
Экзаемн_сварка
.pdf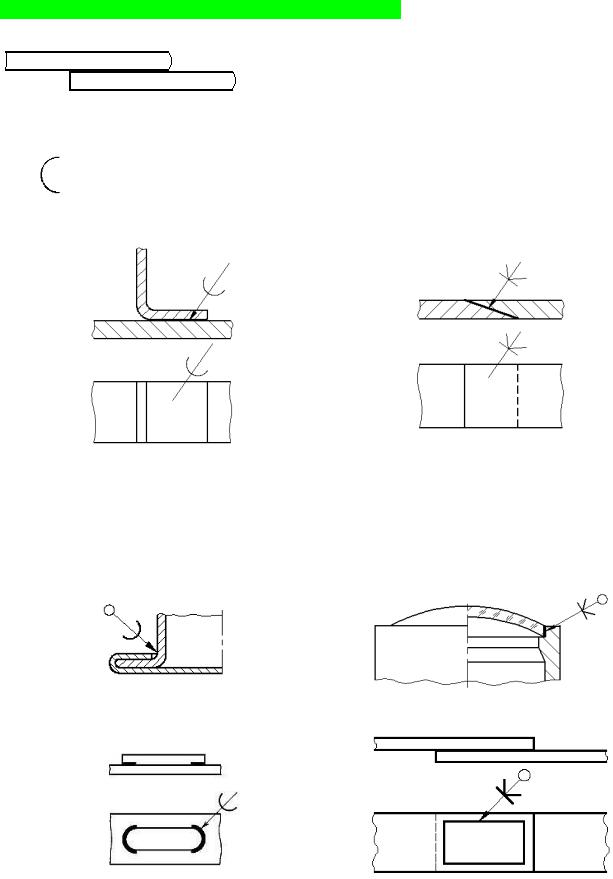
13.Обозначение паянных и клеевых соединений на чертежах
Всоединениях, получаемых пайкой и склеиванием,
место соединения элементов следует изображать сплошной линией толщиной 2s (рис. 3).
Для обозначения паяного и клееного соединения Рисунок 3 следует применять условный знак, который наносят на
линиивыноске сплошной основной линией:
- обозначение для пайки
- обознгачение для склеивания
Пример условного изображения |
Пример условного изображения |
паяного соединения |
клеевого соединения. |
Швы, выполняемые по замкнутой линии, следует обозначать окружностью диаметром от 3 до 5 мм, выполняемой тонкой линией.
Швы, ограниченные определенным участком, следует обозначать, как показано на левом нижнем углу
Обозначение пайки, шов которой |
Обозначение клейки, шов которой |
выполняется по замкнутой линии |
выполняется по замкнутой линии |
Обозначение пайки, шов которой |
Обозначение клейки, шов которой |
ограничен определенным участком |
выполняется по замкнутой линии |
На изображении паяного соединения при необходимости следует указывать размеры шва и обозначение шероховатости поверхности.

Обозначение припоя или клея (клеящего вещества) по соответствующему стандарту или техническим условиям следует проводить в технических требованиях чертежа записью по типу: «ПОС 40 ГОСТ…» или «Клей БФ – 2 ГОСТ…».
При необходимости в том же пункте технических требований следует приводить требования к качеству шва. Ссылку на номер пункта следует помещать на полке линиивыноски, проведенной от изображения шва.
При выполнении швов припоями или клеями различных марок всем швам, выполняемым одним и тем же материалом, следует присваивать один порядковый номер, который следует наносить на линии-выноске. При этом в технических требованиях материал следует указывать записью по типу: «ПОС 4 ГОСТ…(№ 1), ПМЦ 36 ГОСТ…(№ 2), клей БФ-2 ГОСТ…(№3)».
14. Технология сварки алюминия и его сплавов
Сварка алюминия и его сплавов Алюминий. Начать следует с того, что сварка как алюминия, так и его сплавов
осложнена тем, что в процессе сварки на поверхности расплавленного слоя моментально образуется тугоплавкая пленка оксида алюминия. Эта пленка препятствует процессу сплавления отдельных частиц металла. Дело в том, что оксид алюминия плавится при температуре 2050°С, а сам алюминий — 658°С, Чтобы преодолеть эту технологическую трудность, применяют ряд специальных способов.
Первое и важное условие — подготовка к сварке. Соединяемые детали должны быть обязательно обезжирены, при этом уже имеющаяся на поверхности пленка оксида алюминия удаляется. Присадочная проволока обрабатывается таким же способом. Электродные стержни также очищаются перед нанесением на них покрытия. - Металл на ширине 80—100 мм от кромки обезжиривают растворителями (авиационным бензином, техническим ацетоном), затем механической зачисткой или химическим травлением удаляют оксидную пленку.
Удаление пленки оксидов включает следующие операции; травление в течение 0,5—1 мин (состав: раствор едкого натра 50 г и фторида натрия 40 г на 1 л воды); промывку в проточной воде, осветление в течение 1— 2 мин в 30%-м растворе азотной кислоты для алюминия и сплавов типа АМц или 25%-и растворе ортофосфорной кислоты для сплавов типа АМг; промывку в проточной) а затем горячей воде; сушку до полного удаления влаги. Обезжиривание и травление рекомендуется выполнял, не более чем за 2—4 ч до сварки.
Электроды непосредственно перед сваркой надо просушить в течении двух часов при температуре 200°С.
В связи с тем что алюминиевый электрод плавится в 2—3 раза быстрее стального, скорость сварки алюминия должка быть соответственно выше. Сварку рекомендуется выполнять непрерывно в пределах одного электрода, так как пленка шлака на кратере и конце электрода препятствует повторному зажиганию дуги. Для обеспечения устойчивого процесса при минимальных потерях на разбрызгивание рекомендуется принимать сварочный ток из расчета не более 60 А на 1 мм диаметра электрода.
Сварка металла толщиной до 2 мм осуществляется без присадки и без разделки кромок, металл толщиной свыше 2 мм сваривают с зазором 0,5—0,7 толщины свариваемых листов или с разделкой кромок. Оксидную пленку удаляют о помощью флюсов АФ-4А.
Ручную сварку покрытыми электродами применяют в основном при изготовлении малонагруженных конструкций из технического алюминия, сплавов типа АМц и АМг, силумина. Использование постоянного тока обратной полярности и предварительного подогрева (для средних толщин — 250—ЗОО°С, для больших толщин — до 400°С) обеспечивает требуемое проплавление при умеренных сварочных токах.
Ручная дуговая сварка изделий из технически чистого алюминия производится электродами ОЗА-1, а сварка изделий из силуминов — электродами ОЗА-2. Разработаны новые электроды ОЗАНА, которые по технологическим характеристикам существенно превосходят электроды серии ОЗА. При использовании этих электродов обеспечивается мелкокапельный перенос электродного металла, хорошее формирование шва в любых пространственных положениях, легкая отделимость шлаковой корки.
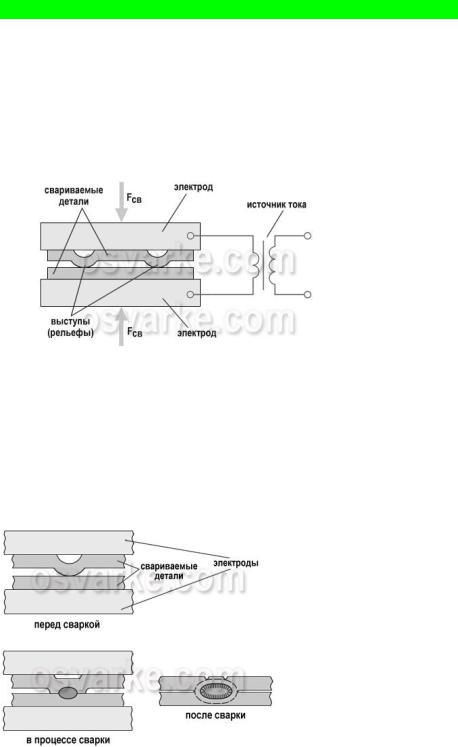
15. Технология рельефной сварки – точно так же как точечная
Рельефная сварка – разновидность точечной контактной сварки, при которой детали соединяются на отдельных участках с предварительно подготовленными или естественными выступами (рельефами) в результате приложения усилия сжатия и подвода тока.
Сущность процесса
На поверхности одной или обеих свариваемых заготовок заранее выштамповываются выступы (рельефы) круглой, кольцевой, продолговатой или другой формы. Затем детали зажимаются между электродами, обычно имеющими форму плиты, с приложением к ним усилия Fсв, и включается сварочный ток.
Схема рельефной сварки
Металл выступа начинает интенсивно нагреваться и постепенно деформируется. На определенной стадии в месте контакта заготовок образуется зона расплавления как при точечной сварке. По мере протекания сварочного тока возрастает объем зоны расплавления, а металл выступа, деформируясь, выходит на наружную поверхность заготовки. После выключения тока расплав охлаждается и кристаллизуется с образованием ядра, окруженного уплотняющим пояском пластически деформированного металла, по которому соединение сформировалось без расплавления.
Основное отличие рельефной сварки от точечной заключается в том, что контакт между заготовками и сварное соединение определяются формой и размерами выступа, а не формой рабочей поверхности электродов, как при обычной точечной сварке. Таким образом, при заранее подготовленных выступах за один ход машины рельефной сварки можно произвести до нескольких десятков сварных точек.
Электроды имеют длительный срок службы изза большой контактной поверхности и концентрации тока и давления в рельефах свариваемых деталей.
Недостатком данной технологии является повышенная электрическая мощность, требуемая для сварочных прессов.
Преимущества:
Рельефная сварка осуществляется по одному и/или нескольким естественно или специально созданным рельефам.
Рельефная контактная сварка высокопроизводительна, удобна для автоматизации, экономически выгодна в массовом и крупносерийном производстве
Кроме того рельефная сварка позволяет получать соединения в тех случаях, когда точечная сварка неэффективна или затруднительна (сварка деталей с защитным покрытием)

16. Технологические и вспомогательные материалы при пайке
Пайка - образование неразъемного соединения с межатомными связями путем нагрева соединяемых материалов ниже температуры их плавления, их смачивания припоем, затекания припоя в зазор и последующей его кристаллизации.
Достоинства пайки:
Возможно соединение металлов с неметаллами;
Паяные соединения легко разъёмные;
При пайке более точно выдерживается форма и размеры изделия, так как основной металл не расплавляется;
Позволяет получать соединения без значительных внутренних напряжений и без коробления изделия;
Возможна полная механизация и автоматизация процесса.
Классификация способов пайки:
По особенностям процесса и технологии пайку можно разделить на капиллярную, диффузионную, контактно-реактивную, реактивно-флюсовую и пайкусварку.
Капиллярная пайка. Припой заполняет зазор между соединяемыми поверхностями и удерживается в нем за счет капиллярных сил. Соединение образуется за счет растворения основы в жидком припое и последующей кристаллизации раствора. Капиллярную пайку используют в тех случаях, когда применяют соединение внахлестку.
Однако капиллярное явление присуще всем видам пайки.
Диффузионная пайка. Соединение образуется за счет взаимной диффузии компонентов припоя и паяемых материалов, причем возможно образование в шве твердого раствора или тугоплавких интерметаллов. Для диффузионной пайки необходима продолжительная выдержка при температуре образования паяного шва и после завершения процесса при температуре ниже солидуса припоя.
Контактно-реактивная пайка. При пайке между соединяемыми металлами или соединяемыми металлами и прослойкой другого металла в результате контактного плавления образуется сплав, который заполняет зазор и при кристаллизации образует паяное соединение.
Реактивно-флюсовая пайка. Припой образуется за счет реакции вытеснения между основным металлом и флюсом. Например, при пайке алюминия с флюсом 3ZnCl2 + 2Al = 2AlCl3 + Zn восстановленный цинк является припоем.
Пайка-сварка. Паяное соединение образуется так же, как при сварке плавлением, но в качестве присадочного металла применяют припой.
Наибольшее применение получила капиллярная пайка и пайка-сварка.
Диффузионная пайка и контактно-реактивная более трудоемки, но обеспечивают высокое качество соединения и применяются, когда в процессе пайки необходимо обеспечить минимальные зазоры. Качество паяных соединений (прочность, герметичность, надежность и т. д.) зависит от правильного выбора основного металла, припоя, флюса, способа нагрева, величины зазоров, типа соединения.
Материалы для пайки.
Припой. Требования к припоям.
Припои для пайки, заполняющие зазор в расплавленном состоянии между соединяемыми заготовками, должны отвечать следующим требованиям:
1.температура их плавления должна быть ниже температуры плавления паяемых материалов;
2.они должны хорошо смачивать паяемый материал и легко растекаться по его поверхности;
3.должны быть достаточно прочными и герметичными;
4.коэффициенты термического расширения припоя и паяемого материала не должны резко различаться;
5.иметь высокую электропроводность при паянии радиоэлектронных и токопроводящих изделий.
Припои классифицируют по следующим признакам:
·Химическому составу;
·Температуре плавления;
·Технологическим свойствам;
По химическому составу припои делятся на свинцово-оловянные, серебряные, меднофосфорные, цинковые, титановые и др.
Все припои по температуре плавления подразделяют на низкотемпературные
(tпл500оС), или твердые припои. Припои изготовляют в виде прутков, проволок, листов, полос, спиралей, колец, дисков, зерен и т. д., укладываемых в место соединения.
К низкотемпературным, или мягким припоям относятся оловянно-свинцовые, на основе висмута, индия, кадмия, цинка, олова, свинца. К высокотемпературным или твердым припоям относятся медные, медно-свинцовые, медно-никелевые, с благородными металлами (серебром, золотом, платиной).
По техническим свойствам делятся на самофлюсующиеся (частично удаляют окислы с поверхности металла) и композиционные (состоят из тугоплавких и легкоплавких порошков, позволяющих производить пайку с большими зазорами между деталями).
Изделия из алюминия и его сплавов паяют с припоями на алюминевой основе с кремнием, медью, оловом и другими металлами.
Магний и его сплавы паяют с припоями на основе магния с добавками алюминия, меди, марганца и цинка.
Изделия из коррозионно-стойких сталей и жаропрочных сплавов, работающих при высоких температурах(>500оС), паяют с припоями на основе железа, марганца, никеля, кобальта, титана, циркония, гафния, ниобия и палладия.
Паяльные флюсы.
Эти флюсы применяют для очистки поверхности паяемого металла, а также для снижения поверхностного натяжения и улучшения растекания и смачиваемости жидкого припоя.
Флюс (кроме реактивно-флюсовой пайки) не должен химически взаимодействовать с припоем. Температура плавления флюса должна быть ниже температуры плавления припоя. Флюс в расплавленном и газообразном состояниях должен способствовать смачиванию поверхности основного металла расплавленным припоем. Флюсы могут быть твердые, пастообразные, жидкие и газообразные.
Флюсы классифицируют по признакам:
Температурному интервалу пайки на низкотемпературные (t4500C); Природе растворителя на водные и неводные;
Природе активатора на канифольные, галогенидные, фтороборатные, анилиновые, кислотные и т.д.;
По агрегатному состоянию на твердые, жидкие и пастообразные По химическому
составу.
Наиболее распространенными паяльными флюсами являются бура (Na2B4O7) и борная кислота (H3BO3), хлористый цинк (ZnCl2), фтористый калий (KF) и другие галоидные соли щелочных металлов.
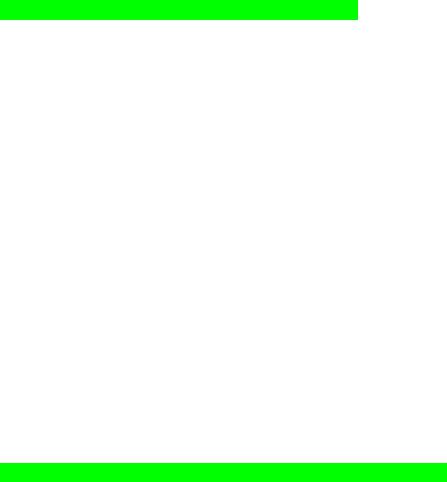
17. Достоинства и недостатки паянных соединений
Достоинства паяных соединений: возможность соединять детали не только из однородных, но и из разнородных материалов, например, стали со сплавами цветных металлов; металлы с графитом, ферритом, фарфором и др.; повышенная технологичность, так как возможно осуществлять пайку в скрытых или малодоступных местах конструкции, изготовлять сложные узлы за один прием, паять не по контуру, а одновременно по всей поверхности соединения; подбирая соответствующие припои, можно выбрать температуру пайки так, чтобы при нагреве под пайку у предварительно термообработанных материалов сохранялись механические свойства в изделии (в готовом соединении) или чтобы нагрев под пайку одновременно обеспечивал и термическую обработку деталей соединения; возможность распайки соединения.
Недостатки: сравнительно низкая прочность паяного соединения на сдвиг и очень низкая прочность на отрыв; высокая трудоемкость изготовления изделий методами высокотемпературной пайки.
Следует отметить, что прочность паяного шва выше (иногда существенно) прочности припоя в связи с растворением в слое припоя материала деталей и в связи с тем, что слой припоя находится в стесненном напряженном состоянии между соединяемыми деталями.
Пайкой соединяют детали различной формы: листы, стержни трубы и др. В последнее время находят применение сотовые паяные конструкции; в обшивке самолетов листы из малопрочных алюминиевых сплавов заменяют паяными высокопрочными и жесткими панелями из тонких стальных листов с сотовым или гофровым промежуточным заполнителем.
Паяные соединения предпочтительно выполнять нахлесточными; площадь перекрытия (площадь пайки) следует назначать так, чтобы прочность паяного соединения была равна прочности целой детали.
18. Техника выполнения валиков при ручной дуговой сварке
При перемещении электрода прямолинейно вдоль шва без колебательных движений наплавляется узкий (ниточный) валик. При наложении валика электрод следует держать наклонно, под некоторым углом к вертикальной линии, чтобы капли металла, перемещающиеся при расплавлении конца электрода в направлении его оси, попадали в расплавленный металл ванны. Электрод должен быть наклонен в сторону направления сварки. При этом глубина проплавления основного металла получается больше. Угол наклона а покрытого электрода к вертикали должен составлять 15—20°.
Изменяя наклон электрода, сварщик может регулировать глубину расплавления металла, способствовать лучшему формированию валика шва и влиять на скорость охлаждения ванны.
Узкий валик накладывают при проваре корня шва, сварке тонких листов, сварке горизонтальных и потолочных швов (независимо от числа слоев). Чем медленнее сварщик перемещает электрод вдоль шва, тем шире получается валик. В узком, но высоком валике объем наплавленного металла невелик, такой валик застывает быстрее, и растворенные в металле невыделившиеся газы могут вызвать пористость шва. Поэтому чаще применяют уширенные валики, которые также менее склонны к образованию кристаллизационных трещин. При выполнении их сварщик сообщает электроду колебательные движения поперек шва, причем конец электрода должен совершать три движения (рис. 65, а): поступательное I вдоль оси электрода сверху вниз, поступательное 2 вдоль линии шва и колебательное 3 поперек шва, перпендикулярно его оси. Колебательные движения электрода способствуют прогреву кромок и замедляют остывание сварочной ванны.
Схемы движений конца электрода при наплавке уширенных валиков показаны на рис. 65, б. В точках 1, 2 и 3 скорость перемещения электрода уменьшается, что способствует прогреванию кромок.
Лучшее качество имеют валики шириной, равной 2,5—3 диаметрам электрода. В этом случае все кратеры расплавленного металла 1, 2, 3 сливаются в одну ванну и обеспечивается наилучшее сплавление основного и наплавленного металла.
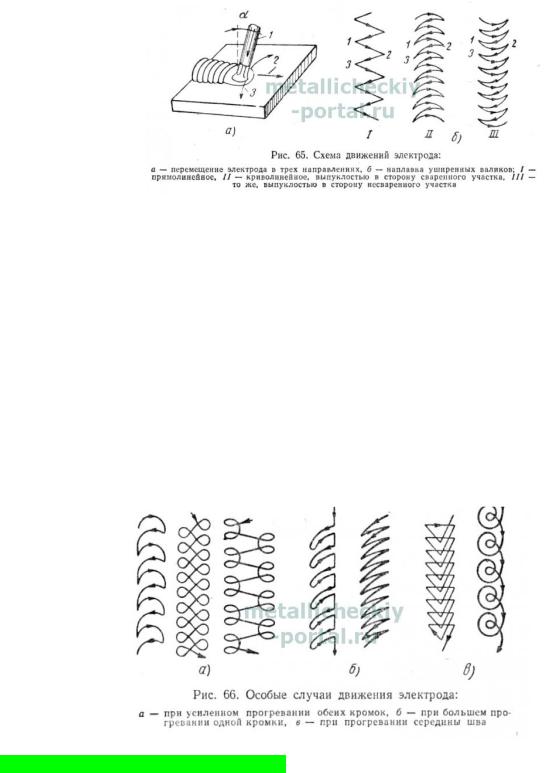
При слишком большой ширине валика металл в точке 1 затвердеет к тому моменту, когда дуга возвратится в точку 3, и в этом месте может образоваться непровар. Кроме того, понижается производительность сварки. На рис. 66, а показаны движения концом электрода, необходимые для прогревания обеих кромок, на рис. 66, б — для прогревания только одной кромки (например, при сварке листов разной толщины). Для прогревания середины шва электрод перемещают по схеме, данной на рис. 66, в. Наплавляя валик, сварщик может находиться сбоку от шва и перемещать электрод слева направо или располагаться по оси шва и вести электрод «на себя» или «от себя».
После окончания наплавки валика остающийся в конце его кратер должен быть тщательно заварен, чтобы в этом месте не появилась трещина.
При сварке электродами с покрытиями необходимо обеспечить полную и равномерную защиту жидкого металла слоем расплавленного шлака. Шлак должен располагаться позади дуги, не смешиваться с расплавленным металлом и не затекать вперед дуги, т. е. не попадать на поверхность нерасплавленного металла. Металл поддерживается достаточное время в жидком состоянии, чтобы частицы шлака всплыли на поверхность ванны и шлак успел раскислить металл.
19. Классификация контактной сварки
Контактная сварка представляет собой процесс выполнения неразъемного соединения, образующегося в результате возникновения пластических деформаций и нагрева деталей в зоне сварки при воздействии на их прижимного усилия и сварочного тока.
Классификация контактной сварки:
По технологии выполнения сварного соединения (точечная, рельефная.ю шовная, стыковая)
По количеству соединений производимых одновременно (одно или несколько соединений)
По роду тока (сварка импульсным или переменным током)
Точечная сварка осуществляется путем плотного прижатия заготовок друг к другу и их соединения в одно или нескольких точках
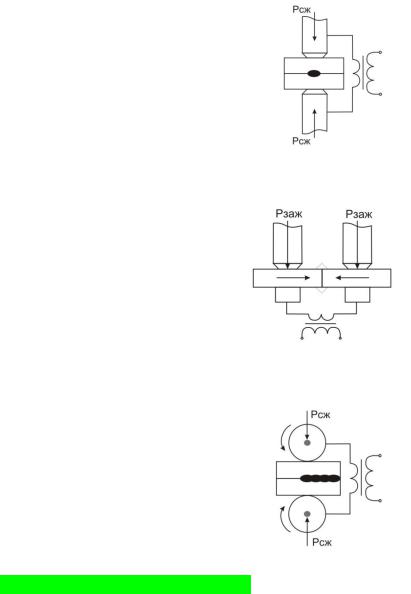
Стыковая сварка – контактная сварка предназначенная для соединения деталей по всей поверхности их соприкосновения
Шовная сварка является аналогом точечной сварки, только в этом случае сварные точки следуют друг за другом, образуя единый шов.
20. Недостатки клееных соединений
Склеивание - технологический процесс получения неразъемных соединений.
Клеевые соединения имеют следующие преимущества: позволяют надежно и достаточно прочно соединять разнородные материалы (пластмассы с металлами) разной толщины, разнородные металлы без образования хрупких интерметаллических фаз, неизбежных при других способах (сваркой, пайкой, с помощью заклепок и болтов), исключают необходимость сверления отверстий, изготовления болтов и заклепок; процесс соединения становится более простым и дешевым, снижается вес конструкции, соединения имеют гладкую поверхность, хорошую герметичность и высокую циклическую прочность.
Основной недостаток большинства клеев заключается в их низкой теплостойкости. Разработан ряд клеев на основе органических, элементорганических и неорганических полимеров, которые могут работать при температурах выше 1000°С, но большинство из них не дает достаточно эластичной клеевой пленки, что пока ограничивает возможность их применения.
Так же недостатком клеевых соединений является также их относительно невысокая прочность при неравномерном отрыве и необходимость во многих случаях производить нагревание при склеивании, необходимость применения сложного оборудования и высокоточной оснастки, снижение прочности соединений в результате старения клея,
токсичность некоторых видов клеев.
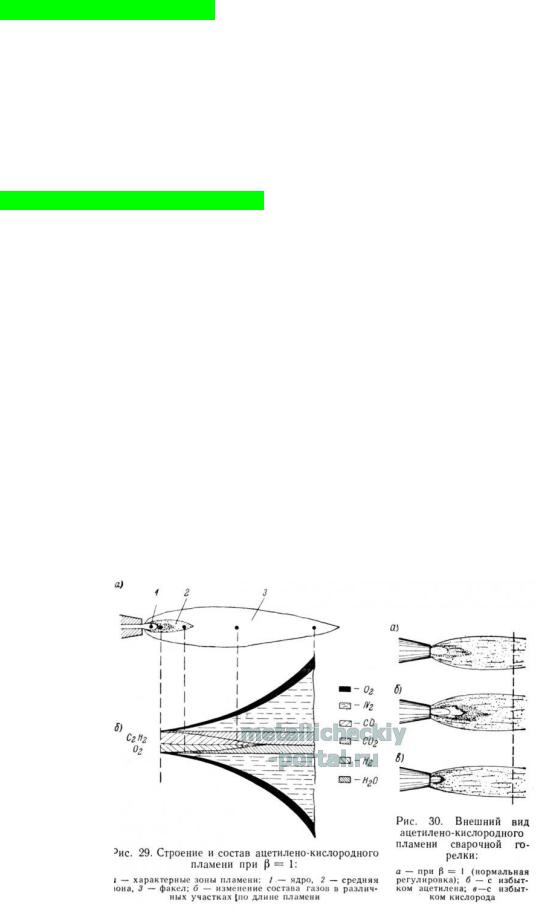
21. Неплавящиеся электроды
Неплавящиеся электроды – один из видов неметаллических сварочных электродов. Применяют главным образом для сварки в защитном газе и плазменной сварки и резки. Неплавящимися электродами служат вольфрамовая проволока — прутки. Вольфрам — тугоплавкий металл, температура его плавления достигает 4500 °С, поэтому при сварке его расход незначителен. Применение вольфрамовых электродов позволяет осуществлять аргонодуговую сварку раз личных высоколегированных сталей и цветных металлов без присадочного или с присадочным материалом, обеспечивая при этом хорошую защиту зоны сварки инертным газом.
22. Газовое пламя состав и свойства
Строение и состав сварочного пламени
Для газопламенной обработки металлов в качестве горючих газов в основном применяются различные углеводороды и только в некоторых случаях водород.
Строение пламени при горении углеводородов в кислороде или в воздухе характеризуется наличием трех зон:
1)ядра;
2)средней зоны;
3)факела.
Форма, вид и относительные размеры этих зон зависят от соотношения кислорода (Vк) и горючего газа (Vг) в смеси, т. е. регулирования пламени, характеризуемого коэффициентом B
= Vк/Vг.
Процесс горения проходит в несколько стадий.
Первая стадия - подготовка горючего к сгоранию - характеризуется распадом углеводорода в конечном виде на углерод и водород.
Реакция ускоряется в случае присутствия кислорода в смеси с углеводородом. Реакции распада осуществляются внутри ядра пламени.
Вторая стадия горения характеризуется образованием СО и Н2.
При горении элементарные частицы углерода накаливаются, их свечение и показывает границу ядра пламени. Если кислорода в горючей смеси достаточно, за этой границей ядра свободного углерода уже нет.
В пламени с избытком кислорода (B > 1,3) во второй зоне кроме СО, Н2 и Н имеются значительные количества С02 и Н20 и большее количество свободного кислорода. Эта зона пламени горячее (имеет более высокую температуру, чем при B = 1-1,1) вследствие
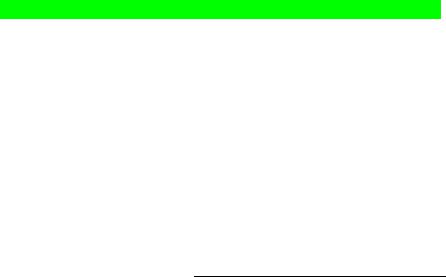
дополнительного теплового эффекта сгорания СО в С02 и Н2 в Н20 и обладает более высокой окислительной способностью по отношению к нагреваемому и расплавляемому металлу В зависимости от соотношения между кислородом и ацетиленом получают три основных вида
сварочного пламени: нормальное, окислительное и науглероживающее. Нормальное пламя (рис. 36,6) теоретически получают тогда, когда в горелку на один объем кислорода поступает один объем ацетилена. Практически кислорода в горелку подают несколько больше
— от 1,1 до 1,3 от объема ацетилена. Нормальное пламя характеризуется отсутствием свободного кислорода и углерода в его восстановительной зоне. Кислорода в горелку подается немного больше из-за небольшой его загрязненности и расхода на сгорание водорода. В нормальном пламени ярко выражены все три зоны.
Ядро имеет резко очерченную форму (близкую к форме цилиндра), плавно закругляющуюся в конце, с ярко светящейся оболочкой. Оболочка состоит из раскаленных частиц углерода, которые сгорают в наружном слое оболочки. Размеры ядра зависят от состава горючей смеси, ее расхода и скорости истечения. Диаметр канала мундштука горелки определяет диаметр ядра пламени, а скорость истечения газовой смеси — его длину.
Площадь поперечного сечения канала мундштука горелки прямо пропорциональна толщине свариваемого металла. Сварочное пламя не должно быть слишком «мягким» или «жестким». Мягкое пламя склонно к обратным ударам и хлопкам, жесткое — способно выдувать расплавленный металл из сварочной ванны. При увеличении давления кислорода скорость истечения горючей смеси увеличивается и ядро сварочного пламени удлиняется, при уменьшении скорости истечения — ядро укорачивается. С увеличением номера мундштука размеры ядра увеличиваются. Температура ядра достигает 1000°С.
23. Покрытия электродов, состав и назначение компонентов
Длина электрода можнт варироваться от 250 до 450, диаметр от 1,6 до 6 мм. Электрод изготавливается 1) окунание(разводят раствор и окунают несколько раз,достается, сушится и окунается несколько раз)2) отрисовка Окунание используется редко,потому что неравномерно наносится. Требования к электроду: 1. обеспечение стабильного горения дуги и хорошего формирования шва. 2. получение задан. Химического состава шва наплавленного металла.3. Спокойное и равномерное расплавленного электрода и покрытие с минимальными потерями. 4. Легкая отделяемость шлака и достаточная прочность покрытия. 5. сохранение физ. И хим. Свойств в течении опр. Времени. 6. Минимальная таксичн. при изготовлении электродов и работе с ними. Состав покрытий :Шлакобранирующие
защищают расплавленный металл от воздействия кислорода и частично рафинирует его. Шлакообразующие составляющие уменьшают скорость охлаждения металла и способствуют выделению из него неметаллических включений. Шлакообразующие составляющие могут включать в себя: титановый концитрат, маргонцевую руду,полевой шпат, калий(мел мрамор, кварцевый песок). Газообразующие составляющие:состоят из дреесной муки,хлопчатобумажной пряжи, целюлозы, крахмал, мука. Раскисляющие составляющие: необходимы для удаления кислорода расплавленного металла к ним относятся элементы, которые обладают большим раствором с кислородом, чем железо(например лед, кремний, титан, алюминий). Раскисляющие составляющие необходимы в составе покрытия для предания метал. Шва спец. Свойства это: жаростойкость, износостойкость, сопротивляемость коррозии повышенных металлических свойств. Лигирующими элементами служат марганец,хром, титан, ванадий, молибден, никель, вольфрам. Так же вводятся стабилизирующие составляющие(для стабильного горения дуги) это те элементы которые имеют небольшой потенциал ионизации(калий,натрий,кальций). Связующие клеющие составляющие: для сварки между собой в покрытии и покрытия на электроде. В качестве них употребляется калиевое или натриевое жидкое стекло, докстрин,желотин.