
Diplomne_ta_kursove_proektuvannya_UKR
.pdf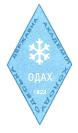
Міністерство освіти і науки України
Одеська державна академія холоду
Єременко Д.М.
Курсове та дипломне проектування
Посібник для студентів, що навчаються за спеціальностями 7.090508 та 7.090.522 напрямку « Енергомашинобудування».
Єременко Д.М. Дипломне та курсове проектування. Посібник для студентів, що навчаються за спеціальностями
7.090508 та 7.090.522 напрямку « Енергомашинобудування». Одеська державна академія холоду, 2008, 62 с.
Згідно з навчальним планом спеціальностей 7.090.508 та 7.090.522 напрямку підготовки «Енергомашинобудування», остаточним етапом підготовки фахівців за освітньо-кваліфікаційним рівнем «спеціаліст» є виконання курсового та дипломного проектів.
У посібнику надано етапи підготовки курсового та дипломного проектів і рекомендації щодо їхнього оформлення.
Рецензент: Хмельнюк М.Г., проф. Зав. кафедрою холодильних машин та установок.
Завідувач кафедрою |
|
К і П |
В.І.Милованов |
Голова науково-методичної комісії з напрямку підготовки «Енергомашинобудування».
М.Б.Кравченко
ОДАХ
2
Зміст
1.Вступ……………………………………………………………………4
2.Опис схеми холодильної машини й особливості дії компресора.....5
3.Розрахунок циклу……………………………………………………..6
4.Визначення головних термодинамічних параметрів……………….7
5.Розрахунок проточної частини відцентрового компресора………..9
5.1. Розрахунок робочих коліс………………………………………9
5.2.Розрахунок конструктивних параметрів і газодинамічних Функцій………………………………………………………...12
6.Розрахунок дифузорів………………………………………………..19
6.1.Розрахунок лопаткового дифузора…………………………..20
6.2.Безлопатковій дифузор ………………………………………26
7.Зворотні напрямні апарати………………………………………….28
8.Равлик (Улітка)……………………………………………………….32
9.Думіс………………………………………………………………….38
9.1.Визначення осьових зусиль, що діють на ротор відцентрової
компресорної секції…………………………………………...38 9.2. Визначення розмірів розвантажувального поршня (думіса).40
10.Визначення критичної частоти обертання ротора компресора…..42
11.Система змащення…………………………………………………..44
12.Підшипники………………………………………………………....47 12.1. Розрахунок опорного підшипника(див. рис.12.2 і 12.4.)…...50
12.2.Розрахунок завзятого підшипника…………………………..55
13.Розрахунок торцевого ущільнювача………………………………58
14.Список використаної літератури………………………………….61
3
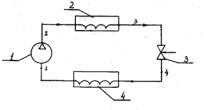
1. Вступ
Посібник призначений для курсового та дипломного проектування. Складовою частиною якого є розрахунок і проектування основних конструктивних елементів відцентрового компресора, котрі необхідні для забезпечення працездатності компресора та організації струму газу.
Відцентрові компресори знайшли застосування в багатьох областях промисловості. До них відносяться хімічна, нафтохімічна, газова та інші, а саме системи вентиляції повітря, холодильні установки глибокого холоду, системи життєзабезпечення в шахтах, для інтенсифікації процесів і інші системи й установки загальпромислового й спеціального призначення.
Одним з напрямків використання відцентрових компресорів є холодильна й тепло насосна техніка. Де за допомогою цих пристроїв у складі інших елементів систем можна одержати стиснені гази та пари й велику їхню продуктивність у широкому інтервалі температур.
За допомогою розробленого посібника студент здатний розрахувати основні термодинамічні властивості стиснутого середовища, газодинамічні параметри, а також конструктивні характеристики елементів компресора.
Як приклад розглянемо холодильну машину, що працює на хімічному комбінаті й повинна забезпечити наступні параметри при роботі на холодильній рідині R12B1:
холодильна продуктивність Qo=2,7 МВт
температура конденсації |
t1=80o |
температура кипіння |
t0=10o |
Цикл і схема установки наведена на рис. 1.1 і 1.2.
Рис.1.1.
4
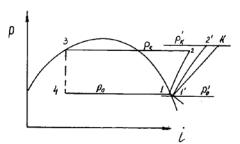
Рис.1.2.
2.Опис схеми холодильної машини й особливості дії компресора.
Розглянемо найпростішу схему, що містить у собі: компресор 1, конденсатор 2, регулюючий вентиль 3, випарник 4.
З випарника пари холодильного агента надходять на лінію усмоктування в компресор. При цьому його параметри відповідають стану т. 1 циклу, зображеного на рис. 1.2. Обертове робоче колесо сприяє збільшенню швидкості потоку агента, що надходить на його лопатки, тому що повна енергія потоку в цьому колесі залишається незмінною, то збільшення кінетичної енергії приводить до зниження потенційної. Отже, на початку процесу стиску тиск робочого тіла зменшується. На практиці проведення розрахунків прийнято вважати, що тиск потоку, що входить на лопатки робочого колеса відрізняється від тиску в магістралі на лінії усмоктування на 3-5%, тобто можна вважати, що Ро' = (0,95-0,97%) Ро, що відповідає стану на діаграмі т.
1'.
У міжлопаточному каналі відцентрового компресора стисливому середовищу повідомляється енергія двигуна. Це приводить до
збільшення потенційної (Р), кінетичної |
|
с |
2 |
|
і теплової (Т) енергій. |
|
|
|
|||
|
|
2 |
|
|
При виході з нерухомих елементів середовище має максимальний тиск, нормованою величиною швидкості й температурою, що відповідає стану газу (К). У процесі виходу стиснутого середовища з
5
компресора частина енергії затрачається на подолання опору потоку. Тому для підтримки тиску в конденсаторі рівному Рк необхідно стиснути газ до стану (т. 2 ') процеси 1 -2 і 1' -2' характеризують теоретичний адіабатний стиск. У той час як т. К характеризує дійсний стан наприкінці процесу стиску. Тиск при цьому прийнято вважати перевищуючий тиск у конденсаторі на (2-3%) тобто Р'к=(1,02-1,03) Рк.
Уконденсаторі 2 речовина прохолоджується, а потім конденсується. Цей стан характеризується т. 3.
Узв'язку з тим, що нами обрана найпростіша схема холодильної машини, то після дросельного вентиля розширене й охолоджене
середовище буде відповідати стану т. 4 і мати температуру кипіння Т 0 при тиску Р0.
Парорідинна суміш у випарнику віднімає тепло від охолоджуваного середовища й у насиченому стані (т. 1) надходить у магістраль лінії усмоктування компресора. Як було відзначено раніше, на лопатки робочого колеса надходить середовище при більш низькому тиску, але тому що відцентровий компресор має велику металоємність і значні теплопритоки, спрямовані до робочого тіла, то прийнято вважати, що
температура його в процесі 1-1' залишається незмінною і рівною t0. Отже, на початку процесу стиску середовища в компресорі її тиск
дорівнює Р0', а температура t0.
У проточній частині компресора стисливого середовища повідомляється енергія двигуна. Кількість прийнятої енергії визначається властивостями речовин, газодинамічними параметрами й конструктивними особливостями проточної частини. Тому не завжди одноступінчастий компресор здатний передати, а речовина - прийняти ту кількість енергії, що визначають задані параметри. Це приводить до необхідності використання такого числа щаблів, що може забезпечити необхідний режим роботи технологічного процесу (циклу).
3. Розрахунок циклу
За вищенаведеним циклом (рис. 1.2) розрахуємо значення параметрів у вузлових точках 1-1'-2-2'-3-4, а потім знайдемо питомі холодопродуктивність і тепло конденсації
6
q0= i1-i4, q k=I k- i3 |
3.1. |
Якщо взяти до уваги, що 2% холоду розсіюється в навколишнє середовище, то необхідно збільшити витрату робочого тіла на цю же
величину. Відповідно до цьому |
|
|
|
|
|
|
|||||
|
|
|
G0=(Q0/q0)x1.02 |
|
|
|
3.2 |
|
|||
Значення параметрів у вузлових точках занесемо в таблицю 3.1 |
|
|
|||||||||
|
|
|
|
|
|
|
|
|
Таблиця 3.1. |
||
|
|
|
|
|
|
|
|
|
|
|
|
|
|
|
|
|
т |
о |
ч |
к |
и |
|
|
|
Параметр |
|
|
|
|
|
|
|
|
|
|
|
1 |
|
2 |
|
3 |
4 |
1` |
2` |
К |
|
|
|
|
|
|
|
|
|
|
|
|
|
|
|
|
|
|
|
|
|
|
|
|
|
|
|
Р, МПа |
|
|
|
|
|
|
|
|
|
|
|
|
|
|
|
|
|
|
|
|
|
|
|
V, м3 / кг |
|
|
|
|
|
|
|
|
|
|
|
t, 0С |
|
|
|
|
|
|
|
|
|
|
|
i, кДж/кг |
|
|
|
|
|
|
|
|
|
|
|
|
|
|
|
|
|
|
|
|
|
|
4.Визначення головних термодинамічних параметрів.
Відомо, що дійсний процес стиску газу проходить по лінії політропи, але нам невідомий її характер. Тому необхідно розрахувати кількість дійсної енергії, витраченої на процес стиску. Із цією метою розрахуємо адіабатний ККД ηад..
Для цього необхідно знати ступінь підвищення тиску в процесі: |
|
Пк=Р2'/Р0' |
4.1. |
і ступінь зниження питомого об'єму: |
|
Кv=v1'/v2' |
4.2. |
тоді умовний показник адіабати буде: |
|
К'=lg Пк/(lg Kv) |
4.3. |
адіабатичний ККД за умови, що ηh=0,9 (газодинамічний ККД) можна визначити виразу:
7
η |
|
= |
ПкК'−1/ K' −1 |
||
ад |
|
K '−1 |
4.4. |
||
|
|
|
|||
|
|
|
ПкK 'ηh |
−1 |
адіабатна робота стиску:
ад = i2'-i1' |
4.5. |
Тоді робота стиску в процесі 1'-К буде дорівнювати: |
|
д =(lад/ηад) |
4.6. |
єнтальпія наприкінці процесу стиску розраховується як: |
|
iк = i1'+ д |
4.7. |
На діаграмі рис. 1.2 знайдемо місце розташування крапки К, що має координати Рк', iк. З'єднуємо точки 1' і К прямою лінією. Для того щоб знайти характер зміни P,v,t, i параметрів у процесі стиску розіб'ємо лінію 1' - К на кілька ділянок (не менш чим 10). Бажано, щоб точки були обрані на ізобарах.
Значення параметрів занесемо в табл. 4.1
|
|
|
|
|
|
|
|
|
|
|
Таблиця 4.1. |
||||
|
|
|
|
|
|
|
|
|
|
|
|
|
|
|
|
|
|
|
т |
о ч к |
|
и |
|||||||||
Параметр |
|
|
|
|
|
|
|
|
|
|
|
|
|
|
|
|
1` |
а |
b |
c |
d |
e |
f |
g |
h |
j |
i |
r |
m |
k |
|
|
|
||||||||||||||
|
|
|
|
|
|
|
|
|
|
|
|
|
|
|
|
Р, МПа |
|
|
|
|
|
|
|
|
|
|
|
|
|
|
|
|
|
|
|
|
|
|
|
|
|
|
|
|
|
|
|
V, м3 / кг |
|
|
|
|
|
|
|
|
|
|
|
|
|
|
|
t, 0С |
|
|
|
|
|
|
|
|
|
|
|
|
|
|
|
i, кДж/кг |
|
|
|
|
|
|
|
|
|
|
|
|
|
|
|
Отримані значення точок від 1' до К внесемо в P,v,t,-i діаграму, що зображена на рис. 4.1 і з'єднаємо їх плавною лінією.
8
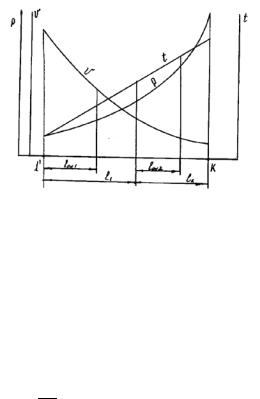
Рис.4.1.
5.Розрахунок проточної частини відцентрового компресора.
5.1Розрахунок робочих коліс
Узв'язку з тим, що для дозвукового плину струму M w1 не повинен перевищувати 0,8-0,9, виберемо Mw1=0,8.
Відношення діаметрів на вході й виході лопатки:
λ= D1 = 0,5 −0,7
D2
Кут |
входу |
βл |
і |
виходу |
βл знаходяться |
в |
інтервалах |
||||
|
|
|
1 |
|
|
|
2 |
|
|
|
|
βn1 =12°−45°, βn2 |
= 22,5°−90° |
|
|
|
|
|
|||||
Варто |
мати |
на |
увазі, |
що |
для |
стаціонарних |
машин звичайно |
||||
βл2 = 45°−60° ,але може бути |
й вище – до 900 , для коліс насосного |
||||||||||
типу βл2 |
=12,5°−32°, для щаблів авіаційного типу βл2 |
≥ 90°. |
|||||||||
Коефіцієнт витрати |
ϕч2 приймають |
при лопатковому дифузорі 0,2- |
|||||||||
0,27, при безлопатковому – 0,25-0,32. |
|
|
|
|
|
||||||
Розрахуємо умовне число Маха: |
|
|
|
|
|
||||||
|
|
|
|
|
M u |
= M w1 |
cos βΛ1 |
|
|
5.1. |
|
|
|
|
|
|
λ |
|
|||||
|
|
|
|
|
|
|
|
|
|
||
|
|
|
|
|
|
9 |
|
|
|
|
|

Тоді окружна швидкість
U |
2 |
= M |
u |
k ' P v ' 106 |
|
5.2 |
||
|
|
|
1 |
1 |
|
|
||
При високому значенні |
U2 |
варто |
оцінити |
допустимість цієї |
величини швидкості з погляду міцності. Для робочих коліс закритого типу, виготовлених з легованих сталей, допускають U2 до 300 м/сек. Робочі колеса авіаційного типу без покриваючого диска можуть мати
U2 до 450-500 м/сек.
Маючи на увазі , що окружна швидкість U2 визначає при обраних конструктивних співвідношеннях величину всіх інших швидкостей,
треба в подальших розрахунках визначити також величину чисел Мw1
і Мc2 і при високих значеннях оцінити допустимість їх. Відомо, що для розрахунків кількості щаблів необхідно
вибрати параметри колеса на вході й знайти коефіцієнт тиску. Для цього скористаємося таблицею 5.1.
|
|
|
|
|
|
|
|
|
|
|
|
|
|
|
|
|
|
|
Таблиця 5.1. |
|
|
|
|
|
|
|
|
|
|
|
|
|
|
|
|
|
|
||||
β |
л2 |
22,5 0 |
|
32 0 |
|
|
|
|
45 0 |
|
|
60 0 |
|
90 0 |
|
|||||
|
|
|
|
|
|
|
|
|
|
|
|
|
|
|
|
|
|
|
|
|
Z2 |
9-11 |
|
|
12-16 |
|
|
|
20-24 |
|
|
24-26 |
26-30 |
|
|||||||
|
|
|
|
|
|
|
|
|
|
|
|
|
|
|||||||
ϕr |
0,14-0,16 |
|
0,16-0,18 |
|
0,22-0,26 |
0,26-0,30 |
0,28-0,32 |
|
||||||||||||
|
2 |
|
|
|
|
|
|
|
|
|
|
|
|
|
|
|
|
|
|
|
α |
|
1,06 |
|
|
1,05 |
|
|
|
|
|
1,04 |
|
|
1,03 |
|
1,02 |
|
|||
тоді |
ϕ |
|
=1− |
π |
sin |
|
β |
|
|
−ϕ |
|
|
ctgβ |
|
5.3. |
|||||
|
|
|
|
|
|
|
|
|||||||||||||
|
|
|
uл2 |
|
r |
z2 |
|
л |
2 |
|
2 |
|
|
2 |
|
|
||||
|
Кількість щаблів рівняється: |
|
|
|
|
|
|
|
|
|
|
|||||||||
|
|
|
|
|
|
|
|
|
|
д 103 |
|
|
|
|
|
5.4. |
||||
|
|
|
|
|
|
|
X = U2 |
2ϕu 2α |
|
|
|
|
|
|||||||
|
|
|
|
|
|
|
|
|
|
|
|
|
|
|||||||
|
Потім кількість щаблів необхідно закруглити до найближчого числа, |
|||||||||||||||||||
і вибрати параметри для кожного щабля з таблиці 5.1. |
||||||||||||||||||||
|
|
|
|
|
|
|
|
|
|
|
|
|
|
|
|
|
|
|
||
|
Слід уточнити: |
U2 = |
|
|
|
|
∂103 |
|
|
|
5.5. |
|||||||||
|
|
|
Σϕu 2αiηhi |
|
||||||||||||||||
|
|
|
|
|
|
|
|
|
|
|
|
|
|
10