
2 курс допол. информ. для ИСУ / Монография Мизюн В.А._2012
.pdf
Основу классической системы кустарного производства автомобилей, широко распространенного в странах центральной Европы, составляли мастераумельцы, которые хорошо знали свойства различных материалов и способы их обработки, детально понимали принципы конструирования машин и были способны создавать и изготавливать автомобили ручной сборки в небольших количествах. Большинство из них являлись владельцами небольших механических мастерских, функционировавших в качестве независимых поставщиков комплектующих в составе специализированных автомобилестроительных компаний, которые заказывали у них конструкторские работы, дизайн, а также необходимые детали, и самостоятельно несли ответственность за сборку конечного продукта. Отличительная особенность этой системы заключалась в отсутствии стандартизованных деталей и измерительных инструментов, а также точного оборудования для обработки металла, что влекло за собой необходимость трудоемкой подгонки деталей на этапе финишной сборки и доводки машин, которые существенно повышали их стоимость и сдерживали рост объемов производства2. В данных обстоятельствах производители концертировали свое внимание на обеспеченных заказчиках, которых, прежде всего, интересовали не стоимость, удобство управления и простота обслуживания, а ходовые качества, скорость и особые индивидуальные черты автомобиля, изготовленного в соответствии с их пожеланиями. Кустарное производство машин по индивидуальным заказам, сохранившееся в Европе до наших дней, вполне отвечало ограниченным потребностям автомобильных рынков европейских стран, небольшие и скудные на ресурсы территории которых, были густонаселенны и хорошо освоены3.
Естественно, что для огромного развивающегося североамериканского континента кустарный способ производства товаров был неприемлем, поскольку растущая экономика Соединенных Штатов требовала большого количества доступных по цене товаров, средств их производства и доставки, для изготовления которых в промышленных масштабах к этому моменту были накоплены необходимые знания, технологии, капитальные и финансовые ресурсы. К тому времени, когда сложилась общая конструктивная концепция автомобиля – кузов/рама, четыре колеса, двигатель внутреннего сгорания,
2Проблема заключалась в том, что в конце 18 века еще не были созданы технологии и станки для обработки стальных деталей, прошедших термообработку (закалку) в печах с целью повышения их прочности. Естественная деформация деталей при их сильном нагреве требовала последовательной подборки/подгонки деталей на сборке, в результате которой автомобили, изготовленные по одним и тем же чертежам значительно, отличались друг от друга из-за так называемого «крипа размеров».
3Состоятельные заказчики автомобилей эксклюзивных марок Роллс-Ройс, Бентли, Ломборджини,
Феррари, Мазерати (Rolls-Royse, Bently, Lamborghini, Ferrari, Maseratti) как тогда, так и сегодня нанимают в свой личный штат шаферов и механиков.
11

трансмиссия, рулевая колонка управления и тормозная система, промышленность достигла технологической зрелости, ставшей основой новых идей и принципов производства. Поиск путей преодоления проблем, содержащихся в основе кустарного способа производства, осуществлялся по мере концентрации производительных сил в виде крупных заводов и фабрик, а также развития инженерных и общественных наук. Питательной средой взрастившей передовые достижения американской техники и технологий были промышленные предприятия, работой которых управляли инженеры. Так, например, известный американский изобретатель Э.Уитни (1765-1825 гг.) организовал производство хлопкоочистительных машин, впервые применив принципы рациональной организации процесса их изготовления: взаимозаменяемости деталей, специализации, конвейерной сборки и контроля качества. Английский математик, автор трудов по теории функций механизации счетных операций в экономике Ч.Бебидж (1791-1871) развил идеи Э.Уитни до уровня организации управления промышленными предприятиями: разделение труда в управлении, механизация производства, контроль над издержками и учет влияния внешней среды. И все же, основные идеи и принципы модели массового производства и потребления, применяемые на многих промышленных предприятиях по настоящее время, были окончательно сформулированы лишь в конце 19 века основателями школы научного управления Ф. Тейлором (1856-1915), А. Файолем (1941-1925), их учениками и последователями, внесшими существенный вклад в промышленное развитие мировой экономики [137, 173]4. Материальным воплощением этой модели стали автомобильные заводы Г.Форда (1863-1947), на которых примененные им технологические новшества и инженерные решения позволили значительно снизить себестоимость, улучшить качество и эксплуатационные характеристики машин [138, 161]. Ключевыми факторами революционных изменений сначала в американской автомобилестроительной области, а затем и во всем мировом машиностроении стали простота конструкции, взаимозаменяемость деталей и технологичность сборки машин – новшества,
4 Развил систему Ф. Тейлора в конкретных условиях материального производства известный промышленник Г. Форд-старший (1863-1947), который основал в 1903 году автомобильный трест, одну из крупнейших монополий США (Ford Motor Company), объединившую железные рудники, угольные копи, металлургические предприятия, машиностроительные, автомобильные и другие заводы. Усилия Форда были направлены на разработку, прежде всего организационно-технических принципов управления производством в рамках предприятия и корпорации. Он разработал принцип вертикальной системы работы предприятия и осуществил его в рамках собственного автомобильного концерна, где все этапы, стадии производства начиная от плантаций, производящих каучук, рудников, металлургических заводов, и заканчивая конвейером для сборки автомобилей, управлялись из одного центра. Форд широко применил стандартизацию и типизацию производственных процессов. Он впервые в мире ввел систему непрерывно-поточного производства, которая основывается на точном согласовании деятельности отдельных его частей в определенном ритме и последовательности с помощью конвейера. Система организации производства Форда развивала принципы научного управления Тейлора применительно к новым условиям механизированного и автоматизированного производства, ставя ту же цель - максимальной интенсификации труда.
12

сделавшие возможным применение механизированных сборочных линий (конвейеров) в промышленных масштабах5.
Взаимозаменяемость деталей достигалась использованием единой системы измерений для изготовления унифицированных деталей на всем протяжении производственного цикла, а также применением новейших на том момент высокопроизводительных точных (прецизионных) металлорежущих станков и мощных штампов, способных обрабатывать закаленную сталь. В дополнение к этому Г.Форд разработал конструкцию машин, которая позволяла снизить необходимое количество деталей и сделать их более простыми (технологичными) для сборки6. Это позволило не только сократить сроки, но и увеличить масштабы выпуска продукции, за счет вовлечения в процесс производства большой массы неквалифицированных рабочих, каждый их которых выполнял только одну операцию на сборке, переходя от машины к машине по всему сборочному цеху. Узкая специализация давала большой рост производительности труда, потому, что быстро и полностью овладевший одной операцией рабочий, мог выполнять ее по времени гораздо быстрее, просто устанавливая точно подходившие детали без их подгонки и доводки узлов7. Вовлечение в производство сложной технической продукции большого количества малообразованных рабочих, не имевших полного представления о том, как устроен автомобиль и процесс его изготовления, многие из которых были эмигрантами и почти не общались между собой из-за того, что плохо говорили на английском, - потребовало централизации функций технического развития, планирования, материального обеспечения, управления ходом работ и контроля качества сборки автомобиля, которые были делегированы профессионалам нового типа – инженерам (конструкторам, технологам, механикам-наладчикам, инженерам по качеству и т.д.). Их труд по мере усложнения техники и процесса ее изготовления также претерпевал все более подробное разделение, в результате которого возникла вертикальная система
5Существует распространенное заблуждение, которое сейчас разделяют многие, относительно того, что главным элементом массового производства является линия непрерывной сборки (конвейер), предложенный Г.Фордом, упуская из виду, что применение сборки на движущемся потоке изделий стало возможным благодаря достижению им полной взаимозаменяемости комплектующих и технологичности сборки.
6Примечательно, что в то время никто в машиностроительной отрасли не понимал преимущества этих нововведений, которые позволили в дальнейшем значительно снизить стоимость сборочных операций, увеличить производительность труда и, соответственно, выпуск автомобилей. Это давало огромное преимущество корпорации Форда над конкурентами, и обеспечило ее полувековое господство в мировой автоиндустрии. Отсутствие моральной поддержки со стороны коллег и общественности компенсировалось осознанием прибыли, которую мог получить Г.Форд, снизив стоимость сборочных операций.
7Форд сам предложил название своей новой системе, опубликовав в 1926 году в Британской энциклопедии статью под названием «Массовое производство». До этого момента многие называли этот метод организации производства «Фордизмом». Предложенная им непрерывно-поточная технология сборки автомобилей позволила отказаться от услуг хорошо оплачиваемых квалифицированных слесарей, составлявших на сборочных заводах, использующих кустарную систему производства, основную часть рабочей силы. Каждый из них собирал автомобиль практически полностью, выполняя его доводку и регулировку [25].
13

централизованной инженерной подготовки, сквозного планирования и регулирования производства, а также свойственные ей неразрешимые проблемы бюрократизации управления. В соответствии с разработанной Г.Фордом парадигмой конвейерной сборки автомобилей рабочие стали (аналогично машинам) взаимозаменяемыми исполнительными компонентами технологического процесса, выполняющими простейшие операции, лишенными возможности участвовать в организации и регулировании процесса производства и, соответственно, оказывать влияние на его результаты. Эти функции (инженерной подготовки, обеспечения, регулирования и совершенствования процесса производства) были переданы вспомогательному персоналу, бригадирам и инженерам-технологам. Последние в соответствии с принципом разделения труда, передавали свои предложения и находки на следующий, более высокий уровень менеджмента, который вынужден был согласовывать свои решения с вышестоящими инстанциями и т.д. Так появилась сложная бюрократическая система вертикального управления, в которой была занята целая армия узкоспециализированных работников ничего не добавлявших к стоимости автомобиля, а также возникла проблема эффективности управления (потери управляемости) крупными промышленными предприятиями и корпорациями, которая является естественным и неизбежным следствием специализации/разделения инженерного труда в условиях роста сложности и масштабов производства8.
Заключительным этапом совершенствования процесса массового промышленного производства машин стала механизированная доставка/подача конвейером деталей и узлов к рабочим местам сборочных линий, которая устраняла непроизводительные потери времени и уменьшала количество человеческих усилий/труда, затрачиваемого на сборку автомобиля9. Проверка качества сборки осуществлялась в конце линии, где специальная группа слесарей выполняла доводку автомобиля10. Комбинация всех этих
8 Углубление специализации, наряду с повышением производительности труда и качества выпускаемой продукции, в дальнейшем неизбежно порождает низкое качество (бессистемность) управляющих решений и, как следствие, потерю управляемости. По этой причине, в противовес специализации, возникает потребность в преодолении разобщенность и координации совместных действий работников предприятия в процессе осуществления ими коллективной предметной деятельности на основе системного подхода к организации производства и управления, основные принципы и положения которого подробно раскрыты в последующих разделах монографии. В современных условиях принцип вертикальности управления корпорацией в известной мере изживает себя; тем не менее, идея о кооперированных связях, единстве управления различными этапами производства одного изделия не потеряла своего значения и в настоящее время.
9Первоначально на заводах Форда применялась стендовая сборка. Пуск первой непрерывной сборочной линии – конвейера состоялся в 1913 году. Конвейер Форда представлял собой транспортер, состоящий из электродвигателя и прикрепленных к нему двух полос металлических пластин, уходящих в низ пола и возвращающихся к исходной точке, на которые колесами ставились автомобили.
10Разделение труда позволяло использовать в производстве низко квалифицированных рабочих, обязанности которых заключались в выполнении простых сенсомоторных операций по манипулированию /управлению механизированным оборудованием, что позволяло в дальнейшем автоматизировать многие
14

конструкционно-технологических и рыночных преимуществ позволила корпорации Форда стать лидером мировой автомобильной промышленности конца XIX – начала XX вв. Отдавая должное оригинальности технологических нововведений в процесс производства автомобилей на заводах Г.Форда, необходимо также отметить рыночно-ориентированную направленность его продукта (серийной модели «Т» черного цвета, 1908 года) на массового потребителя. Автомобили Форда были рассчитаны на мелких фермеров и предпринимателей, которые в развивающейся наполовину аграрной Америке 18-19 вв., составляли подавляющее большинство платежеспособного населения, а также обладали навыками ремонта машин и минимальным комплектом инструментов, необходимых для технического обслуживания сельскохозяйственного и иного оборудования. Почти каждый из них мог управлять автомобилем и ремонтировать его без специальной подготовки и технический базы, отказавшись от услуг шофера и механика. Внешний вид и небольшие дефекты в подгонке деталей при сборке не беспокоили эту категорию покупателей, так как простота конструкции автомобиля и прилагаемая инструкция по эксплуатации, позволяли самостоятельно устранить неисправности. При этом все же необходимо учитывать, что заводы Форда создавались и работали в отсутствии жесткой конкуренции на мировом рынке автомобилестроения, поскольку европейские фирмы, выпускавшие эксклюзивные автомобили на заказ, попросту проигнорировали развивающийся американский рынок массового потребителя XIX в.
Однако в современных условиях конкурентного рынка модель массового/ индустриального производства, прочно вошедшая в сознание ученых и практиков через систему инженерного образования, постепенно теряет свои преимущества. Более того, она становится естественным препятствием на пути структурной перестройки и технологической модернизации отечественного машиностроения, его перехода на передовые методы организации высокотехнологичного гибкого интегрированного производства. Как будет
показано ниже, причины несоответствия |
индустриального |
способа |
|
производства современной экономической |
реальности, |
его |
проблемы, |
противоречия и недостатки заключаются в исторически сложившемся сочетании непрерывности процесса поточного производства (за счет снижения
операции на стадии мехобработки деталей и, соответственно, повысить производительность и качество труда. Однако на сборочной стадии, ручной характер которой невозможно автоматизировать по определению, такой подход к организации деятельности, приводил к тому, что нацеленные на повышение объемов выработки рабочие, не могли (в силу своей низкой квалификации) и не имели возможности (из-за быстрого непрерывного движения конвейера) обнаружить неизбежные при изготовлении деталей дефекты. В дальнейшем (как будет показано в следующих разделах книги), с ростом сложности и разнообразия продукции это создавало неразрешимые системные проблемы, связанные с качеством автомобилей и необходимостью трудоемкой доработки дефектов, что практически полностью обесценивало организационно-экономические преимущества массового производства.
15

технологической гибкости) и централизации управления его ходом, которое осуществляется на промышленных предприятиях инженерно-техническими работниками посредством известной процедуры планирования и диспетчирования [25]11.
1.2.Системотехнические основы и отличительные характеристики
После того как был достигнут значительный рост производительности труда на сборочных заводах, Форд приступил к воплощению идеи и принципов непрерывного производства (в современной англоязычной терминологии – потока создания ценности) в механообрабатывающих цехах, которые занимались изготовлением деталей. Поскольку в условиях развивающейся автоиндустрии и монопольного положения заводов Форда спрос на их продукцию, как правило, превышал производственные возможности и был стабилен на протяжении длительного времени (1908-1955 гг.), - появилась потребность в массовом изготовлении недорогих комплектующих (автокомпонентов). По аналогии с разделением труда на сборочных заводах сложный процесс производства деталей расчленялся на множество простых деталеопераций (элементов работ). Операции в свою очередь закреплялись за строго определенными рабочими местами и станками, что обеспечивало непрерывную повторяемость их выполнения, и, следовательно, полную загрузку оборудования, которая, наряду с совершенствованием трудовых навыков рабочими, приводила к росту производительности (интенсивности) труда и наиболее эффективному использованию производственных фондов. Поскольку это исключало необходимость в использовании переналаживаемых станков и оснастки универсального назначения, широко применявшихся в кустарном производстве, Г.Форд отказался от применения малопроизводительного многофункционального оборудования, изготовив специальные станки, которые выполняли только одну операцию12.
11 Изучение фундаментальных основ и системотехнических принципов организации индустриального производства, представляющего собой базисную основу современных производственных систем, позволяет выявить и понять общие (универсальные) закономерности их построения и функционирования не зависимо от культурно-исторических корней и национальных особенностей возникновения и развития. Это предоставляет возможность оценить преимущества передовых промышленных технологий, методов организации производства и управления, определить целесообразность их заимствования (экспорта) и способы применения в условиях той или иной экономической формации.
12 Во всем мире детали машин изготавливаются путем литья и штамповки из листовой стали металлических заготовок, с последующей их сваркой, механической обработкой и нанесением защитного покрытия. В системе кустарного производства для этих целей применялось универсальное оборудование, которое требовало предварительной наладки и настройки на необходимую операцию, а также трудоемкой подготовительной работы по закреплению заготовки в станке. На заводах Форда были сконструированы специализированные станки, способные выполнять только одну операцию, а также специальные приспособления, с помощью которых неквалифицированные рабочие могли устанавливать детали и быстро фиксировать их с помощью рычага в один прием. Это позволяло полностью автоматизировать наиболее сложные и ответственные операции мехобработки (например, обработка блоков и головок блоков цилиндров
16

В дополнение к этому, поскольку Форд производил только одну модель автомобиля, такие станки стали выстраивать в технологическую цепочку в соответствии с последовательностью выполняемых технологических операций аналогично конвейеру, что создавало условия организации непрерывного потока изделий, перемещающихся в ходе производственного процесса от одной технологической операции к другой. В отличие от индивидуального (ремесленного) производства, такой подход к организации промышленной деятельности значительно упрощал процесс изготовления автокомпонентов, что позволяло существенно сократить потери и общее время изготовления продукции (рис.1.1).
Рис. 1.1. Цепное расположение оборудование по ходу производства
Введенные Г.Фордом в процесс механообработки организационнотехнологические новшества в дальнейшем послужили фундаментом для формирования и совершенствования универсальных принципов рациональной организации промышленного производства (непрерывности, параллельности, прямоточности и ритмичности технологического процесса), возникновению и развитию его различных типов (непрерывно-поточного, серийного и единичного), специфика которых и обусловливает возникновение проблем и противоречий индустриальной экономики на современном этапе развития производительных сил и отношений в обществе, что, соответственно, требует их более подробного рассмотрения.
Поточные методы организации производства
Последовательное (цепное) расположение рабочих мест по ходу технологического процесса в непосредственной близости друг от друга позволяет перемещать детали между смежными операции мелкими партиями (3-5 шт.) или поштучно с помощью специального межоперационного (самодвижущегося и гравитационного) транспорта, а также механизировать/автоматизировать стандартизированные процессы обработки, загрузки/выгрузки и транспортировки предметов труда. Выравнивание продолжительности (синхронизация) операций по времени путем подбора
двигателя), точность выполнения которых теперь зависела только от исправной работы станка. Последнее резко снижало затраты времени и труда, а также потребность в квалифицированных операторах-станочниках.
17
пропорционального количества рабочих мест и мощности оборудования в соответствии с трудоемкостью обработки предметов труда обеспечивает параллельность (одновременность) выполнения работ, ритмичность и непрерывность производственного процесса. Все это в совокупности определяет высокую степень пространственно-временной организации (балансировки) процесса массового поточного производства, которая устраняет непроизводительные затраты труда и времени на перемещение и пролеживание деталей у рабочих мест в ожидании обработки, а, следовательно, значительно сокращает межоперационные запасы (незавершенное производство) и общее время изготовления продукции, повышая экономическую эффективность производства [97, 104].
В дополнение необходимо отметить, что высокий уровень организации массового производства позволяет изначально, на этапе проектирования предприятия, задавать устойчивую во времени (детерминированную) пространственно-временную структуру технологического процесса и, соответственно, автоматизировать/роботизировать большинство технологических операций, что объективно исключает необходимость в детальном технико-экономическом планировании и оперативном регулировании как способе перманентного определения наиболее оптимального сочетания (балансировки) ресурсов и задания эффективного алгоритма работы производственной системы предприятия. Относительно простая задача управления в этом случае сводится к нормативно-календарным расчетам такта/ритма работы поточной линии, числа рабочих мест и их загрузки, цикловых и складских заделов, а также организации технического обслуживания групп рабочих мест/станций/установок, их бесперебойного снабжения инструментом, материалами, заготовками и комплектующими изделиями с целью предотвращения незапланированных простоев и обеспечения ритмичной, взаимосвязанной работы всех участков поточной линии.
Оборотной стороной перечисленных преимуществ является жесткая детерминированность структуры подобных производственных систем, существенно ограничивающая их гибкость/адаптивность к изменениям внешней среды. Сетевая топология производственного процесса, включающая (предустанавливающая) распределенные пространственно-временные алгоритмы (схемы) движения предметов труда между звеньями технологической цепочки (набор и интенсивность операций обработки), задается на этапе организационно-технологической подготовки поточного производства, как это представлено на рис. 1.2.
18
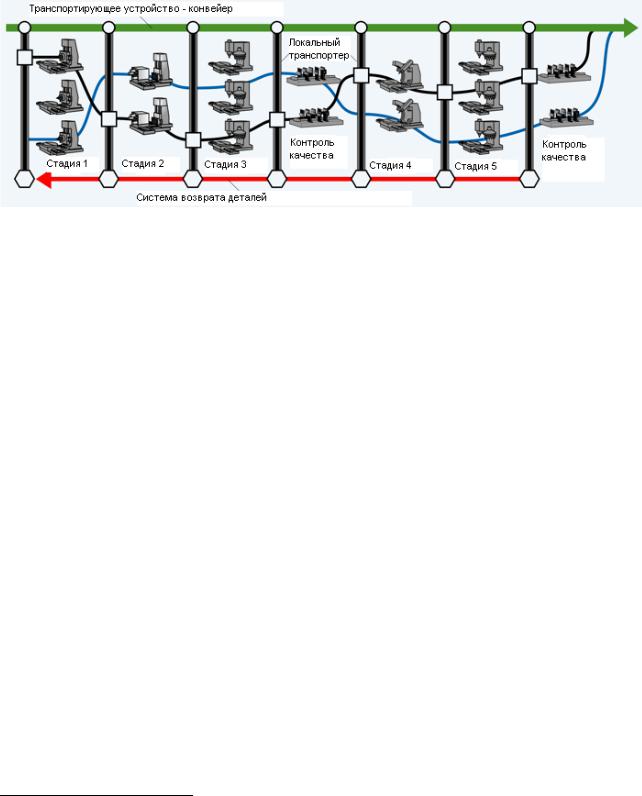
Рис. 1.2. Сетевая топология поточного реконфигурируемого производства
При различных вариантах развития производственной ситуации (например, при необходимости перехода производства с одного вида продукции на другой при изменении спроса; в случае простоя оборудования по причине ремонта, отсутствия сырья и комплектующих изделий) выполняется перенастройка/реконфигурация производственно-технологической цепочки/линии, связанная с перенесением потоков от одних звеньев к другим. При этом перенастройка ограничена количеством предусмотренных (возможных) схем переориентации материальных потоков. Однако, как будет показано далее, историческое развитие рынка потребителей требовало частой смены ассортимента продукции, наделенной особыми/отличительными свойствами, и, соответственно, выпуска разнообразной продукции малыми партиями/сериями. В этих условиях массовое поточное производство стало постепенно терять свои преимущества, и во второй половине XX века перед промышленностью возникла актуальная научно-техническая задача обеспечения гибкости производственных систем при условии сохранения ими преимуществ широкой механизации/автоматизации и высокого темпа изготовления изделий13.
13 Отличительными особенностями массового непрерывно-поточного производства являются: стабильность номенклатуры продукции, большая устойчивость технологии, высокий темп выпуска изделий, которые позволяют широко использовать преимущества станков-автоматов и автоматических линий. На этой основе уровень автоматизации производства на ряде предприятий удалось довести до 80—85% и добиться самой высокой выработки на одного рабочего. В настоящее время данный тип производства сохранился на предприятиях перерабатывающих отраслей с непрерывно-поточной технологией изготовления относительно простой и редко обновляемой (модифицируемой) по составу/свойствам продукции: нефтепереработка, металлургия (в том числе прокат сортового металла), химическая, электронная, пищевая и легкая промышленность, крупносерийное машиностроение (производство унифицированных деталей - крепежа, подшипников, шестерен и т.п.; нормализованного инструмента, электродов, калиброванного стрелкового оружия и боеприпасов).
19
Исследовательские и опытно-конструкторские работы по созданию гибких автоматизированных производств осуществлялись в период 1970-1990-х гг. в направлении повышения функциональной избыточности (степеней свободы) производственных систем на основе широкого использования многофункциональных станков и агрегатов с числовым программным управлением, промышленных роботовманипуляторов, транспортеров (робокаров) и автоматизированных складов, а также управляющих устройств на базе мини/микро-ЭВМ. В таких системах автоматизированы все операции. По программе выполняется загрузка заготовок в оборудование и выгрузка деталей из него. По заданной программе происходят обработка заготовок и изготовление изделий. Эти программы могут быть легко изменены или скорректированы. Автоматически происходит смена инструментов и вспомогательных материалов, а также их хранение, накопление и перемещение от одного оборудования к другому. Управление работой всей системы происходит централизованно от ЭВМ с помощью математического программного обеспечения. Автоматизированные производства быстро и без больших затрат времени и средств переналаживаются на выпуск разнообразной продукции, в пределах технических возможностей производственной системы, посредством замены программы технологического процесса, записанной в памяти ЭВМ. В своем законченном идеальном виде гибкие автоматизированные производства (ГАП) являются высшей, наиболее развитой формой автоматизации производственного процесса, которая позволяет совместить высокую производительность и универсальность (гибкость) в программноуправляемом/перенастраиваемом многофункциональном оборудовании, что открывает, по мнению их разработчиков, огромные возможности для интенсификации производства [10].
Тем не менее, создание полностью автоматизированного многопредметного (гибкого) поточного производства, отличающегося разнообразием выпускаемой продукции, осложняется необходимостью централизованной детальной инженерной подготовки, а также требует точной сквозной синхронизации технологических операций на потоке, которые должны выполняться различными станками и агрегатами в составе автоматической системы машин, как единый непрерывный процесс работы поточной линии. Исключение из автоматизированного производственного процесса живого труда и, соответственно, интеллектуального потенциала рабочих, способных не только быстро перенастраивать и ресинхронизировать технологический процесс, но и оперативно устранять периодически возникающие сбои в производственной системе, - обусловили высокую чувствительность автоматического процесса производства к неслаженной работе оборудования. Неполадки в работе отдельных агрегатов вызывают рассогласование работы и полную остановку гибкой автоматизированной линии (ГАЛ), что приводит к значительным потерям по всему циклу производства и снижает реальную эффективность его автоматизации [63]. Ко всему прочему, игнорирование творческой инициативы рабочих, постоянно занятых в производственном процессе и, соответственно, способных более эффективно осуществлять его технологическую доводку и развитие, существенно ограничили возможности адаптации таких производственных систем к меняющимся условиям рынка и создания на их основе новых конкурентных преимуществ. В итоге это делает процесс оперативной подготовки и ресинхронизации (адаптации) гибкого автоматизированного/ роботизированного поточного производства очень трудоемким/затратным и, соответственно, экономически
20