
Belyaev_M_I_Teplovoe_oborudovanie_OP
.pdf
http://mppnik.ru
Рис. 6.2. Схема теплогенерирующего устройства на паровом обогреве:
а — рубашечного типа; б — трубчатого типа; в — змеевикового типа: 1 — продувочный кран; 2 — греющая камера; 3 — регулирующий вентиль; 4 — конденсационный горшок
ческих сред влажным насыщенным паром различают обогрев глухим паром (через разделительную стенку) и обогрев острым паром (пар непосредственно контактирует с продуктом), а по конструктивному исполнению теплогенерирующие устройства подразделяются на смежные и совмещенные.
При глухом обогреве (через разделительную стенку) пар подается в греющую камеру рубашечного (рис. 6.2, а), трубчатого (рис. 6.2, б) или змеевикового (рис. 6.2, в) типов, конденсируется, отдавая, теплоту парообразования разделительной стенке, а через нее продукту или технологической среде. Теплогенерирующие устройства паровых аппаратов состоят из продувочного крана греющей камеры, подводящего паропровода с регулирующим вентилем, конденсатопровода для отвода конденсата из греющей камеры, конденсационного горшка, регулирующей и защитной арматуры.
При обогреве пищевых продуктов острым паром греющая камера совмещена с рабочей камерой (рис. 6.3). Она состоит из корпуса с размещенной в нем камерой, в которую подается пар, взаимодействующий с продуктом, укладываемым на перфорированный противень. Конденсат из камеры стекает в парогенератор, вода в котором нагревается тэном. Расчет греющих камер паровых аппаратов сводится к определению поверхности нагрева (конструктивный расчет), либо для проверки соответствия поверхности нагрева технологическому процессу (поверочный расчет).
Рис. 6.3. Схема совмещенного камерного тепло-генерирующего устройства:
1 — корпус; 2 — греющая камера; 3 — парогенератор; 4 — тэн; 5 — перфорированный противень; 6 — теплоизоляция
Поверхность нагрева греющей камеры парового аппарата определяется по уравнению
http://mppnik.ru
F = Q/K∆t, |
(6.1) |
где Q — количество теплоты, передаваемой поверхности нагрева в единицу времени, Вт (Дж/с); К — коэффициент теплопередачи от влажного насыщенного пара к продукту, Вт/ (м2 ∙ К); ∆t — разность температур между теплоносителем и нагреваемой средой, °С.
Количество теплоты Q, которое передается от теплоносителя через поверхность нагрева в единицу времени, определяется по тепловому балансу для конкретного технологического процесса.
Коэффициент теплопередачи К от теплоносителя (влажного насыщенного пара) к нагреваемой среде в камере определяется по формуле для плоской однослойной стенки
K (1/ 1 / 1/ 2 ) 1 , |
(6.2) |
где 1 , 2 — соответственно коэффициенты теплоотдачи от теплоносителя к поверхности нагрева и от поверхности нагрева к нагреваемой среде в камере, Вт/(м2∙К); , — соответственно толщина стенки (поверхности нагрева) и коэффициент теплопроводности материала, Вт/(м∙К).
Всвязи с тем, что в тепловых аппаратах предприятий общественного питания разделительная поверхность нагрева выполняется из тонкостенного материала δ 0,01 м, а коэффициент теплопроводности металла достаточно велик: для стали — 40 Вт/ (м ∙ К), то отношение / 0 .
Вэтом случае коэффициент теплопередачи определяется по уравнению
K 1 2 /( 1 2 ). |
(6.3) |
Средняя разность температур (температурный напор) между теплоносителем и нагреваемой средой ∆t определяется как среднелогарифмическая по уравнению
∆t = [(∆tб-∆tм)/2 lg (∆tб/ ∆tм,)] • (∆tб/∆tм), |
(6.4) |
где ∆tб — наибольшая разность температур между температурами влажного насыщенного пара и нагреваемой средой, °С; ∆tм — наименьшая разность температур между температурами влажного насыщенного пара и нагреваемой средой, °С.
Секундный расход пара определяется из выражения
D = Qзaтp/(ix – ik), |
(6.5) |
где Qзaтp — общее количество затраченной теплоты в единицу времени, Вт (Дж)/с; ix, ik — соответственно энтальпии пара и конденсата, Дж/кг.
ix = i' + xr, |
(6.6) |
где i' — энтальпия жидкости при определенной температуре и давлении, кДж/кг; х — степень сухости пара, %; г — скрытая теплота парообразования, кДж/кг.
В паровых аппаратах пролетный пар отсутствует (ix = i'), поэтому общее количество затраченной теплоты определяется из уравнения
Qзaтp = Q1/ , |
(6.7) |
где Q1 — количество теплоты, необходимой для нагрева воды от начальной температуры tн до конечной tк, Вт;
Q = Gc (tк – tн), |
(6.8) |
где с — удельная теплоемкость воды, кДж/(кг∙К); — коэффициент |
полезного действия |

http://mppnik.ru
(задается при проектировании теплового аппарата).
Правила эксплуатации. Перед началом работы паровых аппаратов необходимо слить конденсат из греющей камеры. Для этого необходимо открыть продувочный кран и оставить его открытым на весь пусковой период. Для эффективной работы паровых аппаратов следует удалить воздух из греющей камеры — эта операция осуществляется с помощью пара. На первой стадии разогрева открывается вентиль на паропроводе на четверть оборота, при этом пар постепенно заполняет греющую камеру и при соприкосновении с холодными стенками конденсируется. По мере прогревания аппарата поступающий пар вытесняет воздух. После появления из продувочного крана упругой струи пара его закрывают и полностью открывают вентиль на паропроводе.
Быстрое заполнение греющей камеры паром в начальный период приводит к образованию избыточного количества конденсата, ухудшению теплообмена и увеличению продолжительности разогрева аппарата. Образующийся конденсат удаляется через конденсатоотводчик. Периодически необходимо проверять исправность конденсатоотводчика, открывая время от времени продувочный кран. Если из последнего идет конденсат, это свидетельствует о неисправности конденсатоотводчика. Признаками неисправной работы конденсатоотводчика служит медленный нагрев содержимого аппарата, быстрое увеличение давления в греющей камере. В любом случае необходимо отключить аппарат, выпустить пар через байпасную линию
ипрочистить конденсатоотводчик.
Впроцессе работы необходимо постоянно следить за показаниями манометров. За 5...10 мин до окончания технологического процесса следует прекратить подачу пара и содержимое рабочего сосуда будет доведено до готовности за счет аккумулированной теплоты, что является одним из важных мероприятий по экономии топливно-энергетических ресурсов.
6.3. ТЕПЛОГЕНЕРИРУЮЩИЕ УСТРОЙСТВА, ПРЕОБРАЗУЮЩИЕ ХИМИЧЕСКУЮ ЭНЕРГИЮ СГОРАНИЯ ТОПЛИВА В ТЕПЛОВУЮ
Горение топлива — это химический процесс соединения горючих компонентов с кислородом воздуха, сопровождающийся выделением теплоты.
По реакции горения топлива рассчитывается количество воздуха, необходимое для полного сгорания топлива, а также объем получаемых продуктов сгорания. Расчеты выполняются для определения потерь теплоты с уходящими продуктами сгорания, кпд тепловых аппаратов, геометрических параметров газоходов.
Теплогенерирующие устройства, преобразующие химическую энергию сгорания топлива, имеют аналогичные конструкции, отличающиеся отдельными конструктивными элементами, которые изменяются в зависимости от вида топлива и, способа его сжигания.
Все виды теплогенерирующих устройств этого типа имеют топку, трубопроводы для подачи жидкого и газообразного топлива, газоходы для удаления продуктов сгорания. Вид топлива (твердое, жидкое или газо-
Рис. 6.4. Устройство для сжигания твердого топлива:
а — схема устройства; б — колосниковая решетка с продольными
http://mppnik.ru
щелями; в — чугунный колосник брусчатый; г — колосниковая плита с отверстиями
образное) определяющим образом влияет на конструктивные особенности топок и их классификацию.
Топки подразделяются на слоевые и камерные. Слоевые предназначены для сжигания твердого топлива на колосниковой решетке, камерные — для сжигания жидкого и газообразного топлива (рис. 6.4).
Топки
В понятие «топка» входят колосниковая решетка и топочное пространство, где сгорают горючие вещества, выделившиеся из топлива при его нагреве (рис. 6.4, а).
К о л о с н и к о в а я р е ш е т к а предназначена для равномерной подачи воздуха к топливу и поддержания его слоя. Колосниковые решетки топок собирают из отдельных чугунных элементов — колосников балочного типа (рис. 6.4, 6) или плит (рис. 6.4, г).
Через зазоры между колосниками, щели или отверстия колосниковых плит зола в процессе горения частично проваливается в зольник; остальная масса остается на колосниковой решетке и в виде шлака выгребается через загрузочную дверцу топки.
Размеры щелей и отверстий колосниковой решетки зависят от рода сжигаемого топлива, его фракционного состава и способа подачи воздуха. Отношение суммарной площади сечения отверстий (щелей) для подачи воздуха к общей площади решетки называется живым сечением решетки. Величина живого сечения решетки изменяется в пределах: для брусчатых колосников
— от 20 до 40%, для плиточных — от 8 до 15 %.
Брусчатые колосники используются при сжигании крупнокускового и малозольного топлива с большим выходом летучих газов (древесина, торф), плиточные — при сжигании многозольного и мелкозернистого топлива с малым выходом летучих газов (каменный уголь).
Топливо загружается в топку через загрузочное окно с дверцей.
З о л ь н и к служит для подачи воздуха в топку через колосниковую решетку, а также для сбора золы и мелких частиц топлива. Окно зольника закрывается дверцей, с помощью которой регулируют поступление воздуха в топку.
Г а з о х о д ы служат для обогрева тепловоспринимающих поверхностей аппарата движущимися продуктами сгорания топлива. По газоходам продукты сгорания движутся за счет разрежения, создаваемого в топке благодаря разности плотностей продуктов сгорания и окружающего воздуха либо за счет работы тягодутьевых устройств.
Работа слоевой топки характеризуется тем, что при загрузке новой порции топлива на горящий слой он воспламеняется вследствие непосредственного соприкосновения с нижележащим раскаленный слоем. Одновременно на новый слой топлива излучается значительное количество теплоты из топочного пространства. Все это предопределяет неравномерное потребление воздуха и цикличное протекание процесса горения топлива.
Разжигают топку в такой последовательности. Сухие дрова закладывают равномерно на ⅔ высоты топки так, чтобы они занимали всю поверхность колосниковой решетки. Длина поленьев должна соответствовать длине топки. Затем открывают дверцу зольника, задвижку в дымоходе и поджигают дрова. После частичного сгорания поленья разравнивают и укладывают на них слой топлива. Крупные куски каменного угля измельчают и кладут на разгоревшиеся дрова слоем примерно в 4…6 см. Когда уголь разгорится, толщину его слоя увеличивают до 10...15 см. Поступление воздуха регулируют дверцей зольника и задвижкой в дымоходе. Топочная дверца в процессе горения закрывается, так как поступающий через нее воздух охлаждает топку и снижает ее кпд.
Качественному, т. е. химически полному, сжиганию топлива способствуют хорошее его перемешивание с воздухом, при минимальном коэффициенте избытка воздуха, подогрев воздуха, увеличение поверхности горения. Кроме того, при сжигании жидкого топлива возможны тонкое распыление, подача воздуха в корень факела, закручивание струи.
Структура горящего слоя топлива на колосниковой решетке представлена на рис. 6.5. Если

http://mppnik.ru
поддерживать на решетке толстый слой топлива, через него не будет проходить в необходимом количестве воздух, требующийся для сгорания летучих веществ в топочном объеме. Кроме того, в слое горящего топлива при недостаточном количестве транзитного воздуха, направляющегося в топочное пространство, развиваются более
высокие температуры, вызывающие при сжигании, например антрацита, коробление и перегорание колосников, плавление шлака и химический недожог.
При слое топлива меньше необходимого неполнота сгорания уменьшается, но в уходящих газах увеличивается количество избыточного воздуха, что ведет к увеличению объема топочных газов, снижению их температуры и тепловой эффективности топочного устройства.
При правильно выбранной толщине слоя топлива топка работает с минимальными избытком воздуха и химической неполнотой сгорания.
Рис. 6.5. Структура горящего слоя топлива
В процессе горения часть мелких частичек топлива проваливается в зольник через отверстия решетки (провал), а также выносится из слоя, осаждаясь затем в газоходе, или вместе с уходящими газами рассеивается в окружающую среду (унос). При чистке топки от золы и шлаков вместе со шлаками выбрасывается и некоторое количество несгоревшего топлива (шлак).
Поэтому колосниковая решетка должна соответствовать виду и размерам частиц топлива, а в процессе сжигания следует периодически перемешивать горящее топливо.
Толщину слоя топлива устанавливают в зависимости от сорта топлива, его влажности, зольности, структуры, температуры горения в слое.
О химической неполноте сжигания топлива судят по дыму. О количестве подаваемого и участвующего в процессе горения воздуха судят по цвету и характеру пламени. Если пламя прозрачное, ровное, светло-желтое, а горение происходит без потрескивания, значит, процесс сжигания топлива протекает нормально, с минимальным избытком воздуха. При недостатке воздуха пламя имеет длинные коптящие красные языки. Резко укороченное пламя и горение с потрескиванием свидетельствуют о том, что в топку поступает избыточное количество воздуха. Чем больше приоткрыты поддувальная дверца и задвижка, тем сильнее тяга. После загрузки очередной порции топлива дверцу зольника открывают полностью. По мере прогорания топлива ее постепенно прикрывают, следя за пламенем в топке.
Основными материалами для изготовления теплогенерирующих устройств твердотопливных аппаратов являются хорошо обожженный красный и огнеупорный кирпич, жирная и огнеупорная глина, мелкий без примесей песок, вода.
Р а с ч е т т о п о к д л я с ж и г а н и я т в е р д о г о т о п л и в а сводится к определению площади колосниковой решетки и объема топки. Площадь колосниковой решетки определяют по уравнению
Fp BQнp / QFp 1 , |
(6.9) |
где В — расход топлива, кг/ч; Q BQнp — тепловая мощность топки, кВт; QFp 1 — тепловое
напряжение поверхности колосниковой решетки (зеркала горения) (принимают 450...500 кВт/м2), кВт/м2.
Объем топки определяют по формуле
V |
BQ p / QV 1 |
, |
(6.10) |
|
T |
н |
T |
|
|
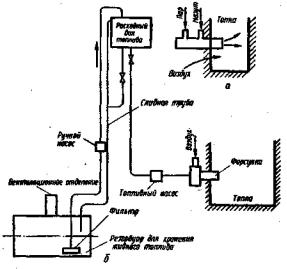
http://mppnik.ru
гдеQVT 1 — тепловое напряжение топочного объема (принимают 250...300 кВт/м3), кВт/м3. Процесс сжигания жидкого топлива значительно сложнее процесса сжигания газа и состоит
из следующих операций: распыление, испарение капель, пирогенетическое разложение топлива, образование горючей смеси и ее сжигание.
Подготовка жидкого топлива к сжиганию осуществляется двумя способами: перед воспламенением топливо испаряется и тогда оно горит в парообразном состоянии; топливо распыляется на мельчайшие капли, которые при смешении с воздухом нагреваются главным образом за счет радиации и затем в процессе горения также испаряются. Первый способ не получил широкого распространения, потому что он неприемлем при использовании низкокачественных и дешевых сортов жидкого топлива, испаряющегося при более высоких температурах.
Существенное влияние на скорость горения оказывает диаметр капли. Чем он меньше, тем более однородной является смесь распыленного топлива с воздухом и тем эффективнее протекает процесс горения.
Тонкость распыления топлива изменяется в значительных пределах в зависимости от способа его осуществления.
Вид распыления |
Диаметр капли, мм |
Механическое (Р=1 МПа) |
1,56 |
Воздушное: |
|
низкого давления (Р = 3,5 кПа) |
0,40 |
среднего давления (Р=15 кПа) |
0,09 |
высокого давления (Р = 0,6 МПа) |
0,025 |
Паровое распыление (Р=0,4МПа) |
0,03 |
Устройства для распыления жидкого топлива и подачи его в камеру сгорания аппарата называются форсунками (рис. 6.6,а,б).
Рис. 6.6. Принципиальные схемы устройства для сжигания жидкого топлива:
а — общая |
схема; |
б — принципиальная |
конструктивная схема |
|
Основные показатели работы форсунок – длина факела пламени и его температура – зависят от качества распыления и условий смесеобразования топлива с воздухом.
Средний радиус капель определяют по следующим приближенным формулам: для механических форсунок

http://mppnik.ru
r = 0,78/Рм, |
(6.11) |
где Рм — давление распыляемого мазута, МПа; для воздушных форсунок низкого давления
r = 700/Рв, |
(6.12) |
где Рв — давление распыляющего воздуха, Па.
Жидкое топливо подается к форсунке из расходного бака самотеком или под давлением, в зависимости от вязкости топлива и вида распыления. Расходный бак располагается недалеко от горячего цеха на высоте 4...5 м. В зонах с низкими температурами во избежание застывания мазутные линии прокладываются вместе с паровыми в одной изоляции или производится специальный подогрев топливопровода с помощью паровой рубашки.
Принципиальная схема щелевой форсунки представлена на рис. 6.7, а.
Мазут самотеком поступает к верхней трубке, а пар подается к нижней. Давление пара должно находиться в пределах 150...4000 кПа. Подачу и распыление мазута регулируют вентилями, установленными на трубопроводах, подающих пар и мазут.
Из паровой форсунки пар выходит со скоростью 300...350 м/с, мазут — со скоростью 1...2 м/с. На распыление 1 кг мазута расходуется 0,5 кг пара.
Мазут выходит из форсунки под небольшим давлением, перемешивается с поступающим воздухом и сгорает, образуя яркий факел пламени.
Пар, как правило, получают в парогенераторе, встроенном в топку аппарата (рис. 6.7, б, в). На чугунной плите и корпусе укреплены нижний и верхний баллоны парогенератора. Вода поступает из водопровода через вентиль сначала в нижний баллон, а затем по соединительной трубе в верхний, где образуется пар. Из верхнего баллона пар направляется по пароотвод-
Рис. 6.7. Схема установки паровой форсунки в топке плиты:
а — схема паровой форсунки; б — паровая форсунка: 1 — чугунная плита; 2 — верхний баллон; 3 — соединительная труба; 4 — сопло; 5 — нижний баллон; 6 — корпус; 7 — водопроводная труба; 8 — вентиль; 9 — вентиль на паропроводе; 10 — воронка;
11 — водопроводная |
труба; |
в |
— общий |
вид |
|
теплогенерирующего |
устройства: |
1 — расходный бак; |
2 |
||
— топливопровод; 3 — паровая рубашка |
топливопровода; |
4 |
|||
— запорный |
кран; 5 — настил плиты; 6 — топка; 7 — |
||||
форсунки |
|
|
|
|
|

http://mppnik.ru
ной трубке через вентиль в форсунку, откуда распыленное паром топливо выбрасывается через сопло в топочное пространство. Жидкое топливо подается из расходного бака по трубопроводу в воронку и далее в форсунку. Внизу под форсункой располагается поддон для жидкого топлива (на рисунке не показан).
Перед пуском форсунки переносным факелом зажигают топливо в поддоне. При сгорании этого топлива предварительно разогревается топочный объем и создается необходимое давление пара в парогенераторе. Затем открывают вентили на топливопроводе и паропроводе. После воспламенения выходящего из форсунки мазута путем регулировки подачи топлива, пара и воздуха добиваются устойчивого факела и необходимой теплопроизводительности. При выключении форсунки сначала
прекращают подачу топлива, затем пара. |
|
||||
При |
сжигании |
газа |
(рис. |
6.8) |
В камерных топках после- |
довательно протекают процессы |
смесеобразования газа с воздухом, |
||||
прогрева смеси до температуры воспламенения и непосредственно |
|||||
горения. |
|
|
|
Рис. 6.8. Схема камерной |
|
|
|
|
|
|
топки |
В зависимости от того, совмещены или разделены процессы смесеобразования и подогрева смеси до температуры воспламенения и горения, различают следующие способы сжигания газа: первый — диффузионный, когда потоки газа и воздуха поступают в топку отдельно и смешиваются в зоне горения; второй — кинетический, когда в зону горения топки поступают поток полностью подготовленной газовоздушной смеси или поток газа с соединением только части необходимого воздуха и поток добавочного вторичного воздуха.
При диффузионном сжигании газа образуется ярко-желтый факел пламени сравнительно большой длины, предопределяющий значительную высоту камеры сгорания. Сжигание газа происходит с большим коэффициентом избытка воздуха, снижающим температуру горения, и со значительной интенсивностью шума.
Кинетический способ сжигания газа лишен указанных недостатков, но предполагает использование более сложной конструкции смесительной трубки.
Показателями, характеризующими топки, являются тепловая мощность Qн и тепловое напряжение Т (для слоевых топок).
Тепловой мощностью Qн называется мощность топки в Вт, отнесенная к 1 м3 объема топочного пространства:
Qн BQнp / 3600V , |
(6.13) |
где В — расход топлива, кг; Qнp — низшая теплота сгорания топлива, Дж/кг; V — объем
топочного пространства, м3.
Тепловым напряжением Т называется мощность топки в Вт, отнесенная к 1 м2 зеркала горения топлива:
T BQ p / 3600R, |
(6.14) |
н |
|
где R — площадь зеркала горения, м2.
В топках газовых тепловых аппаратов основным фактором, влияющим на качество процесса сжигания газа, является качество смешения газа с воздухом. Процессы смешения газа осуществляются в газовых горелках.
Газовые горелки
Газовыми горелками называются устройства, предназначенные для образования газовоздушной смеси, подачи ее или подачи только газа (при диффузионном сгорании) в камеру сгорания (топку) и сжигания. Рациональное сжигание горючего газа зависит в первую очередь от
http://mppnik.ru
правильного выбора типа и конструкции газовых горелок.
Газовая горелка должна обеспечивать возможность зажигания газовоздушной смеси, регулирования подачи газа и воздуха, а также гарантировать при правильной ее эксплуатации тщательное перемешивание горючего газа с воздухом, устойчивое горение и полное сгорание горючего газа.
Работа горелки считается устойчивой, если длительное горение газа происходит без отрыва и проскока пламени. Отрыв пламени происходит при увеличении давления газа в сети и при избытке воздуха. Проскок пламени имеет место при резком понижении давления газа в сети. В этом случае пламя проскакивает внутрь смесительной трубки и горит у сопла. Скорость процесса горения, высота и форма пламени зависят от способа и скорости перемешивания горючего газа с воздухом: диффузионный (внешнее смешение), диффузионно-кинетический (частичное предварительное смешение) и кинетический (полное предварительное смешение).
Наивысшая температура пламени (до 1500 °С) и наименьшая длина его достигаются при полном предварительном смешении горючего газа с воздухом.
Классификация газовых горелок. Согласно ГОСТ 17357—71 газовые горелки классифицируются по следующим признакам: способу подачи воздуха, номинальному давлению газа и воздуха, теплоте сгорания газа, номинальной тепловой мощности, длине факела (калибру) и методу стабилизации (созданию устойчивости) факела.
П о с п о с о б у п о д а ч и в о з д у х а различают горелки внешнего смешения — горелки с подачей воздуха из окружающей среды и смешения газа с воздухом в камере сгорания за счет разрежения в ней и конвекции. Такие горелки называются диффузионными. Длина факела пламени и его свечение в диффузионных горелках достигают наибольшей величины.
Подача воздуха в камеру сгорания может осуществляться принудительно (вентилятором).
В горелках внутреннего смешения в камеру сгорания подается газовоздушная смесь, уже полностью или частично подготовленная. Горючий газ и воздух смешиваются внутри самой горелки.
Образование газовоздушной смеси в горелках с предварительным смешением осуществляется путем принудительной подачи воздуха в камеру смешения путем подсоса воздуха за счет энергии струи горючего газа либо путем подсоса газа за счет энергии струи воздуха. Горелки, в которых воздух подсасывается за счет энергии струи газа, называются инжекционными. Различают инжекционные газовые горелки с частичным и полным предварительным смешением горючего газа с воздухом. Первые горелки называются пламенными и характеризуются количеством воздуха, подсасываемого внутрь горелки за счет энергии струи газа. Такой воздух называется
первичным.
Воздух, поступающий в камеру сгорания за счет конвекции непосредственно около факела и в результате разрежения, называется вторичным.
Горелки с полным предварительным смешением горючего газа с воздухом называются беспламенными и в качестве первичного воздуха подсасывают весь воздух, необходимый для сжигания газа.
По н о м и н а л ь н о м у д а в л е н и ю г а з а различают горелки низкого (до 5 кПа), среднего (от 5 до 100 кПа) и высокого (свыше 100 кПа) давления, соответственно номинальное давление воздуха подразделяют на низкое (до 1 кПа), среднее (от 1 до 3 кПа) и высокое (свыше 3 кПа).
В аппаратах, применяемых на предприятиях общественного питания, используются в основном инжекционные газовые горелки низкого давления с частичным предварительным смешением газа с воздухом.

http://mppnik.ru
Рис. 6.9. Принципиальные схемы газовых горелок:
а — диффузионная; б — инспекционная факельная: 1 — сопло; 2 — регулятор первичного воздуха; 3 — конфузор; 4 — горловина; 5 — диффузор; 6 — насадка; в — формы сопел инжекционных горелок: 1
— сопло с углом конуса 90°; 2 — сопло с углом конуса 50°; 3 — сопло с углом конуса 16°; 4 — сопло с углом конуса 90° и с цилиндрической выходной частью
Устройство газовых горелок. Диффузионная горелка представляет собой насадку с отверстиями для выхода газа (рис. 6.9, а). Диаметр трубы насадки принимается из расчета 1...1.5 суммарного сечения выходных отверстий. Диаметр отверстий d выполняют 1...5 мм с шагом отверстий s (s = 5...6).
Из насадки под низким давлением выходит газ, смешивается с воздухом и сгорает в виде желтого непрозрачного факела пламени.
Диффузионные горелки имеют простую конструкцию, они надежны в эксплуатации, устойчивы и бесшумны в работе.
Недостатками этих горелок являются: большой избыток воздуха в камере сгорания, приводящий к снижению температуры горения и увеличению потерь теплоты с уходящими продуктами сгорания; длинный факел пламени, требующий значительной высоты камеры сгорания. В связи с этим диффузионные горелки не нашли широкого применения в тепловых аппаратах предприятий общественного питания.
И н ж е к ц и о н н а я г а з о в а я г о р е л к а (рис. 6.9, б) состоит из следующих основных элементов: регулятора первичного воздуха, сопла, смесителя-инжектора, насадки.
Газ подается по газопроводу в сопло, которое служит для подачи газа в горелку, превращения части потенциальной энергии газа в кинетическую и придания струе газа определенных форм и направления.
При выходе из сопла скорость газа значительно возрастает, так как диаметр сопла во много раз меньше диаметра подводящего газопровода. При выходе из сопла с большой скоростью газ создает в конфузоре смесителя-инжектора разрежение, за счет которого в смеситель подсасывается (инжектируется) первичный воздух.
Канал сопла (рис. 6.9, в) может быть различной формы с углом конуса от 8 до 45°. Смеситель-инжектор служит для смешивания газа с воздухом, выравнивания концентрации и
скорости движения газовоздушной смеси. В инжекционных горелках смесителям обычно придают форму трубки Вентури. Смеситель состоит из двух усеченных конусов — конфузора и диффузора, соединенных между собой горловиной.
Конфузор предназначен для подсоса воздуха за счет разрежения. Угол сужения конфузора составляет 20...40°. Горловина служит для выравнивания концентрации и скоростного напора смеси. Диффузор используется для дальнейшего выравнивания концентрации газа и воздуха в смеси путем торможения струи и уменьшения скорости движения газовоздушной смеси, что создает дополнительный напор, необходимый для преодоления сопротивления при проходе смеси через отверстия насадки.
Насадка служит для равномерного распределения газовоздушной смеси по выходным отверстиям, а также задает форму и размер факела.
Насадка (рис. 6.10, а, б, в, г) должна соответствовать форме и размерам обогреваемой поверхности.