
up
.pdf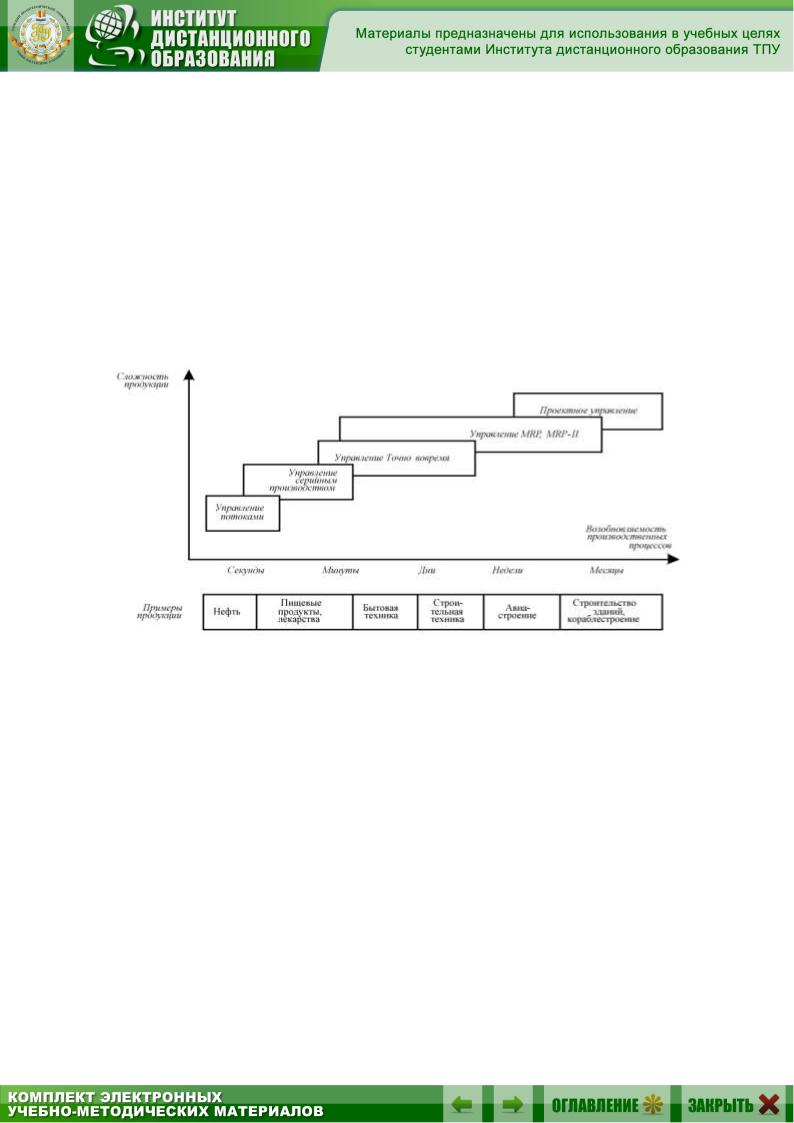
Несмотря на общность разных систем управления, их практическое применение индивидуально. Руководители предприятия могут обеспечить необходимый баланс только в том случае, если они ясно представляют себе стратегию компании, набор задач, вытекающих из стратегии и решаемых при помощи системы, а также элементы самой системы.
Рис. 5.2 иллюстрирует взаимосвязь между подходами к организации систем управления, сложностью производимой продукции (сложность в большинстве случаев может быть выражена в количестве составных частей и продолжительности технологического цикла) и возобновляемостью производственного процесса (определяется периодом или частотой выпуска однотипных изделий).
Рис. 5.2. Классификация систем производственного управления
В левом нижнем углу диаграммы представлен непрерывный тип производства, характерный для предприятий химической, нефтеперерабатывающей и некоторых других отраслей. В этом случае объектами управления системы являются потоки, которые определяются основным производственным планом. Как правило, такие производства характеризуются относительно небольшим числом компонентов, составляющих готовую продукцию, поэтому планирование материалов здесь не вызывает особых трудностей, гораздо сложнее задачи планирования мощностей. Обычно в структуре затрат таких компаний основной удельный вес приходится на сырье, при этом доля транспортных расходов и расходов на хранение также может быть значительной.
Серийный тип производства характерен для многих предприятий, осуществляющих сборку однотипных изделий (производство автомобилей, часов, микрокомпьютеров, телевизоров, фармацевтических препа-
41

ратов, некоторых видов строительных материалов и т.п.). Для такой продукции система управления материалами и компонентами становится жизненно необходимой, при этом такое управление подстраивается под ритм выпуска готовых изделий и нормы расхода соответствующих материалов.
В центре диаграммы представлен широкий диапазон систем типа Точно вовремя. Именно так сегодня стремятся работать многие компании, стараясь сочетать производство «заказных» изделий со стилем управления возобновляемым производством (короткий производственный цикл, сжатые сроки поставок, низкий уровень запасов и т.д.). В настоящее время существует тенденция сочетания такого подхода с традиционными MRP-системами.
Что касается самих MRP-систем, то на схеме они также покрывают весьма обширный диапазон. Эти системы управления наиболее актуальны для производства сложных видов продукции. Такое производство характерно для многих компаний, поэтому системы управления, основанные на методологии MRP, продолжают оставаться одними из самых популярных в мире.
Последний тип систем управления, представленный на рисунке, предназначен для производств проектного типа. К таким производствам относится изготовление уникальной продукции, осуществляемое в течение длительного периода времени (строительство зданий и сооружений, самолето- и ракетостроение, кораблестроение и т.п.). В этом случае в центре внимания оказывается фактор времени как один из важнейших параметров выполнения проектных работ. Основная задача управления проектами – постоянное отслеживание статуса проекта в свете ожидаемой даты его завершения и отнесенных затрат. Некоторые компании успешно сочетают подходы MRP с принципами управления проектами. Это становится особенно эффективным при управлении наукоемким производством, где управление конструкторско-технологическими разработками не менее важно, чем управление промышленным производством.
5.1. Развитие систем управления предприятием
Системы управления предприятием за длительный период своего развития прошли путь от простейших ручных форм учета запасов и производственных ресурсов до современных автоматизированных методов управления, основанных на использовании компьютеров, позволяющих не только учитывать, но и оптимизировать производственные процессы в условиях быстро меняющегося внешнего окружения и внут-
42

ренней ситуации на предприятии. Такие системы предназначены для применения на предприятиях практически любого масштаба и сектора экономики.
В данном подразделе рассматривается эволюция методов управления предприятием. Обозначения этих методов будет приводиться в общепринятых международных терминах, с использованием, где это возможно, русских эквивалентов.
5.1.1. Управление запасами и производством по точке перезаказа
До того как компьютеры стали широко использоваться для управления предприятием, все учетные и управленческие операции проводились персоналом вручную. Одной из первых задач управления, которая решалась таким образом, являлась задача управления запасами. Для учета и отслеживания запасов применялись карточки складского учета, в которых указывалось поступление материалов на склад, их отпуск со склада, а также их остаток. Как правило, информация с карточек дублировалась в книгах учета движения материалов. Скорость реагирования такой системы была крайне невысокой и, в силу специфики регистрации информации, приводила к значительному количеству ошибок и неточностей. Однако в условиях дефицитного рынка этот метод управления вполне удовлетворял производственные компании. Отметим, что «карточный» метод не собирается умирать и все еще используется многими российскими предприятиями. Хотя, по наблюдению авторов, происходит это скорее по привычке, чем в целях реального управления.
При использовании «карточного» метода задача пополнения запасов решалась очень простым (с точки зрения трудозатрат персонала) и очень неэффективным (с точки зрения достижения основных целей предприятия) способом: когда какой-либо материал был полностью израсходован, формировался заказ поставщику или в производство. В этом случае (поскольку поставка не могла происходить моментально) в течение некоторого периода времени необходимый материал просто отсутствовал на складе. Описанная ситуация выглядела так, как показано на рис. 5.3.
Логичным решением, исключающим такую ситуацию, стало установление некоторого минимального уровня запасов на складах, по достижении которого формировался заказ на пополнение. То есть как только реальное количество материала на складе опускалось ниже определенного уровня, называемого точкой перезаказа, значение которой зависело от времени реализации потребности, величины заказываемой
43

партии и некоторых других параметров, происходило оформление нового заказа на поставку этого материала или изготовление изделия.
Простейший способ определения точки перезаказа состоит в расчете средней дневной потребности в данном материале и умножения ее на время выполнения заказа, выраженного в днях. Например, если потребность в материале составляет 100 единиц в день, а период реализации потребности – 10 дней, то точка перезаказа должна быть установлена на уровне 1000 единиц. Каждый раз, когда запас падает до уровня 1000, следует немедленно заказать новую партию, что гарантирует наличие материала на складе в течение того времени, которое потребуется для доставки новой партии.
Рис. 5.3. Простейшая модель управления запасами
Объем партии материала, заказываемый каждый раз по достижении точки перезаказа, может быть рассчитан при помощи формулы оптимального объема заказа (ООЗ). ООЗ рассчитывается исходя из минимума суммарных затрат, включающих стоимость хранения материала на складе (чем больше партия, тем дольше она расходуется и тем выше общая стоимость хранения) и стоимость самого заказа (стоимость доставки от поставщика, стоимость наладки оборудования и т.п.).
Формулы для вычисления точки перезаказа и оптимального объема заказа выглядят следующим образом:
44

|
Годовая потребность |
|
Время реализации |
|
|
Точка перезаказа = |
в материале |
|
потребности (в днях) |
; |
|
Количество дней в году |
|||||
|
|
Оптимальный 2Со D ,. объем заказа (ООЗ) Сн
где Co – затраты на обработку каждого заказа (транспортировка, время
наладки оборудования и т.д.);
Cн – затраты на хранение единицы запаса на складе в течение од-
ного года;
D – годовая потребность в материале.
Графическое представление модели ООЗ выглядит так, как показано на рис. 5.4.
Рис. 5.4. Управление запасами по точке перезаказа
В приведенных выше уравнениях присутствуют два фактора – потребность в материале и время реализации потребности (время выполнения заказа или время опережения), т.е. время закупки или производства. Каждый из них подвержен случайным воздействиям и на практике вряд ли может считаться стабильным. Потребность в материалах также почти никогда не является постоянной: спрос на готовую продукцию
45

меняется, в производстве случается брак, в силу чего неожиданно увеличивается расход материалов, и т.п. Время опережения также известно лишь с некоторым уровнем точности: поставщики срывают сроки выполнения заказов, производство изделия может затянуться из-за возникших очередей и т.п.
Все это – объективные реалии нашей жизни, поэтому в большинстве случаев можно оперировать только усредненными показателями. Это означает, что в одних случаях фактический спрос окажется выше среднего, а в других случаях – ниже (что, впрочем, не столь критично). Можно предположить, что такие колебания происходят случайным образом. Поэтому по крайней мере в половине случаев, будет иметь место ситуация, когда весь имеющийся запас уже исчерпан, а новая партия еще не получена.
Для того чтобы обезопасить себя от таких ситуаций, величину точки перезаказа повышают на некоторую величину. Это – страховой запас или страховой задел. В результате такой буферизации минимальный уровень запаса, имеющий место в начале каждого цикла перезаказа, повышается. Описанный метод графически представлен на рис. 5.5.
Рис. 5.5. Управление по точке перезаказа со страховым запасом
46
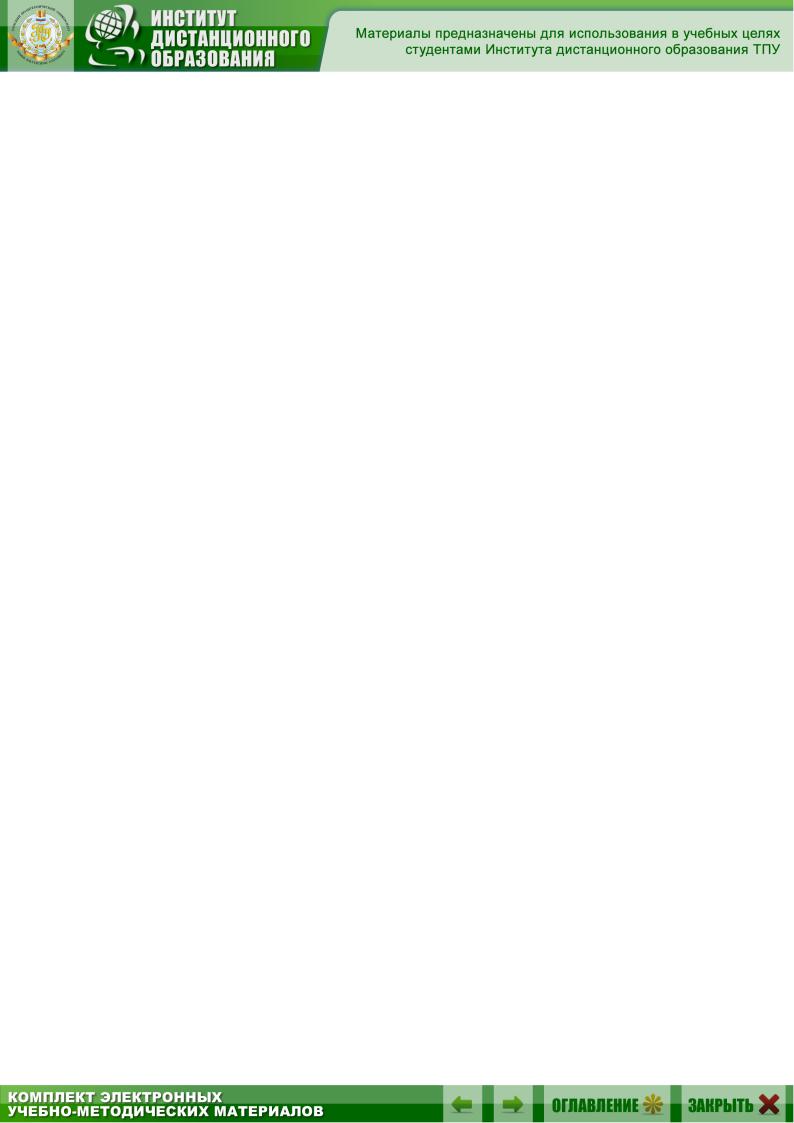
Одна из проблем определения точки перезаказа заключается в том, что оценка уровня перезаказа базируется на прошлом опыте. Заказ делается именно тогда, когда складской запас падает до определенного уровня, но сам факт достижения этого уровня – результат последовательности уже свершившихся событий (поступлений на склад и отпуска со склада). Колебания в потреблении материала, которые могут случиться после достижения точки перезаказа, никак не учитываются. Если спрос на материал в этот промежуток времени растет, то действия по заказу новых партий всегда будут отставать от этой тенденции, при этом вероятность нехватки материала окажется выше, чем предполагалось. И наоборот, при уменьшении спроса принятый темп поставок (производства) даст неоправданно завышенный результат. Эта проблема сохраняется даже в том случае, если уровень перезаказа будет время от времени корректироваться, хотя большинство компаний не делают этого регулярно.
Для того чтобы как-то решить эту проблему, можно измерить колебания спроса, а затем использовать статистический анализ для определения точки перезаказа и уровня страхового запаса. Некоторые компьютерные системы, поддерживающие такой метод управления запасами, позволяют делать это с заданной периодичностью (с учетом необходимых корректировок). Такие вычисления обладают большей стабильностью, но не следует забывать, что даже в этом случае мы будем продолжать работать с данными «из прошлого». Таким образом, управление запасами для всех объектов материального учета на предприятии по этому методу подобно вождению автомобиля с использованием только зеркал заднего вида.
Продвинутые компании, использующие такой метод управления запасами (разумеется, не для всех объектов материального учета), определяют оптимальную величину страхового запаса с учетом выбранного уровня надежности, который рассчитывается методами математической статистики. Не вдаваясь в детали вычисления, определим уровень надежности как вероятность удовлетворения спроса на какой-либо материал в заданном количестве и в заданное время. Например, если уровень надежности составляет 90 %, то это означает, что вероятность отсутствия необходимого материала на складе составляет 10 %.
Таким образом, используя метод точки перезаказа, важно задать допустимый уровень риска неудовлетворения спроса (внутреннего или внешнего). Очевидно, что полностью устранить риск невозможно. Кроме того, необходимо учитывать, что затраты, связанные с повышением уровня надежности, возрастают в геометрической прогрессии: чем выше допустимый уровень надежности, тем выше страховой запас.
47
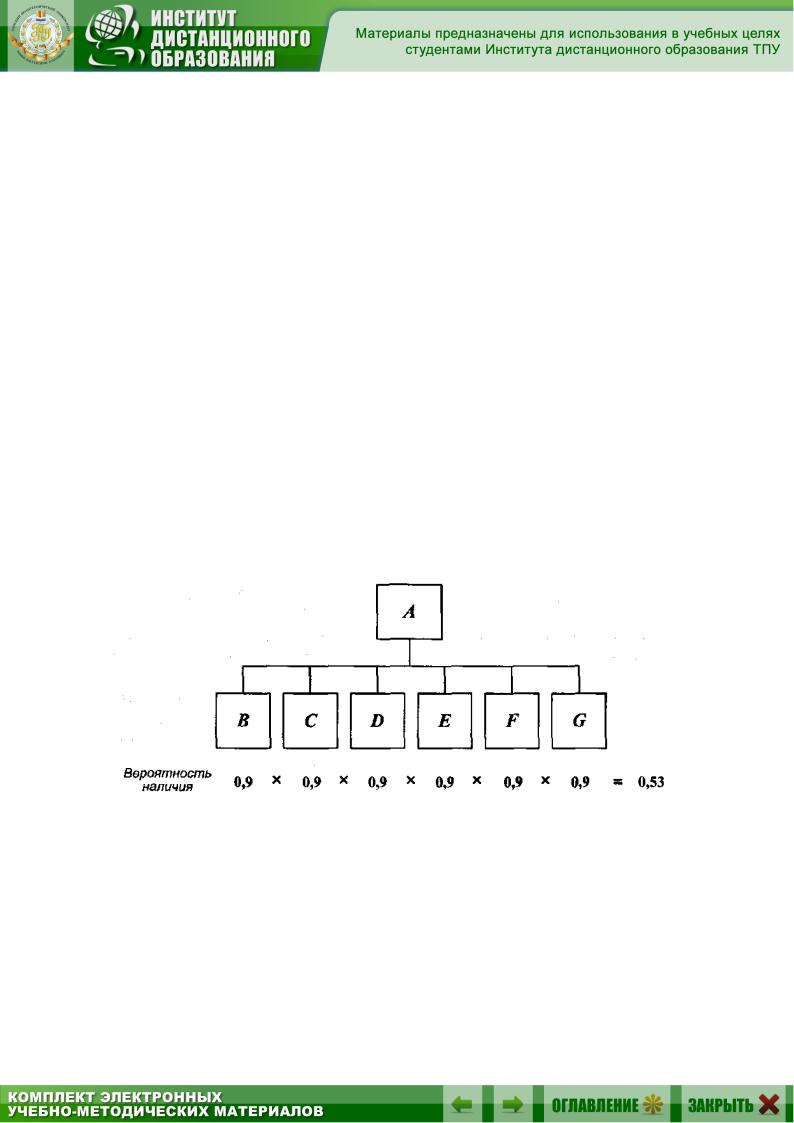
Тем не менее необходимо отметить, что этот подход может применяться в случае планирования материалов (изделий) независимого спроса, т.е. материалов, расход которых практически невозможно спрогнозировать с удовлетворительной погрешностью. Очень часто применение техники точки перезаказа – единственная альтернатива.
Однако в случае использования этого метода для управления материалами зависимого спроса, примером которых могут служить детали (компоненты) производимого изделия, вероятность дефицита или излишков указанных компонентов становится чрезвычайно высокой. Для примера рассмотрим изделие, состоящее из шести компонентов (рис. 5.6). Выбранный уровень надежности для каждой детали – 90 % (это означает, что в любой момент времени при необходимости поставки этих деталей на сборочную линию требуемое количество каждой из них будет присутствовать на складе с вероятностью 90 %). Однако при этом вероятность того, что готовое изделие будет собрано в любой момент времени и в необходимом количестве (допустим, под заказ клиента), составит, по правилу сложения вероятностей, 0,96 ~ = 0,5. Значительное отличие от 90 %, не так ли? Кроме того, немного найдется промышленных предприятий, выпускающих такие несложные изделия. Очевидно, что такой метод не может считаться допустимым, особенно если предприятие работает в условиях жесткой конкуренции.
Рис. 5.6. Уровень надежности для сложного изделия
Метод управления запасами отлично работает в условиях стабильного спроса (например, в условиях плановой экономики). Он также может применяться для управления запасами недорогих материалов, т.е. материалов класса С по АВС-классификации. (На предприятиях могут использоваться различные методы управления материалами в зависимо-
48
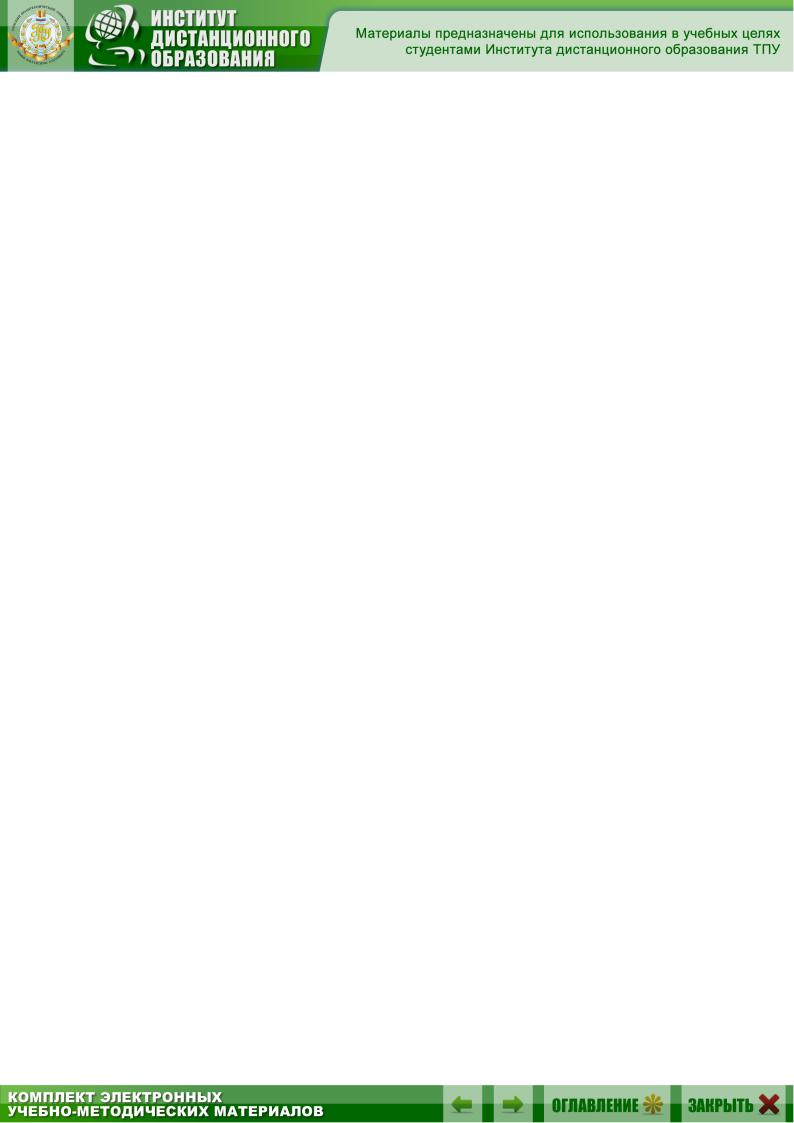
сти от их классификации. Все объекты материального учета, в зависимости от их важности для производственного процесса, могут быть разделены на классы: А, В, С. Материалы группы А составляют 20 % всех материалов/комплектующих, создающих примерно 70 % всей стоимости запасов, В – 30 % всех материалов/комплектующих, создающих примерно 20 % всей стоимости запасов, С – 50 и 20 % соответственно. Как правило, материалы группыА управляются по MRP, материалы группы С по точке перезаказа.)
Однако применение этого метода для управления запасами всего предприятия (т.е. всеми видами материалов и комплектующих) ограничено следующими существенными недостатками:
расчет количества необходимых материалов с помощью метода точки перезаказа в любом случае ведет к образованию на складах излишних запасов материалов и комплектующих (половина партии заказа плюс страховой запас);
даже высокий уровень страхового запаса не способен со 100%-ной вероятностью обеспечить бесперебойное функционирование производства (поскольку потребление материалов всегда может превысить количество, ожидаемое к получению);
метод расчета точки перезаказа основан на исторических данных
опотреблении. В силу этих причин его использование не позволяет оптимально сбалансировать запасы и будущий спрос. При нестабильном спросе необходимый материал всегда может либо оказаться в дефиците, либо его запасы будут необоснованно завышены.
5.1.2.Планирование необходимых материалов (MRP)
ипланирование производственных ресурсов (MRP II)
В 60-е годы усилиями американцев Джозефа Орлики (Joseph Orlicky) и Оливера Вейта (Oliver Weight) был создан метод расчета необходимых для производства материалов, получивший название MRP (Material Requirements Planning – планирование необходимых материалов). Благодаря целенаправленной работе Американской ассоциации по управлению запасами и производством (APICS) метод MRP приобрел широкое распространение во всем западном мире, а в некоторых странах (включая Россию) даже трактуется как стандарт, хотя таковым не является.
Метод планирования необходимых материалов (MRP) стал альтер-
нативой методу планирования по точке перезаказа и позволил преодолеть многие из его недостатков. Объяснялось это тем, что MRP не оперировал данными о потреблении в прошлом, а ориентировался на бу-
49
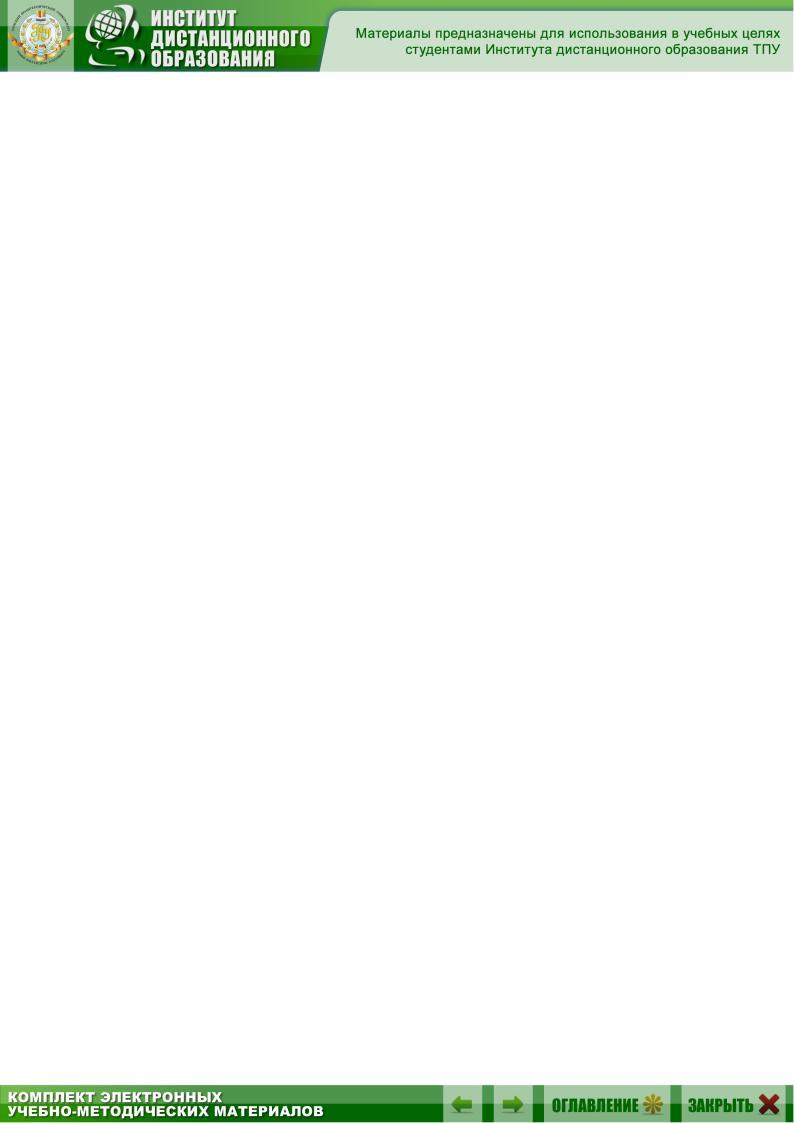
дущие потребности. На практике это означало, что заказ на пополнение запасов формировался только на необходимое количество и только тогда, когда это было действительно необходимо.
Метод MRP основывается на системе расчетов, использующих данные основного производственного плана (ОПП), при построении ко-
торого за исходную точку принимается ожидаемый (фактический) спрос на готовую продукцию. Основной производственный план разрабатывается исходя из прогноза спроса или информации о принятых к исполнению (плановых) заказах с утвержденными (ожидаемыми) датами поставок, а также о потребностях в пополнении страховых запасов
иобеспечении дистрибьюторских центров. Он также может основываться и на комбинации этих данных. Как и MRP, основной производственный план определяет ожидаемый баланс запасов на предприятии
ив случае снижения запасов ниже определенного уровня формирует плановые задания на их пополнение. Фактически ОПП является планом производства, разработанным для изделий, предназначенных к продаже,
ивключающим такие данные, как количество продукции и дата, к которой это количество должно быть произведено. Используя ОПП как отправную точку, по алгоритму MRP рассчитываются необходимые для реализации ОПП объемы материалов, компонентов и деталей с учетом требуемой даты выполнения плана.
Метод планирования производственных ресурсов
(ManufacturingResourcePlanning, MRP II) – результат естественного раз-
вития MRP-алгоритма. Поскольку MRP предназначен для планирования необходимых материалов, идея охватить области деятельности, от которых зависит пополнение или расход материалов, выглядит вполне логичной. Таким образом, MRP II – это планирование по MRP плюс функции управления складами, снабжением, продажами и производством. Поскольку на промышленном предприятии большинство денежных средств так или иначе связано с производством или запасами, использование вышеперечисленных функций делает возможным включение в единую систему также функций учета и управления финансами.
Для понимания алгоритма работы MRP II необходимо представить те начальные данные, которые используются этим методом.
Начальные данные
1. Материальные объекты для планирования (материалы, узлы, го-
товая продукция, инструменты и оснастка и т.д.) с указанием следующих параметров:
50