
Ашихмин Размерный анализ технологических процессов 2010
.pdfМИНИСТЕРСТВО ОБРАЗОВАНИЯ И НАУКИ РОССИЙСКОЙ ФЕДЕРАЦИИ
НАЦИОНАЛЬНЫЙ ИССЛЕДОВАТЕЛЬСКИЙ ЯДЕРНЫЙ УНИВЕРСИТЕТ «МИФИ»
НОВОУРАЛЬСКИЙ ТЕХНОЛОГИЧЕСКИЙ ИНСТИТУТ
В. Н. Ашихмин
РАЗМЕРНЫЙ АНАЛИЗ ТЕХНОЛОГИЧЕСКИХ ПРОЦЕССОВ
Практикум
Рекомендовано УМО «Ядерные физика и технологии» в качестве учебно-методического пособия для студентов высших учебных заведений
Москва 2010
УДК 621.0+621.91 ББК 34.5
A98
Ашихмин В. Н. РАЗМЕРНЫЙ АНАЛИЗ ТЕХНОЛОГИЧЕСКИХ ПРОЦЕССОВ: Практикум. М.: НИЯУ МИФИ, 2010. – 60 с.
Пособие содержит методические указания и рекомендации к выполнению практических работ по курсу «Размерный анализ и обоснование технологических решений» и предназначено для студентов специальности 151001 – Технология машиностроения (очная, очно-заочная, заочная формы обучения). Работа 1 также используется при выполнении практических занятий по курсу «Технология машиностроения».
Подготовленов рамках Программы создания иразвития НИЯУ МИФИ.
Рецензент канд. техн. наук, доцент В. И. Занько
ISBN 978-5-7262-1237-1 |
Национальный исследовательский |
|
ядерный университет «МИФИ», 2010 |
СОДЕРЖАНИЕ
Предисловие …………………………………………………………….4
Практическая работа № 1. Задачи размерного анализа |
|
|
технологических процессов. Разработка стартовой структуры |
|
|
технологического процесса, назначение этапов, методов |
|
|
и планов обработки поверхностей.................................................. |
5 |
|
Практическая работа № 2. Построение размерной схемы и |
|
|
графовых моделей размерных связей технологического |
|
|
процесса ....................................................................................... |
|
26 |
Практическая работа № 3. |
Выявление размерных цепей ............... |
36 |
Практическая работа № 4. |
Проверка обеспечения точности |
|
конструкторских размеров и колебаний припусков в стартовом |
|
|
технологическом процессе........................................................... |
43 |
|
Практическая работа № 5. |
Расчет размерных цепей....................... |
51 |
Библиографический список ............................................................ |
59 |
3
ПРЕДИСЛОВИЕ
Качество продукции в машиностроении определяется прежде всего качеством разработки технологических процессов. Для качественной разработки технологических процессов при использовании настроенного на размер оборудования необходимо проведение размерно-точностного анализа.
Входе проведения размерного анализа должны быть выявлены все размерно-точностные связи в технологическом процессе, начиная от размеров исходной заготовки до размеров готовой детали. Именно такой подход рассматривается в предлагаемом пособии. Актуальность данного пособия обусловлена тем, что в последние годы в отечественной технической литературе практически не издаются книги по размерному анализу технологических процессов.
При решении задач размерного анализа использована методика, основанная на применении теории графов. Это наиболее эффективный математический аппарат для моделирования размерно-точностных связей технологических процессов. Применение этого аппарата способствует развитию навыков математического моделирования у специалиста – технолога.
Вотличие от традиционных методик, в которых выявление размерных цепей производится на совмещенном графе, что связано с определенными трудностями, в пособии использована усовершенствованная методика применения графовых моделей при размерном анализе технологических процессов [1].
Учитывая значение размерного анализа в процессе подготовки спе- циалистов-технологов в ряде вузов в учебных планах технологических кафедр предусмотрены соответствующие дисциплины. Так, например, на кафедрах технологии машиностроения УГТУ – УПИ и НГТИ читается курс «Размерный анализ и обоснование технологических решений». В основу предлагаемой работы положен многолетний опыт изучения указанной дисциплины в УГТУ – УПИ. Пособие может быть использовано при проведении практических занятий в рамках курсов «Основы технологии машиностроения» и «Технология машиностроения».
4

Практическая работа № 11
ЗАДАЧИ РАЗМЕРНОГО АНАЛИЗА ТЕХНОЛОГИЧЕСКИХ ПРОЦЕССОВ. РАЗРАБОТКА СТАРТОВОЙ СТРУКТУРЫ ТЕХНОЛОГИЧЕСКОГО ПРОЦЕССА, НАЗНАЧЕНИЕ ЭТАПОВ, МЕТОДОВ И ПЛАНОВ ОБРАБОТКИ ПОВЕРХНОСТЕЙ
Цель работы − уяснение необходимости и общих положений проведения размерного анализа, освоение навыков разработки стартовой структуры технологического процесса как начальной стадии решения прямой (проектной) задачи размерного анализа.
Задание – для детали класса втулок на основе чертежа детали и условий среднесерийного производства разработать стартовую структуру технологического процесса при использовании метода восходящего синтеза (снизу вверх).
Работа рассчитана на 8–12 ч.
Задачи размерного анализа и методы расчета размерных цепей
Размерным анализом технологического процесса называют выявление и фиксирование размерных связей между переходами и операциями конкретного технологического процесса. Таким образом, для решения проектной задачи, когда есть только чертеж детали, необходима разработка первоначального, стартового варианта технологического процесса [1].
Целью размерного анализа является, прежде всего, обеспечение точности указанных на чертеже размерных связей поверхностей детали. С помощью размерного анализа выявляется наиболее эффективная структура технологического процесса, гарантирующая достижение поставленной цели. В результате размерного анализа
1 Работа № 1 выполняется параллельно на практических занятиях по курсу «Технология машиностроения» и по курсу «Размерный анализ и обоснование технологических решений».
5
наиболее рационально формируются технологические операции и переходы, проверяются и уточняются принятые схемы базирования, определяются все операционные размеры и размеры исходной заготовки. Кроме того, размерный анализ позволяет выявить и устранить недопустимые колебания величины припуска, что особенно важно на финишных операциях.
Вид задачи определяется тем, что задано и что требуется определить. Если разрабатывается новый технологический процесс, то известны и, значит, заданы конструкторские размеры детали. Следовательно, в ряде технологических размерных цепей известен конструкторский размер со всеми его параметрами. Этот размер и будет замыкающим (исходным) звеном в таких размерных цепях.
Если мы анализируем существующий технологический процесс, то известны все технологические (операционные) размеры и их параметры. Эти размеры – составляющие звенья размерных цепей. Таким образом, в цепях, где замыкающее звено – конструкторский размер, мы сможем определить параметры замыкающего звена, которые будут обеспечены в рассматриваемом технологическом процессе.
В теории размерных цепей эти задачи называют соответственно прямой (проектной) и обратной (проверочной).
При прямой задаче заданы номинальный размер, допуск, предельные отклонения замыкающего (исходного) звена и требуется определить номинальные значения, допуски и предельные отклонения всех составляющих звеньев размерной цепи.
При решении обратной задачи по заданным номинальным значениям, допускам, предельным отклонениям составляющих звеньев требуется определить те же характеристики замыкающего звена или поле рассеяния и предельные значения замыкающего звена.
Наиболее распространены два метода расчета размерных цепей: метод максимума-минимума (max-min) и вероятностный метод.
Первый метод иногда называют методом полной взаимозаменяемости, а второй – методом неполной взаимозаменяемости. По мнению многих авторов, для расчета технологических размерных цепей следует использовать метод максимума-минимума. Это
6
обосновывается еще и тем, что число составляющих звеньев в технологических размерных цепях обычно не превышает 4–5.
В данном пособии рассмотрено решение проектной (прямой) задачи, когда технологический процесс еще не существует, а исходным документом является только чертеж детали. Кроме чертежа детали, известна производственная среда, в которой будет реализован технологический процесс, или тип производства.
Стартовый вариант технологического процесса формируется на основе разработанной структуры технологического процесса. В нем назначаются первоначально только величины допусков на технологические размеры и минимальные припуски, снимаемые при выполнении технологических переходов. Таким образом, в отличие от проверочной задачи здесь необходимо определить номинальные размеры и предельные отклонения операционных размеров для всех технологических переходов. Задачи такого типа некоторые авторы [2] называют смешанными.
Методические указания к выполнению работы
В ходе проведения практических занятий каждый студент работает по индивидуальному заданию. На рис. 1.1 приведен эскиз детали типа «втулка», применительно к которой показано выполнение всех этапов задания.
1. Анализ чертежа заданной детали, выбор и определение параметров исходной заготовки. Задана деталь – втулка (см. рис. 1.1). Материал – сталь 30. Масса детали – 2,49 кг. Производство среднесерийное. Предусмотрено использование универсального оборудования, в том числе токарно-револьверного станка с вертикальной осью револьверной головки.
Концентричность поверхностей 4 и 6 будет обеспечиваться по схеме «ОТ ОТВЕРСТИЯ». Отверстие 4 окончательно обрабатывается на токарно-револьверной операции мерным инструментом – разверткой. Торцовые поверхности 1, 5, 7, а также радиальное отверстие 3 связаны линейными размерами. Наружная цилиндрическая поверхность 2 не требует точной обработки. Поверхность 6 обрабатывается на круглошлифовальной операции с базированием на отверстие 4.
7
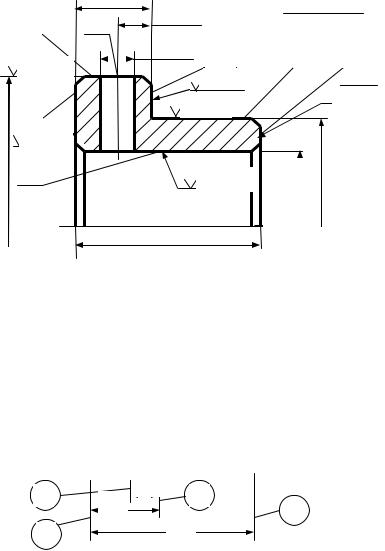
120
|
|
32 |
|
2 |
3 |
17+0,5 |
|
Ra 12,5 |
|
12 |
5 |
|
|
||
|
|
Ra 12,5 |
|
|
|
|
|
1 |
|
|
Ra 1,6 |
Ra 3,2 |
|
|
|
4 |
|
|
Ra 1,6 |
|
|
75 |
|
Ra 6,3 (
)
6 7
Ra 3,2
H8 |
100h8 |
80 |
|
Z |
|
Рис. 1.1. Эскиз детали «втулка» (неуказанные предельные отклонения размеров: H14; h14; IT14/2; номера позиций соответствуют типам обрабатываемых поверхностей)
Нумерация поверхностей детали, связанных линейными размерами, параллельными оси детали, должна производиться по строго определенным правилам:
-номера поверхностей увеличиваются вдоль принятой оси детали;
-фаски не нумеруются;
-для нумерации принимаются только нечетные числа;
-схема конструкторских размерных связей (рис. 1.2) вычерчивается в масштабе.
3 |
32 |
17 |
5 |
|
|||
|
|
7 |
|
|
|
|
|
1 |
|
|
75 |
|
|
|
Рис. 1.2. Схема конструкторских размерных связей
2. Выбор вида исходной заготовки и метода ее получения.
Факторы, определяющие выбор заготовки:
8

-материал детали – сталь 30 (качественная углеродистая сталь, содержание углерода 0,3 %);
-конфигурация детали – втулка с буртиком и сквозным отверстием;
-тип производства – среднесерийное. Рациональнее при этом типе производства выбрать заготовку, форма которой максимально приближена к форме готовой детали (рис. 1.3). Это сведет к минимуму обработку резанием и отходы в стружку.
1
Плоскость
разъема
штампа
5
L1
L2
7
Рис. 1.3. Эскиз исходной заготовки
Выбираем метод горячей объемной штамповки в открытых штампах. При соотношении размеров Dmax > L штамповка производится на молотах или кривошипных горячештамповочных прессах. Сквозные отверстия в исходных заготовках выполняются при условии, что их диаметр не менее 30 мм. Кроме того, длина отверстия должна быть не более диаметра пробиваемого отверстия. Если последнее условие не выполняется, то может быть выполнена наметка (углубление) глубиной до 0,8 диаметра отверстия при изготовлении заготовки на молотах и прессах. Если Dmax < L, то для деталей типа втулок рациональнее выбрать горячую объемную штамповку на горизонтально-ковочных машинах (ГКМ). Предельная длина получаемого отверстия при штамповке на ГКМ – до трех диаметров. С учетом применения газопламенного нагрева класс точности поковки Т5 по ГОСТ 7505-89.
9
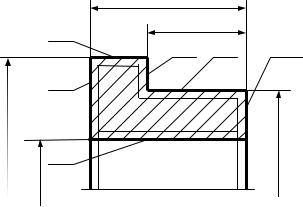
Определяем плоскость разъема штампа [3]. Она проходит по участку наибольшего диаметра. Внутри участок выруба плены соответствует наименьшему диаметру отверстия. Упрощенный эскиз исходной заготовки приведен на рис. 1.4.
|
|
|
L1 |
|
|
|
|
2 |
L2 |
|
|
|
|
5 |
6 |
7 |
|
|
|
|
|||
|
|
1 |
|
|
|
2-2 |
|
|
|
|
6-6 |
D |
4 |
4 |
|
|
D |
|
4- |
|
|
|
|
|
D |
|
|
|
|
|
Рис. 1.4. Упрощенный эскиз исходной заготовки |
||||
(1, 5, 7 – торцовые поверхности, связанные линейными размерами; |
|||||
2, 4, 6 – цилиндрические поверхности со штамповочными уклонами) |
3. Определение общих припусков на обработку и допусков на размеры исходной заготовки.
Определение исходного индекса поковки. Факторы, опреде-
ляющие исходный индекс заготовки, который является ключом к нахождению общих припусков и допусков для поковок:
1)расчетная масса поковки Мп.р., кг.
2)группа стали М1, М2, М3.
3)степень сложности С1, С2, С3, С4.
4)класс точности (для штамповки в открытых штампах Т4 или
Т5).
Расчетная массы поковки определяется по формуле
Мп.р = Мд Kр,
где Kр – расходный коэффициент.
Для деталей круглых в плане (ступицы, шестерни и т.п.) берется
Kр = 1,5–1,8. Примем Kр = 1,7, тогда Мп.р = 2,49.1,7 = 4,23 кг.
10