
Режущий инструмент (часть2)
.pdf
Режущий инструмент. Конспект лекций |
54 |
|
9 ИНСТРУМЕНТЫ ДЛЯ ОБРАЗОВАНИЯ РЕЗЬБ
9.1 Общие положения проектирования и принципы работы резьбообразующих инструментов
Резьба - сложная винтовая поверхность, к которой предъявляются высокие требования по точности и чистоте обработки. Формообразование резьбы является сложным процессом, вследствие чего резьбообразующие инструменты работают в сложных условиях.
Наружную и внутреннюю резьбу получают следующими основными методами:
1)нарезания профиля резьбы (резцы, гребенки, метчики, плашки, резьбонарезные головки, резьбовые фрезы, шлифовальные круги);
2)пластического деформирования (резьбонакатные ролики и плашки для образования наружных резьб и бесстружечные метчики (раскатники) для образования внутренних резьб).
9.2 Резьбовые резцы и гребенки
9.2.1Резьбовые резцы
Резьбонарезной однолезвийный фасонный режущий инструмент, режущая кромка которого при обработке образует профиль резьбы всеми точками. Резцы предназначены для нарезания наружных и внутренних резьб различного профиля.
Основными преимуществами резьбонарезных резцов являются:
1)простота конструкции и технологии изготовления;
2)универсальность (возможность одни и тем же резцом нарезать резьбы различного диаметра и шага;
3)высокая точность расположения оси обработанной резьбы относительно цилиндрической и торцовой поверхностей заготовки;
4)возможность обработки резьб с переменным шагом и на конических поверхностях.
Резцы подразделяют:
1)по конструкции - на стержневые, призматические и круглые;
2)но форме режущей кромки - на однопрофильные и многопрофильные;
3)по исполнению режущего элемента - цельные, составные и сборные;
4)по виду работы - черновые и чистовые;
5)по типу нарезаемой резьбы - для метрической, для трапециидальной и специальной резьбы.
Нарезание резцами резьбы малого шага осуществляется за один проход. При нарезании резьб глубокого профиля (трапецеидальной, прямоугольной и т.п.) применяют последовательное многопроходного точение несколькими резцами различного профиля, причем полный профиль имеет последний чистовой резец.
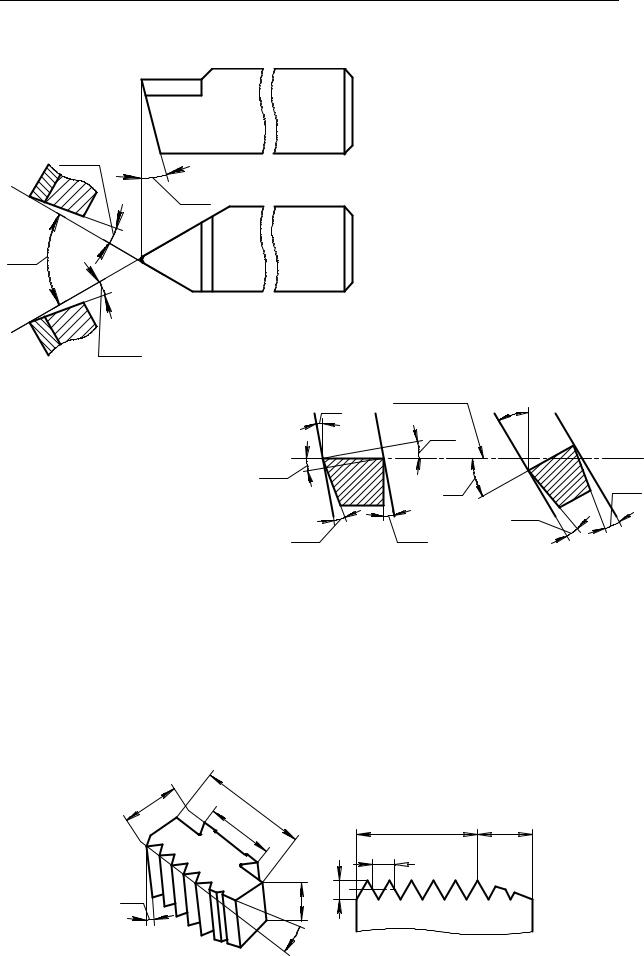
Режущий инструмент. Конспект лекций |
|
|
55 |
|||
|
|
|
|
|
|
|
|
|
Геометрия резьбовых резцов |
|
|
||
|
|
|
|
При малом угле |
подъема |
|
|
|
|
|
резьбы резец устанавливают таким |
||
|
|
|
|
образом, чтобы ось симметрии |
||
a'1 |
|
|
|
профиля резца была расположена |
||
|
|
|
перпендикулярно к оси заготовки |
|||
|
|
a |
|
(а). Задние углы на боковых ре- |
||
|
|
|
жущих кромках выполняют оди- |
|||
|
|
|
|
наковыми как для резцов из быст- |
||
e |
|
|
|
рорежущей стали, так и для резцов |
||
|
|
|
из твердых сплавов в пределах 4-6 |
|||
|
|
|
|
|||
|
|
|
|
градусов для предварительного и |
||
|
|
|
|
8-10 градусов для окончательного |
||
|
a'2 |
|
|
нарезания. Задний угол на верши- |
||
|
|
|
не принимают равным 15-20 гра- |
|||
Если |
угол |
подъема |
|
дусов. |
|
|
t |
Îñü |
|
|
|||
нарезаемой |
резьбы больше |
заготовки |
t |
|
||
3-4 градусов, то |
резец на- |
|
g2 |
|
g1 =g2 =0 |
|
клоняют к оси заготовки под |
|
|
|
|||
g1 |
|
|
|
|||
угломλ= τ(б) ипередние углы |
l |
|
a'2 |
|||
на боковых режущих кромках |
|
|
||||
|
|
a'1 |
|
|||
принимают |
одинаковыми, в |
|
|
|
||
a'1 |
a'2 |
|
|
|||
противном случае γЛ < 00 и |
|
á |
||||
|
|
|
à |
|
|
γП(γ2) > 0°.
Статический боковой задний угол α’, градусы определяется по формуле: tgα’ = tgα × sinε
9.2.2Резьбовые гребенки
Для уменьшения числа рабочих ходов и повышения производительности труда для изготовления крепежной и другой резьбы с мелким шагом применяют резьбовые гребенки.
Резьбовые гребенки подразделяются на призматические (для наружной резьбы) и круглые (как для наружной, так и для внутренней резьбы)
B
a
L
F
P
h
H
j
|
lÊ |
|
|
|
|
|
|
lÐÅÆ |
||||||
|
|
|
|
|
|
|
|
|
|
|
|
|
|
|
|
|
|
|
|
|
|
|
|
|
|
|
|
|
|
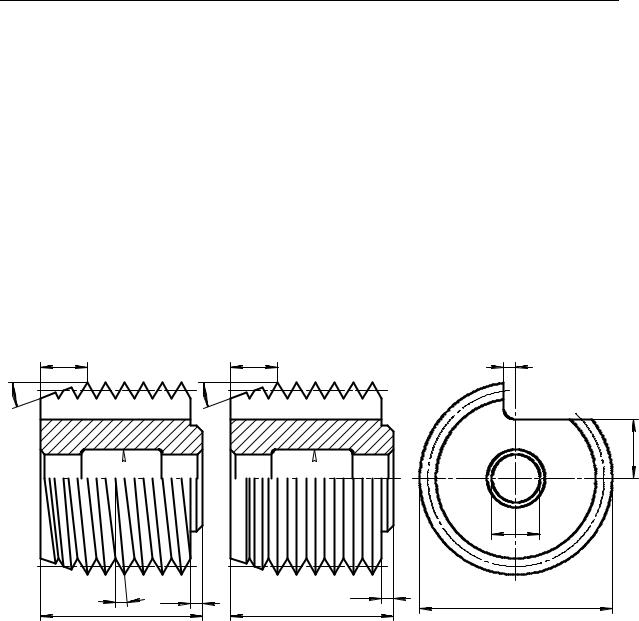
Режущий инструмент. Конспект лекций |
56 |
|
Рабочая часть гребенки имеет 6-8 шагов из них 1,5 ÷ 2 шага расположены на режущей части и 4,5 ÷ 6 шагов — на калибрующей. При нарезании резьбы напроход на режущей части может быть 3 ÷4 шага. Вершины зубчиков резьбы на режущей части срезаны, образуя заборный конус с углом ϕ равным 15 ÷ 30 градусов.
На практике более широкое применение получили круглые гребенки, как более простые в изготовлении и допускающие большее количество переточек. Круглые гребенки обычно делают насадными. Их конструктивные размеры определяются, так же как и у фасонных резцов.
Круглые гребенки бывают с кольцевыми витками и винтовыми. Проще и точнее в изготовлении являются винтовые гребенки, их профиль окончательно формируется на резьбошлифовальном станке. Направление резьбы винтовой гребенки обратно направлению резьбы детали при нарезании наружных резьб и совпадает при нарезании внутренних резьб.
lÐÅÆ |
lÐÅÆ |
j |
j |
|
|
|
|
|
|
|
|
|
|
|
|
|
|
|
|
|
|
|
|
|
|
1 |
|
|
1 |
|
|||||||||||||||||
|
|
|
|||||||||||||||||||
|
|
|
|||||||||||||||||||
|
|
|
|
|
d |
|
|
|
|
|
|
|
|
|
|
|
d |
|
|||
|
|
|
|
|
|
|
|
|
|
|
|
|
|
|
|
|
|
|
|
|
|
t |
lÁ |
lÁ |
L |
|
L |
h
A
d |
D |
9.3 Метчики
Метчики предназначены для образования резьбы в отверстиях. По принципу работы их подразделяют на метчики, образующие профиль резьбы путем снятия стружки, метчики бесстружечные, образующие профиль резьбы без снятия стружки, и метчики с режущими и выглаживающими зубьями, образующие резьбу комбинированным способом.
По конструкции и применению метчики делят на следующие типы:
1.Ручные (делают комплектами по 2 4 3 штуки).
2.Машинно-ручные (одинарные или комплект из двух штук).
3.Машинные для работе на станках.
4.Гаечные для нарезания резьбы в гайках как на гайконарезных автоматах (с изогнутым хвостовиком) так и на универсальных станках (с прямым хвостовиком).
5.Конические для нарезания конических резьб.
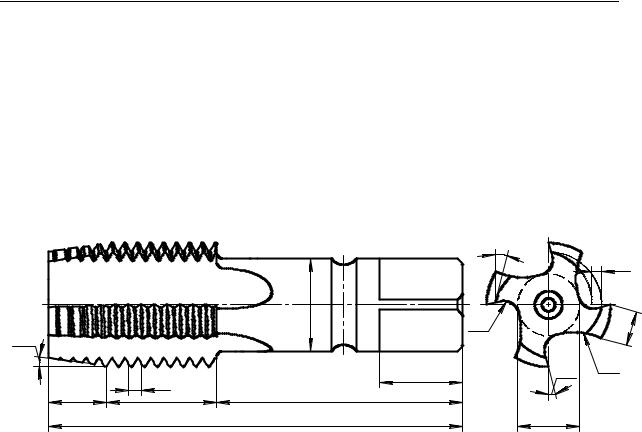
Режущий инструмент. Конспект лекций |
57 |
|
6.Метчики для круглой резьбы.
7.Метчики сборной конструкции нерегулируемые и регулируемые (резьбонарезные головки для внутренней резьбы).
8.Плашечные для нарезания резьбы в плашках.
9.Маточные для калибровки резьбы в плашках после сверления стружечных отверстий.
10.Специальные комбинированные (сверло-метчик, ступенчатые и др.).
Конструктивные и геометрические параметры метчика
d ÕÂ
j
|
Ð |
|
lÊÂ |
l |
l |
l |
|
ÐÅÆ |
|
Ê |
ÕÂ |
|
|
|
L |
a
Ê
r |
|
 |
|
|
|
|
g |
R |
|
|
|
|
dÑ |
|
К основным конструктивным и геометрическим параметрам относятся режущая и калибрующая части, хвостовая часть, число режущих перьев или канавок, диаметр сердцевины, передний угол, задний угол, величина затылования, форма и направление канавок.
Режущая часть (lРЕЖ). С целью сокращения номенклатуры инструмента рекомендуется применять метчики со следующей унифицированной длиной заборной части:
lРЕЖ = (2 ÷ 3) × Р – для глухих отверстий; lРЕЖ = (4 ÷ 6) × Р – для сквозных отверстий; lРЕЖ = (10 ÷ 12) × Р – для гаечных метчиков.
Режущая часть также характеризуется углом заборного конуса (ϕ), величина которого зависит от свойств обрабатываемого материала вида метчика и точности нарезаемой резьбы:
для гаечных метчиков ϕ = 3 ÷ 40; для машинных метчиков ϕ = 10 ÷ 200; для ручных метчиков ϕ = 3 ÷ 70.
При нарезании резьбы втитановых и жаропрочных сплавах lРЕЖ = (12 ÷ 20) × Р.
Калибрующая часть (lК). Калибрующая часть служит для зачистки и калибрования резьбы. Для снижения сил трения и уменьшения величины разбивки отверстия калибрующая часть имеет обратную конусность, составляющую
0,05 ÷ 0,12 мм на 100 мм длины.
Длина калибрующей части для машинных и гаечных метчиков составляет 8 шагов, а для ручных от 6 до 8.

Режущий инструмент. Конспект лекций |
58 |
|
Хвостовая часть (1хв) – Диаметр хвостовика (dХВ) принимается меньше внутреннего диаметра резьбы метчика на 0,5 ÷ 1,5 мм. Хвостовик выполняется с квадратом на конце для передачи крутящего момента. Для зажима машинных метчиков в технологическом оборудовании на хвостовике метчика предусмотрена радиусная выточка.
Число режущих перьев (Z) зависит в основном от, шага резьбы (Р) и толщины срезаемого слоя (аZ) и угла заборного конуса (ϕ).
Z = P ×tgϕ aZ
Толщина срезаемого слоя должна быть такая, чтобы получить необходимую шероховатость обработанной поверхности и нужное качество поверхностного слоя. Исследования показывают, что этим условиям удовлетворяет тол-
щина0,02 ÷ 0,15 мкм.
В зависимости от наружного диаметра метчика (D) число режущих
перьев находится в следующих пределах: |
|
для D = 2 ÷ 20 мм |
Z = 2 ÷ 3; |
для D = 21 ÷ 36 мм |
Z = 3 ÷ 4; |
для D = 37 ÷ 52 мм |
Z = 4 ÷ 6. |
Ширина режущих перьев (В) должна быть достаточной по условиям прочности и допускать несколько переточек метчика по передней поверхности. Вместе с тем ширина пера не должна быть слишком большой, так как это приводит к увеличению сил трения. Исходя из этого ширина пера определяется:
В = (0,3 ÷ 0,32) × D |
при Z = 3; |
В = (0,2 ÷ 0,22) × D |
при Z = 4; |
В = (0,16 ÷ 0,18) × D |
при Z = 6. |
Диаметр сердцевины (dC) рассчитывается исходя изусловияпрочности
метчика и в зависимости от числа зубьев принимается равным: dС = (0,35 ÷ 0,40) при Z = 3;
dС = (0,42 ÷ 0,45) при Z = 4; dС = (0,52 ÷ 0,55) при Z = 6.
Для увеличения объема стружечных канавок и создания условий для более свободного размещения стружки диаметр сердцевины уменьшают к началу режущей части на (0,1 ÷ 0,2) × dC.
Углы резания у метчиков имеют весьма важное значение, так как они работают в трудных условиях образования внутренней резьбы.
Передний угол (γ) принимают одинаковым как для режущей, так и для калибрующей частей, он зависит от физико-механических свойств обрабаты-
ваемого материала: |
γ = 0 ÷ 50; |
при обработке чугуна, твердой стали, хрупкой латуни и бронзы...... |
|
для стали средней твердости и латуни................................................. |
γ = 8 ÷ 100; |
для вязкой стали и меди......................................................................... |
γ = 12 ÷ 150; |
для алюминия и других вязких цветных металлов.............................. |
γ= 16 ÷ 250. |
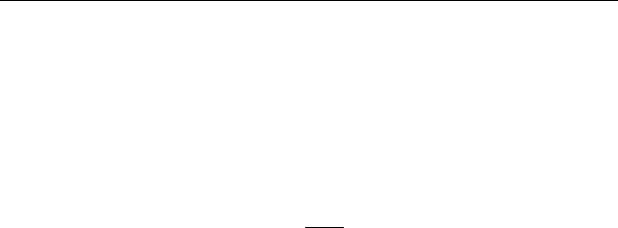
Режущий инструмент. Конспект лекций |
|
|
59 |
Задний угол на вершине режущих кромок (α) в основном зависит от |
|
вида метчика и вида отверстия (сквозное или глухое): |
|
для ручных и машинно-ручных при обработке глухих отверстий |
|
и метчиков к станкам с ЧПУ.......................................................................... |
α = 4 ÷ 60; |
для гаечных и машинно-ручных при обработке сквозных от- |
|
верстий...................................................................................................................... |
α= 8 ÷ 120. |
Задний угол получают затылованием задней поверхности по архиме- |
|
довой спирали. Величина затылования определятся по следующей формуле: |
K = π ×Zd1 ×tgα
где d1 – внутреннийдиаметррезьбы метчика, мм; Z – числоперьевметчика.
У метчиков, не шлифованных по профилю, задние углы не создают на боковых режущих кромках, так как они являются вспомогательными. Для создания более точной и качественной резьбы применяют шлифованные метчики. Шлифованные метчики на режущей части затылуются по всему профилю зубьев, вследствие чего повышаются и режущие свойства инструмента.
Шлифованные метчики затылуются по всему профилю и на калибрующей части. Это необходимо для того, чтобы исключить налипание металла на
боковые поверхности резьбы метчика, особенно при обработке вязких материалов. Величина затылования принимается небольшой от 0,01 (для D = 4 мм) до 0,1 мм (для D = 52 мм) во избежание защемления стружки при обратном вращении.
Форма и направление канавок.
Существующие формы канавок можно подразделить на два вида: канавки, имеющие радиусную переднюю поверхность, и канавки, образующие плоскую переднюю поверхность.
Канавки могут быть прямыми, наклонными и винтовыми (так же как и у разверток).
Некоторые разновидности метчиков
Метчики с укороченными канавками (для повышения прочности метчиков малого диаметра)
Метчики с шахматной резьбой (для обработки вязких материалов, что способствует увеличению пространства для размещения стружки).
Твердосплавные метчики.
Метчики сборной конструкции (как нерегулируемые так регулируемые - резьбовые головки которые могут включаться и выключаться автоматически).
Бесстружечные метчики (треугольные, квадратные и шестигранные)
9.4 Плашки
Плашки служат для нарезания наружной резьбы на болтах, винтах, шпильках и других деталях.
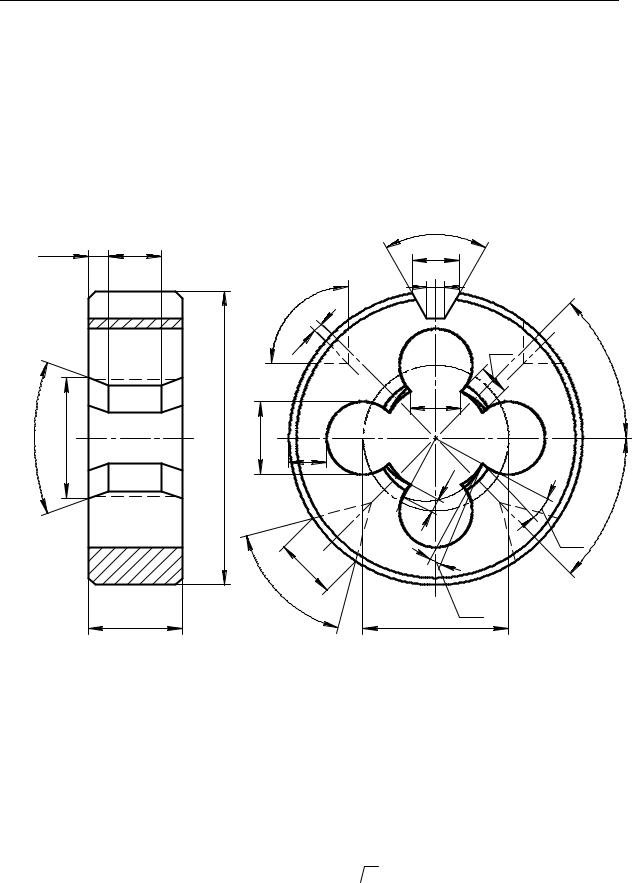
Режущий инструмент. Конспект лекций |
60 |
|
Плашки бывают круглые, квадратные, шестигранные, трубчатые, плоские и призматические разъемные к слесарным вороткам.
Наибольшее распространение получили круглые плашки.
Круглые плашки представляют собой гайку, превращенную в инструмент путем сверления стружечных отверстий и образования режущей части с за-
тылованными зубьями.
Конструктивные и геометрические параметры круглой плашки
|
lÐÅÆ |
lÊ |
|
|
60Å |
|
|
|
|
|
|
|
|
|
b |
|
|
|
|
|
|
||
|
|
|
|
|
a |
|
|
|
|
|
|
|
|
|
|
|
Å |
|
|
|
|
|
|
|
|
|
|
|
0 |
|
|
|
|
|
|
|
|
|
|
|
9 |
|
|
|
|
|
|
|
|
|
|
|
e |
F |
|
|
|
|
5 |
|
|
|
|
|
|
|
|
|
|
|
4 |
|
|
|
|
|
|
|
|
|
|
|
Å |
|
|
|
|
|
|
|
|
|
|
|
± |
|
|
|
|
|
|
|
|
|
|
|
3 |
|
|
|
|
|
|
|
|
|
|
|
0 |
|
|
|
|
|
Ñ |
|
|
|
|
|
' |
|
|
|
|
|
|
|
|
|
|
|
|
2f |
D |
|
D |
d |
|
|
|
|
|
|
|
|
Ç |
|
|
Ñ |
T |
|
|
|
|
|
|
|
|
|
|
|
|
|
|
|
|
|
|
|
|
|
|
|
K |
|
|
|
|
|
' |
|
|
|
|
|
|
|
|
|
|
|
|
|
|
|
|
|
|
|
|
|
|
|
0 |
|
|
|
|
|
|
|
|
|
|
3 |
|
|
|
|
|
|
|
|
|
|
Å |
± |
|
|
|
|
|
|
|
|
g |
4 |
5 |
|
|
|
|
|
|
|
|
|
|
|
|
||
|
|
|
|
|
d |
|
|
|
|
|
|
|
|
|
|
|
|
|
|
|
|
|
|
|
|
|
|
|
3 |
|
|
|
|
|
|
|
|
|
|
|
6 |
|
|
|
|
|
|
|
|
|
|
|
0 |
|
|
|
|
|
|
|
|
|
|
|
Å |
a |
|
|
|
|
|
|
|
 |
|
|
d |
|
|
|
|
|
|
|
|
|
|
Ö |
|
|
|
|
|
|
К конструктивным и геометрическим элементам круглых плашек относятся: наружный диаметр (D), число и диаметр стружечных отверстий (dС) и их центров (dЦ), толщина плашки (В), ширина перьев (F) и просвета между ними (С), угол конуса режущей части (2ϕ), передний (γ) и задний (α) углы резания и элементы крепления плашки.
Наружный диаметр (D) зависит от диаметра обрабатываемой резьбы, диаметра стружечных отверстий (dC) и диаметра окружности размещения их центров(dЦ):
D = dЦ + 2 × dС + 2 × Т
где Т– толщинастенкиплашки T =(1,0 ÷1,2)× D ;
dС, dЦ - диаметр стружечных отверстий и диаметр расположения их центров зависят ширины просвета стружечного отверстия (С), диаметра резьбы, формы передней поверхности (прямолинейная или криволинейная).

Режущий инструмент. Конспект лекций |
61 |
|
Криволинейную поверхность легче получить, однако передний угол по высоте профиля резьбы получается непостоянным.
Число стружечных отверстий рекомендуется принимать в зависимости от диаметра резьбы и колеблется от 3 (при d равном 1 мм) до 12 (при d равном
76 мм).
Толщина плашки (В) определяется по формуле:
В = 2 × 1РЕЖ + lК
где 1К – длина калибрующей части, мм. Принимается равной (3 ÷ 8) Р, в зависимости от вида плашки.
1РЕЖ – длина заборного конуса (режущей части) которая характеризуется углом заборного конуса ф.
1РЕЖ = (t + а) × ctg ϕ
где t – высота профиля нарезаемой резьбы, мм.
а – превышение высоты заборной части над высотой резьбы, необходимое для направления плашки, мм. а = 0,15 ÷ 0,40 мм.
Угол заборного конуса (ϕ) зависит от свойств обрабатываемого мате-
риала: |
2ϕ = 300; |
для высокопрочных сталей................................................. |
|
для легких сплавов и цветных материалов....................... |
2ϕ = 700; |
для стандартных плашек .................................................... |
2ϕ = 500. |
Передний угол (γ) принимается в зависимости от свойств обрабатывае- |
|
мого материала: |
γ = 10 ÷ 120; |
для твердых материалов...................................................... |
|
для материалов средней твердости.................................... |
γ = 15 ÷ 200; |
для легких материалов......................................................... |
γ = 20 ÷ 250; |
у стандартных плашек......................................................... |
γ = 15 ÷ 200; |
Задний угол (α) получается затылованием по вершинам на длине заборного конуса и находится в пределах от 6 до 9 градусов. Расчет величины затылования производится так же как и у метчиков.
Элементы крепления плашки.
При работе плашку устанавливают в гнездо плашкадержателя (на станке) или воротка (ручная нарезка) и закрепляется специальными винтами. Для этого у плашки делают гнезда в виде конических углублений. Нижние гнезда с углом 60 градусов - установочные, а верхние с углом 90 градусов - поджимные.
Перемычка используется для переточки плашки после ее износа (ее разрезают и сжимают при помощи поджимных винтов, а потом перетачивают и восстанавливают)
Режущий инструмент. Конспект лекций |
|
|
|
62 |
|
|
|
|
|
10 ИНСТРУМЕНТЫ |
ДЛЯ |
ОБРАБОТКИ |
ЗУБЬЕВ |
|
ЦИЛИНДРИЧЕСКИХ КОЛЕС |
|
|
|
|
10.1Основные вопросы проектирования зуборезных инструмен-
тов
Цилиндрические зубчатые колеса широко применяют в машиностроении и приборостроении. Нарезание зубьев колес может производиться методом фасонного копирования и методом обкатывания или огибания.
При методе копирования профиль впадины между зубьями колеса полностью соответствует профилю зубьев инструмента. Нарезание всех зубьев колеса производится способом деления, в результате чего данный метод не отличается точностью. Поэтому данный способ используется редко, главным образом в единичном производстве и ремонтных целях.
При методе обкатывания нарезание всех зубьев колеса производится непрерывно в результате качения без скольжения начальной окружности или начальной прямой рейки зуборезного инструмента по начальной окружности колеса. В результате этого профиль нарезаемого зуба получается как огибающая к ряду последовательных положений режущих кромок инструмента.
Существует еще метод бесцентроидного огибания, при котором центроиды отсутствуют, качения начальных окружностей друг по другу нет, а профиль зуба колеса является огибающей к различным положениям производящей поверхности инструмента. По этому методу нарезаются винтовые и шевронные зубчатые колеса дисковыми и пальцевыми фрезами
10.2 Инструменты, работающие с профилированием по методу фасонного копирования
Зуборезными инструментами, работающим методом фасонного копирования, являются дисковые и пальцевые зуборезные фрезы, зубодолбежные головки и протяжки.
Профиль зубьев инструментов определяется по профилю впадины между зубьями нарезаемого колеса. Эвольвентный профиль впадины или зубьев колеса зависит от угла зацепления, числа зубьев, диаметра делительной окружности. Кроме того, должны быть известны модуль, толщина зуба по делительной окружности в нормальном сечении, высота головки и ножки зуба колеса.
Составляют расчетную схему таким образом, чтобы начало координат совпадало с центром нарезаемого колеса
10.2.1 Дисковые модульные фрезы
Дисковые зуборезные фрезы применяют для нарезания прямозубых и косозубых цилиндрических колес 11-9 степеней точности. В первом случае они работают методом фасонного копирования, во втором случае, при нарезании косозубых колес, они работают методом бесцентроидного огибания. Во всех
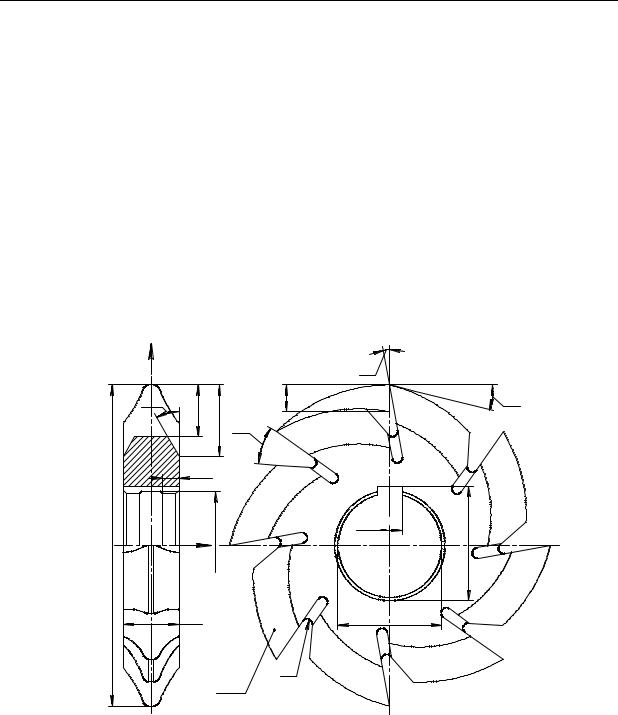
Режущий инструмент. Конспект лекций |
63 |
|
случаях процесс последовательной обработки впадин производится путем деления заготовки на один окружной шаг. Этот метод обработки зубьев является малопроизводительным и низкой точности, что обусловливается погрешностью делительного механизма, погрешностями установки оси симметрии зуба фрезы по оси симметрии впадины между зубьями колеса.
Дисковые модульные фрезы проектируют и изготавливают наборами по 8 и 15 штук (в зависимости от количества нарезаемых зубьев 1- 13, а 8 - 135 и более).
К конструктивным и геометрическим параметрам фрезы относится: диаметр фрезы (D), диаметр посадочного отверстия (d), параметры шпоночного паза (bШ и С1), ширина фрезы (В), количество зубьев (Z), высота зуба фрезы (Н), угол профиля фрезы (α’) соответствующий углу профиля (зацепления) нарезаемого колеса, геометрические параметры режущего клина (углы γ и α), угол стружечной канавки (Θ), радиус дна канавки (г).
Y |
a' |
h' |
Í |
l1 |
Õ |
D |
 |
d |
 |
|
g |
Ê |
a |
Q |
|
bØ
Ñ 1
d
r
Z=8
10.2.2 Пальцевые модульные фрезы
Пальцевые модульные фрезы применяют для обработки крупномодульных прямозубых, косозубых и шевронных цилиндрических зубчатых колес .Так же как и дисковые зуборезные фрезы, при нарезании прямозубых колес они работают методом копирования и деления, а при нарезании косозубых и шевронных колес - методом бесцентроидного огибания и деления. В первом случае профиль зубьев фрезы соответствует профилю впадины зубчатого колеса, во втором случае этого соответствия нет. Профилируются они так же, как и дисковые зуборезные фрезы.