
материалы по метрологии / 100101.65 – Сервис 6. МЕТОДИЧЕСКИЕ УКАЗАНИЯ ПО ВЫПОЛНЕНИЮ ЛАБОРАТОРНЫХ РАБОТ
.pdfИзмерение штангенциркулем внутренних размеров производится аналогично, но при помощи наружных цилиндрических измерительных поверхностей губок, которые вводят внутрь детали. Измеряемый размер определяется как сумма показания инструмента и толщины сдвоенных губок, намаркированной на них.
При измерении штангенглубиномера измерительную плоскость основания 12 (рис. 3.3) накладывают на одну поверхность детали, а штангу
1, при открепленных зажимных винтах рамки и движка, передвигают
(сначала вручную, а затем с помощью устройства 7 микроподачи) до упopa
в другую поверхность детали. Закрепляют штангу в рамке винтом 4
производят отсчет показаний.
При измерении угломером углов до 90° на подвижной линейке 5 (рис. 3.5) с помощью державки 6 закрепляют угольник 7. Открепив зажимные винты 2 сектора и микроподачи, между угольником и неподвижной линейкой
8 помещают деталь. Поворачивая линейку 5 сначала от руки, а затем микроподачей подводят измерительные поверхности угольника и линейки 8
без просвета к поверхностям детали, определяющих измеряемый угол, и
закрепляют подвижную линейку винтом 2. По шкале и нониусу угломера производят отсчет, который и является значением измеряемого угла.
Измерение углов в пределах от 90 до180° производится аналогично, но без дополнительного угольника, который снимается с подвижной линейки.
Для получения действительного значения измеряемого угла к снимаемому отсчету надо прибавить 90°. При измерении расстояния L от края детали до оси отверстия (рис. 3.6) надо воспользоваться штангенциркулем, у которого измерительные поверхности губок выполнены в виде лезвия. Измерив размер
а от края детали до края отверстия, искомый размер определяется косвенным методом как сумма размера а и радиуса отверстия:
L = а+D/2,
где D—диаметр отверстия.
3.4. Проверка погрешности показаний инструментов
Погрешность показаний проверяют в нескольких точках, равномерно расположенных в пределах основной шкалы и нониуса.
Штангенинструменты с ценой деления нониуса 0,05 мм и верхним пределом измерения 200 мм проверяют по блокам концевых мер длины с размерами: 30,15; 60,3; 90,45; 120,6; 150,75 и180,9 мм, а угломер — по угловым мерам
(плиткам) с рабочими углами: 15°10′; 30°20′; 45°30′; 60°40′;75°50′ и 90°.
При выполнении работы поверку штангенинструмента можно проводить в точках: 0; 31,2; 61,5 и 91,7 мм, а угломер — в точках: 0; 30°20′; 60°40′ и 90° или в других точках.
Определение погрешности показаний начинают с проверки нулевой установки, т.е. при совмещении измерительных поверхностей инструмента.
При проверке штангенциркуля его губки должны быть прижаты к блоку концевых мер с усилием, обеспечивающим нормальное скольжение их по плоскостям мер. Для выявления перекоса губок (отклонения от параллельности) поверку производят дважды при установке блока мер в нижней и верхней части измерительных поверхностей, т. е. на большем и меньшем расстоянии от штанги, и снимают показание по основной шкале и нониусу. При поверке штангенглубиномера блок концевых мер устанавливают на поверочную плиту. Глубиномер устанавливают основанием на блок мер, а штангу выдвигают до касания плиты, и в этом положении снимают показание инструмента. При поверке угломера измерительные поверхности линеек совмещают без просвета, сначала друг с другом, а затем с измерительными поверхностями угловых мер и снимают показание Погрешность показаний определяется как разность (с учетом знака) между показанием инструмента и размером меры. Допустимая
погрешность показаний равна цене деления нониуса, т. е. ± 0,05 мм для
штангенинструмента и ±2′ для угломера.
3.5.Порядок выполнения работы
1.Ознакомиться с устройством штангенциркуля, штангенглубиномера и угломера, методами измерения ими размеров деталей и снятием показаний по основной шкале и нониусу.
2.Записать в бланк отчета основные данные о применяемых инструментах.
3.Выполнить в бланке отчета эскиз измеряемой детали.
4.Указать на эскизе детали по 2—3 измеряемых размера разных видов:
наружных, внутренних (круглой и плоской формы), открытых, угловых
(острого и тупого угла), от края детали до оси отверстия и дать обозначения этих размеров.
5.Указать обозначение и вид измеряемых размеров в таблице бланка
отчета.
6.Измерить указанные размеры и результаты измерения занести в таблицу бланка отчета.
Ознакомиться с концевыми мерами длины и с составлением блоков мер.
Определить длины отдельных концевых мер, входящих в три блока требуемых размеров для поверки штангенинструментов.
Выбрать из набора меры требуемых длин. Меры очистить от смазки,
протереть салфеткой, смоченной бензином, насухо протереть чистой салфеткой и притереть в блоки. Собранные блоки положить на чистый лист бумаги или салфетку.
10.Протереть салфеткой, смоченной бензином, и сухой чистой салфеткой измерительные поверхности всех инструментов в блоков концевых мер.
11.Совместив измерительные поверхности штангенциркуля, записать
отсчет по нониусу в таблицу отчета как погрешность нулевой установки.
12.Произвести поверку штангенциркуля (рис. 17), измерив каждый блок мер при двух его положениях: у торца губок (нижнее положение — н. п.) и на ближайшем расстоянии от штанги (верхнее положение — в. п.); при этом измерительные поверхности блока не должны выходить за пределы длинной стороны измерительных поверхностей губок. После поверки каждый блок концевых мер положить на чистый лист бумаги или салфетку. Результаты поверки занести в таблицу отчета.
13.Установить штангенглубиномер основанием рамки на поверочную плиту и выдвинуть штангу до касания его торца плиты. В этом нулевом положении снимается отсчет по нониусу и записывается в таблицу бланка отчета о поверке штангенглубиномера.
14.Произвести поверку штангенглубиномера, устанавливая на поверочной плите блоки концевых мер и измеряя расстояние от верхней измерительной поверхности блока до плиты. Показания инструмента занести
втаблицу бланка отчета.
15.Разобрать блоки концевых мер. Меры протереть чистой салфеткой и уложить в соответствующие гнезда ящика набора.
16.Выбрать из набора угловых мер плитки с требуемым углом Меры очистить от смазки, протереть салфеткой, смоченной бензином, насухо протереть чистой салфеткой и положить на салфетку или чистый лист бумаги.
17.Произвести поверку угломера, совместив без просвета измерительные поверхности линеек сначала друг с другом, а затем с измерительными поверхностями угловых мер. Полученные показания угломера занести в таблицу бланка отчета.
18.Угловые меры протереть салфеткой, смоченной бензином, затем чистой и уложить в соответствующие гнезда ящика набора.
19.Показать результаты измерения и поверки преподавателю.
20.Уложить все инструменты в свои футляры, убрать свое рабочее
место и приступить к оформлению бланка отчета.
3.6.Оформление отчета
1.Заполнить таблицу результатов измерения размеров детали:
а) номинальные значения линейных размеров определяют округлением измеренных размеров до целого числа миллиметров ближайшего большего для наружных, ближайшего меньшего для внутренних и просто ближайшего для остальных размеров. Например, при измеренном размере 20,35 мм
номинальное значение наружного размера 21 мм, а внутреннего и остальных
— 20 мм.
Номинальные значения угловых размеров определяют округлением измеренных углов до ближайшего целого числа градусов;
б) допустимые предельные отклонения размеров устанавливают исходя из допуска на размер по заданному квалитету (например, IТ14) и указывают либо только одним отклонением равным допуску: нижним со знаком минус
для наружных размеров, например, 21h14 (-0,52), и верхним со знаком плюс для внутренних размеров, например, 20Н14 (+0,52), либо двумя симметричными
отклонениями со знаками плюс и минус, равным половине допуска,
например, 20±0,26 (±IТ14/2);
в) действительное отклонение размера определяется как разность с учетом знака между измеренным и номинальным размерами;
г) сопоставляя действительные отклонения размеров с их допустимыми предельными отклонениями, дать заключение о годности детали по каждому размеру отдельно.
2.Определить погрешность показаний штангенциркуля,
штангенглубиномера и угломера как разность (со знаком) между показаниями инструментов и размерами блоков концевых или угловых мер.
3. Дать заключение о годности каждого инструмента, сопоставляя действительную, наибольшую по абсолютной величине погрешность
показаний с допустимой погрешностью показаний.
4. Нарисовать схему устройства нониуса штангенинструмента с
указанием всех формул, необходимых для его расчета.
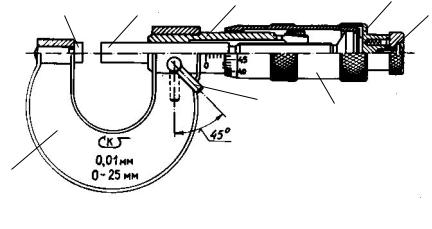
Лабораторная работа №4
ИЗУЧЕНИЕ МЕТОДОВ ИЗМЕРЕНИЙ МИКРОМЕТРИЧЕСКИМИ ИНСТРУМЕНТАМИ
4.1. Устройство микрометра
Микрометрические инструменты и приборы основаны на применении винтовой пары. При вращении винта в неподвижной гайке линейное перемещение винта l пропорционально шагу Р резьбы и углу его поворота,
т. е.
l = Р φ / 2π .
Микрометр для наружных измерений показан на рис. 4.1. В скобе 1
запрессованы пятка 2 и стебель 4. В гладком и резьбовом отверстиях стебля помещается микрометрический винт 3. Гладкое сопряжение микровинта и
5
4
2 |
3 |
6 |
8
7
1
Рис.4.1. Общий вид микрометра для наружных измерений

стебля обеспечивает точное направление линейного перемещения винта при его вращении в резьбовом отверстии. Измерительными поверхностями являются торцевые плоскости пятки и винта. К винту с помощью корпуса 5
трещотки крепится барабан 7. Трещотка служит для создания постоянного измерительного усилия в пределах 7±2 Н (700±200г). При возрастании
усилия сверх установленной нормы головка 6 будет свободно
проворачиваться, не передавая |
вращение на микровинт. В требуемом |
положении винт закрепляется стопором 8. |
|
Рис.4.2. Схема микрометра для наружных измерений
На стебле нанесены две миллиметровые шкалы, расположенные по обе стороны от продольного штриха и сдвинутые друг относительно друга на 0,5
мм, так как шаг резьбы винта Р = 0,5 мм. По числу делений, расположенных слева от края барабана, определяют целое число оборотов винта, т. е целое число и половину миллиметра. На скошенной поверхности барабана нанесена круговая шкала с числом делений n = 50. Цена деления шкалы барабана i = Р / п = 0,5/50=0,01 мм. По этой шкале с помощью продольного штриха стебля (указателя) отсчитываются десятые, сотые и на глаз тысячные доли миллиметра.
Пример отсчета показан на рис. 4.3. Показание микрометра будет равно
5,990мм (5 делений по нижней шкале на стебле — 5 мм; 0,5 деления по шкале по верхней шкале — 5,5 мм; 49 делений по круговой шкале на барабане — 5,99 мм и 0,0 деления на глаз — 5,990 мм).
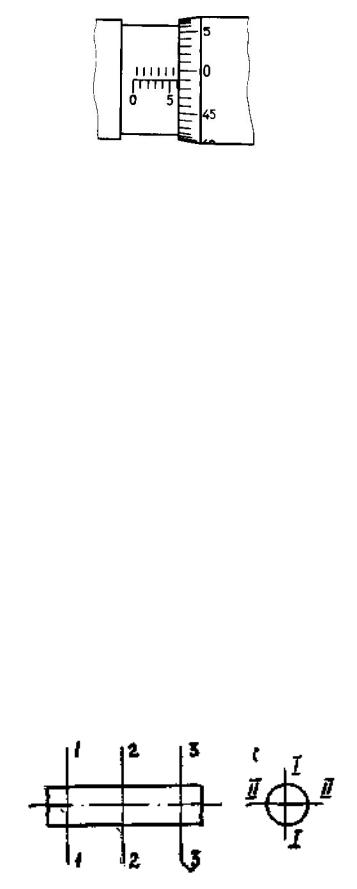
Рис.4.3. Пример отсчета микрометра
4.2. Измерение размеров деталей
Прежде всего, необходимо проверить нулевую установку микрометра.
Вращая микровинт за головку 6 трещотки (рис. 4.1), привести в соприкосновение измерительные поверхности винта и пятки. Вращение прекратить после нескольких (2—3) щелчков трещотки. Снятый по шкале барабана отсчет следует учитывать как погрешность нулевой установки при определении размеров изделий.
Для измерения детали отводят измерительную поверхность винта путем его вращения за накатную часть барабана 7. Между измерительными поверхностями винта и пятки вводят деталь. Плавно вращая микровинт обязательно за головку трещотки до появления щелчков, зажимают деталь между винтом и пяткой и снимают показание микрометра по шкалам на стебле и барабане.
Рис.4.4. Схема измерений отклонений
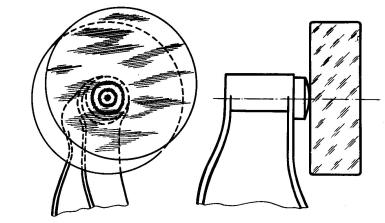
При измерении размера вала одновременно проверяются отклонения формы. Отклонения от параллельности образующих (конусообразность) и
прямолинейности образующих (бочкообразность и седлообразность)
определяются измерением вала в трех сечениях 1, 2 и 3 вдоль оси (по краям и в середине, рис. 4.4). Значение отклонения определяется как полуразность наибольшего и наименьшего из измеренных размеров. Отклонение от круглости(овальность) определяется измерением вала в каждом сечении в двух взаимно перпендикулярных направлениях I и II (рис. 4.4). Значение овальности есть наибольшая полуразность измеренных в одном сечении под углом 90° размеров.
4.3. Поверка микрометра
Поверка плоскостности измерительных поверхностей. Отклонение от плоскостности измерительных поверхностей пятки и микровинта определяется интерференционным методом с помощью плоской стеклянной пластины. Пластину 1 накладывают на измерительную поверхность 2 и,
слегка наклоняя ее, добиваются появления в месте контакта пластины с поверяемой поверхностью интерференционных полос или колец (рис. 4.5).
Рис.4.5. Интерференционный методом поверки микрометра