
Режущий инструмент (часть2)
.pdf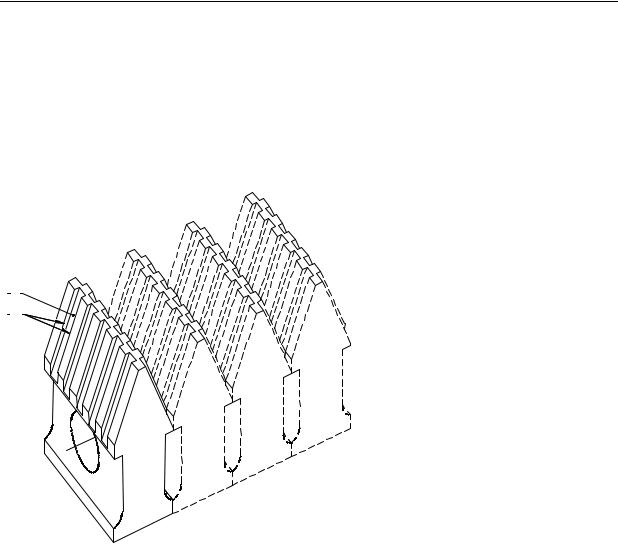
Режущий инструмент. Конспект лекций |
74 |
|
Окружная скорость на начальной окружности шевера из быстрорежущей стали VО = 100...120 м/мин, скорость продольной подачи VSпр. = 0,15...0,10 мм/об заготовки, скорость радиальной подачи VSpaд.. = 0,02...0,04 мм/дв.ход.
Обычно прямозубые колеса обрабатываются косозубыми шеверами, а косозубые – прямозубыми.
10.2.4.1 Шевер-рейка
1
2
Представляет собой зуборезную рейку, сопряженную с обрабатываемым колесом, состоящую из отдельных зубьев смонтированных в корпусе на боковых поверхностях, которых прорезаны стружечные канавки 1 (шириной 0,8...1,0 мм, глубиной 1 мм, с шагом 1,6...2 мм) с режущими кромками 2.
Длина шевер-рейки L, мм, выбирается из условия обработки всех зубьев колеса:
L = π ×mn ×(ZK +n) cos β0
где Zк – число зубьев колеса;
n - число зубьев запаса, учитывающие гарантированную обработку колеса. n = 2…4;
β0 – угол наклона зубьев шевера.
Ширина шевер-рейки берется в 3 - 4 раза больше ширины колеса, что позволяет за счет периодических перемещений заготовки колеса поперек рейки увеличить срок службы шевер-рейки.
Шевер-рейки не получили широкого распространения из-за дороговизны, сложности изготовления и монтажа
10.2.4.2 Дисковые шеверы
Дисковый шевер представляет собой цилиндрическое колесо с прямыми или наклонными зубьями, на боковых поверхностях которых нарезаны канавки
иобразованы режущие кромки.
Впроцессе окончательного образования зубьев колеса его зубья и зубья шевера должны зацепляться с одной и той же косозубой инструментальной рейкой. Поэтому у шевера и колеса в сечении, нормальном к направлению их зубьев, должны быть равны шаги, углы профиля и высотные размеры зубьев.
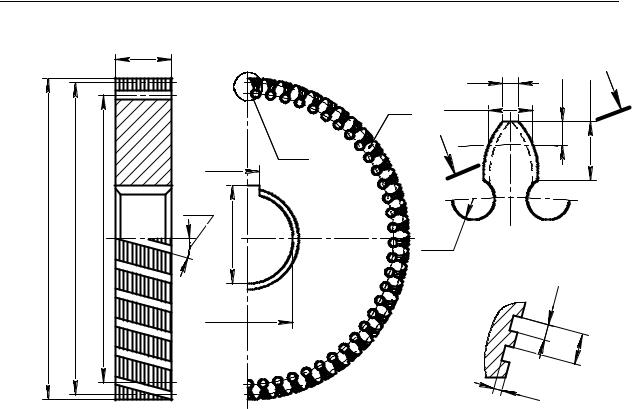
Режущий инструмент. Конспект лекций |
75 |
|
 |
S' |
Á |
|
|
|
|
|
|
|
Z |
S |
at |
È |
 |
tÈ |
h |
h' |
|
|
Á |
 |
|
|
|
b |
|
|
|
bÈ
È |
Ö |
1 |
Rö |
Dà d |
d |
C |
|
|
Â-Â |
|
dÎÒÂ. |
S |
Ê |
|
||
|
|
Ð |
Ê |
|
h |
Ê |
Диаметральные размеры шевера определяют в торцовом сечении, поэтому размеры должны быть пересчитаны в торцовое сечение.
P |
= |
Pnи |
= π ×mn |
, |
m |
= |
mn |
, |
tgα |
tИ |
= |
tgαnи |
|
|
|
||||||||||
tИ |
|
cos βИ |
cos βИ |
|
t |
|
cos βИ |
|
|
|
cos βИ |
|
|
|
|
|
|
|
|
|
|
Диаметр делительной окружности шевера dtИ, мм dtИ = mtИ × ZИ
При шевинговании каждая впадина зубьев колеса обрабатывается одним зубом шевера. При кратном числе зубьев шевера и колеса может повторяться совпадение их зубьев в процессе обработки. Для того чтобы избежать совпадения контакта одних и тех же зубьев при следующих оборотах колеса, число зубьев шевера не должно иметь общих множителей с числом зубьев обрабатываемого колеса. Для соблюдения этого условия число зубьев стандартных шеверов принимают из ряда первоначальных чисел: 29, 31, 37, 41, 43, 47, 53, 61, 67, 73, 83 и только в одном случае 27 (для m = 8 мм).
Высота головки зуба шевера должна обеспечить полную обработку активной рабочей части профиля зуба колеса, поэтому ее делают несколько больше высоты головки зуба сопряженного колеса, но головка зуба шевера не должна обрабатывать дно впадины зуба колеса.
Обычно для обработки колес с h'a = 1 коэффициент высоты головки зуба шевера принимают равным 1,1. Затупившиеся шеверы восстанавливают шлифованием задних поверхностей зубьев. Новые шеверы проектируют с учетом припуска на переточку по толщине зуба и соответственно по головке зуба. По мере переточек смещение уменьшается. Коэффициент смещения Хо нового шевера определяется припуском ∆S на перешлифовку, т. е. увеличением толщины зуба в нормальном сечении на обе стороны.
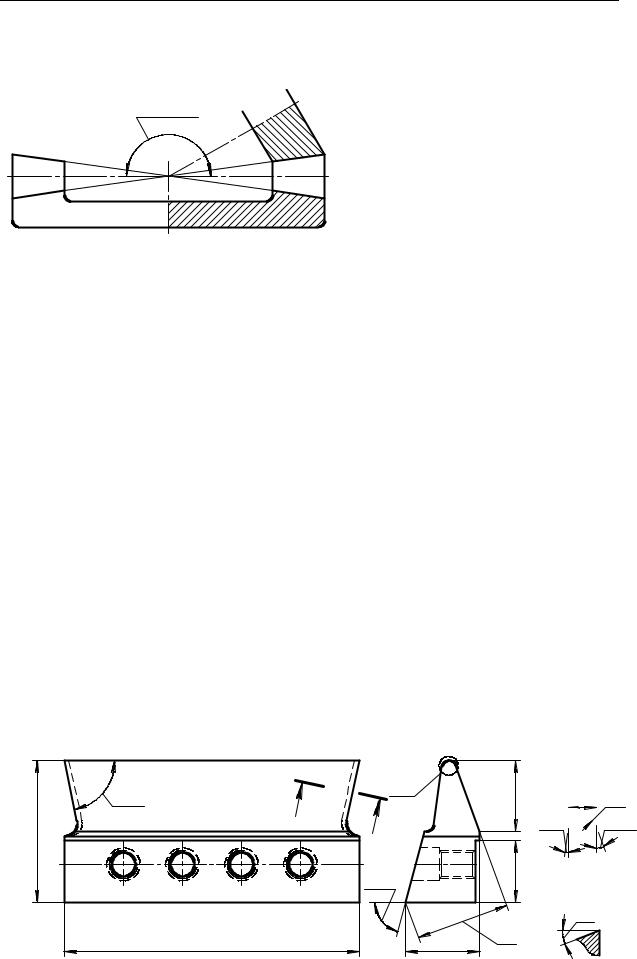
Режущий инструмент. Конспект лекций |
|
|
|
|
|
76 |
|
|
|
|
|
|
|
11 ИНСТРУМЕНТЫ |
ДЛЯ |
ОБРАЗОВАНИЯ |
|
ЗУБЬЕВ |
||
КОНИЧЕСКИХ КОЛЕС |
|
|
|
|
|
|
2d=180Å |
|
При |
|
образовании |
зубьев |
|
|
конического |
зубчатого |
колеса и |
|||
|
определении их размеров используют |
|||||
|
принцип |
зацепления |
образуемого |
|||
|
колеса с |
плоским производящим |
||||
|
колесом, угол делительного конуса |
|||||
|
этого |
колеса |
равен 90° |
т.е. дели- |
тельный конус лежит в плоскости. Этот принцип аналогичен образованию и определению размеров зубьев цилиндрических зубчатых колес при зацеплении с исходным контуром.
Инструменты при образовании зубьев копируют впадину исходного производящего колеса, например зубострогальные резцы, или его зуб зуборезные головки
Обработка обеих сторон зубьев конического колеса, учитывая изменяющиеся размеры по их длине, должна производиться разными инструментами с различными образующими движениями; для каждой стороны зуба колеса главное движение, обеспечивающее движение резания, может быть вращательное (применяют резцовые головки, фрезы) или продольно-поступательное (зубострогальные резцы), совпадающие с направлением образуемых зубьев колеса.
Для образования зубьев криволинейной продольной формы наибольшее применение имеют зуборезные головки, продольная форма зубьев образуется по дуге окружности
11.1Инструменты для нарезания прямозубых конических колес
11.1.1Зубострогальные резцы
Зуборезные или зубострогальные резцы применяют для обработки прямозубых конических колес, имеющих модуль 0,3 – 20 мм.
Нарезание зубьев производится на специальных зубострогальных станках типа 5П23 методом прерывистого обкатывания.
H
78Å |
Á |
|
L
À
h È
Á |
|
|
75Å |
|
K |
|
|
|
|
B |
C |
|
|
À
b R 8Å 20Å
Á-Á
g
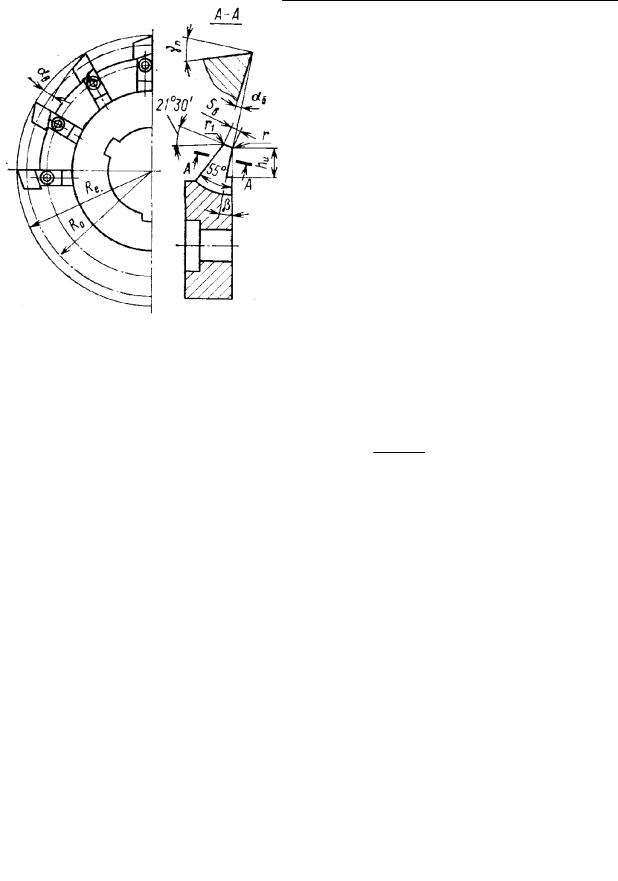
Режущий инструмент. Конспект лекций |
77 |
|
Резец представляет собой призматическое тело. Рабочая часть его делается в виде зуба асимметричной прямоточной рейки высотой hи = 3m.
Величина С является постоянной для каждой модели станка. Она определяет положение режущей кромки относительно опорного клина. Толщина резца В зависит от толщины зуба нарезаемого колеса по окружности начального конуса
Передний угол для вершинной режущей кромки равен нулю. Эта кромка вспомогательная, но наиболее нагруженная по условиям резания. Создать другой передний угол для вершинной кромки конструктивно трудно и не целесообразно, учитывая динамику процесса резания.
Передний угол у резцов в плоскости, нормальной к главной режущей кромке, 10 – 25°. Для стандартных резцов 20°.
Задний угол αВ в рабочем положении резца принимается равным 12°. Задний угол в сечении, нормальном к главной режущей кромке:
tgαN = tgαB ×sinα
Угол профиля резца в нормальном сечении к основанию определяется из соотношения:
tgα1 = tgα0 × cosαε cos B
где ε - угол ножки зуба колеса.
11.1.2 Дисковые зуборезные головки
Нарезание прямозубых конических колес двумя дисковыми головками является высокопроизводительным способом. По производительности он в 3—5 раз превосходит нарезание колес зубострогальными резцами. Поэтому этот способ в основном применяют в массовом и крупносерийном производстве.
Сущность метода — прерывистое обкатывания, где возвратно-поступательное движение резцов заменено вращательным движением двух головок в виде дисковых фрез, которые вместе с люлькой станка обкатываются по заготовке так же, как и резцы. Обработка производится на специальных станках типа 5230.
Головки имеют наружный диаметр D = 150 мм для обработки прямозубых колес небольших модулей до 3 мм, D = 278 мм для колес средних модулей
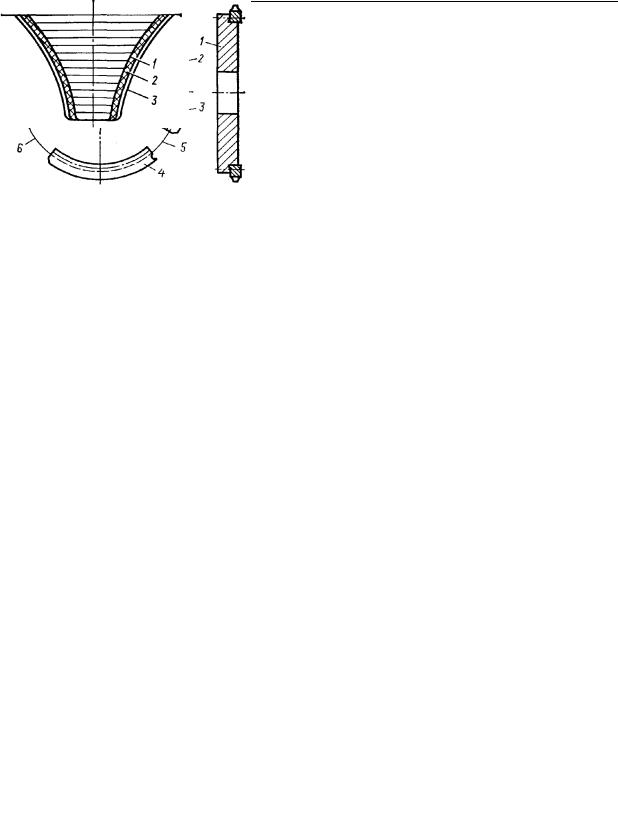
Режущий инструмент. Конспект лекций |
78 |
|
до 8 мм и D = 450 мм для колес m = 3 – 12 мм. Высота режущей части зуба hи = (3 - 4) × m, ширина зуба по вершине Sв такая же, как и у зубострогальных резцов. Размеры резцов головок приведены в ГОСТ 24905 - 81 Е.
Особенностью способа нарезания колес дисковыми головками является отсутствие подачи вдоль обрабатываемого зуба. В результате чего дно впадины между зубьями получается немного вогнутым. Небольшая вогнутость впадины не оказывает никакого влияния на качество зацепления зубчатых колес, так как она находится в пределах радиального зазора.
11.1.3 Круговые протяжки
Производительность метода зубопротягивания в 5—8 раз выше, чем при нарезании зубьев конических колес зубострогальными резцами. Качество нарезаемых колес не ниже чем при обработке их зубостроганием. Но круговые протяжки — это сложные и дорогостоящие инструменты. Для работы ими требуются специальные зубопротяжные станки типа 5С269. Поэтому метод применяется в массовом производстве.
Круговые протяжки делают сборной конструкции диаметром 540—630 мм. Корпус 1 в виде диска имеет с одной стороны у периферии опорную поверхность для установки и базирования резцовых блоков, выполненных из быстрорежущей стали. Каждый блок резцов имеет пять зубьев и крепится к корпусу протяжки двумя винтами.
На протяжке участки 5 и 6 свободны от резцов. Участок 5 необходим для установки приспособления для снятия фасок у зубьев колеса, участок 6 для поворота заготовки на один шаг для обработки следующей впадины. Протяжка вращается непрерывно, пока не будут нарезаны все зубья на обрабатываемом колесе.
Схема удаления металла при протягивании:
1— черновые резцы;
2— получистовые резцы;
3— чистовые резцы.
Схема резания - генераторная
11.2 Инструменты для нарезания конических колес с круговыми зубьями
11.2.1 Зуборезные головки
Нарезание зубьев колес головками производится на специальных зуборезных станках типа 5С26В.

Режущий инструмент. Конспект лекций |
79 |
|
В процессе нарезания происходит согласованное вращение заготовки и плосковершинного производящего колеса, роль которого выполняет люлька станка с резцовой головкой. Роль зуба производящего колеса выполняют резцы головки. При вращении головки они как бы находятся в беззазорном зацеплении с обрабатываемым колесом и в обкаточном движении профилируют зуб заготовки, удаляя металл из впадины. Профиль зуба обрабатываемого колеса получается как огибающая ряда последовательных положений режущих кромок резцов головки.
Таким образом, так же как и для прямозубых конических колес, обработка конических колес с круговыми зубьями производится методом прерывистого обкатывания.
Конические колеса с круговыми зубьями нарезают различными способами. Основными из них являются односторонний, простой двусторонний и двойной двусторонний. Применение того или другого способа определяется точностью зубчатой передачи, производительностью, номенклатурой инструмента, типом производства.
Односторонний способ характеризуется тем, что вогнутая и выпуклая стороны зубьев шестерен и колеса нарезаются раздельно. Этот способ имеет различные варианты обработки.
1.Каждая сторона зуба шестерни и колеса нарезается отдельными головками при различных установках. Здесь для чистовой обработки требуются четыре односторонние головки. Вариант наиболее точный, но наименее производительный.
2.Ведущее колесо нарезается по первому варианту. Ведомое колесо нарезается одной двусторонней головкой с поворотом заготовки вокруг ее оси на угол, при котором обеспечивается необходимая толщина зуба. При этом требуются три головки: две односторонние для ведущего колеса и одна двусторонняя для ведомого колеса.
3.Каждое из сопряженных колес нарезается своей двусторонней головкой с раздельной обработкой вогнутой и выпуклой стороны зубьев. После нарезания одной стороны зубьев производится переналадка на другую сторону зубьев. Заготовка поворачивается относительно своей оси на угол, обеспечивающий необходимую толщину нарезаемого зуба. В этом варианте требуются две двусторонние головки. В целом односторонний способ нарезания обеспечивает высокую точность, наиболее благоприятную форму зубьев сопряженных колес, но весьма трудоемок. В основном применяется в единичном и мелкосерийном производстве.
Простой двусторонний способ — такой, когда каждая сторона зубьев ведущего колеса нарезается отдельно своей односторонней головкой, а вогнутая и выпуклая стороны зубьев, т. е. впадина ведомого колеса, нарезаются двусторонней головкой за одну установку. Таким образом, для обработки сопряженных колес этим способом требуются три головки: две односторонние для ведущего колеса и одна двусторонняя для ведомого колеса. Этот способ обес-
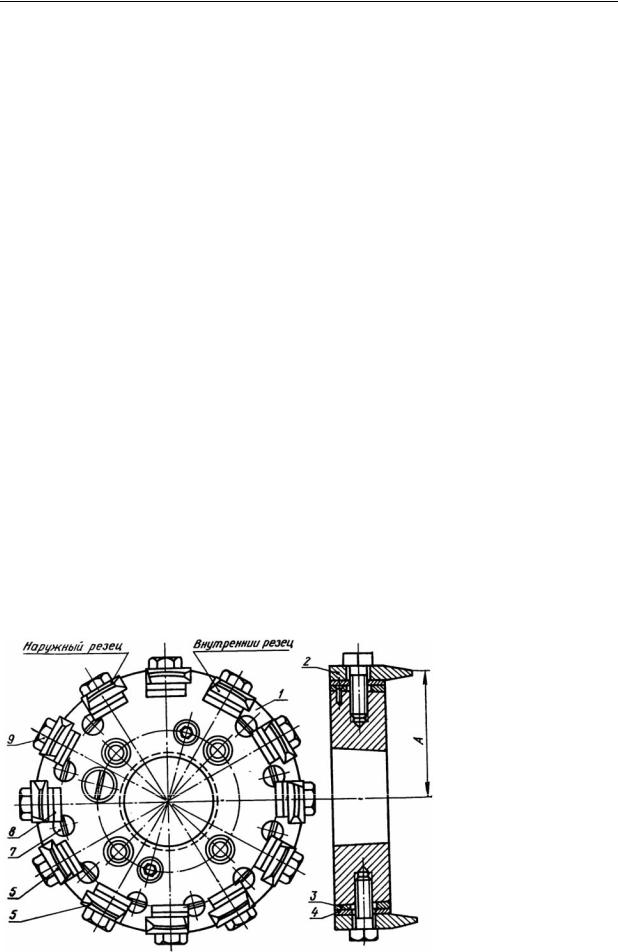
Режущий инструмент. Конспект лекций |
80 |
|
печивает высокую производительность и достаточно удовлетворительную точность — зону контакта сопряженных колес. Применяется в массовом и серийном производстве.
Двойной двусторонний способ характеризуется тем, что обе стороны зубьев каждого из сопряженных колес нарезаются одновременно своими двусторонними головками. Здесь требуется всего две двусторонние головки с определенным разводом зубьев. Способ наиболее производительный, но наименее точный. Применяется в массовом производстве для колес небольших модулей (т < 3 мм) и для колес невысокой точности.
Рассмотренные способы применимы для чистовой обработки зубьев колес. Черновое нарезание обоих колес производится двойным двусторонним способом методом обкатывания или же методом врезания двусторонними головками.
Зуборезные головки делают односторонними, двусторонними и трехсторонними. Односторонние головки служат для чистовой обработки только одной стороны зубьев — вогнутой или выпуклой — ведущего колеса.
Двусторонние зуборезные головки имеют два концентричных ряда чередующихся наружных и внутренних резцов, имеющих определенный их развод. Эти головки в основном применяют для чистовой обработки ведомого колеса, а в единичном и мелкосерийном производстве для черновой и чистовой обработки как ведущего, так и ведомого колеса. Черновые двусторонние головки не имеют регулировочных клиньев для развода резцов. В радиальном направлении резцы регулируются только подкладками.
Трехсторонние головки снабжены третьим рядом чередующихся резцов в такой последовательности: средний — наружный — средний — внутренний и т. д.
Наружные и внутренние резцы обрабатывают боковые стороны зубьев и не работают вершинами. Средние резцы обрабатывают только впадину.
Резцовая головка состоит из корпуса 1, в пазах которой с помощью винтов 9 крепятся наружные 6 и внутренние 5 резцы. Точная установка и регулировка резцов 2 относительно центра резцовой головки осуществляется за счет регулировочных клиньев 3 и прокладок 4 и 8. Регулирование клиньев производят винтами 7. Два резца головки являются нерегулируемыми в радиальном направлении и служат установочными для остальных резцов головки.
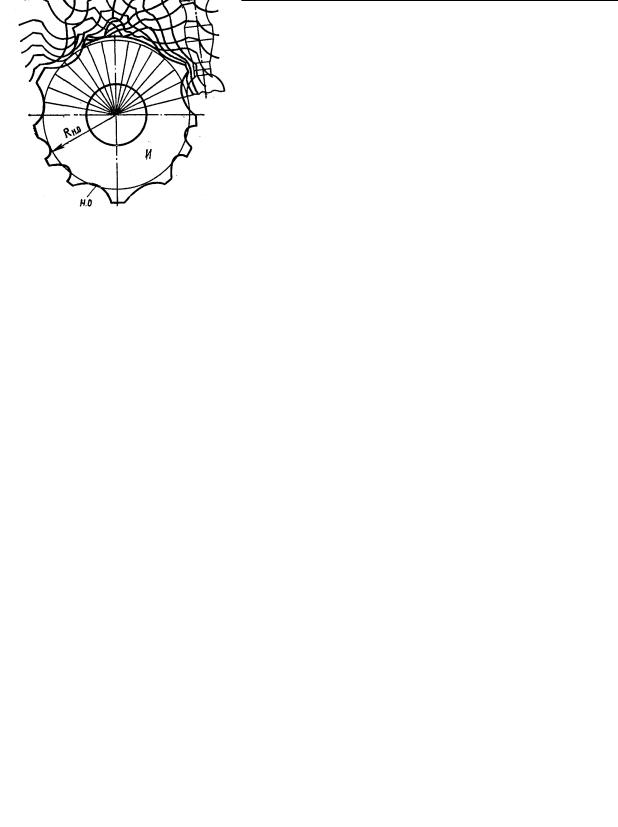
Режущий инструмент. Конспект лекций |
81 |
|
12 ОБКАТОЧНЫЕ ИНСТРУМЕНТЫ ДЛЯ ДЕТАЛЕЙ НЕЭВОЛЬВЕНТНОГО ПРОФИЛЯ
Обкаточные инструменты применяют для обработки сложных поверхностей неэвольвентного профиля: прямолинейного, в виде дуг окружностей и других кривых, с направляющими в продольном направлении, винтовыми и прямолинейными, параллельными оси детали.
Их обработки производится червячными фрезами, долбяками и обкаточными резцами.
12.1Обкаточные резцы
Обкаточные фасонные резцы применяют для обработки длинных деталей типа тел вращения, имеющих фасонный профиль.
Из за большой относительной длины обработать их обычными фасонными резцами невозможно. Обработка обкаточными фасонными резцами является высокопроизводительным и точным методом. Однако этот метод требует специальных станков или специальных приспособлений к токарным станкам.
Если профиль детали задан и надо найти профиль резца, для ее правильного формообразования, то необходимо сообщить детали обкаточное движение относительно неподвижного резца. Тогда линия режущей кромки резца будет огибающей кривой к ряду последовательных положений профиля детали в указанном ее относительном движении.
Длина хорды ≤ (0,005 … 0,010) Rн
Радиус начальной окружности резца должен быть таким, чтобы деталь обрабатывалась полностью по всей длине Rн = 50 ÷ 150 мм.
Обычно обкаточный резец устанавливают так, чтобы его ось была перпендикулярна оси детали, а вершины режущих кромок располагались по центру детали.
В целях уменьшения искажения профиля передний угол у обкаточных резцов, как правило, делают равным нулю. Задний угол получается шлифованием по конусу (6…12 градусов).
12.2Червячные фрезы
Наибольшее распространение имеют инструменты для обработки прямолинейных профилей. В зависимости от профиля выполняются следующие
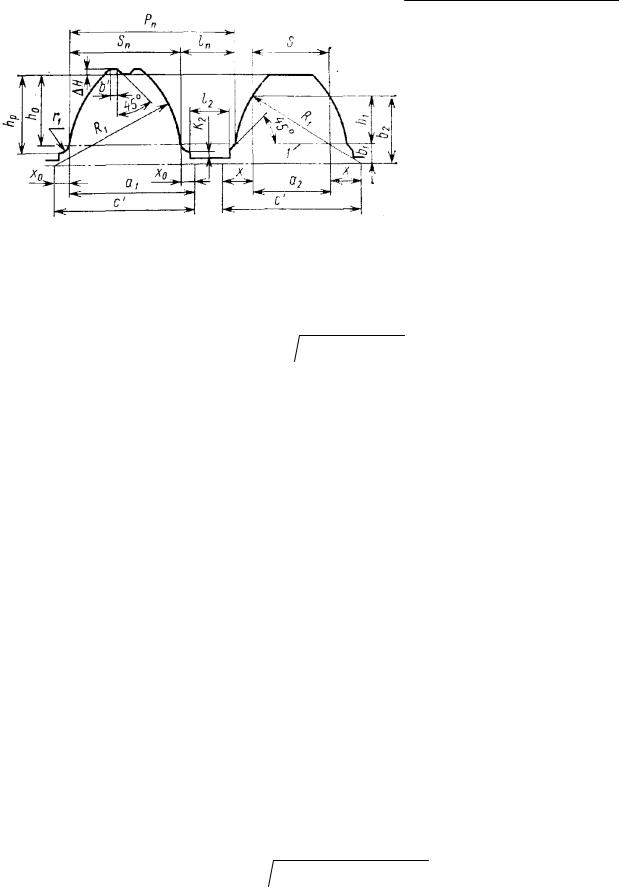
Режущий инструмент. Конспект лекций |
82 |
|
виды фрез: без усиков, с усиками, с удлиненным зубом, определенной установки и фрезы-улитки.
Нахождение необходимого профиля зуба шлицевой червячной фрезы производится графическим и аналитическим способами.
Наиболее распространенным из графических способов построения профиля зуба инструмента является копирование последовательных положений профиля впадины.
Предварительно вычерчиваются на бумаге в максимально большом масштабе профиль впадины. Из точек начала прямолинейного профиля проводятся нормали до пересечения с начальной окружностью.
Радиус начальной окружности, R, мм
R = Re2 − 0,75a2
где R – радиус начальной окружности, мм;
а – расстояние от прямой профиля до центра начальной окружности, мм.
Параметры профиля фасонных червячных фрез определяются в нормальном сечении к виткам исходного червяка на диаметре или цилиндре, на котором расположена начальная прямая рейки зубьев фрезы. Профиль зубьев фрезы в нормальном сечении принимается таким же, как и у инструментальной рейки. В основе инструментальной рейки лежит исходная рейка, правильно сопряженная с профилем обрабатываемой детали.
Зубья фрезы не обрабатывают наружный диаметр валика. Поэтому зуб инструментальной рейки выше зуба исходной рейки на ∆h для образования зазора по внутреннему диаметру фрезы в процессе обработки валика.
12.3Долбяки
Рекомендуемый радиус начальной окружности шлицевого валика
R = Re2 −(0,44 ÷0,50)a2
Рекомендуемый радиус начальной окружности долбяка
Rи = (1,5 ÷2,0)R
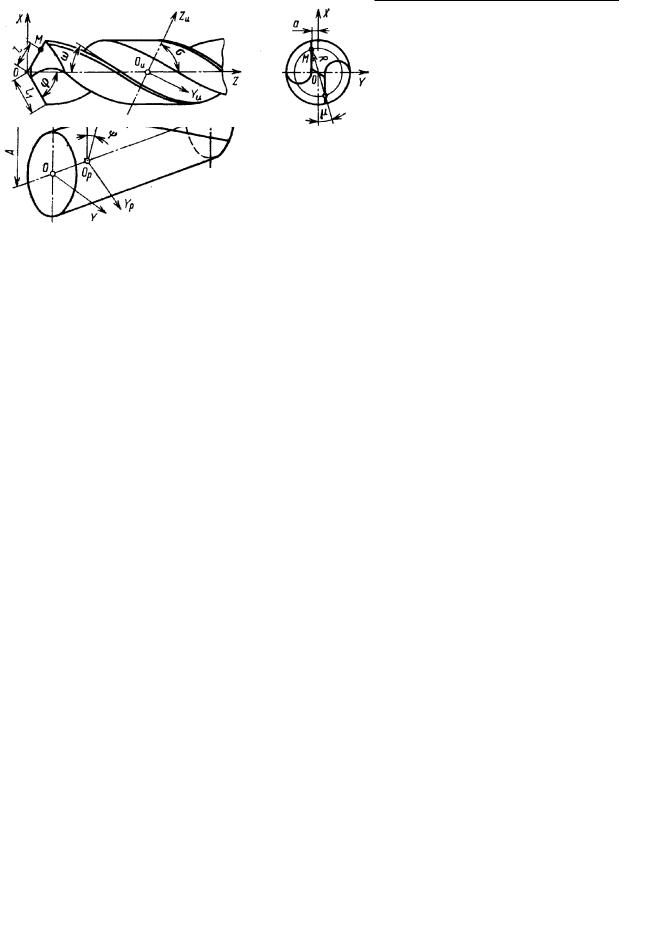
Режущий инструмент. Конспект лекций |
83 |
|
13 ДИСКОВЫЕ ИНСТРУМЕНТЫ ДЛЯ ОБРАБОТКИ ВИНТОВЫХ ПОВЕРХНОСТЕЙ ДЕТАЛЕЙ
Для обработки канавок деталей с винтовой поверхностью типа ходовых винтов, роторов насосов, косозубых колес, спиральных сверл, концевых фрез, червячных шлицевых и зуборезных фрез и др. наиболее распространены инструменты в форме тела вращения — дисковые острозаточенные и затылованные фрезы и шлифовальные круги.
При обработке поверхностей винтовых канавок профиль исходной поверхности инструмента и профиль зубьев фрезы, имеющий передний угол равным нулю, отличаются от профиля таких канавок. Объясняется это тем, что винтовые канавки дисковыми инструментами обрабатывают методом бесцентроидного огибания. При этом нет начальных окружностей, по которым изделие и инструмент в относительном движении формообразования катятся без скольжения, но поверхность канавки образуется в относительном движении в результате ряда последовательных резов режущими кромками различных зубьев в разном их положении.
В процессе образования винтовых канавок заготовке сообщается два равномерных движения: вращательное относительно своей оси и поступательное вдоль оси, т. е. заготовка совершает винтовое движение с заданным винтовым параметром Р = s/2π. Фреза равномерно вращается относительно своей оси с постоянной скоростью.
Для определения профиля зубьев дисковой фрезы должны быть заданы форма и размеры профиля винтовой канавки, угол σ между осями заготовки и фрезы и расстояние между осями А. Профиль канавки обычно задается в торцовом сечении изделия или в нормальном сечении к винтовой канавке. Профиль канавки может быть задан и в другом сечении. Угол между осями фрезы и изделия
σ =900 −ω −(1÷4)0
где ω - угол наклона винтовой канавки к оси изделия по наружному диаметру.