
Экзаемн_сварка
.pdf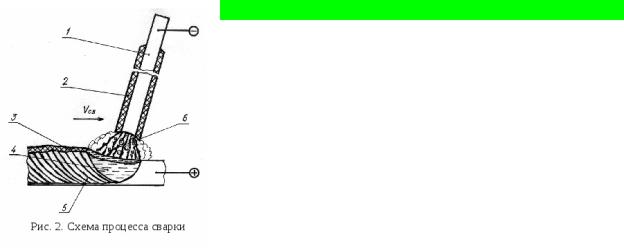
24.Ручная дуговая сварка покрытыми электродами
Электрод для ручной дуговой сварки (см. рис. 2) представляет собой металлический стержень 1 длиной 300– 450 мм, на поверхность которого нанесено покрытие 2. В процессе сварки дуга 6 горит между стержнем электрода и основным металлом. Стержень электрода плавится и вместе с металлом расплавленных кромок свариваемых заготовок образует металлическую ванну 4. Плавится также и покрытие электрода, образуя защитную шлаковую ванну на поверхности расплавленного металла, что предохраняет его от вредного воздействия атмосферы. Совокупность металлической и шлаковой ванн называют сварочной ванной. По мере движения дуги металлическая ванна затвердевает, и
формируется сварной шов 5. Жидкий шлак после остывания образует твердую шлаковую корку 3. Стержни электродов изготовлены из сварочной проволоки. Стандартом предусмотрено 77 марок стальной проволоки диаметром 0,2–12 мм, которые делятся на три группы: низкоуглеродистую (Св-08А и др.), легированную (Св-10Х5М и др.) и высоколегированную (Св-06Х19Н10МЗТ и др.). В марках проволоки «Св» означает «сварочная», первые две цифры – содержание углерода в сотых долях процента, последующие буквы и цифры – содержание легирующих элементов в соответствии с маркировкой легированных сталей; последняя буква «А» – пониженное содержание серы и фосфора.
Покрытия электродов предназначе-ны для обеспечения стабильного горения дуги, защиты расплавленного металла от воздействия атмосферы и формирования металла шва с заданным составом и свойствами. Равномерное горение дуги достигается за счет введения в покрытие стабилизирующих компонентов – легкоионизирующихся веществ (соединений натрия, калия, кальция в виде мела, мрамора и т. п.). Газовая защита сварочной ванны выполняется введением в покрытия газообразующих веществ: целлюлозы, крахмала и др. Для обеспечения шлаковой защиты в покрытия вводят шлакообразующие элементы – рутиловый концентрат, полевой шпат, марганцевую руду. Для удаления кислорода из сварочной ванны в покрытия вводят раскисляющие компоненты – сплавы железа с активными металлами, например, ферромарганец. Входящий в его состав марганец реагирует с растворенным в ванне кислородом, а также с кислородом оксидов и восстанавливает чистое железо, сам марганец при этом окисляется и уходит в шлак. После застывания шлак образует на поверхности шва твердую стекловидную корку. При удалении шлаковой корки ударами молота следует беречь глаза от разлетающихся стекловидных частичек шлака, закрываясь щитком или маской. В покрытия также вводят легирующие элементы для легирования металла шва. Кроме того, в покрытия добавляют пластификаторы и связующие, придающие покрытию прочность и
хорошее |
сцепление |
со |
стержнем. |
Различают следующие виды покрытий: |
|
|
1) кислые (основные компоненты – MnO и SiO2), обладают хорошими технологическими
свойствами, но при сварке выделяют токсичные соединения марганца, поэтому их применение сокращается;
2) рутиловые (основной компонент – TiO2), обладают высокими сварочно-технологическими свойствами;
3)основные (содержат CaCO3 и MgCO3), технологические свойства ограничены;
4)целлюлозные (основные компоненты – целлюлоза и другие органические вещества), создают хорошую газовую защиту и образуют малое количество шлака, например электроды ОМА2.
Стандартное условное обозначение электродов содержит основную информацию о сварочных электродах.
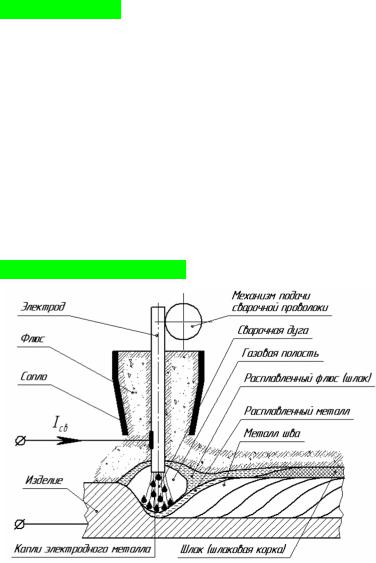
25. Газовая сварка
Порядок поджига: 1. на одну четверть открыв кислород. 2. на один оборот открываем горючий газ. Пламя состоит из 3 видов: ядро, востановительная зона(3100-3200 С) и факел(2000-2500 С). Нормальное пламя используют для сварки. На углераживающем пламени сваривают чугун, на окислительном пламени для сварки латуни.
К параметрам режима газовой сварки относят: тип пламени, мощьность при газовой сварке, номер горелки, давление редуктора, диаметр присадочной проволоки, величина поперечных колебаний, угол наклона горелки, скорость сварки.
Достоинства: 1. не требует снабжение электроэнергии, 2. возможность сварки тонкого металла, 3. возможность сварки в трудодаступных местах и во всех пространственных положениях.
Недостатки: 1. низкая производительность, 2. значительная зона термического влияния, 3. значительная деформация, 4. повышенная взрывоопасность, 5. обратный удар может появиться.
26. Сварка под слоем флюса
Сварку под слоем флюса производят голой электродной проволокой, которую подают в зону горения дуги специаьным механизмом, называемым голтовкой автомата. Токопровод к проволоке осуществляется через мундштук, изготовляемый из меди. На качество сварного соединения, выполненного под слоем флюса, влияют отношение ширины однопроходного шва к глубине провара.
Основными параметрами режима автоматической и полуавтоматической сварки под флюсом являются сварочный ток и
диаметр электродной проволоки, напряжение на дуге и скорость перемещения дуги. В зависимости от режима и технологических факторов будет меняется глубина провара, ширина шва, высота выпуклости и доя участия основного метала в металле шва. Так же на форму качество шва влияет зазор между деталями.
Достоинства способа:
Повышенная производительность;
Минимальные потери электродного металла (не более 2%);
Отсутствие брызг;
Максимально надёжная защита зоны сварки;
Минимальная чувствительность к образованию оксидов;
Мелкочешуйчатая поверхность металла шва в связи с высокой стабильностью процесса горения дуги;
Не требуется защитных приспособлений от светового излучения, поскольку дуга горит под слоем флюса;
Низкая скорость охлаждения металла обеспечивает высокие показатели механических свойств металла шва;
Малые затраты на подготовку кадров;
Отсутствует влияния субъективного фактора.
Недостатки способа:
Трудозатраты с производством, хранением и подготовкой сварочных флюсов;
Трудности корректировки положения дуги относительно кромок свариваемого изделия;

Неблагоприятное воздействие на оператора;
Нет возможности выполнять сварку во всех пространственных положениях без специального оборудования.
Области применения:
Сварка в цеховых и монтажных условиях
Сварка металлов от 1,5 до 150 мм и более;
Сварка всех металлов и сплавов, разнородных металлов.
27. Классификация припоев
Припои имеют более низкую температуру, чем метал который паяется. Пайкаполученные соединения с межатомными связями путем нагрева соединен. Материаллов до температуры ниже температуры плавления, последующим смачивании материала расплавленного припоем. Затекание припоя в зазор и его кристализация.
Различают припои оловянные, цинковые, алюминиевые, медные, кадмиевые, никелевые и т. п. По технологическим особенностям — металлокерамические, самофлюсующиеся и др.По специальным свойствам припои подразделяют на теплостойкие, жаропрочные, кислотостойкие. Их классифицируют по температуре плавления: особолегкоплавкие, легкоплавкие, средиеплавкие, высокоплавкие и тугоплавкие.
Особолегкоплавкие припои — это сплавы, темпераратура плавления которых ниже 150°С. В таких сплавах содержатся олово, цинк, свинец, ртуть, кадмий, индий, галлий, висмут.
Легкоплавкие — сплавы меди и магния на основе алюминия, верхняя температурная граница плавления не более 450°С.
Среднеплавкие сплавы —на основе алюминия, магния, серебра, меди и некоторые титановые, никелевые и палладиевые. Температура плавления до 1100°С. Высокоплавкие — на основе молибдена, титана. Температура плавления до 1850°С. К тугоплавким относят припои, температура плавления которых выше 1850°С.
28. Свойства защитных газов для дуговой сварки
http://build.novosibdom.ru/node/332
Cвойства защитных газов оказывают большое влияние на технологические свойства дуги и форму швов. Например, по сравнению с аргоном гелий имеет более высокий потенциал ионизации и большую теплопроводность при температурах плазмы. Поэтому дуга в гелии более "мягкая". При равных условиях дуга в гелии имеет более высокое напряжение, а образующийся шов имеет меньшую глубину проплавления и большую ширину. Поэтому гелий целесообразно использовать при сварке тонколистового металла. Кроме того, он легче воздуха и аргона, что требует для хорошей защиты зоны сварки повышенного его расхода (1,5-3 раза). Углекислый газ по влиянию на форму шва занимает промежуточное положение. Широкий диапазон используемых защитных газов, обладающих значительно различающимися теплофизическими свойствами, обусловливает большие технологические возможности этого способа как в отношении свариваемых металлов (практически всех), так и их толщин (от 0,1 мм до десятков миллиметров). Сварку можно выполнять, используя также неплавящийся (угольный, вольфрамовый) или плавящийся электрод.
По сравнению с другими способами сварка в защитных газах обладает рядом преимуществ: нет необходимости применять флюсы или покрытия, следовательно, не требуется очищать швы от шлака;незначительное взаимодействие металла шва с кислородом и азотом воздуха; высокое качество сварных соединений на разнообразных металлах и сплавах различной толщины; возможность сварки в различных пространственных положениях; возможность визуального наблюдения за образованием шва, что особенно важно при полуавтоматической сварке; отсутствие операций по засыпке и уборке флюса и удалению шлака; высокая производительность и легкость механизации и автоматизации; низкая стоимость при использовании активных защитных газов. К недостаткам способа по сравнению со сваркой под флюсом относится необходимость применения защитных мер против световой и тепловой радиации дуги.

При сварке плавящимся электродом дуга горит между изделием и расплавляемой сварочной проволокой, подаваемой в зону сварки. По сварке неплавящимся электродом (вольфрамовые прутки) сварочная дуга может быть прямого или косвенного действия. Разновидностью сварочной дуги косвенного действия может быть дуга, горящая между вольфрамом, и беспрерывно подаваемой в зону дуги сварочной проволокой.
Сварка неплавящимся электродом. Условием стабильного горения дуги при дуговой сварке в защитной среде инертных газов на переменном токе является регулярное восстановление разряда при смене полярности. Потенциал возбуждения и ионизации инертных газов аргона и гелия выше, чем у кислорода, азота и паров металла, поэтому для возбуждения дуги переменного тока требуется источник питания с повышенным напряжением холостого хода. Сварочная дуга в среде инертных газов (аргона или гелия) отличается высокой стабильностью и для ее поддержания требуется небольшое напряжение. Высокая подвижность электронов обеспечивает достаточное возбуждение и ионизацию нейтральных атомов при столкновении с ними электронов.
29. Деформации и напряжения при сварке, методы снижения
При сварке деталей из термопластичных материалов под действием неравномерного нагрева основного материала и усадки материала шва, а также в результате структурных изменений в зоне термического влияния возникают внутренние напряжения, вызывающие:
продольные и поперечные деформации (изменяются длина и ширина элементов);
искривление, выпучивание и скручивание элементов, трещины в материале шва; в отдельных случаях снижение прочности изделия.
В результате нарушения технологии сварки изделие может деформироваться и покоробиться, что не допускается технологическими условиями. Напряжения, возникающие в процессе сварки, в некоторых случаях приводят к трудно выявляемому трещинообразованию, приводящему к снижению надежности сварной конструкции. Изучение причин возникновения сварочных напряжений и деформаций и разработка методики их расчета — трудная задача в сварочной технике. Нет достаточно надежных и простых методов расчета напряжений и деформаций в свариваемой конструкции в зависимости от метода и режима сварки и других технологических факторов.
Методы их снижения Мероприятия по борьбе с деформациями и короблениями, осуществляемые на
производстве, подразделяют на конструктивные и технологические. Первые включают вопросы рациональной конструкции изделия. Конструктор, проектирующий новую конструкцию из термопластического материала, должен учитывать не только рациональность его формы и удобство эксплуатации, но и технологию изготовления и возможность сварки без коробления. При этом основными мероприятиями являются:
уменьшение числа сварных соединений и швов;
обеспечение симметричного расположения швов для создания при сварке уравновешенных деформаций;
применение сборочно-сварочных приспособлений;
размещение швов вне зон максимальных напряжений.
К технологическим мероприятиям относятся:
предотвращение обратных деформаций перед сваркой;
разработка рациональной технологии сварки.
Мероприятия по уменьшению коробления могут оказывать разное воздействие на величину внутренних напряжений, например, жесткое закрепление деталей уменьшает коробление, но увеличивает внутренние напряжения и т. д. При осуществлении того или

иного мероприятия необходимо учитывать конфигурацию изделия, механические и пластические свойства свариваемого материала, возможность возникновения трещин.
Обратные и остаточные деформации Для предотвращения обратных деформаций необходимо опытным путем определить
величину и направление ожидаемых деформаций, вызываемых сваркой данного изделия (рис. 37), затем свариваемые элементы или собранную конструкцию до сварки изгибают в сторону, противоположную наибольшим напряжениям усадки.
Обратный изгиб свариваемых элементов выполняют без приложения дополнительного усилия или с усилием в пределах упругих деформаций. Техника выполнения этих изгибов различна. Чаще применяют упругий изгиб в жестких сборочно-сварочных зажимных приспособлениях различных конструкций, в которых свариваемое изделие находится до окончания процесса сварки и полного охлаждения.
Описываемый способ предотвращения обратных деформаций нашел широкое распространение.
Жесткое закрепление снижает остаточные деформации и уменьшает коробление свариваемых деталей. Полностью ликвидировать деформации нельзя, так как образующиеся при сварке в сварном соединении пластические и упругие деформации обнаруживаются после снятия закреплений. Как правило, эти деформации значительно меньше, чем деформации при сварке элементов конструкций, свободных от закрепления. Жесткое закрепление можно применять при сварке любого термопластического материала, а также листов с V-образной разделкой кромок во избежание их вспучивания.
Для предотвращения вспучивания и расхождения состыкованных кромок листов применяют прижимы, находящиеся в непосредственной близости (10—20 мм) от сварного шва.
Деформации при жестком закреплении, а также свободном положении свариваемых элементов можно уменьшить охлаждением шва водой сразу же после сварки. При закалке сварного шва и околошовной зоны образуются большие концентраторы напряжений, которые снижают прочность сварного соединения до 20% по сравнению с прочностью не термо обработанных швов.
30.Формы и конструктивные параметры подготовки свариваемых кромок при дуговых способах сварки
Косновным операциям подготовки металла под сварку относятся: правка и очистка проката; механическая или термическая резка при заготовке деталей и полуфабрикатов; обработка кромок, подлежащих сварке.
Обработка кромок стыковых соединений заключается в отбортовке их при толщине металла до 4 мм или разделке кромок для создания скоса и притупления при большей толщине металла.

При дуговой сварке повышенные требования предъявляются к чистоте кромок и поверхности прилежащих к ним зон свариваемых деталей.
Вцелях избежания образования в швах пор, шлаковых и других включений торцевые поверхности кромок и прилегающие к ним зоны металла шириной 25—30 мм подлежат очистке от ржавчины, краски, масляных и других загрязнений. Очистку выполняют металлическими щетками, абразивными материалами или инструментом, а также газопламенной обработкой.
При сборке конструкций, помимо применения инвентарных и других сборочных приспособлений, кондукторов и кантователей, для фиксации взаимного расположения элементов конструкций и детален часто используют прихватки (короткие швы), осуществляемые ручной дуговой сваркой.
Размеры сечений прихваток не должны превышать 1/3 основных швов (при толщине свариваемого металла более 5 мм). Поверхность прихваток следует зачищать от шлака и загрязнений. При выявлении дефектов их удаляют абразивным инструментом и швы выполняют вновь.
Взависимости от формы и взаимного расположения свариваемых кромок, размеров поперечного сечения шва и положения его в пространстве при ручной дуговой сварке осуществляют простые или сложные траектории движения рабочим (с горящей дугой) концом электрода, которые позволяют: управлять тепловым потоком, охлаждая металл при отводе дуги и увеличивая тепловое воздействие при прекращении движения электрода; выполнять однопроходные швы различной формы и размеров сечения; уменьшать возможность натека или прожога металла; предотвращать стекание металла при наклонном или отвесном положении сварочной ванны.
При перемещении конца электрода вдоль линии соединения без колебательных поперечных движений ширина валика шва не превышает 0,8—1,5 диаметра электрода. Поперечные движения конца электрода обеспечивают получение валика увеличенной ширины.
31.Основные дефекты сварных соединений, причины формирования
Трещинадефект в виде разрыва металла. Поперечная трещина - дефект поперёк оси шва.
Радиальная трещина - несколько трещин различного направления.
Причины появления трещин: нарушение технологии сварки, несоответствие применяемых материалов, склонность свариваемого металла к закалке, высокая склонность охлаждения металла, сварка при низкой температуре.
Свищи - дефект в виде воронкообразного углубления в сварном шве.
Причины появления дефектаналичие ржавчины, масла, грязи и как результат обильное выделение из металла сварочной ванны газов в момент его затвердения.
Порыдефект в виде полости округлой формы, заполненной газом.
Причины появлениясварка непросушенными электродами, наличие ржавчины, масла, грязи, завышение скорости сварки.
^ Непровар кромокдефект в виде наплавления в следствии неполного расплавления кромок. Причины непровара - заниженный зазор между свариваемыми кромками, завышенное притупление кромок, малый угол скоса кромок, завышенная скорость сварки, смещение
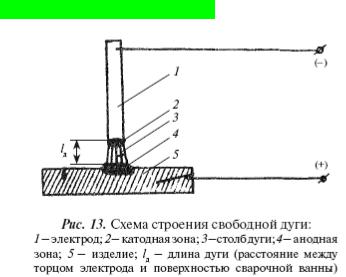
электрода на одну из пластин, малая сила сварочного тока, неточное направление ведения электрода.
Прожогдефект в виде сквозного отверстия в шве, как результат вытекания части металла сварочной ванны.
Причины прожогазавышенный сварочный ток, малое притупление кромок, малая скорость сварки.
^Шлаковые включениядефект в виде вкрапления шлака в сварном шве. Причины - завышение скорости сварки, плохая подготовка кромок, большая длина сварочной дуги.
^Брызги электродного металла - дефект в виде капель на поверхности сварного соединения. Причинызавышенный сварочный ток, большая длинна сварочной дуги, не качественные электроды.
Подрездефект в виде углубления по линии сплавления сварного шва с основным металлом. Причины появления:
низкая квалификация сварщика, завышение сварочной дуги, завышенная скорость сварки. Дефекты формирования сварного шва:
наплывдефект в виде натекания металла на поверхность углублении между валиками, превышение выпуклости сварного шва - избыток наплавленного металла на лицевой стороне углового шва, неравномерная высота шва - большая неровность наружной поверхности, вогнутость корня
шва - дефект в виде углубления на поверхности обратной стороны шва, смещение кромок -неправильное положение их относительно друг друга. Причины появления - неправильная сборка, некачественная прихватка, их малое количество.
32.Основные операции технологического процесса склеивания
33.Плюсы и минусы сварки в среде защитных газов неплавящемся электродом
34.Рациональные конструкции и области применения паянных соединений
35.Органические клеи: состав, достоинства и недостатки
36.Сущность электро шлаковой сварки
37.Дуга: строение и свойства
Дуга – устойчивый вид разряда существующий от 10 до 1000 А. Сварочная дуга – длительный разряд электрического тока в газовой среде между находящимися под напряжением твердым или жидким веществами и источником нагрева (концентрированным)
Для образования и поддержания горения дуги необходимо иметь в пространстве между электродами электрически заряженные частицы (положительные и отрицательные ионы и электроны). Ионы в газовом
промежутке между электродами образуются в результате потери или присоединения к атомам электронов, а электроны испускаются сильно нагретым катодом.
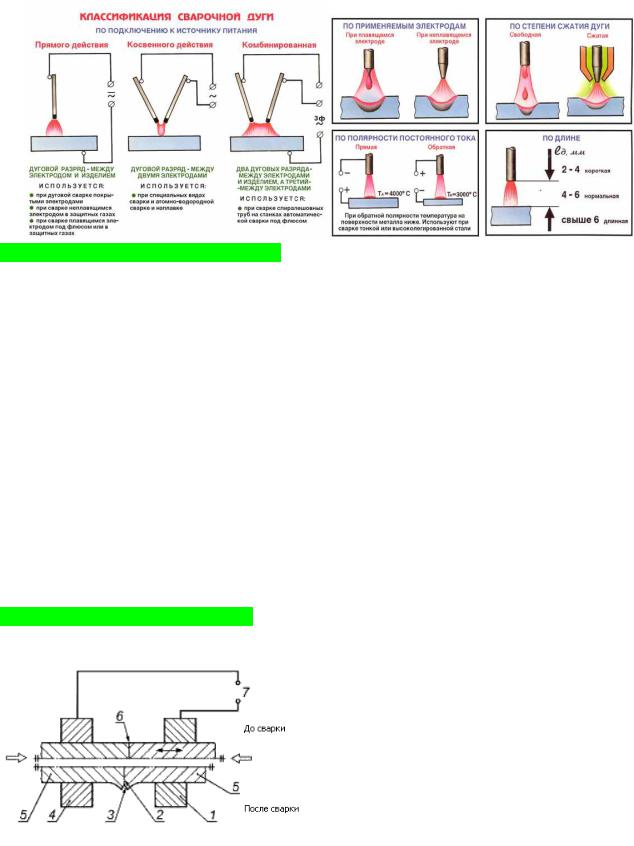
Элементы, обладающие малыми потенциалами ионизации и возбуждения, вводят в состав электродных покрытий, так как они способствуют устойчивому горению дуги. Это первое условие устойчивого горения дуги. Второе условие – напряжение холостого хода источника питания должно быть больше напряжения дуги. Третье условие горение дуги – поддержание высокой температуря нагрева катода. Эта температура зависит от материала катода, состава газового промежутка между электродами, диаметра электрода и температуры окружающей среды.
38. Электроды при контактной сварке
Как правило, для получения отличного результата при контактной сварке, используют неплавящиеся электроды и стержни. К ним можно отнести вольфрамовые электроды, торированные, лантарированные. Это является особенностью электродов для контактной сварки.
Для точечной контактной сварки наиболее распространены прямые электроды. Их изготовляют из прутка диаметром 12-40 мм (ГОСТ 14111—90). Рабочая поверхность электродов может быть плоской или сферической. Для сварки деталей сложной конструкции используются электроды со смещенной рабочей поверхностью (сапожковые). Электрод крепится хвостовиком, который имеет конусность 1:10 или 1:5. Иногда электроды имеют цилиндрические поверхности крепления. В этом случае их зажимают специальными зажимами или крепят конусными резьбовыми соединениями. Электроды со сменной рабочей частью можно крепить на конусе, накидной гайкой, припаивать или запрессовывать.
Для рельефной контактной сварки применяют электроды, конструкция которых зависит от типа соединений и формы изделия. Размер их рабочей поверхности обычно не имеет существенного значения для концентрации тока, так как форма и площадь контакта определяются формой свариваемых поверхностей в месте соприкосновения. Различают электроды для одно- и многорельефной сварки, для сварки кольцевых рельефов и Т-образных соединений.
39. Стыковая сварка оплавлением
Стыковая сварка оплавлением - контактная сварка, при которой детали поступательно сближаются и ток, протекающий через определенные точки контакта, вызывает повторяющиеся искровые вспышки и выбросы расплавленного металла.
1, 4 -зажимы; 2-сварной шов; 3-грат; 5-деталь;

6-зона искровых вспышек (искровой зазор); 7-источник питания
Сварка оплавлением используется для соединения деталей с площадью сечения до 100000 мм², таких как трубопроводы, арматура железобетонных изделий, стыковые соединения профильной стали. Применяется для соединения железнодорожных рельсов на бесстыковых путях, для производства длинноразмерных заготовок из сталей, сплавов и цветных металлов. В судостроении используется для изготовления якорных цепей, змеевиков холодильников рефрижераторных судов. Также сварка оплавлением используется в производстве режущего инструмента (например, для сварки рабочей части сверла из инструментальной стали с хвостовой частью из обычной стали)
40. Газы для газопламенной обработки
Термином «газопламенная обработка» называют совокупность технологических процессов тепловой обработки металлов пламенем горючих газов сварочных горелок. Газопламенная обработка преимущественно ведется с применением кислорода и горючих газов (ацетилена и его заменителей). Иногда используются смеси кислорода и паров горючих жидкостей (керосина или бензина). Применяемые при газопаменных процессах горючие газы и кислород подаются к месту работы в сжатом состоянии по газопроводам или в стальных баллонах.
Газы, применяемые при газопламенной обработке: Газопламенная обработка металлов предполагает задействование горючих газов, как источников теплоты. На первом месте среди них стоит ацетилен. Затем следует его заменители — пропан, бутан, метан, их смеси. Довольно широко применяется кислород и, конечно, жидкие горючие материалы — бензин и керосин. Охарактеризуем упомянутые горючие газы по степени их значимости.
Ацетилен, несомненно, самый широко применяемый газ. Он дает наилучшее качество пламени. Это единственный газ, горение которого возможно при отсутствии кислорода (или окислителя вообще). Для работы ацетилен используется в двух видах — в растворенном (в баллонах), либо в газообразном (из ацетиленовых генераторов). Растворенный ацетилен — это газообразный ацетилен, растворенный в ацетоне. Преимущества этого состояния ацетилена в том, что повышается безопасность проведения работ, более надежно работает весь газосварочный (газорезочный)комплекс. Из чего же можно получить ацетилен? Основное сырье — карбид кальция. В результате гидролиза карбида кальция водой из одного килограмма карбида можно получить до 230—250 дм3 ацетилена. Количество воды, необходимое для разложения 1 кг карбида кальция колеблется (в зависимости от грануляции) от 5 до 20 дм3. Применение ацетилена ограничивается только ввиду его дефицитности. Успешно заменить его могут заменители ацетилена — газы, которые уступают ацетилену по теплотворности. В качестве заменителей могут выступить бензин, керосин и их смеси.
Кислород, как горючий газ, может быть использован только в чистом виде. Причем для обработки поверхностей достаточно 92—98% чистоты, а для резки металла — не менее 99,5%. К индивидуальному потребителю кислород поступает в баллонах в сжатом состоянии. Работа с кислородом требует особой осторожности. Главные враги этого газа — жиры, масло. При контакте кислорода с жиром или маслом, даже в ничтожном количестве, образуется взрывчатая смесь. Вся кислородная аппаратура должна быть обезжирена, вся замасленная ветошь должна быть удалена с рабочего места, рабочая одежда тоже не должна иметь масляных пятен.
41. Классификация припоев
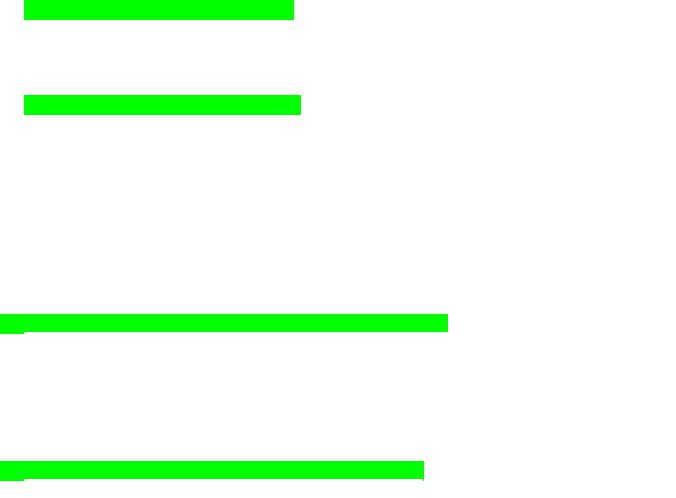
Припой – материал для пайки и лужения с температурой плавления ниже температуры плавления для паяемых материалов.
Припои есть готовые и образующиеся (готовят для соблюдения пробы металла). Классификация по технологическим свойствам: самофлюсующиеся и композитные Пайку осуществляют или с целью создания механически прочного (иногда
герметичного) шва, или для получения электрического контакта с малым переходным сопротивлением. При пайке места соединения и припой нагревают. Так как припой имеет температуру плавления значительно ниже, чем соединяемый металл (или металлы), то он плавится, в то время как основной металл остаётся твёрдым. На границе соприкосновения расплавленного припоя и твёрдого металла происходят различные физико-химические процессы. Припой смачивает металл, растекается по нему и заполняет зазоры между соединяемыми деталями. При этом компоненты припоя диффундируют в основной металл, основной металл растворяется в припое, в результате чего образуется промежуточная прослойка, которая после застывания соединяет детали в одно целое.
Выбирают припой с учётом физико-химических свойств соединяемых металлов, требуемой механической прочности спая, его коррозионной устойчивости и стоимости. При пайке токоведущих частей необходимо учитывать удельную проводимость припоя.
Припои принято делить на две группы — мягкие и твёрдые. К мягким относятся припои с температурой плавления до 300 °C, к твёрдым — выше 300 °C. Кроме того, припои существенно различаются по механической прочности. Мягкие припои имеют предел прочности при растяжении 16—100 МПа, а твёрдые — 100—500МПа.
42.Достоинства клеевых соединений
•при склеивании не возникает коррозии
•непроницаемо для жидкости(герметично)
•вакуум плотный
•поглощает вибрацию
43.Стыковая сварка сопративлением
При сварке сопротивлением детали вначале сжимают осевым усилием для образования плотного соприкосновения свариваемых торцов. Затем подается электрический ток, при прохождении которого стыкуемые поверхности нагреваются до пластического состояния. Далее выполняется осадка (сжатие нарастающим усилием) заготовок с образованием соединения в твердой фазе. При этом ток отключают до окончания осадки.
Сварка сопротивлением используется для соединения деталей круглого или прямоугольного сечения площадью, как правило, до 200 мм2 в зависимости от металлов. Для обеспечения равномерного нагрева торцов они должны быть точно подогнаны и предварительно очищены механическим или химическим способом.
44.Выбор сварочных материалов при ручной дуговой сварке
Электроды, газы, флюсы, сварочные проволока, присадочная проволока. Стальные сварочные проволоки.
Св-18ХМА Г- марганец, Х- хром, Н- никель, М- молбден, В-вольфрам, Ю- алюминий, А-азот, Т- титан, Ф-
ванадий, К- кобольт, Д- медь, Р- бор 1,6-6 ммдуговая.
45.Выбор параметров режима при ручной дуговой сварке
Дуговую сварку контролируют ряд параметров, а именно:
•сварочный ток (выбор сварочного тока посредством подбора диаметра электрода)
•напряжение дуги (длина сварочной дуги)
•скорость сварки
•род и полярность тока (прямая и обратная)