
Английский для Тх / adsorptive Bubble Separation and Dispersed Air Flotation
.pdf
3
Adsorptive Bubble Separation and Dispersed Air Flotation
Lawrence K. Wang
CONTENTS
INTRODUCTION
BUBBLE SEPARATION PROCESS DESCRIPTIONS AND DEFINITIONS
BASED ON THE TECHNIQUES USED FOR BUBBLE GENERATION
BUBBLE SEPARATION PROCESS DESCRIPTIONS AND DEFINITIONS
ACCORDING TO THE TECHNIQUES USED FOR S OLIDS SEPARATION
BUBBLE SEPARATION PROCESS DESCRIPTIONS AND DEFINITIONS
ACCORDING TO THE OPERATIONAL MODES
SURFACE ADSORPTION
BUBBLE PHENOMENA
MULTIPHASE FLOW
MATERIAL BALANCES
FOAM SEPARATION BY DISPERSED AIR FLOTATION CELL
CHEMICAL REAGENTS FOR ADSORPTIVE BUBBLE SEPARATION
LABORATORY FOAM SEPARATION TESTS
ENGINEERING APPLICATIONS
ANALYTICAL METHODS AVAILABLE FOR PROCESS MONITORING
GLOSSARY
NOMENCLATURE
REFERENCES
1. INTRODUCTION
1.1. General Description
Adsorptive bubble separation process is a very effective technology for solid–liquid separation that has been in use outside the environmental engineering field for more than 60 years. Originally applied in the field of mining engineering, the process now provides the means for separation and/or concentration of 95% of the world’s base metals and other mineral compounds ( 1,2). Recently, the adsorptive bubble separation process has become increasingly important in such diverse applications as (a) the separation of algae, seeds, or bacteria from biological reactors, (b) removal of ink from re-pulped
From Handbook of Environmental Engineering, Volume 4: Advanced Physicochemical Treatment Processes
Edited by: L. K. Wang, Y.-T. Hung, and N. K. Shammas © The Humana Press Inc., Totowa, NJ
81
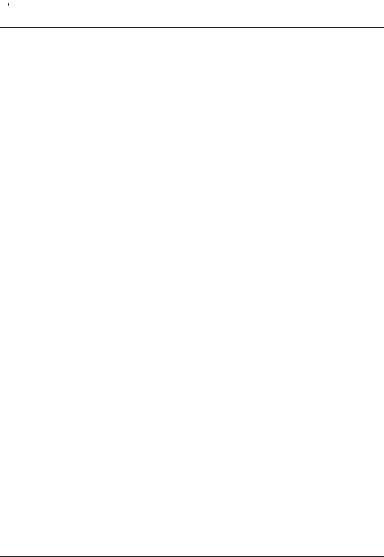
82 |
Lawrence K. Wang |
Table 1
Impurities to be Removed by Adsorptive Bubble Separation
Suspended Solids Wood fiber Cotton fiber Activated sludge Free oil Chemical flocs
Fats
Colloidal Solids Algae Bacteria
Titanium dioxide Turbidity
Soluble Organics Lignin and tannin
Humic acid Protein
Soluble oil
BOD, COD Color
Soluble Inorganics
Heavy metals (lead, copper, chromium, zinc, etc.) phosphate, sulfate iron, manganese, hardness, etc.
Surface-Active Substances
Soap
Detergent
Industrial surfactants Dye
Volatile Solids Xylene Toluene Ethylbenzene
Butylbenzylphthalate Trihalomethanes (chloroform, etc.) Trichloroethylene
paper stock, (c) recovery of protein and fat from food processing streams, peas from pea pods, coal from slate, gluten from starch, and oils from industrial effluents, and (d) more recently, treatment of drinking water, cooling water, wastewater, and sludge (3–120). This chapter briefly introduces all adsorptive bubble separation processes, but introduces dispersed air flotation in detail.
1.2. Adsorptive Bubble Separation
Adsorptive bubble separation process may be defined as the mass transfer process of a solid from the body of a liquid to the liquid surface by means of bubble attachment (42,75,84). The solids can be in dissolved, suspended, and/or colloidal form. The three basic mechanisms involved are bubble formation, bubble attachment, and solids separation (43,75 ).

Adsorptive Bubble Separation and Dispersed Air Flotation |
83 |
Fig. 1. A rising bubble in bubble separation column containing surface-active agent.
Table 1 indicates the solids or substances that can be effectively separated by the adsorptive bubble separation process. In general, the light-weight suspended solids, such as fibers, activated sludge, free oil, chemical flocs, and fats, can be readily separated by the process in accordance with the physical–chemical bubble attachment mechanism shown in Fig. 1 . The colloidal solids, soluble organics, soluble inorganics, and surface-active substances can be separated from the bulk liquid by the bubble separation process after they are converted from colloidal or soluble form into insoluble form (i.e., suspended solids), which can then be floated by gas bubbles.
Alternatively, an adsorptive bubble separation process in accordance with its surfaceadsorption phenomena, shown in Fig. 1 , can separate the soluble surface-active substances easily. Non-surface-active suspended solids, colloidal solids, soluble organics, and soluble inorganics can all be converted into surface-active substances. All surfaceactive substances (in either soluble form or insoluble form) can be effectively floated by gas bubbles (75).
The volatile solids shown in Table 1 are simply stripped out from the water phase into the gas phase (i.e., air) by bubbles according to Henry’s law.
In summation, the adsorptive bubble separation process, in theory, can remove or separate almost any kind of light-weight and/or surface-active substances from water. Because there are various types of adsorptive bubble separation processes, selection of an appropriate type for a specific application is an important skill (43,84).
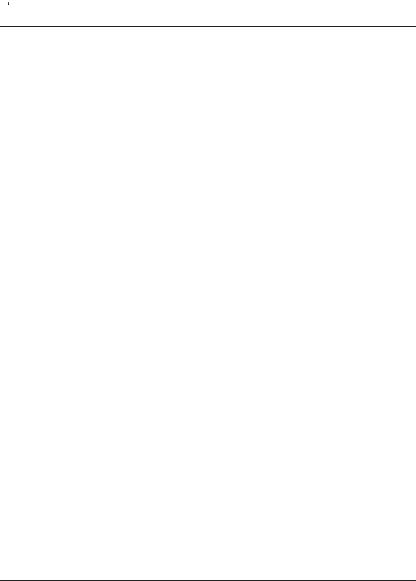
84 Lawrence K. Wang
Table 2
Types of Flotation Processes
1. Plain gravity flotation
Example: |
API Oil–water separator |
|
Wax water separator |
2.Dissolved air flotation (DAF)
Example: Full flow pressurization system Partial flow pressurization system Recycle flow pressurization system
Flow pattern: Laminar flow, Fine air bubbles Air Addition: 1% of liquid influent flow
3.Dispersed air flotation (or induced air flotation)
Example: |
Deinking flotation |
|
Foam separation |
|
Gas stripping |
|
Aeration/oxidation |
|
Ore flotation |
Flow pattern: |
Turbulent flow, large air bubbles |
Air addition: |
400% of liquid influent flow |
4. Vaccum flotation |
|
Example: |
Scum vacuum flotation |
5.Electrolytic flotation (or electroflotation) Example: Sacrificing electrode system
Non-sacrificing electrode system Flow pattern: Laminar flow, fine bubbles
Gas production:
|
Anode: 2H2O 4H+ + O2 + 4e |
|||||
|
Cathode: 4e + 4H2O 2H2 + 4OH |
|||||
6. Biological flotation |
|
2H2O 2H2 + O2 |
|
|||
|
|
|
|
|||
Example: |
Activated sludge thickening under denitrification condition |
|||||
Flow pattern: Laminar flow and fine bubbles |
||||||
Gas production: |
|
|
|
|
||
|
6NO3 |
+ 2CH3 OH → 6NO2 + 2CO2 + 4H2O |
||||
|
6NO2 |
+ 3CH3 OH → 3N2 + 3CO2 + 3H2O + 6OH |
||||
|
|
|
|
|
|
|
6NO3 + 5CH3OH 5CO2 + 3N2 + 7H2O + 6OH
Although many gases, such as carbon dioxide, nitrogen, hydrogen, oxygen, and ozone, are suitable, air is the cheapest and most readily available for bubble generation. Based on the technique and the type of gas used for bubble generation, the adsorptive bubble separation process can be classified mainly as dissolved air flotation, dispersed air flotation, vacuum flotation, electrolytic flotation (i.e., electroflotation) and biological flotation, as indicated in Table 2. If no gas is involved or used at all, the substances (such as oil or wax) are separated from liquid by the density difference between the target substance and the liquid, and the process is termed plain gravity flotation. The most common plain gravity flotation is the oil–water separation process. The following section briefly defines various adsorptive bubble separation processes.
Adsorptive Bubble Separation and Dispersed Air Flotation |
85 |
2.BUBBLE SEPARATION PROCESS DESCRIPTIONS AND DEFINITIONS BASED ON THE TECHNIQUES USED FOR BUBBLE GENERATION
2.1. Dissolved Air Flotation
Dissolved air flotation (DAF) is a process involving pressurization of air at 25–95 psig for dissolving air into water, and subsequent release of pressure (to 1 atm) under laminar flow conditions for generating extremely fine air bubbles (normally 20–80 microns), which become attached to the impurities to be removed. The air flow rate is about 1% of influent liquid flow rate. The attachment of air bubbles to the impurities can be a result of physical entrapment, electrochemical attraction, surface adsorption, and/or gas stripping. The specific gravity of the bubble–impurity agglomerates is less than 1, resulting in buoyancy or non-selective flotation (i.e., a save-all process) ( 1,75). Another chapter of this handbook series presents the theory, principles, operation, maintenance, design criteria, costs, chemical additives, process control, applications, tests, and design examples of dissolved air flotation in detail (2). In the past 40 years, dissolved air flotation has been used mainly for sludge thickening and fiber recovery (3,4,117,118). Now dissolved air flotation becomes a high technology for potable water purification (2,5–9,18,119) and wastewater treatment (2,10–17,22). Table 3 summarizes the US Environmental Protection Agency (US EPA) data on separation of pollutants by dissolved air flotation.
2.2. Dispersed Air Flotation
Dispersed air flotation (or induced air flotation) is a process involving introduction of air directly into the water through a revolving impeller, a diffuser, or an ejector at low pressure (slightly higher than 1 atm) for generating large air bubbles (normally 80 microns to over 1 mm) in large volumes under turbulent conditions. The air flow rate is about 400% of influent liquid flow rate. Physical entrapment and electrochemical attraction play minor roles in a dispersed air flotation system. The attachment of air bubbles to the impurities is mainly a result of surface adsorption, gas stripping, and oxidation. Surface-active substances (inks, detergents, and so on) are selectively separated in a foam phase ( 1 ). Volatile substances are removed by gas stripping. Reducing agents, such as ferrous ions, can be oxidized to ferric ions by air for subsequent separation in ferric hydroxide form. Dispersed air flotation can be used in ore separation (67–70,87 88,92–96,101–107,110–116), coal purification ( 114), fiber de-inking ( 17,21,89), wastewater treatment (2,19,20,22,30,41,116), water purification (23), surfactant separation (24), lignin separation (43,44,53,54), and so on. Because of its significance, this chapter introduces this process in detail.
2.3. Vacuum Flotation
In vacuum flotation, the influent process liquid to be treated is saturated with air at atmospheric pressure. There is an air-tight enclosure on the top of the flotation chamber in which a partial vacuum is maintained (75). The fine air bubbles (20–80 microns) are generated under laminar flow conditions by applying such a vacuum to the flotation chamber. The theory is that the lower the pressure, the lower the air solubility in water. The soluble air originally in water is partially released out of solution as extremely fine bubbles due to a reduction in air solubility caused by negative vacuum pressure. The

86 |
|
|
|
|
|
Lawrence K. Wang |
||
T |
|
able 3 |
|
|
|
|
|
|
|
|
|
|
|
|
|
||
Control Technology Summary for Flotation |
|
|
|
|||||
|
|
|
|
|
|
|
|
|
|
|
|
Ef |
|
fluent concentration |
|
Removal efficiency (%) |
|
|
|
|
|
|
||||
|
|
|
|
|
||||
|
|
|
|
|
|
|
|
|
Pollutant |
Range |
Median |
|
Median |
||||
|
||||||||
|
|
|
|
|
|
|
||
Classical pollutants (mg/L) |
|
|
|
|
|
|
||
|
|
BOD (5-d) |
140–1000 |
250 |
68 |
|||
|
|
COD |
18–3200 |
1200 |
66 |
|||
|
|
TSS (fiber, sludge, floc) |
18–740 |
82 |
88 |
|||
|
|
Total phosphorus |
<0.05–12 |
0.66 |
98 |
|||
|
|
Total phenols |
>0.001–23 |
0.66 |
12 |
|||
|
|
Oil & grease |
16–220 |
84 |
79 |
|||
Toxic pollutants (μg/L) |
|
|
|
|
|
|
||
|
|
Antimony |
ND–2300 |
20 |
76 |
|||
|
|
Arsenic |
ND–18 |
<10 |
45 |
|||
|
|
Xylene |
ND–1000 |
200 |
97 |
|||
|
|
Cadmium |
BDL–<72 |
3 |
98 |
|||
|
|
Chromium |
|
|
2–620 |
200 |
52 |
|
|
|
Copper |
|
|
5–960 |
180 |
75 |
|
|
|
Cyanide |
<10–2300 |
54 |
10 |
|||
|
|
Lead |
ND–1000 |
70 |
98 |
|||
|
|
Mercury |
BDL–2 |
|
75 |
|||
|
|
Nickel |
ND–270 |
41 |
73 |
|||
|
|
Silver |
BDL–66 |
19 |
45 |
|||
|
|
Zinc |
ND–53000 |
200 |
89 |
|||
|
|
Bis(2-ehtylhexyl) phthalate |
30–1100 |
100 |
72 |
|||
|
|
Butylbenzylphthalate |
ND–42 |
|
>99 |
|||
|
|
Carbon tetrachloride |
BDL–210 |
36 |
75 |
|||
|
|
Chloroform |
ND–24 |
9 |
58 |
|||
|
|
Dichlorobromomethane |
NA |
|
>99 |
|||
|
|
Di-n-butyl phthalate |
ND–300 |
20 |
97 |
|||
|
|
Diethyl phthalate |
NA |
|
>99 |
|||
|
|
Di-n-octyl phthalate |
ND–33 |
11 |
78 |
|||
|
|
N-nitrosodiphenylamine |
NA |
620 |
66 |
|||
|
|
2,4-Dimethylphenol |
ND–28 |
14 |
>99 |
|||
|
|
Pentachlorophenol |
|
|
5–30 |
13 |
19 |
|
|
|
Phenol |
|
|
9–2400 |
71 |
57 |
|
|
|
Dichlorobenzene |
18–260 |
140 |
76 |
|||
|
|
Ethylbenzene |
ND–970 |
44 |
65 |
|||
|
|
Toluene |
ND–2100 |
580 |
39 |
|||
|
|
Naphthalene |
ND–840 |
96 |
77 |
|||
|
|
Anthracene/phenanthrene |
0.2–600 |
10 |
81 |
|||
|
|
|
|
|
|
|||
|
|
NA not available; BDL below detection line; ND |
not detected |
|
|
|||
|
|
Source US EPA. |
|
|
|
|
|
|
bubbles and the attached solid particles rise to the surface to form a scum blanket, which can be removed by a continuous scooping or skimming mechanism. Grit and other heavy solids that settle to the bottom are raked to a central sludge sump for removal. Auxiliary equipment include an aeration tank for saturating the wastewater with air, vacuum

Adsorptive Bubble Separation and Dispersed Air Flotation |
87 |
pumps, and sludge pumps ( 1,2). In theory, vacuum flotation is similar to dissolved air flotation because both processes rely on pressure reduction for generation of fine bubbles.
The reactor designs of two processes, however, are significantly different. Vacuum flotation has been gradually replaced by dissolved air flotation in various practical applications.
2.4. Electrolytic Flotation
Electrolytic flotation is also called electroflotation, which is a process involving the generation of hydrogen and oxygen bubbles in a dilute aqueous solution by passing a direct current between two electrodes (75). The anode reaction generates oxygen bubbles and hydrogen ions, while the cathode reaction generates hydrogen bubbles and hydroxide ions. Either aluminum or steel sacrificial electrodes can be employed for generating the gas bubbles as well as coagulants. Non-sacrificial electrodes are employed for generating the gas bubbles only, and can be made of titanium (as the carrier material) and lead dioxide (as the coating material). Electrical power is supplied to the electrodes at a low voltage potential of 8–20 V DC by means of a transformer rectifier. Small bubbles in the range of 20–50 microns are produced under laminar flow conditions feasible for separation of fragile flocs in a small system. There can be unexpected advantages and disadvantages when electrolytic flotation is employed ( 1 ). Electroflotation process has been employed for treatment of septic tank effluent (25,26), groundwater (26), and industrial wastes (27,120–122). The following are the author’s electroflotation reactions ( 1 ) occurring at an anode and a cathode assuming the process water contains sufficient but not excessive amounts of electrolytes:
Anode: |
2H |
2 |
O |
4H+ + O |
2 |
+ 4e– |
|
|
|
|
|
||
Cathode: |
4e + 4H2O |
2H2 + 4OH |
||||
|
|
|
|
|||
|
2H2O |
2H2 + O2 |
|
It can be seen that normally water produces fine hydrogen bubbles at a cathode and fine oxygen bubbles at an anode. In the presence of excessive electrolytes, other types of gaseous bubbles may also be produced from the electroflotation system depending upon the types and concentrations of electrolytes in the water. This is the reason why electroflotation may give either unexpected good results or unexpected bad results
( 120,121 ).
2.5. Biological Flotation
In a biological flotation system, fermentations take place in the presence of anaerobic bacteria, nitrates, and substrates under anaerobic environment. Anaerobic bacteria in waste sludge convert nitrate and the substrate with carbon source (such as methanol) to nitrite, water, and carbon dioxide fine bubbles. Nitrite further reacts with a substrate (such as methanol) in the same waste sludge, producing fine nitrogen bubbles, more fine carbon dioxide bubbles, water, and hydroxide ions. The biological waste sludge, such as activated sludge can then be floated to the surface by the fine nitrogen and carbon dioxide bubbles. While the energy consumption of this process is low, its detention time is as long as 1–2 d (1,3). The following are the author’s chemical reactions in a biological flotation reactor for thickening of secondary activated sludge under denitrification conditions
88 |
Lawrence K. Wang |
assuming nitrate (NO3 ) is present in the sludge and methanol (CH3 OH) is a substrate added to the sludge:
6NO3 |
+ 2CH3OH |
6NO2 |
+ 2CO2 + 4H2O |
||||||||
6NO2 |
+ 3CH3 OH |
3N2 + 3CO2 |
+ 3H2O + 6OH |
||||||||
|
|
|
|
|
|
|
|
|
|
|
|
6NO |
3 |
+ 5CH |
3 |
OH |
5CO |
2 |
+ 3N |
2 |
+ 7H |
2 |
O + 6OH– |
|
|
|
|
|
|
|
It should be noted that the secondary activated sludge usually contains residual soluble BOD, COD, or TOC, which may avoid the necessity of adding a substrate CH3OH. In addition, biological flotation may also occur under common anaerobic conditions (instead of denitrification conditions).
2.6. Deep-Shaft Flotation
In deep-shaft flotation the entire volume of water to be treated is subjected to the increased pressure by passing the water down and up a shaft approx 10 m deep (4). At the bottom of the shaft, on the down-comer side, air is injected by one air blower under low pressure (20 psig). Undissolved air rises up the shaft against the flow, thus increasing the saturation of the water. As the water rises in the up-flow section, the hydrostatic pressure decreases. Some of the soluble air is then released out of solution in the form of fine air bubbles due to a reduction in air solubility caused by pressure reduction. Floc agglomeration and bubble generation occur simultaneously and gently; providing good attachment of the air bubbles to the flocs. The amount of air that can be dissolved is limited by the depth of shaft (e.g., hydrostatic pressure provided). The saturation of the water with air at that depth is dependent on the way the air is introduced to the system (e.g., size of air bubbles produced at point of injection) ( 1 ). Deep-shaft flotation, in principle, is similar to dissolved air flotation although the two process reactors are totally different (3,4,28).
3. BUBBLE SEPARATION PROCESS DESCRIPTIONS
AND DEFINITIONS ACCORDING TO THE TECHNIQUES USED FOR SOLIDS SEPARATION
According to the collection procedure for the enriched gas–liquid and/or gas–solid interfaces, adsorptive bubble separation processes or techniques can also be divided into two large categories: (a) foam separation, which involves the production of foam in the process, and (b) nonfoaming adsorptive bubble separation, which involves no production of foam. Foam separation can be further subdivide into foam fractionation and flotation. Nonfoaming adsorptive bubble separation, however, can be further subdivided into bubble fractionation, solvent sublation, and nonfoaming flotation. Lemlich (84) and Wang ( 1,75 ) provided the definitions of these technical terms in their books.
3.1. Foam Separation
Foam Separation is classified as follows:
(a) Foam fractionation
(b)Froth flotation
(b-1) Precipitate flotation (b-2) Ion flotation
(b-3) Molecular flotation
(b-4) Microflotation and colloid flotation
Adsorptive Bubble Separation and Dispersed Air Flotation |
89 |
(b-5) Macroflotation and ore flotation (b-6) Adsorption flotation
3.1.1. Foam Fractionation
Foam fractionation is one of the two foam separation processes. A foam fractionation system is always homogeneous. In a foam fractionation process reactor, the surfaceactive agent tends to adsorb at the bubble interface generated by a gas producer (i.e., a gas diffuser, a dissolved-air pressure chamber, or equivalent) and are removed in the foam phase. Wace et al. (29) and Grieves (30) have discussed the parameters and procedures for the design of foam fractionation and other foam separation processes. The foam fractionation technique was initially used by medical scientists and researchers. In 1952, London et al. (31 ) fractionated an enzyme by foaming off inactive protein. The separation and purification of enzymes through foaming was further conducted by Charm (32) in 1966. Schnepf and Gaden (33 ) and Wallace and Wilson (34) successfully separated proteins from water by foam fractionation. Other good work has been done to fractionate alcohol (35), anionic surfactants (36), and cationic surfactants (38). Treatment of either kraft black liquor (39,40) or dyeing bath waste (41 ) by foam fractionation, however, was found to be only partially successful.
3.1.2. Froth Flotation
Flotation is the term used to describe a process in which the species being separated from the bulk liquid media are insoluble particulates. Froth flotation is another one of the two foam separation processes. It also involves the production of foam in a heterogeneous aqueous system, and has a great deal of potential for the water and wastewater treatment. Froth flotation can be subdivided into at least seven categories (42,43,84), including precipitate flotation, ion flotation, molecular flotation, microflotation, adsorption flotation, ore flotation, macroflotation, and adsorbing colloid flotation. They are described separately below.
3.1.2.1. PRECIPITATE FLOTATION
Both precipitate flotation and ion flotation involve heterogeneous systems, in which a hydrophilic (solvent-loving) surface is made hydrophobic (solvent-hating) by reaction with a surfactant. Precipitate flotation involves the flotation of precipitates; in this process a non- surface-active agent (i.e., precipitating agent) is first added to the system to precipitate the ion to be removed and then a surfactant is added to float this precipitate, which then becomes attached to the bubble interfaces and is then removed in the foam phase. Under research supported by the US Department of Interior (44), a precipitate flotation process was conducted for the removal of Kraft lignin from water, and higher than 95% of lignin removal was achieved by an optimized system, in which alum and quaternary ammonium compound were used as precipitator and collector, respectively. In addition to the organic lignin removal, precipitate flotation technique has also been used by many researchers for removing radioactive contaminants (45–47), metal ions (48–50), and cyanide (51,52).
3.1.2.2. ION FLOTATION
The term ion flotation is applied to the process in which there is an initially homogeneous solution that becomes heterogeneous after the addition of an oppositely charged surfactant due to the reaction between the surfactant and specific ion(s); thus, insoluble complexes are formed. These insoluble complexes will then attach themselves to the

90 |
Lawrence K. Wang |
bubbles passing through the solution and thus leave the bulk solution in the foam phase. Researches conducted by Rutgers University (43,53,54) have demonstrated that the Kraft lignin in the Kraft pulp-mill effluents, and the lignin sulfonate in the sulfite pulp-mill effluents, can be efficiently removed by ion flotation using quaternary ammonium compounds as the flotation agents. Karger et al. (55,56) has used ion flotation technique to separate the ionic dyes effectively by using an ionic flotation agent of the opposite charge. The researchers investigated the feasibility of treating dyeing bath waste stream by ion flotation and concluded that a removal of 52.1% of the COD, 89.2% of the color, and 75.3% of the turbidity was effected by using 50 mg/L of a quaternary ammonium compound as the flotation agent. Besides, ion flotation has also successfully been used by Grieves et al. (57,58) for floating inorganic ions from aqueous solution.
3.1.2.3. MOLECULAR FLOTATION
Molecular flotation is very similar to ion flotation, except that the surfactant forms an insoluble complex with a nonsurface-active molecule (i.e., not an ion) and the product is floated out. Because the formation of dipolar complexes molecular flotation is much weaker than that of ion-pair complexes in ion flotation, to date, almost all the work has involved flotation of ions using an oppositely charged surfactant (59).
3.1.2.4. MICROFLOTATION AND COLLOID FLOTATION
Microflotation involves the removal of microscopic particles such as microorganisms (60–64) and colloids (65 ) (i.e., colloid flotation) by foaming. The term colloid flotation is specifically used when colloidal materials, other than microorganisms, are removed by a flotation process. Rubin et al. have successfully floated Escherichia coli and several species of algae using low gas-flow-rate foam separation technique (61) and removed Aerobacter aerogenes using both anionic and cationic collectors (62). The work conducted by Cassell and Rubin (65 ) has shown that microflotation is a rapid, efficient, nonselective technique. The separation of microscopic particles (including both microorganisms and colloidal color-causing materials) from water has, in some cases, advantages over gravity sedimentation. Combined with the high-rate filtration, microflotation may lead to an extremely efficient and compact treatment process for both water and wastewater treatment. In 1966, Dolzhenkova (66) improved the microflotation by replacing the single-capillary air-feeding device with a porousglass/diaphragm, by giving a pear-shaped form to the air inlet chamber, by using a microcompressor (instead of a compressed-air cylinder) as a source of compressed air, and by modifying the air-supply rate controlling device.
Adsorbing colloid flotation involves the flotation of colloidal particulate upon which dissolved material is adsorbed. The major objective of this adsorbing, col1oid flotation process is the removal of the dissolved material rather than the colloidal particles. Wang (72) has used a colloidal surface-active agent, dimethyl dihydrogenatedtallow ammonium chloride, as a flotation agent to treat tannery waste, and found that the adsorbing colloid flotation is efficient for the removal of suspended solids (i.e., more than 0.9 fractional reduction), but is inefficient for the removal of dissolved organics (i.e., less than 0.6 fractional reduction) from a tannery effluent. Kim and Zeitlin (74) has separated zinc and copper from sea water by adsorbing colloid flotation, which utilizes a negatively charged ferric hydroxide collector, a cationic surfactant, dodecylamine, and air.