
2 курс допол. информ. для ИСУ / Монография Мизюн В.А._2012
.pdf
упрощает управление интегрированным производством, так как на интерактивном экране большого дисплея (таблоиде) размерами 3х5 м в наглядной форме (градации цвета, яркости, мерцание и т.п.) в полном объеме может быть представлена динамика производственного процесса [112, 139] 61.В целом подобного рода интеллектуальные технологии организационного управления создают организационно-экономические и технологические предпосылки для формирования новой модели конкурентоспособного гармоничного производства, в основе которой лежит процесс интеграции производственно-технологических цепочек создания ценностей на основе самоорганизации и оптимального регулирования деятельности (саморегулирования) производственных единиц в составе ассоциативного предприятия [65]. В этой связи, ключевым фактором конкурентоспособности и эффективности промышленного производства сегодня становится интеллектуальная поддержка процессов кооперации и координации экономических субъектов, осуществляющих совместную предметную деятельность в группе62. Динамическая когнитивная модель в этом случае представляет собой специально разработанное графическое отображение – планарную карту производственного процесса, которая делает его наглядным в режиме реального времени для всех участников и позволяет своевременно выявлять избыток/дефицит мощностей и излишние запасы (определять «узкие места» и оперативно балансировать ресурсы). Теоретической основой и инструментальным обеспечением данного подхода выступают интеллектуальные формы организации управления, методы и информационные технологии поддержки принятия решений, разрабатываемые с использованием логико-смысловых (семантических) моделей представления знаний и когнитивной компьютерной графики. Последние могут успешно применяться при создании интеллектуальных интерфейсов в виде динамических процессных моделей реализуемых в электронной среде ЭВМ, способных объединять различные элементы и уровни управления производственной системы в единую информационную среду принятия групповых управленческих решений по оптимизации производства в реальном масштабе времени.
61 По сути, такая человеко-машинная система представляет собой особого рода информационную (на начальном этапе видеоакустическую) среду, стимулирующую процесс интуитивного синтеза релевантной информации, посредством мульти и автодиалога на языке семантических образов и концептуальных моделей (Григорьев Э.П., Гусаков А.А. и др., 1986, 1993). В настоящее время данная область активно изучается инженерной психологией в рамках ее отдельного направления - когнитивной эргономики.
62 Осознание этого важного следствия, вытекающего из приведенных в данной работе теоретических и прикладных исследований в области неформального организационного проектирования, является весомой альтернативой непродуктивным подходам к реинжинирингу отечественных предприятий, в основе которых лежит «слепое копирование» передовых методов и специфических инструментов эффективной организации производства и управления зарубежных компаний.
101

Необходимо признать, что, теория и методология интеллектуализации управления сегодня находятся лишь на стадии концептуальной проработки, что открывает широкое поле деятельности для ученых и специалистов-практиков в области экономической кибернетики. Отчасти пробел в фундаментальных исследованиях и прикладных разработках в этом направлении науки можно объяснить существенной новизной интеллектуального подхода к решению известных организационно-экономических задач, отчасти – сложностью, непрозрачностью и разобщенностью процессов, протекающих в производственно-экономических системах. На начальном этапе прикладных исследований потребуется разработка специальных методов и технологий распознавания «образов» экономических явлений и процессов по их специфическим признакам (характеристикам, свойствам и особенностям их проявления). При этом архитектура информационных управляющих систем должна быть дополнена мощными сенсорными каналами, позволяющими воспринимать в режиме реального времени различные характеристики объектов и явлений экономики, а также интеллектуальным блоком сравнения различных совокупностей воспринимаемых характеристик с эталонными моделями по «точкам контроля», предварительно зарегистрированными и хранящимися в базе знаний информационной системы (фонд решенных задач/ФРЗ)63. Необходимо отметить, что для пополнения базы знаний (обучения) человеко-машинной системы в процессе решения сложных, плохо формализуемых и не формализуемых (неизвестных, плохо изученных) экономических задач, безусловно, потребуется участие человека-оператора для исследования наиболее близких к эталонам состояний наблюдаемого/управляемого объекта и принятия окончательного решения относительно их идентификации/классификации. В этой связи особая и наиболее важная роль принадлежит проблемам представления (структурирования) данных, создания и пополнения на их основе когнитивной
63 В условиях современного производства при реализации данной технологии должны широко использоваться методы непрерывного контроля над ходом технологического процесса, регулирования его динамики и качества. Усложнения оборудования и технологических систем, переход на робототехнику предъявляет особые требования к системе управления технологическим процессом. Нормальное функционирование автоматических линий и гибких переналаживаемых систем требует получения постоянной информации не только о контроле качества продукции на выходе системы, но и о работоспособности технологических систем, включающих оборудование, оснастку, инструмент, заготовку и исполнителя – рабочего, оператора или наладчика, поэтому объем (трудоемкость) контрольных операций в автоматическом и гибком автоматизированном производстве достигает 50% и более в общих трудовых затратах, связанных с изготовлением продукции. В связи с этим совершенствование существующих и создание новых (интегрированных) интеллектуальных систем управления технологическими процессами требует решения задачи автоматизации контроля и учета; использования новых методов и технологий контроля: акустических, магнитных, оптических, радиационных и др.; создания технологического оборудования, оснащенного кон- структивно-встроенными или сопряженными измерительными, решающими и исполнительными устройствами, обеспечивающими его функционирование в режиме автоматизированного и автоматического (при оснащении производства робототехническими комплексами) управления.
102

базы знаний интеллектуальной (человеко-машинной) системы. Их преодоление откроет новые возможности для автоматизации вполне конкретных экономических задач, например, таких как оперативное управление производством, оценка уровня организации и эффективности хозяйственной деятельности. Ниже на примерах позаказно-поточного/серийного и единичного машиностроительного производства, регулирование которого в современных рыночных условиях представляет собой методологически сложную и до конца нерешенную задачу, приводится практическая реализация декларированного подхода в виде интеллектуальных методов и информационных технологий управления сложными технологическими процессами64.
Синхронизация циклических операций на потоке
Динамика процесса поточного производства характеризуются индивидуальными тактами (асинхронностью) параллельных операций и степенью их синхронизации с общим ритмом потока. Именно эти параметры процесса функционирования поточной производственной системы оказывают существенное влияние на большинство экономических показателей работы предприятия, а именно: уровень производительности труда и ритмичность производства, его непрерывность, и, следовательно, размеры заделов и скорость оборачиваемости ресурсов, себестоимость продукции, степень загрузки оборудования, рентабельность и размер прибыли, получаемой предприятием от производства продукции. Безусловно, многое определяет качество проектирования поточной линии, однако с ростом масштабов и специализации (сложности) производства, нарушение синхронизации операций приобретает отдельное самостоятельное значение, и связано, прежде всего, с проблемой координации элементов производственной системы, обусловленной эффективностью информационных коммуникаций65.
64Его реализация предполагает исследование системотехнических принципов построения и закономерностей функционирования управляемых объектов/процессов с использованием аппарата теории систем и системного анализа, и последующем формировании информационной динамической модели управляемого объекта/процесса на основе универсальной системы показателей качества его организации и эффективности/ оптимальности функционирования (критериев исхода операций).
65Такие ситуации приводят к сбоям производственного процесса и характеризуются неравенством длительности операций и такта потока, вследствие чего возникают простои оборудования, при этом параметры производственной системы существенно отклоняются от нормативных значений, вплоть до потери управляемости и полной остановки. Данная проблема является естественным следствием разделения труда: узкой специализации производства, систем управления и техники. Углубление специализации, наряду с повышением производительности труда и качества выпускаемой продукции, в дальнейшем неизбежно порождает низкое качество (бессистемность) управляющих решений и, как следствие, потерю управляемости. Поэтому периодически на определенном этапе НТП, в противовес специализации, возникает потребность в объединении локальных систем в единые интегрированные системы с общими целями и результатами деятельности. Решение задач системной увязки узкоспециализированных подсистем посредством эффективных информационных коммуникаций на их стыках позволяет эффективно преодолевать разобщенность действий и, по сути, предопределяет дальнейшее поступательное развитие производственно-экономических отношений в
103

Способы регулирования ритма операций на потоке определяются его видом и степенью специализации. На однопредметных поточных линиях с конвейером ритм регулируется либо скоростью конвейера, либо сигнализацией. При применении внешнего транспорта (транспортера) ритм регулируется чаще всего рабочими. Такт в этих случаях - свободный. Решение об изменении интенсивности работ по операциям, на участках и в цехах принимается либо на рабочих местах исходя из ограниченной информации типа «пуск-останов» конвейера, либо специальным координационным подразделением (например, диспетчерской службой) на основании большого количества плохо структурированной информации обо всех операциях, которая поступает разновременно и постоянно меняется в режиме реального времени. В таких условиях время принятия решений по переводу локальных участков производственной системы из одного состояния в другое, и собственно время перехода, несоизмеримо с быстротой изменения оперативной ситуации, - общее время координации (синхронизации) велико, а достижение полной синхронизации и/или ее сохранение в течение длительного периода объективно невозможны. По этой причине возникают различные отклонения от нормального хода производственного процесса, которые могут усугубляться критическими ситуациями, связанными с неритмичностью поставок сырья, комплектующих материалов и/или отгрузок продукции, внеплановыми простоями технологического оборудования, авариями и т.д. В таких условиях диспетчер, производственный менеджмент и персонал предприятия, используя когнитивную/сетевую имитационную модель в качестве средства интеллектуальной поддержки принятия решений, способны управлять материальными/продуктовыми потоками таким образом, что, анализируя состояние производственной системы, товарно-сырьевого хозяйства, и координируя на этой основе работу отдельных технологических операций, участков и цехов, могут добиться устранения критических ситуаций, достичь стабилизации процесса и хорошего уровня выпуска продукции.
Общеизвестно, что пропорциональность и равномерность осуществления отдельных стадий/операций технологического процесса являются необходимыми условиями эффективности промышленного производства. Соответственно данные организационные характеристики могут использоваться в качестве «контрольных точек», а способы их оценки и наглядного сравнения при помощи известных количественных измерителей должны быть приняты за методологическую основу при разработке динамической имитационной модели процесса производства. Известный в
обществе, что собственно и является основой системного (кибернетического) подхода в управлении экономикой.
104
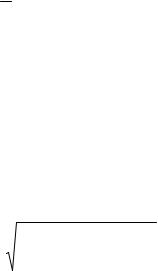
организационной науке и практике алгоритмический аппарат синхронизации работы различных звеньев технологической цепи основан на согласовании локальных ритмов функционирования производственных звеньев с ритмом конечного, замыкающего по технологической цепочке создания ценности звена. Отклонение ритма выполнения локальных процессов от среднего ритма на протяжении выбранного отрезка времени может служить количественным показателем, характеризующим степень синхронизации бизнес-процессов в интегрированной производственной системе [110, 134]. Положительное или отрицательное отклонение ритма локального звена от средней величины определяется соответствующим коэффициентом синхронизации (вариации ритмов), а именно:
Kс = |
|
σ |
(2.1.) |
||
|
|
|
|||
Rt |
|||||
|
|
|
где Кс – коэффициент синхронизации потока; σ – среднеквадратическое отклонение ритмов отдельных производственных звеньев технологической сети от среднего ритма
интегрированного производства; Rt – средний ритм производства, наблюдаемый в период t=1.
При этом:
|
|
1 |
T |
|
|
|
t = |
Rt |
|
||
R |
(2.2) |
||||
T |
|||||
|
|
i−1 |
|
где Т – число наблюдаемых/анализируемых периодов; Rt – ритм конечного звена технологической цепочки производства, наблюдаемый в период tm.
|
1 |
Т |
|
|
|
|
|
σ = |
t−1 |
( |
|
− R )2 |
|
||
R |
(2.3) |
||||||
(Т − 1) |
|||||||
|
|
t t |
|
Коэффициент синхронизации (вариации ритмов) показывает относительное отклонение частного ритма от среднего ритма конечного звена: чем ближе данный показатель к нулю (Кс→0), тем выше степень синхронизации бизнес-процесса. Однако использование аналитического подхода для координации работы звеньев технологической цепи интегрированного производства затруднено отсутствием наглядности вычисляемых с его помощью сравнительных характеристик. По данной причине на практике организация регулятивного управления интегрированным производством с целью достижения необходимой синхронизации многомерной технологической цепочки создания ценности требует создания локального механизма, с присущими ему организационно-экономическими формами и методами (моделями) синхронизации/гармонизации интегрированного производства. Руководствуясь результатами проведенного нами исследования
105
можно заключить, что в качестве основных структурных элементов локального механизма должны быть приняты саморегулируемые производственные участки и их синергетическое взаимодействие в рамках установленных организационно-экономических отношений.
Синергетическое взаимодействие может быть обеспечено посредством наглядного экспонирования единой визуальной количественной характеристики синхронности интегрированного производства и некоторым правилом/технологическим приемом вынесения индивидуальных и коллективных решений относительно согласования/выравнивания локальных и общесистемного ритмов производства. С этой целью нами были сформулированы методологические принципы создания интеллектуального инструментария регулятивного управления, опубликованные ранее в работах [77, 79, 80]. В соответствии с ними на первоначальном этапе разрабатывается сетевая имитационная модель, которая эффективно преодолевает известные трудности традиционного аналитического подхода и позволяет осуществить пространственно-временное сопоставление/представление основных элементов и ресурсов производственного процесса в машинной среде, с последующей количественной оценкой оптимальности его функционирования. При моделировании адаптивного интегрированного поточного производства эта задача облегчается тем, что топология материальных потоков/производственнотехнологических сетей практически полностью совпадает с компоновочной структурой производимых продуктов, которая определяет поэлементную последовательность их изготовления (см.: ERP-технологии планирования). Однако, визуальное представление в виде двумерной (однослойной) динамической сети процесса многопредметного производства сложных технических изделий, состоящих из сотен или даже десятков тысяч деталей, - является трудно осуществимой на практике задачей, поскольку в этом случае необходимо оперировать огромным количеством данных относительно структуры и состояния/динамики производства. При этом сведение оперативной информации о производственном процессе на экран ЭВМ/информационный таблоид ограниченного размера, приведет к необходимости обработки сознанием людей-операторов интегрированной производственной системы большого массива сигнально-символьной информации в условиях ограниченного времени.
С целью устранения данного недостатка, на втором этапе проектирования локального механизма управления, выполняется адаптация/аппроксимация сетевой модели производства (дерева структуры продукта) для построения единой информационной среды оперативного управления процессом интегрированного производства путем ее концептуального
106
обобщения/генерализации в семантические схемы пространственно-временных событий (образы действия). В практическом плане эта задача реализуется с помощью методов интерактивного (когнитивного) моделирования посредством формирования второго уровня/слоя интегрированной модели/системы распределенного управления - планарных процессных карт ресурсных потоков, адекватно отражающих знания производственного персонала о пространственно-временной структуре и динамике функционирования процесса производства в виде концептуальной семантической схемы/образа. Интерактивная планарная карта производственно-технологического процесса формируется в виде произвольного графа и должна вызывать резонансную активацию нейронных ансамблей в сознании операторов человеко-машинной системы (когерентных семантическим схемам/образам), выполняя тем самым функцию метакогнитивной координации активных элементов производственной системы [141]. Феномен и информационный механизм резонансной интрапсихической координации группового поведения операторов человеко-машинной системы изучен и подробно описан нами в работе [77].
При построении интегрированной (слоистой/многоуровневой) когнитивной/сетевой динамической имитационной модели, прототип которой представлен на рис. 2.10/табл. 2.1, используются следующие понятия и определения: шаг моделирования - интервал времени, через который вычисляются значения всех параметров динамической имитационной модели (как правило, за шаг моделирования принимается такт, задаваемый работой конечного звена цепи/конвейера); и объем незавершенного производства/фактические объемы произведенной продукции – измеритель/параметр, количественно характеризующий накопление/прохождение материального потока по этапам (например, в сравнении с запланированными объемами, получаемыми на основе расчета балансовых уравнений). В поточном/серийном производстве к таким измерителям (планово-учетным единицам) относятся детали, узлы, агрегаты и машино-комплекты. Сопоставление их количества на разных производственных участках способно наглядно и точно отражать сбалансированность высокотехнологичного производства по объему/интенсивности осуществления работ по изготовлению/обработке деталей и быстро выявлять диспропорции (избыток/дефицит) ресурсов и мощностей, возникающие из-за сбоев в работе интегрированной производственной системы, которые подлежат немедленному устранению посредством регулирования интенсивности/очередности выполнения деталеопераций.
107

Таблица 2.1
СИНХРОНИЗАЦИЯ ИНТЕГРИРОВАННОГОПРОИЗВОДСТВАПРОДУКТАА
Элемент |
Нормативное количество |
Фактичес |
Отклоне |
|
|
|
ние |
||
(шт.) |
Узел |
Изделие |
кое количество |
|
|
|
|
|
(-/+) |
F/2 |
4 |
8 |
6 |
-2 |
|
|
|
|
0 |
G/4 |
8 |
16 |
16 |
|
|
|
|
|
0 |
H/3 |
6 |
12 |
12 |
|
|
|
|
|
-1 |
C/2 |
- |
4 |
3 |
|
|
|
|
|
+15 |
I/5 |
15 |
30 |
45 |
|
|
|
|
|
0 |
J/3 |
9 |
18 |
18 |
|
|
|
|
|
0 |
K/3 |
3 |
6 |
6 |
|
|
|
|
|
0 |
D/3 |
- |
6 |
3 |
|
|
|
|
|
-1 |
B/2 |
- |
2 |
2 |
|
|
|
|
|
0 |
L/3 |
9 |
9 |
9 |
|
|
|
|
|
0 |
M/2 |
6 |
6 |
6 |
|
|
|
|
|
-2 |
N/4 |
12 |
12 |
10 |
|
|
|
|
|
-1 |
E/3 |
- |
3 |
2 |
|
|
|
|
|
-1 |
A |
- |
1 |
0 |
|
|
|
|
|
|
Дерево структуры продукта A
F/2 |
|
|
H(12/12) |
I(30/45) |
A (1/0) |
|
|
|
|
||||
G/4 |
C/2 |
t4 |
|
|||
|
|
|
|
|||
H/3 |
|
|
G(16/16) |
D(3/3) |
|
J(18/18) |
|
|
B/2 |
C(4/3) |
|
|
|
I/5 |
t2 |
B(2/1) |
|
|
||
|
|
|
||||
J/3 |
D/3 |
t5 |
|
A |
|
|
|
|
|
|
|||
K/1 |
|
A |
F(8/6) |
E(3/2) |
|
K(6/6) |
|
|
|
|
|
||
L/3 |
t3 |
|
|
|
|
|
M/1 |
E/3 |
|
L(9/9) |
|
N(12/10) |
|
N/4 |
t1 = t2 = t3 |
|
M(6/6) |
|
|
|
|
|
|
|
|
Рис. 2.10. Интерактивная процессная карта/гармонограмма поточного производства продукта A66.
66 Данный метод и разработанную на его основе информационную технологию можно использовать для регулирования технологических цепочек без исключения всех часто повторяющихся (циклических) операций по изготовлению, поставке и сборке изделий, которые характерны для поточного и серийного типов наукоемкого машиностроительного производства.
108

Вкаждом блоке планарной карты в реальном режиме времени отражается количество изготовленных деталей/машино-комплектов. Оно автоматически сравнивается с аналогичными фактическими показателями на смежных технологических участках (в сопряженных областях) и/или рассчитанными по балансовым уравнениям исходя из заданного такта главного конвейера. Отклонение в ту или иную сторону отмечается на дисплее голографического экрана тональностью цвета. Это позволяет диспетчеру и ЛПР «на местах» выявлять отклонения и одновременно/параллельно, в режиме групповой динамики, принимать решения об изменении производительности рабочих мест (участков, цехов и т.д.). Загрузка звеньев ценностной цепи и/или производственных участков (размеры партий/интенсивность работ) определяются в разрезе различных одновременно производимых видов продукции с таким расчетом, чтобы не допускалось нарушение условия пропорциональности производства деталей и узлов в увязке с тактом работы финишных сборочных линий [79]. В итоге, используя данный методологический подход к организации оперативного управления производственными процессами в интегрированных ценностных цепях, можно добиться глобальной оптимизации работы (оптимальности функционирования) интегрированного предприятия, которая требует сквозной синхронизации/выравнивания параллельных технологических операций. При этом координатор или диспетчер, а при необходимости – любой активный элемент интегрированной производственной системы, имеет возможность получить детальную информацию относительно работы и состояния каждого элемента системы. Однако для этого потребуется переключение режима работы интерактивного информационного экрана/таблоида на «меньший масштаб», а также большее модельное время67.
Всоответствии с представленным инвариантом мультиагентной модели распределенной параллельной обработки релевантной информации,
оперативное управление адаптивным интегрированным производством
67 Традиционные способы регулирования ритма операций на потоке в вертикально-интегрированном производстве определяются его видом и степенью специализации. Так, например, на однопредметных поточных линиях автосборочных предприятий с конвейером ритм регулируется либо скоростью конвейера, либо сигнализацией. При применении внешнего транспорта (транспортера) ритм регулируется чаще всего рабочими. Такт в этих случаях - свободный. Решение об изменении интенсивности работ по операциям, на участках и в цехах принимается либо на рабочих местах исходя из ограниченной информации типа «пускостанов» конвейера, либо специальным координационным подразделением (например, диспетчерской службой) на основании большого количества плохо структурированной информации обо всех операциях, которая поступает разновременно и постоянно меняется в режиме реального времени. В таких условиях время принятия решений по переводу локальных участков производственной системы из одного состояния в другое, и собственно время перехода, несоизмеримо с быстротой изменения оперативной ситуации, - общее время координации (синхронизации) велико, а достижение полной синхронизации и/или ее сохранение в течение длительного периода традиционными способами объективно невозможны.
109
осуществляется не на основе перспективного производственного плана, а на базе дискретного потока данных относительно фактически поступающих заказов на поставку продукции, производственных заделов, состояния и текущей загрузки оборудования, сроков поставок материальных ресурсов, а также «перекрестного» воздействия множества других факторов и требований, которые в системе задаются автоматически по мере их появления. Процесс определения размеров партий, продуктовой структуры и сроков выпуска продукции приобретает динамичный характер и увязывается с текущим ритмом всех технологических операций. Входными сигналами представленной интерактивной модели процесса производства являются данные о фактическом поступлении заказов на продукцию и количестве изделий, изготовленных на различных технологических переходах, а выходными параметрами, регулирующими работу производственных участков, - данные о пропорциях (диспропорциях) в производстве деталей (узлов, работ), обеспечении необходимыми ресурсами и комплектующими, которые складываются в реальном режиме времени.
Регулирование непоточного производства
Необходимо отметить, что при решении задач регулятивного управления горизонтально-интегрированным непоточным и/или опытноэкспериментальным (единичным), производством сложных технических изделий не представляется возможным для гармонизации/динамического балансирования производственного процесса использовать как хорошо зарекомендовавшие себя традиционные способы и алгоритмические модели, так и представленный выше инновационный инструментарий синхронизации/выравнивания интегрированного поточного производства, основными планово-учетными единицами которого являются предметы труда (типовые детали, узлы и машино-комплекты) [111, 124, 145]. Уникальность конструкции единичных изделий обусловливает функциональную организацию производственной системы с высоким коэффициентом закрепления операций за технологическим оборудованием, а также наличие большого количества нестандартных деталей и узлов, процесс изготовления которых носит нециклический (разовый) характер. Это предопределяет отказ от штучных измерителей динамики процесса производства и переход к характеристикам, основанным на сравнительной количественной оценке трудоемкости/длительности выполнения заказа по видам работ/операций (Т3/ТЦЗ) и располагаемого фонда рабочего времени (ФП), предполагающей расчет трудоемкости отдельных работ по заказу и определение наличия потребного числа рабочих мест (СРМ):
110