
Diplom Linar / Бирдегулов Диплому / 1359417_FD6CA_dahin_o_h_massoobmennye_kolonnye_apparaty_konstrukciya_princ
.pdfВ зависимости от внутреннего устройства различают аппараты та-
рельчатые, насадочные, роторные (с вращающимися деталями). В нефтя-
ной, химической, нефтехимической и газовой промышленностях наиболее распространены тарельчатые и насадочные колонны.
В современных ректификационных аппаратах применяются самые разнообразные конструкции контактных устройств.
На рис. 1.1 приведена классификация ректификационных и аб-
сорбционных аппаратов по типу контактного устройства.
При выборе конструкции рабочих (контактных) элементов колонных аппаратов необходимо учитывать такие факторы, как гидравлическое со-
противление и диапазон изменения нагрузок по жидкой и газовой фазам.
11
2 ФИЗИЧЕСКАЯСУЩНОСТЬПРОЦЕССАРЕКТИФИКАЦИИ
Ректификация - один из самых распространенных технологических процессов в химической, нефтеперерабатывающей и во многих других от-
раслях промышленности.
Ректификация - это процесс разделения бинарных или многоком-
понентных паровых, а также жидких смесей на практически чистые ком-
поненты или их смеси, обогащенные легколетучими или тяжелолетучими компонентами; процесс осуществляется в результате контакта неравновес-
ных потоков пара и жидкости.
Характерной особенностью процесса ректификации являются сле-
дующие условия образования неравновесных потоков пара и жидкости,
вступающих в контакт; при разделении паровых смесей неравновесный поток жидкости (жидкостное орошение) образуется путем полной или час-
тичной конденсации уходящего после контакта потока пара (рис2.1, а),в то времякакприразделениижидкихсмесейнеравновесныйпаровойпоток(паровое орошение) образуется путем частичного испарения уходящей после контакта жидкости(рис.2.1, б).
Вследствие указанных особенностей проведения процесса ректификации неравновесные потоки пара и жидкости, вступающие в контакт, находятся в со-
стоянии насыщения, при этом парболее нагрет, чем жидкость, и в нем содержит-
сябольшетяжелолетучихкомпонентов,чемвжидкости. Послеконтактапар обо-
гащается легколетучими, а жидкость - тяжелолетучими компонентами за счет взаимногоперераспределениякомпонентовмеждуфазами(рис.2.1в).
12
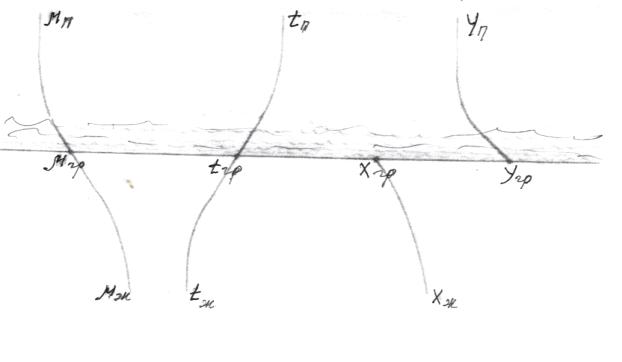
Ядро потока паровой фазы
Граница раздела фаз
|
|
Ядро потока жидкой |
|
|
|
|
фазы |
|
|
t- температура |
|
|
|
|
|
|
|
x-концентрация в жидкой фазе |
|
|
|
|||
µ- вязкость |
|
|
y-концентрация в паровой фазе |
|
|
|
|
|
|
|
|
|
|
|
Рис. 2.1. Схема изменения вязкости - µ, температуры - t, концентрации в жидкой и паровой фазах - x,y на границах раздела фаз.
2.1 Технология процесса ректификации
Для заданного разделения смесей используют ректификационные установ-
ки, основным элементом которых являются ректификационные аппараты, пред-
ставляющие собой ряд ступеней контакта, соединенных в противоточный раз-
делительный каскад. Наиболее простое конструктивное оформление противоточного каскада в ректификационных аппаратах достигается при движении жидкости от одной ступени контакта к другой под действием силы тяжести. В этом случае контактные устройства (тарелки) располага-
ются одно над другим, и разделительный аппарат выполняется в виде вер-
тикальной тарельчатой колонны.
При ступенчатом осуществлении процесса ректификации в ко-
лонных аппаратах контакт пара и жидкости на тарелках может про-
исходить в противотоке, в перекрестном токе, в прямотоке или в сме-
шанном токе фаз. Разделительный эффект, аналогичный многоступенча-
13
тому каскаду, достигается также путем непрерывного контакта фаз при движении их противотоком в слое насадки, то есть в насадочных ректи-
фикационных колоннах. В зависимости от технологической схемы уста-
новки используются простые и сложные колонны, а также простые и сложные системы колонн.
2.2 Простаяректификационнаяколонна
Простая ректификационная колонна имеет один сырьевой поток, два продуктовых потока, один теплопровод и один теплосъем по концам аппа-
рата или только один теплопровод и один теплосъем (рис. 2.2).
Для ректификации смеси на две фракции, обогащенные легко- и тя-
желолетучими компонентами, в заданном количестве или с заданным со-
держанием в них целевых компонентов применяется технологическая схе-
ма установки с полной ректификационной колонной (рис. 2.2, а). В таком аппарате сырье подается в середину колонны, дистиллят, обогащенный легколетучими компонентами или фракциями, отбирая сверху, а остаток,
обогащенный тяжелолетучими компонентами или фракциями, - снизу ко-
лонны.
Секция колонны, расположенная выше ввода сырья, называется кон-
центрационной или укрепляющей; секция, расположенная ниже ввода сы-
рья, - отгонной или исчерпывающей. При подаче сырья в колонну в паро-
вой или жидкой фазах нижняя тарелка концентрационной или соответственно верхняя тарелка отгонной секции колонны называется та-
релкой питания. При паро-жидкостном состоянии сырья обе указанные та-
релки называются тарелками питания. Для создания жидкостного и паро-
вого орошения в полной колонне установка имеет конденсатор и кипятильник.
14
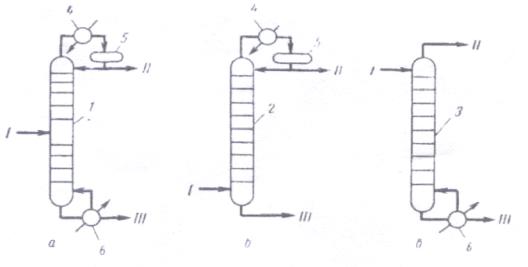
Рис. 2.2. Схема ректификации смесей в простых колоннах:
а - паровые и жидкие смеси в полной колонне; б - паровые смеси в укрепляющей колонне; в - жидкие смеси в отгонной колонне;
1- полная колонна; 2 - укрепляющая колонна, 3 - отгонная колонна, 4 - конденсаторы-холодильники; 5 -емкости орошения; 6 - кипятильники;
I - сырье; II - дистиллят; III - остаток.
При отсутствии особых требований к качеству одного из продуктов
применяют установки с неполными ректификационными колоннами: ук-
репляющими и отгонными (рис. 2.2, б, в). В укрепляющую колонну сырье
подается в паровой фазе под нижнюю тарелку, в отгонную - в жидкой фазе
на верхнюю тарелку колонны.
Ректификация смесей может осуществляться также с водяным паром
или инертным газом, которые подаются в нижнюю часть колонны наряду с
подогревом или вместо подогрева остатка (рис. 2.3), водяной пар может
подаваться также и с сырьем, например при ректификации мазута в ваку-
умных колоннах. В вакуумных и отпарных колоннах (рис. 2.3, а, б, в) во-
дяной пар снижает парциальное давление паров продукта и способствует
отпарке легких фракций без значительного повышения температуры низа
колонны для схемы, изображенной на рис 2.3, а, в, или при температуре
ниже начальной температуры сырья для схемы, изображенной на рис.
2.3, б. В полных колоннах, работающих под давлением, близким к атмо-
15
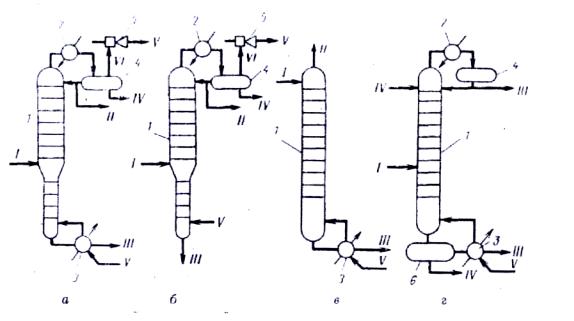
сферному, или при повышенном давлении (рис. 2.3, г), водяной пар или вода подаются для снижения температуры низа колонны и для увеличения производительности подогревателя за счет повышения средней разности температур потоков.
Рис. 2.3. Схемы ректификации смесей с водяным паром:
а- смеси под вакуумом с подогревом и испарением части остатка;
б- смеси под вакуумом без подогрева остатка; в - жидкие смеси в отпарной колонне; г - смеси в полной колонне при атмосферном или повышенном
давлении; 1 - колонна; 2 - конденсаторхолодильник; 3 -подогреватель-кипятильник;
4 - емкость орошения; 5 - эжектор; 6 - отстойник;
I - сырье; II - дистиллят; Ш - остаток; IV - вода; V - водяной пар;
VI - несконденсированный пар и инертный газ.
2.3 Сложная ректификационная колонна
Сложная ректификационная колонна имеет больше одного сырье-
вого и больше двух продуктовых потоков, а также промежуточные теп-
лопроводы и теплосхемы. Из перечисленных условий достаточно лишь од-
ного, чтобы колонна из простой стала сложной. В промышленности уже
давно используются сложные ректификационные колонны, однако в по-
16
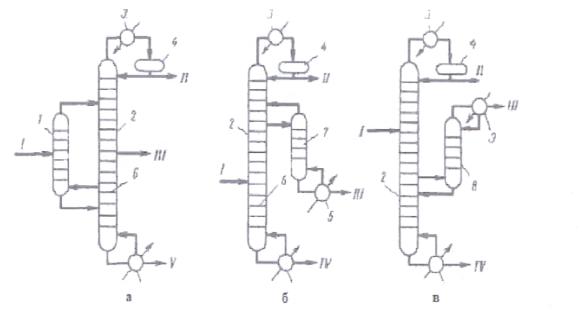
следние годы к ним проявляется повышенный интерес, свидетельством
чему - большое число патентных материалов и научных исследований по
применению сложных ректификационных колонн в различных технологи-
ческих процессах.
Применение сложных ректификационных колонн позволяет зна-
чительно уменьшить не только эксплуатационные, но и капитальные за-
траты за счет улучшения термодинамических условий разделения, рацио-
нальной организации теплообмена, совмещения в одном аппарате
нескольких технологических процессов и т. д.
Рис. 2.4. Схемы ректификации смесей в колоннах, связанных материальными и тепловыми потоками:
а - простая и сложная колонны; б - полная колонна с боковой отпарной секцией; в - полная колонна с боковой укрепляющей секцией; 1 - колонна предварительного разделения; 2 - основная колонна;
3 - конденсатор-холодильник; 4 - емкость орошения; 5 - кипятильник; 6 - тарелки; 7 - отпарная колонна; 8 - укрепляющая колонна;
I - сырье; II - дистиллят; III - боковой погон; IV - остаток.
К сложным ректификационным колоннам можно отнести также сис-
темы колонн, связанные материальными и тепловыми потоками (рис. 2.4),
17
в таких системах предьщущая и последующая колонны связаны про-
тивоположно направленными паровыми и жидкостными потоками, со-
единяющими верх и низ предыдущей колонны с точками ввода питания последующей колонны (рис. 2.4, а) или верх последующей колонны с бо-
ковым отбором предыдущей (рис. 2.4, б) и, наконец, низ последующей ко-
лонны с боковым отбором предыдущей (рис. 2.4, в).
Применение системы ректификационных колонн, связанных мате-
риальными и тепловыми потоками, позволяет на 20-50 % снизить общие затраты тепла и холода по сравнению с простыми или сложными колонна-
ми. Независимо от числа получаемых продуктов технологические схемы установок, где используются колонны, связанные материальными и тепло-
выми потоками, имеют один дефлегматор и один кипятильник, однако на практике такие схемы колонн эффективны только при разделении близко кипящих многокомпонентных смесей, так как лишь в этом случае в по-
следней колонне могут быть приняты температуры верха и низа, удовле-
творяющее экономичным условиям конденсации и испарения получаемых продуктов.
18
3 КОНСТРУКЦИЯ ТАРЕЛЬЧАТЫХ КОЛОННЫХ АППАРАТОВ
Конструкции тарельчатых колонн весьма разнообразны. Это объ-
ясняется чрезвычайно большим ассортиментом перерабатываемого сырья,
широким диапазоном производительности и различным гидравлическим режимом колонн. В качестве конструкционного материала для изготовле-
ния колонных аппаратов наиболее широко применяют углеродистую и ки-
слостойкую сталь, реже - цветные металлы и чугун. В настоящее время ос-
ваиваются тарельчатые колонны из неметаллических материалов -
керамики, графита и фторопласта.
Для удобства монтажа и ремонта тарелок расстояние между ними желательно принимать не менее 450 мм. Монтаж и обслуживание тарелок в аппаратах с цельносварным корпусом выполняют через люки. Люки на корпусе колонны рекомендуется располагать через каждые пять-десять та-
релок в зависимости от диаметра аппарата и типа контактных устройств.
Диаметр люков может колебаться от 450 до 600 мм, а расстояние между тарелками в месте установки люка от 800 до 1000 мм.
Корпуса тарельчатых колонных аппаратов изготовляют большей ча-
стью с постоянным по высоте диаметром, хотя для колонн больших разме-
ров в случае, если нагрузка по жидкости и пару (газу) значительно изменя-
ется по высоте колонны, корпус может быть выполнен ступенчатым, т. е.
состоящим из частей разного диаметра, соединенных конусными пере-
ходами.
На корпусе, например, ректификационной колонны предусматрива-
ют штуцера: ввода продукта и вывода пара, ввода флегмы и пара из кипя-
тильника, вывода кубового остатка и циркулирующей кубовой жидкости в кипятильник. Кроме того, аппарат снабжают штуцерами для измерения давления и температуры по высоте аппарата, уровня жидкости, отбора проб и др.
19
Места ввода сырья и вывода промежуточных фракций зависят от со-
става сырья; поэтому предусматривают несколько запасных штуцеров по высоте колонны.
Корпус тарельчатой колонны может быть выполнен либо сварным,
либо состоящим из царг.
Корпуса аппаратов, работающих при больших рабочих давлениях, а
также аппаратов диаметром более 1200 мм выполняют цельносварными.
Аппараты диаметром 400-1000 мм изготовляют в царговом исполнении,
если рабочее давление в них не превышает 1,6 МПа.
В химической и нефтеперерабатывающей промышленности при-
меняют тарельчатые колонны различных размеров: от небольших, диа-
метром 300-400 мм до крупнотоннажных высокопроизводительных ус-
тановок с колоннами диаметром 5-12 м. Высота колонны зависит от числа тарелок и расстояния между ними. Чем меньше расстояние, тем ниже ко-
лонна. Однако при уменьшении расстояния между тарелками увеличивает-
ся унос брызг и возникает опасность переброса жидкости с нижних таре-
лок на верхние, что существенно уменьшает к.п.д. установки. Поэтому обычно расстояние между тарелками 250-300 мм. По соображениям конст-
руктивного порядка и возможности ремонта и очистки тарелок в колоннах большого диаметра расстояния между ними увеличивают до 500-600 мм.
Рекомендованные расстояния между тарелками приведены ниже:
Диаметр колонны, м |
до 0,8 |
0,8-1,6 |
1,6-2 |
2-2,4 |
более 2,4 |
|
Расстояние между |
200-350 |
350-400 |
400-500 |
500-600 |
более |
|
тарелками, мм |
600 |
|||||
|
|
|
|
Кипятильники в ректификационных установках малой производи-
тельности делают в виде змеевиков, установленных непосредственно в ку-
бе, но более часто кипятильник монтируют в виде выносного тепло-
обменника, который устанавливают вертикально около куба, и связывают с ним двумя патрубками. Колонны периодического действия имеют кубы большой емкости, достаточной для приема единовременной загрузки про-
20