец с компонентами, вычисляемыми по формуле
Mi |
aij qk q j |
|
|
1 akj qk q j , (i 1,3) |
|||||||
|
3 |
|
|
|
|
|
3 |
|
|
|
|
|
|
|
|
|
|
|
|
|
|
|
|
|
i,k 1 |
q |
|
2 |
i,k 1 |
q |
|||||
|
k |
|
|
|
i |
||||||
|
|
|
|
|
258 |
|
|
|
|
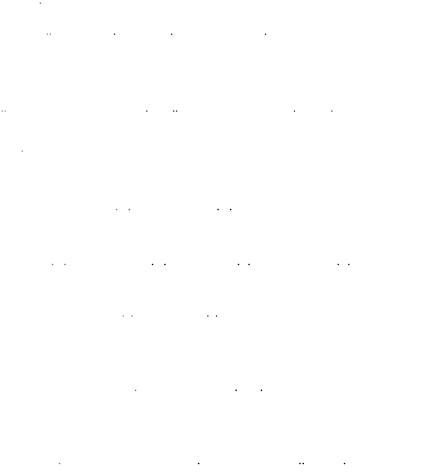
Вектор обобщенных сил Q = Qв + Qc есть сумма внешних сил Qв и управляющих воздействий Qc = Qp + Qs, определяемых в дальнейшем и являющихся совокупностью программных и стабилизирующих сил.
Ниже предполагаем, что движение исследуемой механической системы происходит без воздействия внешних сил, то есть Qв = 0.
Построение программных и стабилизирующих управлений.
Пусть необходимо, чтобы система совершала некоторое программное
движение
r
(t), r
(t)
. Определим, как и в [8], программные силы:
|
|
|
|
|
|
|
|
|
|
|
|
|
|
|
|
|
A |
|
|
B |
B |
|
|
|
|
|
B |
|
|
T |
|
|
(3) |
||||||||||||||
Qp Ar M (r (t), r (t)) |
|
|
|
|
r |
|
|
|
|
|
|
|
|
r |
|
|
|
0 |
. |
||||||||||||||||||||||||||||
|
t |
|
|
|
|
|
q |
t |
q |
|
|
||||||||||||||||||||||||||||||||||||
|
|
|
|
|
|
|
|
|
|
|
|
|
|
|
|
|
|
|
|
q |
|
|
|
|
|
|
|
|
|
|
|
|
|
|
|||||||||||||
Введем новые |
обобщенные |
|
координаты (отклонения) |
по правилу |
|||||||||||||||||||||||||||||||||||||||||||
x q r (t) . Составим уравнения возмущенного движения: |
|
|
|
|
|
|
|
||||||||||||||||||||||||||||||||||||||||
Ах M M |
|
B |
|
|
|
B |
|
|
|
|
|
Аr M |
|
|
B |
|
|
B |
|
|
A |
|
|
|
|||||||||||||||||||||||
|
|
|
|
|
|
|
|
|
|
x |
|
|
|
|
|
|
|
|
|
|
r |
|
|
|
x |
|
|||||||||||||||||||||
x |
|
|
x |
x |
|
x |
t |
||||||||||||||||||||||||||||||||||||||||
|
|
|
|
|
|
|
|
|
|
|
|
|
|
|
|
|
|
|
|
|
|
|
|
|
|
|
|
|
|
(4) |
|||||||||||||||||
A r B T0 Q Q |
p |
, |
|
|
|
|
|
|
|
|
|
|
|
|
|
|
|
|
|
|
|
|
|
|
|
|
|
|
|
|
|
|
|
|
|||||||||||||
t |
t |
x |
|
|
|
|
s |
|
|
|
|
|
|
|
|
|
|
|
|
|
|
|
|
|
|
|
|
|
|
|
|
|
|
|
|
|
|
|
|
|
|
|
|
||||
|
|
|
|
|
|
|
|
|
|
|
|
|
|
|
|
|
|
|
|
|
|
|
|
|
|
|
|
|
|
|
|
|
|
|
|
|
|
|
|
|
|
|
|||||
где через M , M' и M' ' |
обозначены соответственно формы: |
|
|
|
|
|
|
|
|||||||||||||||||||||||||||||||||||||||
|
Mi aij |
xk xj 1 |
|
akj |
xk xj , ( i 1,3); |
|
|
|
|
|
|
|
|||||||||||||||||||||||||||||||||||
|
|
|
3 |
|
|
|
|
|
|
|
|
|
|
|
|
|
|
|
|
|
3 |
|
|
|
|
|
|
|
|
|
|
|
|
|
|
|
|
|
|
|
|
|
|
|
|
|
|
|
|
|
|
|
|
|
|
|
|
|
|
|
|
|
|
|
|
|
|
|
|
|
|
|
|
|
|
|
|
|
|
|
|
|
|
|
|
|
|
|
|
|
|
|
|
|
|
|
|
|
j,k 1 |
|
x |
|
|
|
|
|
|
2 |
j,k 1 |
x |
|
|
|
|
|
|
|
|
|
|
|
|
|
|
|
|
|
|
|
|
|
||||||||||||
|
|
|
|
|
|
|
k |
|
|
|
|
|
|
|
|
|
|
|
i |
|
|
|
|
|
|
|
|
|
|
|
|
akj rk x j , |
|||||||||||||||
Mi aij xk rj 1 |
akj |
|
xk rj aij rk x j 1 |
||||||||||||||||||||||||||||||||||||||||||||
3 |
|
|
|
|
|
|
|
3 |
|
|
|
|
|
|
|
|
|
|
|
|
3 |
|
|
|
|
|
|
|
|
|
|
|
|
|
|
3 |
|
|
|
|
|
|
|
||||
j,k 1 |
x |
|
|
2 |
|
j,k 1 |
x |
|
|
|
|
|
|
|
|
j,k 1 |
x |
|
|
|
|
|
2 |
|
j,k 1 |
x |
|
|
|
||||||||||||||||||
k |
|
|
|
|
|
|
i |
|
|
|
|
|
|
|
|
k |
|
|
|
|
|
|
|
|
i |
|
|
|
|||||||||||||||||||
|
|
Mi aij rk rj 1 |
akj rk rj , ( i 1,3). |
|
|
|
|
|
|
|
|
|
|||||||||||||||||||||||||||||||||||
|
|
|
|
3 |
|
|
|
|
|
|
|
|
|
|
|
|
|
|
3 |
|
|
|
|
|
|
|
|
|
|
|
|
|
|
|
|
|
|
|
|
|
|
|
|
|
|
||
|
|
|
|
j,k 1 |
x |
|
|
|
|
|
|
2 |
|
j,k 1 |
x |
|
|
|
|
|
|
|
|
|
|
|
|
|
|
|
|
|
|
|
|
|
|||||||||||
|
|
|
|
|
|
k |
|
|
|
|
|
|
|
|
|
i |
|
|
|
|
|
|
|
|
|
|
|
|
|
|
|
|
|
|
|
|
|
Задачу о стабилизации решим прямым методом Ляпунова с использо-
ванием функции Ляпунова, которую согласно [8] выберем в виде: |
|
||||||||||||||||
V (t, x, x ) |
1 |
x |
T |
Cx |
1 |
x |
T |
Ax. |
|
|
(5) |
||||||
|
2 |
|
|
2 |
|
|
|
||||||||||
Функция (5) является определенно-положительной. |
|
|
|
||||||||||||||
|
|
|
|
||||||||||||||
Определим стабилизирующее управление равенством: |
|
|
|||||||||||||||
|
B |
BT |
B |
|
|
T |
|
A |
|
||||||||
Qs Cx Dx M |
|
|
|
|
|
|
r |
|
|
|
|
0 |
Ar |
|
r , |
||
x |
T |
|
x |
t |
x |
t |
|||||||||||
|
|
|
|
|
|
|
|
|
где матрица D является ограниченной и неисчезающей и выбирается из условий:
d0 E D(t, q) d1E, (0 d0 d1 const);
259
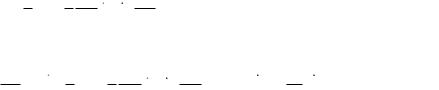
( |
1 A |
|
1 A |
r r |
T |
A |
L D) c E, |
||
|
|
|
|
|
|||||
|
2 t |
|
2 x |
T |
|
|
x |
T |
0 |
|
|
|
|
|
|
|
(0 c |
const). |
0 |
|
Тогда производная функции (5) в силу системы (4) имеет оценку
dV |
x |
|
( |
1 A |
|
1 A |
r r |
T |
A |
L D)x |
|
0 |
|
x |
2 |
|
0 |
||
|
|
||||||||||||||||||
|
|
|
|
|
|
|
|
|
|||||||||||
|
|
|
|
|
|
|
|
|
|
|
|
|
|
|
|
||||
dt |
|
|
|
2 t |
|
2 x |
T |
|
|
x |
T |
|
2 |
|
|
|
|
|
|
|
|
|
|
|
|
|
|
|
|
|
|
|
|
и является определенно-отрицательной функцией по скоростям. Таким образом, на основе теоремы из [7] имеем асимптотическую устойчивость исследуемого программного движения.
Список литературы
1. Афанасьев, В.Н. и др. Математическая теория конструирования систем управления. М.: Высш. шк., 1989. - 447.
2.Летов, А.М. Динамика полета и управление. М.: Наука, 1969. - 359.
3.Зубов, В.И. Проблема устойчивости процессов управления. Л.: Судостроение, 1980. - 375.
4.Раушенбах, В.В. и др. Управление ориентацией космических аппаратов. М.: Наука, 1974. - 589.
5.Руш, Н.и др. Прямой метод Ляпунова в теории устойчивости. М.: Мир, 1980.
301 с.
6.Artstein, Z. Topological dynamics of an ordinary equations // J. Differ. Equat. 1977. V. 23. - 216-223.
7.Андреев, А.С. Об асимптотической устойчивости и неустойчивости нулевого решения неавтономной системы // ПММ 1984. Т.48. Вып.2. -. 225-232.
8.Bezglasnyi, S.P. The stabilization of program motions of controlled nonlinear mechanical systems // Korean J. Comput. Appl. Math. 2004. V. 14, № 1-2.- 251-266.
А. О. Чевелева, аспирант
М. А. Болотов, кандидат технических наук Н. Д. Проничев, доктор технических наук, профессор
М. А. Болотов, кандидат технических наук, ассистент Самарский государственный аэрокосмический университет
имени академика С. П. Королева
Разработка информационной модели при исследовании погрешностей координатных измерений геометрических параметров
деталей газотурбинного двигателя
Известно, что детали авиадвигателей характеризуются высокими требованиями к показателям точности изготовления, ажурностью конструкции, сложной схемой присутствующих внутренних и внешних силовых
260

факторов в процессе обработки и эксплуатации, и как следствие, сложной геометрией погрешностей формы. Перечисленные обстоятельства определяют детали ГТД как сложный объект производства и контроля, в частности.
Внастоящее время в двигателестроении для контроля на промежуточном и окончательном этапах получают широкое распространение современные координатно-измерительные машины (КИМ), зарекомендовавшие себя в промышленности ввиду широких возможностей и высокой точности. Однако в ряде случаев при их внедрении и использовании получаемый результат измерения (контроля) может быть недостоверен в силу следующих причин: 1) недостоверного использования моделей оценки геометрических параметров при разработке методик выполнения измерений (МВИ); 2) недостаточно внимательного отношения к выбору параметров МВИ (количества контролируемых точек и схемы их расположения по поверхности); 3) близости инструментальных погрешностей КИМ
квеличине допуска контролируемых геометрических параметров. Для учета перечисленных причин, обеспечения достоверности контроля и эффективности использования КИМ необходимо осуществлять моделирование процесса измерений.
При моделировании процесса измерения возникает ситуация, когда погрешность измерения зависит от нескольких факторов и является сложной. Так, в результате анализа источника [1], можно составить следующую схему, представленную на рис. 1. В связи с этим большую значимость имеет разработка информационных моделей моделирования процесса координатных измерений.
Всхеме, приведенной на рис. 1: ε − погрешность измерения (оценива-
ния); источники погрешности: ε1 − входные данные от оборудования (такие как погрешность щупа), погрешности, связанные с жесткостью и ди-
намикой машины, и производственные погрешности; ε2 − входные данные от стратегии выборочного контроля, такие как недостаточное количе-
ство выборочных точек и ненадлежащая выборочная траектория; ε3 − входные данные от алгоритмов подбора данных, такие как недостатки в
выбираемых алгоритмах и вычислительных приближениях; ε4 − входные данные от условия измерения, которые включают в себя температурные искажения и вибрацию измерительного оборудования.
Рис. 1. Информационная модель влияющих факторов
В ходе множества практических и теоретических исследований была выработана следующая информационная модель, представленная на рис. 2.
261
Вбазе данных технологий изготовления содержится информация следующего характера: вид механической обработки; технические требования на допуск (формы, расположения, размера); характер ожидаемой и фактической производственной погрешности (волнистость, кратность огранки и т.д.); величина фактической производственной погрешности.
Целесообразность рассмотрения лишь методов механической обработки заключается в применимости координатно-измерительных машин на окончательных этапах технологического процесса вследствие высокой точности и прецизионности упомянутых машин. Однако не следует пренебрегать, к примеру, процессом получения заготовки, поскольку, опираясь на анализ очага деформации: структурного состояния, напряженнодеформированного состояния, − можно теоретически прогнозировать форму деформации и ее величину. Технологическим аспектам получения кольцевых заготовок посвящены работы В. А. Костышева [2].
Для исследования погрешностей формы поверхностей осуществлялось тщательное сканирование, в результате которого формировалось облако точек. При снятии координат точек помимо информации о производственных погрешностях добавляется влияние инструментальной погрешности. С целью нивелировать влияние инструментальной погрешности на действительную геометрию обработанной детали исходная поверхность подвергается фильтрации от инструментальной погрешности путем использования алгоритма прямого и обратного преобразования Фурье. Проведенный для шлифованной поверхности опыт по установлению влияния инструментальной погрешности КИМ на выявление неплоскостности показал целесообразность применения фильтрации, в частности с помощью преобразования Фурье, вследствие сильного влияния инструментальной погрешности при выявлении формы. Кроме того, опыт по выявлению влияния реконструкции исходной поверхности с помощью Фурьепреобразования на результаты моделирования показал, что само преобразование Фурье практически не искажает результаты [3].
Вбазе данных метрологических характеристик координатноизмерительных машин содержится информация о рабочем объеме КИМ, типе КИМ, величинах паспортной погрешности.
Вбазе сформированных зависимостей хранится информация о результатах предыдущих теоретических и практических экспериментов. В нее включаются влияющие и зависимые факторы, диапазоны их изменения и условия проведения эксперимента (температуру, влажность, давление, использование температурной компенсации). В зависимости от модели представления информация может храниться в табличной форме или в виде аппроксимирующей зависимости.
262
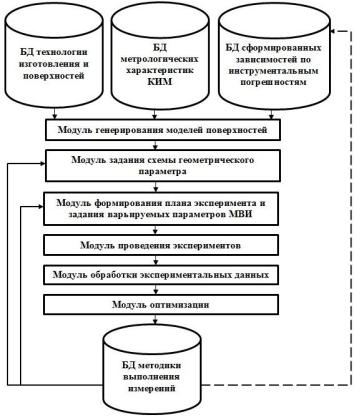
Рис. 2. Блок-схема информационной модели процесса координатных измерений
В модуле генерирования моделей поверхностей предусматривается два варианта представления поверхности:
− полученная информация о тщательно измеренной реальной поверхности из программного обеспечения PC-DMIS (или другого программного обеспечения) в виде координат точек в декартовой системе координат. Преимуществом данного представления является, как отмечалось ранее, оперирование точками реальной поверхности, которые содержат в себе информацию о погрешностях, действующих от совокупности технологических методов обработки деталей ГТД, инструментальной погрешности, вносимой средством координатных измерений, в частности, погрешности, связанной с конфигурацией выбранного датчика/щупа. Недостатком данного способа является более высокая трудоемкость при сборе координат точек поверхностей, а в ряде случаев сложная осуществимость измерения такого количества точек.
263
− моделирование поверхностей, имеющих априорно известное отклонение формы, с использованием рядов Фурье. Моделированные поверхности используются с целью отработки методик для их дальнейшего применения на реальных поверхностях деталей. В основе моделирования заложены алгоритмы конструирования поверхностей элементов, приближенных к реальным поверхностям. Они реализуются путем добавления ортогонально к номинальной геометрии поверхностей погрешностей формы, встречающихся на деталях, и инструментальных погрешностей средства измерения.
Вмодуле задания схемы генерирования геометрического параметра учитывается схема задания геометрического параметра, формируемые построения, расчет геометрического параметра из параметров заменяющих элементов. При этом в модуле также содержатся рекомендации по использованию тех или иных схем геометрических параметров к различным конструкциям при учете требуемой точности.
Вмодуле формирования плана эксперимента и задания варьируемых параметров МВИ формируются параметры, подлежащие анализу (к примеру, диапазон габаритных размеров исследуемого геометрического элемента, диапазон инструментальной погрешности). Как варьируемыми, так
инеизменяющимися могут быть параметры МВИ, под которыми понимают: правило расположения точек контроля по поверхности, число точек в выборке, типы используемых заменяющих элементов (ЗЭ) (линия, плоскость, окружность, цилиндр), схему формирования геометрического параметра (ГП).
Воснове модуля проведения экспериментов лежит часто используемый численный метод Монте-Карло решения математических задач [5].
На выходе из модуля обработки экспериментальных данных после проверки соответствия распределения вычисленного параметра известным законам распределения формируются оценки выборок в виде нижней и верхней границы, а также математического ожидания. Данные оценки рассчитываются для различных параметров методики измерения, вследствие чего, получается многомерный массив оценок. Оценка случайных величин производится исходя из заданной доверительной вероятности α, обычно принимаемой на уровне 99,73 % или 95 % в соответствии с требованиями руководящих документов.
В модуле оптимизации осуществляется построение регрессионных зависимостей оценок погрешностей измерения от параметров методики измерения. На данном этапе возможен возврат к модулям задания схемы геометрического параметра и модулю создания плана эксперимента, а также их корректировка. К примеру, опыт показал [6], что контроль не рекомендуется проводить по числу точек, кратному количеству граней, поскольку данный вид погрешности имеет периодический характер и возможны случаи выявления лишь части макрорельефа.
На выходе формируются выражения для различных геометрических
264
параметров в зависимости от параметров методики измерения. Полученные выражения используются для аттестации и разработки методик измерения деталей ГТД, решения прямой и обратной метрологических задач.
Требование к высоким затратам аппаратных ресурсов (производительность и объем оперативной и постоянной памяти) требует рациональной организации программно-аппаратного комплекса.
Программная часть информационных моделей реализовывалась в системе Matlab®. Была выбрана, поскольку обладает высокой производительностью вычислений, расширенными функциональными возможностями, обусловленными наличием, так называемых пакетов Toolbox, которые реализуют различные математические методы, например аппроксимацию.
Дальнейшее развитие и совершенствование информационной модели возможно за счет разработки новых высокопроизводительных алгоритмов, реализующих возможность работы на многоядерных рабочих станциях. В перспективе планируется использование вычислительных кластеров.
Список литературы
1. Liu, Q. On the effects of CMM measurement error on form tolerance estimation [Text] / Q.Liu, C.C.Zhang, H.P.Ben Wang. – Measurement 30 (2001). – 33-47.
2.Костышев, В.А. Разработка научно обоснованных методов формоизменения тонкостенных профильных колец авиационных двигателей [Текст]: дис. ...
д.т.н. / В. А. Костышев. – Самара, 1998. – 307.
3.Чевелева, А.О. Исследование влияния вида размерной обработки на формирование методики выполнения измерения на координатно-измерительной машине при выявлении неплоскостности [Текст] / А.О. Чевелева, М.А. Болотов// Самолетостроение России. Проблемы и перспективы: материалы симпозиума с международным участием/ Самарск. гос. аэрокосм. ун-т. – Самара: СГАУ, 2012. –
-414-416
4.Flack, D. Measurment Good Practice Guide №42: CMM Verification [Текст]/
D.Flack. – Elseiver, 2011. – 101.
5.Соболь, М.И. Метод Монте-Карло [Текст] / М. И. Соболь. – Изд. 2-е, испр.
– М.: Наука. Гл. ред. физ.-мат. лит., 1972. – 63.
6.Чевелева, А.О. Формирование оптимальных методик измерения, осуществляемых на координатно-измерительных машинах, с учетом технологии изготовления маложестких деталей типа «кольцо» [Текст] / А.О. Чевелева, М.А. Болотов // Проблемы и перспективы развития двигателестроения: материалы докладов международной научно-технической конференции 28-30 июня 2011. – Самара: СГАУ,
2011. – Ч.2. – 297-299.
265
С. Е. Черемных, А. Н. Гарифуллин, магистранты
А. И. Тананин, кандидат технических наук, профессор Ижевский государственный технический университет имени М. Т. Калашникова
Влияние режима резания на силы резания и оптимизация процесса точения углеродистых сталей
В процессе резания при взаимодействии режущего инструмента с обрабатываемым материалом возникают силы, называемые силами резания. Силы резания действуют на обрабатываемую деталь, режущий инструмент, приспособление, станок. Достаточно точное определение силы резания и ее составляющих необходимо для успешного решения многих практических задач. Это и, определение необходимой мощности приводов станков; и прочностные расчеты при конструировании станков, инструментов и приспособлений; и определение оптимальных условий и режимов резания; и многие другие задачи. Особое значение определение сил резания, создание их математических моделей приобретает при решении вопросов эксплуатации станков с ЧПУ, создания и применения систем диагностики состояния режущего инструмента и процесса резания, нахождения оптимальных вариантов и условий использования адаптивных систем управления [3].
Одним из важных параметров процесса механической обработки, который непосредственно влияет на качество получаемой поверхности, является равнодействующая сила резания и для обеспечения получения качественной поверхности необходим ее контроль. Этот параметр разбивается на составляющие: Pz, Px, Py.
Проведенный литературный обзор и патентный поиск позволяет сделать анализ различных методов определения сил, действующих в процессе токарной обработки [1, 2]. Кроме того разработан общий подход к выводам расчетных зависимостей структурного типа, позволяющих определять составляющие силы резания.
Много разработок авторов позволяют ознакомиться с современным состоянием теории резания металлов по одной из ее важнейших научных задач – определение и управление силами резания [2, 4, 5].
Самым распространенным способом измерения усилий и сил резания при токарной обработки является способ тензометрии. Метод основан на измерении величины деформации упругого измерительного элемента под нагрузкой и изменении электрического сопротивления. Как правило, измерительный элемент входит в измерительный мост, и по изменению напряжения в измерительном мосте, вследствие изменения электрического сопротивления измерительного элемента, можем судить о приложенной силе. Для измерения сил резания применяются специальные устройства – динамометры [2, 4]. Другим вариантом таких устройств являются
266
модифицированные узлы станочного оборудования, которые отслеживают нагрузку на шпиндельный узел либо на узел подачи [1, 3]. Но такие устройства требуют существенной доработки станков и не дают достаточной точности при измерении малых сил, например, при чистовой обработке деталей малых размеров или обработке цветных или легких сплавов, что особенно актуально в приборостроении.
Известны устройства использующие при измерении свойства прямого пьезоэффекта, то есть при деформации пьезоэлектрического кристалла, который используют в качестве чувствительного элемента, генерирует электрический заряд. По величине электрического заряда и судят о приложенной силе. Такие устройства лишены такого большого недостатка как инерционность. Одним из таких приспособлений является устройство, использующее в своей конструкции чувствительный элемент, который встроен в резец. К недостаткам такого устройства следует отнести измерение силы резания только по одной координате и его не универсальность, т.к. оно представляет собой оправку со встроенным чувствительным элементом. Еще одним недостатком данного типа устройств является прокладка проводников вблизи зоны резания, где они подвержены воздействию высоких температур, которые влияют на точность показаний и могут привести к повреждению чувствительного элемента.
Для измерения сил резания также используют индуктивные и индукционные датчики, позволяющие измерять силы в динамике, но такого типа устройства не позволяют измерять большие усилия и имеют малый диапазон измерений.
Для эффективного контроля сил резания в процессе токарной обработки необходимо устройство, которое будет давать точный результат в широком диапазоне измерений и адекватно показывать динамику изменения этих сил. Еще одним условием для востребованности такого устройства должна быть простота его использования, не требующая сложного и дорогостоящего переоборудования технологического оборудования и возможность использования стандартного режущего инструмента. С этой целью в процессе экспериментального исследования используются осциллографы, видео и кинокамеры, различные самописцы. В нашем исследовании планируется использование видеокамеры для фиксирования показаний миллиамперметров. Величины сил резания могут быть выражены эмпирическими формулами, отражающими зависимость составляющих силы резания от условий механической обработки [4]:
P |
Cpz t X Z |
S YZ |
K |
|
; P |
Cp t X Y |
SYY |
K |
|
; P |
Cp |
|
t X X SYX |
K |
, (1) |
|
|
Z |
Y |
|
Y |
|
X |
|
|||||||
Z |
V NZ |
|
|
Y |
V NY |
|
|
X |
|
|
V N X |
|
X |
||
|
|
|
|
|
|
|
|
|
|
|
|
|
где Cpz, Cpy, Cpx – постоянные величины, характеризующие вид обрабатываемого материала, геометрию режущего инструмента и конкретные условия обработки; Xz, Xy, Xx, Yz, Yy, Yx, Nz, Ny, Nx – показатели степени при величинах глубины резания t, рабочей подачи S и скорости резания V; Kz, Ky, Kx – поправочные коэффициенты.
267
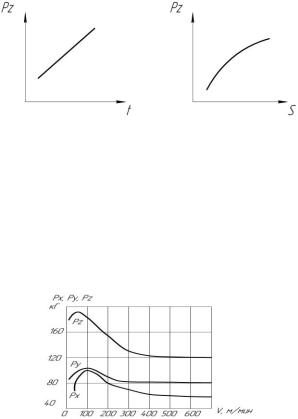
Чем больше глубина резания t и величина рабочей подачи S, тем больше площадь поперечного сечения среза F и объем деформируемого металла и больше сопротивление его стружкообразованию, соответственно больше силы резания. При наружном продольном точении между глубиной резания и силами резания существует прямая пропорциональность (рис. 1) и показатели степени Xpz, Xpy, Xpx обычно равны единице. Между величиной подачи и силами резания также существует прямая зависимость, но значения показателей Ypz, Ypy, Ypx меньше единицы (0,75…0,8). Данное явление объясняется тем, что с ростом величины рабочей подачи увеличивается и толщина срезаемого слоя, а величина коэффициента усадки стружки снижается, так как толстые стружки деформируются меньше, чем тонкие, и следовательно, происходит некоторое снижение величины сил резания.
Зависимость величин сил резания от скорости резания V носит сложный характер (рис. 2), так как между величинами сил резания и коэффициентом усадки стружки существует прямая зависимость [4].
Рис. 1. Влияние глубины резания t и рабочей подачи S на величину силы резания Pz.
Для обработки результатов эксперимента и оптимизации планируется использование метода математического планирования эксперимента [5].
Планирование эксперимента это постановка опыта по заранее составленной схеме, обладающей какими-то оптимальными свойствами.
В резании металлов широко используем зависимость типа
A = CAvnSqtk , |
(2) |
где А ‒ параметр оптимизации (показатель стойкости режущего инструмента, силы, температуры резания и др.); С ‒ постоянный коэффициент.
Рис. 2. Влияние скорости резания V на составляющие силы резания Pz,Py,Px
268
Для нахождения коэффициентов зависимости (2), которая является исследуемой математической моделью, используем планирование эксперимента с преобразованием параметра оптимизации и факторов.
Преобразуем выражение (2) для получения линейной модели (3):
Y=b0+b1x1+b2x2+b3x3 |
(3) |
Для определения коэффициентов уравнения (3) используем полный факторный эксперимент типа 23. Преобразование независимых переменных Xi к безразмерным переменным производим с помощью уравнения преобразования [5].
Далее находим уравнение регрессии и проверяем его адекватность. Определяем показатели степеней и постоянный коэффициент Срz в
обобщенной зависимости:
P C |
P |
t xPz S yPZ v zPz . |
(4) |
z |
|
|
|
|
z |
|
|
Аналогично находим Cpy, Cpx, и для каждой составляющей силы резания записываем уравнения регрессии.
Разработанная методика экспериментальных исследований и обработка результатов позволяет получить уравнения регрессии для составляющих силы резания от режима резания и оценивать протекание процесса резания, качество обработанной поверхности.
Список литературы
1.Григорьев, С.Н. и др. Инструментальная оснастка станков с ЧПУ: Справочник / Под общ. ред. Маслова А.М.– М.: Машиностроение, 2006. – 554.
2.Руководство к универсальному динамометру УДМ конструкции ВНИИ. М.: Всесоюзный научно-исследовательский институт (ВНИИ), 1983. – 22с.
3.Пупков, К.А. Методы классической и современной теории автоматического управления. Том 4. М.: Издательство МГТУ им. Баумана Н.Э., 2004. ‒ 744 с.: ил.
4.Евсеев, Д.Г. Измерение сил резания при токарной обработке: Методические указания к лабораторной работе по дисциплине «Резание металлов» - М.: МИИТ,
2006. – 34 с.
5.Солоненко, В.Г. Резание металлов и режущие инструменты: Учеб. пособие для вузов. – 2-е изд. стер. – М.: Высш. шк., 2008. – 414 с.
Д. В. Чирков, аспирант
Л. А. Галаган, доктор технических наук, профессор Ижевский государственный технический университет имени М. Т. Калашникова
Способы повышения устойчивости оружия со сбалансированной автоматикой
Системы со сбалансированной автоматикой были созданы как альтер-
269
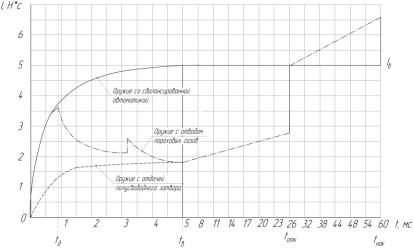
нативное решение систем с классической компоновкой, направленное на повышение устойчивости оружия при стрельбе очередями исключением ударов при работе автоматики. Традиционно эти схемы имеют два приводных поршня, жестко связанных с затворной рамой и балансиром. Для синхронизации движения затворной рамы и балансира между ними существует кинематическая связь через шестерни-звездочки. Характер передачи импульса отдачи данных систем при идеальной балансировке полностью копирует характер отдачи неавтоматического стрелкового оружия (рис. 1), т. е. к концу периода последействия на стрелка передается полный импульс выстрела, что обуславливает их малое преимущество в сравнении с классическими системами с отводом пороховых газов. Результаты исследований по формированию импульса отдачи ручного автоматического оружия с разными схемами работы автоматики, выполненные в соответствии с работой [1] для исходных данных автомата АК74 (рис. 1), позволили сделать некоторые выводы о возможностях повышения устойчивости оружия со сбалансированной автоматикой.
Рис. 1. Особенности формирования импульса отдачи в системах ручного автоматического оружия с разными типами работы автоматики
Работа автоматики должна обеспечивать изменение импульса отдачи на начальном участке (от начала до конца выстрела), аналогичное системе с отводом пороховых газов, либо с отдачей полусвободного затвора, при последующем исключении ударов в крайних положениях. Получение требуемого изменения импульса отдачи предполагает использование соответствующих схем работы автоматики.
Одной из них может быть схема со сбалансированной автоматикой с одним приводным поршнем, представленная на рис. 2, импульсная диа-
270
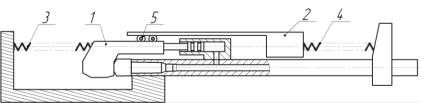
грамма которой приведена на рис. 3. Повышение устойчивости оружия достигается уменьшением импульса отдачи к концу периода последействия за счет применения в системах со сбалансированной автоматикой одного приводного поршнях и газовой камеры, закрытой с одной стороны, импульс от давления пороховых газов на которую противоположен действию силы отдачи и численно равен количеству движения подвижных частей. Наличие блока балансировки (при одинаковых массах затворной рамы с затвором и балансира с рейкой) полностью исключает передачу импульса отдачи на стрелка на остальных участках работы автоматики.
Другая схема с комбинированным двигателем автоматики с откатом стреляющего агрегата и с последующим отводом пороховых газов из канала ствола при наличии блока балансировки представлена на рис. 4. Рациональная для повышения устойчивости оружия импульсная диаграмма (плавное возрастание импульса отдачи за время работы двигателя и отсутствие передачи импульса отдачи в оставшемся цикле отката и наката затворной рамы с балансиром) достигается использованием отдачи ствола и блока балансировки с одним приводным поршнем.
При отдаче ствола до начала истечения пороховых газов из ствола в газовую камеру импульс отдачи определяется реакцией сжимающейся пружины ствола, чем обеспечивается плавность передачи импульса отдачи.
После отвода пороховых газов из ствола в газовую камеру сила давления пороховых газов на переднюю стенку газовой камеры приводит к потере стволом скорости отката, как и реакция от работы дульного тормоза. В результате ствол приходит в крайнее заднее положение с минимальной скоростью и передает оставшееся количество движения на ствольную коробку. Применение блока балансировки исключает передачу импульса отдачи на стрелка в оставшемся цикле отката, а затем наката затворной рамы с балансиром.
На рис. 5 выделены четыре этапа движения стреляющего агрегата, определяющие характер передачи импульса отдачи.
Приведенные импульсные диаграммы и соответствующие им конструктивные схемы определяют теоретическую возможность повышения устойчивости ручного автоматического оружия в системах с неподвижной ствольной коробкой.
Рис. 2. Схема оружия со сбалансированной автоматикой с одним приводным поршнем: 1 – затворная рама со штоком, поршнем и затвором; 2 – балансир с рейкой; 3 – возвратная пружина затворной рамы и затвора; 4 – возвратная пружина балансира;
5 – звездочки;
271
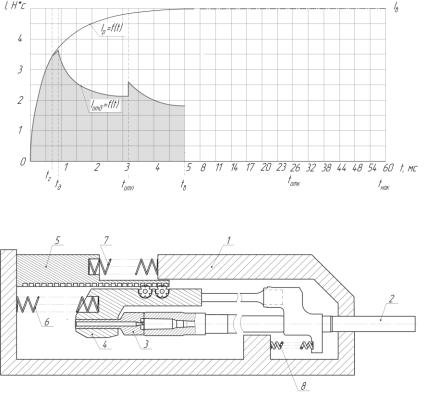
Рис. 3. Импульсная диаграмма оружия со сбалансированной автоматикой с применением одного приводного поршня
Рис. 4. Схема с комбинированным двигателем автоматики с откатом ствола и с отводом части пороховых газов с применением эффекта сбалансированной авто-
матики: 1 – короб оружия;2 – стреляющий агрегат (ствол с газовой камерой и с боевыми упорами, служащими для взаимодействия с затвором при запирании канала ствола);
3 – затвор; 4 – затворная рама со штоком, поршнем и звездочками; 5 – балансир с рейкой; 6 – возвратная пружина затворной рамы с затвором; 7 – возвратная пружина балансира; 8 –пружина стреляющего агрегата
272
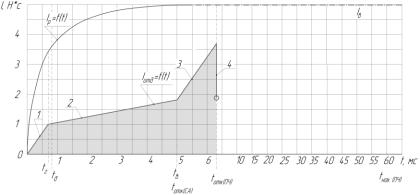
Рис. 5. Импульсная диаграмма для схемы с комбинированным двигателем автоматики с откатом ствола и с отводом части пороховых газов с применением эффекта сбалансированной автоматики
Список литературы
1. Шипунов, А.Г. Проектирование спецмашин. Часть 1. Проектирование стрелко- во-пушечного вооружения: Учебник – Тула: изд-во ТулГУ, 2008. – 306.
А. А. Шаклеин, магистрант А. П. Тюрин, доктор технических наук, профессор
Ижевский государственный технический университет имени М. Т. Калашникова
Моделирование звукопоглощения в акустическом интерферометре
Акустика изучает генерацию, распространение и отражение звуковых волн в жидких средах. Положения этой науки используются для расчета и прогнозирования акустических явлений в различных областях.
Множество акустических задач решается с использованием гармонического анализа. Определив частотный диапазон, можно получить распространение давления в этом диапазоне.
Достаточно подробный акустический анализ доступен в таких про-
граммных продуктах как ANSYS Multiphysics и ANSYS Mechanical. Инте-
рес представляет получение данных о распространении давления в среде на различных частотах, градиент давлений, скорость частиц, уровень звукового давления и другие параметры.
Метод передаточной функции предназначен для определения коэффициента звукопоглощения образца в импедансной трубе (рис. 1). Метод передаточной функции также может быть использован и для определения акустического импеданса или адмитанса поверхности звукопоглощающих
273
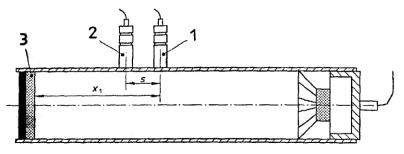
материалов. А так как импедансные соотношения звукопоглощающего материала связаны с его физическими свойствами, такими как аэродинамическое сопротивление, пористость, эластичность и плотность, то измерения, выполняемые этим методом, приобретают особую значимость для базовых исследований материала. Дополнительно он позволяет выявлять степень согласования результатов звукопоглощения физического и численного экспериментов.
Конструктивные особенности импедансной трубы приведены на рис. 1, на котором представлена непосредственно труба с источником звука, вмонтированным на одном из ее концов, и исследуемым образцом, закрепленным в трубе с другого ее конца.
Два микрофона с заранее определенными и зафиксированными положениями, фиксируют величину акустического давления подаваемой плоской волны, а также отраженный сигнал. Затем на базе измеренных сигналов строится комплексная передаточная функция.
Рис. 1. Микрофонные позиции и расстояния в акустическом интерферометре
Метод измерения основан на том факте, что показатель отражения звука при нормальном падении r может быть определен из измеренной передаточной функции H12 между двумя микрофонными позициями впереди исследуемого материала.
Звуковое давление падающей волны pl и отраженной волны pR являются, соответственно:
|
|
|
|
|
|
|
|
|
|
|
|
|
|
|||
|
|
|
|
|
|
|
|
pl |
ple jk0 x |
(1) |
||||||
|
|
|
|
|
|
|
|
|
|
|
|
|
|
e jk0 x |
|
|
|
|
|
|
|
|
|
|
p |
R |
p |
R |
(2) |
||||
|
|
|
|
|
|
|
|
|
|
|
|
|
|
|||
|
|
|
|
|
|
|||||||||||
где pl |
, pR являются магнитудами pl и pR у исходной плоскости (x = 0); |
|||||||||||||||
~ |
Действительная составляющая |
|
|
комплексного |
волнового числа |
|||||||||||
k |
|
|
jk '' |
находится как: |
|
|
|
|
|
|
|
|
||||
k |
0 |
|
|
|
|
|
|
|
|
|||||||
|
|
|
0 |
|
|
|
|
|
|
|
|
|
k0 2 / 0 ,
где λ0 – длина волны, м.
274
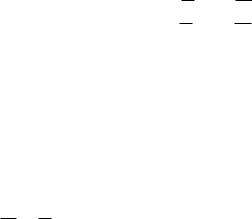
Вычитаемое j k |
'' |
является мнимой компонентой комплексного волно- |
|
0 |
|||
|
|
вого числа или константой ослабления импедансной трубы.
Звуковые давления p1 и p2 в двух микрофонных положениях являются:
p |
p e |
jk |
x |
p |
|
e |
jk |
x |
0 |
1 |
|
0 |
1 |
||||
|
|
|
|
|
||||
1 |
l |
|
|
|
R |
|
|
|
(3)
p |
|
p e |
jk |
x |
p |
|
e |
jk |
x |
|
0 |
2 |
|
0 |
2 |
||||
|
|
|
|
|
|
||||
|
2 |
l |
|
|
|
R |
|
|
|
(4)
Передаточная функция для падающей звуковой волны Hl равняется:
Hl |
p2l |
e |
jk0 x1 x2 |
|
e |
jk0s |
(5) |
p1l |
|
|
|
||||
|
|
|
|
|
|
|
где s = x1 – x2 – расстояние между двумя микрофонами.
Аналогично, передаточная функция для отраженной звуковой волны HR равняется:
H R |
p2R |
e |
jk0 x1 x2 |
e |
jk0s |
(6) |
p1R
Передаточная функция H12 для общего звукового поля может теперь быть получена с использованием уравнений (3) и (4) и при условии, что
pR r pl , как:
H12 |
p |
2 |
|
e jk0 x2 re jk0 x2 |
(7) |
|
p |
e jk0 x1 re jk0 x1 |
|||||
|
|
|
||||
|
|
1 |
|
|
|
Преобразование уравнения (7) для получения r, использованием уравнений (5) и (6), получим:
r |
H12 Hl |
e |
2 jk0 x1 |
(8) |
H R Hl2 |
|
|||
|
|
Фактор отражения звука на исходной плоскости (x = 0) может быть теперь определен из измеренных передаточных функций, расстояния x1 и волнового числа k0.
С использованием уравнения (8), можно затем получить коэффициент поглощения:
1 |
|
r |
|
2 , |
(9) |
|
|
Вданной работе был произведен акустический расчет импедансной трубы в программном продукте ANSYS. Для измерения на частотах от 20 до 1000 Гц с шагом 10 использовали квадратную трубу с гладкими стенками, габаритами 100×100 мм и длиной 1250 мм
Врезультате расчета, получены значения действительной и мнимой части звукового давления для каждой частоты. Для оценки коэффициента звукопоглощения материала использован метод передаточных функций. График зависимости коэффициента звукопоглощения от частоты представлен на рис. 2.
275

Рис. 2. Зависимость коэффициента звукопоглощения от частоты
Выполненная работа по получению данных по коэффициенту звукопоглощения в дальнейшем могут помочь в оценке и разработке геометрии звукопоглощающих материалов. Использование различных значений звуковых давлений и подбор звукопоглощающего материала позволит выполнять оптимизационные расчеты акустических полей в помещении при его гармоническом возбуждении.
Ф. А. Шамурадов, преподаватель Тюменский государственный нефтегазовый университет
Институт промышленных технологий и инжиниринга
Исследование устройства автоматического розжига котельной установки с низкотемпературным кипящим слоем
Повышение цен на энергоносители, дефицит собственных топливных ресурсов, снижение качества угля, рост требований к уменьшению загрязнения окружающей среды требуют внедрения в производство более совершенного метода сжигания угля.
Именно наличие топливно-энергетических ресурсов определяют темпы и масштабы развития отдельных районов промышленного и сельскохозяйственного производства. Главными задачами являются обеспечения более комплексной переработки сырья, создание ресурсосберегающей техники и технологий, резкого сокращения потерь и отходов. В последние годы во многих странах структурная перестройка топливного баланса с целью уменьшения зависимости от нефти и газа возродила интерес к угольной тематике.
276
В настоящее время данным требованиям удовлетворяют котельные установки с топкой низкотемпературного кипящего слоя (НТКС). Топливо в топках НТКС сжигается в псевдоожиженном слое, что способствует существенному улучшению доступа кислорода к топливу в процессе горения, повышенной теплоотдачи к поверхностям нагрева, а также более полному сгоранию топлива [1].
Благодаря внедрению этой технологии становится возможным использовать отходы углеобогащения и угледобычи, нетрадиционные и низкосортные виды топлива (щепа и другие древесные отходы, торф, шламы и др.), при этом допуская сжигание различных видов топлива в одном топочном устройстве. Применение технологии сжигания топлива в кипящем слое обеспечивает выполнение жестких экологических норм по выбросам SО2 и NO2 без сооружения дополнительных установок по серо- и азотоочистке. Однако практическая реализация этого способа в промышленных установках связана с преодолением ряда трудностей, свойственных специфике данного технологического процесса.
Сегодня розжиг топки НТКС выполняется оператором вручную. Это представляет опасность для обслуживающего персонала и существенно снижает качество управления технологическим процессом. Поэтому, для достижения оптимального управления розжиг необходимо осуществлять в автоматическом режиме.
Применение плазменно-топливных систем позволяет отказаться от использования дорогостоящего жидкого топлива, исключается его потеря при неустойчивом пламени и повышается ресурс оборудования.
Для разогрева кипящего слоя и воспламенения угля используется мазут. Совместное сжигание угля и обладающего более высокой реакционной способностью мазута ухудшает эколого-экономичeские показатели котлов: на 10 – 15 % повышается механический недожог топлива и на 2 – 5 % снижается КПД, при этом возрастает скорость высокотемпературной коррозии экранных поверхностей, снижается надежность эксплуатации котельного оборудования с увеличением на 30 – 40 % выхода оксидов азота и серы. Снижение качества энергетических углей приводит к увеличению затрат времени на его воспламенение и дальнейшее сжигание.
Нарушение алгоритма процесса розжига зачастую приводит к потере жидкого топлива из-за неустойчивого пламени на горелке. Поэтому для энергетических и теплофикационных установок требуются системы, обеспечивающие надежный безмазутный розжиг и улучшение экологических характеристик. Для достижения этих целей могут быть использованы пылеугольные горелки, оборудованные электродуговыми плазмотронами. Данная технология заключается в нагреве аэросмеси (угольная пыль + воздух) электродуговой плазмой. Плазмообразующий газ (воздух) продувается через электроды, формируя плазменный факел, среднемассовая температура которого варьируется в интервале 5000–6000 К. Мощность плазмотрона изменяется от 100 до 350 кВт. Технология ПТС заключается
277
в нагреве аэросмеси с помощью плазменного факела до температуры выделения летучих и частичной газификации углерода коксового остатка [5].
Независимо от качества исходного угля из аэросмеси получается высокореакционное двухкомпонентное топливо. Смешиваясь с вторичным воздухом, оно интенсивно воспламеняется и стабильно горит без использования дополнительного топлива (мазут или природный газ), традиционно сжигаемого для растопки котлов из холодного состояния и стабилизации горения низкосортного энергетического угля.
Термохимическая подготовка аэросмеси к сжиганию осуществляется в объеме ПТС при концентрации пыли в аэросмеси 0,4 килограмм угля на килограмм воздуха, что соответствует 44 % от теоретически необходимого количества воздуха для полного сгорания угля [5].
Пылеугольный бункер для обеспечения взрывозащиты выполнен закрытым. При помощи шнекового питателя, который приводится во вращение приводным электродвигателем, угольная пыль попадает в камеру смешения с первичным воздухом и далее через пылепровод круглого сечения со скоростью потока более 25 м/с (во избежание отложений пыли) отправляется на горелку.
При отключенном шнековом питателе осуществляется блокировка шибером подачи угольной смеси. В моменты времени, определенные алгоритмом работы ПТС, управление шибером реализуется с помощью однооборотного электрического механизма (МЭО).
Применение плазменно-топливной системы обеспечивает надежный безмазутный розжиг и улучшение экологических характеристик котлоагрегата в целом. При этом исключаются аварии и потеря растопочного топлива, возникающая при использовании мазута для розжига кипящего слоя.
Применение автоматического розжига котла позволяет создать безопасные условия для оператора, сократить непроизводительные затраты времени и улучшить технико-экономические и экологические показатели процесса розжига котлоагрегата с топкой НТКС.
Список литературы
1.Вискин, Ж.В. Сжигание угля в кипящем слое и утилизация его отходов [Текст] / Ж.В. Вискин, В. И. Шелудченко. ‒ Донецк: Типография “Новый мир”,
1997. ‒ 284.
2.Махорин, К.Е. Сжигание топлива в псевдоожиженном слое [Текст] / К.Е. Махорин, П. А. Хинкис. - Киев: Наук. Думка, 1989 ‒ 204.
3.Чушенко, А.В. Описание патента на изобретение устройства автоматического розжига котла. [Электронный ресурс] / А. В. Чушенко, А. И. Маранценбаум,
В. Ф Лебедев/ ‒ Режим доступа: http://base.ukrpatent.org/searchINV/.
4.Аскарова, А.C. Плазмохимическая активация горения и газификация угля. [Электронный ресурс] / А. C. Аскарова, Е. И. Карпенко, В. Е. Мессерле, А. Б.
Устименко / ‒ Режим доступа к статье: http://www.isuct.ru/istapc2008/PROC/P-8.PDF.
278
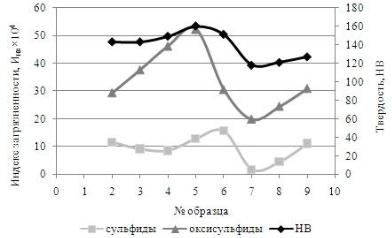
5. Гавриленко, Д.А. Устройство автоматического розжига котлоагрегата низкотемпературного кипящего слоя с использованием плазменно-топливных систем. Автоматизация технологических объектов и процессов. Поиск молодых. Сборник научных трудов IX научно-технической конференции аспирантов и студентов, 20– 22 мая 2009 г. / ДонНТУ ‒ Донецк, 2009. - 14 – 19.
О. А. Шевцова, аспирант
Н. А. Зюбан, доктор технических наук, профессор Волгоградский государственный технический университет
Роль окисленности металла в формировании оксидных, сульфидных и оксисульфидных включений и
свойств готовых изделий
Присутствие неметаллических включений оказывает существенное влияние на прочностные и пластические характеристики сталей и сплавов. Определение состава таких структурных составляющих важно для выяснения природы и механизма их образования.
Известно [1], что особенности образования оксидных, сульфидных и оксисульфидных включений находятся между собой в тесной связи, и в зависимости от их количественного соотношения уровень пластических характеристик готового изделия может существенно изменяться.
С целью установления связи между окисленностью металла и количеством образующихся оксидов, сульфидов и оксисульфидов провели металлографическое исследование опытных образцов из стали 20, раскисленных по различным вариантам: Al (0,059‒0,222 % от массы образца), SiCa (0,059‒0,293 % от массы образца).
Рис. 1. Загрязненность образцов неметаллическими включениями и их твердость
279
На рис. 1 представлены полученные зависимости загрязненности образцов неметаллическими включениями и твердости.
С увеличением количества вводимого Al (2‒4) наблюдается увеличение количества оксидов и оксисульфидов, а количество сульфидов уменьшается. При введении SiCa (5‒6) наблюдается уменьшение количества оксидов, т. к. SiCa эффективен как модификатор только при совместном введении с Al, количество сульфидов увеличивается. При совместном раскислении и модифицировании Al и SiCa (7) наблюдается минимальное количество сульфидов, далее с увеличением количества вводимого SiCa (8‒9) количество оксидов увеличивается, оксисульфиды преимущественно глобулярной формы располагаются внутри зерна.
Металлографическое исследование образцов показало, что при традиционном конечном раскислении литой стали алюминием 80‒85 % неметаллических включений (практически все сульфиды) находятся на границах литых кристаллитов. Значительное очищение границ литых зерен от неметаллической фазы может быть достигнуто дополнительным (к раскислению алюминием) раскислением-модифицированием щелочноземельными или редкоземельными элементами. Редкоземельные металлы, имея высокое сродство к кислороду, сере и другим примесям, активно взаимодействуют с ними, образуя при этом совершенно новый тип включений ‒ твердые растворы переменного нестехиометрического состава. Вновь образованные включения имеют преимущественно глобулярную форму, коагулируют, что способствует образованию более крупных включений [2].
Была определена твердость образцов. Установлено, что наибольшая твердость наблюдается в образцах с максимальным количеством оксисульфидов, что, вероятно, вызвано связыванием сульфидов в более благоприятную оксисульфидную фазу, этим обусловлено снижение негативного влияния сульфидных включений по границам зерен.
Полученные результаты свидетельствуют о наличии определенной связи между количеством образующихся оксидных и оксисульфидных включений, зависящим от степени окисленности металла.
Термодинамические условия образования включений такого типа предполагают образование в металле сначала оксидов, на которых, как на подложках происходит формирование оксисульфидов. По мере расходования кислорода и снижения его концентрации до равновесных значений, происходит выделение «чистых» сульфидов, что может привести к снижению пластических свойств получаемого металла. Поэтому, можно считать, что основным условием выделения сульфидной фазы в стали является отсутствие в металле свободных оксидов.
Таким образом, формирование свойств литого металла во многом зависит от оптимального соотношения между содержанием в металле оксидов, сульфидов и оксисульфидов. Поэтому управление соотношением оксидных, сульфидных и оксисульфидных включений в стали необходимо
280
осуществлять за счет выбора оптимального состава и количества раскислителей, либо посредством увеличения доли оксидов-«подложек» за счет модифицирования стали щелочно-земельными или редкоземельными элементами.
Список литературы
1. Зюбан, Н.А. Влияние вакуумирования на особенности формирования сульфидных включений и свойства изделий из низколегированных конструкционных сталей / Н.А. Зюбан, О.Б. Крючков. // Изв. вуз. Черная металлургия.- 2008.- №5.- 15 – 18.
2. Лунев, В.В. О природе и диагностике неметаллических включений в стали / В.В. Лунев, В.П. Пирожкова // Электрометаллургия.- 2011.- №7.- 26-30.
М. А. Шерстобитов, руководитель направления комплексных проектов, аспирант
В. В. Михрютин, кандидат технических наук, доцент Рыбинский государственный авиационный технический университет
имени П. А. Соловьева ЗАО «Авиационный консалтинг – Техно», г. Рыбинск
Анализ формообразующих систем станков для Обработки тонкостенных листовых заготовок сложной формы
Обводообразующие детали, изготавливаемые из листового материала, гнутых профилей и профилей проката различной формы составляют до 60% деталей, формирующих наружный контур обшивки планера современного самолета. Их производят различными методами в заготовитель- но-штамповочном производстве.
Номенклатура тонкостенных листовых обшивок, применяемых в конструкции планера самолета, достаточно широка. Размеры деталей обшивок колеблются в значительных пределах.
Трудоемкость изготовления обшивок в общем объеме заготовительноштамповочных работ составляет около 15 %. Большую ее часть определяет механическая обработка по контуру обшивки, сверление высокоточных отверстий, обработка карманов, обнижение поверхности.
Для обнижения поверхности листовых обшивок в настоящее время в основном применяется способ обработки методом электроэрозии. Такая обработка подразумевает маскирование зон, не подвергаемых обработке, и погружение в ванну с электролитическим раствором. Данный процесс обеспечивает локальное удаление материала с деталей неразвертываемых форм, но, тем не менее, имеет два серьезных недостатка, связанных с наличием отходов, утилизация которых представляет затруднения, и невозможностью обработки областей с различной глубиной обработки на одной и той же операции.
281
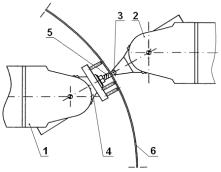
Для устранения указанных недостатков был разработан ряд способов механической обработки тонкостенных листовых обшивок методом фрезерования [1].
Наиболее эффективное на настоящий момент решение для обработки панелей основано на использовании опорного элемента, поддерживающего необрабатываемую сторону панели в процессе фрезерования [2, 3]. Особенность данного решения заключается в том, что опорный элемент всегда перемещается соосно с инструментом, находящемся с противоположной стороны панели, обеспечивая достаточную жесткость и высокую точность. Схема обработки данным методом, получившая название «зеркальное фрезерование» показана на рис. 1. При обработке используются вилочные головки 1 и 2. На вилочной головке 2 установлен жесткий упор 3. На вилочной головке 1 установлен шпиндельный узел 4 с концевой фрезой 5, обрабатывающей заготовку 6.
Рис. 1. Схема обработки при зеркальном фрезеровании [2, 3]
Данный метод обработки позволяет обрабатывать наиболее широкую номенклатуру листовых заготовок, в том числе вести двустороннюю обработку и обрабатывать заготовки с большим радиусом кривизны. Например, детали обшивки в зоне носовой части фюзеляжа, пилотской кабины, окантовки проемов дверей, боковые панели фюзеляжа с проемами под иллюминаторы и другие элементы.
Для моделирования процесса механической обработки тонкостенных листовых заготовок требуется построение уравнения формообразования.
Построение данной модели начнем с рассмотрения формообразующей системы обрабатывающего центра, осуществляющего схему «зеркального фрезерования».
Обрабатывающие фрезерные центры данного типа (рис. 2) являются высокоскоростными станками. Рассматриваемый обрабатывающий центр состоит из горизонтальной станины 1, на которой размещается оснастка для закрепления обрабатываемых листовых обшивок. Станины 2 и 3
282

оснащены двумя подвижными вертикальными колоннами 4 и 5, расположенными друг напротив друг и перемещающимися по направляющим в направлении оси Х. Для повышения жесткости колонны 4 и 5 оборудованы дополнительными направляющими 6 и 7.
Рис. 2. Схема многокоординатного обрабатывающего центра
Колонны 4 и 5 имеют вертикальные Y0 , YA и горизонтальные Z0 и ZA оси с направляющими ползунов 8 и 9. Приводы осей X, Y, и Z реализованы с применением линейных электродвигателей, что обуславливает их высокое быстродействие и относительно малую инерционность. На каждом ползуне установлена вилочная фрезерная головка с приводом по круговым осям A, B и дополнительной осью, управляющей выдвижением пиноли W.
Таким образом, станок состоит из двух шестиосевых модулей, а система управления обеспечивает синхронное управление двенадцатью осями.
Ползун 8 колонны 4 и оснащен шпиндельной головкой вилочного типа с высокоскоростным электрошпинделем и предназначен для фрезерной обработки детали. Обработка карманов, как правило, выполняется на вогнутой стороне панели. Иногда имеется необходимость двусторонней обработки панели, которая обеспечивается разворотом зажимной рамы с деталью, выполняемым вне рабочей зоны станка.
Ползун 9 колонны 5 применяется для поддержки и исключения деформации формы панели, а также устранения вибраций во время обработки. При этом сила, действующая на панель во время обработки, компенсируется опорой с противоположной стороны. У опоры нет вращательного движения, однако вилочная головка поддерживает заготовку панели в положении теоретического контура во время обработки. Характеристики ее движений точно такие же, как и для обрабатывающего инструмента. Движения симметричны и соосны движениям обрабатывающего инстру-
283
мента. Для обеспечения заданного допуска на толщину панели, опора оснащается системой поддержания зазора, работающей в реальном времени.
Использование 12-ти программируемых осей для перемещения шпиндельной головки и сферической опоры обеспечивает взаимную перпендикулярность оси шпиндель-опора по отношению к поверхности панели при обработке любой точки поверхности. Математическое обеспечение системы управления позволяет выполнять позиционирование в «теоретическое положение» и фиксацию панелей во время обработки, идентификацию и измерение позиции и фактической формы панели, при необходимости производить коррекцию программы обработки, составленной на основе заданной формы детали, осуществлять обработку карманов, фрезерование и сверление.
Зажим заготовки производится установленными по периметру и приводимыми от СЧПУ телескопическими захватами, что позволяет избежать деформации панели во время зажима и обработки. Для обеспечения зажима в палете заготовки должны иметь технологический припуск.
Анализ формообразующей системы станка позволяет сделать вывод, что формообразующая система станка образована двумя последовательными цепями блоков. Одна цепь блоков образует цепь инструмента, а вторая – упора, поддерживающего нежесткую заготовку при обработке. Малая жесткость заготовки позволяет задать общую цепь блоков в виде последовательного соединения двух цепей заготовки и инструмента. Для учета наклона и неравномерной толщины заготовки введем фиктивную координату, обозначаемую xyz . Это позволяет записать формулу структурной компоновки данного станка в следующем виде
xyz WABA AAZAYAXA0X0Y0Z0A0B0W0Sh, |
(1) |
где XA, YA, ZA, WA , AA, BA – управляемые координаты цепи упора; 0 – обозначение неподвижного блока; X0, Y0, Z0, A0, B0, W0 – управляемые координаты цепи инструмента; Sh – обозначение горизонтального шпинделя.
Для получения уравнения формообразования заменим в формуле структурной компоновки обозначения символов координатных движений на обозначения матриц, моделирующих перемещения по соответствую-
щим координатам
p t, xyz 0Tz WA 1Ry BA 2 Rx AA 3Tz Z A 4Ty YA 5Tx X A
6Tx X 0 7Ty Y0 8Tz Z0 9 Rx A0 10Ry B0 11Tz W0 12Rz C 13 fр t , (2)
где xyz( ) – функция, задающая толщину заготовки по нормали к обрабатываемой поверхности; – системное время; 0,1,…, 13 – матрицы формы, задающие взаимное положение двух сопрягаемых рабочих органов станка; Tx(X), Tz(Z), Ty(Y) – матрицы плоскопараллельного перемещения в расширенном пространстве относительно осей координат x, y, z; C – угол поворота шпинделя относительно осей координат Z; Rx(A), Ry(B),
284
Rz(C) – матрицы поворота в расширенном пространстве вокруг осей координат x, y, z; fр(t) – уравнение режущей кромки; t – безразмерный параметр, задающий кривую, совпадающую с режущей кромкой.
Полученное уравнение позволяет определить положение режущей кромки инструмента в любой момент времени при моделировании процесса обработки. Это дает основу для определения ряда важных показателей процесса резания, шероховатости обработанной поверхности, влияния погрешностей размеров рабочих органов оборудования на выходную точность обработанной поверхности, а также произвести расчет необходимого положения инструмента и упора во время обработки. Решение данной задачи необходимо для построения системы моделирования процесса механической обработки тонкостенных листовых обшивок.
Список литературы
1.Михрютин, В.В. Методы механической обработки листовых обшивок планера самолетов// Вестник РГАТА имени П.А. Соловьева, – Рыбинск: РГАТА 2012 №2 (23) - 279 – 284.
2.Process and device for the machining of panels : пат. 7682112 US, 2007274797,
заявл. 29.11.2007, опубл. 23.03.2007.
3.Способ и устройство для обработки панелей : пат. 2358850, Рос. Федерация. 2006113372/02, заявл. 22.10.2004, опубл. 20.06.2009.
4.Михрютин, В.В. Методика решения прямой задачи о положениях инструмента и рабочих органов технологического оборудования в пространстве// Справочник. Инженерный журнал. № 4, 2009. - 33 – 40.
В. Н. Широбоков, аспирант
О. И. Шаврин, доктор технических наук, профессор Ижевский государственный технический университет имени М. Т. Калашникова
Перспективы повышения хладостойкости упругих элементов деталей машин
Способность металла сопротивляться деформации и разрушению при понижении температуры называют хладостойкостью. Напрямую с этим понятием связано понятие хладноломкости ‒ потеря материалом пластичности с понижением температуры. Чем ниже порог хладноломкости, тем выше способность металла сопротивляться деформации при низких температурах.
Проблема борьбы с хладноломкостью ‒ большая научная и техникоэкономическая проблема, в решении которой заинтересованы многочисленные предприятия Севера. Это связано с резким снижением эффектив-
285
ности работы оборудования и транспорта на Севере.
При эксплуатации в условиях низких температур, особенно в интервале температур от ‒50° до ‒60°, материалы, применяемые в машиностроении, в той или иной мере меняют свои физико-механические свойства. Многие металлы и сплавы при низких температурах склонны к хрупкому разрушению вследствие потери материалами пластичности [1].
Хладноломкость связана с затруднением движения дислокаций; начиная с некоторой температуры хрупкое разрушение наступает раньше, чем состояние пластической текучести. Температура перехода от вязкого разрушения к хрупкому зависит от режима термической обработки и как следствие от величины зерна и вида кристаллической решетки, от количество вредных примесей в металле, от легирующих элементов, от скорости нагружения, от величины концентрации напряжений, от состояния поверхности, от остаточных напряжений [2].
Механические свойства и хладноломкость стали определяются следующими механизмами упрочнения [6]:
1)измельчением зерна;
2)легирование элементами, образующими твердые растворы внедрения или замещения и вызывающими искажение решетки растворителя;
3)упрочнением выделениями частиц второй фазы различной степени дисперсности;
4)термомеханическим упрочнением (ТМО);
5)поверхностным пластическим деформированием (ППД); Эффективным методом измельчения зерна является термическая обра-
ботка и термоциклирование. Термоциклическая обработка (ТЦО) сопровождается многократными фазовыми превращениями при циклических нагревах и охлаждениях с оптимальными скоростями. Нагревы и охлаждения проводят в области неполного α → γ-превращения в межкритическом интервале температур. Кроме измельчения зерна ТЦО обеспечивает термонаклеп и концентрацию вредных примесей в изолированных участках рельефного феррита, что также способствует повышению свойств стали.
При замене нормализации на термоциклическую обработку происходит изменение структуры от феррито-перлитной к мелкодисперсной упорядоченной смеси перлитообразного сорбита и феррита. При этом также происходит существенное измельчение действительного аустенитного зерна (с 5–6 до 10–11 балла). В нормализованной структуре достаточно хорошо видны контуры грануляционной сетки, которые почти полностью исчезают после термоциклирования. Получаются более высокие характеристики механических свойств, а вязкость разрушения возрастает в 1,5 раза [4].
Не менее эффективным способом повышения хладостойкости стали является легирование. Так, введение в углеродистую сталь до 2 % марганца и до 0,8 % кремния упрочняет ферритную матрицу благодаря образо-
286
ванию твердого раствора замещения. Легирование марганцем измельчает зерно и увеличивает вязкость феррита, что повышает величину работы распространения трещины при низких температурах. Легирование стали малыми добавками титана, ниобия и ванадия позволяет получать мелкодисперсные выделения второй фазы типа VC, TiC, Nb(C,N), V(C,N), эффективно упрочняющие матрицу. Эти же элементы способствуют измельчению зерна и снижают склонность стали к его росту. На границах зерен образуются дисперсные частицы карбидов и карбонитридов ниобия, титана и ванадия, тормозящие рост зерен при нагревании.
Из всех легирующих элементов никель в наибольшей степени понижает хладноломкость стали. Никель и железо полностью растворимы друг в друге, имеют близкое строение кристаллических решеток. Никель не является карбидообразующим элементом, он находится в твердом растворе в феррите или аустените. Никель упрочняет феррит и одновременно увеличивает его вязкость. Никель увеличивает прокаливаемость стали, измельчает зерно, а также снижает концентрацию примесей на дислокациях и уменьшает блокирование дислокаций примесными атомами внедрения. Введение 1 % Ni снижает порог хладноломкости примерно на 20 К.
Наиболее перспективным способом измельчения зерна в сталях является микролегирование такими карбидообразующими элементами, как V,
Ti, Nb, Zr [4].
Упрочнение дисперсными частицами второй фазы может быть осуществлено в α-железе и аустените при выделении из пересыщенных твердых растворов самых разнообразных растворенных в них элементов [5].
Роль дисперсных частиц второй фазы заключается в том, что они препятствуют движению дислокаций. Однако, если бы даже напряжение, необходимое для того, чтобы заставить дислокации пройти через дисперсные включения второй фазы, равнялось напряжению, необходимому для движения дислокаций в основе сплава (матрице), все равно имело бы место некоторое упрочнение сплава, так как после прохождения дислокации система характеризуется наличием большого количества связей типа матрица ‒ матрица или включение ‒ включение. Для создания такого состояния необходимо затратить дополнительную энергию. Эффект упрочнения пропорционален объему, занимаемому дисперсными включениями второй фазы, и может быть увеличен усилением сил связей в выделениях второй фазы, что достигается изменением химического состава в направлении, обеспечивающем получение более стабильной второй фазы. Объем содержащихся в сплаве включений второй фазы лимитируется растворимостью элементов при температуре закалки. Если же прочность дисперсных включений второй фазы превысит некоторое критическое значение, то дислокации не будут больше проходить через них, а будут стремиться обойти их посредством поперечного скольжения.
Уровень прочности, достигаемый при упрочнении сплава дисперсными частицами, очень трудно оценить теоретически. Однако для большого
287
числа разнообразных сплавов предел текучести в этом случае увеличивается в 10 раз по сравнению с пределом текучести основы сплава.
Известно, что одним из наиболее перспективных направлений повышения прочности является создание в кристаллической решетке обрабатываемого объекта особых структурных несовершенств, способствующих развитию эффекта упрочнения. Такие структурные несовершенства могут быть получены в результате пластической деформации или термической обработки.
Термомеханическая обработка (ТМО) ‒ это совокупность операций деформации, нагрева и охлаждения (в различной последовательности), в результате которых формирование окончательной структуры металлического сплава, а следовательно, и его свойств, происходит в условиях повышенной плотности несовершенств строения, созданных пластической деформацией.
Основными факторами, способствующими упрочнению металлов и сплавов при таком комбинированном воздействии, являются увеличение плотности дислокаций и более равномерное их распределение по объему металла по сравнению с отожженным состоянием; создание дислокационных барьеров в виде границ зерен, двойниковых границ, дисперсных вторичных фаз, леса дислокаций и т.д.; уменьшение размера зерен и образование субструктуры заблокированными дислокационными границами; увеличение степени дисперсности вторичных фаз; фазовые превращения в материале с предварительно созданной субструктурой. Структура, образующаяся к концу обработки формируется в условиях протекания процессов деформационного упрочнения аустенита, динамической полигонизации (или динамической рекристаллизации) и статического возврата (или статической рекристаллизации), а кинетика протекания этих процессов зависит от температурных и деформационно-скоростных параметров ТМО. Например, для стали 50ХГА если пауза после деформации не превышает 5 с (проходит лишь частичная рекристализация), кристаллы мартенсита «наследуют» субструктуру деформированного аустенита. При паузе в 30 и 60 с «наследования» не отмечается [5]. В зависимости от различных режимов ТМО изменяются и соотношения структурных составляющих в стали. Что касается комплекса механических свойств, определяющего конструктивную прочность деталей, то он безусловно выше в термомеханически упрочненных заготовках.
Пластическое деформирование приводит к повышению склонности сталей к хрупкому разрушению. В связи с этим распространено мнение, что поверхностный наклеп не следует применять для деталей, работающих на усталость при низких температурах. Опытные данные показывают, что указанное мнение во многих случаях является необоснованным. Опасность повышения склонности стальных деталей к хрупким разрушениям в связи с применением поверхностного наклепа должна учитываться в тех случаях, когда при эксплуатации деталей возможны нагрузки, вызы-
288
вающие напряжения выше предела текучести материала. В других случаях такой опасности нет.
Боковины сварных тележек испытывали при охлаждении до -40 градусов ударными нагрузками, вызывавшими напряжения до 0,8 ζт. Результаты испытаний убедительно свидетельствуют о значительном преимуществе поверхностно наклепанных образцов. Долговечность наклепанных образцов повысилась в 1,5‒2 раза [3].
Вопрос об эффективности методов снижения хладноломкости является актуальным. Например, никель, который является одним из самых эффективных легирующих элементов, с точки зрения снижения порога хладноломкости, является дорогим материалом и средняя цена за лом на него составляет на сегодняшний день 540 тыс. руб/тонну, поэтому данный метод является достаточно дорогостоящим. Конечно, все перечисленные механизмы упрочнения в равной степени достойны рассмотрения в качестве эффективных методов повышения хладостойкости, но более перспективным методом стоит выделить термомеханическую обработку. Многолетнее изучение ТМО и грамотное назначение режимов обработки позволили получить такое строение стали, благодаря которой удалось повысить долговечность цилиндрических винтовых пружин в десятки раз. Кроме того, профиль проката для рессор и пружин (полоса, круг) является наиболее приемлемым для ТМО в промышленных условиях без существенного изменения технологии и действующего оборудования. Внедрение ТМО позволяет снизить расход стали при производстве деталей машин и механизмов за счет уменьшения их сечения, сокращения расхода запасных частей, заменить в ряде случаев легированные стали на углеродистые. В настоящее время на базе ОАО «Ижевский машзавод» была учреждена компания «НПЦ «Пружина», занимающаяся производством высокопрочных пружин, изготовленные по технологии контролируемого формирования наносубструктуры.
Список литературы
1.Кубасов, В.А. Повышение качества машин в северном исполнении. В кн.: Проблемы хладостойкости конструкционных сталей. Иркутск: Вост.-Сиб. кн. изд-
во. 1971.
2.Петч, Н.Дж. Переход из вязкого состояния в хрупкое в α-железе. Атомный механизм разрушения. – М: Металлургиздат, 1963.
3.Кудрявцев, И.В. Повышение долговечности деталей машин методом поверхностного наклепа. В кн.: Проблемы хладостойкости конструкционных сталей. Иркутск: Вост.-Сиб. кн. изд-во. 1971.
4.Солнцев, Ю.П. Хладостойкие стали и сплавы: Учебник для вузов.- СПб.: ХИМИЗДАТ, 2005.
5.Григорьев, А.К. Термомеханическое упрочнение стали в заготовительном производстве.-Л.: Машиностроение, Ленингр. отд-ние, 1985.
6.Шульте, Ю.А. Хладноломкость стали.-М.:Металлургия, 1970
289

7. Захаров, В.Ф. Анализ причин хрупких разрушений металлических конструкций при низких температурах. В кн.: Проблемы хладостойкости конструкционных сталей. Иркутск: Вост.-Сиб. кн. изд-во. 1971.
М. И. Шулятьев, аспирант; А. С. Постнов, инженер
Н. В. Тепин, кандидат технических наук, доцент В. П. Шеногин, доктор технических наук, профессор
Ижевский государственный технический университет имени М. Т. Калашникова
Оценка упрочнения заготовки в местах изгиба при профилировании
Процесс получения гнутых профилей на профилегибочных станах заключается в последовательном изменении формы поперечного сечения плоской заготовки (ленты или листа) при прохождении ее через ряд вращающихся навстречу друг другу пар валков или роликов.
В сортаменте профилей особое место занимают гофрированные гнутые профили, имеющие несколько ребер или волн. Изучение мест изгиба на различных участках поперечного сечения такого профиля представляет наибольший интерес.
Упрочнение, возникающее при изгибе заготовки, ввиду неравномерности распределения деформации в значительной степени зависит как от схемы профилирования, так и от расположения места изгиба в самом профиле.
Для оценки упрочнения мест изгиба при профилировании проведено экспериментальное исследование.
Рис. 1. Схема вырезки образцов из профиля
Для выявления закономерности экспериментальное определение механических характеристик производилось для следующих профилей: С10, Н60, Н75. Они отличаются как геометрически (по толщине, высоте и количеству гофров), так и по режиму деформации. Из средней и крайней части профиля вырезались образцы. Они представляют собой полосы прямоугольной формы 150×15мм. Схема вырезки образцов из профилей представлена на рис. 1.
Интересующие участки были подвергнуты испытанию на растяжение до разрушения при помощи универсальной испытательной машины Instron 5982 (рис. 2). Данная машина позволяет с использованием современных цифровых технологий получать точные экспериментальные данные
290
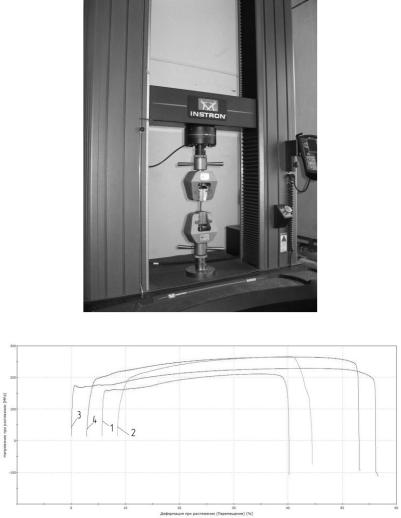
(табл. 1–3) и автоматически строить кривые растяжения испытываемых образцов (рис. 3–5).
Рис. 2. Испытание на растяжение образцов
Рис. 3. Кривые растяжения для образцов профиля С10
Таблица 1. Результаты испытания для профиля С10
|
Образец 1 |
Образец 2 |
Образец 3 |
Образец 4 |
Предел текучести ζТ, МПа |
149,274 |
110,862 |
159,735 |
121,419 |
Предел прочности ζВ, МПа |
211,034 |
265,664 |
228,397 |
263,824 |
|
|
|
|
|
291
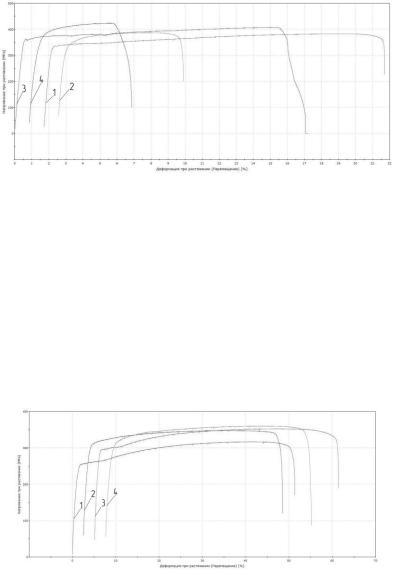
Рис. 4. Кривые растяжения для образцов профиля Н60
Таблица 2. Результаты испытания для профиля Н60
|
Образец 1 |
Образец 2 |
Образец 3 |
Образец 4 |
Предел текучести ζТ, МПа |
332,416 |
315,438 |
361,488 |
313,732 |
Предел прочности ζВ, МПа |
382,208 |
386,672 |
406,787 |
423,837 |
|
|
|
|
|
Анализ полученных результатов показал, что в местах изгиба на крайних гофрах предел прочности увеличивался на 1–26 %, предел текучести снижался на 5–26 %, в то время как на средней гофре предел прочности увеличивался на 2–15 %, предел текучести снижался на 6–24 %.
Калибровка профилей Н60 и Н75 предусматривает формирование центральной гофры за 4 перехода, а для С10 за 2 прохода. Данные эксперимента показывают, что упрочнение выше для профилей полученных с большей интенсивностью деформаций.
Рис. 5. Кривые растяжения для образцов профиля Н75
Таблица 3. Результаты испытания для профиля Н75
|
Образец 1 |
Образец 2 |
Образец 3 |
Образец 4 |
Предел текучести ζТ, МПа |
160,018 |
197,782 |
204,163 |
191,664 |
Предел прочности ζВ, МПа |
316,890 |
348,277 |
352,425 |
360,408 |
292
В работе [2] отмечалось, что усилие профилирования прямо пропорционально пределу текучести и текущему углу подгибки. Результаты эксперимента показали необходимость учета зависимости предела текучести от режима деформации.
Кроме того, полученные значения показали влияние расположения мест изгиба на механические характеристики профиля, что совпадает с результатами, полученными в работе [1].
Таким образом прослеживается общая закономерность по снижению предела пластичности и увеличению предела прочности в местах изгиба при профилировании, что является предметом дальнейших исследований.
Список литературы
1.Тришевский, И.С. Теоретические основы процесса профилирования: монография / И.С. Тришевский, М.Е. Докторов. – М: Металлургия. – 1980. – 288.
2.Шеногин, В.П. Методика расчета технологических параметров при профи-
лировании / В.П. Шеногин, Н.В. Тепин, В.А. Храбров, А.С. Постнов //Заготовительные производства в машиностроении (кузнечно-штамповочное, литейное и другие производства). - 2007.- № 4. – М.- 2007. - 35-37.
293