
материалы по метрологии / 100101.65 – Сервис 6. МЕТОДИЧЕСКИЕ УКАЗАНИЯ ПО ВЫПОЛНЕНИЮ ЛАБОРАТОРНЫХ РАБОТ
.pdf
Величина отклонения от плоскостности определяется или стрелой прогиба полосы (рис. 4.6, а), выраженной в интервалах между серединами соседних, одинаково окрашенных интерференционных полос, или количеством колец, т. е замкнутых интерференционных полос (рис. 4.6, б),
симметрично расположенных относительно центра поверяемой поверхности.
Кольцо, расположенное на 0,5 мм от края, не учитывается.
Интервал полос или каждое интерференционное кольцо соответствует половине длины волны. Для белого света среднее значение длины волны 0,6
мкм. Отклонение от плоскостности на рис.4.6, а составляет два интервала между полосами, а на рис. 4.6, б — два интерференционных кольца, т. е. в
обоих случаях:
∆= 2 λ / 2 = 2 х 0,3 = 0,6 мкм.
Допуск плоскостности измерительных поверхностей микрометра составляет 0,001 мм, т. е. три интерференционных полосы или три кольца.
Рис.4.6. Интерференционные полосы (а) и кольца (б)
Проверка параллельности измерительных поверхностей
Отклонение от параллельности измерительных поверхностей
микровинта и пятки возникает от неперпендикулярности измерительных
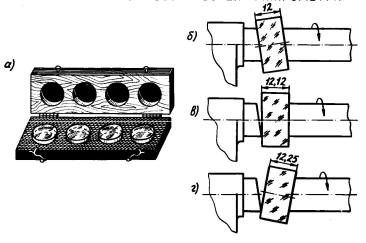
поверхностей оси вращения винта, от перекоса винта при зажатии стопора и других причин.
Отклонение от параллельности измерительных поверхностей микрометра определяется интерференционным методом с помощью четырех плоскопараллельных стеклянных пластин. Проверка производится в пределах полного оборота микровинта, поэтому рабочие размеры (толщина)
стеклянных пластин отличаются друг от друга на 0,12—0,13 мм, что соответствует 1/4 оборота микровинта (рис. 4.7).
Рис. 4.7. Плоскопараллельные стеклянные пластины
Каждую стеклянную пластину последовательно зажимают между измерительными поверхностями пятки и микровинта, плавно вращая винт обязательно за головку трещотки до появления щелчков. Наблюдая интерференционные картины, которые появляются в местах соприкосновения измерительных поверхностей пятки и микровинта с пластиной, подсчитывают суммарное число одноцветных полос на обеих поверхностях и записывают его в бланк отчета.
Наибольшее суммарное количество полос из четырех при поверке всеми пластинами характеризует отклонение от параллельности измерительных поверхностей пятки и микровинта, допуск параллельности
которых для микрометра с верхним пределом измерения 25 мм установлен 2
мкм, т. е. 7 интерференционных полос.
Поверяя параллельность измерительных поверхностей микрометра в свободном состоянии микровинта, т. е. при отпущенном стопоре,
одновременно поверяют параллельность этих поверхностей и при зажатом с помощью стопора винте. При этом непараллельность может увеличиваться не более чем на 0,001 мм, т. е. допускается увеличение суммарного числа интерференционных полос до 10.
Проверка погрешности показаний микрометра
Проверка показаний микрометра производится по концевым мерам длины в шести точках, равномерно расположенных по шкалам: 0; 5,12; 10,24; 15,36; 21,5 и 25 мм. Проверка нулевой установки производится аналогично,
как и при измерении размеров деталей (см. 4.2. Измерение размеров деталей).
Плавным вращением микровинта (только за головку трещотки) до появления щелчков, между пяткой и микровинтом последовательно зажимают блоки концевых мер и снимают показания микрометра.
Разность между показанием микрометра с учетом погрешности нулевой установки и размером блока концевых мер определяет погрешность показаний микрометра.
Допустимая погрешность показания составляет ± 0,004 мм.
4.4.Порядок выполнения работы
1.Ознакомиться с устройством, принципом действия и отсчетом по шкалам микрометра.
2.Выбрать деталь для измерения и выполнить на бланке отчета эскиз детали с указанием измеряемого размера и сечений, в которых производятся измерения (рис.4.4).
3.Записать в бланк отчета данные о проверяемой детали: номинальный размер с предельными отклонениями, допуски круглости (овальности) и
профиля продольного сечения (прямолинейности и параллельности образующих).
4.Закрепить микрометр в специальной стойке.
5.Проверить нулевую установку микрометра (см. 4.2. Измерение размеров деталей), и записать показание с точностью до тысячных долей миллиметра на глаз с учетом знака в бланке отчета.
При показании микрометра свыше ± 0,02 мм подозвать преподавателя
ипод его руководством отрегулировать микрометр.
6.Измерить деталь в указанных сечениях и записать полученные отсчеты с точностью до тысячных долей миллиметра.
7.Снять микрометр со стойки.
8.Осмотреть измерительные поверхности пятки и микровинта,
которые не должны иметь забоин, царапин, следов коррозии, грубой обработки, влияющих на поверку плоскостности
При наличии указанных дефектов для поверки необходимо выбрать другой микрометр и повторить пункт 8.
9. Записать в бланк отчета основные данные микрометра: цена деления,
пределы измерения, чувствительность, завод-изготовитель, заводской или инвентарный номер.
10. Протереть салфеткой, смоченной бензином, а затем чистой сухой салфеткой измерительные поверхности микрометра.
11 Тщательно протереть чистой сухой салфеткой рабочую поверхность стеклянной пластины.
На рабочей поверхности пластины отсутствуют какие-либо обозначения (товарный знак предприятия, заводской номер и т д ).
12. Наложить на измерительную поверхность пятки стеклянную пластину ее рабочей поверхностью и, слегка наклоняя ее, добиться появления интерференционных полос или колец.
13.Определить или стрелу прогиба (кривизну) интерференционных полос в долях расстояния между полосами, или число симметрично расположенных интерференционных колец (рис. 4.6).
14.Зарисовать вид интерференционных полос (наблюдаемую картину).
Указать характер проверяемой поверхности и величину отклонения от
плоскостности в микрометрах.
15.Аналогично проверить плоскостность измерительной поверхности микровинта, повторив пункты 12, 13 и 14.
16.Стеклянную пластину протереть чистой сухой салфеткой и уложить
вфутляр.
17.Закрепить микрометр в стойке.
18.Вынуть из футляра первую из четырех стеклянную пластину,
записать в бланк отчета ее размер (толщину) и тщательно протереть чистой
сухой салфеткой обе торцевые плоскости.
19.Плавно перемещая микровинт вращением только головки трещотки до появления щелчков, зажать стеклянную пластину между измерительными поверхностями пятки и винта.
20.Подсчитать и записать в бланк отчета суммарное число интерференционных полос на обеих измерительных поверхностях.
21.Поворотом стопора закрепить винт и повторить пункт 20.
22.Открепить стопор. Отвести микровинт, вращая его за барабан,
снять стеклянную пластину и положить ее в футляр.
23.Пункты 18—22 повторить со второй, третьей и четвертой стеклянными пластинами.
24.Ознакомиться с концевыми мерами длины и с составлением блоков
мер.
25.Определить длины отдельных концевых мер, входящих в пять блоков требуемых размеров для проверки микрометра.
26. Выбрать из набора меры требуемых длин. Меры очистить от смазки, протереть салфеткой, смоченной бензином, насухо протереть чистой сухой салфеткой и притереть в блоки.
Собранные блоки класть на чистый лист бумаги или салфетку нерабочими поверхностями.
27.Проверить нулевую установку микрометра (см. пункт 5).
28.Измерить блоки концевых мер. Зажимать блоки мер между пяткой
ивинтом можно только вращением головки трещотки до появления щелчков.
После измерения каждый блок мер класть на чистый лист бумаги или
салфетку. Показания микрометра с точностью до 0,001 мм на глаз записать в
бланк отчета.
29.Показать результаты измерения и проверки преподавателю.
30.Разобрать блоки концевых мер. Меры протереть чистой сухой салфеткой и уложить в соответствующие гнезда ящика набора.
31.Убрать свое рабочее место.
4.5.Оформление отчета
1.Учитывая погрешность нулевой установки, записать действительные размеры детали в разных сечениях и направлениях.
2.Определить величину действительного отклонения от круглости
(овальности) в каждом сечении.
3.Определить величину и вид действительного отклонения профиля продольного сечения в каждом направлении.
4.Определить верхнее и нижнее действительные отклонения размера как разность наибольшего (наименьшего) действительного и номинального размеров детали.
5.Сопоставляя верхнее и нижнее действительные отклонение размера
сзаданными предельными отклонениями, а наибольшие отклонения
овальности и профиля продольного сечения с их допусками, дать заключение
огодности детали по каждому параметру.
6.Зарисовать схему микрометра (рис. 4.2).
7.Учитывая погрешность нулевой установки, записать действительные показания микрометра при измерении блоков концевых мер.
8.Определить суммарные погрешности показаний микрометра как разность между показанием микрометра с учетом погрешности нулевой установки и размером блока концевых мер.
9.Сопоставляя наибольшие действительные отклонения от плоскостности и параллельности измерительных поверхностей при свободном микровинте и наибольшую суммарную погрешность показаний микрометра с допустимыми значениями, сделать заключение о годности микрометра или его негодности по какому-либо параметру.
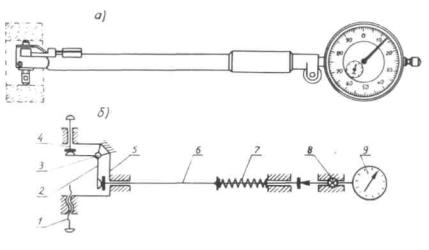
Лабораторная работа № 5
ИЗУЧЕНИЕ РЫЧАЖНО-МЕХАНИЧЕСКИХ ПРИБОРОВ
5.1. Устройство прибора
Индикаторные нутромеры предназначены для измерений внутренних размеров относительным методом, т. е. путем сравнения контролируемого размера с размером образца. В качестве образцовых мер используются установочное кольцо, блок из концевых мер с боковинами, микрометр и др.
Индикаторные нутромеры изготовляются со следующими пределами измерения (мм): 6—10, 10—18,..., 700—1000, для чего к каждому нутромеру приложены сменные неподвижные измерительные стержни (наконечники) и
мерные шайбы различных размеров.
Рис. 5.1. Общий вид индикаторного нутромера и его кинематическая схема
Измерительным устройством в индикаторном нутромере служит индикатор часового типа с ценой деления 0,01 мм. Передаточное отношение нутромера равно 1.
На рис. 5.1 представлены общий вид индикаторного нутромера и его кинематическая схема. Индикатор 9 устанавливается в корпус 10 нутромера,
на другом конце которого расположена измерительная головка 5, имеющая сменный неподвижный 1 и подвижный 4 измерительные наконечники.
Подвижный наконечник 4 через коленчатый равноплечий рычаг 2,
качающийся на оси 3, и шток 6 связан с измерительным стержнем индикатора. Контакт между ними обеспечивается пружиной 7.
Измерительное усилие нутромера определяется суммой усилий индикатора 9
и пружины 7. Индикатор закрепляется в корпусе нутромера винтом 8.
Таким образом, незначительное нажатие на подвижный наконечник 4
вызывает поворот стрелки индикатора. Так как плечи рычага 2 одинаковы, то цена деления индикатора сохраняется без изменения. Для изоляции прибора от температуры рук рукоятка 11 выполняется из нетеплопроводных материалов.
5.2. Установка прибора на нуль и приемы измерения внутренних
размеров
Если не задан номинальный размер, то он определяется штангенциркулем и полученный результат округляется до ближайшего большего из ряда нормальных длин в машиностроении. Индикаторный нутромер настраивается на номинальный размер проверяемого отверстия, в
соответствии с которым подбирается сменный наконечник 1 (рис. 5.1) и
ввинчивается в отверстие измерительной головки 5 прибора.
Установка прибора в нулевое положение производится по установочному кольцу или блоку из концевых мер длины с размером,
равным номинальному диаметру проверяемого отверстия. К составленному
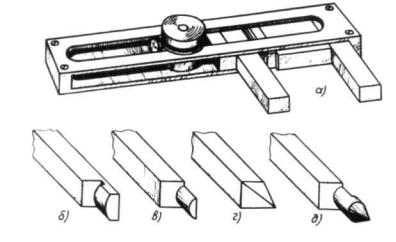
таким образом блоку концевых мер 1 (рис.5.2) по его краям притирают специальные блоки 2 различной конструкции и вместе с ними блок зажимают в державке 3 (струбцине).
Затем измерительные наконечники прибора размещаются между боковиками (рис.5.3), прибор покачивают вправо и влево для фиксации размера блока, являющегося наименьшим размером между боковиками,
которому соответствует крайнее положение стрелки. Вращая шкалу индикатора, совмещают нулевое деление шкалы с точкой изменения направления движения стрелки, т. е. с ее крайним положением. После этого еще раз проверяют правильность установки прибора в нулевое положение путем его покачивания.
Рис. 5.2. Составление блока концевых мер
После установки прибора в нулевое положение измеряют отверстие.
Для этого прибор вводят осторожно в контролируемое отверстие и небольшим покачиванием его находят наименьшее показание прибора. Оно характеризует отклонение отверстия в измеряемом сечении.
Диаметр отверстия равен алгебраической сумме размера блока концевых мер и показания индикатора. Диаметр отверстия (рис. 5.4)
измеряется в двух взаимно перпендикулярных направлениях (I и II) и трех