
Основы проектирования электронных средств Материалы к Экз ОПЭС-2014 РК-01-02 / Не для распространения Введение в технологию поверхностного монтажа
.pdf
Рис. 3.3. ПЗС-камеры для центрирования компонентов
СТЗ на основе камеры с линейной матрицей (Рис. 3.4) позволяет центрировать компоненты на лету во время прохождения установочного модуля над камерой. Момент считывания изображения синхронизирован с сигналом обратной связи с осей перемещения установочного модуля. Таким образом изображение на камере ставится в соответствие компоненту на определенной головке.
Рис. 3.4. Камера с линейной матрицей, центрирующая компоненты на лету
Рис. 3.5. Центрирование компонентов лазером
Центрирование лазером – самый быстрый способ центрирования, поскольку оно производится в процессе перемещения установочного модуля от позиции захвата компонентов к ПП. Однако таким способом можно центрировать только простые и небольшие компоненты, причем только по корпусу. Выводы не только не распознаются, но и мешают распознаванию компонентов. Работает эта система следующим образом. После захвата компонент поворачивает до тех пор, пока размер тени, отбрасываемой этим компонентом на приемник, не достигнет минимума. Так как системе известно положение центра вакуумного захвата, то она может определить смещение компонента относительно
61
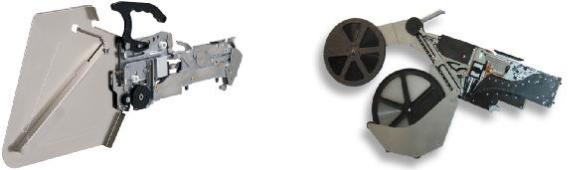
центра захвата по ширине компонента, соответствующей минимальной отбрасываемой тени. Затем компонент поворачивается на 90º, и определяется смещение компонента относительно центра захвата по длине.
СТЗ оборудуются различными системами освещения. Освещение сверху позволяет получить проекцию компонента на камере и используется для распознавания компонентов в корпусе TSOP, QFP, но непригодно для компонентов с выводами под корпусом – BGA, CSP. В этом случае используется освещение сбоку и снизу. Современные автоматы позволяют производить подсветку компонентов под различными углами и с регулируемой яркостью, что обеспечивает высокое качество распознавания.
3.1.2. Типы питателей
Существует большое количество разнообразных типов питателей, однако наиболее широко используются питатели из ленты, кассет, кассет с россыпью, матричных поддонов, которые будут рассмотрены ниже.
Питатели из ленты. Около 80-90% всех ПМИ поставляется в упаковке в ленту. Питатели из ленты подразделяются на пневмомеханические (см. Рис. 3.6) и электронные. Электронные питатели, в свою очередь, бывают одинарные и двойные (см. Рис. 3.7). Двойные электронные питатели позволяют подавать компоненты из двух лент, используя при этом одно посадочное место.
Одна катушка с лентой содержит, как правило, 2000-10000 компонентов. В стандарте Международной электротехнической комиссии IEC 286-3 определены следующие значения ширины ленты: 8, 12, 16, 24, 32, 44 и 56 мм.
Рис. 3.6. Пневмомеханический питатель из ленты Рис. 3.7. Двойной электронный питатель из ленты
Питатели из кассет. В данном случае компоненты упаковываются в кассеты, имеющие форму трубок, в которых компоненты располагаются друг за другом. Соответствие поперечного сечения кассеты размерам компонента гарантирует правильную ориентацию компонентов в кассете. Основные недостатки питателей из кассет таковы:
∙количество компонентов в кассете ограничено, поэтому необходимо производить частую смену кассет;
∙компоненты в кассете касаются друг друга.
62

Рис. 3.8. Ременной питатель из кассет |
Рис. 3.9. Вибропитатель из кассет |
Для подачи компонентов из упаковки в кассеты могут использоваться ременные (см. Рис. 3.8) и вибропитатели (см. Рис. 3.9). Они совместимы с автоматами с пневмомеханическими и электронными питателями. Питатели из кассет занимают несколько посадочных мест в зависимости от ширины питателя. Количество ручьев с компонентами зависит от типа подаваемых компонентов.
Питатели из кассет с россыпью. Как правило, питатели такого типа, используются для подачи чип-конденсаторов, чип-резисторов и компонентов в корпусах melf. Эти компоненты характеризуются простотой конструкции и наличием нескольких осей симметрии. К тому же они устойчивы в работе и имеют низкую вероятность повреждения.
Достоинства питателей из кассет с россыпью:
∙недорогая упаковка компонентов (нет необходимости использования дорогой ленты);
∙большое количество компонентов в кассете;
∙отсутствие отходов, таких как пустая лента и покровная лента;
∙легкое пополнение камеры питателя.
Однако такие питатели обладают и рядом недостатков:
∙более сложная проверка компонентов;
∙большая чувствительность к повреждениям;
∙риск повреждения компонентов;
∙возможность использования для подачи ограниченного спектра компонентов;
∙риск пылеобразования, что может отрицательно сказаться при пайке.
Питатель из кассет с россыпью (см. рис. 1.9) занимают одно посадочное место, что, безусловно, является большим преимуществом. Питатель сконструирован таким образом, чтобы обеспечить максимальную надежность подачи компонентов, а также снабжен автоматическим определением наличия компонента. Смена кассет может производиться без остановки автомата.
Рис. 3.10. Питатель из кассет с россыпью
Питатели из матричных поддонов. Питатели из матричных поддонов используются для подачи больших микросхем, обычно имеющих выводы с четырех сторон корпуса, например, QFP. Поддон – пластиковый держатель, имеющий полости,
63

расположенные в матричном порядке, в каждой из которых содержится по одному ПМИ. Матричные поддоны устанавливаются на лотки, представляющие собой стальные пластины.
Достоинство питателей из матричных поддонов в том, что все ПМИ упакованы отдельно. Кроме этого, жесткая упаковка исключает изгибания, имеющие место при использовании питателей из ленты. Недостатки таковы:
∙относительно малое количество ПМИ в поддоне, поэтому требуется частая смена поддонов;
∙более дорогая упаковка (иногда многоразового использования);
∙поддоны требуют аккуратного обращения, так как компоненты сместятся, если поддоны будут подвергнуты ударному воздействию, что может привести к неправильному захвату или повреждению выводов компонентов.
Савтоматами могут быть использованы различные типы питателей из матричных поддонов: внутренний, ручной, автоматический питатель, питатель из матричных поддонов JEDEC.
Внутренний питатель из матричных поддонов (см. Рис. 3.11), устанавливаемый между задней базой питателей и задней направляющей конвейера, позволяет подавать компоненты из одного или двух поддонов. Немаловажно, что данный питатель не сокращает количество посадочных мест под питатели из ленты.
Рис. 3.11. Внутренний питатель из матричных поддонов
Оборудование автомата ручным питателем из матричных поддонов (см. Рис. 3.12) – недорогое средство обеспечения возможности подачи компонентов из такой упаковки. Данный питатель предназначен для установки на заднюю базу питателей, с которой он может быть быстро демонтирован в случае необходимости.
Рис. 3.12. Ручной питатель из матричных поддонов
64

Рис. 3.13. Автоматический питатель LCS
Вместимость автоматического питателя LCS (см. Рис. 3.13) составляет 120 матричных поддонов, замена которых может производиться без остановки автомата. Питатель оборудован встроенным инспекционным конвейером, позволяющим проводить визуальный контроль ПП. Компоненты из матричных поддонов с помощью двойного челнока доставляются в зону захвата. Дополнительным преимуществом питателя такого типа является то, что он не ограничивает максимальную ширину ПП и количество посадочных мест под питатели.
Питатель из матричных поддонов JEDEC (см. Рис. 3.14) обладает вместимостью до 20 высоких или 30 низких поддонов. Он позволяет проводить замену поддонов без остановки автомата, а, кроме того, быстро демонтируется с задней базы питателей.
Рис. 3.14. Питатель из матричных поддонов JEDEC
3.1.3.Типы приводов
Вавтоматах установки компонентов используются три типа приводов: ∙ приводы с ременной передачей; ∙ приводы с шариково-винтовыми парами; ∙ приводы с линейным двигателем.
Приводы с ременной передачей. Преимущества таких приводов – это простота и дешевизна, главные недостатки – пониженная точность из-за люфтов и растяжения ремня и относительная недолговечность. К тому же существует необходимость использования дополнительного оборудования для контроля натяжения ремня.
65
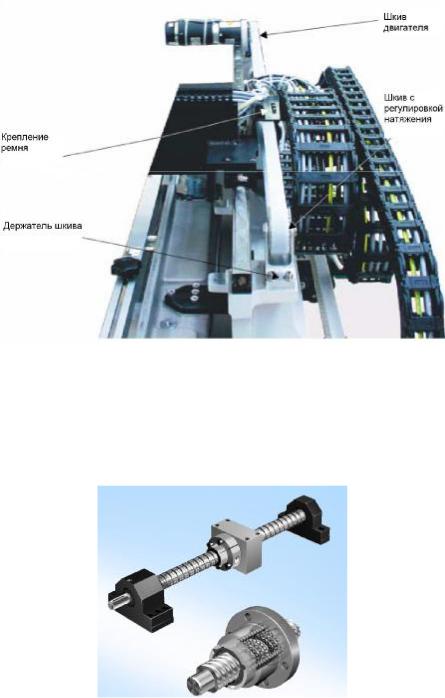
Рис. 3.15. Привод с ременной передачей
Приводы с шарико-винтовыми парами. Данные приводы обладают массой достоинств, включающих в себя высокую точность и надежность, высокую нагрузочную способность и осевую жесткость. Приводы с шарико-винтовыми парами характеризуются большой долговечностью и высоким коэффициентом полезного действия (85-90%). Также они имеют плавный ход и зарекомендовали себя как надежные устройства при работе на высоких скоростях.
Рис. 3.16. Привод с шарико-винтовой парой
Длинная и сложная цепь преобразования вращательного движения двигателя в поступательное движение исполнительного механизма – недостаток приводов такого типа. Кроме того, люфты оказывают влияние на точность позиционирования, которая также снижается из-за износа. Отметим, что на точность влияют и температурные деформации валов. Приводы с шарико-винтовыми парами обладают большей стоимостью, чем приводы с ременной передачей.
Приводы с линейными двигателями. Принципиальное отличие приводов с линейными двигателями от приводов других типов в отсутствии преобразования вращательного движения в поступательное. Более того, за счет отсутствия люфтов достигается очень высокая точность позиционирования исполнительного механизма. Отсутствие изнашивающихся узлов – следующее немаловажное достоинство таких приводов. Единственный недостаток приводов с линейными двигателями – это их высокая цена.
66

Рис. 3.17. Направляющая привода с линейным двигателем
На Рис. 3.18 приведено сравнение динамических характеристик привода с шариковинтовой парой и с линейным двигателем. Очевидно, что по этой характеристике приводы с линейным двигателем превосходят приводы с шарико-винтовой парой, которые имеют довольно широкую зону нечувствительности.
Рис. 3.18. Сравнение динамических характеристик привода с шарико-винтовой парой и с линейным двигателем
3.2. Классификация автоматов установки ПМИ
Классификация автоматов установки ПМИ может быть проведена по нескольким признакам:
1.по принципу действия (см. Табл. 3.1):
∙по движению ПП: o по X;
o по Y; o по X,Y;
o ПП неподвижна;
∙по количеству ПП в рабочей зоне автомата: o одна;
o две;
o больше двух;
2.по производительности:
∙начального уровня (до 4000 комп./ч);
∙среднепроизводительные (4000-10000 комп./ч);
∙высокопроизводительные (10000-20000 комп./ч);
67

∙сверхвысокопроизводительные (более 20000 комп./ч);
3.по точности:
∙прецизионные;
∙высокопрецизионные;
4.по типу приводов:
∙с ременной передачей;
∙с шарико-винтовыми парами;
∙с линейным двигателем;
5.по типу станин:
∙сборные;
∙сварные;
∙литые.
ПП движется |
Количество ПП в рабочей зоне автомата |
|||
1 |
2 |
>2 |
||
|
||||
по X |
Схема X-1 |
|
|
|
по Y |
Схема Y-1 |
Схема Y-2 |
|
|
по (X,Y) |
Карусель |
|
|
|
|
Один портал 1 |
Один портал 2 |
Захват и установка |
|
ПП неподвижна |
Два портала 1 |
Два портала 2 |
сразу нескольких |
|
|
Роторная головка 1 |
Роторная головка 2 |
компонентов |
Табл. 3.1. Классификация автоматов установки ПМИ по принципу действия
3.3. Характеристика каждой из схем автоматов
3.3.1. Схемы автоматов с раздельным перемещением (X-1, Y-1, Y-2)
Возможность оснащения большим числом питателей и одновременный захват и установка компонентов – достоинства автоматов с раздельным перемещением. Данная конструкция обладает повышенной жесткостью, так как и ПП, и головки перемещаются только по одной оси. Как правило, такие автоматы оборудуются сервоприводом по одной оси. Дополнительное преимущество схемы Y-1 заключается в расположении питателей с одной стороны автомата. Отметим, что центрирование компонентов осуществляется на лету, что не требует дополнительных затрат времени.
Y1
Y2 |
X |
Рис. 3.19. Схема X-1
Недостатки, свойственные автоматам с раздельным перемещением:
∙большой ход портала;
∙подвижная ПП;
∙громоздкость;
∙коррекция захвата возможна только с использование интеллектуальных питателей.
68

X1 |
X2 |
|
Y |
Tцикла |
|
Захват |
Захват |
Установка
Рис. 3.20. Схема Y-1 и временная диаграмма
На Рис. 3.21 показана зависимость производительности автомата, построенного на схеме Y-1, от числа головок для различных максимальных скоростей по Y, а на Рис. 3.22 – от ускорения. Из графиков видно, что количество головок на установочном модуле оказывает большее влияние на производительность, чем скорость и ускорение. Это объясняется тем, что высокая максимальная скорость полезна только в случае большого расстояния между позициями захвата и установки компонента. Во время захвата и установки компонента эта максимальная скорость достигнута не будет. Большое значение ускорения вносит только частичный вклад, так как допустимые уровни ускорения, действующего на ПП, значительно ограничены необходимостью снижения риска смещения предустановленных компонентов.
комп./ч |
25000 |
|
|
|
|
20000 |
|
|
|
|
|
Производительность, |
|
|
|
|
|
15000 |
|
|
|
v=1.5 |
|
|
|
|
v=2 |
||
|
|
|
|
||
10000 |
|
|
|
v=2.5 |
|
|
|
|
v=3 |
||
|
|
|
|
||
5000 |
|
|
|
|
|
0 |
4 |
6 |
8 |
10 |
|
|
2 |
||||
|
|
Число головок на Y-приводе |
|
||
Рис. 3.21. Зависимость производительности от числа головок для различных максимальных |
|||||
|
|
скоростей по Y (Amax = 20 м/с2) |
|
Производительность, |
|
17800 |
|
|
|
|
17600 |
|
|
|
|
комп./ч |
17400 |
|
|
|
|
17200 |
|
|
|
||
17000 |
|
|
|
||
16800 |
|
|
|
||
16600 |
|
|
|
||
16400 |
|
|
|
||
16200 |
|
|
|
||
|
|
|
|
|
|
|
|
15 |
20 |
30 |
40 |
|
|
|
Ускорение, м/с^2 |
|
|
Рис. 3.22. Зависимость производительности от ускорения (Vmax = 1,5 м/с) |
69
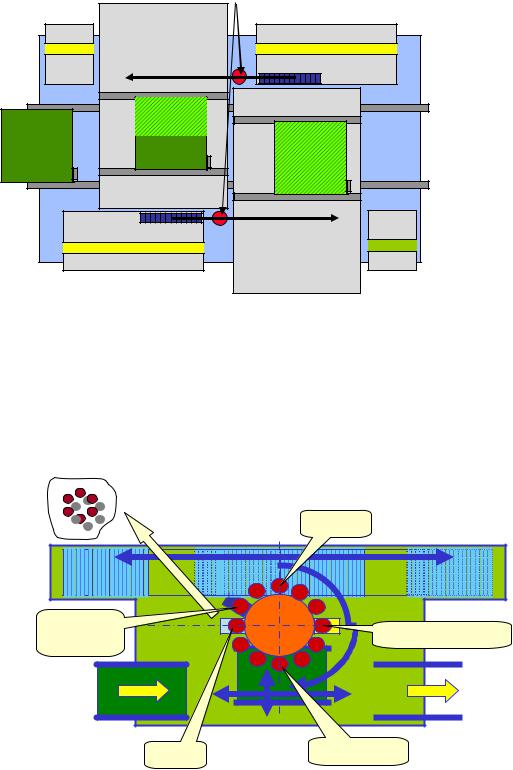
|
Две камеры с линейной матрицей |
8-16 |
40 посадочных мест |
мест |
|
|
Два уст. модуля с 12-ю |
|
головками |
|
Автоматическая |
|
регулировка |
|
ширины |
|
конвейера |
40 посадочных мест |
8-16 |
мест |
|
Рис. 3.23. Схема Y-2. GEM Sapphire |
Существует несколько факторов, снижающих производительность автоматов с раздельным перемещением: затраты на вход/выход и центрирование ПП, ограничения со стороны топологии ПП (расстояние между компонентами и количество устанавливаемых компонентов). В число этих факторов входят изменение расстояния между зоной захвата и зоной установки, затраты времени на смену захватов, а также повторный захват компонентов.
3.3.2. Схема автоматов с установочным модулем карусельного типа
Захват
Выбор |
Центрирование |
|
насадки |
||
|
||
Сброс |
Установка |
|
Рис. 3.24. Схема автомата с установочным модулем карусельного типа |
Данный принцип наиболее часто используется в высокопроизводительных автоматах установки чип-компонентов. Как правило, автоматы оборудуются 12-24 установочными головками, каждая из которых оснащена тремя-шестью вакуумными захватами с возможностью смены на лету. Захват компонентов из подвижной базы питателей осуществляется одновременно с установкой компонентов на ПП с противоположной стороны карусели (см. Рис. 3.24). ПП фиксируется на подвижном по осям X и Y рабочем столе, перемещения которого обеспечивают требуемое позиционирование ПП для установки компонента.
70