
2 курс допол. информ. для ИСУ / Монография Мизюн В.А._2012
.pdfнеэффективным в условиях масштабного производства, работающего в нестабильной экономической среде конкурентного рынка.
Учитывая данные недостатки гибкие автоматизированные линии, обладающие высокой производительностью и определенным уровнем гибкости/адаптивности, ограниченной техническими возможностями существовавших на то момент промышленных и информационных технологий, - нашли свое применение в непоточном/дискретном серийном производстве, которое представляло собой очередную ступень эволюционного развития производственных систем по завершении эпохи массового производства и потребления.
Непоточные методы организации производства
Возросшая в 1960-х гг. конкуренция подтолкнула промышленные предприятия к постоянному улучшению потребительских свойств товаров и технологий по их изготовлению, что вызвало необходимость непрерывного обновления ассортимента выпускаемой продукции, ее производство в небольших количествах (малыми сериями). Традиционные автоматизированные поточные производства, не могли обеспечить требуемую для этого гибкость/легкость перехода производства с одного вида продукции на выпуск другого, так как их пространственно-временная конфигурация имела ограниченное число степеней свободы (вариантов комбинации отдельных звеньев производственной технологической цепочки) и, соответственно, узкую товарную номенклатуру.
В целях увеличения технических возможностей реконфигурации (перестройки) технологического процесса, рабочие места/оборудование в цехах механической обработки деталей стали объединять в функциональные группы, без определенных связей, по типам выполняемых деталеопераций в виде однородных технологических участков (например, группы токарных, фрезерных, сверлильных и др. станков), которые позволяли создавать на основе их многофункциональной матричной структуры виртуальные технологические цепочки с неограниченным числом и разнообразной последовательностью соединения (комбинацией) неоднородных звеньев (см. рис. 1.3). При такой организации производственного процесса переход на выпуск новых и/или модернизированных изделий может осуществляться без трудоемкой перестановки специализированного оборудования, ограничиваясь его переналадкой. Поскольку процесс пространственно-временного сопряжения деталеопераций, в отличие от поточных методов производства, носит слабо согласованный (нечеткий) характер, то последовательность, режимы обработки деталей и алгоритм их перемещения от операции к операции задаются специально разрабатываемыми технологическими маршрутами. Последние представляют собой виртуальные пространственно-временные сети сопряженных технологических операций по обработке деталей, которые
21
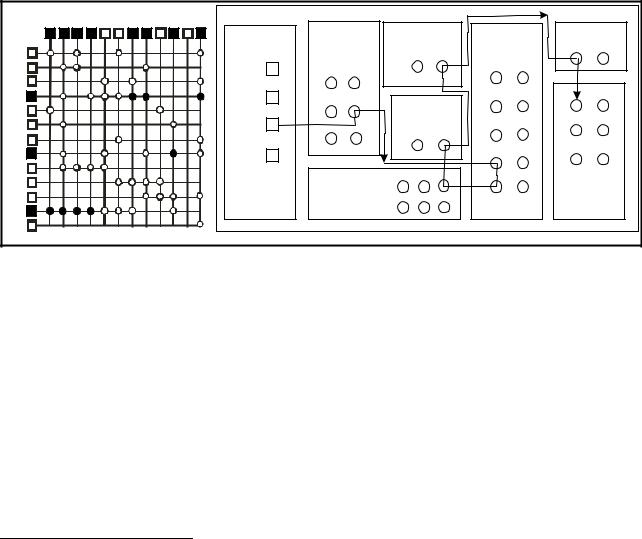
перемещаются между операциями партиями по сложным маршрутам с помощью специальных транспортных средств (краны, тележки, авто/электропогрузчики и т.п.)14.
Заказы / изделия/ узлы/ детали
и |
к |
н |
а |
т |
с |
/ |
М |
Р |
Г |
/ |
и |
к |
й |
е |
ч |
я |
е |
и |
к |
с |
е |
ч |
и |
г |
о |
л |
о |
н |
х |
е |
Т |
Рис. 1.3. Функционально-технологическая (матричная) топология непоточного производства
Преимуществом данного подхода к пространственно-временной организации технологического процесса в сравнении с поточным методом является повышение его гибкости, недостатками – увеличение времени последовательной обработки деталей партиями, которая предполагает многократное выполнение станком операций одного вида (А), и затем, многократное выполнение операций другого вида (В), после осуществления требуемой для этого переналадки оборудования (рис. 1.4).
14 В последствии концепция маршрутизации материальных потоков стала теоретическим фундаментом производственной логистики – дисциплины сформированной и широко используемой западной школой производственного менеджмента. Термин «логистика» (греч. logistike) первоначально обозначавший «счётное искусство» или «искусство вычисления и рассуждения» появился еще в древнем Ромейском государстве, где в период расцвета греко-римской империи (Византии) существовали служители, которые именовались «логистами» и занимались распределением продуктов питания. В первом тысячелетии, а именно во времена византийского императора Льва VI (866–912 гг. н.э.) логистика определялась, как искусство снабжения армии и управления её запасами, включая подготовку каждого военного похода. Благодаря военному делу логистика выросла в науку. Создателем первых научных трудов по логистике принято считать французского военного специалиста начала XIX века, барона А. А. Жомини (1779–1869 гг.); в них он определял логистику как науку об управлении при планировании запасов, перевозках и снабжении войск. Вторая трактовка термина «логистика» в значении математической логики использовалась в работах Г. Лейбница (1646–1716 гг.). Постепенно понятия и методы логистики переносятся из военной области в гражданскую, вначале как нового научного направления о рациональном управлении движением материальных потоков в сфере обращения, а затем и в производстве. Логистика как наука и как инструмент бизнеса стала формироваться в начале 1950-х годов, прежде всего в США. Развитие логистики тесно связано с историей и эволюцией рыночных отношений в индустриальноразвитых странах, причём сам термин «логистика» укоренился в бизнесе и стал повсеместно применяться в мире лишь с конца 1970-х годов. Необходимо отметить, что, по существу, производственная логистика, как дисциплина, практически полностью дублирует теоретический аппарат науки организации производства, не добавляя новых знаний к известным принципам рациональной организации технологического процесса и оптимального управления производственной деятельностью [см.: www.botanik-plus.ru].
22

|
A |
|
B |
A/1 |
1 |
10 |
B/5 |
|
|
|
|
A/2 |
2 |
9 |
B/4 |
A/3 |
3 |
8 |
B/3 |
A/4 |
4 |
7 |
B 2 |
|
|
/ |
|
A/5 |
5 |
6 |
B/1 |
Переналадка
оборудования
Рис. 1.4. Последовательный (а) и параллельный (б) способ обработки партий деталей А и В
Функционально-матричная организация технологического процесса обеспечивала возможность выпуска широкой номенклатуры изделий в небольшом количестве (серями), но существенно усложняла обслуживание заказчиков готовой продукции, запросы которых могли отличаться от производимых в текущий момент времени партий серийных изделий. Это было вызвано тем, что требование гибкости производства вступало в противоречие с существовавшей на тот момент технологической базой индустриальной экономики, основу которой составляло дорогостоящее, сверхточное (прецизионное) оборудование15. Необходимость постоянной загрузки, большие
15 Применение высокопроизводительного специального оборудования в составе жестко детерминированных однопредметных поточных линий, было эффективным в условиях массового и крупносерийного выпуска продукции узкой номенклатуры, поскольку это предоставляло возможность непрерывной одновременной (параллельной) обработки стандартного набора комплектующих по всему технологическому циклу, что существенно сокращало межоперационные потери времени, затраты на переналадку и простои оборудования. Поиск технических и организационных путей повышения технологической гибкости производства, ориентированный на функциональность и быстроту/легкость переналадки высокопроизводительного оборудования не осуществлялся, так как в этом до 1930-1950-х гг. не было необходимости. В результате использование специального прецизионного оборудования в многопредметном серийном производстве в 1960-х гг. привело к необходимости поочередной (последовательной) обработки деталей различных серийных изделий партиями, что значительно увеличивало время и затраты на изготовление продукции широкой номенклатуры. Компромиссным решением возникшей проблемы являлась параллельно-последовательная обработка крупных партий деталей с большим числом продолжительных операций (О.И. Непорент, 1928 г.), а также разработка и применение методов групповой обработки деталей (С.П. Митрофанов, 1955 г.), которые частично компенсировали отставание технологической базы промышленности от развития конкурентного рынка машиностроения. Позднее в 1970-1980-х гг. со схожей проблемой столкнулись производители вычислительной техники при создании операционных систем по обработке больших массивов плохо структурированной разнообразной информации.
23

затраты времени и средств на его переналадку вели к увеличению размера партий деталей, одновременно запускаемых в производство, что неизбежно вызывало межоперационное пролеживание комплектующих в составе крупных партий либо в ожидании окончания их обработки (А), либо в очередях на обработку нескольких партий деталей для различных серийных изделий (В). Это влекло за собой простои оборудования на других технологических операциях, которые вызывали длительные перерывы на узловой сборке из-за отсутствия необходимых комплектующих. Как следствие, неритмичная работа сборочных линий, рост незавершенного производства и замедление оборота активов, а также неспособность оперативно реагировать на колебания спроса, неизбежно приводили к разорению машиностроительных предприятий в условиях конкурентной рыночной экономики.
Непоточные методы организации технологического процесса нашли широкое применение в серийном и единичном производстве, для которых характерны периодическая или относительно редкая повторяемость изготовления изделий и их производство в различных объемах (от крупных партий до отдельных единиц), определяющие в конечном итоге степень организации (структуру) производственного процесса и виды движения предметов труда [63, 97].
Крупносерийное/серийное производство, отличающееся относительно постоянным или регулярным выпуском ограниченной номенклатуры изделий в большом количестве (сериями), имеет простую хорошо организованную структуру (см.:
рис. 1.5
Рис. 1.5. Структура непоточного производства: заготовительные участки/цехи, организованные по технологическому принципу (а); предметные участки поточного типа, применяемые на обрабатывающей и сборочной фазах производства (б).
24
Заготовительные участки/цехи организованы по технологическому принципу, а обрабатывающая и сборочная фазы производства осуществляются преимущественно предметными участками и цехами поточного типа (например, участки корпусных деталей, зубчатых коле, валов и т.п.). На предметных участках применяется специализированные станки (протяжные, токарные с копирами и гидросуппортами для обработки ступенчатых валов и т.п.), которые располагаются по ходу технологического процесса по аналогии с поточными методами организации производства, что сокращает время перемещения деталей между операциями и длительность производственного цикла в целом; на остальных участках преобладает групповая расстановка однотипного универсального оборудования со специальной оснасткой. Централизованно осуществляемая детальная разработка технологических процессов по повторяющимся сериям изделий снижает/исключает потребность в рабочих с универсальной квалификацией.
Мелкосерийное/единичное производство, для которого характерен нерегулярный выпуск небольшого количества или отдельных единиц изделий широкой номенклатуры, отличающихся значительным удельным весом нестандартных оригинальных деталей и узлов, характеризуется разнообразием работ, выполняемых на одном рабочем месте, большой трудоемкостью и длительностью операционного цикла изготовления продукции. Неустойчивость номенклатуры выпускаемых изделий, ее разнотипность, предопределяют ограниченное использование в данном типе производства стандартизованных конструкторских решений и типизированных деталеопераций, а также требуют гибкости/легкости перехода производства с одного вида изделий на выпуск другого. Последнее требует, чтобы пространственно-временная конфигурация производственной системы имела как можно большее число степеней свободы, которым в реальных условиях соответствуют различные варианты комбинации отдельных звеньев производственно-технологической цепочки. Поэтому мелкосерийное и единичное производство имеет сложную плохо организованную структуру по всем фазам производственного процесса, сформированную по технологическому принципу с разнообразными слабоструктурированными связями между смежными технологическими операциями - маршрутами движения деталей. Последнее обусловливает последовательное возвратно-встречное движение предметов труда между смежными технологическими операциями и, соответственно, большую длительность производственного цикла. Рабочие места, не имеющие постоянной специализации, загружаются неоднородной редко повторяющейся работой и/или разнообразными деталеоперациями, которые закрепляются за группой одномодельного (взаимозаменяемого) оборудования. Поскольку заказы на изготовление единичных изделий, как правило, не повторяются, то организационно-экономическая подготовка производства выполняется укрупнено. Детализация и определение очередности выполнения технологических операций по заказам, относящиеся к функции производственного планирования, осуществляются децентрализовано инженернотехническим персоналом производственных участков и цехов (мастерами, технологами) на основе текущих приоритетов [42, 63].
Из этого следует, что основные потери в непоточном производстве, обусловлены неполной загрузкой/простоями оборудования и возвратными движениями (петлянием) деталей по участку/цеху, которые происходят по причинам организационного характера и связаны с качеством составления календарного плана работ. Как показывает производственная практика, эффективно решить эту сложную управленческую задачу с помощью концепции и инструментария централизованного планирования, в частности с применением аппарата теории расписаний, - не представляется возможным по причинам объективного характера, в том числе с применением современных компьютерных технологий и мощных вычислительных систем.
25

Инертность мышления сторонников традиционной модели индустриального производства не позволяла преодолеть ограниченность ее концепции и базисных принципов, тем самым, инициируя безуспешные попытки с их стороны разрешить противоречия и проблемы данного способа производства методами и инструментами централизованного управления взамен поиска новых подходов к обеспечению технологической гибкости и оптимальному регулированию производственных систем16.
1.3.Система централизованного планирования и управления
Повышение гибкости производственных систем, увеличение степеней их свободы требует постоянной балансировки производственных ресурсов с периодически меняющейся программой выпуска продукции. В практике управления индустриальным производством это сводится к составлению расписания технологических операций с последовательной обработкой деталей партиями, поочередно выполняемых на различных участках производственного процесса. Теоретически, в целях уменьшения времени обработки очередей и сокращения производственного цикла, может быть сформирована минимальная по продолжительности выполнения последовательность операций, обеспечивающая непрерывную и согласованную работу всех производственных участков (рис. 1.6, таблица 1.1)17. Однако на практике выполнить это условие не представляется возможным, поскольку число вариантов последовательного запуска партий растет в месте с размером и сложностью номенклатуры изделий18. Последнее является причиной затяжных организационнотехнологических сбоев, которые приводят к сдвигу/совпадению операций по
16По этой причине в отечественной научной и учебной литературе периода 1970-90-х гг. в качестве основных направлений совершенствования промышленности предлагались: автоматизация технологических процессов на основе широкого использования поточных методов организации производства и разработка прогрессивных форм организации управления и планирования деятельности предприятий с применением ЭВМ (Либерман Е.Г., 1967; Латенко В.А., Туровец, О.Г., 1982).
17Определение размера партии является не менее сложной технико-экономической задачей, поскольку уменьшение партий увеличивает число переналадок и снижает производительность труда, а их укрупнение приводит к росту незавершенного производства и длительности технологического цикла, что в том и другом случае повышает затраты на изготовления продукции.
18Простые и точные аналитические способы отыскания порядка запуска деталей в обработку по критерию непрерывности/ритмичности работы существует только для производственных участков, на которых выполняется не более 2-3 операций (С.М. Джонсон, 1954; Р. Беллман, 1957). Расчеты выполняются исходя из оптимального размера партий, сходных технологических маршрутов, располагаемого числа рабочих мест и закрепляемых за ними деталеопераций. Научно доказано, что при большем количестве операций, выполняемых участком, точных методов не существует; для них разработаны приближенные графоаналитические методы (Г. Гант, 1910; К. Адамецки, 1916; С.А. Соколицин, В.А. Петров, 1988 г.). На практике для управления сложными (по маршрутам движения материальных потоков) дискретными производственными процессами, в которых обработка деталей ведется партиями различной величины, а производство ориентировано не меняющийся рыночный спрос, планирование последовательности работ очень часто заменяется диспетчированием [104, 145].
.
26

времени, в результате чего возникают простои оборудования и/или пролеживание деталей в очередях на обработку ввиду его занятости [104, 145].
Табл. 1.1
Рис. 1.6. Определение оптимальной последовательности обработки партий деталей А и В
Широко распространенный в массовом/непоточном производстве способ их устранения, компенсирующий недостатки планирования, предполагает принудительную координацию работы всех элементов производственной системы, которая осуществляется централизованно диспетчерской службой – субъектом/системой оперативного управления (СУ), направляющей на производственные участки команды по корректировке очередности/приоритета выполнения операций исходя из текущей производственной обстановки (рис. 1.7).
Субъект управления
Сравнение План план - факт
Информация обратной
связи Управляющая
информация
|
Фактические |
||
Операционная |
параметры |
||
система |
|
|
|
Ресурсы |
Продукция |
|
Объект управления |
Субъект управления
Обратная |
|
Обратная |
связь |
|
связь |
|
Управляющая |
|
|
информация |
|
Объект |
Ресурсы |
Объект |
управления1 |
|
управления2 |
Рис. 1.7. Процесс централизованного управления производством
27

Результаты выполнения отдельных операций поступают через систему контроля и используются СУ для изменения (корректировки) состава и порядка выполнения производственного плана, исходя из фактических результатов работы участков, их текущего состояния и наличия необходимых ресурсов (см.: обратная связь). Основная проблема заключается в том, что данный способ организации управления операциями (при всей его кажущейся простоте) требует наличия в СУ полной непрерывно обновляемой в режиме реального времени (динамической) модели производственного процесса, учитывающей колебания рынка, а также непрерывной и надежной связи/коммутации субъекта и объектов управления. В условиях индустриального производства реализовать эти требования в полной мере не представляется возможным, поскольку моделью производственного процесса в этом случае является жесткий планграфик (программа) выпуска изделий, низкая оперативность корректировки которого, несоизмерима с быстротой изменения параметров внутренней среды предприятия и конъюнктуры рынка. В результате неадекватности (неполноты) условно-статичной модели производственно-технологического процесса возникают и накапливаются ошибки в системе планирования, снижается эффективность управления, и растут средние издержки производства [73, 78, 145]19.
Основным недостатком централизованной системы управления массовым производством является несогласованная работа обособленных технологических участков в общем процессе изготовления продукции. Смежные участки по производству деталей функционируют независимо друг от друга, производя и выталкивая в межоперационное пространство (на промежуточный склад) продукцию в соответствии с планом-графиком, составленным планово-диспетчерской службой предприятия на основе предположений о том, что понадобится каждому производственному микропроцессу, игнорируя при этом его состояние и текущие потребности в деталях и комплектующих. Действуя в рамках плана, каждый участок самостоятельно устанавливает объемы партий и темп производства исходя из собственного (локального) представления задачи выполнения плановых заданий по производству продукции и экономической эффективности, а не общесистемного
19 Традиционное представление процесса производства в виде детерминированной (статичной) системы базируется на следующем. Предполагается, что длительность производственного цикла детали является величиной строго определенной (неизменной), трудоемкость изготовления изделия распределяется равномерно в пределах каждой стадии производственного цикла и не меняется во времени, а общая длительность изготовления заказа зависит от его индивидуальных характеристик (сложности состава технологических процессов, средней трудоемкости операции на различных стадиях производства и т.п.). На самом деле длительность циклов/ трудоемкость изготовления деталей/заказов (интенсивность работ) является величиной вероятностной и зависит от характеристики того набора деталей/заказов, которые запланированы к производству на один плановый период и от особенностей организации процесса производства на предприятии (средний коэффициент закрепления операций за рабочим местом, размер партий деталей, управление движением узких мест в производстве). Игнорирование динамического характера производства приводит к разбалансировке планов и ресурсов предприятия, дефициту деталей на сборке и, как следствие нарушению плановых сроков исполнения заказов [29, 97].
28

видения всего производственного процесса (глобальной оптимизации потока создания ценности). В такой ситуации предыдущие процессы будут иметь тенденцию выпускать изделия, которые не нужны последующим процессам (их потребителям) в настоящее время. Это означает выпуск одних изделий в большем количестве, чем это нужно для осуществления требуемых на данный момент технологических операций и, соответственно, нехватку других, что приводит к вынужденным простоям оборудования и потерям рабочего времени.
Для устранения этого несоответствия создаются большие запасы изделий на промежуточных (межоперационных) складах и запасы готовой продукции для быстрой отгрузки потребителям, а также отводится больше времени на выполнение заказа, чем это требуется по технологическому регламенту. Сборка партиями означает, что поставляемые комплектующие также будут потребляться партиями, что приведет к раздуванию объема запасов на промежуточных (межоперационных) складах выше по потоку движения изделий. При этом вариабельность процесса конечной сборки сильнее сказываться на вариабельности предшествующих сборке технологических операций, запасы для которых необходимо увеличивать кратно вверх по потоку. Возникает потребность в резервных мощностях, отсутствие которых приводит к возникновению в производственном процессе так называемых «узких мест», которые существенно ограничивают производительность и скорость реакции системы массового производства на изменение условий внешней среды (запросы потребителей). Как следствие этого, увеличиваются объемы незавершенного производства и продолжительность технологического цикла со всеми вытекающими из этого организационно-экономическими последствиями20.
С целью преодоления недостатков централизованного способа управления, усиливающих отрицательный эффект масштаба индустриального производства в современных условиях, крупные машиностроительные корпорации разрабатывают автоматизированные системы управления. Тем не менее, это не приводит к кардинальному улучшению положения: в случае успешности их внедрения кривая средних долгосрочных издержек сначала падает, а затем, начиная с момента исчерпания действия положительного эффекта так называемого информационного реинжиниринга технологического процесса,
становится более или менее горизонтальной [69]. Проблема заключается в том, что централизация управления была необходима и достаточна для обеспечения
20 Экономическое значение длительности производственного цикла заключается в том, что его продолжительность определяет размер незавершенного производства, стоимость которого является одной из наиболее весомых частей оборотных средств предприятия. Так как на предприятиях машиностроения, имеющих относительно длительный производственный цикл, незавершенное производство составляет 30-50% оборотных средств в запасах товарно-материальных ценностей, то увеличение/сокращение его продолжительности приводит к увеличению/уменьшению потребности в оборотном капитале, поскольку он остается без движения (омертвляются) в производстве на больший/меньший срок. Увеличение/сокращение длительности производственного цикла также ведет к росту/уменьшению потребной в складских площадях для хранения незавершенного производства, запасов сырья и материалов, к ухудшению/улучшению использования основных фондов, увеличению/снижению себестоимости продукции.
29
непрерывности стационарного процесса массового производства стандартной продукции, и совершенно не предназначена для организации и регулирования нестационарных потоков изделий и работ, характерных для гибкого рыночноориентированного производства. Именно это обстоятельство лишает предприятия индустриального типа свойства адаптации к меняющейся среде, делает их нежизнеспособным механизмом в новых реалиях конкурентной рыночной экономики.
Особенности балансировки планов и ресурсов машиностроительного предприятия
В традиционном/классическом понимании централизованное управление производством представляет собой непрерывный процесс выработки системой планирования (субъектом управления) регулирующих воздействий, которые по каналам информационных коммуникаций передаются на технологические участки (объекты управления) для обеспечения их слаженной работы в заданном режиме в соответствии с производственной программой (целевой функцией). С этой целью служба планирования предприятия при получении заказов составляет графики работ на определенный период (сутки/неделя/месяц) для всех этапов производственного процесса (изготовление заготовок, деталей и узлов, сборка изделий) с использованием автоматизированной системы планирования, которая рассылает инструкции каждому производственному участку о том, что надо сделать в предстоящий плановый период. Поскольку производственный процесс, как правило, не идет в точном соответствии с разработанным планом, то осуществляется наблюдение за ходом производства с помощью отчетов производственных участков о фактическом выполнении плановых заданий, на основании которых осуществляется корректировка плана и повторная передача инструкций/сменных заданий производственным участкам (рис. 1.8).
Основным инструментом производственного планирования выпуска конечного продукта является расписание работ, которое представляет собой алгоритм пространственно-временного распределения (балансировки) оборотных ресурсов предприятия между технологическими операциями по их обработке. В машиностроении распределение ресурсов осуществляется путем определения календарных сроков запуска деталеопераций и их закрепление за различными группами оборудования, на основании производственной программы и так называемой компоновочной структуры или дерева продукта, которую часто называют «ведомостью/спецификацией материалов».
30