
Chabannyi_Remont_avto_kn1
.pdf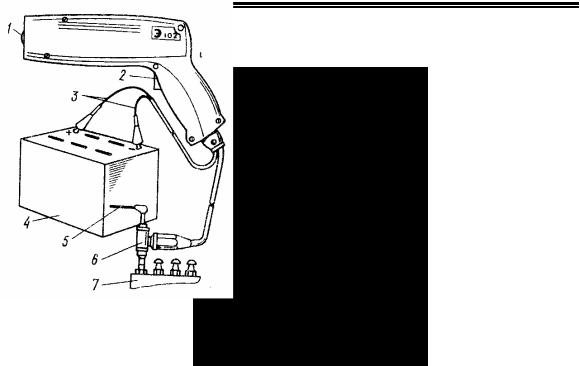
Розділ 2. Передремонтне технічне діагностування і прогнозування параметрів технічного стану автомобілів
замкненні. В справному первинному колі струм, який споживається, повинен бути не більше 5...7 А.
Рис.2.26. Схема підключення приладу Э-102:
1 – лінза; 2 – кнопка; 3 – проводи; 4 – акумуляторна батарея; 5 – наконечник приладу; 6 – перехідник; 7 – перший
циліндр
Установку запалювання перевіряють приладом типу Э-102. Для цього від’ємний і позитивний провідники 3 (рис. 2.26) приєднують до відповідних клем акумуляторної батареї 4. При необхідності регулюють зазор між контактами переривника, який повинен бути 0,35...0,45 мм. Після цього з свічі першого циліндра знімають провід високої напруги і на його місце установлюють перехідник 6 приладу, а провід, знятий з свічі, з’єднують з перехідником 6. Потім наносять крейдою лінії на заводських мітках ВМТ рухомої (шків, маховик) і нерухомої (покажчик, картер) деталей (лінії повинні розміщуватись одна на проти одної), запускають двигун, встановлюють мінімальну частоту обертання колінчастого вала, від’єднують трубку вакуумного регулятора від розподільника, натискають кнопку 2 і направляють світловий промінь лінзи 1 на нанесені крейдою мітки. При правильному встановленні
111

В.Я. Чабанний
запалювання рухома крейдова лінія повинна співпадати з нерухомою. При неспівпаданні ліній повертають корпус переривника вправо або вліво до їх суміщення.
Для перевірки роботи відцентрового і вакуумного регуляторів плавно збільшують частоту обертання колінчастого вала. При справному відцентровому регуляторі рухома крейдова лінія повинна плавно без ривків зміщуватись відносно нерухомої. Після досягнення частоти 2000...2500 хв-1 швидко приєднують до розподільника трубку вакуумного регулятора. При справному регуляторі лінія, що нанесена на рухому деталь, повинна різко відхилитися від лінії нерухомої деталі.
Для перевірки стану датчиків і покажчиків застосовують прилади типу Э-204 (рис. 2.27). Перед перевіркою прилад готують до роботи і перемикач напруги “12...24 В” установлюють в нейтральне положення, рукоятку реостата повертають проти ходу стрілки годинника до упору; в кронштейн кришки установлюють нагрівач, а в нього – термометр; штепсель нагрівача вмикають в розетку “нагрівання” (нагрівач повинен бути заповнений на 2/3 дистильованою водою); рукоятку насосу встановлюють в прилад.
Стан датчика електротеплового імпульсного манометра (рис. 2.27, а) перевіряють таким чином. На датчик нагвинчують перехідний штуцер і встановлюють його в з’єднуючу муфту приладу. Вентиль випуску повітря закривають до упору. Прилад приєднують до акумуляторної батареї і до датчика, який перевіряється. Перемикач перевірок встановлюють в положення Д в секторах Т і Р. Ручкою насоса по манометру створюють максимальний тиск для даного датчика, а потім вентилем випуску повітря знижують його до контрольних точок, кожен раз натискуючи на кнопку “Відлік” і знімаючи показання за мікроамперметром. При тиску в контрольних точках за манометром 0,6; 0,4; 0,2 і 0 МПа показання мікроамперметра відповідно повинні складати 128...150; 92...105; 48...55 і 9...11 мкА при утримуванні тиску в контрольних точках протягом 2 хвилин
112
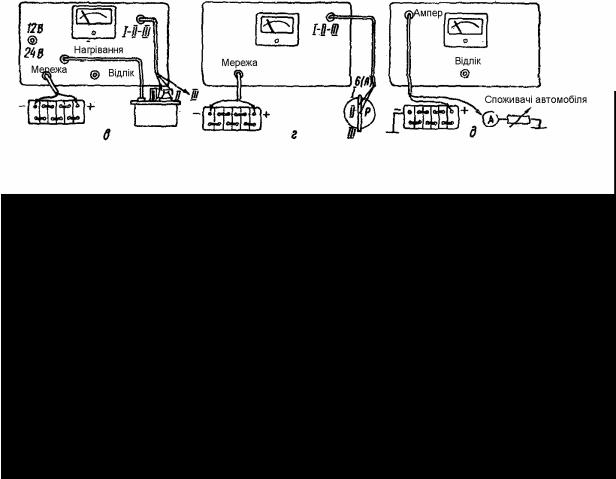
Розділ 2. Передремонтне технічне діагностування і прогнозування параметрів технічного стану автомобілів
(для датчиків – 150...164; 39...45; 12...14 мкА при 0,1; 0,05 і 0 МПа).
Рис.2.27. Схема підключення для перевірки приладу Э-204:
а – датчиків електротеплових імпульсних манометрів; б – покажчиків електротеплових імпульсних манометрів і термометрів; в – датчиків електротеплових імпульсних термометрів; г – покажчиків логометричних термометрів; д – амперметрів
Щоб перевірити стан покажчика електротеплового імпульсного манометра приєднують до нього провідники І і ІІ (рис. 2.27, б), а провідники шнура живлення приєднують до акумуляторної батареї; перемикач перевірок переводять в положення П в секторах Т і Р, рукояткою реостата стрілку покажчика послідовно встановлюють на поділку 0; 0,2; 0,4; 0,6 МПа, і натискуючи кожен раз на кнопку “відлік”, знімають показання на мікроамперметрі. Показання мікроамперметра при вказаних величинах відповідно повинні бути такими: 46...58;
113

В.Я. Чабанний
110...118; 154...166; 184...200 мкА при витримці в контрольних точках 2 хвилини.
Для перевірки стану датчика електротеплового імпульсного термометра до нього приєднують провідники І і ІІ (рис. 2.27, в), а потім встановлюють його в нагрівач. Нагрівач приєднують до розетки “Нагрівання”, а провідники шнура живлення “Мережа” – до акумуляторної батареї. Перемикач напруги встановлюють в положення “12 В” або “24 В”, в залежності від напруги акумуляторної батареї. Перемикач перевірок встановлюють в положення Д в секторах Т і Р. Потім натискають на кнопку “Відлік” з витримкою 3 хвилини в контрольних точках 40, 80 і 100°С і знімають показання з мікроамперметра, які повинні дорівнювати відповідно 119...145; 53...60 і 17...25 мкА.
Аналогічно діагностують датчик логометричного термометра, при цьому перемикач перевірок переводять в положення “500” в секторі “Омметр”. Показаннями мікроамперметра при температурах 40, 80 і 100°С повинні бути відповідно 165...184; 86...97 і 61...68 мкА.
Перед перевіркою стану покажчика електротеплового імпульсного термометра його приєднують до провідників І і ІІ (рис. 2.27, б). Шнур живлення “Мережа” приєднують до акумуляторної батареї, перемикач перевірок переводять у положення П в секторах Т і Р, рукояткою реостата стрілку контрольованого термометра послідовно установлюють на поділки 40, 80 і 100°С, кожен раз натискуючи на кнопку “Відлік”; знімають показання мікроамперметра. Показання мікроамперметра при вказаних температурах відповідно повинні складати 176...196, 116...124 і 64...79 мкА, при витримці в контрольних точках по 2 хвилини.
При перевірці стану покажчика логометричного термометра провід І приєднують до клеми Д покажчика (рис. 2.27, г), перемикачі перевірок і еталонних резисторів відповідно перевіряють у положенні “Лог” і “40”, “80”, “100” або “40”, “80”, “120” в секторі градуси. При цьому контури
114

Розділ 2. Передремонтне технічне діагностування і прогнозування параметрів технічного стану автомобілів
стрілки покажчика, що перевіряється, повинні знаходитись в межах контурів поділок шкали 40, 80, 100, 110 і 120 при встановленні перемикача еталонних резисторів у відповідне положення приладу.
Для перевірки стану амперметра шнур живлення встановлюють в розетку “Ампер” (рис. 2.27, д), з акумуляторної батареї автомобіля знімають плюсовий провід і в утворений розрив приєднують другий кінець шнура живлення. Перемикач перевірок встановлюють в положення А, натискують на кнопку “Відлік” і, послідовно вмикаючи споживачів струму, порівнюють показання амперметра, що перевіряється, з показаннями мікроамперметра приладу. Показання амперметра, який перевіряється, і мікроамперметра повинні відрізнятися не більше ніж на 15% від верхньої межі вимірювання амперметра.
Для перевірки правильності установки передніх фар за допомогою приладу Э-6 конусні кінці штирів 1 і 4 (рис. 2.28) впирають у місцях стиків розсіювача 2 з обідком 3 на рівні центра фар. Відстань К повинна бути менша відстані між центрами фар на діаметр розсіювача фари. Утримуючи приставлений до фар прилад в горизонтальному положенні встановлюють камеру 7 таким чином, щоб її лінза була направлена до фари, яка перевіряється, при цьому повітряна кулька повинна знаходитись між контрольними рисками.
В цьому положенні фіксують камеру 7 на штанзі 6 гайкою 5. Вмикають дальнє, а потім ближнє світло і за розташуванням світлової плями на екрані камери роблять висновок про правильність установки фар. В правильно установленій фарі центр світлової плями дальнього світла повинен розміститися на перехресті лінії екрану. Світлова пляма ближнього світла повинна знаходитись на екрані приладу нижче плями дальнього світла, при цьому оптична вісь а′ – б′ повинна розташовуватися паралельно повздовжній осі а – б машини і паралельно майданчику (підлозі).
115
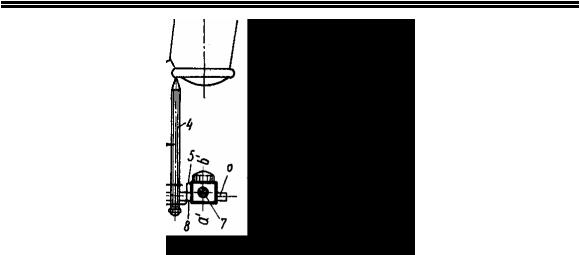
В.Я. Чабанний
Рис.2.27. Перевірка установки фар за допомогою приладу Э-6:
1,4 – штирі; 2 – розсіювач; 3 – ободок; 5 – фіксуюча гайка; 6 – штанга; 7 – оптична камера; 8 – рівень; 9,10 – власники; К– відстаньміжштирями.
В процесі діагностування складових частин електрообладнання проводять операції обслуговування, в результаті яких підтримується його працездатність. При цьому параметри стану, що вийшли із граничних значень, відновлюють підтяжкою з’єднань, регулюваннями, заміною спрацьованих деталей, усуненням пошкоджень. Якщо операціями обслуговування не можливо відновити параметри стану, тоді проводять більш складні технологічні операції – ремонтні.
116

Розділ 3. Технологічні процеси ремонту автомобілів
3. ТЕХНОЛОГІЧНІ ПРОЦЕСИ РЕМОНТУ АВТОМОБІЛІВ
3.1.Поняття і єдина система технічної документації
3.2.Приймання автомобілів і агрегатів в ремонт і їх зовнішнє миття
3.2.1.Приймання автомобілів і агрегатів в ремонт та збереження ремонтного фонду
3.2.2.Зовнішнє очищення і миття автомобіля
3.3Особливості технології розбирання
3.3.1.Загальна послідовність розбирання автомобіля
3.3.2.Особливості розбирання типових сполучень
3.4.Технологія очищення й миття складальних одиниць і деталей
3.4.1.Фізико-хімічні основи видалення технологічних забруднень
3.4.2.Сучасні технічні миючі засоби
3.4.3.Технологічні способи видалення забруднень
3.5.Дефектація спряжень і деталей та їх комплектування
3.5.1.Загальні відомості
3.5.2.Основні способи дефектації деталей
3.5.3.Особливості дефектації типових деталей
3.5.4.Технологія комплектування спряжень і вузлів
117

О.Й. Мажейка
3.1. Поняття і єдина система технічної документації
Ремонтне виробництво – це особливий вид часткового виробництва автомобілів, який характеризується нерівноміцністю їх деталей і не стабільністю регулювань, а саме має у своєму вихідному складі елементи різного строку служби. Воно організовується у сфері споживання автомобілів і полягає у періодичному відновленні частково втраченої внаслідок зносу працездатності їх окремих елементів.
В процесі ремонтного виробництва можливе споживання виробничої продукції машинобудівного виробництва (готових запасних частин, складальних одиниць, агрегатів). Дійсний об’єм по ремонту автомобілів визначається фактичними затратами праці по виконаним розбирально-складальним, мийним, ремонтним і контрольно-випробувальним роботам.
Процеси технічного обслуговування (ТО) автомобілів – це процеси відновлення конструктивних вихідних елементів (змащувальні, регулювальні і т.п.) цих машин. Об’єми їх виконання входять в об’єми ремонтного виробництва, яке має справу з автомобілями, агрегатами і складальними одиницями, що частково втратили працездатність, але які є ремонтопридатними і служать своєрідними заготовками для цього виробництва.
Своєрідність даних процесів на відміну від виготовлення автомобілів, які відбуваються по схемі сировина-виготовлення- автомобіль, полягає в їх замкненості, а саме автомобіль-ремонт- автомобіль.
Під виробничим процесом ремонту автомобіля розуміють сукупність робіт по відновленню працездатності автомобіля, які виконуються в певній послідовності.
Під технологічним процесом розуміють ту частину виробничого процесу, протягом якої відбувається кількісна або якісна зміна ремонтованого об'єкту або його елементів, наприклад, відновлення зношених деталей, складання вузлів, агрегатів, автомобіля та ін.
118

Розділ 3. Технологічні процеси ремонту автомобілів
У виробничий процес ремонту, окрім основних (технологічних) процесів, входять також допоміжні роботи, які не приводять до зміни стану ремонтованого об'єкту: доставка автомобіля в ремонт, контроль якості ремонту, сортування деталей і т.п.
Виробничий процес капітального ремонту автомобілів складається з наступних основних елементів: приймання автомобіля в ремонт; зовнішнє очищення і миття автомобіля; розбирання автомобіля на агрегати і вузли; очищення, миття агрегатів, вузлів і деталей; дефектація деталей; відновлення зношених деталей; комплектування сполучень і вузлів; складання вузлів і агрегатів; обкатка, випробування, регулювання і фарбування агрегатів і вузлів; загальне складання, обкатка, випробування, регулювання і фарбування автомобіля; здача відремонтованого автомобіля. Якщо кінцевим продуктом ремонтного виробництва є не автомобіль, а агрегат (наприклад, двигун), то загальна схема виробничого процесу його ремонту аналогічна.
Особливістю структури виробничого процесу в ремонтному виробництві, в порівнянні з машинобудуванням, є наявність специфічних елементів: зовнішнього очищення і миття; розбирання автомобіля, агрегатів і вузлів; відновлення зношених деталей і ін.
Відремонтований автомобіль по кількості конструктивних елементів (іноді і по номенклатурі) може відрізнятися від нового, оскільки при ремонті для компенсації зносу застосовують додаткові прокладки, шайби і інші компенсатори.
Схема виробничого процесу ремонту автомобіля наведена на рис. 3.1.
119
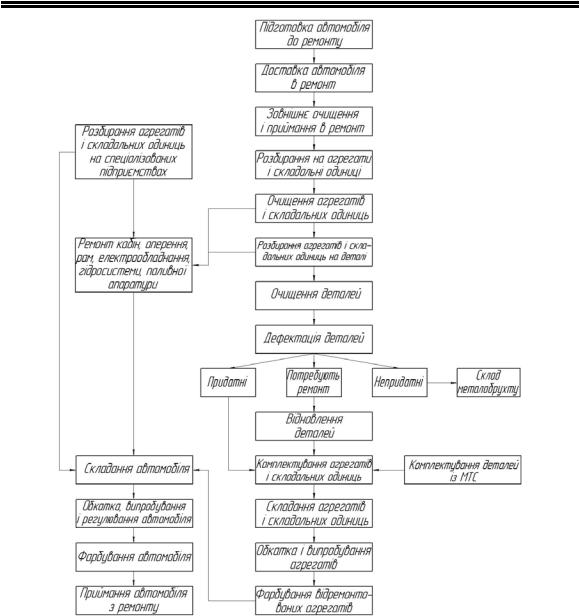
О.Й. Мажейка
Рис. 3.1. Схема виробничого процесу ремонту автомобіля
Структура технологічного процесу. Ступінь його розчленованості в багатьох випадках залежить від конструкції автомобіля і програми ремонтно-обслуговуючого підприємства. Якщо програма велика, то він складається із більшого числа технологічних процесів і включає багато робочих місць, і навпаки. Крім того, якщо автомобіль можна розчленувати на легко відокремлювані агрегати (двигун, коробку зміни передач,
120